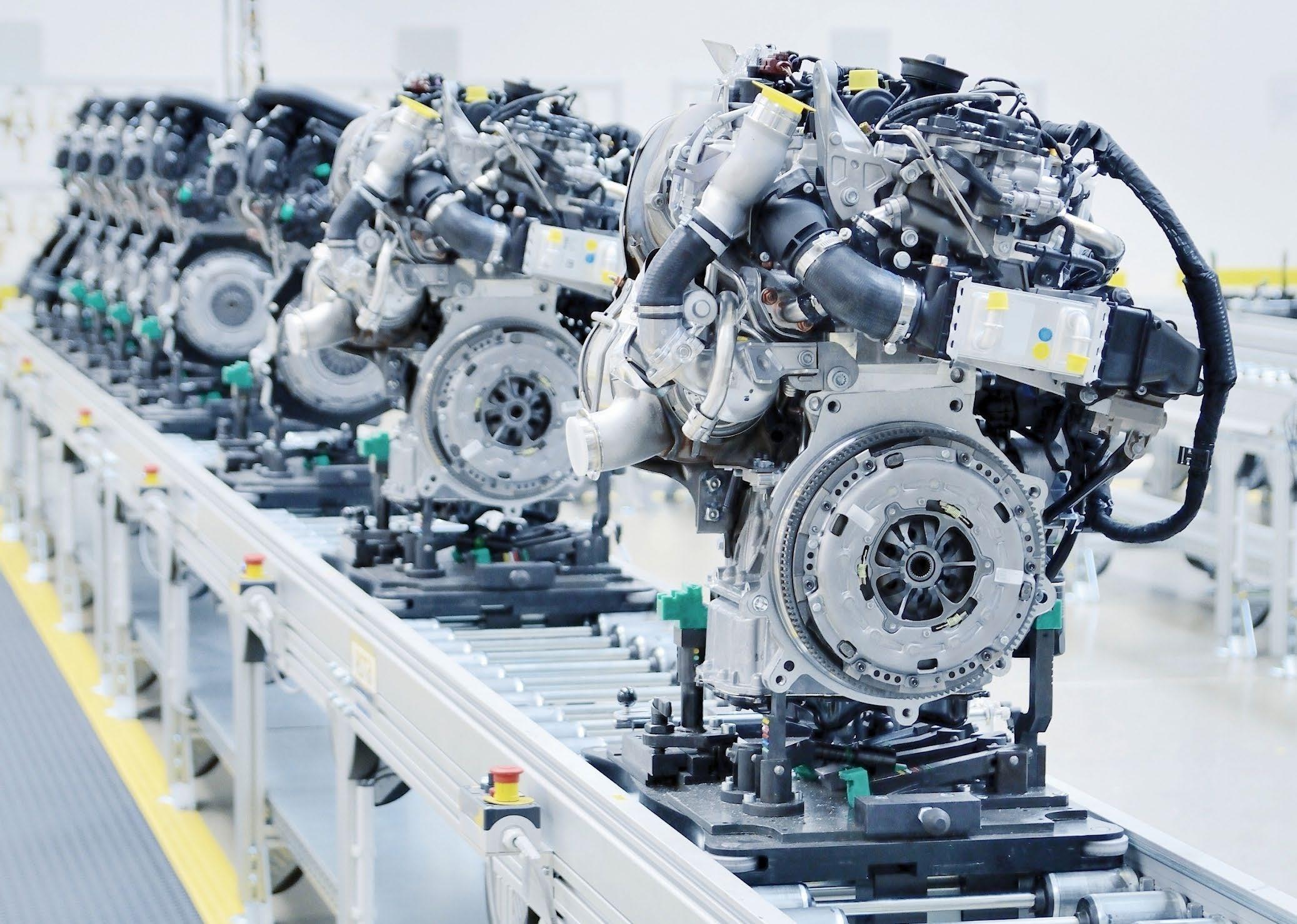
7 minute read
PROCESS
Choosing the “right” drill normally means a tool that perform for longer and produce better quality holes, particularly in tough materials.
The Right Way to Diversify
Manufacturers need the right tools and calculations to embrace new revenue streams
By: James Thorpe, Product Manager at Sandvik Coromant
There will be a “next normal” for manufacturers in the wake of COVID-19 — that’s according to a report published by McKinsey & Company. With losses of revenue in some sectors while others experience unexpected spikes in demand, the crisis is forcing manufacturers to diversify.
McKinsey & Company’s COVID-19: Briefing note report predicts manufacturers can expect “lasting shifts in customer markets” and that resilience will be needed if manufacturers are to “to navigate an economically and socially viable path.” In other words, they must diversify to survive.
Fortunately, today’s engineers are well-versed in mixed production, and most have evolved far beyond the low-tech stereotype of “Fred in his tool shed”. That said, diversifying production is not without it challenges.
Choosing the right tooling solution is essential for facilitating changes in production. This is particularly essential for engineers that work with tough materials like duplex stainless steels, Inconel or heat resistant super alloys (HRSAs) and companies that work with multi-materials.
Operations like this require optimized tools with carefully calculated cutting data. Drilling tools are a prime example. Drill

penetration rates can typically vary from 50 to 1000 millimeters-perminute. For these tools, precise calculations are vital for avoiding poor tool life and, at worst, causing premature tool failures. Put simply, if component material is changing, then drilling cutting data will have to change.
A Tool For All Materials
What do we mean when we say “the right” tool? With drills, this normally refers to tools that perform for longer and produce better quality holes, particularly in tough materials, like Inconel.
Sandvik Coromant has developed a range of CoroDrill® 860 solid carbide drills with optimized geometries suited for different applications that involve tough, difficult materials as well as malleable, abrasive, and soft materials typically found in the ISO-K and ISO-N families. The range includes the CoroDrill 860-GM with enhanced -GM geometry, optimized for multi-materials and applications.
Other tools in the range, like the CD860-PM, are optimised for drilling ISO-P steels. The CD860-SM is optimized for ISO-S materials for aerospace parts manufacturing. The CD860-GM is particularly useful for general engineering with mixed-materials, where productivity is important and engineers seek to diversify their production.
The CD860-GM’s innovative, polished flute design improves the evacuation of chips and yields greater hole quality. It is made from a unique fine-grained carbide substrate that increases hardness while maintaining toughness. In addition, the drill is tip-coated with a multi-layer physical vapor deposition (PVD) thin film coating, which is key to improving the drill’s productivity and tool life.
This was put to the test by an automotive engineering company in South Korea. The company used the CD860-GM to machine a transmission connector in ISO-P material, then compared its performance with a competitor’s drill on the same component. The cutting data used was a cutting speed (Vc) of 100 m/min, a cutting feed (Fn) of 0.21 mm/rev and a drilling depth of 10 mm. In the end, the customer reported a 1,150% increase in tool life with the CD860-GM. Going Online
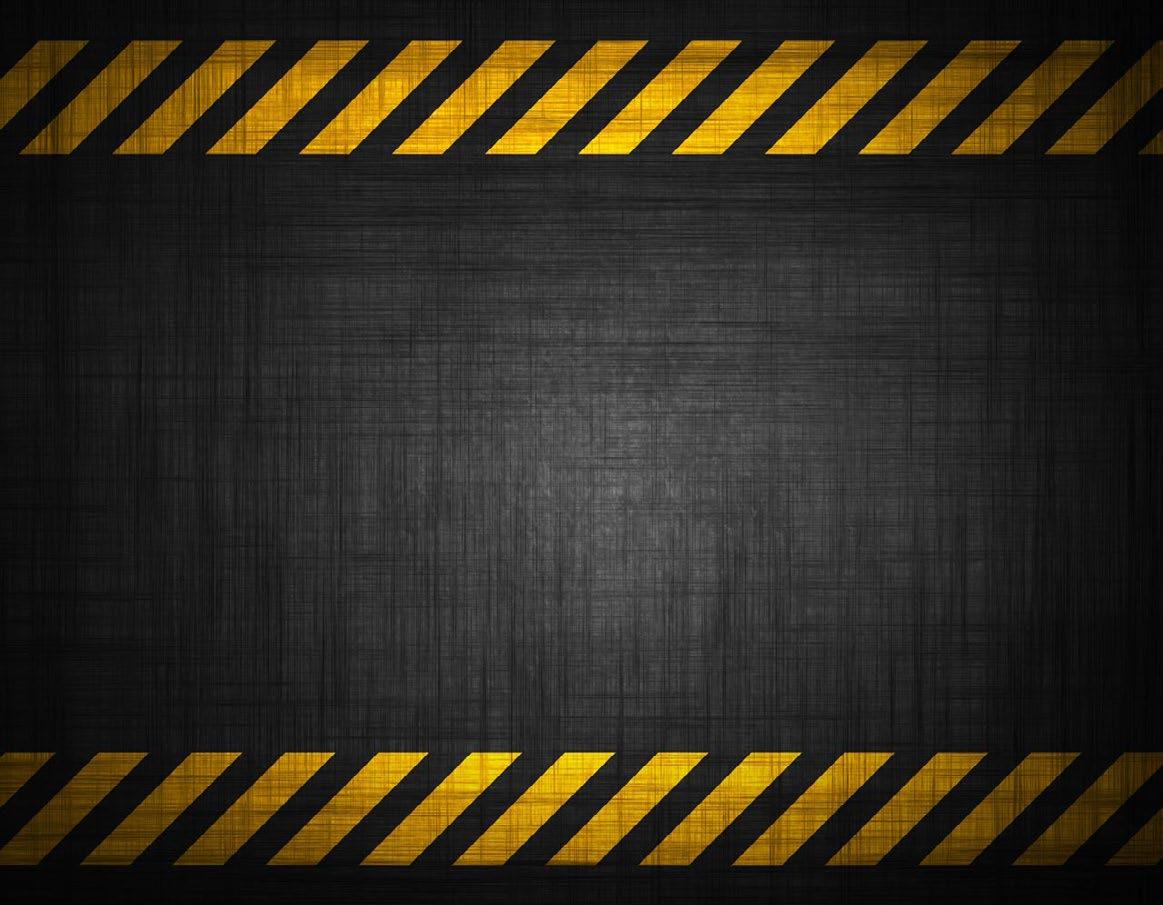
Productivity advantages, like those demonstrated in South Korea, could be crucial in helping manufacturers to diversify their production while remaining competitive. But, just as important are the cutting data calculations that must be optimized for any given application. However, determining this for a new product may require expert opinion.
With the travel restrictions of COVID-19, it’s unlikely that a tool specialist can come and visit your premises. So, how can today’s
WATCH VIDEO BELOW
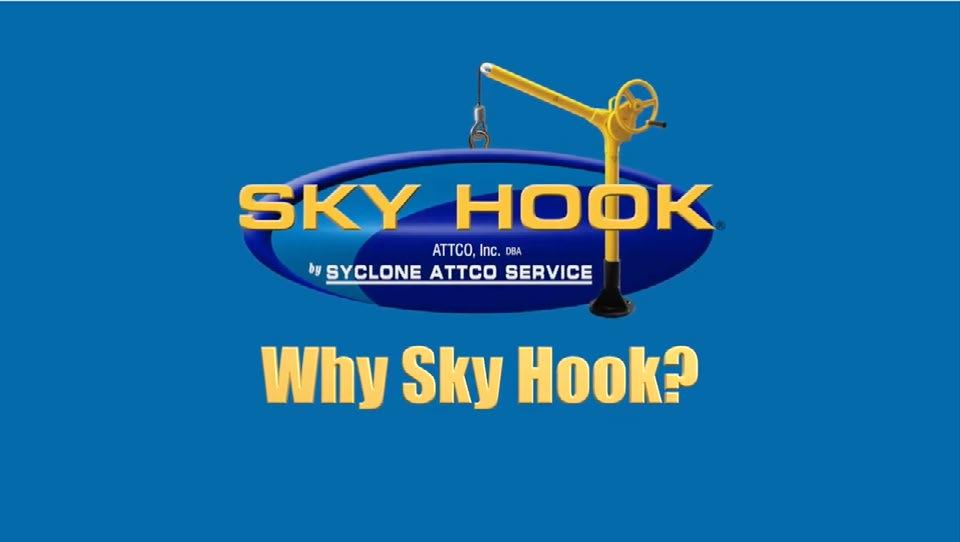
The Sky Hook is your personal safety lifting solution, preventing lifting injuries while saving you both time and money!
800-4-SKYHOOK
800-475-9466 • 208-365-5770 www.skyhookmfr.com

engineers not only calculate the best values, but also marry these to the best-recommended drill for the job? What’s more, how can this be done quickly and accurately to maintain production uptime against today’s diversification challenges?
The answer lies in online software. To choose the right tool and cutting data for new or existing applications, Sandvik Coromant have developed the CoroPlus® Tool Guide. The Tool Guide not only selects the correct tool, it provides cutting data and anticipated tool life for the specific application
The ability to make such important decisions, in relation to tooling and its calculations, is vital if manufacturers are to diversify and do so effectively. What’s more, the ability to access this guidance online could be crucial for engineers adapting to the circumstances of COVID-19.
Combined with optimised tools like the CoroDrill 860 range, the challenges of what McKinsey & Company calls the “next normal” could also be a time of opportunity for manufacturers and engineers.
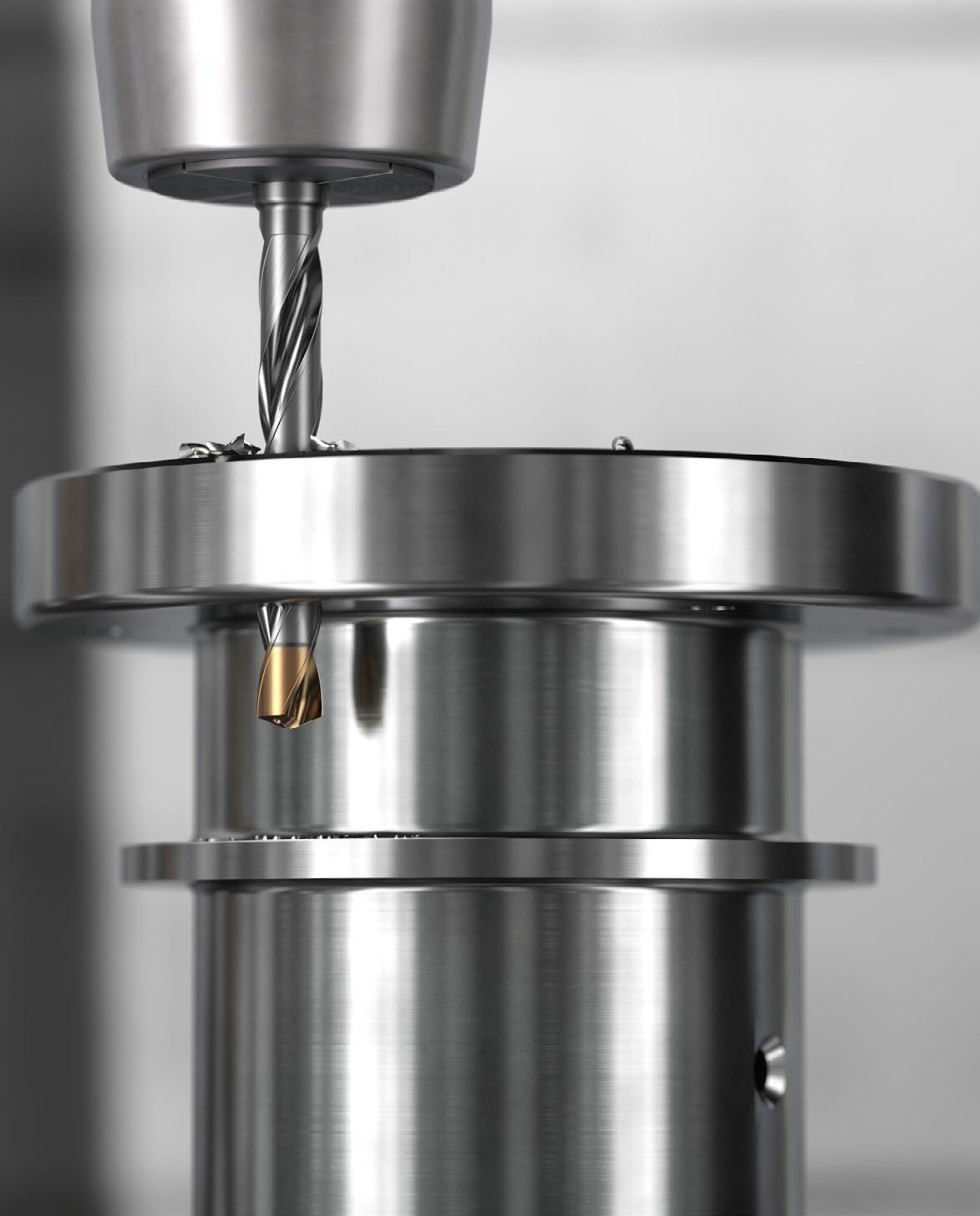
A New Solution For Machining Automation
Sandvik Coromant has announced the release of a machine integrated version of the award-winning Silent Tools™ Plus. The launch coincides with the release of CoroPlus® Connected, a solution to establish connectivity between machine tools and cutting tools. In combination, the products will enable conditional automation for internal boring applications, forming the basis of the future of automated machining.
CoroPlus® Connected is used alongside the existing Silent Tools™ Plus, a digitally connected damped boring bar from Sandvik Coromant. Having been awarded first place in the International Manufacturing Technology Show (IMTS) Production Innovation contest in 2018, Silent Tools™ Plus helps customers by providing visibility at the cutting zone in internal turning applications with long overhang.
Silent Tools™ Plus uses a connected turning adaptor and sensors to monitor load, vibration, deflection, surface finish, temperature and in-cut detection in turning applications. The product was brought to market to overcome the challenge of operator-blindness in internal turning. As an operator has no visuals of the process in question, it was previously extremely difficult to identify potential problems until turning was complete.
For industries boring large components, such as aerospace and oil and gas errors can result in significant costs, waste, downtime, and delays. By streaming data directly to a dashboard, Silent Tools™ Plus provides operators with ‘eyes’ at the cutting zone, creating an opportunity to identify problems, such as excessive deflection, vibration or set up problems, before issues escalate and manufacturers are forced to scrap expensive components.
The newly launched machine integrated version, with CoroPlus® Connected, allows the invaluable data generated at the cutting zone to result in automated cutting actions — removing the need for operators to monitor the machine dashboard for entire processes.
“Using the system, an operator simply needs to set the desired load, vibration and temperature limits, either through the software dashboard, or directly in the NC code,” explained Thomas A Nilsson, Product Manager at Sandvik Coromant. “From here, the conditional automation will protect the process, and reactions are initiated according to the set limits. This increases the process security, avoiding rework and scrap, while allowing the operator to focus on higher value work.”
“Launching a machine integrated version is an exciting development of Silent Tools™ Plus,” added Mattias Tjomsland, Software Product Manager. “The tool has long been used to improve decision making in internal turning processes, delivering information and security to otherwise process-blind operators. In combination with CoroPlus® Connected, Silent Tools™ Plus will provide monitoring that, for the first time, can trigger automated mitigating actions when problems and deviations are detected. This will be a game changer for improving component quality and overall efficiency.”
Sandvik Coromant’s CD860-GM solid carbide drill is useful for general engineering with mixedmaterials in diversified production setups.
ABOUT SANDVIK COROMANT
Part of global industrial engineering group Sandvik, Sandvik Coromant is at the forefront of manufacturing tools, machining solutions and knowledge that drive industry standards and innovations demanded by the metalworking industry now and into the next industrial era. Educational support, extensive R&D investment and strong customer partnerships ensure the development of machining technologies that change, lead and drive the future of manufacturing. Sandvik Coromant owns over 3100 patents worldwide, employs over 7,900 staff, and is represented in 150 countries.