
14 minute read
At the mercy of everything
NEW BUILD
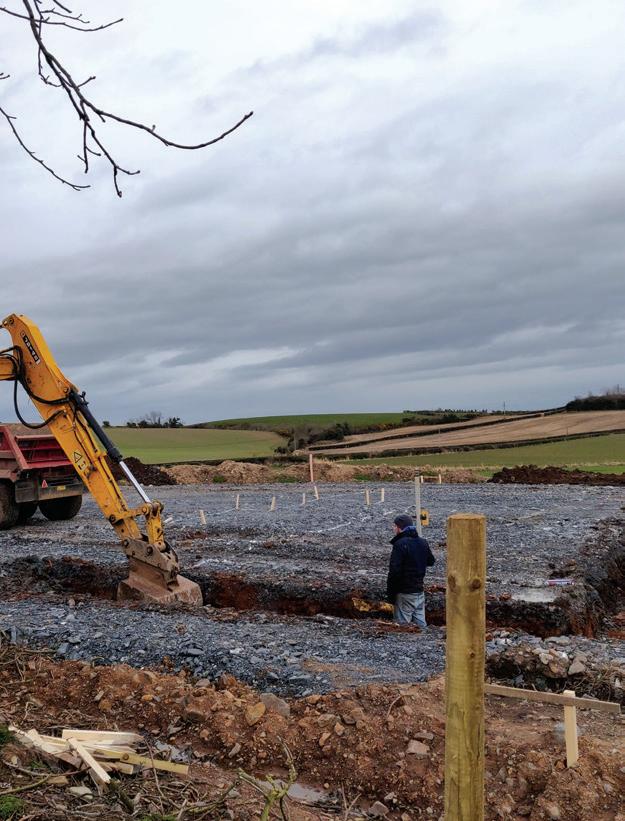

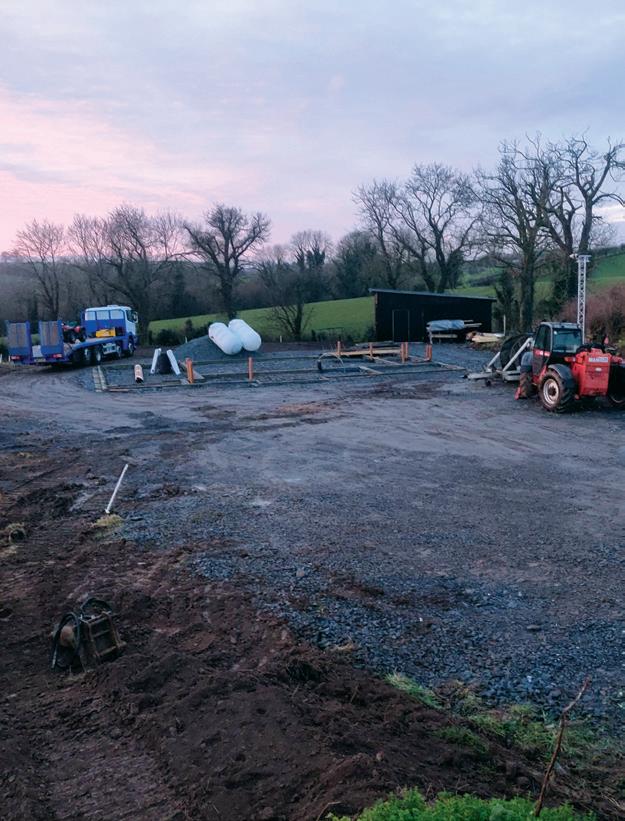

CO DOWN
everythingAt the mercy of
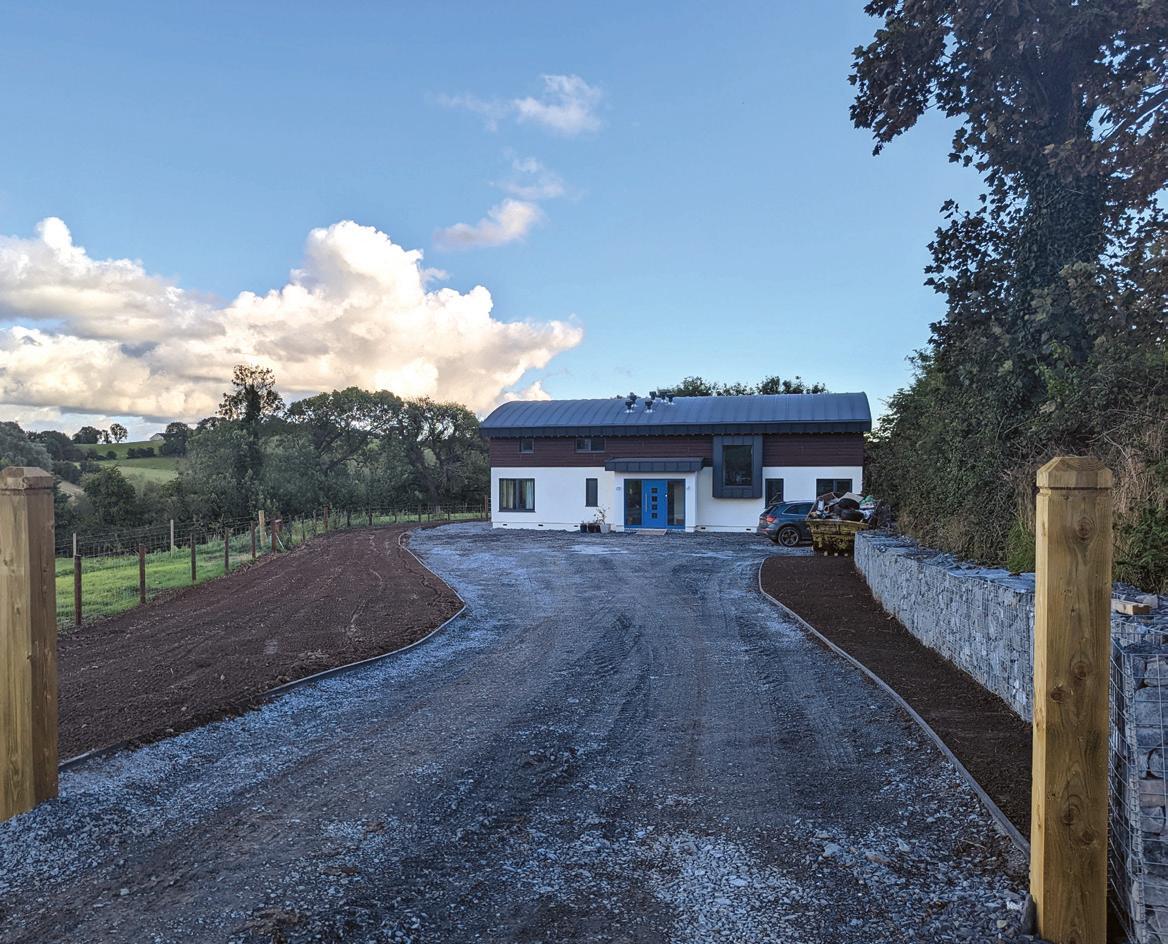
Brian Corry recently completed his self-build amidst a materials price crisis and the pandemic. Here he shares how he got on.
Overview
House size: 275 sqm Plot size: 7 acres Bedrooms: 4
Heating, hot water and
ventilation: exhaust air heat pump Build method: glulam panels and beams (timber) EPC (SAP): A (93)
It only took myself and my wife Karen five months to physically build our house. But if you were to start the clock the day we bought the site, it took us three years. It’s no surprise then that the first night we spent in our new home, we were both elated and exhausted. In the evenings, when I finally get to sit down and relax, my mind still wanders back to everything that happened over the past five months. In retrospect, the schedule was ambitious. Not that we picked the move in date arbitrarily. The end of July 2022 was when we were supposed to hand our old house over to the people who had bought it eight months previously. In the end we ran over this deadline by two weeks. Given all the challenges we encountered along the way, we don’t think that was too bad…
Pandemic beginnings
Our journey started back at the beginning of 2019 when we bought land to build on. The site clearing and levelling took place in the autumn of that year with the plan to start the build in 2020 after we got back from our honeymoon. In early 2020 we had everything in place with the foundations and footings in. I had lined up the tradesmen we needed and ordered the glulam solid timber kit. Our build method is HBE which is a lighter weight version of cross laminated timber (CLT) suited to two storey designs. But in March Covid struck – forcing us to suspend all construction activity whilst I worked hard with our team to ensure our business got through the pandemic. It was hugely disappointing but we couldn’t risk it financially. After spending so much time preparing, it was deflating to walk around the site in the subsequent months imagining what could have been. Karen was always positive and kept repeating that “one day it will happen”
NEW BUILD
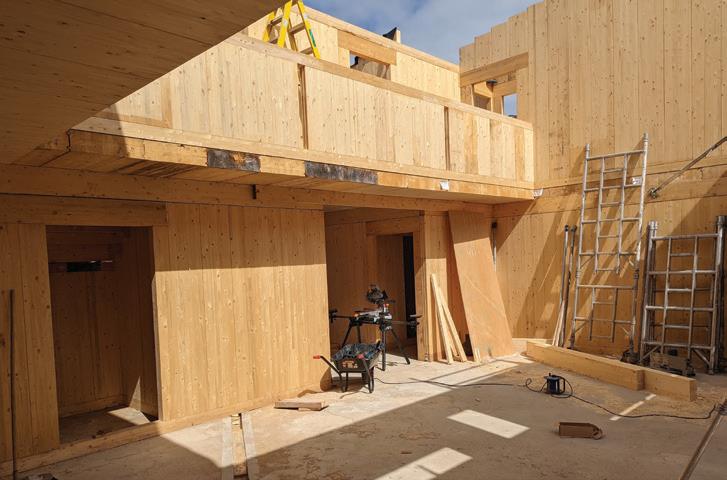
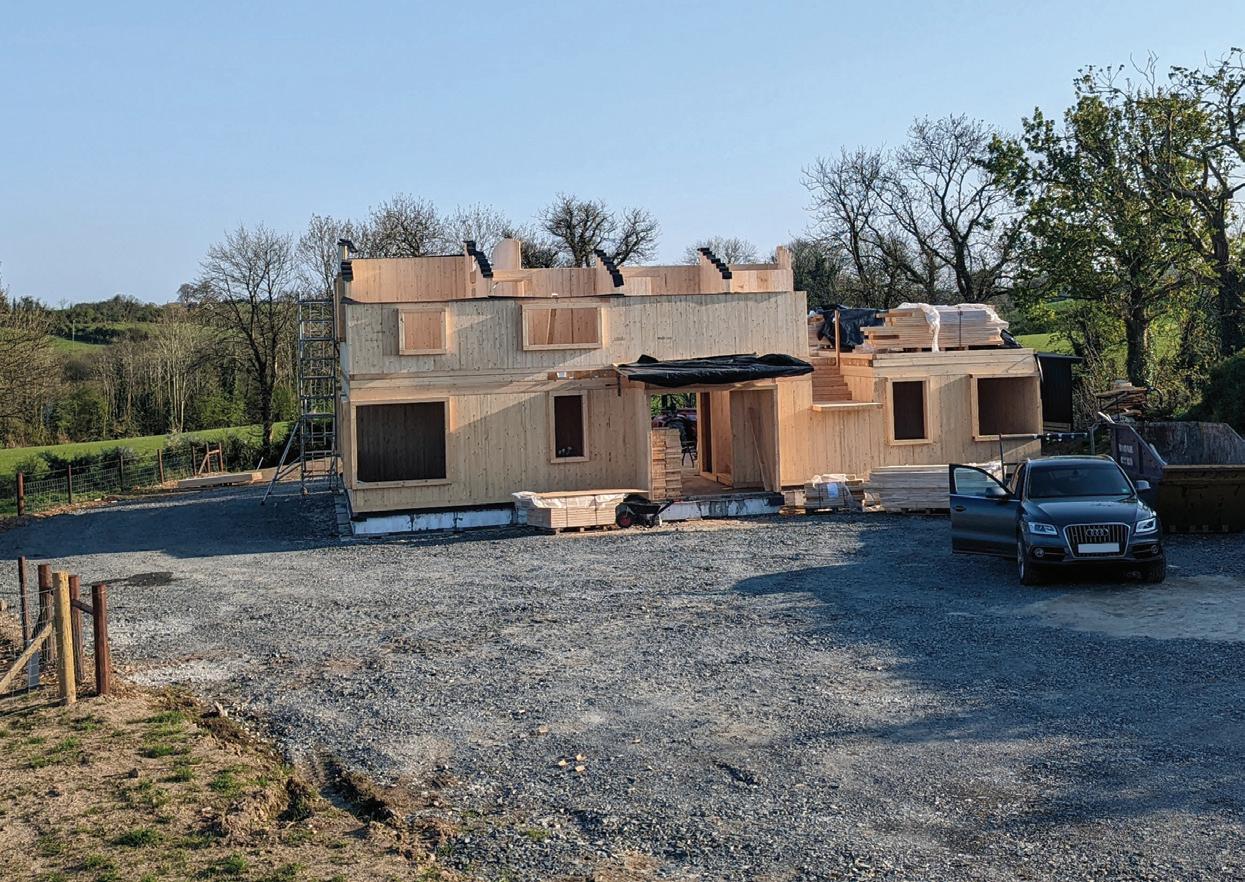
and she was right. But as the weeds started to spring up all over our foundations and we lurched from one lockdown to the next, I sometimes wondered if it ever would. It wasn’t until the autumn of 2021, with our business functioning once again, that we felt confident enough to proceed. However, financially we knew we wanted to sell our old home first and either rent or strike a deal with the new owners to stay on for a time. As it turned out we got extremely lucky with the purchasers who were willing to delay their occupation by eight months, giving us time to build the new house.
Cost and availability
The two year delay had not only cost us time, it also cost us a lot more to buy the materials as prices rocketed with the post pandemic inflation. Fortunately, we had locked in prices for a couple of the main items like the timber kit and the ventilation and hot water systems. But we were not so lucky in others. Everything from the roof system to the insulation and fixings were costing at least 50 per cent more than in 2020 and the lead times for ordering some items were startling. We took the decision in early 2022 to identify materials that might be hard to get and place an advance order so that we could be sure we would not be delayed on site. A large part of this was speaking with suppliers and finding out what products had the longest lead times (how long it would take them to deliver the item after we placed the order). Ultimately this turned out to be an important decision and having sold our house the previous year, we were lucky to have had the cash to be able to do this. The mortgage company only released funds at fixed stages during the build. There is no question that if we hadn’t purchased supplies in advance, we would never have achieved our move in date. Our wood fibre insulation was a good example. It used to take three to four weeks but even though we ordered in January 2022, it didn’t arrive until the end of April. Or three and a half months later. Similarly, when the roofing company came to install the covering they said that if we hadn’t ordered the coils of metal when we did, we could have been waiting another three to four months. Normally the lead time is a week or less. Other items proved impossible to get. We had to choose a slightly different colour cladding as the supplier could not get the stock in from Canada with the global shortage of shipping containers at the time.
Tracking prices and buying just enough
With prices rising throughout the build, it was vital that we buy materials at the best rates. I spent my evenings with the laptop on my knee contacting suppliers for quotes, placing orders and chasing up on deliveries. One thing I learned early on was the importance of contacting the builder’s
CO DOWN
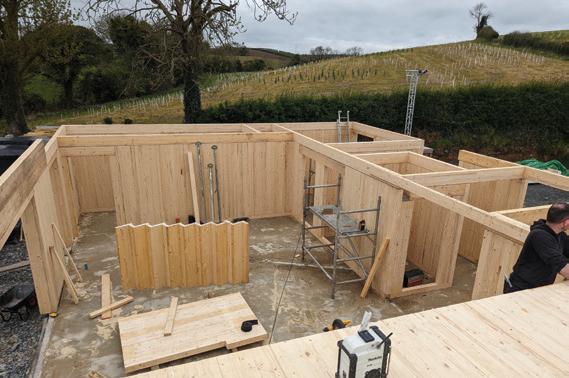
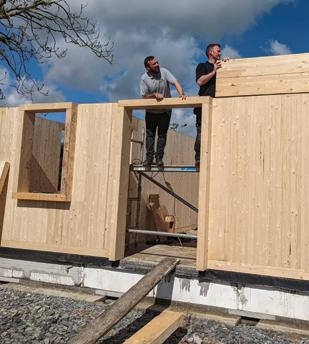

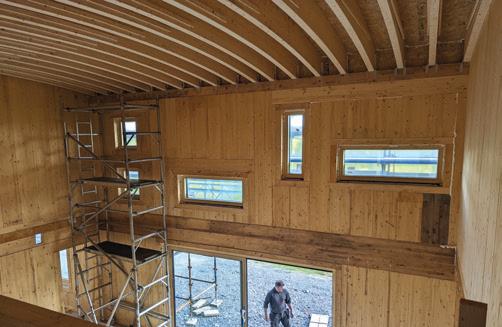
merchant’s sales representative to get the prices he quoted recorded on the self-build account I opened with them. Depending on the item, you could save up to 40 per cent on the retail price. On one occasion I went to get a load of 2’’ x 1’’ planed timber in 4.8m lengths with the deal price set by the rep. The store only had 5.2m lengths in stock, which I took instead. However, because the length was slightly different, I was charged the shop rate instead of the deal rate. To be fair they credited me the difference after I contacted them, saving me several hundred pounds for just that one item, but it proved just how important it was to get a price set beforehand and to then check the invoices afterwards. Knowing exactly how much to order is a real skill and I was keen to minimise waste. Waste is both costly, having bought something you then have to pay to get rid of, and not great for the environment. My lack of experience in building meant that I felt very much at a disadvantage when it came to judging how much material to order. There were some items where the risk was relatively low because there was plenty of availability, but other items such as insulation had an eight to 12 week lead time so we couldn’t afford to be short. Self-builders are probably more incentivised to reduce waste than contractors who tend to take the easier option and reach for a new piece instead of using up an offcut. Most times I ordered just slightly more than I thought we needed and nine times out of 10 this worked out. This thriftiness saved quite a bit of money and also greatly reduced the amount of waste that naturally occurs during any build. I was also careful to store and protect materials that were brought to site so that they could be returned for refunds if there were items left over.
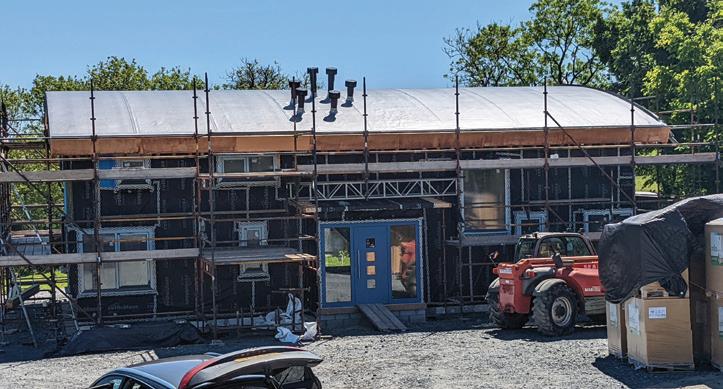
Getting stuck in
As material prices were going through the roof so too were the rates for tradesmen – if you could get them. I had originally lined up two local joiners to help with the build as well as a plumber and electrician. Despite keeping them regularly
NEW BUILD
appraised of the start date, I received a message from the joiners just before we were due to begin that they had taken on another job. The plumber said he was heading to Dublin on a three month contract. We decided then that I would take a more hands on role building the house, and I managed to find a local joiner who could commit to three days a week. I also got a couple of guys whom I knew through our business to provide additional help. Like me, they were not time served tradesmen but the type of construction we had chosen meant that this didn’t matter so much. We were very much a Jack of All Trades – Master of None crew! Despite our enthusiasm for the job, I was under no illusion about our ability to do some tasks and indeed I had arranged for a couple of Welsh joiners who had previous experience building with the HBE glulam kit timber we chose to come over for two weeks at the start to get the main structure up. There were other areas that required specialist skills such as the roof finish and electrics and so I only took on the jobs I thought we were genuinely capable of. Despite this assistance I was still ultimately responsible for all the decisions and works on site and ensuring things were done correctly. Any mistakes would be my fault. This was

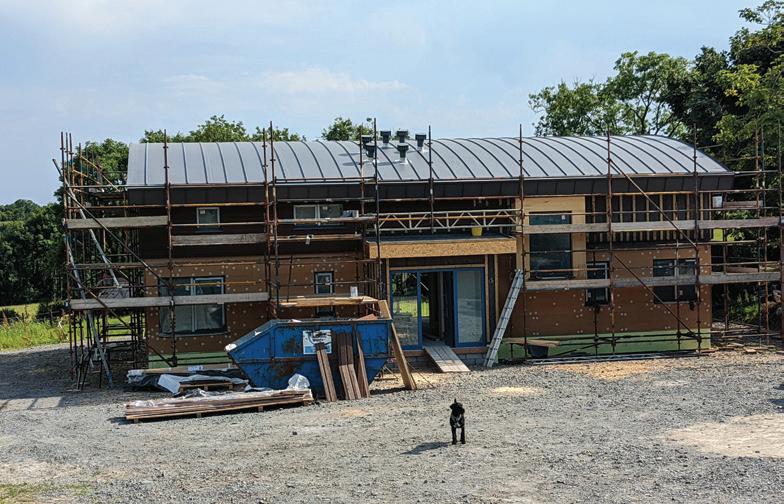
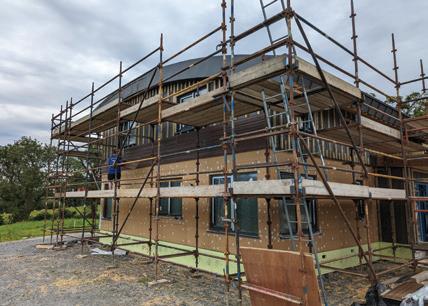
simultaneously scary and exhilarating. After six weeks of living in our new home we haven’t discovered anything major although I did find out that I had accidently plumbed the hot and cold water supplies to the bath the wrong way around – but that was easily rectified.
Planning the build schedule
One of the most challenging aspects when doing the build timetable was predicting how long each stage was going to take and this was primarily down to our lack of experience in managing a build, a position first time self-builders will be familiar with. We took every opportunity to speak to different people for their advice and based on that we drew up a schedule that we sent to key suppliers to pencil us into their calendar so that they had a rough idea when we might need them. This proved to be highly beneficial as we rarely had to wait long for them to finish up other jobs and come to us. There was also a certain obligation on them to turn up when they had known three months beforehand when they were likely to be needed. Every so often I would send them an email or a WhatsApp to let them know how we were progressing and reconfirming the date with them. Despite all the planning, Covid was not done with us. The sawmill in England that was CNC (precision machine) cutting the HBE timbers to the required lengths for our build got hit with Covid. Our build was due to start two weeks later. I had booked accommodation and ferries for the Welsh joiners and arranged transport to pick up the HBE panels from the sawmill in England and it all had to be cancelled and rescheduled for three weeks later – at significant cost. This was the biggest single delay we encountered and we were able to catch up most of it in the subsequent months. The only other delay we encountered was much later on in the project and it caused a substantial amount of trouble. Mid-June was scheduled for the drylining. After the first fix electrics, plumbing and ventilation installation. I had allowed two weeks for fixing the plasterboard and taping and jointing however this took twice as long as I had allowed for, in part due to contractor encountering the universal difficulty in getting skilled jointers and tapers at the time. The painter was due to come in immediately afterwards but this delay meant we were now into the July builder’s holidays and we had to wait another week before they could start. This was probably the most frustrating time of the whole build as we were supposed to be moving in at the end of the month (less than two weeks away) and we still had a lot to do. The finishing stages of the build was incredibly busy. Doors, architraves, skirting all had to be fitted. Kitchen units and bathrooms needed to be installed along with all second fix electrics. Floors needed to be laid and carpet fitted. I had to contact lots of suppliers and delay them for two or three weeks at short notice to wait for the painting to be completed. Most were fine and juggled things around for us and I guess if we
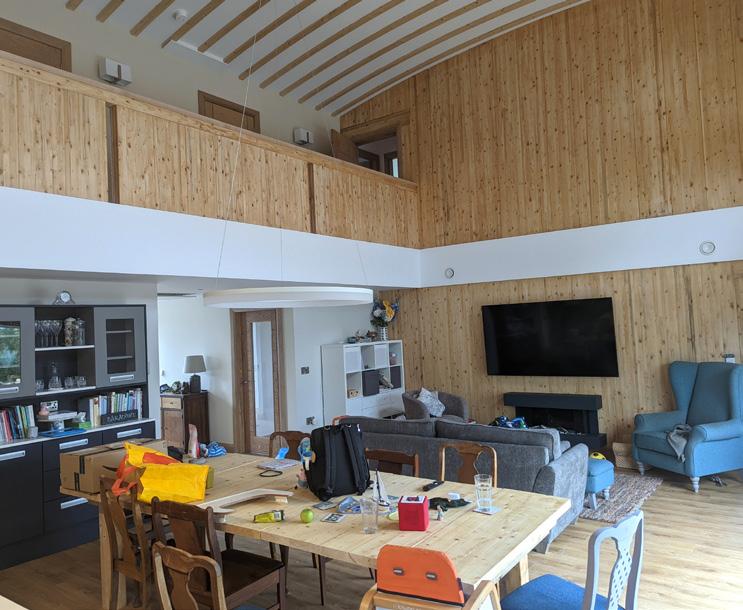
hadn’t had the deadline to move out, it wouldn’t have mattered so much. This episode demonstrated how some parts of the build process can have a huge knock on effect but yet the risk of this was not something I had identified in my original schedule and in hindsight I should have allowed more time.
Mastering the detail of everything
Over the course of the build, I found it pretty much essential to have a good understanding of the detailing for most things. This helped ensure that what we were about to do with one part wasn’t going to cause issues further down the line. At times it felt that I could barely leave the site for more than a couple of hours without getting phone calls. In fact one of the most surprising aspects of the build was the sheer number of queries that needed answered on a daily basis. Particularly when the main structure was up. I think this was undoubtedly exacerbated by the non standard HBE solid timber construction method we had chosen. In some instances we just had to work out what to do at the time but in others we had to adhere to very specific detailing. A good example was the installation of structural fixing screws on both the main structure and also for the roof beams and roof. These large screws (sometimes 600mm in length) needed to be applied at specific angles in a set pattern to conform to the engineer’s specification. It was essential that I understood completely what screws were needed and where, prior to starting the task as no one else was going to show me how to do it or tell me that it wasn’t being done correctly. It required constant checking with the rest of the team so it was absolutely
CO DOWN
essential I was on site 100 per cent of the time during this period. Naturally the suppliers and tradesmen working on site preferred to run everything past me instead of ploughing ahead. And I’m glad they did – but it was relentless. To avoid delays and errors it was crucial to spend time in the evenings reviewing the tasks that were coming up and familiarising myself with the detailing involved. This was something that was very difficult to do on site as inevitably I felt under pressure to make a quick decision with guys standing around waiting for guidance. It was much better to take the time the week beforehand and think it through with the help of Google and YouTube and work out exactly how it should be done so as to be knowledgeable and prepared for the task. On many occasions I contacted the product supplier directly with queries on installation and their advice was usually very useful. It gave me considerable confidence when the time came to do the job, that it was being done correctly and more importantly it allowed me to show the rest of the team exactly how it should be done rather than just guess. The quality and accuracy of the detailing will determine whether the house is both weathertight and airtight and a small error in installation can lead to huge problems further down the road. So all in all, would I do it again? We’re in six weeks and are really enjoying all the benefits of having a house that we designed for ourselves, from the little things like being able to put away 99 per cent of the contents of the dishwasher without moving our feet to enjoying the benefits of a wonderfully social and atmospheric main room that we use 90 per cent of the time that we are awake. So even though I’d absolutely take on another project, I hope we don’t ever have the cause to move.
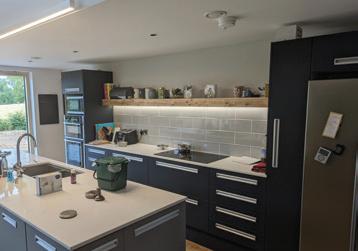
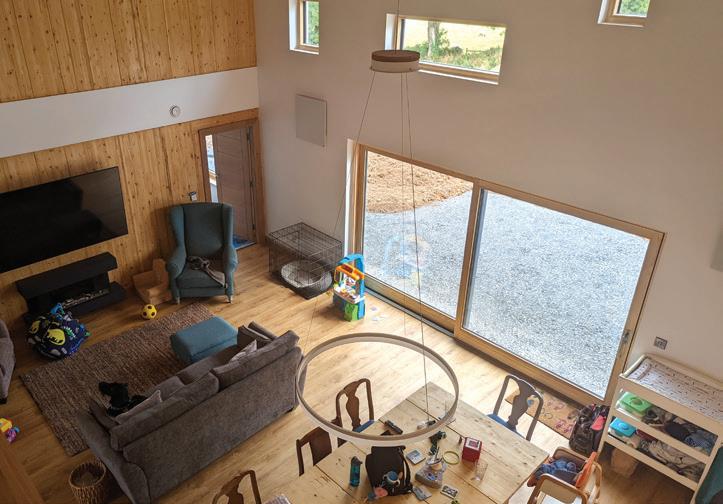