
19 minute read
Transport & Earthmoving Equipment
THE ERGONOMICS OF HEAVY EQUIPMENT

Operator comfort – in the form of ergonomically designed equipment – cuts fatigue, simplifi es operations and reduces the physical and mental toll on the employee
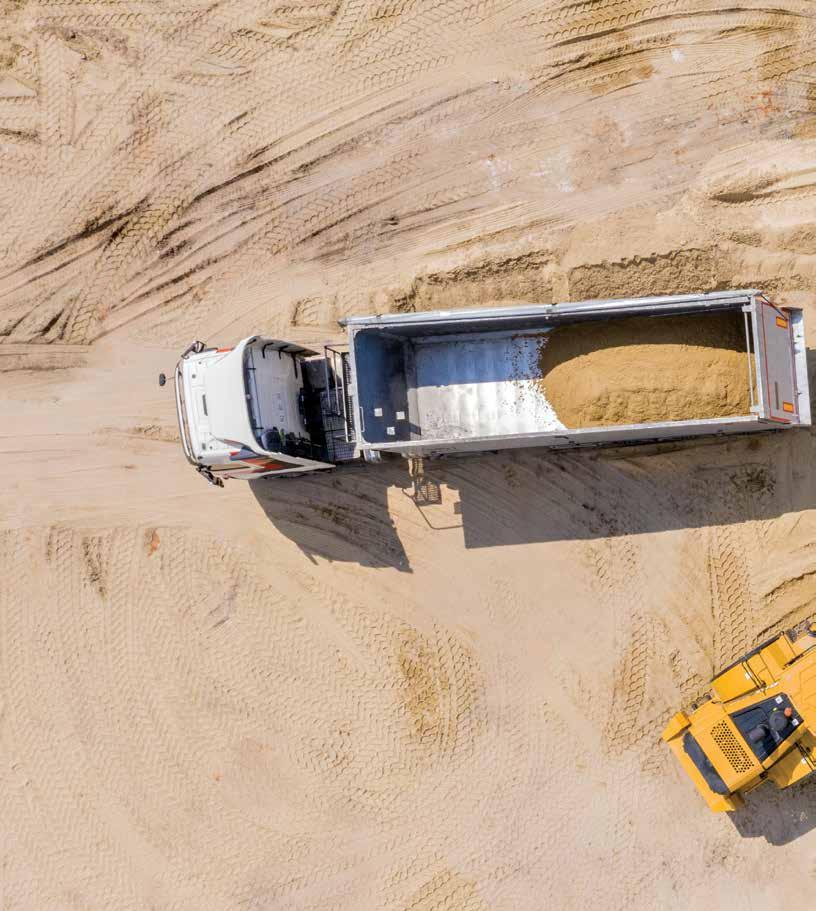
By Benjamin van der Veen
Operator comfort may not be top of mind when making business decisions, but uncomfortable operators become fatigued operators. Fatigue of any kind poses a workplace hazard and reduces productivity. Fatigue a ects all of us, regardless of skills, training and knowledge.
It influences the physical and mental abilities needed for even the simplest tasks.
Shi -work fatigue, a common challenge in construction and mining, exacerbates the problems. Those working long or varied shi s are more prone to being tired and making mistakes that could injure themselves or others. The highest rate of catastrophic incidents is usually found among shi workers.
Fatigue can be attributed to many factors, the most important being a lack of restorative sleep. The various factors typically fall within the physical, mental and environmental load. The physical load includes physical exertion, awkward posture and repetitive movement. Cognitive load can include irregular work hours, job demands and stress. The environmental load has temperature, noise, light level, vibration and humidity.
As myriad factors can contribute to someone’s level of fatigue, there is no single way to eliminate the problem. But with a holistic approach, you can reduce the triggers.
Thirty years ago, ergonomics hardly figured into the industrial design landscape, but well into the 21st century, equipment accommodates a more diverse, genderneutral workforce. From lighter safety tags, to ergonomic trapping shoes, to more accessible controllers – design improvements to heavy equipment are made to enhance operator comfort, increase productivity and reduce injury.
THE IMPORTANCE OF ERGONOMICS
Repetitive tasks, high temperatures or high-noise environments can still cause or intensify fatigue. Newer cabs address specific problem areas for operators: adjustable heated seats, lumbar support, and easier-touse control systems.
Reducing repetitive hand movements in heavy equipment operations can reduce the risk of hand injury for the operator. On electric rope shovels, cabs can be equipped with microwaves and refrigerators, sinks and sanitary facilities, and other amenities to provide additional operator comfort.
“Wellness is a big part of our job,” says Luke Tolley, a product manager of Komatsu’s hybrid shovels. “If there’s a button we can put in position that’s easier to get to, we want to know.” Operators reported less physical fatigue from digging, for example, a er using new adaptive controls on the P&H 4800XPC series shovels, which were upgraded to limit forward and backward tipping. Productivity reportedly went up among users, demonstrating that wellness is good business.
Heavy equipment typically requires wrist movement – forward or backwards – to move, reach, and cut material. To mitigate this, attention has gone into reducing the need for awkward, repetitive hand movements, to reduce the risk of a hand injury.
Heavy equipment has seen vast improvement where joysticks are placed, so instead of reaching and extending, the operator merely pushes a button. Nicholas Voelz, product manager for electric mining shovels at Komatsu, was behind a “low force use” joystick in electric shovel modules. With core functionalities on easily accessible buttons, it responds to a flick of the wrist, rather than concentrated arm movement. It eliminates the need for awkward reaching to control shovel movements.
Thankfully, operator comfort is taking a front seat in product design. “Most shovel operators I’ve met are happy when they’re comfortable,” says Voelz. He recently toured the country to let customers try di erent designs and gather feedback. The result:
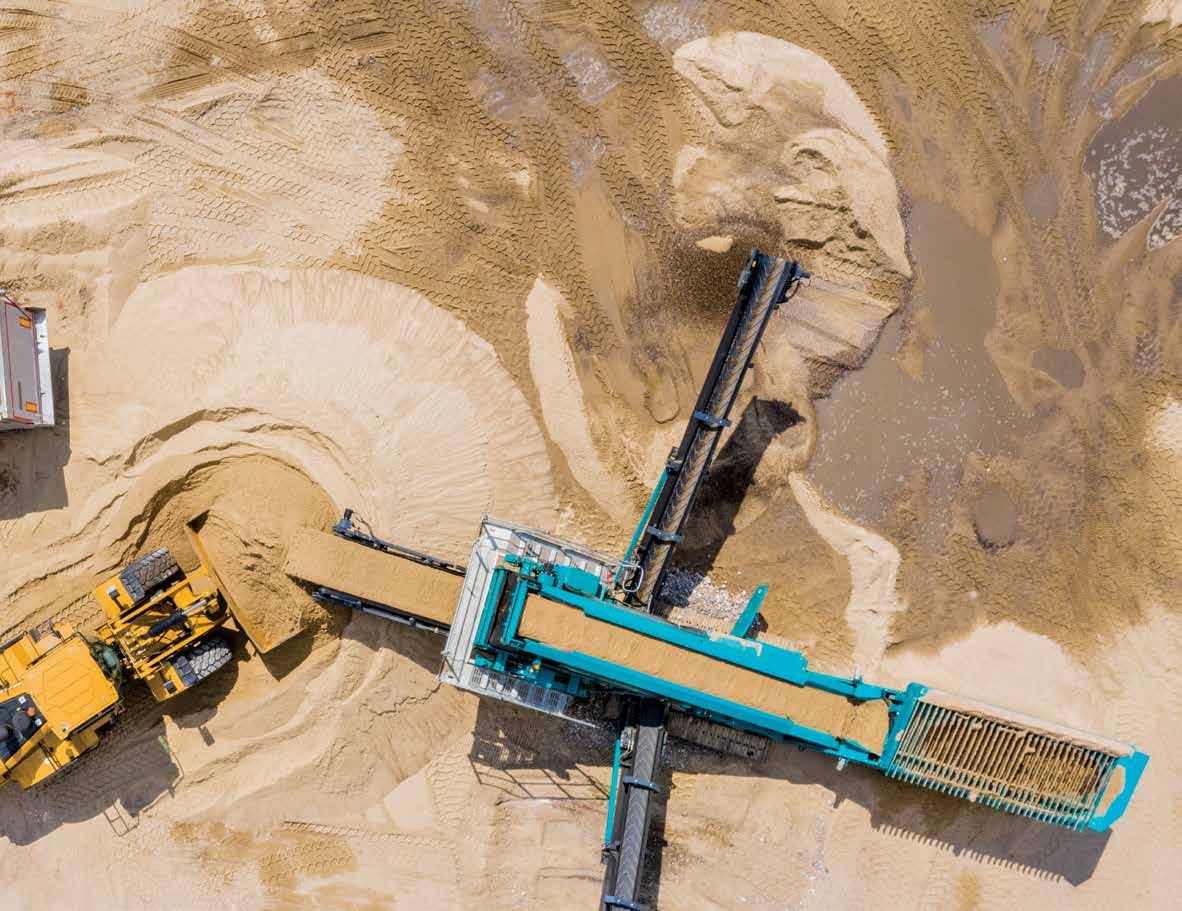
the development of more comfortable seat modules for some of the most extensive equipment in the industry.
NEW HEAVY-DUTY HAULAGE
“2022 has been great for Volvo CE in Africa,” says Per Lorentzen, commercial manager for Market Area Africa at Volvo CE.
In January 2022, Volvo Construction Equipment (Volvo CE) announced the expansion of the distribution of the Volvo EC550E crawler excavator to Tier 3 markets, including Africa and the Middle East. Babcock, the authorised Volvo CE dealer in Southern Africa, has brought in its first unit, which has already been delivered to a customer, confirms Lance Mannix, GM of sales and equipment at Babcock’s Equipment division.
Traditionally, an excavator’s production is directly linked to its operating weight. With the EC550E, Volvo CE broke the norm by introducing the Independent Metering Valve Technology (IMVT) hydraulic set-up, in conjunction with a new engine trim on the D13 engine block and electro-hydraulic command for the joysticks. As a result, the machine punches well above its weight, o ering production more in line with more giant class machines in the 60-tonne to 65-tonne range, despite the decals stating 55 tonnes.
During the design of the machine, Volvo CE was able to accommodate a giant bucket (2.4-4.2m3 capacity) by increasing the size and weight of the undercarriage, which gives excellent stability. By load distribution surface/footprint of the undercarriage, the EC550E has almost an identical size to some competitor 70-tonne machines.
The 2 071Nm (320kW) engine, rated power @1 600rpm, is also well in line with particular competitor 70-tonne machines. This, coupled with the large displacement pumps (832 litres per minute), results in faster cycle times.
O ering high levels of power and productivity, the EC550E can fill a 35-tonne to 40-tonne haulier or on-highway truck in just four to six passes – the result is optimum pass-matching and high-level production, at a low cost per tonne, that also makes life easier for the operator in the cab.
The new model slots are between the existing Volvo EC480D and the EC750D. While the EC480D model is aimed at customers looking for an e icient and reliable 50-tonne class excavator, the EC550E o ers 35% greater production than the EC480D in the typical dig and dump applications – and is closer to the EC750D, thus challenging the 60-tonne to 65-tonne excavator class.
Customers can further take control of their productivity with an On-Board Weighing System, helping to ensure the optimum amount of material is loaded. The optional system provides real-time information to eliminate haul trucks under- and overloading – again, making operation simpler and more e ective for the worker in the cab – and records total tonnage for complete production management.
THE IMPACT OF FATIGUE ON WORK CAN INCLUDE:
■ Reduced mental and physical functioning ■ Increased risk of illness ■ Decreased alertness and slower reaction time ■ Impaired concentration and judgement ■ Decreased motivation
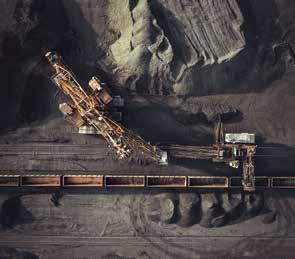
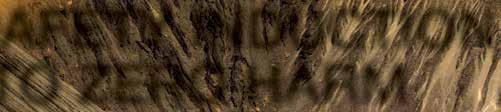

SINGLE STANDARD SAFETY INDUCTION MODEL THE KEY TO ZERO HARM
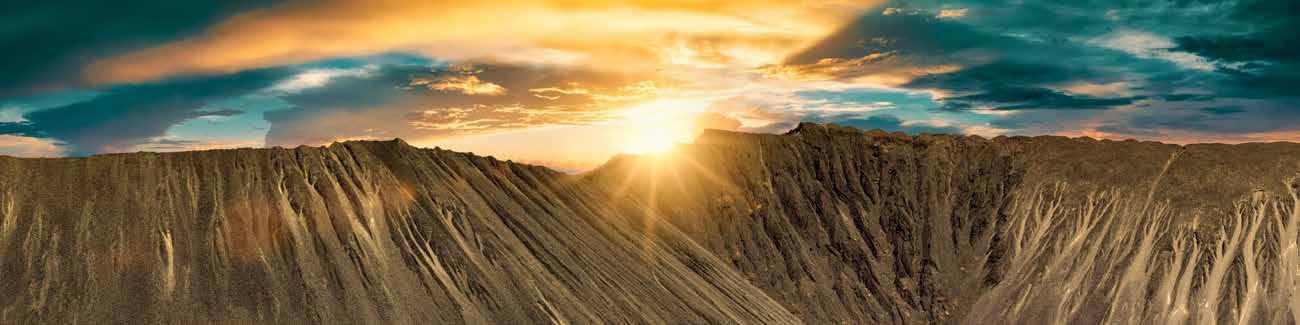
Standardising legally required content into a world-class induction programme allows contractors to undergo a single induction and receive a clearance valid for 12 months, across multiple sites
As one of the most dangerous industries in the world, it is for good reason that there are strict health and safety protocols in mining. Before starting work on any project for a mining house, every individual must complete the necessary health and safety induction at each mine.
Given the high headcount for contractors at any given site, this gets complicated, costly and timeconsuming. The requirement that the induction process be repeated for each returning individual – o en across multiple sites and on numerous occasions throughout the mine’s lifecycle – is simply not feasible.
So, what is the solution to wasted time and induction costs? A single standard induction model that supports inter-company and intra-company movements and eliminates induction duplication.
UNNECESSARILY REPETITIVE
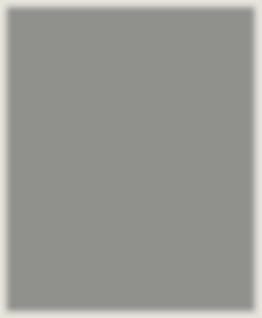
Although the rationale behind the mining site safety induction requirement is sound in theory, in practice there is room to make it a lot more streamlined and e icient.
Section 10 of the Mine Health and Safety Act and the Occupational Health and Safety Act regulate all mining activities and place a requirement on the employer to train an individual on the latest health and safety standards that apply to that mining site.
Each site is empowered to run its own induction processes, if it ensures it has covered the correct health and safety training elements of the acts, in order to be legally compliant. This covers elements of hazard identification and risk assessment on-site, and how to perform the job safely in that environment. Having to repeat this induction upon arrival and return at every site is a waste of time, resources and money.
By Jared Kangisser CEO of KBC Health & Safety
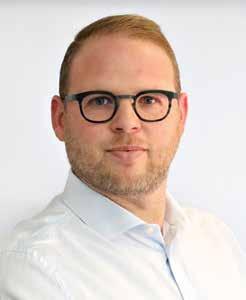
UNNECESSARY COSTS AND DELAYS
With each mine running its own induction programme, which can take between one and three days, e iciency takes strain when onboarding high volumes of workers, causing bottlenecks.
Internal induction resources are stretched thin – classroom, administrator and facilitator resources are limited, which pushes out the lead time, which then impacts the time taken to get on-site. As a result, there is a direct and indirect cost implication to the mining house, but because these are not visible as a single line item on an income statement, mining companies don’t see the true cost impact of these delays.
However, if a mining house takes on 2 000 contractors a year, but each contractor takes an extra two days to get on-site (at an assumed R1 000 per day cost per contractor), that’s an extra R4-million per year, simply in training expenses due to bottlenecks and ine iciency.
THE SOLUTION IS STANDARDISATION
In the early 2000s, a unified induction and training centre was established in KwaZulu-Natal, comprising six di erent mining houses. Across these six mining houses, approximately 10 000 mining contractors migrated between five or six mines for several years, and before standardisation, contractors would need to redo the induction each time they re-arrived on-site. By standardising the legally required content into a world-class induction programme, it became possible for contractors to undergo a single induction, and on passing the assessment, they are issued with clearance valid for 12 months. This would then work in their favour for both inter-company and intra-company movement, and contractors would not be required to repeat the induction to access any of the relevant sites that are party to the single standard induction model.
Any remaining on-site induction requirement is then significantly simplified and reduced, and e iciency increases exponentially. Induction therea er needs to be refreshed only on an annual basis, which presents compelling cost- and time-saving opportunities.
With the creation of a single standard for safety induction, this has benefits beyond health and safety training e iciency. There is also the potential for alignment and standardisation of health and safety within an organisation or across multiple organisations, which is important in embedding the critical message of zero harm across the industry.
There is a tendency for contractors to feel that they’re just there to do a job, and health and safety regulations only slow them down. There is a misalignment between contractors and the site that they’re working on, which is an area of huge concern.
SAVING MONEY, SAVING LIVES
Imagine every single contracting company and every single contracting employee having taken exactly the same induction with the same principles, the same knowledge, and the same value system around safety, barring site-specific requirements.
This is the real opportunity to truly achieve a culture of zero harm, by e ectively reducing fatal incidents. This in turn has a positive impact on all stakeholders – including government, mining houses, unions, and ultimately, the communities at large.
Furthermore, a single standard of safety is the ideal foundation for reciprocity. Not only from a cost-saving perspective, but towards alignment. By centralising inductions, legal compliance becomes easier and through alignment, everyone is working at the same standard, towards the same safety goals.
Simply by streamlining and unifying their induction processes, mining houses that subscribe to a single standard of safety induction have collectively saved north of R1.5-billion in just over a decade. That’s a cost saving worth pursuing, particularly in this economic climate where mining houses are being forced to do more, with less, without compromising on safety or quality.

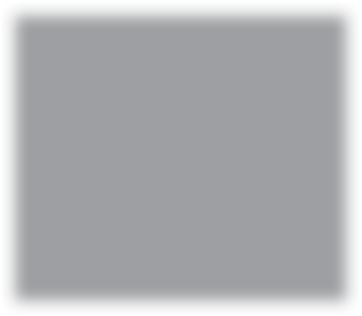
BCX COLLABORATES ON 5G-ENABLED INNOVATION SET TO TRANSFORM MINING
BCX, one of the largest systems integrators in Africa and a division of Telkom, ushered in a new 5G-enabled era for the Nungu Mine, in collaboration with its industry-leading partners.
Unparalleled enhancements in worker safety and business productivity have been introduced at the Nungu Mine in Elandspruit, with pioneering 5G wireless-enabled technology instantly addressing a wide range of challenges faced by the mining industry.
The deployment of the latest 5G-enabled technologies is set to radically enhance the mine’s operational e iciencies and safety. “This is a game changer for the entire industry and the hundreds of thousands of people it employs,” says Neo Phukubje, managing executive at BCX Wireless Solutions.
The mine has been revolutionised with wireless connectivity, data analytics and automation that enables video monitoring via drone technology, integrated connectivity with handheld devices and tablets, and a facial recognition Proximity Detection System.
Wireless technology in the form of 5G creates possibilities to transform every area of the operation, from workplace safety to improved productivity through predictive intelligence. Each of the ecosystem partners, including Huawei, MPI Holdings, Umnotho Technologies and Dahua, has played a pivotal role in this far-reaching venture.
According to Gert Venter from MPI: “The importance placed on the partner ecosystem in the project helped develop vital innovations in safety. This includes 5G-enabled proximity alert between two heavy vehicles for collision prevention, which can mean the di erence between life and death.”
Frenndy Wang, Channel Department director at Huawei South Africa’s Enterprise division, says that in addition to improved safety and operational e iciency, another di erentiator is that 5G allows for artificial intelligence-based real-time data analytics, a key to smart mining.
“Data is a valuable asset for miners, enabling ‘data-driven decision making’ in the critical mining environment. 5G connectivity will make the South African mining sector globally competitive. We are excited about working together with our partners like BCX to drive digital transformation in the mining sector, which is such a crucial industry in the economy.”
Neo Phukubje.
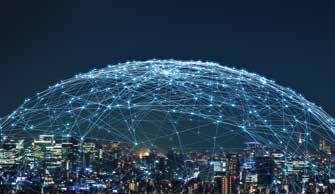
MINING NEEDS A SECURE SUPPLY CHAIN TO GROW
Secure supply is especially critical in vital areas such as explosives and blasting technology, which directly affect a mine’s ability to keep operations streamlined
Although the mining industry remains buoyed by strong commodity prices, the new year will not be without its supply chain challenges, according to explosives and blasting solutions provider BME, an Omnia Group company.
“Future demand for minerals, especially those feeding the world’s decarbonisation efforts, is growing and the sector is having to reset its production capability in response,” says Ralf Hennecke, BME managing director. “This calls for efficient operations that can rely implicitly on their value chains.”
Hennecke notes that mining supply chains continue to be affected by the impacts of COVID-19, followed by the geopolitical disruption of Russia’s war in Ukraine. Secure supply is particularly vital in key areas such as explosives and blasting technology, as these directly affect mines’ ability to keep operations streamlined.
“It is significant that PwC has raised concerns in its recent SA Mine 2022 insight report that resource-rich countries will have to address bottlenecks in their supply infrastructure, if they are to fully benefit from mineral demand trend. For a company like BME, our focus on supply security requires constant investment in local infrastructure and skills, in all our markets.”
It also means close collaboration with mining customers, to ensure not only that supply is reliable, but that it drives efficiency and sustainability within each mining operation. An important contributor is technology, he argues, which in blasting can support both safety and productivity.
“Growing value is being harnessed by the use of electronic detonation systems, for instance, and the range of related digital planning and monitoring tools that BME has developed. It has become clear that more exploration – in battery minerals particularly – is going to be necessary to meet the needs of a lower carbon global economy,” he says.
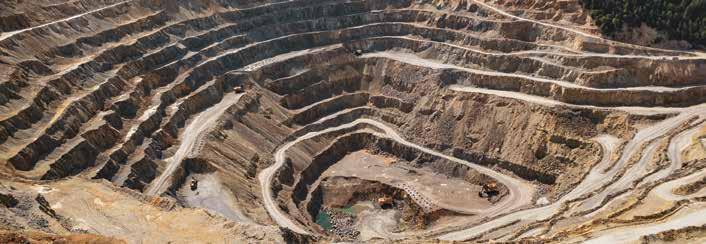
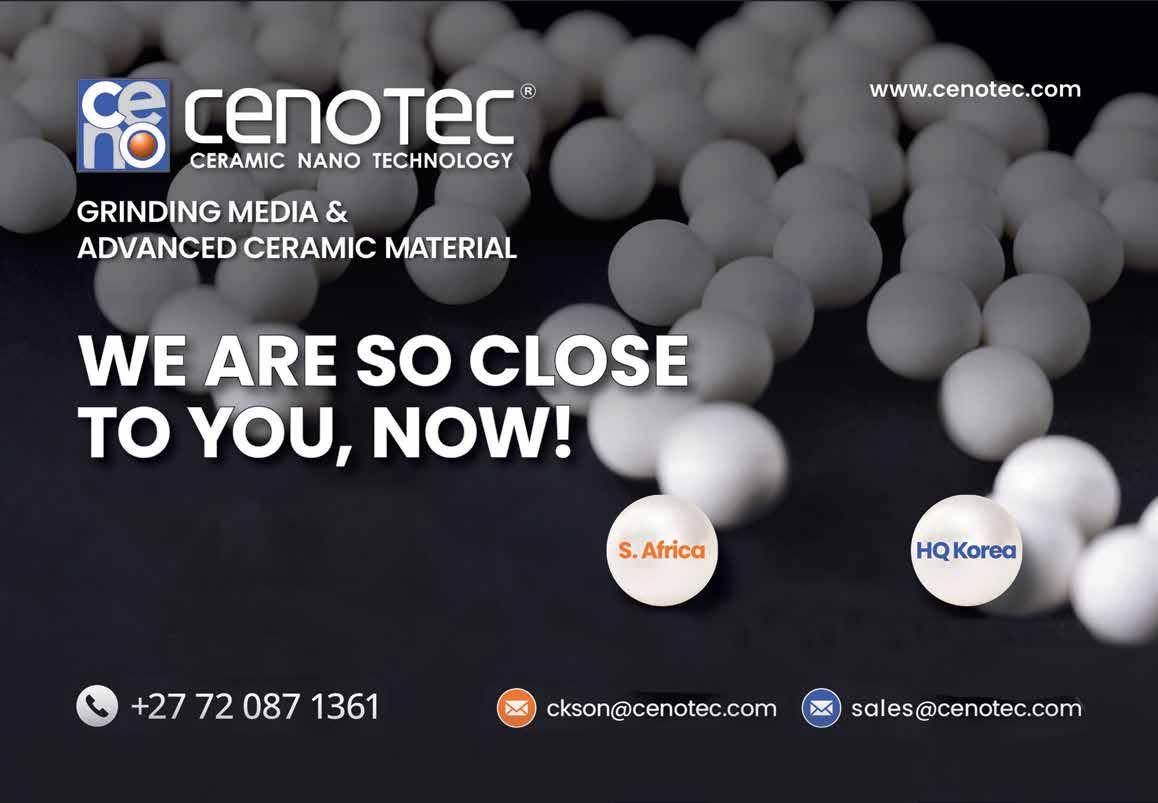
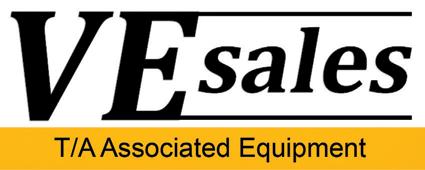
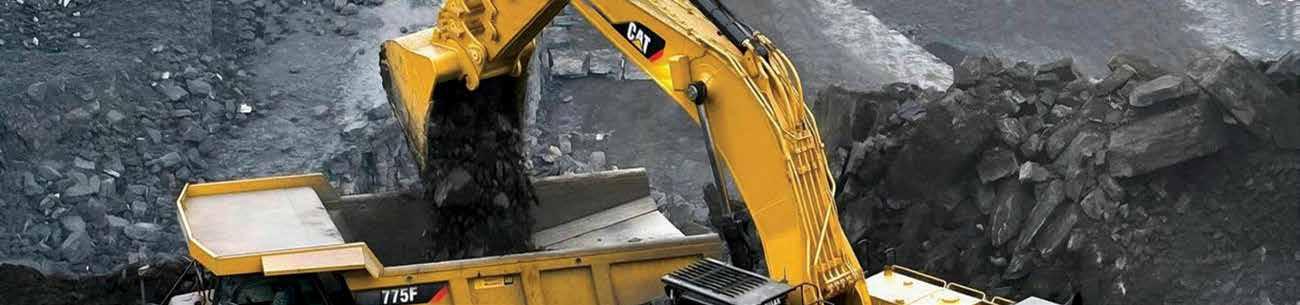


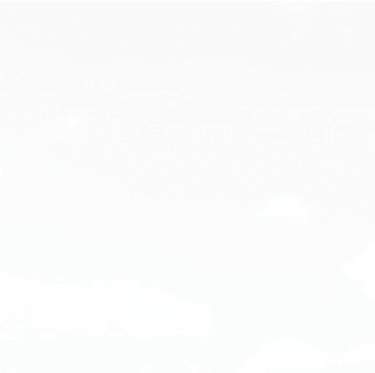
www.associatedequipment.co.za
Plot 92 Indaba Lane-off Beyers Naude, Rietf ontein, Roodepoort, South Africa
Duncan: +27 (0) 83 626 5588 Anton: +27 (0) 82 923 5397 Jaap: +27 (0) 82 892 1327 Loraine: +27 (0) 76 021 4344 Offi ce: +27 (0) 11 801 4911
vendels@mweb co.za associatedloraine@xnet.co.za ves@xnet.co.za
We Are Buyers For Your Good Running Redundant Equipment
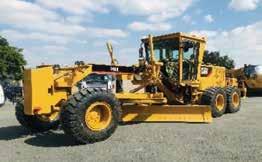
1x 2012 CAT 140K Grader-Refurbished 1x 2011 CAT 140K Grader-Refurbished 1x 2011 CAT 140K Grader With Trimble GCS900 Opti on
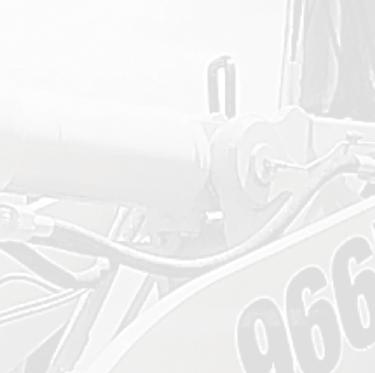
1x 2018 CAT 966L FEL-Refurbished 2x NEW 2022 SDLG L956F FEL’s 2x 2010/08 Komatsu WA430-5 FEL’s (Sti ll In Workshop)
1x 2009 HAMM 3411 SD Roller 1x 2008 HAMM HD120 DDV RollerRefurbished 1x 2014 HAMM 3520 SD Roller (Sti ll In Workshop)
1x 2000 Bomag BC671 Landfi ll CompactorRefurbished 34Ton 1x Bomag BC670 Landfi ll Compactor (Sti ll In Workshop)
3x 2009/07/03 HAMM GRW18 PTR’sRefurbished 1x2009 Hamm GRW24 PTR-Refurb 1x2008 Hamm GRW 15 PTR-Refurb
2x 2006 CAT 140H Grader-Refurbished 1x 2005 CAT 16H Grader (Sti ll in Workshop) 2x NEW 2022 SDLG G9220 Graders
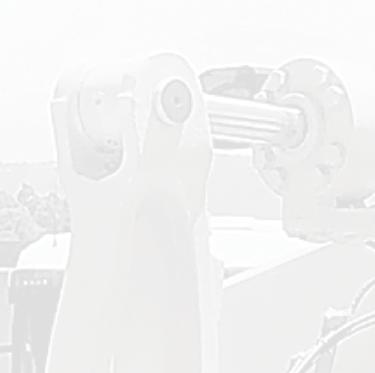
2x2013/2012 CAT 336D LME ExcavatorRefurbished 1x 2006 Hyundai Robex 500LC Excavator (Sti ll In Workshop)
1x 2012 CAT 740 ADT-Refurbished 1x 2010 CAT 740 ADT-Refurbished 1x 2013 BELL B30D 6x6 ADT 1x 2008 BELL B50D ADT (Sti ll In Workshop)
1x 2019 JCB 540-140 Telehandler 1x 2017 JCB 540-140 Telehandler 1x 2016 JCB 540-170 Telehandler 1x 2014 JCB 535-140 Telehandler 1x 2006 CAT TH560B Telehandler
1x 2008 Broce RCT350 Road Sweeper BroomRefurbished 1x 2006 Broce RC350 Road Sweeper BroomRefurbished 2x NEW 2022 Manitou MBL745 4x4 TLB’s 1x 2019 CAT 426F2 4x4 TLB 1x 2016 CAT 428F2 4x4 TLB
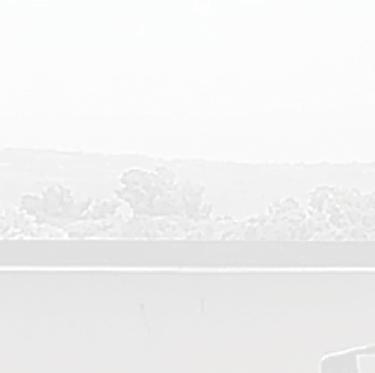
1x NEW 2021 CAT 323D3 Excavator 1x NEW 2021 CAT 320D3 Excavator 1x 2018 Hitachi Zaxis 330LC ExcavatorRefurbished
1x 2017 UD Quester CWE 330 10m3 Tipper Trucks 106 300km 1x 2017 UD Quester CWE 330 10m3 Tipper Trucks 106 400km
1x 2016 CAT AP600F Asphalt Paver (Only 853 Hours) 1x 2009 CAT AP600 Asphalt PaverRefurbished 1x 2003 BITELLI BB670 Asphalt Paver
1x 2008 Volvo A30E 6x6 ADT 2x 2008 Volvo A30D 6x6 ADT 1x 2004 Terex TA30 6x6 ADT 1x NEW 2022 CASE 851FX 4x4 TLB 4x NEW 2022 CASE 770FX 4x4 TLB 1x 2011 CASE 580T 4x4 TLB
1x Etnyre K Chipspreader 4x4 Variable WidthRefurbished 3x Etnyre K Chipspreader 4x2 Fixed HopperRefurbished
2x 2014/08 HAMM HD14 DDV RollerRefurbished 2x 2014 Wacker RD12 Sit OnRollers 1x 2020 Bomag BW65H WB Roller 1x 2005 CAT CB224E Sit On Roller
1x Caterpillar D10R Dozer-Refurbished 1x 2014 Komatsu D65EX-16 DozerRefurbished 2x2009/08 Komatsu D375A-5 Dozers (Sti ll In Workshop)
1x 2008 CAT 824H Wheel Dozer-Refurbished

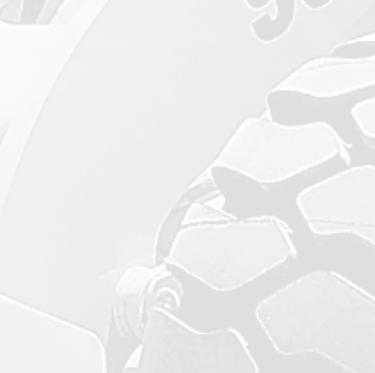
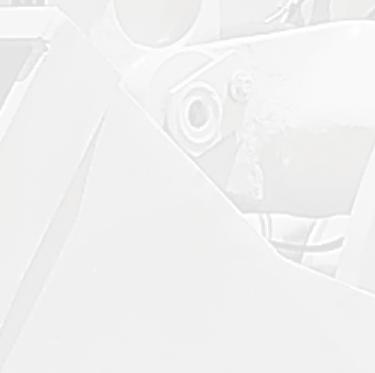
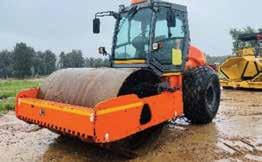

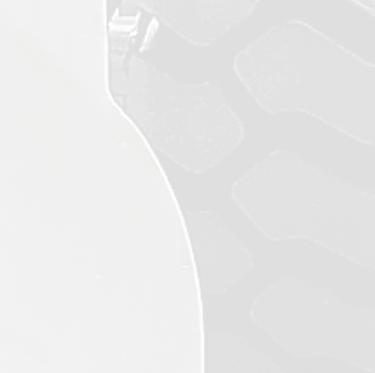
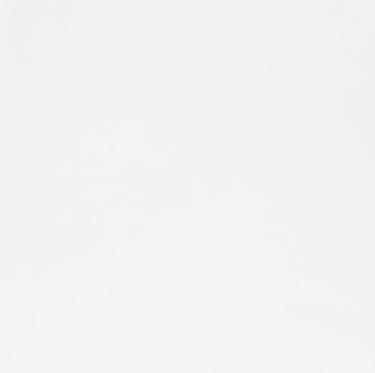
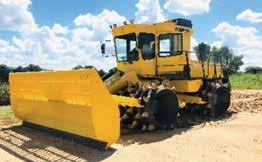
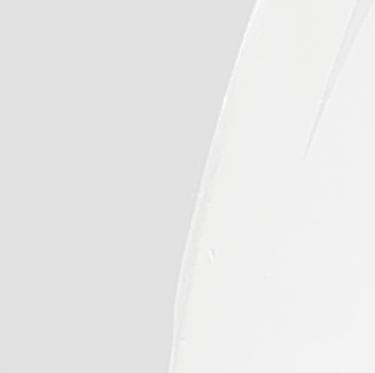
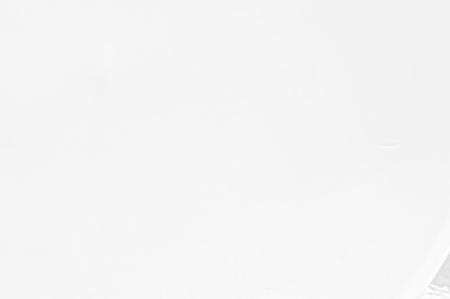
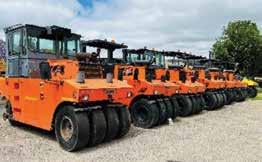
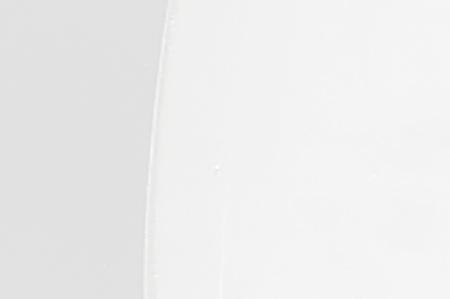
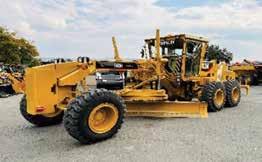



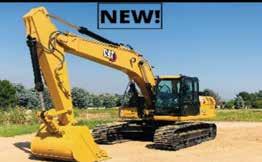
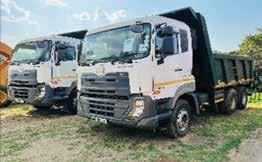
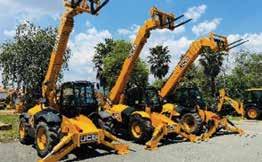
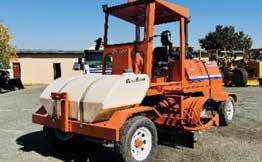
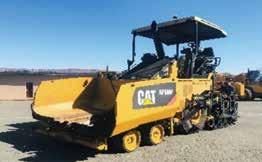
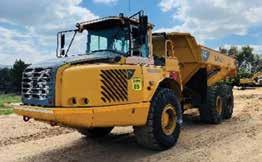
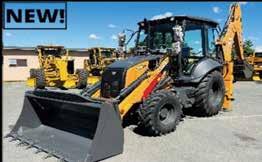


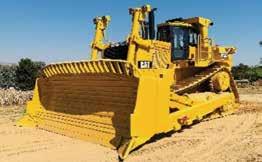
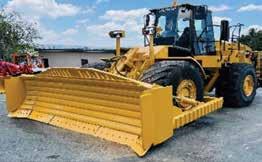
TO ADVERTISE IN www.samining.co.za SAMIN NG MIN NG
READ WHAT REALLY GOES DOWN IN SADC
CONTACT

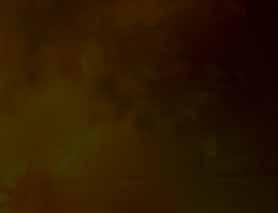
ADVERTISING Ilonka Moolman 011 280 3120 moolmani@samining.co.za

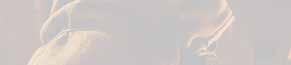

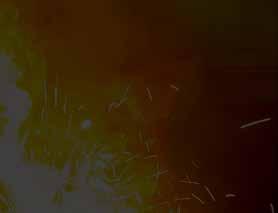
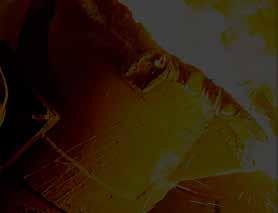
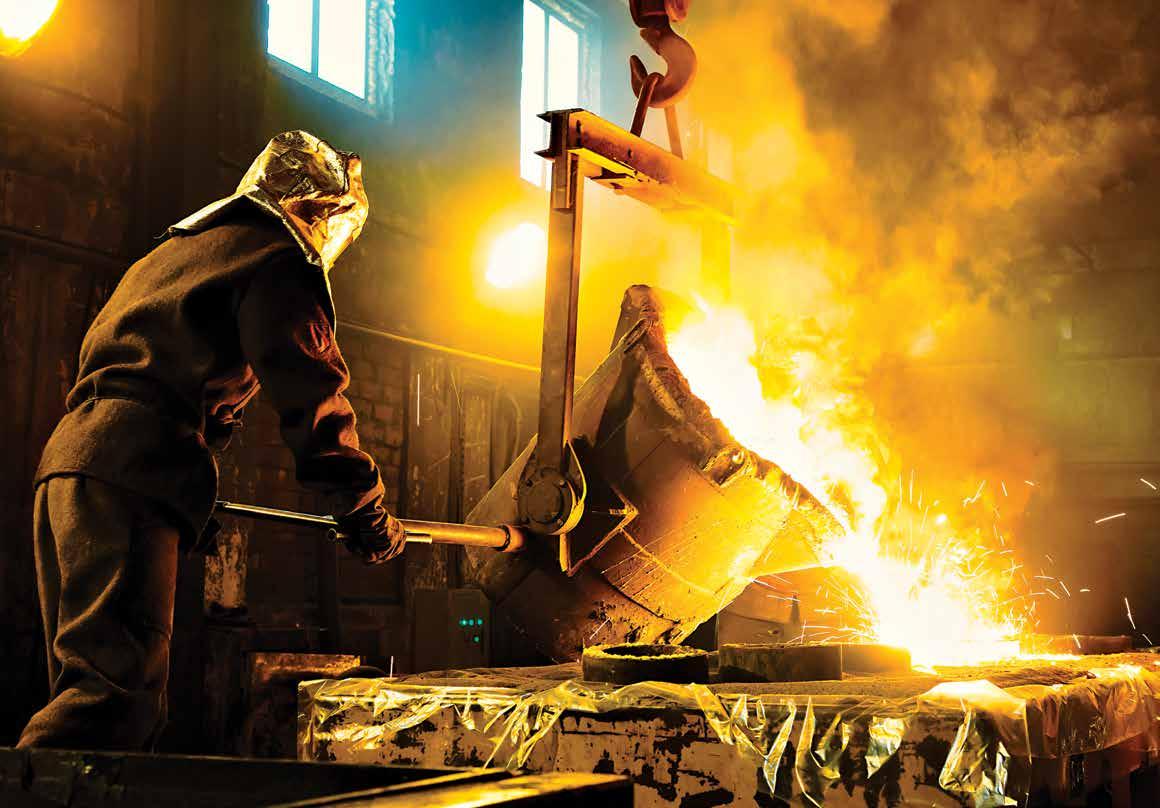
INDEX TO ADVERTISERS
AECI Mining Explosives ................................................................. OBC Auto X ................................................................................................... 2 BLC Plant Company ........................................................................ IBC Bosch Diesel Service ......................................................................... 35 Bosch Off Highway .............................................................................. 5 BME (A member of the Omnia Group) ............................................... 45 Brelko Conveyor Products ................................................................. 48 Cenotech ............................................................................................ 46 Edge Digital ........................................................................................ 11 E&T Minerals ...................................................................................... 39 ENSafrica ................................................................................. Gatefold Invincible Valves................................................................................... 1 Kal Tire ................................................................................................. 7 KSB Pumps & Valves ........................................................................... 9 Komatsu Mining ................................................................................. 33 NSDV .............................................................................................12-14 OIM Consulting .................................................................................. 31 Pinsent Masons ................................................................................. 19 Tomra Sorting Mining ......................................................................... 25 UMS .................................................................................................... 17 Vendel Equipment Sales .................................................................... 47

BRELKO NIP GUARD SAFETY DEVICE
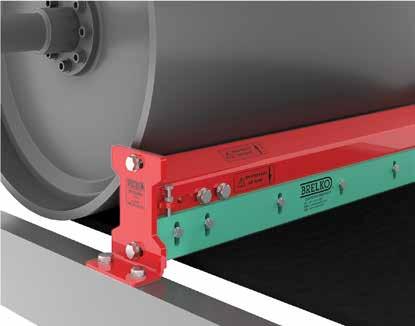
PATENTED