
3 minute read
Automated plastic inspection
delivery systems, and packaging such as contact lens blisters, for the medical, pharmaceutical and nutraceutical industries. The injection moulding machines are mainly housed in one Class 7 and two Class 8 clean rooms. Medical devices are increasing as a proportion of turnover as well as in variety and production volume, climbing over the past decade from 30 to 50% of throughput and still rising. Another trend is towards ever tighter drawing tolerances on newly designed products and more stringent GD&T (geometric dimensioning and tolerancing) requirements.
A rigorous validation process underpins the manufacture of all products at the Christchurch facility. Typically at the outset of a new production run, 30 shots containing, say, 15 components each will be run off and checked, with customers requesting a process capability of at least Cpk 1.33 and often 1.67 or 2 (six sigma). Tolerances are generally fairly open on plastic items, normally in the range 50 to 100 microns, but any inaccuracy of measurement is undesirable, as it would consume part of the tolerance band. Even more important for validation is a high level of repeatability.
Advertisement
Alltrista also wanted better data on features such as the flatness of sealing faces, freeform profiles and chamfers. The use of a Renishaw scanning probe has resulted in an order of magnitude more information to feed back to the production department for fine-tuning toolmaking and manufacturing. It also provides a much richer report for customers to understand in more detail the manufacturing that is being carried out on their behalf.
8 alltrista.com
Technical injection moulding firm Broanmain Plastics has worked with fire safety specialist Fireco to develop and manufacture a new magnetic door release system.
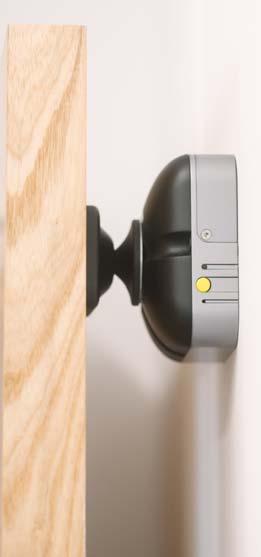
Designed to hold fire doors open to improve access and building ventilation, yet close automatically when a fire or intruder alarm is activated, the radio-controlled DorMag Pro is a sleek, unobtrusive device that is located behind the door rather than in front of it.
The concept has swiftly moved from 3D printed prototypes to a milled CNC tool, to the design and manufacturing of seven component tools with the assistance of Broanmain engineering and processing experts Kamil Stec and Thomas Catinat.
The DorMag Pro is now gearing up to roll off production lines at Dorking-based Broanmain Plastics.
Cost and scalability were major considerations for Fireco. Injection moulding the seven components that make up the DorMag Pro housing was deemed the most viable way to manufacture the volumes that Fireco expects.
Fireco Engineer Matt Ball said: “The market potential for this product range is huge, especially when combined with another acoustically rather than radio activated fire alarm innovation we are looking to release around the same time.”
“Injection moulding in these volumes is far more cost efficient that 3D printing and CNC milling.
It also gives us the repeatability and tight tolerances required for a compliant fire product, combined with the premium brand finish,” he added.
All of the unit’s seven components are moulded to on two-cavity mould tools using a standard ABS material. Rigid, versatile, and high strength, the lid and base are the only component modified to ABS PC to withstand the BS EN 1155 durability test cycles and the impact of the fire door being smacked back into the unit.
As well as mass-moulding the seven components, Broanmain will undertake some of the specialist finishing tasks, including heat staking a metal clip onto the battery carrier and overseeing the paint finish. 8 broanmainplastics.co.uk
Funding support has enabled a Rugby laser and waterjet cutting business to expand its premises and invest in a robot welding machine.
Precision Laser Processing (PLP), which is based at the Butlers Leap Industrial Estate in Rugby, specialises in flatbed cutting, five-axis laser cutting and water jet cutting as well as providing full fabrication services.
Its customers in the aerospace, security, automotive, medical, and power generation sectors are based throughout the UK.
The company, which is part of the Sirius A Corporation, was quickly running out of space at its 12,000 sq ft premises after winning new work in the green energy and electric vehicle sectors and wanted to re-organise its factory and office space.
The 30-year-old business contacted Coventry and Warwickshire Growth Hub Account Manager Adam Plumb to find out if there were any grants available to help them create a mezzanine.
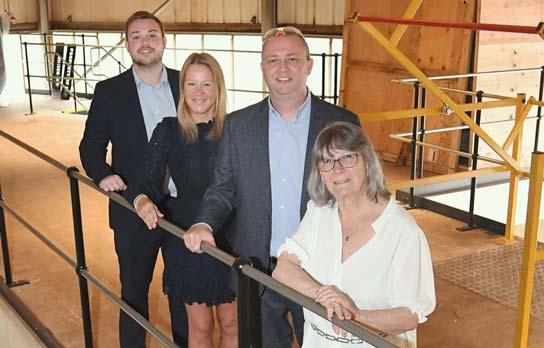
He put them in touch with Rugby Borough Council who assisted with a £49,000 grant from the Government’s Additional Restrictions Grant along with the Coventry and Warwickshire Business Support Programme which was part funded through the European Regional Development Fund (ERDF) who provided two grants totalling £34,323.
This financial support led to PLP creating a 2,525 sq ft