
12 minute read
REPL Group
from SPN Nov 2021
by spnews.com
REPL Group The roadmap towards achieving net zero
Top retail technology and sustainability expert, Graeme Hamlet gave SPN an exclusive interview. This shines new light on the awareness of sustainability within our industry and offers some new perspectives on how to optimise the roadmap towards achieving net zero. Here we publish part one.
Advertisement
How ‘sustainability-aware’ would you say your company is and what recent measures have you taken to improve your overall contribution to the circular economy?
“REPL has been sustainable for many years, but until recently did not badge our efforts as such. There are gaps, but we have used the 5 capitals (social, financial, natural, human and manufactured) to frame how we are sustainable, this helped us understand and increase awareness of what sustainability is.
Whilst we recycle as much as possible, we have reduced paper usage and also use cloud-technology and online collaboration tools. Today, business travel is our largest Co2 emitter. The pandemic proved that we can be more successful with remote working, and continue to implement the right balance between office and remote working to capitalise on lower travel emissions, whilst maintaining engagement and team wellbeing.”
In relation to sustainability, what would you say have been your most important milestones?
Every time we improve our GPTW ranking and see our end of year results – these are a fantastic testament to the team’s management of financial, human and social capital. From an environmental capital (and personal perspective) I think the biggest milestones have been gaining board support for sustainable change at REPL, passing the CISL sustainability management course and “seeing the light”. As well as witnessing the engagement and interest in the subject grow enormously, and most recently the incredible support from the team to invest in our ideas for products and services in this space.
In your opinion what have been the most significant developments in terms of recycling and bio-degradable packaging?
The sheer volume of media coverage about the impact of waste and packaging on the planet and population has increased the focus on the need for change and is driving innovation at a terrific rate.
“The use of data science in retail has dramatically increased transparency. The most significant of these is being in supply chain operations. Data science is key to understanding where and how raw materials are extracted, how products are made, used and what end-of-life looks like as well as exposing the carbon emissions and physical waste associated with any supply chain. Businesses can use this data to identify focus areas for improvement, such as reduced packaging, alternate materials and where a circular economy might be possible”.
Follow up on Graeme Hamlet’s revealing observations in Part 2, to be published in January 2022
KHS more juicy sustainability
Partners KHS and Ecks-Granini are furthering their sustainability goals by launching fully recyclable rPET I litre hohes C Juice bottles. By doing so, the company is now using rPET throughout its extensive product portfolio.
Eckes-Granini is making its packaging portfolio ever more sustainable with the help of the KHS Group. Since earlier this year its one-litre hohes C juice bottle has consisted entirely of recycled plastic (rPET). In fact KHS are Europe’s Bottles & Shapes experts, who were responsible for optimisation of the new recyclable juice bottles. These latest containers will continue to be produced on the company’s tried-and-tested Inno PET FreshSafe block.
“Bearing in mind the EU’s plastic’s strategy and the increase in recyclate quotas that this prescribes, we’ve now decided to switch to using recycled PET only. We want to be a pioneer with regard to the circular economy and set a prime example for the beverage industry as a whole.” said Hermann Naumann, plant manager for Eckes-Granini in Bad Fallingbostel in Lower Saxony.
Europe’s leading producer of fruit juice beverages has pursued an ambitious sustainability strategy for many years as Naumann continued, “We aim to continue steadily reducing our carbon footprint in both our production and in our packaging. This means not only cutting down on the amount of material used but also closing the recycling loop.” Hermann Naumann
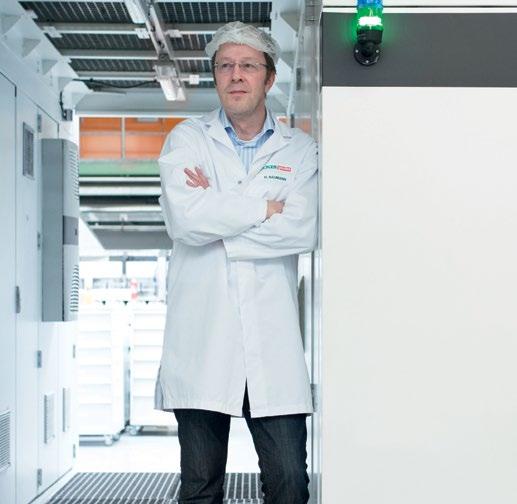
Plant manager for Eckes-Granini
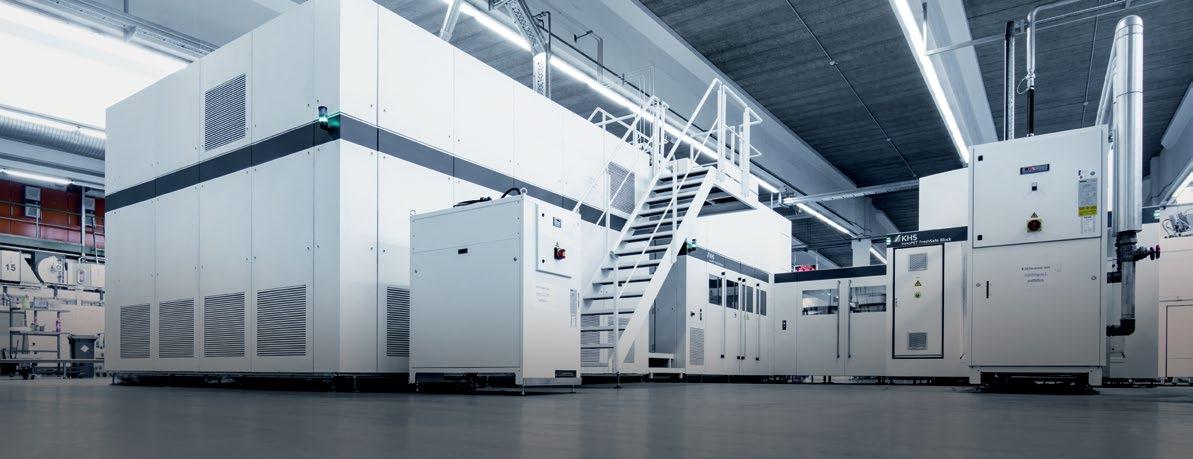
Eckes-Granini has made its packaging portfolio even more environmentally friendly with the help of the KHS Group. Since the middle of May its one-liter hohes C juice bottle has consisted entirely of recycled plastic (rPET). An InnoPET FreshSafe block from KHS has been in operation at Eckes-Granini since 2017
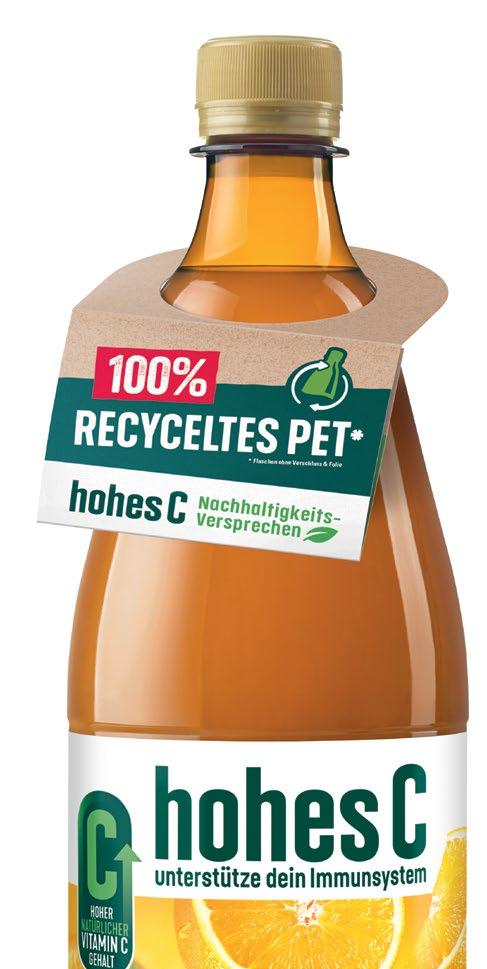
Significant savings
With its unique holistic Bottles & Shapes consultancy programme, customers can now benefit from over 40 years of expertise in container design and production. At KHS, beverage producers detail their preferences regarding the weight, shape or stability of the container and upon these specifications, the systems supplier assesses the feasibility of the design with the help of laboratory tests and simulation. In the case of Eckes-Granini the specifications were clear: switch to 100% rPET whilst maintaining the homogeneous quality of the container. According to EckesGranini, just the changeover of the one-liter hohes C bottle to rPET will save over 4,000 metric tons of new PET per annum. This in turn means that the bottler will cut its carbon emissions by about 8,000 tons a year.
Improved barrier properties
Eckes-Granini will continue to benefit from FreshSafe PET barrier protection following their conversion to 100% rPET. The company has relied on the environmentallyfriendly system from KHS since 2006. The oxygen barrier of chemically pure glass, and a wafer-thin coating on the inside of the PET bottle, not only effectively protects the juice from oxygen pickup, but is also fully recyclable. The coating can be easily washed off any Eckes-Granini bottles during the recycling process. The sustainable packaging alternative therefore permits pure-grade bottle-to-bottle recycling. By combining rPET and future-proof product protection Eckes-Granini and KHS are once again demonstrating their pioneering role for the circular economy.
Sealed Air Every little ‘closed-loop’ helps

Tesco ‘closes-the-loop’ on food packaging as the result of a unique trial that has involved the participation of an entire supply-chain. The four synergistic companies collaborated in close partnership to a achieve a global first: the recycling of soft plastic to a high, food-grade standard. Impossible until now, used, soft-packaging can simply be collected from Tesco customers and be re-used to produce highquality, food-grade packaging.
Sealed Air, Plastic Energy, SABIC and Bradburys Cheese, all partnered with Tesco to conduct this unique trial. It proved beyond doubt that soft plastic, which would normally go to waste, can now be recycled multiple times. The scientifically based, closed-loop trial resulted in the production of uniform, high quality, food-grade plastic packaging.
Traditionally, retailers have relied upon soft plastics to pack foods such as bread, pre-prepared salads, meat and cheese, as it helps them to maintain their freshness and prevent food waste. According to the 2019 UK Household Plastic Collection Survey, the UK uses almost 400,000 tonnes of soft plastics every year, but less than 21,000 tonnes of that is collected, and until now even that has been recycled into non-food-grade material. However, two years ago, Tesco stores installed ten recycling collection points for soft plastics, in order to discover new ways to resolve this problem, and in doing so created an entirely new, closed-loop system.
To prove that the closed-loop concept was both effective and practical, the soft plastic material collected from Tesco customers was sent to ‘Plastic Energy’ who converted the used packaging into oil through an advanced recycling process called pyrolysis. The recycled oil was then used by SABIC in their production process as an alternative to traditional fossil materials, for making new plastic pellets that are as safe and effective as virgin plastic.
The pellets were then utilised by Sealed Air who reformulated one of their existing plastic packaging designs to include this specially recycled, high-grade plastic. Rigorous testing was conducted to ensure that it met all the performance specifications of Tesco’s quality cheese supplier, Bradburys, for safe and effective use in their food packaging.
The new ‘closed-loop’ packaging material contains a minimum of 30% recycled material. The production of recycled soft plastic from food-grade soft plastic packaging has been an on-going challenge for the industry due to the many limitations of existing recycling techniques. This advanced pyrolysis recycling process easily and efficiently overcomes these traditional constraints. Steve Garland, Chief Innovation Officer at Sealed Air said: “This project demonstrates the results that come from taking a leadership position and being committed to investing in the type of innovation that ultimately eliminates plastic waste altogether. As we redesign our plastic packaging to be recyclable, we are working closely with key collaborators to recover the same materials before they become waste and keep them circulating throughout the value chain.”
Consistently, SPN recognises that Sealed Air is at the vanguard of global companies protecting and solving critical packaging challenges. Today the company’s portfolio of advanced packaging solutions includes such well-known brands as CRYOVAC® a brand for food packaging, SEALED AIR® a brand for protective packaging, the AUTOBAG® brand for automated systems and the famous BUBBLE WRAP® brand for diverse brand packaging. Collectively they contribute to a safer, more efficient food supply-chain that protects valuable and fragile goods being shipped around the world.
In 2019, Sealed Air generated $4.8 billion in sales and currently employs around 17,000 people, all of which are dedicated to serving customers in 124 countries worldwide. Today, Sealed Air is a leading global materials and solutions provider that creates packaging for food, consumer goods and medical/industrial supplies.
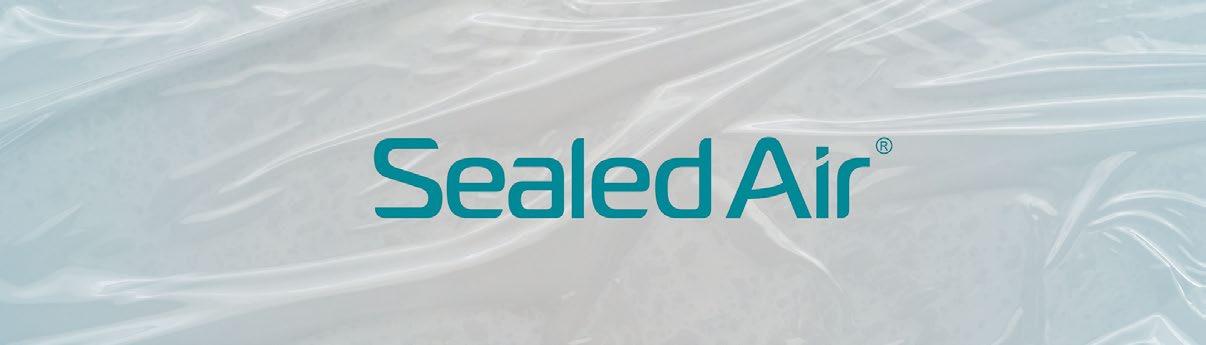
For further details of Sealed Air products visit: www.sealedair.com
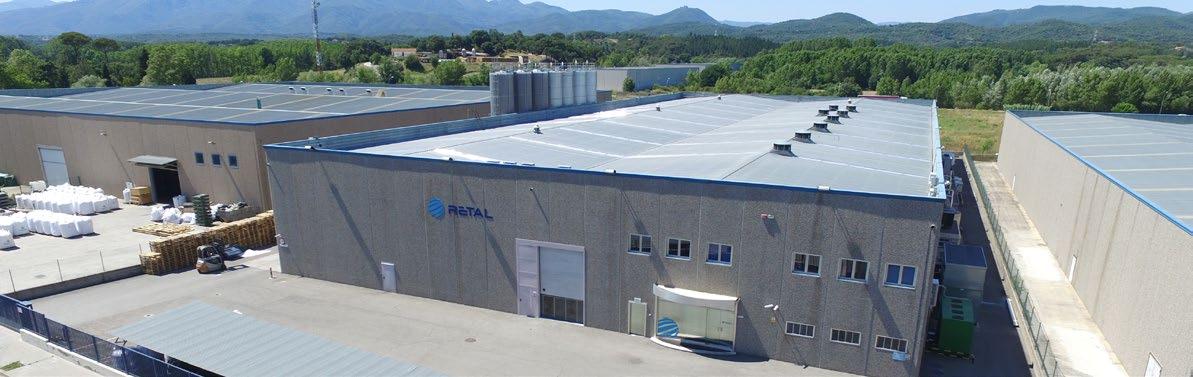
RETAL Iberia expands into North Africa
As a proudly global plastic packaging solutions provider, RETAL has an established presence with 19 production sites and customers in over 70 countries worldwide. With a strategic balance of local knowledge and global capabilities, RETAL is continually working with its FMCG customers to deliver preform, closure and film solutions
RETAL’s European heartland enjoys a range of opportunities to work with the majority of its 22 factories, with customers able to enjoy fast, reliable deliveries from facilities across Eastern, Central and Western Europe. RETAL Iberia, located close to Girona, is just 60 minutes from the port of Barcelona, which is the closest port to Morocco and much of North Africa. Having worked extensively with customers in Tunisia, the RETAL Iberia team is strategically developing its presence in North Africa in order to bring its deep understanding of the market needs for preforms.
Ester Masó Donadeu, general manager at RETAL Iberia, shares how she and her team have built strong relationships with customers in Tunisia. She says, “RETAL Iberia is very pleased to be working with customers in Tunisia for over eight years now; we’ve been able to develop our understanding of what preforms our customers in the region want, and how best to serve them. For example, many of our mineral water customers in Tunisia appreciate our 30/25 neck preforms, which are available quickly and in high volumes if needed, and we can also deliver the lighter weight 29/25, as well as our latest DIN preform which is ideal for cosmetic and personal care applications.” Masó continues to explain the RETAL Iberia’s excellent location allows its deliveries to reach Morocco, Tunisia and other parts of North Africa within just four days. She adds, “We are so close to the port that we can be very efficient with our preform deliveries to North Africa; no time is wasted. We keep a good stock of preforms and have a round-the-clock production that allows us to meet orders effectively. Shipping to Morocco can take just two days, with a little time either side for the necessary maritime transactions and logistics.”
The speed of the delivery is well supported by the expertise of the team at RETAL Iberia. Masó is joined by commercial manager Raquel Oller Bosch, with a full complement of experienced sales, procurement and logistics colleagues, bringing a multilingual service to customers across Spain, Portugal and North Africa.
Oller works closely with customers across the food and beverage industries, including local partners, co-packers, and global brands, with her knowledge of the RETAL portfolio well matched with her close understanding of what customers want.
Oller explains, “We have extensive knowledge of creating and manufacturing PET preforms that can include rPET, and we are always looking for ways to utilize our portfolio. We’re used to producing huge volumes for the very cost-conscious bottled water market, so we are able to pass on that advantage to customers in the hydro-alcoholic gel segment with our new DIN preforms which are available from 0.5l up to 1.5l in a range of neck finishes and weights. We can cope well with high volumes and our solutions are cost-effective.”
Experienced and sustainable
Production capabilities for these preforms are already established at a possible 13.6 million units per month, depending on size and order requirements. RETAL Iberia has invested in state-of-the-art equipment in order to manufacture at volume and speed, offering cost-conscious solutions to brand owners and blowers across Europe. The RETAL Iberia preform range can be offered as standard or customised, and with up to 100% rPET, with all the production facilities and equipment already up and running with experienced teams.
Masó concludes by sharing how RETAL Iberia’s friendly and experienced team is on-hand to service customers across Europe and North Africa, saying, “I am proud to say that our customers often comment on the positive experience they have working with our team; we are responsive, reliable and highly competent, with great experience of creating packaging solutions for our customers. As the market is evolving, we can offer a continuous service that values the changing needs of our customers. We have the support of a global group and the agility of a local partner.”
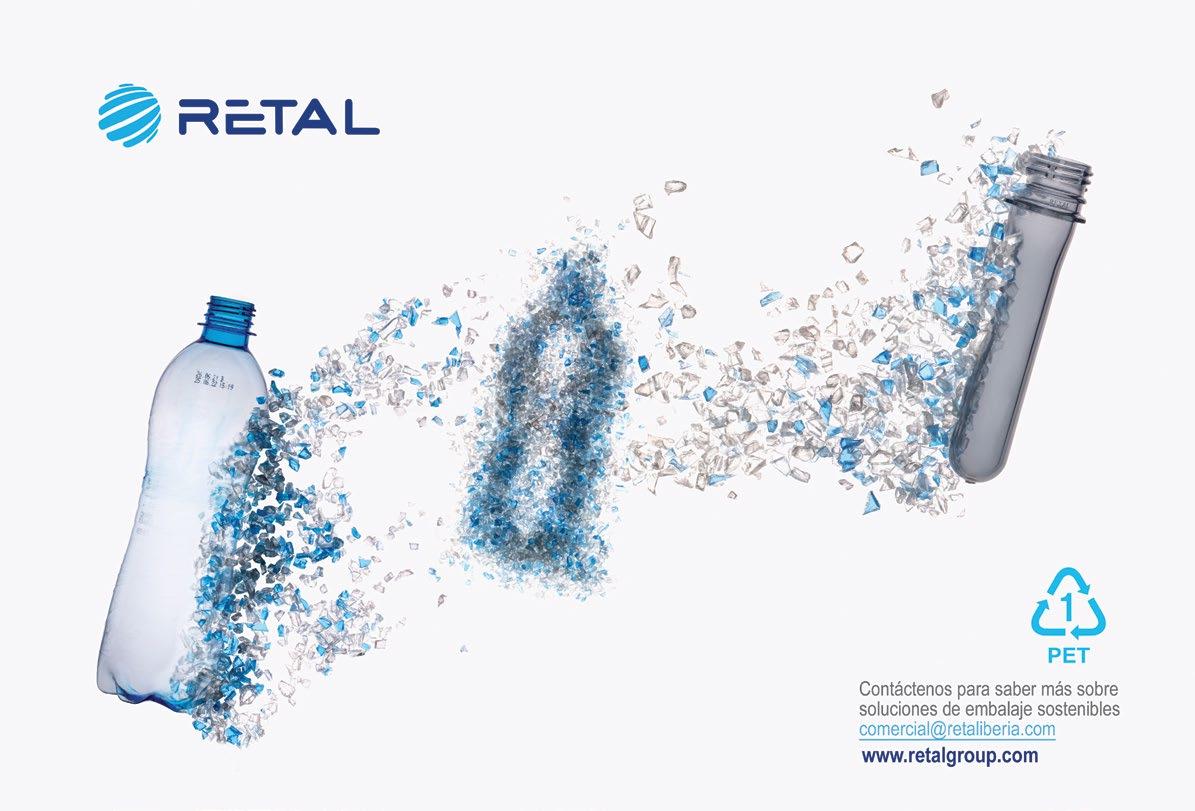