

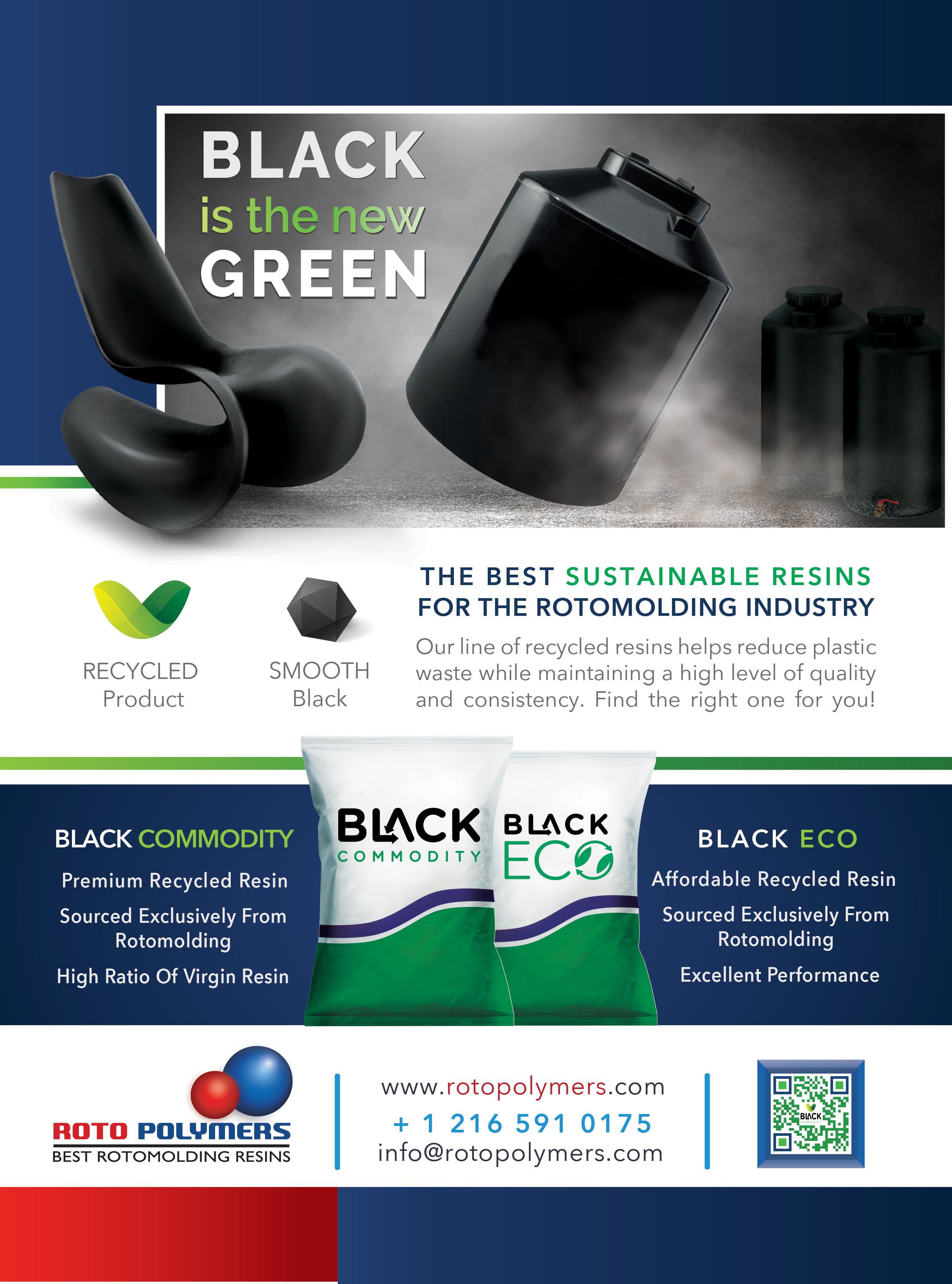
• Highly Automated Direct Drive Pulverizing Systems
• Silos
• Conveying Systems for Pellets and Powder
• Dry Blending High Intensity Mixers
• Lab Testing Equipment for Powder Analysis, Rotap Particle Testing and Dry Flow Testing
• New Disks for Pulverizing Systems
• Largest CNC Disk Sharpening Services for Pulverizers in the World
We also provide responsive technical assistance to customers or any inquiry into the pulverizing process of powder production. We are happy to assist you with knowledgeable and fast courteous services.
sales@powder-king.com
Powder King® LLC
41780 N Vision Way, Units 120-125, Bldg. 2
Anthem AZ 85086
www.powder-king.com
623.551.9897
Cover Photo is courtesy of Slide ®. The Rotomolded novelties featured on the cover of this issue include: AMANDA & AMBROGIO, designed by Favaretto & Partners; and OTTOCENTO LAMP, designed by Paola Navone OTTO Studio - for Slide ®
The ARMO Showcase is designed to educate the world about fantastic, innovative, attractive, practical, and economic rotationally moulded products.
42
Alvin Spence, Centro Incorporated
A close look at the last few years in the Rotational Molding industry.
ROTOMOULD23 QUEENSTOWN
Michelle Rose, ARMA CEO ARMA gathers a large attendance in New Zealand.
8 From the Publisher
Susan Gibson, JSJ Productions, Inc. What’s Buzzing?
10 Credits
Global Contributors, Department Contributors, and Issue Contributors
15 Upfront Industry News, Trends, and Products
49 At Issue
Martin Coles, Matrix Polymers
Sustainability in Rotomoulding – What Does It Really Mean?
54 X-Factor
Tom Innis, Xcelerant Growth Partners
Tenjam’s pivot to rotomolding proved to be its turning point.
58 Leadership
Cutting Edge PR
What PR teams need to know about cybersecurity concerns
62 ARM Report Roto Recharge
70 Roto Around the World
Ian Hansen, RotaConsult
KSC-Plast is Market Leader in Central Asia
74 Practical Roto Tips
R. Dru Laws, Brigham Young University - Idaho
Should you reverse your rotations?
Since the 1940s when mass production of plastics products had their beginning, the market has grown exponentially. The global plastics market reached USD 593 billion by the end of 2021, is estimated to double by 2040, and increase by 2.5 times by 2050.
Plastics are the most common materials for producing end-use parts for a wide spectrum of uses. Plastics are a versatile category of materials, with many polymer options, each with their own specific mechanical properties.
A variety of plastic manufacturing processes have been developed to cover a wide range of applications, part geometries, and types of plastics. For any designer and engineer working in product development, it is critical to become familiar with the manufacturing options available today and the new developments that signal how parts will be manufactured in the future.
The global rotomolding market was reported to reach a revenue of 5 billion in the year 2022 and is estimated to reach a revenue of 9 billion by the end of 2033.
Welcome to RotoWorld® Issue 3, 2023. We are pleased to feature the 2023 ARMO Showcase Special Section inside this issue. This ARMO Showcase is also featured as a separate digital “ISSUU” publication online. We hope to return to the full ARMO Showcase print and online publication in 2024.
The ARMO Showcase is designed to educate the world about fantastic, innovative, attractive, practical, and economic rotationally molded products. In this special section you will see some great product examples of what can be achieved with this process. From an innovative hunting feeder to versatile event applications, end-users are finding rotational molding is the answer for a world of product applications.
When looking for a plastic manufacturing process that produces high-end, versatile, and functional parts, the rotational molding process is the one to look to. This is a process that involves heating a hollow mold filled with powdered thermoplastic and rotating it around two axes simultaneously to produce mainly large hollow objects.
Rotational molding requires less expensive tooling compared to other plastic processes as there in no pressure required to form the part. Molds can be fabricated, CNC machined, or cast from aluminum at a lower cost and shorter lead times compared to tooling for other molding processes, especially for large parts.
Rotational molding creates parts with nearly uniform wall thickness. Once the tooling and process are set up, the cost per part is very low relative to the size of the part. It is also possible to add prefinished pieces, like metal threads, internal pipes, and structures to the mold.
These factors make rotational molding ideal for short production runs or as an alternative to blow molding for lower volumes. Typical rotomolded products include tanks, buoys, large containers, toys, kayaks, and playgrounds just to name a few.
Rotomolding has some design constraints and finished products tend to have broader tolerances. As the entire mold must be heated and cooled down, the process also has long cycle times and is quite labor intensive, limiting its efficiency for higher volume applications. However, it is perfect for lower volumes.
The most common material for rotational molding is polyethylene (PE) which is used in more than 80% of applications, mainly because PE can be easily ground into a powder at room temperature. Commonly rotomolded plastics include:
• Polyethylene
• Crosslinked Polyethylene
• Polypropylene
• Polyvinyl chloride
• Nylons (6, 11 & 12)
• Polycarbonate
We hope you will enjoy this issue as it contains some great reading regarding current developments in the rotational molding industry. See “Adaptability...the Secret Sauce for Many Rotational Molder’s Success Stories”, authored by Alvin Spence, Centro Incorporated starting on page 42. Also, inside is a look at two successful 2023 rotomolding conferences, ARMA’s Rotomould23 Queenstown and the 2023 StAR Conference held in New Delhi. Congratulations to both!
I hope to see you in Poznan for what promises to be an excellent conference for our global industry!
Sincerely,
Susan Gibson Publisher & EditorJerico’s complete line of aesthetic compounded materials brings a bright and dazzling look to your rotational molded products. Our Stone Effect specialty color compounds are designed for many outdoor applications like hot tubs, lawn/garden accessories, flower pots, and patio furniture, and they’re now FDA compliant for use in coolers.
Stone Effect can be produced in any color and with varying color intensities by using our line of Stone Effect color concentrates. We work with you to acheive your optimum color and design expectations every time!
As we grow, we look for ways to exceed your expectations and help you achieve even greater success! Our mission is to be the go-to resource for resins and compounds that meet your precise specifications, arrive on time, and provide the consistent level of quality you’ve come to expect from Jerico! You’ll always receive the kind of personal service that we like to call the Jerico Effect!
Our commitment and flexibility show in everything we do!
info@jericoplastic.com
Publisher & Editor
Susan D. Gibson President - JSJ Productions, Inc. susan@jsjproductionsinc.com
Technical Editor
Alvin Spence PhD MEng aspence@centroinc.com
Process Editor
Paul Nugent PhD MEng paul@paulnugent.com
Design Editor
Michael Paloian President - Integrated Design Systems, Inc. paloian@idsys.com
Global Contributing Editors
Celal Beysel Chairman - Floteks Plastik beysel@superonline.com
Tom Innis Excelerant Growth Partners w@xcelerantgrowthpartners.com
Martin Coles Matrix Polymers martin.coles@matrixpolymers.com
Adam Covington Ferry Industries acovington@ferryindustries.com
Mark Kearns Moulding Research Manager m.kearns@qub.ac.uk
Ravi Mehra Managing Director - Norstar International LLC maramehra@aol.com
Advertising and Art Production
Marketing/Advertising Director Jennifer Gibson Hebert Vice President, JSJ Productions, Inc. jennifer@jsjproductionsinc.com
Chief Art Director Anya Wilcox JSJ Productions, Inc. awilcox@designintersection.com
Circulation & Distribution Administration
Sheryl Bjorn JSJ Productions, Inc. sheryl@jsjproductionsinc.com
Editing & Translations
Suzanne Ketron | Oliver Wandres | Sheryl Bjorn
Website & Online Technology
Jason Cooper JSJ Productions, Inc. jason@bound.by
RotoWorld ® is a JSJ Productions, Inc. Trade Publication JSJ Productions, Inc. 625 West Market Street, Salinas, CA 93901 Phone: (512) 894.4106; Fax (512) 858.0486
Email: rotoworldmag@rotoworldmag.com and Website: www.rotoworldmag.com
Subscriptions One-year subscription (six issues), print or digital, $80 US, $100 Canada/Mexico, $155 All Other Countries. To subscribe or to submit change of address information, call us at (512) 894.4106; fax us at (512) 858.0486; visit us online at www.rotoworldmag.com; or email us at sheryl@jsjproductionsinc.com. You may also write to RotoWorld ® Subscriptions, JSJ Productions, Inc., 625 West Market Street, Salinas, CA 93901
Advertising For information on advertising, please contact Advertising Director Jennifer Gibson Hebert, JSJ Productions, Inc.
Email Jennifer Gibson at jennifer@jsjproductionsinc.com
Letters We welcome letters about our contents. Write Letters to the Editor, JSJ Productions, Inc., 625 West Market Street, Salinas, CA 93901 512.894.4106 phone 512.858.0486 fax, or Email susan@jsjproductionsinc.com.
Editorial Queries We consider unsolicited contributions. Send manuscript submissions as email attachment to Susan Gibson at susan@jsjproductionsinc.com.
JSJ Productions, Inc. bears no responsibility for claim or factual data represented in contributed articles.
Postmaster Send changes of address to RotoWorld®, JSJ Productions, Inc., 625 West Market Street, Salinas, CA 93901
RotoWorld® is a JSJ Productions, Inc. independently owned, bi-monthly trade magazine for the international rotational molding and plastics design industries. JSJ Productions, Inc. owns all copyrights on articles published herein unless ownership is otherwise stated. Reproduction of this magazine, in whole or in part, without the express written permission of the publisher is not permitted.
Polyethylene Granules & Powders
Crosslink Polyethylene
Polypropylene Granules & Powders
Polyamide Powders
Ancillary Products
Designed
Dedicated Technical Services Support Team
Multi-lingual
NEW for 2023 our latest investment in a purpose-built compounding and grinding plant in Rayong, Thailand.
To learn more about our products & material solutions get in touch at:
Alvin Spence is Vice President Engineering at Centro, Inc., North Liberty, Iowa. He provides leadership for Centro’s product development team and quality resources. Alvin received his Bachelor’s degree in Mechanical & Industrial Engineering and PhD from Queen’s University Belfast. aspence@centroinc.com
Paul Nugent
Paul is a consultant who travels extensively across six continents assisting clients in many roles from training to expert witnessing. He received his Eng. degree in Aeronautical Engineering and Ph.D. in Mechanical Engineering from Queen’s University of Belfast. Paul developed the Rotolog system, the first complete computer simulation (RotoSim), and authored a book entitled Rotational Molding: A Practical Guide paul@paulnugent.com
Celal is Chairman of Floteks Plastik, the pioneer and innovative leader of the rotational molding industry in Turkey and a Global Contributing Editor for RotoWorld® magazine. Being an ARM member for more than 20 years, he has made many presentations at ARM meetings in various countries. He is also active in business and political organizations in his country. Celal has authored numerous articles published in various newspapers and magazines about politics, plastics, rotomolding, and innovation. beysel@superonline.com
Michael is President of Integrated Design Systems, Inc., Great Neck, New York. Over the past 25 years, Mike has developed a broad range of plastic products utilizing various processing methods including rotational molding. Mike’s B.S. degree in Plastics Engineering and Masters in Industrial Design, combined with his extensive experience, has formed the basis for his branded and unique insights into the field of plastics part design. paloian@idsys.com
Martin Coles, CEO of Matrix Polymers co-founded the business 30 years ago and is the company’s largest shareholder. Shortly after graduating from London University, he began his career in the plastics industry working for a major Italian petrochemical and soon became passionate about the unique world of rotomoulding. Matrix Polymers are experts in rotomoulding materials and have become a global supplier with compounding and grinding plants in the UK, Poland, Australia, New Zealand, and Malaysia. The company sells more than $150 million of rotomoulding materials each year and has 230 employees. martin.coles@matrixpolymers.com
Adam Covington is President of Ferry Industries, Inc. in Akron, Ohio U.S.A. Covington has been with Ferry Industries for over 11 years, advanced through the manufacturing, engineering, sales, and service positions within the company and was appointed President in 2019. Adam strives to find solutions for customer’s needs and advance machine technology for the rotomolding industry. He is a graduate of Ohio University’s Russ College of Engineering and Technology with a Bachelor’s degree in Industrial Technology. acovington@ferryindustries.com
Mark Kearns is the Rotational Moulding Research Manager of the Polymer Processing Research Centre at Queen’s University of Belfast. He is a Chartered Chemical Engineer with a M. Phil Degree in Rotational Moulding. Mark manages rotational moulding research and development projects for companies across Europe, Australasia, and North America. M.Kearns@qub.ac.uk
Tom Innis is owner and Principal CEO of Xcelerant Growth Partners, LLC (Madison, WI), a multi-discipline consulting firm with specific focus in the global plastics sector. Leveraging industry experience and relationships built over 25+ years in the international manufacturing realm, Xcelerant connects the links in the industry supply chain to accelerate speed-to-market and deliver turnkey personnel, product development and manufacturing solutions to an international audience. tinnis@xcelerantgrowthpartners.com
Ravi Mehra has been associated with the rotational molding industry since the early 1970’s. He is a Past President of ARM – Association of Rotational Molders, and has been inducted into the ARM Hall of Fame. He is the Founding Chairman of StAR – the rotational moulding Trade Association of India. He was the Chairman of ARMO – Affiliation of Rotational Moulding Organizations from 2012 to 2014. Ravi consults internationally with companies in the rotational moulding arena to help their global strategy, facilitate technology tie-ups, and business alliances. maramehra@aol.com
Ian Hansen has over 30 years of experience in the rotational moulding industry and has presented to conferences around the world on the subject of quality, safety, and tank design standards. Rotomoulders around the globe have problems from time to time. Rota Consult delivers production solutions so rotomoulders can improve productivity and profitability, without wasting more of their valuable time. ianhansenconsult@gmail.com, www.ianhansenconsult.com
R. Dru Laws, educator and rotomolding expert, graduated from Brigham Young University in 2003 with a BS in Mechanical Engineering and a minor in Mathematics. In 2005, he graduated top of his class with distinction (honors) from the Queens University Belfast in Northern Ireland with an MSc in Polymer Engineering from their school of Mechanical & Manufacturing Engineering. He has several rotomoulding-related patents. Laws is currently a full-time Manufacturing Engineering professor at BYU-Idaho, as well as CEO of Halltech Systems and High Pointe Plastics.
Kim Harrison, Founder and Principal of Cutting Edge PR, loves sharing actionable ideas and information about professional communication and business management. He has wide experience as a corporate affairs manager, consultant, author, lecturer, and CEO of a non-profit organization. Kim is a Fellow and former national board member of the Public Relations Institute of Australia, and he ran his State’s professional development program for 7 years, helping many practitioners to strengthen their communication skills.
S B Zaman has been an industry promotion professional in the Plastics sector for about two and a half decades; he has been executive head of StAR since inception of the association in 2004. As its Executive Director currently, he has played his role in the continuing success of StAR being a truly representative body of the Indian & South Asian rotomoulding industry, as well as proactive member of ARMO. Coming from a Media background he has been involved in several publication projects and frequent industry articles.
With a Degree in Hotel Management and a background in event organisation, Michelle started with the ARMA almost 15 years ago, in the role of Deputy Executive Officer. During her career so far, Michelle has organised conferences and study tours all over the world and gained extensive experience in membership management, stakeholder engagement, and administrative services, as well as business and project management. Due to her commitment, hard work, and wide range of expertise, as well as the value of her current industry relationships, Michelle was selected for the role of CEO starting January 2021.
BAXTER, MN, USA — a leading tooling manufacturer serving the global rotational molding industry, has announced the sale of its business to Self Group USA, a multi-national thermoforming tool manufacturer headquartered in Rivignano Teor, Udine, Italy. The strategic acquisition aligns and expands the capabilities of the two companies, creating a broader offering of tool building technologies and expertise to customers in the rotational molding and thermoforming manufacturing sectors.
Founded as Lakeland Mold Company in Brainerd, MN in 1988, and later acquired by Tom and Ellen Haglin in 2012, Avantech has leveraged significant investment in state-of-the-art facilities, CNC machining equipment, manufacturing systems, and exceptional people to deliver high-quality tooling and exemplary service to rotational molders throughout the global industry. As the company has expanded, it has become of a target of acquisition, but it was not until the dialog with Self Group began that this piqued the interest of the Haglins.
“Over the years, we’ve been approached numerous times (regarding selling the business),” commented Tom Haglin,
co-owner and CEO of the company, “but until now, none of the potential buyers fit the profile necessary to capture our interest: a company with similar values that is prepared to invest in the organization’s future while respecting its legacy.” Noting Self Group’s family-owned and -operated structure, its ability to diversify Avantech’s manufacturing capabilities, and its sole focus on tool-building, Haglin stated,“There was true alignment with Self Group - from both philosophical and business perspectivesthat drove both parties’ desire to make this happen.”
As Self Group USA assumes ownership, the Avantech management team will remain intact in moving the business forward. “As this transition takes place,” stated Haglin, “maintaining customers’ confidence in entrusting us with their tooling investments is absolutely critical, and we’re excited that the Avantech team will continue to provide the experience, expertise, and service to which our customers have become accustomed.”
Please visit avantech.com for more information, or contact Michael McConnell at (218) 828-0110.
CALGARY, AB CANADA NOVA Chemicals Corporation (“NOVA Chemicals”) and Plastic Energy have entered into an agreement to explore the feasibility of developing a pyrolysisdriven advanced recycling facility in the Sarnia, Ontario, region. If constructed, the facility would be the largest of its kind in Canada with a potential initial capacity of 66kt per annum.
“Post-use plastics offer tremendous value to furthering the circular economy, and our teams at NOVA Chemicals work daily to innovate new and collaborative ways to extend the lifecycle of our products and plastic packaging,” said Greg DeKunder, VP, NOVA Circular Solutions. “This agreement with Plastic Energy is a prime example of two companies working together to create timely, effective, and sustainable solutions that will help us make progress towards our 2030 recycled plastics ambitions, while diverting hardto-recycle segments of plastic waste away from landfills.”
Plastic Energy is one of the world’s leading advanced recycling technology companies through use of its patented TAC™ process to treat post-consumer plastic waste. Recycled polyethylene manufactured using Plastic Energy-produced feedstock, called TACOIL™, has identical properties to virgin polyethylene and can be used in food contact and high-performance applications, helping manufacturers and packagers achieve their recycled content goals. Plastic Energy has two commercial recycling plants in Spain that have been in operation for 7 years, alongside new projects in Europe and Asia.
“We are pleased to sign this agreement with NOVA Chemicals to explore the scope for our first advanced recycling project in Canada,” said Carlos Monreal, Founder and CEO of Plastic Energy. “Advanced recycling will continue to be important for the North American market by providing a solution for incorporating recycled content into food-grade packaging. Together with NOVA Chemicals, we aim to reduce the amount of plastic waste ending up in landfills, incineration, or as leakage into the environment, which is important for the circular economy in Canada.”
NOVA Chemicals recently announced its aspiration to reach 30 percent recycled content as a share of its total polyethylene sales by 2030 in its Roadmap to Sustainability Leadership, including its commitment to build a state of the art mechanical recycling business and continue exploring world-leading and proven advanced recycling technologies. If built, this new facility would see NOVA Chemicals build on its already CAD 2 billion investment into Ontario to inject additional new technology, jobs, and long-term viability into the local and Canadian economies.
NOVA Chemicals, headquartered in Calgary, Alberta, Canada, has nearly 2,500 employees worldwide and is wholly owned by Mubadala Investment Company of the Emirate of Abu Dhabi, United Arab Emirates. Learn more at www.novachem.com or follow us on LinkedIn.
GARLAND, TX, USA Cole Industries is pleased to announce the acquisition of Norstar Aluminum Molds, Inc., including the RotoMart business unit. Norstar, which operates out of two facilities in Cedarburg, WI and Middlefield, OH will strategically complement Cole’s facility in Garland, TX. Both companies are longstanding mold makers for the rotational molding market.
“We are thrilled to partner with Sandy and the entire Norstar and RotoMart team – from the back office to the shop floor. We are excited about the additional capabilities and the combined business, and we look forward to being better able to service our customers from 3 well-situated facilities. This is a win-win for our employees and our customers as we position our business for longterm success with strong foundries and meaningful CNC capacity. We look forward to continuing to find ways to grow and improve so that we can better support the rotational molding community,” said Austin Miller, President of Cole Industries.
“I am very pleased to have Norstar join the Cole Industries family who understands and supports not only the rotational mold making business but our markets and customers, as well. I see this as a strategic alliance which will provide opportunities for our employees and better service for our customers,” added Sandy Scaccia, President and Owner of Norstar.
Austin Miller is President and Owner of Cole Industries. Cole Industries designs and manufactures cast aluminum molds for the rotational molding industry.
Sandy Scaccia is President and Owner of Norstar Aluminum Molds, Inc. Norstar designs and manufactures cast aluminum, CNC machined aluminum, and fabricated molds for the rotational molding industry. RotoMart sells mold enhancement parts, replacements parts, and consumables.
For more information, contact Austin Miller at austin@coleindustries.com.
Centro, Inc.’s newest facility in Hampton, Iowa
NORTH LIBERTY, IA, USA — Centro, Inc. announces the addition of a 30,000 sq. ft. building to expand production capacity throughout the Midwest and accommodate the rapid growth of current demand and future business growth.
The new facility located at 1235 Imperial Road houses two rotational molding machines and employ over 40 Associates.
“This expansion represents continued confidence in our markets and our future business prospects. This, our 11th location, is an exciting opportunity in Hampton, IA, which is a terrific Midwest community,” said Brian Olesen, President & CEO of Centro, Inc. “I really couldn’t be prouder of all Centro Associates that create opportunities for our business to grow through execution in a very challenging time.”
“Centro would like to thank the Franklin County Development Association and City of Hampton for their partnership.” said Nick Hansen, Chief Financial Officer of Centro, Inc. “We have been very pleased with the local and community support and look forward to being a part of the Hampton community.”
Centro, Inc., headquartered in North Liberty, Iowa is the largest custom rotational molder in North America. The company designs and manufactures custom rotational molded product for industry leading Original Equipment Manufacturers in markets such as Agriculture, Construction, and Lawn & Garden.
Since 2021, Centro has added 8 rotational molding machines into their operations to support growing customer demand. The Hampton Business Unit will be the 11th Centro facility added to their global footprint, and falls on the heels of a successful startup in Cascade, IA nearly 1 year ago.
The company employees nearly 1,200 associates and operates domestic facilities in Iowa, Wisconsin, Illinois, North Carolina, North Dakota, and international facilities in Northern Ireland and Brazil.
For more information or to learn about employment opportunities, please visit centroinc.com.
Chevron Phillips Chemical has completed construction of the world’s largest on-purpose 1-hexene unit in Old Ocean, Texas, with operations set to begin at the plant by early September, company officials recently announced.
The company celebrated its new 1-hexene unit with a ribboncutting ceremony at the Old Ocean site, which included remarks by elected leaders and CPChem executives.
New unit increases CPChem’s 1-hexene capacity
CPChem’s investment in the new unit brings its total U.S. 1-hexene capacity up to 646 thousand tons per annum. The new unit’s location provides additional flexibility and production capacity to meet anticipated demand from our growing customer base.
CPChem has been operating two full-range alpha olefin units and one on-purpose 1-hexene unit at its Cedar Bayou plant in Baytown, Texas. CPChem’s new unit in Old Ocean will surpass Baytown as the world’s largest on-purpose 1-hexene unit. The new unit will use the latest iteration of CPChem’s proprietary, on-purpose technology to produce exceptional-purity 1-hexene, a component in the production of polyethylene.
“This represents an exciting step forward in our manufacturing
capabilities, and I am incredibly proud of the work it has taken to get us to this point,” said Bruce Chinn, President and CEO of CPChem.
The 1-hexene unit has become a major economic engine for the region, joining CPChem’s other assets in creating jobs and adding to the local economy. In addition to increased production capacity, this project created more than 600 construction jobs and 50-plus full-time positions.
In 2022, CPChem spent $31.5 million with more than 70 Brazoria County vendors and suppliers for operating materials, equipment, and services for the facility. CPChem spent an additional $1.4 million for catering, office supplies, and other indirect consumable items and services.
Investing in the community is also part of CPChem’s vision to serve as a neighbor of choice, said Jose Trevino, plant manager at the Sweeny, Clemens, and Old Ocean facilities.
“We take pride in investing time, talent, and resources to make a lasting impact in the surrounding communities,” Trevino said.
CPChem has invested in education like the CPChem Career
and Technical Education Center in Sweeny Independent School District and supported scholarships at Brazosport College and Wharton County Junior College. “These investments help prepare generations of local students for careers in our industry,” he said.
Other CPChem community investments include support of local healthcare options like the Sweeny Community Hospital and Matagorda County Medical Center and the Friends of the River San Bernard organization. “And we strive to increase economic prosperity by supporting non-profits like United Way, True to Life Ministries, and Communities in Schools,” Trevino said.
CPChem leverages advances in design to reduce emissions
CPChem leveraged the latest advances in process design to reduce emissions while maximizing production at the new unit. Resource efficiency and reduced emissions are both central to the company’s sustainability strategy.
“Aligning our investment strategy to our sustainability goals is a critical component to our business strategy, and this is a great example of balancing our sustainable commitments with manufacturing growth,” Chinn said. “The new asset harnesses the latest advances in process design to maximize production, optimize resource management, and reduce emissions.”
National survey respondents rated employers on benefits, working environment, work-life balance, training and career progression, company image, corporate culture, sustainability awareness, and proactive management of a diverse workforce. CPChem earned five out of five stars.
“This accolade reflects our ongoing commitment to fostering a workplace where our employees thrive, innovate, and grow,” said Maricela Caballero, Senior Vice President of Human Resources for CPChem.
“At CPChem, we believe that a supportive environment, coupled with a culture of empowerment, is the way to succeed,” she said. “This recognition energizes us to continue prioritizing employee well-being and nurturing a culture that celebrates diversity, encourages learning, and drives both personal and professional advancement.”
Newsweek and the data firm Plant-A Insights Group created the list by gathering public data and anonymous survey responses from around 62,000 American workers about their current or former employers, or the employers of people in their circle.
Plastics and Rubber events will cover Thailand, Indonesia, and Vietnam from 2024 Messe Düsseldorf Asia and Informa Markets. Two of the region’s leading international exhibition organisers have announced a landmark partnership that will see the consolidation of their plastics and rubber trade exhibitions in Southeast Asia.
From 2024, the new alliance will see the two parties jointly organise the Plastics and Rubber series of exhibitions, kick starting with Plastics and Rubber Thailand, which is scheduled to take place from 15 to 18 May 2024 at BITEC, Bangkok.
The strategic alignment of the plastics and rubber portfolio by Messe Düsseldorf Asia and Informa Markets will see them streamline their respective plastics and rubber exhibitions in the region into three anchor events. Starting in 2024, the partners will jointly organise Plastics and Rubber Thailand, and Plastics and Rubber Indonesia, in addition to Plastics and Rubber Vietnam, which has been a long-established collaboration since 2008.
Aimed at harnessing collective capabilities and expertise of both partners to deliver an enhanced business experience for the industry, Gernot Ringling, Managing Director, Messe Düsseldorf Asia, said: “Our alliance with Informa Markets builds upon a long history of successful partnerships in the region. By consolidating the plastics and rubber trade exhibitions to now include Thailand and Indonesia starting in 2024, we are poised to enhance our customer experience both locally and internationally, delivering even greater value for business growth, especially against the backdrop of industry sustainability and circularity goals.”
“This latest endeavour amplifies our regional presence and further streamlines both our efforts to serve the Southeast Asian markets effectively. Following in the successful footsteps of our joint partnership with Plastics and Rubber Vietnam in Ho Chi Minh City and Hanoi, with Plastics and Rubber Thailand and Plastics and Rubber Indonesia, we are paving the way for the absolute best local and regional platforms for international businesses in the most dynamic markets in Southeast Asia within the ever-evolving plastics and rubber landscape,” Ringling added.
The synergy will capitalise on Informa Markets’ deep regional insights and connections, complemented by Messe Düsseldorf Asia’s extensive global expertise in plastics and rubber and multisectorial competence, including their connection with K, the world’s leading plastics trade fair organised by Messe Düsseldorf.
Ian Roberts, Vice President, Informa Markets (Asia), expressed enthusiasm over this partnership and echoed similar sentiments. He said: “Our collaboration with Messe Düsseldorf is a continuation of our successful joint ventures, highlighting our shared commitment to deliver industry-leading experiences. By concentrating our efforts and consolidating the number of plastics and rubber events in the region, we aim to create an unparalleled experience for exhibitors and visitors, offering enhanced business opportunities and thus maximising the impact of each exhibition.”
Roberts added; “Together, we are ushering in a new era of innovation, collaboration, and mutual growth, which is testament to our shared commitment to advancing the industry and the region.”
The plastics and rubber industries in Thailand, Indonesia, and Vietnam play pivotal roles in the global market. Thailand has emerged as a leading manufacturer and exporter of plastic and rubber products, serving key markets such as China, Japan, India, and the ASEAN region. Similarly, Indonesia and Vietnam are crucial players in this sector, contributing significantly to the regional and global supply chains.
For more information on the first edition of Plastics and Rubber Thailand, go to: www.plasticsrubberthailand.com.
Over 1,400 Machines in Over 60 Countries
It is with great pleasure that we introduce the latest “Special Edition” of the ARMO Rotational Moulding Showcase publication, which focuses on showcasing innovative products in the rotational moulding industry.
This issue is dedicated to showcasing the many advantages of rotational moulding, as well as exploring future trends and promoting information sharing within the industry.
Rotational moulding is a versatile manufacturing process that has been used for decades to produce a wide range of products, from large tanks and containers to small toys and household items.
In recent years the global industry has continued to push the boundaries to further prove the capabilities of Rotational Moulding. While there has been great development within the area of specialised materials and improved technology there still seems to be an opportunity for growth and development in this area.
Looking to the future, we see exciting trends emerging in the rotational moulding industry, including the use of new materials and technologies, as well as a growing focus on sustainability and environmental responsibility.
ARMO is represented by 12 associations from all over the globe and prides itself in what has been achieved over the years.
As ARMO, we are committed to promoting information sharing and collaboration within the rotational moulding industry. We believe that by working together, we can continue to drive innovation and growth in this dynamic and important sector.
We hope that you find this publication informative and engaging, and we look forward to your feedback and contributions as we continue to explore the many opportunities and challenges facing the rotational moulding industry.
Sincerely,
Wayne Wiid ARMO Chairman wayne@pioneerplastics.co.zaLooking to the future, we see exciting trends emerging in the rotational moulding industry, including the use of new materials and technologies, as well as a growing focus on sustainability and environmental responsibility.
ARMO Rotational Moulding Showcase is an annual marketing publication by the Affiliation of Rotational Moulding Organizations (ARMO) and published by JSJ Productions, Inc.
ARMO Board of Directors
Past Chair & IT-RO Representative – Katia Zoppetti, DRAM S.r.l. katia.zoppetti@dramsrl.com
‘Rotopol’ Representative – Dr. Marek Szostak, Poznan University of Technology marek.szostak@put.poznan.pl
ARMSA Representative – Wayne Wiid, Pioneer Plastics wayne@pioneerplastics.co.za
Past Chairman & BPF Representative – Martin Spencer, Unique Roto Martin@UniqueRoto.com
ARM Representative – David Smith, H. Muehlstein DLSmith@Muehlstein.com
AFR Representative – Francois Kieffer francois.kieffer@bwt.fr
Anipac Representative – Eduardo Guizar, Spincraft eguizar@spincraft.onmicrosoft.com
ARMA Representative – Scott Magill, Plastic Tanks QLD scott@ptq.com.au
Past Chairman & ARM-CE Representative – Oliver Wandres, MAUS ow@maus-gmbh.de
Nordic ARM Representative – Ronny Ervik, Norner ronny.ervik@norner.no
RPC – CPPIA Representative – Jacky Wang, Zhejiang Rotoun Plastic Technology Co., Ltd. jacky@rotoun.cn
Past Chairman & StAR Representative – Ravi Mehra, International Consulting - Maramehra LLC maramehra@aol.com
Publisher
Publisher – JSJ Productions, Inc.
Chief Editor – Susan Gibson JSJ Productions, Inc. susan@jsjproductionsinc.com
Editor & Marketing Director – Jennifer Gibson JSJ Productions, Inc. jennifer@jsjproductionsinc.com
Designer – Anya Wilcox JSJ Productions, Inc. awilcox@designintersection.com
Internet & Digital – Jason Cooper JSJ Productions, Inc. jason@jsjproductionsinc.com
Distribution – Sheryl Bjorn JSJ Productions, Inc. sheryl@jsjproductionsinc.com
Legal – Joseph V. Gibson, IV JSJ Productions, Inc. jvg@jsjproductionsinc.com
Editorial Contributors
Alvin Spence, Centro Incorporated ASpence@centroinc.com
Susan Gibson, JSJ Productions, Inc. susan@jsjproductionsinc.com
Product Showcase / Photo Contributors
Remote Operated Water Rescue Craft - India
The Flex Box - South Africa
Foot Pedal Wheelie Bin - India
Tenjam Shayz™ In-Pool Lounger - USA
Recycled Bead Tank - Australia
Chubby - Italy
Ferrari Jumps & Trifectas - Australia
Uncle Dan’s USA T-Post Feeder - USA
Inquiries
info@armo-global.org / armo-global.org / rotoworld@rotoworld.com
Reproduction
All Copyrights belong to ARMO and in no part may this publication be reproduced or transferred through any digital or electronic means, photocopied, or otherwise without the written consent of ARMO and the Publisher, JSJ Productions, Inc.
ANIPAC THE MEXICAN PLASTIC ASSOCIATION
www.anipac.com
Herschel # 188, Col Anzures
Mexico, D.F.
Miguel Hidalgo, 11590
Eduardo Guizar
(55) 62 73 88 44 • +27 865682675
ARM - ASSOCIATION OF ROTATIONAL MOLDERS
www.rotomolding.org
North America
USA
3400 W Stonegate Blvd, Suite 2315 Arlington Heights, IL 60005 +1 630-942-6589
Adam Webb adamw@rotomolding.org
AFR - ASSOCIATION FRANCOPHONE DU ROTOMOULAGE
www.rotomoulage.org
French-language countries
France
Immeuble Danica B 21 Avenue Georges Pompidou, 69003 LYON, France +33 67 0452 117
Francois Kieffer, Chairman
Anne De Lansalut, Permanent Member of the Board a.delansalut@rotomoulage.org
ARMSA - ASSOCIATION OF ROTATIONAL MOULDERS SOUTHERN AFRICA
www.armsa.co.za
Southern Africa
Johannesburg South Africa
P.O. Box 8184, Centurion, 0046, South Africa
+27 72 245 5310
Gary Wiid - Chairman info@armsa.co.za
SOCIETY OF ASIAN ROTOMOULDERS (STAR) www.starasia.org
India and Asia
“ROTOPOL” ASSOCIATION
www.rotopol.put.poznan.pl
Poland
60-965 Poznan, Piotrowo 3 street +48-61-6652776 • +48-601785126
+48-61-6652202
Dr. Marek Szostak, President of, ROTOPOL, Association marek.szostak@put.poznan.pl
NORDIC ASSOCIATION OF ROTATIONAL MOULDERS (NORDIC ARM)
www.nordicarm.org
Scandinavia
Iceland
Gunnarsbraut 12, 620 Dalvk, Iceland
+354 863-5373
Ronny Ervik ronny.ervik@norner.no
IT-RO ITALIA ROTAZIONALE www.it-ro.it/it
Italy
E. Brigatti, 12 - 20152 - Milano (MI) +39 348 7652 560
Katia Zoppetti, President info@it-ro.it
3rd Floor, 36 Krishna Market, Kalkaji, New Delhi- 110019, India
+91 9810305356 • +91 11 41634952
Ravi Mehra, Founding Chairman StAR S.B.Zaman, Executive Director StAR sb.zaman@starasia.org
RPC-CPPIA
www.chinarotomoulding.com/
Greater China Region including Mainland China, Taiwan, Hong Kong and Macau
RPC-CPPIA
Room 202, Lon 72, No. 1501, Tong Pu Road, Pu Tou District, Shanghai, China 200333
86 21 6237 1991 • 5271 5002
86 21 6237 1991 • 5271 5002-8005
Mr. C.C Shi, Secretary-General, Jacky Wang, Foreign Affairs Officer – for foreign affairs (English communication) jacky@rotoun.cn
BPF ROTATIONAL MOULDERS GROUP
www.bpf.co.uk
United Kingdom
6 Bath Place, Rivington Street
London EC2A 3JE
+0044 (0)207 457 5013 • +44 20 7457 5045
Graeme Craig, BPF Rotational Moulding Group Executive gcraig@bpf.co.uk
ARM-CE -ASSOCIATION OF ROTATIONAL MOULDERS CENTRAL EUROPE
www.rotational-moulding.de
Central Europe Germany
Keltergrasse 6, D-76356 Weingarten +49 721 948 7412 • +49 721 948 7444 Oliver Wandres info@rotational-moulding.de
ARMA - ASSOCIATION OF ROTATIONAL MOULDERS AUSTRALASIA LTD
www.rotationalmoulding.com
Australasia
Australia
PO Box 237 Moonee Ponds VIC 3039 Australia
+61 (0)404 265 887 • +1 630 790 3095
Michelle Rose
michellerose@rotationalmoulding.com
This product can be operated from up to 1 km Line of Sight and Radio Communication up to 2 kms. This can be deployed from a helicopter, ship from a height of 10 meters near a drowning person and steered using a remote.
A drowning person can hold on to the antiskid handles and can be pulled to shore / boat / jetty.
Designed for Saif Marines Pvt Ltd. by Satish Gokhale and team Design
Directions Pvt. Ltd. and manufactured by Vinodrai Engineers – India
Drowning is the 2nd largest cause of deaths, and to save a person struck in this panic situation the golden time is only 3 minutes. There are cases when there are no lifeguards on the beaches or it is difficult to reach the person in distress using conventional lifebuoys.
Patented Remote Operated Water Rescue Craft, is a battery powered and jet propelled lifebuoy which is compact and fast (ability to travel at 7 m/sec on
water OR 14 Knots) and can be easily manoeuvred to reach the person in distress. A drowning person can hold on to the antiskid handles and can be pulled to shore / boat / jetty. In case it is observed that the person to be rescued is unconscious, a person is sent along with the craft to help the drowning person since the craft can pull up to 3 persons.
This craft is better in many ways than
its global competitors. The main pluses over the competition is the high speed, stability in choppy conditions, and its self-righting capability and good visibility of the craft in choppy sea conditions.
The Rotational Moulding process was used for a much better quality control and uniform hull. The product is manufactured utilising 100% UV stabilized, recyclable HDPE material, which is best suited for all types of waters.
Being a product deployed on water, water tightness is an integral part of the design, and very important to protect all the electronic and electrical components. This was specially taken care of in each and every stages of the design. End goal was to make it easy to manufacture in bulk using the CNC machined moulds and cooling fixtures to avoid and reduce unwanted distortions of the moulded parts.
The overall size considerations were based on how the craft was going to be thrown in the water. It had to be as compact as possible and as light as possible.
This product can be operated from up to 1 km Line of Sight and Radio Communication up to 2 kms. This can be deployed from a helicopter, ship from a height of 10 meters near a drowning person and steered using a remote. In case the craft turns turtle when deployed in choppy sea conditions, it self-rights or straightens itself by buoyant self-righting structure, which doubles as visibility block to spot the craft in sea - a unique feature amongst all global competition.
The designers are working on add-ons to transport, food, medicines, clothes, etc. during flood situations. 180 units have been successfully inducted in the Indian Navy.
A home gym station designed to be a personal home gym that looks like a modern piece of furniture when not in use.
Designed by Nick Swardt and manufactured by Pioneer Plastics – South Africa
The Flexbox is a Home Gym Station designed to be a personal home gym that looks like a modern piece of furniture when not in use. The product is manufactured by Pioneer Plastics with our client seeing the need for a functional, yet aesthetically pleasing, home gym station.
The box is designed as a home gym system with one of the main features being that the user can store his or her weights inside, while the lid acts as an incline bench to exercise the different muscle groups.
Due to its smart design, the home gym system doubles as an item of furniture which, when shut, will happily fit seamlessly into the average living room, but when the resident or guests wish to work out, all manner or gym exercises can be performed and in flash too.
The product consists of thirty-three individual parts, of which 5 are rotational moulded and polyurethane foamed for stiffness. The moulds are CNC machined moulds designed and manufactured in-house at Pioneer Plastics. The design intent was to develop a high-quality product aimed at fitness enthusiasts that is aesthetically appealing when not in use. The Flexbox also has numerous moulded inserts, and the design allows for an inserted Bluetooth speaker.
The product was designed together with a South African entrepreneur, now resident in the USA, coming up with the concept. Nick Swardt, Technical Manager at Pioneer Plastics, designed and developed the final product.
This is a brand new product launching this year with the first orders received to be supplied to the South African market as well as exported soon.
The user can store his or her weights inside, while the lid acts as an incline bench to exercise the different muscle groups.
Designed by Satish Gokhale and team Design Directions Pvt Ltd. and manufactured by Frontier Polymers Pvt Ltd. – India
In an era of increasing environmental awareness and sustainable practices, waste management solutions have become an integral part of every establishment’s operations. Catering to the needs of hotels, restaurants, airports, and similar high-traffic venues, we proudly present the revolutionary Foot Pedal Wheelie Bin – a game-changer in waste disposal efficiency and hygiene.
Key Features and Benefits
Hands-Free Operation: The hallmark of our Foot Pedal Wheelie Bin is its hands-
free design, allowing users to dispose of waste without the need for direct contact to the lid. In high-traffic areas like hotels, restaurants, and airports, where hygiene is paramount, this feature drastically reduces the risk of crosscontamination and the spread of germs. The strategically positioned foot pedal ensures that waste disposal is effortless and convenient. Users can easily open the bin’s lid using their foot, making it suitable for people of all ages and physical abilities. Full closure lid coupled with its sturdy built quality, helps contain
Crafted from highquality, eco-friendly materials, our wheelie bin is designed to withstand the rigors of heavy daily usage.
odours effectively. This is especially crucial in hospitality settings where guest satisfaction is paramount.
Crafted from high-quality, eco-friendly materials, the wheelie bin is designed to withstand the rigors of heavy daily usage. Its robust construction ensures longevity, minimizing the need for frequent replacements and reducing the overall environmental impact. Made from Hexene polymer and UV stabilised, non-fading colours, and utilising cast aluminium tooling, these bins can withstand harsh outdoor weather conditions for years to come.
We understand that different establishments have unique aesthetic preferences. Frontier Wheelie Bins are available in a range of three sizes of 70, 90, and 120 Liters. For waste separation, different colour lid options are available. Colour coded wheel caps adds to the overall aesthetic design appeal allowing seamless integration into your venue’s existing decor.
The most comfortable pool lounger in the world. Designed by Tenjam and manufactured by Tri-Ven – USA
Tenjam furniture created Shayz - the most comfortable in-pool lounger in world. Featuring a patent pending Speed Fill Ballast System and three heights of snap-in risers for various pool depths up to 17”. Armrests were added for easier entry and exit from the seat and a “social” backrest angle is a more comfortable position for talking, watching, reading, and sipping a refreshment. Designed to comfortably fit the entire family from children to adults. Tenjam’s focus on comfortable and easy to use rotomolded furniture is creating a splash in the pool market.
Rotomolding is used to optimize durability, functionality, comfort, aesthetic appeal, design-for manufacture, and integration of differentiating features:
• Cupholders.
• “Speed-Fill” ballast system.
• Speed emptying system.
• Flow-through seats.
• Seat drain.
• Integrated handles.
• Stackability.
Shayz™ is offered in 14 colors with high UV stability to ensure color vibrance in outdoor environments. It has optional risers (three optional heights: 9”, 13” & 17”) that snap into the bottom of the Shayz™ lounger to accommodate various water depths.
Tenjam’s focus on comfortable and easy to use rotomolded furniture is creating a splash in the pool market.
Designed and manufactured by Suncoast Waste Water Management – Australia
Rotomoulding is a sintering process traditionally done with micronised PE but, not essential as it is possible to sinter bead in the same process.
Suncoast Waste Water Management manufactures a multi-layered LLDPE tank incorporating three layers. The outer layer consists of a melt compounded virgin micronised powder. The middle layer consists of a recycled PE in a Bead form, this polymer is NataLab Batch tested to check conformity to our AS/NZS Standard. The inner layer consists of micronised PE to produce a smooth inner layer giving the tank the required impact resistance. Tanks are produced using a templogger for correct multilayer points and piat.
OzziKleen products can recycle water and waste water in a recycled tank. 75% of material in a tank can be recycled LLDPE.
Ozzi Kleen Sewerage Systems act as a digestive system using a unique cyclic
fully aerobic sewage treatment process. This means there is no septic process, so no septic smells, it’s environmentally friendly producing nutrient rich water to reuse on gardens and is cost efficient to run (only half the running cost of other aerobic sewerage systems).
The heavy-duty polyethylene Ozzi Kleen sewerage system tank is up to 20mm thick and is, weight for weight, 100 times stronger than concrete. The material has a 500-year half-life. As the Ozzi Kleen RP10 sewage treatment system tank is roto-moulded and completely seamless, there is no risk of seepage, leaking, or root intrusion.
The Ozzi Kleen RP10 sewerage system tank is not affected by the acidity of sewage. Polyethylene materials are often used to store hazardous chemicals. The mechanical components are all designed and constructed to ensure years of effect, trouble-free service, and are backed with a full manufacturer’s warranty.
OzziKleen products can recycle water and waste water in a recycled tank. 75% of material in a tank can be recycled LLDPE.
Chubby is a perfect mix between the beauty of the lines and the comfort of the seat.
Designed Marcel Wanders for SLIDE Srl – Italy
The armchair Chubby, created by the famous designer Marcel Wanders, is one of the best products of the whole Slide production. Chubby is a reinterpretation of Crochet Chair: it has got the same design but, it is made in polyethylene, suitable for every kind of people. The design armchair Chubby is suitable with every kind of settings, for contract, events, or private houses.
Thanks to its sinuous and linear design, Chubby is a perfect mix between the beauty of the lines and the comfort of the seat.
The Chubby Collection includes the Chubby, Chubby Low, and Chubby Side
Table. It began production in 2008. Its dimensions are 130 x 120h 56 cm (seat H 27 cm). Its packaging dimensions are 131 x 121 x 57 cm and packaging volume 0,903 m3. It comes in thirteen standard colors and 8 lacquered (glossy/matt) finishes. Its weight is 25 Kg.
The product is made from Polyethylene with the rotational moulding process. It is resistant to extreme temperatures (-600°C to +800°C). It is UV resistant and has high tensile strength. SLIDE® has a closed production cycle with no health prejudicial emissions and complies with ecological sustainability rules.
slidedesign.it
The design armchair Chubby is suitable with every kind of settings, for contract, events, or private houses. Thanks to its sinuous and linear design, Chubby is a perfect mix between the beauty of the lines and the comfort of the seat.
Designed and manufactured by NexGenRoto in conjunction with Massey Designs – Australia
NextGenRoto Jumpstarts are solid and versatile. They can be used at several different heights, are safe for the horse and rider, and have no sharp edges. The product is UV stabilised and made super strong. It can be filled with water for extra stability, is easy to stack or leave on the arena, takes standard wooden poles, and comes in a range of colors.
The Jump is a definite money saver because you can make multiple jumps with one set of jump wings. It is a complete all-rounder as it will do it all: Cavaletti’s, Single Jump Spreads, Boxers, and Oxers.
The Ultimate Jump has 9 different heights, ranging from 11cm to 110cm, and the best part is you don’t need cups (no more losing jump cups). The jumping heights are imprinted into the jump for easy setup. It is very stable at 8kgs each side, which makes it easy to move around but can be pegged down or filled with water for stability.
The NextGenRoto Trifecta is a saddle rack, grooming/tack tray, and mounting block. It is the most versatile product on the market. The saddle rack fits easily into the back seat, car boot, or float. The saddle will fit perfectly on top, and the shape is protected and cannot be compromised. The Grooming Tray is designed for packing tack into the grooming tray provide and slide tray in the caddy storage area. The Mounting Block is purpose designed to mount a horse. It reduces strain on the horse’s back and helps maintain the rider’s
balance. It stops stirrup leather being stretched, is used for a seat, and is perfect for quick saddle changes. It has hands on both ends and 2 anti-slip steps. Very stable and sturdy, the Trifectas are light weight, UV stabilized, and have no sharp edges. Their weight is 6kg, 45cm high x 43cm wide x 54cm long. The weight rate is 130Kg.
At NextGenRoto, we’re not just about water tanks. Our talent and expertise in rotational moulding means that if you’re looking to develop a customised product, we have the experience and commitment to get the job done to the highest of standards.
We take pride in our work, and we ensure that the concept you need manufactured is delivered on time, and of the highest quality. From the materials we use, to the experts who lead our custom design projects, we make certain that what we produce is right every time. Our quality control method is of the strictest standards, we don’t cut corners, they are industry-leading quality control procedures. An idea is all you need to get started. Our development process is simple and straightforward.
nextgenroto.com.au
The Jump is a definite money saver because you can make multiple jumps with one set of jump wings. It is a complete allrounder as it will do it all: Cavaletti’s, Single Jump Spreads, Boxers, and Oxers.
Designed by Dan Ross and manufactured by Ken Ross Rotational Molding – USA
The Uncle Dan’s T-Post wild game feeder was designed using an ordinary T-Post to secure the feeder outdoors. Using customer-supplied T-Posts keeps the retail price lower than competitors who rely on leg kits produced in China and supplied with their feeders. Using a T-Post driven into the ground provides an exceptionally secure system that is resilient against game or livestock destruction. The four individual feed ports are equipped with slide gate valves to regulate the flow of different types of feeds - corn, protein pellets, finely ground attractants, and feeds. This innovative game feeder system is designed with the hunter in mind and built to last in all weather conditions.
Dan Ross, aka “Uncle Dan,” has been manufacturing products for the hunting industry for over 30 years and, as an avid hunter for 60 years, he has the experience and knowledge to design products that work for the hunter. All Ken Ross products are designed by Uncle Dan and his team.
The feeder is rotationally molded of Jerico Plastics Stone Effect PE, using threaded inserts and graphics. All secondary operations are performed using CNC routers.
Ken Ross Incorporated, Rotational Molding manufactures the feeder. Jerico Plastic’s Stone Effect material formulated in uniquely specified colors bring the whole package together into a game feeder that is solidly constructed and very attractive to the hunter and the entire outdoor/hunting industry. All products are manufactured in-house using tooling that is produced in a Ken Ross in-house tooling shop.
This innovative game feeder system is designed with the hunter in mind and built to last in all weather conditions.
Much has happened since the last ARMO review of the industry published 4 years ago[1], approximately 9 months prior to COVID-19 taking a stranglehold of virtually every economy around the world. Prior to COVID, the rotational molding industry was in a strong position, with many sectors enjoying healthy growth. Material prices were reasonably stable, helping molders to be competitive with other processes. The industry was surging, and the future looked promising, with one major exception being the tight labor markets in established regions of the world making it exceptionally difficult to fill open positions. Also, the manufactured product value per labor hour ($/hr) was in decline in the US and there was much discussion about the need to automate to reduce labor content and improve productivity[2].
During the COVID years unemployment initially surged and many rotational molding market sectors took a sharp decline. Manufacturing companies came to terms with how to manufacture safely and avoid the spread of the virus. Rotational molders had to react quickly and develop new systems and procedures to protect their employees, which proved to be challenging for this labor-intensive process. Some of the industry’s most faithful employees, who were at or near the end of their careers, decided the risk of working outweighed the gain and opted for retirement. This was the case for many other industries at the time. Global economies went into decline initially and demand for manufactured products waned. It was a very worrying and uncertain time for many molders. The only good news at that particular moment in time was that labor was abundant…but that did not last for long!
Towards the end of 2020, approximately
6-9 months after COVID started, several rotational molding markets started to recover to unexpected high levels of demand. Markets that involved outdoor activities, such as kayaking, boating, camping, etc. remained largely unaffected by COVID and demand for rotationally molded products in these sectors soared. Before we knew it, the labor crisis was back again, and productivity was being greatly impacted by the health and safety measures put in place to prevent the spread of COVID. During this time the sale of rotational molding equipment surged, and many
businesses looked to add capacity. This was caused by increased demand, reduced productivity, and employees not wanting to work overtime, especially at the weekends. Also, mold builders experienced growth from new programs as well as molders needing additional cavities to meet the increase in demand. This was also a time when the lack of industry capacity led to several new companies emerging as they tried to overcome supply chain issues.
From late in 2020 through 2022, molders faced a variety of challenges as they tried to meet growing market demand. One of the greatest challenges came for the supply chain, with many suppliers
6-9 months after COVID started several rotational molding markets started to recover to unexpected high levels of demand.
struggling to obtain raw materials and provide on-time deliveries. As if that was not enough, prices started to escalate for supplied components and raw materials. Labor availability resurfaced again as a major constraint and labor costs increased as businesses competed for the locally available labor. This was a very challenging time for many businesses, but also an opportunity for those who could adapt quickly to grow market share and profitability. It was a time when businesses had to justifiably increase pricing in response to increasing costs, but part of the challenge was that purchased components and materials continue to rise, sometimes resulting in multiple price increases.
The ever-changing environment has resulted in no shortage of challenges for many molders. More recently, some market sectors that boomed during COVID are now in decline due to saturation, and so the cycle of change and the need for adaptability continues. For most businesses managing the decline of markets is much more difficult than managing a surge in business. This is especially true for those molders who added capacity to take advantage of the growth opportunities during COVID. This added capacity will no doubt bring concern to some, as a fall in demand will result in a very competitive marketplace.
Further challenges are now coming from the customer base, who absorbed significant price increases and now would like to see some relief and cost reductions. As molders look forward, one thing is for certain, they will need to have great adaptability to maximize the opportunities that lie ahead. Timely adjustments to business strategies will no doubt ensure competitiveness in an ever-changing environment.
For those trying to maintain a thriving, healthy business, the need for efficiency improvement and cost reduction is clear. It is imperative that molders find suitable technologies to either reduce the amount of labor or reduce the skills needed to manufacture high quality rotationally molded parts. Also, efficiency gains during processing need to be made to minimize machine downtime and maximize arm loading. This will drive technological developments to sustain a balance between the load/ unload cycle time and the other stages of the cycle. While automation is seldom easy, justification for investments is getting easier as labor costs increase and efficiencies decline. With the future likely bringing some harder and more competitive economic times, molders must work to improve these efficiency opportunities to sustain their businesses and be more competitive in the marketplace, which will in turn help to provide growth opportunities.
As molders look forward, one thing is for certain, they will need to have great adaptability to maximize the opportunities that lie ahead.
For those who are reading this article that are unfamiliar with the rotation molding process, the process is best suited to the manufacture of hollow plastic products of various sizes and shapes, with the ability to produce extremely complex geometries. The following information will highlight some of the industry’s most common applications, represented by several product categories. These products demonstrate why rotational molding competes favorably with all other manufacturing process. Here are several product families that are typical rotationally molded applications:
Perhaps one of the earliest and wellknown rotational molding applications is children’s toys. Toys, fitness equipment, and playground structures are extremely common rotomolded applications. For soft touch and flexible products, Poly Vinyl Chloride (PVC) is used. This material can replicate the most intricate of details, as seen in PVC dolls heads. Other toy products are manufactured from Linear Low Density Polyethylene (LLDPE) such as the Cozy Car, kitchen play sets, wagons, etc. These products tend to be brightly colored, thin-walled applications with rounded corners that are relatively easy to manufacture. However, to be competitive with other processes the cycle times for these products have to be very aggressive, requiring the application of automation and lean manufacturing methods. Playground structures are also a very common global rotational molding application because of the durability and weatherability of the Polyethylene (PE) material used.
Flotation of plastic has recently become a serious problem for the plastics industry, creating a negative perception regarding the use of plastics. However, PE’s buoyance, water resistance, weatherability, and toughness all help to make it an excellent choice for
rotationally molded flotation products. Fishing buoys, boat ramps, and floating docks are all common rotomolded products. Some floating docks incorporate either PE foam or Polyurethane (PU) foam to increase both strength and buoyance. Kayaks and canoes are also commonly rotationally molded, and often include PE foam. These types of products are typically molded using a rock and roll machine because of their geometry. Insulated coolers are also rotationally molded, and often include PU foam between the external and internal PE layer. This provides excellent insulation properties, allowing the contents of the cooler to remain chilled for several days.
Another very common rotationally molded product is chemical and water storage tanks, which come in a range of shapes and sizes and are globally manufactured using the rotational molding process. Tank volumes can be substantial, up to tens of thousands of gallons. Product design plays an important role to ensure the geometry has sufficient structure to support the tank contents load in the environment in which it operates. Quite often ribs are employed to enhance stiffness of the wall and/or wall thickness is targeted to areas of the tank that are subjected to the highest deflective loads. Typically, High Density Polyethylene (HDPE) materials are used for larger tanks with sufficient hoop strength to meet the functional requirements. Often carousel machines or rock and roll machines are used to manufacture these products. The applications for this type of product family include water storage or harvesting, static fuel storage, and chemical storage.
Products & Floor Cleaning
Containers, pallets, IBCs, totes, trash cans, dumpsters, etc. are all commonly rotationally molded products. Cases and containers can be highly sophisticated, for the purpose of carrying and protecting valuable goods. IBCs are commonly used for transportation of chemical products. Trash cans and dumpsters
The process is best suited to the manufacture of hollow plastic products of various sizes and shapes, with the ability to produce extremely complex geometries.
are also common applications for the process and can often incorporate recycled material. Single piece septic tanks can be manufactured using the rotational molding process. Floor cleaning equipment benefits from the process’s ability to mold highly complex geometries that are capable of holding cleaning fluids at elevated temperatures. The recent development of electrically heated molds has further enhanced the process’s ability to achieve uniform wall thickness for these types of applications.
Fuel tanks for tractors, construction equipment, trucks, marine engines, generators, compressors, lawn and garden equipment, etc. represents a significant rotomolding sector. Many of these products can be extremely complex in design and include an array of assembled components. For example, agricultural fuels tanks are typically one of the last components to be designed for the vehicle, which results in a very complex geometry to take advantage of any available space to maximize the tank’s volume. These types of applications can include several inserts, bosses, drain plugs, graphics, sending units, etc., all of which must be leak proof. The material of choice for these applications is crosslinked polyethylene because of its UV stability, low temperature impact strength, environment stress crack resistance, and its ability to pass various test requirements such as ECE 34. Crosslinked PE has also been used in combination with other materials that provide excellent resistant to hydrocarbon emission, to reduce fuel weight loss from gasoline tank applications. Many small off-road engines and marine fuel tanks benefit from this material combination to meet environmental regulations.
In addition to those previously mentioned, there are many other industries and applications that utilize the rotational molding process. These
include: air ducts, cargo beds, blower housings, hydraulic tanks (typically from Nylon 6 or 11), urea tanks, roofs, fenders, consoles, display cabinets, road barriers, traffic signs, laundry carts, furniture, plant pots, mannequins, hoppers, rickshaws, etc.
While the future of the rotational molding process is not in doubt, the challenges the industry has faced over the years have not significantly changed. The process remains unique, but heavily dependent on labor, which is becoming less available, less skilled, and more costly. To be competitive, molders must apply their entrepreneurial spirits to find creative solutions to reduce the cost to manufacture rotationally molded products. In order to do that, one of the most critical factors will be for molders to attract the right talent for these types of manufacturing positions. Staffing, managing the impact of rising labor costs, resin costs, and other inflationary costs are the real challenges that the industry faces today. Therefore, focusing on the work environment, production methods, training, equipment/tools, ergonomics, engagement, teamwork, career growth, and compensation needs to be a top priority to attract good employees and make them feel that manufacturing is a career worth pursuing. An energized and engaged team can do great things when pointed in the right direction. Another challenge for some molders will be the changing competitive landscape, especially in the US, as mergers and acquisitions have been extremely prevalent in recent years. It will be interesting to see if higher interest rates will cause a slowdown in the recent trend.
References:
To be competitive, molders must apply their entrepreneurial spirits to find creative solutions to reduce the cost to manufacture rotationally molded products.
Jerico is first in quality resins and compounds! We’ve made our name by providing vibrant colors, specialty blends, and recycled black, while focusing on being that one complete source for ALL your rotational molding compound needs. Now you can add natural PE to the list!
Time and again over the years, our team has responded to the changing times with resilience, ingenuity, resolve, and confidence. In true Jerico fashion, we developed sustainable and adhesion compounds, then
blended vibrant colors into both. Make no mistake, we are expanding and are focused on becoming your supplier of choice for rotational molding materials.
As we grow, we look for ways to improve so that we exceed your expectations and help you achieve success! Our mission is to be the go-to resource for resins and compounds that meet your precise specifications, arrive on time, and provide the consistent level of quality you have come to expect from Jerico!
In September, the ARMO rotomoulding conference in Poznan, Poland, will focus on the topic of “Sustainable Rotational Moulding”.
In our industry, the term sustainability is one of those buzzwords that is thrown around a lot and it is important for us to think about its meaning and how it applies to our business.
There are many definitions, but the one I like most is – “Sustainability is fulfilling the needs of the current generation without compromising future generations’ needs.”
There are many topics to discuss when it comes to sustainability, including change, carbon dioxide emissions, and NetZero.
As most rotomoulders use natural gas, the efficiency of converting this non-renewable fossil fuel into rotomoulded parts is poor. In general, the actual production of the final product consumes only 5 - 8% of the energy used by conventional machinery.
This is why our industry’s recent focus on improving energy efficiency and heating molds directly is a welcomed development. Several rotomoulding companies are now exploring alternative energy sources, including biogas and renewable electricity, to reduce their carbon footprint.
As we begin to realize that resources are finite, the concept of reducing waste, using fewer resources, and recycling have become more and more common, and rotomoulders and their suppliers are now discussing what else can be done to reduce waste and improve resource efficiency.
In my view the third main area of focus when considering sustainability in the industry is plastic pollution. As plastic pollution in streams, rivers, and oceans continues to grow, it is evident that we are “compromising the needs of future generations” as a result. The plastic pellets and powder handlers have a major responsibility not to contribute to this problem, and everyone should take part in programs such as “Operation Clean Sweep” and do everything they can to prevent plastic from entering the environment.
Another issue that is being forced onto the agenda is the end of product life. While I was in New Zealand recently, I discovered
that some moulders had developed recycling programs for old rotomoulded junction boxes and water storage tanks.
As a company that specialises in materials for rotational moulding, we take this subject of sustainability very seriously and have several projects, mostly related to materials that we are working on in different regions of the world. Indeed, we are supporting one of our employees Jake Kelly-Walley in studying for a PhD titled “A Sustainable Approach to Materials for Advanced Rotational Moulding Applications” at the Polymer Processing Research Centre at Queen’s University in Belfast.
At the forthcoming conference in Poznan, we will be giving an update on some of the areas we’ve been working on to help reduce energy and material consumption, to develop bio-based polymers and to incorporate post-consumer and post-industrial waste into consistently performing rotomoulding materials.
We are very much looking forward to discussing and sharing ideas at this global event, which will be attended by rotomoulders from all over the world. See you in Poznan
Queenstown remains a consistently stunning destination, and it has once again proven to be the ideal host for Rotomould. Upon arrival, delegates were captivated by the majestic mountains embracing the pristine Lake Wakatipu, along with the welcoming and relaxed atmosphere that enveloped us all.
The location’s allure for Australians was expected, yet I was pleasantly surprised by the international and local New Zealand industry participants who also decided to join. With a substantial turnout of over 115 attendees at the Millennium Hotel, it promised to be a great event.
We were fortunate to have Professor Dru Laws as the presenter for the Sunday morning Introduction to Rotational Moulding Workshop. The workshop encompassed crucial aspects of the rotomoulding process, such as material options, primary equipment types, processing parameters, process control techniques for enhancing part properties, and essential design guidelines. Attendees had ample opportunity for questions and engagement, and as they departed the workshop, they were already praising the exceptional quality of the information provided by Dru.
Rotomould23 commenced with an official Mihi Whakatau, featuring a warm welcome from esteemed local Māori elder,
Darren Rewi, followed by Chris Glenn, the President of ARMA. Chris emphasised the conference’s valuable nature as a platform to reconnect with like-minded industry leaders and renew friendships with familiar faces.
The afternoon sessions commenced with Professor Dru Laws leading a technical workshop on advanced rotomoulding. During the session, Steve Lewis, the General Manager of Vision Plastics, our session sponsor, provided insights into the internal dynamics of the mould using the Roto Rocket.
The first day of learning was truly remarkable, but the excitement continued as delegates and partners anticipated the Price Plastics Welcome Dinner in the picturesque surroundings. Attendees had the opportunity to unwind and savour locally brewed beer paired with delectable cuisine at a nearby brewhouse situated beneath the historic Edith Cavell Bridge, offering a captivating view of the Shotover River.
Day two commenced with a presentation by Trudi Duncan from Gyro Plastics and Bob Dedekind from Aspect Productivity Technology. Through a compelling case study of Gyro Plastics’ ongoing project in New Zealand, Bob and Trudi provided a comprehensive overview of how implementing the right software
can optimise a business. This was followed by Andrew Currie from Price Plastics openly discussing the valuable lessons learned from a finger amputation incident. He guided the audience through the incident’s unexpected occurrence, the subsequent investigation, and the implemented corrective actions while emphasising the compassionate care provided by the staff to the injured team member. The presentation was candid and forthright, which was appreciated by attendees.
Mark Jeffries from Portstar Plastics took the stage to deliver an authentic presentation sharing his firsthand experience as a newcomer in the rotational moulding industry during the initial 5 years of owning and operating his business. As outsiders, the Jeffries family sought a transformative change from their urban jobs in New Zealand’s major cities to embrace a rural lifestyle and venture into the world of rotomoulding. Facing a steep learning curve, they navigated the complexities of establishing a new business, adapting to a new home, and embarking on a fresh chapter in their lives. Mark’s presentation offered a unique perspective on the triumphs, challenges, and invaluable encounters with individuals, including the impact of COVID and natural disasters, which he candidly shared with fellow industry peers.
Sharon Zhu and Grant Palling of Rising Sun Rotomolding Machinery then provided us with an overview of their company and the advancements they have made for the industry and their clients.
Following the morning tea break, the Matrix Polymers Innovation Session commenced with Martin Coles, the Group Chief Executive, addressing the pressing concern of polyethylene supply security and its vital significance for the sustainability and continuity of rotomoulding, a current and highly relevant topic in our region.
Subsequently, Igor Silva, Design Manager at Rotadyne, shared his teaching involvement with design students and their utilisation of rotational moulding as a compelling case study. He showcased examples of student projects wherein they ingeniously incorporated second life concepts into products using both pre and post-consumer waste materials. The innovation session
concluded with Dr. Lei Wang discussing the global challenges associated with plastic waste reduction and recycling, along with highlighting the industry’s contributions in addressing these issues. Following the session, attendees transitioned into a sponsored lunch, finishing with delectable cupcakes.
After the lunch break, we introduced our first Ask Anything Panel Session, featuring esteemed panelists Professor Dru Laws, Bill Spenceley from Flexahopper Plastics Canada, Dario Masutti of Vision Plastics, and Ian Gough from Gough Plastics. The stage was graced with a wealth of knowledge for attendees to tap into. Toby Peacock from Q Tank skilfully facilitated the session, blending professionalism with a touch of levity to address some thought-provoking topics. Safety, future outlooks, 4-day work weeks, and AI were among the questions posed, and such panel sessions will be a recurring feature at future Rotomould events.
Stuart Mackenzie from STP Rotomachinery highlighted the distinctive modular shuttle systems provided by the Rotomachinery Group. Following this, Rob Miller of Rotoload presented on the concept of “Tomorrow’s Powder Automation...Today.” He discussed
the multitude of benefits, ranging from cost savings on resin to environmental enhancements and process improvements. Attendees had the opportunity to enjoy local beer accompanied by sausage rolls during the afternoon tea, which added a special touch to the Rotoload presentation.
Despite the initial concerns about the duration and complexity of the topic, Hugh Devereux-Mack from CertNZ delivered a remarkable hour-long presentation on the challenging subject of cyber security. His approach was both enlightening and educational, striking a balance between being informative and engaging. The
presentation received high praise from attendees and was particularly timely given the current landscape of cybersecurity concerns.
The day’s program concluded with Dr. Jeroen Wassenaar from Qenos discussing the prospects of advanced recycling and its potential in producing food-grade plastics incorporating recycled content. Wayne Solomon provided an update on Qenos’ status and extended a warm invitation to attendees to unwind at the Qenos Gala Dinner scheduled for the evening.
Delegates savoured exquisite wines and indulged in delectable, shared platters at the breathtaking Stoneridge estate, nestled in the
scenic Queenstown countryside, as they gathered around a roaring open fire. During the event, board member Brad Smyth presented the ARMA 20-year Membership Award to Formit Services, Galloway Group, La Plastecnica, R & V Aqualine, and Superior Rotomoulding, extending congratulations to these companies for their ongoing support of the industry. Additionally, the 2023 Icon of Industry honouree was announced, recognising Bloys Rijkmans for his significant contributions to rotational moulding.
The final day of the conference typically begins quietly after the conference dinner, but most delegates attended, eager not to miss any part of the outstanding program that had been presented so far.
Chris Glenn from the Bushmans Group commenced
the day by sharing his business expertise and discussing the challenges that keep him awake at night. Given the ever-present nature of change, there are continuous updates to regulations and legislation, improvements to be pursued, and procedures to be revised. Chris shared captivating stories to enhance his presentation.
The conversation around diversity, equity, and inclusion is relatively new to our industry and when including this on the program I was unsure how it would be received. I knew it had the potential to be controversial, not because our industry lacks awareness of these topics but because it would emphasise that the significance extends beyond what we initially perceive. In today’s world it is crucial to have a comprehensive understanding and Zach Edwards from Diversity Works NZ helped us to explore the
foundations of workplace DEI and how to translate awareness into action.
Everyone was very excited to hear from Claudia Persico of Persico about the SMART H2. Claudia discussed the different technologies for the manufacture of polymer liners for hydrogen tanks and how rotational moulding can provide cost-effective solutions for their production.
The conference program concluded with an engaging presentation by Graeme Hall, Micah Carreon, and Ben Hopley from Pact Reuse, titled “Quest for Knowledge: ARMA Library Gems.” They emphasised their reliance on research to expedite their product journeys and aimed to encourage the use of the ARMA library. Highlighting the value of past studies and experiences, they demonstrated how they conduct research and apply insights from the broader industry, focusing on the perspective of a moulder.
ARMA President, Chris Glenn provided a conference wrap-up and proudly announced that Gold Coast was the chosen destination for the Rotomould 2024 Conference & Trade Exhibition.
The Association of Rotational Moulders Australasia Ltd would like to take this opportunity to thank all attendees, speakers, and event staff for assisting us to pull together this amazing event.
Thank you to Micropellets Australia for providing all attendees with an impressive puffer vest and to STP Rotomachinery for providing the ongoing barista coffee!
A huge thanks to all conference sponsors; Qenos, Price Plastics, Matrix Polymers, Rotoload, Micropellets Australia, Persico, Vision
As a final note, I will leave you with some of the feedback we have received:
“Thanks for putting on a great conference, I found it thoroughly worthwhile and enjoyable. It was my first ARMA conference and overall I found the conference had a nice friendly vibe to it which was awesome.”
“This was a great opportunity for us to meet our Australian manufacturers along with a number of other manufacturers we know here in New Zealand. We truly enjoyed it.”
“I wanted to say a big thank-you to you both for all your support and co-ordination for Rotomould23. It was a fantastic and wellorganised event that we were pleased to be a part of.”
“I wanted to write to express my thanks for looking after me (and all of us ) in Queenstown and for putting on such a great conference! I had a great time and learned a lot.”
“I was initially worried about having to meet so many new people – it is not really my thing – but was awesome to meet so many people from our industry. It has made me realise we are all truly in this together. There will be no hesitation from me to sign up for the next conference, I will be one of the first.”
In 2013, following a successful career in the commercial furniture industry, Mike Collins decided to launch a proprietary furniture product line with his newly founded business, Tenjam. Flash forward a decade later, and Tenjam has enjoyed impressive growth and expansion thanks in large part to adopting the rotational molding process as its primary manufacturing medium.
With initial focus on the educational and commercial furniture space, Collins and Tenjam saw an opportunity for lightweight, seamless, and flexible furniture to fill growing and largely open market demand. To address this need, Collins deployed a manufacturing process involving cutting blocks of polyurethane foam into a variety of geometric shapes, then secondarily spraycoating the foam with flexible polyurea. This process created flexible, lightweight and durable furniture with a colorful “rubberized” texture.
Leveraging contacts from his commercial furniture experience, Collins quickly established a network of dealers and sales representatives to drive demand for Tenjam products. This network was bolstered by aggressive promotion at sector-specific
trade shows such as EdSpaces, an annual event that brings together educators, administrators, architects, and supply chain entities to continuously refine the learning environment. “Exhibiting at shows like EdSpaces allowed us to gain credibility in a target sector as well as build our presence with dealers and sales reps to score some early wins,” stated Collins.
While market response to this initial iteration of Tenjam furniture was positive, Collins learned quickly that this manufacturing process was not sustainable, and by 2015 was seeking alternate means of production. “Overall, the cut foam, spray-coating process was very inconsistent and difficult to control,” commented Collins, “and coupled with excess foam scrap and polyurea over-spray waste, we knew we had to find a different way to manufacture Tenjam products.”
Pivoting to plastic.
While performing some competitive reconnaissance at the show, Collins noticed a significant amount of colorful, hard plastic furniture offerings and through crafty inquiry, learned it had been produced by rotational molding. As he considered a viable alternative manufacturing process for Tenjam furniture, Collins
Tenjam’s pivot to rotomolding proved to be its turning point.Tenjam Splash Mibster Chair & Ripple Side Table, White Granite
decided to dig-in and find what this roto stuff was all about. “I didn’t know anything about it but thought it would be worth looking into as potentially more efficient manufacturing, plus the opportunity to expand the Tenjam product line to include hard plastic furniture,” Collins noted.
Shortly thereafter, Collins deployed the tried-and-true Google search approach to identify potential rotomolder partners located within geographic proximity of Tenjam headquarters. Initially, this proved a frustrating venture that almost steered Collins away from the rotational molding process. “Again, I knew virtually nothing about the process, and as I first reached-out to potential partners, I was hit with questions that were like ‘acronym soup’: what’s your material M.I.? Are you running LLDPE or HDPE? What UV stabilizer do you need? I didn’t know what any of this meant, couldn’t answer their questions, and they all blew me off,” Collins lamented.
Fortunately for Tenjam, Collins’ path crossed with Baxter, Minnesota-based tool-builder, Avantech, who in addition to helping navigate through the acronym soup, also developed a cost-effective strategy for initial tooling investment and connected Tenjam with willing and capable rotomolders for the onset of production. This facilitated Tenjam’s initial rotomolded product line launch in 2015, which consisted of many of the same geometric shapes previously offered, now rotomolded in polyethylene and in a broad variety of compounded colors.
“Connecting with Avantech was a real turning point for Tenjam,” said Collins. “Through their tool-building capability, understanding of the process and network of rotomolders, we finally had a path forward in making this vision a reality. We got high-quality product into the market, had an immediately positive response from customers, dealers, and reps, and were finally able to leave our old way of manufacturing (spray-coating polyurethane blocks) behind for good.”
Despite some initial setbacks, Collins recognizes that Tenjam’s success and the rotational molding process are inextricably linked. “I remember watching my fabrication team taking off their respirator masks after two hours of spray-coating foam blocks, seeing so much waste and how exhausting the process was, and thinking ‘there’s gotta’ be a better way’,” Collins recalls. “Adopting
rotomolding as our manufacturing process has absolutely been the difference-maker in so many ways: controllable outcomes, virtually no material waste, less environmental impact, more durable products, easy color changeovers…I can’t imagine where we’d be without rotomolding.”
Flexibility is foremost.
Having launched its line of rotomolded polyethylene products, Tenjam sought a means of producing a flexible product line to replicate the spray-coated polyurethane foam furniture it had been producing since 2013. “Though response to our hard plastic furniture was very positive, we continued to see demand for our flexible furniture, despite having shut down that operation,” commented Collins. “So, we needed to find a way to produce it in rotomolding.”
Working through its expanded industry network, Tenjam determined that rotomolding a flexible rotomolded outer shell with a foam-filled core provided a solution in satisfying this demand. But like its previous spray-coated polyurethane manufacture, Tenjam eventually found the flexible rotomolded material route to be non-viable. “High material costs, supply chain issues, delayed production lead times, high manufacturing costs…we just couldn’t find a way to make our flexible furniture work, and decided to discontinue it,” commented Collins. “We struggled with it (the decision to discontinue its flexible product line), but typical of the roller coaster ride of launching new products, you have to make the tough decisions as unforeseen market conditions guide the path of the business.”
Making a splash in new markets.
Now focusing solely on polyethylene-based rotomolded furniture, and in-line with its ongoing service to the educational and commercial realms, Tenjam has steadily and significantly expanded its market reach. “Tenjam furniture is found in thousands of schools, libraries, pediatrician and dental offices, children’s hospitals, car dealerships, aquariums, animal shelters and a wide variety of high-traffic public spaces,” commented Collins, “and we continue to design and develop products for these (educational and commercial) environments.”
In addition, its more recent foray into the swimming pool market, which began in 2020, has proven wildly successful by virtue of its “Splash Series” product line, which is designed and manufactured to optimize aesthetics, comfort, and ease-of-use for this relatively new customer base. “We successfully re-purposed several existing products – the “Moon” and “Mibster” chairs, for example – to appeal to this market, mentioned Collins. “We added features such as cup holders, carrying handles and drains to the initial design, and the response has been terrific.”
Most recently, Tenjam has launched its “Shayz” pool lounger, incorporating design that combines good looks, comfort and patent-pending quick- fill and -drain capabilities for optimal ease-of-use. “The Shayz lounger has absolutely exploded in the market,” commented Collins, “and through our reps, retailers, and distribution partners, we’re selling Tenjam “Splash” products to resorts and residential homeowners throughout North America, Central America, and the Caribbean.”
Concurrent with the game-changing conversion to rotomolding, strategic industry partnerships have further catalyzed Tenjam’s success and expansion, fueling 800%+ growth since 2015. “Due to a number of factors, it was evident early on that developing a captive manufacturing capability was the key to long-term success,” stated Collins.
“From the get-go we partnered with Avantech in building tools, and we eventually partnered with Tri-Ven (also based in Baxter, Minnesota) for the rotomolding, assembly, logistics and order fulfillment of our products.” This strategic partnership provides Tenjam a turnkey manufacturing solution, allowing Collins to focus on developing new products and markets for the company. “When I started the business, I used to do everything: from sales to spray-coating to shipping to invoicing, which limited how far I could take this thing. Our growth and success would not be possible without this partnership.”
Ten-jamming.
Reflecting on his circuitous journey since starting the Tenjam business a decade ago, Collins recalls a presentation he made at the 2015 Society of Plastic Engineers (SPE) rotomolding conference in Cleveland. “We had just launched our rotomolded furniture line, and my presentation covered the challenges and successes we had encountered in starting a new, roto-focused business,” Collins recalled. “I remember stating our goal to grow Tenjam into the largest manufacturer of rotomolded furniture in North America. We still have a long way to go to achieve this goal, but we continue to make the right moves and are delivering first-class rotomolded products to our customers.”
Communication and PR professionals face a variety of day-today challenges. One of the most important problems that may not always be obvious is the potential for disruptions related to cybercrime. It’s vital for staff to understand that while the PR industry may not appear to be a traditional target for criminals, there are various aspects of PR activities that are valuable to unethical actors.
It is, therefore, essential to put in place measures that protect individual team members, your organization, and clients from the damage that can be caused by a range of hacking tactics. This begins by understanding where the prevalent threats lie, what elements make teams vulnerable, and how to address issues.
We’re going to take a moment to dive into what PR teams need to know about cybersecurity concerns.
Most successful PR corporate teams and agencies are well-oiled machines. In all likelihood, your teams’ efforts are supported by a range of essential resources. This may include files of your industry research, event plans, and social media management platforms, among others. Keeping these resources online or on
company networks helps your team access them and organize communication activities effectively. Unfortunately, this also puts teams in a vulnerable position if they experience ransomware attacks.
Businesses of all sizes need to adopt protections against ransomware threats. Even if your PR team is relatively small in terms of staff numbers, you might still find it’s targeted by hackers. By definition, communicators have more information about the organization and its clients than other branches. This may include sensitive information about corporate clients, industry data related to projects, and even company financial records. Each of these can be an incentive for cybercriminals to commit data breaches.
The result can be significant financial setbacks due to both the ransom your organization needs to pay, as well as productivity losses. Not to mention that client confidence may be shaken if you have any of their material such plans for forthcoming corporate activities.
The primary tool in preventing ransomware threats is ensuring all staff understand how these threats occur. Hackers can use social engineering techniques to convince staff to click on links sent in emails. Some ransomware is introduced through vulnerabilities
in company networks. Alongside ensuring all staff have solid fundamental cybersecurity knowledge, it’s worth investing in effective intrusion detection and anti-malware software for your networks. It’s not just in big companies or agencies – I mention in passing that my small firm receives daily emails containing malware that my security software has detected and destroyed.
The valuable data your PR team is likely to have may include sensitive information about clients, industry data related to projects, and even company financial records. Each of these can be an incentive for cybercriminals to commit data breaches.
The result of theft isn’t limited to the loss of information alone. There can be staggering financial consequences, with the average cost of a data breach in the U.S. hitting $9.44 million in
» ROTOLOAD™ is the ONLY solution to ALL of your powder resin handling needs.
» ROTOLOAD™ is the ONLY comprehensive line of powder resin conveying and weighing equipment, specifically designed to meet the demands of the Rotational Molding Industry.
» ROTOLOAD™ uses vacuum to load your material, hold it above your process machine, and dispense, quickly and accurately. In addition it is the ONLY solution to the question of how to reduce under and overweight parts, mess, downtime and resin loss.
2022. Hackers are able to utilize these resources for further illegal activities and illegitimate gains.
There are some steps your PR staff can take to communicate greater awareness and protection against illegal accessing. One of the simplest is to ensure that all passwords within the organization are complex and regularly changed. Implementing 2-factor authentication procedures for accessing any accounts on your company networks or downloading data is also a smart approach. This is especially important if you have hybrid PR teams accessing networks out of the office. With two-factor authentication, if someone does choose a weak password or a service gets hacked, there’s always another checkpoint to make sure it’s really that person who wants to log in.
It’s also vital that your PR teams always communicate around the organization that staff should treat all data as though it comprises valuable
There can be staggering financial consequences, with the average cost of a data breach in the U.S. hitting $9.44 million in 2022.”ROTOLOAD™ powder weighing & dispensing systems Manufactured by Wittmann Battenfeld Canada Inc.: 35 Leek Crescent | Richmond Hill, ON L4B 4C2
assets. This includes never leaving data unattended and being mindful of who can view documents in the vicinity. This caution must extend to disposing of old electronic devices in safe and secure ways, too.
Items such as smartphones and computers may be storing client or proprietary information even after staff think it’s been deleted. It’s wise for your teams and even clients to utilize electronic shredding methods to ensure data can’t be accessed by unethical actors.
Regardless of threat levels, your PR employees should be educated about security threats and the importance of protecting critical data. Without sufficient education or awareness, many individuals may not be thinking about the increased risk of a cyberattack these days and how their actions can contribute to systems’ vulnerability to attacks.
For example, employees should be trained to identify and monitor for malicious links, attachments, or phishing in emails and on websites. They should report anything that looks suspicious and flag any emails or content that may contain viruses or threats.
While every organization should create a crisis communication for cyber risk, at a minimum your organization’s leadership team, in cooperation with the communication team, should:
• outline the top 10 risks to the organization, including IT and cybersecurity;
• work across departments to learn about different perspectives or risks you may have not considered; and
• compile these into a document and plan a response to each.
With cyber issues especially, it’s important to consider who is at the table. The C-suite, PR, legal and your board of directors should all be connected to the processes you choose to follow and the questions they need to be prepared to ask when crisis hits.
Your communication team should also have visibility into technology vendors and partners that may need to be added to a response when issues arise.
As part of your plans, it is advisable to develop holding statements for each of your 10 major known issues so you can easily adapt and streamline approvals for these initial communications. Consider having statements ready for breaches
that impact internal, external, and all types of stakeholders. You will also need to prepare stakeholder communication plans to include customers, partners, employees, board members, and investors – ready to fire up if the breach is far-reaching. Consult senior management in this case and ensure your head of cyber security and other relevant cyber leader close to the issue is in step with your communication response.
There may be times when your PR team is involved in your organization’s follow-up to sensitive corporate negotiations such as takeovers and mergers with high-profile individuals or organizations. When criminals find out about your firm’s involvement in negotiations, you could find your business specifically targeted by cybercriminals who want to gain sensitive information about the other parties for nefarious purposes.
Your efforts here should begin with limiting the exposure that such data has to the outside world. This may involve ensuring your team members don’t access client or other sensitive information on their personal devices or outside of the office. Avoid electronically transferring documents unless encryption protocols are in place. In some instances, it’s worth protecting these files from internal and external theft by storing the data on separate cloud accounts and limiting use to senior team members only.
It’s also wise to make identifying files related to high-risk, high-profile, or potentially highly profitable activities difficult for anybody who isn’t directly involved with the project. This could include choosing a pseudonym for the client or major company you are dealing with and naming all related file folders and documents accordingly.
PR teams need to take a responsible approach to protect themselves, their organization, and their clients from cyber attacks. Your business must educate workers on threats associated with ransomware and data breaches, alongside the methods to mitigate these.
It’s also vital to put protocols in place that protect high-profile clients that may draw targeted attacks. Remember, though, it’s not enough to put protections in place now and then move on. The cybercrime landscape is always changing. Your PR teams should also make efforts to stay up to date on new threats and utilize relevant tools to reduce risks.
PR teams need to take a responsible approach to protect themselves, their organization, and their clients from cyber attacks. Your business must educate workers on threats associated with ransomware and data breaches, alongside the methods to mitigate these.”
“I
The mission of the Association of Rotational Molders is to promote, educate, and inspire the rotomolding industry. For more information, visit ARM’s website at www.rotomolding.org or contact the Association at 630-942-6589 or info@rotomolding.org.
I am excited to announce the ARM Training Academy, a new website that allows our members to track their progress and earn a certificate of completion for our Operator Training Program.
The Training Academy is a significant ongoing investment from ARM and a result of our discussion with members at our 2022 Spring Meeting about how our Association should invest resources. The clear direction from that meeting was that ARM should continue to increase training opportunities for molders.
The Operator Training Program includes 25 training videos and 21 short quizzes. Participants can save and track their progress in the Training Program. The outline for the program was initially developed by our charitable organization, the Roy Crawford Education and Development Foundation. ARM Technical Dr. Director Nick Henwood organized and hosted many of the training videos. Additional videos were presented by Jim Henry of Diversified Mold and Castings, Dru Laws of Brigham Young University Idaho, Evan Silo of McLube, and Larry Whittemore of Stoner Molding Solutions. I want to thank all of them for their work on the program.
The ARM Training Academy is available free to all members. Soon we plan to add the ability for companies to track their employees’ progress within the program as well. Over time, we will add ARM’s other training series to the Academy, beginning with our Safety series.
Please visit the ARM Training Academy website at https://www.pathlms.com/arm.
In addition to the ARM Training Academy, our Intro to Rotomolding Seminar and Advanced Rotomolding Seminar are offered multiple times throughout the year in various locations. The Board has made a point of keeping the prices for these seminars low to allow companies to send as many employees as possible. Both seminars will be offered at our Annual Meeting in Kansas City. You can learn more about the meeting on the next few pages. I look forward to seeing you there!
Matt Bushman President, Association of Rotational Molding President, Plasticraft Corporation“ARM continues to increase training opportunities for molders.”
Join ARM for the Annual Meeting in Kansas City, MO, September 26-28. The Association of Rotational Molders brings hundreds of rotomolders and their suppliers together to learn from one another, troubleshoot, and network. Molders call our Annual Meetings “the most informative conference” they have ever been to and they report that solving one problem can pay for the meeting registration many times over. First-time attendees report they were “made to feel very welcome” and the meeting is “exceptional for me in meeting key players in the industry.”
From technical seminars to networking events to our soldout exhibit hall, you won’t want to miss any of this year’s Annual Meeting. Here is a snapshot of the schedule. You can visit https:// rotomolding.org/page/AnnualMeeting for more information.
Tuesday, September 26
Committee Meetings
Seminars: Roto 101, Advanced Rotomolding, Design
Optional Tour to Boulevard Brewery
Welcome Reception
Wednesday, September 27
Keynote: Chad Hymas
General Sessions
Exhibit Hall Open
Younger Members Reception
Thursday, September 28
Exhibit Hall Open
General Sessions
Workshops
Networking Lunch
Awards Gala Dinner
After-Party
Friday, September 29
Optional Tour to The National World War 1 Museum
Visit these exhibitors to learn more about the newest technology, products, and special offers only available at the Annual Meeting:
493K
Avantech
AXEL Plastics
Brunk Plastic Services
Chem-Trend
Cole Industries
CPChem
Diversified Mold & Castings
Dow
Entec Polymers
ExxonMobil Chemical Canada
Ferry Industries
Foam Supplies Inc.
Gasbot Pty Ltd
Gulf View Plastics
Ingenia Polymers
Jerico Plastic Industries, Inc.
Lone Star Chemical
LyondellBasell
Lyten
M. Holland
McCann Plastics
McLube
Mosaic Color & Additives
Muehlstein
Nexeo Plastics, LLC
Chad Hymas: Leaving a Legacy
Chad inspires, motivates, and moves audiences, creating an experience that touches hearts for a lifetime. In 2001, at 27, Chad’s life changed instantly when a 2,000-pound bale of hay shattered his neck, leaving him a quadriplegic. But Chad’s dreams were not paralyzed that day—he became an example of what is possible. Chad is a best-selling author, president of his communications
Norstar Aluminum Molds
NOVA Chemicals
Optimax Plastic LLC
Orenda Automation Technologies
Persico
Powder King
Precision Products Enterprises
PSI Brand
Quantum Polymers Inc
Re-Gen Inc
Rock Lake Robotics
Rotaloc International, LLC
RotoEdge Pro
Rotoline
RotoPolymers
RotoWorld®
Shaw Polymers, LLC
Solvay
Stoner Molding Solutions
STP Rotomachinery
Teknor Apex
Trademark Plastics
Wittmann Canada
Xcelerant Growth Partners LLC
company, and recognized world-class wheelchair athlete. In 2003, Chad set a world record by wheeling his chair from Salt Lake City to Las Vegas (513 miles). Chad’s speaking career in leadership, team building, customer service, and mastering change has brought him multiple honors. As a member of the National Speakers Association, Chad travels as many as 300,000 miles a year, captivating and entertaining audiences worldwide.
• Advancements in Rotational Molding: Explore modeling, simulation, and sensor technologies for improved product development, presented by Mark Kearns.
• Crosslinked Polyethylene Recycling: Denis Rodrigue discusses recycling techniques and preliminary research findings.
• Cyber Security: Protect yourself and your family from cyber crimes with expert tips from Scott Augenbaum.
• Enhancing Competitive Advantage: Discover cost-effective product design strategies through case studies by Tom Innis.
• Hydrogen Liners: Join Sergio Zilioli as he unveils smart machinery solutions for the manufacturing of Hydrogen liners, a potential new era for the industry.
• Plastics Forecast Panel: Get insights from Chris Gick and Perc Pineda on future trends in the plastics industry.
• Product Track and Trace: Jim Crawshaw will highlight the benefits of RFID and plastic tracking methods for rotomolders.
• Recycled Solutions in Rotomolding: Dustin Turgeon explores incorporating flexible recycled polyethylene into products.
• Scientific Approaches to Part Quality: Gareth McDowell shares measurement strategies to meet and exceed quality targets.
• Tango Manufacturing: Learn about the award-winning design of Halltec Hornet, the 2022 Product of the Year.
• Cooling — Still the Final Frontier?: Examine the challenges and lack of control in the cooling process of rotomolding. Understand the mechanisms at work and their impact on part quality.
• Curing of Mold Release and Controlling Warpage: Learn the importance of curing mold release for improved quality and cost reduction. Understand when and why to apply different formulations of mold release.
• Cyber Security: Protecting the Business: Scott Augenbaum, a former FBI agent, shares knowledge on preventing cybercrime. Provides no-cost action plans to protect individuals, families, and organizations.
• Problem-Solving Concepts for Roto: Learn problem-solving techniques and tools for overcoming technical challenges in rotomolding including practical examples.
• Resin Automation: Explore different ways to utilize resin automation for improved manufacturing. Discuss small to complex solutions tailored to customer needs and desired results.
• What’s Your Problem: Collaborative troubleshooting session with industry experts to address operational issues.
• Introduction to Rotomolding: Dru Laws covers key elements of the rotomolding process, materials, equipment, and design guidelines.
• Advanced Rotomolding: Dr. Nick Henwood explores Melt Index, density, alternatives to PE, data sheets, thickness control,
curing, shrinkage, process monitoring, troubleshooting, and scrap reduction.
• Design: Michael Paloian focuses on rotational molded part design, fundamentals, case studies, problem-solving exercises, and becoming design experts.
• Brewery Tour: Boulevard Brewing Company, founded in 1989, is the largest specialty brewer in the Midwest. The hour-long walking tour includes beer samples during the tour and a choice of two more samples or one full pour at the end.
• Welcome Reception: Attendees gather for a warm welcome in Kansas City, enjoying light bites and cocktails. It’s an excellent opportunity to reconnect with old friends and meet new people who will be part of the upcoming learning experience.
• Spouse Jewelry Making Class and Lunch: Guests visit the Madison Stitch fashion studio in downtown Kansas City, learning about the city’s fashion history and jewelry-making
process. They can create their own set of earrings, bracelets, or a small card wallet before heading to a nearby restaurant for lunch.
• National World War 1 Museum Tour: The National WWI Museum and Memorial is dedicated to the remembrance and understanding of the Great War’s enduring impact on the world. Through exhibits, films, and first-hand accounts, visitors gain insight into the cataclysmic event of the 20th century, featuring diverse collections from all belligerent nations.
Join ARM members under 40 to enjoy libations and discuss the future of ARM. This is a great opportunity to meet new people and share your challenges and victories.
Our Annual Awards Dinner and After-Party is the grand finale of this exciting meeting. Join us for a reception and dinner to honor the best of the best in rotomolding. Then, let your hair down and sing some karaoke at our annual After-Party. This year’s theme is Blues and BBQ.
The ARM Annual Meeting will be held at the Kansas City Marriott Downtown. The group rate is $199/night with some upgrades available. Our hotel occupies a historic building, reflecting the charm and history of Kansas City, MO. When you’re ready to venture out, walk to many of the area’s prominent destinations, including the Power & Light District, Kansas City Music Hall, and T-Mobile Center.
JUNE 9-14, 2024
Tour of Italian Rotomolders and Congress with IT-RO in Lake Garda, Italy
September 23-27, 2024
Rosemont, Illinois
Well over one hundred attendees and fourteen leading supplier exhibitors, both Indian and Global, were part of an energetic return to an in–person StAR Conference & Trade Show. After the 3-year pandemic break, the conference was held on January 28–31, 2023 in New Delhi. The theme, topics, and spirit of the conference brought back the bonding and bonhomie that could never be part of online meetings during COVID times.
The conference theme Together Towards Tomorrow carried the momentum of revival in the 3–day programme of sharing new knowledge and proactive global networking.
There were four Workshops on forward looking and essential topics conducted on the opening day, 28th January:
New Age Opportunities – New markets for rotomolding Anchored by: Akshay Saini, BDI, India; with co-panelists Celal Beysel, Floteks Turkey; Martin Spencer, UniqueRoto, UK; and Rustom Patell, Baroda Polyform, India.
Beyond Polyethylene – Other sustainable materials Anchored by: Umakant Savadekar, Phychem, India; with co-panelists Aldo Quaratino, Matrix, UK; Eric Maziers, Total Energies, Belgium; Craig Burgess, PSD Rotoworx, Australia; and Paul Nugent, PolymerLink, Malaysia.
Future Rotomoulding Technologies – A global rototour Anchored by: Swetang Dave, Consta Cool, India; Matteo Cortesi, Persico, Italy; Dhanu Patell, Reinhardt, India; and Davide Accornero, Rototech, Italy.
Who Moved My Profits? Anchored by: R Ravikumar, Roots Multiclean, India; and co-panelists Blaise Costabir, GMI Zarhak, India; Rajnish Gera, Sintex,
India; and Dominic Polayil, BAPL Rototech, India. Conference presentations held on days 2 and 3; 29 and 30 January covered a gamut of rotomoulding segments in tune with the conference theme:
Keynote presentation: The Future of Rotomoulding by Martin Coles, Matrix Polymers, UK
Be a “Rotomoulding NERD” by Martin Spencer, Unique Roto, UK
Future Trends and Concerns about Environmental
Aspects of Rotomoulding by Celal Beysel, Floteks, Turkey
Sustainable Rotomoulding Technology – The Future Today by Matteo Cortesi, Persico, Italy
Hydrogen for Future Mobility Applications –Opportunities and Challenges for Rotomoulders by Davide Accornero, Rototech, Italy
Does Quality Cost by Blaise Costabir, GMI Zarhak, India
A Comparative Study on the Effects of HVO-100 & Biodiesel Vs Conventional Fuels on Physical Properties of Crosslink & Linear PEs by Maisyn Picard, Ingenia, Canada
Good Design is Value Creation, Not Value Engineering by Satish Gokhale, Design Directions, India
The Circular Economy – The face of future sustainability by R Ravikumar, Roots Multiclean, India
Hot Markets for Polypropylene by U Savadekar, Phychem, India & Craig Burgess, PSD Rotoworx, Australia
Effective Marketing and Branding through Rotomoulding Business Programme by Peram Prasada Rao, TechnoBiz, Thailand
Industry Engagement: Practice School (PS) by Sachin
Waigaonkar, BITS – Pilani, Goa
Polymer Composites for Rotomoulding- Problems & Challenges by Marek Szostak, Rotopol, Poland
Decades of Presence in the Automotive Industry: Total Energies is a Preferred Supplier of Plastic Fuel Tank Solutions by Eric Maziers, Total Energies, Belgium
PCR From Milk Pouches Converted into Rotomoulded Products by Permpoon Chaijaroen [Billion], SCG Chemicals, Thailand
Rotomoulding Opportunities in Hydrogen Fuel Storage by Aldo Quaratino, Matrix Polymers, UK
Rotomoulding in Americas – Sans USA by Conchita Miranda, Miraplastek, Mexico
Decorative Graphics and Functional Coatings by Konstantia Asteriadou, Lysis Technologies, UK
How to Select the Right Type of Rotomoulding Machine by Kiran Panchal, NA Roto Machines & Moulds, India
The social events, like the Networking Dinner Reception on 28th evening and Gala Dinner with entertainment and awards on 29th evening, enhanced the networking opportunities and provided special Delhi winter evenings with food and drinks to match. These fun events were mixed with a lot of camaraderie of course. India’s leading sufi singer Dr. Mamta Joshi provided a great blend of soulful songs and dance numbers to make the Gala Dinner evening truly memorable.
Sponsors for such a milestone event deserve much more than the last word. They were recognized and honoured all along the way. The sponsors included: Matrix Polymers, Greenage Industries, and PolmyerLink as the Principal Sponsors; NAROTO as Diamond Sponsor; and PSD Rotoworx and Salee Colour, MPlast, and Reinhardt Teknik as Platinum Sponsors.
The next 2024 StAR Conference is to also be in person, and that has kept the excitement going.
Kazakhstan is a huge country, the size of Western Europe, situated in Central Asia, bordering Russia to the north and China to the east.
The Kazakh Steppe is a vast region of open grassland in northern Kazakhstan, which is much like the Great Plains in North America. The grassland was originally used extensively by nomadic Kazakh people for grazing their animals, somewhat like the Plains Indians who followed the migration of the buffalo.
The name “Kazakh” is said to come from the Turkic word “kaz” meaning “to wander,” referencing the Kazakh’s nomadic lifestyle; the Persian suffix “-stan” means “place of”, so the word Kazakhstan literally means “Land of the Wanderers”.
the first country to recognise its independence. It now has a population of nearly 20 million, of which two thirds are ethnic Kazakhs.
Raw mineral extraction is by far the biggest sector of Kazakhstan’s economy. It has vast hydrocarbon and mineral reserves, with Kazakhstan ranked as the world’s ninth-largest crude oil exporter.
Kazakhstan became a Soviet republic in 1936 and following the collapse of the Soviet Union in 1991, the United States was
KSC-PLAST (KSC) commenced operations in 2002, in Almaty, the largest city in Kazakhstan. While Astana is the capital, Almaty is considered the cultural, financial, and economic center of the country. KSC began business supplying the national
telecom company, Kazakhtelecom, which was experiencing significant growth and development. Kazakhstan now has one of the most developed telecommunications sectors in the Central Asian region.
KSC has modern injection molding machines with a clamping force ranging from 120 to 360 tons. In 2008, the first rotational moulding production line was commissioned, to make telecommunication chambers.
KSC quickly expanded their roto product range to include water tanks.
In 2018, KSC introduced a range of decorative water storage containers in collaboration with European designers. These high value decorative containers offered KSC customers attractive water storage vessels that were never manufactured in Central Asia before to decorate and complement the interior and exterior of urban homes.
While Kazakhstanis living in the large cities do not lack drinking water, water issues have become an increasing challenge for Kazakhstan and Central Asia, amplified by climate change. This occurred most recently in a 2021 drought, which negatively affected wheat production — Kazakhstan’s most important agricultural export.
In 2020, KSC designed and manufactured its’ own series of modular tanks for underground installation, with a diameter of 1.6m & 2.3m. (63” to 90”). The solutions that were used in designing this series of tanks make it possible to use them in an earthquake-prone region and in rocky soils.
KSC now has a range of above ground water tanks, from 50L up to 25,000L (13 to 6,600USG), while underground tanks range up to 100,000L(26,400USG). Every fifth citizen of Kazakhstan
now use plastic water tanks manufactured by KSC.
In 2023, there are 5 different rotational moulding companies operating in Kazakhstan.
KSC has invested in modern state-of-the-art production infrastructure during the past 15 years enabling it to become a multifunctional manufacturer capable of producing a wide range of products and tooling with the ability to perform complex equipment repairs.
KSC developed rotomoulded underground telecommunication cable management chambers (wells) which have simplified logistics and installation, accelerated the modernization of telecom networks, and met or exceeded the expectations of Kazakhtelecom.
The KKT-1 and KKT-2 telecommunication wells, just like other rotomoulded products, have replaced the traditional reinforced concrete wells.
During the country’s transition from copper to fibre-optic
cabling, KSC designed and manufactured a group of innovative fibre-optic products.
Included in the wide variety of products KSC rotomould are urban infrastructure products such as road barriers, street signs and traffic signal pole protectors. Maximising the advantages of durable long life polyethylene.
KSC is now a market leader in the Central Asia region for the production of plastic products. Central Asia includes the former Soviet republics of Kazakhstan, Kyrgyzstan, Tajikistan, Turkmenistan, and Uzbekistan.
KSC-PLAST now consists of 3 separate factories equipped with a total of 11 rotomoulding machines with ovens ranging from 1.6m to 5.5m (63” to 216”) diameter in shuttle and carousel configurations.
The annual volume of polymer processed by injection moulding is 5,000 tons (11million lbs), while rotational moulding is 2,000 tons (4.5million lbs).
Large products like water tanks or recreational boats are fabricated in sheetmetal, while smaller more complex shaped products, like decorative containers, are cast aluminium or CNC aluminium tools.
KSC-PLAST is a diversified manufacturing company using the rotomoulding process to design, manufacture and market a range
of solutions within Kazakhstan and internationally.
KSC recognise the benefits of industry associations and joined ARM and have actively attended rotomoulding conferences in North America, as well as attending ARMO conferences around the world.
They have taken advantage of the educational opportunities offered by ARM membership to train staff, reduce scrap, and learn from peers and experts.
KSC is a veteran of the Rototours organised by ARMA, visiting moulders in Australia, southern Africa, India, China, USA, UK, Europe, and most recently the Nordic countries, which has given them the opportunity to communicate with the rotomoulding industry worldwide.
While state-owned enterprises continue to dominate the economy in the 30 years since independence, KSC-PLAST is an example of private sector development and innovation which has been possible in Kazakhstan.
Rotational moulding continues to be a process, when well executed, offers the possibility to make almost anything you can imagine, wherever in the world you are.
In the last Practical Tips column, I invited each of you to imagine our wonderful rotomolding process from the inside out. Mentally living inside the mold during the process will improve your ability to understand it, and thus improve it.
I often get asked questions about reverse rotations, which can be a confusing and abstract concept … until we change our vantage point as suggested above. So, should you reverse your rotations? If so, when should you start and how often should the direction change? Let’s address these three questions one at a time.
Although it is not always necessary, the short answer is ‘yes, you should’. I have yet to discover a situation where reversing rotations is a bad thing. When needed, reversing rotations helps. When not needed, reversing rotations doesn’t hurt. (OK OK, maybe doing so when not needed isn’t the ideal situation for the gears and motors driving the rotations of your arms and plates, but the major machine manufacturers have confirmed that the machines are designed and built for it.)
Well then, how do you know if it is truly needed? The need to reverse rotations is primarily driven by powder flow and part geometry. Sometimes there are regions of the inside of your mold that never touch any powder due to the material “falling” over edges and beyond any associated undercuts. Like a waterfall over a sharp precipice. Image 1 is a low-resolution screen capture taken from some old footage of a camcorder placed inside a kayak mold. The rotations of the mold are such that the material is flowing inside in a clockwise fashion, indicated by the blue arrow. As such, when the material flows over the ledge feature on the right side of the image, it entirely skips the portion of the mold highlighted by the “dead-zone” red triangle. If the process is allowed to continue in this fashion through the entirety of the cycle, this dead-zone portion of the part will have no material buildup. Reversing the rotations at some point will largely address this concern.
The low-resolution Image 2 shows the same snapshot a few minutes later in the process. This time the powder is flowing the opposite direction, thus capturing the missed area from earlier. Notice that under these conditions, a different dead-zone is created on the opposite side of the same ledge feature.
If you have any odd shapes or features in your mold, then reversing rotations is probably a good idea.
2. WHEN should reverse rotations commence? Some would suggest that the only time reversing rotations are necessary is
during the plateau phase change of the process — when the powder is melting and forming the hollow part. This is indeed a critical phase of the process, but reversing rotations should start at the very beginning of the process. Remember those dead zones mentioned before and highlighted in the two low-res images? Not only will they be void of material build up, but they are getting significantly hotter than any other portion of the mold. As powder tumbles across the inside surface of the tool, it is constantly picking up heat from the mold. During the first several minutes of the oven time, there is significant moldto powder and powder-to-powder heat exchange happening. If you have regions of the mold never seeing any powder, they are continually heating up with no powder to share that heat with. They become unwanted hot spots inside the mold. Reversing rotations from the very beginning of the cycle eliminates these dead-zones and their resultant hot spots.
3. HOW OFTEN should reverse rotations happen? The answer to the first two questions is much simpler than the answer to this question. How often should you program your recipe to swap directions back and forth? It entirely depends on the length of the phase-change plateau mentioned previously. Image 3 shows a typical rotomolding cycle where the phase change plateau occurs approximately between minute 8 and minute 16, shown by the vertical red lines. In this instance, if you were to program the recipe to reverse every 8 minutes, you would get one reversal at the beginning of the plateau, and another one after the plateau was over. These settings would not adequately solve either the powder flow dead-zones or the mold hot spots.
It has always been my recommendation to program your settings such that you get 3 to 4 reversals during this phasechange plateau. Perhaps every 2-4 minutes would be more appropriate for this scenario. Image 4 shows the reversal instances if you were to do so every 2.5 minutes. This would provide about 3 such toggles before the plateau, thus eliminating any mold hot spots, and well as 3-4 toggles during the plateau to avoid any powder flow dead-zones.
In summary, here are the answers I provide to these three reverse rotation questions I get asked the most:
• Should I be using rotation reversals in my products? Yep, you probably should be.
• When should I start reversing rotations in my cycle? Start at the beginning, and at least carry them through until all the powder has been consumed.
• How often should I change directions? Often enough that you get 3-4 toggles during the melting phase plateau. (Which means you need to use some sort of temperature monitoring device to discover approximately when that is actually happening.)
ARMA proudly presented the Icons of Rotomoulding Award to this year’s honouree, Bloys Rijkmans from Micropellets Australia.
Bloys has proven himself to the rotomoulding industry by successfully designing and implementing in-house resins. He also meticulously provides advice to Rotomoulders. He has helped with the implementation of standards, provided technical support and advice on new projects, and was on the original Tank Standard Committee from 1999 to 2006 as well as on the Revision Committee for 2020.
Bloys has been an ongoing beacon of understanding in the Australasian rotational moulding industry for well over 24 years. His understanding of material behaviour is unsurpassed in the rotational moulding industry. His ability to convert his knowledge to real-world applications is of the highest level and it is delivered with strength of conviction that is rarely seen by technical practitioners.
He has been a valuable member of every organisation he has been involved in and is universally admired. Bloys is without doubt a brilliant mind that quietly goes about his business with little fuss or fanfare.
Congratulations Bloys!
ARMA has recently established a new insurance partnership with KBI Group Australia, expanding our collaboration beyond our members to include them as the provider of our association insurances as well. During our most recent meeting, they highlighted prevalent issues within our industry.
• Historical limits often fail to adequately cover current asset values, resulting in minimal or no claims payouts.
• Many members frequently express dissatisfaction with their brokers’ lack of proactive adjustments over extended periods.
• Despite its critical importance in manufacturing, only a small fraction of the industry have adequate Machinery Breakdown cover in place.
• Indemnity periods are often set excessively long, surpassing the actual time required to resume operations, leading to potential premium savings.
• Business Interruption coverage is often miscalculated, resulting in incorrect assessments.
• Insurers ill-suited to the nature of the product and manufacturing industry are prevalent.
• Cyber insurance, despite being crucial in addressing significant risks, remains relatively underutilised among the industry.
It is a very busy time of year for ARMA with a lot happening.
• We have recently held our annual Rotomould Conference in Queenstown, New Zealand which you can read all about in this issue.
• We have now finalised the ARMA Cyber Security Policy and updated our Privacy Policy.
• The ARMA staff have completed their very first cyber security audit.
• Rototour 2023 Nordic is underway with 37 attendees from across the globe.
• The amendments process for ASNZS4766:2020 is underway. The draft amendments are available for public review and comment via the Standards Australia public comments system until October 4, 2023.
• We are actively involved with the Australian Standards Forum on Microplastics and Operation Clean Sweep.
• The ARMA 2023 Industry Survey has recently been conducted. The results help to ensure we are up to date with vital data and statistics. An Executive Summary will be distributed to the members.
The Rotational Moulding Group of the British Plastics Federation (BPF) enjoyed its first factory tour in Italy in May this year. Co-organised with the Italian rotomoulding association IT-RO, 21 BPF members enjoyed a two-day trip to four rotational moulding sites in northern Italy.
Founded in 1933, the British Plastics Federation is the UK trade association representing the British plastics industry. Their Rotational Moulding Group is one of the longest established groups within the Federation and was founded in 1978. The Italian rotomoulding association IT-RO, Italia Rotazionale, was started in November 2013 by a large group of companies active in rotational moulding. The opportunity to engage with IT-RO and develop an informal fact-finding/knowledge sharing event seemed too good to ignore.
Graeme Craig is a senior industrial issues executive at the BPF and the executive for its Rotational Moulding Group:
“The BPF has taken a strong focus on sustainability, productivity, and efficiency for the plastics industry for some time and our ability to learn and progress is often improved with collaboration. We are acutely aware that rotational moulding is a significant part of the plastics industry in Italy, so it was an obvious choice to approach IT-RO.”
Katia Zoppetti is tech and sales engineer at DRAM srl and IT-RO President:
“IT-RO is honored to have hosted the first international factory tour organized by the BPF: we believe that international collaboration strengthens trade associations, and their members, even further by enabling brainstorming while learning first-hand other companies’ best practices. The event gave attendees an opportunity to learn about the management and the products of four factories, quite different from each other but all committed to continuous improvement.”
Beginning at the historic city of Padua, the group took a short coach trip to Limena, about 22 miles west of Venice, where they
were welcomed by Elbi. Founded in 1965, Elbi developed a range of products starting with thermo-hydraulics. Over time it has built a solid reputation and experienced growth in major world markets. In 1989, the company began production of rotationally moulded polyethylene tanks.
Attendees were then introduced to the business by Valentina Brustio, Elbi Marketing & Sales Manager, and daughter of Elbi founder, Luigi Brustio. On the site tour swathe group witnessed production of Elbi’s own-brand product ranges, including 21st
Garden Art (indoor and outdoor planters), 21st Living Art (designled furniture and lighting for the hospitality industry), Ambiente (a wide range of containers for the separate collection of municipal waste), and Aquapura (tanks and waste-water systems).
The extensive range means that Elbi needs to be compliant with a number of quality systems and certifications. Following the site tour, the visiting group was treated to lunch with some of Elbi’s management team and suppliers.
Following lunch, there was a 50km drive to VECA S.p.a. Just 30km from Padua, VECA has been designing, producing, and selling high-quality plastic pots since 1988, producing 25 million pots annually and exporting to 50 countries worldwide. Its product range also includes designer furniture for the hospitality industry. Like Elbi, VECA produce high volumes of big products, which requires complex management of polymer, process, tooling, and stock on a large scale. The BPF members found impressive systems and controls in place on both sites that help to reduce overheads and increase efficiency.
In the evening, members enjoyed a reception and dinner with IT-RO board members, Moulding Service, Elbi, VECA, and some of IT-RO’s suppliers. The evening provided a useful and sociable opportunity to get to know each other and share even more knowledge and experience.
Sara Cammarano of Dram srl, a member of both IT-RO and the BPF, summed the evening up perfectly:
“We could feel the true spirit of trade associations working at their best: we shared, learned best practices from each other, spoke about common issues (cost of work, increasing energy prices, need to use our resources better) and did not feel like competitors, but like people that are indeed stronger when working together.”
It was an early start on day two, with the coach departing at 8:00 am for a two-hour journey to the Emilia-Romagna region to meet our third host, Spila. However, the BPF group woke up to the tragic news that more than 20 rivers in Italy had burst their banks, with almost every river flooded between Bologna and the north-east coast 70 miles away – precisely where Spila is located.
Overnight the area had been devastated by floods, killing 14 people and requiring 36,000 residents to be evacuated. After calling ahead, the group were told that yes, there had been some disruption, but Spila were not only able to maintain production, but were looking forward to their arrival.
Production Manager Alessandro Massari and owner Paolo Tamagnini gave a warm welcome and an excellent insight to their manufacturing ethos, producing technical products with a high level of secondary processes. Spila closely manages its production to reduce waste and improve quality and has systems in place that deliver traceability from powder to product to pallet.
Following the visit, the hosts treated the visitors to a long, Italianstyle lunch in a nearby farmhouse restaurant. As they say in Italy –la bella vita.
The last stop on the whirlwind tour was at Moulding Service, another technical moulder supplying to several markets. Founded in
1999, this is a business that takes its environmental responsibilities very seriously. Moulding Service owns a strong process know-how not only for the most common materials such as LLDPE, MDPEe, HDPE, but also for technical materials such as PP, XPE, Multilayer, PA6e and PA12, allowing them to supply technical products and markets like agriculture, industrial, and automotive.
Moulding Service carries out regular checks on all phases of the production cycle, and the performance of machinery and extraction systems to minimize atmospheric emissions. With growth plans and partnership options available, Moulding Service invited members to discuss opportunities for collaboration and the potential benefits, strongly believing that partnership could make the rotational moulding industry stronger and more competitive.
Tom Fleming and Selwyn Jones from Corilla Plastics came on the tour as part of a fact-finding mission. Corilla Plastics has been producing quality rotationally moulded plastic products for more than forty years, but continuous improvement is a key part of their philosophy, and they were pleased to take valuable lessons away from their Italian counterparts:
“The layouts and use of technology, especially in production planning and stock control, are something that we need to drive here at Corilla to maximise efficiencies. We plan to incorporate some of the ideas witnessed on the tour, e.g. a ‘slotted’ finishing table incorporating a receptacle for capturing waste and trimmings to aid housekeeping, and we will be rolling out more ideas shortly.”
In addition to insights into alternative production methods, Corilla Plastics is also exploring the possibility of developing a distribution network related to their marine sector as a result of introductions made on the tour.
Moulding Service would not allow its visitors to leave without experiencing more hospitality and the chance to reflect on the similarities between the UK and Italian sectors.
David White of Rotational Mouldings Group stated: “We found the trip extremely beneficial to experience first-hand how our counterparts in Italy deal with the day-to-day operations of a roto moulding facility. The factory tours gave a wide scope of manufacturing from proprietary products to custom moulding with various scale of product sizes in production. We picked up a few good ideas on operational techniques and we were impressed with the facilities, knowledge, and techniques on display particularly the different methods of safe access and bulk handling of materials.
It was a great experience for our younger team and good to
Association of Rotational Moulders Australasia Inc.
Tel: +61 (0) 7 3812 1450
www.rotationalmoulding.com
CEO: Michelle Rose
Cheif Executive Officer: Michelle Rose michellerose@rotationalmoulding.com
show that we have many common ideas in production control and focussed on producing good quality mouldings. Being able to tour different facilities highlighted our own strengths and also areas in which we can improve.
The hospitality and welcome given was warm throughout and thoroughly appreciated and it will be good to keep in contact and see if we can find any mutually beneficial business ventures in the future. It was also good to meet with other BPF members and establish connections with its companies.”
The close collaboration enjoyed between moulders and suppliers in IT-RO was familiar to members of the BPF Rotational Moulding Group. Members witnessed similar challenges faced by the sector and noted some of the innovative solutions that can help to move the sector forward to deliver quality rotationally moulded products that were visible at all four sites.
Graeme Craig added: “Travelling to Italy and seeing the high standard of work by IT-RO members was a perfect forerunner to the ARMO Conference 2023 in Poland. Sharing knowledge and best practice helps to raise the standard across the whole sector.”
Katia Zoppetti agreed: “The four IT-RO members that opened their factory doors to their British counterparts also felt enriched by the conversations that followed and are looking forward to the opportunity to return the visit. We are delighted with the feedback received from our members on the visit by the BPF’s Rotational Moulding Group and are looking forward to meeting up again in Poznan for ARMO in September.”
For more information about the Rotational Moulding Group of the British Plastics Federation, and future events contact gcraig@bpf.co.uk.
Association of Rotational Moulders Southern Africa PO Box 6966
Birchleigh 1621
Gauteng, South Africa
Tel: +27 82 772 3769
Fax +27 12 541 1738
Chairman: Grant Heroldt info@armsa.co.za www.armsa.co.za
IT-RO Italia Rotazionale
Katia Zoppetti
Via E. Brigatti 12
20152 Milano (MI)
Italy
Tel: +039 348 7652560
www.it-ro.it
Society of Asian Rotomoulders (StAR) 40/145, Ground Floor, Chittaranjan Park
New Delhi 110019
Tel: + 91-11-41630157
Fax: +91-11-41634952
Mob: + 91- 9810305356
sb.zaman@staraisa.org
arnacz@satyam.net.in
www.starasia.org
Association of Rotational Moulding (Central Europe) e.V. (ARM-CE)
MAUS GmbH - Rotationsgießformen
Am Viehweg 9 - D-76229 Karlsruhe
Amtsgericht Mannheim, HRB 103433
Tel.: +49 (0) 7 21 / 9 48 74 12
Fax: +49 (0) 7 21 / 9 48 74 44
Mr. Oliver Wandres, ARM-CE Chairman info@rotational-moulding.de www.rotational-moulding.de
British Plastics Federation
Rotational Moulding Group
6 Bath Place
Rivington Street
London EC2A 3JE
United Kingdom
Tel: 020 7457 5000
Fax: 020 7457 5045
Chairman: Mr. Philip Maddox PhilipM@LeafieldEnv.com
The Nordic Association of Rotational Moulders
Executive Board Chairman: Mr. Ronny Ervik
ul. Zielona 8, 61-851 Poznań, Poland
Tel: +48 607-126-004
Fax: +48 61-858-8611 info@rotomoulding-europe.org
www.nordicarm.org
SEPTEMBER 27-30, 2023
SEPTEMBER 10-12, 2023
NOVEMBER 7-10, 2023
JANUARY 28-30, 2024
MAY 6-10, 2024
StAR 20th Annual Conference and Trade Show
Uday Samudra, Kovalam Beach Front Kerala India
JUNE 9-14, 2024
NPE 2024
Orange Country Convention Center Orlando, FL npe.org
SEPTEMBER 24-26, 2024
Stephens
Lake Garda, Italy rotomolding.org
Rosemont, IL rotomolding.org
19 Diversified Mold & Castings
19800 Miles Road
Warrensville Hts., OH 44128-4118 USA
216.663.1814 | 888.642.1222
info@diversifiedmolds.com www.diversifiedmolds.com
84 ExxonMobil Chemical Co. PO Box 96126 West Springs Calgary, Alberta Canada, T3H 0L3 800.668.0177
kevin.c.jamieson@exxonmobil.com https://www.exxonmobilchemical.com /en/products-and-services/ polyethylene
5 Ferry Industries, Inc. 4445 Allen Road Stow, OH 44224-1093 USA 330.920.9200 sales@ferryindustries.com www.ferryindustries.com
9, 15, 47 Jerico Plastic Industries, Inc. 7970 Boneta Road Wadsworth, OH 44281 USA 330.334.5244
Minerva Plant: 330.868.4600 steve@jericoplastic.com www.jericoplastic.com
11 Matrix Polymers
The Priory Orchard Hill Little Billing Northhampton, NN9 9AG United Kingdom
+44.1604.789100
sales@matrixpolymers.com www.matrixpolymers.com
7 Orenda
165 Steelcase Rd. East Markham, Ontario L3R 1G1, Canada 905.513.8043
sales@orenda-automation.com www.orenda-automation.com
17 OREX Rotomoulding SP. Z O.O. Cieszyńska 6, 43-520 Chybie Poland
+48 32 440 83 15 magda.wantola@orex.pl www.orex-rotomoulding.com
73 Poliplast S.p.A. Via Carrali, 8 24020 Casnigo (BG) Italy +39.035.724145
info@poliplastspa.com www.poliplastspa.com
3 Powder King, LLC 41780 N. Vision Way Unit 120 Bldg. 2 Anthem, AZ 85086 USA 623.551.9897
sales@powder-king.com www.powder-king.com
57 Rock Lake Robotics 100 S. CP. Avenue Lake Mills, WI 53551 USA 920.648.3402
sales@rocklakerobotics.com www.rocklakerobotics.com
2 Roto Polymers 26210 Emery Road, Suite 202 Cleveland, OH 44128 USA 1.844.POLIMER (1.844.765.4637) info@rotopolymers.com www.rotopolymers.com
83 Rotomachinery Group Via Crosa, 53 28065 Cerano (NO) Italy +39.0321.772021 polivinil@polivinil.com www.rotomachinerygroup.com
61 SMAK Plastics, Inc. / RotoEdge Pro 9116 NE 130th Avenue, Suite 106 Vancouver, WA 98682 360.882.0410 Ext. 1707
14 VMP, Inc. 24830 Avenue Tibbitts Valencia, CA 91355-3404 USA 888.4.VMP.INC
661.294.9934
info@vmpinc.com www.vmpinc.com
59 Wittmann Battenfeld Canada Inc. / ROTOLOADTM 35 Leek Crescent Richmond Hill, ON L4B 4C2, Canada 905.887.5355
Toll Free: 1.888.466.8266
info@wittmann-group.ca
www.wittmann-group.ca
20 Xcelerant Growth Partners 624 W. Washington Avenue, #411 Madison, WI 53703 440.384.7654
info@xcelerantgrowthpartners.com xcelerantgrowthpartners.com
ARMO Showcase Special Section
22 Ferry Industries, Inc. 4445 Allen Road Stow, OH 44224-1093 USA 330.920.9200
sales@ferryindustries.com www.ferryindustries.com
23 Powder King, LLC 41780 N. Vision Way Unit 120 Bldg. 2 Anthem, AZ 85086 USA 623.551.9897
sales@powder-king.com www.powder-king.com
47 Jerico Plastic Industries, Inc. 7970 Boneta Road Wadsworth, OH 44281 USA 330.334.5244
Minerva Plant: 330.868.4600
steve@jericoplastic.com
www.jericoplastic.com