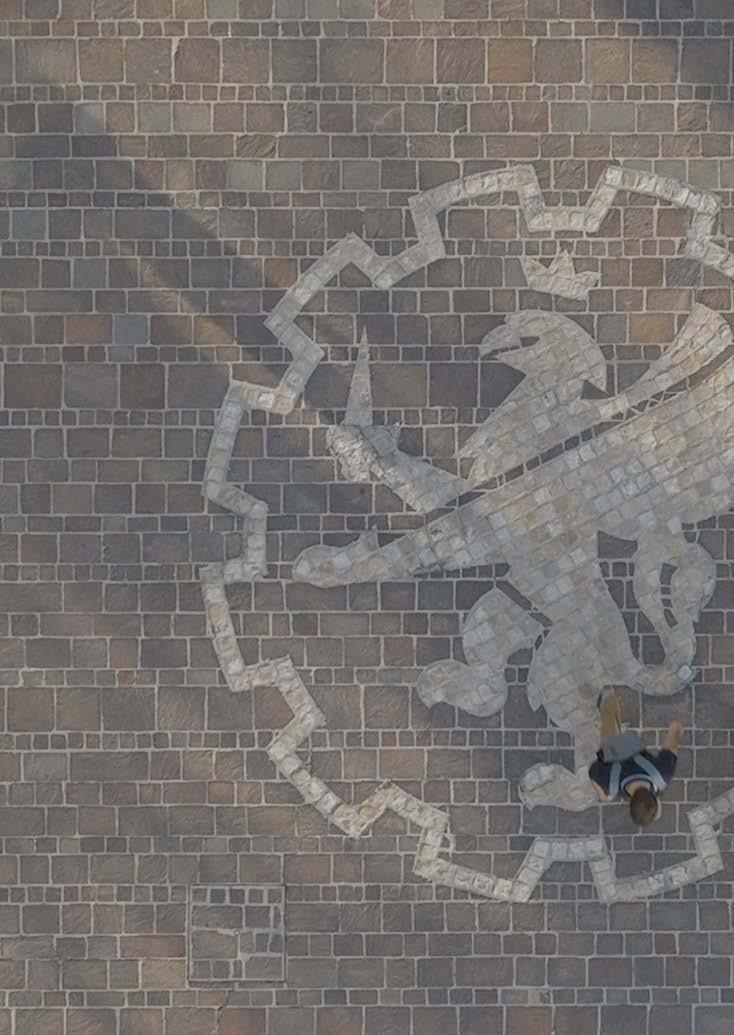
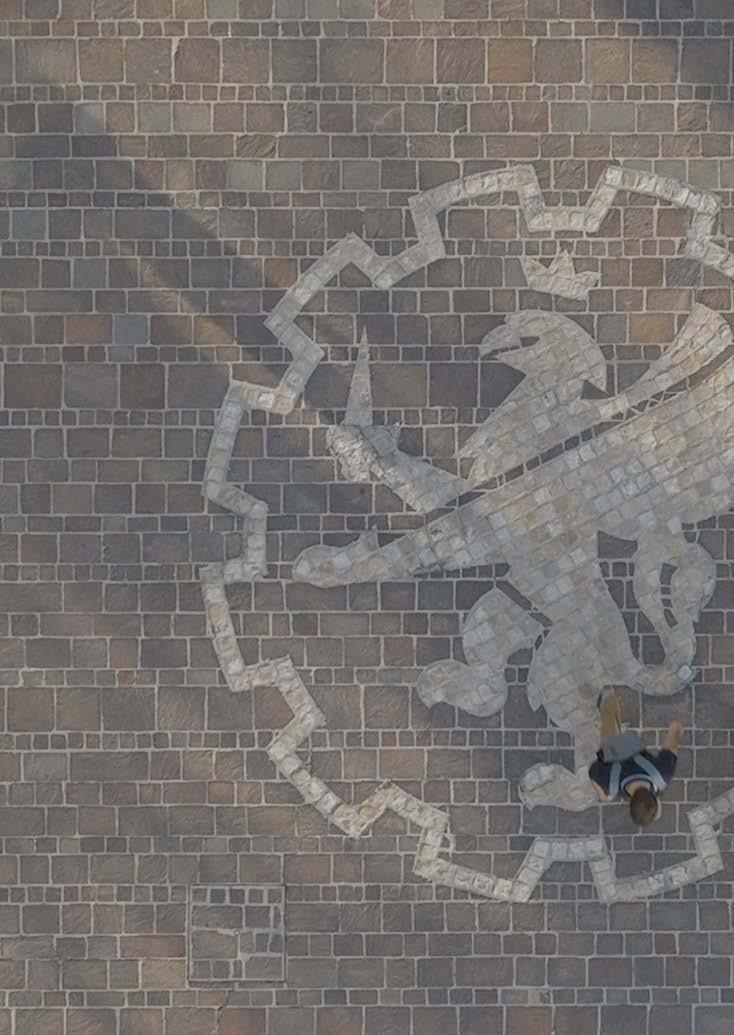
Integrated Annual Report 20 23
Letter from the President
The year 2023 marked a change of pace in the SACMI story. The strong volume growth seen over the last three years resulted in a scaling-up of the Group, with consolidated revenues breaking the 2 billion euro threshold, the best result ever.
In 2023, SACMI strengthened its reputation and leadership by investing in new products and skills, and by taking customer support facilities and services to the next level.
The achieved result is particularly encouraging when one considers the unstable macroeconomic and geopolitical backdrop, which has necessitated continuous adjustments to strategy in order to mitigate business risks, provide customers with optimal service and identify, together, new growth opportunities.
Key contributing factors to the excellent operating result included a continuation of the strong economic recovery that began in 2021 and gathered pace in 2022. For the first six months of the year, order acquisitions proceeded apace, allowing the company to achieve systematic growth and engage in orderly operational management.
The second six-month period proved to be stormier as a combination of factors - high interest rates, persistently high energy prices, the Middle East crisis - inevitably impacted the market, slowing or postponing customers' investment decisions and raising new questions about both macroeconomic and geopolitical medium-term scenarios.
Component procurement regained fluidity in 2023. In parallel, careful planning and monitoring of orders kept project lead-times under control,
maintaining customer satisfaction levels and coupling manufacturing requirements with balanced finances.
Early 2024 was, again, characterized by remarkable complexity. Alongside the expected investment slowdown in some sectors (e.g. ceramic plant engineering), demand remained stable across other SACMI businesses, as did the acquisition of new orders. The high degree of internationalization and cross-industry diversification have stabilized SACMI’s long-term performance and constitute effective risk mitigators.
Within the reporting boundary, Capex and R&D expenditure are expected to remain consistent as part of an innovation strategy that focuses on digitalization and environmental sustainability. That strategy aims to make SACMI technologies and processes increasingly green, automatic, flexible, resilient and capable of effective interaction with end markets
In this context, 2023 further strengthened the fundamentals of the SACMI Group, ensuring the solidity that is vital to further development and instilling confidence in the future as our 105 th anniversary approaches.
“Inaugurate your sustainable factory”
From a Sustainability Reporting perspective, 2023 saw the tasks of measurement, control and strategic governance move another decisive step
closer to the CSRD (Corporate Sustainability Reporting Directive) standards that will come into force in 2025.
The year 2023 also involved an expansion of the ESG (Environmental, Social, Governance) performance reporting boundary beyond the Italian companies of the SACMI Group to some of the main foreign companies, in particular our production sites around the world; by 2024 the scope is expected to extend to the entire Global Network. For a complex, highly internationalized organization like SACMI, the goal we’ve set ourselves is ambitious: we aim not just to define a coherent sustainability performance reporting logic for all SACMI companies but also to strategically link it to daily planning/strategizing within the individual Businesses.
To enact this, in 2023 SACMI established the Corporate Innovation Management team to align SACMI innovation strategy with the drivers of digitalization and sustainability, the emphasis being on professional development, skills enhancement and infrastructure. On the other hand, an extension of the ESG perimeter has expanded the resources and professional capacities available to our corporate Green team’, set up in collaboration with the Imola Board and other managerial bodies. The team currently includes 128 people.
This collective effort is also reflected in the sustainability messaging. A good example of this was the extension of the Up To Us campaign to all SACMI businesses. This now covers all sustainable practices aimed at customers (the machine range, systems, services that help reduce consumption, raise efficiency and make factories healthier and safer) and policies designed to make our manufacturing sites (the parent company in Imola and all other SACMI companies in Italy and worldwide) sustainability trailblazers, fully aligned with international best practices.
The formula “Inaugurate your sustainable factory” was chosen to promote the consultancy services SACMI provides to customers. Such consultancy ensures sustainability is implemented effectively, profitably and in alignment with plant digitalization to take the market towards higher green standards.
As per SACMI standard practice, the bulk of the
effort was directed at translating these principles into first-time technologies, tangible results that we previewed during the year. Perhaps the best such example was the first tile to be fired in a kiln that is 100% hydrogen-fueled. Moreover, developments in the packaging sector - where SACMI works alongside major global brand owners to implement a 3Rs (reduce-reuse-recycling) strategy - produced the first practical solutions from a D4R (design for recycling) perspective. With digitalization confirmed as a strategic factor - and a prerequisite for ‘practicing’ sustainability2023 also saw Artificial Intelligence driving the development of new ‘Industry 5.0’ investment opportunities based on collaborative logic between humans, machines and systems
Financial performance
The 2023 income statement was the best in the SACMI Group’s entire history.
In 2023, consolidated revenues exceeded €2 billion this figure comprises revenues generated by BMR, which was included in the consolidation area last February following its complete takeover by SACMI Imola. This figure confirms forecasts and is 12% higher than its 2022 counterpart.
Operating margins also improved significantly, ending the squeeze caused by the post-pandemic inflation shock and generating satisfactory EBIT and EBITDA.
At the end of the year, the Net Financial Position (NFP) was positive at 53 million euros, net of the effects of the BMR takeover. After 2022, the year 2023 again saw sub-optimal cash flow on account of the significant number of orders still in progress. This was highlighted by the level of warehouse stock. In 2024 stabilization of production volumes will allow progressive conversion of the Net Working Capital (NCC) accumulated over the last two years into cash, making for a healthier NFP. Control of NCC dynamics to protect operating cash flows remains central to management strategy.
In July, SACMI Imola stipulated a €75 million MLT loan with Cassa Depositi e Prestiti to purchase the remaining 80% of BMR. Given their considerable market shares and a demonstrable ability to
influence ceramic slab/tile trends, SACMI and BMR - and their technologies - are acknowledged as playing a decisive role in keeping ‘Made in Italy’ ceramics competitive. The merging of BMR into SACMI strengthens the entire Italian ceramic system by boosting its qualitative advantages and uniqueness.
In general, the Group continues to enjoy a solid financial debt structure, oriented towards the medium-long term and mainly characterized by fixed interest rates. At the end of the year, Net Equity stood at 883 million euros, a further improvement on an already-impressive 2022 figure. In addition to the complete takeover of BMR, other major operations during the year included the establishment of SacmiCassioli Intralogistics, a joint venture between SACMI and Cassioli that supplies plant logistics automation solutions worldwide.
Looking to a 2024 that, despite multiple sources of uncertainty, aims to stabilize the key financial performance indicators, it will be crucial to continue investing heavily in innovation, also - indeed, above all - to achieve R&D goals that make production processes more environment-friendly.
Markets and trends
End-of-year indicators were positive for all SACMI Businesses. In most cases, the results were the best ever both in terms of machine sales and the increasingly important area of spare parts sales and after-market services.
An exceptional recovery in 2022 and the large backlog of orders and projects undoubtedly contributed to the result. Simultaneously, the market has rewarded SACMI's ability to respond to new needs by providing ready-to-use innovations that offer customers tangible, measurable advantages. For example, in the Rigid Packaging sector SACMI has been delivering ready-to-use solutions for some time to help the market transition towards the new tethered standard.
System digitalization has again proved to be a valuable cross-business driver. This is coordinated by the Digital Innovation & Automation HUB, which has now instituted the figure of the Digital Business Agent to impel digital innovation within individual SACMI Businesses and translate it into products/services that meet new market needs.
In terms of scenarios and trends, 2023 closes a two-year period of uninterrupted growth following the recovery begun in 2021. Consequently, the market is suffering from a (cyclical) slowdown in investment in some sectors that now have overcapacity (e.g. ceramics); in parallel, though, it continues to reward SACMI products where they deliver product, process and service innovation
At global level, China has posted below-expected growth rates despite its confirmation as an increasingly important market, also with a view to the direct manufacture of machine or system parts.
India is performing well: a steadily growing middle class is driving demand for high-quality products in various sectors (home, food, etc.).
The decision to invest in Africa is revealing itself to be a far-sighted one: double-digit growth continued into 2023, making it, in fact, the Rigid Packaging Business's leading market. Signs from Europe are more contrasting. The major players continue to go for the ‘premium’ SACMI range, albeit against a backdrop of high interest rates, persistently high energy costs, and uncertainties linked to the winding-down of the post-lockdown manufacturing incentives implemented by governments in several countries.
SACMI technology, innovation and service have gone from strength to strength in the Americas especially in Brazil, Argentina and Mexico, but also in the USA and Canada, where SACMI is set to build the world’s first zero-impact sanitaryware plant.
With regard to plant digitalization/automation strategy - also a key factor in making processes more environment-friendly - 2023 saw advances with many of the proposed innovations (e.g. systems that reduce in-factory water requirements or automate further stages to improve workplace health and safety).
SACMI's work in the Energy sector is increasingly strategic, both in terms of results achieved and prospects. All-round solutions have been developed, ranging from the design and management of renewable energy power plants to Protesa’s broader role as an Energy ‘Competence Center’ in support of SACMI Businesses.
Continuing an already-observed trend, 2023 saw the development of new after-market businesses and services. This was achieved both by strengthening teams and on-site facilities and by making the most of opportunities provided by the latest digital tools; the latter include the new scheduled plant maintenance assistance packages, increasingly popular with customers thanks to the evident advantages they deliver in terms of efficiency, cost control and resource optimization.
Employment and training
Another trend that continued into 2023 was steady growth of the workforce. The SACMI Group now employs more than 5,200 people, +8% compared to 2022.
This expansion has occurred throughout the Global Network and is particularly evident in the lower age brackets, with more than 50% of new hires in 2023 aged under 30. This policy - alongside high levels of employee loyalty and low employee turnover (<6% in Italian companies) - favors the inter-generational development that has always been a SACMI hallmark.
Investment and man-days dedicated to Research and Development continued to rise in 2023, as did the number of patents. At Group level, almost 6,000 (5,970) patents have been filed: that’s more than one per employee. In 2023 alone, 272 new inventions were registered.
The SACMI Academy remains vital to the skills enhancement strategy. The 70,517 training hours that involved both Italian and network companies marked a significant increase in the number of training hours provided (+32% on 2022) and the average training hours (17 per employee, +31%).
The 22,200 hours of Health, Safety and Environment training brought the total to nearly 93,000 hours
The Academy’s role as a training hub, not just for employees but also customers, partners, schools and universities, continues to expand. In 2023, it again acted as a 142-strong in-company ‘nursery’ made up of thesis students, doctoral students, research fellows, interns and those collaborating on ITS and local degree courses.
Communities and the Planet
Over the last 3 years, SACMI has allocated 1.9 million euros to local and international charity projects, mainly in health, assistance and education. The parent company SACMI Imola’s main initiatives included a major donation to the Casa Gialla project run by Ageop Ricerca, which has been at the forefront of pediatric oncological research, treatment and support for over 40 years.
Integrated Annual Report 2023 / Letter from the President
Taking a network-wide perspective, pro bono projects focus on people’s dignity, starting with their basic education and healthcare rights. Every year, ongoing attentiveness to the needs of communities - in collaboration with the main associations and voluntary organizations that operate in them - results in several projects being enacted.
In 2023, SACMI again took an approach that favors local suppliers, thus strengthening local industry and nurturing long-term partnerships. To cite a key figure, it should be noted that, in 2023, the SACMI Group purchased goods and services valued at approximately 1.28 billion euros and that 89% of that expenditure involved suppliers based in the region/country where the relevant SACMI headquarters is located.
Last but not least, we can also confirm that the environmental profile of our manufacturing sites improved further in 2023. SACMI has reduced its dependence on non-renewable energy sources (-9% natural gas consumption, +10% self-produced electricity), reducing direct emissions by 9% and greenhouse gas emissions by 8%. Water usage (-9%) and waste production (-13%) are also down.
This progress is set to continue in 2024, in parallel with the definition of the Group Sustainability Plan to be drawn up on the basis of strategy and in accordance with application of the CSRD Directive.
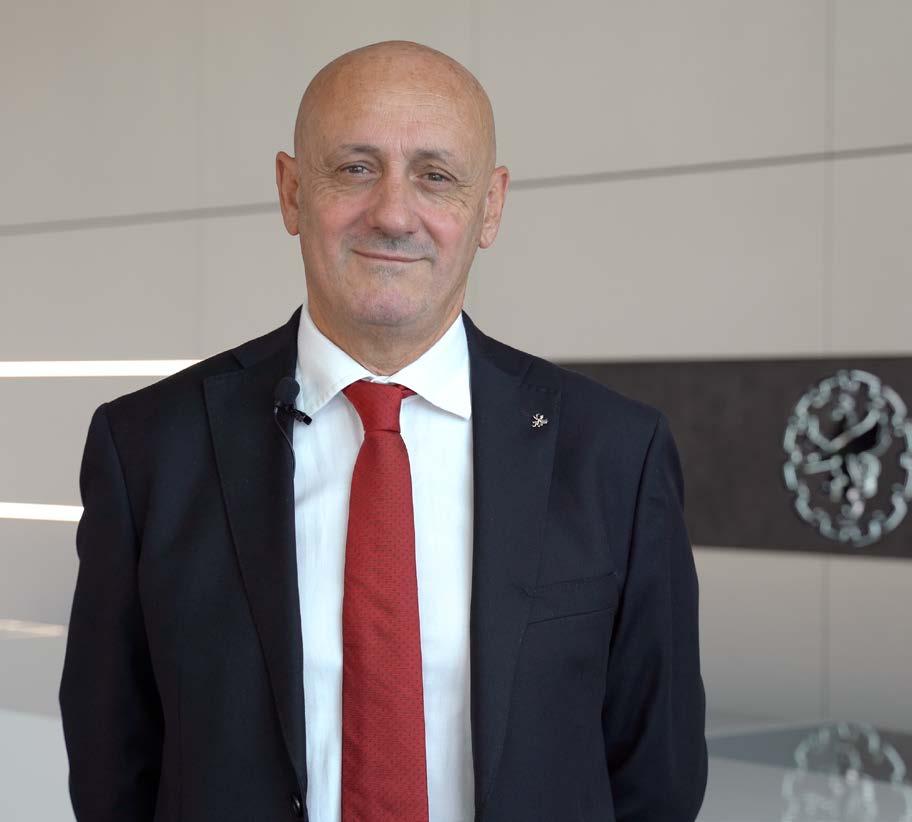
“The
2023 financial year saw a strengthening of the SACMI Group’s economic fundamentals, instilling confidence and encouragement for the future.
Solidity will be a must for further development.”
PaoloMongardi
Presidentof SACMI Imola SC
CHAPTER 1
SACMI
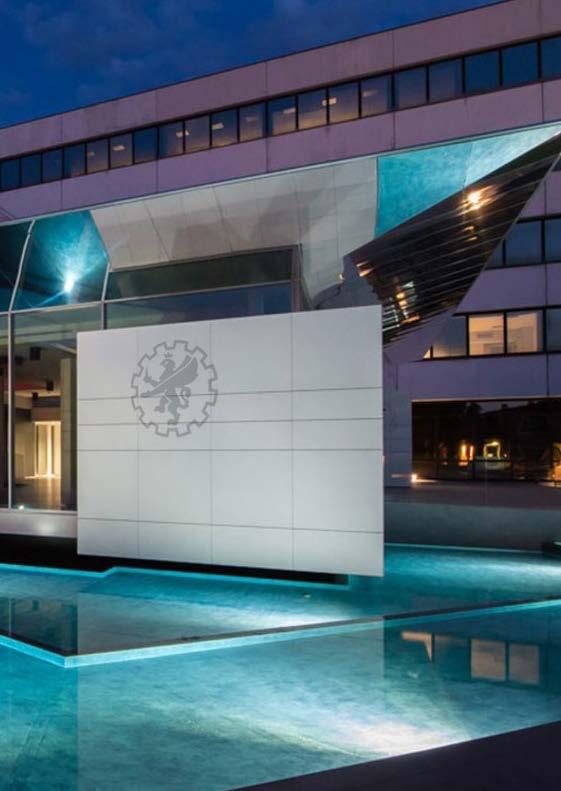
SACMI Group
SACMI is an international industrial group with a daily mission to improve people's quality of life. It accomplishes this by providing solutions with high-tech content that help everyone meet their basic needs
Our story
SACMI was founded in 1919 in the town of Imola, Italy, on the initiative of 9 young mechanics and blacksmiths united by the same ideal: work as a means to improve their social standing and that of the community. This happened at an extremely difficult time for Italy. The First World War had ended and there was a severe economic crisis, with high unemployment and inflation.
From its origins as a workshop for ‘small mechanical repairs’, the 1930s saw SACMI produce its first own-brand machines, mainly for the nascent agro-industrial sector. During the bombing of the Second World War, it was our own workers who risked their lives to save the machines and equipment. Later, in an Italy liberated from German occupation, SACMI was the one of the first companies to get back on its feet.
SACMI was founded in Imola (Italy) in 1919, on the initiative of 9 young mechanics and blacksmiths.
From its origins as a workshop for ‘small mechanical repairs’ it has grown to become a global industrial Group with 73 manufacturing, distribution and service companies in 27 countries
Between 1948 and the early 1950s SACMI developed two key innovations that would make company history: the first ceramic press and the first complete machine for crown caps Years of intense development followed as SACMI worked alongside the growing Italian ceramic and packaging industries. Our vocation for ‘plant engineering’ began to take root. This saw the development of comprehensive solutions, from raw material to finished product, especially in the ceramic sector. Expansion into foreign markets began, with the first branches opening in Spain and Brazil in the 1960s. Other branches and foreign offices would soon follow across all Group businesses. By 1963, exports were already accounting for more than 50% of revenues.
In 1989 the SACMI Research Center was established. Between 1990 and 1994, SACMI developed compression technology, which would go on to be the world’s leading plastic cap manufacturing technology, flanking the historical crown cap business. With the development of preform machines, bottling lines and labeling machines, this put us in a position to supply complete plants to the packaging sector too.
The 2000s saw SACMI enter new areas, such as chocolate processing and packaging machines. In 2008 we entered the Metal Powder sector, the first step towards a strong, well-organized presence in the automotive sector. Expertise in ceramics continued to grow, resulting in the launch of Continua+ technology, now the global benchmark for slab and sub-size forming. In parallel, SACMI developed Deep Digital, a new approach to digital, integrated control of surface decoration/glazing.
This was followed by the creation of a Business Unit that focuses on developing Advanced Technologies and Materials: the aim was to make the most of skills already acquired by the Group and intercept new opportunities for growth, especially in sectors linked to electric mobility and high-performance components.
The 2020s see SACMI pushing ahead with investments in process automation digitalization and sustainability . For example, the ‘circular economy’ concept is being approached from a plant engineering perspective. This involves the development of systems for full recovery of raw materials and water purification. In parallel, a complete re-think of thermal processes focuses on alternative fuels and efficient heat recovery so that individual machines or even entire plants can run on ‘zero fuel’. Such activities go hand in hand with the Research & Development of eco-sustainable materials (e.g. in the packaging sector) and the technological progress needed to implement the transition to a greener industry. Alongside digital innovation, which cuts across businesses, SACMI supports important investments in core businesses, in particular in completing the offer in the ceramic end-of-line and intralogistics.
The year 2023 and, to an even greater extent, 2024 mark the emergence of Artificial Intelligence as a key SACMI investment driver: here, new opportunities are being explored both at individual machine level (management and maintenance, quality control, Customer Service) and to take plant design towards an "Industry 5.0" model based on collaborative human-machine-system logic.
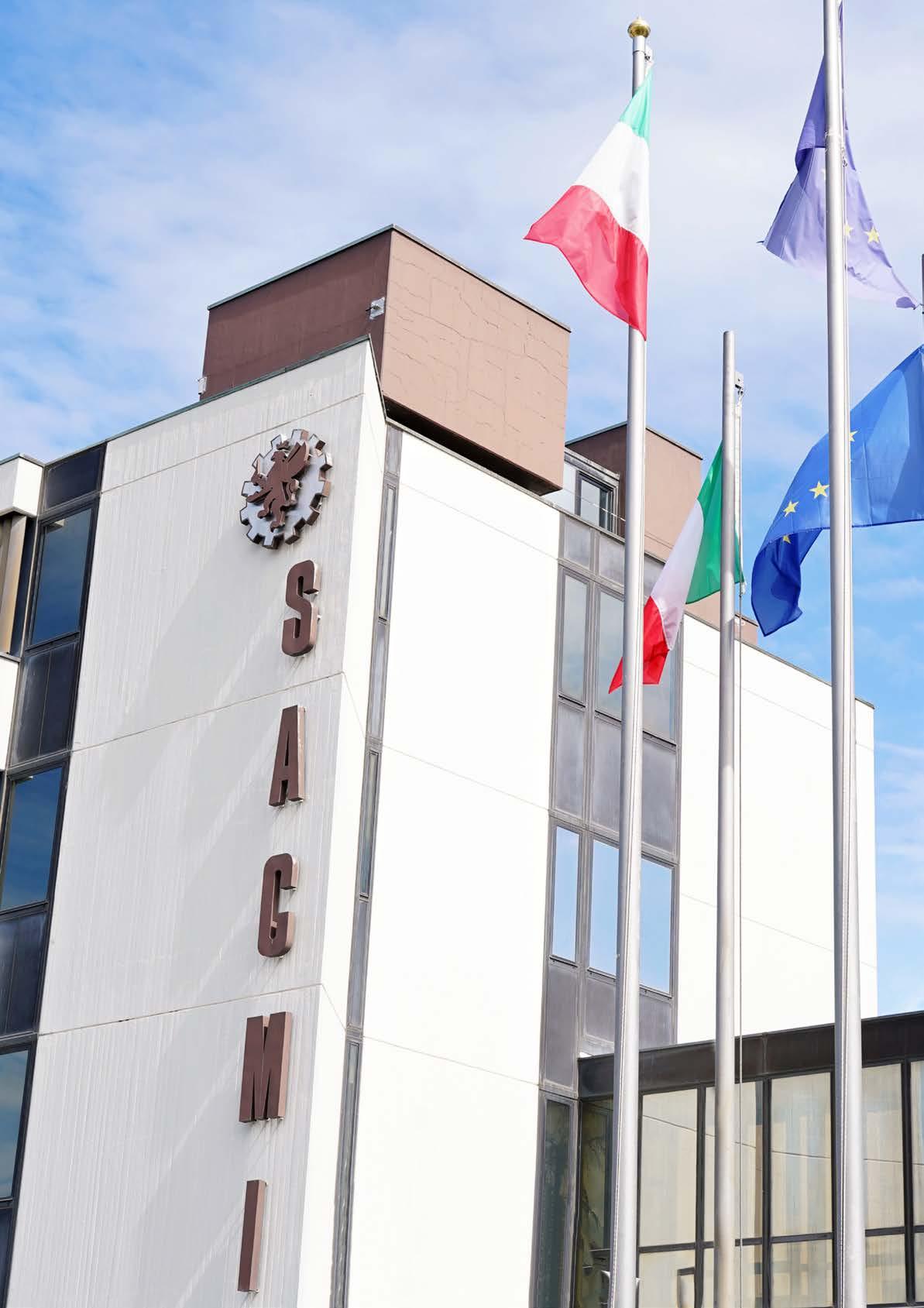
It’s up to us to protect the future

vision
Ensuring the company handed to future generations is an even better one.
mission
Research and innovation
We invest in cutting-edge research, driving technological innovation.
Quality
With a sharp focus on product and service quality, we provide effective answers to the real needs of global markets.
Synergy
Our flexibility lets us make full use of technological synergies and implement operational integration across widely differing industries.
Sustainability
Our Group drives economic growth by creating solutions and projects that prioritize the global community and the protection of the planet.
Loyalty and integrity
We take pride in our openness and transparency. Discussions are in-depth, decisions taken together, promises maintained. We play by the rules, putting people and communities first.
Freedom with responsibility
We’re free thinkers with an entrepreneurial spirit, we take the initiative and take responsibility for the results of our work. If we make a mistake, we see it as a valuable learning opportunity.
Innovation
We’re guided by a passion for research and innovation.
Partnership and cooperation
We build long-term, mutually respectful, rewarding business relations with customers by working together. Working together because together we’re stronger.
Belonging
Our roots run deep, yet our vision is decidedly future-focused.
SACMI: a global presence
Dialogue with stakeholders and materiality analysis
SACMI sees its relationship with all stakeholders as crucial to both business and the value creation process. The term ‘stakeholders’ refers to all those internal and external subjects who interact with SACMI on a daily basis and have a specific interest in attaining the organization’s goals from an economic, environmental and social perspective.
Relations based on dialogue and continuous involvement reflect the company’s sense of responsibility with regard to the communities with which it interacts and its wish to create shared, lasting value. Accurately identifying one's stakeholders through the ongoing monitoring of expectations, needs and opinions provides a solid basis for an effective engagement process.
Stakeholders are those subjects on which an organization depends for its survival: for SACMI these are its members, employees, partners, suppliers, customers, public institutions, the academic and research world (including universities and schools), professional associations, other industry-related operators, trade unions, the media, and the local and international community.
SACMI takes a proactive approach towards a plurality of worldwide interlocutors. It promotes constant dialogue to listen to their needs, as it is
acutely aware that such discussions provide mutual opportunities for growth and development.
As part of ESG auditing, materiality analysis aims to identify environmental, social, economic and governance aspects considered relevant and significant for SACMI's businesses and its stakeholders
In recent years, several standardization and regulatory bodies have expanded the concept of materiality within an ESG context. More specifically, the Corporate Sustainability Reporting Directive (CSRD), approved in late 2022 by the EU, and the International Sustainability Standards Board (ISSB), recently established by the International Financial Reporting Standard (IFRS) Foundation, refer to the double-materiality concept.
SACMI has therefore chosen to conduct an initial analysis of dual relevance by mapping and quantifying not just the impacts (positive or negative, actual or potential, short- or long-term) that its activities might directly or indirectly have on the environment, people and human rights (Impact Materiality), but also the risks and opportunities that ESG aspects can exert on its resilience, performance and Business Continuity (Financial Materiality).

Professional associations and media
Specifically, 16 potentially material issues and the impacts associated with them were identified beginning with the material topics identified in 2022, as per the main international standards and frameworks adopted in sustainability reporting (GRI Standard, SASB, TCFD, ESRS), and by way of two workshops involving the main corporate areas. These topics have, traditionally, been grouped within seven sustainability areas Governance, Environment, Human Resources, Economic Responsibility, Suppliers and Partners, Local Community, Product and Customer Responsibility.
The 16 topics and their related impacts were assessed by the workshop participants and the personnel of Italian companies of the SACMI Group by way of a questionnaire. To identify the ESG issues and impacts that are truly ‘material’ for SACMI, a so-called materiality threshold was defined with regard to analysis concerning both Impact Materiality (generated impacts) and Financial Materiality (impacts suffered).
At the end of the entire process, the results were assessed and validated by all members of the Organization's internal Workgroup.
For each of the 13 topics found to be material for SACMI, the following table describes the main impacts the company’s activities have on the economy, the environment and people, including any impact on human rights, and identifies the company activities that generate, directly or indirectly, the identified impacts. The main risks and opportunities to which the Organization is exposed in the short, medium and long term are also illustrated. Lastly, the 2030 Agenda Sustainable Development Goals (SDGs) associated with each material topic are presented.
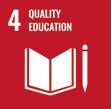
AREA: Human Resources MATERIAL ISSUES: Resource development and training
RELATIVE IMPACT OF SACMI (positive and/or negative):
• Workers have the opportunity to embark on a path of professional growth and realize their full potential
• Availability of courses to strengthen and develop professional skills
• Capacity to attract and retain resources and ensure stable employment
RELATIVE IMPACT ON SACMI (positive and/or negative):
Level of exposure to operational risks linked to inadequate technical and/or soft skills on the part of company personnel
• Worker motivation and retention, with a potential impact on company ‘attractiveness’
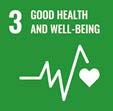
AREA: Human Resources MATERIAL ISSUES: Workplace health and safety
RELATIVE IMPACT OF SACMI (positive and/or negative):
Protection of the well-being, health and safety of employees and all individuals whose tasks are under the direct control of the organization (e.g. temporary workers, contract researchers, interns, etc.)
RELATIVE IMPACT ON SACMI (positive and/or negative):
• Corporate administrative liability for accidents in the workplace (fines, legal action, damage to corporate image, suspension of production, etc.)
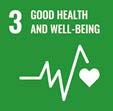
AREA: Human Resources MATERIAL ISSUES: Welfare and life-work balance
RELATIVE IMPACT OF SACMI (positive and/or negative):
• Offering a positive working environment and implementing a set of programs intended to improve employees’ work-life balance results in their psycho-physical well-being, with consequent impacts on the degree to which they can effectively realize their full potential
RELATIVE IMPACT ON SACMI (positive and/or negative):
• Level of exposure to operational risks linked to staff turnover and insufficient employee retention
• Level of exposure to risks associated with an increase in absenteeism
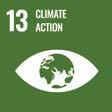
AREA: Environment MATERIAL ISSUES: Environmental responsibility
RELATIVE IMPACT OF SACMI (positive and/or negative):
• Protection of ecosystems and preservation of biodiversity
• Safeguards for local communities/areas concerning exposure to extreme weather events (e.g. floods, hurricanes, desertification, etc.)
RELATIVE IMPACT ON SACMI (positive and/or negative): Level of exposure to operational risks related to energy market volatility
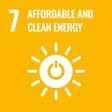
AREA: Environment MATERIAL ISSUES: Energy efficiency
RELATIVE IMPACT OF SACMI (positive and/or negative):
• Possibility of lowering energy costs through energy efficiency actions/projects
• Safeguards for local communities/areas concerning exposure to extreme weather events (e.g. floods, hurricanes, desertification, etc.)
RELATIVE IMPACT ON SACMI (positive and/or negative):
• Level of exposure to operational risks related to energy market volatility
Integrated Annual Report 2023 / SACMI Group / Dialogue with stakeholders and materiality analysis
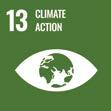
AREA: Environment MATERIAL ISSUES: Decarbonization
RELATIVE IMPACT OF SACMI (positive and/or negative):
• Protection of ecosystems and biodiversity
• Exposure of local communities/areas to extreme weather events (e.g. floods, hurricanes, desertification, etc.).
Accentuation or mitigation of climate migration
RELATIVE IMPACT ON SACMI (positive and/or negative):
Adoption of low-emissions components with consequent prevention of sanctions resulting from noncompliance with laws and regulations (also of a voluntary nature)
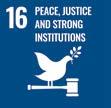
AREA: Governance MATERIAL ISSUES: Contrasting corruption
RELATIVE IMPACT OF SACMI (positive and/or negative):
• Protection of the well-being, health and safety of employees and all individuals whose tasks are under the direct control of the organization (e.g. temporary workers, contract researchers, interns, etc.)
RELATIVE IMPACT ON SACMI (positive and/or negative):
• Corporate administrative liability for accidents in the workplace (fines, legal action, damage to corporate image, suspension of production, etc.)
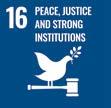
AREA: Governance MATERIAL ISSUES: Ethics and integrity in business conduct
RELATIVE IMPACT OF SACMI (positive and/or negative):
• Availability of investment/capital for the benefit of the individual company and the wider economic ecosystem in which it operates
• Well-being and prosperity of the main stakeholders with whom the Organization interacts
RELATIVE IMPACT ON SACMI (positive and/or negative): Prevention or (vice versa) imposition of administrative/prohibitive/criminal sanctions stemming from any non-compliance with laws and regulations (also of a voluntary nature)
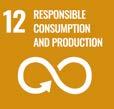
AREA: Economic responsibility, suppliers and partners
MATERIAL ISSUES: Supplier management and assessment
RELATIVE IMPACT OF SACMI (positive and/or negative):
• Availability of raw materials and products/services of high environmental and social performance
• Management of environmental/social impacts along the supply chain
• Well-being and prosperity of all stakeholders along the supply chain RELATIVE IMPACT ON SACMI (positive and/or negative):
• Level of exposure to operational risks related to market volatility
• Product/service innovation
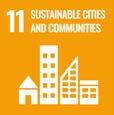
AREA: Local communities MATERIAL ISSUES: Relationships with local communities
RELATIVE IMPACT OF SACMI (positive and/or negative):
• Availability of investment/capital for the benefit of the individual company and the wider economic ecosystem to which it belongs (e.g. the industry, the geographical area etc.)
• Improvement of local socio-economic conditions
RELATIVE IMPACT ON SACMI (positive and/or negative):
• Reinforcement or erosion of the organization's reputation in the eyes of its key stakeholders (e.g. customers, financial institutions, investors, etc.)
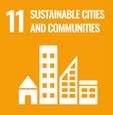
AREA: Local communities MATERIAL ISSUES: Partnerships with schools and universities
RELATIVE IMPACT OF SACMI (positive and/or negative):
• Well-being and prosperity of the main stakeholders with whom the Organization interacts (e.g. employees, local communities, business partners, etc.)
• Development of the innovative, productive and economic capacity of the area and the market within which the company operates
RELATIVE IMPACT ON SACMI (positive and/or negative):
The Organization’s capacity to attract investment and access capital
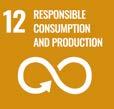
AREA: Product and customer responsibility
MATERIAL ISSUES: Product quality and safety
RELATIVE IMPACT OF SACMI (positive and/or negative):
• Safeguards for the environment, biodiversity, ecosystems and the people in areas where SACMI operates
RELATIVE IMPACT ON SACMI (positive and/or negative):
• Customer acquisition and retention levels
• Compliance with market-required product quality and safety levels
Reinforcement or erosion of the organization's reputation in the eyes of its key stakeholders
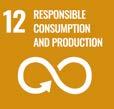
AREA: Product and customer responsibility
MATERIAL ISSUES: Capacity for innovation
RELATIVE IMPACT OF SACMI (positive and/or negative):
Market availability of products with high environmental performance
RELATIVE IMPACT ON SACMI (positive and/or negative):
• Reinforcement or erosion of the organization's reputation in the eyes of its key stakeholders
For further information on the tools used to monitor organizational processes, please refer to the specific sections.
Integrated Annual Report 2023 / SACMI Group / Dialogue with stakeholders and materiality analysis
Partnerships
The materiality matrix
The above-described results stem from an aggregation of the responses obtained from the corporate population and the participants in the two workshops. These are illustrated in the materiality matrix shown in the figure. Note that "internal stakeholders" refers to the main members of the ESG data collection workgroup, involved via workshops, while "external stakeholders" refers to the corporate population. Financial materiality is represented by the size of the topic-related circle.
The topics shown to be material and the relative impacts associated via the above-described process are generally in line with the material topics of the previous reporting cycle. Specifically, the new topics identified for 2023, as compared to 2022, refer to the area of Product and customer responsibility, Economic responsibility, suppliers and partners, and Environment.
More specifically, reference is made to:
• Capacity for innovation
• Product quality and safety
• Supplier management and assessment
• Decarbonization
In accordance with the logic by which a topic is considered material if it is a priority from the perspective of Impact Materiality, Financial Materiality or both, Decarbonization is deemed material as it obtained the maximum rating with respect to financial materiality, despite being below the threshold established for Impact Materiality.
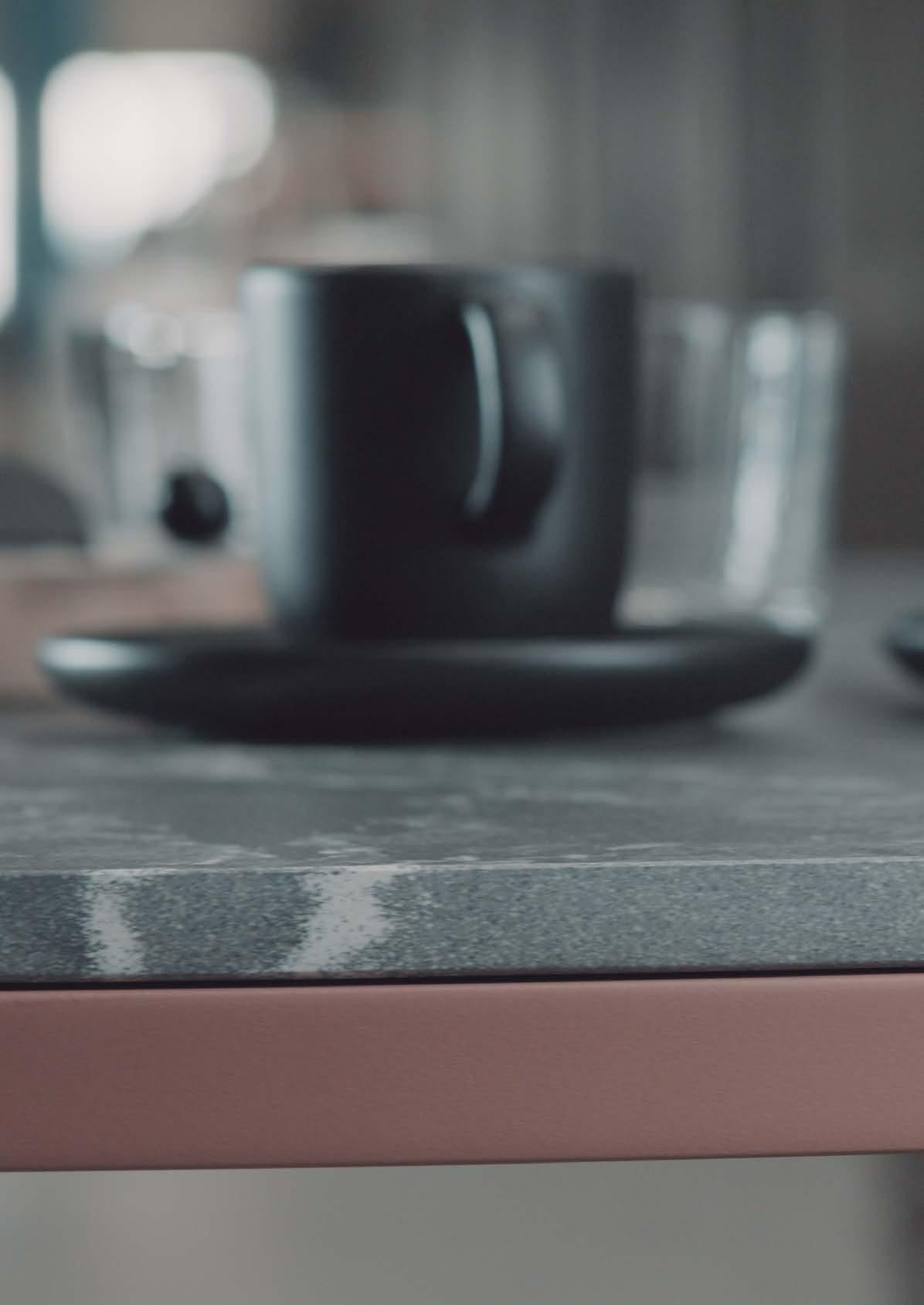
2023 closes a three-year period of excellent performance for the business, the best in SACMI's history.
Throughout the first part of the year, order acquisitions for new installations remained strong. The slowdown observed in the second six months was, in many respects, predictable and cyclical. It was the result of a fairly prolonged period of over-investment in output capacity, itself partly an offshoot of post-lockdown policies enacted by governments in several countries as they sought to stimulate industrial production and provide consumers with greater liquidity in the Covid/post-Covid period.
Higher interest rates also contributed to this cyclical inversion by causing a downshift in global construction; this occurred in parallel with a financial crisis in the Chinese construction sector. Moreover, worsening geopolitical tensions - first and foremost (but not only) the Russia-Ukraine conflict - placed constraints on the free movement of goods.
In the latter part of 2023 and, to an even greater extent, in early 2024, this generated a significant falloff in global demand for tiles, with a marked slowdown in customers' investment projects.
Against this backdrop and despite greater competitive pressure from Chinese competitors as they struggle with sluggish domestic demand, SACMI maintained shares and volumes across all markets.
Technologies and markets
In 2023 the total number of Continua plants installed worldwide rose to 170, confirming its status as the go-to solution for all companies looking to enter the large ceramic slab market and advantageously manufacture coordinated sub-sizes.
1.1
Tiles
SACMI maintained shares and volumes across all markets. Digitalization and automation of plants continues apace to improve the finished product and help customers innovate
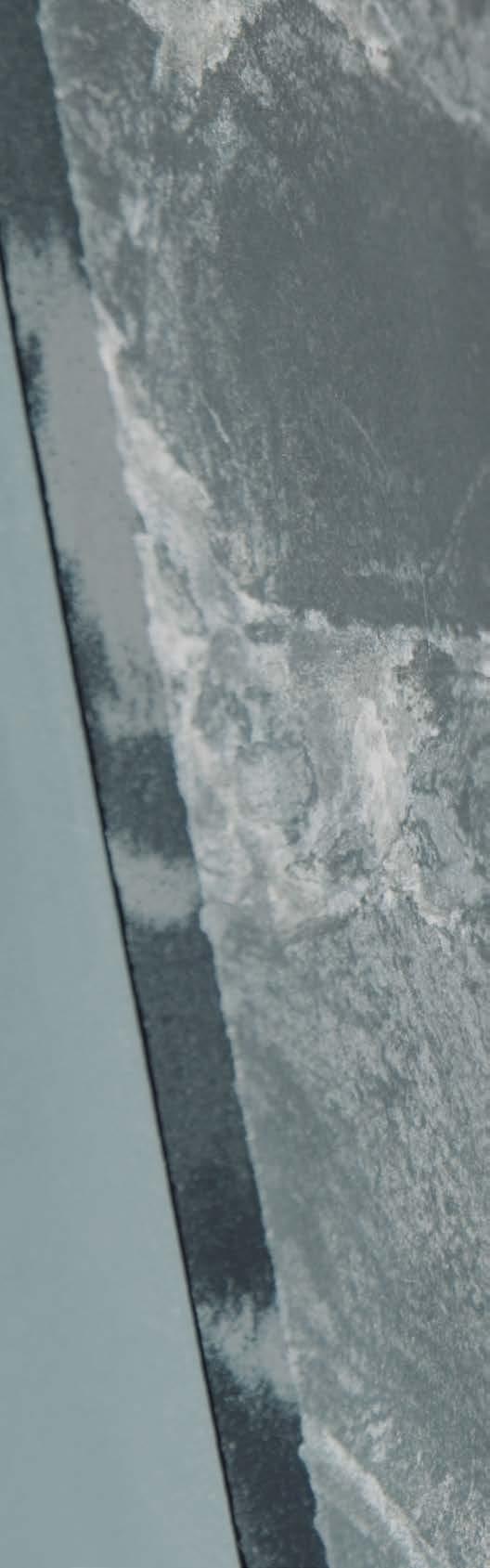
Simultaneously, new solutions in the range (PCR2180 and PCR210) have started to gain ground, with major projects finalized both in the traditional markets of Italy and Spain but also in China, Vietnam, India and the Far East.
With traditional pressing instead, 2023 saw the arrival of new, strengthened high-added-value packages (energy, environment and self-diagnostics kits). Sales of accessories were high, with the SPE new Plana ejector performing particularly well. Moreover, a new family of PHC Red Edition presses - manufactured directly in SACMI Nanhai - was launched to maintain leadership across Asia.
Trends in body preparation continue to favor larger machines (mills and spray dryers are increasingly larger and more powerful) as they raise efficiency and contain costs: several projects have been implemented in South America, especially in Brazil where SACMI retains its position as the leading partner for the switch from red bodies to porcelain stoneware.
Moving on to kilns the FMA Maestro remains the world’s best-selling firing solution. ‘Widemouthed’ configurations designed to fire large slabs are particularly popular on account of their reliability. The FMD Maestro range of new fully digital solutions has also been expanded, with various projects completed around the globe.
In the end-of-line area, 2023 saw the company make the strategic decision to expand the finishing range by attaining 100% ownership of BMR, leading to new projects and synergies in Europe, North Africa and Brazil.
After several months of steady investment, Turkey too has felt the impact of fierce Chinese competition as rivals seek to make it a strategic bridgehead from which to enter European markets. In areas where the Chinese competition is considerable, the Business continues to focus on safeguarding its position in the pressing arena and, more generally, on strengthening the SACMI Nanhai facility, pivotal to maintaining a presence in China’s ‘economic sphere’.
In Asia, India remains the leading country in
terms of both completed and potential projects, as many customers are leaning towards the high end of the market.
Product strategy
In 2023, SACMI continued to follow a threepronged strategy: digitalization/automation of ceramic processes and plants, their sustainability, and ceramic products and their innovation The aim is to bolster SACMI's position as a supplier of integrated industrial systems by deploying strategies that focus on the finished product and deliver solutions designed to put customers on the path to success.
More specifically, 2023 saw us move closer to total integration-digitalization of ceramic line machines, from implementation of new filling devices on the Continua+ to coordination with Deep Digital devices (DHD and DDG). The result: the creation of new products that offer texture and aesthetics on a par with marble and natural stone, offering customers fresh market opportunities.
One of the year’s key events was SACMI Ceramic Innovation Open Week held in parallel with the Cersaie fair. Taking place in both Imola and Casalgrande - and involving SACMI’s product design partners, BMR and Stylgraph - the event garnered highly positive feedback, in terms of both attendance (over 400 people) and appreciation.
Part of the new Open Labs format, the Open Week provided an opportunity to showcase new solutions such as the V-Nature devices on the Continua+, which seamlessly combine in-body and on-surface decoration. Also on show was the new hydrogen kiln prototype, alongside the pure hydrogen production and storage station at the Salvaterra facility. The week also highlighted the work done by the Full Digital Decoration Laboratory. Here, Tile-related digital printing know-how is being extended, with good growth opportunities, to other sectors such as Metal Packaging.
The Open Week offered a unique opportunity to respond to customers seeking to differentiate their products in terms of technology (e.g. the
ability to enter new segments with higher added value), production process sustainability and digitalization.
Customer Service
Improving on an already-impressive 2022, Customer Service performed outstandingly during the year, achieving record results.
Alongside encouraging spare parts sales, 2023 saw consolidation of the new Smart and Secure Service scheduled maintenance-assistance plans. Increasingly appealing to customers, these plans have led to the signing of new contracts and won over new customers (e.g. Mexico, Turkey, etc.). Similarly - and in synergy with the new digital services (S.P.A.C.E.) - the company continued its strategy of strengthening local facilities (new Rio Claro Technical Center in Brazil, the launch of the Morbi area technical hub in India). In parallel, scheduled maintenance plans and indepth training for SACMI machines and plants were promoted.
This explains why, despite significant shrinkage in global demand, 2024 could still be a positive year for SACMI, with the value proposition being further enhanced by focusing on the finished product, digitalization, plant sustainability and state-of-the-art customer support.
Quality control
Key technological innovations
Expansion of the machine range with a sharp focus on the development of ultra-large spray dryers to optimize production and boost overall process efficiency. Development of the ‘hybrid’ spray dryer (gas-hydrogen and gas-electric) completed.
On Continua+, consolidation of the latest models in the range, with more versatile management of sub-sizes (PCR2120), higher speeds and a wider compaction front (PCR2180).
New V-Nature devices for the controlled deposit of powders on the compaction belt and the creation of combined in-body and on-surface decorations have been incorporated on the Continua+. Used in combination with the DHD and DDG decorators, these devices provide 3D texturing on a par with natural materials, opening up new fields of use in the furnishing and interior design sectors.
In traditional pressing, the new high-added-value Self-diagnostics kit, Energy Saving Pack and P. Back Environment kit were upgraded. This approach, which will also involve medium-term development, aims to make the machines more energy-efficient, allow recovery-reuse of raw materials and streamline any repair work in the event of breakdowns (i.e. greater plant availability).
The exclusive DDG system for the creation of material effects and textures continues to perform well on the market. The machine range was expanded with new variants (e.g. specific heads for water-based inks) and upgrades to the CRONOs graphics control software.
Alongside improvements to coordinated DHD+DDG digital applications, new mechatronic systems (e.g. alignment devices), capable of executing the ultra-precise combined application of inks and materials while reducing waste, were also developed.
The Maestro kiln range was developed further, most notably the FMD digitally-controlled version, which is designed to optimize consumption, minimize emissions and maximize product quality. Design, development, construction and testing of the world’s first kiln (FMH) to be fueled with 100% hydrogen (zero emissions) proceeded apace. Further improvements were also made to the zero fuel dryer, designed to augment factory energy efficiency and re-use the heat contained in the kiln fumes. Construction of the new gas-electric hybrid dryer SACMI Forni&Filter continued to develop and market solutions that recover thermal waste from the chimney using heat exchangers. First successful installation of the new RTO-UP system for post-combustion of the organic compounds found in the kiln fumes.
Completion of the D-Line range for packaging/sorting with the new high-performance D-Roll packaging machine and the new D-Pick&Place palletizer. Consolidation of process control systems (new Flawmaster for finished product quality
control in the sorting zone) and development of a new monitoring system for unfired materials leaving the forming zone (OPTIMA).
Development of HERE modules dedicated to product quality and maintenance control/planning continues. First automatic batch tracking systems covering the entire production line installed.
Body preparation
Development of gas-hydrogen and gas-electric
new hybrid ATM
Continua+ | V-Nature and Deep Digital
Forming through-veining
New devices for digital
-250,000 consumed on each press kWh/year
Drying and firing
100 of raw materials recovered tons/year -66% to repair mean time
Consolidation of the and kiln heat recovery solutions (RVE+RVA)
“zero fuel” dryer
RTO-UP
New system for post-combustion of organic compounds in kiln fumes
Impact on sustainability
Energy Thanks to low consumption (0.04 kWh/m2), the 170 Continua lines in operation worldwide have saved 143 GWh of electricity compared to traditional lines of equivalent productivity, helping prevent the emission of over 57,000 tons of CO2 into the atmosphere. Digitally-controlled Maestro FMD kilns have reduced heat energy consumption and related CO2 emissions by 7%. During 2023, the 11 Maestro FMD kilns in operation saved, compared to traditional kilns of equivalent capacity, 2,400 MWh thermal meaning 5,200 tons less CO2 eq in the atmosphere.
Consolidation of the Zero Fuel’ dryer range, designed to boost factory energy efficiency and retrieve thermal waste from kiln fumes. Compared to a traditional dryer, consumption is reduced by 7,700 MWh thermal, preventing the in-atmosphere emission of 1,500 tons of CO2 eq per year.
New energy packages on the PH presses reduce their electricity consumption by up to 25%, the equivalent of 250,000 kWh per year per press.
Emissions
Decarbonization
Solutions for retrieving thermal waste from the chimney (via heat exchangers) reduce heat loss. In the configuration in which the recovered hot fumes are directed to the spray dryer, consumption is reduced by 3,250 MWh thermal, preventing the emission of 650 tons of CO2 eq per year per production line.
In 2023 the first innovative RTO-UP post-combustion system was completed, successfully removing 95% of the organic compounds (VOC) and odors in the kiln fumes.
First prototype of an electric generator for spray dryers with a hybrid power supply (gas+electric). First trial in the lab.
Compared to traditional kilns, Maestro FMH kilns (hybrid gas-hydrogen with mixes containing up to 50% H2) reduce CO2 emissions by as much as 23%. If powered by a fuel mix containing 50% hydrogen, each FMH kiln would allow a manufacturer to reduce direct CO2 eq emissions by more than 1,500 tons per year.
Design, development and construction of the world’s first kiln to be 100% hydrogen-powered, with zero CO2 emissions into the atmosphere. Each FMH kiln powered by 100% hydrogen from a renewable source would avoid the emission of approximately 6,800 tons of CO2 eq each year. This kiln lets users modify the gas-hydrogen mix. By increasing the proportion of hydrogen from 50% to 80% the reduction in total emissions would more than double (-55% vs -23%). If the kiln were to run on H2 only, that figure would jump to 100% (zero-emissions kiln). Following start-up, completed in October 2023, SACMI performed the first firing tests on the new 100% hydrogen-powered kiln. In the coming months, the company aims to continue quality tests on customer-supplied products.
The new gas+electric hybrid dryer provides an opportunity to partially decarbonize the process. Each of these new machines can reduce consumption by 1,460 MWh thermal lowering emissions by up to 290 tons of CO2 eq per year if powered with electricity from renewable (photovoltaic) sources.
Raw materials/ waste/ process control
Development of special DHD machine heads for the use of water-based inks to reduce the use of solvents and pollutants. Each new DHD machine that uses water-based inks prevents the emission of approximately 50 tons of CO2 eq per year.
The ‘wet’ part of DDG decoration has also been adapted to use new heads for water-based (not solvent-based) glues. Each new working DDG that uses water-based glues prevents the emission of approximately 150 tons of CO2 eq per year.
In general, development of new alignment devices for coordinated DHD+DDG applications has further optimized the use of raw materials (inks, glues, grits and effects), with an accompanying reduction in water and energy consumption.
On the 170 Continua+ lines installed worldwide, ultra-low hydraulic oil requirements (90% less than on a traditional or discontinuous press) have prevented the production of over 73,000 liters of used oil
New process control and feedback systems (OPTIMA) have reduced fired waste by eliminating defects before they can reach the kiln. This means materials can be recycled, thus avoiding the subsequent processing (firing, decoration, etc.) of defective items and the associated waste of energy and resources. This makes it possible to achieve savings of approximately 400 MWh thermal per year on each line, cutting CO2 eq emissions by 80 tons What’s more, recycling the raw waste back into the preparation process can cut raw materials consumption by 690 tons per year.
Use of the Environment P.Back Kit on PH presses allows the retrieval of up to 100 tons/ year of raw materials and their reuse in the process. With the Self-diagnostic Kit, instead, the Mean Time to Repair can be reduced by up to two thirds, streamlining plant control on the part of the operators.
Decarbonization
FMH Maestro Kiln
-23%
CO2 emissions
Hybrid gas+electric dryer
-1,500 tons/CO2 eq emitted every year
-1,460 MWh thermal -290 tons/CO2 eq emitted every year
Raw materials/waste/process control
DHD (Digital Humid Decoration)
Hydrogen kiln
Development of first hydrogen-fuelled kiln
-6,800 tons/CO2 eq emitted every year 100%
Continua+
special heads
Development of for water-based inks
-50 tons/CO2 eq emitted every year
Energy consumption the lowest on the market
0.04 kWh/m2
90% less oil needed compared to a traditional press
Integrated Annual Report 2023 / SACMI Group / Tiles
-73,000 liters of waste oil
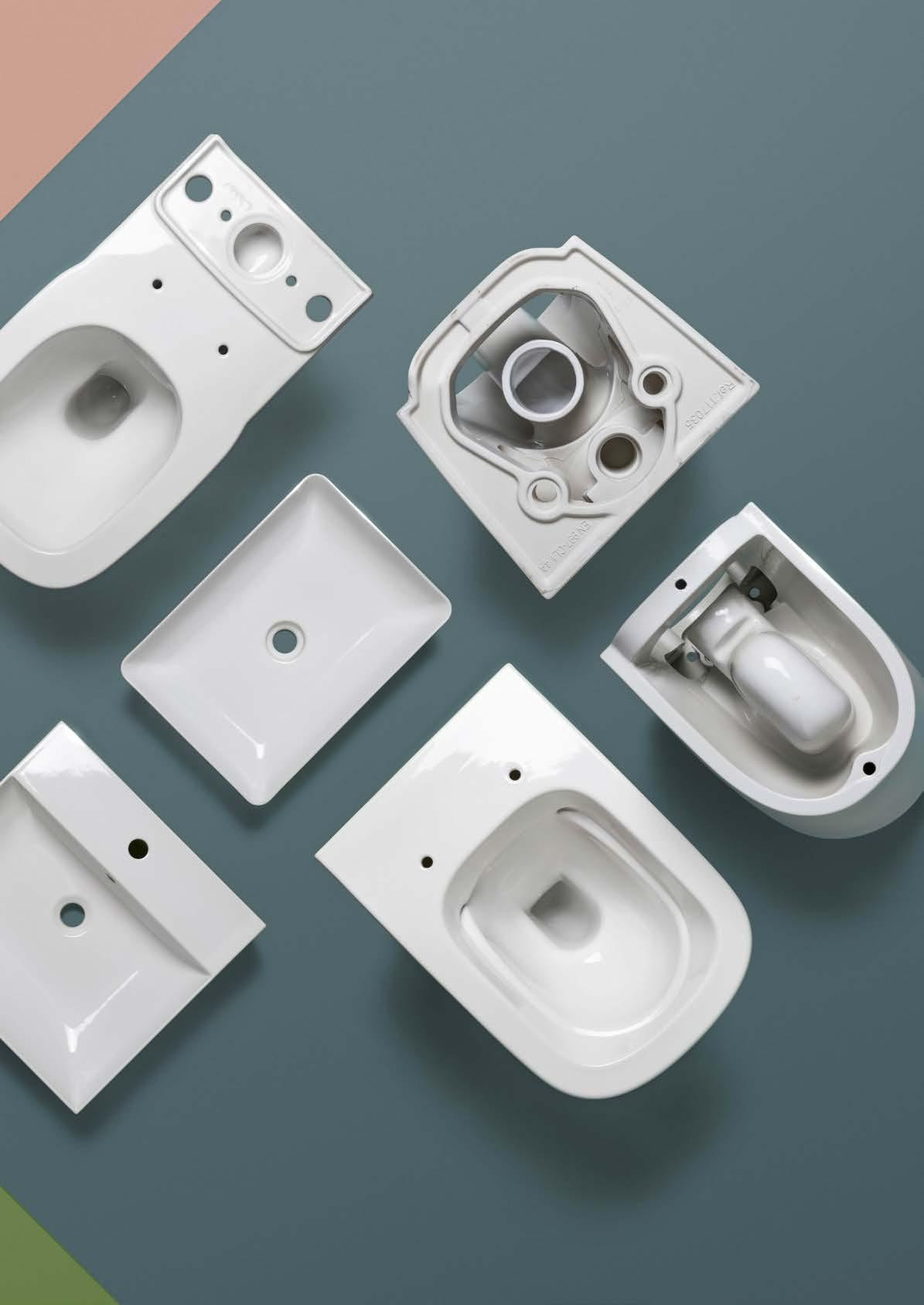
Sanitaryware
In 2023, as in 2022, the Business benefited from the actualization and/or rebooting of multiple projects as the industry exited the Covid-induced slowdown. End-of-year results were excellent, the best ever for the Business.
The various product families have regained significant volumes, favoring saturation of production facilities. These results look even more encouraging when one considers that the industry has been struggling with the rising cost of electronic components, robotics and refractory materials, all of which are widely used in automation projects.
Markets
In Italy, SACMI continues to supply prestige brands. Alongside standard machines, it implements innovative projects such as robotic finishing and glazing, which have also benefited from government incentive schemes. More specifically, the installation of new RobotClean stations continues apace, confirming the standard-setting soundness of this new product.
Looking further afield, the key markets continue to trend towards highly automated projects, not just in Europe but also in Turkey, Bangladesh, Brazil and China. This matches and rewards a Business strategy that seeks to adapt automation solutions to customers’ individual needs.
All the major groups have again placed their confidence in SACMI products, especially so in Mexico, China, Portugal, Finland, Hungary, France, China and the United Arab Emirates. Note also that numerous complete plant projects are under way.
1.2
The 2023 result was the best ever. All the major Italian and foreign groups renewed their confidence in SACMI products.
Casting and glazing solutions, plus highly innovative projects such as robotic finishing, played pivotal roles
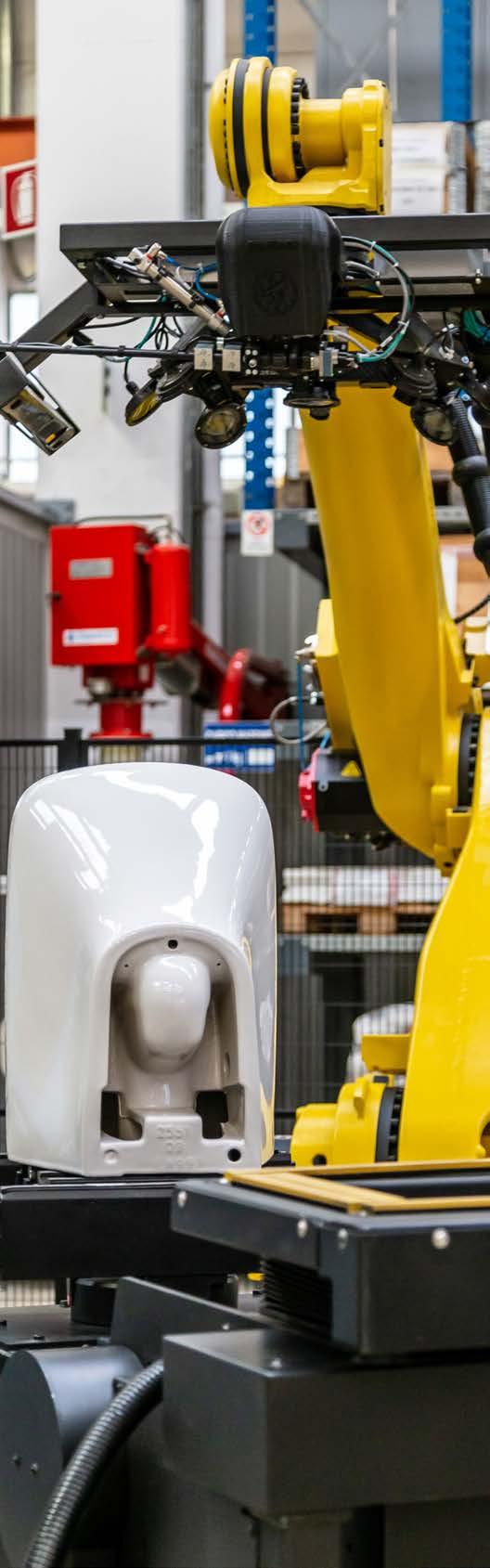
These include the launch, in Canada, of the world’s first sanitaryware factory to be powered with 100% renewable ( hydroelectric ) energy The plant is expected to become operational in 2024-25.
In the general industry segment, where most sales are concentrated in Italy, promotion of Gaiotto-supplied technology continues, both in and beyond the ceramic sector.
Products and projects
On all markets, the standard machines and plants are dominated by the casting and glazing product families. One of the year's key milestones was the sale of the 280 th AVM which remains the world’s best-selling high-pressure casting solution.
Investment in highly innovative projects continued in 2023 (albeit with some postponement in order to prioritize order execution and reduce the considerable backlog carried over from 2022): the AVI one-piece (large rim) project and the development of automatic green/white finishing, with the latest release of the SmartOffline NG software offer two outstanding examples. The latter project covers a range of uses, underlining just how important it is for SACMI to retain mastery of all those technologies, software included, that help factory personnel implement automation processes.
Development of the RobotLoad (automatic loading-unloading) and Qualitrack (robotic quality control) solutions continued throughout the year, the goal being to adapt the SmartOffline software to these stages too. From a digitalization perspective, in-Cloud connection of machines via software (HERE and MDC, Machine Data Collector) and dedicated sensors on production modules are increasingly significant.
With regard to sustainability, the in-the-field projects with the most direct impact include - in addition to the previously mentioned factory powered by renewables - consolidation of the new waste water ultra-filtration system prototyped in 2022 and successfully installed by a major customer in early 2023.
Another step towards enhanced sustainability was made with the development of glazing stations that feature resin screens to facilitate cleaning and glaze recovery.
More generally, a medium-term strategy aimed at reducing the average weight of manufactured items is being implemented. This could lead to raw material savings of up to 30% and energy savings of up to 10% . However, it will also pose technological challenges in order to prevent any warping or functional-mechanical issues that might stem from thinner, lighter articles. This project is already at an advanced stage of development with a major Italian customer.
Again from an environmental viewpoint, in 2023 the Business pioneered sustainable packaging ’, a project that seeks to reduce/recover/re-use machine packaging. Two pilot projects are under way with two leading Italian customers: once they’ve been completed, the solution could be extended to other SACMI businesses/production facilities.
Scenarios
Following two years of uninterrupted growth, 2023 delivered an excellent result. In the second half of the year, however, ever-higher production costs and worsening geopolitical tensions led many customers to cut back on investment, downsizing or postponing projects, including some that were already under way: a volatile and complex market that, given the high cost of credit, makes it increasingly burdensome for our customers to maintain high levels of stock. Such signs are not to be underestimated because in 2024 the focus will be on cost control and providing greater added value for individual product families.
Customer service continues to play a crucial role, not just in terms of its contribution to the business but also as a strategic tool for maintaining direct contact with customers, regardless of new machine sales performance. From this perspective, customers are increasingly appreciative of SACMI's ‘consulting’ services, which involve periodic contact and on-site visits. Further growth in this direction will be strategically vital to strengthening mutual trust with customers, also at the technical team level.
Key technological innovations
Modelling / Molds A new automatic machining center for the manufacture of molds and case molds using CAD/CAM milling techniques was started up. This investment reflects the ongoing trend towards producing molds with ‘by tooling’ technology, which is fast replacing traditional ‘by casting’ flows (the former already accounts for 60% of output). Digitalization of the modeling process has been extended to include the production of supports, prototypes, molds and case molds.
Creation of highly automated casting projects with multi-mold AVB machines. Development of AVI casting plant accessories for the production of complex items such as one-piece WCs. More generally, SACMI continues its strategy of combining high module productivity/flexibility with finishing automation.
Development of automatic finishing solutions both on casting modules (green finishing) and on dried articles (white finishing, RobotClean). Expansion of the Smart Offline platform to extend its use to green finishing and complex multi-robot lines, together with white finishing and glazing, areas in which the system has demonstrated several key advantages such as faster programming and optimization of patterns and processes.
Acceleration of the Qualitrack 2.0 automatic sanitaryware sorting project, involving collaboration with a major international digital solutions provider and the University of Bologna. The goal: to be ready to present the latest system version, which incorporates AI, at upcoming trade fairs.
Impact on sustainability
Water The first plant in Italy to retrieve and treat water from the pressure casting department using ultra-filtration technology was tested: in the first 7 months alone, this saved approximately 1,500 cubic meters of water, plus considerable quantities of solid precipitate that provide high-grade raw materials to feed back into the process. Studies aimed at delivering a solution that recovers 90% of the water used throughout the production process - with the development of standard solutions for differently sized plantshave been completed.
Here, collaboration with the University of Bologna, which involves support from final-year students, is ongoing.
A highly innovative project located in North America - and the first of its kind in the world - will see sanitaryware manufactured in a plant powered by electricity from renewable sources (hydroelectric). The keystone of that project is the new Riedhammer TRS-E full electric roller kiln.
In Europe, development of a high-density tunnel kiln (with double-decker kiln cars) continues: this will reduce consumption and emissions as it can be fueled with gas-hydrogen mixtures containing up to 80% hydrogen.
A new self-cleaning porous resin panel is being tested to simplify cleaning of glazing booths and raise the percentage of recoverable solid glaze. In 2023 the design stage was completed; a prototype has already been installed in the Lab pilot plant glazing module and is undergoing tests with a key customer.
A system that recovers the scrap produced in ‘by tooling’ mold-making has been developed. The aim is to achieve total re-use of resin by suitably grinding and treating it so it can be employed as a polymeric filler in the primary formula. The possibility of recovering all the swarf for use in supports, case molds or paneling is also being explored.
A sustainable packaging pilot project was set up to reduce packaging by using more sustainable materials, retrieving/reusing the packaging used for machines sold and shipped in Italy and some parts of Europe.
Development continues to focus on achieving complete automation of the different stages of production. This also aims to improve health and safety in the factory with operators increasingly assigned to off-line supervision and programming tasks instead of work that is physically tiring, repetitive and/or potentially dangerous. In 2023 there was a sharp focus on the development of automatic finishing, both green (in Europe casting modules for the production of fully automatic WCs were tested) and white (in Italy, an automatic line with 14 robots in series for the complete finishing and glazing of WCs, integrated with automatic quality control). Development
of a new, complete white finishing (RobotClean) + robotic glazing (RobotGlaze) line was also completed. Installation and start-up are expected in 2024, the goal being to combine technical solutions with customized plant layouts that reflect actual production requirements.
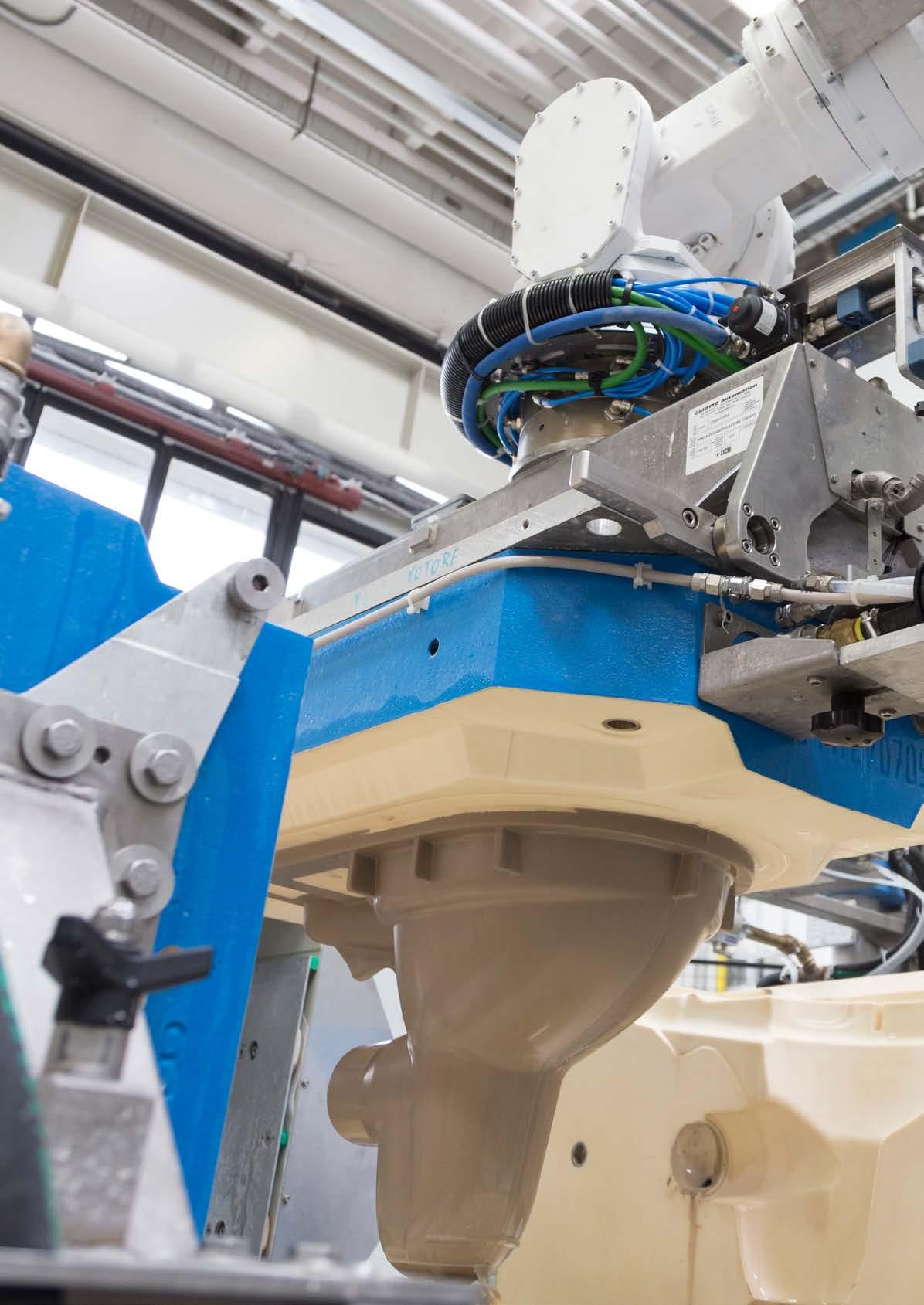
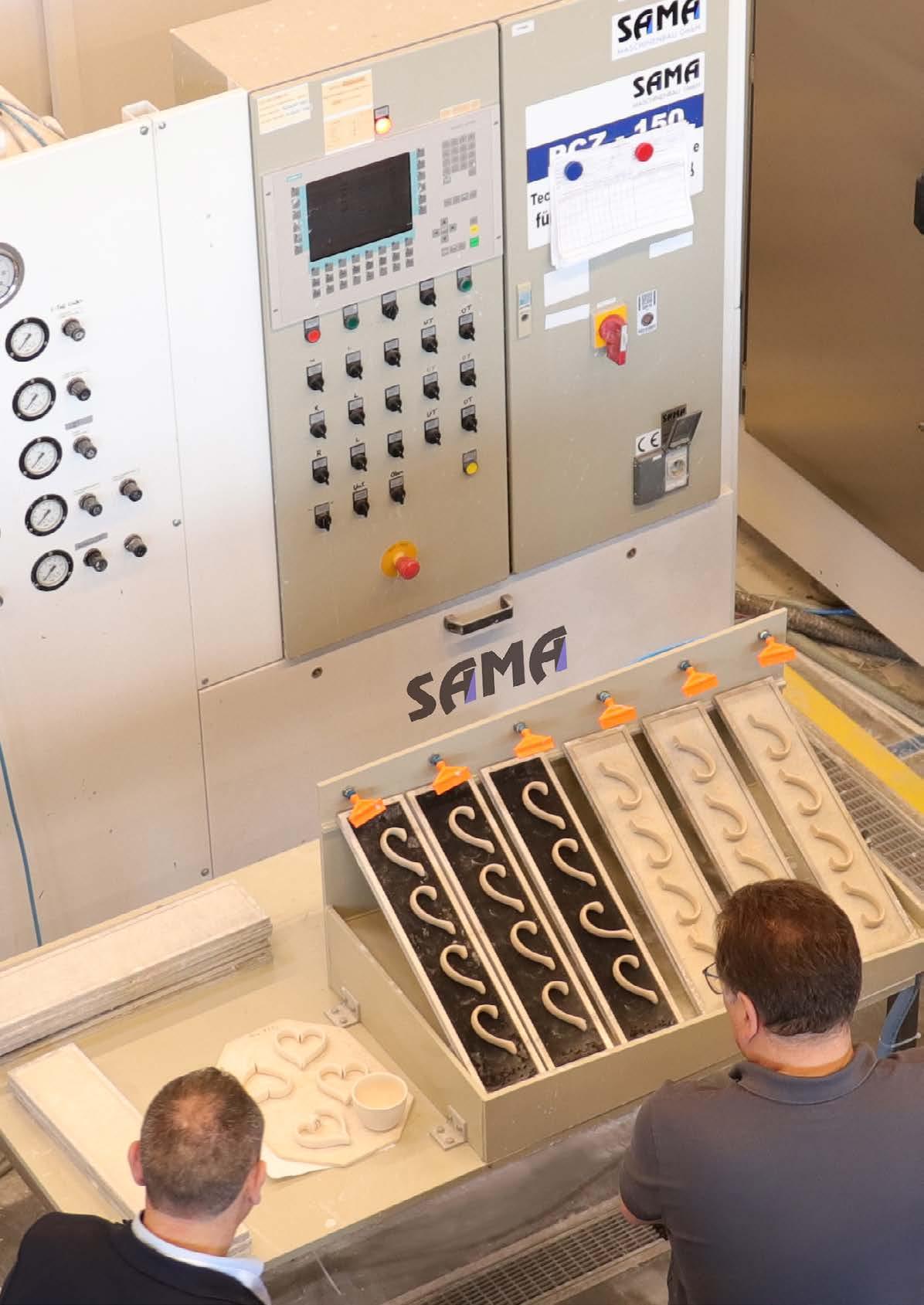
Tableware
After the sudden slowdown in 2020, the sector has made a slow but encouraging recovery. Order acquisitions picked up rapidly in the second half of 2022 when orders for both 2022 and 2023 were received.
Markets
Portugal, Romania, Brazil, United Arab Emirates, India, Bangladesh are some of the markets that saw key projects finalized during the year.
Specifically, in the ‘old world' - and in keeping with the strategy of leading European retailers - the market showed a near-obsession with sustainability issues. For example, SACMI supplied a customer with all the key machines needed to finalize the first European tableware (plate) manufacturing project to use ceramic scrap as a raw material: a project rewarded by the leading European retailer, who in 2023 launched the first plate collections made from recycled material.
Further successful projects include a new production line for cups with handles, located in Portugal . Major cup line orders were also received in India, where the outlook is bright on account of the Indian government's decision to limit imports of Chinese products.
The steadily recovering Tableware market is increasingly focused on leveraging sustainability to add value to finished products. Some of the year’s most significant projects included complete plants, with SACMI sole supplier for the entire machine range Integrated Annual Report 2023 / SACMI Group / Whiteware
Forming / Finishing
Products and projects
The most noteworthy projects included two complete plants, the only ones in the world to be built during this period, with SACMI sole supplier for all the machines in the portfolio These projects offer a not-to-be-missed opportunity to implement further synergies among SACMI Group companies, opening the way to the promotion of new products and the delivery of new integrated, automatic production lines.
In tableware firing, most sales are accounted for by kilns for glazed items, an area in which Riedhammer’s expertise and the quality of their solutions are unrivalled.
In terms of automation-linked innovation, major projects carried out in the field of automatic finishing gained considerable market acknowledgement. Spray glazing systems are increasingly in demand as replacements for traditional dip glazing technology as they allow for the application of reactive glazes that produce aesthetic effects during firing.
Scenarios
Since 2022 the world’s total output of tableware machines has grown by over 45%. However, in the second half of 2023, the sector also suffered a sharp slowdown in investment. The start of 2024 was marred by unstable demand for finished products and further uncertainties regarding product types, which depends on the share of demand from the Ho.Re.Ca. sector.
Nevertheless, the year laid the basis for a further strengthening of SACMI's role in the industry: it reorganized operations, renewed the SAMA management team and bolstered its reputation with customers thanks to the successful conclusion of several projects. Moreover, its always-available support, consultancy and customer assistance services were strengthened.
Forming / Finishing
Key technological innovations
Testing of isostatic pressing line with a PHO700 equipped with dual automatic finishing for irregularly shaped and circular plates. The line was successfully started up at a key customer’s plant, with SAMA and Gaiotto involved in developing the automation.
A leading European customer doubled the capacity of its cup production line with isostatic pressing (able to process special geometries such as cups with non-circular cross-sections). The plant features automatic finishing, a robotic cup handling system and automatic handle gluing.
Consolidation of bone china tableware manufacturing expertise, with projects successfully implemented for leading customers. Exquisite yet difficult to produce, bone china tableware is valued by airline caterers as it reduces on-board weight, saving on aviation fuel.
Testing of PH700 line with
dual automatic finishing
Cup production line with isostatic pressing and automatic handle gluing spray glazing
Automatic finishing and
Impact on sustainability
European project for the manufacture of plates made entirely from production scrap: in early 2023 the project was completed with the delivery of several key machines (most notably the spray dryer) to one of our customers; Europe’s main retail player was a driving force on the project and later launched the first collections on the market.
Start-up of the isostatic cup pressing line which, compared to the classic jiggering system, delivers significant energy savings and drastically reduces waste (less than 35%).
All latest-generation kilns are equipped with heat recovery systems and optimized firing curve control to minimize consumption and emissions.
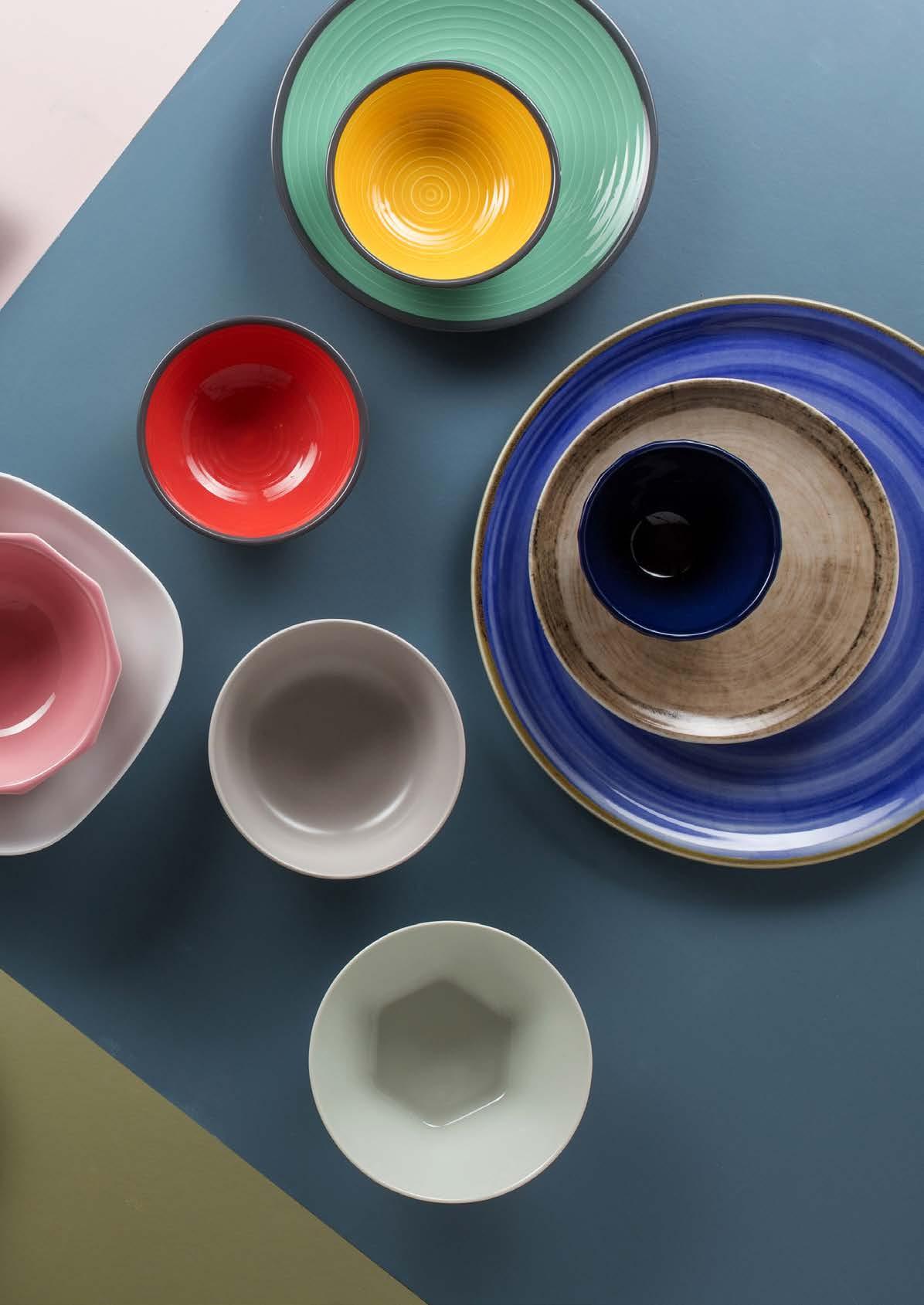
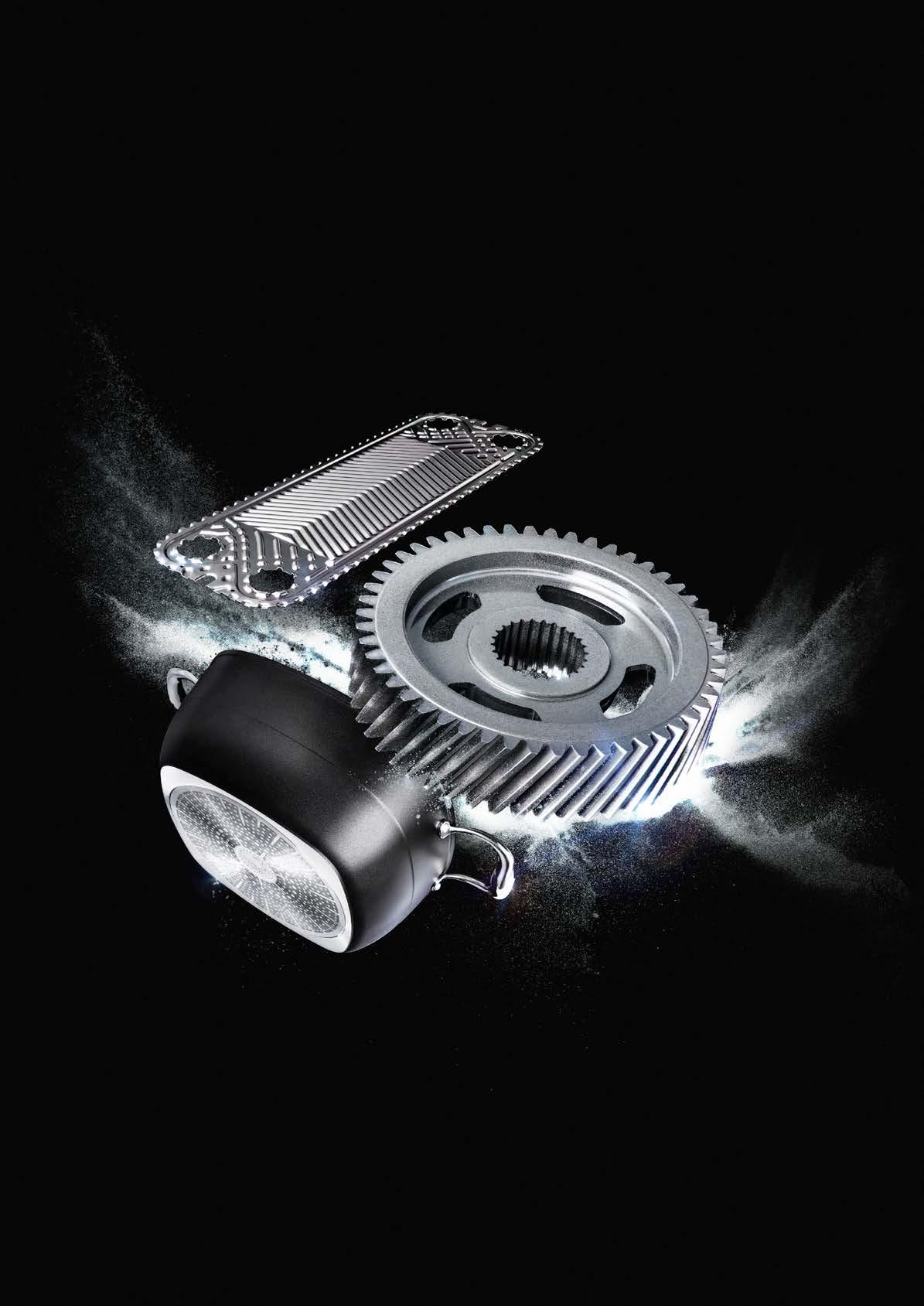
Advanced Materials 1.3
Metal
Record sales were achieved in 2023, largely driven by the sheet metal shaping press sector.
Demand for heat exchangers continued to rise. This resulted in the sale of six new PHL1500 lines (and the acquisition of contracts for another ten similar lines), three new PHL16000s (the largest presses SACMI has ever supplied on this market) and 2 PHL5000s: all these machines will go to the world's leading heat exchanger maker, with whom SACMI has enjoyed mutually rewarding business relations for years.
In parallel, the Powder Metal market continued to shrink, partly as a result of the transition towards electric mobility. Nevertheless, the latter still saw the acquisition of two new customers and the installation of some new presses for existing customers.
Against this backdrop, investment in the development of a helical gear compaction system proceeds apace: the market continues to show keen interest in the system, with the potential for concrete opportunities in the near future.
Note also that the DWL (mold wall lubrication) system has been optimized, generating strong interest from a market that continues to seek out new applications for press & sintering technology. Towards the end of 2023, work began on combining these two technologies in order to offer the market a high-density helical part manufacturing solution.
In the Cookware field, a leading European customer selected SACMI as its technological partner to launch a new project in the forming sector. This involved the supply of a 5000-ton PHP press, complete with loading and unloading automation for the cold forging process.
The record results of 2023 were driven by sales of sheet metal deformation presses (for heat exchangers).
In the hard metal segment, the quest for new opportunities continues with the development of ‘helical gear’ and mold lubrication (DWL) solutions
Key technological innovations
Development and testing of the 16,000-ton PHL press.
DWL (mold wall lubrication) optimized on powder metal presses. Optimization of the helical gear system and assessment of a combination of the two technologies (DWL+HG) to press high-density helical components.
Sale of the first 80-ton electric press - to be used in technical ceramics - to a leading American customer in the medical sector. To be installed in 2024.
Development and promotion of new smart service packages on presses. Design work began on a system that incorporates sensors on machines for the purposes of data collection, real-time operating status monitoring and maintenance planning.
Impact on sustainability
Industrialization of the DWL system, a powder metallurgy technology that eliminates the need for lubricant in metal powders thus shortening thermal cycles and, therefore, reducing consumption and CO2 emissions.
Increased expertise in the development of electric presses which, compared to hydraulic presses, cut consumption on average by up to 60-70%
Design of a system to reduce energy consumption on metal waste compaction hydraulic presses. Once the technical feasibility study was completed, a solution was put forward to a key customer.
New smart service packages for presses mean fewer inefficiencies (and, therefore, less waste of energy and resources) stemming from frequent downtimes and wear.
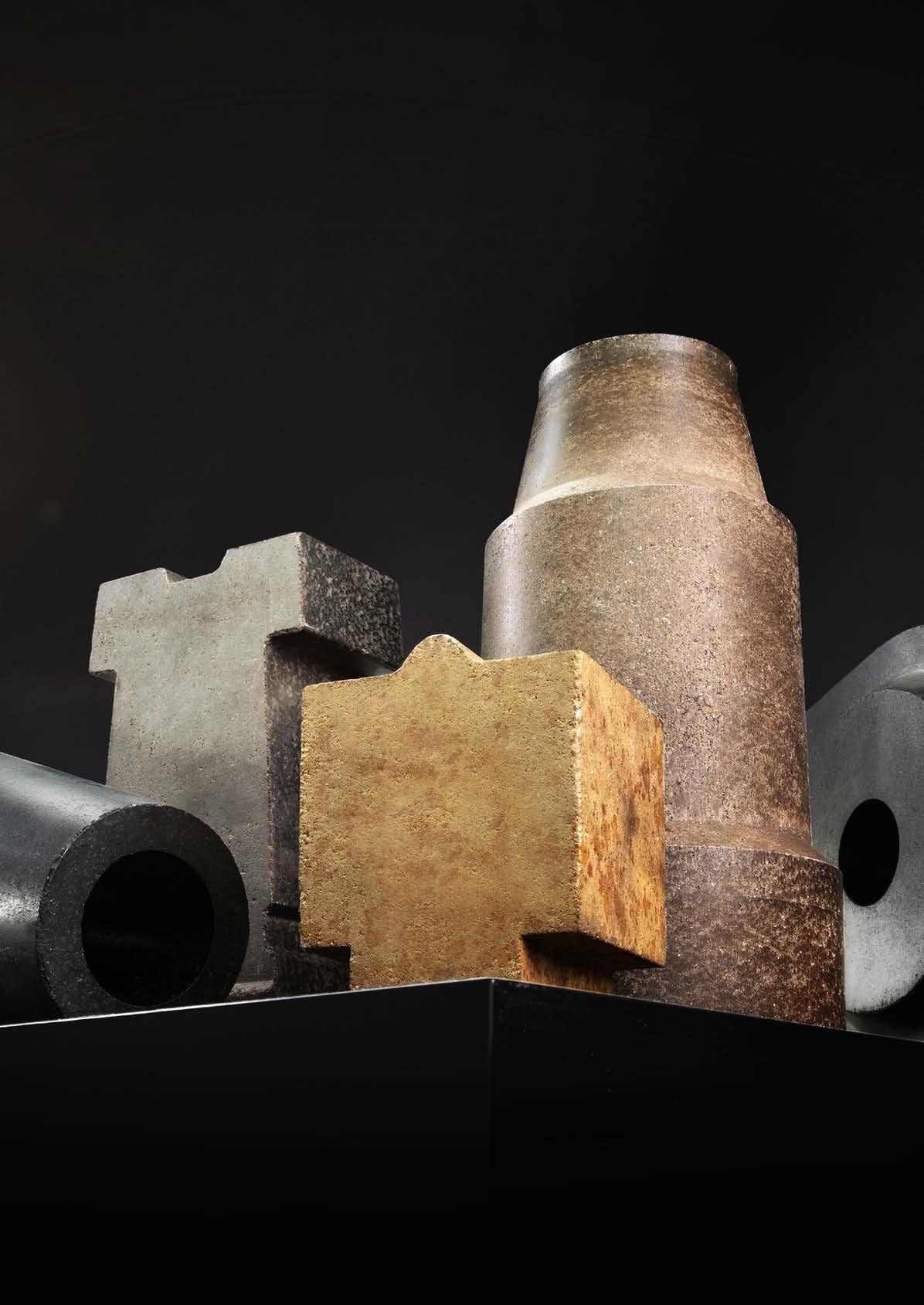
Advanced Materials
Refractories
Industry performance continues to be affected by geopolitical tensions which have wiped out sales opportunities in markets that were previously highly receptive (Russia, Ukraine, Iran, etc.).
Note that the persistence of the Russia-Ukraine conflict has prevented adequate coverage of the Russian refractory market, which had always been of considerable importance to the business. We are also witnessing a general slowdown in the market. This is partly due to key players having already completed projects over the last 3-4 years and a certain return of investments in Asian countries, where price competition is remarkably high.
Despite this backdrop, LAEIS has retained leadership on international markets, installing ten new presses and strengthening its positioning in China and India as a result of effective marketing of the machines produced directly by SACMI Nanhai.
The year bore the first fruits of synergy with Gaiotto: an order from a major Turkish customer for a series of pressed brick handling robots has now moved on to the executive phase.
The Korea-based project to manufacture saggers - containers made of refractory material that are used to heat-treat lithium-ion battery anode and cathode powders - was completed with the installation of three new 1,000ton hydraulic presses and a Riedhammer kiln. This solution is generating considerable customer interest due to fast-growing demand in the electric mobility sector and, therefore, for the materials used in the relative processes.
Despite the foreclosure of opportunities in once receptive areas, SACMI maintains its leadership with a range of solutions acknowledged as the most reliable on the market. First installation of the innovative sagger production solution

n general, on a refractory market which remains closely tied to the global production of crude steel, the SACMI range is acknowledged as being the most reliable and comprehensive, with good synergies between the various Group companies and production facilities ( LAEIS SACMI Imola SACMI Nanhai , then Riedhammer for the kilns and Gaiotto for automation).
All the top players remain extremely loyal and this allows us, even at a time of market sluggishness, to seize opportunities for the revamping and upgrading of existing machines. A further boost to the sale of spare parts has come from polarization of the market, with more and more large groups acquiring smaller companies, restructuring them and putting technological adaptation plans into action.
Key technological innovations
Production Inspection Consolidation of direct production of refractory presses in SACMI Nanhai, both the SACMI (PHR) and LAEIS (HPF) models, to better intercept market opportunities. Strengthening of synergies between SACMI and LAEIS to offer customers revamping plans for the already-installed SACMI machine pool.
Development of a new refractory press control system. Fine-tuning of a system for live quality control of pressed bricks, in collaboration with Gaiotto. Development of a complete plant concept (targeting the fast-growing Indian market). Upgrading of assistance packages (smart service).
Consolidation
of direct production of
refractory presses
revamping plans
between SACMI and LAEIS to provide for existing presses
New plant concept for ‘live’ quality control of pressed bricks
Impact on sustainability
Launch of a project to develop a new generation of refractory presses with low energy consumption.
For its part, Riedhammer is implementing new electric-hydrogen firing solutions to lighten the environmental footprint of the process.
A new ‘complete plant’ concept and promotion of press maintenance packages (smart service) to optimize resources and reduce waste. A new dashboard that gathers data on machine operating states was also implemented in 2023, laying the basis for further development of scheduled maintenance plans..
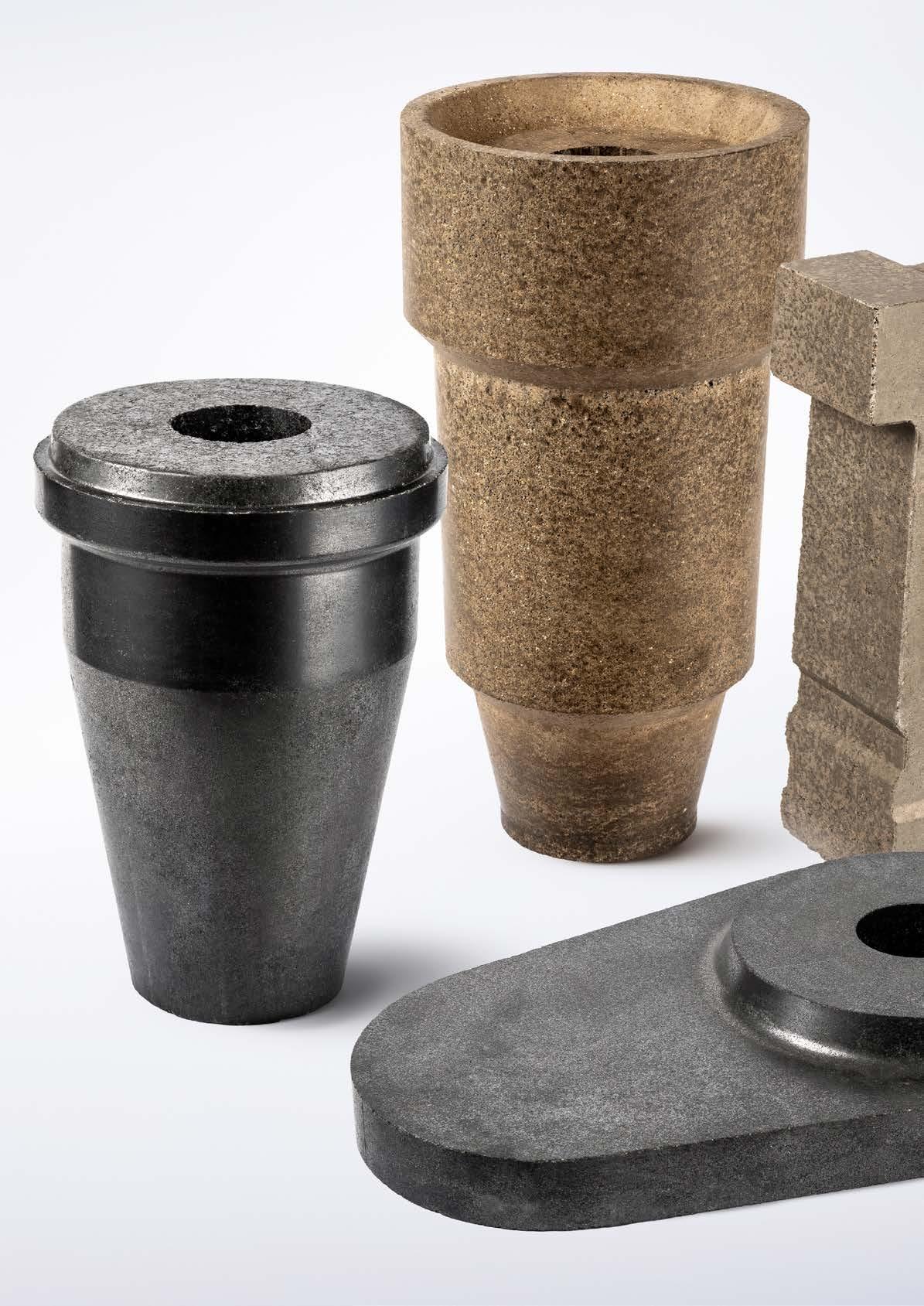
Advanced Materials
Technical Ceramics
Technical ceramics have a broad, diverse application range. In this sector, much of the focus is on the sale of stand-alone machines, in concert with a network of companies made up of SACMI Imola , LAEIS (presses), Riedhammer (kilns) and Alpha Ceramics (the latter plays a key role in both testing and direct production).
Riedhammer completed assembly of a lining plate line for one of the world’s leading aerospace firms and plans new investment projects for the current year.
Assembly of a cladding plate line for a global player in the aerospace sector was completed
Carbon
As in the previous year, 2023 saw stable performance, with finalization of several key projects with major players. For example, a major revamping project on a 2010 kiln was completed and two new kilns were sold in Kazakhstan and China. In Europe, instead, a key project got under way in Spain: this is now nearing the final engineering phase. Major new projects were launched in the Middle East, their timelines extending into 2025.
Sector performance remains tightly bound to the sale of heat treatment solutions for carbon electrodes and anodes (for the special steels and aluminum sectors); growth opportunities continue to be restricted by ongoing Russia-Ukraine conflict.
Projects with leading market players finalized. Kazakhstan and China stand out, as do new projects being launched in Spain and the Middle East.
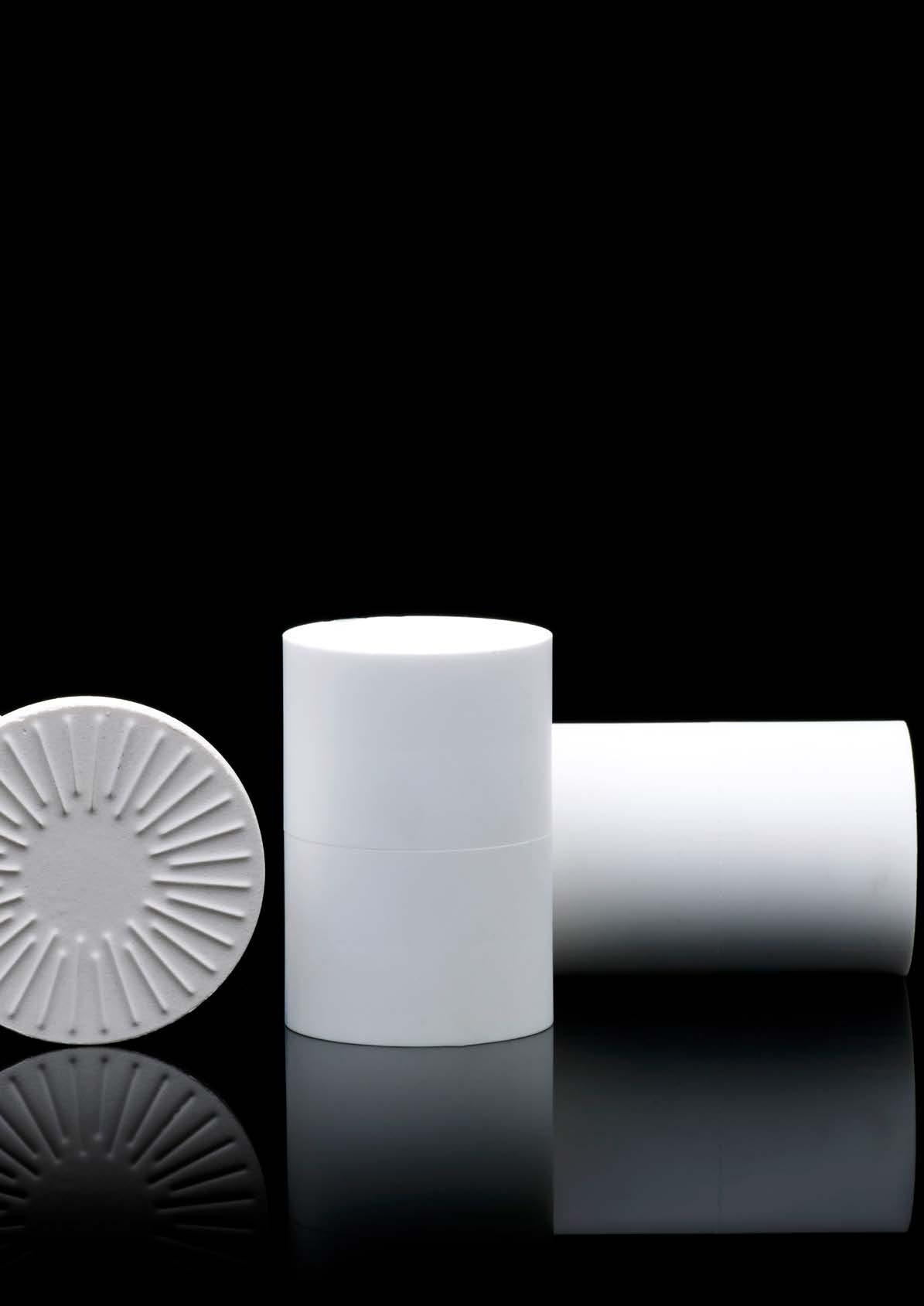
Advanced Materials
Lithium
Volumes proved to be highly satisfactory. As the year progressed, the market continued its gradual shift away from China. Nevertheless, the country still retains the vast majority of lithium battery production capacity.
Several new ‘giga-factories’ are being started up in Europe, the USA and Canada . Thanks to extensive experience in the thermal treatment of anodic and cathodic powders and an excellent market reputation, Riedhammer is starting to acquire major projects in these countries. Consequently, in 2023 Europe saw an expansion of direct production, an area previously dominated by China.
More generally, the year strengthened synergies between SACMI companies with expertise in this sector, most notably Gaiotto which provides sagger handling systems for use in calcining kilns. Several new contacts were established with anodic and cathodic powder producers who are interested in acquiring grinding, spray drying and handling solutions.
Overall, the lithium market continues to grow, opening the way to fresh, strategic opportunities for SACMI along the value chain that align with the specific heat treatment phases in which Riedhammer is already well positioned.
The trend towards a partial shift of production outside China continues, with the launch of new ‘gigafactories’ in Europe, the USA and Canada.
During the year, synergies between the various SACMI companies strengthened against the backdrop of a steadily growing lithium market
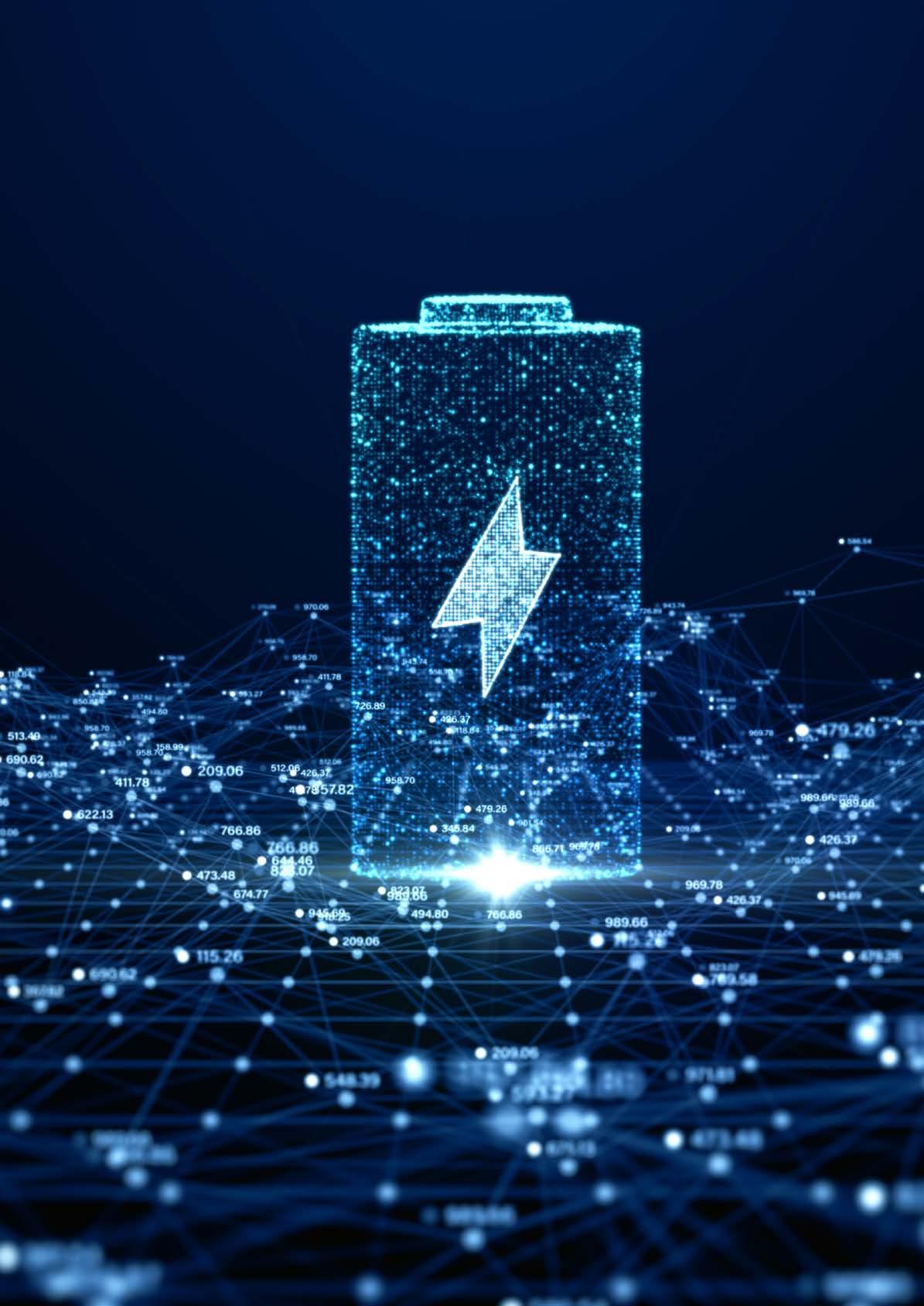
Research and Development
Key technological innovations
Design and production of applications for gas kilns that run on fuel mixes with a high percentage of hydrogen
Design of a kiln combustion air pre-heat system that recycles air from inside the kiln itself (via a Venturi burner).
Design of a water heating system that uses exhaust fumes.
Optimization of electric roller kilns
Optimization of sagger automation systems for the lithium industry with optical and flaw detection sensors (to extend sagger lifespan).
Participation in new plant projects in China, Europe and USA. Analysis of supply chains and technologies for recycling used batteries
The innovative lithium calcining process that requires no saggers in the kilns continues to undergo development.
Development of a new tunnel kiln to boost productivity on calcining lines.
Consumption and emissions Recycling
Impact on sustainability
Lower consumption and emissions on kilns that use hydrogen burners or electric heating elements . Utilization of thermal waste to heat air and water.
Energy and emissions savings thanks to a new lithium calcining process that requires no in-kiln saggers.
Development of engineering and layout for a plant that grinds battery cells and separates their constituent materials.
Design-patenting of an i nnovative recycling system that uses pyrolysis in a rotary kiln design of a production process exhaust gas treatment system. Further potential plant concepts, also for the recycling of different materials, are undergoing analysis.
Consumption and emissions
New hydrogen burners and heating elements, re-use of
thanks to new system that avoids using saggers in kilns
Design and patenting of an innovative recycle system via pyrolysis in
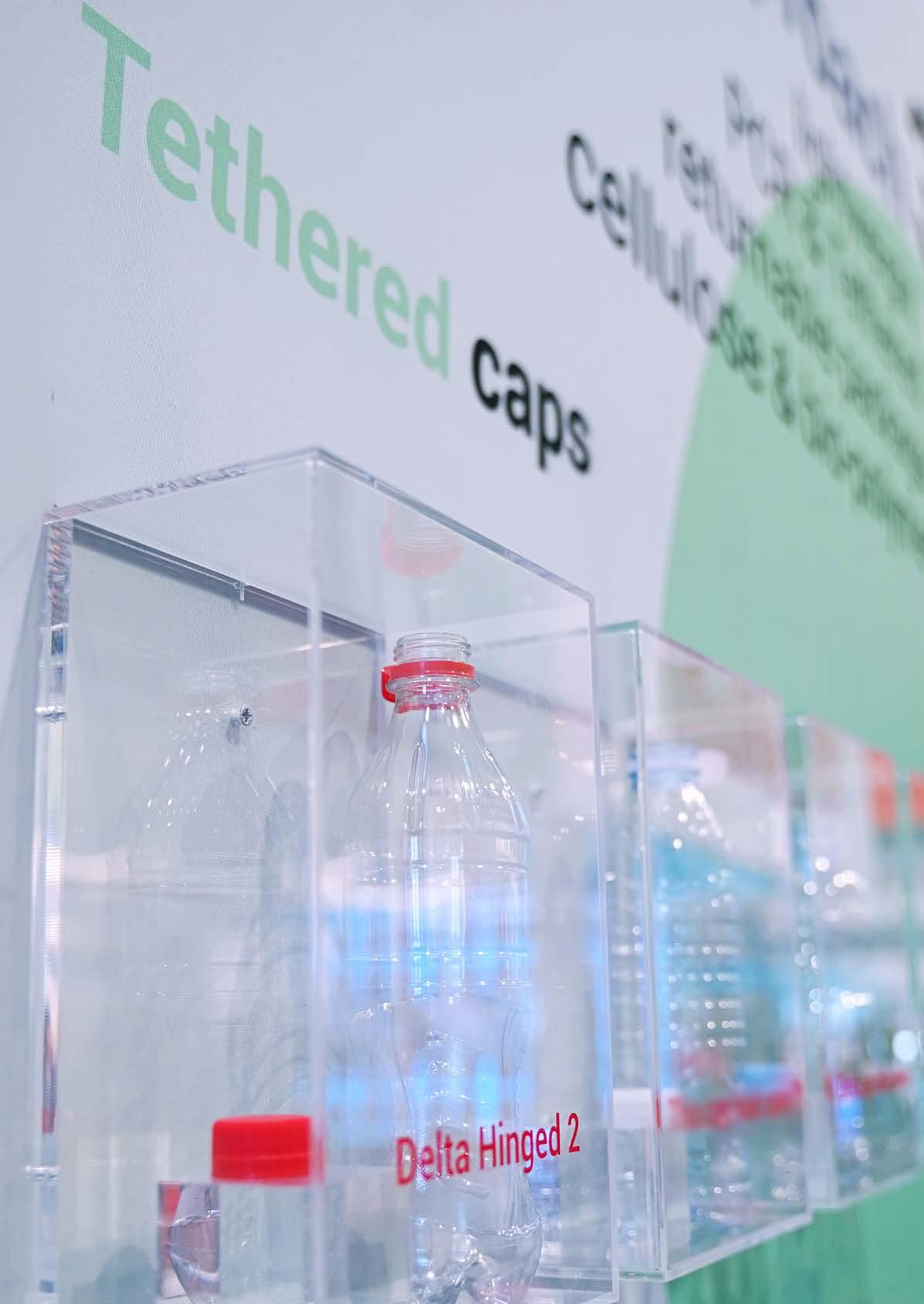
Rigid Packaging
In 2023 the Business achieved net growth, further improving on a 2022 that had already outperformed 2021. Orders remained high throughout the year, up 26% on the previous year and outstripping forecasts by 5%. Spare parts sales also performed well, with significant gains (+19% in 2022, +44.5% in 2023 ).
Rigid Packaging, together with the beverage sector in general, continues to grow thanks to demographic growth and the more widespread consumption of bottled water, which solves problems of food safety and accessibility, especially in rural and developing areas.
Past socio-economic challenges, such as the pandemic and concerns about excessive use of plastic, are gradually receding, while emerging trends point towards growth and confidence in the sector's ability to pursue innovation. Such innovation largely focuses on the environmental impact of products and processes: this is increasingly the case worldwide, regardless of the regulatory framework which is, as is known, considerably diversified.
From the perspective of Rigid Packaging Business, this positive backdrop nevertheless requires a degree of caution. The complexity of the patent landscape, the growing influence of Chinese players (especially in Russia, where they are facilitated by the Europe-US embargo) and constant efforts by mold and injection press manufacturers to boost performance demand a guarded approach. In this scenario, SACMI's reputation and brand continue to go from strength to strength thanks to synergies between the various products and its valued ‘consulting’ services vis-a-vis SACMI’s market-leading technologies. The outcome is the ability to build long-term partnerships.
As market shares increase, challenges nevertheless remain: punctual delivery on what is a highly competitive market, the ability to follow customers at every stage of the order and, crucially, provide effective post-sales services,
The sector continues to enjoy systematic growth, with a net increase in volumes following an already-impressive 2022. SACMI reaffirms its reputation and technological leadership, as highlighted by its ability to provide customers with valuable innovation and green transition consultancy services
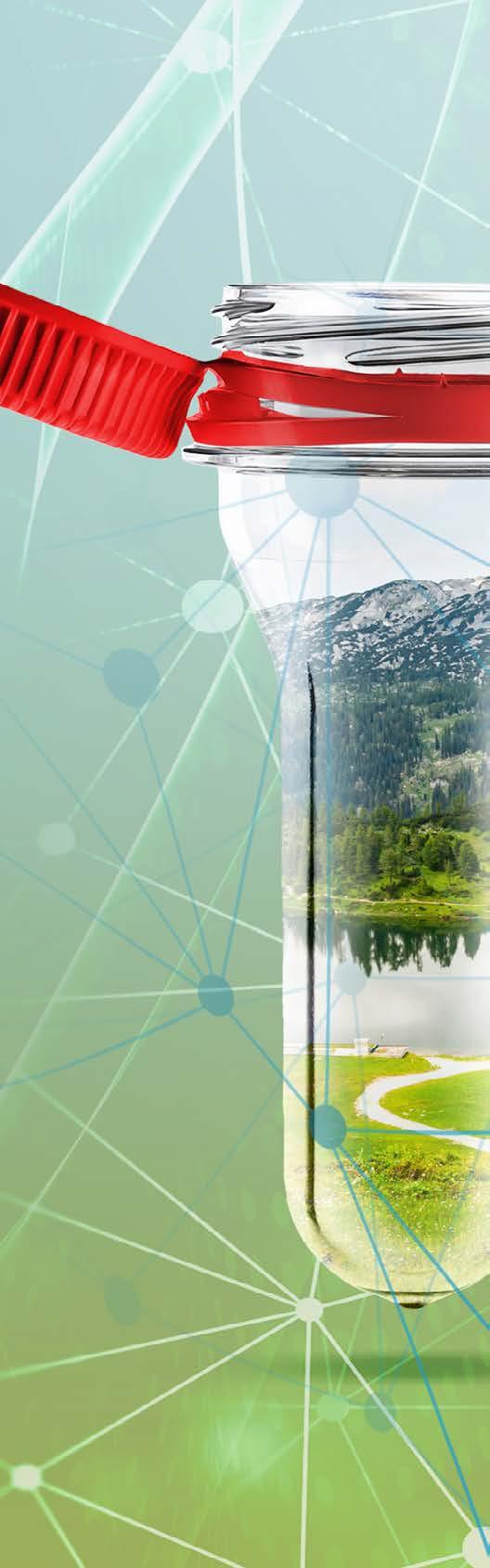
all while listening attentively to their needs. This is why the Business continues to invest in greater effectiveness, versatility and organizational efficiency , with valuable support coming from the adoption of digital tools and platforms.
Markets
In China, 2023 saw many bottlers moving towards self-production of caps. This had a positive impact on sales, allowing us to maintain good revenues despite a slowdown in growth on the Chinese market.
Consequently, this has led to excess installed capacity with an increase in the supply of used machinery on Chinese and African markets. Looking ahead, concerns about the macroeconomic instability induced by the construction crisis remain. Significant investments were made during the year.
One key player installed two new CCMMs and placed repeat orders for several ring-pull metal cap production plants.
Following a period of contraction caused by the pandemic and its aftermath, Latin America enjoyed an extremely dynamic 2023. Solid relationships established with the main multinational groups are bearing fruit, helping to generate one of the most significant results of the current year.
In the three-year period 2020-2023, Africa grew steadily, becoming the Business’s leading market. However, while there has been rapid expansion of the installed machine pool, the challenges of such a diverse continent remain. These take the form of difficulties in providing uniform service, with bureaucratic and logistical complexities hampering the establishment of facilities from which to deliver after-sales services coherently and efficiently.
In India SACMI technology continues to arouse keen interest, especially among leading beverage producers who are considering self-producing caps. This brings new opportunities, together with a need to maintain a delicate balance with traditional customers.
Widespread adoption of SACMI cap design solutions - undoubtedly a positive in itself - merits
caution as it galvanizes large-scale players to become autonomous, thus encouraging the emergence of local mold suppliers.
Customer Service
During 2023, the after-sales sector experienced a series of significant events that influenced both approach and strategy. On the one hand, volumes continued to rise significantly, particularly as regards Network sales, resulting in achievement of the strategic goal set in 2020. On the other hand, rising costs emerged as a serious challenge; at the same time, however, this offered an opportunity to structure spare parts lists in a way better suited to maintaining market competitiveness.
The introduction of Smart Pack services and further development of subscription service plans in 2024 ( Smart Care , on-site preventive maintenance contracts) are in line with market trends and therefore have the potential to make additional contributions to future results. Supply chains and logistics remained a key priority in order to prevent any delays in deliveries. Higher sales volumes, of both machines and spare parts, also raised issues vis-à-vis the facilities and the organizational frameworks needed to ensure adequate levels of assistance in individual areas, especially in regions such as Africa. This is why, in the face of such exceptional expansion (+44.5% in 2023), it will be crucial to keep pace with new challenges to ensure sustainable growth and continued customer satisfaction.
Several promotional events were held during the year to strengthen SACMI's role as an all-round partner in technological fields where it holds a leadership position. For example, Green&Digital involved over 250 participants from 61 countries. Covering topics that ranged from global trends to technological innovations - especially the advanced controls that deploy digital tools and Artificial Intelligence – the event offered an opportunity to discuss sustainability/digitalization prospects in the Rigid Packaging field, with considerable emphasis on the transition towards new standards such as the 26/22 mm necks and the D4R (Design For Recycling) approach, developed by SACMI in synergy with the global industry’s key players.
Sectors
Plastic caps. Plastic closures enjoyed significant volume growth during the year. Key factors contributing to the reinforcement of SACMI's market position included the imminent conversion to tethered caps, scheduled for July 2024. This has led customers to accelerate their switchover plans and take advantage of SACMI solutions that let them adapt their production facilities and approach potential new customers.
Transition to the new 26/22 mm necks also speeded up as part of a wider effort to reduce bottle weight and optimize still and carbonated drinks packaging. This adjustment, which also involved the adoption of new SACMI caps by some of the industry’s major players, was the result of constant efforts to provide original, timely solutions; this paves the way for a broad range of products that help customers make any replacement of the traditional 28 mm necks (PCO1881) as smooth as possible.
Higher market shares also stemmed from the emergence of new customers, underscoring SACMI's ability to penetrate new segments and win the trust of a growing customer pool. Multiple orders from a leading Chinese customer also made an important contribution to the financial result in 2023.
Integrated Annual Report 2023 / SACMI Group / Rigid Packaging
Metal caps. Similarly, the metal sector also experienced significant volume growth in 2023. Interest in crown caps remains steady. This results in new investments that allow existing producers to upgrade their technology or new ones to enter the market. As an alternative to crown caps, more and more manufacturers are proposing Pull Ring closures, especially on the Chinese market. With regard to alu-caps, significant investments continue to be made in both ROPP and MASC solutions despite strong competition. PMA machine sales remained stable.
Preforms. The PET Division closed 2023 with a substantial increase in revenues (+55%). The result was also satisfactory in terms of order regularity, despite the fact that most orders came through towards the end of the year. Sales were well balanced, with all machine models ( IPS 400 IPS 220 and IPS 300 ) being purchased. Some of the projects completed during the year included new combinations, such as the IPS 300 with 128 cavities or the IPS 400 with 144 cavities, equipped with NanoPitch molds for 26 mm necks.
Looking at markets, repeat orders were received from major customers in Africa and Asia, underlining customers’ trust in the reliability and performance of IPS technology. Looking ahead, the crucial factors will be cost control in order to maintain competitiveness, the expansion of mold-making partnerships and completion of the mold range produced directly by SACMI to cover the full machine range.
Containers. The Linear Blow Forming ( LBF ) project is nearing finalization. On completion, it will be possible to assess the potential of this ‘linear’ evolution of the compression and blow-forming process. Although not yet available on the market, the technology has already aroused keen interest, opening the way to future opportunities and developments.
Overall, 2023 was characterized by several key events from both a market (especially pharmaceutical) and technological perspective, with a trend towards adoption of ground-breaking, more sustainable ‘full electric’ solutions that fall within the scope of the new SACMI LBF proposal.
Post-processing. In addition to Velomat products, the Division also supplies slitting and folding machines . Revenues increased notably in 2023 (+58% for Velomat, a staggering +69% for slitting and folding solutions, which can also be sold as stand-alone units). There were several reasons for this increase, one being the imminent coming into force of legislation on tethered caps (SUP Directive), with a resulting increase in projects concerning slitting of the tamper-evident band both on compression-made and injection-made caps. In the assembly sector, the number of customers and projects in the dispenser field continues to rise, favoring direct Velomat-managed volumes. Projects involving product synergies between slitting-forming (SACMI Imola) and assembly (Velomat) are also experiencing a steady upswing in both the plastic and metal sectors.
Computer Vision Systems. The CVS Division closed the year with higher volumes (and extremely strong growth compared to 2021). During 2023, several initiatives sought to enhance the competitiveness and positioning of the systems. These included optimization of components and reallocation of some production operations on the Network (e.g. in China, with direct production of CHS systems). Considerable work also went into standardizing inspection solutions to simplify production processes. Investment in the specificity of the systems (e.g. introduction of the SACMI Smart Camera) sought to provide targeted answers to customer needs. In parallel, the year saw a leap towards the introduction of systems that deploy Artificial Intelligence such as the installation of the first AI-based inspection (Anomaly Detection) systems. New AI functions have been incorporated in the CVs software suite , such as the new Classy AI for automatic defect classification. Development of the new chatbot-style machine assistant, GILDA AI - previewed during Green&Digital - also continues.
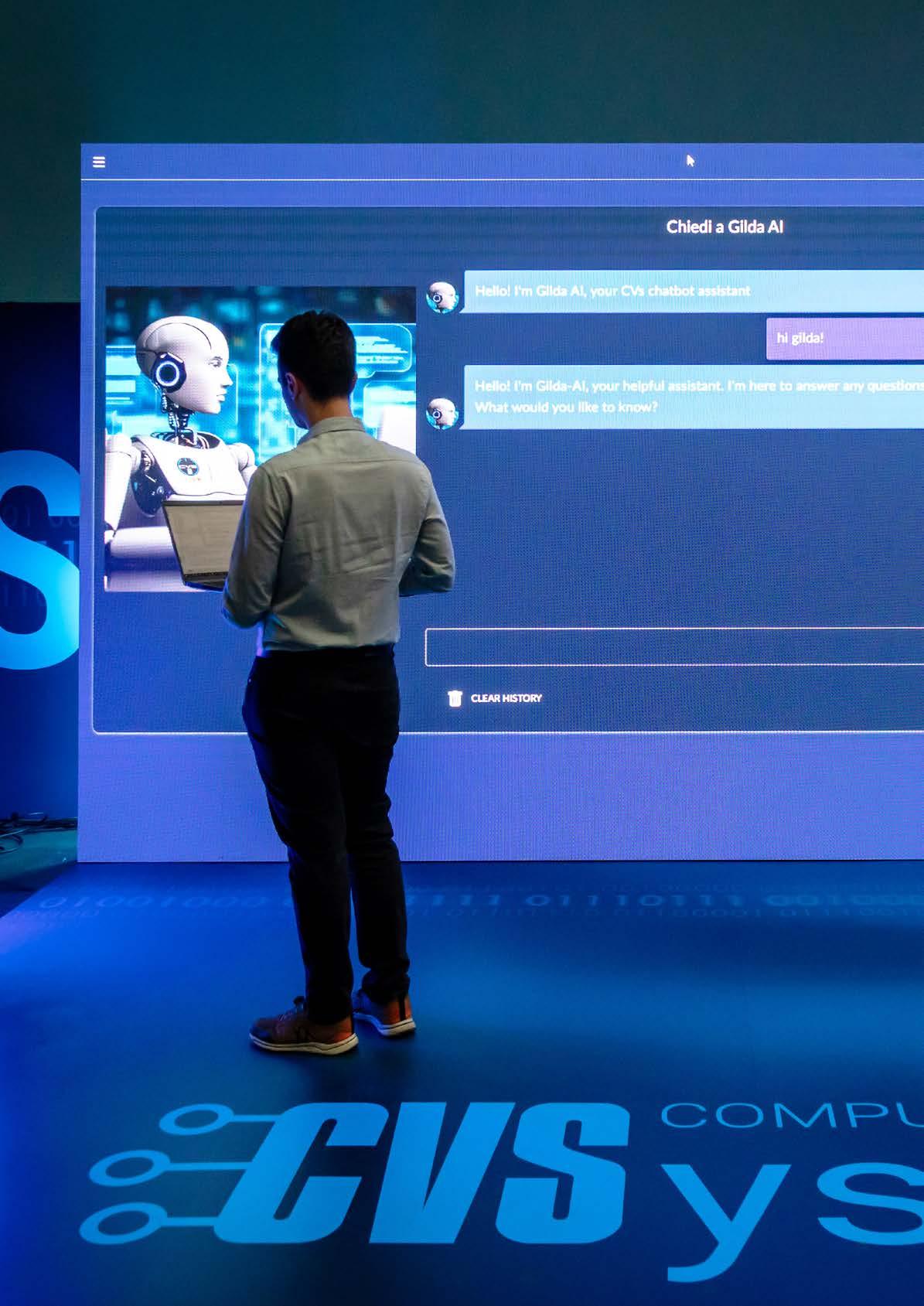
Key technological innovations
In 2023 SACMI invested in areas that have the highest development potential, involving both product development/design and further digitalization of the CCM range of presses and compression molds.
Digitalization as a tool for raising plant efficiency and simplifying the use, management and maintenance of machines continued with the release, in early 2024, of the new Smart Pack 2 which allows even more proactive, accurate control of hydraulics and deep control of plant consumption.
At the same time, development and promotion of the Smart Care project for incloud gathering of machine data continued with the arrival of new assistance and proactive problem-solving packages. Another new feature is the on-press prediction function which, via Smart Care, gives users a heads-up on production parameters and allows for predictive maintenance. Looking at lines that are likely to be strategically vital in the coming years, the first full electric CCM press model was developed, in part with the aid of extra-sector technological scouting.
On the product side, the year marks the consolidation of the 26/22 mm solution, for which SACMI offers the widest family of caps on the market in both tethered and non-tethered versions. The SACMI Lab has a unique ability to combine comprehensive product (cap+preform) consultancy with solutions certified by the industry’s main global players. This has helped many customers make the transition, taking the global annual installed output capacity for this new standard to over 39 billion caps: a figure that continues to grow.
A project to develop the annular lining on press & twist baby food caps by using PMA technology and PVC-free material offers major advantages in terms of energy savings (30-40% compared to traditional technologies). These savings stem from a plastic cooling process that, unlike traditional technologies, releases no fumes into the environment. In this same field, SACMI is also exploring solutions aimed at developing complete twist-off and press-twist cap lines Investigation of the new ULG (ultra low gauge) lightweight crown cap continues.
The IPS 300 remained in a class of its own in 2023, as it is still the only press on the market to incorporate the PVS156 process inspection system
During the year, a system that ensures compatibility of both SACMI and third-party molds (already a feature of the larger IPS 300 and IPS 400 models) was completed on the IPS 220
From a strategic standpoint, development of the new IPS 500 extends the range even further.
A project to implement an AI tool on IPS to simulate the flow of operator actions-decisions is also in the pipeline: this will provide new output probabilistic control functions to lend support to the Customer Service team.
Technology
Smart Pack 2 latest release
On CCM presses, for even more advanced hydraulic controls and deep control of plant consumption
integrated PVS156 system
IPS 300, the only press on the market with an for process control.
New IPS 500 completes the range
LBF (Linear Blow Forming)
New technology to optimize container production processes
CVs software Suite
Structuring of software packages for data analysis/logging and automatic defect classification
EFL (Electronic Flexible Linear)
Renewed success for technology following the first project in 2022
Development of Linear Blow Forming (LBF) continues: this new technology takes the long-standing CBF solution to the next level by introducing a linear process that optimizes efficiency of the different phases and the compressionblowing preform production sequence. Once the first simulator tests have produced good results, the solution will be trialed and presented to the market during 2024.
Standardization work to achieve manufacturing simplicity and optimization of system costs and footprints was completed, providing the dual advantages of lower environmental impact and greater versatility.
The main development in 2023 was the structuring of the software packages within the new CVs suite (CVs22, integrated on machines and common to all systems, CVsWEB, the remote-controlled data analysis/logging platform, Classy AI for automatic defect classification).
Both branches of improvement (hardware optimization, new software packages) are part of a broader SACMI vision development strategy that increasingly sees such systems as a complex of highly specific mechatronic systems for each stage of the process; in parallel, they’re also designed to help workers perform the deep detection that identifies any process drift, thus simplifying management while embracing cybersecurity principles.
The EOS ‘electronic nose’ project, co-developed with the Polytechnic of Milan to uncover applications in the biomedical field (support for the identification of serious pathologies), aims to proceed by establishing a dedicated start-up.
In 2023 Velomat further refined its multi-component closure assembly solutions for the Food & Beverage, cosmetics, pharma and medical sectors, with the company continuing to grow by strengthening technological and commercial synergies within the SACMI Group.
Consolidation of the dispenser assembly application with Electronic Flexible Linear (EFL) technology produced good results during the year, winning over major new customers following the project’s successful completion in 2022.
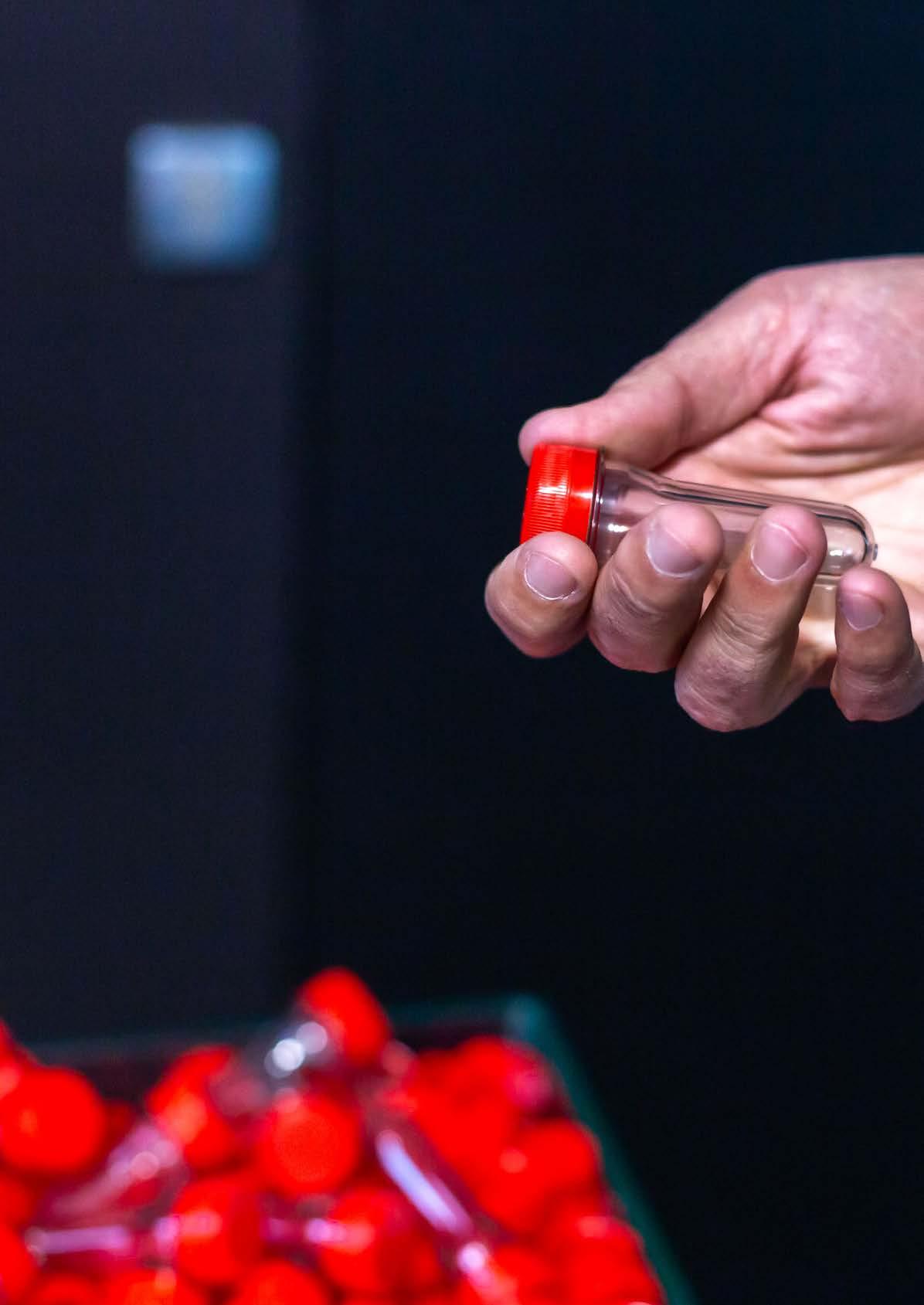
Impact on sustainability
Plastic caps Once again in 2023, SACMI capitalized on its global leadership in the manufacture of one-piece caps with compression technology to help customers make the green transition
On the one hand, this has meant ongoing adjustments to machines (for example, the new CM-Flow launched in 2022 was upgraded; this, alongside other solutions, has helped drive down overall electricity consumption on the presses by up to 20%. Moreover, further studies on plant optimization were initiated to implement an increasingly holistic approach to each component of the line).
On the other hand, it has meant tireless research, development and the market launch of new products, designed to accelerate results from a 3Rs (reduce, reuse, recycle) perspective.
From a lightweighting viewpoint, the SACMI Lab has further expanded the family of 26/22 mm neck solutions, now the broadest on the market; this format can reduce the quantity of plastic in each cap by up to 30%. Certified by the industry’s key global players, the SACMI Rigid Packaging Lab is increasingly a point of reference for manufacturers: it provides optimized, customizable solutions for individual customers and markets, also factoring in consumption habits to streamline the success of the proposed innovation. On finished caps, SACMI's role as a partner in the transition towards the tethered standard (the application of which is imminent) continues to go from strength to strength thanks to its post-processing slitting solution. A solution for hot’ band slitting is also being investigated with a view to saving energy, reducing TCO and optimizing plant layouts.
Looking to 2030 (i.e. the Plastic and Plastic Waste Regulation Directive that will set container re-use quotas), SACMI has completed the design of the new lining machine (PMD) for floating disks on plastic screw caps for reusable bottles. Research into alternative materials also continues. More specifically, in 2023, development of the new cellulose fiber cap, which uses dry molding technology, stepped up a gear. The first molding tests will be performed in the field in 2024 together with a leading global player in the dairy sector (fresh milk packaging).
PMA annular lining machine: this SACMI solution makes it possible to supply products that use less plastic and are, above all, PVC-free With the ULG project, SACMI delivers net raw material savings without lowering cap performance. From an environmental perspective, this not only means reduced raw material requirements: it also translates into significant processing-related energy savings and can reduce metal-steel consumption by up to 20% requisites remaining equal.
Already a reality on international markets, the recycled PET supply chain has led the world’s main preform machine manufacturers to modify the design of their presses to accommodate ever-increasing quantities of recycled PET. The current SACMI IPS range is configured to operate with up to 100% rPET.
On the plastic caps front, one of the most promising trends in terms of the industry’s future sustainability is the rHDPE project (i.e. the creation of a cap-to-cap recycling chain for food- grade use that meets specifications established by key international authorities such as EFSA in Europe and FDA in the USA).
Already a reality in the PET sector (thanks to the coming into force of the Single Use Plastics directive, which requires containers to have a recycled PET content of no less than 25% by 2025, yet also the intrinsic nature of this supply chain where the bulk of the retrieved material, namely PET, already comes from food use), the challenge of creating a high-density polyethylene (HDPE) recycling chain led SACMI to outline a four-phase project, which was completed successfully in 2023.
• Procurement of recycled HDPE deriving mainly (>95%) or exclusively from the foodgrade supply chain (a possibility aided by the new tethered standard, as caps are still attached to bottles when sent for recycling).
• Regrinding of the flakes from which the pellet is obtained (already subdivided by macro- color) and separation/selection of flakes according to color.
• Research to determine the most effective decontamination system to guarantee food safety.
• Molding tests on a compression press for performance comparison purposes (cap made with recycled resin vs cap made with virgin resin).
So far, the results have been highly promising. This will allow SACMI to present itself to the market as a direct supplier of raw material and know-how (regranulated HDPE already divided by macro-color and with the correct usage specifications according to the product to be made), ensuring compliance with existing regulations. This project is part of the D4R (design for recycling) approach, in collaboration with the major global players in the sector.
Containers
Post-processing Plants
Note also the availability of a new hopper that extends the proportion of recycled PET in flake form to 75%.
In container manufacturing too, research continues into alternative materials (composite bioplastics) and the replacement of standard resins with those that are easier to recycle (e.g. PET). Several application areas have already been identified for development (containers and coffee pods).
Velomat has created an assembly solution that allowed a leading international player to produce, as early as 2022, the market’s first ever dispenser made entirely of plastic (i.e. without springs or metal spheres), aiding proper disposal from a circular economy perspective. This solution has continued to gain consensus, winning over new customers in 2023.
Remaining on the topic of post-processing, development of the new slitting/ folding machine with an electronically timed cut continues: this new platform increases the sales potential of lines for the returnable empties market, the aim being to achieve more efficient waste cycle management.
With PROTESA, a feasibility study to respond to demand for turnkey photovoltaic systems that help ensure continuity of production, especially in Africa where around a hundred systems could potentially be built.
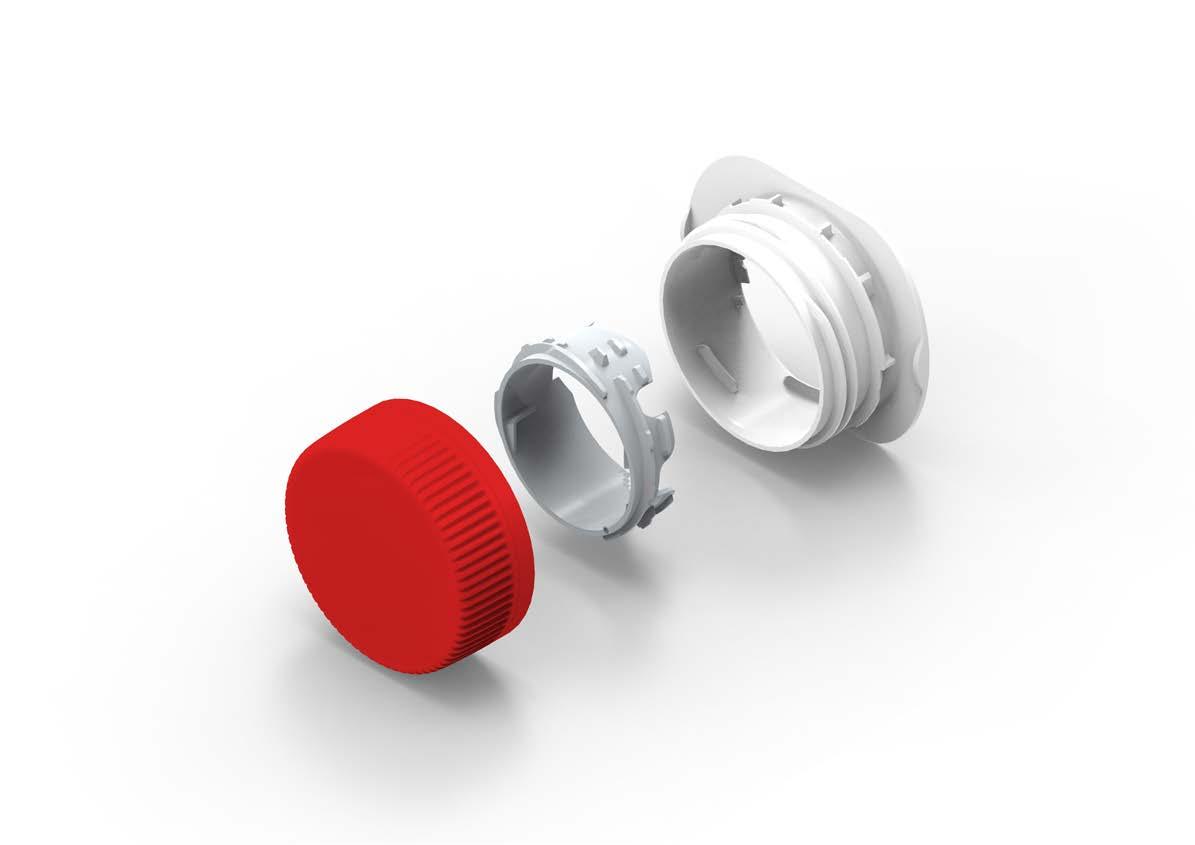
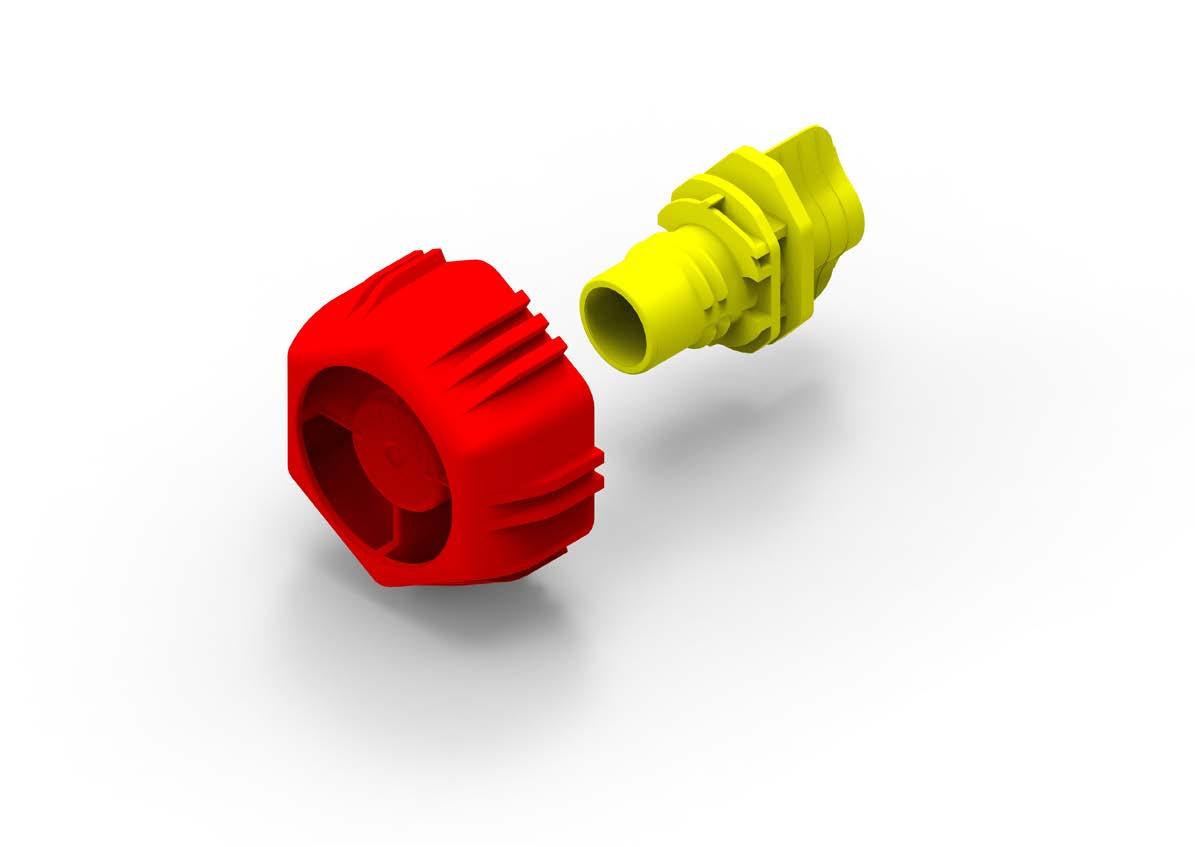
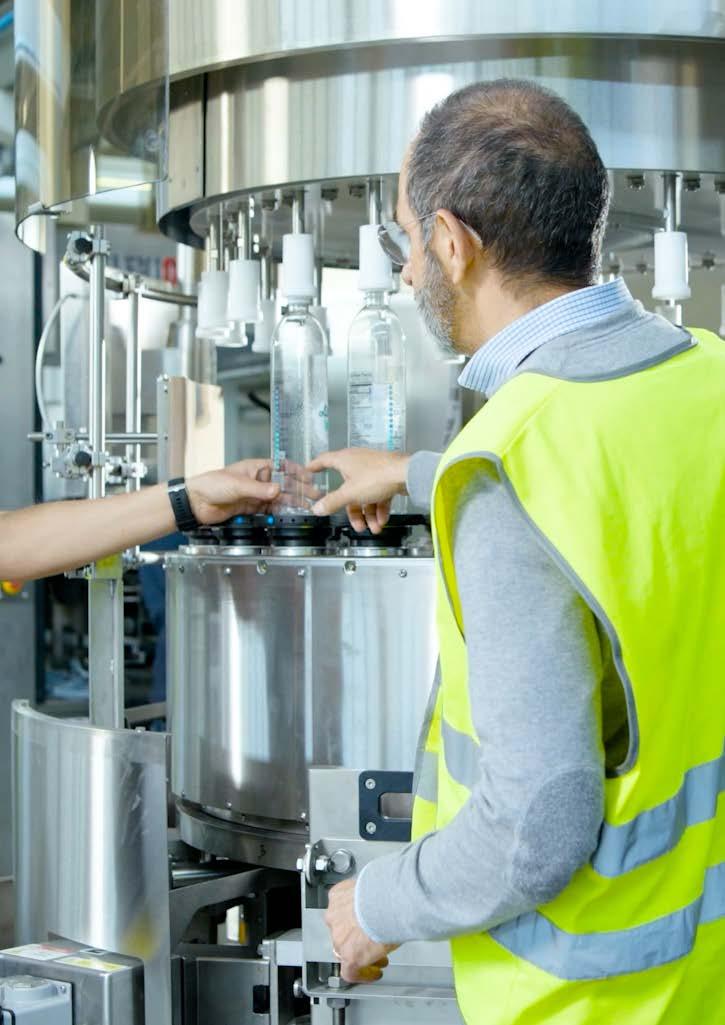
2023 was a positive year for the Business, with performance outstripping that of 2022. Record revenues and growing economic results occurred in all areas, from complete plants to labelers and after-sales services. The number of orders continued to rise, a trend already seen in 2022 with the post-pandemic recovery. In general, the market has rewarded the business strategy of focusing investment on ‘ core technologies such as PET and CSD.
The procurement issues that had affected the previous year gradually waned, especially in the electronic components sector.
Vice versa, the higher volumes of 2023 required an adjustment - which is still ongoing - to the organization’s output capacity, both in terms of machine manufacturing and the supply of spare parts.
Labelers and Bag-In-Box
Again in 2023, the bulk of direct machine sales were made on mature markets . Despite the outstanding results, continued investment in R&D to bolster SACMI's role as the industry’s technological leader remains a strategic necessity.
Bag-In-Box operations succeeded in tripling their 2022 result: 2024 has also got off to a strong start. The segment has won over some major customers, again mostly on mature markets.
The 2022 trend towards the sale of complete plants continued.
Bag-In-Box results tripled and labelers performed well, with sales concentrated on mature markets.
In the after-market segment, the new customer service model was upgraded with personalized, medium-long term maintenance plans
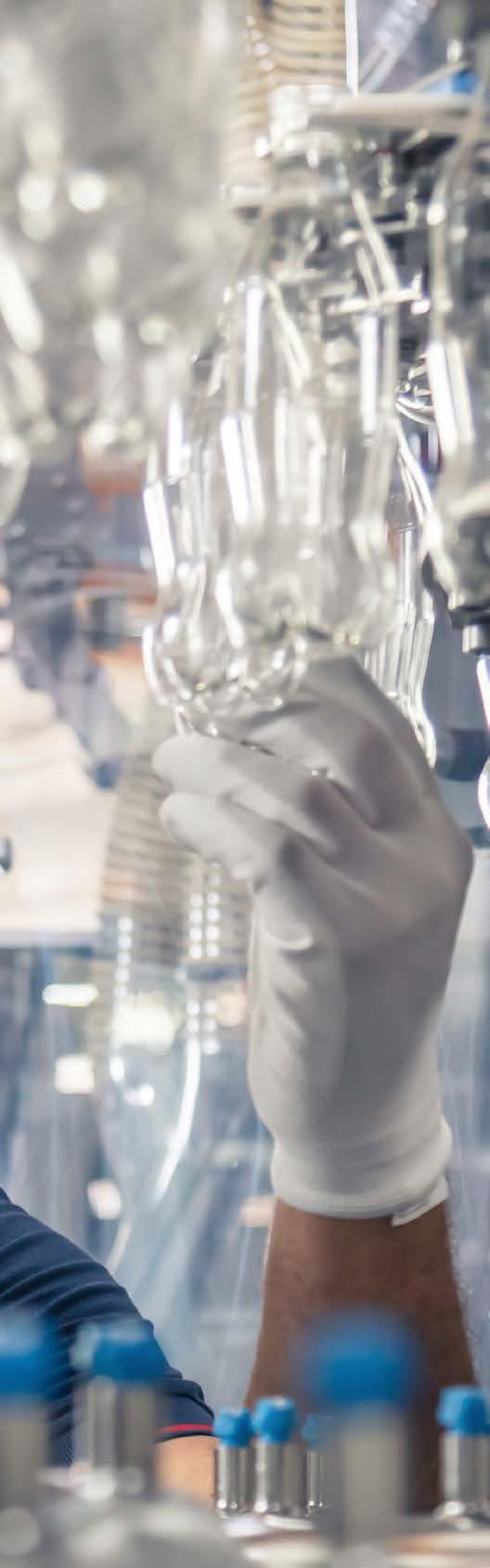
Beverage machines and plants
In 2023 sales of machines and plants followed the trend observed in 2022, with the majority being supplied to emerging economies . Already-acquired customers placed further orders and new ones were gained. Several stand-alone solutions were also sold. Performance on Asian markets was down slightly. On the FFS (form-fill-seal) front, the number of projects was limited. Nevertheless, the main customer in Japan continues to place orders, potentially acting as a driver for further sales opportunities.
Customer Service
Results were outstanding, especially spare parts sales, which are being driven by a broadening range of multi-year scheduled maintenance plans. From this perspective, the after-market results stem from years of work aimed at building and enhancing an effective customer service model (personalized, medium-long term maintenance plans). We are now reaping the rewards, with good prospects for further business growth in the years to come.
In keeping with this logic, the goal is to adapt and extend such services to all the business's production facilities (Parma and Verona).
machines and plants
Key technological innovations
Standardization and modularization of the product portfolio continued throughout the year in order to capitalize on SACMI expertise and expand the range of solutions available to customers.
The new electronic capper (FEC), released in 2022, continued to perform well in 2023. During the year, several projects confirmed the soundness of the solution, with high levels of customer satisfaction.
With a view to completing the stretch-blowing and filling range, a new preform feed system prototype was developed during the year. Initial testing demonstrated excellent functionality and efficiency compared to traditional systems. This year’s goal - in partnership with the leading supplier of preform orientation systems, who has been licensed to use the system - is to carry out full testing of the prototype on the customer's site.
Throughout 2023, the strategy of customizing the range proved to be a winning one, with a second solution for the one-gallon format being sold on the American market.
In keeping with the strategic service model development plan, the help desk was optimized in 2023 to enhance the customer experience.
Established in 2022, the center confirmed its strategic role in terms of both relationships with customers (product design) and its capacity to capitalize on Group skills (Rigid Packaging Lab).
2023 highlighted the soundness of synergies within the Group, with Computer Vision solutions being integrated across the entire range of Beverage machines. System digitalization proceeds apace: a far-reaching revision of machine diagnostics was launched, with the implementation of new self-diagnostic functions that simplify and speed up troubleshooting
Impact on sustainability
Exclusive SACMI solutions designed to enable the set-up of r eturnable glass and PET supply chains continued to gain approval (special washable glues, fewer glue dots applied to the label).
The Business also continued research into replacing traditional container-making materials with alternative resins the goal being to enhance compatibility with existing recycling chains. More specifically, the search continues for market actors interested in new applications such as PET yoghurt pots or, in the BIB segment, the possibility of replacing traditional non-recyclable bags with ultra-light PET bottles (PET-In-Box), an opportunity already brought to the attention of key players in the industry.
The range continues to evolve, making it easier to manage ‘lightened’ caps and containers on Beverage machines. A case in point, the electronic capper (FEC) provides greater performance and flexibility with light caps.
Development of the new compact oven for stretch-blow molders finalized: this increases energy efficiency by +20% and takes up less space. A successful experimental phase was followed by construction of an industrial model that confirmed the results.
The development of remote diagnostics (with troubleshooting and preventive maintenance functions) continues to play a strategic role in reducing the use of consumables and optimizing work on lines. The business pursues its connectivity goals in keeping with the wider Group strategy of developing new digital customer assistance services based on machine data acquisition.

The year proved to be a positive one, with a sharp increase in net profits. The distinctive Defranceschi range continued to go from strength to strength at both technological level - thanks to numerous patents - and in terms of customers and market reputation.
Alongside finalization of multiple projects , order books continued to fill throughout 2023. This has resulted in a portfolio that will commit production facilities throughout 2024 and 2025, thus improving a manufacturing efficiency that is normally impacted by the seasonal nature of the industry. More specifically, 2023 saw the completion of the KRUG project, which produced excellent results and high levels of satisfaction: indeed, the customer is already thinking about further expansion over the next few years. Already operational, the new winery will be officially inaugurated by spring 2024.
The project's success has paved the way for further orders, most notably Defranceschi’s attainment of the tender for Cométe, another prestigious Maison belonging to the LVMH Group.
At the heart of the Champagne range are our vertical twin-compartment tanks and the Defranceschi-patented multi-cell tanks, with layered domes that integrate into the architectural elements.
In Italy, the most noteworthy project was the complete winery contract signed with Tenute del Cerro, with Defranceschi being assigned both the standard and the architectural/design parts. Tank production began back in October 2023, and construction is expected to commence in July 2024.
The year also saw ‘consolidation’ of several aspects of the range: the new tank containing ceramic plates (highlighting the uniqueness of the Defranceschi range), stratified domes made of ceramic and other materials, and design solutions in pigmented steel. Given these characteristics, the new tank was selected by Vietti, in Piedmont, where it’s already being used to refine the fruits of the 2023 harvest.
In addition to the already-delivered 32-hectoliter version that has been on the price list since early 2024, development of a 17-hectoliter tank is also set to go ahead. Defranceschi will display this solution at upcoming trade fairs (starting with Simei 2024), alongside the new ceramic-bottomed barrique currently under development.
Fast-growing net profits. Successful finalization of projects paved the way for further orders.
Synergies with the ceramic sector are stronger, as highlighted by tanks with ceramic plates and the new ceramic bottom project for barriques
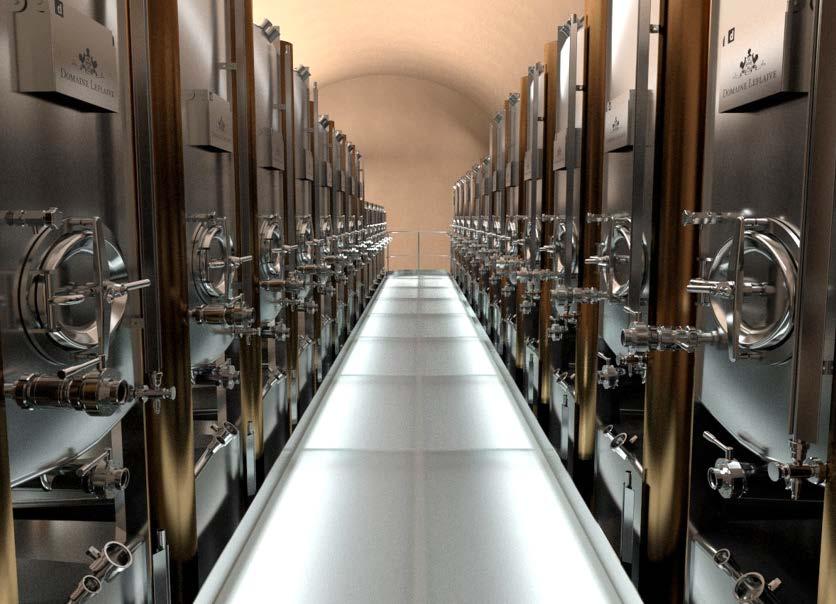
Every year, the world produces no less than 4 million barriques, 900,000 in France alone. The introduction of a ceramic bottom has huge potential as it could help solve a long-standing problem: the astringency caused by the untoasted wood on barrel bottoms which, unlike the staves, does not release the tannins correctly. To identify the best technical solution (a base strong enough to allow attachment of the wooden staves), development work is proceeding in synergy with the Whiteware and Tiles BUs.
This project also enhances the uniqueness of the Defranceschi range by leveraging internal synergies within the SACMI Group (i.e. by drawing on expertise in ceramics and extending its advantages to other sectors).
With regard to presses, development of a special press to extract aromas from coffee and chocolate powder continues. New growth opportunities are also expected on the spare parts side (e.g. replacement of the ‘drains’, the removable cloth
that filters the aroma distillates by retaining the powders).
In terms of investment in manufacturing facilities, the new cooling jacket spot welder installed in 2023 became fully operational. Moreover, a new polishing machine was installed and is expected to come online in early 2024. There was also extra-budget investment in the establishment of a new laser cutting line . All of the above focus on higher process quality, productivity, efficiency and sustainability.
Stable profitability and a considerable increase in the net end-of-year result for 2023 indicate Defranceschi is successfully implementing the strategy embarked on when it joined the SACMI Group: this has opened up new opportunities from an internal synergies standpoint and, more generally, prospects for new investment in business growth, driven by a healthy project portfolio and a strengthening market reputation.
Key technological innovations
Consolidation of the new tank containing ceramic plates with in-the-field confirmation of the advantages observed during prototype development (controlled micro-oxygenation thanks to the porosity of ceramic). The first sale of the 32-hectoliter tank was finalized, with a 17-hectoliter version currently under development.
Ceramic bottoms for barriques are now at the advanced testing stage, in synergy with the Whiteware and Tiles labs.
Development of a new aromas press: work continues on an optimal technical solution (the ‘drains’) to retain the powders and extract the liquids. Applied, at the design stage, to cocoa and coffee powders, this solution could later be extended to other products.
Introduction of the new laser cutting system to replace the previous (plasma cutting) line, boosting quality and productivity while reducing the need for further (edge grinding) processes. At the start of 2024 the new polisher was installed; this happened soon after the cooling jacket spot welder, installed in 2023, became fully operational.
Impact on sustainability
Defranceschi’s application of ‘stratified’ design on complete winery projects reduces wash water requirements. In the case of complete wineries, this allows for much more efficient use of water resources. In practice, the entire 3D winery can be washed as if it were a 2D floor, which also allows for the implementation of a water recovery and recycling system The Defranceschi wash bay features a water retrieval and purification system, which means the same water can be used for multiple washes or to perform leak tests.
Note also that the latest series of stainless steel presses with mirror-finish cylinder reduce press-cleaning water requirements.
Defranceschi’s exclusive tank with ceramic plates gained ground. In addition to technical advantages - micro-oxygenation, controlled porosity - this design extends the tank lifespan It does so by allowing, when necessary, intervention on individual worn plates without having to replace/dispose of the entire tank.
The new ceramic barrique bottom has the potential to reduce the environmental impact of barrel production (by using less wood) while offering advantages in terms of durability (the ‘eternal’ glazed ceramic bottom can be reused to make new barriques simply by changing the worn staves).
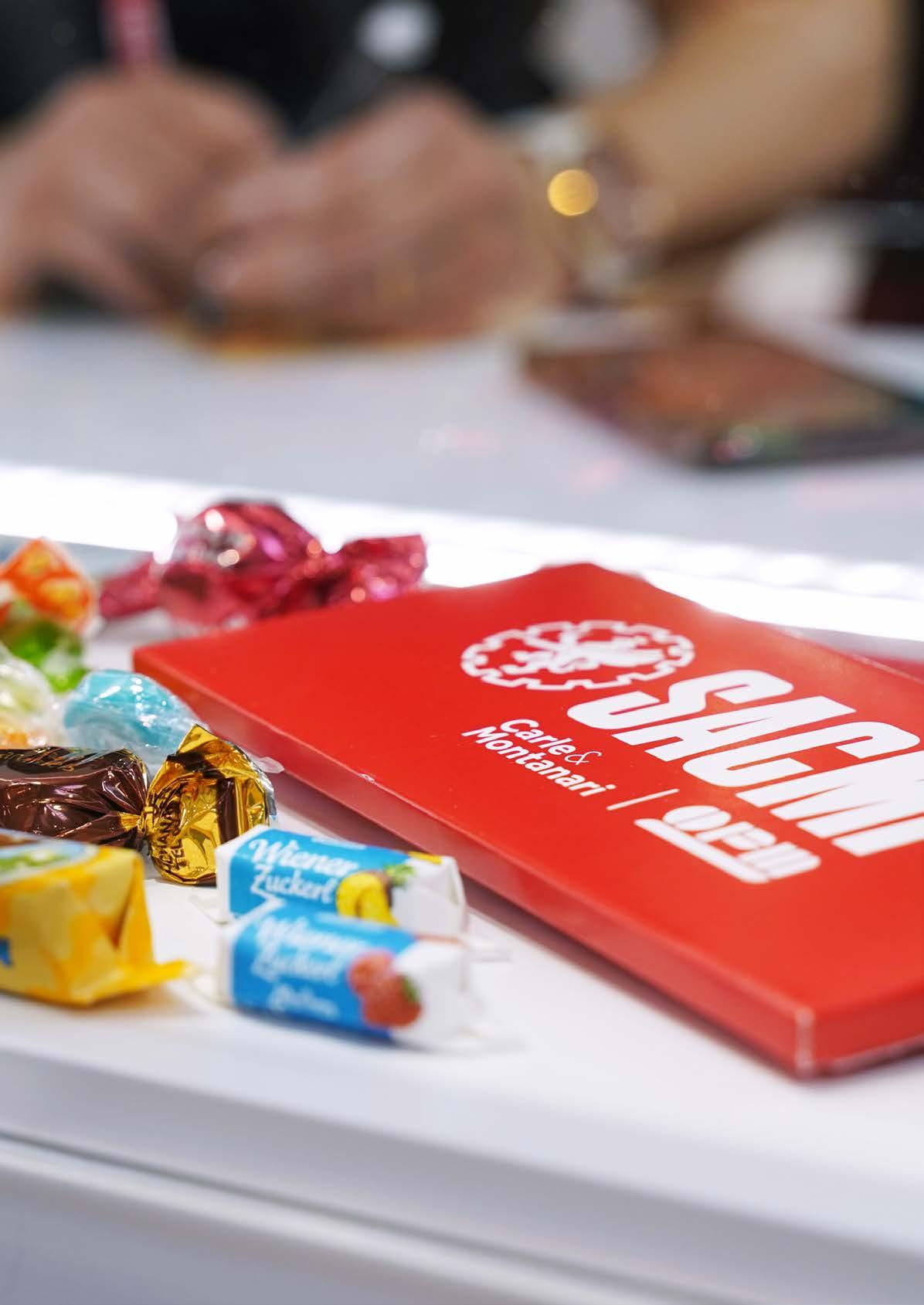
Packaging & Chocolate 1.6
In 2023 the Business generated record revenues, +15% compared to the previous year and by far the best result ever. This stemmed from a clearing of the 2022 backlog and steady growth in the first half of the year, generating excellent performance despite a certain market unease in the latter half of 2023. Results were driven both by machine sales and a steadily expanding after-sales sector, up by 20% compared to 2022.
Order acquisitions reflected market performance, strong in the first part of the year and sluggish in the second when serious geopolitical instability and the macroeconomic burdens of inflation and higher interest rates began to bite.
More specifically, customers in the Chocolate Business saw their investment decisions influenced by sudden, sharp price increases in key commodities such as cocoa and sugar.
Product Units
The year 2023 saw a to-be-expected rebalancing of the different product units. Wrapping and Tray Forming sales were essentially stable. Chocolate Process sales, instead, dipped slightly, with the downward trend more marked in Primary and Secondary Packaging (which had nevertheless sealed a major deal in 2022). Molding continues to grow steadily. Sales rose by more than 10% compared to 2022, itself a record-breaking year.
A record-breaking result, despite a slowdown in the second half of the year. Wrapping and Tray Forming stable, Molding steadily on the up.
Outstanding Chocolate performance in India, major premium-segment projects in Europe
Markets
Analysis of sales trend by geographical area underscores India ’s increasing importance as a chocolate market thanks to constantly improving social conditions and the resulting changes in consumption patterns.
In Europe , key projects went ahead in Belgium, a strategic country for the premium chocolate market, while Eastern Europe, despite a challenging political situation, continues to be led by Poland. The Italian market remains pivotal, thanks also to a major order tied to a Secondary Packaging project for a leading food customer.
Overseas, a good portion of orders were accounted for by the Mexico area, mainly linked to a Secondary Packaging project for a major, long-standing multinational customer. In parallel, the USA and Canada, which now have a consolidated Business presence, underwent significant adjustment following two years of strong growth.
After-Sales
Moving on to services, note that a more proactive approach - together with optimization of internal processes and a strengthening of the after-sales organization - has resulted in changes that enhance customer service and help boost revenues.
Scenarios and prospects
After two years of uninterrupted growth, the adjustment that came in 2023 was predictable: it allowed the market to metabolize the higher prices of industrial machinery and react to the chronic shortage of electronic components (this latter situation has since improved considerably).
The final two months of 2023 saw an upswing in the number of inquiries and related opportunities, allowing us to look to 2024 with confidence.
Key technological innovations
Numerous job orders were completed in 2023, two of them with a sharp focus on the design of plants that use ground-breaking robotic mold changeover systems Demand for such systems is expected to grow as they provide workers with considerable ergonomic benefits when handling large, heavy molds.
Strengthening of the medium-speed machine range continued throughout 2023: this was achieved, on the one hand, by driving development of the Pack Sud line through investment in facilities and, on the other, by expanding the OPM-brand flowpack offering by applying the concepts used on our top-of-therange JT-Advance
Development, on behalf of a large food multinational, of a snack/biscuit packaging line on which packaged items are placed in cases and shipped to largescale retailers where they reach consumers: this project is ambitious not just in terms of the adopted technical solution - camera-guided robot pickers - but also its sheer size (32 robots) and the required performance.
Impact on sustainability
New robotic mold changeover solutions improve working conditions and ergonomics for line operators, especially in large-scale plants where molds can be extremely heavy.
Throughout the year, heavy investment in facility development - needed to support volume growth, product/market changes and customer service - was accompanied by a strengthening of ties with universities and professional training schools, ties that play a crucial role in procuring talent with industry-specific expertise
Investment in the development of digital tools to define specific on-machine functions and drive the evolution of human-plant interfaces continued during 2023.
Meticulous attention to eco-sustainable materials, towards which the market is moving from both a social awareness and regulatory perspective. Thanks to its own research facilities and new technical solutions adopted by the wrapping and primary packaging sector, SACMI Packaging & Chocolate is ready to guide its customers as they make this critical transition.
ergonomics thanks to robotic mold changeovers
New technical solutions in wrapping to facilitate use of
eco-sustainable materials
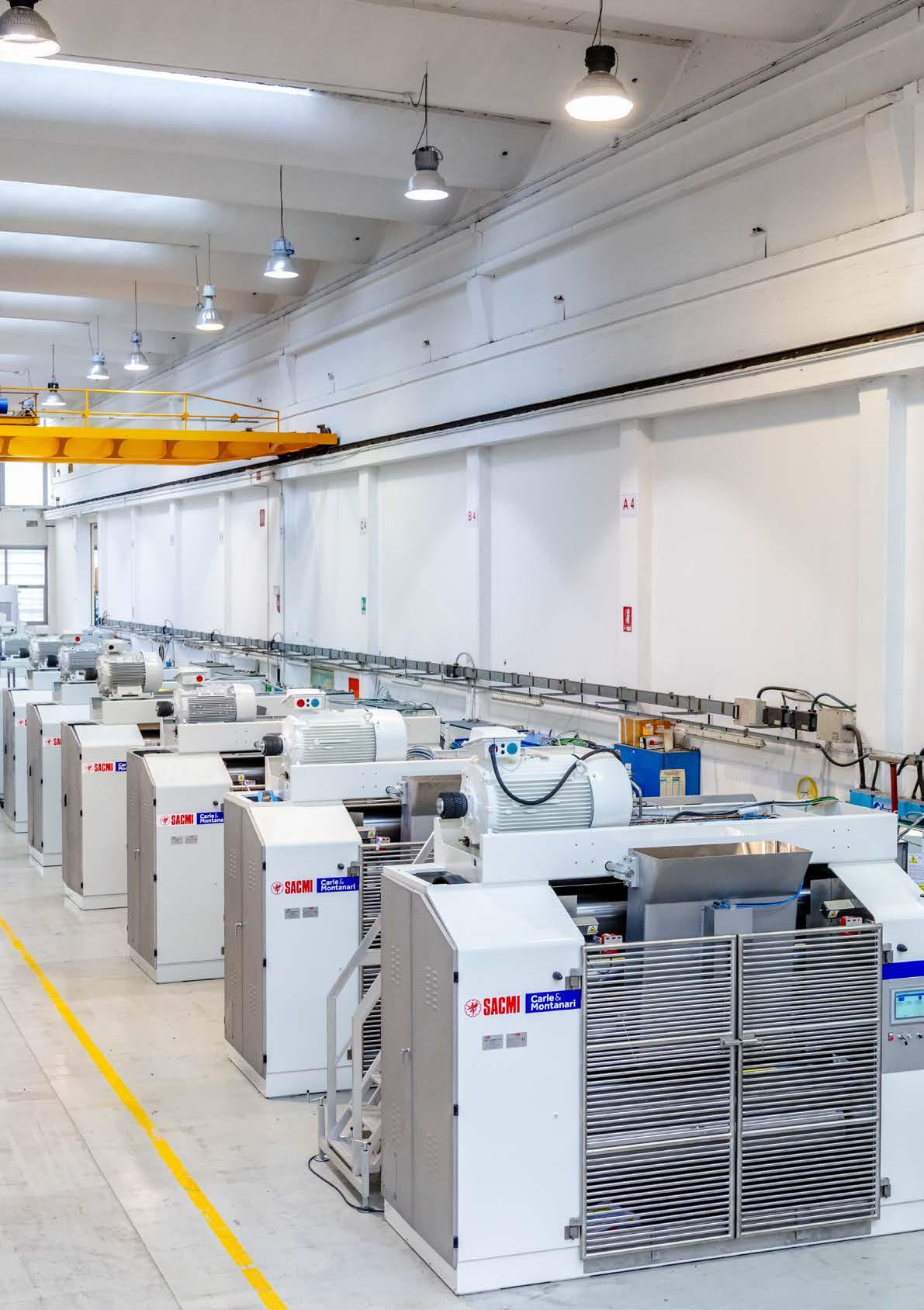
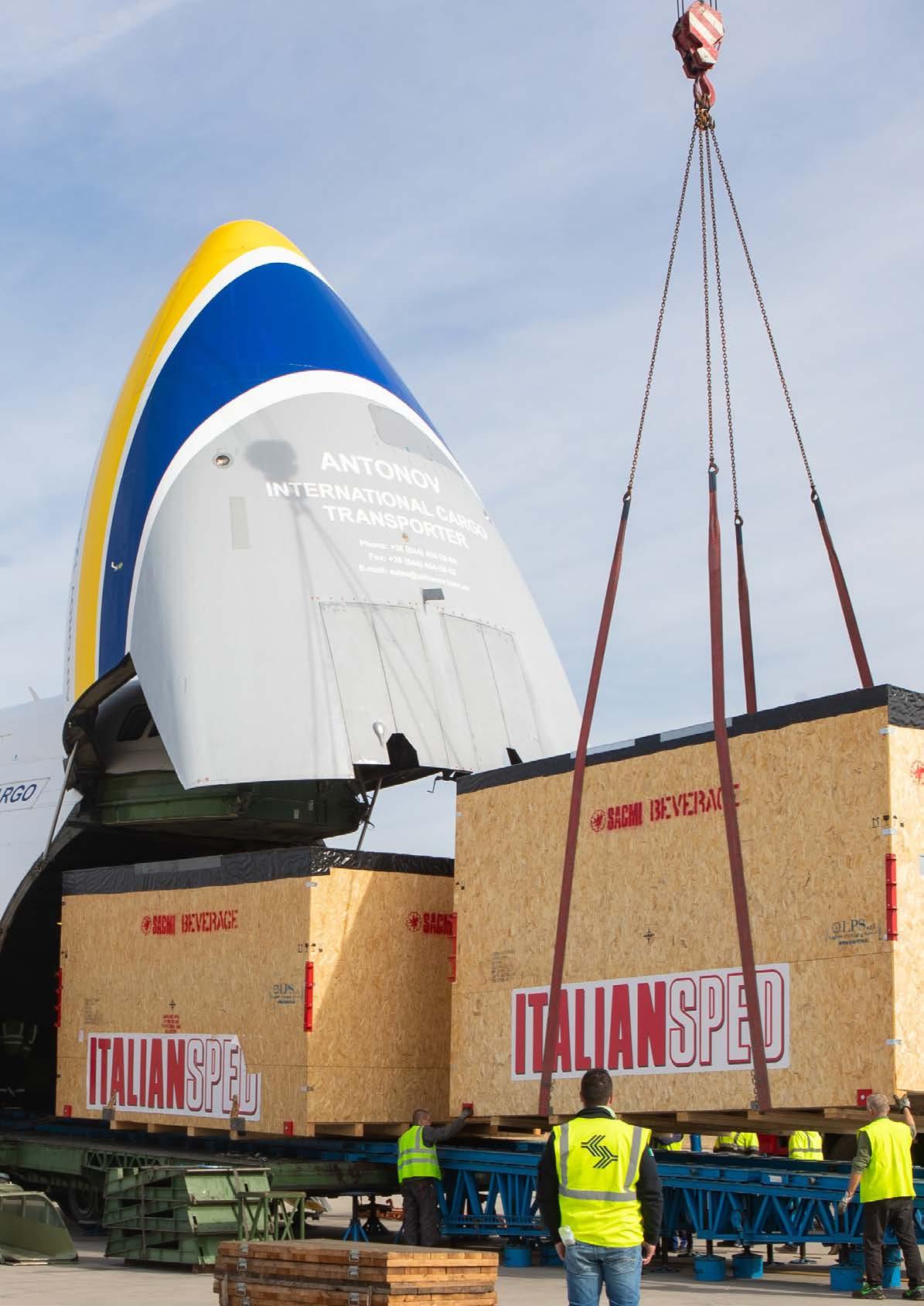
1.7
Logistics Engineering & Forwarding
The year 2023 was characterized by considerable market turbulence. Nevertheless, Italiansped responded with an outstanding result which, while it fell short of the extraordinary 2022 figure, far exceeded the anticipated budget and produced a healthy operating profit.
Early 2023 saw a continued drop in maritime freight charter fees which, starting with Sino-European routes, returned to pre-Covid levels. This stemmed also from a contraction in trade, which is most likely the result of excess investment in previous years.
Ongoing international tensions, combined with the Gaza crisis and clashes in the Red Sea towards the end of the year, have further shifted the balance between supply and demand. China posted the smallest increase in GDP for decades, despite it being a good 5.2%.
More specifically, the emergence of new instability factors has led to the application of higher insurance premiums, with costs exacerbated by speculation. This has led to considerable fluctuations in fees and the need to frequently renegotiate them with customers and suppliers. In turn, this has increased the costs associated with each individual sales agreement, in terms of both time and pressure on margins: nevertheless, the company defended itself adroitly.
The main driver of this greater-than-expected result was the sharp rise in shipments for extra-group third parties . The latter now account for 57% of total sales, thus highlighting the competitiveness, professionalism and reputation that Italiansped enjoys on the market.
Revenues were also boosted by several unexpected large-scale operations These included an air shipment of goods from the Beverage business to Uganda, with significant extra-budget carryover for the air freight sector and
Despite market turbulence, results outstripped the budget. Strong performance in the extra-group third parties’ segment and several successful large-scale shipments underscored Italiansped’s role as a key player in a highly competitive sector.
Federative tracking is now running smoothly, ensuring tangible benefits for operations and greater customer satisfaction
Integrated Annual Report 2023 / SACMI Group / Logistics Engineering & Forwarding
the enhancement of Italiansped’s credentials as a leading brand in Project Cargo.
Equally noteworthy was the shipment to Turkmenistan, a crucial contract relating to the Tiles and Sanitaryware businesses: this one shipment involved some 550 containers, the complex routing of outsize loads, at least three border crossings and intermodal transport by land and sea.
In addition to boosting the year’s operating results, this level of performance confirms Italiansped’s standing as a prominent player in what is a highly competitive sector populated by both extremely large companies and small-scale players.
The year 2023 also saw the acquisition of major new customers - including a leading American multinational that’s renowned in oil&gas and several other sectors - and the establishment of new
business arrangements with existing clients. Looking ahead to 2024, we can expect finalization of new joint ventures in countries that offer promising business development prospects.
Federative tracking (a software that can track shipments by harvesting data from any carrier, with guaranteed interoperability and real-time adjustment) has become permanently operational, bringing tangible benefits to operations and raising customer satisfaction.
On the intragroup logistics front, Methods Time Measurement (MTM) of individual flows concerning the Tiles Business continues. This type of analysis plays a vital role in the precise quantification of costs, the required human resources, distribution of workloads and, more generally, in the ongoing improvements to efficiency that underpin Italiansped strategy within the SACMI Group.
Artificial Intelligence
Key technological innovations
Development of a new spare parts warehouse management system powered by machine learning and artificial intelligence was completed.
This project seeks to provide workers with cutting-edge support and thus eliminate potential errors in the spare part picking and shipping process. Machine learning algorithms have, in fact, the task of accurately identifying the materials and tracking them inside the warehouse.
Key system features include a comparison of the code of the item being picked with a photograph of it taken on site. The result: unequivocal identification and immediate warnings in the event of any discrepancies.
In keeping with the machine learning approach, the system is designed to improve its own performance over time the operator, in fact, takes a photo each time he/she picks an item: the image is compared to the one in the database and, if it matches, is filed for subsequent comparisons.
Presently configured on the SACMI spare parts warehouse, the adopted approach can be extended to the Italiansped general warehouse. The database already contains 1 million photographs and is ready for in-the-field verification and consolidation. The operational phase is expected to begin by summer 2024.
Process fieldware
Tracking
Further developments are being driven by the application of new IT functions that automatically record each ‘physical’ task (moving a package, picking a load) on the SAP IT system. Here, it’s the physical action itself that triggers data recording: this ensures all check lists are always updated and made available both to operators and the new management software.
Launched in 2022, the new federative goods tracking system was upgraded in 2023, offering customers immediate, tangible benefits. The basis of this system is the Italiansped-identified supplier’s ability to take responsibility not just for the tracking as such but also any changes that may have been made to carriers' databases/software, thus ensuring interoperability (i.e. the ability to ‘read’ the system, accommodate changes in real time and adjust tracking accordingly). Italiansped aims to extend its use to all ‘nodes’ where possible (customs, sea, land).
Spare parts warehouses
Development of new system based on
machine learning and artificial intelligence
250,000
30,000 pick photos
spare parts codes
Federative tracking
80,000 packaging photos
850,000 picks/year for customer-bound shipments
Interoperability of systems
system real-time tracking updates
Impact on sustainability
This tool - available on the tracking dashboard - monitors the carbon footprint of every single shipment and for each of its individual nodes (sea, air, land). With the project already approved, the new tool is expected to be implemented and made available during the year.
This software is mainly used for groupage operations (i.e. merging different shipments in a single load unit). Optimized container loading lowers economic and environmental costs, minimizing emissions per unit of load.
The use of electronic devices throughout the supply chain (i.e. at every stage, with the exception of customs management) makes it easier to trace operations, reduces the risk of human error and allows for more precise, objective assessment also from a sustainability perspective, subcontracting chain included.
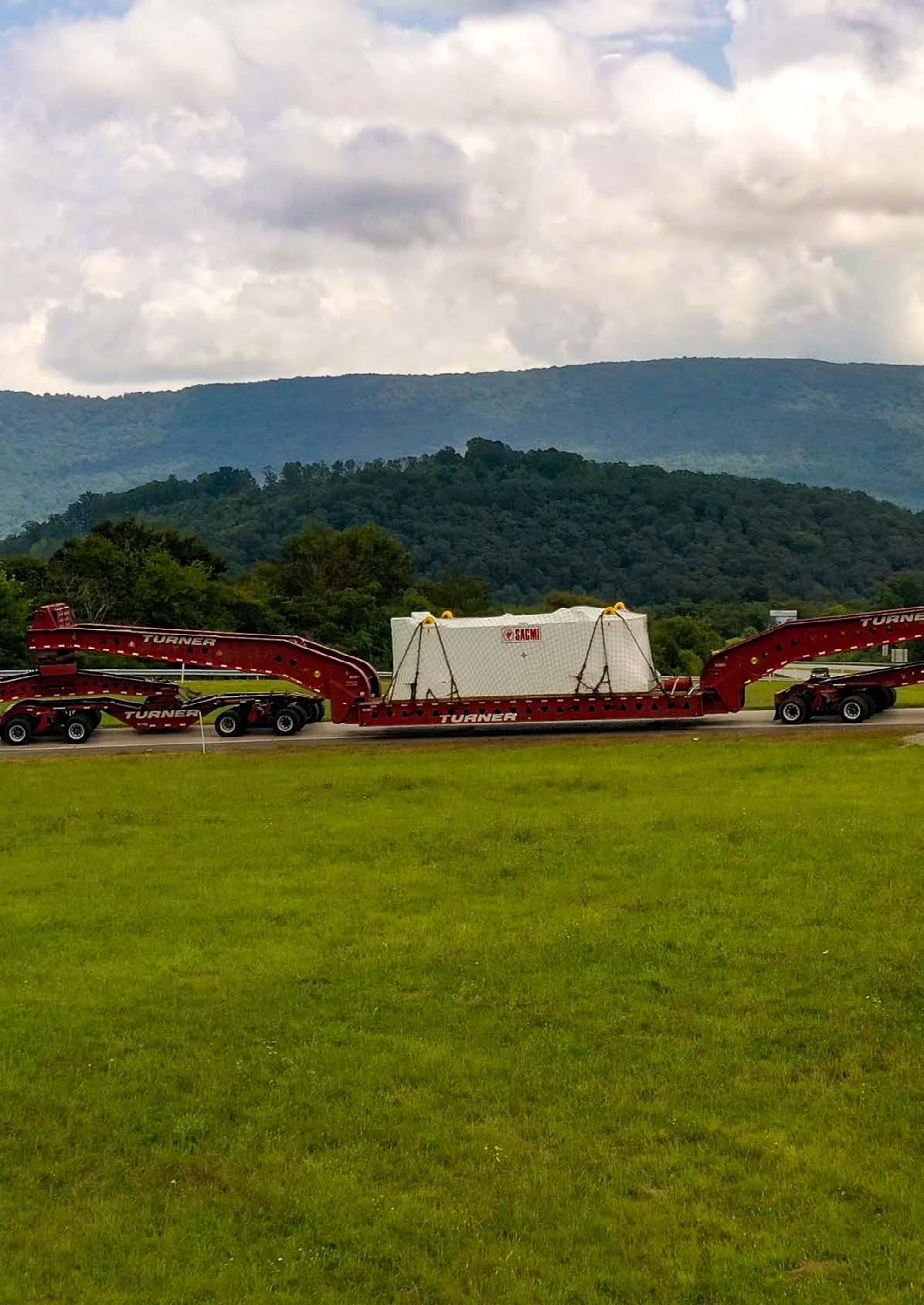

In 2023 Protesa continued its work as a Service Provider within the SACMI Group. More specifically, Energy Division volumes continued to rise in the wake of customers' growing awareness of energy issues and their desire to shield themselves from market fluctuations in the energy sector.
During the year, Protesa's REM (Renewable Energy Management) Division extended its reach beyond the traditional photovoltaic field to provide a comprehensive range of sustainability-focused efficiency enhancement and tool development services, positioning itself as an Energy Competence Center ’ in support of the Group and the individual SACMI Businesses.
From 2022 to 2023, Protesa doubled its revenues, with the extra-group share increasing substantially. This result was driven by the Energy Division, which posted a +150% increase in volumes, which had already nearly tripled between 2021 and 2022.
In 2023, in addition to the installation of the rooftop photovoltaic system at SACMI Imola (more than 2MWp ), major solar panel projects were completed at the ceramic plants of Gresmalt, Sant'Agostino and Antica Ceramica Rubiera. Beyond the Tiles sector, a large-scale 7MWp array was installed at Spal Automotive, a 3MWp system at Unigrà and a further 3.5MWp at the Pelliconi Closures plant in Atessa. During the second half of the year, the first next-gen ground-based solar panel array featuring a single-axis tracking system and a power rating of approximately 3.7MWp, came online.
It should be noted that some 2023 projects were postponed to 2024 due to delays in obtaining authorization. The resulting backlog ensured continuity of operations and further projects are expected to get under way in the first few months of the current year. Among the latter, the agreement with Gruppo Altoatesino Stafil is particularly noteworthy: over the next two years this will raise the profile of ground-based photovoltaic systems and open the
1.8
Sales doubled, performance being driven by the REM (Renewable Energy Management) Division.
Business now extends to nextgen ground-based solar panel arrays, with Protesa equipped to follow the entire technological and authorization process. Company takes on new role as an energy ‘Competence Center’ serving the various SACMI Businesses
way to participation in tenders with key international players. Indeed, the forecast is for a rapid expansion in ground-based photovoltaic arrays: this field offers numerous opportunities which, if realized, could, in 2024, result in projects on a scale of up to 10MWp.
Note that 2023 was affected by severe weather. In spring, disastrous floods hit the Emilia-Romagna region. Other extreme weather events included summer hailstorms, which significantly damaged plants under construction, inevitably raising costs.
Overall, for the Energy Division 2023 was a year of far-reaching consolidation. Operational facilities were strengthened and additional resources were channeled into managing the growing volumes and complexities of this extremely dynamic business.
Services
On the services side, research into cellulose, which made significant progress in 2022, produced the first tangible results in 2023 with development of the first automatic and semi-automatic machine prototypes; over the coming months, these will be deployed in material molding operations. March 2024 saw an expansion of R&D facilities. This will allow more flexible, simultaneous testing of multiple solutions.
D4P operations continue apace on everything concerning digitalization and simulation. With regard to intra-Group activities, in addition to services that create virtual content for trade fairs, events and training programs, the latter six months of the year saw the launch of the first simulations and animations for the newco SacmiCassioli Intralogistics : this work will continue throughout 2024 and aims to exploit the full potential of digital tools that aid the design and promotion of intralogistics solutions.
D4P's extra-Group work with Alphatauri and, most notably, Lamborghini, continued with the further expansion of services that make use of virtual reality. Lamborghini is also a customer in the field of quality control; projects that focus on their engines have again intensified, as have those concerning the quality control of delicate car interior parts. Additionally, dimensional controls on highly critical yet fragile parts were performed for the Man-Chevron group (large valves used in the Oil & Gas industry).
Metrology and measurement systems
Moving on to metrology and measurement systems 2023 saw a continuation of the accreditation process for the LAT 17025 laboratory (calibration of single-axis measuring machines using laser systems). Accreditation was obtained in March 2024, making the Protesa lab only the third facility in the country to achieve this milestone.
Scenarios
More personnel are expected to join the various departments in 2024, mainly in the Energy sector; the latter has expanded beyond direct production of solar panel arrays and management of their authorization procedures into the extremely promising area of renewable energy storage system authorization.
The year was also a noteworthy one in terms of market recognition. Protesa won the ‘ best project category of the Longi Solar Hi Mo6 Awards for its photovoltaic system (which uses Hi-Mo6 panels) on the plant in Manitou, in the province of Modena, Italy.
Ground-based solar panel arrays
Key technological innovations
In the ENERGY field, Protesa has completed the feasibility study that allows it to handle authorization procedures for ground-based photovoltaic systems, which are much larger and more powerful than the classic rooftop solutions that require only simplified approval protocols. This allows Protesa to take care of all system engineering aspects, from both a technological and bureaucratic perspective (from urban planning to licensing paperwork, provision of services, etc. to final authorization).
These procedures have a medium-long timeframe (on average, authorization takes 2 years) and expertise in them is set to make Protesa both a leading provider of authorization services and a leading direct installer of systems (of up to 10 MW). To do this, a team with cross-sector skills was put together, with Protesa authorizing systems with a combined capacity of 350 MW.
systems
Protesa's capacity as a sole manager for the entire authorization process expanded in 2023 with its remit extending to authorization of storage systems: these consist of accumulators (i.e. batteries) that store the excess energy produced by photovoltaic systems and ensure continuity when there is little or no sunlight (e.g. at night). Demand for these highly innovative systems, which can focus a storage capacity of 120-200 MWh within just a few hectares, is set to soar in the coming years. Protesa is fully equipped and qualified to handle every stage of the authorization process, to the advantage of both the large-scale concerns that make such systems and then ‘rent’ them to the provider (Terna) and individual customers (e.g. ceramic manufacturers) who find ‘mini-storage’ (1-2 MW) facilities increasingly appealing as they maximize the economic and environmental benefits of rooftop solar panels. In this field, the focus is on projects designed to provide each customer with a ‘turnkey’ system that meets their specific needs.
Protesa’s distinctive range of renewable energy system solutions also includes advanced software for 3D mapping-surveying with drones (dot clouds, parametric analysis). Protesa can already integrate highly advanced, detailed renderings into its offers. These illustrate power output curves, panel tilt angles, array patterns and obtainable yields: in short, a meticulously detailed ‘preplan’ that enhances project credibility and solidity. The company’s 3D calculation-design capacities, incorporated into offers using the most advanced tools on the market, have been matched by a strengthening of in-Cloud services The latter aims to meet the goal of implementing - on more than 240 currently managed systems, mainly in Emilia-Romagna - advanced monitoring and predictive maintenance services.
Certifications
In the testing field, March 2024 saw the conclusion of the LAT 17025 certification process for the Metrology Lab (calibration of single-axis measuring machines via laser technology), making the Protesa Lab one of only three facilities in Italy with such certification.. Protesa is already SOA certified for the OG11 category (technological systems); during 2024 it is also expected to obtain the OG09 category (electricity generating systems).
Energy “Competence Center” to support SACMI's operations/businesses
Impact on Sustainability comprehensive engineering Services for
solar panel arrays
3D simulation/calculation services to assist in design
240 photovoltaic systems designed, installed and managed (mainly in Emilia-Romagna)
38MW installed power in 2023 alone
350MW authorized in total
-24,100 tons/year of CO2 eq released into the atmosphere
in-Cloud monitoring and control to provide advanced maintenance services of plants
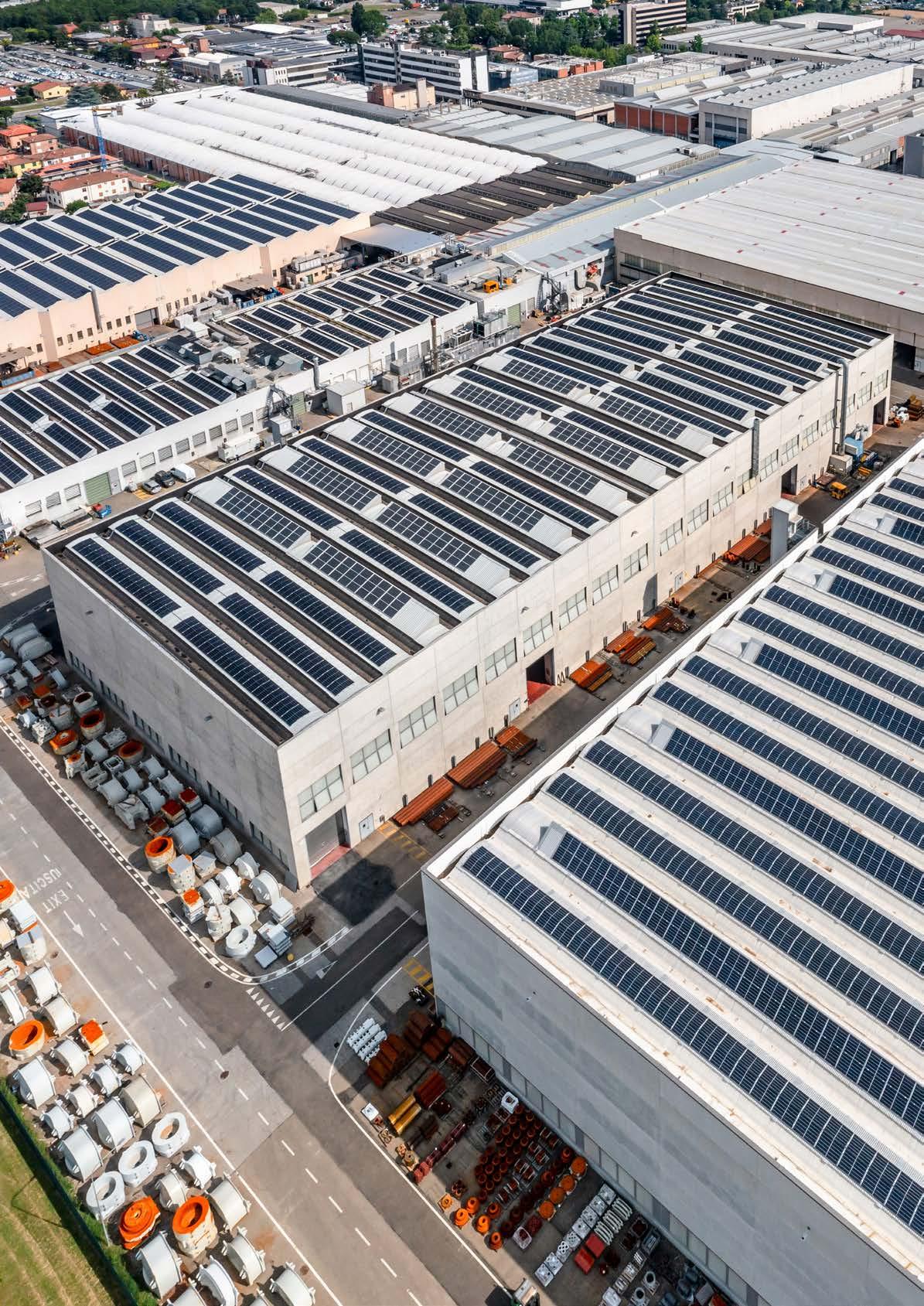
CHAPTER 2
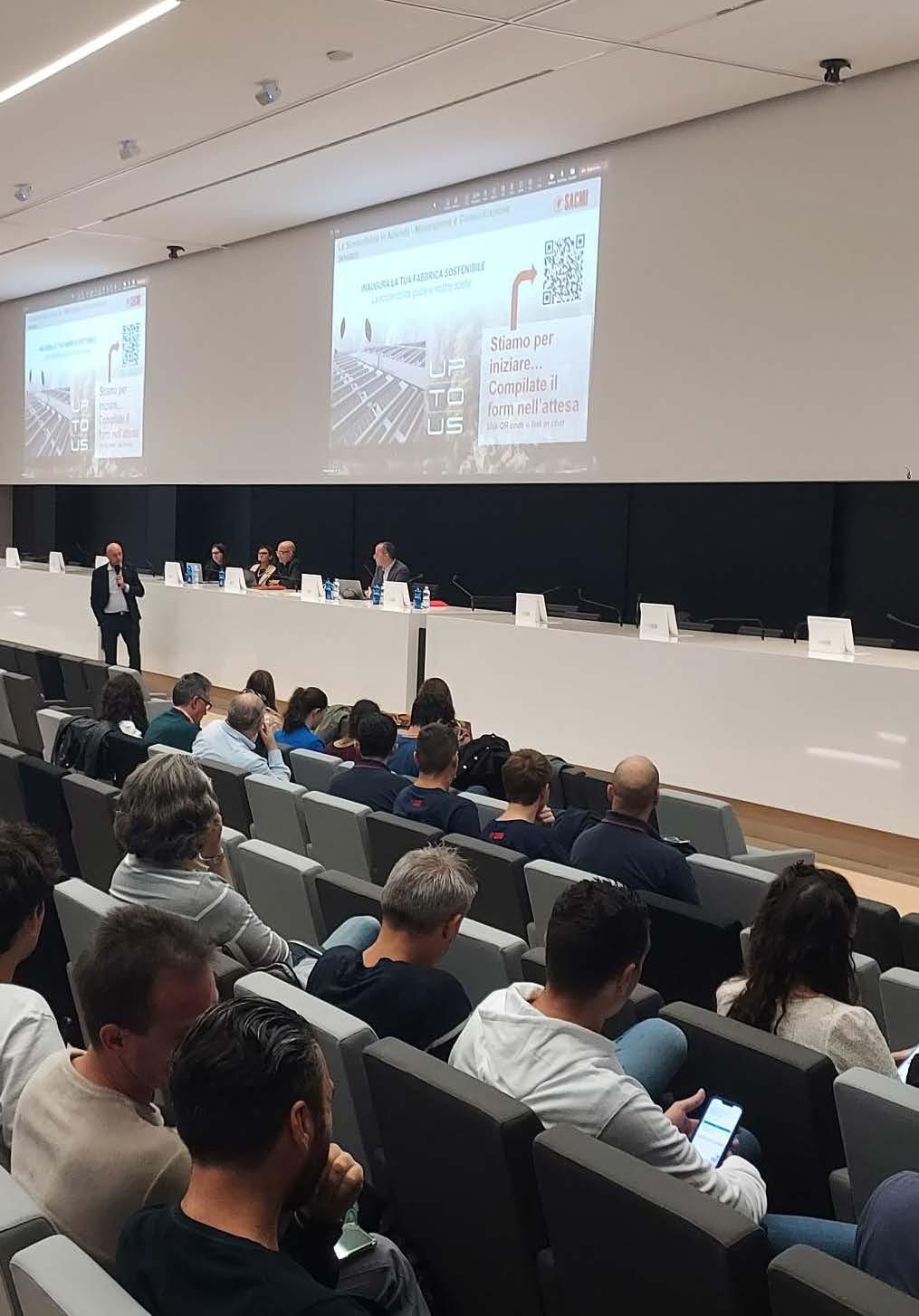
Governance
and organization
The SACMI Group consists of over 73 manufacturing, distribution and service companies in 27 countries worldwide. The Parent Company, SACMI Imola, is a cooperative company managed according to the principles of cooperative democracy and the active participation of members . Its organizational model is founded on the involvement of Members, management and employees in the decision-making process
Appointed by the Members, the Board of Directors of the Parent Company, SACMI Imola, is supported by bodies with specific expertise on economic, environmental and strategic matters
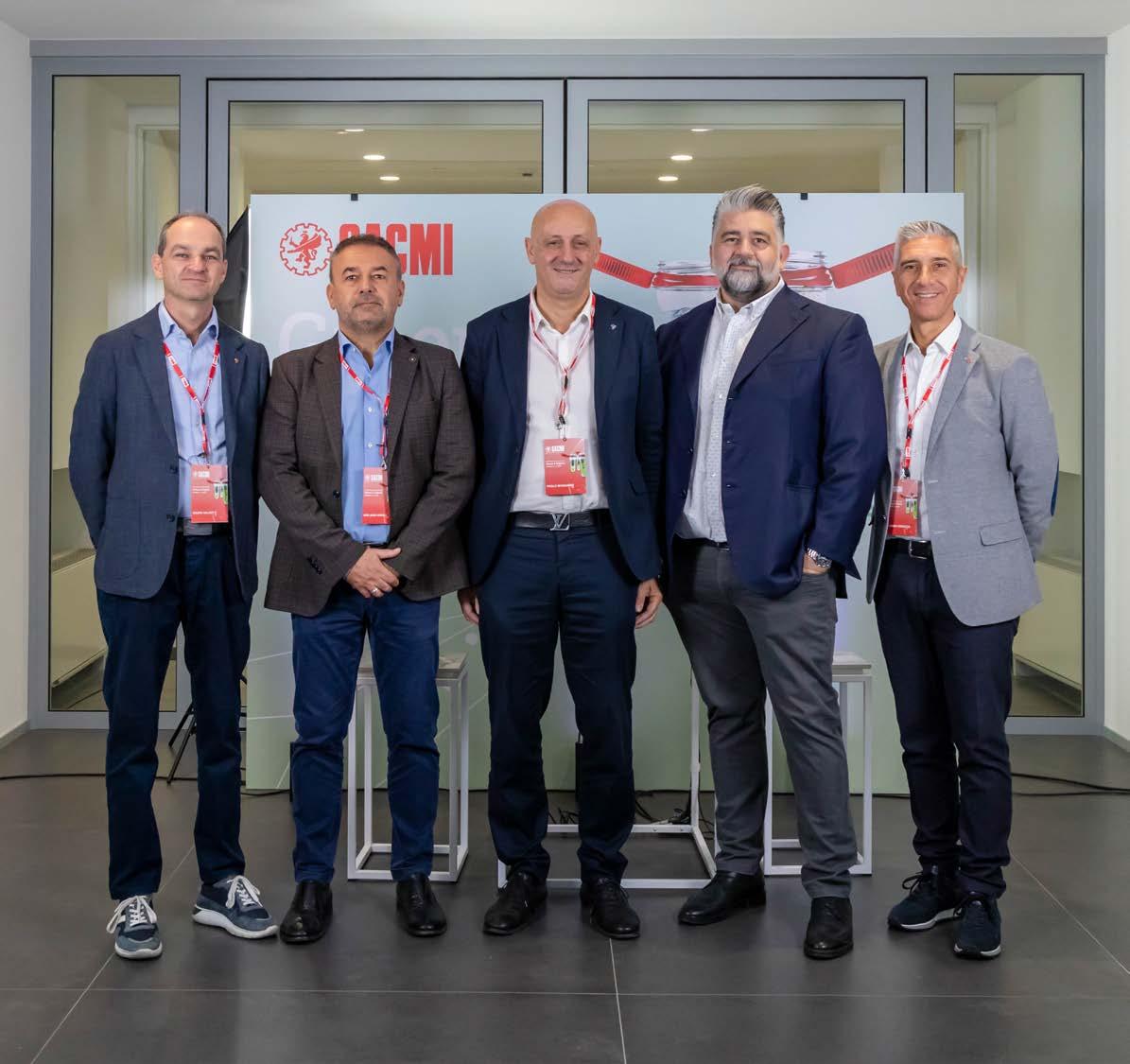
Governing bodies
In managing its organizational operations, the SACMI Group is governed by different bodies, each with a dedicated function. Specifically:
• Member’s Assembly : the Parent Company's Members’ Assembly is a collective body in which corporate will is formed and expressed before being implemented by the Board of Directors.
• Parent Company’s Board of Directors : the SACMI Imola Board of Directors has the crucial role of guiding and governing the Group. It is granted the widest powers concerning both routine and special management of SACMI Imola. In particular, the Board is granted full powers to implement and achieve corporate purposes, excepting those reserved for the Members' Assembly by law or by the Articles of Association. The BoD defines development goals, the strategic thrust, Group governance and the make-up of the Boards of Directors of Group companies. It also periodically consults with General Management.
• General Group Management has the role of coordinating and strategically aligning the Businesses. Focuses on corporate development through coordination of the Businesses; assesses new projects/opportunities and puts them to the Board of Directors in keeping with strategic guidelines issued by the BoD.
• General Managers of Business Units responsible for their specific Business, comprising, also indirectly, Group companies that fall within the various BUs; they develop plans and programs, ensuring achievement of goals assigned by Group General Management, all in compliance with company policies/strategies and the autonomy of the individual legal entities.
• Group Staff : corporate entities across the various Businesses act in their respective sectors to regulate and harmonize the activities of individual BUs with policies defined by the Parent Company; they provide support to achieve goals.
• Committees : bodies that engage in strategic discussions and consultancy so that specific bodies can develop projects.
More specifically, the Board of Directors consists of 5 members, of whom 1 male aged 30 - 50, and 4 males aged over 50. Each director is selected by a vote held among the parent company's membership.
The clear legal and moral requirements laid out in the Articles of Association apply to Members and, therefore, Directors: they do not provide for limits on mandates. Directors are also entrusted with positions in other governance bodies of Group companies. No members of the Board of Directors belong to vulnerable categories. The BoD is made up as follows:
Paolo Mongardi > President
Lorenzo Mimmi > Vice-President
Giuliano Airoli > Director
Andrea Vernocchi > Director
Mauro Galeotti > Director
The Board of Statutory Auditors has 3 members, all male and aged over 50. It is made up as follows:
Claudio Solferini > President
Roberto Chiusoli > Auditor
Gianfranco Santilli > Auditor
The Parent Company Board of Directors is nominated by the Members. The Group Companies BoD is nominated by the Parent Company BoD.
The Board of Directors has support staff with specific skills in key technical areas relevant to organizational, economic and environmental aspects. Continuous discussions ensure that monitoring of these issues is consistent with company strategy. During the year, periodic meetings see the Board of Directors report to the Members’ Assembly not only on the Group’s economic and strategic performance but also its organizational and sustainability performance. Each Board of Directors then delegates specific powers and responsibilities within the corporate organization in keeping with personnel’s functions and roles, with particular regard to:
• operational mandates, relating to management of individual corporate departments that attribute specific powers in certain areas (e.g. sales, purchases, finance, administration, etc.).
• safety mandates pursuant to art. 16 of Italian Legislative Decree 81/2008 concerning internal safety (to safeguard health and safety in the workplace), product safety (i.e. safety of products manufactured and/or marketed by the company) and safety on external construction sites (i.e. assembly, start-up and technical assistance, including after-sales services, provided on customers’ sites).
This system has been implemented in all of the SACMI Group’s Italian companies and has been partially extended to some foreign companies (e.g. Germany). The above mandates, especially those on safety, require that annual reports on mandate-related functions be sent to the Board of Directors. To date, no tools for monitoring and assessing the performance of the Board of Directors are in place.
Note that SACMI Imola SC Management is made up as follows: SACMI IMOLA SC MANAGEMENT
SACMI Group General Manager
Unit General Manager
Advanced Materials Business Unit General Manager
Rigid Packaging Business Unit General Manager
Packaging & Chocolate Business Unit General Manager
SacmiCassioli Intralogistics Manager
Chief Human Resources and Organization Officer
Audit and Shareholders Affairs Manager
Model of Corporate Governance
Efficient management and organizational innovation are SACMI Group hallmarks. In keeping with its cooperative spirit it has, over the years, adapted its governance and corporate organization models to meet new challenges posed by global markets. In April 2022, the SACMI Imola Board of Directors updated the Corporate Governance model approved in 2017.
Consisting of various BoD and general management roles, the governance model establishes a Sustainability Board . Headed by the Board of Directors, its goals are to:
• encourage dialogue on developmental trends and sustainability issues so that executive plans can be drawn up.
• define strategic lines by identifying areas that should be the focus of growth and/or sustainability development policies.
• approve the business plan.
The goal is to define, by the end of 2024, a Group Sustainability Plan along strategic lines, in compliance with the CSRD ( Corporate Sustainability Reporting Directive ).
The Sustainability Board has several components: general management, financial management, human resources, assets, operations management, public relations, QSE (quality, safety, environment) and Group sustainability. This model has been developed for several reasons. These include the need to extend the scope, quantity and quality of SACMI’s financial, social and environmental sustainability indicators (parent company, then other Italian and foreign companies) and make such aspects more strategic vis-à-vis focus/ control of financial decisions.
One of the key tasks of theSustainability Board is with the support of the ‘company Green Team’ - to extend the reporting boundary and the quantity/quality of financial, social and environmental sustainability indicators
Measuring and certifying environmental performance according to internationally recognized criteria and standards is a key SACMI goal. Within this new organizational architecture, the Sustainability Board works alongside the Advisory Board and Strategic Management Board to help define and implement strategic guidelines and plans. These deliberations are then carried forward to operational level through further bodies involved in General Management. More specifically, the Strategic Business Board has the task of expressing Group strategy as Business Unit strategies by monitoring market trends and opportunities.
Managers on this Board are supported by the heads of the key corporate bodies and the Board of Directors itself. Note that the model now adopts the concept by which the Strategic Business Board is open to suggestions concerning methods, experience and knowledge from independent subjects, even outside the Organization.
In terms of development and investment opportunities, the model also provides for the Corporate Business Review Meeting : involving General Management, BU managers and other managerial bodies, its aims include drawing up proposals for changing the way the various businesses are organized, assessment of development projects, management monitoring and the drawing up of budgets.
At operational level, the model also incorporates developments actualized in previous years. On the one hand, this aims to enhance the visibility and strength of corporate components relating to core businesses and, on the other, identify new areas with high development/growth potential. For example, an integral part of the model is the Strategic Innovation Board , established to serve the SACMI Imola Board of Directors and General Group Management. It has the purpose of encouraging reflection on: selected business models, direction of growth, lines of development/ change and the resources/skills needed to compete successfully in the future.
Board of Directors
Advisory Board
Sustainability Board
Corporate Business Review Meeting
General Manager
Strategic Management Board
Strategic Innovation Board
SUSTAINABILITY BOARD – SCOPE OF THE BUSINESS
Key innovations in 2023 include the completion of the process - begun in 2022 - that extends sustainability performance reporting/measurement to all SACMI Group Italian companies and overseas manufacturing sites. In 2024, this reporting approach shall be extended to the entire SACMI Global Network.
To achieve this, resources were selected for each individual Legal Entity and given the task of handling sustainability-related data collection and reporting. An interdisciplinary ‘Corporate Green Team’ was created in cooperation with the Board of Imola and the management of the various entities; at present the team has 128 members.
Strategic Business Board
Merge & Acquisition
With respect to Merge&Acquisition policy, note that the complete takeover of BMR Spa, based in Scandiano (Re, Italy), was finalized at the start of 2023, thus completing the plan implemented in 2019. This operation completes the range of endof-line solutions for ceramic manufacturers.
In April 2023 that same logic - completing the range by extending it to the strategic intralogistics area – led to the establishment of SacmiCassioli Intralogistics. The goal: to pool the experience and skills of two companies that are leaders in their respective fields and develop solutions that automate plant logistics in SACMI's core businesses (tiles, whiteware, packaging, renewable energy, others).
The strategic goal is to help customers optimize their intralogistics functions - both on existing plants and greenfield projects - and provide support to develop production flow governance by exploiting the potential of control, interoperability and completeness of digital information.
On the Global Network, 2023 saw the inauguration of the new SACMI branch in Nigeria, part of a wider plan to provide local facilities for the African market.
During the year, strengthening of local office operations continued with regard to both direct production of machines and machine parts - by optimizing lead times and offering targeted responses to specific market needs - and, in particular, the reinforcement of after-sales assistance (also provided in synergy with the Italian parent company by leveraging new digital tools).
SACMI has increasingly used its worldwide offices to encourage awareness and training activities on new technologies within its areas of competence. To do so, it has established a close dialogue with customers by organizing events/ seminars at its own Network offices and by attending conferences in various fields (ceramics, automation, packaging, etc.). Looking to 2024, note that SACMI Engineering's work in India has been further strengthened by the establishment of a new headquarters in Morbi.
SacmiCassioli Intralogistics
• Automatic handling/storage – Design, management and control of mechanical means of transport/handling: stacker cranes, picking islands, automatic palletizers, robots, LGVs
• Software development – Development of WMS (Warehouse Management System) and WCS (Warehouse Control System) software and their integration with plant supervision software.
1 For development of Customer Service support tools see, among others, chap. 6.3, Customers.
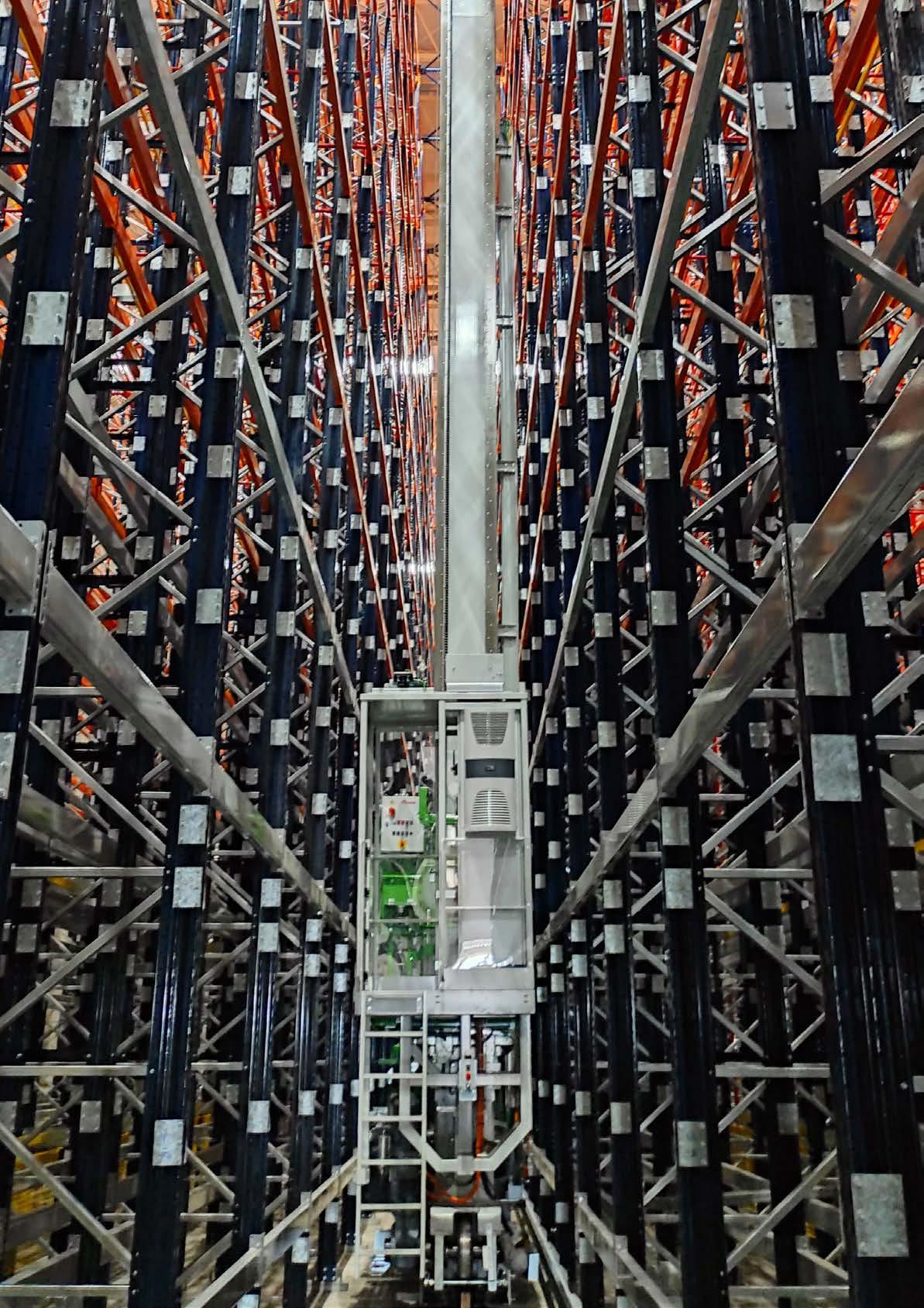
Business integrity, control and management systems
For over fifteen years SACMI Imola has had an independent Internal Auditing team, currently part of Assets, Audit and Shareholders’ Affairs Management, which is, in turn, subordinate to the Board of Directors.
In 2023 a Group Code of Ethics was drawn up. This aims to establish the ethical principles of behavior with which everyone must comply in all business and corporate dealings
WHISTLEBLOWING
In 2023, in accordance with Italian law (Legislative Decree 24/2023), a Whistleblowing tool was adopted to report any violations or illegal conduct within the company.
Any requests for clarification regarding implementation of the organization's policies and practices on responsible business conduct, or any queries about the organization's business conduct, may be submitted to whistleblowing@sacmigroup.com.
Moreover, as per Italian Law Decree 24/2023, which implements EU Directive 2019/1937, reports may also be made anonymously via the LegalWhistleblowing platform, accessible by all employees via the company SharePoint.
Lastly, any requests for clarification can also be sent to the Supervisory Body, appointed pursuant to Italian law decree 231/2001, at organismodivigilanza@sacmi.it: this is for subsidiaries that are not equipped as per Italian Law 231/2001.
No reports pertaining to the whistleblowing procedure were submitted by employees of SACMI Group Italian subsidiaries (for which the procedure has been in force since 14 July 2023). Neither were any reports received from foreign subsidiaries in Spain and Germany (where the procedure has been in force since 17 December 2023). At present there is no reporting procedure in place for the remaining foreign companies.
Conflict of interest is regulated by a Policy that is applied throughout the Group. In this regard, ‘conflict of interest’ situations - which are managed and monitored directly by the Board of Directors, which takes specific measures to protect the company from possible negative impacts - are not reported. Should a concurrence of director roles give rise to a potential conflict of interest, this is highlighted in the minutes and, depending on the specifics of the case, the person involved abstains from voting or the absence of conflict in the specific situation is formalized. Furthermore, during 2023 a Group Code of Ethics was drawn up, approved and sent out to all Italian and international subsidiaries. This aims to ensure that everyone observes the relative ethical principles in all their corporate and business dealings.
100% of governing body members and employees have received information and training on anti-corruption procedures and policies. In 2023 there were no incidents of corruption within the SACMI Group, nor were any legal actions taken against it for anti-competitive, antitrust or monopolistic practices.
During 2023 the SACMI Group reported no monetary or non-monetary penalties concerning compliance with laws and standards.
At present no SACMI Group subsidiary operating sites are certified as per the ISO 37001 standard or other anti-corruption management system.
On the topic of cybersecurity, SACMI recorded a security incident in December 2023, which involved three Group companies. Nevertheless, no damage or interruption to continuity of operations was detected.
Certification and management systems
Customer satisfaction is a key company goal, hence the early adoption, by the parent company SACMI Imola SC, of an ISO 9001 certified Quality System in 1996. In subsequent years certification was extended to subsidiaries.
Commitment to safeguarding the environment, protecting workers’ health and safety, and compliance with legal requirements has naturally taken us towards attainment of the respective certifications, namely: ISO 14001 in 1999 and ISO 45001 in 2002.
SACMI Imola currently has an Integrated Management System that complies with:
• UNI EN ISO 9001:2015 - Quality
• UNI EN ISO 14001:2015 - Environment
• UNI ISO 45001:2018 - Health and Safety
The year 2022 saw the creation of a Corporate Quality, Safety, Environment and Sustainability framework in order to increase in-Group awareness and expertise on such issues. At the same time, a Corporate Certification project was launched. This led to the establishment of a multidisciplinary team, coordinated by the Corporate Quality and Process Improvement body, the aim being to obtain UNI EN ISO 9001 Group certification for all Italian sites soon.
Integrated Annual Report 2023 / Responsible governance and value creation / Business integrity, control and management systems
Organizational, management and control model as per Italian d.lgs 231
In 2008 SACMI Imola adopted an Organizational, Management and Control Model in compliance with Italian d.Lgs. (law decree) 231/2001; together with the Code of Ethics, this constitutes a set of rules and procedures to be observed in all areas of company business and concerns both internal and external relations.
This Organizational Model aims to prevent and counter offences sanctioned by Italian Law 231 (e.g. corruption, extortion, falsification of accounts, money laundering, violation of workplace health and safety or environmental standards); the Organizational Model also places a clear emphasis on health and safety, to which a specific section is dedicated.
To ensure the Model is applied properly the Board of Directors has nominated a Supervisory Body which reports directly to the Board of Directors; this has independent powers of initiative and control and is a collective body whose members include SACMI Imola’s Asset, Audit and Shareholder’s Affairs Manager and an external consultant. During 2023 the Supervision Committee analyzed the new offences included within crimes pursuant to Italian Law Decree n. 231/2001, evaluating their probability of being committed in the company and the relative impact on the Model. On 10 October 2023, a new version of the Organizational Model was approved by the Board of Directors of SACMI Imola SC. During 2023, new versions of the Organizational Models of all the Italian subsidiaries that already had a Model were also approved by the respective Boards of Directors. All employees were informed about d.Lgs. 231/2001 and the relative Organizational Model by way of a newsletter. Moreover, personnel in positions of responsibility have been provided with training pursuant to the relative Law Decree. Given the importance of this issue, 2019 saw the Organizational Model extended to all Italian Group companies in which the Cooperative holds a majority share.
Human rights policy
Observance of personal rights is an integral part of the SACMI governance model. On the basis of this principle - applied at all SACMI Group manufacturing and service sites worldwide - a Code of Ethics was drawn up. The cornerstone of this approach is rejection of any kind of discrimination at any level. In practical terms, in SACMI this principle means the clear definition and application of workers’ rights, especially as regards:
• the right to privacy, in observance of the GDPR.
• continuity and longevity of employment, significant parameters on a par with quality and performance.
• rejection of all forms of forced labor, particularly child labor.
In keeping with the corporate vision, which takes an inter-generational development approach (‘to ensure the company handed to future generations is an even better one’), and the set of company values, which draws inspiration from, among other things, the principle of entrepreneurship (‘freedom with responsibility’), respect for a proper work-life balance is evident in the actions taken/services provided by the Group to promote people's well-being
Since 2021, Agile Working has been implemented in all SACMI Group Italian companies. This tool aims to improve the work-life balance and promote inclusiveness for persons with special personal or family needs (where their specific professions so allow). Employees can also take advantage of Smart Working. This stems from a managerial approach that sees flexibility and working autonomy as key drivers of productivity and enhancers of environmental, social and economic sustainability.
Workers’ well-being is also prioritized at economic-regulatory level: for several years the SACMI Group has provided a digital platform that gives
workers tax-advantaged access to family services (kindergarten, social security, education) and personal services (gym, shopping vouchers, culture).
Considerable attention is also paid to organizational well-being via the definition and application of a listening and feedback model that is organized into multiple areas. In 2023, some Group companies organized their second consecutive ‘climate survey’ to obtain feedback from all workers on the perceived quality of their working environments. This investigated aspects such as job satisfaction, training and development, quality of relationships between colleagues and quality of relationships with managers; it also looked at workers’ perceived level of safety and their interest in remaining in the company medium-long term (employment longevity principle).
To ensure full participation of those involved in this ‘listening’ scheme, focus groups involving workers and their managers were set up to add qualitative feedback to the survey data and share an action plan that, on the basis of the gathered feedback, highlights: improvement priorities, appropriate timing and action. Ultimately, the goal is to make this feedback an integral shared, transparent, measurable part of the way the organization’s sustainable development and workplace quality model is defined.
The last aspect of this model - and an integral part of the new business management system - sees the introduction of a performance appraisal system. A system that focuses not just on results but also on people’s observance of company values. In a model that aims to achieve full meritocracy, the performance appraisal system provides a foundation for all decisions relating to opportunities for advancement and development within the organization. Integrated Annual Report 2023 / Responsible governance and
CHAPTER 3
Innovation and research
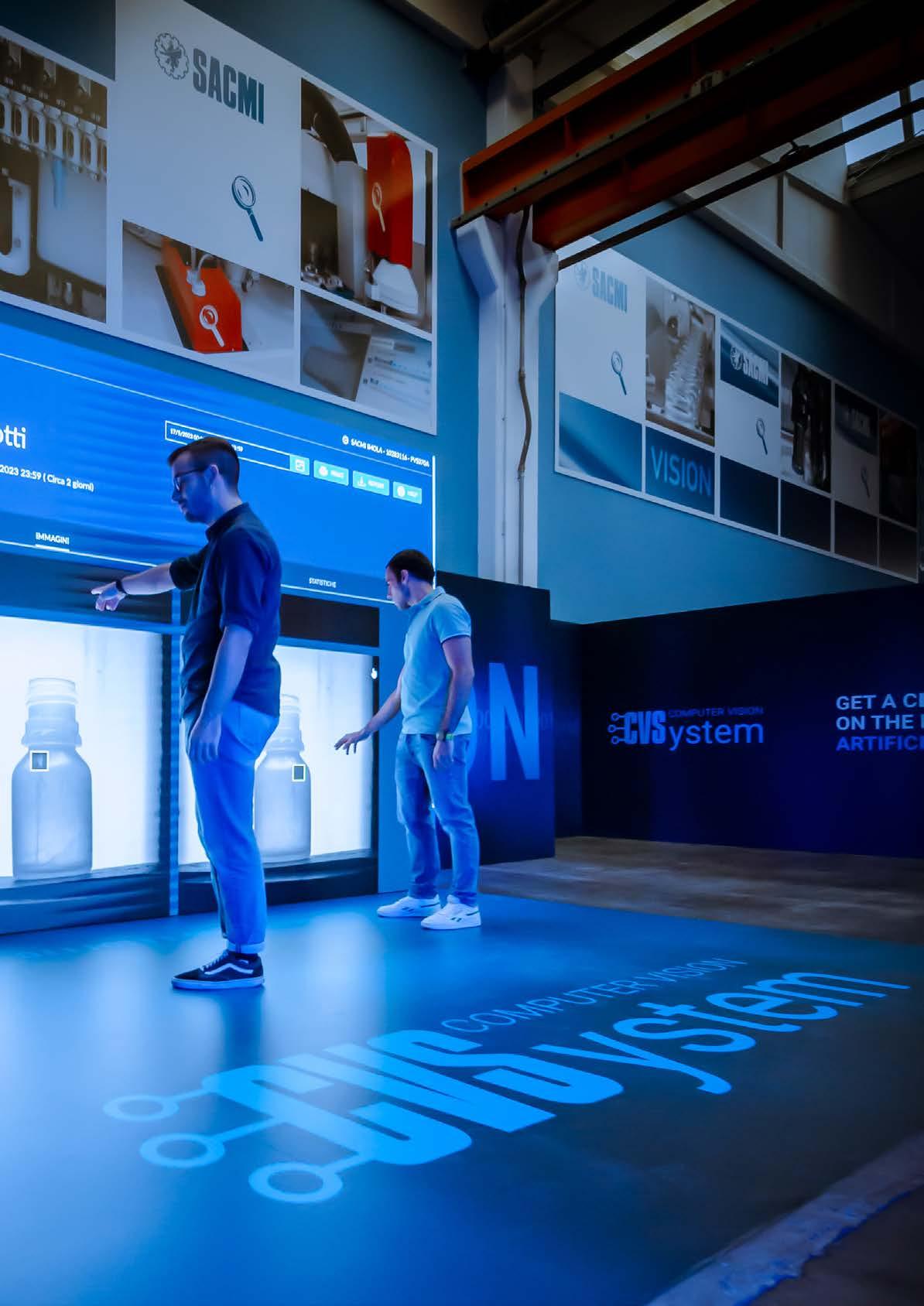
Innovation and research
Coordination between SACMI’s innovation-oriented facilities and departments strengthened in 2023, with a sharp focus on crossBusiness training to deliver the new skills that are vital to an effective, forward-looking innovation model
Innovation is a key driver at SACMI. It is vital to development of the Business in terms of the quality of the technologies and services offered; it also lays the groundwork for new skills with which to enact strategy on the basis of the scenarios/priorities defined by the business model.
In 2023 SACMI took its innovation strategy in two main directions. The first targeted a reinforcement of the facilities, skills and governance linked to digital innovation.
Established in 2022, the Digital Innovation&Automation HUB grew during the year to become a true Digital Business Partner ’, helping individual SACMI Businesses achieve their innovation goals in terms of developing digital&automation enabling technologies.
In 2023 SACMI also established the Corporate Innovation Directorate . This directs and coordinates policies (also regarding partnerships and opportunities) and establishes stable relationships/synergies between methods, infrastructures, people and processes.
One of the key innovations of 2023 was the establishment of the Corporate Innovation Directorate, which directs and coordinates innovation at strategic level.
The Digital Innovation & Automation Hub effectively became a ‘Digital Business Partner’, nurturing the innovation goals of SACMI Businesses
Integrated Annual Report 2023 / Innovation and research
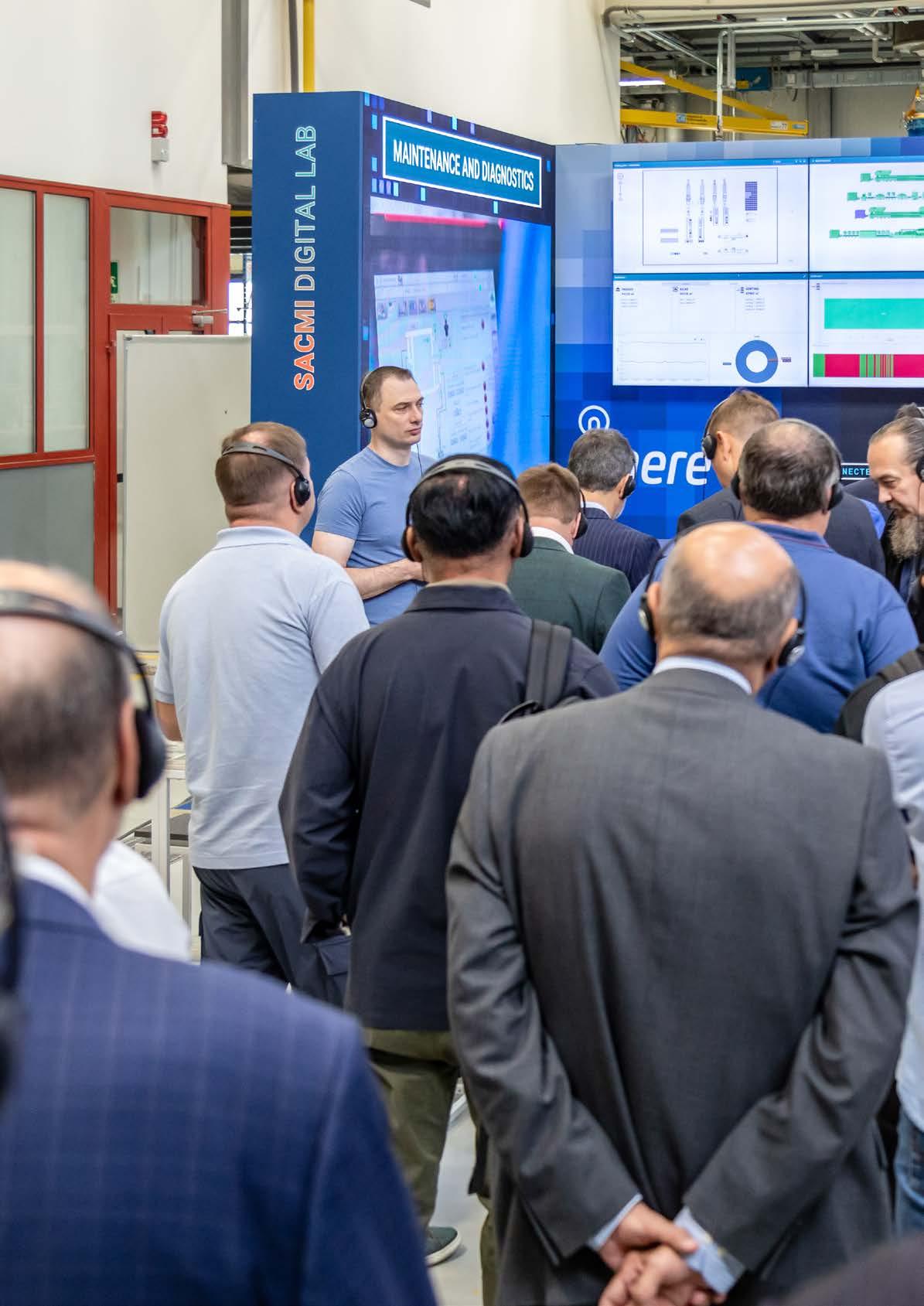
3.1
Digital Innovation & Automation HUB
Just as the factory transforms raw materials and components into finished machines/products, the SACMI Digital Innovation&Automation HUB (DAH) transforms ‘bits’: it takes on the digital innovation challenges facing the Businesses and defines pathways that lead from ‘idea’ to ‘proof of concept’, prototype and, ultimately, a finished product that will join the individual businesses’ range of technologies and services, helping to drive their sales strategies and provide responses to new market needs.
Why a hub?
The first reason, which underlies the strategy launched in 2022, is the intrinsic nature of digital technologies: unlike ‘vertical’ innovation (a specific understanding of materials and processes), which remains the responsibility of individual businesses, digital innovation is, by definition, a cross-sector affair. Pooling digital experiences, skills and facilities therefore generates efficiency both in terms of resources used and the effectiveness of the proposed solutions.
More specifically, the HUB operates on the following families of enabling technologies:
• Development of software and IoT technology with in-Cloud applications
• Development of embedded systems
• Production plant digitalization
• Production process discrete-event simulation
• Robotics and self-driving vehicles
• Virtual prototyping
Augmented/virtual reality
Numerical simulation
• Data analysis and artificial intelligence , with emphasis on generative AI based on LLM (large language models)
Coordination continues to drive the strategy initiated in 2022: sharing experiences, skills and facilities to generate efficiency, thus nurturing the development of digital innovation and its transformation into a product by way of ‘digital contamination’ both within businesses and between them
DAH functions and workflow
As Digital Business Partner, the hub:
• works alongside the personnel of the individual Business Units, tracing a path from product idea to ‘ workshop ’.
• follows the development of the specific systems and sub-systems that the Business Units integrate into their products (e.g. CRONO software for digital printing, HERE software for plant supervision, the Leviga BMR simulator, etc.).
• directly develops/provides technology (e.g. new AI-based digital tools to support Customer Service).
• contributes to the development of new skills via ‘digital contamination’ by promoting a digital culture both within individual businesses and throughout the Group.
Team, skills and organization
Definition of the idea: done both within the Business Units, which are directly in contact with markets and know their needs, and within the DAH hub.
Definition of priorities together with General Management of the Business Units
Idea development (DAH) and drafting of a Business Case
Validation of the proposed Business Case by the General Management of the Business, the Board of Directors and General Group Management.
Development and industrialization of the prototype.
The role of DAH from an ESG perspective: examples of implemented projects
Initially established to streamline SACMI's innovation strategy in the automation and digital fields (to augment the quality, productivity, versatility and efficiency of the technologies and services offered by the Businesses), the Digital Innovation & Automation HUB is now a strategic driver of the digital innovation that seeks to achieve specific social, environmental and governance sustainability goals.
A good example of this is the development of digital tools that can measure the efficiency and
iTools Edge
The result of SACMI's decades of experience in industrial automation, iTools Edge is a library of configurable software components: these are used to create specific multi-platform applications that can be tailored to customers’ specific needs.
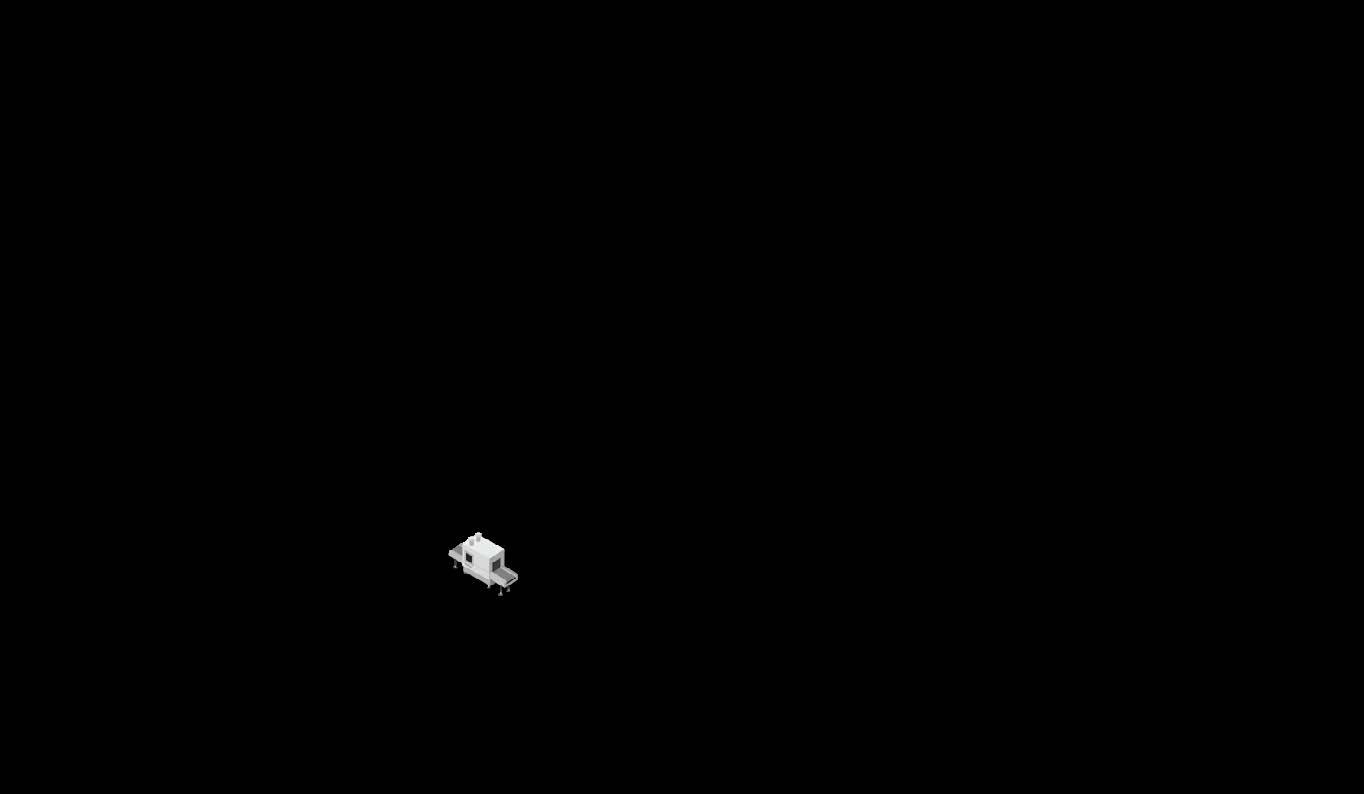
purpose being to simulate the productivity of a certain layout and identify any bottlenecks in advance: this info is shared with the customer and used to smooth interaction with the supplier.
• LGV (self-driving vehicle) route optimization software to reduce inefficiencies, shorten downtimes and boost plant availability
• application of artificial intelligence to wrapping machines made by SACMI Packaging & Chocolate, its purpose being to ‘intercept’ product defects (e.g. a chocolate bar with incorrect wrapping) not by integrating additional sensors but simply by acquiring issue-related signals from the motor (e.g. torque).
Use of anomaly detection algorithms has made it possible to detect defects in advance (before they actually occur), avoiding waste, scrap and further reprocessing.
Generative artificial intelligence solutions based on LLM (large language models) took on a larger role in 2023: these provide customer service operators with valuable support (by delivering uniformity of procedure and faster/data-driven responses that are independent of individual operators’ experience and perceptiveness). Other ongoing projects include:
• development of an in-plant tracking system; in this context, tracking aims to create a ‘digital identity card’ of the ceramic product (this could also contain relevant ESG data such as the environmental footprint of each tile, quantity of energy consumed, etc.).
• SEM (order and production progress status), now enhanced with OEE calculation functions, has been fully operative at the Imola production plant since 2023.
Alongside the development and release of new ‘from cradle to gate’ tools, SACMI's Digital Innovation & Automation HUB promotes knowledge sharing In numerous fields, in fact, it’s inadvisable to begin product development from scratch; it’s actually more practical to seek out potential partners who can provide a POC (proof of concept).
There are three ongoing projects in this area, carried out in partnership with AmmaGamma:
• development of generative artificial intelligence tools to respond semi-automatically to assistance tickets.
• study and optimization of the flow of goods and warehouse stocks
• in intralogistics (SacmiCassioli Intralogistics), the design of algorithms to optimize allocation of goods in a warehouse (to speed up picking and placing).
Digital Business Agent
Regardless of the potential ESG benefits, the main innovation driver behind the SACMI Digital Innovation & Automation HUB is always the Business and its understanding of customers and market trends. This is why one of the year’s key goals - pursued in concert with HR Management, which implemented a specific project - was the establishment of a DBA (Digital Business Agent) to represent the DAH ‘counterpart’ inside the Business, the aim being to follow every stage of product development and establish its go-to-market strategy.
To this end, the hub fine-tuned a demo of the technological infrastructure and organized a 5-stage workshop; this involved General Management, Sales Management of the individual Businesses and the Customer Service management and led to the definition of a new business model for ‘selling’ digital services. The result was subsequently submitted to the Board of Directors, with the DBA at the head of each individual BU then being defined.

3.2
Corporate Innovation R&D
In 2023 the Corporate Innovation Directorate was established to:
• define and implement a shared Group innovation process, integrated into the various BUs.
• manage R&D funding, protect innovation-related intellectual property and coordinate partnerships with universities, innovation centers, certification bodies and customer-partners themselves.
This directorate complements the vertical skills of the Business with a view to strategic coordination and focuses on seeking out partnerships and financing opportunities.
To achieve cross-fertilization between different innovation projects within the various internal areas, the Corporate Innovation Directorate also strives to identify enabling technologies/topics that concern all Business Units, proposing coordinated action to achieve SACMI Group goals that prioritize lower environmental impact.
The Corporate Innovation Directorate also has the task of implementing an effective, future-proof innovation model and, in outlining its actuation, defining innovation scenarios and priorities that focus on people and the creation of permanent synergies between methodologies, infrastructure projects and processes.
The new Directorate also guides SACMI innovation strategy by focusing on financing opportunities and related partnerships.
The model pivots around people and the creation of permanent synergies between methods, projects, facilities and processes
From a scenario perspective, Corporate Innovation R&D aims to:
• embrace innovation to provide products, technologies and services that place customers at the forefront of the market
• drive the innovation that reduces environmental impact, making sustainability an essential competitiveness factor (customers of the future will increasingly demand sustainable technologies and products).
• create advantageous connections and strategic development lines within the process digitalization area (in coordination with the Digital Innovation & Automation Hub’s Digital R&D department).
• support new business models by maintaining the high levels of research that markets demand.
SACMI innovation priorities
Digital assistants. Development of ‘digital assistant’ chatbots with proactive problem-solving features to support Customer Service operators, speed up response times and standardize procedures regardless of the human factor.
In-Cloud Services. Again with an eye to streamlining customer support, development of digital assistance services based on the in-Cloud acquisition of machine data and its integration in the SACMI S.P.A.C.E. spare parts and assistance portal.
Quality control. Use of AI in quality control to help workers manage systems and shift the focus from quality control to process control (e.g. Classy AI project).
Materials. Research into new materials from renewable sources (e.g. cellulose caps and containers) or recycled materials (rPET, rHDPE, etc.).
Energy. New hydrogen and electric kilns to achieve climate neutrality goals. Comprehensive systems for heat recovery, fume treatment, lower emissions.
Eco-enhancement. Systems for total recovery of water, waste and any other raw material that can be fed back into the production process.
Methodology and processes
To create an effective, future-focused innovation model, the SACMI Corporate Innovation Directorate acts to:
• promote greater awareness of the latest challenges at all levels of the company.
• bring about conditions that drive professional development, resulting in well-trained personnel who are ready to face expected and, more importantly, unexpected challenges.
• invest in the establishment of facilities where people can access long-term training and make the most of their innate talents.
The bedrock of this work is the definition of structured corporate methods and processes that can drive innovation yet still retain enough agility to encourage creativity and make the most of human resources.
SACMI also pursues innovation in partnership with public and private bodies and institutions Doing so intercepts every opportunity to create a company-wide innovation model that has positive synergies-repercussions throughout the local economic ecosystem (schools, universities, customers, institutions, stakeholders).
The Labs
From an infrastructure perspective, the Imola Research Center and the various R&D Labs within the individual Business Units are key drivers of SACMI innovation.
The SACMI Research Center is on the National Register of research laboratories drawn up by the Italian Ministry of University and Research. While organized as a set of technological labs and research units within individual Business Units and Group companies, it also takes on the task (as in the case of the SACMI Innovation Lab) of achieving across-the-board R&D Automation goals for all the Businesses.
With almost 300 highly specialized technicians and researchers, its direct research lends support to customers at every stage of product development, making a major contribution to the innovation ecosystem that encompasses the company, the community and partner companies.

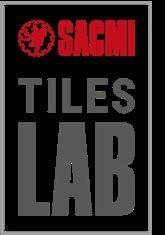
SACMI Tiles Lab
This Lab engages in cutting-edge aesthetic research on ceramic products in connection with the ongoing development of machines, especially forming and decoration technologies. This places SACMI in a position to offer customers innovative product design services to convert aesthetic needs into high-quality industrial products made with modern sustainable technology.
The Lab is equipped with state-of-the-art instruments and highly qualified technical personnel. It offers customers comprehensive technological facilities (e.g. analysis and characterization of raw materials and body recipes). It provides problem-solving services, on-site assistance, specialist training in the use of SACMI machines and plants, plus product development and market analysis services.
The Tiles Lab - in concert with technical facilities and the Experimental Department - develops new tile manufacturing technologies.

SACMI Sanitaryware Lab
Like the Tiles Laboratory, the SACMI Sanitaryware Laboratory and pilot plant offer a full range of services, from body/glaze formulation to mold-making, all the way to the finished product. More specifically, the Laboratory offers technological support: this consists of comprehensive expertise on raw materials and body recipes and advanced services for sustainability (R&D to optimize water, energy and raw material consumption). This is followed by on-site assistance during the plant start-up, industrialization and testing stages and Digital Product Development services that span from creation of models/molds to industrial testing on the pilot plant and the development of innovative process solutions.
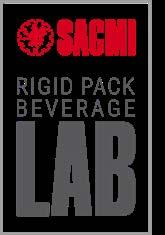
SACMI Rigid Packaging-Beverage Lab
This facility researches the materials used in rigid packaging (cap, preform, container) production processes. In recent years, the Laboratory has focused on developing ever-lighter, higher-performing caps and containers (lightweighting), guiding customers towards the adoption of new standards and working alongside the main international certifying facilities and bodies (e.g. CETIE).
Performed in partnership with key academic institutions and industry associations, the work includes research into new eco-compatible materials (recycled PET and HDPE, cellulose, ‘hybrid’ plastics) and the development of specific applications/prototypes with a view to industrialization.
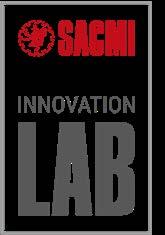
SACMI Innovation Lab
Operational since 2017 and officially inaugurated in 2019 - with co-funding from the Emilia-Romagna tender to attract investment in advanced Industry 4.0 sectors - the SACMI Innovation Lab was established to develop and disseminate 4.0 enabling technologies throughout the company in the vast fields of Automation R&D, digital simulation and software development.
More specifically, SACMI Innovation Lab:
• develops innovative digital printing systems, designing both Embedded Hardware, Firmware and software applications optimized for color control.
• develops methodologies and skills applicable in the Robotics & Industrial Automation field, with a sharp focus on automation systems, robotics and mobile robotics.
• performs TRL (technological readiness level) investigations into the industrial applicability of research results, also from an ‘open innovation’ perspective, according to the needs of the SACMI Business Units.
• builds multi-level simulation systems (from mechatronic to process) to seek out new technologies to drive digitalization in processes and other areas.
With co-financing from the ‘Emilia-Romagna tender to attract investment in advanced Industry 4.0 sectors’ at an end, the Lab continues to operate within the Digital Innovation & Automation Hub and coordinate with the Corporate Innovation Directorate. The Digital R&D Relationship Manager plays a valuable ‘link’ role.
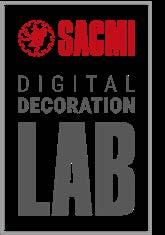
SACMI Digital Decoration Lab
The Lab is co-funded by the ‘Activity 5.1 Local competitiveness infrastructure development support’ regional tender, part of the Regional Manufacturing Projects Program. By expanding its equipment pool and skills set, the Lab aims to provide an engineering and applied research facility for the digital surface decoration field.
The LAB was established in 2021 in Casalgrande (Reggio Emilia) at the SACMI Tech headquarters, where most of SACMI’s digital decoration technology (primarily ceramic but also metal) development takes place.
This facility, fully operational since 2022, centers on the new pilot plant area where both SACMI client companies and raw material suppliers (e.g. pigments, inks, materials) can test and trial the materials.
Again, the Lab’s mission centers on operating as a trait d'union between corporate businesses, suppliers and potential customers. However, it also works closely alongside the regional research system to speed up response times and the transfer of innovation to businesses.
More specifically, in 2023 the Digital Decoration LAB was involved in projects related both to ceramic decoration (e.g. new water-based inks on digital ceramic printers) and new metal decoration technologies (DMD).
Integrated Annual Report 2023 / Innovation and research / Corporate Innovation R&D
SACMI enjoys flourishing partnerships with numerous Italian and European Research Institutions/Universities. It also takes part in projects financed at regional, national and European level.
R&D – Resources and projects¹
Corporate Innovation R&D
Resources, projects, patenting
Research and Development play a strategic role in a company like SACMI, which invests heavily and continuously to ensure customers can count on innovative products and effective services.
SACMI has placed energy and environmental sustainability at the center of its strategy, highlighting the company’s commitment to green innovation and environment-friendliness. This approach is evident in a series of initiatives and projects launched by the company, demonstrating now the company proactively manages environmental impact and promotes sustainable practices.
Projects related to the topic of a circular economy ’ are especially significant. These mainly concern the Rigid Packaging area (with the search for more sustainable, easier-to-recycle materials for containers) and efforts to mitigate climate change. The latter involves the ongoing development of plant engineering solutions for the Tile sector that are designed to reduce CO 2 emissions (e.g. replacement of fossil fuels in kilns by investigating hydrogen and electric heating alternatives).
Further projects aim to reduce water consumption in production processes and allow its complete re-use by way of innovative ultra-filtration systems (Whiteware and Tiles area). Key investments include the design and implementation of ground-breaking ceramic tile/slab firing/drying solutions powered by renewables or electricity.
In the Rigid Packaging sector, much of the investment has focused on a pilot version of a continuous automatic machine that can sustainably dry-mold caps made from 100%-recyclable natural fibers.
It should be noted that all three ‘dimensions’ of sustainability - environmental social and economic – are particularly relevant to ceramics (which uses energy-intensive production processes), an industry in which maintaining one’s competitive position is closely linked to innovative advances on the three ESG fronts.
of which FTEs engaged in funded R&D projects
Patents²
The substantial level of research and innovation is also evident in the number of new patent applications, with 272 new inventions filed in 2023 alone and more than 2,400 active patents out of a total of nearly 6,000 filed in the Group’s history (more than one patent per employee).
Patent applications (overall number)
N. of patent applications filed in the year
N. active patents (overall number)
Patenting costs incurred in 2023, which included maintenance and consultancy costs for the Business Units, amounted to 4,052,188 euro for SACMI Imola, up from the 3,145,000 euro incurred in 2022.
1 The data in the table refers to the following Italian companies of the SACMI Group: SACMI Imola, SACMI Tech, SACMI Forni, Iprel, SACMI Beverage, Gaiotto.
2 2021-2022 data refers to the parent company, SACMI Imola. To make data comparisons easier, the 2023 column indicates both SACMI Imola data and Group data.
Integrated Annual Report 2023 / Innovation and research / Corporate Innovation R&D

Membership associations
SACMI plays an active role in several associations to promote the principles of cooperation , a culture of quality and innovation and sustainability.
More specifically, SACMI adheres to Legacoop, Legacoop Produzione e Servizi, ACIMAC (Association of Italian Ceramic Machine and Equipment Constructors), UCIMA (Union of Italian Constructors of Automatic Packaging Machines), AMAPLAST (National Association of Manufacturers of Machines and Molds for Plastic and Rubber), UCIMU-Systems for manufacturing, ANIPLA (National Italian Automation Association) and is a member of ANFIMA (National Association of Manufacturers of Metallic and Related Packaging).
Furthermore, SACMI works alongside pan-European and transnational professional associations that seek to promote advanced research and training in their respective industries.
SACMI is a member of the Italian Ceramic Society (I.Cer.S.). Founded in 1972, the latter is a key reference point for the worldwide dissemination of Italian ceramic technology and plant engineering know-how.
It also adheres to the Brussels-based European Powder Metallurgy Association (EPMA), which unites key players in the European sintered products industry. Participation as a member of the Association Council involves SACMI in the development of further training and research projects, together with leading European universities and research facilities.
It is also a partner of the European Machine Vision Association (EMVA), a non-profit association representing the European vision systems industry.
3.3
Collaboration takes the form of participation in industry-specific associations - both pan-European and transnational to promote advanced research, training, and new standards/opportunities concerning sustainable materials and technologies
Since 2019 SACMI has sat on the board of AIM (Italian Association of Science and Macromolecule Technology), a non-profit association that promotes training and development in the polymers and macromolecules field. Once again, this is a key partnership that involves us in innovative research projects on, for example, new bio-compatible materials and the development of higher-performance, less energy-intensive processes.
SACMI advances the dissemination of international standards in the Rigid Packaging field through its membership of CETIE, the international association that promotes, on a voluntary basis, innovation and technical standardization in the sector. SACMI is a partner of Plastic Recyclers Europe, PETCore Europe and the American Plastic Industry Association. It is also a member of ABMI (Association of Beverage Machine Industries).
In Italy, SACMI is a partner of Unsider, the UNI-federated body that draws up regulations and standards for the steel sector (steel and cast iron).
Research consortia
SACMI works with key research institutes and consortia. These include the Bi-Rex Competence Center of Bologna (Big Data Innovation & Research EXcellence), Mist-ER (Mechatronics, Biomedical and ICT industrial research and technology transfer lab) and the InterMech Mo.Re, CRIT Research Interdepartmental Center (consortium based in Vignola, founded as a vehicle for regional manufacturing excellence to promote collaborative innovation, technological scouting/research and lend support in accessing the best national/EU funding opportunities).
SACMI is one of the private founding members of the Circular and Sustainable Made in Italy foundation, established in late 2022; this is responsible for implementing and managing the Extended ‘MICS Made in Italy Circular and Sustainable’ Partnership funded as part of the National Recovery and Resilience Plan (PNRR). The Extended Partnership involves private companies, universities and public bodies. It aims to co-finance basic research projects in areas concerning economic, environmental and social sustainability, the circular economy, and the digitalization of materials, products, services, processes, factories and production chains, the main focus being on ‘Made in Italy’ industries.
SACMI is an associate of the National Smart Factory Cluster. The latter (which includes companies, business associations, local government bodies, universities and research bodies/institutes) seeks to actuate a research- and innovation-based strategy to sharpen the competitiveness of the Italian manufacturing system.
Moreover, since 2021 it has been a member of two Regional Clusters. These aim to bolster the ability of the Emilia-Romagna innovation system to engage in collaborative research and technology transfer as defined in the Regional Intelligent Specialization Strategies: CLUST-ER MECH (which seeks to hone competitiveness in the mechatronics and engine sector) and CLUST-ER INNOVATE (which focuses on service innovation).
From the Bi-Rex competence center to national-regional innovation Clusters, SACMI is also a partner of the ‘Circular and Sustainable Made in Italy’ project, funded by the PNRR (National Recovery and Resilience Plan)
Universities and research bodies
SACMI has about 100 partnerships with universities, institutes and research consortia in Italy and other countries.
At university level, SACMI has close research ties with: Alma Mater Studiorum of Bologna (Departments of Civil Engineering, Chemistry, Environment and Materials, Industrial Engineering, Electrical power and Information, CIRI MAM, UNIBO Inter-departmental institute of Industrial research). It also enjoys valuable partnerships with the Universities of Modena and Reggio Emilia (UNIMORE), Politecnico di Milano, the Università Cattolica del Sacro Cuore and LIUC, the universities of Parma, Università del Piemonte Orientale, Università Politecnica delle Marche, and the universities of Ferrara, Padua, Trento, Salerno, Cassino, Lecce, Sassari, Palermo, Pavia, Brescia, Università del Salento, Università di Bolzano and Università della Calabria.
SACMI works with CNR (National Research Council). More specifically, it partners with CNR ISTEC (technology of ceramic materials) and CNR INO (National Optics Center). It also works with Bologna Ceramic Center, EcamRicert (Vicenza), Iseven Servizi (Modena) which performs microbiological analysis in the plastics-packaging field, SSV (Experimental Glass Station), AlmaPlasma (Unibo spin-off concerning plastic surface treatment), the CRA center (Rome, dairy sector) and the National Agency for New Technologies, Energy and Sustainable Economic Development (ENEA).
SACMI also engages with several foreign institutions, such as the German Fraunhofer Institut (structural strength and reliability of systems department), IREQ (steels, large components), KIMW (Kunststoff Institut Lüdenscheid), the University of Wageningen, the Spanish ITC (Instituto de Tecnología Cerámica), the French Université Grenoble Alpes, the University of Magdeburg and Montreal Polytechnic. There are also internal synergies with Alpha Ceramics (a Germany-based Group company that works with advanced ceramics and new materials) and the Laboratory/Competence Center of German subsidiary Sama Gmbh (tableware).
SACMI has over 100 partnerships with universities to develop strategic business projects. Research facilities belonging to the worldwide SACMI company network are involved in several partnerships with foreign institutions
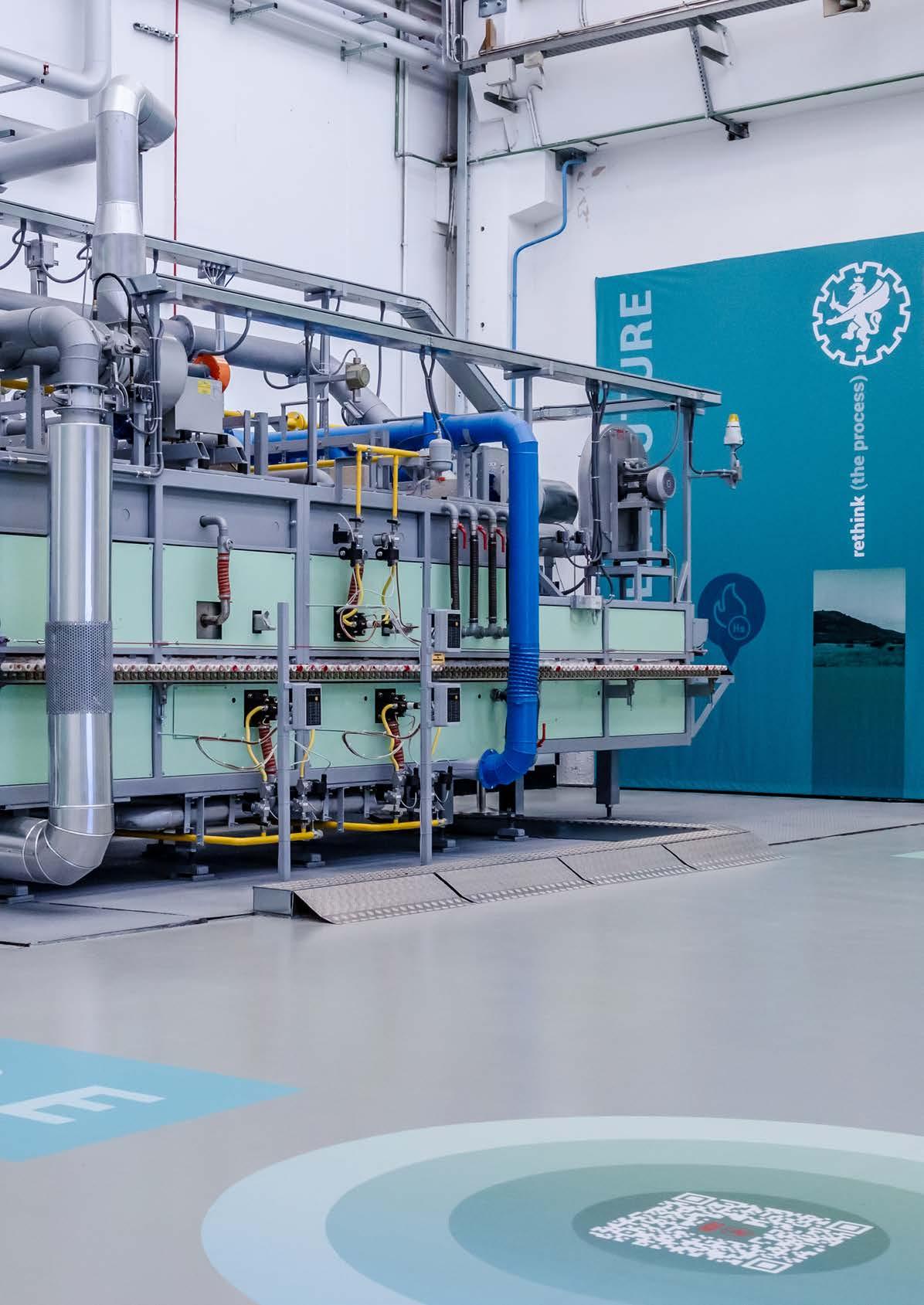
Main ongoing funded projects
SACMI is involved in numerous R&D projects, co-organized with national and international partners.
More specifically, these projects are co-financed by the Region of Emilia-Romagna, the Ministry of Enterprise and Made in Italy (MIMIT), the Ministry of Universities and Research (MUR) and national Competence Centers. Further projects are supported by the European Commission via the Horizon Europe program.
These projects generally run for several years. The most significant to be financed during 2020 include:
Ceramics
SACMI is a partner of the START (Sustainable Data-Driven Manufacturing) project promoted by MIMIT. This aims to create and test technological solutions/operational protocols to convert ‘smart factories’ into ‘intelligent factories’ with 5.0 capabilities. This goal will be pursued in specific steps that include: the development of a ‘digital twin’ model equipped with both AI and ‘bio-intelligence’ capabilities, able to manage bidirectional data/information flows between the physical and virtual realities of the factory; construction of a statistical model to describe interactions between materials, processes and products; development of an AI-powered application framework specifically for the ceramic industry (the main goal being to make it more sustainable through more efficient management of natural and energy resources) and testing of such AI algorithms in an operational environment; design of Intelligent Factory architecture using an Abductive Design Thinking approach; extending the concept to the building itself by designing ceramic cladding equipped with sensors to monitor indoor and outdoor environmental parameters.
Development of new digital services for design and industrial automation, including research on new operating protocols and OT-to-Cloud applications, is a common factor on all projects 3.4
Integrated Annual Report 2023 / Innovation and research / Main ongoing funded projects
The GLUELESS (Digital Tool for the Design and Evaluation of Glueless Ceramic Solutions) project, instead, aims to develop digital services for industrial design and research into new, more sustainable, energy-efficient tiles. This project is financed by the ‘Extended MICS Made in Italy Circular and Sustainable Partnership’ using PNNR funds, with SACMI Imola as lead partner in close collaboration with the University of Bologna. The project explores production methods for an innovative ceramic tile and the relative digital tools available to industrial designers. The key point of the project is to develop a ‘glue-free’ way of attaching the tiles onto a plastic substrate. The goal is to obtain a digital tool that can guide sustainable tile design on the basis of the input material and simulate the properties of the finished tile.
The PHOTOCURABLE (Innovative Photocurable Formulations for AM Application in the Production of Ceramic Tiles Molds) project, instead, is dedicated to molds and is, again, financed by MICS. The project’s main objective is to identify photo-curing liquid formulations suitable for the production of ceramic tile molds that are also manageable from a digital mold manufacturing perspective. PHOTOCURABLE also involves the building of a scale prototype to test new formulations, obtained using high-temperature DOD technology. The goal is to take mold performance beyond the current state of the art (e.g. abrasion resistance) and expedite the replacement of fossil-origin resins (monomers and oligomers) with chemical products that are attainable from renewable resources.
Advanced materials
SACMI took part in the CPM project, part of the MISE-Horizon 2020 PON co-financing scheme, which focuses on the construction of complex gears by compacting metal powders. Project goals include the development of a technique that maximizes density near the sides of the sintered teeth and the refinement of further innovative ‘one-step’ machining techniques for such parts that are faster and more reliable than conventional ones. Project development follows ‘cir-
cular economy’ guidelines (as highlighted by the powder pressing and sintering process which, unlike chipping-type removal processes, generates no scrap).
Rigid Packaging
FIBER-CAP (part of the MIMIT ‘Agreements for innovation’ tender), instead, focuses on technology for the sustainable dry molding of rigid packaging caps made from 100% recyclable natural fiber. This project aims to overcome current limitations on fiber treatment and dry forming processes. It also centers on the functionalization of materials, design and construction of molds/ molding machines (based on CCM technology) and includes the set-up of an ‘industrial’ performance’ pilot line that can be used to carry out on-product testing.
Digital Innovation & Automation
With VISUALXR (Advanced Virtual Tools for Digital Acquisition and Visual/Haptic XR Interaction for Textile Industry), funded by MICS with the University of Bologna as lead partner, the goal is to improve the remote co-design processes that characterize the textile industry; this is to be achieved by developing a calibrated workflow, guided by augmented-reality perception to perform digital acquisition and processing (including definition of the IT architecture to save and share the obtained results and so reduce new product-project development times). SACMI Businesses are interested as the project refers to the possibility of ‘digital tactile perception’. Introducing tactile perception into augmented reality may have applications in ‘low relief’ objects such as tiles or food containers. The tactile concept is particularly pertinent to Virtual Training, a topic strategic both to SACMI Group businesses and the external market.
With SACMI Imola as lead partner and the involvement of Iprel, the POWOPS project (part of the Bi-Rex tender) aims to create a cloud-native software development platform for the manufacturing sector that follows a platform-as-a-service
model. The goal is to respond to the manufacturing industry's need to develop versatile, fault-resistant, scalable applications in an OT-to-Cloud environment. The adopted approach favors the use of modern commercially available IT tools and emerging methods , notably the creation of a DevOps methodology adaptable to the Operations environment (control of automatic operations and processes according to strict security parameters).
ILUMINAS (Large language model after-sales)led by SACMI Imola, and part of the Bi-Rex 2023 tender - focuses on the opportunities offered by Artificial Intelligence to develop a demonstrator, ‘trained’ by way of machine use and maintenance manuals and the relative task/repair sheets. This aims to develop an after-sales support (Customer Service employees) model (and tool) based on machine learning and LLM models, rationalizing and codifying responses without compromising the dynamism and flexibility of the service. Ultimately, the goal is to integrate the tool into ticketing management by developing an IT assistant that provides operators with decision-making and troubleshooting support.
With PLAAS+ , co-financed by Bi-Rex, the aim is to develop next-gen machine control panels (PLC as-a-service) by combining consolidated traditional automation methods with the benefits of Edge and Cloud systems (speed, scalability, reliability, etc.). To address the topic of IT-OT interaction in industrial automation settings, it was necessary to begin with the heterogeneity of existing devices and from there define a Data Model to standardize data representation and ensure interoperability and integration into the Edge environment.
In the field of industrial machine eco-design, SACMI is a partner of QUEST , co-financed by Bi-Rex. The main goal is to develop a systemic approach, based on shared methods, to continuously improve aspects linked to the life-cycle management of automatic wrapping and packaging machines with a view to sustainability. This project aims to develop a specific environmental impact assessment method (based on LCSA, Life Cycle Sustainability Assessment) for these machines and explore how it can be applied in other areas.
The MATRIX project (co-financed by the Bi-Rex 2023 tender, collaborative robotics area), instead, focuses on robotic handling/conveying of liquids for high-performance industrial applications. This mainly concerns automated packaging lines. More specifically, it involves the testing of innovative handling and co-manipulating techniques for liquid containers. Technical challenges include the intrinsic nature of liquids - i.e. their fluidity - and the need to develop and test highspeed motion planning and control techniques to minimize in-container ‘sloshing’. The ultimate goal of the project is to create a demonstrator with a broad application range.
The EVOCATION project - again co-funded by BiRex - seeks to develop innovative, cost-effective sensors that monitor machine diagnostic parameters and load conditions. This aims to leverage the capacity of monitoring, diagnostics and prediction techniques - which rely on advanced sensors - to improve process efficiency and quality while significantly boosting competitiveness. Current limits include the ‘acquisition cost’ of certain items of information: this could be reduced by implementing latest-generation sensors and defining methodologies and analysis techniques that incorporate elements of AI.
Iprel
Co-funded by MISE, the SCREAM project aims to develop distributed, customized analytics that support decision-making processes on manufacturing machines and infrastructure (iTools development-testing). With IPREL - the SACMI Group’s software house - the main goal of the initiative is to help manufacturing companies implement smart manufacturing projects by creating an advanced predictive maintenance and monitoring software platform for real-time, remote, safe control. Ultimately, the goal is to help operators make ‘data-driven’ decisions concerning machines and processes, anywhere, any time, in order to maximize their performance.
Integrated Annual Report 2023 / Innovation and research / Main ongoing funded projects
SACMI Tech
This company (which, in 2020, merged the facilities and skills of Cmc, Intesa and Nuova Sima), continues the UNDER CONTROL: MADE IN 4.0 ’ project. Its aim: to create a new, all-Italian digital control technology based on IoT architectures, the ambition being to set a new plant management standard.
Ultimately, the goal is to translate process control into services and standards that are universally applicable to customer companies. Such services and standards are intended to be sustainable from both an economic and a technical feasibility perspective and allow for the production of ‘fully customized’ large semi-finished ceramic slabs of variable thickness (3 - 30 mm).
Gaiotto
Gaiotto continued to develop advanced industrial robot programming techniques. Selected as part of the Emilia-Romagna investment attractiveness tender (Italian Regional Law 14/2014), this project aims to build a new generation of robots that are easier to program and capable of moving and even ‘thinking’ like humans. Looking ahead, the work will focus on fine-tuning the following: an offline programming system and self-learning programming algorithms; the relative modular/customizable hw/sw system for sensor-based analysis of the workplace and the objects to be handled: a robot ‘self-programming’ system that starts with the assigned task/problem. The technological results will allow Gaiotto to develop a new generation of industrial robots with simple, fast, adaptive programming.
SACMI Forni & Filter
In 2022 SACMI Forni & Filter launched the AMAZZONIA project to reduce the CO 2 emissions that stem from the ceramic manufacturing process. Its goal: to implement solutions that reduce environmental impact, especially in terms of heat consumption (analysis of technological cycles, new ‘green’ fuels, optimized plants and raw materials, new processing techniques linked to indepth energy research).
More specifically, the project focuses on kilns and dryers, exploring innovative technological solutions and power sources (such as hydrogen and renewable-based electric) and building the relative prototypes. Ultimately, the aim is to validate any attainable environmental benefits via LCA (life-cycle assessment).
As part of this project, in 2023 SACMI built and inaugurated a hydrogen production and storage station. It also presented a new industrial kiln prototype capable of running on up to 100% hydrogen; initial firing trials have proved to be successful. Industrial testing of the product will now continue; moreover, the new electric kiln project is expected to be completed in 2024.
Open innovation projects
Open innovation as an opportunity to identify enabling technologies and share their development not just inside the company but within the wider local ‘ecosystem’ (schools, universities, businesses) is an integral part of SACMI's innovation strategy. The year’s initiatives and projects included:
OPER.CBI
With OPER.CB I, SACMI joined Almacube's ‘open innovation challenge’ project. This sought to develop fresh in-the-field experience to give substance to the ‘open innovation’ concept. Launched in October, the project involved the selection of six undergraduates studying a range of subjects at the universities of Bologna, Ferrara, Modena and Reggio Emilia; their task was to identify new solutions to problems concerning SACMI businesses.
By taking a broad, interdisciplinary approach (the students were from vastly different fields, spanning the technical and humanistic), the ‘challenge’ was not limited to the search for specific answers to specific questions but also sought to identify a wider enabling technology, at both technical and organizational level, which might be applicable to the different businesses.
The challenge was posed as follows: “How can we help research and development employees make the most of networking as a tool to foster connections and opportunities?” Subject areas (the problem ‘assigned’ to the students) included powder molding/forming, with cross-Business Unit applicability in Tiles, Advanced Materials and Rigid Packaging.
The hallmarks of the project were its specific methodology, the step-by-step sharing of results and the establishment of work groups. Moreover, in February the ‘final milestone’ of the project saw a SACMI delegation visit the CERN facility in Geneva, where the potential of AI to read/analyze complex data tools/systems was explored.

InterMech - Mo.Re.
With InterMech - Mo.Re. Interdepartmental Research Center on Advanced Mechanics and Motor Engineering of the University of Modena and Reggio Emilia, the lab is sustaining two industrial doctorates in ‘user experience design’ and in design according to ‘triple sustainability’ principles. In the robotics-intralogistics field, Gaiotto is working on a project alongside Tecnopolo di Reggio Emilia - Industria Tecnologica Italiana
University of Ferrara
With the University of Ferrara, the Lab cooperates with the Department of Physics and Earth Sciences (sensors and semiconductors based on nano-structured metal oxides for environmental and industrial applications) and with the Department of Computer and Automation Engineering.
SACMI Innovation Lab
2022 completed the SACMI Innovation Lab co-financing phase, part of a tender to attract investment in advanced Industry 4.0 sectors within Emilia-Romagna. This involved the development of adaptive production systems, intelligent molds and advanced sensors, taking within the SACMI Digital Automation & Innovation HUB and in alignment with Corporate Innovation Directorate projects.
Even though co-financing of the SACMI Innovation Lab came to an end in 2022, it continues to pursue its institutional mission - to bring the world of research closer to industry from an open innovation perspective - within the Digital Innovation & Automation Hub. Several projects moved forward in 2023, including:
University of Bologna
Close collaboration saw the launch of a research project to optimize articulated robot trajectories with the University of Bologna (Department of Electrical Energy and Information Engineering). Then, with the Department of Computer Science and Engineering, the Lab was involved in two doctorates on computer vision and knowledge injection. It also collaborated with ALMA AI (Unibo's AI research institute). SACMI also partnered with DIFA (Department of Physics and Astronomy) on a project exploring new sensors for the process industry, engaging in two university thesis projects. Alongside the DISI (Department of IT, Science and Engineering) SACMI activated the new ‘Building a knowledge base: integration, extraction and organization of key information for advanced machine learning’ doctorate.
CNR Bologna technical hub
Various in-the-field projects with MistER - Smart Innovation are in progress. These include the production of sensors that continuously measure the moisture content of ceramic raw materials and the development of intelligent molds for SACMI machines (CCM cap presses in particular) that feature predictive diagnostics and anti-counterfeiting functions.
Initial analysis of materials using THz technology - to reveal defects or changes in the density of materials such as plastic, paper, ceramics and fabrics - was concluded.
Regional clusters
With regional Clusters (Clust-Er Mech), SACMI works with the Advanced Materials, Industrial Automation, Big Data & Analytics Departments.
With regional Clusters (Clust-Er Mech), SACMI works with the Advanced Materials, Industrial Automation, Big Data & Analytics Departments.
CRIT
With CRIT, SACMI performs technological scouting and takes part in numerous round tables on Automation & Robotics, Advanced Materials, Big Data & AI, and Advanced Factory Management.
Bi-Rex
In addition to already-completed projects, 2023 will see SACMI continue working with Bi-Rex to establish an internal work group that, over three years, will ascertain the viability of developing projects in several areas of potential interest to SACMI Business Units.
Integrated Annual Report 2023 / Innovation and research / Main ongoing projects
R&D Automation projects The ‘life cycle thinking’ approach
Further projects by SACMI Innovation Lab - some completed, some in progress - include a particularly interesting series of activities that take a life cycle thinking approach: these aim to expand the sustainability concept within manufacturing industry from a broader perspective, taking into account the entire life cycle of the product by considering its economic-productive impact and, therefore, its environmental and social impact. Underlying these activities is a ‘digital’ approach to defining large datasets in order to define sustainability and incorporate it into products and production processes.
The paper ‘Sustainability and Industry 4.0: definition of a set of key performance indicators for manufacturing companies’, published by the University of Modena and Reggio Emilia, highlights some of the projects carried out by the Lab. For 2022 and this current year, the following stand out:
Embedded Hardware
Numerous boards were redesigned to offset the obsolescence of machine electrical components (microchips) and, at the same time, overcome supply chain issues (longer lead times, price volatility, obsolescence).
A study was conducted to introduce EFINIX technology as an alternative to Altera technology. Design of the new APD architecture for multi-color deep digital printing was also completed.
In the Tiles sector, testing of the ‘continuous flow’ moisture content measuring system was completed, in collaboration with MistER. In Rigid Packaging, instead, production of a new spark tester to measure cap integrity began.
Further studies on CCM machine molds-tools focus on better control of force, vibration, pressure and temperature parameters and assessment of THz technology (sub-TeraHerz Imaging Unit material scanning).
Digital printing
The Lab continued its enhancement of CRONOs software for the control of graphics on ceramic lines. This included feasibility analysis of ‘on-the-fly printing’ algorithms and new highly ‘responsive’ hardware architectures (in collaboration with SACMI Tech).
To streamline decoration machine programming, a new feature - Digital Vein Preview - was added to CRONOs: this provides a 3D representation of the ceramic product, illustrating the decorated surface and the internal veining pattern. A new architecture for electronic printing process control, which aims to improve on the current state of the art, is currently at the design stage.
SW Automation
Some of the most noteworthy activities in this project family include studies on refactoring of the particle size distribution measurer for ceramic powders (GMS measurer).
On the Tiles front, the search continued for more efficient, economical systems to measure slip technological parameters while scouting projects investigated integrated vision systems in automation-robotic environments (e.g. TwinCat Vision, Mapp Vision).
Robotics
In robotics, the LAB collaborated in the study and market launch of new off-line programming software for sanitaryware robots (Smart Off Line NG); in a similar context, it also worked on the industrialization of kiln car load optimization software. Drawing on the technology already used with whiteware, studies were conducted to design a system for the robotic deburring of tiles.
In collaboration with the Rigid Packaging BU, a feasibility study was carried out to see whether robotic handling of preforms might be used to perform total quality control with the aid of automated vision/weighing technologies.
Industrial simulation
In 2023, the LAB continued to develop plant digital twins (particularly for the body preparation, powder storage and pressing, warehousing and handling, processing and sorting phases). It also contributed to the complete virtual commissioning ecosystem project (in-the-loop hardware-software development, ML interoperability-automation).
Note also the project with BMR on the Leviga and Supershine machines (optimal crossbeam speed calculation for homogeneous surface coverage,
satellite head rotation speed modeling), plus quality control-focused technological scouting.
Working in concert with the Tiles BU, the Lab contributed to the development of the digital dry glazing process simulator and, in the Beverage sector, to simulation of the new bundle-making machine. For SACMI Packaging & Chocolate, instead, a simulation library of primary and secondary packaging lines was developed.
Data Analytics
The design of experimental molds for cellulose caps involved investigation of cause-effect relationships between values monitored during forming and any detected defects. A further project concerns the analysis of wear-related data on slitting tools (i-Slit) for tethered applications. On BMR Leviga, process modeling was used to obtain data that extends the utility of the simulator.
Also deserving of a special mention is the Industrial MLops study on machine learning model life-cycle management methods and technologies in an industrial context, including any edgecloud integration (SACMI Smart Care service).
Lastly, a study that takes a deep learning approach to metal forming focuses on increasing the predictive power of images by limiting the necessary data set. Further big data projects in partnership with Bi-Rex are ongoing (above all in the IoT/edge-cloud computing area).
Corporate Automation
Analysis of sales codes for automation is being completed to optimize procurement and supply management (MDM-Master Data Management project).
CHAPTER 4
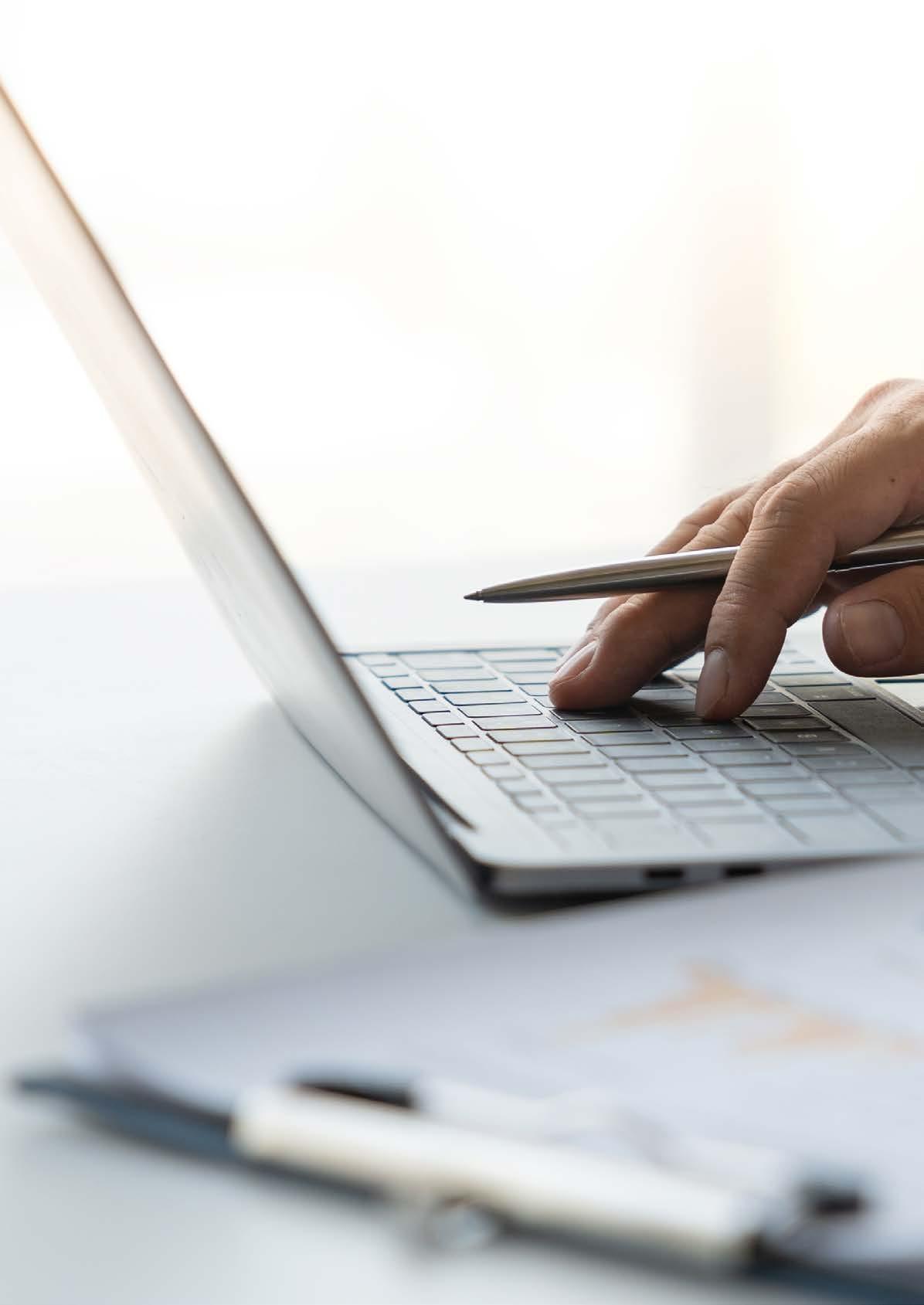
Economic value generated and distributed
The ‘economic value’ attributed to SACMI's core activities is identified through the calculation of Economic Value Generated and Distributed (i.e. the wealth created by the company in carrying out its daily business)
Economic Value Distributed is a basic element for assessing the Company's economic and social impact. It also helps evaluate the wealth generated and distributed to certain categories of subjects who have, via their involvement, contributed to producing it and/or count, in any case, among the Organization’s key stakeholders.
The Retained Value instead, represents that part of economic resources retained within the Company for its own sustenance and sustainability over time.
1
During 2023 the SACMI Global Network earned revenues of 2.036 billion euros, an increase of 12% compared to the previous year
During 2023 the SACMI Global Network achieved revenues of 2.036 billion euros, an increase of 12% compared to the previous year, generating an overall economic value of 2.091 billion euros; analogously, items relating to operating costs, personnel, remuneration of public administration and in-company investment increased by an average of 53% compared to 2022. The only exception concerns borrowed and risk capital, which dropped by 13% compared to the previous year.
In total, economic value distributed came to 1,898 million euros, 7% higher than in 2022. Lastly, retained wealth was 193 million euros, again an increase on the previous year's amount.
Economic performance reporting criteria
The company prepares its financial statements in the form and content laid out in the international accounting standards (IAS/IFRS) issued by the International Accounting Standards Board and approved by the European Union, including all interpretations of the International Financing Reporting Interpretations Committee (IFRIC) and in compliance with the provisions pertaining to art. 9 of Italian Legislative Decree (D. Lgs) 38/2005.
The Financial Statement up to 31 st December 2023 - consisting of the Financial and Asset Situation, Income, Total Income, Cash Flow and Changes in Net Equity statements - is audited by Deloitte & Touche S.p.A. in compliance with art. 14 of Italian D. Lgs. 27.1.2010 n. 39 (art. 2409-ter of the Italian civil code) and art. 15 of law n. 59 of 01/31/1992 on cooperatives.
For the purposes of this Report, the data contained in the aforementioned financial statements has been reclassified in the Added Value and Distribution framework in which economic value directly generated and distributed (EVG&D) is determined on the accrual basis in line with the provisions of GRI standard 201-1 of Sustainability Reporting Standards (GRI Standards), issued by the Global Sustainability Standards Board in 2016 and in force since 1 st January 2018.
Taxes have been calculated with specific reference to legislation governing cooperatives.
The Cooperative is subject to the tax regime envisaged for cooperatives other than prevailingly mutual assistance cooperatives. Consequently, the estimate of the tax burden was calculated by tax-relieving 90% of the amount allocated to the legal reserve, equal to 30% of the profit (thus tax-relieving 27% of profit) and 3% of the profit to be allocated to mutual aid funds for the promotion and development of Cooperation.
Economic value generated and distributed (euro)
Revenues
Total wealth generated
Operating costs
Remuneration of personnel
Borrowed and risk capital
Tax
Investment in the community
Total wealth distributed
Wealth retained by the organization
Economic Value Distributed 2023 Operating costs
Remuneration of personnel
Borrowed and risk capital Tax
Investment in the community
1
Approach to taxation
With regard to taxation, SACMI acknowledges its responsibilities towards investors, governments, suppliers, employees and the various Italian and foreign communities where it operates.
This approach also applies to taxation in order to ensure regulatory and accounting obligations are met in a balanced way.
In Italy, SACMI adopts procedures for detecting, measuring, managing and controlling tax risks. Compliance is ensured at all company levels by taking prompt corrective action with respect to any shortcomings and/or issues.
In fact, the process of determining taxes stems from and begins with a proper, truthful representation of the financial statements in compliance with accounting standards; it continues with identification and monitoring of any changes to tax regulations over time for the purposes of proper and timely submission of returns to tax authorities.
At international level, SACMI adopts Transfer pricing policies compliant with OSCE guidelines by preparing a master file, a local file and applying country by country reporting.
There are no advance pricing agreements (APAs) nor are there any ongoing Mutual Agreement Procedures (MAP).
SACMI also benefits from tax incentives such as R&D credit and Patent box. With regard to the latter, SACMI has concluded an agreement for the five-year period 2015-2019 and is waiting to sign a renewal for the period 2020-2024. To ensure proper management of customs aspects, SACMI has delegated the supervision of export procedures to its subsidiary Italiansped which handles the logistics of all Group companies.
At international level, SACMI adopts Transfer pricing policies compliant with OSCE guidelines (country by country reporting)
With regard to governance, clear roles and responsibilities in relation to tax risks have been defined within the various sectors of the organization. The Group Tax Manager reports to the Administration Department Manager who, in turn, reports to the CFO and the Board of Directors. SACMI tax policy is based on the utmost collaboration with tax authorities, with which it has no pending disputes. Additionally, while no tax control framework is currently in place, the Emilia-Romagna DRE (regional tax office) has always shown itself willing to discuss any relevant issues with the Organization.
Country by country report
The CBCR (Country by Country Report) is a tax risk assessment tool that is sent by the Italian Financial Administration to all Financial Administrations with which an agreement for mutual information exchange is in place. This must be sent within the twelve-month period following the last day of the tax year (for subjects with a tax year that aligns with the calendar year this day is 31 December). The SACMI Group fulfils this tax obligation within the aforementioned legal deadlines.
Data presented for the tax years 2023 shall be prepared by the Parent Company SACMI Imola SC for each of the jurisdictions in which the Group operates and sent to the Tax Office by 31 December 2024.
Integrated Annual Report 2023 / Wealth generated and distributed / Approach
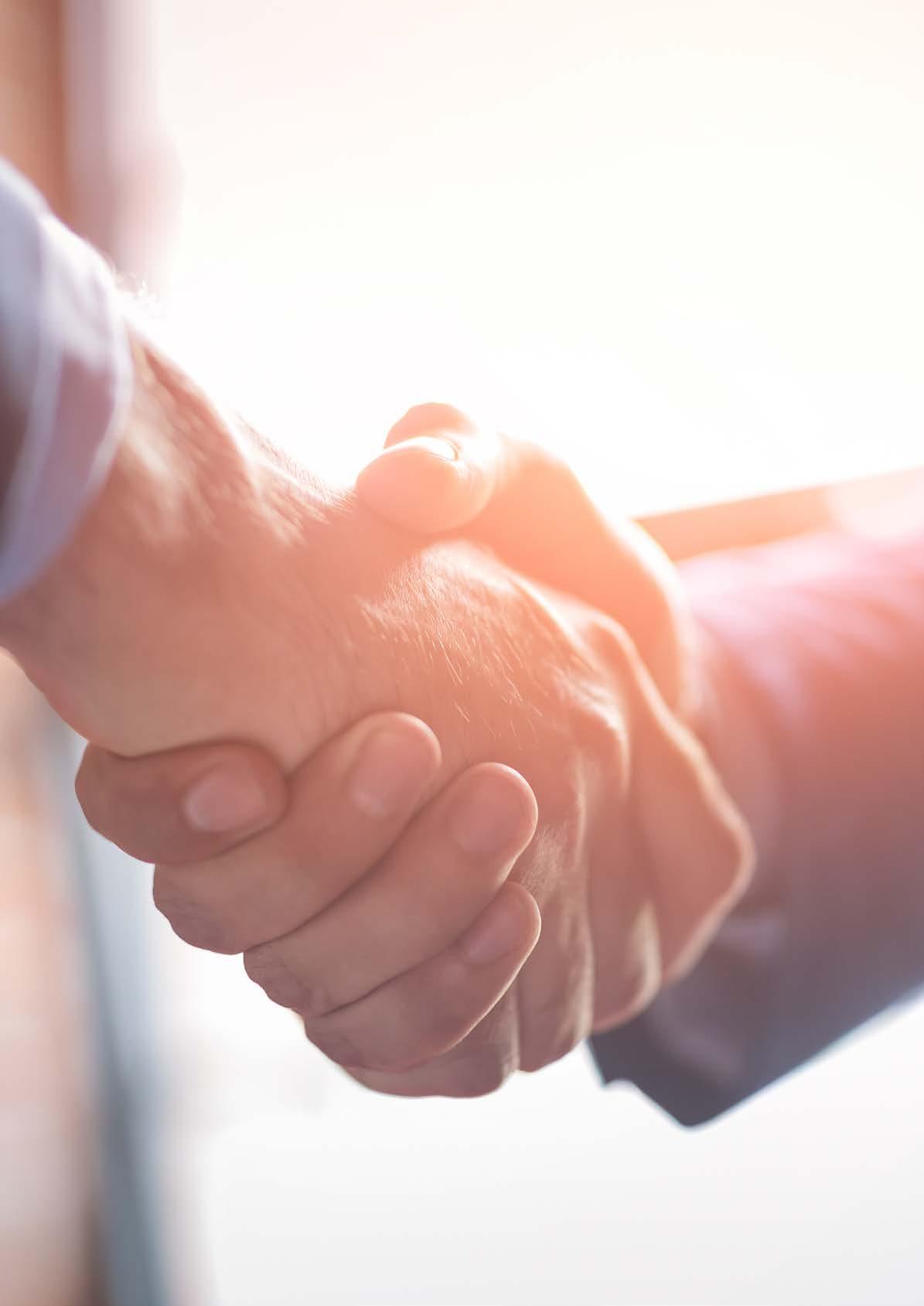
05
CHAPTER 5 Suppliers
Suppliers 1
SACMI works with suppliers according to the principles of openness, equity and fairness and pursues a Sustainable Procurement Policy
Relations with strategic suppliers that produce units or machines made to SACMI specifications rely on a partnership principle based on mutual enhancement and sharing of know-how.
The need to reduce time-to-market has streamlined such collaboration and steadily driven optimization in terms of quality and competitiveness.
SACMI is provided with a wide range of goods and services by over 2,000 suppliers.
More specifically:
• raw materials
• machine parts or machines made to SACMI specifications
• commercially available components or machine parts purchased from catalogue
• machines made by suppliers as per their own design
• consultancy investment and other services (transport, logistics, packaging), the latter mostly outsourced or provided internally.
The increase in machine and spare parts purchasing continued during 2023 with a strong preference for local suppliers (89%)
1 The chapter refers to the performance of the entire SACMI Global Network vis-à-vis quantitative and qualitative data linked to corporate procedures and processes, unless specified otherwise.
Integrated Annual Report 2023 / Suppliers
Imola SC Resto of the Group
700,000,000
Number of suppliers by geographical area (on 31.12.23)
Regional suppliers
National suppliers
Supply chain partnerships
Products designed by SACMI differ enormously in terms of their complexity and size and are characterized by specific market positioning in terms of performance/quality/price.
Suppliers, identified on the basis of product type, may differ in terms of the technology they use and their size. Nevertheless, they are all organized in such a way as to guarantee quality control, monitoring of the different stages of production and, consequently, cost control and prompt delivery. They share a desire to invest in their company, see it grow and meet the needs of both customers and markets. Thanks to this approach, SACMI is able to guarantee outstanding quality while ensuring its products retain their market competitiveness. In the same way, this approach has allowed the Organization to strengthen its international leadership over the years, contributing to the generation of shared value in communities
SACMI has always preferred not to hold shares in suppliers of made-to-specifications parts as it does not wish to alter a balance, built up over the years, that enhances their entrepreneurship; it
2 The following definitions should be borne in mind:
favors relationships based on transparency and mutual respect for customer-supplier/partner roles.
At the same time, the plant engineering sector continues to benefit from a policy of carefully targeted takeovers, sometimes involving long-standing suppliers; this has allowed SACMI to increase its direct oversight capacity in various sectors deemed strategic.
Know-how transfer
SACMI has built solid partnerships with many suppliers. They have been selected because they are organized in a way that provides the Group with supporting skills throughout the production process, can apply R&D results rapidly and have effective IT systems.
As part of a Suppliers Relationship Management plan, which aims to speed up the transfer of business and technical information, SACMI has developed Business-to-Business IT tools that allow automated mailing of purchase orders, technical drawings and shipping info to key suppliers.
• “Regional suppliers” refers to all those suppliers based in the same Region in which the Group company that made the purchase is located.
• “National suppliers” refers to all those suppliers based in the same Country in which the Group company that made the purchase is located.
• “Continental suppliers” refers to all those suppliers based in the same Continent in which the Group company that made the purchase is located.
“Global suppliers” refers to all those suppliers based outside the Continent in which the Group company that made the purchase is located.
Integrated Annual Report 2023 / Suppliers
Quality assessment
SACMI has personnel who monitor supplier quality to ensure products are consistently of the highest standard, whether made internally or externally. The resulting flexibility has allowed us to meet customer needs in terms of both volumes and observance of delivery schedules.
Suppliers of products made according to SACMI’s specifications are subject to a 4-monthly appraisal (involving aspects such as Purchasing, Quality Control and Assembly services ). If findings highlight any issues, corrective action is decided on together with the supplier; should problems persist the supplier is piloted towards a repositioning in terms of product complexity and volume. For plant engineering providers too, where the supplier pool (both third-party and Group firms) is more stable, ongoing performance monitoring is increasingly important.
All SACMI companies or branches that work with suppliers are asked to make appraisals via appropriate indicators such as quality and level of service. The result is a performance chart that provides an intuitively understandable ‘snapshot’ of the supplier or a comparison with previous years’ results.
Scenarios and trends in 2023
The volume growth that began the previous year continued into 2023. Many of the critical procurement issues experienced in 2022 were resolved. However price-related tensions have persisted despite a significant dwindling of the factors (energy cost, inflation, cost of raw materials and transport) that had caused the price explosion in the first place.
To avoid a repeat of the production crisis seen in 2021 and 2022, the major component manufacturers have set about restoring significant levels of both semi-finished and finished product ware-
house stock by combining Lean Manufacturing with more prudent strategies. The expansive effect on invested working capital was a significant issue in 2023. This was brought about by persistently high levels of warehouse stock, which resulted from a need to cope with volume growth and orders taking more than a year to complete due to dilated Lead Times. This necessitated a major re-planning of purchase orders to take a reduction in Lead Times and actual manufacturing requirements into account. Furthermore, it required careful monitoring of strategic suppliers to intercept and manage any deteriorations in their financial situations.
Code of ethics, sustainability assessment
In its relations with stakeholders, the SACMI Group pursues sustainability, propriety and transparency. This policy also applies to suppliers. Their selection always begins with an in-company inspection and a meeting with the owners to verify not just production-related aspects but compliance with values such as freedom of association, openness to negotiation and, of course, the nonuse of child labor. The Purchasing Department is responsible for verifying compliance with the above principles.
Since early 2022, the SACMI Group has enacted a policy of broader, improved Sustainability management. One of the first steps towards more responsible supply chain management was the drafting of a Sustainable Procurement Policy. Hence the need to assess and monitor the entire production process and Supply Chain: for this reason the SACMI Group has entered into an agreement with CRIBIS, a CRIF Group company. This agreement involves suppliers joining Synesgy. The latter is a global digital platform which, via compilation of a self-assessment questionnaire, rates suppliers’ overall commitment to environmental, social and governance issues via the integrated evaluation of service, affordability and quality aspects.
Specifically, assessment relates to the following areas:
• Environmental: water, energy, waste and environmental certification.
• Social: personnel management, certification and standards, relations with stakeholders and the community
• Governance: framework and composition, certification and standards.
Synesgy applies a methodology based on international sustainability standards, including the Global Reporting Initiative (GRI), the UN Global Compact, the Carbon Disclosure Project and Taxonomy guidelines.
At operational level, the improvement process was launched by sharing the Sustainable Procurement Policy Quality, Safety and Sustainability Policy and the Code of Ethics with suppliers. The awareness campaign began with strategic suppliers and those with larger volumes; the aim is to extend it to more suppliers over the next three years.
Subsequently, the questionnaire was shared via the platform. Out of all the involved suppliers, over 830 have registered on the platform, of which:
• 43% have completed and sent the questionnaire (13% at the renewal stage)
• 46% are in the process of compiling the questionnaire
• 11% have registered on the platform but have not yet begun compiling the questionnaire.
For 41.5% of SACMI Group suppliers, then, sustainability and CSR assessments are in progress.. Suppliers who did not complete the questionnaire were sent a reminder and offered all the necessary support.
Subsequently, to ensure all suppliers are ‘on board’, a second reminder will be issued to those who have still not registered.
Sustainable Procurement Policy: self-assessment questionnaire
830
key suppliers involved in 2023
Furthermore, all the SACMI Group’s Italian purchasing offices were provided with training sessions designed to illustrate the project goals and the platform operating methods. The purpose of the training was to put all Purchasing Offices in a position to respond quickly should suppliers request detailed information on the project.
During 2024, the global Sinesgy Digital Platform will be integrated into the SAP ARIBA Procurement platform currently being implemented in the company's ERP. Suppliers can use this platform to register on the SACMI portal by entering their personal/technical data, completing the Sinesgy questionnaire to obtain qualification as a suitable supplier (subject to ongoing assessment).
Integrated Annual Report 2023 / Suppliers
Local ancillary industries and integration in the local manufacturing hub
SACMI strengthens the local ‘ecosystem’ of skills, entrepreneurship and know-how in areas where it manufactures by making good use of - and, where possible, favoring - local suppliers. This logic, a historical consequence of the parent company, SACMI Imola, being an integral part of the mechatronics district, also applies at Group level.
In 2023, the SACMI Group purchased goods and services with a total value of approximately 1.28 billion euros 89% of expenditure involved suppliers who have their headquarters in the region or country where the Group company that made the purchase is located.
89% of purchases from local suppliers
The partnership principle - which takes a long-term approach based on trust, transparency, proprietary and the application of a win-win mindset - is the bedrock of the relationship between SACMI and its suppliers. The results are evident in the quality of the products and the ability to anticipate market needs. This has not, however, impeded exploration of new industrial hubs in all the areas of the world where the Group operates in order to locate specific skills and pre-empt production problems.
As far as the parent company, SACMI Imola, is concerned, many of the strategic suppliers with whom it has established decades-long relationships are located in its local district. Induced economic and employment growth in the region continued, confirming SACMI Imola’s role as a key developer of communities in Emilia-Romagna.
A breakdown of the Group's purchasing volumes by type identifies the three key categories in 2023:
• Products: constructive and commercial products purchased to make the machines designed by the Group.
• Third party machines: machines designed by third-party manufacturers and needed for the operation of lines sold by the Group.
• Services intangible assets, consultancy, external design, transport, extra-Group assembly services, installers, energy supplies, etc.
Purchases relating to machines and spare parts amounted to 945 million euros at Group level, with SACMI Imola increasing expenditure by 3% compared to 2022.
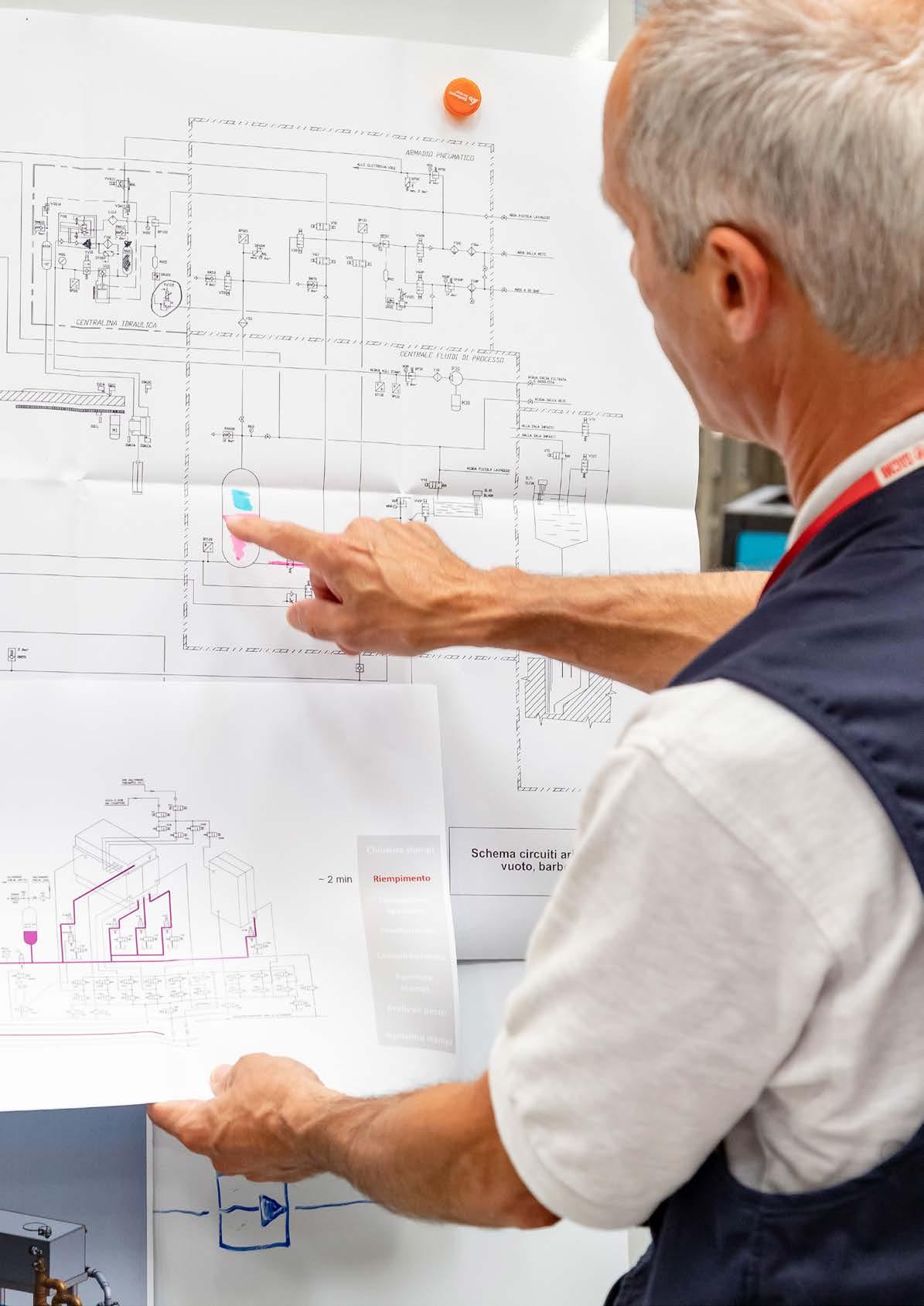
CHAPTER 6
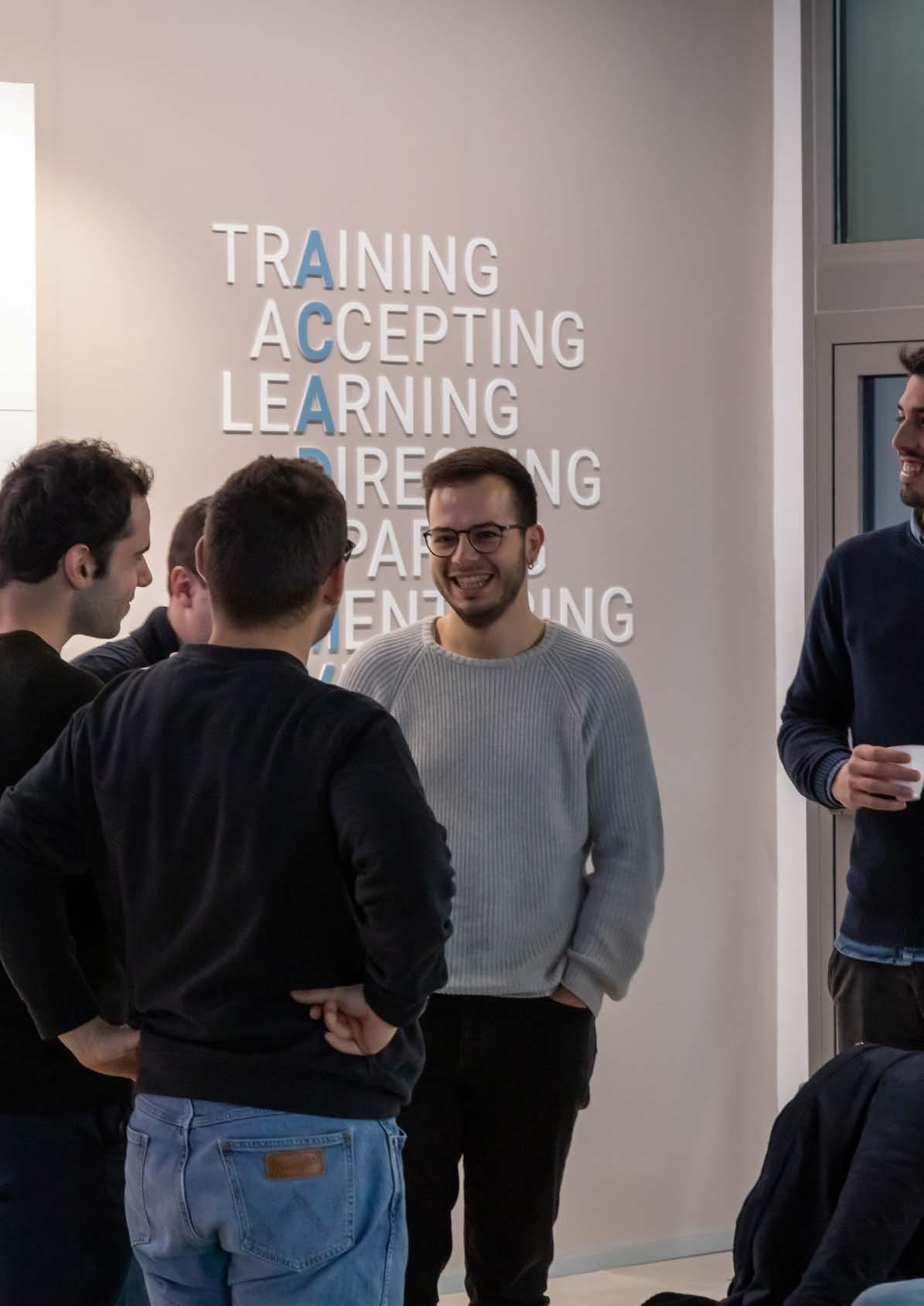
Composition and characteristics
People play a vital role in SACMI's corporate organization and success. The cornerstones of corporate policy for employees are: stability and continuity of employment, development of human resources, measures designed to safeguard health and safety.
SACMI supports and safeguards the development of human capital by creating employment.
Over the last few years, the SACMI Group has seen a steady increase in staffing levels, with 5,210 people 2 employed at the end of 2023. A total of 4,570 employees were contained within the reporting boundary, 95.5% of whom have permanent employment contracts.
1 The information contained in this chapter does not include PackSud S.r.l.
2 The data includes all the companies in the SACMI Global Network, even those not included within the reporting boundary.
1
SACMI supports and safeguards the development of human capital by creating employment. Throughout 2023, the workforce continued to grow in Italy and worldwide. The year also saw a 32% increase in training hours 6.1
More specifically, on 31 December 2023 the Italian companies in the SACMI Group counted 3,601 employees compared to 3,393 in 2022 (an increase of 208). Of these, 3,331 people have permanent employment contracts (98.3% of the total).
Employees by geographical area (on 31/12/2023)
Imola
Rest of Italy
Asia (China-India)
Europe (Germany, Luxemburg, Spain)
of employees work in a subsidiary of the SACMI Group with its operational or administrative headquarters in the Imola area
Employees by profession³ and gender
3 The categories refer to the international scope of the Group where, in most jurisdictions, there is no distinction between ‘office staff’ and ‘workers’, hence the ‘General Employees’ category. With regard to senior management, the Managerial Roles category is comparable to that concerning persons in the organization who are responsible for performance and results within their department (typically, in Italy, Managers/Middle Managers).
In SACMI female staff account for 19.08% of the total workforce. Looking solely at the Italian subsidiaries, female employment levels stand at 19.1%, a continuation of last year’s upward trend.
Employee loyalty is reflected in the length of service: 16% of employees have been with SACMI for a period of 16 - 25 years, while 12.5% have been with the company for more than 25 years. The average length of service in the company is longer than 11 years. This average is strongly affected by the high number of under-30s hired (some of whom have come from education programs).
of employees have been with the company more than 16 years
During 2023, the SACMI Group hired 572 new employees, 52.79% of whom were under 30, thus lowering the average Group employee age. This trend is evident in the Italian companies, where the number of under-30 new hires grew by 35% compared to 2022.
new hires aged under 30 in 2023
New hires and leavers by age
New hires and leavers by geographical area
ITALY ASIA (China-India)
EUROPA (Germany Luxemburg Spain) Total
The turnover rate remains very low: in the SACMI Group’s Italian companies it is just 5.89%.
<6%
Turnover rate
All the Italian sites of the SACMI Group adopt national collective labor agreements stipulated by the most representative organizations of the respective industry. This is done to regulate - in addition to that provided for by the Constitutional Sources and Law (Workers' Statute) - working conditions for all workers and all industrial relations.
All employees of the SACMI Group’s Italian companies are covered by collective bargaining agreements: the National Collective Agreement for Cooperative Metalworkers applies to all employees of the parent company SACMI Imola SC, while the National Collective Agreement for Metalworking Industry Employees or the National Collective Agreement for Transport and Logistics
Workers apply to all subsidiary employees. All executives are covered by the National Collective Agreement for Industrial Executive Workers (refer to Italian text for original-language contract definitions).
Where present, collective agreements that regulate working conditions are also applied in the Group's foreign companies.
Employees of the Group's Italian sites are also represented, where applicable, by formally elected committees and protected by further forms of collective bargaining, valid within the individual site, that seek to further improve the principles defined in the National Collective Labor Agreements.
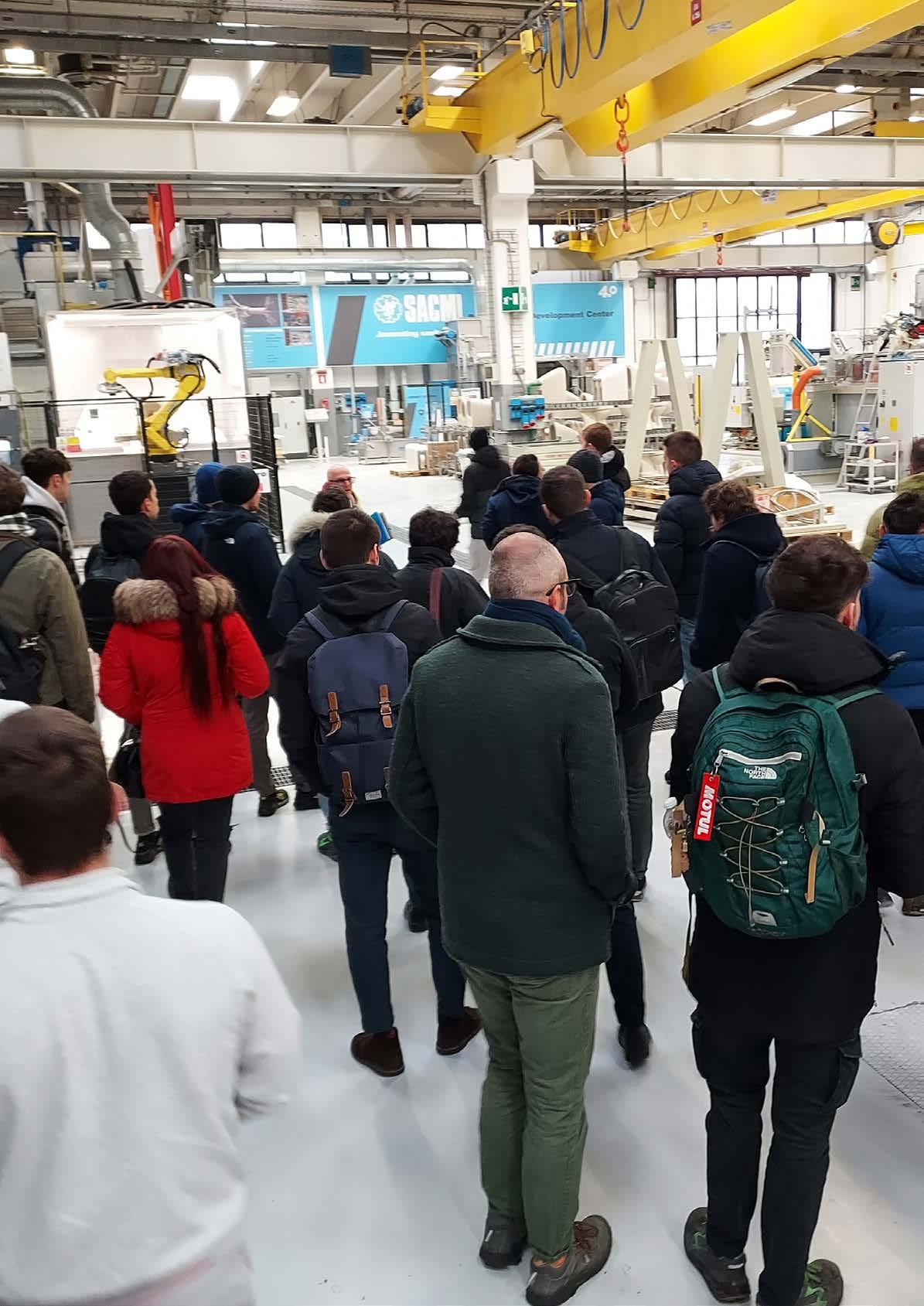
Our people
Skills enhancement
Personal and professional growth, framed by the respect, willingness to listen and feedback principles established in the governance model, lie at the core of SACMI HR policy.
In general, skills enhancement at SACMI follows both a bottom-up model (listening to workers’ needs, perceived quality of work, areas for improvement) and a diffused top-down model.
The strategic aim is to ensure that key development skills are acquired and coordinated by team leaders - not just management - as they’re the ones in direct contact with workers and have the task of helping to build harmonized teams.
In 2023, SACMI began mapping and analyzing employees’ knowledge and skills in order to identify training requirements and define training plans for each target in these two years. Enhancement of this mapping operation will be one of the key goals for 2024.
Mapping of critical skills has also led to the definition of an organizational sustainability strategy that includes preventive training: the latter takes into account the expected ‘population dynamics’ within SACMI (e.g. retirements, new business needs) and seeks to continuously improve SACMI's ability not just to manage but also plan current and future needs.
The adoption of new digital tools - alongside the growing number of roles in the organization requiring their use - has become crucial in recent years as it allows training to be delivered in a way that’s structured, transparent, homogeneous and, last but not least, in synergy with everyday manufacturing tasks.
SACMI Academy
In February 2023, the new Academy at SACMI Imola was inaugurated: 400 m2 set aside for training, an investment of some 2 million euro. Offering practical, flexible spaces that are well suited to ‘collaborative training’, the facility is designed to act as a growth driver and a catalyst for the exchange of ideas and expertise.
The year 2023 also saw the launch of a new section of the SACMI portal dedicated to the Academy; this is intended for all persons currently or potentially recipients of training (employees and customers, university graduates or diploma holders interested in learning more about SACMI’s training strategy and facilities).
During 2023, the SACMI Academy provided 70,517 hours of training to 3,512 employees of SACMI Group companies an average of 15.91 training hours per employee Additionally, a further 22,233 hours of training relating to health and safety in the workplace and environmental issues were also provided.
SACMI training: basic info
70,517 hours of training in 2023
3,512 persons involved
160 certified trainers
400 m² set aside for training purposes
4 The information contained in this paragraph does not include BMR S.p.A.
Training provided to employees by gender
During 2023, employees of the Italian companies of the SACMI group received 58,861 hours of training, with an average of 17 hours per employee, compared to 44,532 hours in 2022 (with an average of 13.12 hours per employee).
Main training programs
SACMI favors a goal-oriented diffused leadership model based on the corporate principles and values of solidarity, ethics, listening and teamwork. Accordingly, some of the main training programs were as follows.
Train the trainers
Passing on company skills is a key part of the Academy's training programs. Inter-generational development is a SACMI hallmark. Hence the ‘Train the trainers’ program, which has led to the certification of over 160 internal trainers Involving several companies in the Network, this ensures the skills and the motivation of experienced personnel are put to excellent use both in routine training and, above all, during onboarding.
Me@SACMI
Back in December 2021, ‘me@SACMI’ was launched: this is an internal digital platform where workers can see which training courses are available (recommended on the basis of skills specific or complementary to their job) and sign up to them. This platform can also be used to rate the courses attended, providing useful feedback for other colleagues. At the start of 2023 a new questionnaire was published to identify the training priorities of the various departments.
Performance management
In 2023, managers and other members of personnel completed their performance management training (a system to assess corporate performance and ensure it aligns with the organization's goals). Participants received a total of over 960 training hours. This approach, which focuses on knowing both how to be and not just how to do is consistent with the governance-level ‘leadership and listening’ model and aims to introduce a culture of feedback, inclusion and performance.
For the majority of Italian subsidiaries 5, 100% of the workforce received regular performance appraisals and 78% received careers development and skills training.
The Performance Management system has been adopted in the Group's foreign companies located in Germany and Spain. Digital implementation of the Performance Management tool is expected for 2024.
“Leading by values”
Designed together with the Bologna Business School, this 3-module course (each module is 20 hours) was aimed at members of the organization who have team coordination and leadership roles. No less than 179 people attended the course, subsequently going through a follow-up process to test the effectiveness and the margins for improvement of the collaborative model. As the name implies, ‘Leading by Values’ looked beyond the attainment of goals: it also placed emphasis on the methods - which need to be compatible with SACMI’s principles and values - used to achieve them. It focused, in equal measure, on the technical organizational and behavioral (collaborative logic inter-sector and inter-company) skills needed to implement growth strategies and, therefore, define interdisciplinary training programs according to a model that is cohesive and uniform throughout all SACMI Group companies.
Project management
In 2023 the SACMI Academy pressed ahead with implementation of the ‘project management’ module, coordinated by the PMO (project management office) and co-produced with Turin Polytechnic
5 The information contained in this paragraph does not include BMR S.p.A.
This aims to deliver homogeneous intergroup management of orders and relative issues by delivering in-the-field solutions. A further aim of the module is to broaden the target for the Academy's programs, which will, in future, be open to both SACMI stakeholders and customers.
Goals for 2024 include internalizing basic project management training skills, with continuation of the partnership with the Polytechnic of Turin on advanced training.
Digital & IoT Academy
In keeping with the line taken in 2021, the Academy continues to focus on enhancing in- company use of tools that streamline the digital transition
This means training in key aspects such as collaborative co-working. However, it also means instilling a far-reaching, interdisciplinary ‘digital mindset’ that aligns with the organization’s goals. Initiatives in 2023 included implementation of a unified system for managing attendance, vacations, travel, expense reimbursements (from 1 January 2024 for employees of SACMI Imola, SACMI Service and Protesa).
Digital Business Modeling
A ‘Digital Business Modeling’ training course has been activated: this alternates methodological theory with practical workshops, the aim being to generate new service business models with the support of digital technology. Ultimately, the goal is to boost competitiveness and margins in the service market.
To date, all senior levels have been involved (a total of 46 participants), with the aim of extending the course to other company levels to develop widespread expertise on new models within each SACMI Business Unit.
Effective, collaborative communication
An ‘effective and collaborative communication’ course was activated in 2023. This module seeks to develop people’s ability to communicate and cooperate at all company levels. The course provides participants with models and techniques designed to make them better listeners and questioners, enhance their ability to speak ‘the other person’s language’ and ensure clear discourse. The module also includes simulations and practical exercises. As of 2023, 196 people have been trained.
Schools and Universities
Training is the lifeblood that feeds the organization’s growth: with the Academy, SACMI extends such training to customers, the other companies in the SACMI network in Italy and worldwide, and to relations with universities and schools.
This approach - which seeks to make the most of ongoing partnerships between SACMI and the world of education/ training - also aims to attract new talent to fill key positions in the company, in keeping with the outlined needs, strategies and programs.
The Academy and its courses - provided to SACMI personnel on a continuous basis - also have a secondary ‘employer branding’ purpose (i.e. to make the company more appealing, especially as regards the new, strategically important STEM roles) to ensure the continued growth of the organization.
54 thesis projects in the company
2 PhDs (doctorate theses)
For 2023 the SACMI project portfolio consisted of: 142 TOTAL
59 courses for cross-sector skills and onboarding
1 research appointment 11 internships 15 partnerships with local high schools and degree courses
Remuneration policies
All SACMI employees receive support to promote their personal development and well-being. This takes the form of, for example, professional training and, in parallel, equal opportunities and pay without any form of discrimination.
Given this, the entire corporate organization, Senior Managers included, is involved in remuneration policy. The awarding of bonuses, defined by an internal Group policy, stems from individual performance in terms of achieving assigned goals. During 2023, all SACMI roles were assessed according to an international method. Roles were clustered into skill-specific bands and, for each band, a market positioning curve was drawn up to evaluate internal and external equity with respect to guaranteed pay (Total Guaranteed Compensation).
This methodology, linked to formalized performance assessment, assists managers in prioritizing and evaluating 2023 salary increases, in line with the remuneration model defined for each company. The entire process was made easier thanks to a dedicated IT tool that allows salary growth to be planned according to individual performance and market-related individual remuneration positioning.
The salary model and the remuneration policies connected to it have been approved by the highest decision-making bodies of each SACMI company. Moreover, they approve, on a year-by-year basis, the remuneration budget, in keeping with the company's economic and financial plan.
Integrated Annual Report 2023 / Social performance / Our people
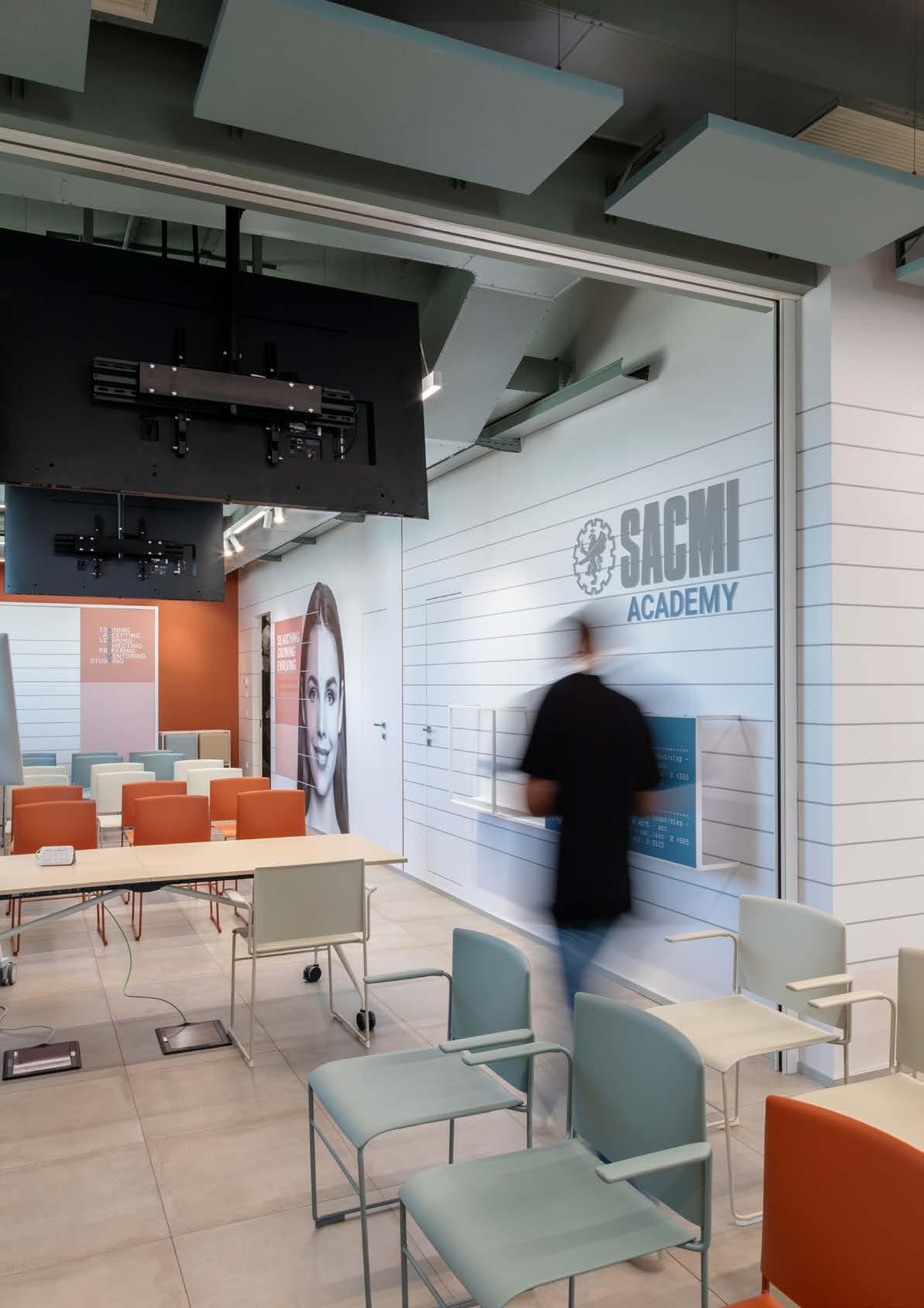
Company Welfare
All the Italian companies of the SACMI Group provide specific welfare services to their employees.
Supplementary health care
Every SACMI employee and his/her family members who are dependents are covered, free of charge, by a supplementary health care policy, the cost of which is met in full by the company. Employees also have the option of extending coverage to family members who are not financially dependent.
Pension fund
All employees have the right to join a supplementary pension fund to which company-paid contributions are added.
Other benefits
By early 2020, the SACMI Group was already extending contract-regulated ‘smart working’ to provide a better work-life balance for all employees.
The SACMI Group, foreign subsidiaries included, is committed to providing welfare services that match both workers’ needs and the specific geographical context. By way of example, in European subsidiaries health insurance, pension plans and flexi-time hours etc. are offered where applicable.
Integrated Annual Report 2023 / Social performance / Our people
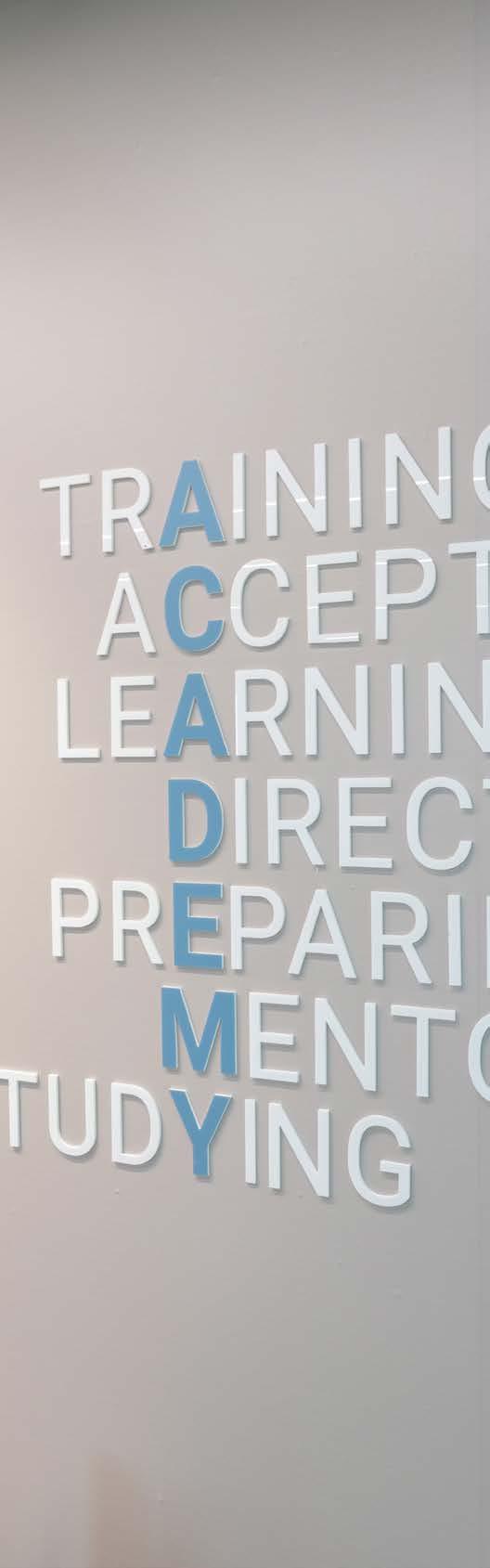
Internal commissions in SACMI Imola
SACMI personnel enjoy a strong sense of belonging to the company. This takes the form of a series of employee-organized recreational, cultural and charity initiatives, involving the organization’s members and personnel in a wide range of activities.
In 2022, reorganization of the SACMI Imola internal commissions was completed and new delegates for the period 2023-2025 were duly elected. The Board of Directors can assign the SACMI Imola internal commissions tasks pertaining to their sphere. To fulfil its role, the Commissions coordinate with other corporate departments or personnel and are made up of and elected by Cooperative Members only.
Cultural, Recreational and Publishing Commission (C.C.R.S.).
Founded in 1968 on the initiative of members and employees, the Circolo Culturale Ricreativo SACMI (SACMI Cultural and Recreational Club) was set up to promote cultural and leisure activities and, simultaneously, strengthen the sense of belonging to the Cooperative. The SACMI CCR experience is similar to that of various Cooperative Clubs established in Imola as part of the cooperative movement. Given the considerable involvement of local people and authorities, such experiences have often enhanced the town's civil and cultural heritage.
Over the years, cultural and recreational activities have given rise to self-organized acts of charity leading to continuous support for international missions, especially in Brazil, Ethiopia and Bolivia (getting people into employment, organizing long-distance adoption schemes and various local community support programs).
As part of the new framework for the three-year period 2023-25, the C.C.R.S. will also oversee activities previously carried out by the Press Commission, namely publication of La Ruota, the official house organ, which explores company issues and disseminates the values to which SACMI
adheres. La Ruota provides updates on results achieved, technological innovations, new products, and publishes news concerning personnel or ancillary industries.
Cooperative Shareholders’ and Training Commission
For the three-year period 2023-2025, a ‘Cooperative Social and Training Commission’ has been established: this covers the activities previously performed by the former ‘Training and Social Commissions’. Its aim is to:
• promote initiatives that ensure the strengthening and continuity of cooperation principles among all employees, thus promoting greater awareness of cooperative identity and a deeper understanding of the company.
• promote training for Members and Employees.
• promote events to raise awareness of the company and the Group an area of considerable importance as it reaches beyond any specific job, department or business to which the individual employee belongs.
In 2023, three particularly significant training events were organized in parallel with strategic customer-focused promotion of SACMI technologies. The first two initiatives took place during Tiles Open Week. They involved two days of visits, one to the Imola Lab, the other to the Sassuolo district: the latter took participants on a tour of SACMI Forni (new hydrogen production/storage station and hydrogen-fueled kiln prototype), SACMI Digital Lab (digital decoration) and BMR (ceramic product finishing machines), which came under full SACMI ownership in 2023.
The Rigid Packaging BU’s international Green&Digital’ event, instead, offered a valuable opportunity to provide participants with an in-depth understanding of the scenarios that are driving this industry towards ever-greater sustainability and process digitalization. The event also illustrated the technological innovation that SACMI delivers to customers worldwide. The event included a presentation in the Auditorium 1919, then a visit to the production departments to observe the CCM in action; the latest vision systems, the first to incorporate AI solutions on the Group's machines, were also illustrated.
As per its mandate, 2023 also saw the Commission participate in meetings with the Board of Directors to discuss various issues of social interest and take part in local events promoted by Legacoop.
Our people
Health and safety
The SACMI Group sees workplace health and safety as much more than a matter of compliance with the letter of the law: it is not simply a regulatory aspect but, rather, an intrinsic, deeply-rooted part of our corporate culture..
Quality, Safety and Sustainability Policy
SACMI is well aware that quality, safety and environmental sustainability represent more than founding principles: they also provide major competitive advantages. Accordingly, the Board of Directors of the SACMI Imola parent company has approved the Group quality-safety-sustainability policy . More specifically, SACMI is committed to continuous improvement of workplace health and safety, transforming its culture of social responsibility into an untiring quest for optimal worker-focused solutions.
Commitment to employees’ health and safety is ongoing. This ensures all tasks are performed in a secure environment, in full compliance with internal and regulatory prevention-protection standards.
Culture of Safety: approach and tools
Group companies seek to spread a culture of safety at every organizational level, encouraging responsible behavior among all those involved, directly or indirectly, in production processes. Their full commitment to preventing and mitigating any impact on health and safety at work involves the following approach:
• Compliance with laws and regulations in each country where the Group does business and compliance with the relevant workplace health and safety standards. To ensure such compliance most Group companies have established workplace health and safety committees made up of management representatives, worker representatives and various designated supervisors.
• Workplace health and safety risk assessment for all tasks relating to production, the provision of services and tasks performed by suppliers, contractors and partners.
• Involvement/teamwork with workers - and suppliers, contractors and partners - to encourage a shared commitment to workplace health and safety so that all relative parties exchange information, address issues and implement joint initiatives to prevent and mitigate risk.
• Constant information/training for their own workers and those of suppliers and contractors on workplace health and safety practices in order to prevent danger, implement safe working procedures and disseminate a culture of safety.
• Continuous improvement through monitoring of all health- and safety-related practices, assessment of the effectiveness of implemented risk mitigation measures and the taking of appropriate corrective action as required.
SACMI Imola, SACMI Carpmec and Velomat have a certified Health and Safety Management System as per ISO 45001 this guarantees efficient, effective management of aspects related to health and safety in the workplace. Such certifications are renewed and updated annually.
All SACMI Group Italian companies comply with Italian D.Lgs. 81/2008 and organize one or more team meetings a year; these are attended by management, the company’s safety delegates, the company Prevention and Protection Service, the company doctor and the Workers' Safety Representatives.
With regard to Health Monitoring management, at Italian Corporate level the Group Coordinating Doctor ’ project has been active since 2022. This aims to fully coordinate the health surveillance of Italian subsidiaries by appointing a sole Group ‘coordinating doctor’ to define shared working methods and standardize the health monitoring of all workers; this project will be completed in 2024.
Moreover, with regard to the parent company SACMI Imola, applying the principle of internal mutuality means that the cooperative has, for many years, provided - in addition to legally required medical check-ups - specialist check-ups for those aged over 40. These benefits are extended to over-40s every two years, whatever their role, and to retired SACMI Imola employees.
Risk assessment
SACMI is involved in several different types of manufacturing. Since the company consists of different Businesses, production-related risks vary considerably from one to another. More specifically, the main production-related risks are found inside the plant (e.g. lifting heavy objects/ materials with mechanical equipment, manual assembly tasks on machines or equipment, using machine tools, internal walkways and layouts, etc.) or outside it (e.g. installation construction sites at customer factories).
Assessment of workplace health and safety hazards/risks and the relative measures for their elimination is contained in the Risk Assessment Documents ( RAD ): these are specific to each SACMI Group site and are updated in compliance with the law.
100% of the SACMI Group's operational offices are covered by assessment of risks to employees’ health and safety.
Attention to safety is not limited to SACMI employees but extends to all those who work in or visit the company's offices, factories and construction sites on a daily basis; SACMI Prevention and Protection Service managers routinely monitor the technical/professional requisites of workers engaged under contract or sub-contract in compliance with the relevant laws and standards. In this regard, some Italian companies of the Group have set up a dedicated internet portal, managed by qualified professionals: this is designed to ensure suppliers are properly qualified by applying standardized safety-related parameters. It also ensures a continuous sharing of information on technical and professional requirements and allows supervision of any detected non-conformities.
SACMI Imola has also implemented an access control system to ensure the authorization status of all visiting suppliers complies with safety regulations. The company also has a ‘Safety Room’ that provides all visitors with the PPE (Personal Protective Equipment) needed to access production departments.
Prevention and Protection Service
Over the years the SACMI Group Prevention and Protection Service has engaged in multiple projects.
In particular, recent years have seen some Group companies develop a deeper understanding of all aspects involving technology, health and safety. For example, auditing of manufacturing departments and installation sites - performed periodically by qualified personnel and company managers involved in workplace health and safety management - has ensured proper assessment of risks associated with the use of machines, systems, substances and products.
In general, a combination of auditing procedures ensures monitoring and reduction of all risk factors (e.g. use of electricity, mechanical dangers, workplace orderliness/cleanliness also via application of the 5S method, electromagnetic fields, the use of chemical substances, noise, emergency procedures, artificial optical radiation, vibration, manual load handling, explosive atmospheres, pressurized equipment, all lifting gear/tools/accessories etc.).
For Italian companies of the Group, 100% of the workforce is represented in formal joint health and safety committees that involve managers and workers.
HSE (Health, Safety, Environment) training and information
SACMI companies have implemented procedures that inform and train personnel on workplace health and safety matters in compliance with the relative standards and/or laws. This has always been a major commitment, both in terms of hours allocated and employees involved; the company Prevention and Protection system directorate periodically verifies mandatory and non-mandatory training needs and organizes periodic meetings to discuss topics deemed be a source of risk.
In 2021 a corporate body that deals with all the Italian subsidiaries was established to organize health, safety and environmental training.
This body is responsible for drawing up the C orporate Safety Training Plan which lists the compulsory training required within each company. It also organizes training events at Group level, in concert with individual company Occupational Health and Safety officers.
SACMI Group companies provided a total of over 22,200 health safety and environmental training hours in 2023, involving more than 3,170 workers
+30%
HSE (Health, Safety and Environment) training hours compared to 2022
In 2023 health, safety and environmental training involved:
• courses for new hires
+13% workers trained compared to 2022
• courses for company managers and other designated personnel in positions of responsibility
• general updating courses for all workers
• courses on proper use of PPE
• courses on how to use company equipment (aerial platforms, fork-lift trucks, bridge cranes, electrical risks etc.)
• courses on accessing enclosed spaces, management and transport of dangerous good, use of dangerous substances
• emergency team upgrade courses (fire-fighting, first aid, defibrillator use)
• training courses concerning use of equipment and company procedures
The language and terminology used in all training sessions is designed to be understandable to all workers. Comprehension is assessed via a test and satisfaction measured by way of a questionnaire.
SACMI companies have opened multiple communication channels with all employees to ensure continuous improvements to workplace health and safety. SACMI aims to disseminate an inclusive culture of safety to which everyone can rightfully and responsibly make an active contribution. This goal is being pursued in all Group companies via meetings that involve all personnel from all departments, third parties included. The process includes:
• periodic audits or meetings to share company performance information for each corporate area
• periodic teamwork with the various company managers (in addition to meetings required by law)
• IT applications to gather reports on any critical situations (near misses, unsafe situations) or environmental issues
• periodic training courses (also beyond legal requirements)
• regular newsletters
• an intranet with a space dedicated to safety, environment and sustainability information
• use of check lists to verify safety devices on equipment and machines used by workers in manufacturing
Integrated Annual Report 2023 / Social performance / Our people
In 2023 the key Health and Safety investments concerned:
• installation of new systems to extract and process pollutants (including the commissioning of a post-combustor) in new production facilities
• redefinition of new production layouts
• renewal of fire detection systems
• seismic risk-related improvements to buildings
• investment in preventive safety checks on factory machines
Tavolo 81 Imola Association
The Associazione Tavolo 81 Imola promotes a culture of workplace health and safety in the Imola area. It was founded in 1999. Every year it organizes seminars, conferences and events on topical health and safety issues, illustrating how to put improvements into practice. It also organizes training in schools in and around Imola. SACMI actively supports the Association, after having held its presidency for 5 years up to July 2021 on behalf of Legacoop Imola.
During 2023 the Association organized some training meetings that involved various stakeholders (clients, suppliers, partners, supervisory bodies, consultants, trade associations). Their purpose was to analyze legislative changes, assess their ramifications, look at the requisite implementation methods and examine any problem areas. Specifically, three meetings were held on the following topics:
• chemical and carcinogenic risks (hosted at the SACMI Imola headquarters)
• extreme weather events and emergency management
• safety, inclusion and well-being.
Furthermore, SACMI Imola (through Legacoop Imola) nominates a person to sit on the board of Più Sicurezza Srl, a company that provides a wide range of safety-related worker training courses at a modern facility: the latter offers the settings, machines and equipment needed to simulate the main scenarios in various manufacturing industries.
Near-misses and accidents
Several years ago, as part of ongoing improvements, SACMI created an app that lets employees independently report any near misses ’ or unsafe actions they may have witnessed. Reports are converted into an anonymous format before being investigated.
Work-related accidents - Employees6
Recorded work-related accidents
Number of hours worked7
Number of days lost due to recorded work-related accidents
Work-related accident rate
(Number of accidents/hours worked *1,000,000)
Seriousness of recorded work-related accidents Days lost due to accident/hours worked *1000)
In 2023, 53 workplace accidents involving SACMI Group employees were recorded, with no fatalities. The accidents registered in 2023 mainly involved cuts, bruises and burns to the upper and lower limbs and foreign objects in workers’ eyes. During 2023, no workplace accidents with serious consequences were reported in any of the SACMI Group companies.
Workers travelling abroad: 24/7 assistance
SACMI is meticulously attentive to the safety of its personnel traveling abroad workers operating abroad are informed of any risks in the country where they will be working and can access an information and support service to resolve any medical or security issues that might arise overseas. The service is provided by a specialized company that updates information in real time and responds 24/7 to requests for assistance worldwide. A centralized travel booking system allows for the management of specific information for each destination and person.
6 The data for 2021 and 2022 shown in the table does not include the following companies: BMR S.p.A. and SACMI Engineering Private Limited (India).
7 Data on hours worked for LAEIS GmbH (Luxemburg) is an estimate.
Integrated Annual Report 2023 / Social performance / Our people
A further cooperative-specific feature is the application of basic democratic principles. These allow members to play a role in the decision-making process and take part in the Assembly and the election of the Board of Directors.
During 2023 six assemblies were held, with average attendance running at 88.16%. In 2023 the corporate capital of the parent company amounted to 38.1 million euro.
Cooperative membership
The distinguishing element of the cooperative firm - the principle of mutuality (also known as the principle of cooperation) - lies in the economic relationship members have with the Cooperative and their role in its democratic bodies.
SACMI Imola membership levels were in line with those of previous years. Twelve workers became members in 2023 (against 10 losses: 9 retirees and a death); they were selected on the basis of requisites such as a minimum of 5 years’ service, moral and professional qualities such as dedication and cooperative spirit, dynamism and professionalism. In compliance with Italian law 142/2001 concerning worker-members, profit shares are issued as per legal requirements and may take various forms such as an increase in the value of share capital (as a form of capitalization and therefore self-financing for the company) and wage bonuses.
Another key feature of the relationship between Cooperative and Member is the membership loan . This tool, which lets members invest in their own work and finance the activities of the cooperative, is managed according to rules drawn up by the Members’ Assembly. Compared to the previous year, its value increased by about 300,000 euro.
Members are selected on the basis of certain requisites such as the number of years service, moral qualities, dynamism and professionalism
Total corporate capital (euro) Total membership loans (euro)
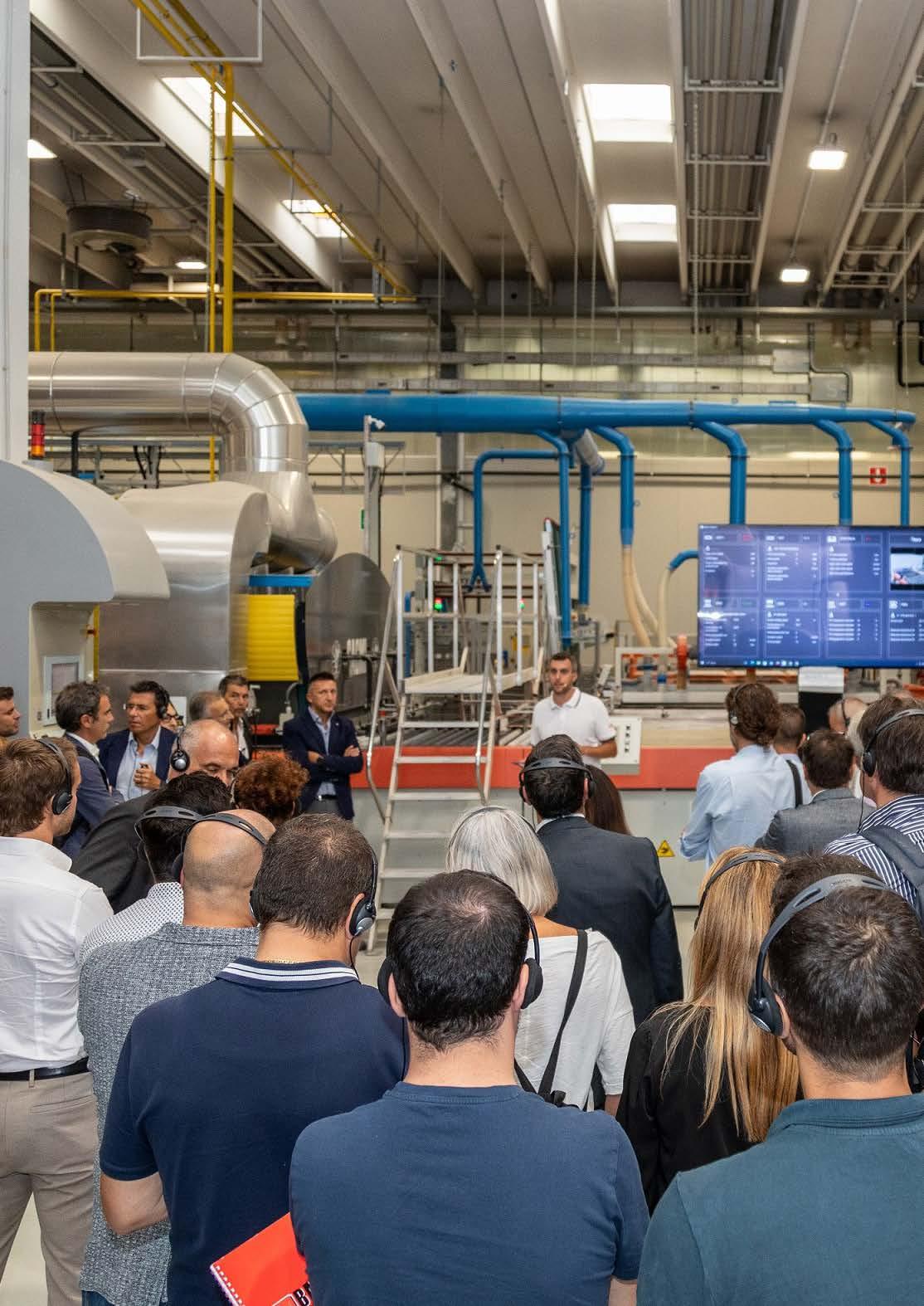
Customers
SACMI pursues technological and market leadership in all the sectors where it does business by focusing on design skills and seeking out innovative solutions. The ability to engage not simply as a supplier but as a solutions-focused consultant - from ‘project concept’ to technological construction of the plant and its correct installation, start-up and running - is a SACMI hallmark that forms the basis of mutually rewarding long-term relationships with customers.
The SACMI Group earns revenues in all areas of the world , with the exception of Oceania. Some 84% of SACMI's business is done with foreign customers. SACMI generates a little over 16% of its revenues in Italy, where the Parent Company is based, mainly through the sale of Tile machines and plants (which accounts for more than 70%); analogously, the Whiteware business also has large sales volumes on the Italian market.
In the Rigid Packaging business, 97% of revenues come from exports, with significant volumes in emerging areas such as Africa. The Packaging & Chocolate business achieves a significant portion of its sales in Europe and the Americas (approximately 60%).
Customers differ considerably in terms of structure, size and assets. Moreover, the different business areas typically have different customer types.
SACMI bases its customer relations on a continuous quest for excellence and constant quality assurance.
Digital and on-site assistance services were further strengthened in 2023 6.3
Partners in development
Customer relations are built on a continuous quest for excellence and ceaseless quality control: this is why SACMI periodically monitors, directly and indirectly, customer satisfaction, the aim being to amass all those elements that might be useful for improving goods and services.
SACMI bases customer relations on the partnership principle which aims to:
• ensure the effectiveness of control systems throughout the production process
• provide consultancy and training on proper plant use
• involve customers at the product design stage.
After-sales service is a salient part of SACMI policy. Strengthened customer relations are a must to ensure maximum service efficiency and reliability.
In the process control sphere, SACMI offers services designed to implement a new machine/ plant maintenance logic: this takes the form of scheduled maintenance plans, ongoing monitoring of ‘plant health’ and the provision of ‘preventive’ spare parts kits. These aim to provide customer support by optimizing control and efficiency of SACMI machines/plants over time; the goal is to prevent problems before they can actually occur and protect the customer’s investment
For example, in recent years new Smart & Secure Service assistance plans have been launched all over the world. Moreover, new functions have been incorporated into the SACMI assistance portal S.P.A.C.E. (SACMI Portal for After-sales and Customer service Excellence): in 2022 the latter was complemented by the introduction of the SPACE UP App that customers can use to request assistance via the QR code applied on the machines.
Revamping services are increasingly important. Specific kits help customers boost the efficiency of existing SACMI machines and plants in terms of both production performance and consumption.
To broaden its consultancy role with customers, SACMI continuously proposes initiatives aimed at encouraging training and disseminating industry-specific technical expertise. For example, updated versions of the company’s own Tiles, Sanitaryware and Tableware technology books were recently published.
SACMI also promotes events at its Network offices to keep customers informed on the latest technological developments and new services; it also regularly takes part in the main international trade conferences. In 2023, several events saw the direct involvement of SACMI offices around the world. For example, SACMI do Brasil organized two seminars in Rio Claro and Criciúma, attracting 90 representatives from Brazil’s leading ceramic customers. SACMI also took part in nu-
SACMI Smart & Secure service
S.P.A.C.E. and SPACE UP
enhancement
New revamping kits for existing machines and plants
merous international conferences in the Sanitaryware-Automation, Rigid Packaging fields etc.
Customer health and safety
daily task. This service has allowed the SACMI Group to significantly improve construction site safety in recent years.
In parallel with checks on documentation, a further service sees site safety technicians inspect the work done by suppliers who operate on customers’ sites on the Group’s behalf. Both services use software that allows data exchange between SACMI Group technicians, suppliers and customers. To oversee construction site safety properly, some Group companies have implemented best practices, such as the drafting of coordination reports or periodic internal meetings.
To safeguard customer health and safety, the SACMI Group takes all necessary measures to guarantee outstanding product safety. The Group applies internal procedures that ensure safe design and detect any deviation from mandatory standards. Such procedures guarantee that all machines and equipment comply with the EU Product Directive; compliance checks are also extended to the sale of machines provided by third-party suppliers. Furthermore, to ensure installation work is performed safely on construction sites, in 2018 the SACMI Group set up a service that checks suppliers’ documentation before they enter installation areas. The main purpose of the service is to encourage continuous dialogue with suppliers and customers in order to nurture a culture of safety and ensure it permeates every Integrated Annual Report 2023 / Social performance / Customers
SACMI Group companies did not find any cases of non-compliance with standards concerning the health and safety impact of their products. Any non-conformities revealed during inspection of on-site installation services are periodically reassessed and analyzed.
To take any reported operational non-conformities into account, a new KPI for evaluating suppliers is being implemented.
Involvement in local communities
SACMI extends its cooperation principle into the wider world where it supports numerous projects in Italy and beyond. This ongoing support is in keeping with its core values. Over the last 3 years, SACMI has allocated 1.9 million euro to local and international charity projects, mainly in health , assistance and education . This amount includes both resources pertaining to the income statement and disbursements from the SACMI Imola parent company cooperative fund for institutions/projects approved at the time of allocating profits from previous years.
Helping to provide training and personal care services in those parts of the world where SACMI operates is a key part of community service, as are initiatives to support art, culture and sport.
Deciding which projects to adhere to in a given year depends on the actual needs of communities, identified by listening carefully to local people and the main charity associations that work there.
SACMI Imola (Italy)
Projects are selected by listening to the needs of communities and the associations that operate within them. In 2023, the focus was again on support for training, assistance and personal care services, yet also culture and sports
The donation of a next-gen electrosurgical unit to the Gastroenterology department of Imola Hospital, already approved during Christmas 2022, was also completed.
Other disbursements were made during the year, in continuity with past ones. Many were made to associations that provide local health, disability care and other services for those in need: these include the ANT Foundation (free home care for cancer patients), LILT (Italian league for the fight against cancer), the Cystic Fibrosis Research Foundation charity, Professione Medica (health training and education in schools) and Anteas Imola (services for disabled persons lacking in self-sufficiency).
Health - above all, in the sense of personal dignity - remained the focus of initiatives to sustain various local associations: these included donations to the Fondazione Banco Alimentare Emilia-Romagna Onlus (food bank), Associazione No Sprechi Onlus (free meals for persons facing hardship), plus donations to the Diocese of Imola, Intercultura ODV and Associazione Noi Giovani). At international level, SACMI continues to support the São Bernardo Onlus Committee (which has missions in Brazil and Senegal), a project that has been the hallmark of Imola’s solidarity with the rest of the world for 35 years.
On the education and training fronts, 2023 saw SACMI finalize donations to the University of Bologna in support of local degree courses, specifically the course on Chemistry and Technologies for the Environment and for Materials (Faenza campus) and the Mechatronics course (Imola site). Research doctorates also received funding on the basis of a framework agreement with Unibo. These initiatives stand alongside ongoing projects SACMI has established with universities, schools and research centers in strategic areas of the Business.
Also in 2023, significant contributions were made to Imola’s main sporting associations and local cultural organizations and events (e.g. sponsorship of the diversity and inclusion event ‘WOWWomen Motor’ at the Imola Racetrack, the Imola in Musica festival, the Winter Emilia-Romagna Festival program at the Stignani Theatre, the Municipality of Imola for its staging of the exhibition ‘Architecture in Imola in the second half of the 20th century’ at the International Ceramics Museum – MIC of Faenza as part of the Italian government’s ArtBonus initiative).
SACMI also contributed to the Flood Solidarity Fund, following the natural disasters that impacted the Emilia-Romagna region in May 2023.
SACMI Group - Support provided to local, national and international community by sector (euro)
The parent company’s main initiatives in 2023 included a donation for the Casa Gialla facility run by Bologna-based association Ageop Ricerca which has been at the forefront of pediatric oncological research, treatment and support for over 40 years. Based at the Sant'Orsola Polyclinic in Bologna, Ageop offers free accommodation at 4 facilities located outside the hospital, allowing young patients and their families to face the long rehabilitation process. These include ‘Casa Gialla’, purchased and modernized by Ageop in 2015. SACMI's donation will help the association pay off the mortgage on the property and thus ensure continuity of this essential service, which constitutes a true ‘extension’ of the hospital care that supports the children and their families.
Integrated Annual Report 2023 / Social performance / Involvement in local
Riedhammer (Germany)
The three focal points of Riedhammer's work for the local community are sport, training and networking. For more than 30 years the company has managed the Riedhammer Sport und Kulturförderung e.V. association, which promotes sport and culture, streamlines access to sports facilities/equipment and sustains cultural events. Furthermore, Riedhammer works alongside International Co-operative Studies e.V. , a non-profit association that supports high-quality training by promoting a special course with a sharp practical focus. The latter reflects the Riedhammer way of doing things: it also acts as a hive for new talents who are then taken on by the company.
The company is also part of Stifterverband , a joint networking initiative launched in Germany by companies and foundations that focuses on consultancy, networking and making improvements in education, science and innovation.
SACMI Iberica (Spain)
SACMI Iberica operates extensively in the field, mainly through its support of healthcare and education charities.
In 2023, donations were made to Caritas , to the Spanish Association for the fight against cancer, and the Castellón Down syndrome research foundation. All training-related funding went entirely to the EDEM Business School and, on the sports side, to the Club Sportivo Villareal foundation.
SACMI Engineering (India)
The success of last year’s Blood donation camp was repeated in 2023 with a second edition: this directly involved employees from the three SACMI offices in India (Mumbai, Ahmedabad-Sanand and Morbi). No less than 76 employees responded to the appeal; their combined donation of tens of liters of plasma was then delivered to local healthcare facilities. This project is particularly relevant in India as many of its 1.4 billion inhabitants still have difficulties accessing healthcare.
The ‘Blood donation camp’ is one of a series of charity projects promoted by SACMI Engineering, most of which focus on health and education : beneficiaries include the Smile Foundation, Swastik Foundation and the Vrudha & Matimand Seva Trust.
- sacmi.com
SACMI Impianti (Italy)
Initiatives in favor of non-profit organizations primarily concern health . However, there is also vigorous promotion of culture and sports especially for younger people. A good example is the company’s sponsorship of Sassuolo Calcio, which embodies the links between the local economy, industry, sports and the pursuit of excellence. SACMI Impianti thus provides the Sassuolo area with tangible support, enhancing the company’s sense of belonging to a community that delivers excellent growth prospects via the efforts of the many people who live and work there.
Health/social initiatives include donations to the ANT Foundation, Emilia Flood Fund, Amici per la Vita Ospice and APRO. The company also participated in charity events in favor of the Nuovi Orizzonti Association and Italian Red Cross held at the Florim Gallery.
SACMI Forni & Filters (Italy)
With SACMI Forni & Filters, donations again mainly concern the health and social sectors. Much of the support lent stems from the awareness-raising efforts of those employees who are actively involved with local associations . Noteworthy actions include the support lent further afield, such as the help given to flood-affected populations (2023) and aid for those impacted by the conflict in Ukraine (2022).
SACMI Packaging & Chocolate (Italy)
The company enjoys long-standing relationships with universities and professional training schools. These are strategically important as they provide access to fresh talent for the future development of the Business and help us support research; such relationships also generate new contacts and increase the company’s appeal as an employer. Internships for secondary school students also play a key role in this cooperation.
Moving on to healthcare, 2023 saw SACMI Packaging & Chocolate adhere to - through sponsorship - the ‘Free Mammography and Ultrasound’ public health initiative : female colleagues from the Alba facility aged between 35 and 45 were invited to participate.
SACMI Verona (Italy)
Key activities included a donation to the municipality of Mozzecane (VR) for the purchase of a van equipped to transport disabled persons.
Integrated Annual Report 2023 / Social performance / Involvement in local communities
In 2023, SACMI Imola’s Auditorium 1919 hosted 60 events . Their scope was broad, covering internal training, the promotion of topics/projects for the local community, and meetings with stakeholders and the SACMI associative network.
Whether used for internal training/communication or events open to customers and the public, the Auditorium continues to operate in mixed mode making it ideal for both in-person discussions and online access to events, thus boosting the potential audience while delivering advantages from a sustainability perspective.
Key learning moments included the Train The Trainers and Leadership Talks courses. Events open to the general public included the keynote lecture by Lucio Caracciolo geopolitical expert, journalist and director of Limes: this talk - the final event of the geopolitics course run by Università Aperta Imola held on 7 June 2023 - drew an audience of over 400 people, with a further 120 connected to the live stream.
It should also be noted that the year included events to involve employees in SACMI’s sustainability strategy: these were designed to take into account the profound changes of recent years and prepare the ground for further regulatory changes. In October, for example, the Sustainability in the Company - Measurement and Communication event involved 500 employees (200 in person, 300 online).
In terms of opportunities to meet customers, the pivotal event of 2023 was Green&Digital , which saw the Auditorium host over 250 customers from 61 countries. An innovative presentation method saw live connections alternate between the hall and the SACMI workshop. Thanks also to the participation of several international experts, the event proved to be a truly global networking event, making it highly popular with participants and offering a valuable opportunity to discuss sustainability and digitalization in Rigid Packaging.
Auditorium 1919 also continues to be a key venue for events concerning SACMI’s network of associations with universities, research centers and businesses. For example, in January 2024 the hall hosted the General Members’ Assembly of ClustER-Mech , the Emilia-Romagna mechatronics and motor engineering association. In March, the now-traditional presentation of Vini Buoni d'Italia a guide published by the Italian Touring Club, was held there: during the event the best 703 wines produced from native vines were awarded their ‘Crowns’.
202
SACMI - sacmi.com
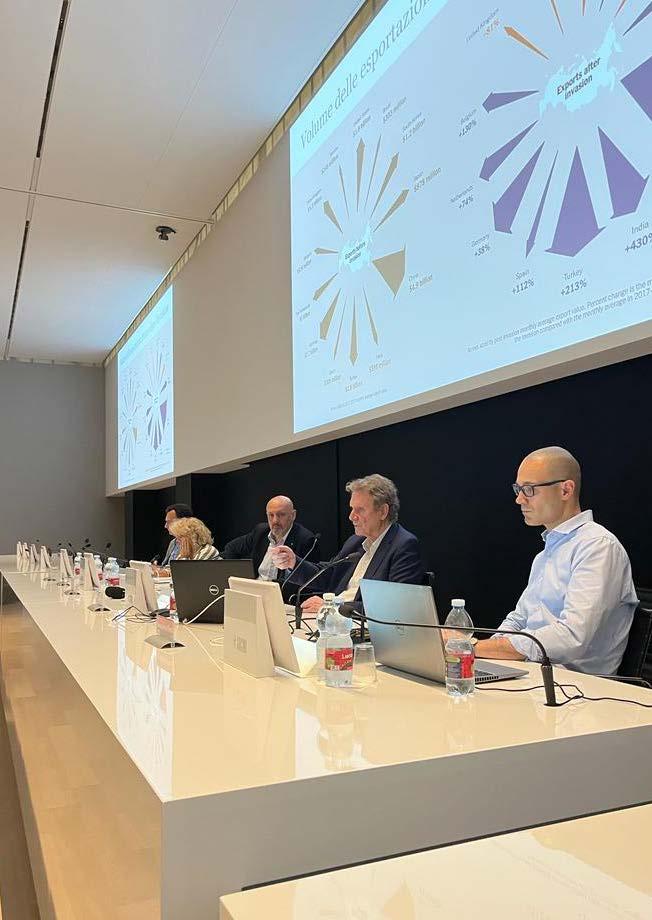
CHAPTER 7
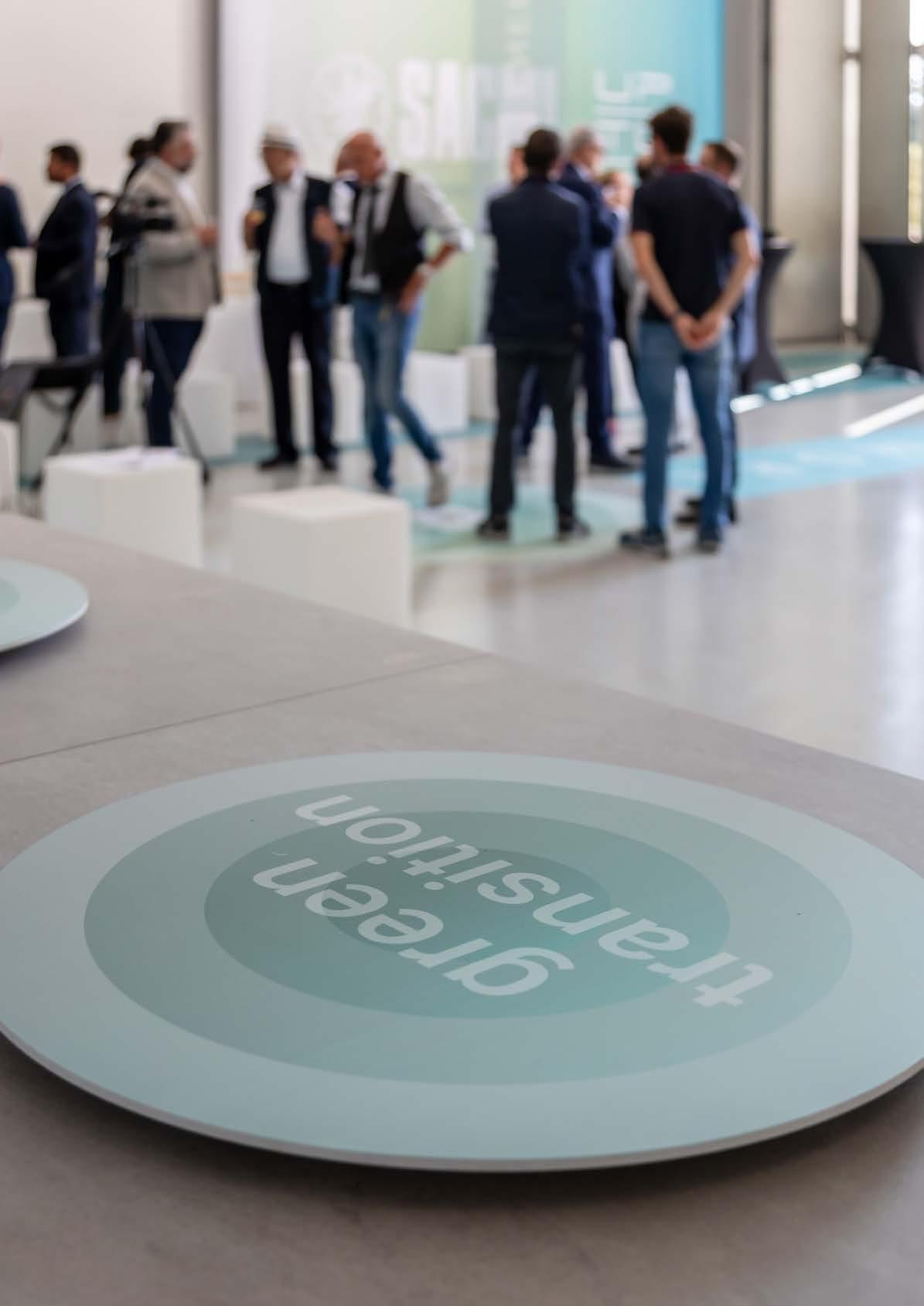
Environmental performance
SACMI sees environmental protection as an essential part of company strategy. Hence the implementation of highly environment-conscious processes and procedures, in compliance with laws and regulations, including those of a voluntary nature. The goal: progressive improvement via periodic analysis of work-related environmental risks and the planning of prevention and/or mitigation actions
No company within the reporting boundary reported any significant environment-related negative impact. The environmental impact of SACMI's manufacturing activities mainly stems from: atmospheric emissions, consumption of water and energy resources and waste production.
The Quality, Safety & Sustainability Policy, which makes sustainability one of the company's key competitiveness factors, was renewed in 2023
1 The information contained in this chapter does not include PET Projecta or SACMI Service BMR, having joined the SACMI Group in 2023, is included in all quantitative indicators (302-1, 303-3, 305-1, 305-2, 306-3, 306-4, 306-4, 306-5) for the year 2023 only.
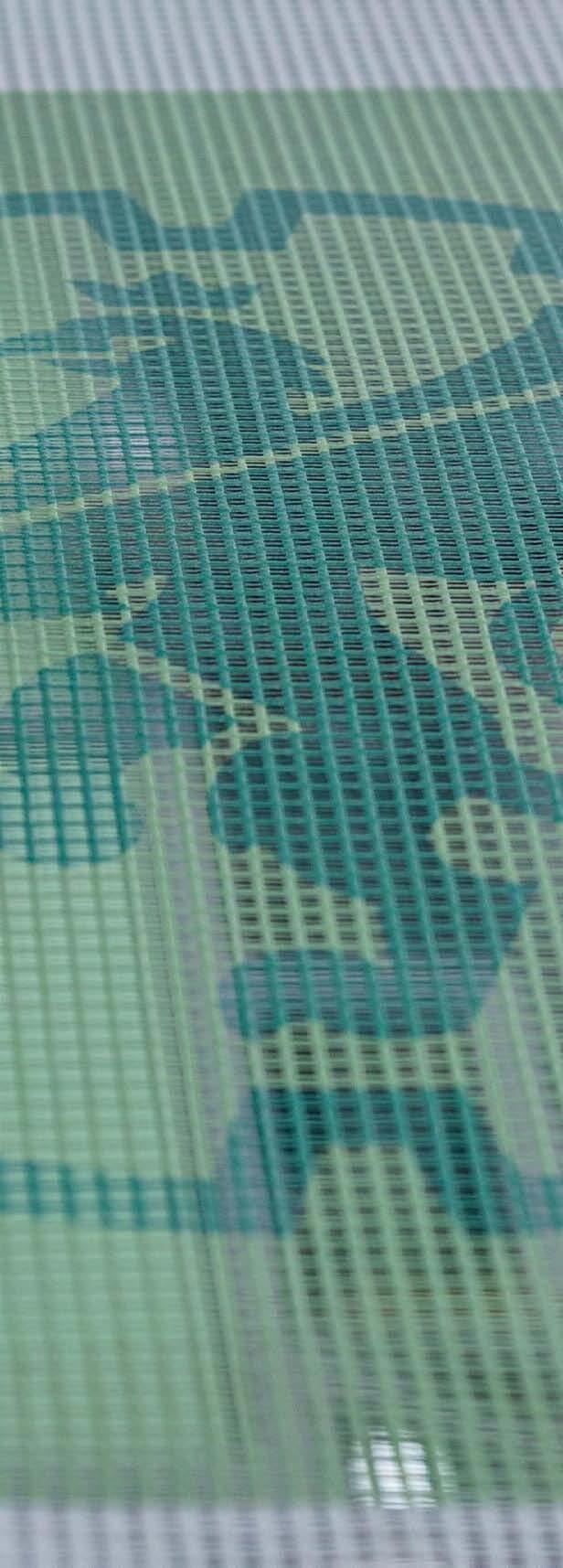
More specifically, the parent company SACMI Imola SC is committed to addressing the impact issue via its ISO 14001-compliant environmental management system and meets the requirements set out in the Autorizzazione Unica Ambientale (AUA, or Unified Environmental Authorization).
In December 2019, the Board of Directors published the Quality-Safety-Environment Policy making sustainability one of the company's key competitiveness factors (the policy was reviewed in July 2023). Note that SACMI is committed to the continuous improvement of all environmental safeguards and the implementation of production processes consistent with a circular economy.
Energy management
Energy is an essential component of all work done within the Group, from energy-intensive production processes to daily administrative duties. The importance of proper, efficient energy management was reconfirmed in 2023 by the materiality analysis³.
Energy and fuel consumption in 2023
Most of the energy used by the SACMI Group comes from the combustion of natural gas diesel and petrol. In 2023, this share was estimated to be approximately 67% of consumption. The remaining portion is represented almost exclusively by electricity purchased or self-produced
Over the two-year period, gas consumption was reduced by 20%.
The share of ‘green’ energy and self-produced electricity continues to grow
2 The information contained in this chapter does not include PET Projecta or SACMI Service Note that electricity consumption does not include SACMI Engineering Private Limited (India) or SACMI Machinery Foshan Nanhai CO. LTD. for the year 2023 only. Data on fuel and energy consumption does not include SACMI Engineering Private Limited (India) for the years 2022 and 2021.
3 See Chap. 1, Dialogue with stakeholders and materiality analysis.
For years now, the Group has encouraged individual subsidiaries to pursue initiatives that improve the energy efficiency of their processes and daily tasks in order to reduce consumption. In 2023, such initiatives included the replacement of light fittings with LED devices, the installation of solar energy systems and the replacement of obsolete boilers with high-efficiency models.
Energy and fuel consumption
In total, 316,401 Gj were consumed in 2023. This stemmed from the use of fuels, such as natural gas, diesel and petrol, and the consumption of electricity.
As the graph shows, the most-used fuel is natural gas, some of which is fed to the trigeneration plant installed in SACMI Imola in 2016. More specifically, the Group consumed a total of 4,889,510 standard cubic meters (177,050 Gj) of gas in 2023, approximately 48% of which was used for the trigeneration of 9,574,022 kWh (34,466 Gj) of electricity and 8,721,710 kWh thermal.
Electricity is produced by a gas-powered internal combustion engine. Some of the heat generated by the engine is recovered by drawing it from the exhaust fumes, the cooling water and the engine lubricating oil circuit. The high temperatures of the above make it possible to heat water to 95°C and feed it into the company's heating systems. Moreover, excess hot water is used to chill water to 7 °C (by means of an absorption unit). This chilled water is then fed into air conditioning systems.
4 Note that, in the graph, electricity consumed does not include the portion of electricity obtained from the trigeneration plant (34,466 Gj).
208
SACMI - sacmi.com
Comparison of data over the three-year period shows that overall energy/fuel consumption remains substantially unaltered compared to the previous year. In fact, greater use of electricity (+15%) was offset by less consumption of natural gas, down by 9% compared to the previous year and 20% compared to 2021. Fuel and
Considering the energy intensity - calculated by comparing total energy consumption and revenues - an overall decrease is observed: on the one hand energy consumption remains constant, on the other there is a significant increase in revenues. Total Integrated Annual Report 2023 / Environmental performance / Energy management
The remaining non-renewable fuels used were diesel for generators and petrol/diesel for the company vehicle fleet.
-9% natural gas consumption
(-20% compared to 2021)
Intensity of energy consumption
energy consumption (Gj)
Revenues (million €)5
intensity
Self-production of electricity (kWh)
Reduced “energy intensity”
Electricity accounts for approximately 33% of total consumption. In 2023 the SACMI Group consumed 38,808,342 kWh (139,710 Gj)6 a 9% increase compared to the previous year.
It should be noted that almost a third of all electricity consumed (31%) was self-produced by solar panel systems and the trigeneration plant, which in 2023 produced 1,903,887 kWh and 9,574,022 kWh respectively (see “Energy self-production” graph).
Electricity
in 2023
Notably, 2023 saw a significant increase in solar power production, largely thanks to the installation of a new photovoltaic system at the SACMI Imola site.
In 2023 approximately 3% of all self-produced electricity was fed into the grid and sold.
5 For more information on the scope of the data, see paragraph 4.1 Economic value generated and distributed.
Electricity self-produced with photovoltaic panels
6 Including electricity produced by the trigeneration plant. +10% electricity self-produced
Integrated Annual Report 2023 / Environmental performance / Energy management
The following graph compares electricity self-produced and electricity purchased over the threeyear period. Note that consumption of the latter increased a little in 2023 (+12% compared to 2022), while self-production of electricity rose 10% compared to the previous year.
(kWh)
While electricity self-production is substantial, a portion is nevertheless purchased from the market. In 2023, 25,078,894 kWh (90,284 Gj) were purchased, of which 836,700 kWh (3,012 Gj) were obtained from renewable sources with Guarantee of Origin7. Since 2021, the parent company SACMI Imola has been committed to purchasing a percentage of electricity produced exclusively from ‘green’ sources and aims to steadily raise that percentage over the coming years. Compliance with the set percentage of ‘green’ energy purchases is guaranteed directly by the service provider, who determines the quantity on the basis of the Organization’s effective energy consumption.
In 2023, the ‘green’ energy purchased by the Parent Company amounted to 8% of the total taken from the grid (800,000 kWh).
+3% ‘green’ energy
by Parent Company (reaching 8% of the total=800,000 kWh)
7 Guarantees of Origin (GO) are certificates issued by the Energy Services Manager (GSE); they attest to the renewable origin of the sources used to produce the electricity.
Diesel for company fleet
Petrol for company fleet
Total consumption of non-renewable fuels
Other types of energy purchased for consumption
Energy for district heating
Total consumption of electricity and purchased district heating
Self-generated electricity
Electricity self-produced with photovoltaic panels
Electricity self-produced with trigeneration plant
Electricity self-produced and sold
Total electricity self-produced Total electricity self-produced and sold Total
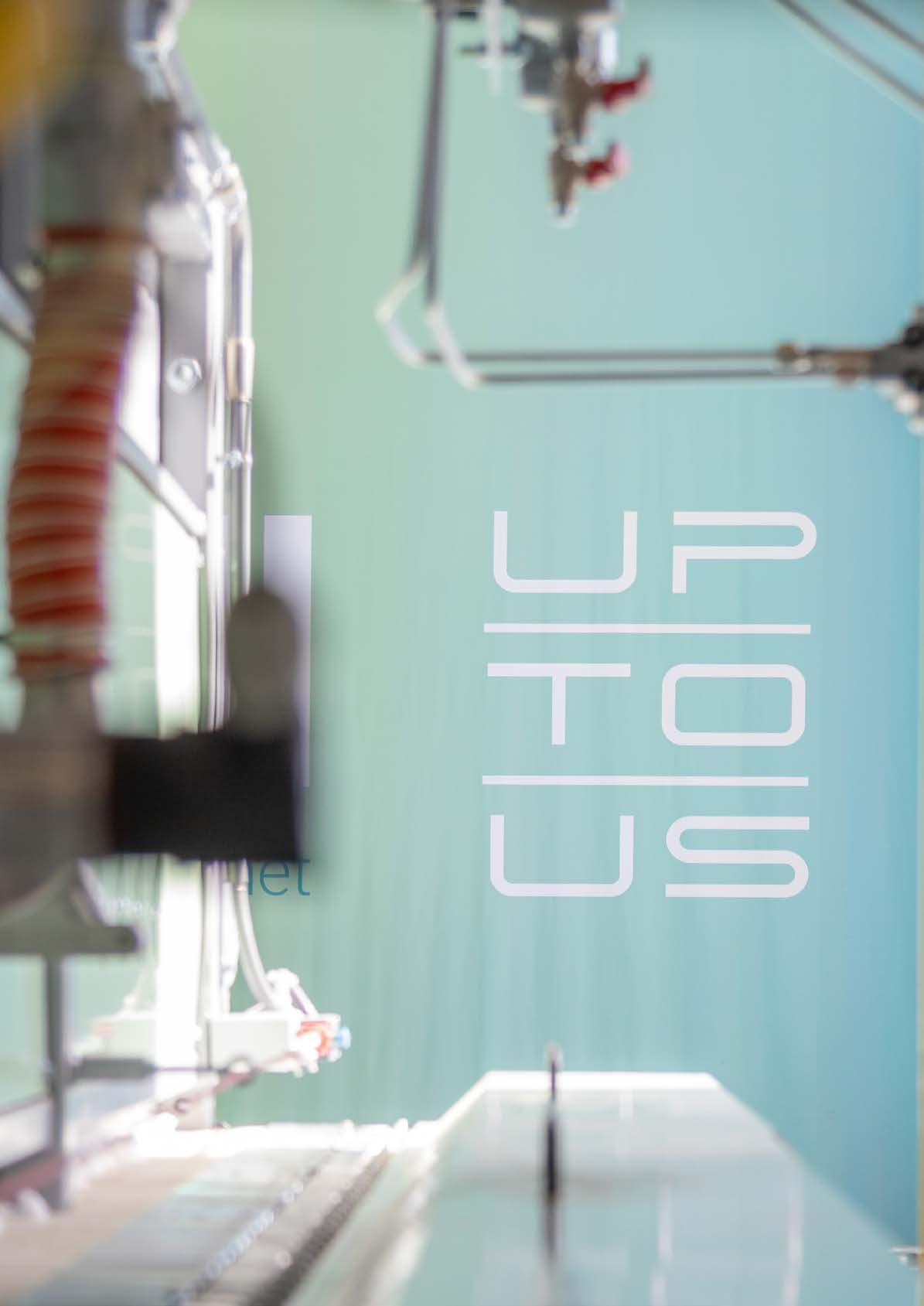
Energy management
Management of GHG emissions 8
The SACMI Group is devising a strategy to reduce its GHG (Greenhouse Gas ) emissions. This plan aims to act on various decarbonization levers such as energy efficiency and replacement of current energy sources with low- or zero-CO 2 emissions alternatives.
Following the example set by SACMI Imola, several Group companies plan to install photovoltaic systems so they can self-produce electricity in the coming years; in some cases energy is purchased from certified renewable sources9 . On the subject of fuel usage, the construction of an experimental plant for the production of hydrogen should be pointed out.
DECARBONIZATION INITIATIVES
SACMI Forni & Filters: hydrogen production station and experimental kiln
In 2023 a pilot/experimental plant was built at the SACMI Forni & Filters facility: this produces hydrogen by way of electrolysis and uses it as fuel in an experimental low-environmental-impact kiln.
Firing is an energy-intensive, technologically significant stage of the ceramic production cycle. On average its contribution to energy consumption can be estimated at at least 3,100 kJ/m² (more than 51% of overall consumption).
To eliminate GHG emissions in firing processes, SACMI Forni & Filters has built a hydrogen production station and an experimental kiln able to run on this gas. The project seeks to fire ceramic tiles while minimizing emissions, reducing energy consumption and abandoning fossil fuels (with the exception of biomethane). Moreover, the project aims to reduce the release of nitrogen oxides into the atmosphere (a cause of acid rain) via a complete redesign of the combustion system.
The electrolyzer is fed with mains drinking water and produces demineralized residual water. For every liter of water processed, half a liter is released into the environment
8 The information contained in this chapter does not include PET Projecta or SACMI Service.
9 SACMI Imola and PackSud have signed electricity supply contracts that provide Guarantees of Origin (8% for SACMI Imola, 100% for PackSud).
Integrated Annual Report 2023 / Environmental performance / Energy management
The Group also pays close attention to emissions generated by employees during home-work transfers. A growing number of initiatives tackle this issue: working from home is encouraged (profession allowing) and several electric car charging stations have been installed in Group company car parks. Furthermore, use of low-emissions means of transport such as trains10 and bicycles is encouraged (for more detailed information see the section on the Bike to Work project).
INITIATIVES TO REDUCE EMISSIONS
Bike to Work project
SACMI Imola has joined several initiatives aimed at alleviating the environmental impact of home-workplace transfers (i.e. projects that seek to alleviate traffic and reduce pollution).
For example, thanks to the Bike to Work Imola project SACMI employees rode no less than 128,315 km during their home-workplace commutes in 2023, reducing CO2 emissions by an estimated 17,949 kg
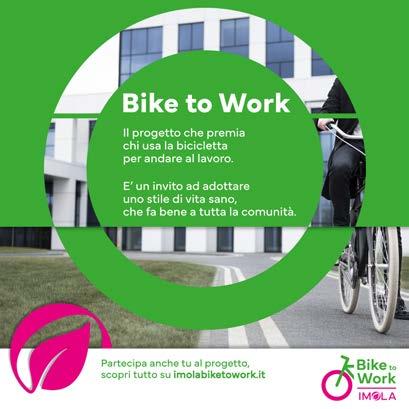
In 2023, a total of 21,424 tCO2e were produced, a slight increase (+4%) on the previous year. GHG emissions are mainly attributable to the combustion of natural gas (9,967 tCO2 e). Indirect emissions (Scope 211) constitute an equally significant portion: if calculated using the Location-Based approach they amount to 9,061 tCO2e
The ‘GHG Emissions graph shows production of CO2 over the three-year period. Note that there has been a steady decrease in GHG emissions (Scope 1), in alignment with the reduced use of natural gas. In 2023, in fact, production of CO2 linked to consumption of natural gas and fuels for the company vehicle fleet fell by 5% compared to the previous year and 12% compared to 2021. Consistent with the increase in consumption of purchased electricity, Scope 2 emissions increased in 2023.
10 For example, LAEIS pays a portion of the rail ticket fees for employees who travel to work by train.
11 The term ‘Scope 1 emissions’ refers to direct emissions of greenhouse gases that come from sources owned or controlled by the company. For example, the quantity of CO2 equivalent produced by the organization’s combustion of natural
Scope 1 emissions. Instead, indirect
the company fall within Scope 2.
Other significant in-atmosphere emissions
In-atmosphere emissions are generated by combustion reactions and specific production processes that occur inside Group facilities. Emissions monitoring is regulated through specific authorizations, issued to individual plants.
The bulk of emissions are concentrated in the manufacturing plant of the parent company, SACMI Imola. The data closely correlates with effective plant operation, itself a function of manufacturing requirements.
Other significant in-atmosphere emissions
(kg)
-5% less CO2 production
re consumption of fuels such as natural gas and fuels for the company vehicle fleet
13 The emissions factors used to calculate Scope 1 tCO2e are taken from the DEFRA (UK Department for Environment, Food and Rural Affairs) database 2023.
14 The emissions factors used to calculate Scope 2 tCO2e are taken from the following sources: Report 386/2023 published by ISPRA; “International comparisons” by Terna (2019); “European Residual Mixes” by AIB (2020, 2021 and 2022). The data provided by ISPRA, Terna and AIB is expressed exclusively in CO2 and does not include other greenhouse gases in the carbon dioxide equivalent (CO2e). In the text it was decided to maintain the CO2 e unit of measure to ensure uniformity and clarity and take into account the negligibility of the impact of greenhouse gases other than CO2 in generating electricity.
15 The Location Based approach is a method of calculating CO2 equivalent emissions (tons) based on geographical location. It reflects the average emissions intensity of grids on which energy consumption occurs (using mostly grid-average emission factor data).
16 The Market Based approach is a method of calculating CO2 equivalent emissions (tons): it calculates emissions based on the electricity that organizations have chosen to purchase (or selected through lack of choice).
Volatile organic compounds (VOCs)
NOx
In-atmosphere particulate (PM) SOx
Total of other emissions
17 Figures are obtained by examining the in-chimney chemical analysis performed as per authorization requirements, estimating maximum authorized operating hours as a function of individual chimney flow rates.
Integrated Annual Report 2023 / Environmental performance / Energy management

Water resources management
Water is used by the Group mainly for bathrooms/toilets, canteens and the occasional irrigation of gardens and outdoor green areas. Only some companies19 use water in production processes.
In certain manufacturing processes, water is used as a raw material input or accessory.
For example, water is used to produce the emulsified waters used on machine tools, to reduce emissions in coating and machining processes, or in the production processes that take place in the various workshops (ceramic, sanitary-whiteware, modeling and resin departments).
In other situations water is used to cool company systems, for washing, in painting system filtration tanks or in filling tests.
In 2023, water withdrawal was significantly reduced (-9%), with a further slight increase in the quantity of water treated by the SACMI Imola purifier 7.3
Use of withdrawn water in 2023
Industrial use
General sanitary use
18 The information required by GRI standards 303-4 and GRI 303-5 concerns SACMI Imola only; the information required by GRI standard 303-3 concerns all companies in the reporting boundary with the exception of PET Projecta, SACMI Service, LAEIS and SACMI Engineering Private Limited (India).
19 SACMI Imola SC, SACMI Beverage, SACMI Carpmec, SACMI Molds & Dies, SACMI Packaging & Chocolate, Sama Maschinenbau.
Integrated Annual Report 2023 / Environmental performance / Water resources management
Since withdrawn water is mainly used for bathrooms/toilets, the impact the Group might have on water resources is not deemed significant 20 Nevertheless, the Group is working towards increasingly accurate monitoring of water use in order to implement reduction and optimization measures.
In terms of waste management, most waste water flows into civil discharge points. The companies that use water in their production processes operate in compliance with current regulations and, where applicable, have specific national authorizations to manage discharges.
Water withdrawal
In 2023 the SACMI Group withdrew and used 98,644 m³ of water (-9% compared to 2022) Most comes from the public mains while a small amount is taken from wells or surface waters.
Water withdrawal, discharge and consumption for SACMI Imola (m³)
20 The materiality analysis conducted in 2023 confirmed that ‘Water resource management’ is not a material issue.
21 This table responds to the GRI 303-3 indicator. To make the information easier to read it was decided
meters. For GRI compliance
it is specified that 1
Water resources management: SACMI Imola
Approximately 55% of water withdrawal and use is attributable to the parent company's main plant, SACMI Imola, which uses water in some of its production processes.
More specifically, the water supply is sourced from three wells and from the industrial and potable mains water supplied by the local utility provider. Aquifer use is monitored constantly by means of an automatic system.
Discharge points on company premises can be divided into four different types:
• industrial discharges channeled to public sewers after purification
• industrial discharges directly into public sewers (cooling waters containing no pollutants)
Water
(m³)
• civil discharges (water used for bathroom and canteen purposes)
• discharges into surface waters without purification (rainfall run-off).
Industrial waste waters released into the public sewer system after purification mainly consist of the wash waters used in the various departments (ceramic workshop, painting department, resin department, whiteware and modelling workshops).
In 2023, the quantity of water treated by the purifier remained practically unaltered, increasing slightly by about 2% (8,242 m³ against 8,055 m³ in 2022). This occurred in parallel with an increase of about 4% in the hours worked by the departments involved (73,170 hours against 70,380 in 2022).
Underground waters
Total water withdrawal by third parties
discharges by type (m3)
Civil discharges
22 Areas subject to water stress were identified using the World Resources Institute (WRI) Aqueduct Water Risk Atlas, which provides accredited tools and methodologies. For disclosure purposes, only areas with ‘high’ or ‘extremely high’ levels of water stress were considered.. The rating scale has five levels (‘low’, ‘medium-low’, ‘medium-high’, ‘high’ and ‘extremely high’).
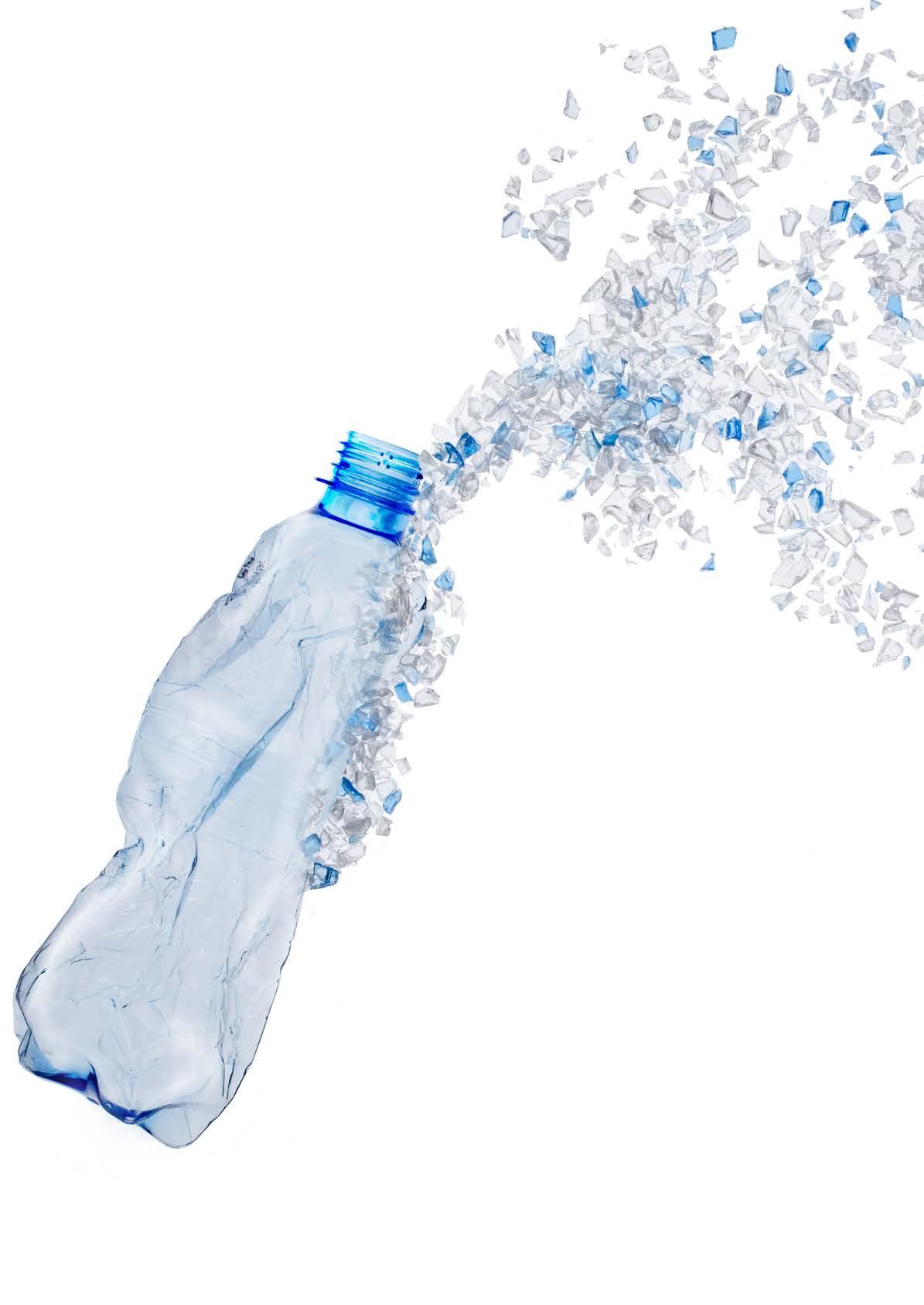
The SACMI Group produces several types of waste. In keeping with trends, company policy aims to ensure waste is managed in compliance with standards to ensure its proper disposal and to make it a resource as opposed to a burden. SACMI also engages in experimental work that can lead to large swings in waste output that depend on the machines being tested.
In 2023, 7,722 tons of waste were produced, a decrease of 13% compared to 2022. More specifically, this result stems from a reduction in the metal waste/inert materials produced by the testing of ceramic machines (this waste is generally sent for retrieval or recycling).
In 2023 88% of the waste produced was recycled or reused. Furthermore, only 0.4% was sent to landfill
SACMI aims to further reduce the waste it produces, almost all of which is destined for recycling or retrieval. The year 2023 saw the start of the ‘Sustainable Packaging’ project
Recycled/non-recycled waste (2023)
As the graph shows, most of the waste produced during 2023 was made up of ferrous materials (34%) which are recycled and resold. A significant portion of waste is generated by packaging for the raw materials and/or components used in production processes. This portion - made up of plastic, paper, cardboard, wood and other mixed-material packaging - accounted for 33% of all waste produced in 2023.
Overall, the percentage of hazardous waste remains limited ( 10% of the total).
Waste produced by the organization is handled and processed by specifically authorized third parties in compliance with national legislation. All bodies involved in waste disposal and recovery processes are duly verified by the organization. Production of hazardous and non-hazardous waste (2023)
Circular economy initiatives
The Group seeks to raise awareness vis-à-vis proper management of all waste produced and encourages, where possible, actions aimed at reducing waste.
During 2023, the SACMI Group continued to invest - through partnerships with specialized companies - in projects that improve circularity and make use of production waste.
Some of the initiatives taken by SACMI Imola concerned, for example:
• wood waste: recycling of a portion of the material to produce pallet blocks
• ceramic waste: used to obtain a semi-finished product which, in turn, is used to produce spray-dried ceramic powder
• plastic cups and stirrers used in canteen/ refreshment areas: participation in a plastic recycling program to make new products
• vegetable oil: reuse of canteen waste to produce bio-fuel
• recycling of approximately 1,000 tons of metal chippings produced by machine tools
• recovery of approximately 630 tons of plastic waste, which stems from testing of the machines made by the company.
The Parent Company also registered a significant decrease in some hazardous wastes, such as oily emulsions (CER code 12.01.09), which in 2023 amounted to 441,290 kg against 284,144 hours worked in the involved departments. The indicator based on the ratio between these values decreased by 2.94% compared to the previous year.
More specifically, this reduction has been achieved by:
• tracking consumption of the emulsifiable oil disposed of
• improving warehouse management
• installing meters to monitor tank inflow on each machine tool
• creating a KPI for oil consumption (liters consumed/hours worked).
Over the last two years these initiatives have resulted in a 22% reduction in the indicator.
Lastly, it should be noted that some Group companies have started using paper as a packaging filler instead of polystyrene and polythene film. Other initiatives concern the recovery of certain types of packaging which, through agreements with customers, are collected and reused (subject to suitability)24
24 In Gaiotto Automation it is estimated that 60% of packaging was retrieved.
In 2023, the ‘Sustainable packaging’ project was finalized with the Whiteware BU. This project aims to maximize use of recycled materials, reducing unnecessary packaging and retrieving as much packaging as possible after it has been used. This pilot project concerned materials used to package machines/molds shipped from the Italian Sanitaryware production facilities in Imola, Piacenza and Verona.
Shipped machines were packaged with recycled plastic film: plans were also made to retrieve a part of this packaging for subsequent reuse. From a broader perspective, the project aims to develop a tracking chain for all types of packaging entering and exiting SACMI factories and ensure observance of internationally acknowledged packaging supply chain standards. Planned actions include:
• a certified wood supply chain for the wood used to make the crates in which machines are shipped
• use of ‘ eco-sustainable ’ plastic films subject to technical limitations and with careful preliminary testing to ensure performance is on a par with that of traditional packaging
• retrieval of packaging from customers’ sites, mainly pallets that can be reused.
- sacmi.com
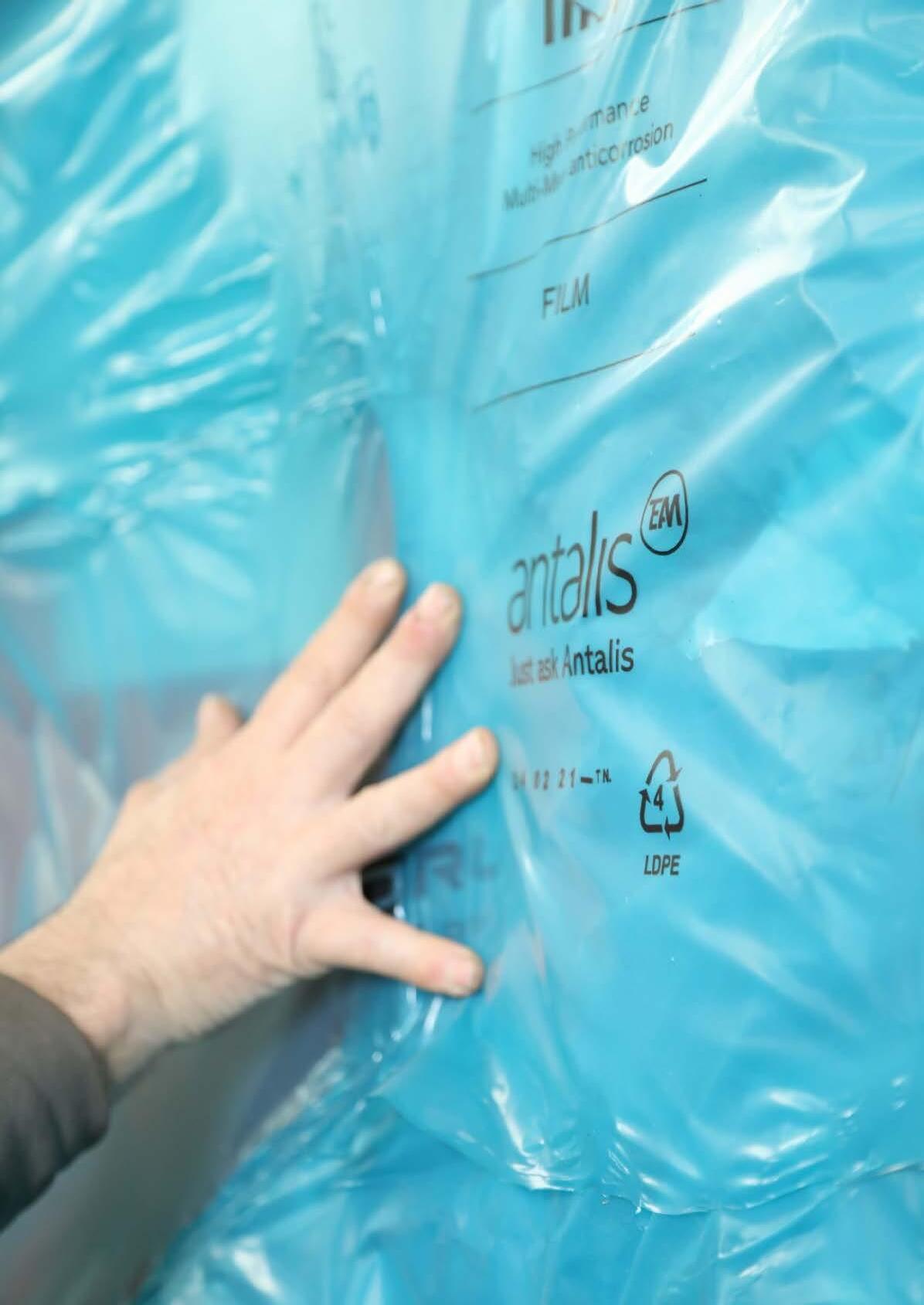
Methodological Note
For the tax year ending 31st December 2023, the SACMI Group has decided to draw up an Integrated Annual Report to render its disclosure of non-financial performance even more transparent.
This document aims to transparently inform stakeholders of achieved results and share future goals with them. It aims to promote continuous comparison and improvement, providing an all-round view of the Group’s economic-financial and sustainability performance.
The principles of reciprocal assistance, both internal and external, have been an intrinsic part of SACMI since its founding and its nature as a Cooperative. These principles extend throughout the SACMI Network, taking, year after year, the form of practical action: from projects designed to safeguard the environment and enhance skills to those that seek to provide new opportunities for communities both locally and internationally in the countries where the Group operates.
Since 2018, SACMI has published an Integrated Annual Report that combines the reporting of Group results, broken down into the various Business areas, with analysis of the sustainability performance of the parent company, SACMI Imola SC. As of 2022, the expansion of the reporting perimeter involves almost all the Italian companies in the SACMI Group. Further expan-
sion of scope was actuated in 2023, involving all the Italian companies and five foreign ones. In the coming years the goal is to extend the reporting boundary to the entire Global Network.
Given the fast-changing nature of sustainability standards, the SACMI Group has, with the drawing up of the Integrated Annual Report, enacted further improvements in the relevant reporting practices. This move is designed to ensure increasingly higher quality and an appropriate strategic direction for its products; over the coming years the aim is to develop annual non-financial reporting and integrate it with the Consolidated Financial Statements to establish a starting point for further ESG activities.
Reporting period and boundary
Data and performance reported therein refer to the tax year from 1st January 2023 to 31st December 2023 and are published annually in a document separate from financial information. Similarly, the items covered are presented in a way that ensures, as far as is possible, comparison with the previous two-year period so that all stakeholders can compare performance over time.
Unless otherwise specified, the data/information in this Report refer to the reporting boundary that includes the above-listed SACMI Group companies, hereafter referred to as ‘SACMI Group or Group’.
• The section on Responsible governance and value creation covers the SACMI Group's strategic guidelines and illustrates how the governance bodies of the parent company, SACMI Imola SC, operate.
• The ‘Innovation and Research section describes the performance of all SACMI Group companies, with the exception of the data shown in the table ‘R&D – Resources and projects’ which refers to the following Italian companies of the Group: SACMI Imola, SACMI Tech, SACMI Forni, Iprel, SACMI Beverage, Gaiotto.
• In the Wealth generated and distributed’ section the information refers to the performance of the entire SACMI Global Network.
• The Suppliers section refers to the performance of the entire SACMI Global Network vis-à-vis quantitative and qualitative data linked to corporate procedures and processes.
• The Social Performance’ chapter illustrates the performance of those companies within the reporting boundary, with the exception of Pack Sud. In the “Health and Safety” section Pet Projecta and SACMI Service are excluded from the reporting boundary. Lastly, the ‘Customers’ section refers to the performance of the entire SACMI Global Network.
• The Environmental Performance’ chapter illustrates the performance of those companies within the reporting boundary, with the exception of Pet Projecta and SACMI Service. Further limitations in scope linked to the unavailability of specific data are reported directly in the chapter.
• Lastly, data and information contained in the Letter from the President and ‘The SACMI Group’ section refer to the entire SACMI Global Network (for a list of companies see “SACMI around the world”).
SACMI companies included in the reporting boundary
SACMI Imola S.C.
SACMI BEVERAGE S.p.A.
SACMI VERONA S.p.A.
GAIOTTO AUTOMATION S.p.A.
PACK SUD S.p.A.
SACMI PACKAGING & CHOCOLATE S.p.A.
SACMI CARPMEC S.p.A.
TECNOS S.r.l.
PET PROJECTA S.r.l.
VELOMAT S.r.l.
EUROELETTRA S.r.l.
SACMI FORNI & FILTERS S.p.A.
SACMI IMPIANTI S.p.A.
SACMI MOLDS & DIES S.p.A.
SACMI TECH S.p.A.
DEFRANCESCHI S.r.l.
IPREL PROGETTI S.r.l.
ITALIANSPED S.p.A.
SACMI SERVICE S.p.A.
Integrated Annual Report 2023 / Methodological Note
SAMA MASCHINENBAU GmbH
RIEDHAMMER GmbH
BMR S.p.A. LAEIS GmbH
SACMI MACHINERY FOSHAN NANHAI CO. LTD.
SACMI ENGINEERING INDIA Pvt. Ltd.
SACMI IBERICA S.A.
PROTESA S.p.A.
Scope of the report
The Annual Report has been drawn up as per the GRI Sustainability Reporting Standards (GRI Standards) issued in 2016 by the Global Reporting Initiative and subsequent amendments; such guidelines constitute the most widely used sustainability reporting standard at international level, as per the ‘In accordance with’ accounting option.
The Report is drawn up according to the principles in GRI 1 Foundation, which defines the content and quality of the reporting:
• accuracy so that the reported information is sufficiently detailed to allow assessment of the organization’s impact
• complete balanced information in order to represent the Company's sustainability performance in the most appropriate way and ensure the document offers a balanced view of both positive and any negative aspects.
• clarity of the way the gathered quantitative data and qualitative information is processed and presented, and of the underlying data/ info calculation methods, thus allowing all stakeholders to make an objective, sufficiently complete appraisal of performance.
• comparability of data and information over time by using a three-year timescale.
• timeliness of the drafting and publication of the Annual Report, which will be on an annual basis in conjunction with the approval of the Financial Statements.
• verifiability, i.e. the implementation of a process of recording, compiling and analyzing information in a way that ensures the information provided is of a certain quality.
• sustainability context: presentation of the sustainability context in a broad and comprehensive manner (economic, social and environmental impacts at local, regional or global level).
The Annual Report is not subject to auditing by any third party.
Contacts and addresses
Should you wish to make any comments or requests or offer any opinions or suggestions regarding this Annual Report please write to sostenibilita@sacmi.it
The Annual Report is available on the website: www.sacmi.com
SACMI IMOLA SC Via Selice Provinciale 17/A, 40026 Imola (BO) –Tel. 0542 607111
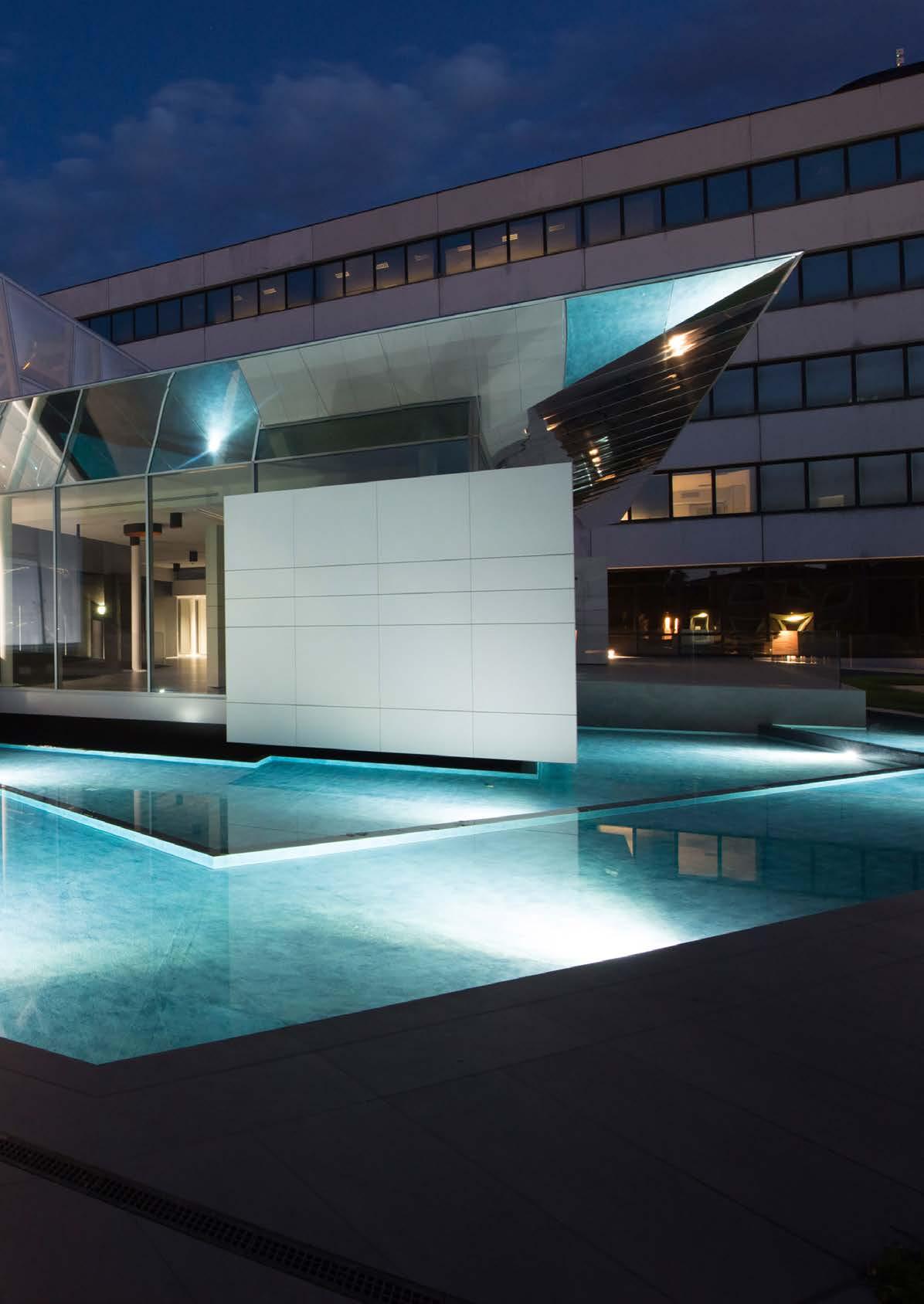
2-5
2-6
GRI contents table
2-18
* Requisites omitted: b.iii. Reason: information unavailable. Explanation: In future tax years SACMI shall undertake to report information relating to sub-division by non-guaranteed hours.
** Requisites omitted: a, b, c. Reason: information unavailable. Explanation: In future tax years SACMI shall undertake to report information relating to non-employee workers.
*** For GRI 2-19 and 2-20 the omitted requisites are: a, b. Reason: information unavailable. Explanation: In future tax years SACMI undertakes to report information relating to standards concerning remuneration and the determination of wages.
**** Requisites omitted: a, b, c. Reason: information unavailable. Explanation: In future tax years SACMI undertakes to report the information relating to the ratio between the annual payments.
***** Requisites omitted: b. Reason: information unavailable. Explanation: In future tax years SACMI undertakes to report information relating to accidents involving non-employee workers whose tasks and/or workplace are under the organization’s control.