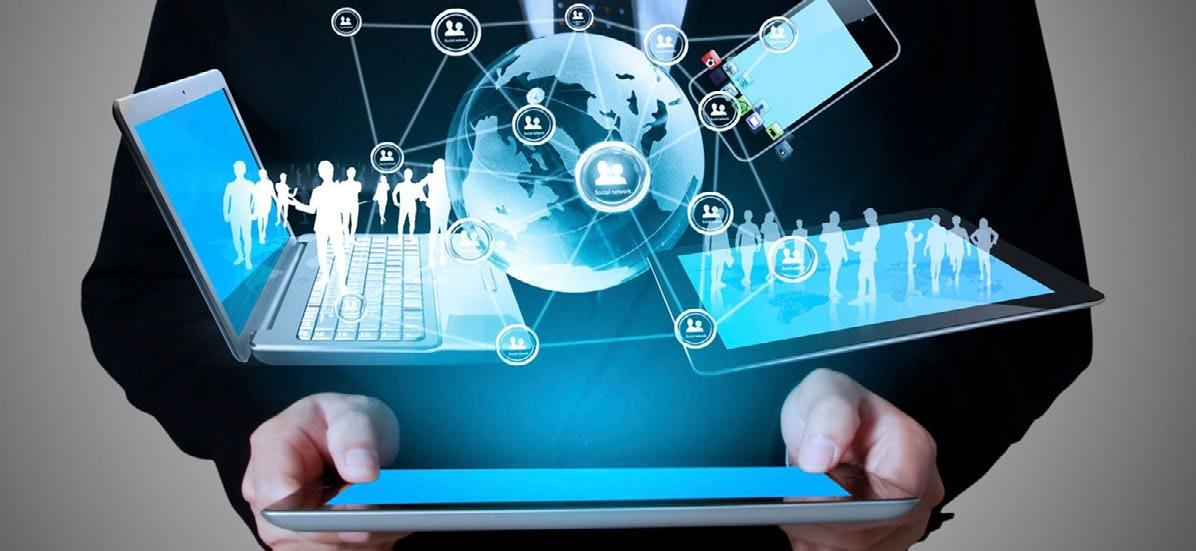
4 minute read
Smarter moves for SME’s 24
from SPN Nov 2021
by spnews.com
Industry 4.0 Smarter moves for SmE’s
Industry 4.0’s Digital Manufacturing concept offers huge potential, to company’s by improving productivity, shortening lead times, reducing working capital and improving cash flow. It can also be used to shorten the time for New Product Introduction, allow mass customisation of products, and improve the customer experience and aftermarket service of packaging businesses. Ingpro recently provided some interesting insights.
Advertisement
Many business owners and directors see INDUSTRY 4.0 as an opportunity only for large, global, corporations, but in fact even Small to Medium Sized Enterprises (SMEs) can also benefit from the current range of new technologies on offer, some of which can be cheaply and easily implemented. The UK government commissioned the Made Smarter review, which revealed the following information:
The work undertaken for the Made Smarter Review found that the positive impact of faster innovation and adoption of IDTs could be as much as £455 billion for UK manufacturing over the next decade, increasing manufacturing sector growth between 1.5 and 3 percent per annum, creating a conservative estimated net gain of 175,000 jobs throughout the economy and reducing CO2 emissions by 4.5 percent. Overall, from the data and evidence collated, we are confident that industrial productivity can be improved by more than 25 percent by 2025.
There is a lot of jargon and terminology that surrounds digital manufacturing: Internet of Things, 3D printing, Industry 4.0, digital pairing, Smart factories, augmented reality, virtual reality, big data, artificial intelligence and so on. However, we see the principle areas of consideration for SMEs as well as big corporations as being the need to adopt the following actions:
1. Automate processes (physical / data flow) to reduce waste 2. Connect devices to allow for improved visibility, improved scheduling, and faster throughput 3. Employ smart technologies to reduce costs, enhance product design and improve service 4. Collect data and analyse outcomes to improve; products, services, and operational performance that they may require
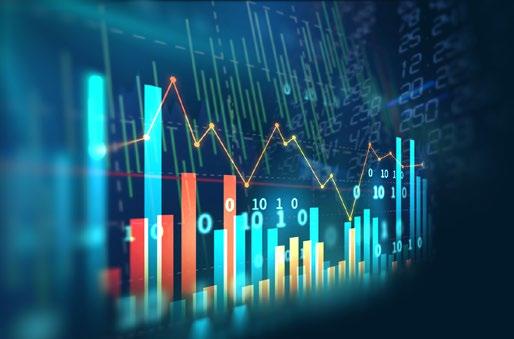
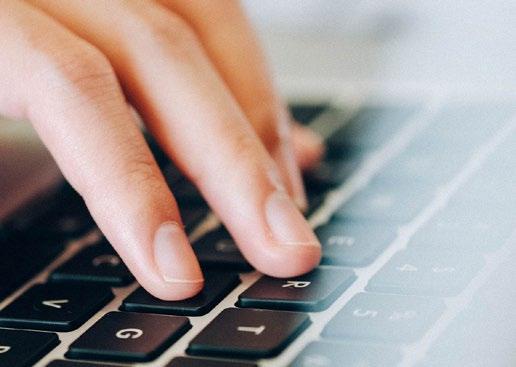
Defining the focus
The answer is to focus where you can achieve the biggest return on your investment. If you are new to the technologies there may be a good argument for starting with some simple things, that have little cost. The first step is to understand from your business what would help you the most. Would faster, better, product introduction make a significant improvement to your business? Or productivity and reduced lead time? Maybe better visibility and control of the supply chain? Then look at some simple steps. Consider using a simple diagnostic tool to evaluate your current status as well as your appetite, capacity and capability to adopt new digital manufacturing technologies. Some examples for manufacturing companies may include; having a view of Overall Equipment Effectiveness (OEE) on crucial production machines or predictive maintenance on a key piece of equipment.
Condition monitoring
If you are manufacturing a complete piece of critical equipment for a customer, then having condition monitoring embedded in the product may be a good place to start. If you have long supply chains, and high volumes of boughtin components, or complex sub-systems, you may well start with a simple method of having visibility of your supplier’s production and your parts. It is easy to post data onto a shared drive, such as Google or Microsoft OneDrive. Once data is there, from your supplier, or from your factory you can start monitoring and analysing. At first, just manually. If it is proving insightful or useful, you can then look at more sophisticated sensing and analytics.
Cost-effective option
Another inexpensive and easy option, is to look at data and information flows within the company. Can you eliminate the process of people e-mailing data? Instead, can it be posted on to a shared drive, where everyone who needs it can use it, and know they have the latest version. One of the overriding principles here, is to get data into one central repository, and in a common format. It can then be more easily analysed and accessed by other systems or people that require the data to make your business more efficient and transparent.
This article contributes to the packaging industry’s ability to become leaner and more efficient in its global quest to reach zero emissions and increase Circular Economy protocols. SPN hopes that SME’s and large corporations alike are able to take full advantage of the recommendations outlined here.