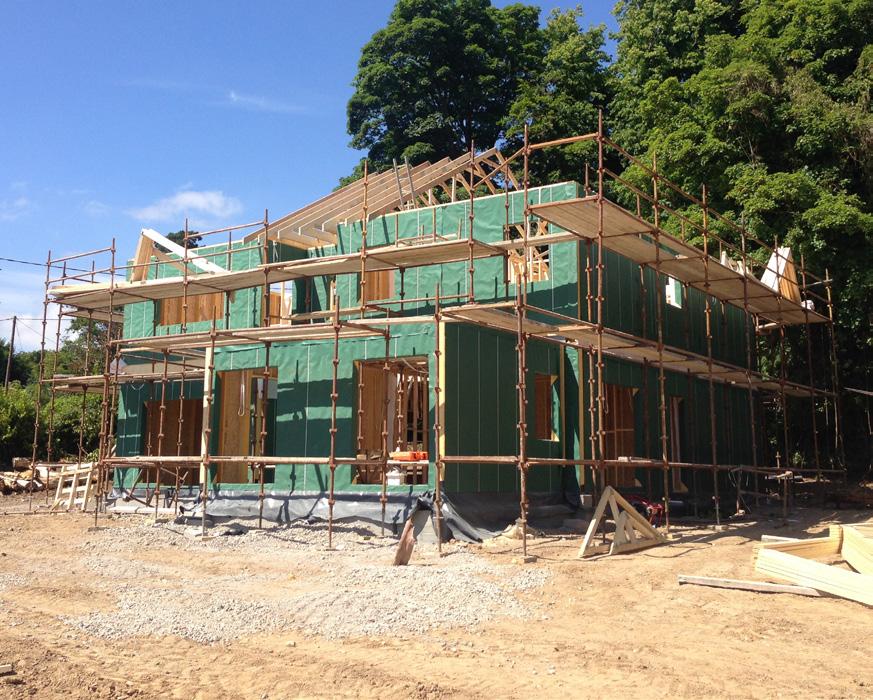
2 minute read
What to check for on site
What
Moisture is the enemy of all timber frame construction, where leaks and trapped moisture can cause timber to rot and decay. The process of decay in timber needs three things; food (the timber itself), water and sufficient oxygen.
So whilst timber that is permanently wet and starved of oxygen, such as the famous timber piles in Venice, the Mary Rose, or our own bog oak; can survive intact for hundreds of years, timber that gets exposed to a combination of air and water will suffer.
Watchpoints
Not only are timber panels at risk during the delivery and handling phases, but after erection they can suffer from excess wetting. One of the greatest problems is that they get wet and are then covered over before they have time to dry out. Insulation will generally retain moisture for longer so select insulation that dries quickly and that doesn’t slump when wet.
Some design features are best avoided if they present a risk of trapping water. These could include flat roofs, parapet walls, balconies, level valleys between roofs, canopies on external walls and the like.
Differential movement can also allow ingress of moisture through areas such as cracked render, gaps around windows and doors and so on. The main problem with leaks is that they tend to remain unnoticed until damage has already occurred.
Leaks during a building’s lifetime can also arise from plumbing, sanitaryware and heating systems, so regular maintenance of these fixtures is perhaps even more important in a timber frame home than traditionally built ones. Provided that the potential issues are taken care of at the design phase, then human error will be responsible for most problems during and after construction.
The old rule “if a thing can go wrong, it will go wrong” is too often confirmed by hard experience and it can be applied especially to the erection of prefabricated timber framed structures on site.
One golden rule to keep in mind is that everyone on site at any time for whatever reason, is responsible for correcting errors and no one should ever be allowed to claim “that wasn’t my job”.
If they cannot correct the error themselves, then they have a responsibility to report it to someone who can and will take the correct course of action. I have sometimes seen wellmade timber frame panels left out in very poor conditions such as standing in deep puddles of dirty water, or covered in snow, or stacked misshapenly at odd angles, or with badly torn breather membranes. connection required on the project, including those for structural connections, framing, wall ties, VPM, sheathing and VCL; and should show: l The number and spacing of fixings, including nailing patterns and edge distances. l The size and type of fixing, including material and corrosion protection. l The method of fixing, for example, skew nailing.
Anyone, from the truck driver, the telehandler operator, individual tradespeople, to the site foreman; should have intervened in these situations but failed to do so. Always remember that work completed by one trade should be left to an appropriate level of finish and in the correct state for other trades.
Where wall design relies on plasterboard to take racking forces, the design should clearly show those walls include the type and spacing of fixings required.
The design (and later the