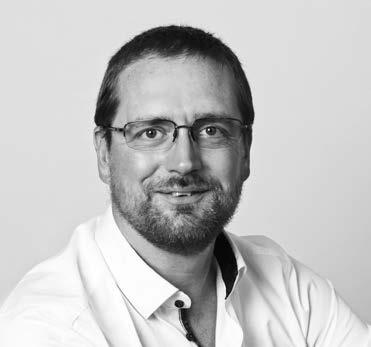
24 minute read
A towering dilemma
In an eye-opening look at the island’s population density, chartered architect Oliver Brock of the Guernsey Society of Architects crunches the numbers to show the reality facing us all.
Advertisement
I make no apology for writing a piece about the housing situation, but I must stress, what follows are not proposals, or solutions, but illustrations that I hope will help to demonstrate just how important the decisions that our politicians are having to make are.
While architects in Guernsey generally enjoy the challenges and opportunities of one-off houses, office refurbishments and compact little housing developments, the island faces some significant issues over land use that stem from an inability to understand and define what we are and where we stand comparatively with other jurisdictions. There are many who believe we are a rural idyll, and others would describe our built environment as a sprawling metropolis.
We can start with some numbers and some comparisons. Guernsey’s population is in the region of 63,500. The island of Guernsey has a land area of approximately 24 square miles, which equates to 62 square kilometers. This indicates that Guernsey has a population density of around 1,020 persons per square kilometer (p/km2).
The worldwide average population density is just 15.3p/km2 .
On an international level, that puts Guernsey in 12th place on the list of the world’s most densely populated jurisdictions. Putting our population in ecological terms, the average Western European has an ecological footprint (the area of land required to provide the resources they consume) of approximately 4.5 hectares (10,000m2), which means our current population would need 46 more islands the size of Guernsey to support itself. Alternatively, the population of Guernsey should be a mere 1,377 persons to live sustainably within the island’s land area, but that is a whole separate issue. Returning to simple matters of population density, of course, we are one of the smallest land masses in that long list of nations worldwide, and therefore it may seem unfair to compare us to whole nations like the UK and France that have wide open spaces between their urban areas. Let’s look at some smaller and more accessible comparisons which may provide some helpful context.
Guernsey’s population density would put it in 136th place (of 317) on the list of the most densely populated Council districts in the UK, slightly higher than Wakefield (1,012p/ km2), Preston (997p/km2) and Swindon (965p/km2). I am guessing not many readers will think of these places as being areas of great beauty and rural character?
If we consider our landscape, I would expect some people to think we might feel comparable to places like Carlisle, Melton or Shropshire, with some urban centres but predominantly rural character? In fact, these locations have a population density ten times lower than our island. Perhaps we are more akin to Tewkesbury, the New Forest, or Basingstoke? These areas have a quarter of the number of persons per square kilometer of Guernsey. Even relatively built up areas such as Chelmsford, Warwick or Bromsgrove are only half as densely populated as our little isle.
We should understand what our current land use policy is moving us towards. According to the Island Development Plan, only approximately 1/10th of the land area of the island is ‘developable’, in so much as new building, including housing, is limited outside the main centres of St Peter Port and St Sampson’s, the main centre outer areas and the local centres, which together amount to around 10% of the land area of the island.
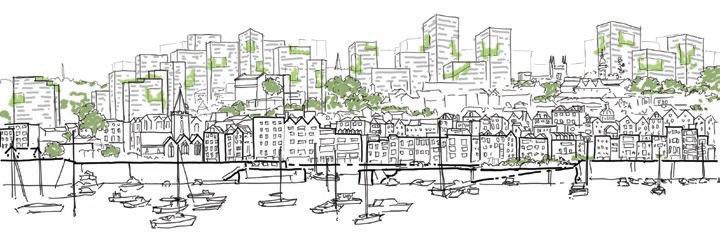
If we were to achieve the great majority of the population being accommodated within these developable areas, we would have a population density in those areas of over 10,000p/km2, and would rank 11th on the list of UK Councils, amongst the most densely populated London Boroughs.
A 50/50 split putting half the population in the ‘urban’ areas, and half in the countryside, would result in an urban density of around 5,000p/km2, similar to Cambridge, Plymouth or Derby, at no. 60 in the chart. The countryside areas would be around 566p/km2, akin to Doncaster, or Bath.
If we managed to achieve a 2/3-1/3 split, we might see the urban area match Greenwich, while the countryside might be more like the Isle of Wight.
Let’s get back to the sums. If we consider dividing the island equally between all of its inhabitants, 63,500 persons on the island would each individually have a footprint of approximately 980m2 (around 1/46th of their ecological footprint), which is around 1/10th of a football pitch, or 1+1/2 tennis courts.
To accommodate education and employment land, we might reasonably allow an employee an area of 10m2, and every school child around 12m2, based on current design expectations. On this basis we need around 350,000m2 to work and learn in. If everything else is given over to the purpose and enjoyment of households, of which there are around 25,000 on the island, we might currently each enjoy 2,486m2 of space for our family. This is an area approximately 50m x 50m, a quarter of a football pitch.
That figure tells us what we enjoy if we use up all of the island’s surface area for housing equally and allowing areas for learning and working, but let’s return to the ultimate goal of the Island Development Plan - focused development in the developable areas. I am going to explore what we might need if we had the same living space as we have now, but all living in that 1/10th of the island - St Peter Port, St Sampson’s and the main centre outer areas.
Our equally distributed area is currently 2,500m2 per household if we cover the whole island, so if we are using only 1/10th of the island, we are logically restricted to 250m2 per household. Such a reduction would be untenable, so what if we start to stack those allocations to get back to our current level? A double stack would give us 500m2 per household. A triple stack 750m2, etc. so to achieve an equivalent 2,500m2 per household (what we enjoy currently) we need to stack ten times. That’s all of us living in stacks ten storeys high.
Let’s do some more work on this. If an average household is 2.5 persons, an average living unit (dwelling) might reasonably be considered around 115m2 . Recent tall building development in urban areas typically configure an average of 7 dwellings per floor, giving an area requirement of 805m2 per floor. Allowing for circulation and amenity space, we can say 1,000m2 per floor, or a footprint of 20m x 50m.
Seven apartments per floor at 10 storeys gives us 70 apartments per block. We have 25,000 households, which at 70 apartments per block suggests we need room for 360 apartment blocks. Throw in some taller blocks and some smaller ones, and we might end up with a number of blocks around 320. Each block needs space to ensure light, privacy, access etc, and so we should provide a clear zone of 20m all around, giving a minimum distance of 40m between blocks. A building footprint of 20m x 50m extends to a free space of 60m x 90m per block, or 5400m2. 320 blocks at 5400m2 totals 1,728,000m2, which represents just a quarter of the developable area. The actual building footprint is just 1/20th of the developed area, so we can assume that there is capacity for plenty of quality public and private space in the spaces between, including all the retail, hospitality, leisure and employment uses we demand. That allows us room to preserve the most characterful parts of our urban area whilst providing housing for our entire population within the developable area, and keeping the whole of the rest of the island a rural paradise providing space for agriculture, horticulture, leisure, pleasure, conservation and biodiversity. The illustration accompanying this article indicates how the seafront may appear if this approach were adopted.
This has been an exploration of the extremes, considering what the most dense result would need to be to satisfy our community’s needs as they currently stand. It would require a significant shift in planning policy, and a cultural change from our housing ideal of the box on the plot, but it may open the mind to what may be necessary to adequately resolve the increasingly common pitched battles over the use of pieces of land that are identified as potentially developable. After all, we simply don’t have the extended hinterland to accommodate those on lower incomes commuting from further afield to service those who can afford the increasingly high property values. We have to find solutions somewhere and somehow.
ADVERTISE IN THE NEXT ISSUE...
THE WINTER EDITION WILL FEATURE:
• Interiors
Trends and ideas for a cosy winter
• Looking ahead to 2023
What will next year bring the industry?
• New Build v Renovation
From the advantages of both to the pitfalls to avoid, a comprehensive feature focused on one of the biggest decisions for many developers.
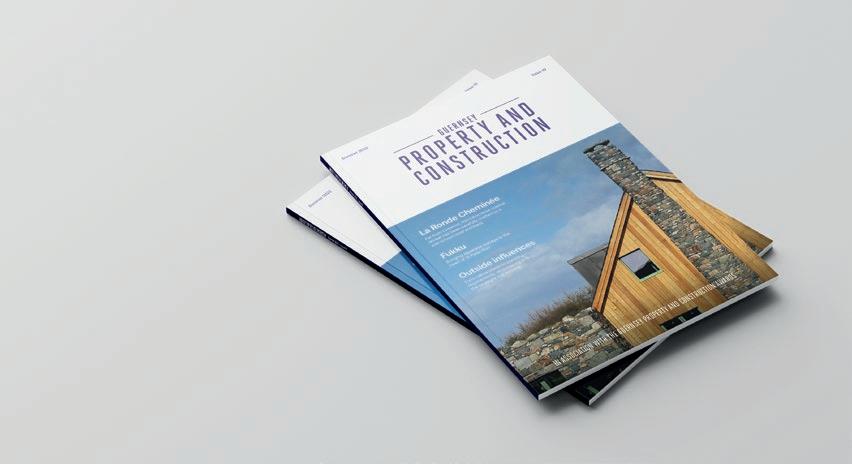
Copy deadline: Monday 17 October 2022
Distribution: Early November both in print and online
ADVERTISING ENQUIRIES
MATT COLLAS
matt@rockandsmall.com
HOLLIE MARTORELLA
hollie@rockandsmall.com
Tel: 01481 724705 www.rockandsmall.com
EDITORIAL ENQUIRIES
TAMARA TIMOTHY
editor@gpcmagazine.com
PUBLISHER
Rock and Small Limited, Ruette Braye, St Peter Port, Guernsey, GY1 1PL
GUERNSEY PROPERTY AND CONSTRUCTION
Climate change and construction
Following the record-breaking weather seen this summer, Caroline Gumble, chief executive of the Chartered Institute of Building (CIOB), reflects on how the industry can help communities mitigate the effects of climate change.
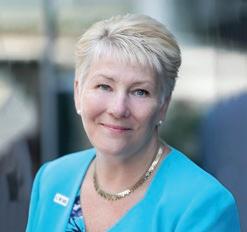
As I write, the storms are breaking to give some much-needed relief from the second summer heatwave. There may be something of an irony here, as this will appear in the autumn and who knows whether it will be wet and windy or still “above average for the time of year”. The last article I wrote, a few weeks ago for CIOB’s Construction Manager magazine, included mention of the hottest day ever in the UK as I was writing during that heatwave as well. It felt important to reflect on what this means for the built environment and for CIOB - parts of England, some not far from where I live, were literally on fire.
I spoke earlier this year about the UK construction sector facing fundamental changes following the Royal Assent of the Building Safety Act in April. It feels like time for a fundamental shift on the link between the impacts of climate change and the built environment too.
We have talked for years about how construction processes and the specification of building materials have a role in the drive to net zero. But we do not talk enough about what the finished products can do to protect people and communities from the worst excesses of climate change – which, let’s not forget, will be increasingly hotter summers and colder winters.
This column isn’t the place to list all the things construction can do to mitigate the effects of climate change. But there are two things which leap to mind which I believe need more focus.
New-build homes must have measures to design out heat retention where possible and help protect people in increasingly harsher summers. There are many things which require no technology or innovation - ensuring windows are oriented to limit direct sunlight, tree cover for shade, white walls, more natural ventilation - principles we’ve all come across before and which may be more in evidence across the Channel Islands than they are in England.
But the existing building stock also needs attention. CIOB has advocated for this many times before - the Construction Leadership Council first published a National Retrofit Strategy document two years ago. Part of the purpose of this, which over 50 organisations have signed up to, is to make existing homes more energy and water efficient.
Furthermore, CIOB has just published a policy paper proposing a reform of the tax treatment of demolition – we want to encourage a shift towards a presumption in favour of retrofitting.
Not only will measures like this deliver better, more energy efficient homes and contribute to our legally binding carbon targets, they also create jobs, help to deliver growth and have the potential to take many people out of fuel poverty. It is a ready-made policy that can deliver on social value, support the economy and improve health and wellbeing.
We already know that CIOB’s next corporate plan will include sustainability as a priority theme and our president for 2022-23, Michael Yam, has agreed to champion sustainability as his presidential theme for the year. But we also know the climate emergency requires a collective, long-term response. A great starting point would be the adoption of the National Retrofit Strategy.
The value of people
John Bampkin, chair of the Guernsey Construction Forum, considers how important it is to train and retain people within the industry.

Covid taught us or reminded us of so many things – how precious our loved ones are, how important our freedom is, how much we crave social interactions. Important lessons, but ones that get relegated by the day-to-day pressures of our busy lives.
The post-Covid era is now teaching us other lessons we should never forget – mostly the value of people. Not just our friends and families but all the people we rely on to ‘do their jobs’ in our everyday lives. Many businesses, including my own, are finding it more and more challenging to fill their employment quotas with enough willing and effective people to be able to produce their products or provide their services to take advantage of the mini boom we have been experiencing since lockdown exit.
Demand is still outstripping supply in just about every sector, yet we cannot work to our full capacities because we don’t have enough employees. This is a very disappointing position to be in – especially with businesses still trying to make up holes in their profit numbers from the lockdown periods, something which has not been as easy as people might think.
The construction industry has an added complication when it is trying to attract and embed new people. The industry is very technical and requires a certain amount of knowledge, skills and expertise which take time to learn and become effective. We cannot therefore quickly build up our human capital and must plan accordingly. That is why the peaks and troughs of our industry make it so challenging to ‘resource up’ or ‘resource down’ quickly enough to be able to cope with the demands of the workload.
Most companies cut their investments in training and development at the first sign of any downturn in market activity. Our industry must challenge this rationale and continue to produce qualified individuals for our industry with the longer term in mind. We must make sure we are attractive to newcomers and school leavers and we must provide a tangible career path to help the best talent flourish. We are all competing within a finite labour pool so being an ‘industry of choice’ is vital to our future and that of the islands.
The good news is that we are one of the most effective industries in providing those tangible career paths to those that want it. Every one of our construction contractors has homegrown people at the top of their businesses. I am proud to say that my career evolved from starting in a timber yard aged 15 to now being CEO of the NP Group, having held down sales, managerial and director roles within the leading builders merchants in the UK along the way.
As an industry we are working very hard at improving our health and safety. We are also working hard to provide our people with the best working conditions that the job allows and have a great track record on apprenticeships and development programs to bring through that talent. The list of specialist roles available is also very impressive – architects, designers, engineers, finance, marketing, HR, sales, specialist manufacturing, supply chain, merchandising, procurement and many more. Whatever your skillset and knowledge, the construction industry is a great place to find yourself.
There is an abundance of opportunity, challenge, growth and fun to be found in construction along with the most rewarding job satisfaction when you see the fruits of your labour.
My final reminder is to say how important our industry is. Our homes, hospitals, schools, workplaces and infrastructure are vital to our existence. They all need maintaining, they all need repairing and they all need building in the first place. This is all done by people, so it’s vital that we attract those people, nurture them and allow their natural drive and talent to flourish in an industry that, in my opinion, is second to none.
Keeping scaffolding safe
Andrew Mills, chair of the Guernsey Occupational Safety and Health Association, looks at the risks around scaffolding, and how they can be mitigated.
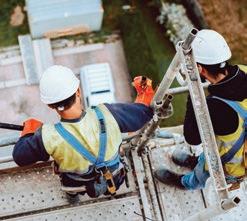
LEARN MORE
The National Access and Scaffolding Federation (NASC) is providing a free presentation on scaffolding standards this autumn. It will set out what NASC does and why it is essential, along with how it goes about ensuring scaffolding is safe and legally compliant.
The event will end with a Q&A session, and is being run with the support of the Guernsey HSE.
When:
12.00-14.00 Thursday, 15 September
Where:
KGV Playing Fields
Tickets:
available via Eventbrite It takes a special person to be a scaffolder: you need a good head for heights, fitness, ability, awareness, training, good protection and procedures and readiness if something goes wrong. Without good scaffolders, our construction and property sectors would not be able to achieve the great things they do.
For scaffolders, the key is to do things safely and well. It is easy to be complacent and not take risks seriously but when the outcome can be death or serious injury, you must carefully consider your work and your responsibilities, be well informed and implement sound procedures.
Our local HSE has taken a proactive role in educating our local scaffolding industry, but it is the responsibility of everyone who arranges for scaffolding to be placed at their workplace or who uses it to ensure that contractors are competent and implement good standards.
The HSE’s guidance is found at www.gov.gg/hse. Here are some extracts:
Employing a scaffolding contractor
The Guernsey Construction (Design & Management) ACoP2020
The ACoP states contractors have an important role in managing health and safety risks during the construction phase. They are required to check that anyone they appoint has the skills, knowledge, experience and, where relevant, the organisational capability to carry out their work safely and without risk to health.
Scaffold design, calculations and risk assessment/method statement (RAMS)
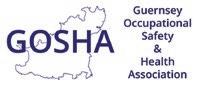
It is important that scaffolding is erected to either a recognised configuration or to a specific design with calculations. The scaffold should also be erected, modified, and dismantled to a Safe System of Work. All relevant documentation should be communicated to the scaffolding operatives and kept on site.
Scaffolding inspections and handovers
The hirer/user of the scaffold has a legal duty to ensure the scaffold is inspected when it is first erected, significantly modified and also weekly. Once the scaffold has been completed, it should be inspected and handed over in good order, together with any required paperwork.
Once the scaffolding is up
Scaffolds must be inspected before they are used and confirmed in the initial inspection report or in a handover certificate. They must be inspected every seven days and following events which could affect the safety of the structure, e.g. alterations, adverse weather or an earthquake.
Inspection reports must be kept in a format which can be reproduced in a printable form and is secure from loss or unauthorised interference. A report must be prepared before the end of the working period within which the inspection is completed and shared with the client/employer within 24 hours.
An employer receiving a report must keep it at the site where the inspection was carried out until the construction work is completed and then at his/her office for three months. Protection may be removed but only for the time and to the extent necessary to gain access for the performance of a particular task and shall be replaced as soon as practicable. The task must not be performed unless effective compensatory safety measures are in place.
Final thoughts
There are many people who have responsibility for scaffolding and its use when it is put up – know if you are one of them and know what needs to be done.
There are many potential dangers associated with the use of scaffolding – know them, respect them, protect against them and be prepared if something should go wrong.
Project delivery approach
Scott Crittell, a Chartered Fellow of the Association for Project Management, looks at the benefits of a more flexible approach for those managing projects.
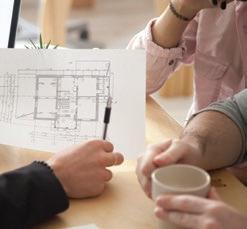
This article sketches two influential approaches to project delivery. One attempts to provide a perfect outcome which only needs ongoing maintenance. The other model offers a series of good outcomes, though not necessarily perfect ones at first, which are delivered in a sequence.
The first approach is known as ‘Waterfall’. This model involves several key stages: setting the requirements to be delivered, designing a delivery outline of those requirements, and effecting the requirements. In other words, build it, test it, deliver it. Afterwards, the solution is maintained as it was delivered with minor improvements, since it was already a finished article on completion. Waterfall has long been the dominant model for project delivery.
The second approach has more than one method, including ‘Lean’ or ‘Agile’, which are topics for another article along with any hybrid mix of delivery methods. The term agility is used here to cover methodologies which offer perhaps better potential for project success, delivering an earlier viable product or good outcome, but needing a series of iterative improvements at later dates to continually perfect the product.
For agility methodologies you will typically start with a vision, set a measure for success, plan to deliver the first step, and adapt to what this means as you produce each output. The output may not initially be perfect each time, but further outputs will build on each other as the project progresses.
Agility is important. In a recent APM survey conducted jointly by The Science Policy Research Unit at the University of Sussex and the Advanced Project Management Research Centre at the University of Southampton, 51 per cent of 1,015 respondents rated agility as important or very important for project success. A further 30% identified it as being fairly important to success. As respondents were typically senior change professionals this is noteworthy.
There are some obvious benefits to agility. In particular, an agile model of project delivery will result in the earlier completion of some aspects of a project, allowing elements of the final product to be used at an earlier date by the customer. This enables quicker return on investment. Moreover, further refinements can be identified by the customer and funnelled back into future release cycles. Naturally, any changes will need to be considered carefully: any changes in the delivery scope may result in an additional cost to the project and this may in-turn drive up the price for the end client.
Among the other benefits of agility, I want to emphasise one in particular: embedding the client into delivery requirements. Making concerted efforts to include the client, and to solicit feedback along the delivery path, will help to avoid disappointment and difficult conversations after delivery. This should help give the client a sense of ownership. It is beneficial to foster this feeling of involvement in sponsors and stakeholders alike.
Since sponsors and stakeholders may take a Waterfall delivery mechanism for granted, time must be taken at the start of a project to explain that agile models offer greater opportunity for visible and actual success. This has advantages for everyone: stakeholders, the customer, and you as a project manager. After all, a staggered series of good outcomes, which progressively hone in on an ideal outcome, are more easily measured against the key performance indicators (KPI) which will have been agreed in advance of a project starting. Projects are stronger when, as Patches O’Houlihan may have put it, they can dodge, duck, dip, dive, and er dodge. But why bother with the five D’s? It can be summed up in one word: agility.
Safe storage
Mark Baudains of the BTS Storage Centre looks at the factors to consider when installing storage equipment, and the importance of getting it right.
So, you have a new warehouse, now you just need to make the most efficient use of the space available to you.
Simple?
Not really, and those who would like to fit out a new warehouse or refit their existing one should resist the temptation of going for the cheapest and quickest solution they see, as they can find themselves in the middle of a minefield, potentially wasting precious time and money.
In a perfect world you have acres of space and height, products are always the same shape and size and money is no object.
Of course, that scenario is not realistic, your requirements are unique to you, and when it comes to storage equipment there is no such thing as an out of the box solution.
So, what do you need to consider?
What is being stored or handled? Are they palletised or loose, what is the weight and size and do they require horizontal or vertical storage? Do you require extra security such as secure partitioning or caging for individually locked locations?
You also need to think about how you are going to handle the goods as design considerations need to be made for equipment such as forklift trucks and access equipment.
Next is the warehouse or yard itself.
Will there be a mix of foot and vehicle traffic as impact protection, barriers and signage may be required. What is the storage equipment being installed on or within, ie floor capabilities. Are you picking and packing, do you need to consider goods in / out?
This is where the design aspect is so important, details such as the layout of the equipment can have a huge impact on the safety, workflow, and efficiency of your business.
Taking all of this into account will help you pinpoint the correct storage equipment for you.
So what is storage equipment?
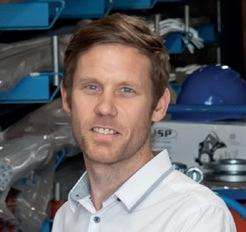
Storage equipment is any equipment within your business that helps to hold, handle, or move the goods you are storing safely and securely whilst maximising the space available.
The most common systems you will find within a warehouse are pallet packing and cantilever racking for heavier bulky or awkward items and longspan, static and mobile shelving for hand loaded, smaller items. Systems such as multi-tier and mezzanine floors are also great to enable you to maximise the height that may be available to you.
Once armed with all of this information you will need to ensure that the equipment is designed, supplied and installed to industry standards. This will help to ensure you are compliant when it comes to your health and safety obligations.
The best way to do this is to find a SEMA Distributor Company (SDC) in your area.
SDCs are recognised for the high-quality storage equipment they supply, and as distributor companies they must submit and successfully pass a rigorous and independent audit every three years. They also work closely with SEMA Full Members, with privileged access to their technical departments if your racking system requires that.
Remember, whilst it’s important that you do your research, it is also vital that you talk to industry experts who will ensure you have all of the information to plan your next investment carefully.
Storage equipment will, if specified correctly, increase safety and productivity whilst reducing damages and risk, but only if you get it right. There are lots of choices out there and companies willing to take your money without ensuring that what they supply to you ticks all the boxes.
Further information on SDCs in your area can be found here: