
14 minute read
Project Management
LEVERAGING TECHNOLOGY
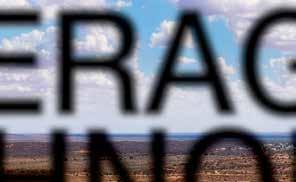
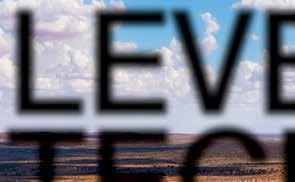
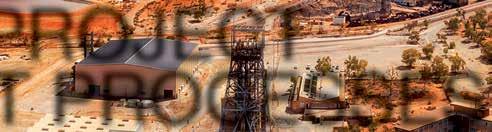

TO IMPROVE PROJECT MANAGEMENT PROCESSES
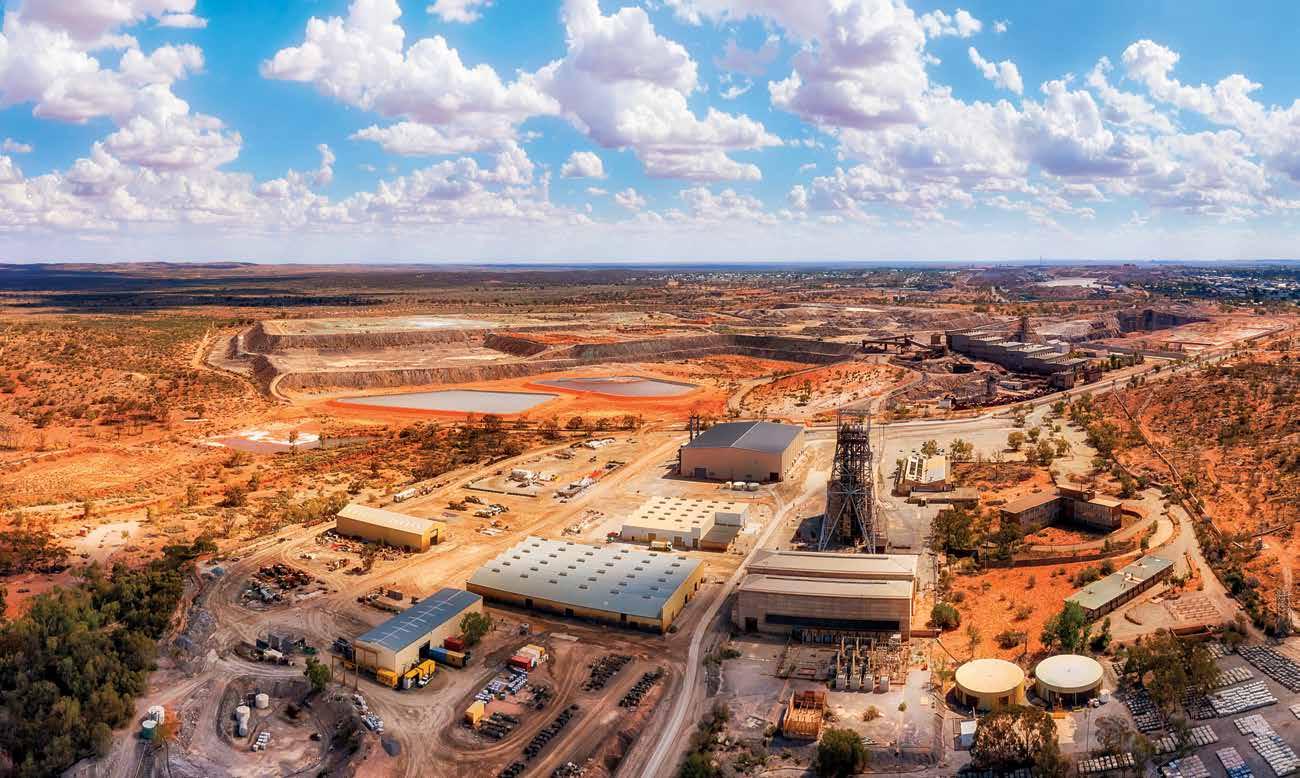
The mining sector faces several potential challenges, but numerous digital technologies available today can help overcome these barriers
By Benjamin van der Veen
The mining industry is a critical pillar of the global economy. Its products, like natural gas and minerals, contribute to approximately 35% of the world’s GDP. The industry has evolved and become highly sophisticated, requiring heavy capital investment in machinery, equipment and personnel.
The mining sector is now facing several potential challenges (see box), although the good news is that numerous digital technologies available today can help overcome these barriers by improving project management processes.
However, these need to be adopted, implemented and monitored correctly to deliver anticipated benefits while reducing risks associated with adopting new technologies at scale (e.g. security breaches).
DEVELOPMENTS WITHIN THE INDUSTRY
While in a constant state of evolution, South Africa’s mining industry aims to remain competitive. One of the industry’s many challenges is that mining companies must improve capital productivity, or how well they can generate revenue from their existing assets. To maintain competitiveness in an increasingly digital world, mining companies must implement better project management practices that enable them to use data analytics and innovate simultaneously.
To learn about new advances and benchmarks in the mining industry, the Mandela Mining Precinct (MMP) embarked on a study investigating international applicable technology developments for South African hard rock mining applications, covering mechanical cutting and drill and blast methodologies, and to strengthen collaboration e orts.
The study included visits by MMP research programme manager Martin Pretorius to ASSMANG Black Rock Mine Operations in the Northern Cape, Herrenknecht AG, a manufacturing company in Germany, and ended at the Sandvik Summit 2022.
“The road to modernisation is a bold step ASSMANG has taken. We have seen increased maturity levels within the operation, supported by each person taking responsibility and accountability,” says Pretorius. “The positive vibe and the keen drive towards continuous improvement were predominantly present in every person we saw on our visit,” he says.
Encouraging for ASSMANG is the paradigm shi approach taken – the detailed design of each task and action through practical risk assessment and procedure/task process that provides the means for each employee to be highly competent.
One of the biggest takeaways from
CHALLENGES FOR THE MINING SECTOR
■ Increased pressure from environmental, social and governmental organisations to respond to global challenges such as climate change and depletion of resources. ■ Cost pressures resulting from technological advancements have increased productivity but reduced margins for miners. ■ Increasing complexities related to project execution (due to size and location-specific aspects) can make it di icult for mining companies to streamline their operations. ■ Overcoming project barriers through digitisation. ■ Capital investments have traditionally driven the mining industry; a large part of these have been physical assets such as vehicles, equipment and buildings. Traditionally, mining project management has been a manual process involving lots of back-and-forth between di erent departments within an organisation.
Not only does this consume time and resources, but it can also lead to delays that may compromise quality or increase costs.
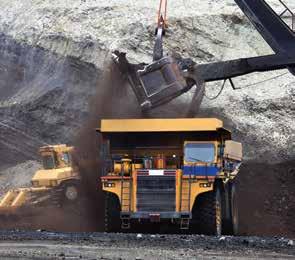
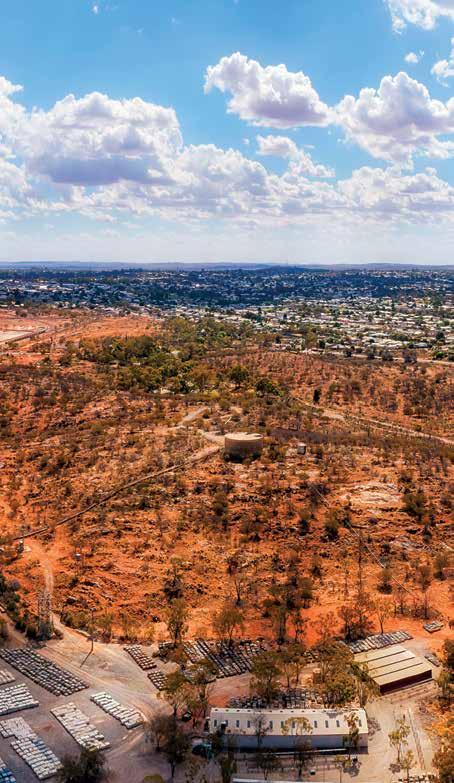
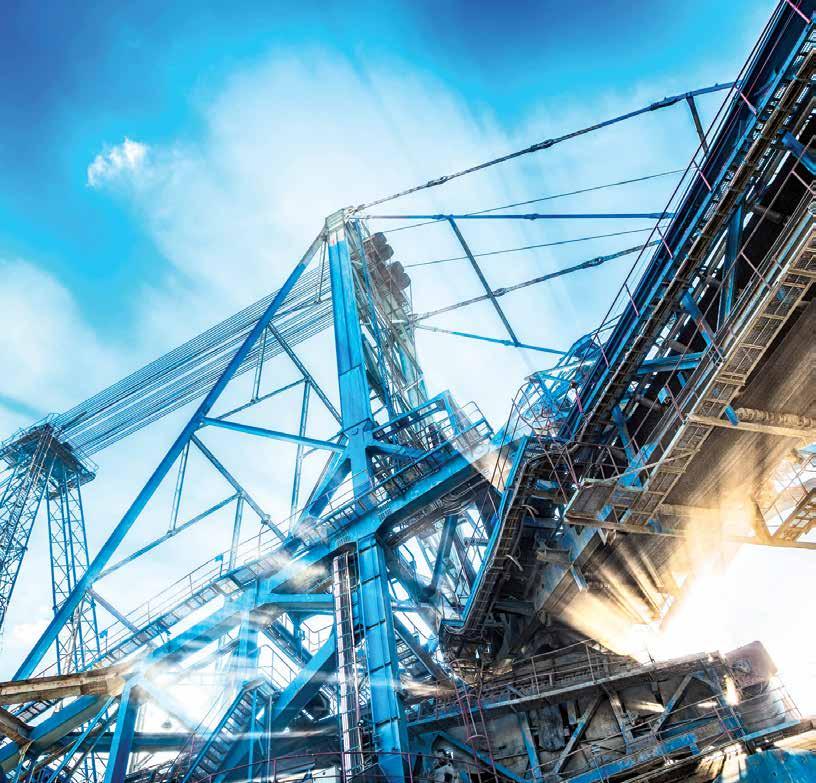
OEMs and service providers are strengthening the integration“ “ between operational planning activities, monitoring of these activities, and responsive reporting. – Pretorius
Herrenknecht is how each of their machines is uniquely designed for a specific application, based on geotechnical study output, to be used as mechanical design input for successful design, construction and implementation. “We also strengthened collaboration partnerships for involvement in our research work in the Mechanised Mining Systems research programme,” says Pretorius.
At the Sandvik Summit, several trials were presented, and the common thread is that the timeline from the arrival of equipment to completion of trial work – on average one year – is too long. The reason is that there needs to be adequate planning and preparation, as the operators are only trained once the equipment has arrived. Site preparation is also done once the equipment is transported to the site.
“The future strategy taken by original equipment manufacturers (OEMs) and industry is leading towards the acceptance of electrification, automation, data and analysis, and end-to-end optimisation,” Pretorius says.
“OEMs and service providers are also merging efforts to strengthen integration between operational planning activities, monitoring of these activities, and have responsive reporting strongly under development.”
The MMP is working on aligning its strategy and efforts to the global trends, and strengthening its efforts with the test mine to conduct equipment trials. Performance testing with a demonstration of results would positively impact successful uptake in the industry.
DIGITALISATION: THE WAY FORWARD
“While traditional methods of monitoring are well established in the mining industry, these methods are not necessarily suited for the new world of business imperatives,” says IMS Engineering CEO Paul Brancher.
I-Most, or Integrated Monitoring Optimisation Support Technologies, allows stakeholders to operationalise their equipment data, in order to optimise performance and efficiencies through valuable insights. This will enable a mine to maintain a competitive edge, while keeping up with the fast-paced world and the technological advancements that come with it.
I-Most provides data insights into a single piece of equipment or an entire process plant, allowing the management and operational teams to make data-driven decisions to improve their operation, whether from a performance or environmental perspective. Additionally, a rules engine allows the operations team to monitor procedure adherence.
I-Most is the product of a partnership with Acrux Sorting Technology, a wholly owned subsidiary of commodity trader and resource funding and investment specialist Acrux Resources, and IMS Engineering, a crushing, screening and sorting equipment manufacture. They have entered into a strategic partnership to provide sensor-based sorting technology to mineral resource owners on a fully funded basis.
The partnership aims to create value for miners by upgrading marginal or uneconomical ore into valuable material that can be fed into an existing processing plant, or sold on a concentrated basis at no financial risk to the capital spent.
The uniqueness of the partnership offers innovative de-risked solutions to mineral resource owners, customised to the mineral commodity and operational environment, and provides a unique opportunity to engineer sorting solutions with a heightened focus on adding additional value to operations.
E&T MINERALS

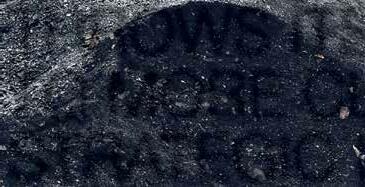
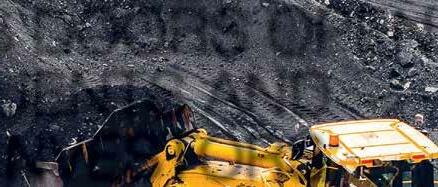
THROWS ITS DOORS OPEN TO MORE CLIENTS AND STRATEGIC INVESTORS
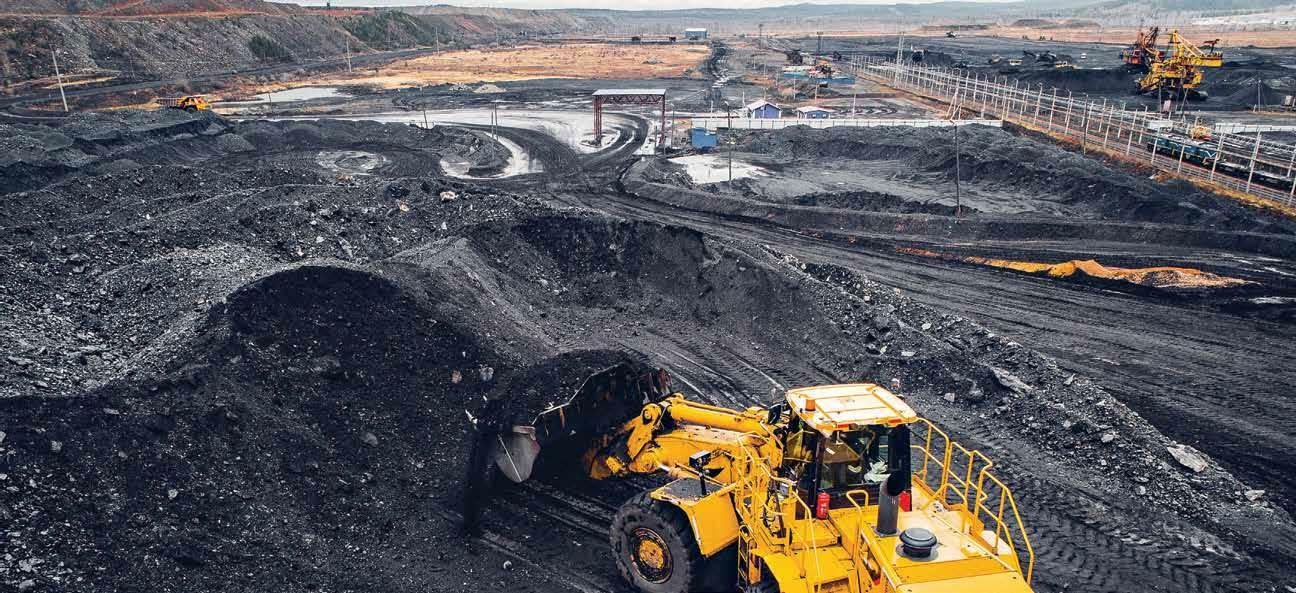
E&T Minerals, a 10-year-old African trading and investment firm specialising in coal and various commodities, has successfully embarked on its expansion into global exports. Having added coal mining, including pit-to-port solutions, and other essential commodities to its portfolio over the years, it is opening its doors in 2023 to additional clients and strategic relationships with co-investors. “This year’s Mining Indaba will provide a great opportunity to meet and discuss mutually beneficial opportunities with coinvestors who can not only contribute capital resources but also invaluable expertise in areas we have identified as core,” says CEO
Emmanuel Ngulube. “We’ve spent the past decade patiently yet persistently laying our foundation while establishing ourselves as the preferred and trusted choice for commodity origination in Africa,” he says. “We are keen to discuss new ideas that will advance our ambitions to become a truly diversified minerals and energy global trading entity.”
MOVING ONTO THE GLOBAL STAGE IN 2022
In 2022 E&T Minerals achieved a significant milestone by successfully executing its maiden shipment of RB1 coal to Europe, just as global thermal coal prices hit a record high. This enabled E&T to post its highestever revenue figure to date. The company has now chartered its first 75Mt vessel and signed a JV with an established junior miner with a measured resource of eight million tonnes of export-quality coal.
E&T will be exporting a cargo of coal into Europe throughout 2023, which will be sourced from its well-established network domestically as well as its own coal mines in the near future with plans already at an advanced stage. E&T is in the process of raising capital to invest in port throughput and infrastructure with various ports and back-of-port storage facilities throughout the Southern African Development Community region. This includes the Richards Bay Multi-Purpose Terminal, Richards Bay Coal Terminal, Durban Dry Bulk Terminal and Maydon Wharf Terminal in Durban, Maputo and Walvis Bay in Namibia.
Ultimately, E&T aims to capture 14% of Southern Africa’s pit-to-port value chain in order to help meet domestic demand as well as for customers throughout Africa, Europe and Asia. Potential customers not only include international utilities, but also local and international end-users in the paper and cement manufacturing sector and various other industries.
EXPANSION AND DIVERSIFICATION
Reflecting its revenue growth and forecasts, E&T Minerals recently moved into bigger o ices in Johannesburg. In line with its continued global expansion, E&T has established strong partnerships with businesses based in Switzerland, the United Kingdom, Monaco and Singapore, to name a few.
While Ngulube sees an at-least 30-year future for coal, especially given that it currently accounts for 27% of the world’s energy consumption, he says E&T is acutely aware of the role coal has played in climate change. One of the company’s strategic goals is to invest in alternative assets that will play a role in addressing climate-related risks.
E&T is seeking to develop various assets containing minerals linked to the decarbonisation e ort, including lithium assets in Namibia and copper assets in Zambia. It is also involved in developing a solar power plant in Balfour in Mpumalanga province.
E&T already has a partnership in place in North West province, through which it has access to chrome deposits with a potential life of mine of approximately 20 years. Other minerals in the pipeline include lithium and manganese, copper and anthracite. Over the next two years, the plan is to establish trading desks for the commodities mentioned to diversify the company’s revenue mix.
“We are well situated to understand changing market trends and adapt to them,” says Ngulube. “Our dynamic team has gained vast amounts of knowledge and experience over the past decade and will continue to do so indefinitely.”
E&T’S ROOTS IN THE SOUTH AFRICAN ECONOMY
The company was started in 2013 by Ngulube and Daniel Eyre, who secured a contract to supply coal to Sappi Paper. Over the following years they grew their domestic customer base and built strong relationships, sourcing coal from top multinational mining and trading houses. However, South African junior miners form the bulk of E&T’s annual coal origination and have successfully partnered with E&T to leverage the company’s global export reach and pit-to-port trading strategy.
“Clearly, to build trust in an industry which is characterised by many overnight traders, E&T had to forge relationships with miners patiently and gradually to obtain long-term coal o take agreements,” says Ngulube.
SUPPORTING LOCAL COMMUNITIES, ESPECIALLY YOUTH
E&T is committed to supporting and giving back to the communities where it operates. Its community investment strategy will focus on four principal areas: social inclusion, education and life skills, infrastructure refurbishment and employment. The company is passionate about developing South Africa’s youth and ensuring they have access to opportunities, and has recently supported young footballers and donated textbooks and a laboratory to underprivileged schools.
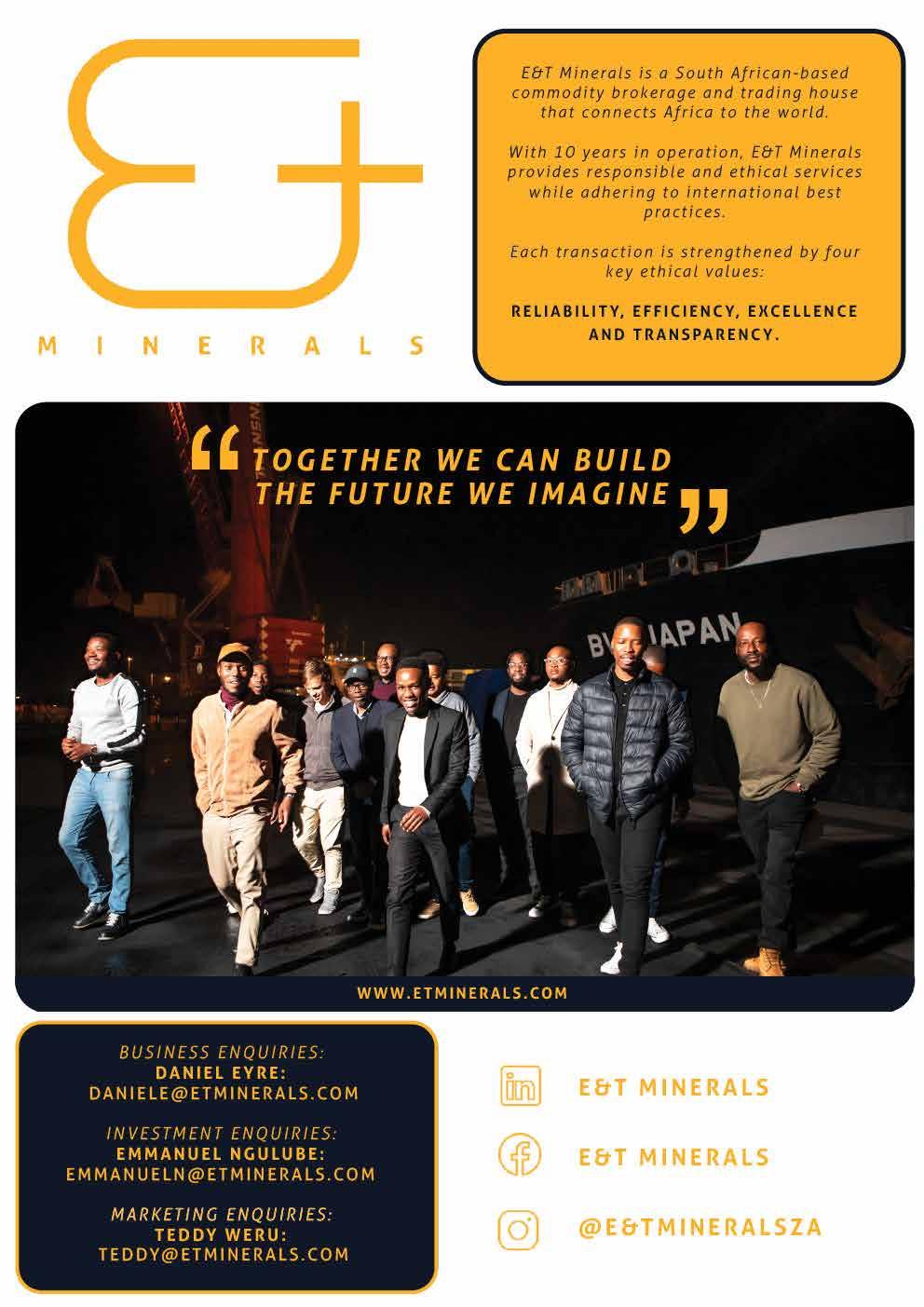
TECHNOLOGY

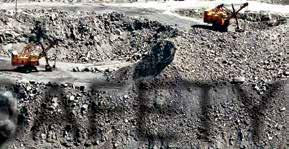
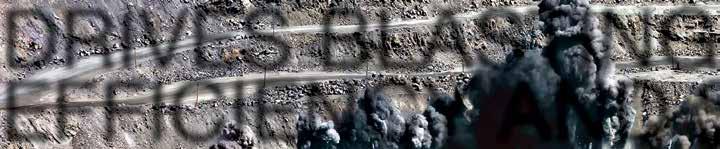
DRIVES BLASTING EFFICIENCY AND SAFETY
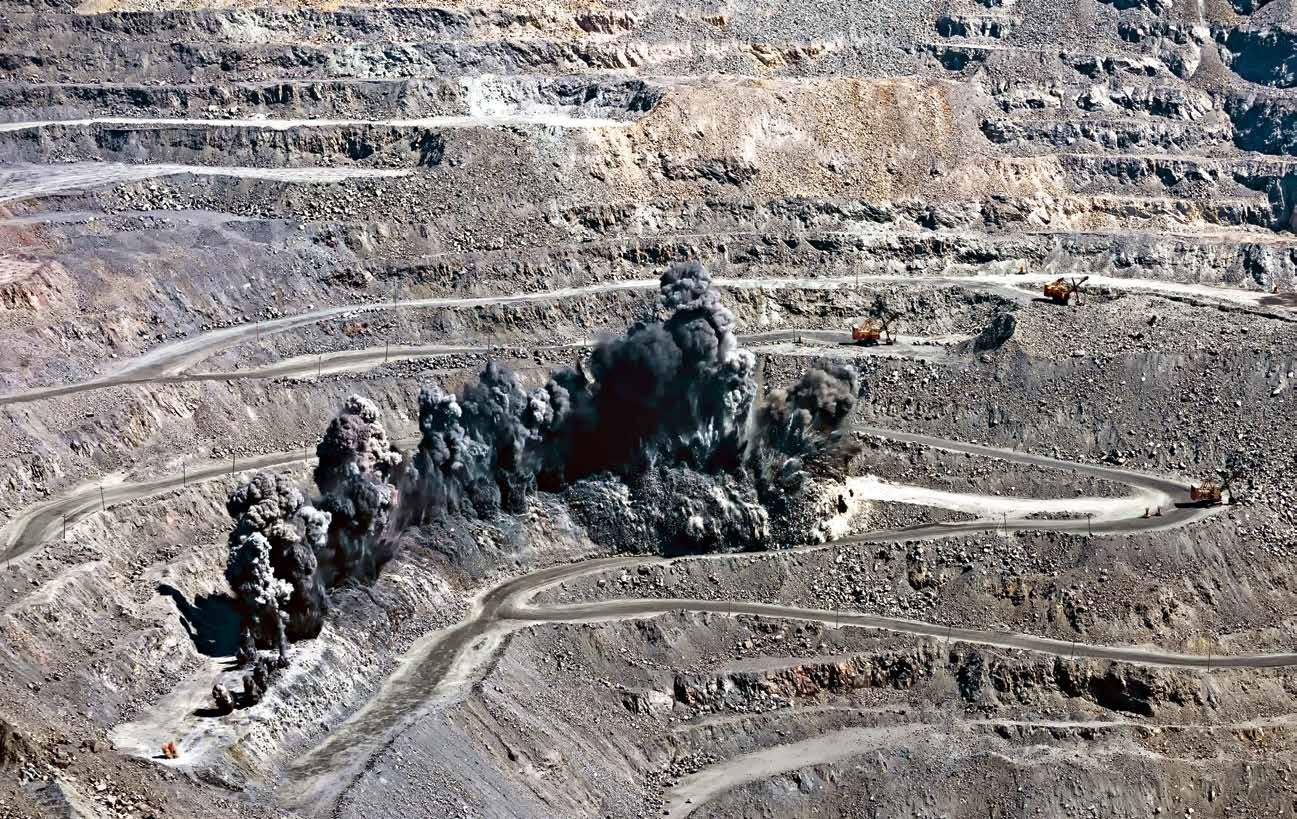
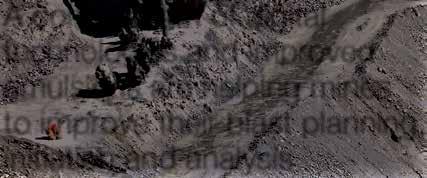
A combination of digital technologies and improved emulsions are helping mines to improve their blast planning, initiation and analysis
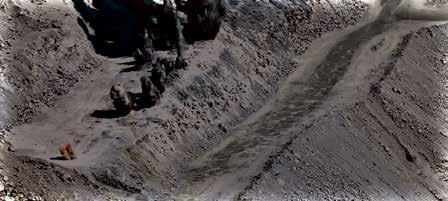
Mines have traditionally been considered slow adopters of technology, but in the field of blasting, digital technologies have certainly made a significant contribution to improvements in e iciency and safety. A good example, says Ralf Hennecke, MD at explosives manufacturer BME, is mining’s uptake of electronic delay detonator technology, which lends itself to a range of digital innovations. Electronics provide the crucial bridge to modern digital platforms which can generate, store and utilise valuable operational data. “Another aspect of mining’s adoption of innovative blasting technology is its buy-in to sustainability initiatives, such as BME’s inclusion of used oil in its emulsion explosive.
Mines have been quick to support BME’s used oil initiative, in which the company supports
Sustainable Development Goals through the responsible disposal of waste oil in our emulsion products,” he says. “When it comes to performance, emulsions have a higher velocity of detonation than ammonium nitrate fuel oil.
This improves rock fragmentation, and in underground applications, this helps reduce damage to side walls and hanging walls – as there is less gas energy and more shock energy in the product.” AECI Mining Explosives notes that blasting has to be accurate to achieve optimal fragmentation, which directly impacts load and haul, which needs to be managed to improve handling and processing time.
The company has been exploring a range of technologies to help mines improve their blast planning, initiation and analysis, using a range of digital tools. For example, a digital twin is a digital duplication of a production facility in a so ware model, which assists mines to better understand the impact of changes made to the process.
In addition, its Blast Design solution includes the disparate data generated by multiple design and data capturing so ware in a single repository. This facilitates dissemination and data mining for continuous improvement of field application, operational transparency and business intelligence. mining, interrogation and application of methodology.
Finally, AECI says its autonomous MMU technology will be available in the near future. This allows for the delivery of explosives in hazardous environments through application of a computer controlled and propelled delivery system.
BME’s Hennecke points out that while the early days saw the rise of so ware-based blast design, in recent times this has evolved to include real-time reporting, data mining and the quest to achieve predictability before every blast.
“These technological advances have accelerated their contribution to mining more than ever over the past decade. The take-up of these systems was faster in opencast mines, as connectivity above surface was more readily available. Data and analytics are giving mines quick access to information on drill holes, explosives and other blast-related indices – to ensure quality blasting.”
He adds that there has since been more take-up of digital technologies in the underground environment, as connectivity capabilities have improved.
“Increased digitisation in blasting has improved the precision, accuracy and quality of blasting – all key aspects of mines’ e orts to continuously improve productivity and e iciency. Underpinning this trend has been a progression towards smart mining, where processes are carefully monitored, more data is collected, and more e ort is directed at properly analysing this data,” he says.
Other technologies it has developed include BlastHub, a so ware portal, which is a receiving and launching platform for predictive so ware and links to enable data
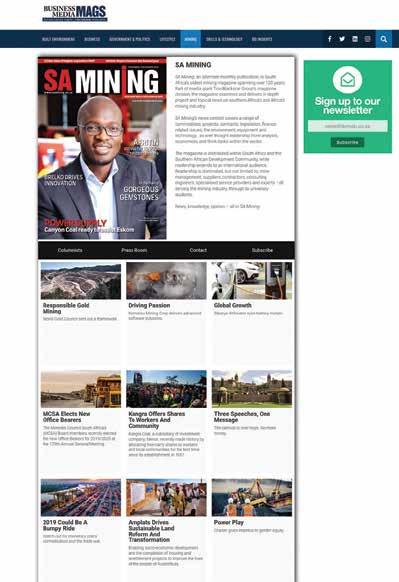
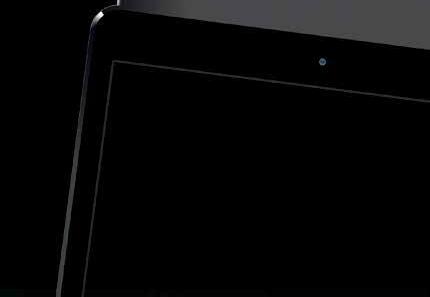
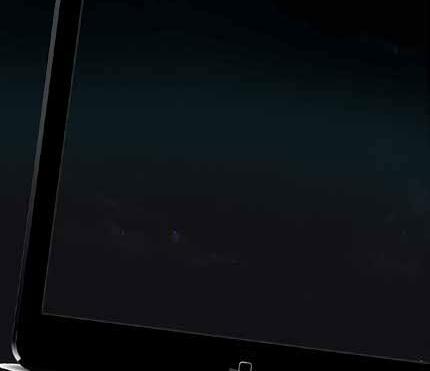
SA
www.samining.co.za
MIN NG
READ WHAT REALLY GOES DOWN IN SADC
WHY ADVERTISE ONLINE
● ADDED VALUE/EXPOSURE TO YOUR BUSINESS VIA
ONLINE CONTENT.
● Help build/strengthen your company’s brand. ● DRIVE TRAFFIC TO YOUR COMPANY’S WEBSITE.
● Expand your reach with various packaged o erings suited to your company’s needs, such as bundling your advertising with news/corporate pro les and/or a video online.
SA Mining, South Africa’s oldest mining magazine, has been providing insight into the local, Southern African and African mining space for 125 years.
COMBINE DIGITAL WITH PRINT FOR GREAT SAVINGS!
We are now giving our readers and clients an opportunity to take their news and advertising online in real time through www.samining.co.za
Banner 728 x 90 px
Island / Medium Rectangle 300 x 250 px YOUR ADS HERE
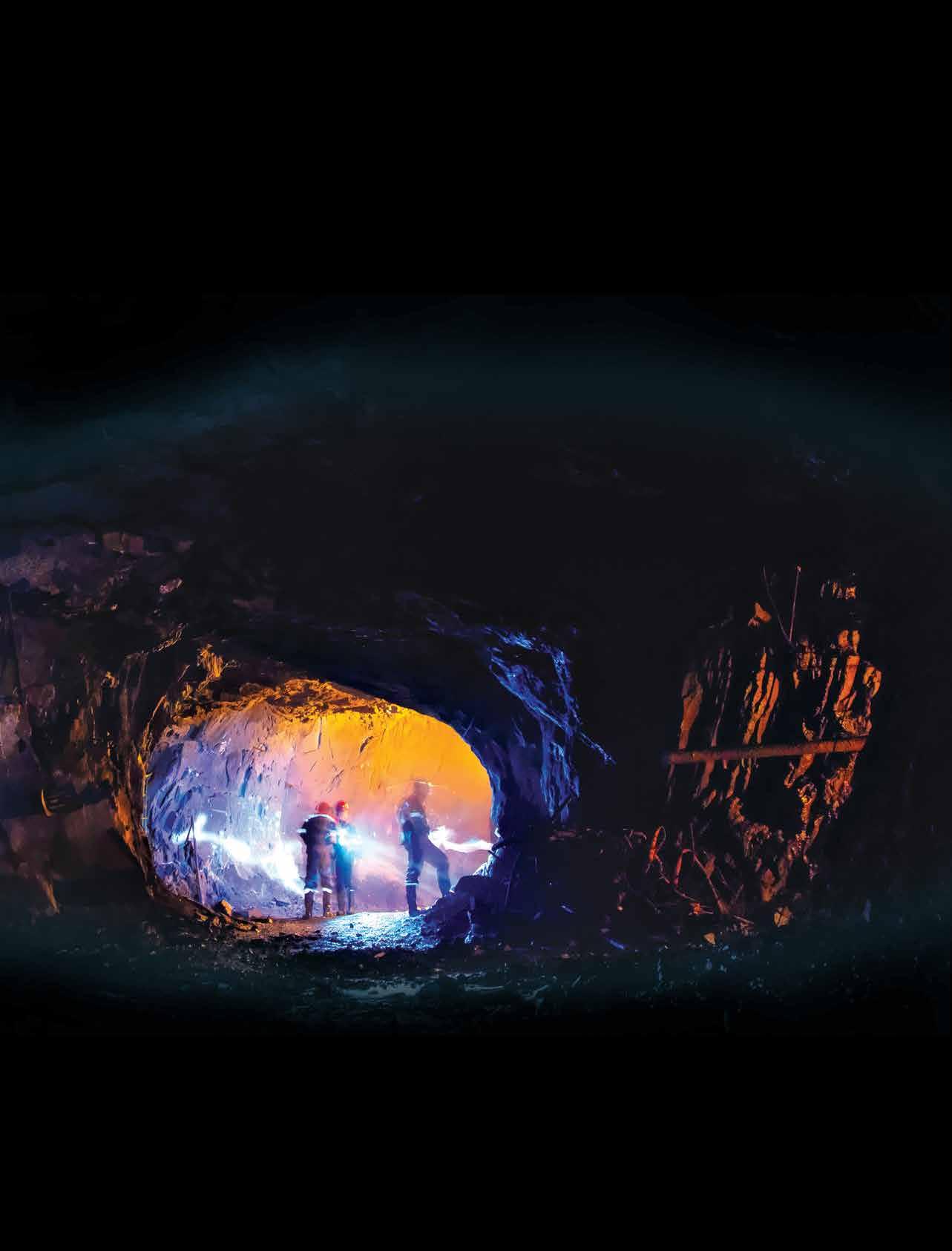
businessmediamags.co.za/mining/sa-mining/subscribe/
www.linkedin.com/company/samining/
www.facebook.com/businessmediaMAGS/company/samining/
SCANHERE
To visit our website.
twitter.com/BMMagazines
www.instagram.com/business_media_mags/
ADVERTISING: Ilonka Moolman 011 280 3120 moolmani@samining.co.za Tshepo Monyamane +27 62 239 3538 Tshepom@samining.co.za
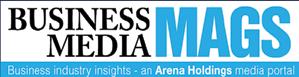