
7 minute read
BUSINESS OPERATIONS-Legal Protections for Project Delays
By Denise M. Motta, Esq and Corey J. Taylor, Esq
Legal Protections Related to Project Delays and Acceleration
Many legal issues face subcontractors on construction projects, and subcontractors in the steel construction industry are some of the hardest hit. Often their scope of work is a large portion of the project budget and steel erectors are one of the first trades on the critical path.
Current legal disputes trends affecting erection subcontractors include delay and acceleration of project schedules, supply chain issues, force majeure, and the new hot button item: tariffs.
Delay claims in the construction industry occur when the work on a construction project has not proceeded pursuant to the project’s work schedule. These delays often arise from circumstances that were unanticipated by the parties when they entered into their contracts and often result in the construction work being extended or, alternatively, accelerated in order to get the project schedule back on track. As a result, delays often add an additional layer of difficulty and frustration for parties involved in the modern, complex construction industry.
All construction delays can be categorized as either excusable or non-excusable. Generally, excusable delays are those that are: (1) beyond the control of the subcontractor; and (2) unforeseeable to the subcontractor. For a subcontractor to have a right to be compensated for delays, the subcontractor cannot be responsible for the delays.
Generally, the remedy for excusable delays is the granting of a time extension. Specific examples of excusable delays are often enumerated in contract documents, such as owner changes or force majeure.
Delays are considered non-excusable when they occur due to actions or negligence by the subcontractor, its sub-subcontractors, or suppliers at any level, or arise from risks assumed by the subcontractor under
the contract. Because these delays may be caused by negligence or poor performance, they are considered controllable.
Non-excusable delays are usually rooted in at least some of the following causes: improper scheduling, ineffective site management, incorrect methods of construction, delayed performance in overall activities, and poor monitoring and control.
When delays are compensable
A subcontractor is entitled to an extension of time and additional money as compensation for a compensable delay. In general terms, a delay is compensable to a subcontractor only if the delay is caused by someone upstream and the subcontractor has not waived its right to compensation in the contract. For example, if a subcontractor is delayed by unusually severe rain showers, it would be a non-compensable, excusable delay, leaving the contractor with a time extension, but no compensation. However, if the owner failed to provide a contractually required cover that would have allowed the work to proceed despite the weather conditions, then the delay becomes compensable because the owner had control over the potential delay.
A subcontractor can waive its right to compensation
for owner-caused delay in a “no damages for delay” clause, agreement that the only remedy for delay is a time extension, or waiver of consequential damages.
Subcontractors should carefully review contract terms to allow for a time extension and compensation for compensable delays.
Compensation for acceleration
When a subcontractor is required to meet new or shortened deadlines, they are accelerated. To avoid lost overhead and profit, subcontractors can protect their interest by including contract provisions that contemplate acceleration and provide additional compensation. One key aspect of an acceleration claim is to request a time extension. When the duration in the schedule is shortened or sequencing changes, the subcontractor should immediately provide notice to the contractor and request a time extension. This will set up a constructive acceleration claim, which is compensable.
If acceleration is directed by the contractor (or the schedule is changed), the subcontractor should work with the contractor to get an agreement upfront on the equitable adjustment for the directed acceleration. On the other hand, if the subcontractor voluntarily accelerates its work, the subcontractor is not entitled to compensation.
Subcontractors should watch for contract clauses that allow the contractor to change sequencing or the project schedule without compensation and try to negotiate language that allows the contractor to seek a change order in those circumstances.
Mitigating supply chain woes
The COVID-19 Pandemic brought to light the potential severe impacts arising from supply chain delays. The potential for supply chain issues remains in our current environment due to volatility surrounding the effect tariffs may have on the supply chain. Most contracts do not accommodate time extensions due to supply chain impacts.
To address this gap in contract terms, subcontractors can include language such as: “lack of or failure of or other inability to obtain necessary transportation, fuel, power, materials, machinery, equipment or facilities, delays caused by other contractors, subcontractors or their subcontractors of any tier, or any materialmen or suppliers” as part of the defined force majeure events under the contract.
Steel erectors should be cognizant of potential supply chain issues and make sure that the contractor is aware that it will be impacted by supply chain issues.
Tariffs, the supply chain, and schedules
New and increased tariffs on imported goods into the United States have made an immediate impact on the steel industry, as
about 25% of steel is brought in from around the globe. Talks of additional increases in tariff amounts along with which nations will be taxed have fueled uncertainty in the marketplace and most of all, increased prices for materials. While tariffs may not directly increase erection costs, supply chain issues associated with tariffs could delay the erection schedule and increase costs.
It is recommended that subcontractors have ongoing communications about any potential issues arising from tariffs that may delay the erection process. As an upfront protection, subcontractors should consider limiting the time that proposals are open (30 days or less) or establish a sunset date to allow for adjustments. If asked to extend the time a bid is open, reconfirm prices before agreeing.
Also, an erector can reduce risk by making it clear that the bid is based on performing the work during the designated timeframe and pursuant to the erection window set forth in the current project schedule only, as well as including terms in the contract that allow the erector to seek a change order for any of these impacts.
Force Majeure
A force majeure event is defined as an unforeseeable circumstance that prevents someone from fulfilling a contract. A Force Majeure provision will provide protection for unforeseen events. Look for a clause like this:
Any failure or omission by Owner or Contractor in performance of its obligation shall not be deemed a breach or create any liability for damages or other relief (other than additional time) if it arises from any cause beyond the reasonable control of such party, including, without limitation, acts of God, floods, fire, explosions, storms, earthquakes, acts of public enemy, war, terrorism, rebellion, insurrection, riot, sabotage, invasion, epidemic, quarantine, strikes, lockouts, labor disputes or other industrial disturbances, or any order or action by any governmental agency, or causes of similar nature.
In most circumstances, upstream contracts will have a Force Majeure provision, which will flow down to the subcontractor. However, inclusion of a clause in the subcontract will ensure protection in the event of an unforeseen event.
Project delays and acceleration continue to be legal issues that subcontractors face on construction projects. Supply chain, tariffs, and force majeure events all play into the potential for delays and acceleration and may culminate in additional costs and time. It is best to address these risks at the outset by including clear contract terms. If there are impacts, it is essential that subcontractors provide immediate notice and request an equitable adjustment of both time and money. •
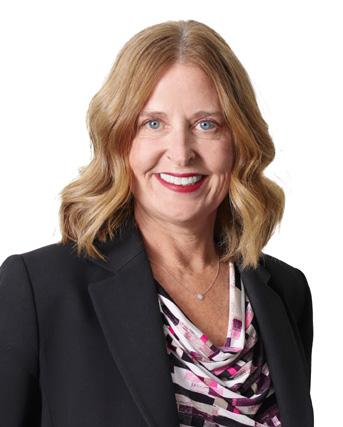
Denise M. Motta is a partner in the Louisville office of GRSM50. In addition to representing steel subcontractors nationwide, Denise is a Panel Member for the American Arbitration Association, serving as a mediator and arbitrator for construction and commercial disputes. She has 30 years of experience and regularly advises clients on contract negotiation, change order disputes, and delay and acceleration claims.
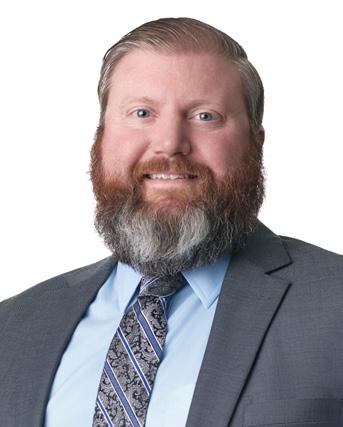
Corey J. Taylor is an associate in the Louisville office of GRSM50. His practice focuses on representing steel companies across the United States in mediation, arbitration, and litigation in a variety of disputes. Corey also assists clients in reviewing and revising contracts to reduce and avoid risk should a dispute arise during a project.