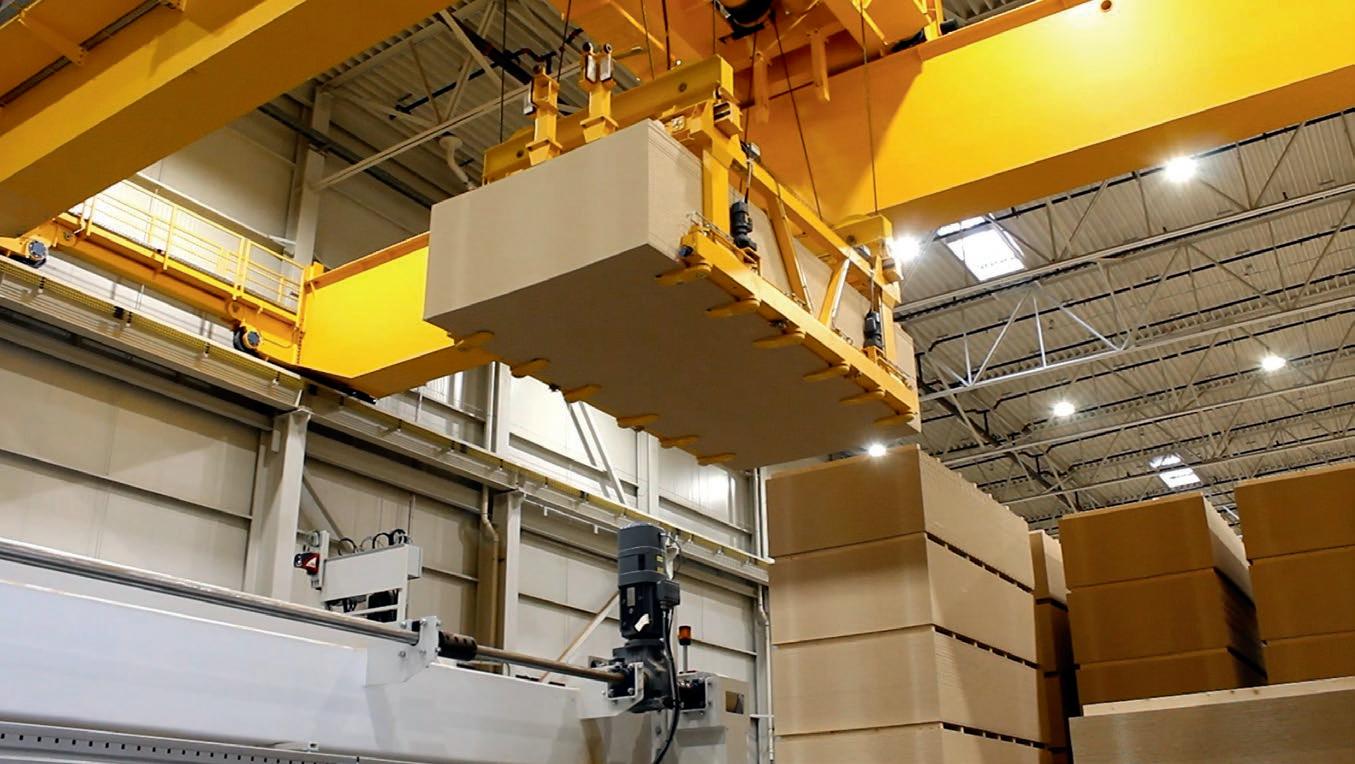
4 minute read
Rising to the Occasion
AUTOMATION HELPS ALLEVIATE SEVERAL CONCERNS IN POST-PANDEMIC PRODUCTION
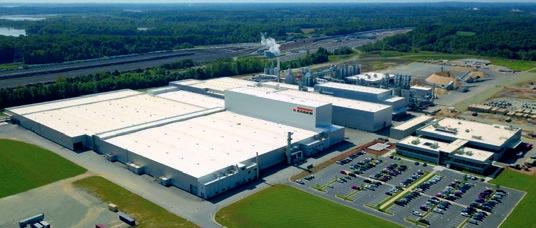
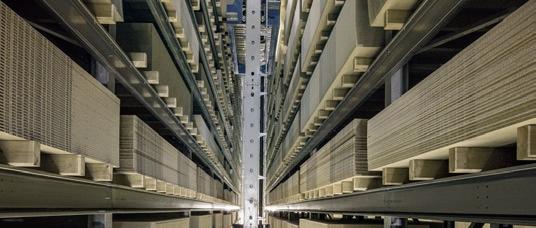
EGGER’S CRANE STORAGE AND HIGH BAY WAREHOUSES ARE PART OF A MULTIBUILDING PRODUCTION AND SHIPPING FACILITY IN LEXINGTON, NORTH CAROLINA. TOP IMAGE: THE PRECISION AND INTRICATE BALANCE REQUIRED FOR THE OPERATION OF AUTOMATIC CRANE SYSTEMS IS MADE POSSIBLE BY SUPPORTING STRUCTURAL COLUMNS THAT DROP NEARLY 100 FEET INTO THE GROUND.
WBY JENNIFER G. WILLIAMS ith continued problems finding skilled workers, many industries have turned to automation to help bridge the gap, and are finding that using automation offers other benefits, as well. EGGER’s Crane Storage and High Bay Warehouses are part of a multi-building production and shipping facility for raw particleboard and thermally fused laminate (TFL) made from the particleboard. You’ll see a lot of activity in these buildings, but what you won’t see a lot of are workers: the entire process, from production to storage to shipping, is completely automated, using cranes, conveyor belts and an automated rail system to move boards between buildings. “By incorporating automated systems into our processes, our production warehouses need very limited staffing, typically just a single material flow administrator,” says Kenneth Brown, Plant Manager for Logistics. “This allows us to prioritize our employees in other areas of the facility, allowing us to more effectively manage labor challenges.” Once particleboard panels are produced at EGGER, conveyors move the stacked boards from production to Crane Storage. A computer-controlled warehouse crane stacks the boards for storage and quality testing. Once quality testing is complete, the boards
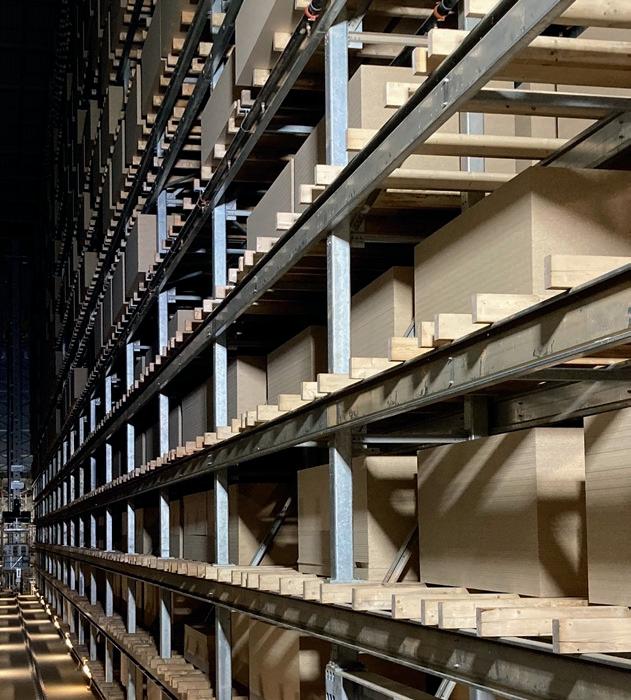
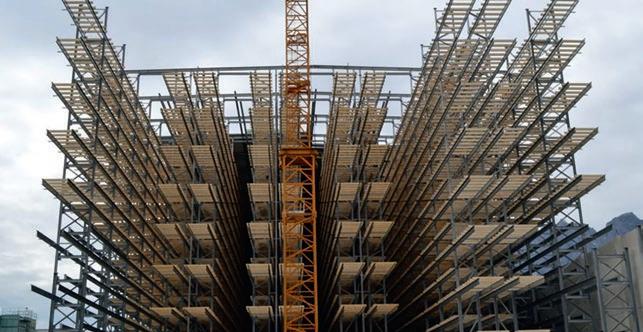
KENNETH BROWN, EGGER'S PLANT MANAGER FOR LOGISTICS
are cleared to be shipped as raw particleboard or to be used in TFL production. Bundles that do not meet the quality requirements are either used as packing material or recycled to create another batch of particleboard, eliminating any waste.
The North Carolina warehouse will hold up to 750 truckloads of particleboard, or about 10 days’ worth of production.
“Our production warehouses allow us to stock enough particleboard to serve as a buffer in the event of any production downtime,” Brown says. “We can continue to produce thermally fused laminate even if rawboard production is down and replenish the warehouse when those repairs are complete.”
Once these panels leave Crane Storage, they are cut to size and either sent to logistics to be shipped as raw particleboard or moved by automated rail carriage to the High Bay Warehouse. These boards will be used to produce TFL.
The soaring, 100-foot-tall High Bay Warehouse also has deep roots, with supporting structural columns that drop nearly 100 feet into the ground. This allows for the precision required by these automated systems and prevents any settling that would throw off the intricate balance of the automated cranes, even as they move extremely heavy loads.
The vertical layout optimizes available space for storage. When particleboard is needed for TFL production, one of two High Bay Warehouse cranes place the stacks aboard automated rail carriages which move the boards to the lamination lines for TFL production.
Healthcare applications designer options.
Available Through:
Fontana CA
909.357.7730
Phoenix AZ
623.936.2627
Las Vegas Nv
702.430.3433

‹ CONTINUED FROM PAGE 41
“With the additional stock held in our production warehouses, we are better positioned to manage supply chain issues, avoiding the delays that would lead to extended lead times for customers,” says Brown.
COMBATTING LABOR CHALLENGES Even though the automation in these facilities eliminates the need for a lot of employees, the ones they have are crucial to its operation.
And the automation contributes to worker safety, as well. “The safety of our employees is a top priority. The state-of-the-art automation at our facility, including our production warehouses, limits employee proximity to operating equipment,” says Brown. “Instead, employees are focused on programming, overseeing and maintaining equipment.”
“Even when maintenance is required to the automated warehouses,” he adds, “lock-out, tag-out procedures ensure that no equipment is running while employees are performing that work.”
MODERNIZING THEIR ROOTS Development and construction of the three-phase project in Lexington began in 2018. The first phase, a state-of-the-art particleboard manufacturing plant with lamination capacities, reached a key milestone in September 2020 with the start of production.
Now, EGGER’s very first production facility in St. Johann, Austria, is adding a high bay warehouse similar to the one in Lexington, using the same logic and systems, both featuring the latest technology, which was created by Siemens.
The newest EGGER high-bay warehouse in Austria has a footprint of approximately 48,500 square feet. Up to 1.1 million cubic feet of wood-based materials can be stored automatically on 18 levels in the building that rises only 100 feet above the ground.
LOOKING TO THE FUTURE The rise of automation really changes the game in the industry, say officials. Automation is the future, and can help at every level of a company’s operations—labor, productivity, safety and even customer service.
The growing demand for more efficient production and distribution for materials and products has prompted many companies to jump on board the automation bandwagon—and there’s no sign of stopping. s p
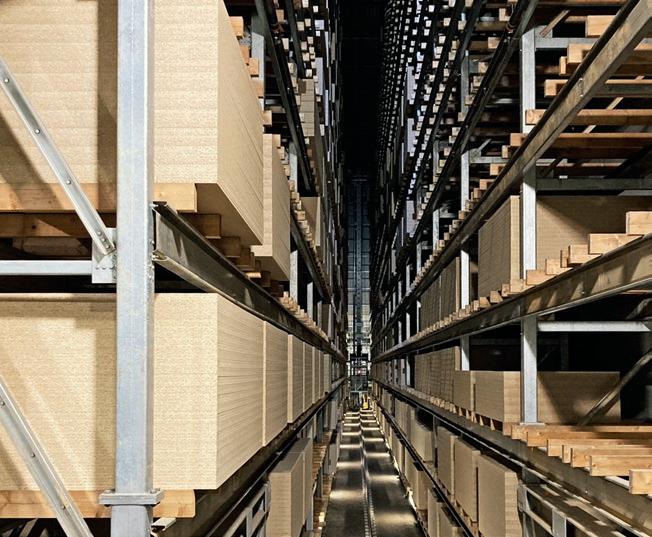
EGGER’S NEWEST FACILITY IN LEXINGTON, N.C., IS THE COMPANY’S FIRST MANUFACTURING PLANT IN NORTH AMERICA AND 20TH WORLDWIDE. THE CRANE STORAGE WAREHOUSE WILL HOLD UP TO 750 TRUCKLOADS OF PARTICLEBOARD, OR ABOUT 10 DAYS’ WORTH OF PRODUCTION.