
13 minute read
VERFAHRENSTECHNIK
from ChemieXtra 11/2020
by SIGWERB GmbH
Bedürfnisse der Life-Science-Branche in der Schweiz
Kalibrierung – im Wandel der Zeit
Advertisement
Ohne regelmässiges Kalibrieren stünden ganze Branchen still – allen voran die Life-Science-Industrie. Denn was nützt einem das neueste und genaueste Messgerät, wenn dessen Werte nicht der Realität entsprechen? Ralph Schöpflin und René Lippuner von der Endress+Hauser (Schweiz) AG erklären im Interview, welche Irrmeinungen sich hartnäckig halten, wo überraschende Wissenslücken verborgen liegen und worauf die Pharmaindustrie in punkto Kalibrierung besonders achten sollte.
Roger Bieri
«So viel wie nötig – so wenig wie möglich» lautet wohl die Devise bei jeder Kalibrierung. In der Life-Science-Industrie wird dies nicht anders sein. Worin unterscheiden sich aber die Bedürfnisse dieser Industrie besonders von anderen, wenn es um die Kalibrierung geht? René Lippuner: In der Life-Science-Industrie ist die Kalibrierung im Vergleich zu anderen Branchen am anspruchsvollsten. Dies hat im Wesentlichen mit den hohen Sicherheitsanforderungen an die Produkte zu tun. Auch in der Lebensmittelindustrie sind die Anforderungen ähnlich streng, aber dennoch nicht in diesem hohen Masse. Die hohen Ansprüche an die Produktesicherheit führen dazu, dass die kritischen Messstellen im Produktionsvorgang entsprechend evaluiert und definiert werden. Die Werte dieser kritischen Messstellen sind wichtig für die Produktionsqualität. Man muss nachweislich sicherstellen, dass der gemessene Wert der Realität entspricht. Um diese zu erreichen, werden die Messstellen in einem festgelegten Zeitintervall – viele tun dies einmal im Jahr – kalibriert. Mit einer Kalibrierung macht man im Endeffekt nichts anderes, als festzustellen, ob sich die Messwerte der Messstellen innerhalb der festgelegen maximalen Abweichung befinden. Dies erfolgt im Vergleich zu einem Bezugsnormal. Befinden sich die Werte nach einer Kalibrierung ausserhalb der definierten Toleranzen, könnte dies rückblickend negative Einflüsse auf die Produktion haben. Es stellt sich unmittelbar die Frage, was im Zeitraum zwischen der letzten «guten» Kalibrierung und der jetzt «schlechten» Kalibrierung geschehen ist. In einem solchen
Ralph Schöpflin ist Leiter der Marketingabteilung der Endress+Hauser (Schweiz) AG. Er war zuvor unter anderem auch im Produktionswerk der Firma tätig.
Fall werden Massnahmen notwendig. Mit einer Risikobetrachtung wird Zeitpunkt und Auswirkung der Toleranzverletzung ermittelt. Solche Aktionen können schnell sehr teuer werden, vor allem die Auswirkungen können erhebliche finanzielle Kosten und auch Image-Schäden verursachen, denken wir an eine mögliche Gefährdung der Patientensicherheit und die dadurch notwenigen Rückrufe von Produktionschargen. Abhilfe schaffen kürzere Kalibrierintervalle, je kürzer desto kleiner das Risiko, aber desto höher die Kosten für die Kalibrierung und die damit verbundenen Stillstandszeiten der Produktionsanlagen. Auch hier gilt es, Kosten und Risiken entsprechend abzuwägen und die richtige Balance zu finden.
Würden Sie die Aussage: «Die Life-Science-Industrie ist eher eine konservative Branche», so unterschreiben? Ralph Schöpflin: Ja. Ich denke, die LifeScience-Industrie ist schon sehr konservativ und zurückhaltend. Wobei dies in erster Näherung nicht etwas Schlechtes ist, sondern erst einmal so sein muss. «Konservativ» heisst ja frei übersetzt «bewahrend», also an Bewährtem festhaltend. Die Branche bedient sich hoher Sicherheitsstandards. Hinter diesen Standards stehen viele Audits und Inspektionen. Die Patientensicherheit steht immer im Vordergrund. Alles läuft streng nach Good Manufacturing Practice (GMP) oder nach Regeln, welche im Schweizer Heilmittelgesetz verankert sind. Die Sicherheit und die Risikominimierung stehen eindeutig im Vordergrund. Daher kann man schon sagen, dass die Branche konservativ ist.
Ist es denn bei einer Branche, die konservativ und bewahrend ist, nicht sehr schwierig, innovative Lösungen einzubringen? Schöpflin: Die Umsetzungsgeschwindigkeit ist einfach eine andere. Auf der Marketingseite ist es wichtig, dass man Innovationen immer wieder kommuniziert und
pusht, so dass sie schliesslich wahrgenommen werden. Es wird dann aber nicht gleich «Hurra geschrien» und alles über den Haufen geworfen. Ich mache ein Beispiel: Wir bieten die Möglichkeit an, den Kalibrierungsprozess über Algorithmen zu «optimieren». Das heisst, wir können sagen, ob eine Kalibrierung in den gewählten Abständen überhaupt notwendig ist oder ob öfter kalibriert werden sollte. Oder im Umkehrschluss: Reicht vielleicht auch der doppelte Zeitraum für eine Kalibrierung? Nur: In der Pharmaindustrie wird dies sehr schwierig, denn dort müssten sie einen validierten Prozess ändern, einen Prozess, der eine hohe Sicherheitsrelevanz mit sich bringt. Das heisst, man müsste verschiedenste Stellen involvieren, man müsste Bewilligungen einholen. Kurz gesagt, man müsste diesen validierten Prozess komplett anpassen. Das wird in der Pharmaindustrie sehr schwierig. In anderen Branchen ist das um einiges einfacher.
Endress+Hauser bietet umfangreiche Kalibriermanagement-Services an und unterstützt so die Branche vom kleinen bis zum grossen Ganzen iterativ. In welchem Bereich ist der Beratungsbedarf am stärksten? Lippuner: Kunden möchten oftmals mehr über Kalibrierzyklen und über die zu definierenden maximalen Messwertabweichungen wissen. Das heisst, sie möchten wissen, was die erlaubten maximalen Abweichungen eines jeden Messgerätes sind. Wichtig bei dieser Definition ist die Betrachtung des gesamten Messkreises. Es ist nicht nur das Messgerät, welches innerhalb eines Messkreises Abweichungen generiert. So haben auch die Installationen sowie die Steuerungskomponenten Einfluss auf die gesamte Messabweichung. Unnötig enge Vorgaben führen zu mehr Kalibrierungen, welche ausserhalb der gesetzten Grenzen sind, dies kann, wie bereits gesagt, zu hohen Kosten führen. Oftmals werden kundenseitig kleinstmögliche Toleranzen definiert, um eine vermeintlich hohe Genauigkeit zu erreichen. Aber eng gesetzte Vorgaben haben zunächst nichts mit Genauigkeit zu tun. Eigentlich sollten die Toleranzen so gross wie möglich – genau auf den jeweiligen Prozess abgestimmt – gewählt werden. Ein anderes zentrales Thema ist die Adaptierbarkeit der Messgeräte. Oft müssen die in den Anlagen eingebauten Geräte für eine Kalibrierung ausgebaut werden. Hier stellt sich die Frage: Wie kann ein Messgerät schnell und einfach ausgebaut werden, um Kosten für die Kalibriertätigkeit zu senken und vor allem auch, um die Stillstandszeiten der Anlagen zu verkürzen? Ich mache zwei Beispiele. Im ersten Beispiel geht es um ein Temperaturmessgerät. Wenn dieses so gestaltet ist, dass die Temperatursonde ausgebaut werden kann, ohne den Prozess zu öffnen, hat das entscheidende Vorteile. Wenn das Kabel des Sensors dann noch lang genug ist, um den Sensor problemlos in einen Temperaturofen zur Überprüfung einzuführen, erfolgt die Kalibrierung auch sehr schnell und effizient. Das pure Gegenteil wäre, zuerst die Rohre der Anlage zu entleeren, alles auszubauen und den elektrischen Anschluss zu trennen, bevor die eigentliche Kalibrierung erfolgen kann. Das zweite Beispiel betrifft den Durchfluss. Durchflussmessgeräte, die in den Rohrleitungen eingebaut sind, sollten für die Kalibrierung möglichst dort belassen werden. Das bedeutet, dass das Bezugsnormal (das Durchflussmessgerät, welches den Referenzmesswert darstellt) an den Prozess adaptiert werden muss. Dies bedeutet, dass das Bezugsnormal temporär in die Anlage integriert wird, so dass es denselben Volumenstrom messen kann wie das zu kalibrierende Messgerät. Wenn Anlagenbauer unter hohem Kostendruck stehen, fehlen oft geeignete Anschlüsse, die später in der Betriebsphase äusserst nützlich wären. Das sind Themen, die wir mit unseren Kunden angehen. Wie kann man beispielsweise eine bestehende Installation sauber adaptieren? Sind gewisse Umbaumassnahmen nötig? Solche Fragen sind wichtig, denn über die gesamte Betriebszeit einer Anlage lässt sich wiederum viel Geld sparen und Stillstandszeit minimieren. Schöpflin: Ich denke, man sollte Überlegungen zu Kalibrierung oder Kalibrierprozessen bereits während der Anlagenplanung miteinbeziehen. Wenn man diese Prozesse zu Beginn richtig einplant, spart man später viel Geld und Zeit bei der Kalibrierung. Hier kommen zum Beispiel auch Produktinnovationen zum Tragen. Wie kann man beispielsweise, wie vorhin schon angesprochen, eine Temperatursonde ausbauen, ohne den Prozess direkt zu beeinträchtigen? Dazu gibt es Innovationen mit geeigneten Anschlüssen. Das Thema greift also von Anfang an.
Dass man die Kalibrierungsprozesse nicht bereits zu Beginn in die Planung miteinbezieht, scheint auch aus einer gewissen Unwissenheit zu geschehen. Gibt es andere Wissenslücken, die immer wieder auftreten und unbedingt geschlossen werden sollten? Lippuner: Der Bedarf ist unterschiedlich, aber oft stellen wir Unsicherheiten bei der Gestaltung der Kalibrierprozesse selbst fest. Das Stichwort hier ist die Standard Operation Procedure (SOP) für Kalibrierungen. In diesen Dokumenten steht die definierte Vorgehensweise, wie eine Messstelle zu kalibrieren ist. Ferner befinden sich dort auch die Vorgaben, ab wann eine Messstelle justiert werden muss. Das heisst, dass bei einem Messwert, der ausserhalb einer definierten Grenztoleranz liegt, am Messgerät Einstellungen vorgenommen werden, so dass es wieder innerhalb der tolerierten Abweichung im Vergleich zum Bezugsnormal misst. Das sind alles Beschreibungen in den SOPs. Wünschen sich Firmen in diesem Bereich Unterstützung, bieten wir gerne unsere Erfahrung und Beratungsleistungen an. Auch die Dokumentation ist ein wichtiger Punkt. Das Resultat einer Kalibrierung ist ein Zertifikat, das den Nachweis gibt, ob die Messstelle in Ordnung ist. Einige Firmen haben IT-Systeme, womit die Kalibrierdokumentationen automatisiert im System abgearbeitet und gespeichert werden. Ist kein solches System vorhanden, können wir unsere Unterstützung anbieten, indem wir ein Dokumentationssystem anbieten, in welchem alle Zertifikate zusammengefasst werden, so dass diese immer griffbereit sind, Datensicherung inklusive. Schöpflin: Hier muss ich noch etwas Wichtiges erwähnen. Es ist immer wieder erstaunlich, wie viel Verwirrungen es aufgrund der Begrifflichkeiten gibt, obschon sie für den Fachmann eigentlich klar sind. Wenn wir von einer Kalibrierung sprechen, dann ist nur die Dokumentation der Abweichung vom Ist zum Soll gemeint. Wenn man am Gerät dann zusätzlich etwas an-
passt und korrigiert, dann ist das eine Justierung und gehört nicht zur Kalibrierung. Viele nehmen fälschlicherweise an, dass bei einer Kalibrierung auch das Gerät justiert wird.
Kommen wir nun zu einem ganz anderen Thema. Wie war für Sie die Arbeit zu Beginn der Corona-Pandemie? Welche Einflüsse hatte diese besondere Situation auf die Kalibrierdienstleistung und wird es noch neue Einflüsse geben? Lippuner: Zu Beginn gings uns wie allen anderen, wir wussten nicht, wie sich Corona auf unser Dienstleistungsgeschäft auswirken würde. Vielleicht noch eine kurze Randbemerkung: Der Service, den wir für unsere Kunden leisten, beinhaltet nebst Kalibrierung auch Wartungen, Inbetriebnahme und Reparaturen. Bei den Wartungen und Inbetriebnahmen wurden Termine des Öfteren kundenseitig verschoben. Anstatt eine Reparatur vor Ort durchführen zu lassen, wurden entweder neue Geräte gekauft oder die defekten in die Reparatur eingeschickt. Bei der Kalibrierung war alles ganz anders. Hier lief alles genau gleich wie bisher, denn kalibrieren lässt sich nicht so einfach verschieben. Auch können Kalibrierungen nicht vom Schreibtisch aus «remote» ausgeführt werden. Man muss physisch vor Ort sein. Gerade in dieser Branche müssen die definierten Kalibrierzyklen eingehalten werden, Abweichungen davon würden einen erheblichen Aufwand an zusätzlicher Dokumentation/Changemanagement bedeuten. Einzige Ausnahme: Ein Kunde wollte eine Kalibrierkampagne zeitlich dehnen, um das Kontaktrisiko zu minimieren. Die Kalibierkampagnen dauern bei diesem Kunden normalerweise zwei Wochen und werden von vier bis sechs Personen durchgeführt. Sie wurde dann auf Wunsch auf vier Wochen gestreckt und mit weniger Personal durchgeführt, damit das Kontaktrisiko gesenkt werden konnte. Schöpflin: Ein Trend wird sich sicherlich fortsetzen: der Wunsch nach der Lieferantenreduzierung bei den Kalibrierdienstleistern. Die Kunden bündeln die Dienstleistungen, was den Schulungs-, Administrations- und Qualifizierungsaufwand stark reduziert. Man kann sich so auch auf eine Firma mit Kompetenz fo-
René Lippuner arbeitet seit 25 Jahren für das Unternehmen. Er ist Serviceleiter der Endress+Hauser (Schweiz) AG.
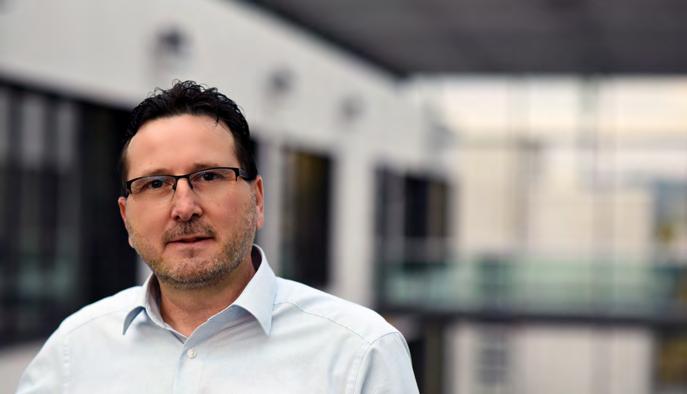
kussieren. Und gerade in der Corona-Zeit sind Reduzierung der Kontakthäufigkeit aber auch Optimierungen von Prozessen Themen, die wir in Zukunft noch stärker sehen werden. Auch denke ich, dass die Kalibriergüte mit der Kompetenz und den Erfahrungswerten der Fachleute steht und fällt. Ohne die entsprechende Erfahrung passieren sehr schnell Fehler. Ein Partner mit Erfahrung ist sehr wichtig.
Herr Lippuner, Sie haben ja bereits erwähnt, dass für die Kalibrierung das Gerät unter Umständen ausgebaut werden muss. Nun hat Endress+Hauser einen sich selbstkalibrierenden Temperaturfühler entwickelt. Zwischen diesen beiden Gegebenheiten bewegen sich Welten. Wie wird sich die Kalibrierung unter diesem Aspekt in Zukunft weiterentwickeln? Lippuner: Sie haben den Temperatursensor angesprochen, der sich selbst kalibrieren kann. Wir haben viele weitere Messgeräte mit integrierten Kontrollmechanismen, die sich selbst immer wieder überprüfen. Diese Überprüfungen können für Verifikationen herangezogen werden, also Plausibilitätsprüfung der ausgegebenen Messwerte. Das sind aber zwei unterschiedliche Themen. Beim angesprochenen Temperatursensor haben wir tatsächlich ein Bezugsnormal im Gerät integriert. Es wird also wirklich kalibriert. Bei der Verifikation ist dies nicht der Fall. Nach den aktuellen regulatorischen Vorgaben ist eine Kalibrierung verpflichtend. Eine Verifikation gilt nicht als solches. Verifikationen können aber ergänzend genutzt werden, um beispielsweise die Kalibierzyklen zu strecken. Grundsätzlich dürfen wir aber auf die kommenden Weiterentwicklungen moderner Messsysteme wie auch auf die Entwicklung der einschlägigen Regulatorien gespannt sein.
Und was denken Sie, Herr Schöpflin? Schöpflin: Dieser Temperatursensor ist eine Innovation. Wir sind die ersten auf dem Markt mit einem solchen Sensor. Daran wurde jahrzehntelang geforscht. Diese Technologie wird sich bestimmt auf der Ebene der Temperatur weiterentwickeln. Ich denke aber auch, dass der Trend weiter in Richtung Digitalisierung geht (z. B. die Digitalisierung von Protokollen). In diesem Zusammenhang ist sicherlich die Total Productive Maintenance ein wichtiges Stichwort. Die Selbstkalibrierung von Temperatur wird langfristig sehr wahrscheinlich einen entscheidenden Anteil am Kalibriervolumen in der pharmazeutischen Industrie erhalten. Das ist eine Entwicklung, die über eine sehr lange Zeit gelaufen ist, sehr viel Know-how erforderte und zu vielen Patenten geführt hat.
Herr Schöpflin und Herr Lippuner, vielen Dank für das Gespräch!
www.ch.endress.com/de/dienstleistungsportfolio
Die Künstliche Intelligenz unterstützt die chemische Produktion.

Störungen frühzeitig erkennen
Diagnose und Handlungsempfehlungen
Schon immer war die betriebssichere Pumpe, der zuverlässige Kompressor, die langfristig verfügbare Lüftungsanlage ein zentrales Auswahlkriterium der Betreiber. Werden die Maschinen bestimmungsgemäss eingesetzt, haben sie eine zu erwartende Lebensdauer von mehreren Jahren. Solche Maschinen fallen daher meist durch Störungen oder Abweichungen im Betrieb der Gesamtanlage aus. Gefordert ist also eine Lösung, mit der solche Störungen frühzeitig erkannt werden.
Aus Big Data durch Analyse und Mustererkennung Smart Data generieren: Es ist eines der ganz grossen Versprechen der digitalen Transformation. Das gelingt in Sachen Instandhaltung über das langfristige Erfassen von relevanten Daten (Temperaturen, Drücke, Volumenströme) und deren Analyse (Trends, Abweichungen) sehr gut. Massiv gefallene Preise der immer leistungsfähiger werdenden Sensoren unterstützen dies. Data Mining versucht dann, mithilfe anspruchsvoller statistischer und mathematischer Verfahren beziehungsweise Algorithmen verborgene Muster, Trends und Zusammenhänge in grossen Datenmengen zu erkennen.
97 Prozent der Daten bleiben ungenutzt
Die Crux ist bis heute, dass smarte Feldgeräte wie Pumpen, Kompressoren und Ventilatoren zwar mit dem zentralen Gebäude- oder Prozessleitsystem kommunizieren, aber die fleissig gesammelten Massendaten aufgrund von Sicherheitsbedenken und wegen technischer Hürden vielfach nur zur nachträglichen Fehlerana-

Das Machine-Health-Konzept (GMH) greift auf eine der weltweit grössten Datenbank für typische Maschinengeräusche beziehungsweise Vibrationsprofile zu, mit deren Hilfe äusserst präzise Diagnosen möglich sind.
lyse genutzt werden. Experten schätzen, dass 97 Prozent der Daten aus der Feldebene ungenutzt bleiben. Die Herausforderung ist, an diese Daten ranzukommen. Heute stehen dazu sehr leistungsfähige Echtzeit-Bus-Systeme wie das Industrial Ethernet und Cloud-Anbindungen bereit. Eine datenbasierte Verzahnung der Bereiche Produktion und Instandhaltung ist somit möglich. Sehr anschaulich sprechen Experten von einem «Langzeit-EKG».

LASER SPECTROSCOPY MICROPOSITIONING
Spectroscopy

Gerade die strenge Life-Science-Industrie profitiert von einer vorausschauenden Produktion, wie es die vernetzten Strukturen ermöglichen.
Das Langzeit-EKG auf dem Feld
Grundfos greift mit seinem Machine-Health-Konzept (GMH) auf eine der weltweit grössten Datenbank für typische Maschinengeräusche beziehungsweise Vibrationsprofile zu, mit deren Hilfe äusserst präzise Diagnosen möglich sind. Mehr noch: Aus Maschinendaten werden Handlungsempfehlungen – dank Echtzeit-Meldungen und Algorithmen, die geeignete Reparaturen und Wartungsmassnahmen vorschlagen. Hochwertige Sensoren und smarte Algorithmen überwachen kritische Aggregate rund um die Uhr. Schon beim ersten Anzeichen eines Problems meldet sich das System mit einer detaillierten Analyse inklusive einer erfolgversprechenden Lösung für das sich anbahnende Problem. Der Betreiber kann Wartungsmassnahmen gezielt terminieren (wenn es vom Betriebsablauf her am besten passt), er spart Kosten ein und vermeidet teure Ausfälle. Das Ergebnis ist überzeugend: In der Praxis ergeben sich 30 Prozent geringere Wartungskosten, 90 Prozent niedrigere Reparaturkosten, 75 Prozent weniger Ausfälle, eine 45 Prozent länger verfügbare Betriebszeit. Eine wichtige Besonderheit von GMH ist, dass die genutzte Datenbank schon kurz nach der Installation der Sensoren und Empfänger Aussagen über den Zustand der Anlage treffen kann – die Algorithmen der Künstlichen Intelligenz müssen also nicht wie sonst oft üblich erst angelernt werden. Tausende von hinterlegten Geräusche- und Vibrations-Mustern können sofort mit den installierten Maschinen verglichen werden. Grundfos Machine Health gewährt dem Betreiber einen Blick in die nahe Zukunft – damit wandelt sich Instandhaltung zum Asset Management, vom Kostenblock zur Werterhaltung.

Kontakt Grundfos Pumpen AG Bruggacherstrasse 10 CH-8117 Fällanden +41 44 806 81 11 info_ch@grundfos.com www.grundfos.com
UV/VIS/NIR – Modular spectrometers

DS5 – Dual Beam UV-Vis Spectrophotometer absorption and transmission

FLS 1000 – Lifetime fluorescence

Particle Size Analysis
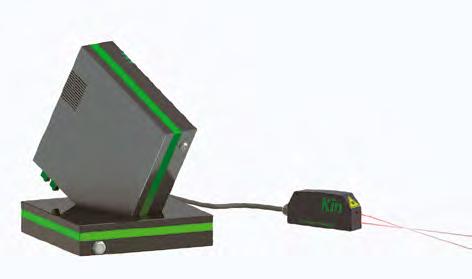
VASCO KIN™ is a new generation of Time-Resolved instrument for accurate kinetic analyses combined with an in situ and contactless remote optical head