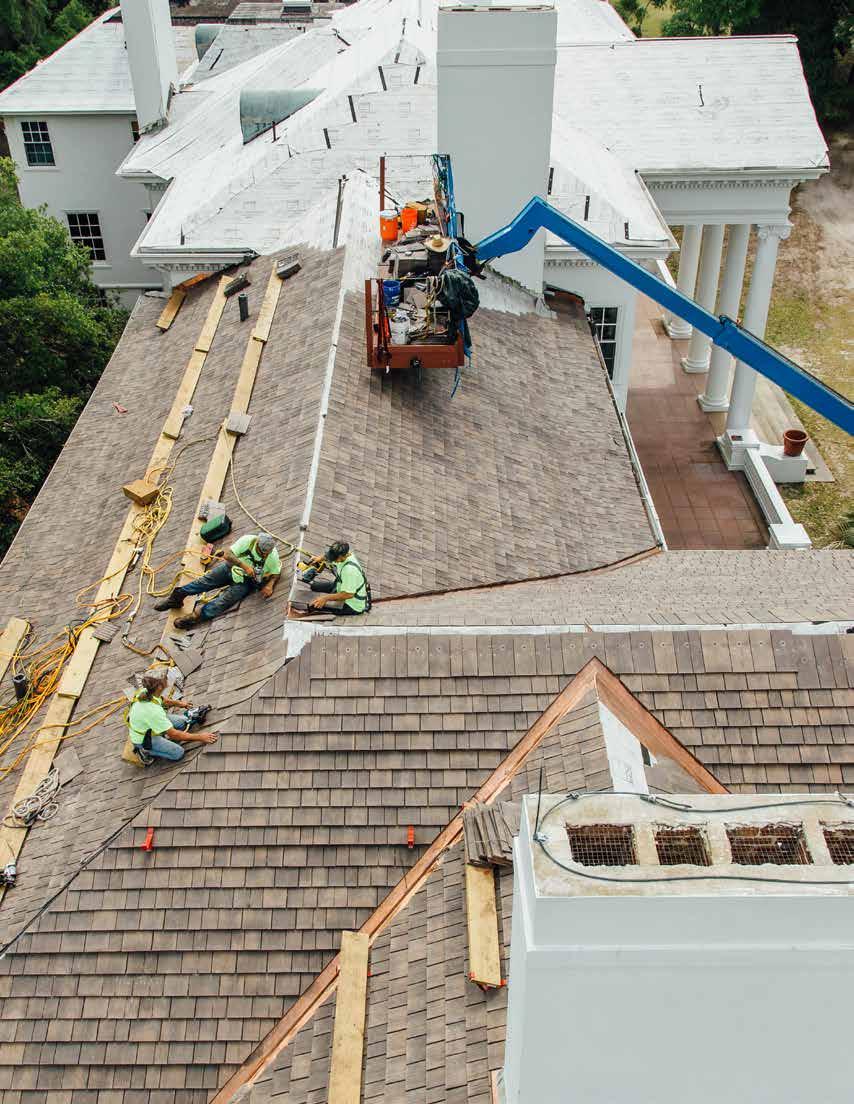
Stop by and visit us at: BOOTH #611
Stop by and visit us at: BOOTH #611
Every day ABC Supply associates from over 800 locations nationwide dedicate themselves to making your job easier. It starts with 24/7 access to pricing and order placement with myABCsupply and ends with your materials delivered accurately, complete and on time, every time.
Hassle-free returns.
Deliveries complete and on time. Every time.
Manufacturer Rewards SupportTM . 24/7 access to products, pricing and order placement with myABCsupply.
Experience the ABC Supply Difference.
FRSA-Florida Roofing Magazine Contacts: For advertising inquiries, contact: Lisa Pate at: lisapate@floridaroof.com
(800) 767-3772 ext. 157
All feedback and reprint permission requests (please include your full name, city and state) contact: Lisa Pate, Editor, at: lisapate@floridaroof.com
(800) 767-3772 ext. 157
Florida Roofing Magazine, PO Box 4850
Winter Park, FL 32793-4850
View media kit at: www.floridaroof.com/ florida-roofing-magazine/ #FRSA #roofingprotects
Equally strong and attractive , these metal roofing panels are available in Florida in our full line of PAC-CLAD painted steel, aluminum and Galvalume Plus coatings, ensuring that your roof will endure whatever comes its way. All panels are Miami-Dade County and Florida Building Code approved.
DuPont Tedlar, the global leader in technology-based materials and solutions, recently signed with SPE Foundation to sponsor various events and support the Foundation’s three-pronged approach to enrich and develop the future workforce for the plastics industry.
to training for its APOC brand of commercial and residential building products. The Tampa location complements contractor and installer training facilities in Andover, Mass. and Phoenix, Ariz. and expands the reach of ICP’s APOC MasterWorks Training and Education Program farther south and into the heart of tropical storm territory.
APOC MasterWorks training courses are designed to educate installers on the proper application of APOC products and systems, as well as to increase awareness of new technologies, application techniques, codes and regulations and industry updates. Courses offered include a one- to two-hour introduction to roof restoration and the more in-depth, two-day certified applicator training, which is required for any contractor installing an APOC system.
“The partnership with DuPont Tedlar supports our work in many ways. A scholarship for a student who will be joining us in a few short years, helping young women see the numerous STEM opportunities in plastics and polymer science through our Girl Scout patch program and bringing the PlastiVan to its local community, with whom DuPont team members can engage and inspire students through our hands-on K-12 plastics education programming, ” said Eve Vitale, SPE Foundation’s Chief Executive.
The collaboration will include a DuPont Tedlar Scholarship for a STEM student, PlastiVan Tedlar education at the Girl Scouts of America Phenom in Orlando and PlastiVan school visits in Buffalo with opportunities for DuPont employees to engage with the community.
“We are very proud to be working with SPE Foundation to help educate and support the next generation of plastics engineers,” said Matt Urfali, VP Sales & Marketing, DuPont Tedlar. “We especially look forward to collaborating with our New York manufacturing facility to help SPE bring in-person learning to local students.”
To better support the growing need for product education in the construction and maintenance industry, ICP Group recently opened its third facility dedicated
“Building and restoration activity continues to gain momentum throughout the Southeast,” said John Walker, ICP’s National Technical Manager, Roofing and Waterproofing. “Keeping up with that demand requires having top-tier knowledge of the very technical products being used for those projects. ICP’s training teams create tests and conduct live demonstrations so contractors can experience the products firsthand, which helps to educate and ensure competency, accuracy, safety and, ultimately, a quality result. Expanding our footprint to Tampa makes it convenient for contractors in this area of the country to access valuable training for high-quality installation,” Walker said. “We’re helping them not only to earn certifications but also to lead with knowledge and earn customers’ trust in the process.”
5,000 Industry Professionals
153,000 Industry-focused Digital Impressions monthly
When undocumented workers witness workplace safety issues, they may be hesitant to speak up. After all, if they sound the alarm and draw attention to themselves, they could be subject to deportation, right? Well, with a new policy announced by the Occupational Safety and Health Administration (OSHA) on February 13, that fear of immigration officials could be eliminated.
According to the new policy, which took effect on March 30, OSHA has been given authority during safety and health inspections to issue certifications that support U and T visa applications. These visas offer immigration status to noncitizens, permitting them to stay in the United States to assist authorities with investigations.
U and T visas were created as part of the Victims of Trafficking and Violence Protection Act of 2000.
■ U visas are suited for victims of certain criminal activities who have suffered significant mental
or physical abuse and have information about the crimes in question.
■ T visas are suited for victims of human trafficking who can assist law enforcement in investigating such crimes.
The Wage and Hour Division (WHD) of the Department of Labor began completing U visa certifications in 2011 for victims of five qualifying crimes related to its workplace investigations. Those crimes are trafficking, involuntary servitude, peonage, witness tampering and obstruction of justice. In 2015, WHD added T visa certifications and expanded the qualifying crimes to include forced labor, extortion and
U and T visas can be issued for up to four years and then can be extended. They can also be granted to family members. It is important to note, however, that the Department of Homeland Security has the final approval for granting these visas. The certification from OSHA is considered a recommendation.
By having the leeway to issue U and T visa certifications to undocumented workers during their site inspections, OSHA officials could gain information they otherwise would not receive. Immigrant workers will no longer fear retaliation from their employers or deportation from immigration authorities. Instead, they will have the option to speak freely about what they have observed.
Companies that illegally employ undocumented workers can no longer gamble on these workers keeping quiet about any questionable activity. Further, if such workers can receive a temporary visa in the process, they may be even more eager to assist OSHA with an investigation.
Assistant Secretary for Occupational Safety and Health, Doug Parker, explained it this way: “Expanding OSHA’s U and T visa certification authority helps the agency better fulfill its mission to make U.S. workplaces as safe and healthy as possible. Workers in the U.S.
need to feel empowered and able to trust OSHA and the U.S. Department of Labor enough to voice their concerns about workplace safety regardless of their immigration status and fears of retaliation.”
As always, it is essential that you maintain safe and secure worksites that comply with OSHA standards. This new policy is one more example of OSHA’s reach and its determination to root out safety hazards and violations. No matter who you employ, make every effort to follow OSHA regulations and keep your workers safe.
If you have questions about OSHA compliance or how this new policy could affect you, do not hesitate to reach out and use your member benefit.
The information contained in this article is for general educational information only. This information does not constitute legal advice, is not intended to constitute legal advice, nor should it be relied upon as legal advice for your specific factual pattern or situation.
Trent Cotney is a Partner and Construction Practice Group Leader at the law firm of Adams and Reese LLP and serves as FRSA General Counsel.
Adams and Reese LLP is a full-service law firm dedicated to serving the roofing industry. FRSA members can contact Trent Cotney to discuss and identify legal issues and to ask general questions through access to specialized counsel. They offer free advice (up to 15 minutes) for members. If additional legal work is required, members will receive discounted rates. This is a pro bono benefit provided to FRSA members only. To use this service, contact Trent Cotney, 813-227-5501.
As the Earth continues to warm, the effects of climate change become an increasing threat to homeowners in Florida. Among the concerns are hurricanes, which are growing in frequency and intensity. The Florida Climate Center at Florida State University indicates that the state’s hurricane season spans six months of the year, running from June 1 through November 30. The peak of the season occurs between mid-August and late-October when the waters in the equatorial Atlantic and Gulf of Mexico are warm enough to support the creation of tropical waves.
While Florida’s southeast coastline and Panhandle regions are extremely susceptible to hurricanes. It is a common misconception that there are parts of the state that do not get hurricanes. Since 1850, all of the state’s coastline have been impacted by at least one hurricane event.
Hurricanes can cause serious damage to Florida homes and roofs can be severely impacted. Therefore, contractors working in the state must become adept at assisting homeowners both before and after a hurricane or intense storm. Education and product selection are important areas of focus.
Following hurricanes, tornadoes and other natural disasters, homeowners with damage to their roofs are naturally anxious to get repairs completed quickly. At the same time, many others around them are also likely in need of repairs due to the same weather event. When disasters occur and demand is high for repairs, it creates an environment ripe for homeowner scams. Untrustworthy or outright fake contractors targeting homeowners to take advantage of situations like these, often making promises of repairs then skipping
town with the insurance money, never to be heard from again.
While they can’t prevent scam artists, reputable local and licensed contractors can and should help to educate homeowners in their region how best to approach repairs after a disaster to avoid getting scammed. By helping homeowners through the process, contractors can build trust with their prospective customers and increase the likelihood these homeowners will want to hire them; a win-win for both parties. When educating homeowners, there are five main areas of guidance to provide. These include advising homeowners to:
Start with Their Insurance Company – Homeowners should always get their repairs assessed before completing them to avoid having their claim denied.
Work with a Licensed and Insured Contractor
Consumers should view the Department of Business and Professional Regulation website to ensure there are no complaints and that the license is active and in good standing. Florida requires contractors to have workers’ comp coverage or a certificate of exemption that can be verified at www.floridaroof.com/wcproof.
Be Wary of Steep Discounts or Zealous Promises – If a contractor’s promises sound too good to be true, they probably are. Homeowners should keep in mind that it is unlikely a contractor will offer steep discounts
during a time of heightened demand (such as right after an intense hurricane).
No matter how anxious they are to get repairs done immediately, homeowners should always check the contractor’s reviews on Google, Yelp and the Better Business Bureau. Homeowners should also consider using tools that connect them with approved, vetted contractors, such as FRSA’s website or the state’s Disaster Contractors Network.
Cost, work to be done, time schedules, guarantees, payment schedules and other expectations should all be detailed and itemized.
While it may seem somewhat counterintuitive to give your potential customers all of this guidance, as it may encourage them to vet you, it will also help to build their trust in your professionalism and integrity – two things that will set you apart from unscrupulous competitors and outright scam artists.
Helping homeowners navigate the repair process following a hurricane or severe weather event is key but so too is the selection and installation of durable, resilient roofing materials ahead of any significant storms. The right materials can help prevent damage in the first place.
More specifically, homeowners should select from roof materials that will not only provide lasting beauty but will also withstand and perform against the region’s worst climate conditions. Florida is known for its hot and humid weather, as well as its severe wind. Because the roof is often the first point of contact for these conditions, it must act as the first point of defense. The complete roof system chosen, including the roof material and underlying components, should all be resilient options that are able to handle Florida’s specific weather risks.
Here are a few roofing material options and their resiliency and efficiency performance benefits in Florida’s hot and humid environment:
Sourced and manufactured from naturally occurring geologic material, clay and concrete tile is durable, sustainable, low-maintenance and easy to repair. Additionally, clay and concrete tile offers an excellent cool roof solution, maximizing energy efficiency and energy savings.
The thermal mass and above-deck airflow provided by clay and concrete tile systems make these products some of the most energy efficient available on the market today. Homeowners choosing tile over asphalt shingles can reduce their home energy bills by as much as 22 percent with a tile roof, as indicated
by the 2005 industry study, “Steep-slope Assembly Testing of Clay and Concrete Tile with and without Cool Pigmented Colors,” conducted by the independent Oakridge Laboratories. Note that results will vary based on the profile of tile installed, location, weather and other factors.
Stone-coated steel roofing systems are recognized for their durability, lighter weight and cost effectiveness, making them ideal for reroof or storm-damage applications. The strength of steel combined with the natural aesthetics and stone color deliver improved curb appeal while offering superior protection from severe weather events.
Stone-coated steel roofing panels are proven to resist high wind speeds, making this roofing option ideal in regions where high winds occur, such as Florida, Hawaii and the Caribbean coastal markets.
In addition to roofing material, the appropriate roof system and components should also be selected based on their ability to handle weather conditions and risks endemic to Florida. The underlayment is important to overall roof performance, resiliency and efficiency. A thermal insulating and reflective underlayment, which also protects from the elements, can act as a water barrier, energy-saving radiant barrier and insulation blanket all in one. An alternate underlayment solution is one with nail gasketing technology that provides all-season weather protection for steepslope applications of steel, tile, shake and shingle roofing. When an underlayment combines these benefits with UV and thermal stability, it can also be left uncovered and exposed for a period of time without degradation.
Another roof system consideration is flashing. Permanent options, as determined by IAPMO UES (ER-579) – that have undergone and passed rigorous 2000-hour UV testing – will maintain original performance properties, including adhesion to various roofing materials (for example, concrete, stone coated steel, polymer, aluminum, galvanized steel, vinyl and wood structured panels). Ideally, such flashing may be used for applications including step flashings, headwalls, pipe penetrations, pitch transitions, valley junctures, valley soakers, chimneys and skylights, as well as for various repair applications and tricky details requiring weather protection. Lead-free flashing options are ideal and safer than options that incorporate lead.
Robin Anderson is Technical and Strategy
Development Manager at Westlake Royal Roofing Solutions, a leading provider of durable, resilient roofing systems and components. For more information, visit www.westlakeroyalroofing.com.
FRSA will be offering a total of 31 hours of industry-specific continuing education (C.E.) seminars during the Convention, where you’ll be able to earn up to 11 hours of continuing education credit over three days. Continuing education seminars include:
FBC 8th Edition Roofing Related Changes | 2.0 hour G
FRSA-TRI 7th Edition Tile Manual | 1.0 hour G
Fall Protection – What Employers Need to Know | 1.0 hour WPS
How to Start or Grow a True Service Department | 1.0 hour G
Wind Mitigation Methods, the Law! | 1.0 hour WMM
Lightweight Insulating Concrete Roof Decks | 1.0 hour G
Reputation Management Legal Issues | 1.0 hour BSP
The OSHA Inspection and Citation Process | 1.0 hour WPS
Top 5 Insurance Issues in Roofing | 1.0 hour L+R
Estimating the Right Way | 1.0 hour BSP
Tile Hip and Ridge Installation | 1.0 hour G
FBC Requirements for Underlayments | 1.0 hour G
July 12-14, 2023 Kissimmee, FL
For a complete list of seminars, visit www.floridaroof.com/convention
In addition to industry-specific seminars, we’ve added business management, sales and promotion seminars. These courses do not carry C.E. credit and include:
Contractor Blueprint Bootcamp
– KPI Managing by the Numbers | 6 hours (no C.E. credit)
KPI Managing by the Numbers | 1 hour (no C.E. credit)
Effective Digital Marketing and Lead Optimization | 1 hour (no C.E. credit)
Registration is required for all attendees and fees apply for all seminars.
www.floridaroof.com
It seems as though the requests for roofing contractors to attest to certain facts or opinions in writing continue to increase with each year. Whether it is a re-nailing affidavit, an I-complied-with-the-buildingcode affidavit, a hurricane mitigation inspection form or a roof condition inspection form, these requests have become a big part of the roofing business. The proliferation of these very confusing forms can be overwhelming. Which ones should I sign and which ones am I prohibited from signing?
During the property insurance reforms enacted by the legislature over the last couple of years, a new category of roof inspection was created. It has to do with the overall condition of the roof and when it can be required to be replaced for insurance purposes. The language used to describe those who can complete an inspection and those who can sign any related forms is almost identical to the language used to describe who can do the same on roof mitigation inspections. Those sections from the Florida statutes are shown below. If your qualifications as an “authorized inspector” include those described in one through five, it is clear that you meet the requirements if you are approved by the insurer. Please note that roofing contractors are not included in those five categories. This leaves those holding a roofing contractor’s license with category six.
(5)(a) As used in this subsection, the term “authorized inspector” means an inspector who is approved by the insurer and who is:
1. A home inspector licensed under s. 468.8314;
2. A building code inspector certified under s. 468.607;
3. A general, building, or residential contractor licensed under s. 489.111;
4. A professional engineer licensed under s. 471.015;
5. A professional architect licensed under s. 481.213; or
6. Any other individual or entity recognized by the insurer as possessing the necessary qualifications to properly complete a general inspection of a residential structure insured with a homeowner’s insurance policy.
(b) An insurer may not refuse to issue or refuse to renew a homeowner’s policy insuring a
residential structure with a roof that is less than 15 years old solely because of the age of the roof.
(c) For a roof that is at least 15 years old, an insurer must allow a homeowner to have a roof inspection performed by an authorized inspector at the homeowner’s expense before requiring the replacement of the roof of a residential structure as a condition of issuing or renewing a homeowner’s insurance policy. The insurer may not refuse to issue or refuse to renew a homeowner’s insurance policy solely because of roof age if an inspection of the roof of the residential structure performed by an authorized inspector indicates that the roof has 5 years or more of useful life remaining.
(d) For purposes of this subsection, a roof’s age shall be calculated using the last date on which 100 percent of the roof’s surface area was built or replaced in accordance with the building code in effect at that time or the initial date of a partial roof replacement when subsequent partial roof builds or replacements were completed that resulted in 100 percent of the roof’s surface area being built or replaced.
(e) This subsection applies to homeowners’ insurance policies issued or renewed on or after July 1, 2022.
Many roofing contractors have been completing the roofing portions of the mitigation forms for years. Some forms encourage them to do so (see highlighted section of forms below). Other forms point out that it may be illegal to sign them as in this section from the Uniform Mitigation Verification Inspection Form - OIR-B1-1802 (Rev. 01/12) Adopted by Rule 69O170.0155 also shown below.
An individual or entity who knowingly or through gross negligence provides a false or fraudulent mitigation verification form is subject to investigation by the Florida Division of Insurance Fraud and may be subject to administrative action by the appropriate licensing agency or to criminal prosecution. (Section 627.711(4)-(7), Florida Statutes) The Qualified Inspector who certifies this form shall be directly liable for the misconduct of employees as if the authorized mitigation inspector personally performed the inspection.
When you join materials together, you create a precise bond, a vital connection that builds strength in every direction. This is not just how our products functionit’s how we function too. ICP delivers innovation and excellence from roof to floor. Our extensive array of professional grade coatings and adhesives builds the first layer, but our bonds extend well beyond the surface.
At ICP, we stand behind our solutions, and we’re constantly pushing the building envelope towards enduring success.
Also included in this commonly used form is this statement that requires individuals other than contractors licensed under 489.111 or 471.015 to personally inspect the structure, which can’t be done by an employee. Since roofing contractors are licensed contractors under 489.111, we may be able to have an employee do the inspection but the same form included in section 3 above, shows only A general, building, or residential contractor licensed under s. 489.111. So, who can physically do the inspection? The form makes this confusing.
Individuals other than licensed contractors licensed under Section 489.111, Florida Statutes, or professional engineer licensed under Section 471.015, Florida Statutes, must inspect the structures personally and not through employees or other persons
Licensees under s.471.015 or s.489.111 may authorize a direct employee who possesses the requisite skill, knowledge, and experience to conduct a mitigation verification inspection.
The lack of respect and consideration given to licensed roofing professionals in all of this is frustrating, to say the least. Like other professionals, we have demonstrated our knowledge and experience in our trade. Many, if not most of those “authorized inspectors” listed in sections one through five, lack extensive roofing knowledge and often rely on a familiar roofing contractor or consultant to provide that expertise. So, who is more qualified to inspect roof coverings and roof systems than a licensed roofing contractor who has demonstrated his or her extensive knowledge of roofing?
Uniform Mitigation Verification Inspection Form – Excerpt from Page 4
NEW FOR 2023! MFM introduces IB-3™ StormStopper Plus, designed specifically for the Florida roofing market. Stop storm damage in its tracks and offer your customers a qualified FORTIFIED PROGRAM product for years of worry-free service. This 50-mil, self-adhering roofing underlayment features a granulated surface and a non-removable selvedge edge for a secure seal on overlaps for whole roof protection.
A similar lack of respect may also be demonstrated in another piece of recent legislation, SB 4-D. Among other changes, it created mandatory inspections of existing buildings meant to address the Champlain Towers South Condominium Building collapse in Surfside. The bill includes specific steps the condominium association and inspectors must take regarding the inspections.
(2) As used in this section, the terms: (a) “Milestone inspection” means a structural inspection of a building, including an inspection of load-bearing walls and the primary structural members and primary structural systems as those terms are defined in s. 627.706, by a licensed architect or engineer authorized to practice in this state for the purposes of attesting to the life safety and adequacy of the structural components of the building and, to the extent reasonably possible, determining the general structural condition of the building as it affects the safety of such building, including a determination of any necessary maintenance, repair, or rep lacement of any structural component of the building. The purpose of such inspection is not to determine if the condition of an existing building is in compliance with the Florida Building Code or the firesafety code.
(g) Structural integrity reserve study.
1. An association must have a structural integrity reserve study completed at least every 10 years after the condominium’s creation for each building on the condominium property that is three stories or higher in height which includes, at a minimum, a study of the following items as related to the structural integrity and safety of the building:
a. Roof.
b. Load-bearing walls or other primary structural members.
c. Floor.
d. Foundation.
e. Fireproofing and fire protection systems.
f. Plumbing.
g. Electrical systems.
h. Waterproofing and exterior painting.
i. Windows
Since these condominium inspection requirements are relatively new, it remains to be seen who will ultimately be allowed to do the roofing portion of the inspection. Based on the previous information, it may be fair to assume that whatever is implemented won’t take roofing contractors and the knowledge they possess into consideration.
You can see by the small representation of the forms shown here how hard it is to arrive at an answer as to which ones you should sign or not sign and how confusing they are to say the least. Included in most of the list of “authorized inspector” requirements, we do have this:
6. Any other individual or entity recognized by the insurer as possessing the necessary qualifications to properly complete a general inspection of a residential structure insured with a homeowner’s insurance policy.
In my opinion, the “recognized by the insurer” language can be helpful. There is a simple fix that will allow you to assert that you are, in fact, recognized by the insurer. Have your customer request that their insurer or insurance agent send you the form that they would like you to complete, along with a request from the insurer or agent to do so. It will be difficult for anyone to argue that you are not recognized by the insurer when they ask you to complete a particular form
and provide the form to you. Copy the letter or email and the form and keep them in your job or inspection file. This approach may not address all the possible concerns or answer all your questions, but hopefully it will help.
The decision to sign or not to sign these documents rests with you as the license holder unless you are contractually obligated to do so. Caution should be exercised. As with all information provided in this column, this is not to be construed as legal advice but is
Commercial Roof Condition Inspection Form – Excerpt
meant to bring important information to your attention so you can make an informed decision about how you should proceed. That process may include seeking legal advice.
FRM
Mike Silvers, CPRC is owner of Silvers Systems Inc., and is consulting with FRSA as Director of Technical Services. Mike is an FRSA Past President, Life Member and Campanella Award recipient and brings over 40 years of industry knowledge and experience to FRSA’s team.
Employee record keeping is one of those necessary evils that can be tedious and time consuming, especially if you are trying to run a business while ensuring required documents on new hires are filed on time. Record keeping may seem like a burden until a lawsuit or discrimination case is filed against you. Then you’ll be glad you took the time to document employee files properly. But how long do you need to keep files? If an employee is active with your company, you’ll need to keep those records as long as they are employed and at least three years after they leave. However, there are parts of the files that you don’t need to keep long-term.
While there are a few payroll records you can get rid of at the two-year mark, including records that pertain to pay increases, timecards, schedules and wage rate tables, you’ll need to keep the majority of your payroll records on hand for at least three years.
As the years pass and you hire more hourly employees, those payroll records can quickly become a lot to keep track of. Let’s review how long you need to keep different types of payroll records and when it’s safe to clear them out.
Before we jump into how long to keep your payroll records, you should know why proper recordkeeping is so important in the first place.
Federal, state and local laws require you to keep your payroll records. If you don’t keep them, not only are you breaking the law but you’re putting yourself at serious risk. If you were ever to get audited, sued or have any other type of legal action brought against you or your business, you wouldn’t have the records to defend yourself and you could lose a lot of time, money and energy as a result.
Payroll record retention is a must for protecting your business. The question is how long do you need to retain those records? The Department of Labor recommends at least three years for the following records:
■ Payroll records – from the date of last entry, all payroll or other records containing employee compensation information.
■ Age certificates, salary plans and employee contracts.
The following records should be retained for at least two years:
■ All employment, time sheets and earnings records
– from the date of last entry, time and earning cards or time sheets on which you have entered the daily starting and stopping time of the individual employee.
■ Wage rate tables – from their last effective date, tables or schedules of the employer which provide the piece rates or other rates used in computing straighttime earnings, wages, salary or overtime excess compensation.
■ Work time schedules – from the last effective date, schedules or tables used by the company which establish the hours and days of employment of individual employees.
■ Records of addition to or reductions from wages of employees – for example, authorizations for payroll deductions.
It’s important to note that records for previous employees should be kept for at least three years. In addition, employment applications should be retained for two years whether the person was hired or not. I-9 forms must be retained for three years after the date of hire or one year after the date the employment is terminated, whichever is later and must be stored in a separate folder from all other information. This folder should only contain an I-9 form for employees that meet the timeline requirements above. For companies that don’t have a human resources department, the task of keeping employee records may seem daunting. Below is a list of items that should be included in an employee file under the following sections:
■ Checklist for new employees
■ New employee personal information – emergency contact info.
■ Employee acknowledgement of probationary period
■ Receipt of employee handbook
■ Job description
■ Exemption test
■ Job application
■ Employment agreement.
Education (Training and Development)
■ Resumé
■ Recommendation letters
■ Diplomas
■ Certifications
■ Trainings
■ In-house training/seminars notification letters/ emails
■ Awards
■ Recognitions
■ Resolutions
■ Notes or letters from customers about employee.
Employee Relations and Performance Appraisals
■ Performance appraisals
■ Employee warning notices
■ Counseling sessions.
Separation Notices
■ Exit interview checklist
■ Separation notice form
■ Resignation letter (if applicable)
■ Record of documents given.
Payroll Information
■ Tax forms (W-4’s)
■ Authorization for deductions
■ Payroll change notices.
Time Sheets
■ Time log forms.
Time Accrual/Taken Forms
■ Leave request forms
■ Employee time log reports (end of the year report).
You should also consider keeping a separate confidential file on each employee that includes:
Confidential File
■ Medical information (including medical questionnaires and health insurance info.)
■ Life insurance
■ Long-term disability
■ Workers’ compensation documents (injury/illness reports, claims, etc.)
■ Drug-free program
■ Drug test results
■ Doctors notes with specific health information
■ Garnishment notices
■ Criminal background records.
This information is a starting point for keeping accurate and legal employment records. FRSA members can utilize services through Seay Management Consultants. If you have more serious human resource concerns or need more detailed information, they can provide you with an anticipated expense for the service. Members can also access more human resources information through the Member Login section on FRSA’s website, www.floridaroof.com.
There is no shortage of Professional Employer Organizations (PEOs) targeting the roofing industry. PEOs are most frequently utilized to help newly established or emerging roofing contractors secure workers’ compensation insurance for their first few years in business. The PEO providers are occasionally re-engaged later, after a roofing contractor experiences a severe injury with their stand-alone workers’ compensation carrier. While PEOs commonly provide payroll services and workers’ compensation benefits to roofing contractors, we find many contractors are not always completely aware of what fees are charged by the PEO for their services and what limitations there can be from a workers’ compensation insurance coverage perspective. This article aims to answer some frequently asked questions about PEOs from roofing contractors.
What is a PEO and How Does it Work?
PEOs, sometimes referred to as employee leasing
arrangements, are organizations that were developed to help small to midsize businesses outsource their human resources, payroll, employment taxes and workers’ compensation related functions. For the PEO to provide these services, the PEO becomes the co-employer and essentially leases the employees back to the roofing contractor. Though the roofing contractor still officially hires its employees, the PEO coordinates business functions as a co-employer and the contractor pays the PEO for its services (often a percentage of total salaries) as well as payroll for the employees.
Due to the risk of severe injury inherent in the roofing industry from a workers’ compensation perspective, many “stand-alone” workers’ comp carriers are not willing to offer workers’ comp policies to newly formed roofing companies with no performance rating or track record. The PEO market offers a solution to this underserved emerging contractor segment. They also create an ease of business by allowing the roofing contractor to focus on revenue generating activity, outsourcing the back-office related human resources and provide some tax-related accounting functions. In theory, PEOs also assume the liability of adhering to the legal tax and workplace standards as the administrative employer.
While there are various opinions voiced about difficulties in working with PEOs, the two most objective drawbacks of PEOs we commonly observe are the cost structure and the potential insurance coverage gaps for the roofing contractor. Most PEOs administrative fees are charged as a percentage of total payroll (typically 2-5 percent), which can be quite costly as a roofing contractor increases his or her staffing and associated payroll. They will also charge weekly minimum fees, which often exceed cost for weeks with lower payrolls due to production gaps or weather conditions when crews don’t work.
As for the potential insurance coverage gap, only the employees on the PEOs roster are eligible for workers’ comp benefits. Put another way, unless the employer follows the PEOs required steps to notify the PEO of an added employee, the PEO and its workers’ comp insurance carrier will exclude that employee from coverage and then deny any claims. PEOs offer workers’ comp benefits individually to each employee on a roofing contractors’ roster, whereas a stand-alone workers’ comp policy extends to anyone working for the roofing contractor. Stand-alone carriers charge premiums based on processed payroll but will cover anyone working for the roofing company. Two common scenarios that leave a roofing contractor exposed are:
Case Study #1: There are five employees on the roster for the day and one of the crew members brings a friend or family member to make extra money one day. That additional person does not have workers’ comp coverage. If that person is injured on the jobsite, the roofing contractor would be obligated to absorb all medical, wage loss, impairment benefits, legal fees and future medical treatment for the duration of the injured workers’ injuries.
Case Study #2: The prime roofing contractor that has a PEO for workers’ comp coverage hires a subcontractor who also has a PEO for workers’ comp. If the subcontractor is not regularly updating their PEO roster and one of their employees not listed on the roster is injured, the cost of the claim would rise upstream to the prime roofing contractor. When this claim rises upstream, the prime roofing contractor’s PEO is not obligated to protect their interests, as the subcontractor’s employee is not on the prime contractor’s roster either. In this situation, the prime contractor would be obligated to absorb all medical, wage loss, impairment benefits, legal fees and future medical treatment for the duration of the injured workers’ injuries.
A further outcome of this second scenario is that the prime contractor will often bring a lawsuit against the subcontractor for amounts that the prime contractor had to pay for the injured worker. Of course, the prime contractor would most likely no longer be using this subcontractor for any additional work.
Both scenarios can result in massive, unfunded and unforeseen financial burdens that could potentially bankrupt a roofing contractor.
The answer to this question will be different for every roofing contractor because it is dependent upon several factors including the size of the workforce, years in business, percentage of subcontractor usage and the owners experience in the roofing industry. PEOs are often the starting point for a roofing contractor and create an ease of business for firms not well equipped to handle internal payroll, taxes and human resource-related functions. From a risk management perspective, the roofing industry recognizes that a stand-alone workers’ comp policy will protect a roofing contractor from potentially catastrophic uncovered workers’ comp claims. If you are a roofing contractor and find yourself contemplating this question, reach out to a roofing insurance and risk management expert to help your roofing business consider how best to protect employees and your organization.
FRMMany articles written about fall protection discuss the slope of the roof and occasionally the width of the building when determining what type of fall protection can be used. A clear understanding of how to determine both the slope of the roof and width is essential.
Slope is defined as “a surface of which one end or side is at a higher level than another; a rising or falling surface.” OSHA provides terminology for a low-slope roof as “a roof having a slope less than or equal to 4 in 12 (vertical to horizontal),” and steep-slope roof as “a roof having a slope greater than 4 in 12.” Regardless of the type of roof system being installed or removed, the substrate deck is used to determine the slope of the structure.
Since this article is specifically addressing the slope and width in relation to fall protection systems, it’s a good time to review the systems permitted with different roof slopes. For steep-slope roofs, contractors are limited to conventional fall protection systems, which include personal fall arrest (harness, lanyard, rope-grab, lifeline and individual anchor point), safety net and guardrail systems. For low-slope roofs, two additional fall protection systems are permitted for roofing work – warning line and safety monitoring systems.
There are many structures that may have multiple roof slopes on the same working surface. In these situations, the greatest elevation on the surface must be used to determine the type of fall protection required to be used on that working level. For instance, the rear side of the structure may be a 4 in 12 slope and the front side of the structure may be a 6 in 12. If the two roof areas join at the roof ridge or hip at the same elevation and are not broken by a firewall parapet or break in elevation, the two roof areas are considered to be one surface and therefore the type of system used would be limited to those associated with a steep-slope application. Similarly, there are structures where the perimeter of the roof surface is either greater or less than the field of the roof of the structure. Again, if the two roofs join and are not broken by a firewall parapet or break in elevation, they are considered to be one surface and therefore the type of system used would be limited to those associated with a steep-slope application.
There are many devices and phone applications that can be used to determine the slope of the structure and have the ability to provide such documentation as slope determination using a photograph. Regardless of the instrument utilized to determine the slope of the structure, documentation of the measurement must be made prior to work beginning.
Due to the configurations of many structures, it is often difficult to determine the width of the roof. The width of an area is the lesser of the two primary dimensions of the area, as viewed from the aerial view. OSHA has provided a reference table within the regulations in section 1926 Subpart M Appendix A to illustrate the ways in which a contractor is expected to measure a roof to determine the width of the roof. They are available at www.floridaroof.com/osha1926. When considering fall protection, the slope of the roof must be taken into consideration first. If the roof is determined to be a 4 in 12 slope or less, the fall safety monitoring system may be used alone without any other type of fall protection on the areas where the roof width is 50 feet or less. For all roof areas with a slope of 4 in 12 or less and a width greater than 50 feet, the fall safety monitor system must be used in conjunction with another type of fall protection system. Please note that there is no distinction within the OSHA regulations pertaining to the type of roof –residential or commercial – only the slope and width of the roof.
Regardless of the type of fall protection system utilized during roofing operations, regulations pertaining to documented training, correct set-up and documented verification throughout the project must be maintained by the employer.
The FRSA Self Insurers Fund (FRSA-SIF) has professional safety consultants throughout the state who are able to provide SIF members with safety training at no additional cost. To find out if you qualify for FRSASIF workers’ comp insurance, please contact Alexis at 800-767-3772 ext. 206 or email alexis@frsasif.com.
To learn more about the FRSA Self Insurers Fund, please visit www.frsasif.com.
PAC-CLAD’s new Ore finishes provide the look of natural metal patinas with the durability and consistency of a PVDF finish. Unlike expensive and unpredictable natural metals, these 16 beautiful finishes will not tarnish, discolor or rust. Available on PACCLAD wall and roof panels, coil and sheet in aluminum and steel. Consult a PAC-CLAD representative for warranty and lead times. For more information and for Petersen’s full product line, please visit pac-clad.com.
Carlisle's introduction of the industry's first-ever 16-foot-wide TPO sheet brings labor savings and efficiency to get more done in less time. With fewer rolls to load onto the roof, less time spent positioning and kicking out rolls and fewer seams to weld, 16-foot wide TPO is the fastest and most efficient way to install adhered and induction welded TPO roofs.
For more information please visit www.carlislesyntec.com.
Integrity Metals, LLC announces the release of the latest addition to its Snap-Lock Clip Series of standing seam metal roofing panels. The IM550SL offers a sleek profile for both residential and commercial applications while providing the strength and versatility you expect from a standing seam panel. Available in 26- and 24-gauge steel as well as .032 and .040 aluminum, the IM550SL panel is ideal for use in most deflected decking environments where a nail-strip panel would telegraph deflection. Florida Product Approved. For more information on this product and others, please visit www.integritymetalsfl.com.
MFM is proud to introduce IB-3 StormStopper Plus, a new self-adhering, 50-mil, granulated surfaced roofing underlayment. The underlayment features a non-removable selvedge edge for a secure seal on overlaps for whole roof protection. IB-3 StormStopper Plus does not require priming of the roof deck due to an enhanced adhesive system for aggressive adhesion. IB-3 StormStopper Plus meets ASTM D 1970 and has Florida Building Code Product Approval FL 41919.1. For more information or to request a free sample, please visit www.mfmbp.com.
A.C.T. Metal Deck Supply announces the release of its Metal Deck 101 Videos that will give industry professionals a resource to enhance their knowledge about metal decks, metal deck accessories and address frequently asked questions.
“Today, more than ever, consumers are viewing videos to receive their information,” states Carm Termini, Marketing Director. “We offer the best way to educate our customers about the features, usage and properties of metal deck.” The video library contains 13 videos, in both English and Spanish versions, is housed on its web and mobile sites along with a YouTube channel. For more information, please visit www.metaldecksupply.com.
Roof Hugger has recently completed extensive testing on their sub-purlins. that shows, in many cases, they can add capacity to existing building purlins.
Roof Hugger has developed software that analyzes the existing building without Huggers and then with Huggers added, to determine if they can add strength and, if so, how much. This is a new application for Roof Hugger and an industry first. For more information, please visit www.roofhugger.com.
One of the most difficult management skills to learn in the roofing industry is using market cycles and changes in volume to your advantage. Roofing and construction are highly cyclical; however, the cycles are rarely analyzed to understand their fundamental conditions or symptoms. Another challenge is that owners and senior managers often cannot react correctly to the company’s current cycle because they are usually still reacting to the last cycle.
For example, if the company has just been through a fast growth period where good people were hard to come by, management may hesitate to let go of productive workers even though the company can’t keep them busy. This is especially true if leadership feels that the expected volume of work will return soon.
Similarly, if a company has been through a long cycle of stagnation or decline and has cut back its overhead severely, when the market rebounds it will be slow to add overhead back because it was so painful to reduce. A growth stage often must last for a considerable period of time before an owner will feel comfortable enough to build up general and administrative departments again.
In a significant growth cycle, say 15 to 20 percent or more from one period to the next, a roofing company will likely go through some or all the following conditions:
■ Higher incidence of “bad” jobs, customer challenges and fading margins.
■ Cash flow difficulties, including increasing underbillings, problem receivables and unexpected debt.
■ Administrative challenges including slower or poor quality information and delayed billings.
■ Growing demands for capital expenditures.
■ Human resources challenges including implementing compensation systems, high turnover, lack of training and stress.
■ In the early part of a fast growth stage, the net income percentage improves because the company stretched out the overhead over a larger volume of work but the balance sheet ratios will show stress.
■ In the latter phases of fast growth, the profitability may return to normal or less, while the balance sheet ratios may show extreme stress.
In a decline stage, where volume falls by 15 percent or more, a roofing company will likely experience some or all the following conditions:
■ When work slows down, employee performance does too. Crews notice the decrease in the number of projects and tend to slow down out of fear of not having another project to start.
■ The estimators feel pressure to get work, so they lower margins, use unrealistic productivity figures and other aggressive assumptions.
■ The overhead is too high for the smaller volume, especially when margins shrink.
■ Outside creditors and bonding companies react to the income statement stress, get nervous, reduce credit capacity, require more frequent or demanding reporting and tighten terms.
■ The company struggles with reducing overhead, first with belt-tightening and then with more painful measures.
■ Field overhead or indirect costs are too burdensome and the company struggles to reduce them while running jobs effectively.
Managing overhead is one of the greatest challenges a company will face when it grows or shrinks in size. A company’s overhead structure doesn’t and shouldn’t grow or shrink in direct proportion to volume changes. G&A tends to grow and shrink in a stair step pattern, staying reasonably constant throughout the revenue range. For example, a company needs a certain amount of overhead to perform and control a certain amount of work productively. However, once a company crosses a certain upper volume threshold that generates too much stress on the organization, the company will need additional overhead. The company can grow to a higher volume level with the extra overhead. When the company grows enough to cross another volume threshold, more overhead will be required and the cycle repeats itself.
It is common for a roofing contractor to grow overhead in stair steps, escalating G&A up to a new step as the company crosses a threshold, then moving across the step to higher volumes before hitting the next step. As the company volume grows, moving toward the right side of the step, profits increase but stress also increases. On the left edge of the step, while the company is at the lowest volume in the range, profit is the worst and, generally, stress is lowest at this edge. The right edge of the step has the highest profit and stress.
Consider this stair step concept in conjunction with the conditions of market cycles. Suppose a company is declining in volume and starts at the step’s right side or stressed side. In that case, you should be able to project how far the company can fall in volume – move to the left side of the step –before you must make a dramatic change in G&A. The more to the left side of the step the company starts, the more quickly you must react and cut overhead. If a company starts growing rapidly, the same idea
side of the step, the longer management must react as the company moves to the right side. Most companies add incremental overhead enhancements as they move to the right but few are likely to make substantial additions until they are forced to do so.
The place to stay comfortable is near the center of the step. Unfortunately, that is hard to do. If a company tries to stay close to the right edge of the step, the stress will eventually cause too many breakdowns and if the company tries to stay on the left side, the high overhead will eat up the profit. Even if the volume doesn’t grow, overhead pushes the company back to the left edge of the step.
Next month, we will discuss using cycles positively, fighting the tendencies in consecutive cycles and the steps to take to be successful in your roofing business.
If you would like any further information on this or another subject, you can contact John at jkenney@cotneyconsulting.com.
Carlisle Construction Materials, headquartered in Carlisle, Penn., announced the donation of over 18,800 pairs of socks to communities in need. Socks are the number one most requested item at shelters around the country, with over 500,000 individuals experiencing homelessness on any given night.
During the month of February, Carlisle collected socks at 28 facilities around the United States. The initiative, called “Sockuary,” helped to impact 17 organizations, from youth-oriented groups like Preble Street Teen Services in Portland, Maine, to emergency shelters like Helping Hands House in Puyallup, Wash. In a statement, Carlisle says it has always tried to be a good corporate steward with initiatives like “Sockuary.”
“This was the first time we have done a nationwide company initiative,” said Mike DuCharme, Vice President of Marketing and sponsor of Carlisle Construction Material’s Community Stewardship Team. “We were excited to see the level of employee engagement around this initiative and the impact that we were able to make. Our company has
demonstrated a commitment to the communities in which it operates and we are already looking toward our next project.”
FRSA is proud of the volunteer work completed by members in the industry and would like to share those projects as often as possible. If you have a community service project you’ve completed, please send the information to Lisa Pate at lisapate@floridaroof.com.
Enriching the lives of young adults on the verge of homelessness.
Dozens of Central Florida young adults have lived at The Faine House, opened their first bank account, found employment, attended technical school or earned a college degree. Through The Faine House, young adults have the chance to discover themselves and what a future outside of the system can hold.
floridaroof.com/charityofchoice
Everyone pays the same workers' comp rate, but does your workers' comp insurance carrier provide you with the potential for a yearly dividend for operating safely? If not, you need to consider the FRSA Self Insurers Fund. These members received their share of $3 million during FRSA's Convention. For more information about joining the Self Insurers Fund, contact Alexis at 800-767-3772 ext. 206 or by email: alexis@frsasif.com
How did you get started in the roofing industry?
In 1984, I went to work on the roof for Pritts, Inc. out of Ft. Lauderdale and, within a short period of time, went into sales and estimating. After two years, we started Pritts-McEnany in Jacksonville, staying there long enough to get married and almost go broke. Then we decided to pack everything in my blue van and move down to Plant City, roughly 20 miles east of Tampa, and start McEnany Roofing, Inc.
What’s your favorite part of the job?
I love to get work that’s not bid out. Realizing that owners have put their money and trust in McEnany Roofing, Inc., is a great responsibility. That really motivates me. Also, I get a front-row seat watching the men and women around me living out the American Dream, many starting with nothing and growing into new vehicles, homes, families, college, etc.
What is the most unusual roofing project that you’ve been a part of?
Almost everything we do is for Disney. All of the themed roofing, China, Germany, the two $20,000 gold laced ornate pieces installed at the completion of Japan. We roofed The Tower of Terror completely off a crane and the Regions Bank project was 600 feet in the air and a 21/12 slope, where we replaced the metal roof and a lot of metal decking. We love challenges!
What do you consider a waste of time?
Being stuck in traffic - I-4, I-75, I-275. I avoid heavily traveled roads and traffic jams at all costs.
What is your favorite vacation?
Anywhere I can go with my family. I also enjoy my turkey hunting trips in the spring to Texas and Chihuahua, Mexico.
What would be your dream job?
I really wanted to get into Forestry Management, but when I realized you had to take Calculus and knowing that I failed pre-Calculus, I changed my mind. I still have a great passion for Forestry Management, minus the Calculus.
If you could spend time with three people (living or not), who would they be and why?
The Apostle Paul, learning about his conversion and his path to Rome. John Muir (Naturalist). He saw Florida and woodlands, swamps, wildlife and people before development. My father, who I lost when I was six years old.
What do you personally find most rewarding about being involved with FRSA?
The fact is that we (Florida roofing contractors) have a full-time advocate working for us in Tallahassee or wherever it’s necessary. There is a common bond that runs through all contractors in Florida and that is FRSA.
What advice would you give someone interested in joining the roofing industry?
Just do it! It’s for any man or woman who loves to be outdoors or at least not stuck behind a desk all day. Working with “real people” on the roofs, having the freedom to decide who you will work with, being a part of a team, building our brand. This is a dynamic industry that cannot be duplicated with robots.
What would surprise others to learn about you?
Leanne and I have three wonderful kids, Kayleigh, Michael and Ryan. All with heavy influence from their mother. Our oldest, Kayleigh was President Trump’s Press Secretary.
Double Down on Your Protection! Offer homeowners the assurance of long-term waterproofing with exposure ratings available up to 365 days when using Polystick ® self-adhered roof underlayments in a 2-ply system.
Imagine what’s next! Polyglass.us/polystick2ply
Homestead, FL 33032
(786) 829-2761
Jacksonville, FL 32209
(904) 503-9400
Tallahassee, FL 32304
(850) 574-7600
Odessa, FL 33556
(813) 749-5354
Orlando, FL 32804
(407) 291-7244
Tampa, FL 33619
(813) 740-8790
Fort Myers, FL 33916
(239) 935-5077
Deerfield Beach, FL 33442
(954) 969-8000
Miami, FL 33142
(305) 635-7177
Orlando, FL 32809
(407) 367-6246
Ocala, FL 34474
(352) 622-3933
Melbourne, FL 32904
(321) 369-7892
Ormond Beach, FL 32174
(386) 301-4471
Palmetto, FL 34221
(941) 722-6800
Leesburg, FL 34748
(352) 818-6120
Orlando, FL 32804
(407) 859-9997
Winter Haven, FL 33880
(863) 293-1555
St. Petersburg, FL 33716
(727) 565-4630
Sarasota, FL 34243
(941) 203-6320
Fort Pierce, FL 34982
(772) 466-3461
Stuart, FL 34997
(772) 223-8881
Vero Beach, FL 32960
(772) 778-0549
Orlando, FL 32810
(321) 442-0061
Fort Lauderdale, FL 33315
(954) 525-1158
Riviera Beach, FL 33407
(561) 863-9899
Clearwater, FL 33762
(727) 573-6075
North Port, FL34289
(941) 732-1029
Panama City, FL 32405
(850) 763-0851
Find your local branch with the Beacon PRO+ Mobile App. Download the Mobile App today!