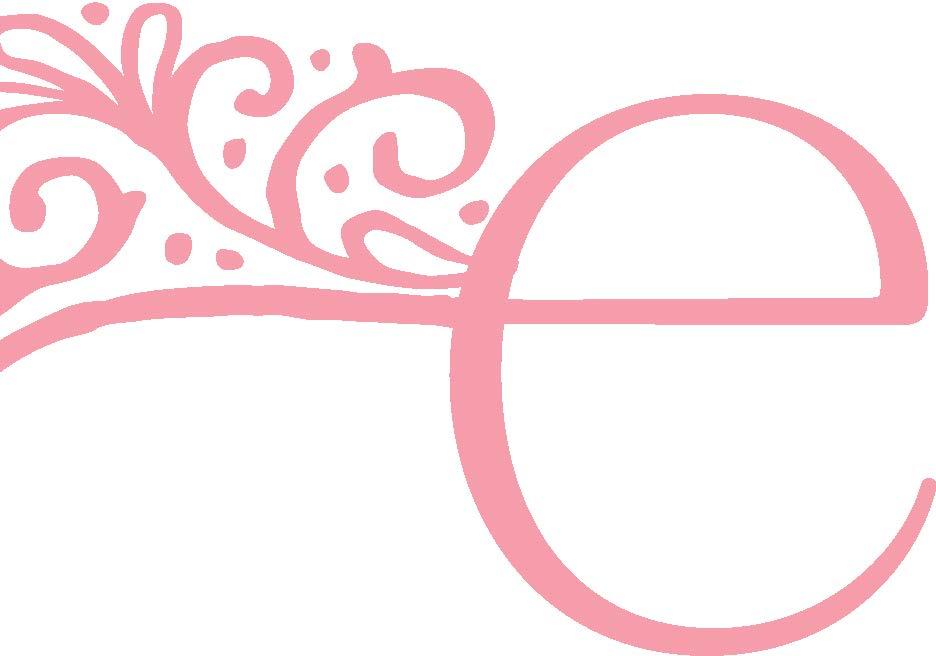
6 minute read
e.cuSTOM CUTS THAT STAND ouT!J
mbellishments help create a tactile experience for the print recipient. In addition to specialty coatings, the shape of a printed piece also leaves an impression. And this is an attribute that scales-from business cards to packaging, wall decals, and life-sized posters and displays. No matter how you slice it, custom cuts level up a print.
By Cassandra Balentine
In this piece, we highlight some ofthe benefits and limitations of three types of die-cutting technologies well suited for digital print environments-rotary die cutting, flatbed cutters, and laser-based cutting equipment.
Rotary Die Cutting
Although not a digital process, rotary die cutting has a solid place in the digital print space, bringing speedy, custom cuts at a lower cost per piece for longer, static runs that still fall within the sweet spot for digital volumes. Target environments include digital print shops, inplants, commercial printers, trade binders, manufacturing, and packaging and label manufacturers. tags, coasters, door hangers, light packaging, stickers, and labels.

Key applications include invitation and greeting cards, gift card holders, Above: The Duplo UD-310 offers high-speed cutting forcustom-shapedjobs.
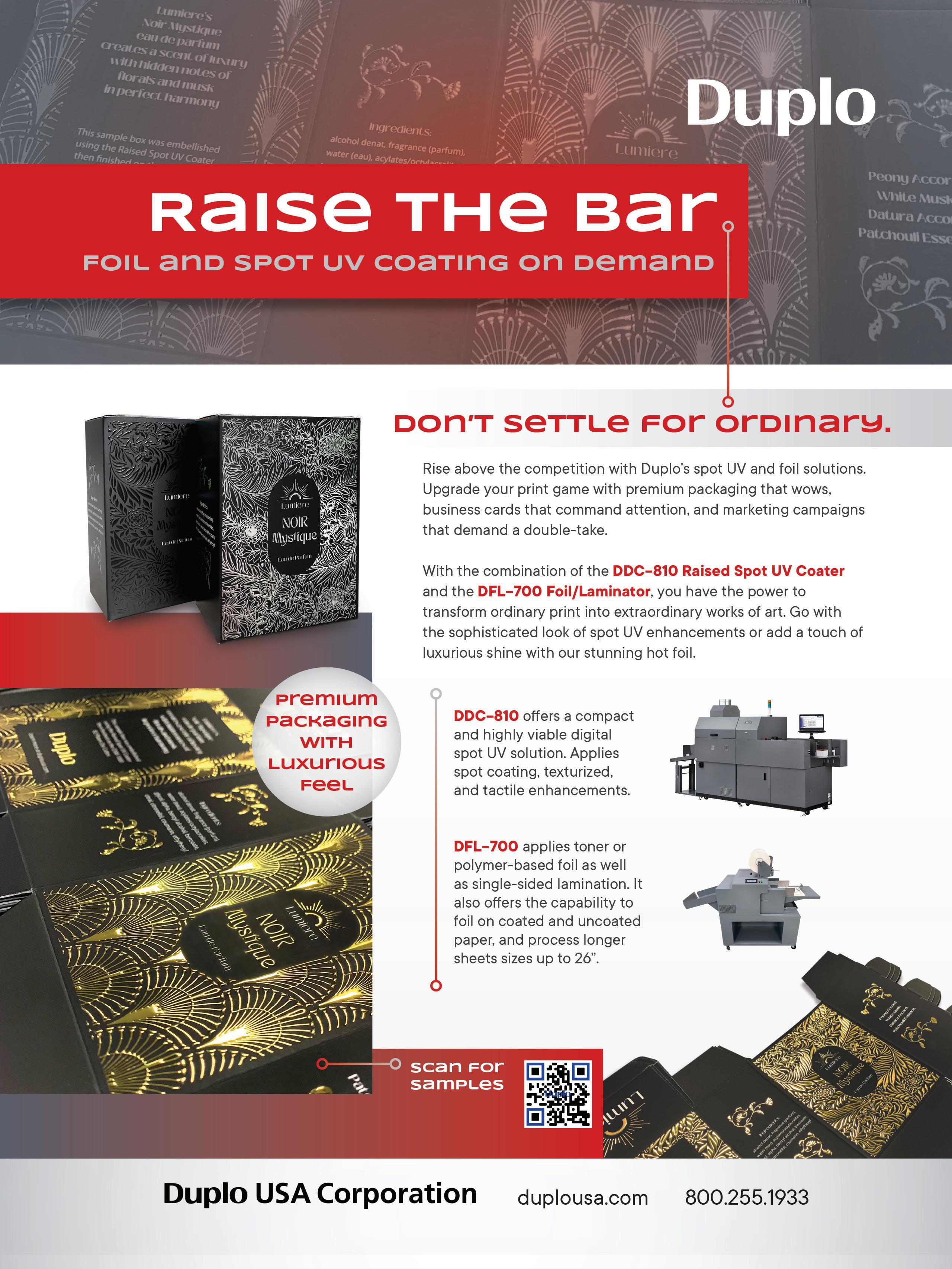
Benefits of rotary die cutting include fast turnaround times as well as repeatable, consistent cut pieces. Often the machines provide additional functions like embossing, kiss cutting, and even lamination in one pass.
“Die cutting is a versatile way to create, cut, shape, and form products from a sheet,” shares Kevin Chen, product manager, Duplo USA.
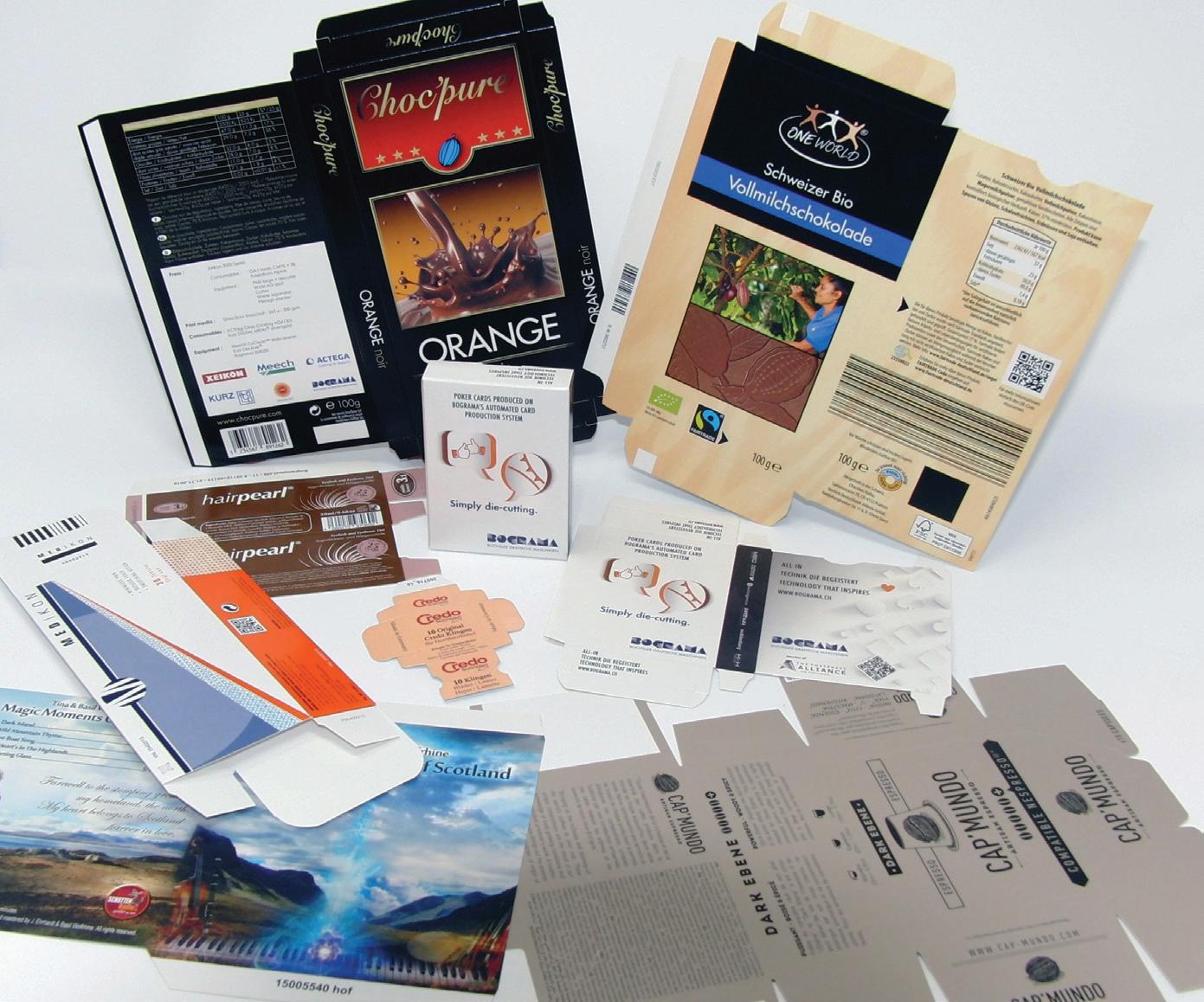
Ease of use is another advantage, “Once the printer’s design and prepress team are trained, the design and ordering of flexible dies becomes an easier process than producing die board tooling for platen die-cutting machines,” offers Susan Corwin, director of marketing, Rollem International.
According to Don Dubuque, director of marketing, Standard Finishing Systems, modern rotary die cutters have a relatively low acquisition cost and do not require special considerations like proper venting. Rotary die cutters are also able to handle a range of substrates and can operate at higher speeds—even at scale.
Lance Martin, VP, marketing, MBO and Komori America, points out that die cutting has an inherent advantage to alternative technologies like flatbed die cutting because there is no need for nicks in the matrix to process. He explains, “the products exit the machine nick free and ready for shipping to the customer. The nick-less edges have high shelf appeal and there is no secondary labor required to remove the product from the matrix and scrap before shipment.”
There are limitations to consider, and Dubuque admits that rotary die cutters are less suited for producing variable patterns that change from piece to piece, such as security applications, compared to a solution like a laser cutter. “In addition, the rotary die cutters on the market now aren’t quite able to handle large format applications or heavy substrate applications as well as router cutters.”
“At this time rotary die cutting is focused on the B2 sheet size and smaller, so full B1 sheets, which are widely used in the offset market, must be cut in half prior to processing,” adds Martin.
Chris Van Pelt, president, Therm-OType, adds that certain materials, material thicknesses, and material coatings may not be suitable for finishing on a rotary die cutter using a flexible die.
Other limitations include the fact that flexible dies must be designed, purchased, and stored—and replaced if damaged or worn.
This can be looked at from a positive perspective as well, as print providers can develop a library of flexible dies to use repeatedly. “Users benefit from the longer life of flexible dies. Depending on the make up of the substrate being cut, dies can be used for hundreds or thousands of runs,” counters Corwin.
Compared with alternative technologies—like flatbed cutting and laser cutters, rotary die cutters offer certain advantages and disadvantages. “Rotary die cutters not only compete with laser and non-laser flatbed cutters, they also compete with cutter/slitters and right angle slitters,” comments Van Pelt.
However, next to to laser and non-laser flatbed cutters, he says rotary die cutters are faster and typically do not require manual sheet loading, unloading, and stripping. Compared to cutter/slitters and right angle slitters, rotary die cutters produce products with round corners, decorative edges, or complex shapes.
Flatbed Cutting
Flatbed cutters are gaining attention in commercial, in plant, and packaging environments. This is due to proven versatility and the introduction of newer options with smaller footprints.
Tino Thür, digital marketing manager, BERHALTER Swiss Die-Cutting, says in general flatbed die cutting offers advantages in stacking, versatility, precision, customization, and efficiency.
Max Allen, dealer manager, Graphic Whizard, feels that some of the pain points associated with traditional die cutting are removed when using flatbed cutters, such as cost, turnaround time, accuracy, and software.
“With continued growth in digital printing comes equal growth in the demand for efficient, highly productive digital cutting/finishing equipment. While order quantities and delivery times decline, the pressure for customization and personalization—areas where digital print and cut workflows are a particularly good fit—continues to increase. Well-designed and implemented automation elevates digital cutting systems to an industrial level, where reliable, efficient, non-stop productivity are a must,” shares Beatrice Drury, marketing and communications manager, Zund America, Inc. get dull, they must be refurbished or replaced,” comments Hower.
Flatbed cutting devices target various applications in commercial print, trade finishers, folding carton, corrugate and display environments including custom boxes to pocket folders, foam board signage, as well as point of purchase displays. They are suitable for both large and small production volumes.

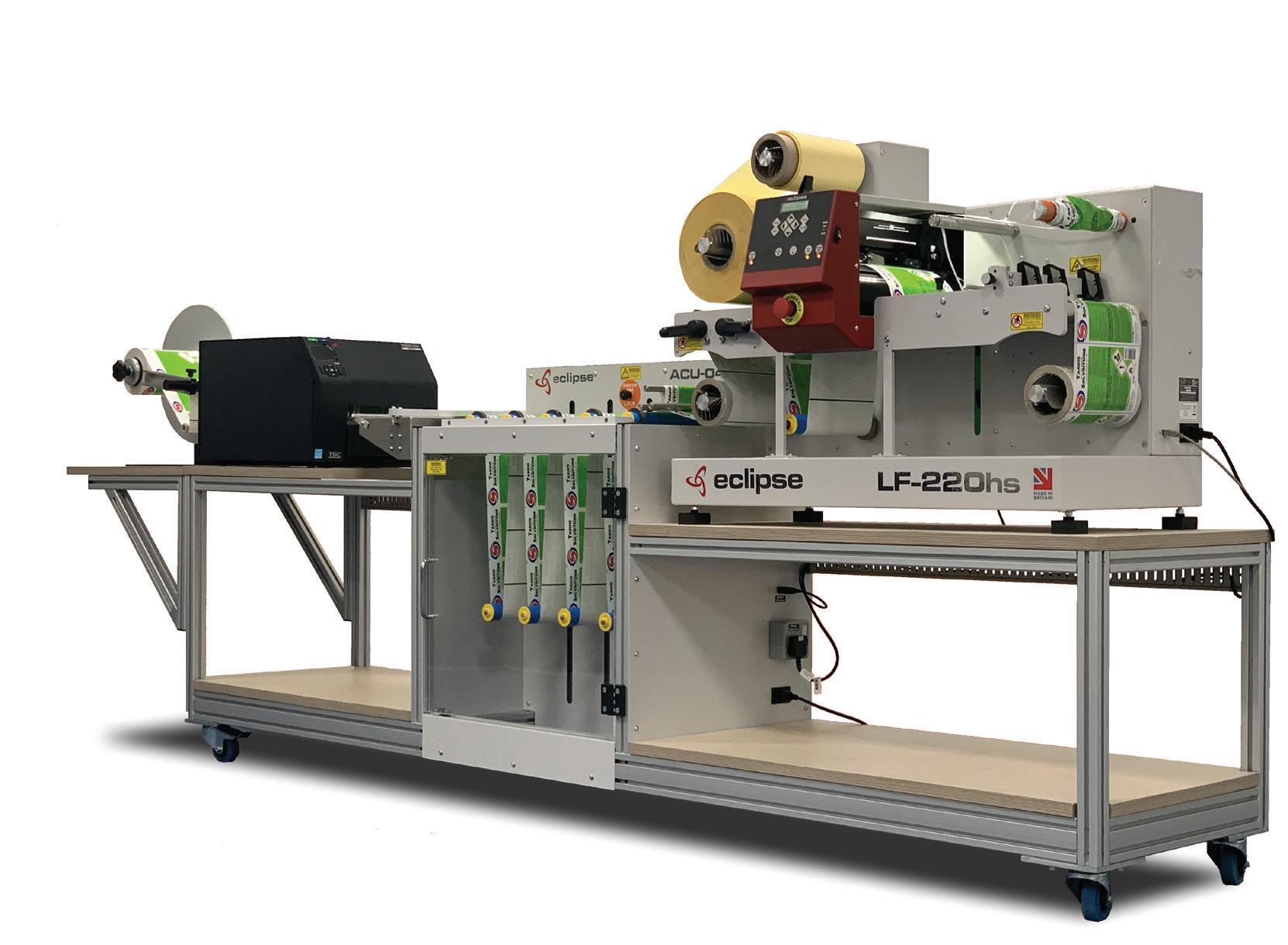

Speed may be another limitation. “A drag knife is slower than laser or rotary die cutting,” admits Fabrice Conq, global sales manager, Eclipse Label Equipment.
On the flip side, the setup time is faster for shorter runs with digital die cutting. “The setup time on traditional die cutters is far longer than the new digital systems. Not only can custom dies take days to produce, operators must devote more time into repairs and alignment than in a digital die system with built-in registration. With PDF files digital die cutters can create a oneoff custom die in a matter of minutes,” comments Allen.
Bell feels that limitations tend to arise when companies install new, faster printing equipment without considering that they’ll create a production bottleneck if they don’t increase their capabilities in terms of cutting/finishing. “One main limitation is automation, as often companies don’t want to invest in full automation immediately,” she says.
Laser Die Cutting
Besides blades and knives, laser technologies are utilized in the print industry to cut custom shapes.
Laser cutters cater to a range of applications, including labels and packaging.
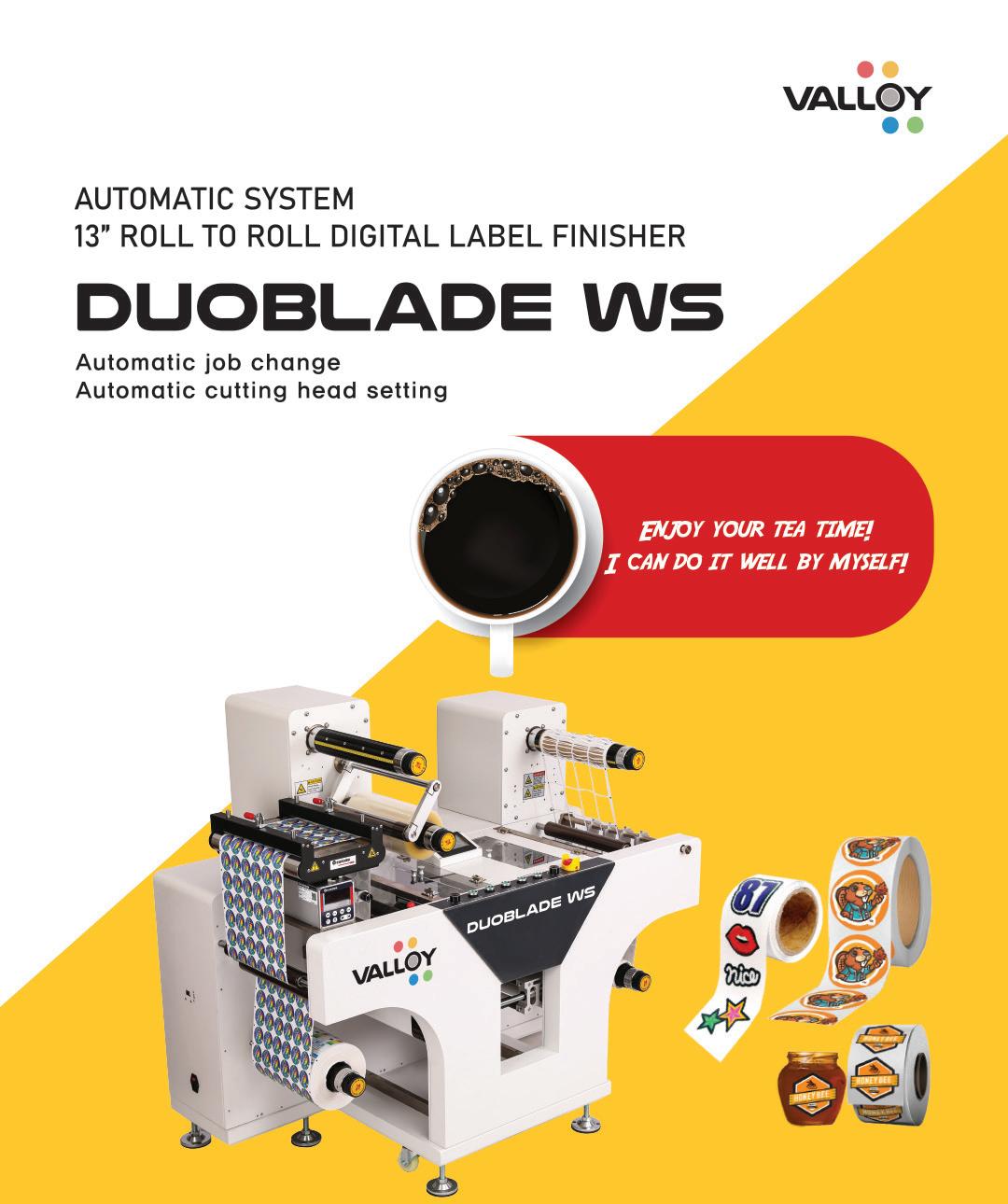
Hower points to high precision as a top advantage of a laser cutter. “Laser die cutting is ideal for elaborate, complex designs that require close accuracy and finishing; while rotary and flatbed die cutting are restricted by how close blades may be positioned together.”
Secondly, it is prototype friendly. “When a rapid prototype is required, laser die cutting is easier and less expensive than acquiring and performing hard tooling,” shares Hower.
Also, files are treated the same as digital print files. “They can be ripped from almost any platform/RIP software on the market or proprietary RIP engines and sent to the lasers,” shares Wesley Belmans, product manager, Grafotronic.
According to Vivien Kim, assistant marketing manager, Anytron, laser cutters offer cost savings by eliminating the need for new dies when designs change, reducing consumable costs for businesses. They also provide a range of cutting capabilities in a single pass, including full cut, half cut, perforation, and marking. “Unlike analog dies that require regular cleaning, laser cutters eliminate the need for cleaning, saving on labor costs and working time. It can effectively handle diverse materials that analog dies or knife cutters may struggle with, including thick and rigid materials like foam, adhesive-bonded materials such as VHB tape, and materials with special properties like reflective film.”
Conq agrees, noting that with laser cutting you get flexibility and speed— as well as the elimination of consumables. “Laser is a non-contact technology, therefore there is no wear and tear of the tools that can impact the quality of the cut. Laser provides a consistent cut over a very long period.”
Kim points out that due to the nature of laser cutting equipment, it is unable to cut media that contains metal. There is a risk of burn marks.
Hower admits laser doesn’t always get the cleanest cut. “Laser die cutting can result in laser ablation. To penetrate through a substance, the high-intensity laser beam melts or burns it, leaving some residue on the cut’s edge,” he warns.
Laser equipment also tends to come with a larger capital expenditure. “It is a larger financial investment, but return on investment is fast on larger volumes,” adds Conq.
Weighing the Pros and Cons
Nearly every print shop relies on some form of cutting technology. As the need to stand out on the shelves and in mailboxs, enhancements like custom cuts become increasingly in demand. No matter how you decide to get there, a variety of technologies are available.
Find product highlights for each category of die cutters mentioned here online at dpsmagazine.com. dps