
7 minute read
SAFETY WEAR


PUTTING THE BEST FOOT FORWARD SAFELY
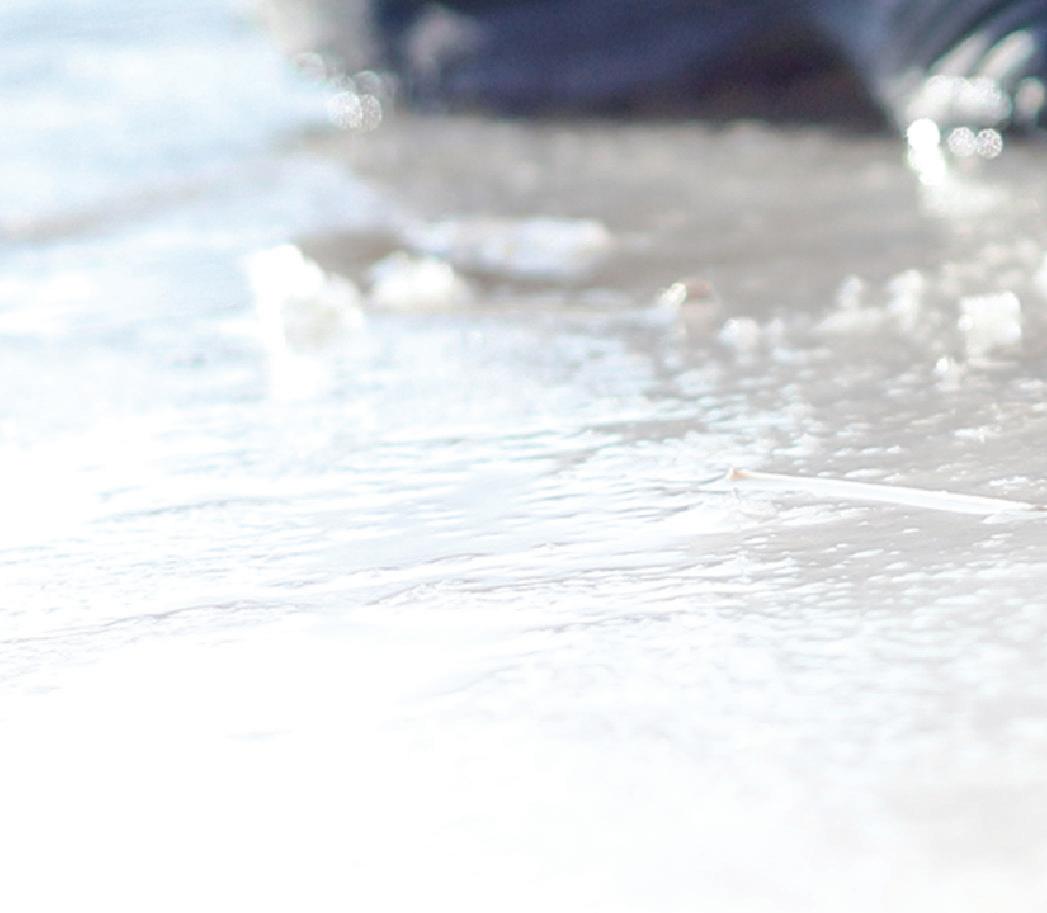
From wearable technology to advances in footwear, new innovations are ensuring that safety workwear provides better protection than ever. By LISA WITEPSKI

Toe-capped boots may be the best-known safety footwear, but the fact that they leave the tender bones of the metatarsal vulnerable to falling objects means that they are not the most effi cient, says Thandi Momubaghan, founder and CEO of Khulunathi PPE specialists.
In fact, says Deane Nothard of the BBF Safety Group, the area is gaining attention as a growing number of case studies highlight the importance of metatarsal protection, especially for workers in industries such as mining. This has led to the development of new technologies. One such development is a gel that hardens on impact, moulding to the shape of the footwear to create a lightweight “shoe”. The drawback, though, is that this gel does not consistently pass tests specifi ed by 20345 regulations. “That’s why, at present, the traditional metaguard is still preferred – albeit with improvements in shape and weight,” says Nothard.
The metatarsal guard is another option, says Momubaghan. Such guards are available as internal or external protection, with a new variety – the external/internal super met guard – gaining traction. “We’ve moved on from the days when external guards made of impactresistant plastic were the only choice. These sat on top of the shoe, covering the entire metatarsal region as well as the toes and were made of hard plastic. The next design featured a leather-like material that was covered with resistant plastic inside. This had the advantage of protecting the foot from sparks and heat, but the hard plastic meant that it was heavy and uncomfortable, and because the guard covered the shoe down to the sole, it often caused falls.
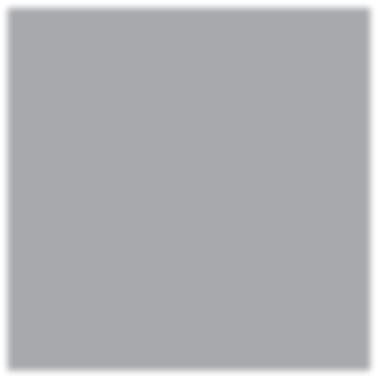
Thandi Momubaghan
the only choice.” – Thandi Momubaghan, founder and CEO of Khulunathi PPE Specialists

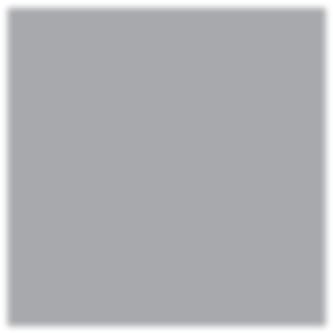
This led to the development of internal guards, along with improved external guards, which are lighter and more fl exible.” Momubaghan predicts that further innovations are certain to come, as worker safety becomes a greater priority.
Sisi Safety Footwear’s Predahni Naidoo agrees, pointing to changes in the growing focus on safety shoes for women as an example. This was prompted by the introduction of the Mining Charter of 2004, which stipulated that 10 per cent of the mining industry’s workforce should be female by 2009. Despite this, a 2012 Unisa report found that most personal protective equipment (PPE) was neither suitable nor safe for women, hence Sisi Safety Footwear’s focus on creating footwear that accommodates the narrowness of the female foot. This is important, Naidoo explains, as a shoe that doesn’t take this unique characteristic into account leads to an oscillation that places strain on the ankle, ultimately, impacting the knee and hip.
WEARABLE TECH
Wearable technology is an especially dynamic area of the industry, says BBF Safety Group’s Nothard, and there are some exciting offerings emerging. These promise to bene t a number of industries not only from a safety perspective, but also in terms of the traceability of PPE. Sensors able to monitor gas, heat and chemicals are a case in point, but Thandi Momubaghan of Khulunathi PPE Specialists warns that these technologies are not without drawbacks. “The process of developing wearable tech should be a multidisciplinary collaboration between experts in medical science, engineering, textile and material science. The usability of wearable tech should be evaluated and accepted in terms of safety and comfort for the human body. It should also be able to pass a water test – for example, what would happen to a person wearing gear tted with electronic components if it started to rain?”
Wearable tech doesn’t come cheap, especially if it is to be worn companywide, she says. However, technologies may help to bring down the number of work injuries, which are also costly for a company. “I think it’s important for companies to weigh these costs against each other,” she says.
Cost notwithstanding, the idea is attractive to South African companies – evidenced by the many private sector enterprises investing signi cantly in R&D, each hoping to make a discovery that would lead either to the development of new products and processes or improve existing ones.
Deane Nothard
WALK THIS WAY
Such injuries are a common hazard for people who spend long hours on their feet, Nothard acknowledges. That’s why podiatrists’ insights are vital when developing safety footwear, from the time the shoe last is designed. “Soling technology has progressed to provide suffi cient cushioning to protect the knees and joints, along with arch support through insoles and orthotics,” he says. However, the considerations don’t end there: the incorporation of materials like colloidal silver and antibacterials is crucial for people working in environments where fungal infections are a risk. Again, mining is a prime culprit here, especially since conditions make it impossible to remove the boot to air the foot. Nothard says that another solution lies in moisture-wicking sock technologies.
A new consideration, from an orthopaedic perspective, is the natural pump action of the foot – a key mechanism for driving blood through the body. “Designing the bottom of the shoe to aid this action can hold signifi cant benefi ts for health conditions like diabetes,” says Nothard.
AND ORTHOTICS.” – DEANE NOTHARD, BBF SAFETY GROUP
PPE DEMAND BY THE NUMBERS
According to data from the Trade and Industrial Policy Strategy, between April and June 2020 South Africa imported 23.2 million kilograms of nonwoven fabrics to be used in the production of face masks and other essentials.
That’s not to say that the country was entirely reliant on imports. The BBF Safety Group increased its capacity threefold to produce PPE, while other companies shifted focus to answer demand. JMP is one such organisation: prompted by a need to keep factories operational during the pandemic, it moved away from its usual manufacturing activities, centred around automotive and engineering, to produce 315 000 face shields.
These success stories are encouraging, and possibly a good omen for South Africa’s manufacturing industry, says Nothard. He notes that the BBF Safety Group partnered with many local suppliers to produce PPE, creating new opportunities for these companies. Moreover, the masks were manufactured entirely out of locally sourced materials.
There is a dark edge to this silver lining, however. Nothard says the lack of understanding of industry regulations is concerning. “South Africa adheres to the European standards, rather than American. This is important because the N95 is an American standard; the South than American. This is important because the N95 is an American standard; the South African equivalent is the FFP2,” he explains.
Unsurprisingly, the market was ooded with masks as companies identi ed a Unsurprisingly, the market was ooded with masks as companies identi ed a potentially lucrative niche. However, many of these had not been regulated or homologated by the National Regulator for Compulsory Speci cations, as required. homologated by the National Regulator for Compulsory Speci cations, as required. The implications are far-reaching: beyond providing protection against COVID-19, The implications are far-reaching: beyond providing protection against COVID-19, FFP2 masks are frequently used to lter chemicals and harmful gases in industries FFP2 masks are frequently used to lter chemicals and harmful gases in industries like mining. It is, therefore, critical that technical properties such as breathability like mining. It is, therefore, critical that technical properties such as breathability comply with regulations.
WHAT’S NEW IN NONSLIP
When it comes to nonslip technology, the development of lighter-weight polyurethane soles is big news, says Thandi Momubaghan of Khulunathi PPE Specialists. She’s also excited about the use of direct-attach construction, as well as cement construction techniques that improve the resilience and elasticity of the soles and mid-soles of safety boots.
This is an area that may increasingly come under the spotlight, says Deane Nothard of the BBF Safety Group. He points out that the SRC slip rating included in the 20345 regulations is becoming a norm, where once it was an exception.
However, it is important to bear in mind that SRC measures are based on tests on smooth surfaces. While this may be appropriate for industries such as hospitality or in hospitals where extra grip is needed, it is not necessarily the correct measure at a construction site or open cast mine. Here, stability in uneven terrain is the main consideration.
At the same time, the South African Income Tax Act’s R&D Incentive, designed speci cally to encourage innovation, may also be contributing to the interest in developing wearables, Momubaghan says.


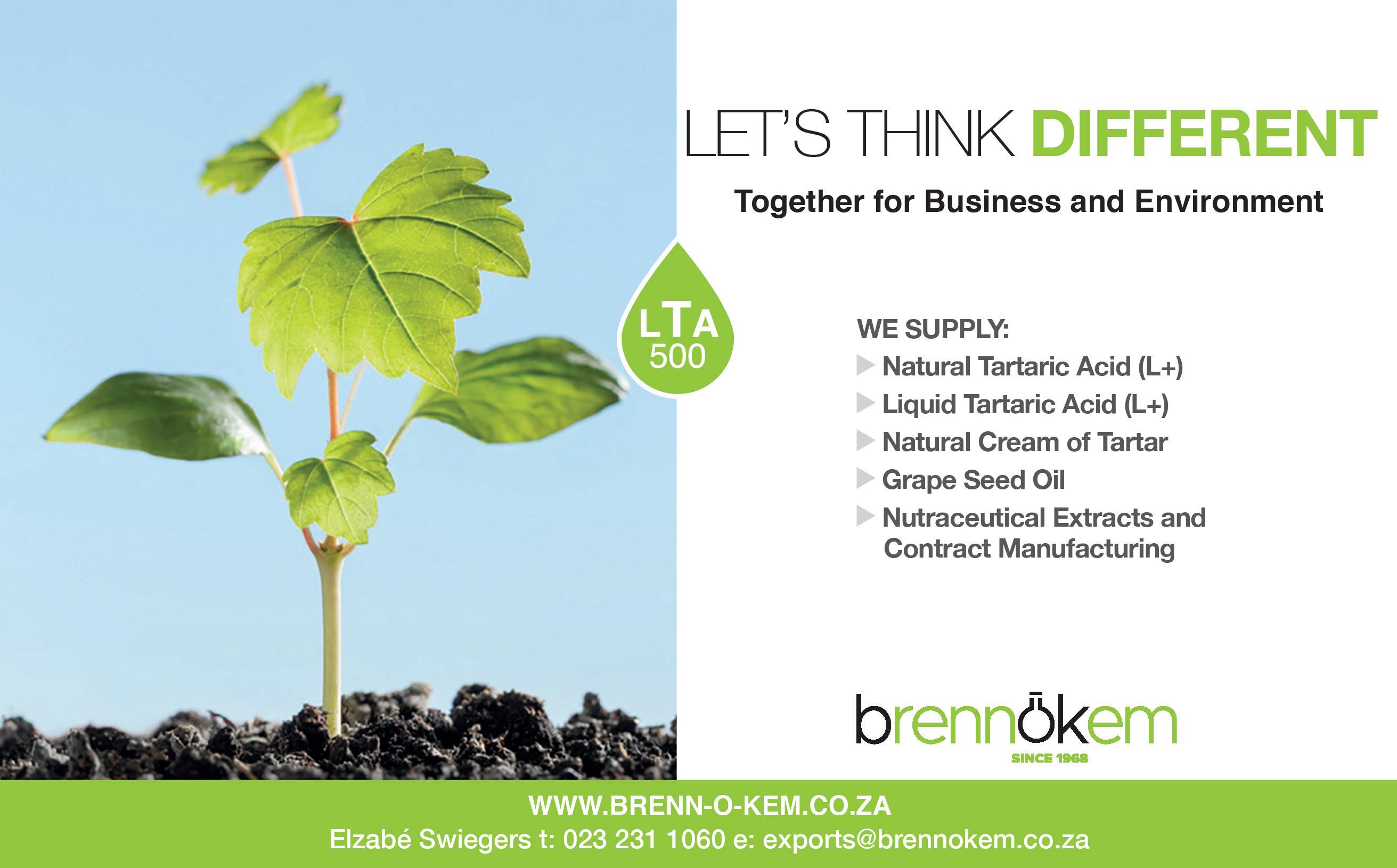
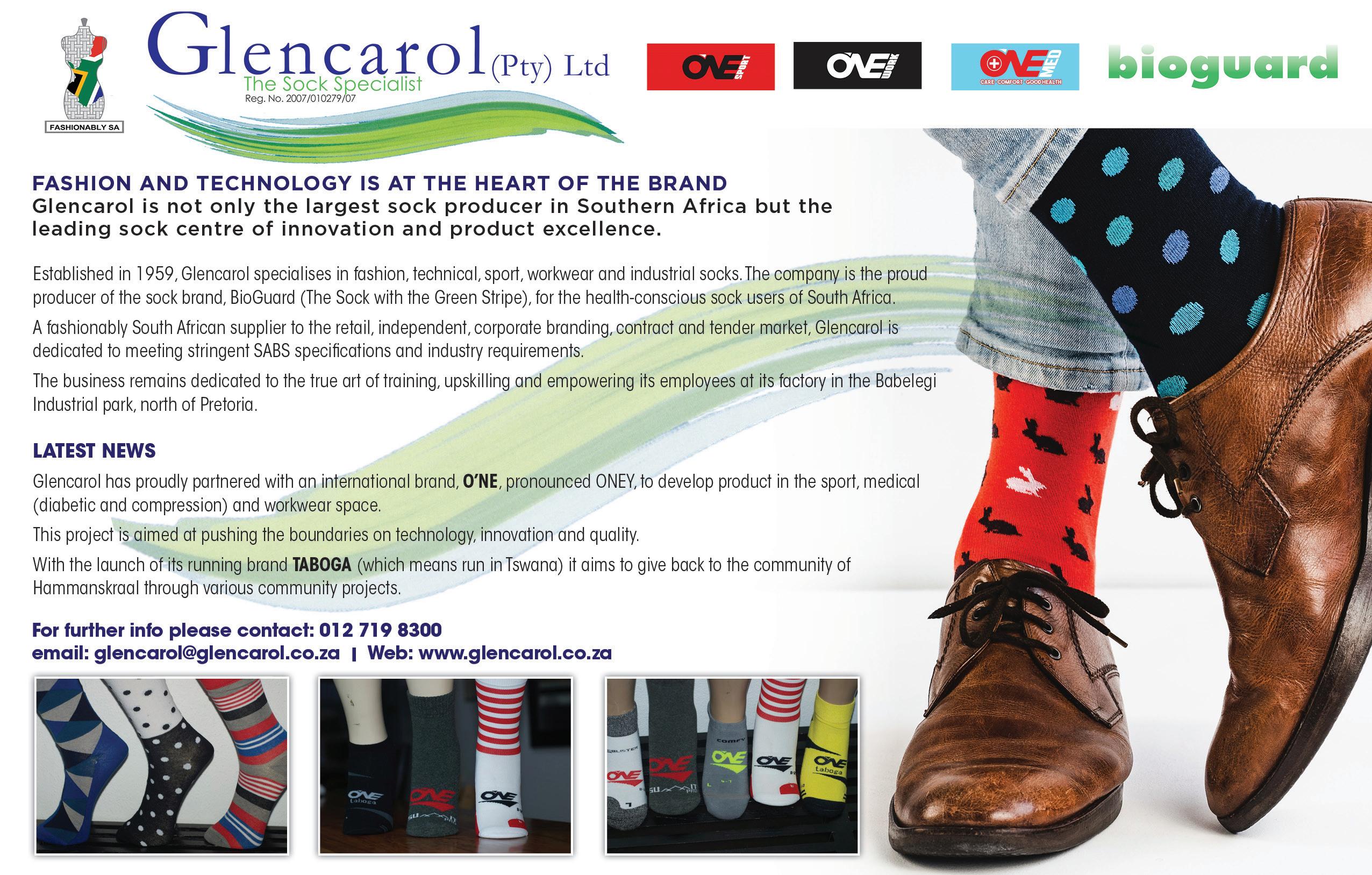