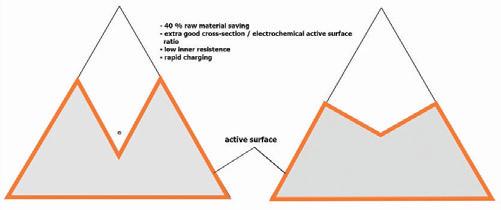
3 minute read
Meszaros Tamas: Increasing power density by ultra fine fibre grids
from BCI Yearbook 2022
by hamptonhalls
This year Meszaros Tamas submitted an entry suggesting that a radical new grid design using ultrafine fibres could dramatically improve battery performance.
Breaking through the 100Wh/kg power barrier
Advertisement
An unusual entry from retired Hungarian academic Meszaros Tamas looked at what he named Uff (ultra-fine fibre) technology tied with a manufacturing process he called the Blewin System — the intellectual property of both of which are his.
The Uff solution keeps the geometry of the grids unchanged with the already known in-plane arrangement, but in the third dimension it transforms the now-usual convex quadrilateral and the already improved triangle cross-sections into concave polygons.
Figures 1 and 2 above: note the extended electrochemical active surface ratio and there is a 40% raw material saving in lead, there is also lower internal resistance allowing for more rapid charging
Research on these grids — which had even achieved a specific power of around 80Wh/kg at the turn of the 21st century — was halted. At this level r, the system resulted in 30% lead savings / batteries, as well as a reduction in internal resistance that reduced the previous charging time to less than a third, eliminating unnecessary heating and acid vapor emissions.
“Optimized current paths and extremely low internal resistance have made it suitable for handling extreme power fluctuations and much more, making the four variants capable of performing virtually any energy storage task for a quarter of the price of a Li-base of the same power (capacity),” says Tamas.
The internal elasticity of the Blewin system is important because it can accommodate parameters that are not uniform but fit in an internal structure.
Figure 3 above illustrates the size and design of the smallest (moped) battery grid and the magnified detail of the microporous surface waiting for the paste.
“The grid manufacturing system is capable of producing any shape that is suitable for an acid lead-acid battery grid and produces better results than current products,” Tamas says.
“It can be seen that the grid is still built of ubiquitous convex cross-section elements, so the ratio of the electrochemical surface area to the fiber cross-section (mass) is still not optimal.
The cross-sections in figures 1 and 2 improve the crosssection-to-surface area ratio by more than 25%. The effect of this can be demonstrated by mathematical modelling, any solution will bring the value of the specific power above the value of 100Wh/kg (102~105).
Mathematical modelling also offers additional curiosities, as the use of grids with such a cross-section results in a lead saving of over 40% (with the same performance), e.g. it results in a weight loss of over 4kg for a normal (60Ah) starter battery, which costs ~ $8 in lead.
The extremely high electrochemically active surface results in extreme load-bearing capacity and a significantly shorter charge (also) with a higher current. This presupposes, for example, an outstanding recuperation capacity for urban cycle vehicles and the ability to withstand extreme current changes in wind turbines, says Tamas.
The material of the grids is pure lead, but it can be hardened with an alloy that does not cause internal damage (Na), any Ca alloy should be avoided due to its tendency to form gypsum.
The production of Uff solution grids requires the transformation of a previous machine system operating on a similar principle, primarily by entrusting process control to more precise artificial intelligence and transforming it into an automated process, he says.
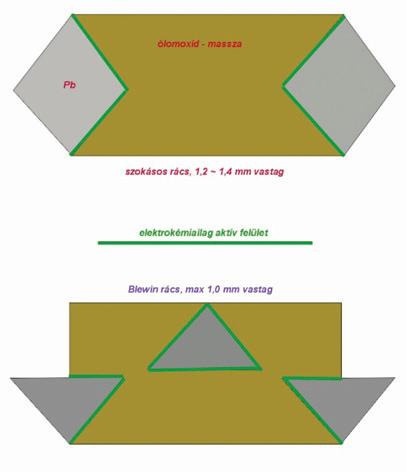
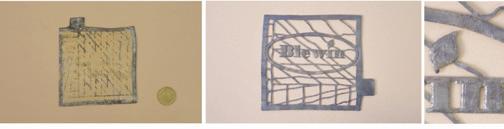
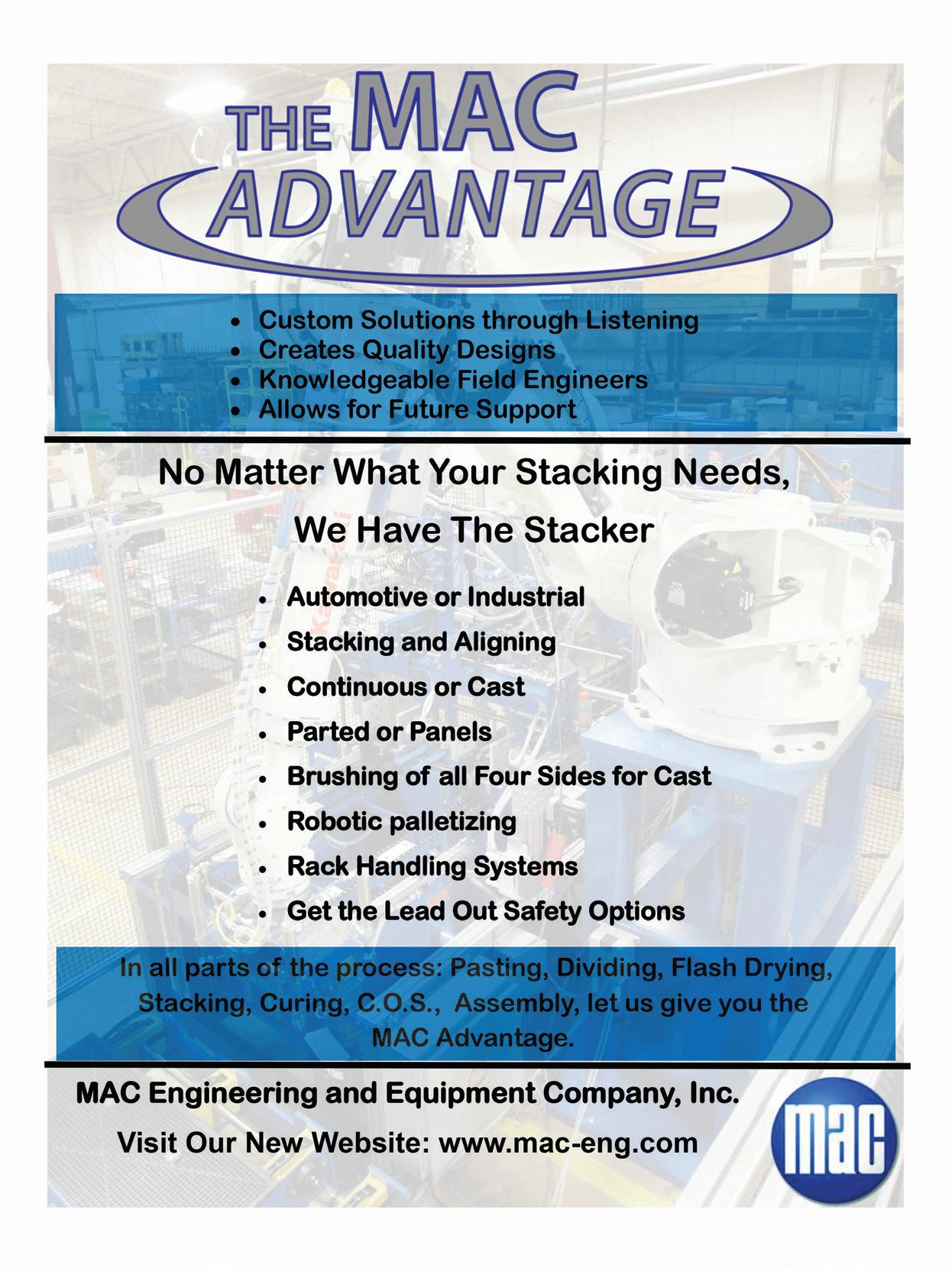