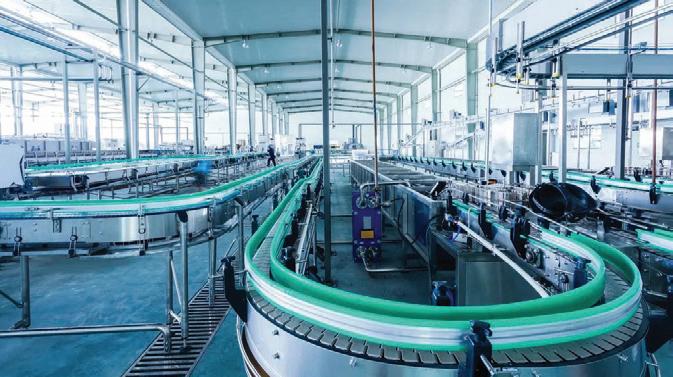
2 minute read
Vivet Technology: Where repetition leads: costs decrease, profits rise
from BCI Yearbook 2022
by hamptonhalls
Michigan-based manufacturing technology developer Vivet has designed a novel manufacturing process that it says can be applied to a number of industries, including for the production of lead acid batteries.
Where repetition leads, costs decrease, profits rise
Advertisement
Vivet co-founder and director of R&D, Amjad Hashem, is leading R&D engineering efforts to find, develop, and build unique projects that aim to disrupt manufacturing industries.
In its innovation award submission, Vivet says its ‘Repeating Layer Process’ (RLP) manufacturing system reduces costs as equipment is scaled up.
RLP is suitable for products that have a multiple of sub-components or operations, which repeat for a defined number.
The system design is scalable, enabling companies to add more machines to expand production at any time, while keeping downtime to a minimum and with no changes to the existing equipment being used.
In a case study prepared by Vivet, the company shows the build of a single system to build a battery module. The system is later scaled to seven times the initial capacity for four times the initial cost.
According to the study, the first build of the assembly system could produce more than 40 battery modules an hour and a total of 205,000 in the course of a year. This is for an initial estimated investment of $1.5 million.
The second layer would increase the capacity by 1.9x (390,000 modules a year) for a total of 1.3x the initial cost (an estimated $2 million).
The third layer would increase to 3x the capacity (615,000 modules a year) for a total of 1.7x the initial cost.
As the system is scaled further, total costs and the final manufacturing cost per unit “will fall to levels the market has never seen before”, Vivet says.
RLP systems are configured to continually perform operations until a specified number of layers is completed and then remove the product from the system. The repeating layer may include one or multiple parts.
“The process is an alternative to the linear method of manufacturing and offers a totally different level of manufacturing efficiency.” Says the firm.
“Our process not only improves production, but also quality, efficiency, scalability, modularity and more.”
The company says its process also introduces the concept of ‘zero system downtime’, with production able to ‘bypass’ any individual machine that is out of operation such as for repair or maintenance.
This in turn eliminates bottlenecks and increases utilization of equipment.
Vivet says its process is the first to give companies the option of increasing investment incrementally in line with its production requirements — providing an ability to build a lowcapacity system for low investment, without existing equipment becoming obsolete.
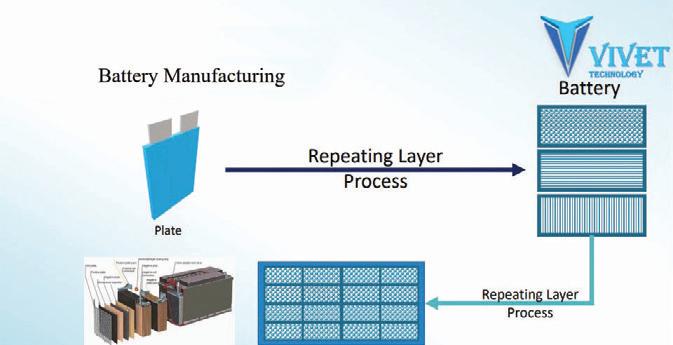
The capacity of the production system can be scaled to over 5x the initial capacity. Vivet says it can provide several options of manufacturing operation capabilities through its manufacturing branch and partners.
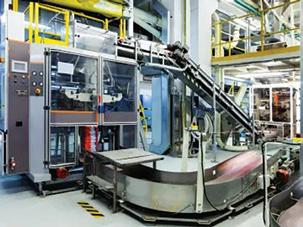