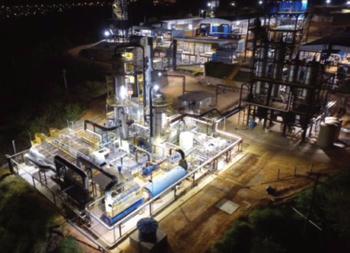
9 minute read
Clark Solutions: 30 years of continuous innovation
Feature Clark Solutions: 30 years of continuous
innovation By: Bruno Ferraro, Victor Machida, and Nelson Clark
This year Clark Solutions celebrated its 30th anniversary. For three decades, the company has been solving complex problems for our industry, developing new technologies and bringing state-of-the-art solutions to customers.
This article is a retrospective of what we accomplished and contributed, especially for the sulfuric acid market.
thirty years of continuous innovation
Nelson Clark Engenharia (NC) was founded in 1991 as the exclusive representative in Brazil and Chile of the former Monsanto Enviro-Chem Systems (MECS) for Sulfuric Acid Products and Technologies.
Early in 1992, the company started a successful business relationship with Otto H. York Company Inc., which culminated in 1995 with the licensing to NC of the rights and technology for the manufacture of Otto H. York’s wire mesh mist eliminators. At that time, Clark Solutions was, and still is, one of the very few wire mesh mist eliminator manufacturers in the Southern hemisphere.
Wire mesh mist eliminators, invented 1959 by Dr. Otto H. York, consist of a mesh formed by extremely fine-knitted metal fabric that is woven, corrugated, and layered in such a way as to provide a very high surface area and high void fraction. This construction enhances mist elimination by inertial impaction and direct interception of droplets, while the gas easily bypasses the wire obstacles imposing low pressure drop.
By the time NC started this manufacture, high-capacity eliminator models were improved by employing geometric changes and multilayer designs with different wire characteristics.
Also, co-knitting wires with extremely fine multi-filaments of fiberglass, PTFE, PET, and other thermoplastic or thermoset polymers radically increased particle collection surface area, which, in turn, provided a similar increase in mist elimination efficiency.
Wire mesh 100% capture efficiency improved from 10-micron particles to 2-micron particles due to these developments.
Today, Clark Solution’s MaxiMesh® is widely used in the sulfuric acid, petroleum, and chemical industries, where its application has provided important lessons learned and technological enhancements to the product’s development.
By 1999, NC Engenharia developed the capacity to manufacture ceramic saddles for absorption and drying towers. Mass transfer media also progressed toward more effective contact area and lower pressure drops, two often competing factors. Due to acid concentrations and temperatures in the process, acid-resistant ceramic packing was most commonly used. The packing’s geometric complexity was limited to what is mechanically robust and manufacturable in large-scale.
One of the first widely known packing is the cylindric Pall Rings, a geometrical design dating back to 1907. It has seen surface area improvements Lessing Rings and Cross Partition Rings. Other popular ceramic packing is the Berl Saddle from the 1930s, which in the 1950s evolved to saddles, a very successful geometry that became the industry standard for sulfuric acid tower applications. Of course, there were also many improvements to the geometry and ceramic techniques that increased the packed bed efficiency and/or lowered pressure drop.
Using a quality controlled automated process, Clark Solutions produces its standard MaxiSaddles® and its very successful MaxiSaddle® BPC line, which is a more open, low pressure drop ceramic packing. Developed in 2016 and continually optimized since, this model lowers pressure drop by 35-50% compared to standard saddles used to enhance tower capacity.
In 1997, Koch Industries acquired Otto H. York Company and its mother company Koch-Glitsch and, in 2003, NC formed a joint venture with Koch-Glitsch to manufacture and improve the line of solutions in mist elimination and mass transfer, creating the company Clark-Koch. At that time, the almost 25 year business relationship with MECS came to an end.
The production of fiberglass Brownian diffusion mist eliminators started in 2005. These candle-type filters are mostly applied in drying, absorption, and heat recovery towers, due to the massive presence of fine (<1 µm) mist generated by condensation chemical reaction.
To efficiently collect such fine droplets, mechanisms that take advantage of Brownian diffusion phenomena are required. When particles are this small, they follow a random pattern generated by the fluid in which they are suspended. They follow their path until they collide with the glass fibers from the mist eliminators. The grid that holds the fibers can be made of different materials depending on the application.
Clark’s candle filter manufacturing started with vast accumulated experience and many improvement ideas that have been implemented over the years.
Today, Clark Solutions FiberBed® fully automated manufacturing allows a wide variety of arrangements with unique capabilities such as fiber variable traction (density) control, continuous pressure drop monitoring, and different winding patterns (parallel or angled), along with multiple diameters, heights, and bed thicknesses. In 2018, Clark Solutions introduced an innovative DrySeal™ device that seals the
Fig. 1: Co-knitted MaxiMesh® model shows the increased surface area.
Fig. 3: FiberBed® products can be customized to meet specific requirements. Fig. 5: Largest sulfuric acid towers in Brazil, by Clark Solutions.
Fig. 6: Testing high efficiency trough-type acid distributors.
Fiberbed® without the need for the dangerous and unsafe filling of seal cups.
In 2006, a major step was taken when the first Clark Solutions complete absorption tower was manufactured in Brazil, with all the internals, for application in sulfuric acid plants. Since then, dozens of sulfuric acid process towers and several tower internals were designed, manufactured, and installed, with continuous improvement in materials and design for mist eliminator, liquid distributor, ceramic packing and packing support, corrosion protection, and brick lining technologies.
In 2007, Clark Solutions developed and installed its first trough and downcomer distributor for sulfuric acid. This product was born from vast company experience in mass transfer in large refinery operations where distributions need to be extremely homogeneous. Metal work know-how has evolved within the company, and the benefits of high silicon and other sulfuric acid resistant alloys are present in our products.
In 2015 the joint venture was terminated, and the company name changed to Clark Solutions. In the same year, Clark Solutions worked on a new technology called SAFEHR BFW®. It focused on heat recovery in absorption towers, where normally the SO3 absorption heat reaction is wasted on cooling water. Designed to partially recover this lost heat, SAFEHR BFW® consists of two plate heat exchangers in between a closed water loop, transferring heat from the hot absorption acid in one heat exchanger and heating boiler feedwater in the other heat exchanger, using the closed loop water as medium. The design increases energy efficiency with limited risk to boiler feed water, which can debottleneck and improve steam generation capacity.
This indirect heating of boiler feed water allows control over any eventual instrumentation leakage in the closed circuit. The closed circuit also prevents contamination of the steam lines with acid and can be applied to heat not only boiler feed water, but also other plant utilities.
Clark Solutions SAFEHR® technology was also created and developed by 2017. The system principle shares similar configuration philosophy to SAHFER BFW® , introducing an intermediate cooling system for the hot acid. However, the process takes a different approach, to recover SO3 absorption energy from sulfuric acid to generate steam.
The complete system is basically composed of a two-stage absorbing tower with integrated pump booth, an acid pump, and the SAFEHR® system. The circulating absorption acid is concentrated above 99% and SO3 is admitted in the lower packing deck where the reaction heats the acid to 200-225°C. The gases leaving the lower absorption stage pass through a collector tray and goes to an upper packing deck, reducing gas temperature, absorbing residual SO3, and collecting mist.
The hot concentrated acid in the bottom of the tower is pumped to a heat exchanger in the SAFEHR® circuit which has a refrigerating inert CS fluid in closed loop. The inert fluid circulating in the enclosed system heats boiler feed water or other fluids in this circuit with capacity to generate mid-pressure steam.
Thus, SAFEHR® technology is a new approach to sulfuric acid heat recovery processes that addresses its major concern, which is safety. Hydrogen incident risks may render conventional heat recovery systems unattractive. However, in SAFEHR® operation, any leakage scenario is covered by the presence of the intermediate inert CS fluid. This operation is considerably safer due to the following fluid characteristics:
Inert to acid and water: the fluid is totally inert to acid (in any concentrations) and to water. Also, the fluid is noncorrosive, non-toxic, non-flammable and non-oxidant (so it can be used and stored in non-blanketed environments). In addition, it is non-miscible in water and in acid, allowing proper separation through coalescers with fluid density staying in between water and acid operating temperatures.
With heat recovery safety issues addressed, the plant can provide its best specific steam generation. To illustrate, conventional simple absorption plants have approximately 1.6 ton steam/ton sulphuric acid yield, while a simple absorption with SAFEHR® has a 1.8 ton steam/ton sulphuric acid yield. The first SAFEHR plant has been in service for two years and, despite an occasional hot heat recovery acid leak, the plant has remained in service until the scheduled maintenance turn-round, as promised by the technology.
In recent years, Clark Solutions developed a concept of small modular plants to cater to small sulfuric acid demands. This required reducing equipment size and quantity. The solution is a simple absorption/scrubbing plant since it eliminates both the gas-gas heat exchangers and the intermediate absorption tower. These are huge and costly equipment, representing a significant portion of the CAPEX and OPEX. The reason being the pressure drop that the gas stream needs to overcome when having both present.
To replace the gas-gas heat exchangers, thermal equipment such as boilers, economizers, and superheaters can be used. This enables more control and capacity for the steam system.
Considering that there is no intermediate absorption tower, the SO2 oxidation reaction is less favorable to the SO3 side. Thus, the overall conversion on the catalytic reactor is lower. To compensate for the excess SO2, a tail gas scrubbing system is placed upstream from the stack. The scrubbing solution is selected according to the client’s needs, as it can yield a high value co-product. Here are some examples: • Using ammonia (NH3) to retrieve ammonium sulfate (NH4)2SO4 • Using caustic soda (NaOH) to retrieve sodium sulfite (Na2SO3) and/or bisulfite (NaHSO3) • Using hydrogen peroxide (H2O2) to retrieve diluted sulfuric acid
The option of hydrogen peroxide is normally used when no co-product is desired, and the diluted sulfuric acid is sent to the sulfuric acid circulation tank as dilution water. Regenerative SO2 technologies can also be employed when no co-product is needed.
In 2020, Clark Solutions created its first plant with such concepts. This plant is designed as a single absorption plant with an oxygen peroxide tail gas scrubbing system. The plant uses sulfuric acid to extract high value minerals from raw material, and the plant can use calcination exhaust gases as a SO2 source as well as elemental sulfur. It has a max capacity of 135 MTPD for pure sulfur burning and 150 MTPD capacity for sulfur and calcination gas combination. The sulfuric acid plant is equipped with SAFEHR® technology system, validating Clark Solutions patented process in industrial scale.
Fig. 8: This SaFeHR® schematic shows how the heat recovery system performs.
Conclusion
As our clients’ requirements and environmental needs increased, we increased efficiency and safety for our previous and new products and projects. Over time, Clark added more products to its portfolio and accumulated more knowledge, to offer better and more innovative solutions to its clients. This close relationship built strong ties with the sulfuric acid market, especially in Brazil. Today, Clark Solutions is known not only for internals, but also for delivering entire towers, piping, and all sorts of engineering projects and services.
Our job is far from over, as investments in research and development are still very strong. All efforts are made to better understand where the process can be optimized and find creative ways to implement these ideas.
For more information, visit www. clarksolutions.com. q