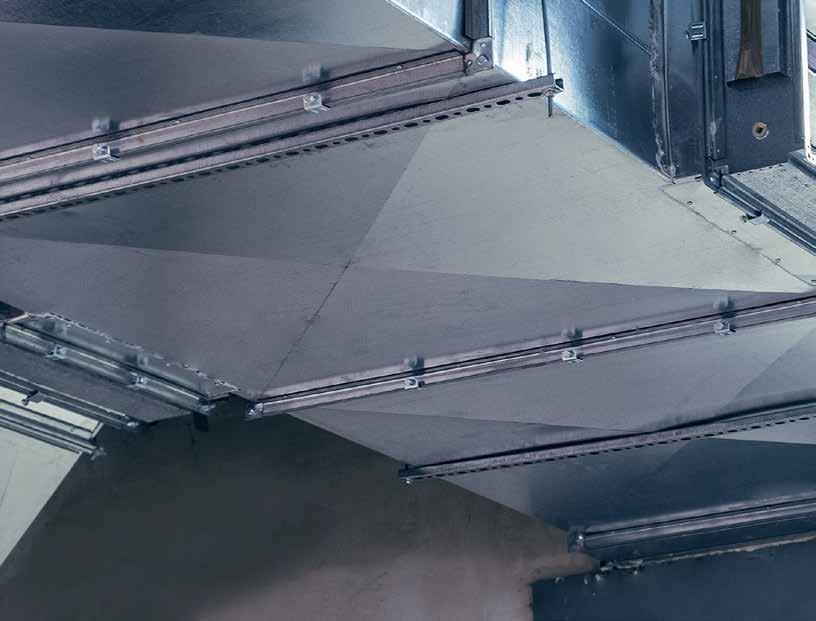
11 minute read
The Air Up There
from CHF Summer 2021
by MediaEdge
Effects of ductwork leakage on HVAC systems
By Josh Lewis
Advertisement
Properly designed and operated HVAC systems are critical to achieve comfort, adequate indoor air quality and energy efficiency in healthcare facilities. These systems are governed primarily by American Society of Heating, Refrigerating and Air-Conditioning Engineers (ASHRAE) standard 170, Ventilation of Health Care Facilities, which sets out temperature and humidity levels that must be maintained; minimum outdoor air and total air changes per hour; filtration levels; whether recirculated air can be used; and room pressure relationships to adjacent areas. The standard has evolved as ongoing research has shown it’s necessary that HVAC systems effectively filter, dilute, purify and humidify air to reduce the risk of healthcare acquired infections (HAIs). As a result, healthcare facilities often have some of the largest HVAC systems, which consume a high amount of energy per square metre compared to most commercial buildings.
Since no price can be put on the health and safety of patients and staff, energy efficiency has historically taken a backseat to the minimum design and operational requirements of HVAC systems. (If the standard is not followed, there is potential increased risk of HAIs and legal liability.) But now, with Canada’s commitment to reduce greenhouse gases to achieve net-zero emissions by 2050, solutions must be found to address these competing priorities and then systematically implemented.
THE X-FACTOR
There are many factors that determine both the operating state and energy efficiency of an HVAC system. They include the necessary fan speed and power to move the air through the system; the heating and cooling energy input to achieve the desired temperature; and the effort needed to humidify or dehumidify the air to maintain the space conditions required by standard 170. Many of these factors can be optimized through commonly used strategies, such as variable frequency drives (VFDs), parallel fans, high-efficiency boiler and chiller systems, heat recovery equipment and building automation, as well as tuning the systems to operate at the optimal level. This is primarily achieved with testing and air balancing by professional service providers.
There is another factor that can greatly impact the operation and efficiency of these systems — ductwork leakage. Most people easily recognize the waste produced by leakage in other types of systems like a steady drip com-
ing from a garden hose around the connection to the water tap or a compressed air line that is whistling loudly due to a defect. A leak in a compressed air line or in ductwork are essentially two versions of the same issue; the major difference is that ductwork systems operate at a much lower pressure. This in no way implies that duct leakage can be ignored. In fact, quite the opposite is true.
DUCTWORK LEAKS
When testing and balancing HVAC systems, the goal is to obtain the building code mandated amount of supply, return and exhaust air flowing to and from occupied areas of the facility. That is accomplished by taking airflow readings at the registers, diffusers and ventilation hoods. Adjustments are then made to various system components like the fans, dampers and controls to achieve the desired outcome.
But what about air leaking out of or into the ductwork between the air handling units and occupied areas?
Any leakage into utility areas, such as mechanical rooms, ventilation shafts or ceiling spaces, wastes a portion of the system’s capacity, resulting in higher energy consumption. It can also reduce the total volume of air that is delivered to occupied areas, causing non-compliance with standard 170, and increase the risk of cross contamination of air streams that service different areas of the facility.
According to ASHRAE’s duct design manual, three-quarters of commercial duct systems leak 10 to 25 per cent of their total airflow. Lawrence Berkley National Laboratory has also studied this issue and determined that, on average, 10 to 20 per cent of air provided to supply fans does not reach occupied spaces in a building.
A quantitative way of estimating ductwork leakage for an HVAC system is to review testing and air balancing reports and compare the total system airflow at the air handling unit to that measured at discharge points. The difference between these numbers is primarily ductwork leakage.
A qualitative method is to inspect unoccupied spaces, such as above ceilings and in mechanical rooms, and listen for air noises and feel the temperature. These areas can often be hotter in winter and cooler in summer than the desired building set-point when ductwork leakage is significant.
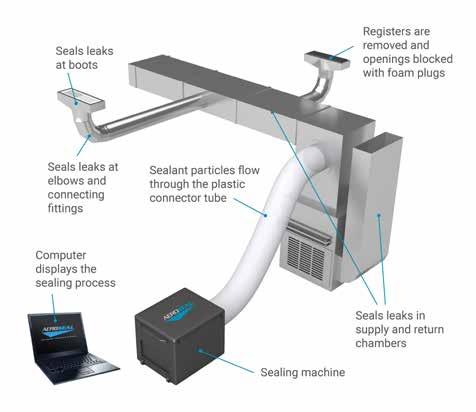
t Pressurize and spray technology overview.
SAVE ON ENERGY
From an energy efficiency perspective, a simple example illustrates the benefits of addressing ductwork leakage. The base case assumption is the HVAC system is balanced and providing the required amount of air to the occupied spaces. The fan is running at a fixed speed of 100 per cent, with 25 per cent ductwork leakage. If the leakage is lowered to five per cent or less, then in most cases the fan speed can be reduced to 80 per cent from 100 per cent fixed running speed using a VFD, while still meeting airflow requirements. This reduction in fan speed will have an immediate and permanent effect on the energy usage of the system, lowering the fan electrical consumption by up to 50 per cent, while also avoiding up to 20 per cent of heating and cooling energy usage, depending on the percentage of outdoor air being introduced.
But what if that same system is running at 100 per cent fan speed with 25 per cent ductwork leakage and is not meeting airflow requirements?
Addressing leaky ducts can help a facility achieve current ASHRAE requirements without undertaking an expensive and invasive project to replace the entire HVAC system.
The issue of cross contamination of air due to ductwork leakage also cannot be ignored when performing an assessment, especially in the healthcare sector.
An example of the energy efficiency and cross contamination benefits of fixing ductwork can be found in a case study from the University of Ottawa Heart Institute. Hospital monitors detected that a radioactive isotope created in one of the institute’s laboratories had somehow migrated to an adjacent wing of the building. This issue was determined to be occurring due to ductwork leakage at a rate of approximately 800 cubic feet per minute (CFM). After implementing a solution to fix the duct leakage, the isotope contam-
ination issue was resolved and due to the extremely low level of ductwork leakage that remained in the system (approximately 10 CFM), it was also discovered that the ventilation fan could be permanently slowed down while maintaining a higher airflow rate than was originally possible, saving both energy usage and wear and tear on the mechanical components.
SEALING SOLUTIONS
From an execution perspective, there are two primary ways to seal ductwork to minimize leakage. The traditional method is to apply sealants (primarily mastic, tape and caulking) to the exterior during construction or renovation. While theoretically effective, real world results quickly uncover flaws with this method, including variability in the caution and care taken by the installers, lack of access to certain areas of the ductwork to apply sealants (especially if the ductwork is insulated and/or there is asbestos in the space), and the inability to know where all possible holes may be along the joints, seals and folded edges of the ductwork. In addition, exterior sealant products used in more modern buildings are typically waterbased due to health and safety concerns. This causes them to dry out and crack earlier in their service life, compared to those products used in older buildings that were oil-based and retained more flexibility and adhesiveness over their lifetime.
The newest way to seal ductwork can be described as ‘from the inside,’ through the utilization of pressurize and spray technology. This method eliminates guesswork and makes for a quicker and less invasive installation. As well, it uses a computer-controlled system to produce results that are monitored in real-time during the sealing process, which provides a straightforward path to achieve guaranteed leakage rate targets. Pressurize and spray technology is quickly becoming the standard way to seal ductwork for both new construction and retrofit projects in not only the healthcare sector but also in commercial and institutional building sectors.
STAY ON TARGET
Ductwork leakage is a serious issue that needs to be addressed. Existing facilities should investigate their current duct systems, set a leakage target and then utilize the most appropriate sealing method to fix any problems. For new construction, the leakage target should be clearly defined in the specifications, along with a requirement to test and validate the ductwork systems as they are built and commissioned in order to hold the contractor accountable, regardless of whether they use traditional or new technology to achieve their deliverables.
Josh Lewis is the engineering manager at Nerva Energy Group Inc. Nerva Energy provides award-winning energy advisory and speciality contractor services, deploying cutting-edge technologies to enable high-performance green buildings. Josh can be reached at 289-856-9717 ext. 103 or josh@nervaenergy.com.
MAINTAINING BUILDING ENVELOPE INTEGRITY WITHIN THE HEALTHCARE ENVIRONMENT
When it comes to building health, keeping a building dry and leak free is paramount. Water intrusion in a medical facility can lead to millions of dollars in lost revenue and potentially compromising patient outcome. The key to a “healthy” building is addressing the entire building envelope, eliminating the unseen gaps, cracks and holes in roofs, walls, windows, connections and doors that let in water, humidity, insects, dust and the problems they bring.
THE BUILDING SCIENCE OF AIR LEAKAGE
The best first step to improving healthcare building performance and indoor air quality (IAQ) is to stop air leakage. “Air leakage” is any breach in the building envelope that disrupts continuity between connections, allowing unintended infiltration/exfiltration to occur in a conditioned (heated or cooled) space.
When this happens, HVAC systems struggle, resulting in uncontrollable hot and cold spots, wasted energy and skyrocketing costs. Health and safety issues can also arise with the airborne spread of dirt, pests and even viruses.
Part of Tremco Construction Products Group
DIAGNOSTIC TECHNIQUES
So how do you begin to address air leakage? A professional building envelope assessment consisting of a visual inspection and tests such as a simple smoke pencil can help pinpoint the sources.
Another common diagnostic tool, Infrared Thermography, measures and maps surface temperatures, which may reveal surface heat patterns that signify heat loss/gain.
Blower door testing is also popular. This test can determine the air leakage rate and reveal how much energy is being lost to air leaks.
After identifying where leaks are located, the next step is to seal those pathways and enjoy benefits such as:
→ Reduced heat loss → Less dust, mold, and pollutants → Reduced noise and odours → Less condensation, mold, and mildew → Improved building envelope and building performance
IT BEGINS WITH THE BUILDING ENVELOPE
Maintaining the integrity of the building envelope is essential to providing a safe, comfortable, and healthy environment. Quite simply, better indoor air quality paired with better building performance yields healthier buildings with happier occupants.
The restoration industry in Canada is one of the most diverse in the world with contractors ranging in scope, scale, and training from single person owner/operators to complex multi billion-dollar global firms. The most important factors in selecting a contractor in the healthcare sector should be: experience, knowledge of regulations, training and specialized equipment.
Experience in this sector is critical. As you know, to protect our most vulnerable, adherence to policies and procedures in a healthcare facility is critical. What would normally be a simple lapse could have dire consequences. For these reasons especially it is critical that any restoration contractor provide a list of references and experience in similar facilities before they are retained. Unqualified contractors can result in incalculable damages to a facility and its community.
It should be a requirement that your contractor is intimately familiar with all relevant government regulations, specifically CAN/CSA Z317 as well as being able to complete a detailed ICRA for all portions of the work. Not only should the firm be familiar with these standards, but also consider key project personnel. Do the project management team and key field supervisors have appropriate training and experience in healthcare related restorations? Do the individual workers have this training? Are these individuals comfortable participating in a multi-disciplinary IPAC team to complete the work? SPONSORED CONTENT
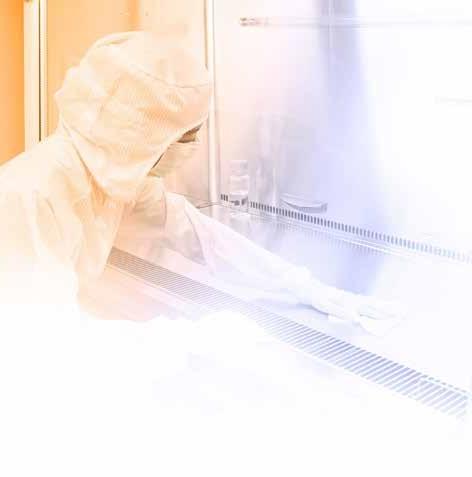
Restoration in healthcare facilities also requires specialized, dedicated equipment. Any equipment used in a healthcare project should be thoroughly cleaned, wrapped and inspected prior to it arriving on site. The risk of cross contamination, especially from restoration related equipment (air filtration devices, air movers and dehumidifiers) is substantial if they have been relocated from another project without these critical steps.
Having a trusted partner, who is experienced, trained, and has the right resources should be a critical part of any BCP in a healthcare facility. Without this partner small floods, fires or environmental issues could drastically impact the operations of the facility and its community.
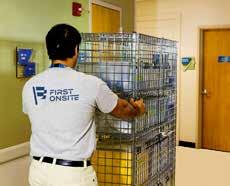
UVC Germicidal for Air Handler Unit Coils
üImprove Indoor Air Quality üExtend HVAC System Life üSave Energy
Now, more than ever, indoor air quality is an issue of vital importance for Healthcare facilities.
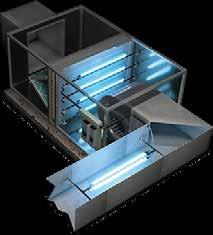
UV germicidal UVC light systems reduce the risk of airborne infectious disease and have been proven to inactivate the SARS-COV-2 virus. This virus, like all viruses, bacteria, and mold has no defense against UVC light. The very short 254 nm wavelength of UVC light is able to penetrate the cell walls of microorganisms and disrupt their DNA which inactivates them.
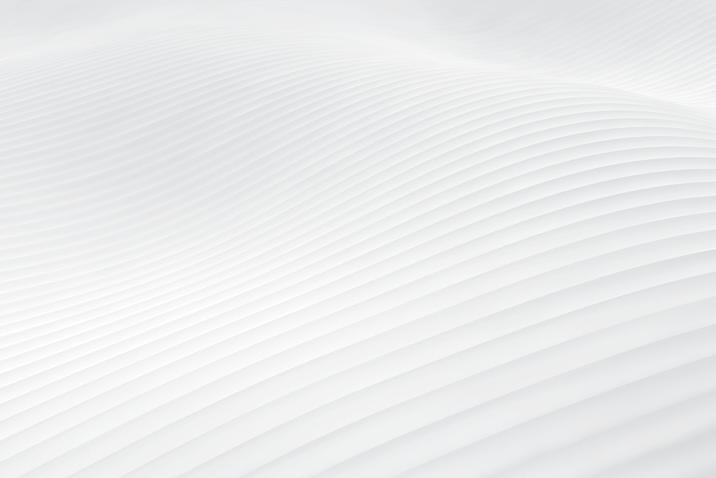
Every healthcare building can benefit from germicidal UVC disinfection; reducing biofilm on coils, resulting in significant energy and maintenance savings.