
9 minute read
The latest in sulfuric acid plant process gas dewpoint/moisture leak detection
By: Daniel T. Menniti, Director of Business Development, Mississippi Lime/Breen
Since the mid-1980s the sulfuric acid manufacturing industry has desired a maintenance-free, early indication of moisture ingress (most likely from boiler or economizer tube leaks) into their sulfuric acid manufacturing process. It was understood that if there was moisture present in the process gas, that the acid dew point temperature of the gas would increase. So, it was decided that if one could measure the acid dew point continuously, producers could monitor the trends and an increase of acid dew point would indicate a leak, or moisture ingress into the process gas.
This desire brought about decades of frustration, while the industry trial and errored an acid dew point meter technology through various phases of commercial design. Finally, after multiple attempts, the industry gave up and the acid dew point meter manufacturer discontinued their product.
In 2016, the industry discovered that there was a second manufacturer of acid dew point technology who had designed a robust system for permanent installation in traditional combustion applications. Breen, part of Mississippi Lime Company, was approached for a solution.
The criteria given were “simple”—survive in a standard acid plant process gas condition, without maintenance or failures for a year, and the industry would regard the product suitable for use in their applications. Responding to the request from the industry, Breen and the sulfuric acid industry collaborated to develop a commercially available permanently installed sulfuric “acid dew point” monitor.
the problem
The gas laden with SO3 in the process is kept moisture free and the only time moisture gets introduced in the gas is when there is a process upset.
Moisture in the process gas combines with the SO3 which will condense on the process equipment surfaces, and is generally indicative of one of the following conditions, among others: • Drying tower malfunction • Contamination in sulfur feed • Waste heat boiler tube leaks • Economizer tube leaks • Superheater tube leaks • Sulfur gun steam jacket leaks
The presence of moisture, and therefore weak acid vapor, in the gas stream is detrimental to equipment health and can cause extreme corrosion. This is a highly undesirable condition and can be potentially hazardous.
A secondary impact of moisture in the process gas can be the formation of hydrogen gas, which can create an explosion hazard [1]. • SO3+H2O H2SO4 • Fe+H2SO4 FeSO4+H2
The H2 formed in the previous equations can create an explosion hazard in the presence of O2 and an ignition source.
the solution
Since the industry had coined the term “acid dew point” monitor for a leak detection instrument, Breen attempted a probe with the same design criteria as the prior attempt. In short, the continuous measurement of acid dew point with the Breen probe had similar short term operating life and considerable maintenance requirements that made the use of traditional continuous acid dew point monitoring a failure in the first three months of development.
After discussion with industry experts, Breen determined that to keep the sensor free of process condensables for the long term and provide moisture leak detection, the probe would have to operate “above dew point cycle.” The above dew point cycle would allow the probe to operate in the duct at a temperature higher than the process gas dew point, but low enough to detect an increase, or step change, in process gas dew point. The commercial design for the Breen-SA Probe can be seen in Fig. 1.
Fig. 1: Breen-Sa probe for sulfuric acid manufacturing plants.
Moisture leak detection commercial design
In the Fall of 2018, Breen installed the commercial design into a sulfuric acid plant in California (Fig. 2).
The probe system was allowed to run at the above dew
point mode, with weekly “Check Cycle” cooling the sensor to the process gas dew point. The probe cycle and check cycles are shown in Fig. 3.
On January 23, 2019, the plant performed a test to verify that the system would indeed detect a moisture leak. At approximately 10:45 (Fig. 4) we can see a probe response when a pressure point line was cleared out with instrument air. A compressor was then hooked up to the line to pump ambient air into the duct; no response was seen, and it was assumed that the air pressure was not powerful enough to push sufficient air into the duct.
Subsequently, the process engineer put water into the pressure point line and used instrument air to push that water into the duct. The amount of water added was approximately a gallon. At 13:15 we can see the probe immediately responded to the event. It was concluded, with a fairly strong certainty, that the probe is very responsive to even small amounts of moisture.
There were also other minor responses in the previous weeks which were believed to have been caused when other pressure point lines were cleaned out.
Fig. 2: Breen Sa probe installation at J.R. Simplot Lathrop plant. Fig. 3: Breen-Sa probe normal cycle and check cycle.

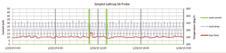
Fig. 4: Leak detection simulation.
further evidence of response to moisture ingress and leaks
In July 2019, a second and third system were installed in another acid plant in the Western United States. One SA-Probe was installed at the waste heat boiler outlet and one probe at the final economizer exit (Fig. 5).
During start-up operations, this plant experienced a small leak. In Fig. 6, we can see that the Breen-SA Probe detected the leak when it was still very small at about 05:00 on June 27th. The first plant DCS indication that there was an issue was much later, at about 13:30 on the 27th, when the dilution water flow starts to drop indicating the leak is large enough that less water is needed to maintain the acid concentration balance in the plant.
Clearly, the probe provided almost eight hours advance notice compared to the traditional method of leak detection at the plant.
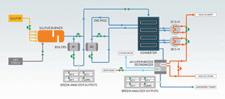
Fig. 5: Breen-Sa probe installation points.
Feature
Continued from page 28
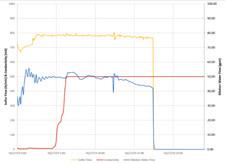
Fig. 6: Leak detection from Breen-Sa probe vs. dilution water flow.
advanced detection of “undetectable” leaks
In our previous Sulfuric Acid Today editorials, one can view the leak detection capabilities of the system. The early detection of tube leaks was well documented and confirmed by site operations. The same plant referenced earlier had run leak free for almost a year, when, subsequently in June 2020, the Breen SA-Probe system indicated a high process dew point at the waste heat boiler outlet and the economizer outlet systems beginning on June 16th. Multiple dew point measurements were taken to verify the higher dew points. (See Fig. 7, June 14-June 30)
As Fig. 7 shows, from June 16th through July 14th, the dew point temperatures progressed upwards over time.
Finally, around July 16th, the evaporation temperature of the condensate rose above the process gas temperatures and the condensate could not be evaporated from the sensors (Fig. 8).
Having little experience with the Breen technology, the plant hesitated to bring the unit offline until the following traditional methods indicated a leak: 1 Increase in economizer temperature. 2 Condensate in the economizer drains. 3 Indication from the dilution water flow.
Root cause analysis showed that there was a very small leak in the waste heat boiler shell close to the tube sheet/shell weld. This small leak was most likely the source of the original moisture ingress and all indications show that the SA-Probe responded to the leak as expected. The leak then propagated into the tube sheet, causing the further rise in dew points and conductivity and ultimately (30 days later) condensate was detected in the economizer drain.
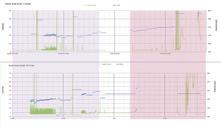
Fig. 7: progressive increase in dew point. Fig. 9: economizer temperature and dilution water flow.
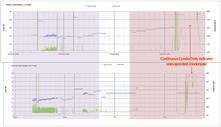
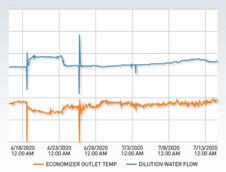
the latest data available test results
From May-July, 2021, a new customer had been running their system continuously, first measuring dew point weekly and subsequently shifting to daily measurements, with no sign of probe fouling (Fig. 10).
Subsequently this same plant performed a moisture detection test with successful results (Fig. 11).
Quoting the customer: “By injecting some small volumes of water into the duct upstream, the probe responded with a spike in conductivity, whereas none of our existing methods picked up such a small ‘slug’ of moisture. This was a great achievement in validating early detection in our plant with the Breen probe, so our next steps would be to look at making the probe a permanent install and integration to our DCS.”
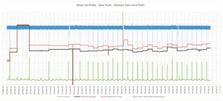
Fig. 10: Weekly and daily dew point trends.

summary
To further support the commercialization of the Breen SA-Probe, the measurement philosophy has been proven effective to detect both large and small moisture leaks, consistently responding to moisture ingress into the process in real-time and demonstrably quicker than traditional methods.
The dew point measurement provides solid trending of the process gas dew point over time as well as in situ verification of sensor function through the automatic and periodic system “check cycle” (dew point measurement).
As of the date of this publication, the Breen SA-Probe, “acid dew point” monitor, has logged over 100,000 hours of operation, with zero failures of the measurement system. Equally important, there has been zero maintenance hours on any permanently installed system, outside of probe cleaning and re-installation during a scheduled production train turnaround.
Breen attributes this success to the cooperation of the engineers and staff at our various commercial beta sites and the industry acceptance of the “above dew point” measurement logic, which provides for continuous detection of moisture ingress, and periodic measurement of process gas dew point measurement.
For more information, visit www.breenes.com. q
footnotes
[1] Information developed and presented by the Hydrogen Safety Workgroup.
[2] “The Latest in Sulfuric Acid Plant Process Gas Dew Point/Moisture Leak Detection,” Sulfuric Acid Today, Fall/ Winter 2020, Vol. 27, p. 30-32.
references
Daniel T. Menniti, 2020 “Detecting Real-Time Moisture Leaks in Acid Plant Process Gas,” Sulfuric Acid Today, 32-33, Spring/Summer 2020, Vol. 26 No. 1.
Daniel T. Menniti, 2019 “Detecting Moisture Leaks,” Hydrocarbon Engineering, 65-67, January, 2020.
Daniel T. Menniti, 2019 “The Real-Time Measurement of Sulfur Bearing Vaporous Compounds (SO3, Sulfuric Acid, Ammonium Bisulfate) and its Application for Use for Process and Environmental Control,” World Pollution Control Association, 1-2, Summer 2019.
Daniel T. Menniti, 2019 “Process Gas Dew Point/Moisture Leak Detection Measurement System,” Sulfuric Acid Today, 28-29, Fall/Winter, 2019.