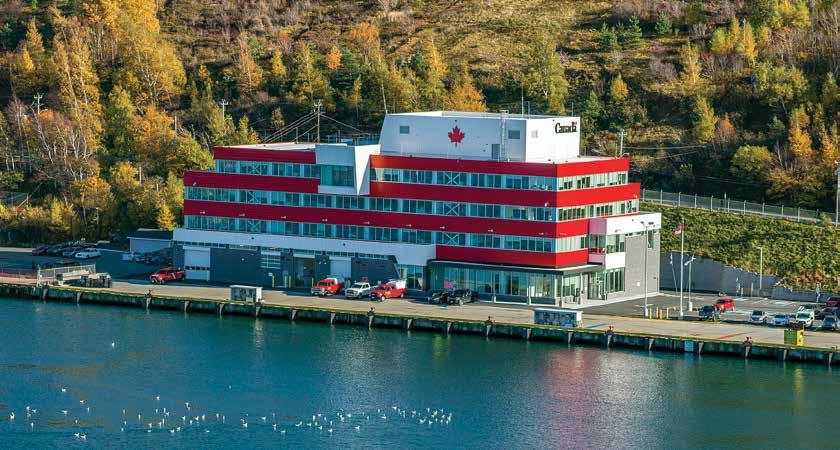
4 minute read
Canadian Coast Guard Atlantic Regional HEADQUARTERS
LEED Gold building designed for longevity and worker comfort
By Rolfe Kaartinen and Emad Miran
Advertisement
The new Canadian Coast Guard (CCG) Atlantic Regional Headquarters building located at the southwest end of St John’s harbour connects to parking areas, underground services and geothermal wells undertaken during an earlier phase of revitalization.
The 6,190 sq.m total gross floor area, four-storey steel frame building constructed by Lindsay Construction accommodates the approximately 183 staff servicing the entire expanse of Newfoundland and Labrador.
Planned according to the Federal Office Building Standards and Government of Canada Workplace 2.0 Fit-up Standards, the CCG Headquarters contains open and enclosed offices, support spaces including meeting rooms, quiet/ conversation rooms, kitchenettes, areas for shared equipment, printer stations, waiting and reception areas, other non-designated support space with fixed walls, first aid room or station and special purpose space for the respective CCG divisions.
Interior spaces are organized pragmatically to achieve the optimum desired adjacencies, exterior views, internal natural light penetration, efficient functional relationships, and security zone boundaries. The ground floor, which contains meeting rooms, executive offices and the elevator core, has the main entrance at the west end where the security office can manage access from the reception area, workshops and other areas.
The building achieved LEED Gold certification due to sustainable practices which encompass highperformance building envelope design and glazing, high indoor environmental quality achieved through advanced HVAC systems and choice of building materials, and provisions for daylighting and views.
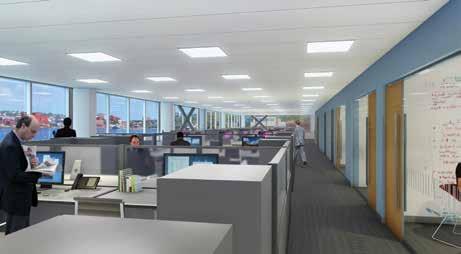
The architectural design gives the building a modern expression with a complementary and harmonious material mix of corrugated and flat metal panels, aluminum curtain wall, glazed sectional overhead doors and architectural concrete block.
The red, white and black colour palette and sloping forms of the Coast Guard fleet are adapted in an abstract manner to render the exterior facades of the building and highlight some of its features such as the protective overhang and the signage wall, the protruding meeting room, and the sculpted mechanical penthouse which presents a distinctive silhouette across the harbour.
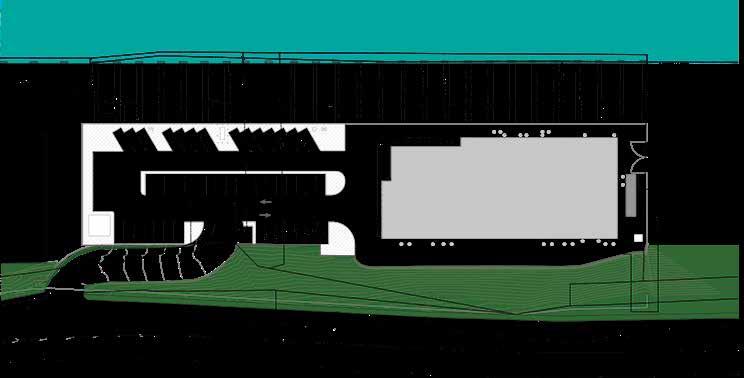
The exterior envelope has been designed according to the ventilated “rainscreen” principle with wall assemblies that meet the 50-year full-service life and 30-year rehabilitation service life. The envelope assemblies were developed in concert with the integrated team (NORR / FMA/ Lindsay) and informed by energy modelling software and the model energy code.
Envelope integrity has been ensured by the continuity of the thermal, air, water and vapour control layers at all material and assembly transitions. The design exceeds the ASHRAE climate Zone 6 effective R-values stipulated for the thermal performance of the wall, floor and roof assemblies.
Exterior cladding is comprised of high-quality architectural concrete block, composite metal and wall cladding panels, and curtain wall. The materials wrap their way around and up the building elevations in a diagonal and horizontal banding which provides a unified, clear, and cohesive appearance.
This is helped by the fenestration which starts on the ground floor with sizable sections of curtain wall at the main entrance and office areas, progressing to clerestory openings at the workshops, and then ribbon windows around the office levels, eventually terminating with a full-height curtain wall expression on the third-floor building pop out.
Measures taken to reduce the operational and maintenance effects over the building’s 50-year life-cycle include:
• Creation of a compact and efficient floor plate.
• Efficient mechanical systems that are appropriately sized and located for efficient distribution of systems.
• Reduced number of mechanical shafts to provide for flexibility in the planning of future renovations.
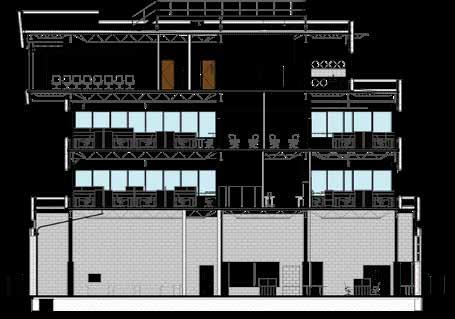
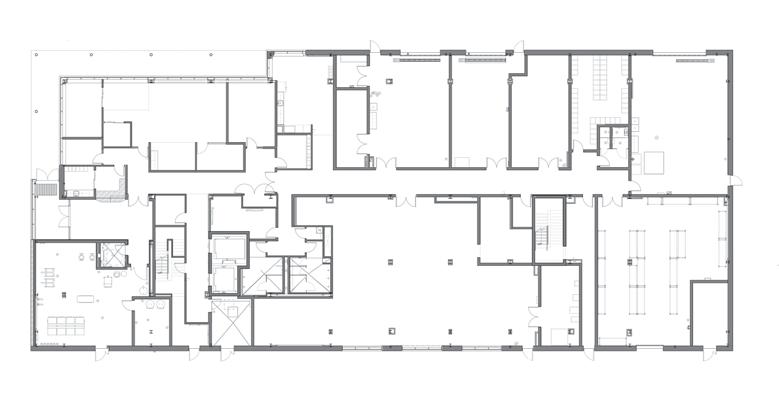
• Using readily available materials to reduce long term operating costs, and a durable envelope to withstand freeze thaw cycles, and high winds.
• Employing modular systems that permit replacement of individual components.
• Use of environment-appropriate systems that resist corrosion such as stainless-steel masonry anchors and ties and high-performance paint systems.
Architectural design strategies to reduce energy use and increase user comfort include:
• Low-E coated high-performance glazing.
• Thermally-broken building envelope support systems.
• Wall, floor, and roof assemblies that meet or often exceed the NECB minimum standards for thermal performance.
• Renewable energy sources such as daylighting and geothermal heating and cooling.
• Efficient HVAC and LED lighting systems.
• Optimized building performance by employing energy modelling programs, occupancy and CO2 sensors, and air quality alarms.
PT wood blocking, 2% slope
22 gauge parapet flashing Cap sheet flashing Backing rod and sealant Metal siding
152mm structural metal stud, filled with mineral wool insulation
2 ply mbm roofing membrane with a positive lap over parapet
Vapour barrier to have a positive lap down sheathing
152mm structural metal stud
Structural HSS
Roofing type R1.1
Project Credits
OWNER Public Works Government Services Canada
ARCHITECTS NORR Architects & Engineers Limited/ Fougere Menchenton Architects Inc.
STRUCTURAL ENGINEER DMG Consulting
MECHANICAL/ELECTRICAL ENGINEER Core Engineering Inc
GENERAL CONTRACTOR Lindsay Construction
CIVIL ENGINEER MAE Design Limited
LEED CONSULTANT Solterre Design
DURABILITY CONSULTANT WSP
PHOTOS Celebrity Photo Studio
Vapour barrier
Structural steel
Finally, the harbour location was used to advantage. The hills to the south were considered strategically in the design, with the lowoccupancy mechanical spaces being located on the ground floor toward the hill where the lack of natural light is not an issue. The laneway between the hill and the building acts as a “back of house” opportunity for the location of exit doors, mechanical room access, workshops, and recycling.
Facing the harbour, large expanses of glass provide excellent views and natural daylighting conducive to a productive, positive working environment.

ROLFE KAARTINEN, OAA, MAA, NLAA, AANB, MRAIC IS VICE PRESIDENT AND EMAD MIRAN, SENIOR ASSOCIATE IS PROJECT MANAGER, BOTH AT NORR ARCHITECTS & ENGINEERS LIMITED.
22 gauge metal flashing
Aluminum curtain wall
Vapour barrier to wrap entire window opening
Fill void around window opening with low expansion spray foam
Non continuous glazing connection back to structure
Structural HSS
Vapour barrier over 22 gauge metal flashing
152mm structural metal stud
16mm pre primed glass mat sheathing on 22mm hat channels connected to 150mm thermal spacers
Wall section detail