3 minute read
COMING OF AGE
Next Article
WORDS: Sam Davies C ollaborative workspaces, silver spherical monograms nailed to the walls, room to grow by five times, the implementation of lean manufacturing and a resounding American voice carrying through the corridors as a press tour navigates the 15,000-squarefoot space, ambles along a steel walkway and heads down to the squeaky-clean shop floor.
This is not the Arcam the additive manufacturing industry has grown accustomed to over the last 20 years. This, as the logo now tells us, is a GE Additive company.
Before, Arcam was based inside a building three times as small; an ‘entrepreneurial start-up’ bringing to market a ‘unique but young’ technology from multiple offices throughout Gothenburg. Now, with the support of GE, it is looking to propel itself to new heights.
“The commitment was to help this entrepreneurial company become world-class in terms of quality and supply,” opens Jason Oliver, GE Additive CEO and the owner of those intonations reverberating through Arcam’s newly opened Centre of Excellence. “Part of building a great company is having the right facilities and tools for our teams, our customers, our suppliers to come and collaborate together.”
GE has pumped €18m into this new facility, three years after completing the takeover as it launched its Additive business. But its dealings with Arcam predated that acquisition; in 2013, GE Aviation had bought out Avio’s aviation business, which had been using Arcam’s Electron Beam Melting (EBM) technology for four years.
Four weeks before the unveiling of Arcam’s new Gothenburg site, the trio celebrated a landmark moment: Boeing successfully flying two GE9X engines on its 777X aircraft, each of which featured around 250 titanium aluminide blades printed with EBM technology by Avio Aero.
One of these blades is being swung repeatedly by Arcam General Manager Karl Lindblom to demonstrate the 30% weight reduction which is contributing to a 10% increase in fuel efficiency compared with the GE90 engine that came before it. GE Additive is also keen to point out these critical and moving parts can’t be made any other way. Beyond the application showcase, Arcam has materials development and research labs, testing centers for customers, and software, hardware and electronics engineers working on the floor above. The 100 or so people situated here are managed by Annika Ölme and Isak Elfström, who now also have 1,000+ additional R&D brains to pick via GE. They both say it’s nice to have an industrial owner. Lindblom agrees. COMING OF AGE
Lindblom is one of a host of workers who lives upstairs but now finds himself without a desk thanks to a hotdesking policy that encourages internal collaboration. He’s also enjoying the implementation of lean manufacturing, which sees him spend at least 30 minutes on the shop floor three times a week listening to the vexations of the workers there. “Trust your employees, listen to your employees, stop small problems becoming big problems.”
As problems within the business are supressed, the aim is for the machines they are manufacturing to scale. GE took over the company with aspirations of manufacturing 10,000 machines in ten years, with an extra 1,000 for GE’s own deployment. Applications like the GE9X engine blades, and with it the 340 preorders of the Boeing 777X aircraft, will go some way to making that possible. “It takes a certain amount of time before it comes through the pipeline, of course,” Lindblom assesses, “but yes, this means a lot of business for us going forward. It at least shows the direction we are heading. It’s going to be a volume business in ten years, for sure.”
6 SHOWN: AVIO AERO TURBINE BLADE MADE ON THE SPECTRA H EBM MACHINE
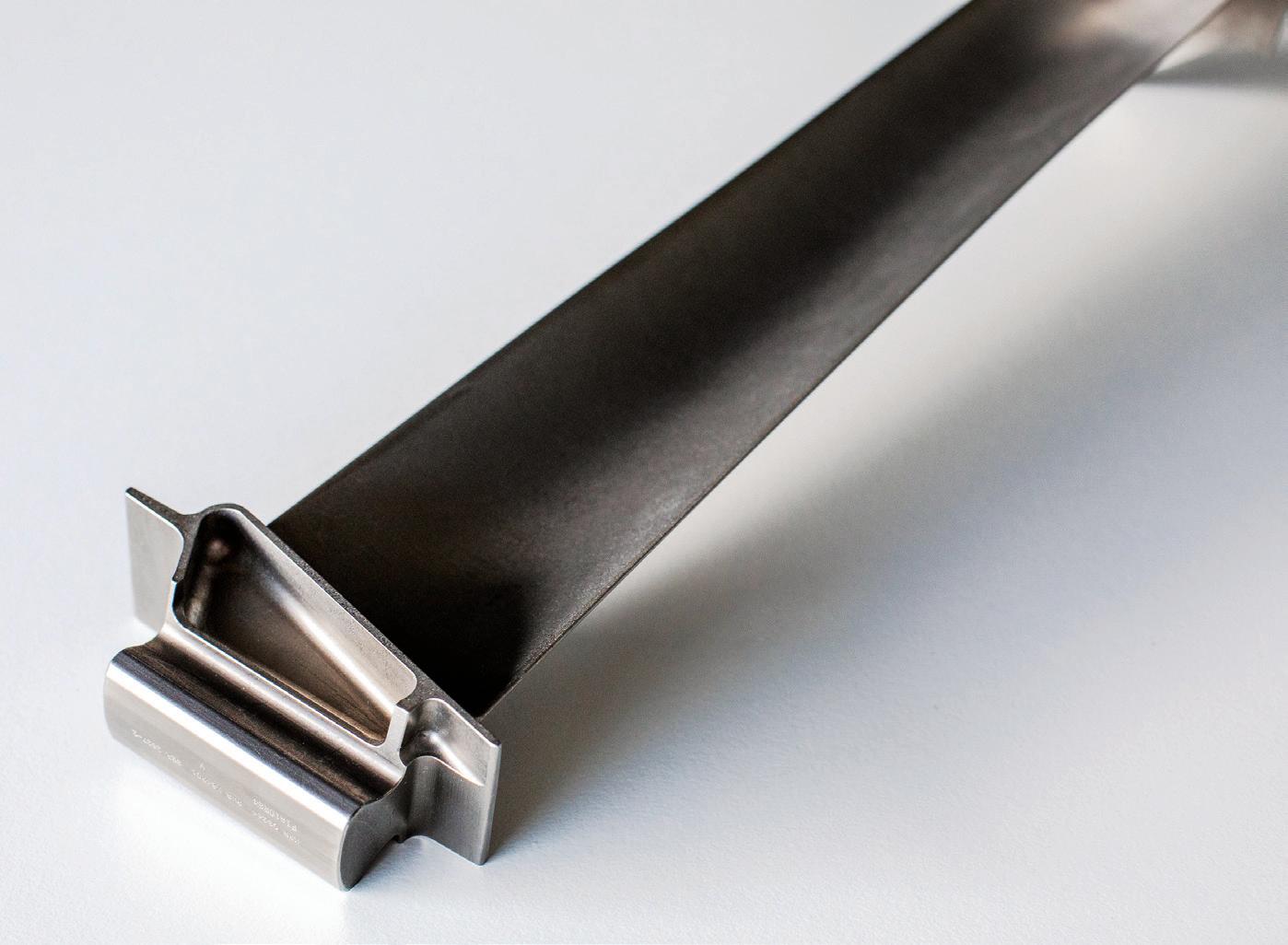
“IT'S GOING TO BE A VOLUME BUSINESS IN TEN YEARS.”