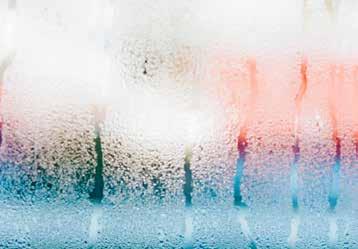
12 minute read
Top Tip
“I have water in my lines”
By Bruno Chabot, Retired Pneumatic Specialist at Normand
With the arrival of summer, the heat and humidity return, and with it comes the increase in water condensation problems in the compressed air system. Why does this happen?
It is essential to know that the air drawn in by the compressor is the same air found in the factory with its humidity percentage. This explains why there is a significant increase in problems related to condensation during the summer months. The temperature rises as the air is compressed, turning water into steam. Condensation forms, and water appears by cooling the air in the compressor tank or the distribution network.
There is no need to remind you that water is very damaging to pneumatic tools and even more so to the pneumatic controls found on almost every machine in your factory - not to mention all the problems caused by spray guns in your finishing department.
How to fix this problem? For starters, the compressor should be in a cool and dry area to prevent excessive temperature differences between the air in the tank and the air in the factory.
Additionally, installing an automatic drain on the tank is imperative to remove the water that forms in the reservoir and thus prevent this moisture from re-entering the distribution system. A filter at the tank outlet is useless because there is no water accumulation on that part.
Ultimately, there are numerous ways to help you minimize or eliminate water in the distribution system. Installing an after-cooler on the compressor, a refrigerant air dryer, or a silica gel filter dryer are only a few examples. The choice will depend on the required degree of efficiency and your budget.
PRICES AND PROFIT
Learning the value of time
By Sandra Wood
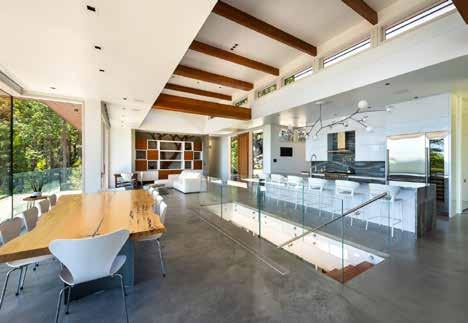
LEFT: Sunshine Coast Contemporary Home by Van Arbour Design RIGHT: Gerald Van Woudenberg, President of Van Arbour Design
Many people would think that someone in business for over 35 years would know everything, right? But Gerald Van Woudenberg, President of Van Arbour Design, knows there’s always more to learn.
“Start with being curious and open,” explained Van Woudenberg. “Take the time to seek advice from our peers facing the same challenges.”
The company president values his time and spends it on important things for him and his business. A few years ago, Van Woudenberg sought out a business coach who helped him take more control over his business and the time he spent in his company. He is now much more in control of working on his business than in it, giving him more clarity and less stress. He admits that you wear many hats when running a business, and things can quickly get away from you.
It’s a known fact that most business managers don’t feel they can afford to spend the time working on themselves and their business because they are too busy just keeping their head above water. It can be a vicious circle that you, as the business owner, must be prepared to address. For Van Woudenberg, the experience of leveraging a business coach has been “Nothing short of amazing, and I would highly recommend to anyone to have a renewed focus.”
Van Woudenberg was committed to stopping making the same mistakes, including figuring out a better pricing structure and learning how to value his team’s labour and skill correctly. He started from scratch, and it was daunting. He revisited jobs previously completed and repriced them using new formulas. The biggest challenge was accounting for time. Time spent was hard to calculate. According to Van Woudenberg, there’s only so much relevant data you can glean from past jobs. This then brings him to three options: 1 / You can guess, which exposes you to underestimate your time and build for free, or you protect yourself by padding the numbers as a guess or a protection measure, and by doing so, you may price yourself out of a job. 2 / You can track, but that’s only really relevant from the past tense perspective. 3 / You can agree with the client that takes the largest part of the uncertainty, which is the time it will take.
Van Woudenberg admits this is Van Arbour Design’s current approach because it builds trust with his clients. They tell the client the material, finishing, and margin costs and estimate how long they think the process will take. The company bills for actual time. He admits this takes the client’s trust, but he believes it’s the only way his company has found any degree of certainty to work every single time. Van Arbour Design solicits feedback from people in the shop regarding how much time they think it would take to engineer the
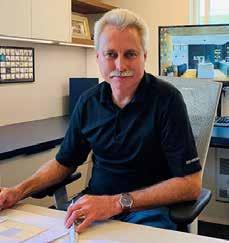
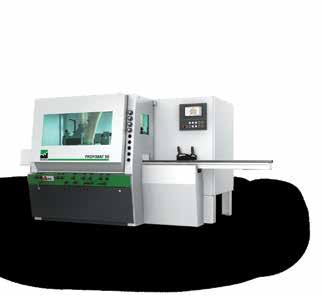
custom piece, which helps establish the price.
“It is tough to price custom millwork, especially when they are one-offs; they are never the same.”
Van Woudenberg also reads the annual industry survey results on pricing. In his opinion, there are shop prices so low he’d like to hire them to do work for him. Where are these companies shopping for their materials? In his opinion, these shops are not factoring in the material costs, overhead, insurance, wages, heat, light, property taxes, etc.
Admittedly, many wonder how the survey results will change in 2022 with the current supply chain issues. CKCA still receives calls from members who are being pressured to keep their costs down, yet their supply costs have gone up exponentially. One member reached out to tell us their melamine costs had gone up 86%, and their developer client was not accepting any price increase. We know members are under pressure, but some companies make those difficult decisions and tell their customers they can’t do the work if they don’t accept the price increases.
One member told us recently: “No builder wants to accept price increases; however, this is the world we live in, and rest assured that they will protect their bottom line, bypassing the increase to the end consumer.”
Van Woudenberg has found that looking at survey results on pricing over the years has revealed a complete ignorance of the value of time.
“If you are not attending to what matters, no one else will, and you may find yourself in that uncomfortable spot where you realize you have not been turning a profit.”
So what are the three main lessons Van Woudenberg has learned over the past 35 years of business? 1 / Time can harm how you do your business. 2 / You can change and learn from your mistakes. 3 / There are opportunities for everyone. He also makes time to engage with the industry, remain curious, and drive to learn more.
“We can read books, listen to podcasts; we can solicit help from business coaches, and, last but not least, we can get involved with organizations like the CKCA and learn through that network,” he said. “Because it’s important, we continue to connect with our peers and suppliers and get introduced to new opportunities and new ways of thinking. All of which creates new ways to move forward.”
Many in this industry have enjoyed fulfilling careers in our sector, and the time will come when you will want to move on. But as you start thinking about that, remember that you have spent considerable time building up the wisdom and business knowledge you currently have. What will you do with that knowledge?
Consider this: A next-generation is entering our industry that needs the mentorship and advice that many experienced woodworkers have. How can you pass along what you have learned to help set up this next generation for success? Can you spare precious time to share what you know with others? How will you evaluate that knowledge just as you evaluate a project?
Reach out with your ideas. How can we help you take the next step? Because we need mentors, and we need them now. We are facing unprecedented challenges in attracting talent into our industry, and the truth is no one knows the industry better than you do!
CKCA Members strive for quality, professionalism, and innovation. For more profiles like these and many other benefits, consider becoming a CKCA member!
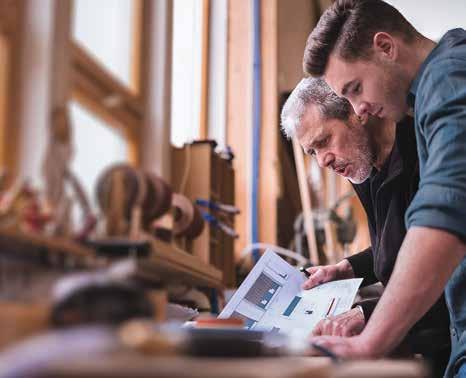
TIME HAS COME FOR THE NEXT GENERATION.
THE NEW PROFIMAT 50.
BEST IN CLASS, GERMAN MADE, AND UNMATCHED VALUE.
Learn More At profimat.weinig.com
FOR THE PERFECT FINISH
Turbine and air compressor maintenance
By Marty Schlosser
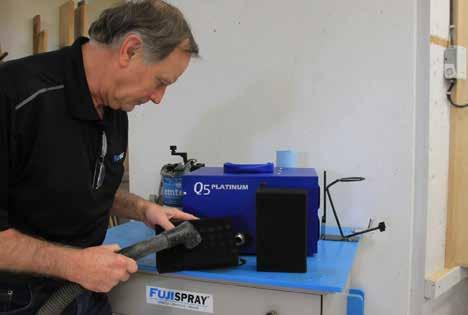
Marty Schlosser vacuuming off a dirty filter
Today’s well-engineered and manufactured turbines and air compressors are so reliable and capable of operating with a minimum of attention that we tend to forget about them. Until they break down, causing work interruptions and costly repairs. So here are tips and tricks to help you keep such problems to a minimum.
TURBINES
Properly maintaining your turbine requires little more than ensuring it can draw in clean air and efficiently send it along its way. That translates to two things: placement and filters.
PLACEMENT
Ensure your turbine is placed well away from any overspray and dust when operating. This will help keep its filters clean and draw in fresh air. And when you’re finished using it, store it out of the way where it won’t be subjected to freezing temperatures and dust.
FILTERS
Every turbine model is unique in the number and shape of its filters, so refer to your manual to learn all about yours. And if you haven’t already done so, go ahead and order a spare set. Get into checking the filters at the end of the day. Vacuum the outside of the filter housing before pulling filters out to check on them. Then vacuum off the filters themselves — never use compressed air to blow them off as it tends to drive the dust and contaminants into the filter membrane.
If vacuuming doesn’t get them clean, a quick wash in warm soapy water followed by a thorough rinse in clean water will do the trick. Vacuum, wipe off the inside of your filter housing with a water-dampened cloth, then dry it thoroughly before inserting your spare filter or the one you’ve cleaned and left to dry thoroughly.
AIR DELIVERY
Hoses require very little attention. Ensure the hose is positioned to keep it from kinking and only handtightened to your turbine. If you have one, check that the flex hose connections are tight. If the flex hose develops cracks at the spray gun end due to flexing (that’s its job!), repair it yourself. With a box knife, carefully cut off the split section, and screw the fitting back into the now slightly shorter flex hose. Check hoses every week or so for leaks and, if necessary, replace washers and hand tighten the connections.
That’s all there is to Turbine System Maintenance. Together, these efforts will allow your system to efficiently deliver the necessary volume and pressure of clean air to your spray gun.
AIR COMPRESSORS
At the beginning of this article, I mentioned that air compressors require more maintenance than turbines. 1 / Read your operating instructions manual. Understand the initial start-up procedures, preventive maintenance instructions, and troubleshooting guidance it provides. 2/ Conduct initial start-up procedures to break in your new pump. 3 / Schedule and undertake preventive maintenance checks.
DAILY CHECKS
Before starting up your compressor each day: • Check the pump oil level. • Drain condensation from the air receiver.
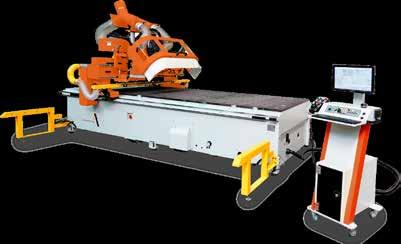
• Turn on your air compressor and check for any unusual noise or vibration. • At the close of the day, drain your air tank. If you have installed an autodrain system, this will not be necessary.
WEEKLY CHECKS
At the end of each week: • Clean the air filter by removing the air filter cap and vacuuming (do not blow with compressed air!) the inside. Clean or replace filters as necessary. • Check the pump oil level and top up if necessary. • If one is installed, confirm that the air tank auto-drain system is operating correctly. • Check for air leaks and correct them as necessary. • Check the condition of your air line filters and clean them if necessary.
Drain any condensate that may have collected in the water separator. If you have a desiccant system, check to see if the desiccant requires drying and do so if necessary. • If your system has a refrigerated air dryer, check to ensure it is operating correctly.
QUARTERLY CHECKS
At the end of each quarter (or every 300 hours of operation, if that usually comes first): • Change the pump oil and filter element. • Check the condition and alignment of the belt, flywheel, and motor pulley. Adjust belt tension if necessary and replace worn belts. • Ensure the pump cooling fan is neither cracked nor damaged. • Check the crankcase breather and clean as necessary. • Check the pressure switch unloader is operating correctly. • Clean and blow off pump fins and motor. • Inspect the air system for leaks by applying soapy water to all joints.
Tighten joints if leakages are observed. • Check that all electrical connections are tight and wiring insulation is not cracked or showing wear signs.
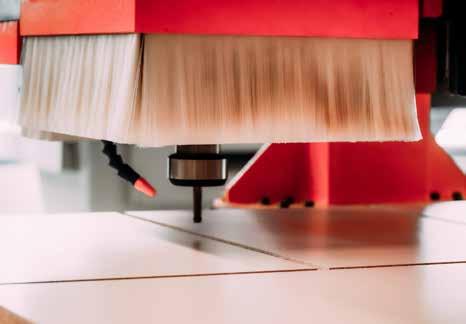
CLOSING REMARKS
If you’re regularly performing routine preventive maintenance checks, pat yourself on the back. If not, then you’ve got plenty of company. And that’s a shame because a quality turbine or air compressor system is a significant investment that will degrade over time if checks aren’t being followed. And in the worst-case scenario, the air compressor tank could explode with disastrous results. ‘Nuff said?
CNC ROUTING SOLUTIONS
Building Trust. Creating Together.
SELEXX SERIES | CNC ROUTER
HIGH PERFORMANCE NESTING CNC ROUTER FOR MAXIMUM OUTPUT.
The Omnitech Systems Selexx Series CNC Router has been developed specifically for higher production CNC router requirements demanding the utmost precision and accuracy, all within a cost-effective investment. The Selexx is the ideal CNC router for nesting applications as it is packed with standard and optional features to maximize output. An industrial design provides for maximum cutting & processing speeds. It is available as a stand-alone solution with automatic part offloading or can be integrated into a full line solution.