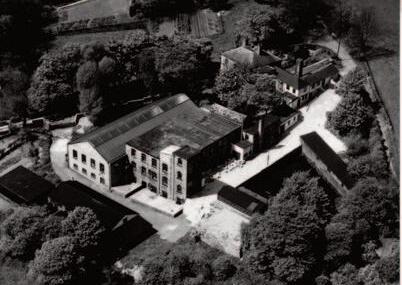
4 minute read
Learning on the job, the Reliance way
The Editor visits the Lepton-based Reliance Precision Ltd to see a well-run apprenticeship scheme in action.
IN the February issue of The Almondburian Abbi Terry wrote of the importance King James’s School rightly attaches to giving students guidance on future career opportunities. I was therefore particulary pleased to be offered a tour of Reliance Precision Ltd , the Lepton company with which the School has worked closely over many years.
Advertisement
Many Almondburians will be old enough to remember when the firm was called Reliance Gear Company and was located at the junction of St Helen’s Gate and Dark Lane. For cross-country runners it was a particularly welcome sight, as it marked the end of the School crosscountry run as one turned left at the end of Dark Lane for the final welcome downhill stretch back to the School. It always seemed strange to find a manufacturing company in such a country location, though it would not have seemed odd 150 years earlier when Almondbury played such a major role in the area’s woollens manufacturing industry. The site was the original location of St Helen’s Mill (also known at one time as Alexandra Mills ) and was once prominent in the manufacture of fancy woollens. By 1900 it had become a four-storey mill with 36 looms, but with the decline of the industry it suffered the same fate as others in the area and fell into decay. The premises were purchased by Reliance Gear Company Ltd in 1959.

The company had originally been set up in 1920 when it took over the gear cutting and engineering company Byrom, Jury and Co in Moldgreen. It acquired new premises in Union Street, Huddersfield; an early product was an innovative washing machine, patented in 1936.
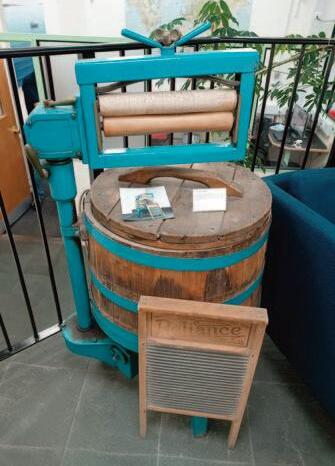
In 1955 the company was purchased by Max Selka, whose parents ran a highly successful textiles business in Bradford. Mr Selka decided to break away from the textiles industry and it proved a shrewd move as the new company went from strength to strength in the years that followed.
In 1970, the firm set up a second company Reliance Precision Manufacturing (Ireland) Ltd, based in County Cork. By the 1980s the shortage of space at St Helen’s Gate saw the company purchase Rowley Mills where it set up a new laminar flow cleanroom for the manufacture and assembly of specialist equipment for the mass spectrometry industry. Major extensions at Rowley Mills enabled the company to move all its operations on to the single site in 1995, and the company formally changed its name to Reliance Precision Ltd in 2005.
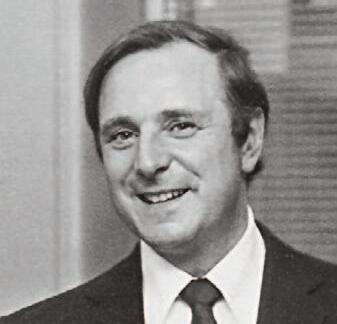
Today, Reliance Precision manufactures a vast range of high-precision products for the analytical instrument, medical and aerospace defence industries.
Max Selka acquired the company in 1955 and spearheaded its growth for over 60 years. He died in 2016 at the age of 92.
Training is the responsibility of Training School Manager Robert Farrell , who himself joined Reliance as an apprentice back in 1986. The company takes on four to six apprentices each year and seeks motivated applicants with a genuine interest in engineering and a real drive to learn more. Applicants are required to have five GCSEs at grade 5 or above (or equivalent) including Maths, English and Science, and be com- puter literate. Apprentices are on the company payroll from their first day.
Rowley Mills, Fenay Bridge: major expansions enabled the company to consolidate all operations on a single site from 1995.
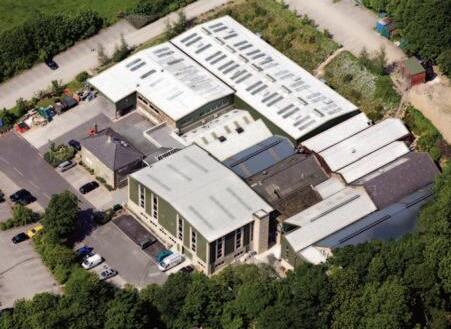
It’s a four-year programme. In the first year, the apprentices undergo foundation training; in Year 2, they move around the various parts of the business, spending a month in each department. The final two years are then spent in their chosen specialist areas.
I met four current apprentices who joined Reliance from King James’ School: Archie Barraclough (KJS 2015-20), Maegan Green (KJS 2016-21), Leon Tomlinson (KJS 2016-21) and Lucie

Harding (KJS 2017-2022). It was evident from our chat they were all enjoying working for a company in which they clearly have great pride.
Newest recruit Lucie is enjoying moving around the various parts of the company whilst studying for her Level 2 Certificate in Mechanical Engineering.
Leon, now in his second year, is specialising in mechanical assembly. Maegan applied to become an apprentice in the middle of the Covid-19 lockdown and had the unusual experience of undergoing most of the process online. Part of the 2021 intake, she is currently on her business wide rotation, experiencing a month in each department, including Design Engineering, Quality, Inspection, Milling, Turning and the Apprentice Training Facility (looking after the new apprentices).
Oldest of the four apprentices is Archie, currently in the third year of his apprenticeship. Winner of last year’s Year 2 ‘Apprentice of the Year’ award, Archie has chosen milling as his specialism and works as a member of the production team on the computercontrolled milling machines. He attends Kirklees College one day a week, where he is studying for his Level 3 Diploma in Advanced Manufacturing Engineering.
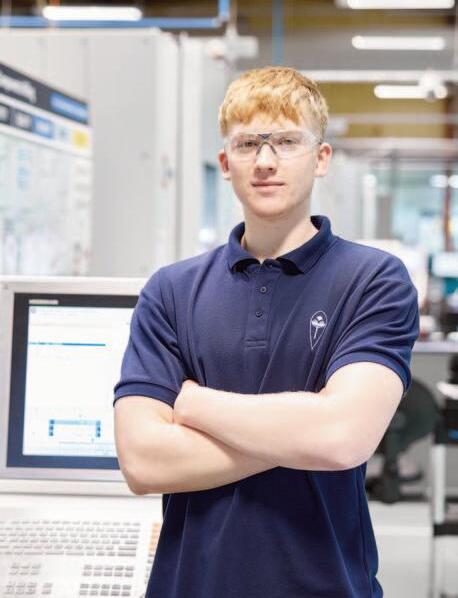
Rob Farrell has no doubts that a well-run apprenticeship scheme is a productive and effective way to grow talent and develop a motivated, skilled and qualified workforce, and my visit to Reliance Precision led me to the same conclusion. Whilst it is understandable that many school leavers will hope to go on to university, it should not be forgotten that there are many with practical skills and interests who would derive greater benefit from the sort of training that only a good apprenticeship scheme can provide.
What’s more, apprentices are earning money from Day One rather than living off a student loan to be paid off at some indeterminate point in the future. Parents might therefore see advantages from their viewpoint of a potentially reduced dependency on ’the bank of mum and dad’… n