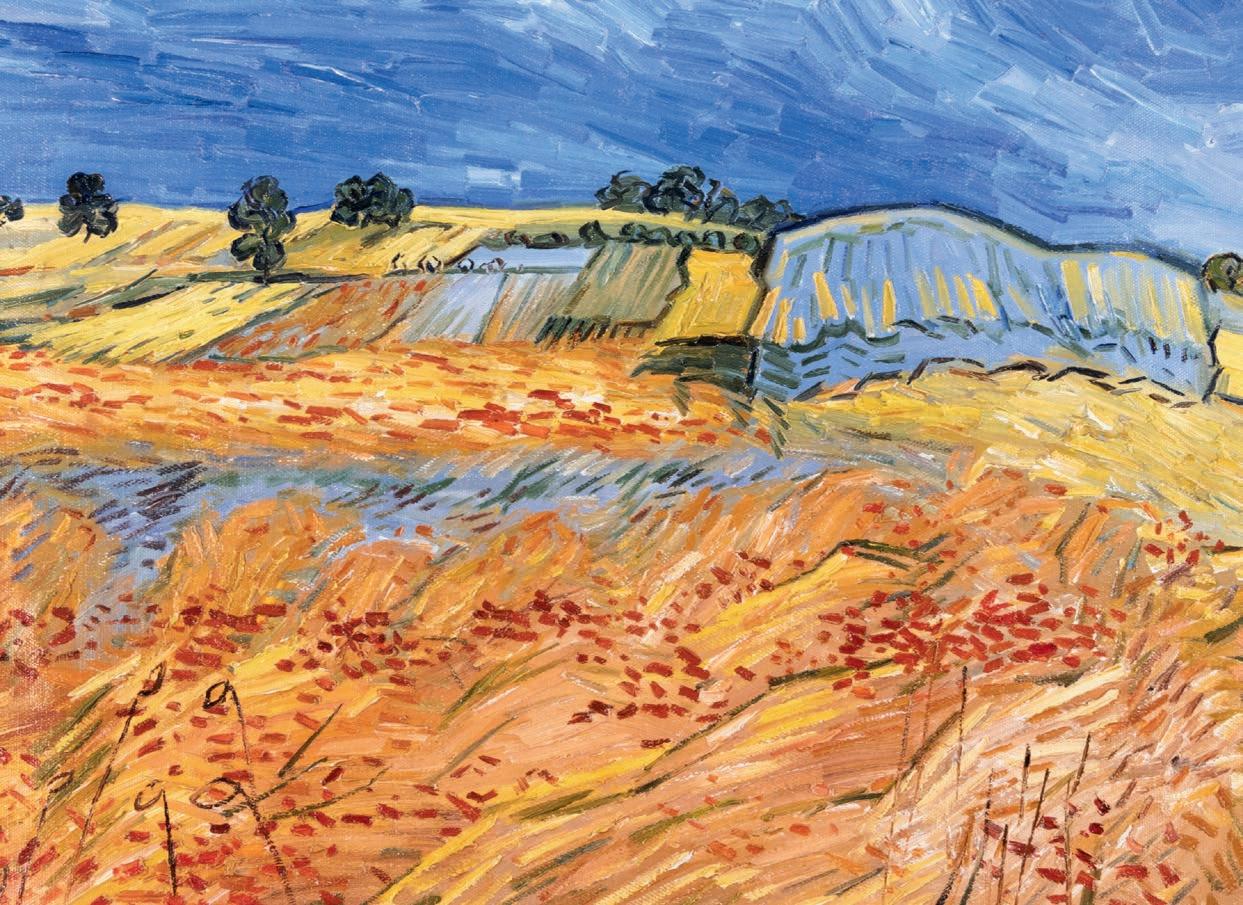
9 minute read
Futuristic Finishes
TODAY’S DIGITAL SCANNING AND PRINTING OPTIONS HAVE TAKEN CUSTOMIZATION TO A WHOLE NEW LEVEL.
BY JENNIFER G. WILLIAMS
Two years ago, David Hernandez bought a large-format inkjet scanner and printer to bring more finishing options to customers of United Finishers, a company that has been making custom furniture for more than 30 years in High Point, North Carolina. “Now, this is our core focus with our business,” says the company partner. “We can apply virtually anything a designer is thinking of onto a wall or boards and really dial it into what they want to achieve. The feedback has been fantastic—we’ve had return customers just because of the versatility we can offer them.” Advances to digital scanning and printing have opened a world of possibilities in the design and manufacturing markets. From small, custom furniture makers to huge panel fabricators, the incredible realism captured by today’s scanners and applications are nothing short of breathtaking. And experts say they are just scratching the surface of possibilities with this evolving technology.
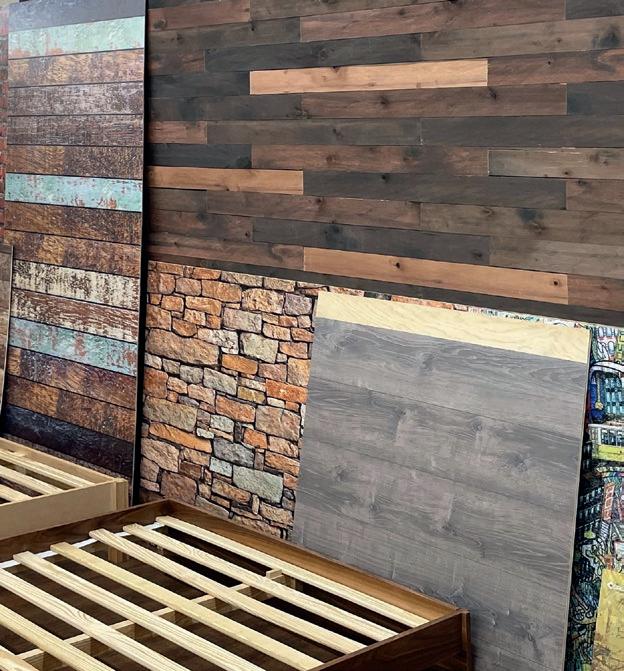
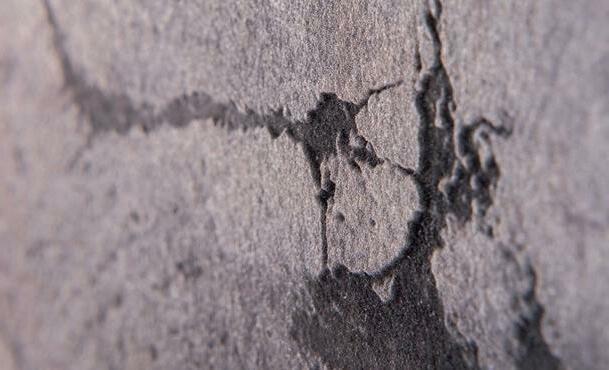
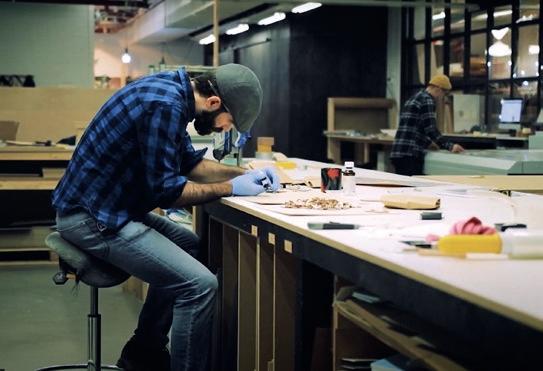
THE ABILITY TO ACCURATELY RECREATE THE TEXTURE OF A SURFACE WITH SPEED AND EASE IS AN INTEGRAL PART OF A SUCCESSFUL IMPLEMENTATION OF A DIGITAL MANUFACTURING PROCESS.
LASER CUT STUDIO, A CREATIVE PRINTING COMPANY BASED IN PASILA, HELSINKI, SPECIALIZES IN PRINTING DIRECTLY ONTO WOOD, SPECIFICALLY PLYWOOD.
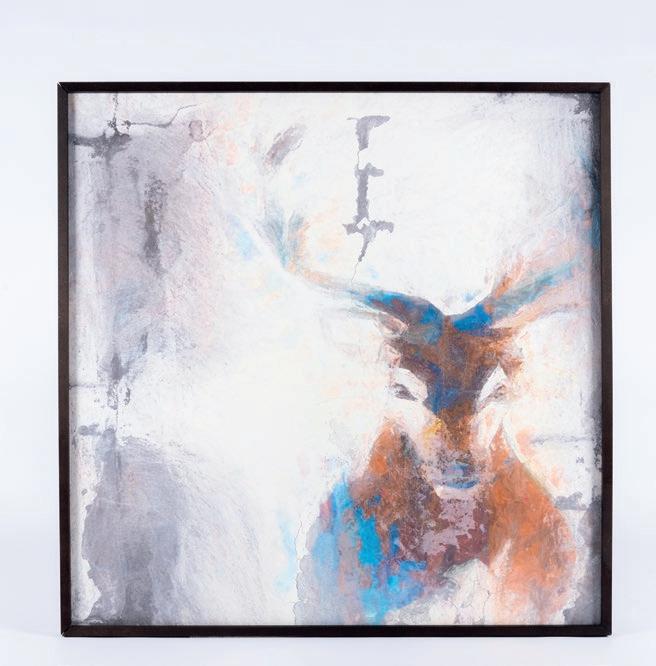
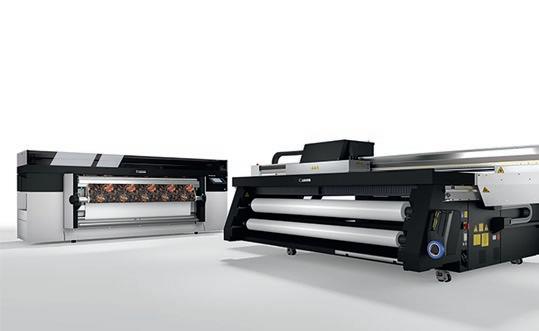

‹ CONTINUED FROM PAGE 32
“These technologies open the door to manufacturing customized products that may have never been envisioned before,” says David Palmieri, Vice President of Sales & Marketing with CGS ORIS. “The key driver has been the scanning technology. These imagecapturing systems have been instrumental in capturing not just accurate color of surfaces but most importantly the 3D surface and texture. The ability to accurately recreate texture of a surface with speed and ease is an integral part of a successful implementation of a digital manufacturing process. The advancements in inkjet printing technologies have also played a tremendous part in accurately recreating these textures. The combination of the two working in harmony has been a game changer for the décor manufacturing business.” Randy Paar, Marketing Manager with Canon USA, says we are only in the infancy of using inkjet printers to create textured, flat surfaces. “With 3D object scanning and 3D printers, the possibilities are truly endless,” he says. “It is really too early to spot trends as this approach is still so new in the market. That said, it provides an excellent opportunity for early adopters to capitalize on this exciting, new capability.”
Hernandez says United Finishers uses their Canon 6170 Flatbed printer to primarily print on 4x8 sheets of plywood up to an inch thick, personalizing and then cutting to size depending on specs. The sheets or boards are then used to craft their custom, patented platform beds, wall panels or art and really anything their customers can dream up, he says. “It really opens up a world of possibilities,” he adds. “No previous method was capable of doing what this does.”
UF chose the Canon printer, he adds, primarily because of “the vacuum, the versatility and the speed with which it can accomplish
CONTINUED ON PAGE 36 ›
Introducing Arclync®

Arclync® is a highly versatile and easy-to-press overlay that protects decorative surfaces against UV, scratches, and moisture. It provides extremely high performance at a fraction of the cost of traditional decorative products. Designed for interior and exterior applications throughout the home, garden, and commercial buildings. Arclync® will add beauty and performance to any wood and non-wood surface.
Experience Arclync® Intelligent Surfacing at IBS Jan 31 - Feb 2, 2023 Las Vegas, NV
Booth # C7125

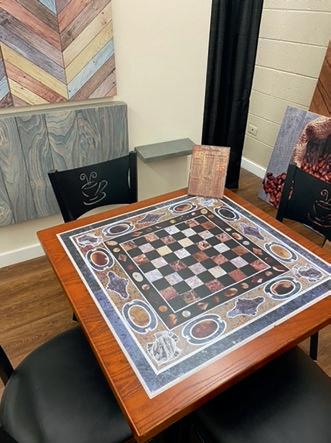
UNITED FINISHERS HAS BEEN MAKING CUSTOM FURNITURE FOR MORE THAN 30 YEARS IN HIGH POINT, NORTH CAROLINA, APPLYING DIGITALLY PRINTED DESIGNS TO WALLS AND BOARDS.
“We can apply virtually anything a designer is thinking of onto a wall or boards and really dial it into what they want to achieve.�
DAVID HERNANDEZ, UNITED FINISHERS the job,” says Hernandez. “Not to mention the machine’s flexibility and its ability to work with wood—specifically plywood.”
UNDERSTANDING THE PROCESS Large format scanners have already been around for quite some time to capture 2D images, says Canon’s Paar. “By using different lighting angles with multiple scanning passes and software to process the data, the scanning systems are also able to capture elevation data. This data can then be combined with the image data, split into separate print files and printed together in sequence on the printer—all with perfect registration.”
Canon’s approach to printing texture with a UV flatbed printer came about from observing how the cured ink created a tactile profile on the surface of printed graphics used for retail POP and signage applications, he adds. “For most typical graphic arts applications this is not necessarily a desirable effect, [but] we quickly realized that due to the accuracy and repeatability of our printer that we could actually use it positively and print multiple layers in correct sequence on top of each other, each layer being progressively different to create the final tactile effect.”
The developments of technical possibilities in both scanning and digital printing have inspired and enabled
PREMIUM TFL PANELS
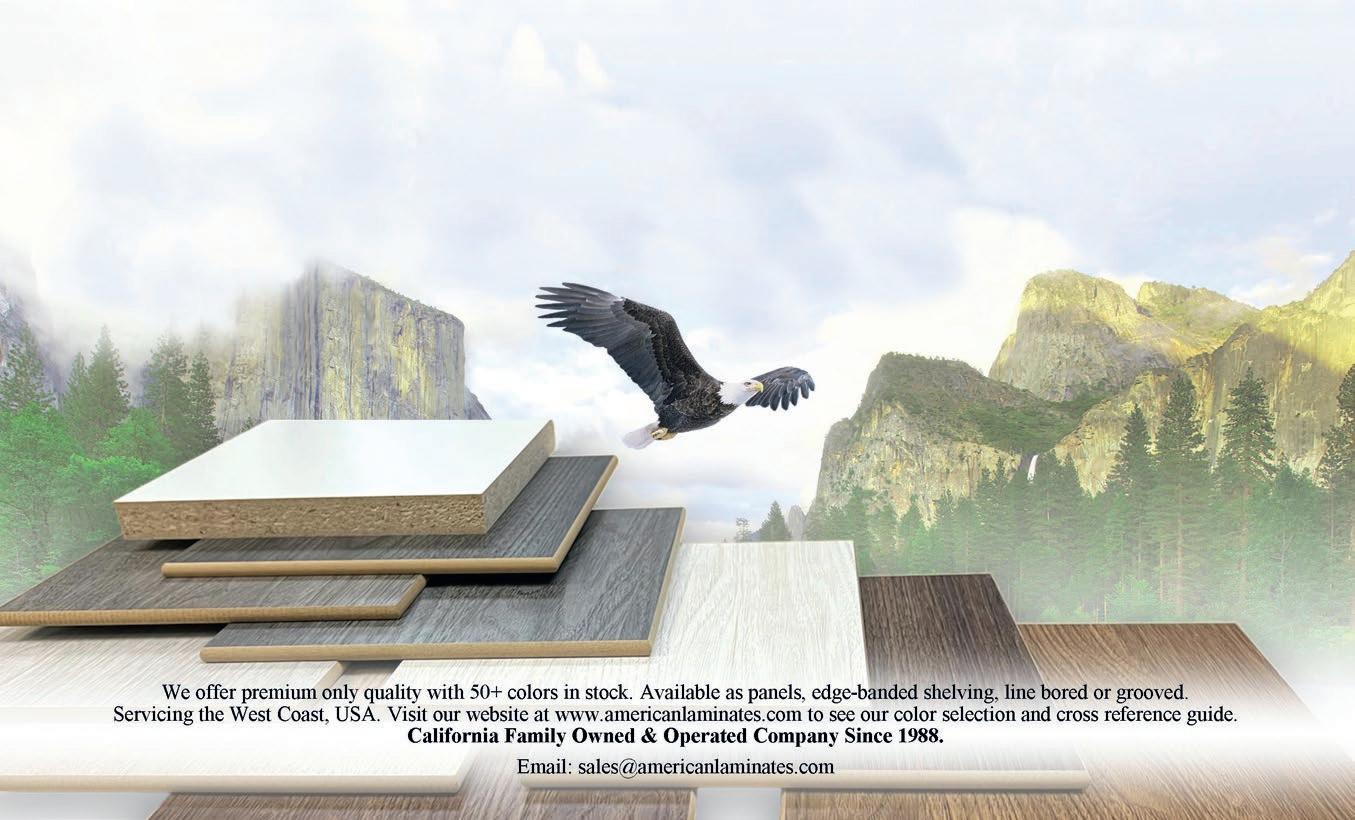
creative applications in a new dimension, says Roberto Zinser, international key account manager with swissQprint. “High-quality 3D scanners not only capture the optical 2D surface, but also the topographic 3D values. True flatbed printers, such as the swissQprint Nyala 4, can reproduce the processed data by printing multiple layers. Software tools and interfaces make the process user-friendly.”
“As far as customization, the sky is the limit it seems, given these new technologies,” he says. “In theory, everything that physically fits under a scanner or on a printer can probably be scanned and printed. That said, the entire application should be evaluated for effort and revenue: What is the material? What is the application? Is some special substrate involved, such as glass, that requires special ink or pre-treatment or post-treatment?”
Helping customers to understand the benefit of digital printing and scanning capabilities has been a key driver in the development of this technology, says Palmieri. “Once the benefits and flexibility of the technology are understood customers have been keen to pursue these alternative manufacturing processes.”
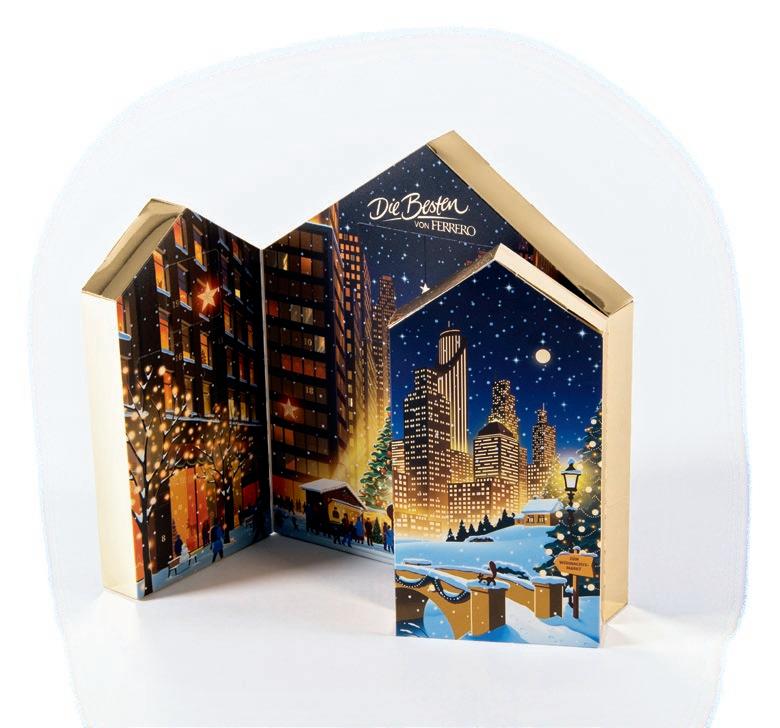
CONTINUED ON PAGE 38 › �The developments of technical possibilities in both scanning and digital printing have inspired and enabled creative applications in a new dimension.�
ROBERTO ZINSER, INTERNATIONAL KEY ACCOUNT MANAGER WITH SWISSQPRINT
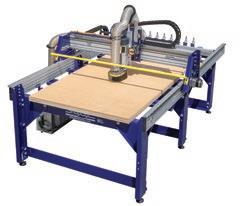
Panel Process Like a Pro Without the Pro Price Tag
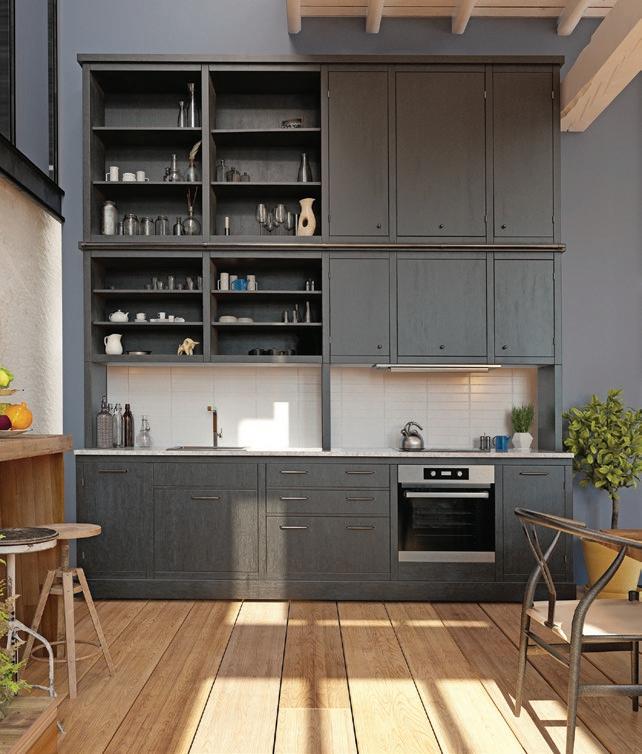
With a ShopBot CNC, you can increase production throughput while minimizing material handling. For example, you can drill shelf pin holes, cut rabbets and dados, and profile-cut the completed panel. The operator only needs to handle the full sheet once to load the machine, and then remove the perfectly cut parts that are ready for assembly.
Thanks to the affordability of ShopBot’s professional grade CNC tools, the technology of manufacturing cabinet boxes, doors, drawer fronts, shelves, and even countertops, is now well within the reach of smaller shops, not just large cabinet manufacturing facilities.
See our full line of tools at ShopBotTools.com. Then give us a call at 888-680-4466. We’ll find the tool that works best for your needs.
DAVID PALMIERI, VICE PRESIDENT OF SALES & MARKETING WITH CGS ORIS
‹ CONTINUED FROM PAGE 37
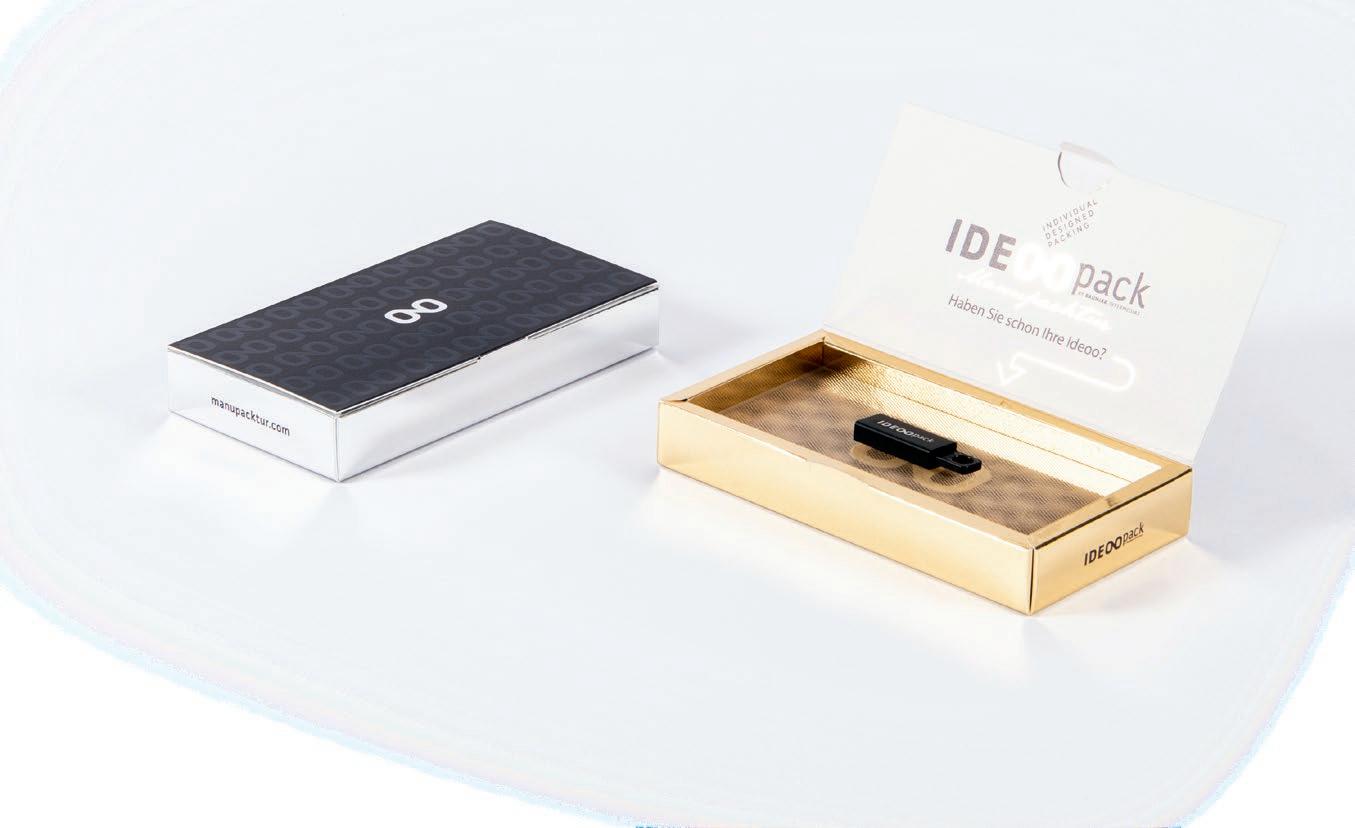
TRENDS AND SAVINGS Customization seems to be the key trend in using these new technologies today.
“We see clear trends in art reproduction and signage as well as in interior decor, furniture and flooring industries, and in the automotive sector,” says Zinser. “But we also see applications in POS: Think of prints with a tactile feel, based on inexpensive and recyclable materials, providing a wood decor, just to name one example. This increasing demand naturally requires ever more productive printing systems. This is where printer manufacturers come into play, and that is what swissQprint continuously working on.”
Hernandez says the most exciting trend at his business are the customized wall planks and board. “Just the ability to give a designer an open canvas to apply anything they want on the wall planks,” he explains. “It’s very exciting. Coffee shops, restaurants, designers can really go wild with their ideas. Our wood wall art is very popular with hotels and motels…for designers, there are just endless possibilities as to what they want to present in their environment.”
And the ability to recreate finishes that mimic more expensive treatments or materials is very cost effective for designers, fabricators and consumers, as well, says Hernandez.
Savings are not only found in the reproduction of more expensive finishes, but also in the benefits of on-demand manufacturing, the biggest trend Palmeri says he has been noticing. “This is a trend that has been in practice and proven in the traditional printing industry for decades,” he explains. “Now that manufacturers of décor products are recognizing that digital workflows can reduce unnecessary inventory of product and produce as needed it creates an obvious opportunity to save money. This trend has only just begun but we expect it to be the new norm as more and more manufacturers of product begin to adopt digital manufacturing processes.” LOOKING TO THE FUTURE Palmieri believes that the adoption of digital manufacturing has only just begun. “The industry has just scratched the surface of what is possible and still relies primarily on legacy manufacturing processes,” he says. “Once more and more businesses adopt digital manufacturing processes for décor, it will create far more possibilities for unique designs. This offers tremendous opportunities and a limitless variety of unique décor options for the end consumer.”
Hernandez says he is excited for future possibilities in the industry. “I like to think we’re at the fringe of it,” he says, “I know this is something that’s definitely going to catch on, and I think the industry is going to really lean into it.” s p
“With 3D object scanning and 3D printers, the possibilities are truly endless.�
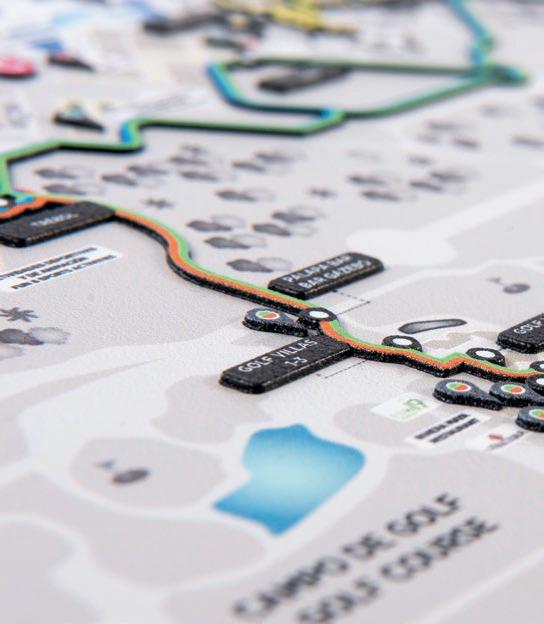