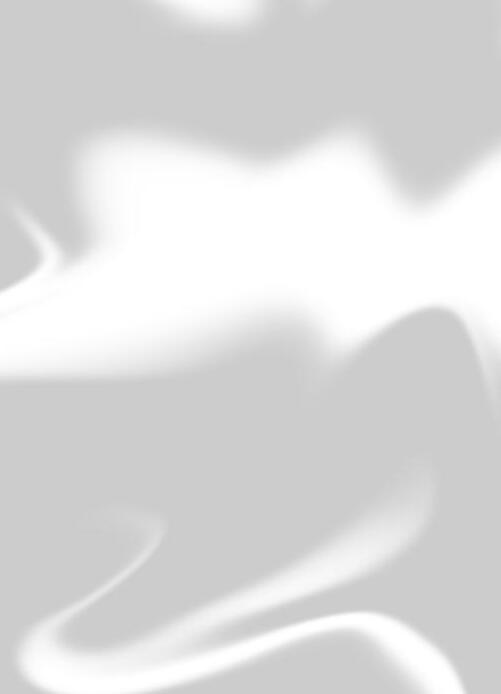
8 minute read
DESIGN DEVELOPMENT PROJECT PROPOSAL
from process book
by shon.maini
The footwear/ fashion industry is facing a huge problem as around 85% of the pairs produced (20 billion+ pairs of shoes) are dumped into landfill all around the world each year due to which a lot of resources and materials go to waste.
The design will help in providing the customers with the following-
Advertisement
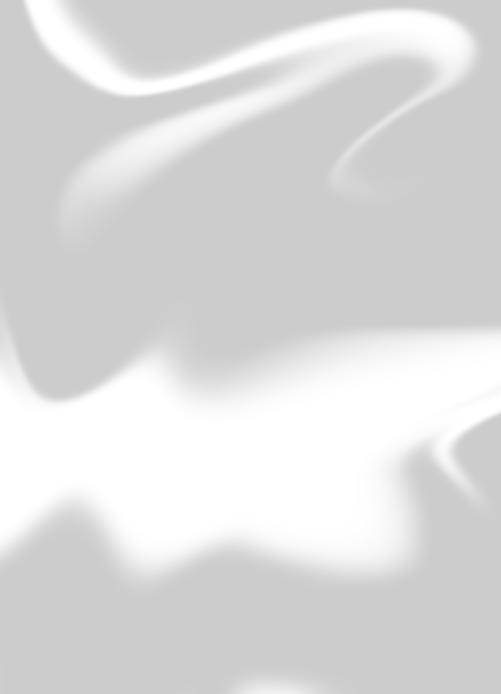
Personalization: The ability to customize the virtual sneakers according to color, style, and materials allows users to express their unique fashion taste and create a one-ofa-kind pair of sneakers that reflects their individuality. The option to have a physical pair made according to their foot measurements further enhances the personalized experience.
The designer came up with a concept for creating sneakers in the MetaVerse that can be purchased and worn virtually by users, while also allowing them to obtain a physical pair of fused 3D lattice constructed sneakers tailored to their feet and design preferences in the real world. By merging the virtual and physical realms, this proposal aims to offer a unique and personalized experience to consumers, combining the benefits of digital fashion with the tangible appeal of physical products. A new design will be released on a monthly basis and the buyers can return their original pair which can be reused to create the new shoe making it extremely sustainable and recyclable.
Immersive Virtual Experience: By integrating the MetaVerse, users can enjoy an immersive and interactive experience within virtual showrooms, trying on different virtual sneakers, and exploring the latest designs. This bridges the gap between digital fashion and the real world, providing users with an engaging way to explore and shop for sneakers.
Convenience and Accessibility: Purchasing sneakers in the MetaVerse eliminates the limitations of physical stores, such as limited stock or geographical constraints. Users can access the virtual platform from anywhere, at any time, and easily browse through a wide range of designs, ensuring a convenient and accessible shopping experience.
Visualizing Fit and Style: The virtual try-on feature using AR technology enables users to visualize how the customized sneakers would look on their feet before making a purchase decision. This eliminates uncertainties and helps users make more informed choices, ensuring that the physical pair they receive aligns with their expectations.
Virtual Sneaker Design: The designer plans on developing a versatile collection of sneakers designed specifically for the MetaVerse, featuring a range of styles, colors, patterns, and materials, These virtual sneakers will be created with meticulous attention to detail, ensuring an immersive and visually appealing experience for users and will be 3D printed on order and be a custom fit for the buyer.
Customization Options: To enhance personalization, users will have the ability to customize various aspects of their virtual sneakers, such as color combinations, textures, branding elements, and additional embellishments. This will allow them to create a truly unique pair of sneakers that reflect their individual style in the metaverse and in real life.
Using advanced augmented reality (AR) technology, users can virtually try on the sneakers they’ve customized within the MetaVerse. This feature will enable them to visualize how the sneakers would look on their feet, allowing for a more informed decision-making process before purchasing
Tailored Fit and Comfort: The incorporation of foot measurement and analysis allows for the production of physical sneakers that are customized to fit the individual’s feet. This ensures optimal comfort, support, and a better overall wearing experience compared to off-the-shelf sneakers.
Sustainability: By offering virtual sneakers that exist purely in the digital realm, this concept reduces the waste of over-production and associated environmental impacts. Users can enjoy the latest fashion trends without contributing to excessive material waste, making it a more sustainable choice.
Project Plan Including The Design Process-
WEEK 1: Research on foot anatomy, the metaverse and shoe making
WEEK 2: Use of Double Diamond and Good, quick and cheap pyramid to review the proposal
WEEK 3: Initial sketches and Final sketches, Designing in VR
WEEK 4: Tweaking the design, finalsing colour ways and final renders of the shoe
• The designer began the design process by creating initial sketches on paper to conceptualize the shoe design.
• Transitioning to the digital realm, Adobe Illustrator was employed as a powerful tool to bring the sketches to life.
• Utilizing the pen tool within Adobe Illustrator, the designer meticulously outlined the shoes, capturing every intricate detail.
• The digital platform provided flexibility and precision, allowing for seamless refinement and modification of the designs.
VIRTUAL REALITY: GRAVITY SKETCH
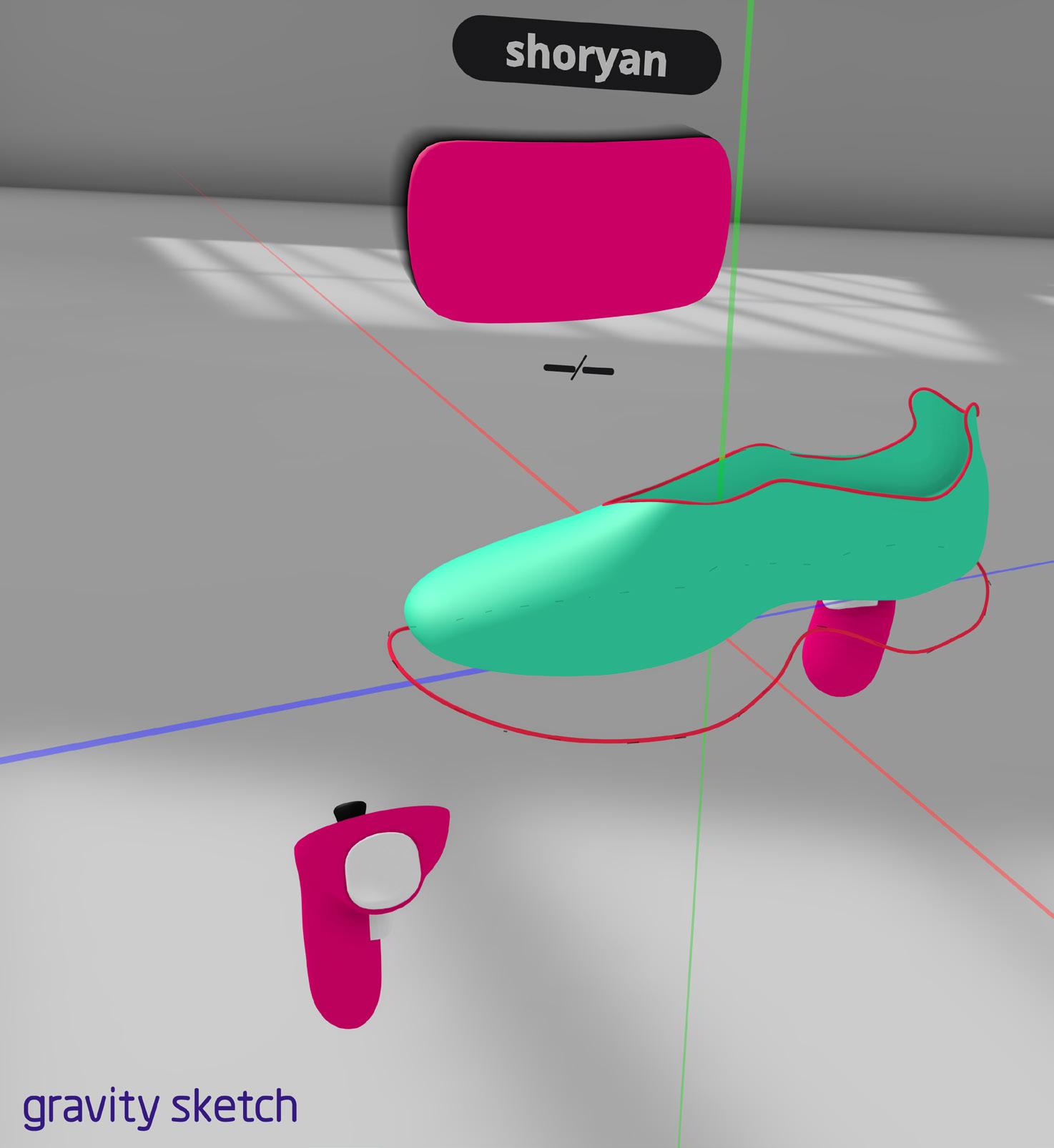
• After a few induction tutorials at the Innovation studio the designer used Gravity skeetch to make the shoe and work on it as a lot of footwear designers and makers use it to create shoe as it makes it easier and much more precise to add detials and work overall on the shoe.
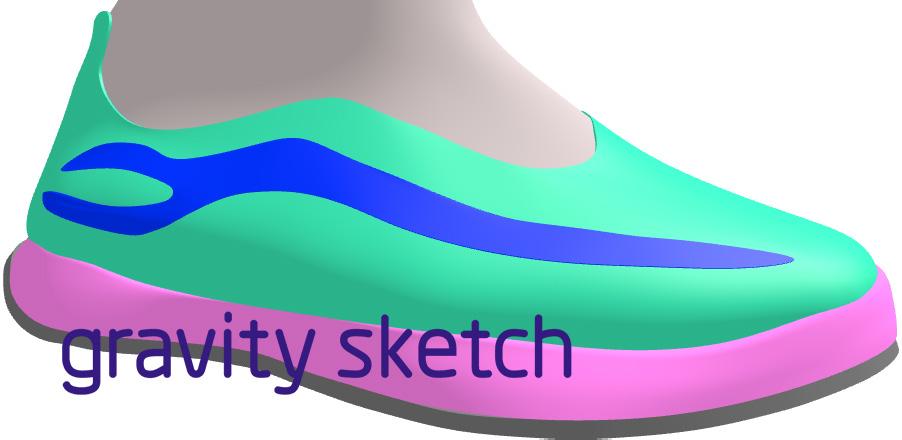
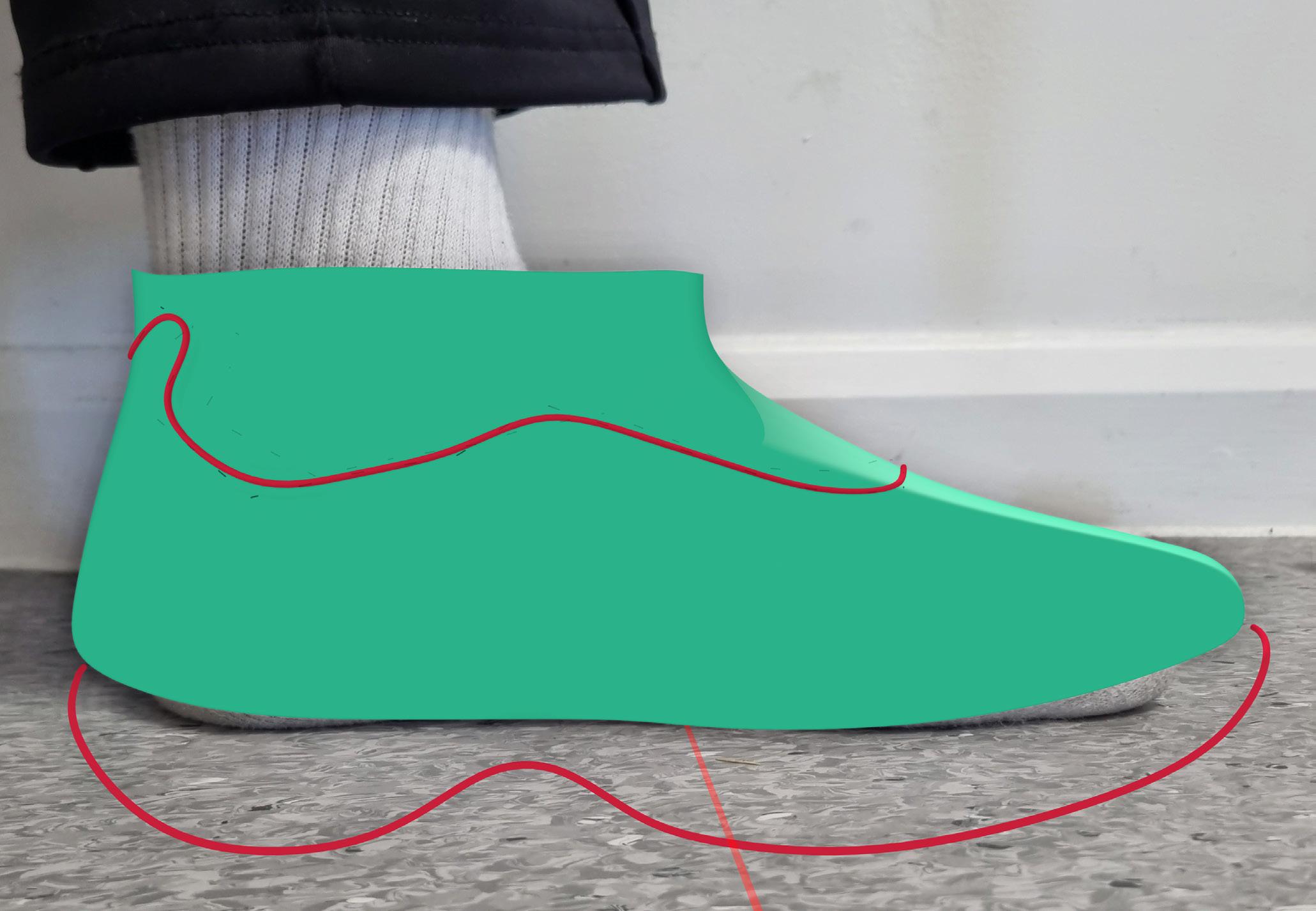
• The designer initiated the process by creating a last that precisely matched the contours of their foot.
• A separate last was then constructed to specifically accommodate the dimensions of the designer’s foot.
• The completed last was outlined using a loop tool, ensuring accuracy and attention to detail.
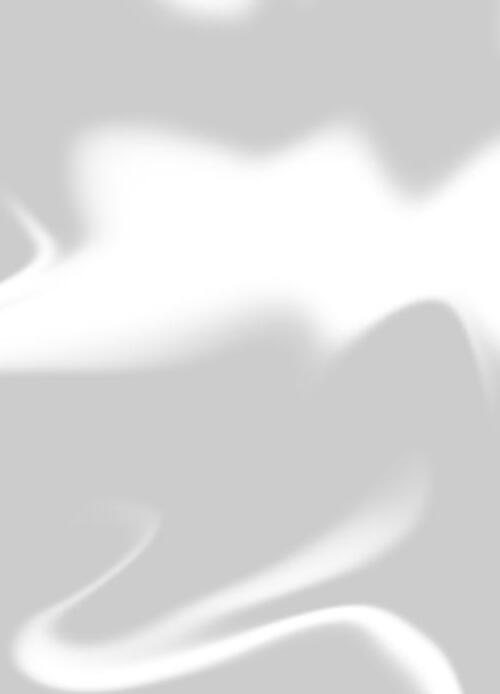
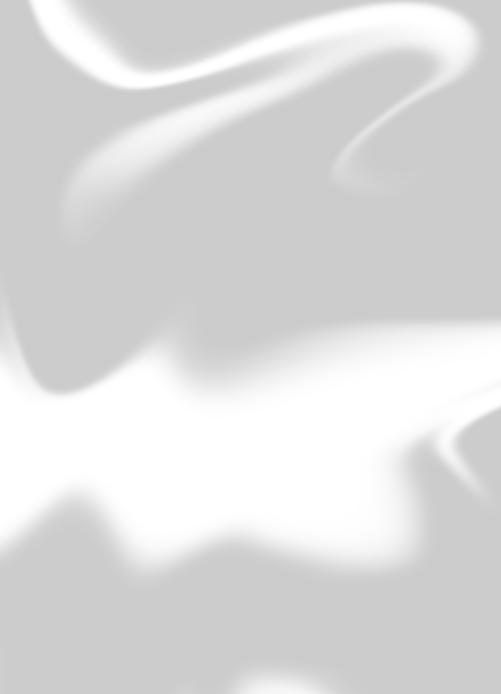
• The designer subdivided the last to align with the initial sketch, ensuring a seamless integration.
• Design elements were thoughtfully incorporated onto the shoe, enhancing its visual appeal.
• The designer proceeded to focus on the development of the midsole and outsole of the shoe.
• The midsole and outsole were attached to the upper part of the shoe, creating a functional and cohesive product.
Blender
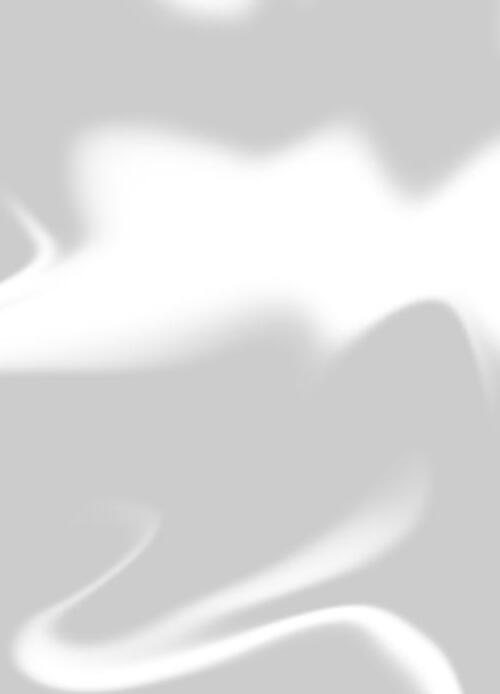
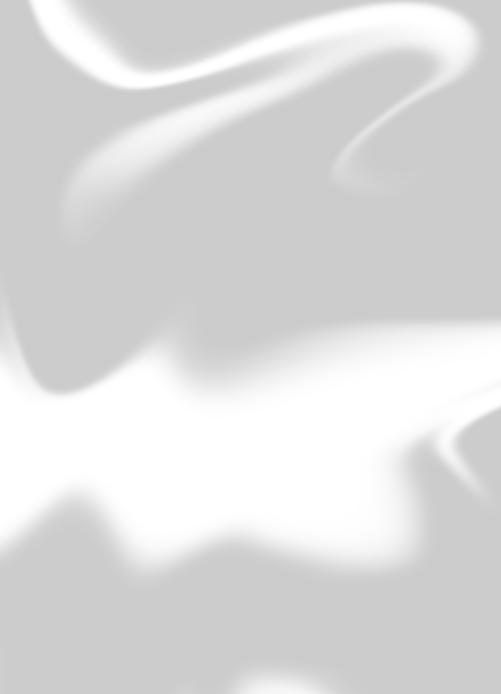
• After finalizing the design in Gravity Sketch, the designer proceeded to convert it into an FBX file format, facilitating smooth transfer to Blender for additional refinement.
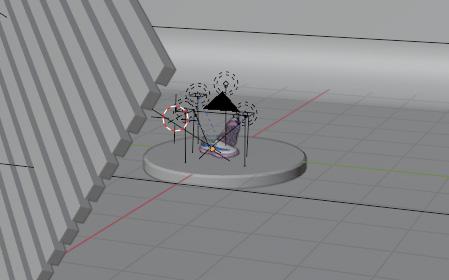
• In Blender, the designer used the software’s capabilities to incorporate intricate details, textures, and meticulously make precise adjustments to perfect the 3D model.
• The designer took advantage of Blender’s versatility, allowing for heightened creative control and the ability to fine-tune the design in accordance with their vision.
• Through an iterative process, the designer iteratively modified and enhanced the design, ensuring that the final 3D model captured the desired aesthetics and functionality of the envisioned shoe design.
• This refining process in Blender resulted in a more polished and realistic representation of the shoe design, encompassing the finalized colorways and attaining the desired level of perfection.
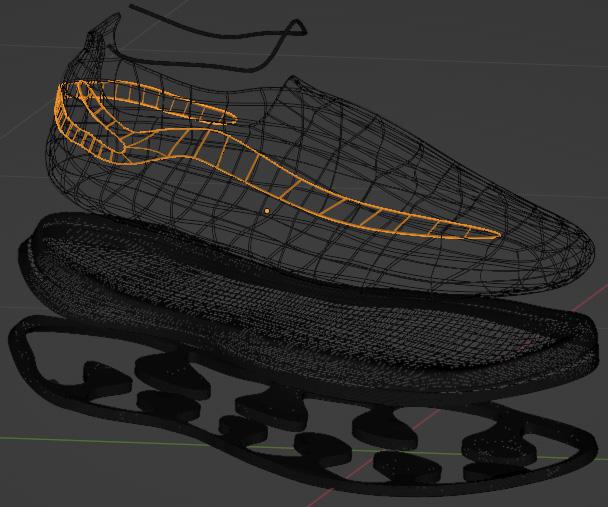
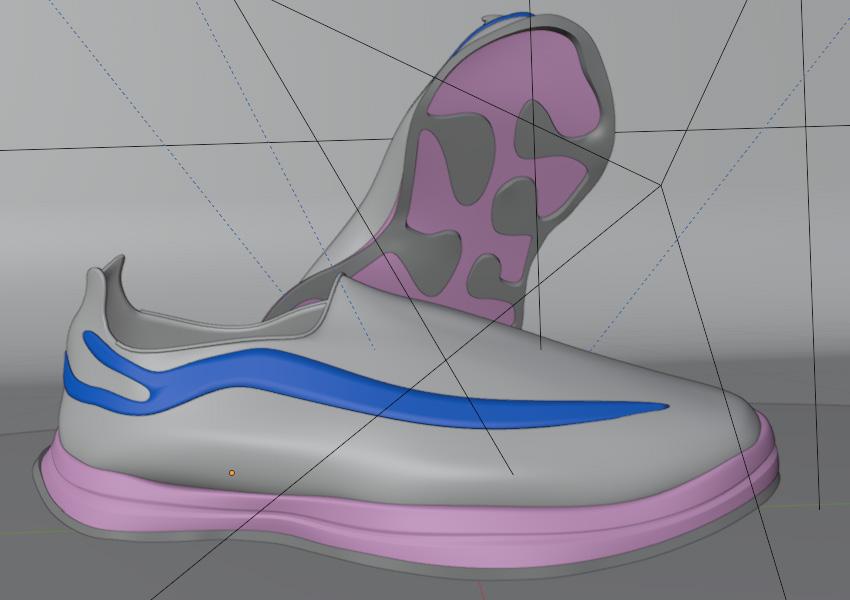
• The designer also created a set for taking hero shots of the shoe added a turntable and various 3 point lightings and external objects for adding shadow for the better hero shots.
• The designer tried working on re modelling a few parts of the shoe by using the sub division tool which was a process of trial and error.
Final Renders
• The designer attended sessions for Twin motion 2023 trail version and learned different ways it can be used for rendering and presenting products.
• The designer also created a whole set on blender with 3 point lighting, a turntable, a few pannels and a backdrop shown on FIGURE 24 to create a surrounding around the shoe and added surface imperfections to create a realistic render.
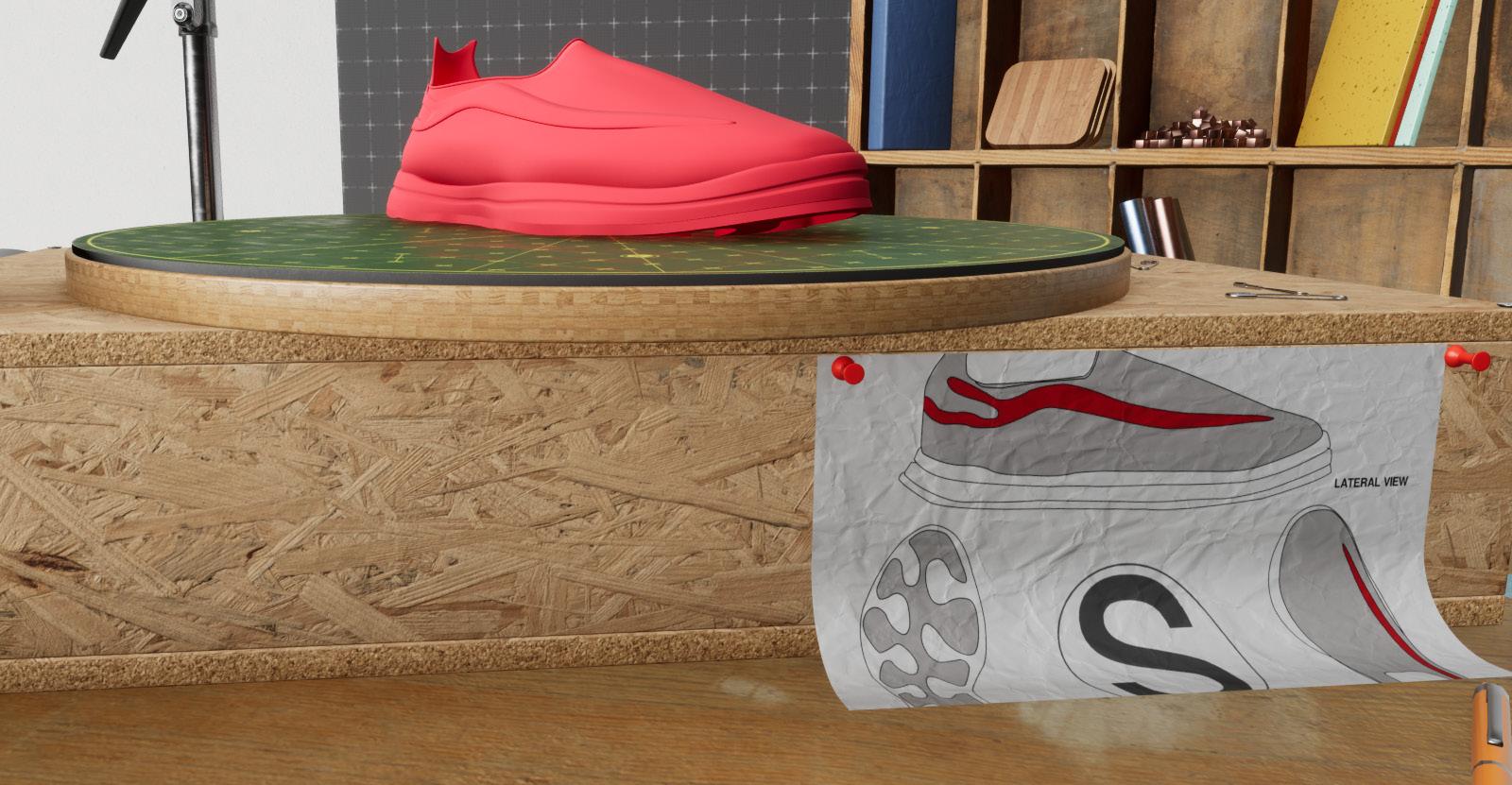
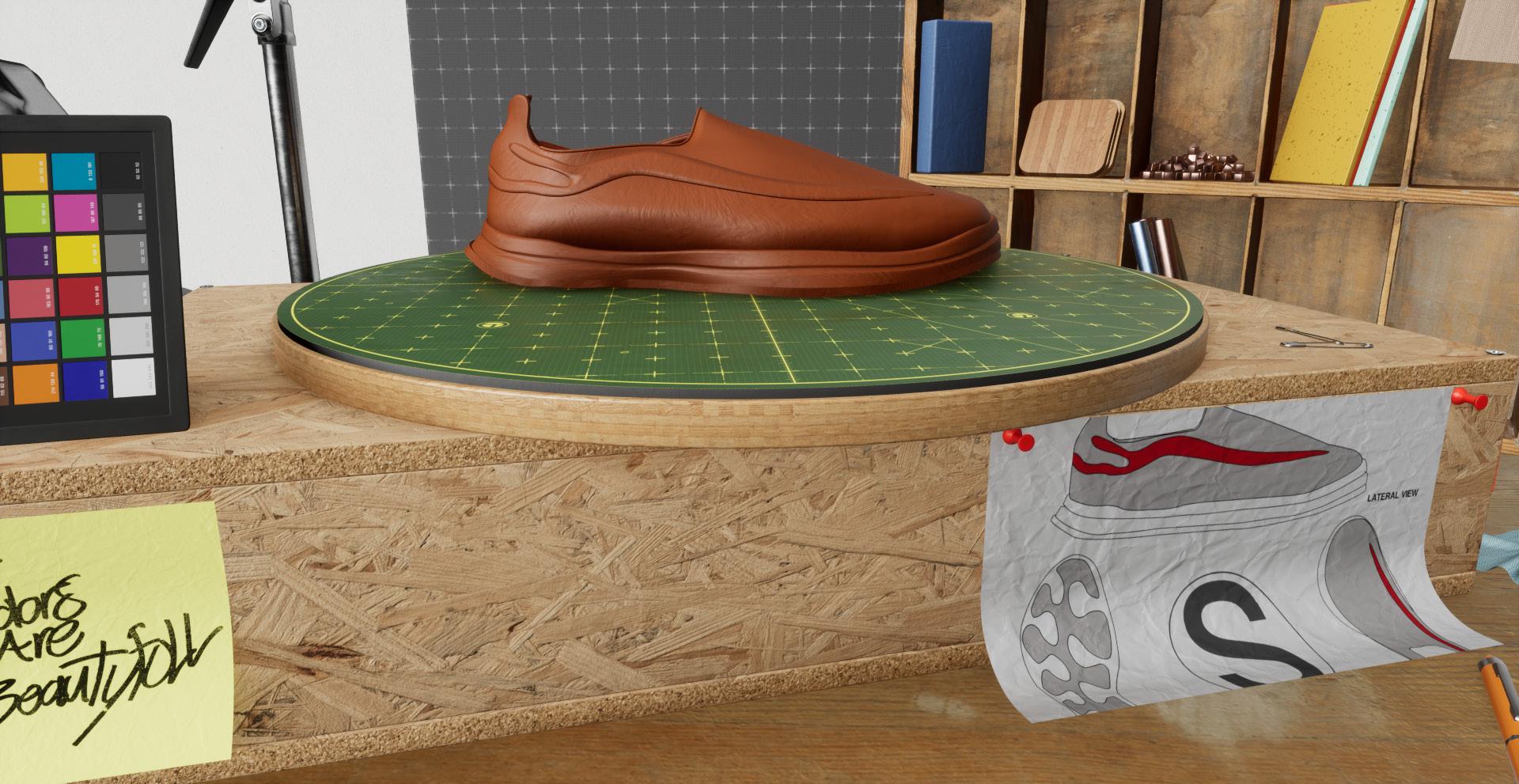
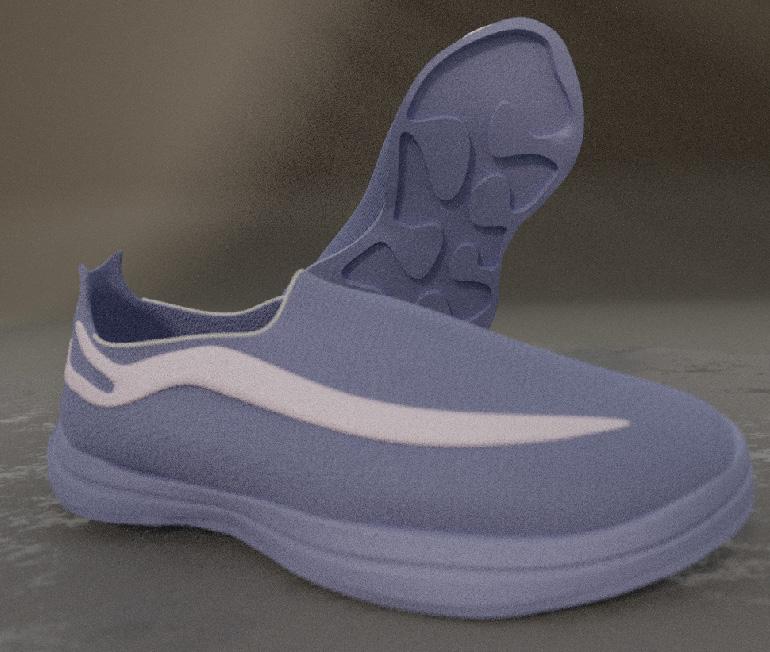
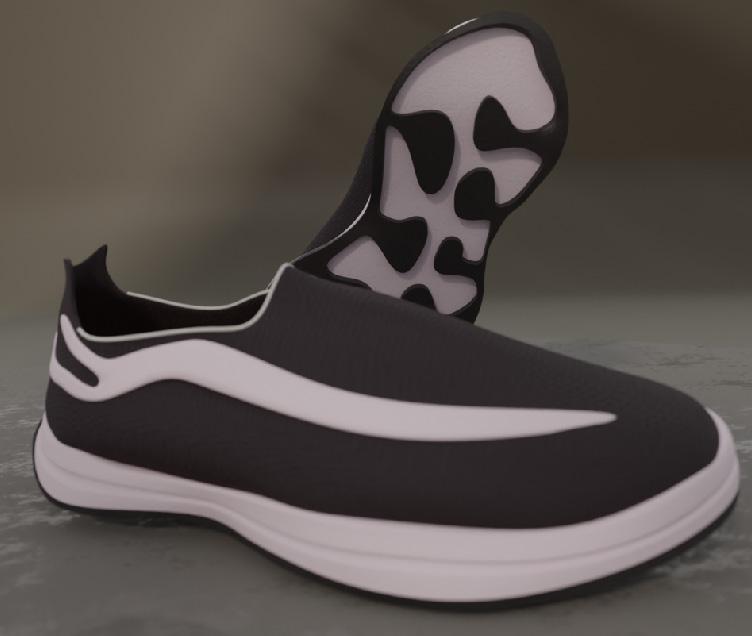
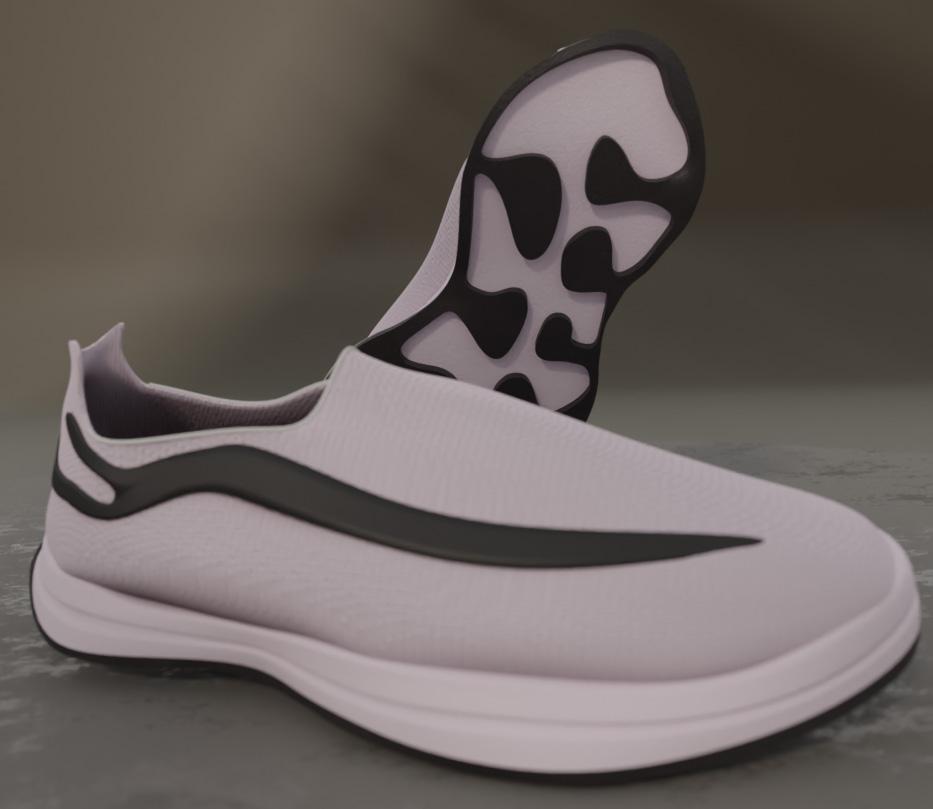
DETAILED CLAY RENDER ON TWIN MOTION WITH SKETCH
DETAILED RENDER ON TWIN MOTION WITH SKETCH
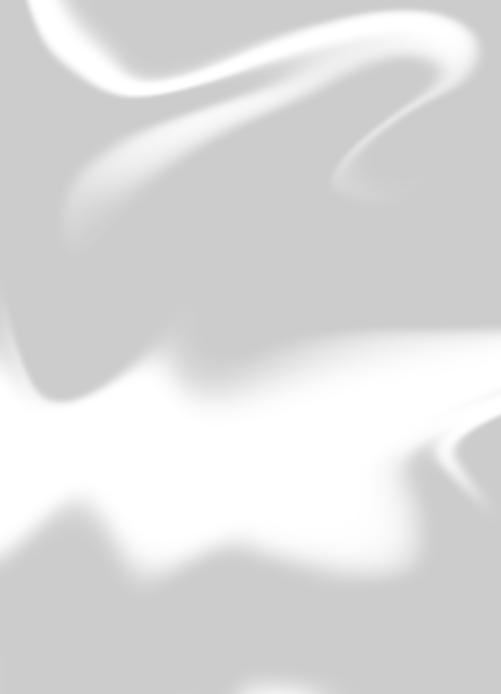
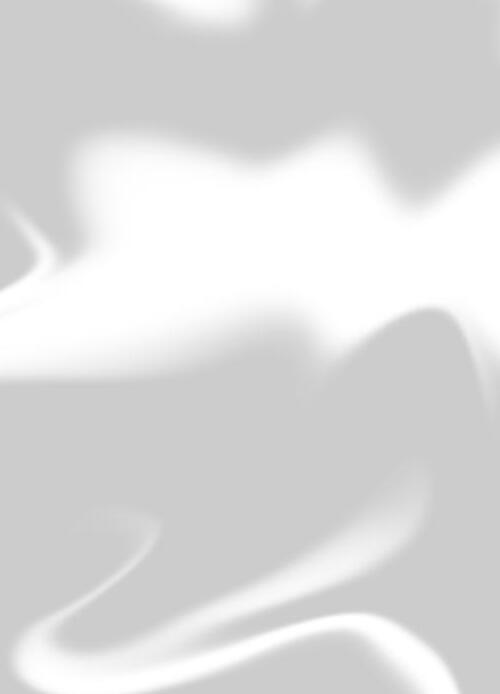
Prototypes
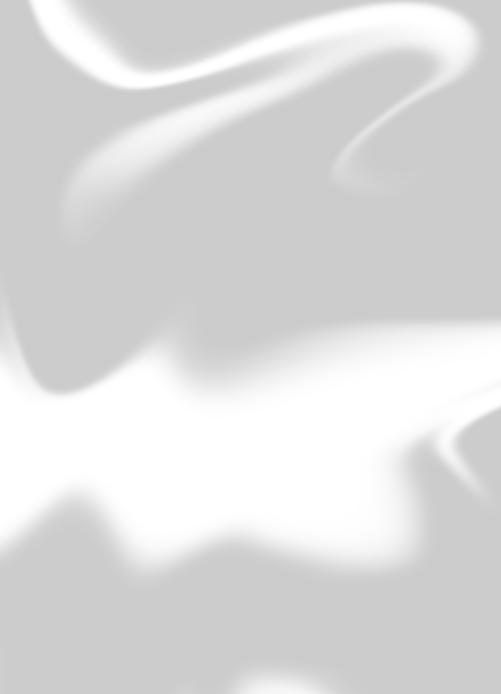
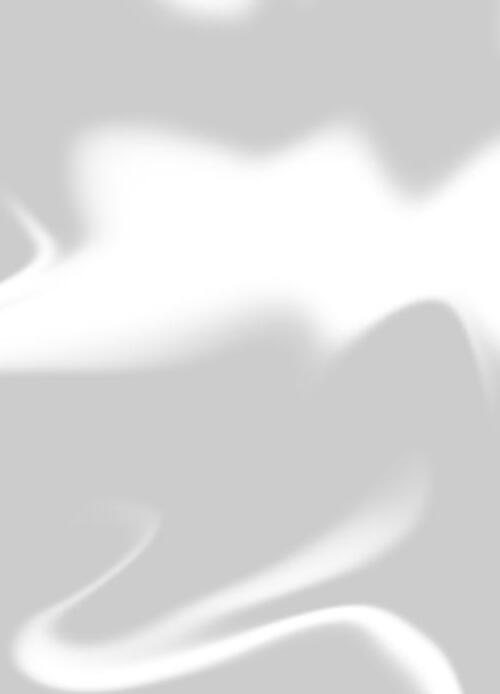
• The designer created mini 3D printed protype with minimal support on Cura using the PLA filament to gain insights into the intricacies of the sneaker’s distinctive shape and form.
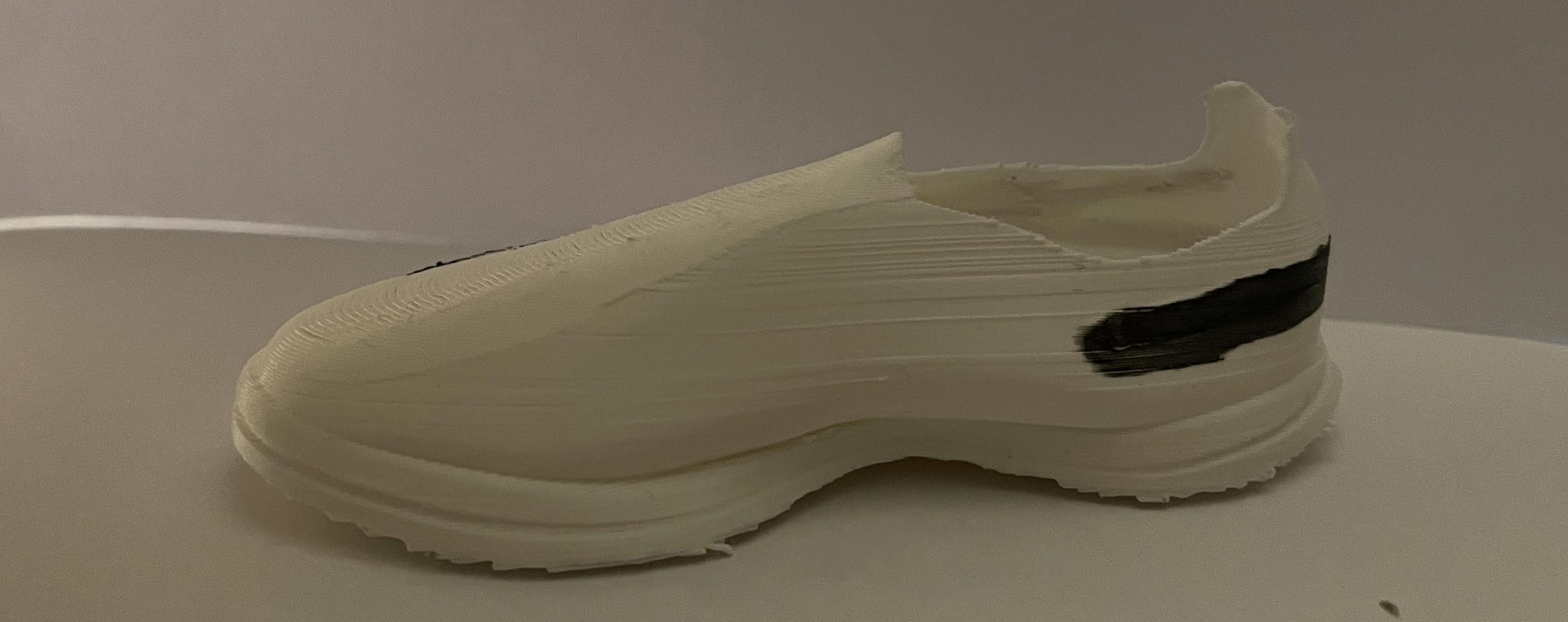
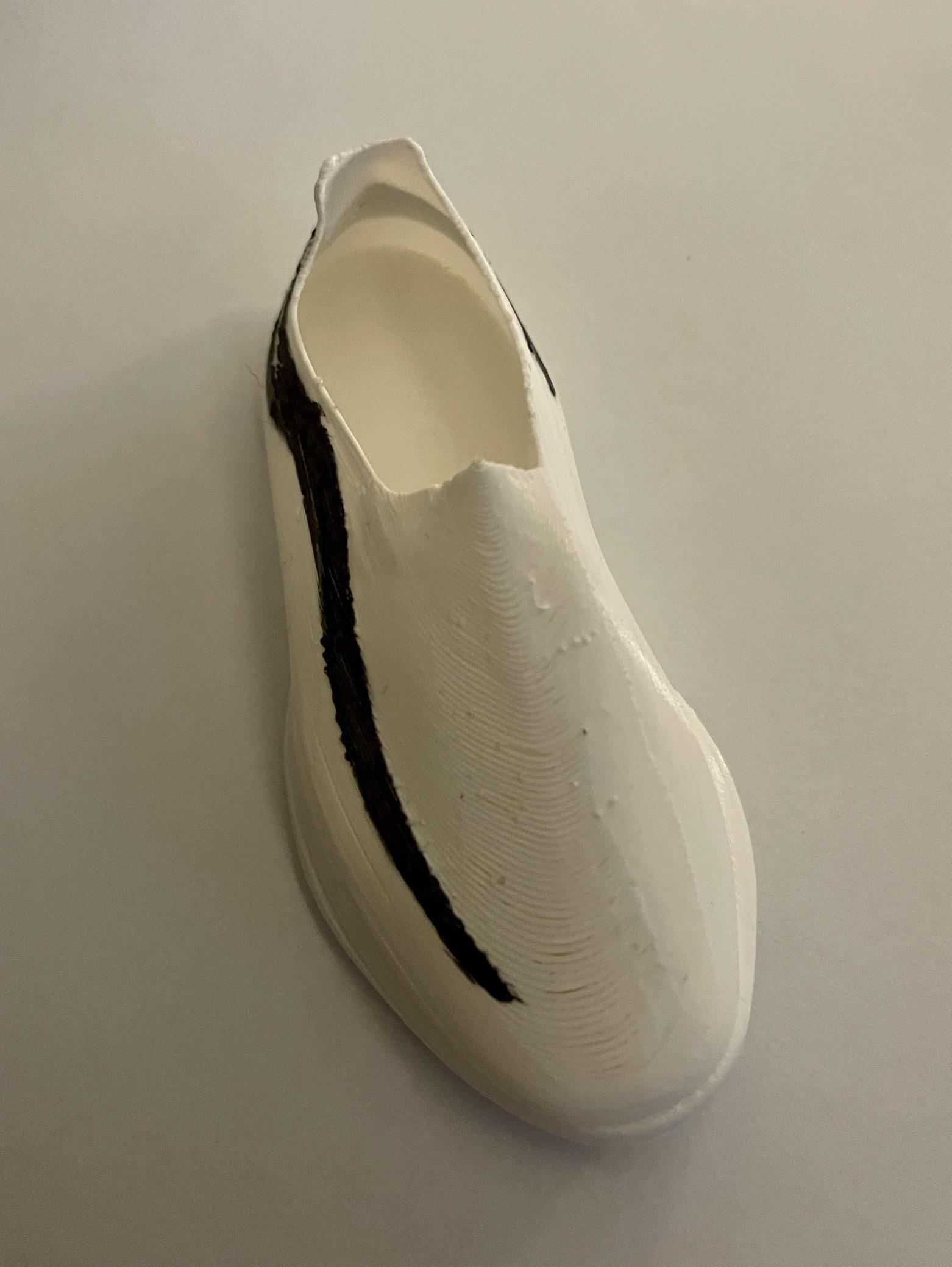
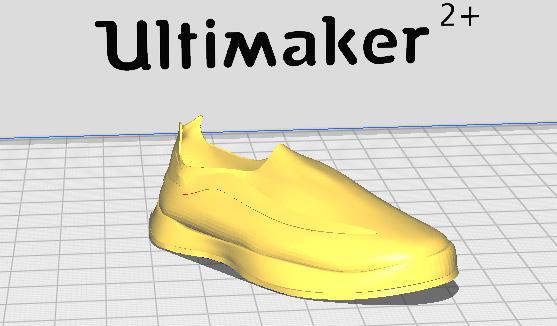
• By bringing the design to life in a tangible manner, the designer was able to assess the contours, understand the ideal proportions, and explore the interplay of various elements, ensuring that the sneaker is a fusion of aesthetics and functionality.
• The designer watched a few videos to understand the settings and the files to be used: I 3D printed Air Jordan 1’s by Seth Fowler- https://youtu.be/9_KzRpMC8EE and Can you 3d print shoes for free by Seth Fowler- https://youtu.be/FdSNYK2r1u8
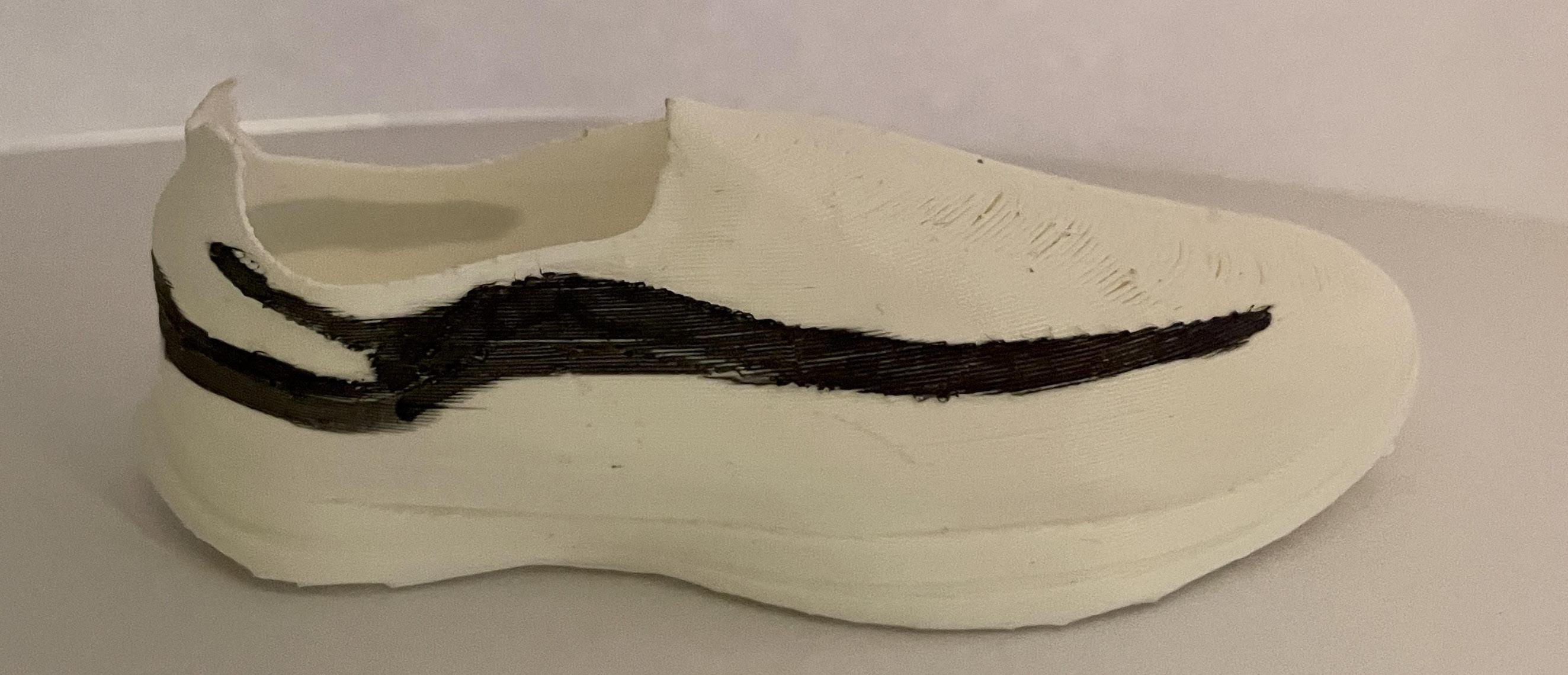
Visuals On Blender And Twin Motion
Visuals On Twinmotion
The designer added the fbx file from blender onto twin motion and adjusted the size of the shoe and changed the colours to create the renders of the shoe.

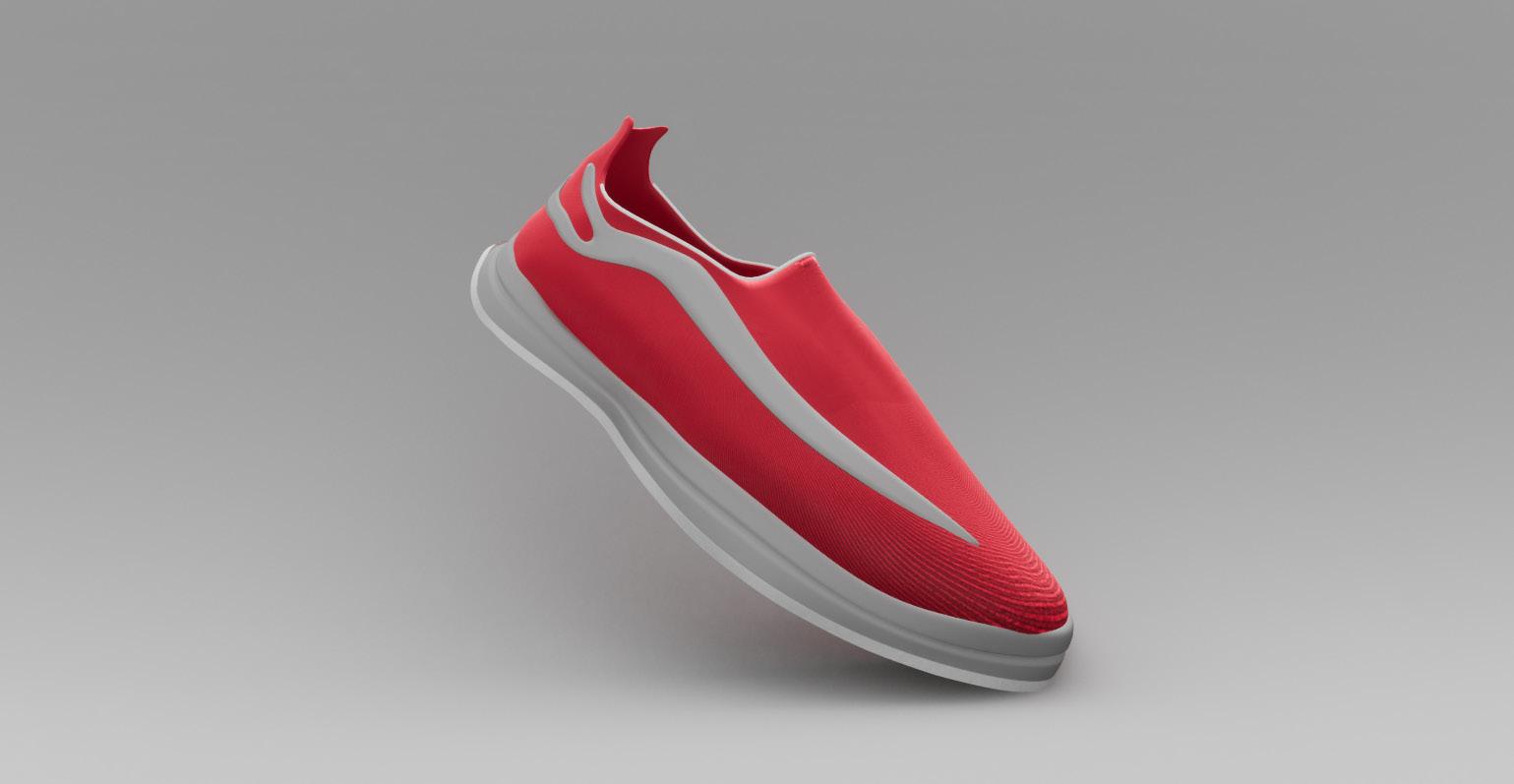

Visuals On Blender
The designer made the renders on Blender, then added the PNG onto photoshop and added some noise and liquified the background.
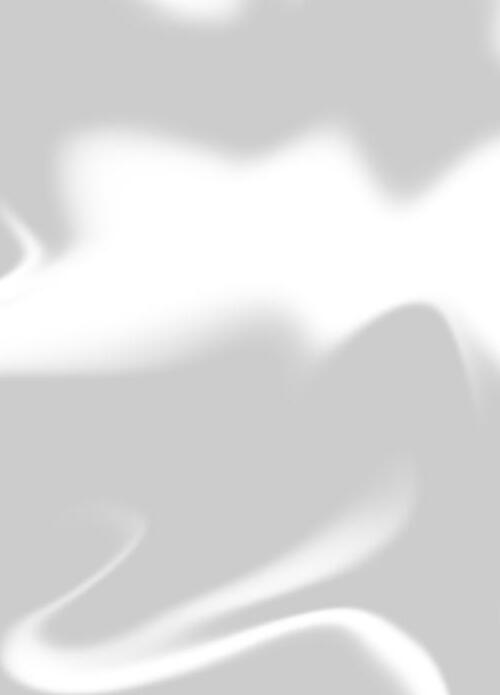
In this semester, I got to learn new design methods and techniques and used them to design and make prototypes of the product and create something which matches the personal interest of the designer and would be able to make the designers portfolio better.
I was able to define my own design brief based on my passion of designing and making footwears and solve the problems of waste of resources and footwear and how different approaches and designs can reduce wastage of materials and resources in the footwear industry and make futuristic sneakers that can be worn virtually in the metaverse and create fully customisable 3D printed shoes that will be made according to the scan of the buyers feet.
In this semester, I understood the importance of independent research and how primary research can help me in utilising better resources and techniques to create sneakers and model them.
I used the concept of Double Diamond as I used the design model to find a problem- the wastage of materials in the footwear industry, do my research on ways to solve the problem, and find a solution for the industry and the future which is creating a sneaker that can be worn in the metaverse and can be 3D printed to create a physical version of the shoe which will made fully custom from the buyers scan.
I also used the model of Good, Quick and Cheap to review my product and tried achieving all 3 goals the product will help in reducing the wastage of materials and resource in the industry and the 3D printed filament can be reused and recycled, as the product can be purchased in the metaverse the only time will be consumed in producing the shoe when the buyer wants to get a 3D printed pair which is also a quick process. The price of using 3D printed filament like TPU is also inexpensive which was discovered by the designer after doing the research on existing 3D printed shoes and the best filaments to make a sneaker. The designer found that TPU has a lot of benefits and can be reused and recycled easily.
I attended a few sessions of Gravity sketch which was a new skill for me as they got to learn how to use VR and gravity sketch to make designs and understand the process of creation of sneakers used by industry professionals after finalising one design from the sketches made by me.
Once the design was created in Gravity sketch the I started working on Blender to make a few adjustments and add details and textures onto the shoe the refining process in Blender resulted in a more polished and realistic representation of the shoe design and how it would look in real life.
I also used Blender to create realistic Hero shots for the sneaker and created a whole set for it. I also used Twin motion to create various different renders of my shoe and I also used Photoshop to make the background a bit blurry and used the liquifying tool to make the sneaker the main focus.
During the prototype phase, I planned on 3D printing a mini version of the sneaker to understand the shape and the form of the shoe in real life with the PLA filament with infill and support which made the shoe extremely stiff and stable.
I wanted to create a wearable version of the shoe but was not able to do it in the timeline of the project.
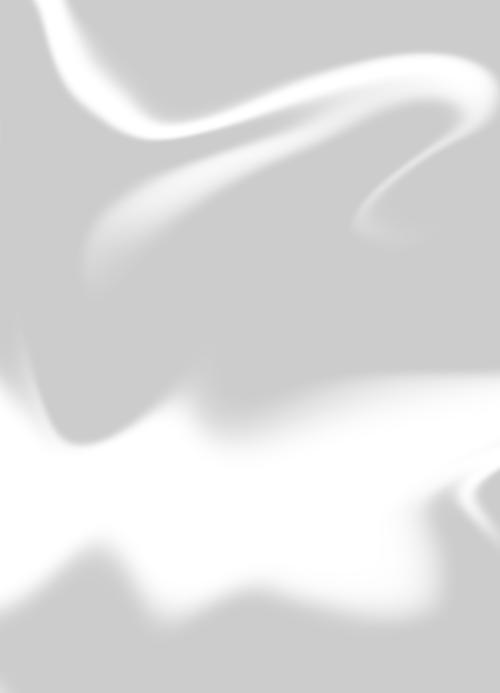
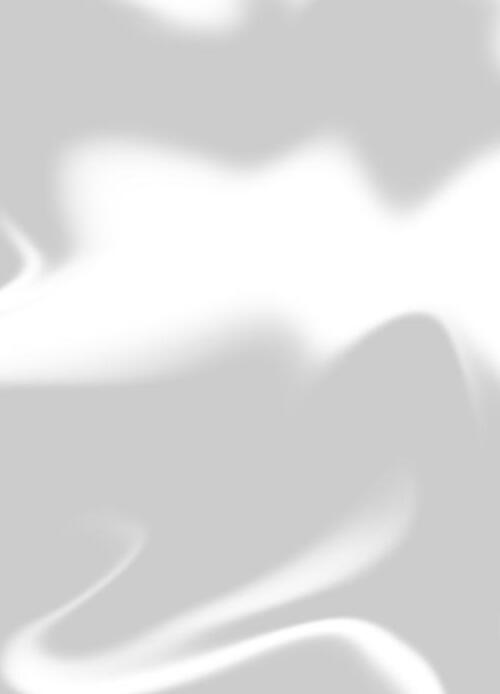
In the future I plan on creating a real life wearable version of the shoe which is as good as a factory produced sneaker and create new versions of the sneaker in the metaverse. The buyer will be able to replace the pair purchased by them in real life and exchange it for the newer version of the shoe making the shoe sustainable and the filament used to make the shoe reusable and better for the future.
In conclusion, I got to create a sneaker using the same process created by the industry professionals and learn new things about the Metaverse, 3D printing and a whole new software Gravity sketch that can be used in the future to create new versions of the sneaker and develop a real life version of the shoe in the future.