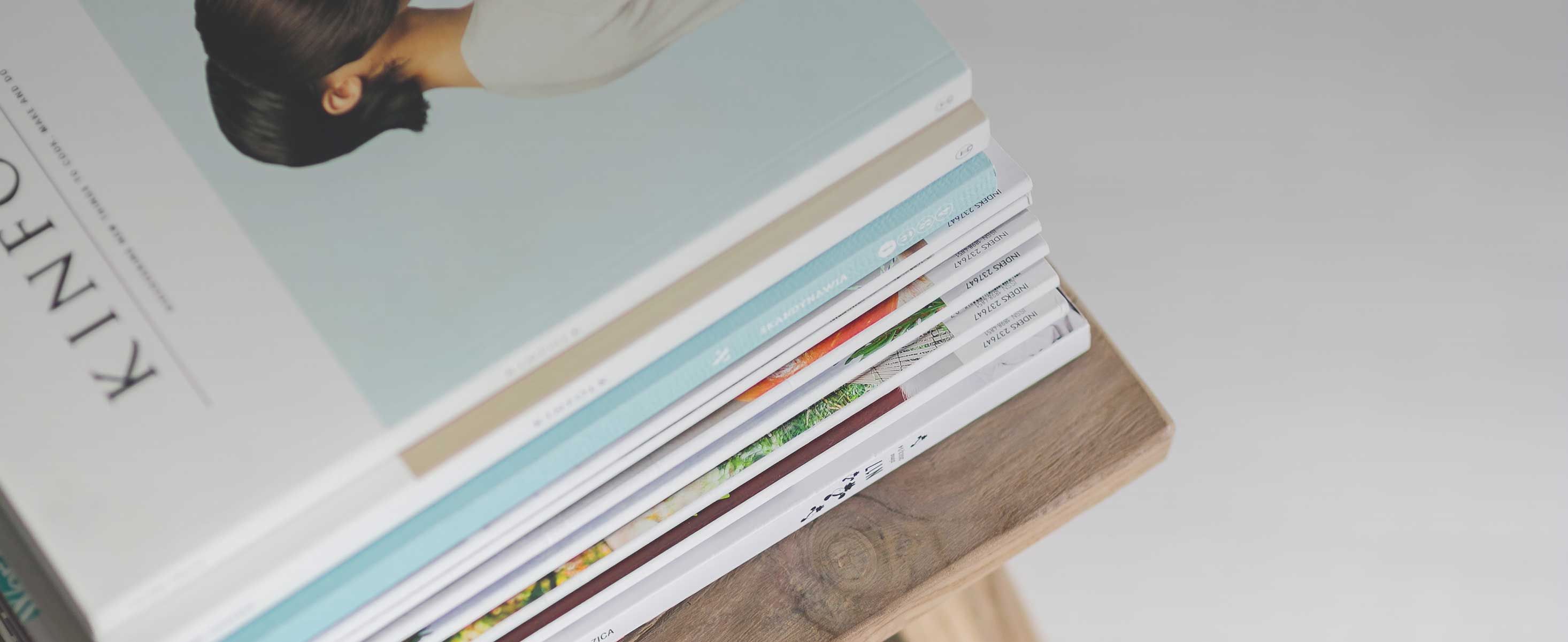
6 minute read
Irrigation Update
Poplar Grove, IL
21283 IL Route 76 Poplar Grove, IL 61065
Clinton, WI
11228 East County Road X Clinton, WI 53525
Salem, WI
7530 288th Avenue Salem, WI 53168
Irrigation Update 2022 Supply Chain Challenges and Price Increases Face Irrigation Contractors
by Meta Levin
A perfect storm of the
pandemic, bad weather, logistics, labor shortages and demand have served to send the irrigation industry – like most others – scrambling. “We got emails from suppliers weekly,” says Brett Gold, CTO and project manager for American National Sprinkler & Lighting. “We had to edit our price book throughout the year.”
He estimates that between March 2020 and the present, the cost of installing a $5,000 sprinkler system jumped to $6,500.
“It’s been an astounding year,” says Kevin Koss, divisional sales manager for the Great Lakes region for Ewing Irrigation & Landscape Supply. “We continue to see supply challenges in almost all categories.”
He points to March 2020 when the pandemic forced everything to shut down. “Manufacturers pulled back,” Koss says. “Employees couldn’t come in.” Many irrigation equipment manufacturers are in Mexico, where there also was a “massive shut down.” Three to four months later demand for work skyrocketed, in part because people who were working from home wanted to enhance their outdoor environment. “Demand continues to remain high,” he says.
The weather has played a part in the challenges, as well. For instance, Louisiana, which was plagued by fires and hurricanes, is the largest resin manufacturing location in the United States. Oregon, which is responsible for 80 to 90 percent of grass seed, has had severe rains in the winter and spring, followed by a summer drought.
In fact, Mike Martin, who heads Business Development and Commercial Sales for Muellermist irrigation, pinpoints some of the materials shortages to the February 2021 winter storm in the Dallas, TX area. He also noticed problems with getting PVC pipe in early 2020 and, he says, “It spiraled from there. I just heard that PVC is going to be an issue again this year.” Copper and brass prices have gone up every two weeks or so. “It’s tough keeping up.”
The well-known backup at some of the largest and busiest shipping ports also affected the industry, as did, says Koss, the lack of truck drivers and shipping containers.
All of this and more influenced prices. “We seem to be getting price increases weekly or monthly,” says Koss. These, of course, are passed along to customers – whether by suppliers to their contractor clients or contractors to their clientele.
“I had to raise prices across the board,” says Alex Mayfield, principal at JM Irrigation. From January 2021 to January 2022 Mayfield raised prices five times by approximately 30 percent. The cost of PVC pipe alone he estimates went up 200 percent in the last 18 months.
“It hit us hard, but I don’t think it was quite as hard as some of the smaller contractors,” says Martin. Muellermist typically works with three suppliers, which, he says, has allowed them to keep up with demand. If he needs 10 of one part, he might have to go to all three, getting a few from one suppler, a few more from the second and more from the third until he gets his 10.
Customers who postponed work and now want to get the project done are the ones most surprised by the price increases, says Laury Feldman, President of Sales for American National Sprinkler & Lighting. He points to some prospective clients with whom he talked with in early 2020, who have put off the work and now have decided, based on the 2020 prices, to get on with it. “There’s been significant price increases since
Supply Chain Challenges and Price Increases
Irrigation Contractors in Illinois
then,” he says.
Like many irrigation contractors, American National Sprinkler & Lighting limits prices on any proposal to 30 days, “because the prices keep going up,” says Feldman.
“Before 2020 we usually honored our quotes for three months or so,” says Martin. Now, however, with the price increases and material shortages, Mueller Mist limits that to 30 days. Still, once a customer agrees to an estimate, he orders the materials to lock in the price. His suppliers then put it aside for him.
Mayfield goes even further, writing estimates that are good for only five days. “I’ve even started putting in escalation clauses,” he says.
While it may take a few weeks to get supplies that once were available within days, some materials take much longer. For instance, Mayfield went to six or seven manufacturers in search of pumps used to push pressure. “I still don’t have the one I ordered in May,” he says. “My customer is not happy.”
Specialty items used to be available in seven to 10 days, says Martin. Now, however, he can expect to wait eight to 10 weeks for such items as colored tags for sprinkler heads to indicate they are for reclaimed water. Recently, an order took 20 weeks.
Many suppliers and contractors are ordering substantial amounts of materials to stockpile, to not only beat price increases, but also to ensure that they have plenty of what have become scarce resources. “My barn never has been more full than it is now,” says Mayfield.
“We have a pretty sizeable warehouse,” says Feldman. American National Sprinkler & Lighting uses the space to order materials they use frequently.
For the first time in his memory, Gold notes that the company is ordering parts to hold through the winter, instead of right before the season starts. With a 10,000 square foot warehouse, there is plenty of room to do this.
Prior to this stockpiling wasn’t necessary. “A lot of our customer base hasn’t had to plan, because we, as distributors, have done a good job of providing product,” says Koss. Now, however, he’d like to counsel his customers to “communicate with your suppliers. Place orders as early as you can so we can help you have the product.”
In this tight labor market, employers have found themselves paying higher salaries, contributing to the price increases from the manufacturing, transportation, distribution and contractors’ sides. “Since May 2021, we’ve also seen labor increases,” says Feldman.
Koss ticks off a list: “freight constraints, lack of drivers, labor issues, lack of containers to get from point A to point B,” he says. It affects everything from raw materials that need to be transported from their point of origin to manufacturing facilities to ships, trucks and trains needed to move the finished product to distributors, then on to the contractors.
“Until now, I hadn’t thought about the availability of or price of a (shipping) container,” says Koss. Now, however, he knows that one could be had fairly easily two years ago for about $2,000 to $3,000. “Now, if you can get one, it can cost $20,000 to $30,000.” Difficulty in obtaining shipping containers contributes to the difficulty in obtaining parts and materials.
Customers are hit all ways. Manufacturers pass the higher labor and transportation costs down to the distributors, who pass them along to the contractors, who pass them to their customers. The scream you just heard was the result of sticker shock.