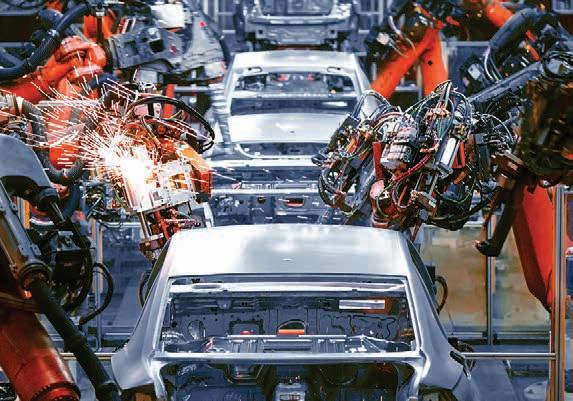
15 minute read
AUTOMOTIVE

Technological advances continue to automate vehicle production lines.
BMW’s Rosslyn manufacturing plant manufactures upwards of 76 000 X3 models for local and export sales.
IN THE HEADLIGHTS
How long will it take for the local automotive industry to recover from the impact and consequences of the pandemic? By TREVOR CRIGHTON
With new vehicle sales in South Africa already having declined 2.8 per cent in 2019, the automotive industry was hoping for an improvement in 2020, but saw a 29.1 per cent decline from 536 612 to 380 449 units on the back of the lockdowns and subsequent economic pressures of the COVID-19 pandemic, according to the National Association of Automobile Manufacturers of South Africa (NAAMSA). Its December 2020 sales report showed that the impact of the pandemic put domestic new vehicle sales numbers back two decades.
Dr Martyn Davies, managing director for emerging markets and Africa at Deloitte, says the recovery process is complex. “The peak for automotive sales in South Africa was 2013. If you take into account the structural decline new car sales and the economy have experienced since then, we need to ask whether ‘recovery’ looks like returning to the highs of 2013 or simply getting back to tepid 2019 levels.”
DID YOU KNOW?
Counterpoint analysts estimate the industry will decline nearly 20 per cent over 2019. Comparisons between January–September 2020 sales and those during the same period in 2019 showed volumes down 29.3 per cent in Europe, 18.8 per cent in the USA, 18.1 per cent in Japan, 32.9 per cent in Brazil and 12.5 per cent in China.
says that the success of franchise dealers is not measured only on vehicle sales, but also on services and parts. “Since September, NADA’s member dealers have returned to near-normality in workshops due to more regular commuting patterns. Supply challenges around new vehicle stock across brands are also impacting negatively on new vehicle sales.” He estimates that, depending on how the pandemic plays out over the remainder of 2021, it could take at least another 18 to 24 months to full recovery.
McCraw says that motor vehicle dealerships support about 60 000 jobs, with closures and consolidations in the past year resulting in the loss of just over 7 000 jobs in that sector alone. “Within the last 11 months we saw seven dealership amalgamations, 21 dealerships sold and 42 closures. We don’t anticipate many more casualties, as the big groups have already taken the hard decisions and right-sized their businesses in the face of the pandemic.”
LEADING THE WAY?
Davies cites the SA automotive industry as the only successful case of industrial policy in the country in the past generation. “While every other sector has been hollowed out, the automotive industry has remained solid. Credit to the DTIC and the industry for working together to shape policy that retains and grows original equipment manufacturers (OEMs) in South Africa,” he says.
He cites Korea as an example where plans like South Africa’s delayed Automotive Production and Development Programme (APDP) have worked. “Korea has a smaller population than South Africa, but it’s the eighth-largest car market in the world. It has been able to produce massive volumes for export on the back of a huge windfall from a local market that’s been protected,” he says. “The APDP aims to export a million cars by 2035, so there’s going to have to be a dramatic shift to get there. The UK – one of our largest export markets – plans to ban the sale of petrol and diesel cars by 2030. The industry needs to make a major shift to producing electric vehicles for export or scramble for new markets, fast.”
WORK IT
Gary McCraw, director at the National Automobile Dealers’ Association (NADA),
THE AUTOMOTIVE INDUSTRY’S VALUE
The automotive industry contributes 6.4 per cent to South Africa’s gross domestic product (GDP). • Total automotive revenue in South Africa amounted to R500-billion in 2019. • In 2019, the export of vehicles and automotive components reached a record R201.7-billion, equating to 15.5 per cent of South Africa’s total exports to 151 international markets. • The industry accounts for 27.6 per cent of the country’s manufacturing output. • The manufacturing segment of the industry presently employs more than 110 000 people across its various tiers of activity. • Combined with the industry’s strong multiplier effect, the automotive sector is responsible for about 457 000 jobs across the South African economy’s formal sector.
Source: NAAMSA
MANUFACTURING

WWW.BUSINESSMEDIAMAGS.CO.ZA APRIL 2021

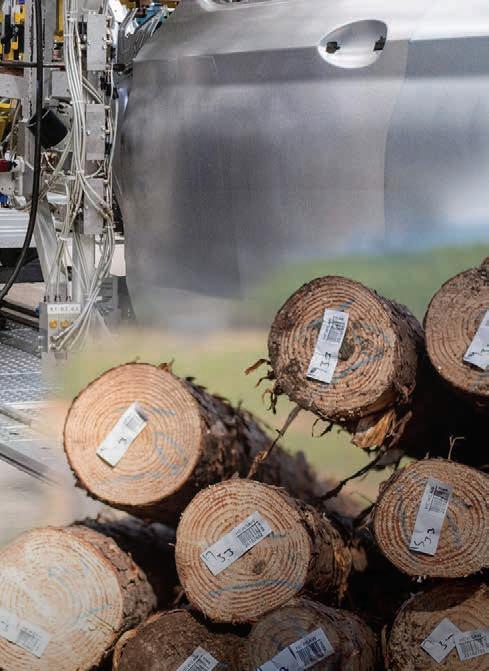

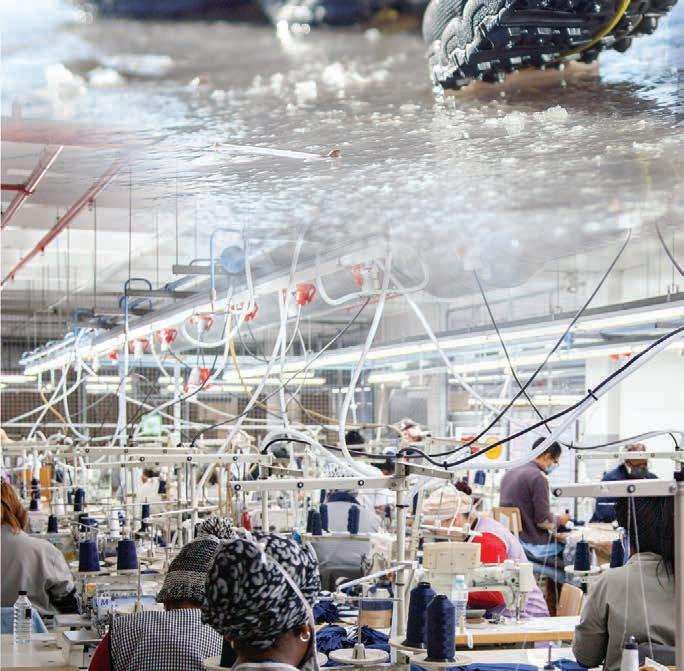
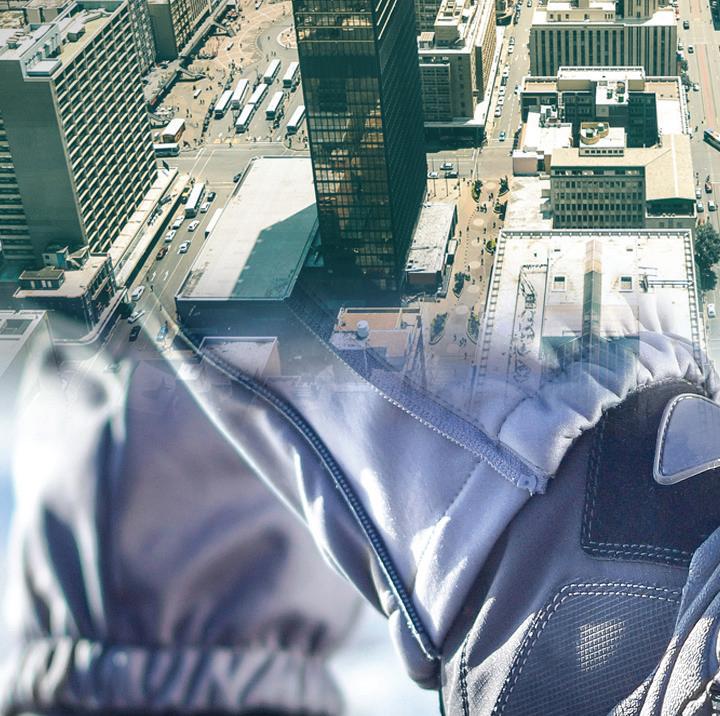


THE NEXT ISSUE OF MANUFACTURING WILL BE PUBLISHED IN SEPTEMBER 2021
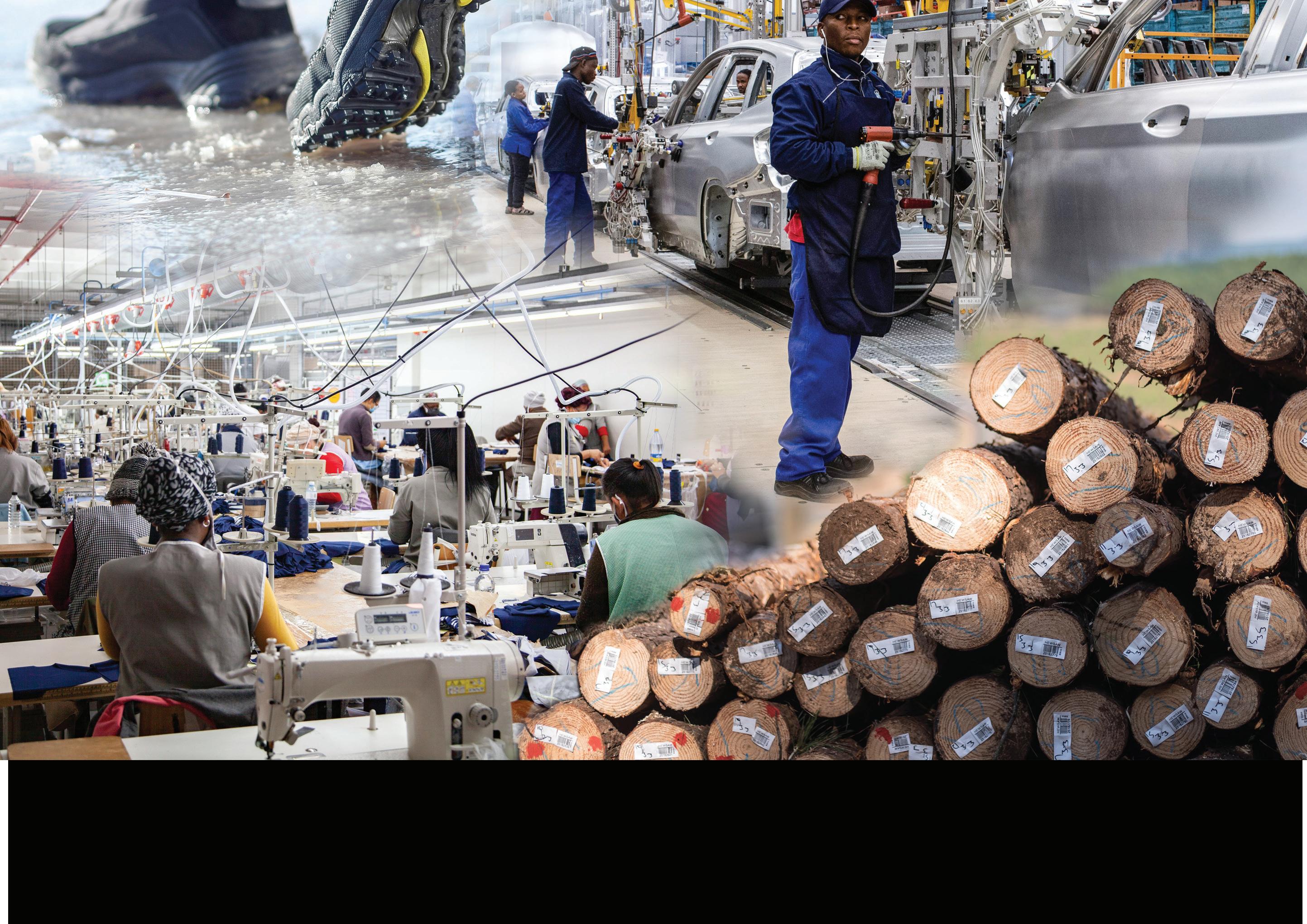
To advertise contact: Tarin-Lee Watts Business Development Specialist p: 087 379 7119 m: 079 504 7729 e: wattst@picasso.co.za

LITHIUM-ION VS LEAD-ACID
While both types of battery have benefits and disadvantages, which has the greatest staying power? By RODNEY WEIDEMANN
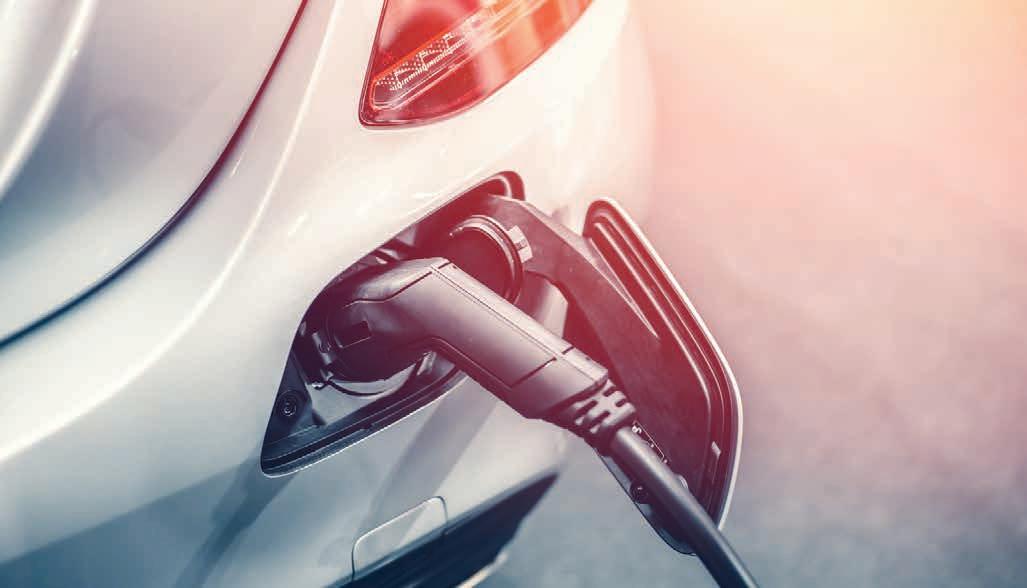
The increasing uptake of electric vehicles (EVs) around the globe is resulting in a growing number of advancements in lithium-ion battery technology, along with a related fall in prices. All of this raises the question: does the traditional lead-acid battery still have a long-term future?
Proponents of lead-acid batteries will point to their lower costs and greater recyclability as key advantages, but the truth is that both types offer certain unique benefits, as well as disadvantages.
Gareth Farrell, solar and eco energy specialist at Oxbow, indicates that the continuing technological advancements and decreasing price of lithium-ion batteries may signal the beginning of the end for lead-acid batteries. “We are reaching a tipping point where the popularity and use of lithium-ion batteries will begin to overtake the traditional lead-acid type. There are many applications and uses for batteries in general, so I am sure many will remain on the lead-acid platform for a long time to come. However, it should be clear that in the renewable energy space, at the very least, the tide is turning firmly in favour of lithium-ion.”
Professor Bernard Bladergroen, head of the Energy Storage Innovation Lab at the University of the Western Cape, adds that it boils down to the individual use case for the battery. “As a pure energy storage device, for example, a lead-acid battery power backup system is a cost-effective option if power outages are happening less than once a week. On the other hand, if the battery is used in conjunction with something like a photovoltaic solar array and exposed to daily cycles, then lithium-ion is the better option,” he says.
“Overall, lithium-ion certainly seems to be the future of battery manufacture, particularly as electric vehicles become increasingly popular. Current lithium-ion battery demand warrants the construction of gigafactories. Mass production drives down prices, further improving the market position for lithium-ion – there is a massive future for these batteries.”
Bladergroen says that the required supply chain for manufacturers to distribute is also growing, and ongoing research is leading to regular improvements in the technology, so quality is increasing as price is decreasing.
FAST FACT
Having the ability to manage the use of lithium-ion batteries through an electronic battery management system, via inverters, has made these batteries the first choice for the solar industry.
Source: Gareth Farrell, solar and eco energy specialist, Oxbow
LEAD-ACID BATTERY INNOVATIONS
There are regular advancements made in battery technologies, and in the lead-acid space, the focus has been to reduce the charging time and increase the lifespan of the cells. A key innovation has been absorbent glass mat technology. This ensures the battery is extremely resistant to vibration, remains totally sealed, nonspillable and maintenance-free, while also offering better cycling performance and minimal gassing and acid leakage.
Source: Gareth Farrell, solar and eco energy specialist, Oxbow
THE RECYCLING QUESTION
Farrell suggests that at present, lead-acid batteries are by far the more recyclable product due to their make-up being primarily plastic and lead. Alternatively, the counterargument for lithium-ion is the lower requirement for recycling, due to the far greater lifespans of these batteries.
Bladergroen adds that this is also because lead is far more toxic than lithium-ion battery components, which has resulted in a far more regulated environment. “As the lithiumion market grows and things like EVs become the technology of choice, so the lithium-ion recycling processes will themselves mature.”
Farrell agrees that lithium-ion technology is certainly going to dominate in the future, noting that it is technology already used on a grand scale in all manner of applications, including power tools, radio-controlled devices like drones and many other similar offerings. “However, potentially the biggest driver for the advancement of lithium-ion is the huge global push towards EVs that no longer rely on fossil fuels. This is because lithium-ion offers a far greater output from a smaller form factor – and power, weight and size are all key factors in EV design.”

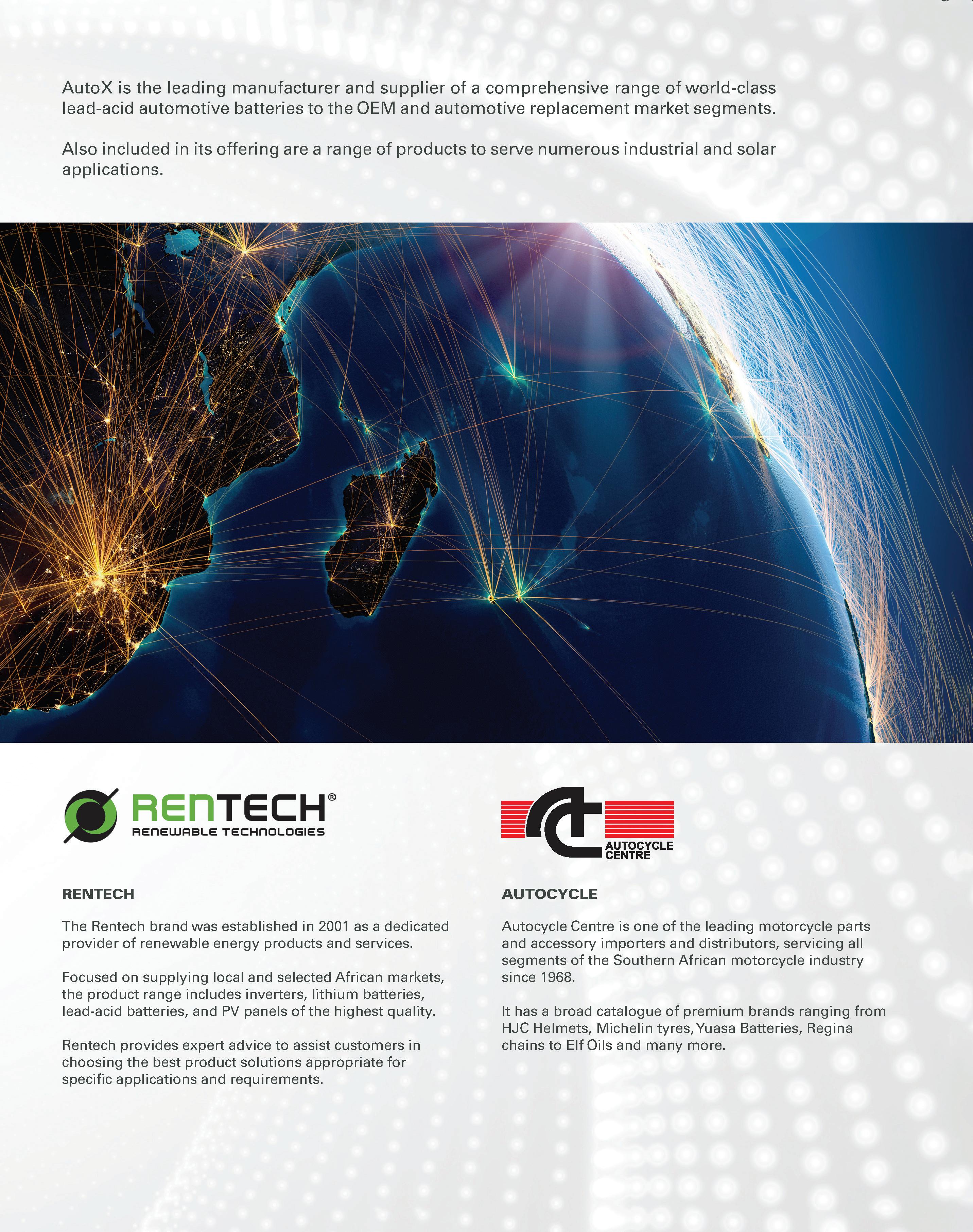

OTHER USES FOR LITHIUM-ION BATTERIES
Lithium-ion batteries have a wide range of applications beyond just electric vehicles, and as prices drop we can expect to see widespread adoption across a number of other industries. Almost all portable consumer electronics today, including laptops and mobile phones, use this technology. It is also implemented as stationary storage for telecoms, railways, uninterrupted power supplies and power back-up solutions.
Other uses include as a lightweight and safer alternative for boats, for implantable medical devices (due to its long-lasting capacity) and as the best-match storage device for solar energy, due to its manner and speed of charging.
Source: James Mackay, South Market lead for Energy, PwC Africa
THE BENEFICIATION GAME
THE E-VALUE CHAIN
As a large manganese producer, will South Africa remain an exporter of this lithium-ion battery component, or will it begin producing the end products? By RODNEY WEIDEMANN

As the demand for electric vehicle (EV) batteries rises, South Africa is well positioned to potentially capitalise signifi cantly on the growth of this market, being the world’s largest producer of manganese, a crucial component of the lithiumion batteries used for EVs.
However, producing the raw material and creating the fi nished product are two different things. Is South Africa truly capable of becoming a competitive producer of fully functional EV systems, rather than just a primary exporter of raw or partially developed materials?
Kelvin Naidoo, manufacturing and technical director at Auto-X, a leading local battery manufacturer and distributor, says that the South African government has been driving mineral benefi ciation hard, with lithium battery manufacture a key channel. “At present, local companies are working on producing high-purity manganese for export primarily for the battery industry. Unfortunately, we do not yet have large-scale lithium battery manufacture, but a signifi cant amount of research and policy development is underway to facilitate the growth of this industry.”

NO EASY CHARGE
James Mackay, PwC Africa South’s market lead for energy, says that there are multiple steps in the manufacturing process for lithium-ion batteries, from the extraction and purifi cation of mineral ore to the construction of the battery components and fi nal cell assembly. “With the right policy and regulation, South Africa can harness a signifi cant part of the value chain domestically for lithium-ion manufacturing. “Mineral refi ning for
Kelvin Naidoo producing the active precursor chemicals required for the cell components is certainly an area where the nation should develop and harness capabilities. The proximity of raw minerals in the country and nearby regions along with our mining and refi ning capabilities positions South Africa as an ideal location for the manufacturing of lithium-ion cells and batteries.” Benefi ciating the minerals to one extent or another is a good thing, but still offers nowhere near the benefi ts of being able to produce fully functional EV systems. To do this, Naidoo says, will require development of the broader value chain. “While the raw materials are available, producing the active materials is a complex, expensive process, which tends to be viewed as high risk because battery technologies are changing very fast.
“Battery cell manufacture is perhaps the lowest-risk element of the value chain,” Naidoo continues, “but even this requires active materials from other sources if not available locally. On the other hand, battery pack assembly is relatively easy and low risk – several small assembly facilities are already active.”
Mackay believes that for South Africa to become an integral part of the lithium-ion battery industry, the government must recognise the importance of this technology, and draft policy and regulations for driving and incentivising innovation and investment in the manufacturing of lithium-ion batteries. “Integration of the country’s production capabilities with global markets is needed, as international demand for lithium-ion batteries is increasing rapidly. Furthermore, attracting private investment in this sector will play a key role in the development of the domestic industry. After all, creating local content and value chains can unlock signifi cant growth and jobs for South Africa,” he concludes.
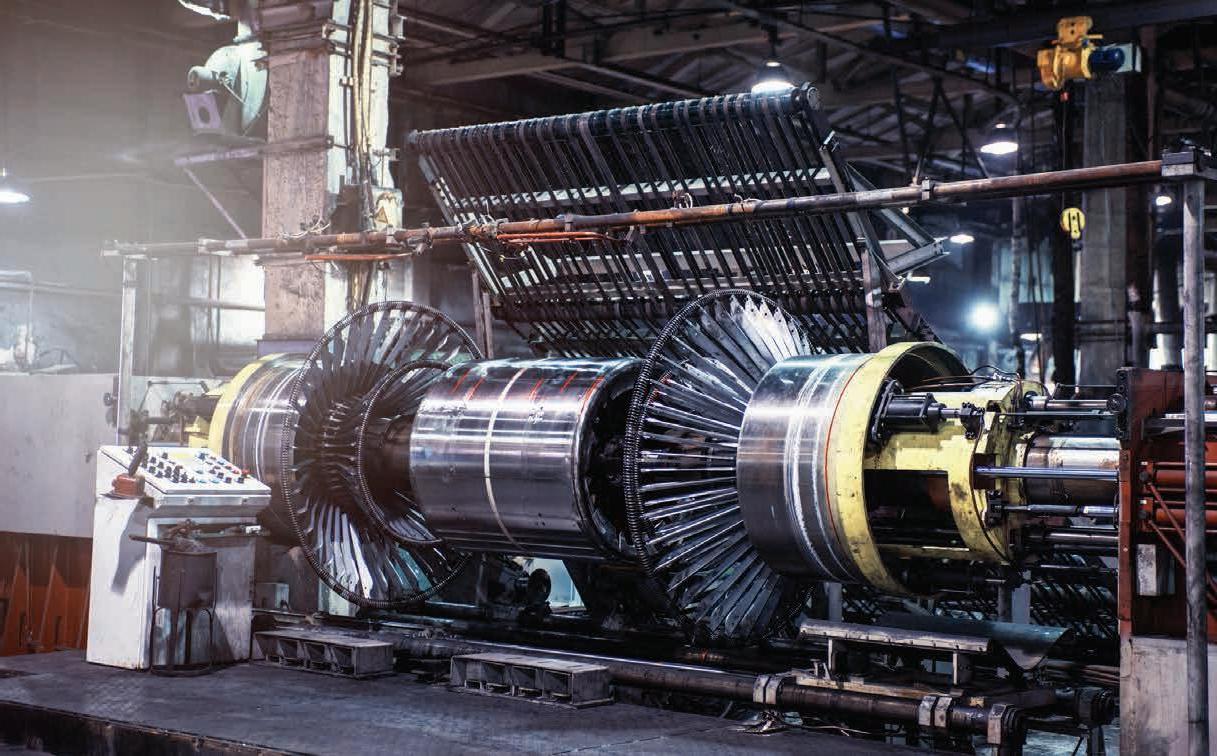
“T he post-COVID reality for most industries in the country, if not the world, is that on the back of job losses, pay cuts and lockdowns, fewer people are driving. Someone who previously drove 30 000km a year is now driving 5–10 000km, so their tyres aren’t wearing as much,” says Bridgestone South Africa CEO Jacques Fourie. “With mileage being lower, when it’s time to buy new tyres, people are opting for lower-tier products – also with an eye on cost effectiveness – putting the local tyre manufacturing industry under pressure.”
South African Tyre Manufacturers’ Conference (SATMC) managing executive Nduduzo Chala is upbeat about the industry’s prospects, however. He says that SATMC members have done plenty to stabilise sales, with a focus on production quality and the retail space, and communicating better with customers. The SATMC, which comprises local manufacturers Bridgestone, Continental, Goodyear and Sumitomo, reports quarterly on tyre sales. At the end of Q4 2020, the new tyre sales market was down 15 per cent across the board, with sales shrinking to below 10 million tyres – the majority of lost sales coming at the expense of the local manufacturers.
Chala says that imports from other brands have been making inroads into local market share since 2016, with price sensitivity a major factor. Local products still account for just over half of sales, though. “Some of these imports are cheaper because of the manufacturers’ economies of scale. We rely to an extent on retailers promoting South African products as the go-to, but also look to government to assist with production incentives to ensure we can remain competitive.”
BUILDING RUBBER
Increasing imports from Asia and the economic downturn have put the tyre industry under pressure in recent years. TREVOR CRIGHTON looks at the outlook for this pivotal local industry
GROWTH OPPORTUNITIES
INNOVATIONS IN TYRE TECHNOLOGY
Bridgestone was the rst of the local manufacturers to produce run- at tyres in South Africa. The Alenza range, also produced here, is an OEM product on several vehicles and is exported to the US, Europe and Australia. The company is also expanding into mobility solutions provision, with a focus on developing solutions for eet customers in particular, on the back of the international purchase of TomTom Telematics a few years ago.
Source: Bridgestone
The presence of these four manufacturers in South Africa makes the country a manufacturing hub for the rest of the continent. Chala says their focus had largely been on stabilising the local market before expanding into the rest of the continent. All the brands make products here for both local and export markets, and also import some lines for use here.
“There’s certainly a growth opportunity in the rest of Africa,” says Chala. “That will come with the right support from the policy space – things like the African Continental Free Trade Agreement – which will help us become more competitive in the export market.”
Fourie says that locally produced Bridgestone tyres are exported as standard fi tments for original equipment manufacturers (OEMs) like BMW and Toyota that produce vehicles in South Africa for other markets, while also exporting their products. “The tyre industry is a broader part of the automotive industry and South Africa is its continental home, so products from our industry are exported into many other markets across Africa,” he says.
Despite having to close the company’s Port Elizabeth plant – which had been operational for 86 years – Bridgestone’s main Brits plant has seen an investment of hundreds of millions of rands recently to enable it to produce new product lines. “We’ll soon be announcing substantial OEM contracts, for which we’ll be producing those new lines,” says Fourie. “The technology we’ve brought to South Africa allows us to manufacture those products for global export with the OEMs – this is a tremendous boost.
“We’ve also worked hard to secure contracts with local automotive manufacturers that have announced investment in their plants to produce vehicles for the local market and global export.”