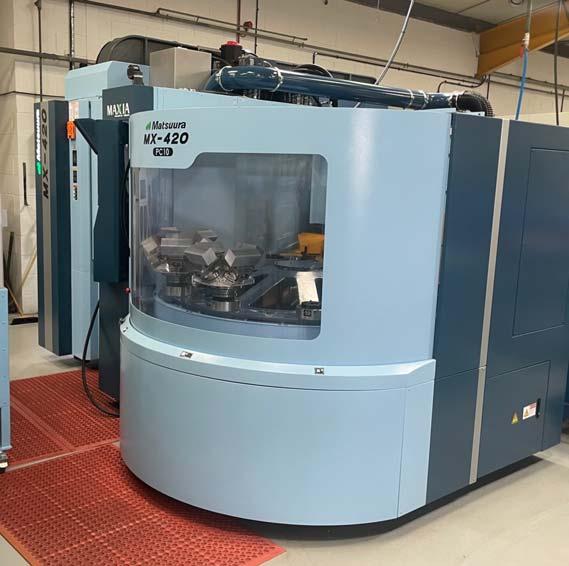
2 minute read
LMS adds 5-axis machining
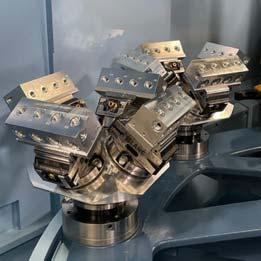
LMS has invested in a new five-axis machining centre that is giving high quality and improved service at a competitive price on work that has been reshored from Europe.
Advertisement
The Matsuura MX-420 PC10 machining centre is a full five-axis machine with a 10-pallet carousel, 90 tools and Renishaw probing. It joins a Matsuura H Plus-405 horizontal machining centre with a 6-pallet carousel, 240 tools, B axis, rotary table and Renishaw probing.
The new machine is currently set up to produce aluminium manifold components that had previously been made overseas in Europe. They had very long lead times and the customer was getting let down all the time by the suppler.
Roger Street, partner in LMS, said: “We are now running the manifolds on four of the pallets with four fixtures on each pallet –so we are running 16 at a time which gives us a five-hour run. The customer benefits from local supply, high quality, quick turnaround and components that are cost competitive with an overseas supplier.
“This new work was the prompt for us to invest in 5-axis machining as we suffer from the same problem as everyone else – we can’t get the people to run the machines, so we have to find the machines that will do more for us with fewer people. We needed something we could set up and let it run while the operator does something else.”
The new machining centre can accommodate parts up to 420mm diameter and 300mm high on each pallet. Up to 90 KG per pallet. It has significantly reduced the number of operations, part handling and setups. A single clamping ensures better control of tolerances between the faces and less chance for human error.
Roger said: “These parts are aluminium, but we machine a wide range of materials. We work across a wide range of sectors with some of the main ones being hydraulics, pneumatics and aerospace. We also do a lot in after-market motor cycle parts”.
He says that LMS has a good long-term relationship with Matsuura. “They are a great company to deal with and have always given us really good backup, which is important for our customers as they know that they can rely on us to deliver.”
As well as the machining centres, LMS also has two Muratec lathes supplied by Matsuura – both set up for automatic operation. These are an MT200 multi-tasking machine equipped with magazine bar feed, 80mm bar capacity, also with gantry loader for billet work and an MT100 Multi-tasking machine equipped with magazine bar feed, 51mm bar capacity.
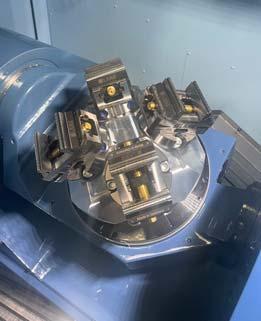
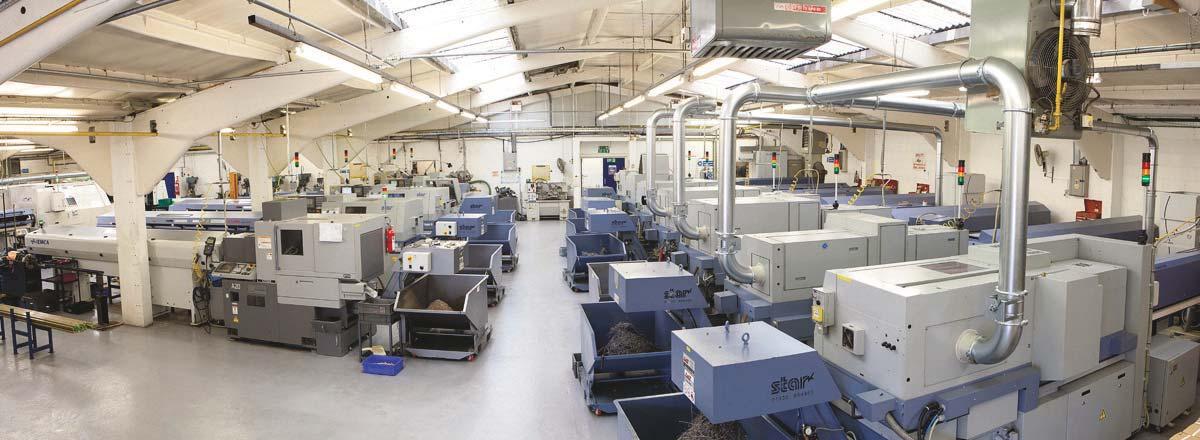
LMS also have a range of sliding and fixed head lathes.
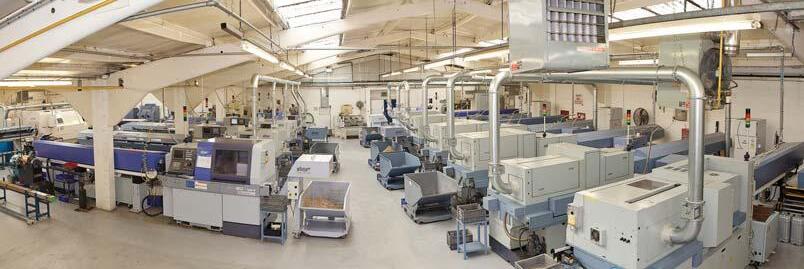
“It is all about productivity, all about taking out operations and dealing with the difficulty of finding skilled staff. We are doing more with fewer people.”
LMS is now celebrating 40 years in business, having been set up by Roger in 1973. Now his son Scott is also a partner in the business, ensuring continuity for the future.
8 lmsprecision.co.uk
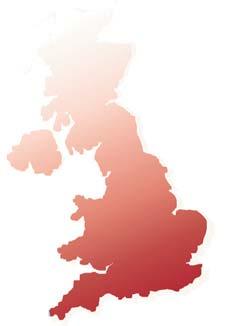
Birmingham toolmaker
Tooling 2000 has invested over £1.8m to develop a subcontract machining services and diversify its business.
Since 1996 the company has focused mainly on the design, production and try-out of tools for the automotive industry, notably for Jaguar Land Rover, Nissan and Rolls-Royce / Bentley.
With a view to strengthening its position in the industry and also to break into providing subcontract machining services to other sectors such as power generation, especially renewable energy, the company has invested £1.8 million in the last two years in new plant and hiring extra people.
A significant proportion of the spend has gone on acquiring new machine tools from Hurco including a TM12i CNC lathe with a 12-inch chuck and the toolmaker's first two 5-axis machining centres, a VMX60SRTi and aVMX42SRTi.
The SRTi machines have a torque motor-driven, swivelling B-axis spindle head and 600 mm diameter C-axis set flush into a fixed machine table create a compact, high-capacity platform that can be used as a largecapacity 3/4-axis machine whenever the need arises.
Tooling 2000's manufacturing director Brian Abbott said, "In recent years, there has been a growing demand from customers for the supply of more complex components that require 5-axis machines to produce them cost effectively.”