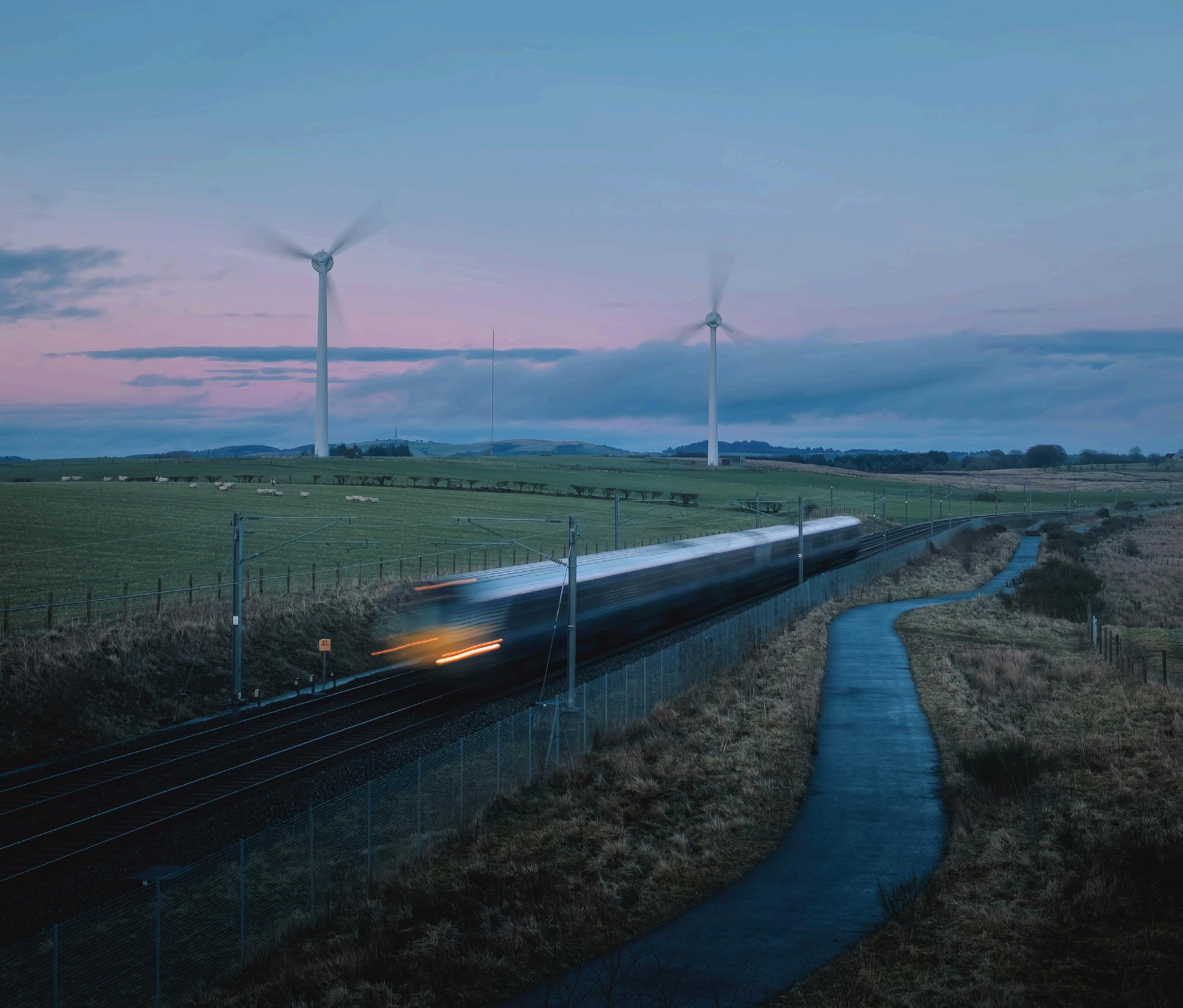
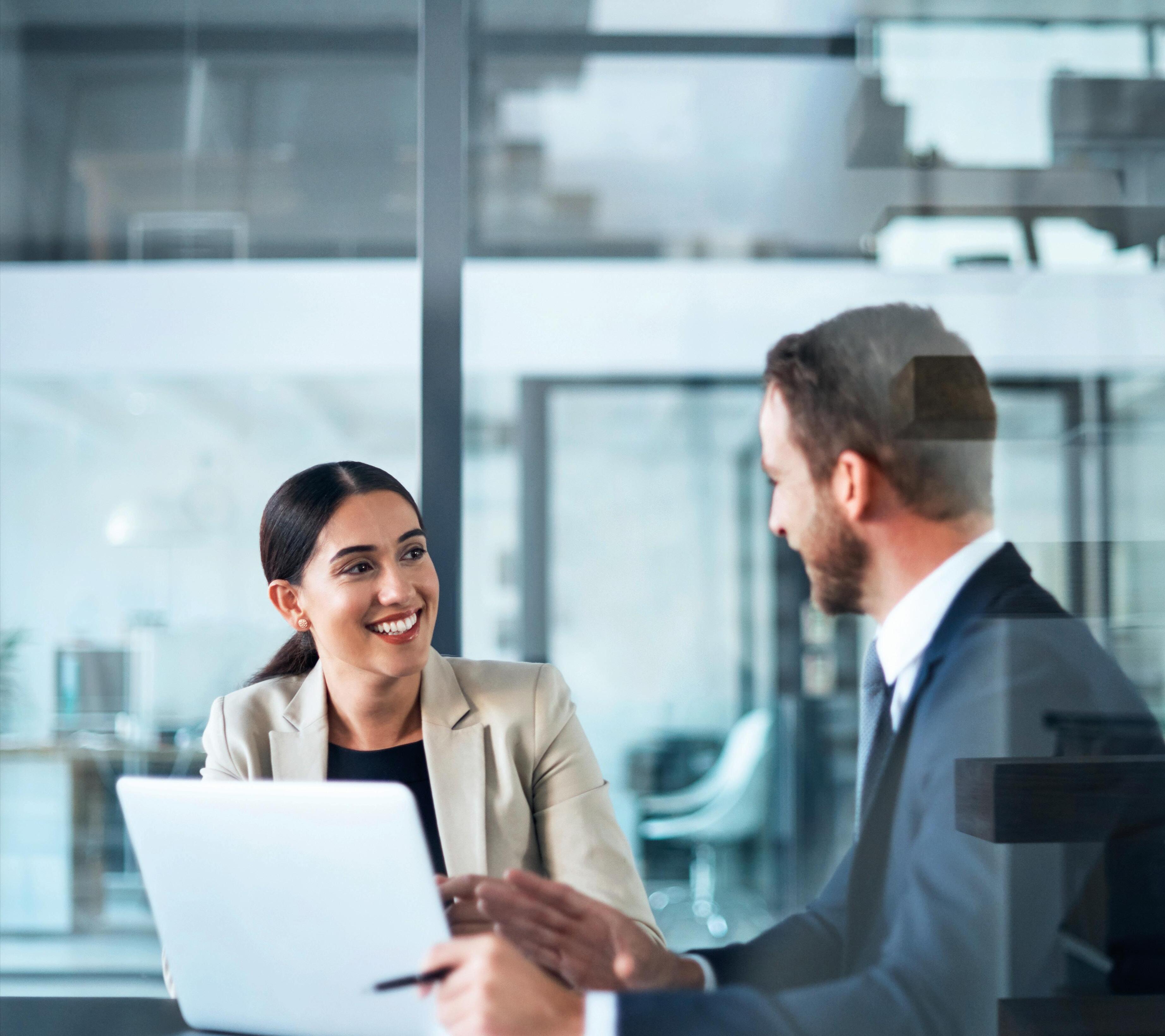
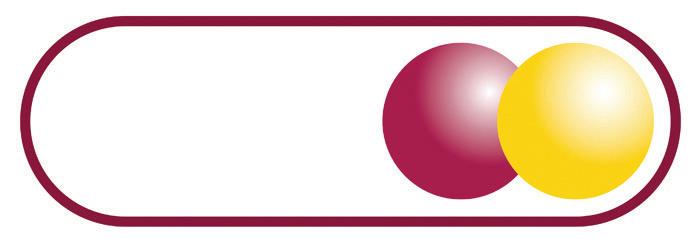
Jamie Tregarthen jamie@railpro.co.uk
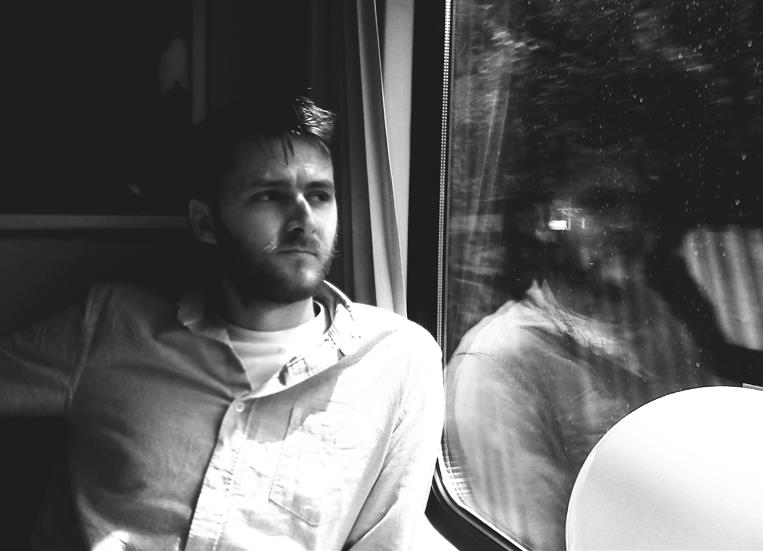
RECRUITMENT
Jamie Tregarthen jamie@railpro.co.uk
RECRUITMENT
Cherie
A month of the longest and hottest days came to an end with Rail Live welcoming over 5,000 rail professionals to Long Marston. It was a busy month for the site as earlier on in June engineers in the making gathered at the Long Marston Rail Innovation Centre to celebrate the culmination of their achievements in the Primary Engineer Rail Project, supported by Porterbrook. We also have a story this month from Ben Ackroyd Chief Operating Officer at Porterbrook on the company’s new £3 million facility at Long Marston which opened in April. The facility includes three pitted roads that can accommodate up to a six-car set, is supporting customers with maintenance and upgrade work.
Looking forward to this issue we are focussing on sustainability with stories from Dr Victoria Hutchinson, Director, Environment Practice at Atkins Global on the different challenges facing infrastructure growth and Rachel Preen on Prolectric’s goal to reduce its environmental impact with zero emission, hassle-free solar technology, specially designed to deliver increased worksite sustainability, safety and efficiency.
As always we have our regular columnists with our opening piece from Richard Schofield, Group Infrastructure Director for MTR Corporation (UK) Limited, reflecting on the operation of the Elizabeth line to-date.
Predictive analysis
Data standardisation
AI capabilities
Risk tools
To manage a nationwide rail network, we need to leverage information from a rapidly increasing volume of data.
Our Data Insights team analyses safety risks to unearth the intelligence with the biggest impact on safety and performance.
This can be used to improve industry decision making and drive meaningful change. We’re constantly enhancing rail’s practical knowledge, working with industry experts and innovating with AI, new datasets, and new statistical models. We find new ways to answer the tough questions, no matter how much data or what format. But most of all, we collaborate with our members to find new ways to deliver value.
To suggest new opportunities for analysis, visit rssb.co.uk/data-capability
We’re
every step of the way
All the latest from HS2, DB Cargo, Nexus, Network Rail, TOCs and more
31 Alongside utilities and the road network, our rail infrastructure is the backbone of the UK’s economy and society at large says Mark Thomas of Fugro
35 LAYING DOWN THE LAW
The UK's Mental Health Awareness Week, which ran from 15 to 21 May this year focussed on the impact that the cost of living crisis is having on the nation's mental health
37 LOGISTICS UK
Ellis Shelton, Policy Advisor, Logistics UK explains why it is imperative that rail adapts and implements new infrastructure to ensure the sector remains efficient and sustainable
39 Hansen Chan, IP Product Marketing Manager at Nokia on why operators need to reimagine their station networks to meet the expanding needs of passengers and operations
41 WOMEN IN RAIL
18 INTERVIEW
Sam Sherwood-Hale spoke to William Cook, Group Commercial Director for The William Cook Group
22 Richard Schofield, Group Infrastructure Director for MTR Corporation (UK) Limited, reflects on the operation of the Elizabeth line to-date, and speculates on emerging challenges for MTR and the industry
25 THE CHEEK OF IT
Demand recovery still patchy in first quarter but Elizabeth Line growth still flatters to deceive, says Chris Cheek
29
SAMANTHA GREER, Senior Consultant, Setfords Solicitors asks, what are the legal implications for ownership and liability?
On 21 June 2023, companies representing the UK’s rail industry came together at Newark Showground to participate in the seventh annual Big Rail Diversity Challenge
43 The Rail Ombudsman is working to raise industry standards and improve consumer confidence
45 GBR will bring a step change in operational efficiency – but how? Matthew Flynn of Vendigital finds out
47 SUPPLY CHAIN
Rail Forum announces final TOCTalk line-up
48 SUSTAINABILITY
Dr Victoria Hutchinson, Director, Environment Practice at Atkins on the different challenges facing infrastructure growth
53 SUSTAINABILITY
Another Milestone for Edinburgh Trams
1 and 2 November
2-day conference with inspiring keynotes including:
– Huw Merriman MP, Rail and HS2 Minister
– Andrew Haines, Chief Executive, Network Rail
– Baroness Grey-Thompson DBE, DL, Member of the House of Lords
– And many more…
Large interactive exhibition area with spotlight pitches presenting services, products and solutions
Evening programme including networking drinks, dinner and entertainment
56 SUSTAINABILITY
Rachel Preen on Prolectric’s goal to reduce its environmental impact with zero emission, hassle-free solar technology, specially designed to deliver increased worksite sustainability, safety and efficiency
59 SUPPLY CHAIN
Ben Ackroyd Chief Operating Officer at Porterbrook on the company’s new £3 million facility
65 SUSTAINABILITY
Maccaferri supplies Anti-Burrowing mesh for major rebuild of UK railway lines
67 VIEWPOINT
Midlands Rail Hub by Numbers
70 IN CONVERSATION
Stuart James, Sales Director at Marlec Engineering Co Ltd
73 VIEWPOINT
John Golden, UK Regional Director at Nozomi Networks explains why cyber resilience is essential for the railway sector
74 IN CONVERSATION
Wayne Carrington, National Accounts Manager at Vogelsang Ltd
77 VIEWPOINT
NIS backing paves the way for youth zone’s critical work in Wolverhampton
78 IN CONVERSATION
Ian James Allison Business Development Director At Park Signalling
81 VIEWPOINT
Jim Steer of Greengauge 21 explores the key Northern Powerhouse link between Sheffield and Leeds and points to a set of cost-effective measures that can be introduced in the 2020s
82 IN CONVERSATION
John Lawrence, Director at JPL Diversified Ltd
85 MACHINERY
Lifting Jacks for Snowdon Mountain
86 IN CONVERSATION
Harry Watson, Business and Design Consultant at Bpi Bespoke Project Installations Ltd
89 VIEWPOINT
The power of working smarter, not harder
90 IN CONVERSATION
Antonio Sequeira, Vice President Market Manager Strategy & Business Development Railway at HUBER + SUHNER
93 VIEWPOINT
Fabien Rech, SVP EMEA at Trellix on protecting the mission critical transportation and shipping operations
94 IN CONVERSATION
Steve Freeman, Managing Director at iPort Rail
97 VIEWPOINT
Three ways for rail to shift towards always-on resilience
99 BOOK REVIEW
The Great Train Robbery and The South Coast Raiders. By Graham Satchwell
Mal Drury-Rose, Karen Schofield, Carolyn Ferguson, Andy Burnham, Susan Hinchcliffe, David Ellis
When critical industry processes and concerns require the elimination of lost tool issues, the solution is to minimise human error. Let Snap-on ATC handle the control and tracking automatically
• Standardise Work
• Improve Productivity
• Control Inventory
• Reduce Losses
• Control FOD
• Improve Security
• Audit Trail
• Increase Accountability
• Oversight Prevention
• Calibration and Maintenance Reminders
With advanced digital imaging technology and proprietary software, Level 5 Automated Tool Control System (ATC) scans the tool drawer and records which tools are removed and replaced in real time. You know where everything is at all times without your techs being slowed down for a second. The system also knows when tools are broken, allowing you to replace or repair them right away. It’s tool control that works hard to keep your techs working at their best.
snapon-industrial.co.uk snaponlevel5.com
• Automated Tool Control Box
• Automated Tool Control Locker
• Value Add: Networking
• No individual scanning required
• No RFID tags to install
• No limitations on tool sizeif it fits in the drawer, it works
• Optional polyurea elastomer coated top vs. stainless steel
WORKS WITH
• Intuitive touchscreen interface
• Audible voice confirmation of tool removal and replacement
• Automatic locking
• Errors announced and displayed for incorrect tool position
• 10.1” widescreen, 16:9 LED, resistive touchscreen
• Dual wireless antennas for improved connectivity
• Hardware – 64-bit processor with 8GB RAM
• Track irregularly shaped items like extension cords, tools kitted in plastic or fabric carrying cases, personal protective equipment and more
• Track serialised items like torque wrenches, multimeters or micrometers
• Fully networkable – connects to Level 5™ administrative interface
• Recharge while storing power tool
ALL THE ACCESSORIES YOU NEED
• FastFlag™ adds status display lights
• ZoomID™ gives you the ability to track serialised, certified and calibrated assets in the ATC Box
ZoomIDTM
FastFlagTM
Tel: 01536 413 904
industrialuk@snapon.com
POWERFUL ADMINISTRATIVE SOFTWARE WITH REAL TIME REPORTING
• Comprehensive analysis, reporting, and inventory tracking can be performed from administrator workstations located anywhere on the network in real time
• Reports are fully customisable and exportable to Excel or PDF
• Registers transactions in real time – both at the box and between the box and the admin client
• Real time communication includes email alerts when tools are used, when calibration is required, when tool status changes and lost or broken events
STATE-OF-THE-ART BATTERY POWER
• 16+ hours of battery run-time; 30 minutes of backup power for uninterrupted power supply
• Snap-on rechargeable batteries feature state-of-the-art circuit protection that prevents overload
SPECIFICATIONS
• 1 year electronics warranty
• Extended warranty available
• Unlimited number of assigned users
• Networking through Ethernet or wireless
• 1 copy of ATC software required for each administrator
PROVEN FAST SAFE
A new signalling system is to be installed at the £70 million Gosforth Metro depot as the state-of-the-art facility continues to get ready for the new train fleet. Nexus, the public body which owns and manages Metro, said the work was vital for ahead of more new trains arriving, and the first one entering service at the end of the year. Digital signalling systems will be installed and staff will move into a modern new depot control room overlooking the Gosforth site, which will be used to safely manage train access to and from the mainline.
DB Cargo UK has unveiled a new-look Class 66 locomotive (66023) to mark the coronation of King Charles III.
The locomotive was officially unveiled at the company’s annual colleague event held at Toton TMD on Saturday, 17 June.
The unveiling was performed by Depot Manager Matt Manson in front of more than 800 employees and invited rail enthusiasts.
The Royal blue locomotive bears a Union Jack and the official coronation logo featuring emblems from the UK nations - a rose, a thistle, a daffodil and a shamrock. The transformation took place in Toton TMD’s on-site paintshop.
Chief Executive Officer Andrea Rossi said: ‘DB Cargo UK has a long and proud relationship with the Royal Family, holding the Royal Charter for the maintenance and operation of the Royal Train. It seemed fitting to mark His Majesty the King’s coronation with a colourful tribute of our own.’
HS2 has begun assembling the UK’s first major railway viaduct to be entirely manufactured off-site, in a move that represents a major step forward for viaduct design and promises to boosting safety and efficiency on site.
Unlike more traditional viaduct designs, every major element of the 880m long Thame Valley Viaduct is being manufactured in a factory before being slotted together on site like a giant Lego set, cutting its carbon footprint by around a third.
Crossing the flood plain of the River Thame, just outside Aylesbury, the viaduct will carry HS2 trains at speeds of up to 360kph between London, Birmingham and the North – dramatically improving journeys while freeing up space for more freight and local services on the existing network.
The 68 giant concrete piers – each weighing 42 tonnes – are being cast at PACADAR UK’s factory on the Isle of Grain, in Kent, before being transported to site by road. The first 14 piers were lifted into position on top of their foundations over the last four weeks.
Set low into the landscape with a simple and consistent profile, the underside of the viaduct will be just three metres above the ground, with thirty-six even spans crossing the river and surrounding wetlands.
Applying lessons from the construction of recent high-speed rail projects in Spain, the design team opted for a simple structural solution with two 25m long hollow beams per span, which cuts the amount of carbon-intensive concrete and steel, while simplifying work on site.
Tomas Garcia, HS2 Ltd’s Head of Civil Structures said: ‘Thame Valley may not be HS2’s biggest viaduct, but it does represent a major step forward in terms of its structural design. The post-tensioned double-beam approach used here has enabled the whole
viaduct to be manufactured off-sitedramatically improving efficiency, safety and quality while delivering outstanding performance and durability.
‘Once complete, HS2 will offer zerocarbon journey across the UK, but structures like this will also help us develop new ways to cut embedded carbon in construction that can be adopted across the rest of the industry in the future. That’s why it’s great to see the first piers in place as our construction partners begin to assemble this ground-breaking viaduct.’
The viaduct was designed by HS2 Ltd’s main works contractor, EKFB - a team made up of Eiffage, Kier, Ferrovial Construction and BAM Nuttall - working with specialist on-site construction partner, FC Civils Solutions.
Traditionally, viaduct beams are secured together above each of the piers with a concrete diaphragm which is cast in situ. The larger pre-cast beams that will be used at Thame Valley can be secured directly to one another, removing the need for the diaphragm – and allowing every major element of the structure to be prefabricated.
As well as cutting embedded carbon in terms of materials, the pre-fabricated
approach requires less lorries to deliver material to site, simplifies construction, cuts waste, reduces disruption for the community during construction - and improves safety by reducing the need for people to work at height.
Off-site manufacturing also helps spread contract opportunities and supply chain jobs across the UK, with 200 people – including apprentices and graduate engineers from nearby Universities – employed on the Isle of Grain, delivering the viaduct and also making tunnel segments for HS2’s London tunnels.
Tiago Palas, FC Civils Solutions Head of Operations, said: ‘The construction team is thrilled with progress made so far. In a short amount of time, we have successfully installed fourteen pre-fabricated piers as well as pressing ahead with the other stages of works, on-and-off site, such as pile cap construction and the production of the precast beams ready for installation in autumn.
‘Slotting the piers into place takes precision, collaboration and the expertise of the team, however, it’s a relatively quick process - an efficiency enabled by its innovative design and construction methodology.’
Kent-born trailblazer Verena Holmes honoured with train naming on International Women in Engineering Day as Southeastern looks to boost number of women in engineering roles. In marking International Women in Engineering Day, Southeastern wanted to raise awareness of roles for women in engineering, traditionally a male-dominated field. Verena a native of Ashford, Kent, was born on 23 June in 1889, the same date International Women in Engineering Day is marked each year.
The train being named after Verena Holmes is a Class 375 operating on Mainline routes between London, Kent and East
Sussex, which was unveiled at a ceremony at London’s Cannon Street station. Verena Holmes’ family was represented by her great niece Caroline Yardley, and she was welcomed by Southeastern’s Managing Director, Steve White.
Verena was arguably the first female in the UK to have a fulltime career as a professional mechanical engineer. She was also a strong advocate for women in engineering and was dedicated to the development of her fellow female engineers. She set up her own allfemale engineering firm in 1946 after working on naval weaponry during World War Two.
Artificial intelligence software is helping Network Rail find and remove forgotten scrap materials from the side of the railway more quickly and safely than ever before. Network Rail Southern region is spearheading a trial of One Big Circle’s video and AI technology to locate old railway kit that can either be re-used or recycled, reduce the risk of injury to colleagues from slips, trips and falls, and tidy up the railway at the same time.
The technology captures high-definition train’s-eye-view video – known as Automated Intelligent Video Review (AIVR) – from across the rail network, with the footage instantly accessible in the cloud. The footage is then analysed by AI to find scrap rail, sleepers and bags of ballast and map their locations using GPS, enabling maintenance teams to plan how and when to safely remove the items.
The project is currently being trialled on the Wessex route – which is one of the busiest on the rail network, taking in all or part of the counties of Surrey, Berkshire, Hampshire, Dorset, Devon, Somerset and Wiltshire – before looking to roll it out more widely. In addition to helping improve efficiency, the new technology also has safety and financial advantages.
On Network Rail’s Wessex route, ‘slips, trips and falls’ are the largest causes of injury and scrap on the side of the track is a significant hazard, particularly as most work happens during darkness.
Martyn Shaftoe, Network Rail’s Wessex route health and safety advisor, who is leading this project, said: ‘We are delighted to be working in partnership with One Big Circle on this exciting project. I believe this
technology will play an important role in helping keep our front-line colleagues safe, help us become more efficient in locating and removing scrap, as well as improving the overall condition of the railway for the benefit of our passengers and local residents. Unfortunately, over recent years, the railway has become somewhat of a dumping ground for discarded railway sleepers, scrap rail, redundant ballast bags and many other assets. The challenge we face is there is no definitive list of where these materials or assets are.
‘The prospect of accurately locating scrap material using high-definition video footage and AI without the need for colleagues to walk along the railway is a huge safety improvement opportunity.’
Financially, not only can some of the scrap material be recycled and any money accrued used to support running of the railway, but some of the leftover materials are also reusable. For example, Bomac concrete sleepers are no longer manufactured, but there is still a demand for them as replacements on sidings and on some stretches of track. Thanks to this technology, 40 of these sleepers have been identified on a site between Yeovil and Weymouth where they can be recovered and stored for future use across the business, preventing the need to buy costly new equivalents.
A £30 million project to restore rail services to Aldridge for the first time in almost 60 years have taken a major step forward after securing Government backing. The Department for Transport has given conditional approval to start work on an outline business case to build and open a station on the Sutton Park line to provide direct passenger services to Walsall.
This means that funding can now be drawn down to take the project, which is being led by Transport for West Midlands (TfWM) and the West Midlands Rail Executive (WMRE), to the next more detailed design, and development phase.
TfWM, which is part of the West Midlands Combined Authority (WMCA), is funding the development from its £1.3 billion City Region Sustainable Transport Settlement.
The town sits on the freight only Sutton Park Line between Walsall and east Birmingham which closed to passenger services as part of the Beeching cuts in 1965.
The proposal is for a single platform station to be built on the edge of Aldridge Town Centre, with road access from Westfield Drive.
Torrent Trackside is a business built for rail
We are committed to investing in the latest battery powered tools, lighting and equipment which provide outstanding levels of power and efficiency. The advantages of battery power include:
l Zero emissions - better for the environment and safer for the operator
l Instant power at the flick of a switch - no tugging on pull cords
l Significant reduction in HAVs - up to 80% for some tools
l Battery tools are smaller, lighter and easier to transport
l Noise Reduction - ideal for built up residential areas and night time working
l Battery and solar lighting is powerful, lightweight and silent r
Download our brochure
As part of our commitment to a greener future Torrent Trackside will no longer be printing brochures To view or download our new brochure scan this QR code or visit the brochures section on our website: www.torrenttrackside.co.uk/brochures/
helpline 0845 769 7168
Brand-new tram-trains that will revolutionise public transport are now being tested on the South Wales Metro railway lines. Supplied by leading manufacturer Stadler, the light rail vehicles will be able to run on both rail and tram lines and will operate on electrical lines and battery power. At 40 metres long the CITYLINK tram-trains can carry more than 250 passengers and on rail run at 100kph.
The high-floor vehicles feature spacious, bright and air-conditioned passenger compartments with six multifunctional areas for bicycles, seats for people with reduced mobility and two wheelchair passenger spaces.
Transport for Wales recently electrified the first phase of the South Wales Metro and the first tram-trains are now in testing, ready for passengers in 2024.
The Deputy Minister for Climate Change with responsibility for Transport, Lee Waters said: ‘This is great news. Funded by our £800m investment in a new fleet of trains, these new light rail tram-trains, electrically powered, faster and with greater capacity, will play an important part in our plans to transform rail services in Wales.’
Alexia Course, Chief Commercial Officer at Transport for Wales said: ‘This is another major milestone for us at TfW, we’ve already introduced three new types of train to our
network for passengers to use this year. We’re now pleased to be testing our light rail tram-trains that will operate a turn up and go service on the South Wales Metro in the very near future.
‘Wales has yet to experience light rail travel and these vehicles will provide faster,
A North East Community Rail group is hoping to pique the interest of rail passengers with an innovative new machine designed to spark conversations about community rail. The Tyne Valley Community Rail Partnership’s ‘Cyclo Knitter’ wowed passengers at Newcastle station on 19 June when it was unveiled by the community group and rail industry leaders. The machine has been funded by a £3,000 investment from CrossCountry’s community engagement fund.
The multi-functional bike was inspired by Dutch artist George Barret-Jones, who published a video online in 2018 featuring his Cyclo Knitter at Eindhoven rail station. The North Eastern version was constructed by Geoff Wallman of Hexham-based Northern Skunkworks, who designed and built a fully-accessible machine that can be transported by train. Swapping attachments on the static cycle – which can be safely used on rail station platforms – enables riders to knit scarves, blend smoothies or even charge
cleaner and more efficient travel. We’re investing £800 million in brand-new trains for Wales and a billion pounds on the South Wales Metro and through transforming our network we want to encourage more people to travel sustainably.’
William Cook is the sixth generation of his family to run the eponymous engineering group. He joined the business in 2013 after a brief stint as a journalist. After a decade in manufacturing for the rail, defence and industrial sectors he considers himself an engineer by inclination if not by training.
What is your role within William Cook?
I am the Group Commercial Director for the William Cook group, which includes William Cook Rail and its sister companies serving the defence and industrial sectors. My formal role is mainly outward facing; I work with our customers to understand how we can satisfy their requirements and I keep track of trends and opportunities in the sectors we serve. However the William Cook group is (just) small enough for me to be involved with almost every aspect of running the business, which keeps it interesting.
How long has William Cook been in business?
The William Cook group was started by my great-great-great-grandfather in the 1840s. He was a sawmaker, and we recently repurchased his original workshop in Glasgow. In 1883 the family started a steel foundry in Sheffield and we have been casting steel there ever since. The group acquired its Leeds factory – now the home of William Cook Rail – in the 1980s – and in the last twenty years this factory has focussed more and more on the rail sector. Today it is a fully fledged designer, manufacturer and overhauler of safety critical components and systems for rolling stock.
What types of products and services do you offer?
The larger segment of William Cook Rail’s business is the design and manufacture of safety-critical structural components for rail rolling stock. These comprise castings and fabrications which are supplied machined, painted and often within more complex assemblies. Typical products are highstrength steel bogie frames and complete coupler systems.
William Cook Rail also offers comprehensive refurbishment and overhaul services for couplers and bogies. These range from testing and re-wiring electrical harnesses to total bogie overhaul including non-destructive examination and repair of bogie frames. We have a policy of performing all overhaul work in-house to guarantee quick turnaround times.
How have the products and services you offer developed over the years?
William Cook Rail used to simply be a subcontract manufacturer working to its customers’ designs. Over the years we have developed significant in-house design engineering expertise. These days we have some degree of design input in everything we make. This ranges from design for manufacture – optimising the customer’s design to suit our production processes – to clean-sheet design of new components and systems in response to specific challenges.
What are some major projects you’re currently working on?
Some of the biggest new-build projects we are currently working on are for light rail rolling stock. We are supporting several rolling stock builders on new tram and metro programmes in Europe and North America.
William Cook Rail’s largest single project at the moment is an upgrade to the M7 railcars on the Long Island Rail Road in New York. We are supplying traction motor components in a specialist grade of stainless steel to overcome the challenges of operating in a corrosive maritime environment on the Atlantic coast. The components will extend the life of the fleet and reduce the noise of the trains to improve comfort for passengers.
We will shortly commence a major overhaul of the wedgelock autocouplers on London Underground’s Jubilee Line tube trains. This involves electrical and mechanical refurbishment on a tight turnaround time to keep the line running as usual.
What are some standout projects you’ve been involved in over the years?
One of the largest projects from the early days of William Cook Rail was with the former Bombardier Transportation on the Electrostar and Turbostar trains. William Cook Rail designed and manufactured the bogie frames which each comprised eight high-strength steel castings machined and fabricated into a single assembly. Over the years we made over 5,500 bogie frames for
Electrostar and Turbostar trains running on the British and South African railways.
Some of the smallest but most memorable projects are for the heritage rail market. William Cook Rail worked on – and indeed sponsored – the construction of the Peppercorn A1 Pacific class steam locomotive ‘Tornado’ in 2008. Since then we have made wheels and other steel castings for similar new build steam locos such as B17 class ‘Spirit of Sandringham’ and P2 class ‘Prince of Wales’. We are very proud to help preserve railway history in this way.
What types of companies do you collaborate on projects with?
William Cook Rail’s customers fall into two categories. For new-build projects they are the rolling stock builders; Alstom, Siemens, Stadler and smaller players such as Skoda
and Pesa. For refurbishment and overhaul our customers are rolling stock owners and operators including London Underground, the big leasing companies and freight operators.
We also work more and more with consulting engineers such as Ricardo and Mott Macdonald to develop and implement solutions to specific customer challenges.
What are your plans going forward to ensure William Cook’s services are still around for years to come?
Over the last few years William Cook Rail has invested massively in its manufacturing and overhaul facilities. We have installed millions of pounds worth of new CNC machining centres, high-efficiency heat treatment facilities, a dedicated bogie overhaul workshop and most recently a
brand new paint facility. These investments have made us independent of any subcontractors and allows us to offer our customers a ‘one-stop shop’ with very quick turnaround times.
What are some of the biggest challenges this sector currently faces?
By far the biggest challenge to the UK rail sector is the lack of a real domestic rolling stock builder. Yes, the likes of Hitachi and CAF have assembly lines in the UK but these really just put together kits of imported parts. This is hollowing out the UK rail supply chain and rendering us wholly reliant on overseas technology. William Cook Rail is an all-too-rare exception; almost all of the parts we make for new-build trains are exported.
What are some potential solutions?
The most obvious solution is mandatory minimum UK content obligations for rolling stock procured with public money. Government procurement decisions sometimes seem to ignore the fact that a pound spent at home is worth more in tax receipts and economic added-value than a pound spent abroad.
William Cook Rail works with train builders and operators to design, manufacture and overhaul safetycritical components and systems for the global rail industry. William Cook Rail serves international rolling stock companies including Alstom, Bombardier, Siemens, Stadler and Transport for London from its world-leading foundry in Leeds, West Yorkshire, and its products can be found on trains around the world.
Want to know more about William Cook Rail?
Tel: +44 (0)113 249 6363
Email: rail@cook-rail.co.uk
Web: www.william-cook.co.uk
Richard Schofield has extensive experience in UK railway operations and major projects. Previous roles include Head of Civil Engineering for the Channel Tunnel Rail Link (High-Speed 1), where he took it from construction to operation. He then ran it as Network Rail General Manager for five years. He has been Route Managing Director for Network Rail on the Anglia route, and led delivery of rail transport infrastructure for Stratford at the 2012 Olympics.
From 2017, as MTR Elizabeth line’s (MTREL) Programme Director, Richard contributed to the wider Crossrail project as Chair of the Trial Running Mobilisation Board. In 2021, Richard became MTR UK’s Infrastructure Director, responsible for developing MTR’s rail infrastructure capability. He led MTREL’s support of the Crossrail project’s final critical stages.
London now has a railway that is the envy of the world. Just over a year has passed since the Elizabeth line started to carry passengers on a brand-new railway through London. However, the city has been waiting eighty years for a railway of such quality; that’s how long has passed since an eastwest London railway was first mooted. The project that became the Elizabeth line has origins in the 1943 County of London Plan and 1944 Greater London Plan.
The construction phase of the Elizabeth line (then known as the Crossrail project) began in 2010, and in July 2014, MTR was awarded the concession to operate the line for a duration of eight years, with an option to extend by an additional two years.
There was an expectation that the infrastructure would be handed over in time for passenger operations to commence in 2018, and MTR began to create an entirely new team to run a brand-new railway. However, the handover of the railway faced significant delays and encountered technical challenges, leading to revised timelines and rescheduled opening dates. With just four months to go before the planned opening, a delay was announced due to various problems, including the train readiness, station construction and signalling integration.
Building a new team requires commitment, and a common-sense of purpose for all involved. Once the opening date was postponed, it was important to keep resources and teams working closely together and motivated while the project was reshaped, and new dates emerged.
Keeping the public informed was also essential. There was strong anticipation
Richard Schofield, Group Infrastructure Director for MTR Corporation (UK) Limited, reflects on the operation of the Elizabeth line to-date, and speculates on emerging challenges for MTR and the industry
building prior to the opening. In 2016, it was announced that Crossrail would officially be named the Elizabeth line in honour of Queen Elizabeth II, as excitement grew for the eventual opening. At this point I should commend the professional communicators at Transport for London and elsewhere, for their sustained and coordinated PR and information campaigns. Maintaining a positive dialogue with the media, politicians and the wider public can be particularly challenging when delays turn into months and months turn into years!
Big projects work. However, there are not many enduring infrastructure projects that open on time – and even fewer that open on time and to their original planned budget. This was no exception. Longer, complex projects always take longer than originally anticipated, and they cost more as additional challenges come to light, and some requirements are redefined (often for reasons beyond the engineering needs). We don’t have to look very far back to see that the 2012 Olympics in London was envisaged to cost £2 billion but ended up costing £7 billion. Whilst the Olympic Games has its critics, there is an overwhelming public sense that in London, something was delivered properly and to the credit of the nation a whole. The public has huge capacity for forgiveness if the result is both successful and enduring. Politicians are not shy to bask in the glow of success, either!
The public will not forgive you however, if you don’t eventually deliver the promised result (I write this as the HS2 project seems vulnerable to further postponement and ‘de-scoping’). One person’s simplification is another person’s imperfection. It could have been possible to descope Crossrail when problems loomed, and costs escalated, but the ambition remained to push forward
and create the service that had been promised, doing so in such a way that was both deliverable and robust. When you are building a railway designed to last well into the 22nd century (and - if Victorian railways are anything to go by – lasting into the 23rd) then getting it right is vital.
There was a period of trial running and ‘shadow operation’ of just over a year before passenger services started. On 24 May 2022, services between Paddington and Abbey Wood commenced. Initially these ran for six days a week from 06:30-23:00, with twelve trains per hour. As experience was gained, this ramped up to 18, then 22 trains per hour and both the operating hours and the days in the week were extended.
I believe that Crossrail is the most complex rail infrastructure project I’ve seen. This includes previous UK projects such as HS1/Channel Tunnel, and those underway, such as HS2. Crossrail has required a degree of integration and complexity that has been unmatched elsewhere. Although the central section is an entirely new railway, the eastern and western extremities require considerable integration with legacy systems and operations.
One of those complex elements is the train, the Alstom class 345. Mechanically,
‘The infrastructure needs of the UK demand much better than short-term commitment and continual de-scoping.’
the 70 trains are sound but they are a huge leap forward in terms of technology and on-train software, they must integrate with three different signalling systems (TPWS, ETCS & CBTC), and initiate ‘off train’ systems, such as the passenger screen doors at stations.
There have been three major software upgrades to signalling systems since opening, and the manufacturer continues to work on train improvements. It may be ‘three steps forward and one back’ –but that’s still progress although there is a way to go yet to ensure the train is reliable enough.
Although some of our people were in place some four years before operations, it is only once physical movement takes place, that true familiarity can be achieved. A real team spirit has emerged, and whilst nothing is perfect, recent Office for Rail and Road statistics (Q1) show that the Elizabeth line was the only part of Britain’s railway where performance improved – 85.2 per cent, an improvement of two per cent on previous figures and is now established as both the best performing and most used railway in the country.
There has also been a push to recruit from local communities – particularly for station and operational colleagues and this is noticeable in the demographic and ‘local
feel’ for those stations to the east and west of London. Enhanced connectivity and accessibility provided by the Elizabeth line has facilitated economic growth. Businesses situated near Elizabeth line stations have experienced increased footfall, and previously underserved areas have witnessed new investment and development.
The line hasn’t just benefited those living in and around London; it has made it easier for tourists to explore London's attractions, resulting in a positive impact on the tourism sector when it is most needed. Stand at any Elizabeth line station at peak times and the numbers of people travelling is remarkable.
MTR’s UK portfolio brings together rail operations, infrastructure, and transportfocused property development to enable thriving communities across our network and create railways people love. We are now introducing MTR’s renowned Rail + Property development model to the UK. I’m certain that our proposal to transform London’s Liverpool Street station and surroundings (in partnership with Sellar and Network Rail), will have a similar impact.
People tend to forget that the previous improvements at Liverpool Street were made when the station had a footfall of 40 million passengers a year, and rail was in decline. The station now sees over 135 million users a year and passengers –including tourists and those with reduced mobility – can be both overwhelmed and bemused by the place. ‘Do nothing’ isn’t a credible option. Our vision is to deliver a world-class accessible transport hub for London at no cost to the passenger or taxpayer, transforming the station experience for millions of station users.
At the other end of the scale, MTR continues to quietly improve facilities for transport operators. For instance, there’s an ongoing upgrade at Blackwall DLR station that will improve operations in readiness for the new trains over the next year.
While we continue to work on a variety of opportunities in London and the UK, elsewhere, we have major projects being undertaken in Hong Kong; we are helping the Metro Tunnel project in Melbourne and we also have an involvement with the Sydney Metro.
MTR continues to share experiences with key stakeholders involved with significant UK projects such as HS2, and we are helping the wider ‘railway family’ both nationally and overseas to create high-performance, resilient, and robust train plans, through MTR trenolab’s analysis and planning consultancy.
With a General Election in around a year’s time, it is impossible to predict the future structure of the railway with great certainty; however, MTR is looking at a variety of train operating scenarios, with a view
to improving connectivity, choice, and economic wellbeing.
One thing is for certain: private involvement and investment is the only realistic way to underpin long-term infrastructure projects. Network Rail’s ‘control periods’ run for just five years, outside of which the political landscape can change. The infrastructure needs of the UK demand much better than short-term commitment and continual de-scoping.
Only by creating a sustainable longterm plan will our infrastructure solutions improve to serve future challenges. This will require public and private commitment over many years. The Elizabeth line has demonstrated what can be achieved by developing a plan and sticking to it. The trick for the rest of the UK is not to let it take eighty years.
MTR UK is a subsidiary of MTR Corporation. We demonstrate our reputation for operational excellence, exceptional customer service and innovation across our UK portfolio, bringing together railway operations, rail infrastructure and transport-focused property development.
With a consistent track record of delivering through collaborative partnerships and joint ventures, we offer ground-breaking, technologyled approaches. The company's UK rail operations includes oversight of MTR Elizabeth line, the operator of the Elizabeth line (on behalf of Transport for London), covering all aspects of train and passenger service operations.
MTR UK has operated South Western Railway, one of the largest UK franchises, as a joint venture with First Group since August 2017.
For more information about MTR UK, please visit mtr.uk.com
‘It could have been possible to descope Crossrail when problems loomed, and costs escalated, but the ambition remained to push forward and create the service that had been promised.’
‘Crossrail is the most complex rail infrastructure project I’ve seen. This includes previous UK projects such as HS1/Channel Tunnel, and those underway, such as HS2’
The recovery in demand for rail services in Britain from the Covid pandemic continued over the winter, with passenger numbers more than 41 per cent higher than the same quarter in 2022, reaching a new post lockdown high. However, massive 609 per cent growth in numbers using the new Elizabeth Line distorted the figures: growth on the rest of the network was a more modest 18.9 per cent per cent.
Overall, demand came to within 88.1 per cent of pre-Covid levels, according to National Rail Trends statistics, published by the Office of Rail and Road (ORR). However, without the Elizabeth Line, the recovery is to 74 per cent.
The provisional figures cover the fourth quarter of fiscal year 2022/23, finishing at the end of March: across the network, 388.7 million passenger journeys were made during the twelve-week period, up from 275.1 million in 2022. Between them, they covered 13.4 billion passenger kilometres, 23.7 per cent up, and paid a total of £2.2 million in fares, 19.3 per cent more than in 2022.
Looking at demand by ticket type, advance tickets were up by 31.7 per cent, taking sales 30 per cent higher than before the pandemic. Anytime peak and off-peak fares were up by 53.6 per cent and 42.3 per cent respectively, leaving them 15 per cent and 22 per cent ahead of the preCovid figure.
Season ticket holders made over twenty per cent more journeys than last year, but the 62 million total remained 64 per cent below the 2019 figure.
The long-distance InterCity sector saw the strongest growth over the winter –demand was 21.5 per cent up on the 2022
figure, leaving passenger numbers 15 per cent short of 2019 levels. East Midlands Railway (EMR) saw the strongest growth in the quarter, at 23.8 per cent taking demand to within 0.8 per cent of 2019 levels. Great Western saw growth of 22.4 per cent but remained 23.2 per cent short of pre-pandemic demand. LNER saw 21.8 per cent more passengers, taking patronage above 2019 levels by 10.9 per cent – the only franchised operator to achieve this so far. Cross Country saw a rise of 21.3 per cent in passenger numbers but remained almost a third short of pre-Covid levels.
West Coast was the laggard, seeing just 11.8 per cent growth and sticking 31 per cent short of 2019 numbers.
Excluding the Elizabeth Line, services in London and South East moved ahead by 19.6 per cent during the quarter. Between them, the operators carried 208.9m passengers in 2023, up 19.6 per cent on 2022, but remaining 29 per cent below 2019. Strongest quarterly growth came at GTR (28.7 per cent), Greater Anglia (22.4 per cent) and Chiltern (19.0 per cent). Weakest were South Eastern (nine per cent) and London Overground (14.4 per cent).
The Elizabeth Line carried 74 million passengers in its third full quarter of operation. The line was eventually opened throughout in November 2022, and accounted for almost a fifth (19 per cent) of the entire network’s patronage in the January to March quarter.
Amongst the regional franchises, total patronage was just 15.4 per cent up on 2021 and remained 24.0 per cent below 2019 levels. Amongst individual TOCs, Scotrail saw the strongest recovery, growing passenger numbers by 31.6 per cent during the quarter, though still 29 per cent short of
Progressing towards its autumn opening, Brent Cross West station has passed a range of safety and technical tests, with Thameslink trains successfully arriving and departing on overnight trial runs over two weeks in the middle of June. The essential testing ranged from safe boarding, alighting and dispatch from the platforms to on-board passenger information displays, with the station name added to arrival announcements and route diagrams.
JANE
Long-serving GWR employee Jane Jones was at Windsor Castle on 14 June to receive her MBE from Princess Royal. As Head of Public Affairs, Jane has nurtured and grown important relationships with local authorities, communities and stakeholders across the whole of the GWR network.
Network Rail and its contractor, AmcoGiffen, will begin working round the clock on the Severn Estuary line to improve resilience from Monday 31 July to Friday 18 August.
Engineers will be working on a onemile-stretch of railway, close to Purton, and will remove around 15,000 tonnes of material from the cliff face. Teams will then begin to install an ‘active’ mesh system covering 19,500m2 secured by more than 5,000 rock bolts. This system will hold the cliff face in position and help to prevent landslips from damaging and subsequently closing the railway. This section of railway is in desperate need of resilience upgrades as it was hit by three landslips in January 2023 alone, following a bout of prolonged heavy rainfall.
their 2019 figure. TfW saw growth of 15.6 per cent on the quarter but remained a third short of its 2019 figures. Northern saw a rise of 11.6 per cent in passenger journeys, after the previous quarter’s loss, leaving a shortfall of 16.8 per cent. Merseyrail saw growth of 7.1 per cent but remained over 38 per cent short of pre-Covid patronage. TransPennine, still hit by driver shortages resulting in reduced timetables and continued on-the-day cancellations, saw modest growth of 1.3 per cent in the quarter, almost 40 per cent short of their 2019 demand.
Amongst the non-franchised operators, Hull Trains saw growth of 40 per cent and exceeded their 2019 number by 21.9 per cent whilst Grand Central grew numbers by 14.2 per cent and moved 10.7 per cent ahead of their 2019 patronage. As air travel demand continued to recover, Heathrow Express saw growth of 66.4 per cent in the quarter, but carryings remained 22.3 per cent lower than in 2019.
The national totals for the twelve months ended 31 March show that, compared with the last pre-Covid year of 2018/19, the number of passenger journeys was 17.5 per cent lower at 1.4 billion. However, excluding the Elizabeth Line, passenger numbers remained 27 per cent short of the 2019 figure. Passenger kilometres travelled were 22.3 per cent lower at 52 billion, whilst passenger revenue saw a shortfall of 17.6 per cent at £8.4 billion.
As in previous quarters, performance varied between the sectors. Passenger journeys were still 29 per cent below 2019 levels in London and South East and 25.5 per cent on the regional networks but moved to within 16.8 per cent on the InterCity routes.
These figures might be the statistical manifestation of the original curate’s egg. Politeness requires as to call them good in parts, but overall they remain pretty
dreadful, particularly if you’re sitting in HM Treasury.
After all, real-terms revenue is almost £950 million down on the 2019 quarter, and the annual shortfall in 2022/23 was £3.64 billion at a time of accelerating operating costs. Excluding the Elizabeth Line, passenger numbers remain more than a quarter short of where they were before the pandemic. There were more strikes during the twelve weeks as well and hopes of a settlement were frustrated by trades union inflexibility over reform to working practices.
As noted above, there were some bright spots – notably on the East Coast main line, but also on the Midland Main Line, where EMR came within a whisker of topping its 2019 patronage. Congratulations are due, I think, to all the management teams concerned.
Elsewhere it’s a sorry tale – especially on the commuter railways, where there was some further recovery, but numbers remained at least a quarter and in most cases over a third lower than pre-pandemic levels. Despite the urgings of some employers and politicians, there is little sign of a return to the office – at least for more than two or three days a week.
That tends to be confirmed by the continued shortfalls in sales of season tickets, still down by two-thirds, with revenues down from £2.1 billion in 2019 to just £714 million in 2023. They accounted for 8.3 per cent of revenue in 2023, compared with 20 per cent in 2019.
Hybrid working could be one of the forces driving the sale of full price peak tickets: passenger journeys using these were 15.4 per cent ahead of 2019 during the quarter. A similar effect on off-peak tickets resulted in a 22 per cent increase in passenger numbers over the pre-pandemic figure. As with the last quarter, though, it was advance purchase tickets that were leading the charge, with 29.7 per cent growth in passenger numbers.
Yields on the system continued to fall short as well. After allowing for inflation,
the network-wide revenue earned for each passenger kilometre travelled in 2023 was 16.47p, which was 13.9 per cent down on the same quarter in 2019. The figure for the InterCity sector, at 15.92p was 16.7 per cent down, with the regional franchises seeing a fall of 10.6 per cent to 13.15p.
The commuter lines saw the smallest fall in yields at 8.6 per cent. The transport use statistics published monthly by the Department for Transport still give a picture of more recent trends in demand. These weekly estimates have been published since the start of the first lockdown began in March 2020. Other than strike weeks, they suggest that demand averaged around 9395 per cent of pre-Covid levels during the January to March quarter. This increased by a couple of points during April and May to around 96 per cent.
Even if patronage does top the 100 per cent figure over the next few months, the problems of structural changes to travel patterns, falling yields and revenue shortfalls are likely to remain: the challenges of the last four years are by no means over.
BIG PICTURE IN PUBLIC TRANSPORT FIND A FRESH ANGLE
‘As in previous quarters, performance varied between the sectors. Passenger journeys were still 29 per cent below 2019 levels in London and South East and 25.5 per cent on the regional networks but moved to within 16.8 per cent on the InterCity routes.’
Rhomberg Sersa Rail Group is one of Europe’s leading railway contractors offering a comprehensive range of railway infrastructure services and products for design, engineering, construction, renewal and maintenance.
Operating throughout the project lifecycle, we deliver solutions including track renewals and maintenance, overhead line, tunnel refurbishment, gauge enhancement, and specialist on-track plant in-line excavation and material handling systems. We are Europe’s leading slab track design and build specialist and our solutions are complemented by a wealth of experience from our global business.
Innovation is at the heart of everything we do and our focus is on customer-oriented and tailor-made solutions working collaboratively with our clients, partners and suppliers.
Samantha Greer, Senior Consultant, Setfords Solicitors asks, what are the legal implications for ownership and liability?
Artificial intelligence (AI) is playing an increasingly large role in the transport sector, including helping to manage traffic, offering forecasts to prevent flight delays, and enabling autonomous vehicles. While AI is set to transform the transport industry as we know it, its growing use has huge legal implications. Here we break some of these down, from who owns things produced by transportrelated AI products, to what the situation is around liability.
Under English law, intellectual property (IP) rights presume that the creator, inventor or author is a human. This makes the rise of AI-generated productions tricky from a legal standpoint.
Essentially, traditional copyright law protects the original creations of authors (such as artists, composers and other creators), who are defined as the individual who creates a work. For literary, artistic, dramatic or musical productions, the work must be ‘original’ (Section (1)(a) Copyright Designs and Patents Act 1988 (CDPA)) in order to be protected by copyright law. This work needs to be its ‘author’s own intellectual creation’, however, with no human author, the work can’t be deemed original.
That said, it’s accepted that authors can utilise tools, including computer software, to help in the creation of their works. UK copyright law even explicitly states that works can be ‘computer-generated’, which are defined as a ‘generated by computer in circumstances such that there is no human
author of the work’ (Section 178 (CDPA)). Section 9(3) CDPA states that the author/ owner of a computer-generated work is the one who makes the required arrangements to create it.
Who owns the creation?
So, if an AI tool is deemed to have acted independently of any human, the identity of the author is therefore legally uncertain. We can look to Section 9(3) CPDA for some guidance, however, which states that whether copyright is applicable to a piece of AI-generated work depends on if it is clear who the individual is ‘by whom the arrangements necessary for the creation of the work are undertaken’. Currently, this probably means ascertaining whether a human user of the AI tool is the owner of the created work or the original programmer of that tool.
Taking all of this into account, it’s very hard to state categorically who created a given work or made the arrangements necessary for its creation. At the time of writing, where the AI is fully autonomous and no person made the arrangements
required for the creation of a work, then no copyright can exist in the work, because there is no author. However, there is a lack of case law to definitively answer what ‘undertaking necessary arrangements’ means in the context of AI. There is also the question of whether high-level instructions given by the AI system operator will equate to them being deemed authorship/ ownership in the work, or if the role of the programmer of the AI system should be considered. Otherwise, it could be seen that the work was created without any human intervention, meaning it isn’t safeguarded by copyright? These issues could have very serious financial consequences for somebody looking to profit from works generated using AI tools.
It therefore seems that proving the author of a work generated by an AI system is a twostage process. Firstly, we must see if there is a human author of the work. Secondly, if there isn’t, we must identify the person “by whom the arrangements necessary for the creation of the work are undertaken”. However, there isn’t currently a way of telling what necessary arrangements a business should take to ensure it owns and protects any AI creations. Consequently, it appears that traditional IP rights cannot be relied upon and standard IP clauses will need to be revised.
Under English law, nobody can own data, and there are only rights in relation to data. This must also fit into a specific class to be protected – such as confidential information, personal data or database rights. Because there is no general ownership of data, it must be practically and contractually controlled in order to be protected.
So, legally speaking, all rights and requirements must be explicitly detailed in the contract, otherwise you won’t be protected.
Establishing liability is also difficult, as you need to prove a fault. No matter if it’s establishing breach of a duty of care in tort, breach of an express or implied term in a contract, the fault or defect must have caused the loss (known as ‘causation’). However, as the decisions AI-powered devices take increasingly become their own and not at the direction of humans, it becomes more difficult to attribute fault to any human or legal entity.
The ‘persona’ in AI is its data-driven character, so in any future ‘likelihood’ of future action (such as train delays and likelihood of penalty), the models are given a massive amount of input data in order to make a prediction, often without the causality between input and target decision.
Some have questioned whether the person’s responsibility for the damage (be it the AI manufacturer, the programmer, the
‘Others have stated there should be a ‘quasi-legal’ personality for robots that could safeguard manufacturers and users against liability.’
The Transport for the North (TfN) Board met in Manchester at the end of June welcoming the progress on the TransPennine Route Upgrade (TRU) programme, which is a vital component of the expanding capacity on the North’s rail network.
TRU is a multibillion-pound programme of railway improvements and will deliver major upgrades on the 70-mile route between Manchester and York. Whilst some elements of the TRU programme are still in design phase, key elements of work are already being delivered including a new station with longer platforms due to open later this year at Morley, the installation of overhead electric cables between Church Fenton and Colton Junction near York and track upgrades through Leeds.
supplier or the user), should be proportional to the ‘degree of autonomy’ of the robot/ AI system. While others have stated there should be a ‘quasi-legal’ personality for robots that could safeguard manufacturers and users against liability. This is unlikely to come in practice any time soon, as it implies a huge legal shift towards technologies and AI products within our case law. Currently, it appears that whoever is the proprietary owner of the software would be liable if they create legal harms that require a remedy.
In September 2020, the UK High Court dismissed a patent application by an individual in respect of a machine-created invention, on the ground that an ‘inventor’ had to be a natural person. The question was also heard before the European Patent Office, which refused two European patent applications naming an AI system as inventor, and the US Patent and Trademark Office, which similarly declined to grant patent applications in the US. Each case concluded that only natural persons can be named as inventors on a patent.
The end of April 2023 marked a pivotal moment for AI across industries, as the European Commission approved the draft AI Act. Under the draft, AI tools will be
classified according to their perceived risk, which is set out in four stages, from minimal risk to unacceptable risk. Challenges still remain, however, in certain areas. These include the use of AI for reviews of CVs without discriminating against candidates, or, more pertinently to this piece, in high risk scenarios where critical infrastructures such as the transport sector could put the life and harm of people at risk.
Disclaimer: This article is for informational purposes only and does not constitute legal advice. It is recommended that specific professional advice is sought before acting on any of the information given.
For over 100 years WISKA have been at the forefront of cable management design and innvoation. This level of expertise has resulted in the development of our lastest range of products, introducing The Railway Series by WISKA.
The Railway Series is a comprehensive range of industry-specific cable glands and conduit solutions in accordance with EN 45545.
Need an expert? Speak to us today. 01208 816062 / 01208 816708 / www.wiska.co.uk / info@wiska.co.uk
‘Under English law, nobody can own data, and there are only rights in relation to data.’
Alongside utilities and the road network, our rail infrastructure is the backbone of the UK’s economy and society at large says Mark Thomas of Fugro
But this infrastructure comes under an immense amount of wear and tear from day-to-day operations, as well as from constantly shifting weather and ground conditions. As such, it must be constantly monitored and measured. As the rail network ages, monitoring and knowing when to perform routine maintenance on these assets is crucial, not only to minimise downtime, but to keep passengers safe.
Historically, asset management of this kind has been conducted through a combination of methods including specialised monitoring vehicles, physical inspections and manual surveys, with staff physically walking routes to assess the status of tracks, bridges and tunnels, signal infrastructure, and everything else that’s needed to run a rail network. Not only do some sections of track need to be closed to carry this out, but there are the accompanying safety risks that come with deploying boots on ballast.
There is now an array of technological solutions which capitalise on advances in
data visualisation, modelling, and processing to overcome these issues. Being able to represent real world features and measured detail as a digital twin and being able to visualise the data in a 3D space is already having a huge impact across all manner of industry sectors, from construction and utilities through to aerospace and healthcare.
These visual representations of objects and systems can span their entire lifecycles and are updated regularly or in some cases in near real-time to support change detection and assist with decision making and planning.
Digital twins are being increasingly used within the rail sector. Fugro’s RILA® monitoring system is one way that rail operators can gather Geo-data that’s required to design, build and maintain them.
Mounted directly to in-service trains that can operate at speeds of up to 125mph/200kph, RILA® captures precise information on the railway and surrounding infrastructure. Obtaining data in this way significantly enhances health and safety, cost
and delivery programmes. For example, in 2019 Fugro was contracted by Network Rail to survey 850 route-miles across Wales and the border counties of England – a major part of the rail network. Deploying RILA® on Transport for Wales (TfW) in-service passenger trains and operating within the existing regular timetable, the data was collected in under six weeks, immeasurably faster than conventional surveying with no requirement for track possession and no disruption to service.
RILA® is an integrated system of positional sensors, lidar scanners and video cameras that captures standalone assets (signals, overhead line masts etc.) and linear assets (track centreline, overhead line wires, platforms etc) to produce a geodeticpositioned digital twin of the railway corridor, giving designers greater access to full scale information, video or extracted features.
In combination, the data from a single collection can be used for numerous purposes by different teams, from planning track access for maintenance teams, to renewals engineers considering how to
As part of its Innovation programme, HS2 Ltd has teamed up with Leamington Spa-based Altair Ltd, to develop a unique, automated civil engineering design process driven by its software tool, OptiStruct®, that can reduce embedded carbon in HS2’s viaducts by up to ten per cent, as well as shrink viaduct design time from around a month to as little as one hour.
CIRAS, the transport sector’s confidential safety reporting hotline, is launching a new app today, helping transport workers to raise confidential health, safety and wellbeing concerns simply and quickly, on the go. The free app, which works on both Android and iPhone devices, has been developed in response to feedback from CIRAS members and transport workers. CIRAS receives hundreds of contacts a year from people working in transport –including the rail, bus and tram sectors.
GB Railfreight (GBRf) has agreed on a seven-year deal with Caledonian Sleeper Ltd to continue hauling the Caledonian Sleeper coaches. The contract, effective from 25 June,
comes into effect following the service entering into public sector control by the Scottish Government. The services will see GBRf support the new era of the Caledonian Sleeper, operating seven trains a night, six nights a week, hauling the Mk5 coaches between London, Edinburgh, Glasgow, Inverness, Aberdeen & Fort William.
design new track alignment. Operators can survey once and use many times as the collected data is sufficiently accurate to be used to both monitor the condition of the track and create the new design for the intervention works.
A geodetic digital twin, especially when linked to an enterprise resource planning (ERP) system, is a powerful tool from which many different types of information can be extracted. The basic application is location awareness: video footage of the track and surrounding area show all the details at that location, like Google Street View but for railways.
The digital twin or Track Twin offering can also be used to analyse trackside assets, critical clearance issues and areas obscured from airborne systems. Pre-renewal, it can be used to screen for any anomalies or issues with the existing track that can be addressed during reconstruction.
Post-renewal, it can deliver high accuracy data for all-important quality assurance – to check that any pre-existing issues with the trackbed or geometry have been resolved, and to troubleshoot any non-alignment or non-conformities. This all helps maintenance programmes become more cost-effective and proactive.
By adopting these more digitally driven techniques to track surveying, these projects can also have a much smaller environmental impact. The often hundreds of potential van journeys needed to transport surveyors to sites, for instance, are removed. These systems can make use of rail services that are already in operation, with no specialist trains or closures required.
While rail only currently contributes less than one per cent of the UK’s total annual greenhouse gas emissions, it is in a better position than many other forms of transport to operate using zero-carbon solutions.
As electrification projects move forward, significant investment in new infrastructure will be needed in terms of gantries, cabling, and other equipment along the railway. This is only possible if there is a single source of truth around what the network currently looks like and the space that’s available to work with. This is where digital twin technologies come in, providing a whole life support to infrastructure once in place and operational.
RILA® has already been deployed on the Great Western route modernisation, an extensive programme undertaken by Network Rail to electrify one of Britain’s oldest and busiest railways. Over 2,000 miles of rail track were surveyed using the system, performing the analysis without interruption to scheduled services. The robust and timely asset data has been used to help plan electrification work and calculate passing clearances for the new high-speed electric trains.
Other examples include Scotland’s rail network, where Fugro has surveyed the entire network to generate data that will support the introduction of new rolling stock. The network, which consists of around 2,750 kilometres of track, 93 different sections and 638 station platforms, covers many remote and difficult-to-access areas. Having rich survey data and asset information available via a digital twin will support several engineering, asset management and maintenance applications as well as help the design of future electrification schemes.
The UK rail network is more than 150 years old. This, combined with environmental targets and tighter project time frames, means rail infrastructure operators need to get smarter about how they survey sites, and collect and leverage data. Digital twins will allow for faster, better decisions, and help the sector achieve long-term asset viability.
The UK's Mental Health Awareness Week, which ran from 15 to 21 May this year focussed on the impact that the cost of living crisis is having on the nation's mental health
While having a specific awareness week helps to focus attention on certain mental health issues, it goes without saying that mental health issues occur in the workplace all year round and the rail sector is likely to have at least as many employees who suffer mental health problems as other sectors.
The sight of Trespass and Welfare
Officers at many railway stations is now a regular occurrence and arguably a sign of the impact that mental health issues have on the population at large. It is also a positive action that train operators are taking to engage with and help the travelling public as well as promoting safe use of the railway. However, if employers have not yet taken Mental Health Awareness Week as an opportunity to revisit their own mental health and wellbeing strategy, the next month would be a fine opportunity to do so.
Mental health problems can range from short term to long term and include depression, anxiety, or stress. Official data from the Office of National Statistics shows that in 2022 over 17 million working days were lost in the UK due to work-related stress. With one in four people having a mental health problem at some point in their lives it is no surprise that there is increasing pressure on employers to do all they reasonably can to support their employees' mental health, safety and wellbeing.
There is no formula for the occurrence of mental health problems, and they can:
• Happen suddenly, because of a specific event in someone's life.
• Build up gradually over time.
• Be hard to spot because everyone has
different signs and signals.
• Be hidden by the employee as many people find it difficult to talk about their mental health.
• Fluctuate over time, which means an employee's ability to cope with the demands of their job might change.
Employers should be aware that there is a legal angle too, as some employees with poor mental health can be considered to be disabled and therefore receive the protection afforded by disability discrimination legislation. This may occur if their mental health problem:
• Has a ‘substantial adverse effect’ on their ability to carry out normal day-to-day activities.
• Lasts, or is expected to last, at least twelve months or to recur.
There is no requirement for the employee to experience the symptoms all of the time for it to be considered a disability. Furthermore, the use of medication to manage the effect does not remove the fact that there is a disability. The underlying health issue still exists, even when there is a method available to help with the management of the disability.
Under the Equality Act 2010, employers should consider the reasonable adjustments that they can make to support employees (including contractors and self-employed people hired to personally do the work) with a mental health issue, much in the same way as the employer would for an employee with a more obvious physical disability or illness. These adjustments can include changes to an employee's working arrangements or responsibilities such as:
Martin Fleetwood is a Consultant at Addleshaw Goddard’s Transport practice. The Rail Team has over 30 lawyers who advise clients in both the private and public sectors across a wide range of legal areas. As well as contractual issues, the team advises on operational matters, franchises, concessions, finance, regulatory, property, employment, environmental and procurement issues.
Disclaimer: This article is for informational purposes only and does not constitute legal advice. It is recommended that specific professional advice is sought before acting on any of the information given.
• Allowing the employee more rest breaks.
• Offering more flexibility to work from home.
• Temporarily reducing their hours.
• Providing additional support to an employee each day to help them manage their workload.
The Advisory, Conciliation and Arbitration Service (ACAS) issued new guidance and resources in April to help support employers when handling reasonable adjustments for mental health work, including practical steps and the considerations they should be aware of.
Important areas to consider include:
• Every job is different, so what works in one situation may not work in another.
• Every employee is different, so what works for one employee might not work for another.
• Mental health fluctuates over time, so what works now for an employee now may not work in the future.
ACAS encourages employers and employees to work together to agree and review reasonable adjustments over time to make sure that such adjustments continue to work well.
In 2017, the UK Government commissioned an independent review of the role employers can play to support employees better with mental health conditions in the workplace. The final report ‘Thriving at Work: The Stevenson / Farmer review of mental health and employers’ set out a framework of actions, called ‘Core Standards’, so that both employers and employees would have the knowledge, tools and confidence
The Devon & Cornwall Railcard has become the first regional railcard in the UK to go digital. Residents in Devon and Cornwall, aged 16 or over, can now purchase the railcard, download it to their phone and use it to save up to a 1/3 on standard class rail fares. It’s all
about making the journey experience smoother for Great Western Railway customers and is thanks to funding from the Devon and Cornwall Rail Partnership (DCRP), the Community Rail Partnership for the two counties.
to understand mental health issues and organisations, whatever their size, were equipped with the awareness and tools to provide relevant support.
Employers were recommended to:
• Produce, implement and communicate a mental health at work plan that promotes good mental health of all employees and outlines the support available for those who may need it.
• Develop mental health awareness among employees by making information, tools and support accessible.
• Encourage open conversations about mental health and the support available when employees are struggling during the recruitment process and at regular intervals throughout employment, and offer appropriate workplace adjustments to employees who require them.
• Provide employees with good working conditions and ensure they have a healthy work life balance and opportunities for development.
• Promote effective people management to ensure all employees have a regular conversation about their health and wellbeing with their line manager, supervisor or organisational leader and train and support line managers and supervisors in effective management practices.
• Routinely monitor employee mental health and wellbeing by understanding available data, talking to employees, and understanding risk factors.
Recent research from the Health and Safety Executive shows that, despite more employers stepping up their efforts in relation to mental health, half of employers still do not have a formal mental health and wellbeing strategy or policy in place. Such a strategy or policy is important and provides employees with a centralised document setting out information they may need to signpost them to mental health support. It can also help colleagues and managers to understand how they can help someone who is struggling.
A good policy should be tailored to the employer and include both employer and employee responsibilities, policy objectives, information on what assistance the employer can offer, as well as information on additional support and advice. However, simply having a strategy or policy which is not then implemented is no defence to a claim by an employee under the Equality Act 2010. Active engagement with all employees is a necessary action.
maintenance operations to be conducted without endangering the safety of staff or damaging infrastructure
It is:
• Fully configurable, flexible and functional
• Proven in use and installed globally
• Capable of interfacing with third party equipment including signalling systems.
• Adaptable to the safe requirements of the depot www.zonegreen.co.uk
Ellis Shelton, Policy Advisor, Logistics UK explains why it is imperative that rail adapts and implements new infrastructure to ensure the sector remains efficient and sustainable
Rail freight is an indispensable part of the logistics industry, boosting economic growth, reducing carbon emissions, and enhancing supply chain reliability within the UK. Rail freight also boosts road safety by reducing the number of Heavy Goods Vehicles (HGV) on the roads – use of rail removes an estimated seven million lorry journeys per year, therefore easing congestion and reducing journey times, as well as improved road safety statistics. Railways are particularly advantageous for the movement of heavy and bulk commodities and can transport larger volumes of goods in a single trip, each freight train able to carry the load of up to 76 HGVs, resulting in cost savings for businesses. However, there must be an increase for capacity on the rail network for freight to accommodate modal shift and support the sector. In addition, it is imperative that all opportunities to support rail freight are maximised by both government and industry as this will underpin potential future growth. Challenges such as track upgrades also need to be addressed ahead of time to reduce delays and further complications.
Transporting goods by rail can be more time and cost-effective than road depending on the cargo carried and if just-in-time deliveries are required. Government funded initiatives such as the Mode Shift Revenue Support (MSRS) scheme, which supports freight customers in moving their goods by rail, are crucial for allowing the sector to support industry in decarbonising and is a significant step forward in revitalising the
economy. Rail produces significantly lower emissions than other modes, with each tonne of freight transported creating 76 per cent fewer carbon emissions compared to road. Modern trains are often more energyefficient, as they emit fewer greenhouse gases and have lower carbon footprints compared to older rolling stock or other modes of transport. Increased investment in rail will enhance the national infrastructure network and encourage modal shift, leading to further reductions in greenhouse gas emissions which is crucial for mitigating air pollution and ensuring the UK meets its 2050 net zero deadline.
Rail freight offers businesses a greener, faster and more reliable alternative for transporting their goods, preventing 1.4 million tonnes of CO2 emissions being emitted annually. This enables companies to align their operations with sustainable supply chain practices more successfully. Use of rail services also improves urban air quality and enhances the liveability of cities and communities along busy transport corridors – using rail is a great way for logistics businesses to support their own corporate social responsibility initiatives while also benefitting the environment.
In prioritising modal shift from road to rail and improving rail infrastructure, such actions align with the United Nations’ Sustainable Development Goals (SDGs) – which promotes sustainable cities, responsible consumption and climate action. Rapid urbanisation has resulted in increased congestion within our cities, air pollution and strain on existing transportation systems, whilst the demand for efficient
Logistics UK is one of the UK’s leading business groups, representing logistics businesses which are vital to keeping the UK trading, and more than seven million people directly employed in the making, selling and moving of goods. With Covid-19, Brexit, new technology and other disruptive forces driving change in the way goods move across borders and through the supply chain, logistics has never been more important to UK plc. Logistics UK supports, shapes and stands up for safe and efficient logistics, and is the only business group which represents the whole industry, with members from the road, rail, sea and air industries, as well as the buyers of freight services such as retailers and manufacturers whose businesses depend on the efficient movement of goods. For more information about the organisation and its work, including its ground-breaking research into the impacts of Covid-19 on the whole supply chain, please visit logistics.org.uk.
transportation of goods has increased substantially. In not only creating capacity on the network but electrifying its existing lines, the rail sector can reduce its carbon emissions dramatically, enabling the integration of renewable energy sources and the development of efficient electric train systems and advanced energy storage solutions. Research shows that only 800 miles of additional electrification is needed in the UK to enable 95 per cent of rail freight to be electrically hauled, and so Logistics UK is calling on government to implement plans for electrifying the network without delay.
To ensure the rail sector remains efficient, government must also invest in modernising the current infrastructure as this will support just-in-time deliveries and reduce inventory holding costs for businesses. Improved rail networks will generate employment opportunities such as construction, engineering, logistics and other related sectors but also foster economic activity by attracting new businesses, encouraging investment and promoting regional development. Increased efficiency in rail infrastructure will help facilitate trade and commerce by enabling smooth movement of goods across the country: this in turn will improve productivity, competitiveness and end user satisfaction, supporting both domestic and international trade.
Achieving a robust rail freight network will provide exporters with reliable and cost-effective transportation options,
Industry partners in the transformational East Coast Digital Programme (ECDP) have signed a £32.7 million contract to upgrade the Class 700 Thameslink fleet to the latest specification of European Train Control System (ETCS). The fiveyear contract was signed by Cross London Trains, DfT, Govia Thameslink Railway, Network Rail and Siemens Mobility.
The 115-strong Thameslink fleet is the largest passenger fleet in a programme designed to replace conventional signals at the side of the track with state-of-the-art digital signalling – providing continuous, real-time information to the driver’s cab. The technology will mean more reliable and greener services for passengers and freight, creating the next generation railway.
enabling them to remain competitive across global markets. Well-designed rail networks bypass congested areas and traffic-prone routes, ensuring faster transit times and allow for the efficient movement of goods from manufacturing centres to ports and international gateways, further strengthening export competitiveness.
Modernising the railways will involve embracing technological advancements, such as digitalisation, Internet of Things (IoT) and Artificial Intelligence (AI). These technologies will enable real-time monitoring, predictive maintenance and data-driven decision-making, leading to a better service quality. Embracing innovation in rail systems ensures they remain competitive, adaptable to future needs and integrated with emerging smart transportation networks.
Logistics UK is urging government to invest in the rail sector as improved infrastructure ensures the long-term viability and resilience of the transport network which will support the highly anticipated growth in freight demand as the country continues to recover from Covid-19. Making this investment for rail freight will ensure that the network is fully prepared to handle larger cargo volumes and will help to
and technologies, therefore future proofing the transport system. Further benefits for the industry include seamless integration between other modes of transport including road, maritime shipping and air. Facilitating this connection is crucial for the UK’s economy as it ensures further trading but also optimises the use of all different modes of transport. Intermodal connectivity significantly strengthens supply chain efficiency and enables better multimodal transportation solutions, including
Over the past 20 years Gall Zeidler Consultants has completed 550km of tunnelling projects across the globe, establishing our position as a world-leader in tunnel design and consultancy services.
Our specialists relish a challenge and always deliver – it’s why we’re a leader in innovative underground solutions, geotechnical engineering, bespoke tunnel design, tunnel rehabilitation, and project/construction management.
Elevated thinking, underground
‘Rail freight offers businesses a greener, faster and more reliable alternative for transporting their goods, preventing 1.4 million tonnes of CO2 emissions being emitted annually.’
The advent of the digital station ushers in many new applications with network requirements that exceed current station LAN capabilities. With recently released Department of Transport figures showing that in February, passenger levels on the UK national rail network hit 100 per cent or more of pre-pandemic levels, it’s clear people are getting back to their travel routines. These figures reflect a doubling of passenger numbers in little over a year. But it’s no surprise. As mobility needs increase, rail travel provides a sustainable option for both business and consumer travel around the country.
The passenger journey may begin and end at the station, but these bustling hubs perform a greater purpose for those that pass through them. They serve as a meeting place, offer a chance for travellers to rest or enjoy a meal before continuing their journey, or catch up on e-mails. With passenger information systems and public announcements at the station, passengers can access the very latest information to manage their journeys.
As passenger traffic continues to grow, rail operators will need to deploy more services to support them. More CCTV cameras will offer greater situational awareness for passenger and staff safety, high-coverage Wi-Fi connectivity will be needed to meet growing data needs and more predictable, secure and reliable operations will facilitate the smooth flow of passengers. This highly connected environment is being coined the ‘digital station.’
Rail operators that currently rely on enterprise local area network (LAN) communications networks offering one gigabit per second (Gbps) speeds for their
enterprise and voice and data needs, will find they won’t cut it as they evolve their services. The digital station network will have to connect to more Wi-Fi access points and high-resolution CCTV cameras.
It will also need to connect new capabilities such as remote health monitoring of equipment using, for example, supervisory control and data acquisition (SCADA) and Internet of Things (IoT) systems. This will allow rail operators to gain visibility of potential failures in heating, ventilation and air conditioning (HVAC) systems, escalators and other equipment, and support more sustainable predictive and preventative maintenance activities that prolong equipment life.
While exact network needs will vary by station size, rail operators should reimagine their network with resiliency, security and flexibility in mind. This will allow them to benefit from network scaling to manage service demand as it continues to rise, as well as the integration of new digital technologies and capabilities as they are introduced to continue enhancing the customer experience.
The current Ethernet LAN network architecture should be replaced by highperformance, secure, resilient 10Gbps access Ethernet fibre rings. Comprised of many industrialised high fan-out Ethernet switches, these rings serve the communication needs of a plethora of station equipment. In addition, with high wattage power over Ethernet (PoE) technologies capabilities, industrialised Ethernet switches can also act as a power source, avoiding separate power cabling.
The Ethernet ring networks will collect data from all connected equipment including CCTV cameras, Wi-Fi access points, SCADA systems, ticketing, passenger display systems and other data points. Then they will
aggregate that data in dedicated Ethernet services toward the backbone core network which transports it on to operations and control (OCCs) and data centres. IP/MPLS is the proven and prevalent core backbone network technology because of its ability to run multiple application types, including legacy and new services and apply quality of service levels to prioritise traffic, in support of mission-critical communications needs such as signalling, SCADA and CCTV.
There can be no tolerance for network downtime in rail communications, and within this resilient, secure end-to-end network architecture, system redundancy can be enabled through the deployment of two station gateway network nodes, with the first connected to the main backbone core network and a second to a backup core. If there are any failures on the primary network, the backup provides continuity, ensuring that passenger and operational services at the station are unaffected.
Using this blueprint, rail network operators can scale networks to meet demands dictated by the station size and levels of passenger traffic, opting for a multiring architecture that supports a greater number of Ethernet switches at large, busy stations. And, by implementing a ten gigabit Ethernet access network, they’ll also have room to support new digital services in the future.
As more trains are introduced on the tracks, and their speeds increase, more rail operators are leveraging global standardsbased private 4G/LTE and 5G wireless networks for enhanced train-to-ground communications. These networks allow the implementation of automated train operations for precision control and greater adherence to scheduling.
With this new private wireless network in place, rail operators can deploy small cells in the station for more station network access options. While stations may not need the highest level of mission-critical control that is required along the tracks, small cells can support more sensors as they are introduced to measure environmental conditions and equipment health, as well as group communications such as push-to-video. The station network can play the critical role of backhaul for this private network.
It’s clear that rail operators today have an important decision to make. The growth in passenger numbers may pose major challenges for them today, but digital stations will be crucial in helping them overcome those challenges. Working with trusted network suppliers, they can reimagine their station network blueprint and introduce the resiliency, scalability and security required to support digital station applications today and into the future. In doing so, they can accelerate their digital transformation and enable new operational capabilities to effectively support growing passenger numbers for a greener society, while also enhancing the customer experience.
Hansen Chan, IP Product Marketing Manager at Nokia on why operators need to reimagine their station networks to meet the expanding needs of passengers and operations
On 21 June 2023, companies representing the UK’s rail industry came together at Newark Showground to participate in the seventh annual Big Rail Diversity Challenge
First held in 2016, The Big Rail Diversity Challenge has truly captured the hearts and minds of the industry – demonstrating the passion, support and enthusiasm for the brilliant work that Women in Rail undertakes. Growing by a staggering 80 per cent since its launch, The Big Rail Diversity Challenge has become a staple in the industry’s event calendar, with many key industry stakeholders supporting it year-on-year.
As one of charity Women in Rail’s annual flagship events, The Big Rail Diversity Challenge is the only team-based rail event showcasing the diversity the UK railway industry is seeking to achieve. The challenges are designed to promote the message that diverse teams work better together, with companies taking part in a series of physical, mental and skill-based sessions including; Catwalk Challenge, The Great Diversity Bake Off, Human Table Football, Shelter Building, the Mighty Quiz and Dancing with the Shows!. Designed to put a team's communication and teamwork skills to the test, the challenges are developed to ensure that everyone has a role to play.
Shona Clive, Vice Chair of Women in Rail said: ‘This is the eighth year of The Big Rail Diversity Challenge and the largest to date. It’s one of our key events in the Women in Rail calendar and is a dynamic, fun-filled
day with gender balanced and diverse teams participating, networking and competing with peers across the sector.
‘The event highlights an important message that diversity is good for people, good for business and good for the rail industry and raises the profile of EDI and the rail sector’s commitment to improving diversity within its workforce and fostering an inclusive culture. Thank you to everyone who took part.’
The event is supported by many key industry bodies, organisations and charities; The British Transport Police returned for a fourth year to deliver the ‘Lines of Duty’ challenge – designed to support a cross industry campaign which encourages officers and rail staff to use their professional curiosity in order to safeguard people they may encounter on the rail network.
The Railway Benefit Fund had participants supporting one another through the toughest of times, blindfolded and carrying ‘beans’ through an inflatable obstacle course as part of their ‘Bring on the Beans’ challenge, whilst the Railway Children charity had teams constructing a one-person shelter using basic materials that could be available to a child living on the streets.
After a tiring day of learning the Haka, Broadway routines, and countless inflatables, awards were presented.
For more information about WR visit https://womeninrail.org/.
The 'Best Team Name Award' went to Alstom for ‘Lock, Rolling Stock and Smoking Barrel’, presented by Simon Parkin, Operations Manager of McCulloch Group, representing our 2023 Fundraising Sponsors. The British Transport Police ‘Lines of Duty Award’, judged and presented by Mark Lawrie, Superintendent: Special Constabulary with the British Transport Police, was won by ‘CRSA - Systems’ from Central Rail Systems Alliance. For creating the best shelter – and showing the best teamwork on the Railway Children ‘Shelter Building’ Challenge, Cat Howourth, Event Manager for Railway Children presented the ‘Shelter Building Award’ to ‘Railhouse Rock’ from Atkins ECP. The Railway Benefit Fund's ‘Bring on the Beans Award’ was presented to ‘The Determinators’ of LNER by the charity’s Fundraising Manager, Suzy Powell, for showing the ability to laugh at the toughest times, whilst still achieving their goal.
‘The Most Collaborative Teamwork Award' was judged on the team performance across two of the event’s favourite challenges – It’s a Knockout and Walk the Plank. The winner was Porterbrook for displaying outstanding teamwork and motivational support. And finally, the most coveted trophy of the day 'The Team of the Year Award' for achieving the highest overall score with an impressive 243 out of a possible 260, went to ‘Team Frauscher’ from Frauscher. The 2023 winner's trophy was presented by Abigail Hancock, Head of Environment and Sustainability of Linbrooke Services and Women in Rail Yorkshire Steering Committee Member.
On the day, there was also a Charity Tuck Shop and a Hamper Raffle which helped raise over £800.00 for the Women in Rail Charity. The official images from the event will be available to view shortly on The Big Rail Diversity Challenge website. A big thank you to all the teams attending. If your company would like to join The Big Rail Diversity Challenge 2024 please contact Nimble Media to secure your place.
Add 19 June 2024 to your diary and we hope to see you at #BigRail2024!
The Rail Ombudsman opened its doors on 26 November 2018, offering expert, alternative dispute resolution (ADR) service to help sort out unresolved customer complaints about service providers within the rail industry. Our service is free for consumers to use
Our vision is to inspire customer confidence and to deliver our service fairly to ensure the evidence is appropriately considered in every case. We also support the rail industry to raise standards. Importantly, from a service improvement perspective, we publish case studies and data and make recommendations which can help Rail Service Providers to understand what they could do to raise standards.
The rail industry can be complicated for consumers to navigate with several key players and stakeholders, such that it was considered that a ‘one-stop’ shop for consumers to bring their complaints would simplify matters and make access to fair remedies easier for consumers.
This means that consumers can bring any complaint to us and this forms part of our feedback to the industry. However, we do operate within a defined scope and if we are unable to look at a particular dispute, we give reasons to the consumer and let them know where to go next. We can transfer their claim to one of the passenger
watchdogs, such as Transport Focus or London TravelWatch, or, in some instances, the claim might be better suited to the courts or other channels and we signpost the consumer if this is the case.
Also, for people using multi-modal arrangements, our collaboration with other organisations such as BusUsers, which provides ADR in that sector, becomes even more important.
Our role is to investigate the quality of service provided to the consumer based on the commitments a rail service provider has made in the National Rail Conditions of Travel and their Passenger Charters.
Examples of this include: customer service; provision of information; losses arising out of train delays and cancellations; availability and access to station facilities including toilets, lifts, waiting rooms, parking, cycle storage, announcements, ticket sales, and lost property; on-train facilities, such as accessible toilets, catering and other advertised services. We can also investigate disputes arising out of passenger assistance, facilities for customers with
disabilities, and discrimination or issues arising under the Equality Act 2010. We cannot look into complaints to do with industry policies or regulations or how the railways are run. Similarly, strike action, how engineering works on a railway line affect a consumer’s home and staff disciplinary matters would all fall outside of our scope.
From 1 October 2016, the Consumer Rights Act 2015 was extended to cover rail travel which means that consumers have consistent rights where services are not carried out with reasonable care and skill. This means that consumers can claim damages, including out of pocket expenses, as a right. Information and the provision of this both prior to the ticket purchase and ongoing throughout the journey can also be a key consideration and forms the basis of many claims that are considered under the Consumer Rights Act 2015 by the Rail Ombudsman. For example, Strike Action: whilst, as referenced above, the Rail Ombudsman has no remit relating to the industrial action itself, we have worked through may scenarios that have arisen during periods of industrial action. There has been scope for award regarding, for example the provision of information during strikes and where first class was de-classified, we made an award for the difference between the first and standard class price of the tickets where the consumer did travel.
Broadly, we recognised that there are learnings for the rail industry, for example relating to the lack of information provided on booking confirmations which was raised as part of the evidence in some cases arising from industrial action. The Rail Ombudsman recommended that the industry considers the format for booking confirmations to consider if the check before travel requirement could be made more explicit, and where possible, if specific notifications could be included as standard, such as strike action warnings.
Some claims for additional or consequential losses were not considered by rail service providers because they arose during periods of industrial action. The Rail Ombudsman has therefore recommended that there must always be consideration of wider rights for example under the Consumer Rights Act 2015 and this includes the provision of information when purchasing and travelling.
Having said that, the outcome of a claim brought to the Rail Ombudsman may still vary since it will depend on the circumstances of each case and might be agreed between the parties at mediation. Decisions taken by an ombudsman at adjudication may include a refund, discount or an award including out of pocket losses or compensation for time and trouble. We may ask that the rail service provider gives an explanation, apology or a gesture of
A plan to deliver new transport links, homes and regeneration in Thamesmead and Beckton Riverside has moved a step closer with Transport for London (TfL) and its partners submitting a Strategic Outline Case (SOC) to Government. The business case outlines how an extension of the DLR could have a transformative effect on the area. Thamesmead and Beckton Riverside sit at the heart of the London’s major growth areas and are a priority for regeneration and economic development. The Mayor of London outlined his support for the east London project in his Transport Strategy.
goodwill which could be complimentary travel or a gift.
We publish case studies which give some greater insight into the types of claims and how we approach these – www. railombudsman.org/resource-area/faq-3/ case-studies
In all cases, we consider the evidence provided and listen to the accounts of both parties. We have made awards to consumers and made recommendations to the sector to improve the consumer experience, both whilst travelling and whilst navigating the complaints processes and seeking redress. These recommendations can be made to the individual rail service provider and also to the industry more broadly, for example, recognising the potential information gap, and possible implications of this, the Rail Ombudsman, through collaboration with industry and other stakeholders, provided recommendations via its Young Person’s Train Guide (http://bit.ly/3IPMN9a) a resource pack aimed at explaining and simplifying the complex rail sector by-laws to young, potential vulnerable rail users. Recognising a knowledge and understanding gap via its casework, the Rail Ombudsman was able to target this resource at a specific
group of passengers whilst also raising awareness of the issues in the sector more widely.
The Rail Ombudsman has a broader remit than the individual decision, but it is from each individual’s voice that we learn and provide feedback to enable the industry to continuously improve. It remains crucial, therefore, that an independent Ombudsman is available to not only listen to each dispute and impartially assess it, but also that people’s voices are heard and their recommendations for improvements are taken on board.
www.vendigital.com
As the industry prepares for the launch of Great British Railways (GBR), decision makers across the sector believe there is a significant opportunity to improve operational efficiency, reduce cost and improve passenger services by adopting a more integrated approach to operational management.
With the prospect that draft legislation could be included in the King’s Speech later this year, plans to proceed with GBR are firmly on the Government’s agenda. Both Network Rail and train operating companies (TOC) view the transition to GBR as an opportunity to transform operational efficiency by managing capital projects, as well as infrastructure improvements and maintenance works, more efficiently and effectively. But how will it work in practice?
Currently, every time track maintenance work is needed, Network Rail has to take possession of the affected route, often for several hours. The time slot for the works has to be agreed with the TOC, taking account of the current timetable of passenger services and freight pathways. Depending on the urgency of the proposed works, it might be possible to select a slot when there are no passenger services... However, if this isn’t possible and some disruption is caused, Network Rail is required to pay the operator a fee to reflect any loss in associated revenues. Naturally, some routes are more profitable than others, and the period of possession might be longer in some cases than others. These and other factors can affect the possession fees payable.
With the current operating system, under utilisation of data means Network Rail is missing out on opportunities to plan routine track maintenance or other improvement works more efficiently. Under GBR, operator intelligence could play a significant role in improving efficiency. For example, TOCs could provide real-time video data to GBR from cameras inside driver cabs, to highlight any potential issues such as infrastructure damage, graffiti or encroaching vegetation along their routes. Much of this data exists already, but a lack of integration has left it largely unused.
In some cases, under utilisation of data could be causing Network Rail to make the wrong decisions. For example, Network Rail may be seeking to protect rail freight services as far as possible in order to increase freight volume. However, freight pathways are not always used – and Network Rail has no way of knowing this in advance. Equally, planned works expected to take eight hours, might only take four, which means other repairs could have been scheduled for the same slot. Instead, in this scenario, Network Rail would be forced to go ahead with taking possession of the same route on a separate occasion, disrupting passenger services again unnecessarily.
As a new public body that will own infrastructure and be responsible for operating services, fixing fares and earning revenues, GBR will have greater visibility of the rail network as a whole. This should enable a more joined up approach to planning and all aspects of operational management. For example, where routes or sections of track lack overhead lines,
electric-only rolling stock can’t currently be used. Aligning track and train will empower GBR to take a whole-system view that considers the capital infrastructure projects required to decarbonise the railway, the current rolling stock portfolio, the requirement for new trains and balance this capacity with the demand of customers. In this way, GBR would be fulfilling its objective as a ‘guiding mind’, making well-informed, strategic decisions that are designed to protect profitability, while directing investment to areas where the commercial benefits are greater.
Taking on responsibility for overseeing infrastructure and operations is not without risk for GBR of course. Whereas TOCs shoulder responsibility for the fare box and ticketing under the current structure, this would no longer be part of their remit, and once GBR is in place, they will simply be required to focus on delivering a good passenger experience. Instead, GBR will take on this area of responsibility, although it is expected to retain some reliance on local operator knowledge.
Developing the role of data further, AI-powered systems could be trained using information from past and present projects to predict the most likely outcomes and assess the cost-value benefit of future projects as accurately as possible. This could help GBR to further improve operational efficiency by making betterinformed decisions about whether a specific maintenance or improvement project should go ahead and if so, how to go about it. For example, if a section of track has minor repair requirements, and categorised as low risk, is it worth taking possession of the route to carry out repairs that will only deliver a small efficiency gain? Or is it better to wait until the next maintenance review?
In another application of AI and machine learning, bespoke algorithms could be developed to support decision-making processes. For example, an AI-powered system could be trained to predict the impact that a specific decision could have on certain passenger groups as well as its knock-on effect on the route’s profitability in the short, medium and long term. This could inform strategic decisions about whether to limit maintenance work to one day a week for a period of three months, or close the route entirely for a period of two weeks.
With GBR on the way and some structural preparations already in place, it is important that industry leaders don’t lose sight of the opportunity to make bold decisions and harness the decisionmaking power of AI and rich industry data to transform Britain’s rail network for the benefit of everyone.
Approved Hydraulics have been supplying some of the largest rail build and maintenance firms for over 10 years, now considered some of the best in the world!
Rail Forum is excited to announce the final line-up for TOCTalk Live, with 14 confirmed table hosts consisting of 11 Train Operating Companies (TOCs), two Owning Groups and Great British Railways Transition Team
This new supplier engagement event, taking place on 6 July 2023, presents an unrivalled opportunity for the supply chain to understand what is happening within the TOC environment and how they can support them, by speaking directly to those that are at the cutting edge of National Rail Contracts (NRCs).
Anyone with an interest in understanding how the NRCs are impacting future activities and how to prepare your organisational offer to support should attend. Our table hosts are keen to support early engagement with the supply chain to fit with business planning processes.
Rail Forum is also delighted to introduce our TOCTalk event partner, DeSimone. The support of event partners enables Rail Forum to deliver high quality events which remain free for members, and in the case of TOCTalk, wider industry too.
Stuart Bosley, Managing Director of DeSimone said: ‘DeSimone, an exclusive supporter of TOCTalk Live, brings decades of experience as New York-based structural engineers since 1969. Our expertise and commitment to excellence enable us to
deliver comprehensive program advisory services, including pre-contract to final account, dispute avoidance, and alternative dispute resolution, including international arbitration. With a proven track record, we are proud to contribute to the industry's innovation and success at TOCTalk Live.’
In advance of TOCTalk, Rail Forum is also pleased to be running a NRC online briefing webinar with East Midlands Railway (EMR). This session will provide suppliers with an overview of how NRCs work, an insight into the business planning process and what this means for the supply chain, as well as how to engage with EMR on some future opportunities.
EMR speakers include Will Rogers –Managing Director and Joanne Etchells – Head of Procurement, plus guest speakers from Transport UK and Greater Anglia. We encourage TOCTalk attendees to tune into this online session on Wednesday 14 June between 12:30 – 14:00. This webinar is open to all and free to attend, there are no restrictions on attendee numbers. Book here.
TOCTalk Live will take place between 13:00 – 14:30 on Thursday 6 July 2023 in a dedicated space within the Rolling Stock Networking (RSN) event in Derby.
Delegates must register for both TOCTalk Live and as a visitor to RSN. Tickets are free and any UK company may register for a place, however, spaces are strictly limited to one per company/group and will be prioritised to Rail Forum members and/or RSN Exhibitors.
‘We are delighted to introduce TOCTalk to our events calendar. Modelling the successful and popular InfraTalk format, with no presentations, no PowerPoints and no applications, TOCTalk Live offers barrier free and fast networking; allowing attendees to quickly engage with senior representation from across a range of TOCs.’
Cat Appleby Membership Manager at Rail Forum
More flooding, more drought, more extreme weather conditions: our future is fraught with climatic risks.
Planning is becoming harder - and yet there is growing pressure from investors, stakeholders and citizens to deliver a positive impact on our environment, our ecology and our places. To meet the scale of the challenge, we need to change. The environment used to be a barrier that got in the way of development. Proposals would be submitted, surveys and impact assessments carried out, and breaths held that the results wouldn’t hold up the project or send the designs back for rework.
That’s no longer sufficient. We recognise that nature, people and communities need to be at the heart of decision-making, and at the front-end of planning. We face a daunting range of interconnected challenges – our solutions cannot simply reduce carbon emissions, but build thriving communities, empower inclusive growth and champion biodiversity net gain. Only by creating truly holistic solutions can we build infrastructure fit for the future. Thankfully, that reality is being recognised.
Investment is increasingly tied to the much-needed task of regional rebalancing, developing the transport and employment foundations for long-lasting, sustainable growth. Stakeholders now expect data, insight and answers to the most pressing questions of our time. And investors want clear business cases that show an understanding and mitigation of risk. But delivering a nature-positive status quo is complex.
As part of the Environment Practice’s renewed approach we’ve developed five new service lines. These are broader market services owned by the practice, comprising a mix of underpinning technical disciplines. Service lines are created in order to draw skills and expertise from across the Environment Practice and the wider Atkins business, which reflect the challenges/ opportunities of our clients, for the infrastructure sector, and for society.
What this means in practice is that we are able to coordinate and develop our technical offer and go to market with a coherent and forward-looking client value proposition. The service lines are key to delivering growth across the business.
We have a number of different service lines across the business but have identified a number which we see as priorities that will catalyse growth. These are ‘golden threads’ that will connect the exceptional work of our Environment disciplines and reach into the wider business.
The new Service Line Director roles are aligned with the new challenges we face such as growing our infrastructure as a country, while at the same time achieving Net Zero goals, becoming nature positive, reducing our impact on the climate and delivering wider social value.
Five new service lines have been launched in response to the changing needs of our clients and will enable us to engage more directly with clients to bring communities and the environment to the heart of clients’ decision-making:
Nature Based Solutions will be led by Claire Neale as Service Line Director. Claire is an experienced environment professional with broad ranging skillset gained over 20 years' experience in the water industry and environment sector. She has worked in government, regulator, private sector, consulting, water utilities and in large crosssector collaborations. She is focused on delivering outcomes for a more sustainable future, with enhanced natural and social value, connecting communities and improving liveability. She joins Atkins from Southern Water.
Valuing a Sustainable Future is led by Dr Philippa Ross. This service line focuses on supporting our clients to make better, more sustainable decisions by measuring and acting on environmental and social impact and value. It will harness the fantastic skills and expertise from across Environment in areas such as non-financial disclosures, sustainability reporting, multi-capitals, economics, decisional making frameworks and many other disciplines and shape them into focused client value propositions. Dr Ross has a doctorate in sustainability and resilience and brings nearly 20 years’ experience working in multidisciplinary teams with governments and development banks.
Planning and Consenting is led by Dr Andrew Jones as Senior Service Line Director. Andrew is an established business leader in the built environment sector, with 30 years’ experience in urban planning, mixed-use regeneration, global events, and sustainable place strategies, building awardwinning design, town planning and economic development teams.
Carbon Advisory is led by Paul Taylor as Service Line Director, a Technical Director with 32 years consultancy experience and a background in GHG emissions his recent focus is on embodied carbon reduction opportunities in linear infrastructure for major clients. This has led to the creation of carbon resources, carbon processes and carbon value propositions that have already been successfully used and reused in projects.
Sustainability and Climate Resilience Service line lead position to be confirmed. This service line will drive environmentallyled design by embedding sustainability and environment into all our engineering designs. This will ensure our design solutions maximise the opportunity to leverage nature, net zero and community benefits from the outset.
The rail industry is a great example of where we have brought our environmental teams in early in the process to steer design to minimise environmental and social risk and realise opportunity – including an assessment project with one of our key clients on plans for a new rail link.
By using our state of the art Pangea approach that combines processes, digital technology, information management and different behaviours applied throughout delivery we provided an environmental sustainability comparative assessment of the five proposed route options, to inform the selection of a preferred route option and the alignment development process.
Our Pangea tool enabled us to manage, analyse, visually interrogate and display design and environmental baseline datasets together.
We also performed geospatial analysis identifying environmental assets affected, providing a quantum for comparison between options. And we were able to generate a 3D model visualising the vertical and horizontal alignment, to assist with defining the zone of influence and clash detection.
The successful digital application created design and environmental objective-specific databases, including topography, routes and criteria scores, with geospatial analysis providing a quantum for comparison between options.
This approach enabled us to explore environmental opportunities before the alignment was finalised so that design choices could drive enhancement of the environment, rather than simply limit impact reduction through compensation and mitigation.
The result was a number of benefits for the environment including:
• Direct loss avoided of ancient woodlands, Local Nature Reserves, Scheduled Monuments and buildings.
• 60 per cent area reduction in Registered Parks and Gardens affected by track development.
• 73 per cent area reduction in Country Wildlife Sites affected by track development.
This is just one example of how we can support our clients in delivering environment-led design solutions, drawing on expertise from across our business practices. This ensures clients achieve their project aims without costly hold ups, while reducing impact on the environment, which is at the heart of our renewed approach to environmental services.
Dr Vicky Hutchinson is Atkins Environment Practice Director for the UK and Europe. She leads the development of service lines to help define best practice for collaboration between the likes of Atkins’ environmental science, ecology, noise, land quality and water specialists. She will also be responsible for driving industry engagement, to ensure that industry experts are given a platform to debate and advise on the journey to a low carbon economy.
June marked another exciting milestone in Edinburgh Trams’ nine-year history as the award-winning network opened a new £200 million line, providing a further boost for businesses and local communities across the city
Construction of the 2.9-mile Trams to Newhaven project got underway in November 2019 and was delivered on time and on budget, with the first passenger services leaving the new Picardy Place stop in the city centre on 7 June.
Now serving a host of key destinations, including Leith, Ocean Terminal and Newhaven, the route opened within a few days of the ninth anniversary of the launch of the original 8.7-mile, 16-stop line
between Edinburgh Airport and the city centre that has undoubtedly proved popular with both local residents and visitors.
Prior to the Covid-19 pandemic, Edinburgh Trams enjoyed year-on-year growth, with annual patronage levels peaking at around 7.5 million per year. Since then it has worked hard to remind people of the benefits of tram travel, resulting in an impressive post-pandemic recovery.
A commitment to delivering operational excellence and outstanding customer service
has netted Edinburgh Trams a host of local, national and international awards. Now, tens of thousands of new customers will benefit from the expansion of the transport system into the most densely populated part of the city.
Managing Director, Lea Harrison, explained: ‘In less than a decade the network has become hugely popular, both with the local communities we serve, and the millions of visitors Edinburgh attracts each year. This success laid the foundations on which
decisions to continue the line to Newhaven could be taken with confidence.
Thanks to the strength of our operational team, we have consistently met our targets and often exceed them, even during the pandemic when we continued to run 99 per cent of scheduled services.
‘In fact, every one of our employees can be proud of the part they have played in the Edinburgh Trams’ story to date and, looking forward, we’re excited to be welcoming even more customers on board following the introduction of convenient transport services to the vibrant communities along the new route.
By providing a rapid and reliable link between some of Edinburgh’s most densely populated neighbourhoods and the city centre, we aim to help those communities unlock their full potential and provide a real boost for local businesses.’
Of course, the Trams to Newhaven project has not been completed without overcoming significant challenges, not least the global health crisis. The response of the Edinburgh Trams team, heralded by industry commentators, was to redouble its efforts to maintain a reliable and robust service for customers who still needed to travel.
Thanks to the team’s flexibility and the ‘can do’ attitude of managers and front-line employees the response to the crisis once again demonstrates the value of the tram system to the city. Now, the network is on track to repeat the near-perfect customer satisfaction scores it recorded in prepandemic surveys.
Since Covid restrictions were lifted the tram system has further boosted its popularity by doubling down on its support for major sporting and cultural events in the city, embarking on a series of initiatives that improve convenience and offer added value for money to passengers while cementing long-standing partnerships with some of the capital’s world-famous visitor attractions.
Increasing the number of trams running at key times during major events avoids congestion and delays, improving
the passenger experience. The network routinely boosts services during the festival season, and to simplify travel for rugby fans heading to and from the Six Nations and Autumn Internationals in 2022, service frequency was boosted to every three minutes before and after key games. Most recently, Edinburgh Trams set a new record of more than 100,000 customer journeys over two days by putting on extra trams for the Harry Styles concerts at the BT Murrayfield Stadium.
George Lowder, Chief Executive of Transport for Edinburgh, credits the ongoing success of the network to solid foundations laid down over several years.
‘Undeniably, Edinburgh’s light rail system is a huge hit with locals and visitors alike, and its popularity certainly strengthened the case for light rail as a viable way means to further improving the city’s excellent transport links. The tramway has already delivered huge benefits for the city, and its achievements over the years are directly attributable to the hard work and commitment of the entire Edinburgh Trams team’ he explained.
‘With the opening of the new line we’re witnessing another major milestone for the tramway, but it also heralds a new era for our great city. Even more communities are now able to access this reliable and environmentally friendly mode of public transport as Edinburgh works towards becoming a sustainable net-zero city.’
The successful launch follows the completion of a complex construction programme that has seen contractors, led by the Trams to Newhaven project team, overcome a series of unforeseen hurdles. As well as Covid-19 lockdowns, there were unexpected utilities diversions and a medieval graveyard was uncovered during preliminary groundworks.
Despite these challenges, core infrastructure works were completed within expected timeframes and history was made in March 2023 when the first tram in almost seven decades ran along Leith Walk. This
milestone signalled the start of a major testing and commissioning programme to fully integrate the new line, with its eight new tram stops, within the existing network.
Edinburgh Trams also needed to take on around 60 new drivers prior to the opening and, alongside a successful recruitment campaign, a state-of-the-art simulator at a purpose-built learning and development facility was deployed to put drivers through an intensive training and route familiarisation programme. Using the latest technology to train multiple candidates simultaneously was highly advantageous, reducing costs and driving operational efficiencies.
As the launch date drew near, testing increased in frequency and members of the public were offered the chance to find out how the expanded network will open up their travel options.
‘Whilst it was essential to conduct thorough safety and operational checks, we also had to avoid any negative impact on current services and manage the seamless integration of our expanded timetable’ Mr Harrison said.
‘This now sees trams running from every seven minutes, seven days a week between 6.00am and midnight along the entire line from Edinburgh Airport to Newhaven.’
The expansion of the system has also led to the creation of a further 40 jobs within the customer experience team. These staff, together with longer-serving colleagues, have been out and about at key locations providing information on the new services, as outlined by Marketing Manager, Jamie Swift: ‘As well as meeting potential customers face-to-face, we’ve been talking to local businesses to help them capitalise on the opportunities the new line offers.
‘We’re working with them to attract more visitors to the areas we’ll be serving, explaining how the tram is an ideal way for their employees to get to and from work, and playing our part in boosting investment opportunities for the future.
‘This information exercise was conducted alongside a vital campaign focussing on safety, which urged members of the public to stay alert when near the new tramway. This is particularly important in areas where pedestrians, cyclists and motorists may be sharing the roadways with trams for the first time.’
Mr Harrison added: ‘For us, the entire project has been about creating a more connected city, building on the tram’s undoubted success, and re-doubling our efforts to ensure the benefits extend to all the communities the new line serves.
‘The city’s light rail plans always had a vision and purpose, and we’re now bringing them to fruition with a clear commitment to taking the popularity of the tram to the next level. We’re confident the network can go from strength to strength and that Edinburgh Trams will have an increasingly important role to play in driving the city’s future prosperity.’
‘Thanks to the strength of our operational team, we have consistently met our targets and often exceed them, even during the pandemic when we continued to run 99 per cent of scheduled services.’
Lea Harrison, Managing Director of Edinburgh Trams’
If you’re looking to take the next step in your career, a CIRO academic course could be the perfect opportunity.
We offer Certificate, Diploma or Degree level courses in Railway Operations Management taught by industry experts and designed to equip you with the knowledge you need to elevate your career to that next level.
Get in touch with our academic team for more information, visit ciro.org, or come along to our virtual open evening for Q&A from CIRO students past and present.
We’re delighted to be hosting an online open evening on August 9th for those who are considering a CIRO academic qualification. Whether you have already registered your interest for this year’s intake, or are just curious about the possibilities, come along and speak to the team.
To register, email learning@railwayoperators.co.uk
Clearly, there has never been a better time to switch to solar. As off-grid, renewable lighting and power specialists, we are incredibly proud to be part of the solar revolution transforming the sustainability of the rail and infrastructure sectors, alongside the health and safety of its workers and local communities. It is encouraging to witness the significant strides that have been made towards a cleaner, greener rail sector, but the race is far from complete, with so much more for us all to do in every facet of modern-day business to achieve our 2050 net zero targets.
We are fully supportive of the rail industry’s commitments to reduce emissions. Working together with our rail partners, as leading manufacturers of sustainable solar lighting, solar hybrid power generators and solar CCTV systems, our specialist range of environmentally friendly products work hard every day on worksites across the rail sector, providing direct like-for-like replacements for diesel systems, making them a simple switch for companies looking to lower their carbon footprint.
With quiet, zero emission and hasslefree technology, all Prolectric products have been specifically designed to deliver increased worksite sustainability, safety and efficiency. The technology is tried, tested and proven to work all year round, in all weather conditions, and is backed by real world performance data and customer testimonials.
In 2019, Prolectric’s solar technology was used on a major rail renewal project at Llanwern, South Wales. The ambitious project led by Network Rail and Colas Rail Ltd used innovative solar lighting and power generation to prove the viability of a sustainable ‘Site of the Future’. The pioneering collaboration achieved a 97 per cent reduction in diesel use, saved 6,000 litres of fuel and more than 15 tonnes of CO2 during the 14-day initiative.
The results were a significant achievement marking an environmental milestone towards clean, carbon-free offgrid working, in support of Network Rail’s
CP6 target to reduce non-traction energy consumption by almost 20 per cent and carbon emissions by 25 per cent.
Prolectric’s clean, silent solar lighting and power generation technologies were used across the site covering more than 21 acres. This included access roads, car parking, welfare cabin and track working area.
With more than 70 rail staff employed on site, two 25kW Solatainer solar generators replaced conventional diesel generators providing light and heat for seven welfare cabins, including site offices, a canteen, toilets and a drying room.
A total of 21 Prolectric ProLight solar tower lights illuminated the site compound, car parking and work preparation areas, as well as being deployed on the trackside, where 200 metres of ProTrack batterypowered link lighting was also used. In
addition, Prolectric ProTemp column streetlights were positioned along the access road to the site.
The project was the first of its kind. Previously diesel generators were the only option to provide reliable off-grid power to support rail renewal work. The ‘Site of the Future’ project made a viable case for the use of solar technologies, which are now making a vital contribution to non-traction carbon targets, as well as reducing the noise, smell and air pollution from diesel exhausts. Staff and visitors to the Llanwern compound remarked on how quiet the worksite was, compared to the usual continual background hum of diesel generators.
The Llanwern ‘Site of the Future’ project was the culmination of determined development work driven by Network Rail and the Colas Rail team to adapt and refine
solar and renewable technologies for the rail industry, with an aspiration to achieve diesel-free operations as standard.
Central to the Prolectric solar power philosophy are the Prolectric Power and Lighting Portals, which offer unrivalled telematic software engineering to provide remote monitoring, control and reporting across our hybrid power and solar tower lighting range. The Prolectric Power and Lighting Portals are an industry gamechanger in remote device fleet management, enabling cutting-edge access to critical performance data of each unit, with customised real-time responsive control and alert functionality from any location.
By combining intelligent hardware, software, and GPS tracking, the Power Portal gathers over 400 pieces of telemetry data to provide a complete view of each unit’s operating condition, including fuel usage, solar generation and the battery’s state of charge.
Working in close collaboration with rail partners, Prolectric expects future advances in the design, function and versatility of solar and battery technology, with telematics driving forward the capabilities of off-grid solar light and power generation.
Prolectric is the off-grid, renewable lighting and power specialists. Leading manufacturers of sustainable solar lighting, solar hybrid power generators and solar CCTV systems – to the construction, national house building, infrastructure and rail industries.
The company’s game-changing solar technology provides a practical way for businesses to achieve their carbon-reduction commitments, enabling them to move away from polluting fossil fuelled or mains powered systems. Our solar tower lights, hybrid generators and CCTV provide high-performance site lighting, power and security – with minimal environmental impact and low running costs. In particular, our lighting systems produce zero carbon, zero noise, need little maintenance and require zero fuel.
A range of environmentally friendly, advanced performance products have been designed as direct like-for-like diesel replacements, making them a simple switch. The technology is tried and tested and proven to work all year round, in all weather conditions, over multiple winter and summer cycles. This is backed up by real world performance data and customer testimonials.
As a specialist sustainability disruptor, Prolectric was awarded a Queen’s Award for sustainable development in 2021 and holds a Gold CSR accreditation.
Prolectric’s pioneering solar and offgrid systems are designed, built and engineered by an expert in-house Research & Development team at the company’s Headquarters in Clevedon, Bristol. For further information visit: www.prolectric.co.uk
Rachel Preen is Managing Director of Prolectric, the off-grid, renewable lighting and power specialist, shares the company’s goal to help the rail industry to reduce its environmental impact with zero emission, hassle-free solar technology, specially designed to deliver increased worksite sustainability, safety and efficiency.
In addition to supplying individual components, the global companies of STAUFF and their authorised system partners use the STAUFF Line approach to support Original Equipment Manufacturers with the supply of custom-designed and ready-to-install fluid power lines from connection to connection and also provide supplemental services that create added value: · Components · Systems · Services · Contact
Sheffield Tel: 0114 251 8518
Email: sales@stauff.co.uk
Aberdeen Tel: 01224 786166
Email: sales@stauffscotland.co.uk
Ireland Tel: 02892 606900
Email: sales@stauffireland.com
Southampton Tel: 023 8069 8700
Email: sales@stauffsouthampton.co.uk
www.stauff.co.uk
When Porterbrook first acquired a rail site in Warwickshire, it’s fair to say that the decision raised a few eyebrows across the industry. It was certainly a departure from normal business for a ROSCO, but we saw an opportunity to create something that added unique value to the railway – today and for the future – as well as supporting our own ambitions and innovation to develop new traction technology. Now, two years down the line, our Long Marston Rail Innovation Centre is truly a facility for the benefit of the industry.
The 135-acre site has a rich history in supporting the rail industry. But its significance goes back to 1940 when the Ministry of Defence established it as the Royal Engineers Supply Depot – a place for storage and supplies during the Second World War. Towards the end of the War, some space was used for a German Prisoner of War camp and in 1948, these sections of the Depot were repurposed to house Polish Servicemen as part of a resettlement programme. While this accommodation closed in 1974, a chapel built for the local Polish community remained on site until the entire Depot closed in 1999.
Fast forward several decades and the former Royal Engineers Depot has been reimagined for a new purpose. Since June 2021, when Porterbrook acquired the site, £10 million has been invested to transform it into the Long Marston Rail Innovation Centre.
Work has been done to tarmac roads and improve access across the site while many of the buildings, including the Romney sheds, are undergoing renovations.
One of the recent upgrades to the site has been converting maintenance sheds that had fallen into a state of disrepair into a modern Asset Management Facility (AMF).
Opened in April this year, the £3 million facility, which includes three pitted roads that can accommodate up to a six-car set, is supporting customers with maintenance and upgrade work.
Respecting the site’s heritage is at the forefront of our minds when it comes to these investments and, where we can, we’re restoring the existing structures to their original state and making them fit for the future.
Accessible by rail via Honeybourne with lines to Oxford, Worcester and Birmingham, and close to the M40 for road deliveries, Long Marston is an ideal site for storage with space for around 700 vehicles. Another key feature of the site is its potential for industry training and testing. A recent example of this was in March when we hosted a major incident training exercise for Network Rail with over 300 people from industry and emergency services.
Innovation is central to the site’s purpose, with some of the most exciting projects in UK rail being led by our talented engineers and supply chain partners at Long Marston.
It was here where HydroFLEX, the UK’s first passenger-ready hydrogen train, was built and is being extensively tested. The train was showcased at the COP26 climate change summit in Glasgow in 2021, and
has recently reached speeds of over 80mph during mainline testing.
Alongside the development of cleaner traction technologies, we’re focused on reducing the carbon footprint of our own operations on site. We’re working towards ISO 14001 certification for Long Marston, like we have done with our Derby and London offices, and we’ve introduced electric pick-up trucks and are planning for battery-powered shunters to replace diesel vehicles. We’re also exploring how we can use solar energy for a variety of purpose around the site, including office buildings and warm storage.
To protect and enhance the site’s biodiversity we’re repurposing unused areas of land seeding wild meadows, planting new trees and working with Network Rail to support the Railways for Nature programme.
The community has always played an important role at Long Marston and that is something we want to continue to nurture. Much of our investment to date has been with local businesses and the site has been identified in Stratford-on-Avon and Warwick District Councils economic strategy.
We’re also working with local schools to create work experience opportunities on site for secondary school pupils. To support younger students, we’re proud to be partnering with the not-for-profit
charity Primary Engineer to deliver their Rail Project to ten schools in Warwickshire. This programme, in which our experienced engineers are mentors, is designed to encourage more young people to consider careers in STEM-related professions. It’s something we’ve done with schools local to our Derby office and so we’re thrilled to be bringing it to Long Marston too.
Looking to the future and our ambition is to support UK rail businesses to accelerate works in areas such as research, development and innovation to create a more reliable and sustainable railway.
To further increase the site’s benefits to the industry, we’re preparing to upgrade the track to make it suitable for low-speed dynamic testing and digital signalling, working with Network Rail to give new life to surplus track from the network. Power supply upgrades are also part of our future plans, which would open up Long Marston to testing of new EMUs as well as warm maintenance services to keep off-lease trains in prime condition.
At every step of the way, we want to ensure our investment in the Long Marston Rail Innovation Centre is not only for the benefit of the rail industry but also supporting the local community while respecting the site’s heritage and promoting sustainability.
Want to improve employee wellbeing but don’t know where to start? Every organisation we work with is unique ... we work with you to tailor effective and practical wellbeing solutions that you can implement today.
Business Partner Services
» Strategic wellbeing planning
» Practical support and advice
» Corporate event facilitation and speaking
» Lunch ’n’ Learn events
Training
» Mental Health First Aid
» Resilience and wellbeing programmes
» Non-technical skills for safety critical workers
» Train the trainer
Coaching
» Leadership teams
» Operational and project teams
» Individual wellbeing, life and executive coaching
“The resilience training course has helped me focus on my priorities, and on how to better manage work-life balance. Well recommended.”
Phil Court, Certification Director, AEGIS Certification Services Ltd.
When a prominent railway company encountered a daunting challenge of severe fuel contamination, SDM Fuel Solutions swiftly emerged as the trusted expert, equipped to deliver an effective solution.
This case study highlights how SDM Fuel Solutions’ prompt response and comprehensive solutions, driven by the dedication of their staff members, helped restore the railway operations and mitigate significant financial losses.
On 21/04/23, an on-site investigation was conducted, which led to the discovery of a significant problem at the depot where the trains and fuel tanks were located.
Shortly after receiving a call from the fleet manager at 4.30 PM on Friday night, the SDM Fuel Solutions team arrived on site within an hour. They conducted a thorough survey of both 100,000 litre tanks, which revealed extensive contamination at every level and significant external damage.
This critical information, along with SDM Fuel Solutions’ unique fuel analysis report, allowed them to rapidly communicate the severity of the issue. Throughout the weekend, they worked diligently to onboard the client and establish the necessary agreements for the next steps.
Unforeseen Spike: Sudden rise in FAME levels to 7%, impacting fuel and engine performance.
Train Disruptions: Delays due to particulate contamination and microbial growth.
Financial Impact: Substantial expenses.
Delays from Previous Provider: Two-week response delay from previous fuel service provider.
Engine & Filter Blockages: Contaminated fuel causing engines and filter blockages.
Persistent Contamination: Significant contamination despite regular refueling
SDM’s highly skilled engineers acted promptly, arriving on-site by Tuesday of the following week. They swiftly isolated the fuel tanks’ outlet and inlet, removing the top lid to extract all contaminated fuel. The manned entry tank clean (METC) was carried out through the opened side hatch.
Leveraging their expertise in fuel system management, SDM Fuel Solutions efficiently reinstated the side hatch, replaced gaskets, and removed isolations for re-delivery. The next morning, their dedicated tanker delivered pristine, clean fuel to tank 1. This process was repeated for the second tank, ensuring uninterrupted business operations.
Prompt on-site response, isolating fuel tank outlets and inlets.
Efficient removal of contaminated fuel through meticulous entry tank clean (METC).
Seamless reinstatement of side hatch, replacement of gaskets, and removal of isolations.
Timely delivery of clean fuel to both tanks, guaranteeing uninterrupted operations.
In summary, SDM Fuel Solutions swiftly responded to a severe fuel contamination issue faced by a prominent railway company. Through their comprehensive solutions and proactive actions, operations were restored, and significant financial losses were mitigated.
This successful case study exemplifies SDM’s commitment to excellence in fuel management, as demonstrated by their ability to promptly address the issue, communicate effectively, and deliver efficient solutions. SDM Fuel Solutions continues to be a reliable partner in providing effective and reliable fuel management services, ensuring uninterrupted operations for their clients.
In April 2022, government regulations regarding fuel underwent changes across numerous industries, placing a stronger emphasis on the adoption of alternative fuels such as HVO (Hydrotreated Vegetable Oil).
HVO is a renewable fuel that offers cleaner combustion and significantly reduces environmental impact. Red HVO retains the same fuel benefits while also providing a distinct advantage for select industries,
including the railway sector, through a rebate. A rebated product entails the government applying a duty rate of only 11.14ppl, as opposed to the full duty rate of 57.95ppl.
SDM Fuel Solutions specialises in assisting businesses in their transition to HVO. Our services are specifically tailored to each site and their individual requirements, ensuring
a seamless and trouble-free switch. With our expert support, businesses can embrace the benefits of HVO while minimizing any disruption during the transition period.
Renomesh anti-burrowing mesh is approved by Network Rail as a protective measure to mitigate burrowing by small mammals such as rabbits, badgers and beavers which have the potential to undermine geotechnical assets such as rail embankments through a system of burrows and tunnels. This can lead to increased instability in the embankment, especially if surface water can then penetrate the slope, which can ultimately lead to catastrophic failure of the rail asset.
Renomesh anti-burrowing mesh is applied to the slope face of the embankment and the small aperture size of the mesh deters mammals from digging into the embankment by preventing access to the embankment soil in a humane and sustainable way. The tough double-twist steel wire mesh is highly resistant to gnawing, it is made from class A Zn-Al5% galvanised wire and additionally coated for long-term durability with an advanced polymer coating called Polimac, which is highly resistant to abrasion whilst also being totally inert and harmless if the animals attempt to gnaw on it. The Polimac coated mesh is BBA certified with a design life in excess of 120 years.
Renomesh anti-burrowing mesh can be supplied in an open mesh configuration for use on vegetated slopes, or with an integral permanent erosion protection mat to retain soil particles and reinforce new root structures where slopes are to be revegetated. Unlike chain link style meshes, the strong mechanical connection of the
double twist woven mesh enables Renomesh anti-burrowing mesh to be locally cut to accommodate established trees and shrubs, without compromising performance or durability.
Steelgrid® HR is a high-performance composite rockfall protection drapery mesh combining double twist rockfall netting with high tensile wire ropes to create a mesh with high tensile strength and high resistance to punching whilst at the same time having extremely low elongation properties under load. It can be used for both simple drapery and stabilised drapery rockfall protection systems as well as a facing mesh to soil nailing applications. Both the double twist mesh and the integral high tensile wire ropes are made from class A Zn-Al five per cent wire which can additionally be coated with advanced polymer coating called Polimac. Steelgrid® HR is BBA certified and the Polimac coated mesh will provide a design life in excess of 120 years.
Where the rock slope has a need for erosion protection to prevent the loss of surface soil and vegetation, or to mitigate smaller falling debris from impacting the protected infrastructure Maccaferri can supply Macmat® HS. Macmat® HS is an erosion protection composite high tensile mesh combining the technical performance of Steelgrid® HR with an integral erosion protection mat consisting of a 3D matrix of polymer fibres. The integral 3D polymer matrix acts to both prevent loss of soil and small debris from the slope whilst also reinforcing new vegetation root structures. Macmat® HS is BBA certified and will
provide a design life in excess of 120 years where Polimac coating is applied to the wire mesh.
In recent years Renomesh anti-burrowing mesh has been used extensively on the East-West Rail project, with over 90,000m2 being used in 2021 to protect the rail embankments from burrowing. In 2022 Renomesh anti-burrowing mesh was used on the Bransford Rail Embankment in Worcestershire, where over 3,000m2 was applied to the embankment slope directly below the rail line to provide protection to a slope that was at risk of burrowing by rabbits.
Steelgrid® HR has been widely used for a number of years on the rail network. In the summer of 2022, 27,000m2 Steelgrid® HR30 was installed to rock slopes along the Severn Estuary Line between Lydney and Gloucester as part of Network Rail’s Severn Estuary Resilience Programme. Between October 2022 and May 2023 around 6,000m2 of Macmat® HS was installed as part of a soil nailing solution to mitigate debris falling from a steep rock face running alongside the Manchester to Sheffield Line as part of the Hope Valley Railway Upgrade at Bamford.
Tel: 01865 770 555
Email: Info.uk@maccaferri.com
Visit: www.maccaferri.com/uk/
In Rail Professional earlier this year, we at Midlands Connect called the Midlands Rail Hub a ‘no brainer’. That view is unchanged, but we now have further evidence from businesses to support us!
To recap, Midlands Rail Hub is Midlands Connect’s flagship rail scheme. Through providing new infrastructure in the Midlands, it provides capacity for up to ten additional trains per hour to operate into and out of Birmingham to points in the Midlands and beyond.
The strategic case for making this investment is compelling – through providing excellent interchange between conventional and HS2 services at Moor Street and Curzon Street respectively; through providing much improved links from the West to the East Midlands; and through providing a high capacity, high performance railway with flexibility for the future. We want the scheme in place for Day One of HS2’s service to the West Midlands, at the end of this decade.
While that milestone once felt a long way off, it is now fast approaching, and those who have passed the building site at Curzon Street in recent months – or indeed along much of the route to London – will know that there is tangible progress on the ground.
New capacity is provided principally by two new chords at Bordesley, just east
of Birmingham City Centre, to provide connections from the South West and East Midlands to Birmingham Moor Street. Currently, trains from those locations run to New Street, but with Midlands Rail Hub in place, trains can also run to Birmingham Moor Street. This provides a major opportunity to remap services across Birmingham and deliver a step change in both capacity and connectivity.
Without Midlands Rail Hub, it will not be possible to robustly operate additional services or make significant changes to timetables or service patterns to meet changes in passenger demand. The concept of new chords at Bordesley is not new – far from it in fact – but the scheme gained considerable momentum in 2017, following publication of two important industry documents – Network Rail’s West Midlands and Chilterns Route Study and Midlands Connect’s Strategy. More recently, Network Rail’s 2022 Strategic Advice, and Midlands Connect’s 2022 Strategic Transport Plan, have made Midlands Rail Hub their centrepiece.
The Outline Business Case for the scheme has been developed and submitted, and we’re working hard with our partners and the Government to get the money for the next stage – the Full Business Case. This will allow us to develop the plans in much more detail – to PACE ES4 for those familiar with the intricacies.
So what has changed recently? We’ve completed a business survey! This isn’t our
first survey on the scheme though – late last year we went out to residents of the Midlands and asked for their views. At the time, Maria Machancoses, our Chief Executive, summarised the findings and said that ‘this mega-research shows massive and overwhelming support for the Midlands Rail Hub. It is at the heart of changing the region’s transport network’.
Onto the current day, and the survey that just closed, in mid-June. We were delighted to receive responses from 90 businesses, employing approximately 16,300 people collectively in their local offices. Of those 90, around half employ 1-25 people, but we had an excellent response from larger businesses too, with 15 businesses who employ 100500 people, and over ten responses from those employing over 500 people. These businesses are spread far and wide, with good representation across both the West and East Midlands.
Of the 39 businesses who said employees use the train ‘not much’ or ‘never’, nearly 70 per cent stated it was because of infrequent train times or slow journey times. Midlands Rail Hub is of course seeking to overcome these barriers by offering higher frequencies and reduced journey times.
Nearly 95 per cent said their employees would likely use the trains more for work if the region was better connected. Again, better connectivity is the bread and butter of Midlands Rail Hub.
Over 95 per cent said their business would directly benefit from the region being more closely connected.
Although this can only ever be a snapshot of business views in the Midlands, this provides a great body of evidence around the ‘real’ benefits. As a rail planner, or indeed an organisation that focuses on promoting strategic connectivity, it can be easy to focus on the nuts and bolts of the scheme. Sometimes, as I did last week, it is useful to take a step back and reflect on what the public and the businesses are telling us, and how a scheme of this magnitude makes a meaningful impact on their lives and jobs.
We continue to have a compelling scheme that complements HS2 in the Midlands. We have numbers that back this up – with £1.50 in benefits for every pound we invest. We attract ‘mode shift’ from highway, as people choose rail for their journey instead of the car. But we don’t just shift people from one mode to another – our evidence shows that we ‘generate’ new trips. We have support for the scheme within and beyond the Midlands. We have support from businesses, as proven in our very recent survey, and of course, the general public.
What don’t we have? Funding for the next stage – the Full Business Case – yet. But we are working hard to make this happen and the evidence from our latest survey ensures that the business voice is heard –loud and clear.
Stuart is the Sales Director at Marlec Renewable Power. He has a wealth of experience in both off and on-grid power generation, concentrating on PV and micro wind power. His role enables him to work closely with small and large scale renewable installers and contractors to providing complete, turnkey power solutions bespoke for customers individual requirements.
Marlec Engineering, the longeststanding renewable energy company in the UK, handles and designs energy systems. Alongside their design expertise, Marlec manufactures their range of Rutland Windchargers and supplies a range of the most efficient solar panels available. Their PV immersion controller, the Solar iBoost+ is the UK's favourite domestic solar accessory. Marlec has projects on the railways, highways, utility sectors, telecoms, land and marine leisure industries and sustainable signage solutions, proving renewable energy is more versatile than we could imagine.
Want to know more about Marlec Engineering Co Ltd?
Tel: 01536 201588
Email: ryan@marlec.co.uk or connie.cowell@marlec.co.uk
Visit: www.marlec.co.uk
Sustainability works on a community level, especially with so many people worldwide gaining a passionate interest in how they can contribute to a sustainable movement. So sustainability has become something that brings people together just as much as it represents a global fight against the climate crisis.
One of my favourite aspects of my role revolves around the people I work with, whether my colleagues at Marlec or external clients. Yes, we’re talking about business, but the projects we’re working towards and the collaboration it takes to bring the work to fruition are rewarding because of the sustainable underpinning that drives everyone’s aim.
Marlec came into the world in 1978 in Rutland, hence the name of our Rutland Windcharger range. Our founder, John Fawkes, had begun investigating battery charging methods on farmland in electric fencing applications. And now we have the Rutland Windcharger, a wind-driven battery charging generator.
These days, especially given the advancement in renewable technology over this time, Marlec have its hand in a much wider variety of applications. The products, models and system components we provide, and manufacture are just as varied as their applications and are all designed for offgrid battery charging. We have projects based worldwide in some of the planet’s most challenging climates ranging from Antarctica to the Sahara Desert.
Regarding rail applications, Marlec provides wind, solar, or hybrid energygenerating systems to power various signs and lighting to the rail industry. We provide a range of kits for pedestrian level crossing applications, track lubrication systems, CCTV, sensors and IOT systems across the network.
Uses for the Rutland Windcharger quickly diversified, and they were soon seen on ocean-going yachts, remote telecommunication sites, static caravans, rail networks, isolated homes, navigational buoys and clinics in Africa.
Our heritage and expertise in renewable energy enable us to provide a turnkey design service for our customers. If you need to run your equipment off-grid, we can configure and supply a complete power system for application to give you reliable year-round power generation. We have provided systems for powering traffic equipment, remote CCTV installations, rural broadband sites, seismic activity sensors and hundreds of other applications.
What is your USP (Unique Selling Point)?
We are the UKs longest-standing renewable energy company and have our products operating in around 53 countries worldwide. It’s rare, too, to find products that were developed in the UK and then manufactured in-house, like our Rutland Windchargers. Solar panels have become a common sight in the UK in the last few years, Marlec have been stocking and supplying them into the market since 1985!
Our customers enjoy that we were founded in the UK and still craft our products in the original factory. The idea that local service provides better customer service isn’t lost on us, and we’re proud that we are in such a knowledgeable position to advise and assist our clients.
Plus, we have a dedicated Green Systems team of renewable engineering experts. The team take on design-based projects and works to provide bespoke systems using the latest software and technology. They have an unrivalled knowledge of the Marlec product range and their real life application.
What types of companies do you collaborate on projects with?
All companies across all industries and markets may find themselves in need of a power supply solution. The business may have purchased the camera, solar panel and micro-wind turbine for CCTV applications, requiring support in harmonising the system. Within the rail sector, companies we work with could offer security services, track safety equipment, level crossing equipment, or remote monitoring. All we need to know is the power requirements of the load and the location. From there, we can design the energy system. We find today that more and more equipment is made to be super energy efficient, meaning there’s more scope to power more devices from low-power renewables.
When a client comes to you with a particular problem, what’s your process for coming up with a solution, and how closely do you work with clients throughout the projects?
We work to provide a bespoke service for all of our clients, so the process of meeting and working together could look different each time. Sometimes we will visit sites in person to access the energy requirements ourselves
because we can test client equipment to retrieve accurate data; other times, we have customers who are just as excited by renewables as we are and can provide us with a deal of information over the phone. The whole process entirely depends on how much support the client requires, and we have the tools to meet wherever those needs sit on the spectrum.
Because of the types of products we offer, occasionally, members of the public will get in touch simply for advice regarding their energy system rather than wanting to purchase anything. In cases such as this, we appreciate that education is essential to the business’s relationship with the public, and we’re happy to help.
Has the market grown since the company was established?
The market has grown exponentially. This may be due to the increased interest in the renewable sector and the boom in technology. Because tech is so much more advanced these days, access to a broader range of applications is much more advanced too.
As mentioned earlier, advancements in solar panel efficiencies have allowed small-scale systems to take on higher power demand. The markets are growing because the public has become naturally more exposed to renewables as an energy alternative today. Everyone knows someone with a PV array on their home, and most people are driving past one of our Rutland Windchargers powering speed signs on their daily commute. There is an awareness that the tech works.
What are your plans to ensure your services are still around for years to come?
We invest a huge amount of time in new products, which requires patience from concept to production, but is necessary to stay ahead of the curve. We’re currently developing our next generation of Rutland Windchargers and are investigating the latest technology in battery storage, and our R&D team is constantly innovating. We
‘Bad press and damaging misconceptions are what hurts the reputation of renewables.’
‘We find today that more and more equipment is made to be super energy efficient, meaning there’s more scope to power more devices from low-power renewables.’
only work with the latest solar technology regarding the range of models we stock and supply in the UK.
What are some of the biggest challenges this sector currently faces?
Our main challenge comes from bad press and public misconceptions. Because renewables are trendy, we see many systems deployed that aren’t ours that aren’t specified correctly or installed properly. The resulting systems do not meet the customer’s energy requirements. Bad press and damaging misconceptions are what hurts the reputation of renewables.
What are some potential solutions?
By upholding the company’s values of honesty and integrity, we offer no delusions as to what solar and wind systems can manage. Our honesty is born from a proper understanding of the technology and how the systems are designed to operate.
Do you think the rail industry could be greener and what is your organisation’s green strategy?
We have just secured our position as a carbon-neutral company by offsetting our carbon emissions. A great deal of the energy used on site is generated using renewables. Solar charges our electric company cars, our lighting and any surplus is stored in our batteries.
Concerning the rail market, the rail industry could be greener. But barriers come from accessibility in getting product approval. A by-product of the entire process is time and cost, so what once could have been a relatively affordable concept becomes more expensive after approval has been granted.
At the same time, I respect the reasoning behind the policies in place, but we can’t escape the fact that it does make the rail sector less accessible to new technology.
At some point, every company will face the question of how to continue maximising earnings from their current business practice whilst also investing enough in innovation so they can turn a profit in the future. How can a company achieve the necessary creativity to innovate without compromising their existing business?
We suggest (although it’s not easy) investing in the right people from the get-go. The right people with the correct skillset and knowledge. It’s essential to allow the R&D team time and freedom to innovate. It allows them to feel like their workspace is creative and innovative.
Marlec works to encourage those working in research and development to pursue projects they are passionate and excited about because if you’ve chosen the right person, their passions and interests will crossover with the businesses.
Plus, we are active across various industries. We aren’t reliant on one singular market.
Providing off-grid power systems for:
•
•
•
•
•
For decades, railway networks have relied on Operational Technology (OT) systems which are legacy in nature. However, as the industry progresses towards modernisation and digitalisation, integrating legacy OT assets into newer control and Internet of Things (IoT) systems has become a significant challenge while also opening the door to cyber threats.
The problem lies in the fact that the initial legacy OT systems installed in the past were designed to be air-gapped with little security in mind, meaning they were isolated and prevented from establishing external connections. This presents a challenge for rail companies: How can they modernise these environments so that they can be connected to the network without exposing themselves to a multitude of potential cyberattacks?
As legacy systems are seen to hold back modernisation, consume a disproportionate share of budgets and expose systems to cyberattacks, railway companies can no longer overlook the potential risks of relying on outdated technologies to perform critical tasks.
But while striving to implement a wide range of services, including traffic signalling systems and railway power and control systems, as part of this transformation, operators need to develop a successful modernisation strategy taking into consideration and understanding the priorities and risks associated with it.
Control systems have a long operational life meaning that throughout their lifespan the conditions they continue to operate in could not be predicted. This includes business requirements, supporting systems, vulnerabilities and so on. For instance, railroads can expect some components to last
for at least 25 years. As a result, today’s rail sector is operating as a blended ecosystem of digital and legacy OT and IoT assets –creating a wide range of environments that need to be monitored and standardised.
The aim of the networks’ modernisation is to increase operational and financial efficiencies. To make the rail network more digital and efficient, the systems in place have to get connected to the internet or corporate IT network which will provide asset visibility across OT/IoT and information technology (IT) environments.
Achieving visibility of all OT and IoT assets is therefore crucial for gaining a comprehensive understanding of who has access to critical systems and how network traffic operates. By having clear visibility, operators can effectively identify potential vulnerabilities and risks associated with their assets. These risks can originate from both internal and external sources, making it essential for operators to acknowledge and address all potential threats.
To achieve this, operators need to start by identifying and cataloguing all their assets, thus providing a foundation for further analysis of vulnerabilities and the development of risk profiles. By understanding the specific characteristics and potential vulnerabilities of each asset, operators can prioritise their security efforts and allocate resources accordingly.
Unfortunately, maintaining an accurate and up-to-date asset inventory throughout the asset lifecycle can be challenging. Surprisingly, only 45 per cent of organizations are effective in consistently maintaining such inventories. This underscores the importance of improving asset management practices in the railway industry.
While the adoption of new technologies is a crucial step, it creates new opportunities for malicious actors like cyber criminals, cyber terrorists and state-sponsored attackers. Wherever railway components have a connection to an external network without the right security, they are vulnerable to attack. As critical infrastructure, rail networks are high-value targets. A recent report has demonstrated that in 2022 ransomware and data-related threats were the predominant threats (45 per cent and 25 per cent, respectively), followed by DDoS attacks.
The motivations behind the attacks vary from financial gain, to political reasons like in the case of the Belarusian ransomware attack in January 2022. In any case, the consequences of disrupting railway operations can be severe and should be mitigated so that companies are able to provide safe, reliable, and secure transportation services to the public. As new threats emerge and old ones evolve, railway operators need to stay one step ahead of the attackers to prevent them.
Fortunately, having the visibility of assets and understanding their vulnerabilities also allows to anticipate where the risks could come from and to identify the source of the breach. Real-time situational awareness is necessary for fast and efficient problem identification, response, and remediation. Besides that, operators can exploit threat feeds and threat detection, invest in robust security measures, conduct regular backups, and provide staff training programs on cybersecurity best practices to safeguard systems and mitigate attacks.
Governments have recognised the escalating threat landscape in the railway industry, leading to the implementation of new requirements like NIS Directive that organisations must adhere to. These regulations compel rail operators to address existing security gaps, report and mitigate any cyber incidents or anomalies that arise.
It is expected that cyber threats will become increasingly sophisticated and frequent in 2023. While predicting the exact strategies of attackers can be challenging, adopting appropriate solutions is vital to gain asset visibility and enhance the cybersecurity posture of critical railway infrastructure. By implementing the right measures, rail operators can detect and respond to threats more effectively, reducing the potential impact of cyberattacks on their systems.
Wayne Carrington is the National Accounts Manager for Vogelsang Ltd, a pump and machinery manufacturer and supplier of fixed and mobile equipment to the rail industry. He joined in 2006 and oversees all rail projects for the company in the UK.
Vogelsang GmbH & Co. KG develops, produces and distributes highly-engineered equipment that is easy to maintain. The head office is located in Essen/Oldb. in Lower Saxony, Germany. Founded in 1929 as a manufacturer of agricultural machinery, the company has grown to become a specialist in individually configurable machines, plants and systems for the agricultural, biogas, industrial, transportation and wastewater sectors.
Want to know more about Vogelsang Ltd?
Tel: 01270 216 600
Email: wayne.carrington@ vogelsang.info
Visit: www.vogelsang.info/en-uk/
I’ve always been interested in engines and enjoyed motocross racing. I started as an apprentice diesel mechanic after completing two year’s national service in the army in South Africa, where I’m from, in 1990. At the time, diesel engineers were paid more than petrol engineers so that’s what I did. I didn’t enjoy getting covered in diesel, but I found they were bigger and easier to work with than petrol engines.
All my mates at the time were sales reps driving flash cars and I was in my old banger, so I started a technical pump sales role in 1992 and have been involved with pumps ever since – over 30 years. I was the company gofer for the first five years but the time was invaluable, learning about customers’ pumps.
I found that whilst working as an engineer on trucks and buses was physically demanding, working with pumps was more mentally demanding. Back when
I started you used a lot of calculations and trigonometry as there were no pump selector computers. I got a lot of job satisfaction working out the pump systems and mathematical calculations, then compiling the quotes for the customer. Also, I’m a bit of a talker so working with people in a sales role comes naturally to me.
I moved to the UK in 2000 and joined Vogelsang in 2006 when it was a fledgling company in the UK (although it's been around since 1929 in Germany and is still family-owned). Due to the company’s continual engineering development, we saw a gap in the market and developed a series of pumps and associated equipment perfectly suited to rail use, which sold well. As such, the UK needed a rail-specialist salesman who would integrate themselves into the rail industry. Because of my extensive background in pumps, I became that salesman.
What challenges have you faced in the industry?
Initially, I became a manager of a pump company when I was 25, but almost everyone I worked with was in their 50s and were reluctant to take advice from a young upstart. It was a challenge to get the rail industry to accept me, but due to my engineering background I was able to talk about their needs technically with them and they appreciated my knowledge. I found that if you can solve their problems they’ll realise you’re no fool.
When I joined the UK Vogelsang subsidiary it was an unknown, young company in the UK pump market – if you asked anyone in the pump industry, most people hadn’t heard of Vogelsang. It was a challenge to grow in the industry and one I was keen to pursue. It’s paid off as we’re a strong name 17 years later purely because we’ve got a decent amount of quality equipment available to the industrial markets. We also do more marketing, networking and events to help get in front of the right people.
One ongoing challenge is trying to convince people to buy quality products over cheap ones, which reduce cost in the long-run. The UK rail industry likes to work with a very limited budget sometimes and the powers that be will spend money on unnecessary stuff and not prioritise the parts that really matter. It seems that waste disposal is deemed to be less important than other cosmetic features. Richard Branson said of Virgin Trains that ‘they’re clean and on time’. That always stuck in my mind.
Another current challenge is working around everything going back to the control of the Government. As far as I’m aware, any project or equipment over a certain value goes through the Government which is time-consuming for all involved and creates a lot of unnecessary hoops to jump through. It seems the industry gets in its own way at times.
What success have you experienced in the last twelve months?
Despite the increasing popularity of bioreactor toilet systems, Vogelsang is the only company with a proven system for cleaning these units. Not only are our BioUnits specially designed for cleaning on-board bioreactor wastewater treatment systems, special chemical and descaling cycles can be carried out to perform a full system recovery of the bioreactor wastewater treatment unit. This is setting us apart in the market.
What are some standout projects you’ve been involved with over the years?
I’ve been fortunate to oversee large-scale installations of our waste extraction systems at many sites across the UK. For Alston in Glasgow and Hitachi Rail in Doncaster we installed 16 CET (controlled emission toilet system) suction units and TUnits - which give water supply and toilet wastewater disposal services in one compact point.
How have the products and services you offer developed over the years?
Every year, Vogelsang’s R&D department is tasked with developing new improved products and systems to ensure our policy of on-going improvement. Over the years, our products and services have become more efficient and more automated to offer easier operation.
An example is our non-drip coupling used on waste extraction from trains, which has been a game-changer for us and our customers. It ensures that no waste effluent spills onto the ground, which keeps the platform, passengers and station works safe. It also allows our units to be used at live stations making it easier for train operators to empty their trains of waste.
What are some of the biggest challenges this sector currently faces?
I think a big challenge the rail industry is facing is having to cut through the high level of bureaucracy to get projects either up and running or collated on time and to budget. Of course, safety is of paramount importance and you don’t want to endanger anyone’s life, but things could be done in a more efficient way. I believe the rail industry is sometimes more hung up on the red tape than getting the job done, when a potential solution could be to apply some common sense.
How can the industry tackle its skills shortage and how do you recruit/retain/ train your staff?
Rail seems to be one of the foremost industries to offer apprenticeships, and must continue to do so as learning on the job is the best way to become an expert in a skill. Some might be put off by the thought of
their apprentice, once fully trained, suddenly leaving. Of course this is a valid concern, but communication, good training and offering a good salary are the most important things when it comes to keeping staff.
What are your hopes for the new regulatory bodies, such as Great British Railways?
If this Government does in fact move forward with it, it could be a good thing. Whatever the body, I think it’s important that it doesn’t get disconnected with reality. It needs to be fiscally well-managed and operated in a frugal manner with zero financial wastage.
It’s all too easy for people working in industry bodies to become insular, but if it’s going to be Government-funded then they must treat the taxpayers' money like their own cash; with due care and attention. My advice would be not to buy the cheapest equipment, but the best equipment that will last.
What do you think is the biggest challenge currently facing the industry?
Creating a greener image in the minds of the customer is the next big challenge. People still think of trains as a dirty sort of business.
The general public aren’t aware of the move towards increasing sustainability in the rail industry, but I certainly think it's moving towards becoming green in terms of waste treatment as Vogelsang has seen with increasing interest in our BioUnits.
I understand that the industry is looking at alternative renewable sources to power trains, but we must consider how we treat the fuel and waste once used. For instance, all the waste that comes off a train each day could go into an AD plant from which a station could generate heat, power and gas which could be used to drive the train or the depo to power equipment.
I’m sure someone in the industry is working on this somewhere, but the public needs to be made aware of the way the industry is changing. Right now they only see adverts talking about WIFI on a train or journey prices, they’re not informed about the investment that goes into keeping rolling stock up to date.
What is your view of the future of security within the rail sector?
I think the rail industry has a healthy future ahead of it, providing pricing is not out of proportion to alternative forms of transport. For instance, you could drive from Manchester to London on a tank of fuel, which would cost less than the price of a train ticket, and you can only travel from station to station without taking into account connecting transport such as taxis. The discerning passenger won’t be spending unnecessarily so it’s important the rail industry doesn’t turn its back on this fact.
In everything we do, we never lose sight of what is essential to you: working economically with reliable technology.
As the inventor of the elastomer-coated rotary lobe pump and a pioneer in the area of wastewater technology, we have been supplying technical solutions whose functionality, quality and reliability set the benchmark for our competitors. Leading railway operators put their trust in our intelligently designed pumping stations and Vogelsang’s demand-oriented technical equipment. These include systems for water supply and wastewater disposal as well as servicing and cleaning for passenger trains to ensure the highest standards regarding hygiene, usability and cost-efficiency.
Contact person: Wayne Carrington
Tel. 07845 541 429 | wayne.carrington@vogelsang.info
vogelsang.info
that we may have the contacts and the employability skills that could make a difference going forward.’
The Way Youth Zone is a youth-led, state-of-the-art space for young people aged 8-18 and up to 25 years-old for those with additional needs.
It costs more than £1.3 million to run the venue every year and, whilst funding from generous city patrons – including the City of Wolverhampton College and the City of Wolverhampton Council – is in place, the centre still relies heavily on the support of local businesses and private donors.
The donations go towards the maintenance of a multi-use games area, a fitness centre, boxing gym, recording studio, kitchen, sensory room, and a large indoor climbing wall. There are also arts and crafts sessions, fashion design, podcast recording facilities and a café that serves nutritious hot meals for just £1, as well as snacks and drinks. All of this is available for £5 membership per year and 50p per session, with The Way open six days per week.
Susan Barlow, Head of Fundraising at The Way Youth Zone, added her support: ‘We are really pleased to be adding NIS to our Patrons and look forward to building a strategic relationship, where we can also leverage its strong employability skills and expertise in training.
‘Following Covid-19 we lost a lot of supporters, and we are only slowly beginning to get more corporates involved again. Having Davie and his team banging the drum will be great in hopefully engaging more businesses in the city and surrounding areas.
‘We are also on a big volunteer recruitment drive. They are at the heart of everything we do and for people looking to get involved, we can be a great way to make a real difference to your local community.’
National Infrastructure Solutions (NIS), which was started by former Royal Marine and professional footballer Davie Carns, is the latest firm to become a Patron to one of the city’s most important charities.
The company has made a significant donation as part of the deal and this will help the organisation build on its crucial work in supporting more than 600 young people (aged between 8 and 18) every week with access to sports facilities, recording studios, group activities, arts and crafts and cooking lessons.
It has also encouraged its 40-strong workforce to volunteer and is exploring ways in which it can help provide employability skills and highlight career opportunities in rail.
‘We are a firm that was born in Wolverhampton, and we are very passionate
about the place we call home – this made the decision to support the amazing work The Way does very easy’ explained Davie Carns, Managing Director of NIS.
‘Since it was opened in 2016, over 16,400 people have been supported, many of whom live in some of the most deprived areas of our city. These children will have little access to the types of facilities that The Way provides, and some of them may even go hungry without the free meals that were in place during the winter months.’
He continued: ‘One of the other key features is the ability to raise aspirations. The individuals who go here during the week and at weekends are our future and the next generation of workers. We must show them they can build good careers if they work hard.
‘That’s why NIS has become a Patron. We believe in the excellent work the organisation undertakes and we believe
National Infrastructure Solutions, which has also committed to give 2.5 per cent of its annual net profits to good causes, runs courses that are available for both newcomers to rail and those already working in the sector who want to upskill and develop their knowledge further.
It works extremely closely with City of Wolverhampton College, who together operate an advanced rail training centre at the Wellington Road Campus in Bilston that is helping to reskill and upskill hundreds of people for projects including HS2.
Peter Merry, Deputy Chief Executive of City of Wolverhampton College, concluded: ‘As a founding patron of The Way, the College takes immense pride in its pivotal role in shaping the lives of young people across the city. Working in collaboration with our partner, NIS, together we are all poised to make an exponential impact, providing exciting opportunities for young people that will set Wolverhampton apart from surrounding areas.’
For further information or to donate, please visit www.thewayyouthzone.org More details on NIS can be found at www.nisgroup.co.uk
Ian is an Experienced Director in the global railway industry, specialising in health and safety, technical, commercial, and staff processes. Skilled in managing complexity, fostering positive change, and overseeing budgets. Extensive expertise in signalling, telecommunications, maintenance, civil engineering, power engineering and permanent way. Proven track record in gaining Network Rail Product Acceptance and promoting digital solutions. Ian was Editor of IRSE NEWS for 13+ years, currently a Trustee/Director, Chair of Audit Committee, and Volunteer Development Committee at IRSE.
Park Signalling was formed in 2000 by key staff from Alstom Signalling, since then we have evolved into an industryrenowned highly motivated team of specialists, who together offer unrivalled signalling system knowledge complemented with in-house hardware and software design and build expertise.
Want to know more about Park Signalling?
Visit: www.park-signalling.co.uk
How did you get started in the industry?
In 1987 I joined British Rail’s Signalling Telecommunications maintenance team at Leicester, I was part of one of the local maintenance teams starting as a Junior Railman. I progressed quickly through the technical grades until privatisation in 1992, I was then promoted to Signalling Technical Support in Birmingham, where I undertook a wide range of technical challenges and developed a deeper understanding of
signalling technologies of the time and historical signalling infrastructure.
In 1994 I became a supervisory manager at a number of locations which resulted in ultimately working for GTRM back in Birmingham in 1998.
Since then I have undertaken a number of challenging positions within the signalling and telecommunications arena and started to engage with the IRSE at a local level. Within the IRSE I quickly progressed to support the running of the local section and then become the editor of the IRSE news publication for 13 years. During this time I had a breadth of opportunities to engage and network with a vast range of signalling & telecoms professionals worldwide which has served me well in my future roles.
Since 2000 I have had more opportunities to work with a number of the critical big players in the sector, including; Siemens, Bombardier, Signalling Solutions and Atkins and worked on high profile projects such as: Bournemouth Resignalling, Victoria Line Upgrade, Bristol Resignalling and East Kent Resignalling - phase 2. During this time, I also had the opportunity to work in a number of countries around the world, including Europe, Australasia, Far East and Africa.
When did you join the company and what is your current role?
In 2017 I was approached by the then Managing Director of Park Signalling and invited to join them in a Business Development role, as part of the Senior Leadership Team. As Business Development Director my priority is to continue to acquire new customers and accelerate growth. The role is a crucial one for Park Signalling Ltd who have the ambition and drive to expand and diversify its clientele over the next five to ten years.
I am responsible for the development and implementation of commercial strategies according to company goals and objectives aiming to accelerate growth. We actively promote digital signalling and telecommunication solutions and products around the globe and conduct analysis to create detailed business plans on commercial opportunities.
Responsible for all related tasks and processes to develop and implement growth opportunities within the business including Sales, Commercial, Finance, Marketing, Strategic planning and management, Proposal management and Legal issues.
I provide Engineering Technical Support into Park Signalling Ltd from previous experience/knowledge.
What challenges have you faced in the industry?
Over the last 30 + years I have witnessed a huge array of changes, I have been lucky enough to meet and work with a great number of excellent professionals who have driven positive change cultures, but I have
also seen a number of redundancies and sadly witnessed great losses of technical capabilities across sectors globally.
What success have you experienced in the last twelve months and how do you measure success?
Park Signalling is a Unipart Company and as part of a recent restructuring we have now become part of the new Unipart Technologies Group, this has placed us now with a number of technology businesses which enhances and builds upon our existing technical capabilities. Through collaboration within the Unipart Technologies Group we can draw upon a wider range of skills, knowledge and experience to successfully deliver technology performance improvements for our customers and ultimately become the improvement partner of choice.
Success for me is to ensure that we can be fully aligned to our customers, having a deep understanding of the needs and issues they are experiencing and to be able to deliver solutions that exceed their expectations within a timely and cost effective manner. Collaborative working with our wider group will enable us to deliver a greater range of performance improving technology solutions to the global signalling and telecommunications market.
What does sustainability mean to you?
Sustainability is at the forefront of all of our minds, at Park Signalling we make a responsible choice when developing technology product solutions for the rail industry. We seek to minimise the negative impacts of our developments which can be witnessed in products such as DiBloC, our digital alternative to the historical Token Block Instrument. By designing a solution which directly retrofits and integrates into the existing signalling system we are building resilience into our solutions, by delivering future proof products.
How has technology developed since you started in the industry?
At the beginning of my career mechanical and power signalling solutions were predominant across the UK and with the introduction of safety critical computers, technologies have advanced considerably. The presence of mechanical signalling in the UK is now minimal and can only be found in a limited number of locations.
Digital solutions and the drive to improve rail performance has resulted in a huge leap in the capabilities of both the infrastructure and on-board rolling stock with a clear requirement for condition based monitoring to be included.
Given the pace of the changes in technologies that have had a positive impact on the overall industry, it has also had a significant impact on the levels of
competency and available resources, there is a noticeable cultural shift from the ‘job for life’ vision that used to be within the industry. We should be ensuring the technical and corporate competencies and knowledge are retained and developed.
What are your views on collaborative working?
Collaborative working facilitates the development of new and improved products and solutions, this style of working helps to reduce the elements of individual risk. By working towards common goals, collaborators can actively share their own ideas, skills and knowledge which often leads to delivering exceptional results. Building trust within the team, encouraging members to contribute and leveraging strengths rather than focussing on weaknesses helps the team to overcome challenges to deliver effective and efficient solutions for the customer and thus benefiting the end users.
Have you changed your approach to work at all since Covid?
Whilst Covid was an extremely challenging time for all businesses and individuals it forced us to make best use of the technologies that are available to us. By adopting and retaining many of the changes in working practice, we are now able to connect and communicate very efficiently through video calls etc. This has resulted in improved productivity and increased efficiency in responding to multiple customer needs. The work life balance can be difficult to manage at times, with flexible working hours being inconsistent there is often an expectation to literally be available 24/7.
In terms of technology, how do you anticipate things might change in the next five to ten years?
Whilst the roll out of ETCS is anticipated on the mainline routes in the UK and mainland Europe, current costs will prohibit the complete rollout on all railway infrastructures. Railway organisations will need to effectively manage signalling & telecommunications renewals and upgrades that they can afford.
Digital In Cab Signalling Solutions (Such as Radio Electronic Token Block) should be considered as an alternative and cost effective SIL4 proven solution for secondary lines and rural routes to ensure the survival and viability of the rail networks in those locations.
The wide scale roll out of remote condition monitoring for infrastructure and rolling stock will enable efficiencies through the adoption of a predictive maintenance approach, however we must also ensure that we maintain knowledge and competencies to ensure we have the capability to ‘fix issues’ when things do go wrong.
A replacement for the existing Block Controller for single line track.
Our fully digital version of key token equipment communicates digitally through IP based systems, including provision for TPWS and section signal release.
The DiBloC features:
• IP connectivity with two redundant connections
• Physical key compatibility with existing key token machine equipment such as ground frame locks
• Ability to work in sets of 2-6 units
• Ability to operate TPWS and/or single throw/starting signals
• No on-board equipment – compatibility with all rolling stock
The digital equivalent of the electro-mechanical standard
Greengauge 21 is a non-for-profit registered company, founded in 2006 by Jim Steer that aims to investigate and develop the concepts associated with a UK highspeed rail network.
Jim Steer of Greengauge 21 explores the key Northern Powerhouse link between Sheffield and Leeds and points to a set of cost-effective measures that can be introduced in the 2020s
Sheffield-Leeds is an Innovation corridor, with a concentration of businesses and research facilities in advanced manufacturing and other spheres. To build on successes to date, expand the economy and grow employment prospects, the cities,
towns and ex-mining villages of South and West Yorkshire need to be properly interconnected.
But this is in danger of being a land that time forgot as far as rail improvements are concerned. While rail use in South and West Yorkshire has changed, passenger
volumes on some days of the week at Sheffield and Leeds stations now exceed prepandemic levels.
Key elements in the action plan for the 2020s:
• Adding a second hourly fast service between Leeds and Sheffield (and onwards to Nottingham).
• Extra capacity for stopping services.
• East Midlands Railway London St Pancras-Sheffield services extended to Barnsley, Wakefield Kirkgate and York.
• A new station for Rotherham, with fast connections to both Sheffield and Leeds.
The report also outlines exciting plans for Bradford. Here, Steer adds, where there is uncertainty around the long term plans in the Integrated Rail Plan. There are great opportunities to bring early benefits and help pave the way for longer term plans.
Introducing new LNER Bradford-Leeds(non-stop)-London Kings Cross services, would take 15 minutes off the standard Leeds-London journey time and transform Bradford’s connectivity. And while another initiative requires reopening a short section of disused section of line, it adds a new station (to serve Ossett) and provides a direct Sheffield-Barnsley-Bradford connection that has been long missing.
These improvements could come 15-20 years before longer term high-speed plans and help set Yorkshire on the path to a greener transport future. We would urge all parties, including DfT, to come together and implement the plans set out here for improving rail services between South and West Yorkshire.
John Lawrence is Director of JPL Diversified, a company successfully helping innovation companies bridge the gap into the rail industry. He has 20 years rail experience at all levels and areas and has successfully developed and delivered a range of high-profile, award-winning innovation, change and improvement programmes.
JPL Diversified Ltd is dedicated to market entry, product and service development and sales pipeline building.
How did you get started and how long have you worked in the industry?
I’ve worked in the industry for around 20 years now. I joined Network Rail in 2003, as part of something called the Conversion Programme, set up to bring in experienced engineers from other industries, give us a twelve-month grounding in the rail industry with a broad base of knowledge and understanding and then let us loose to try and bring something new to the industry.
The training was delivered by Signet at Derby, and we had an energetic twelve months sharing our time between a residential training programme at the RTC or on placement in the regions. Our cohort started life as D&C (project) Engineers, and it was a really great way to learn the ropes. We studied various aspects of signal engineering, from design through to testing and commissioning and maintenance. We had a great group with us and I’m still in contact with most of them to this day, I also enjoyed the counsel of some very experienced people, with special mentions to Dave Doggett, Ruben Dakin and Dave Kerr, my appointed mentor. Mentorship is very important on the railway, as I was to learn.
It's fair to say that the conversion engineers across the UK had a mixed reception in some quarters when we first landed but it was really good experience to see first hand how change was received. Lessons to take forward into my career, for certain!
Tell us about your early rail career before you started JPL Diversified.
I’ve been blessed with being able to enjoy a very broad base of experience on the railway. I’ve worked in pretty much every department and every region, including working in central teams and on major projects, but I’ve always developed each role into an improvement exercise and enjoyed a high level of autonomy to look for improvements and then set up the means to deliver them from concept to completion.
The early work in Six Sigma was great, I developed a number of projects that had national spread, topped the league table both years for savings and won a National Award chosen by the Chief Exec, which was all pretty exciting for my first years in the
industry. I brought SMEs into the industry to work on my projects, something that would be a feature as my career progressed and through learning six sigma, I developed an understanding of the power of hard evidence in encouraging change.
However, the most important thing in this early period, for me, though, was the exposure and engagement I had with everyone from shop floor to the executive. This gave me fantastic insight into being able to see the industry from so many different perspectives and to experience delivering change in this environment.
And the career development you have had since, in rail?
Following this, I spent time in Maintenance Improvement, where I developed and delivered a very broad range of business improvements, doing everything from sponsorship and business case development to standards changes and safety process improvements. I worked for a short period of time as Maintenance Delivery Unit Manager, where I managed an industrial action to a successful conclusion and opened a mothballed line, both of which were a real eye-opener into rail industry culture! I was then requested to take up a troubleshooting role, improving asset reliability on West Coast to allow the VHF timetable introduction, where I developed a suite of changes that improved asset performance by 50 per cent and developed and implemented a full asset management process, plus a very cost-effective remote condition monitoring system.
These projects were just the best grounding you could wish for in understand the vast range of processes and the underlying culture of the railway, as well as to experience the whole range of stakeholders from the executive at NR and the TOCs to direct delivery staff. I learned a great deal about the processes and behaviours required to make things change across all disciplines.
I went from this into what is now the Digital Railway Programme where I developed new systems, working on the ETCS EDS, taking COMPASS DMWS from an idea through its early research and development years and into first live deployments, working across infrastructure and rail undertaking.
Want to know more about JPL Diversified Ltd?
Tel: 07935 788604
Email: john@jpldiversified.co.uk
Visit: www.jpldiversified.co.uk
I then went over to Atkins to run the R&D programme, bringing in the ElectroLogIXS signalling system and Atkins Signalling Method, both safety critical technology and process developments that will change the way things are done on the railway for years to come. I finished my time at Atkins on the digital consultancy programme, where I developed a mathematical proof for Risk Based Maintenance and some of the foundations for what has become the fantastic Insight tool.
‘Al will have a similar effect on the whitecollar workforce that robotics and automation had on the blue-collar worker’
Tell us about your career before you joined the railway?
In terms of creating change on the railway this is probably the most important element, I worked somewhere else in my formative years! I started life in the steel and quarrying industries, which in the UK was a shrinking industry and brutally competitive. The company I worked for actually delivered operational contracts for the steel industry and our role was to find new ways to automate, improve and make operations more efficient – winning contracts and in the process make the company a healthy profit.
I developed my first idea for an automation project when I was still an apprentice, writing a report on how to integrate two different operations and replace operators with maintainers. Needless to say, although it was regarded as something of a novelty that an apprentice would see this opportunity, management considered it too radical to take forward, so I got my first lesson in change management –not everyone embraces change!
The technical side of the job, working on complex control systems and having to maintain and fault a very varied range of processes and equipment was an excellent foundation for someone with an eye for improvement. Being taught and applying a range of processes for investigating and finding faults and issues on complex processes under operational pressure and in a safety critical environment gave me the foundation that drove my later business process analysis and improvement work. It’s no surprise that many control systems and electrical engineers move into business improvement.
In addition to engineering, I worked in operational and contract management, I ran the electrical function and held a free role to find and improve operations around the company. I developed and delivered several large-scale automation projects, a number of large novel infrastructure projects, a full suite of standards for the organisation and created a number of novel technology deployments that improved safety, business and environmental performance.
What was the inspiration behind starting JPL Diversified and what is your USP (Unique Selling Point)?
I’m very driven towards creating change and improvement. I’ve done this in the client organisation, the tier 1 and 2 supply chain and as a consultant but there was always a finite element to what I could achieve in this space. I’ve spent a lot of time mentoring people and companies to develop and improve, whilst working in steel, for Network Rail and the Tier 1&2 supply chain. I’ve specialised in bringing SMEs into the rail market, and creating the commercial and business environment for them to thrive.
I fundamentally enjoy helping people and businesses flourish and I really enjoy creating change so, from this perspective, the obvious thing to do was to set up a company to do this on a larger scale. I’ve had a great deal of success in creating change and have developed a unique perspective and set of experiences to be able to support companies to really bridge the innovation gap in rail. I really understand how to create change and improvement in the rail environment!
JPL Diversified was set up to assist companies who want to either get into rail or to build and diversify the businesses of those already there. We work with clients to deliver those plans until they are fully embedded into the industry for the long term, identifying and removing all roadblocks along the way. Our experience as a company of turning over every stone in the industry affords us a unique position in being able to understand a client’s USP, see an opportunity and do all the necessary work required to exploit it.
When a client comes to you with a particular problem, what’s your process for coming up with a solution, and how closely do you work with clients throughout the projects?
All client’s needs are different, but we do follow some common principles that serve our clients well. We strongly believe that there are three pillars required to be successful in rail: Sponsorship, Mentorship and Partnership. Sponsorship comes from inside the client organisation and will provide the pull for your new product or industry change. Providing there is a need, they will assist you to navigate the buying organisation and support you to overcome obstacles and roadblocks. A Sponsor will work for the interests of the client organisation.
Mentorship must come from outside of the client organisation from a company like JPL Diversified, and we work with the client to find sponsors, engage stakeholders and develop the strategy and plans for entering and thriving in the right markets. We then work to assist in identifying and delivering all that is needed, based on our knowledge and experience of the market, to achieve solid long-term sales.
The partnership element is the primary aim of the combined efforts of the sponsor and mentor to find the users that will benefit from a client’s product or change and work to develop long term, mutually beneficial partnerships with them, delivering enabling work – like Product Acceptance and Design for Reliability, business case development, funding identification, standards change, competence development and product awareness – to ensure a smooth landing. This is the key to longevity in the industry.
What technology would you say will make the biggest short term difference in the industry moving forward?
I think we have a two-step requirement for technology change in the UK railway. The first is to look at the short term to improve efficiency within the normal cycles of work we currently deliver. Then we need to look at the medium to long term with a more strategic approach.
The short-term move is to bring in COTS technology that we would see in general use across a multitude of industries, covering both control and automation and remote condition monitoring. We’re still not making anywhere near the best use of this technology, in my opinion.
For example, at the heart of the railway is the signalling system, this system can be an enabler or a blocker when it comes to creating business improvement. The majority of existing signalling technology is not specified to be part of the whole railway system and does not provide all the information that it could to enable innovation and process improvement in other areas. ETCS assists with this, but this is still some way off becoming the standard. I have been an exponent for many years of using the humble Programmable Logic Controller (PLC) to become the standard technology for signalling systems, with a requirement to separate the critical from non-critical processing.
We started this with COMPASS DMWS and also achieved an element of it with ElectroLogIXS but there is still a huge amount of process and wholesystem improvement that can be derived from bringing PLCs into the signalling mainstream.
The medium to long term move is to develop a controlled strategy to integrate AI into the railway. I say controlled, as Al will have a similar effect on the white-collar workforce that robotics and automation had on the blue-collar worker, and it will need to be deployed strategically so not to create unwanted societal issues. Moving away from the terminator-talk we’re seeing of late; AI has the power to automate large swathes of administrative effort and analysis and afford engineers, project and business
‘We strongly believe there are three pillars required to be successful in rail: Sponsorship, Mentorship and Partnership’
management the chance to focus on the big picture and practical delivery.
However, the obvious place where AI will make the most impact in the medium term is in operations control. The solution to plan and deliver an effective train service that maximises use of the network, with all the complexity that surrounds the moving parts around it, including managing perturbation is to use AI. Combined with an agile and interconnected moving block signalling system, AI will deliver the day, week, month and season’s best use of the network regardless of the situation presented to it.
What are some of the biggest challenges this sector currently faces and what are some potential solutions?
At the moment, there is an acute need to catch up and consolidate the major changes that have been applied to the industry over the last few years and find an amount of stability. There has been a lot of change in a short space of time, and this inevitably hits the delivery units and project delivery teams the hardest.
The modernisation programme has thinned the workforce and needs to be supported by more remote monitoring, greater process and task automation and intuitive process digitalisation to ensure we can still deliver the required safety, performance and efficiency required of an operational railway. The welcome, and much overdue, removal of red zone working needs to be backed up by closed-loop monitoring of the workbank to ensure everyone is supported to deliver. It also needs to be underpinned by complete implementation of fact-supported, risk-based maintenance with support from refreshed effective asset failure mode analysis plus support from technology and process improvements.
We also need to push to find innovative ways to deliver in the challenging financial headwinds affecting CP7, as this is inevitably going to have an impact on renewals and maintenance improvement. This again can be supported by digital process improvement, remote monitoring and challenging the standards underpinning work done on track.
How can we get more use of the rail assets and how does this fit with your vision of rail in 10 or 20 years?
There are a few things that could make a difference, here, one being incremental in nature and the others a bit more blue sky. In the short term, we need to make the move completely to an Asset Management organisation from that of maintenance and renewal. We’ve seen a strong move over a number of years to this effect, but we need to bite the bullet and make the move completely. This means getting a much deeper and wider understanding of every asset and its failure modes, implementing actions to eliminate design and installation defects, creating monitoring systems that detect wear and tear and putting in place effective whole-life management plans for them.
This will transform the way work is done, drive down costs, allow spot replacement and targeted renewals based on accurate condition assessment and afford the asset manager an opportunity to plan two and three control periods ahead.
A second more blue sky thought, is to rethink what the railway can physically do, over and above the conveyance of passengers and freight. If you consider the railway connects geographic place with a linear conduit, then much more can be made of the assets and space contained within. I know we keep looking at the telecoms asset and what commercial uses can be made from that, but we also have an electrical asset that could be used to improve electrical charging and storage for Electric Vehicles, for example, particularly in places where grid connections can’t cope.
We could also look at ways to be able to move water from place to place, given a bit of thought. This type of thinking of the rail landscape as a conduit and set of geographic nodes could increase the range of services the railway could offer and would greatly increase its business case and diversify service offering in the new world of lower commuting.
If you were in charge of the UK rail industry, where would you look for improvement?
There are three key areas that I would focus on to find improvement in the rail industry. One is the principle of informed local decision making, the second is east-west travel and the third defining the place of the railway in the UK business and society ecosystem. In the case of the former, I would, in the short term, strengthen and support the Long-Term Planning Process by driving up local authorities’ knowledge and expertise in rail and associated connectivity to get a much more knowledgeable client and specifier of the future network.
I would then consider devolving the network design over to local authorities for their respective patch and connections, with
the national picture then being managed by NR. I would reinforce this with a much stronger focus on east-west links, including tunnels under the Pennines. This would be transformational for the movement of people and goods in the UK.
The final piece of the jigsaw would be elevating the railway’s position in the business ecosystem in the public perception by improving political focus on the longterm overall value to the UK.. I would drive this down into the business decisions and KPIs of the operational railway by focussing on elements like buying-for-export, by adding a weighting to procurement decisions for technology that can have a large impact on balance of payments I would also look at the development of strategic partnerships with importers that provided opportunities in other markets for the UK railway supply chain.
In terms of technology and industry change, how do you anticipate things might change in the next five to ten years and how can your clients position themselves to make the most of it?
Looking first at the infrastructure situation, I hope, there will be an inexorable drive toward automation, digitalisation and a move toward total asset management, as technology, processes and data systems improve to provide the information to be able to manage the whole system over its whole life. The engineering and maintenance function will increase competence, knowledge and experience and thus confidence with respect to whole life asset management and will be furnished with accurate, proven information to deliver best performance by the policies of the Government, Regulators and funders.
In terms of operational efficiency, we will see AI coming more into operational planning and management and even greater centralisation of operational control due to automation and the ability to deal with greater complexity. ETCS deployment on East Coast will be the acid test for UK cab signalling, with the delivery model showing great promise at the moment, and there will be more opportunities to improve operational management with targeted cab signalling solutions on fixed infrastructure.
And, lastly, if I have anything to do with it, there will be much greater take up of technology transfer from the foundation and process industries to accelerate improvements, and a greater push for fact-based decision making for total asset management (which will inevitably require more attention to understanding and eliminating sources of failure in asset and process).
Our clients will be able to take advantage of this by getting the most proactive and informed mentorship and support available and enjoy the benefits of long-term business development in the rail industry at home and abroad.
‘The short-term move is to bring in COTS technology that we would see in general use across a multitude of industries, covering both control and automation and remote condition monitoring.’
The Snowdon Mountain Railway operates both traditional diesel services and heritage steam experience trips to the summit of Snowdon between April and October each year, the latter pushed by an original Swiss steam locomotive from 1896.
To ensure continuation of service, timely and efficient maintenance of the locomotives is essential and the investment in a set of railway lifting jacks from Totalkare will help to facilitate this by providing access to the underside of both the locomotives and carriages.
Totalkare’s railway lifting jacks are made to order and are available in lifting capacities from 5,000 – 50,000kg per jack. While a set
of four lifting jacks are sufficient to lift a single carriage, the jacks can be connected in series up to 128 jacks, enabling an entire train to be lifted at once if required. They feature a computerised control unit, providing easy synchronicity, and carry an IP55 level of electrical protection.
The 5,500kg railway lifting jacks for Snowdon Mountain Railway replace a previously supplied solution from Totalkare, based on their road vehicle mobile column lifts with bespoke anvil attachment, which has reached end of life. The new lifting jacks will be supported by a Totalkare service package which includes two field service engineer visits per year as standard.
‘Our previous locomotive lifting equipment served us very well but was nearing the end of the line’ commented Hugh Jones of Snowdon Mountain Railway.
‘We’ve always been pleased with the quality of service support provided by Totalkare, so it was a natural choice to return to them for our new rail lifting jacks.’
Brian Young, National Accounts Manager and Rail specialist for Totalkare, said: ‘Our railway lifting jacks are a versatile and effective way of raising rail vehicles into the air for the purposes of essential repair and maintenance. We are delighted to continue supporting such an iconic rail service at one of the UK’s premier tourist destinations.’
Has many years’ experience in the world of engineering manufacture. The markets the products supplied ranged from large pressure vessels, through earth boring rigs, pile driving hammers and finishing up with staircases and handrails.
BPI Project Installations Ltd design, manufacture and install balustrade, handrails and other associated metalwork to the Railway, construction, public and private markets. They operate throughout the UK mainland.
Want to know more about BPI Bespoke Project Installations Ltd?
Sales contact: Steve Thompson
Email: sales@bespokeprojects.biz
Tel: 07840 997322
Office:
Tel: 01623 634589
Email: info@bespokeprojects.biz
Visit: www.handrailsuk.co.uk
How did you get started in the industry?
I became involved with the railway industry many years ago when we were looking for new markets for handrail and staircases. At the time we were supplying the education, commercial and public sectors but realised that railway stations and footbridges required good quality, strong handrails and balustrades.
I was owner and managing director of the balustrade and handrail business which I had purchased in 1996. For the last few years, I have been acting as a consultant to BPI Bespoke Project Installations Ltd. who supply and install balustrade and handrails to the Rail industry as well as other market sectors.
Tell us about your career before you joined BPI?
I began employment with an engineering apprenticeship in heavy engineering, moving on to engineering design. I then moved from the Northeast of England to East Anglia and into medium engineering on the design of pile driving hammers and earth boring rigs. From this I moved into management in light engineering, in particular the design, manufacture and installation of staircases and handrails, eventually buying the business.
What challenges have you faced in the industry?
The construction market has for many years, been ‘feast or famine’. Some areas dependent on government spending others on commercial ‘fashion’ but the railway sector appeared to be steadier. However, like most construction projects the most difficult area to accommodate as a manufacturer is that of site delays. A bespoke product cannot be manufactured in advance. It needs actual site dimensions to be taken before manufacture can commence. A site delay means that one minute there is a full load
in the factory, then a project is delayed, and other work needs to be found very quickly. Of course, when the work has been found then the delayed contract is required!
This situation always requires the company to be very flexible both in the method of working and in the working the extra hours needed to keep to the revised programme.
What success have you experienced in the last twelve months and how do you measure success?
We have continued to receive orders for railway stations because of supplying and installing a product that exactly met the customers’ requirements on previous railway projects. It meets all the relevant standards, has a long-life span and requires the absolute minimum of maintenance. This gives product sustainability and a low cost over the life of the product.
How has technology developed since you started in the industry?
Many years ago, when I started in engineering, drawings were prepared on the drawing board and design calculations required the use of slide rules and trigonometry tables. CAD has dramatically changed this for the better. It has speeded up the process and reduced the risk of error and with the internet and emails, efficiency has improved. Good communication is essential and mobile phones are now used for much more than simply speaking to each other. In the workshop, automation has improved efficiency although old fashioned craftsmanship is still needed with some products. Of course, all these improvements have meant that different skills are required. Health and Safety has improved dramatically over the years.
What types of products and services do you offer?
BPI Bespoke Project Installations is a family business specialising in the design manufacture and installation of quality balustrade and handrails. Originally a company specialising in the installation of various engineered products for the construction industry, the company decided to move into manufacturing some of the products it had been installing, namely, balustrade and handrails. It later continued its development by adding design to its manufacturing and installation activities.
The balustrade and handrails are manufactured in Stainless Steel, Aluminium and PVC sleeved galvanised steel, (the original ‘warm to the touch’ handrail), which is DDA compliant and excellent for heavy pedestrian traffic areas. Product development led the company to invent the original ‘warm to the touch’ handrail and develop this so that it incorporates LED lighting within the handrail.
This product (Stargard) has now been installed in over 20 railway stations, as well as schools and many public buildings. The company considers its employees, customers, quality, service and product development to be top priorities.
Which
The products are supplied to the Public, Private, Commercial and Railway sectors of the market, and are installed throughout the UK mainland. Shopping centres, council offices, schools, hospitals and private developments are all typical applications for the companies products.
What is your USP (Unique Selling Point)?
Apart from high quality, the company has unique selling points such as ‘Stargard’ the original ‘warm to the touch’ handrail, which is galvanised steel, sleeved after fabrication with 4 mm thick PVC. Individual LED lights are now supplied fitted into the handrails, both ‘Stargard’ and stainless steel. A new handrail surface finish is currently undergoing initial manufacture and trials. This will bring something completely new to the marketplace. The company is always looking to develop new ideas with ‘unique selling points.’
What new strategies do you have?
The overall strategy is to continue to develop existing products whilst watching market trends, and looking for associated products that, in the main, can utilise existing skills and processes. New products must be complimentary to the existing.
What do you think is the biggest challenge currently facing the rail industry?
A big challenge for the industry, and for the manufacturing and construction industries too, is that of a shortage of good skills. Wherever we look around us, almost everything has been manufactured, and, the machines to make the products have to be manufactured, yet we have not been carrying out enough formal training to have these skills for many years. We have great difficulty in finding good welders and
fitters. It is, in my opinion, essential that proper ‘training schools’ are set up as soon as possible otherwise the problem will only get worse.
Another problem for the rail industry is keeping / increasing the passenger numbers. The current station upgrades will obviously help here, but timetable efficiency is another key area for improvement.
At some point, every company will face the question of how to continue maximising earnings from their current business practice whilst also investing enough in innovation so they can turn a profit in the future. How can a company achieve the necessary creativity to innovate without compromising their existing business?
Improved efficiency linked to new products and markets is the future of the business. Existing employees must continue to be trained in the latest developments of materials, equipment and processes, and new employees with new ideas brought in to add to the ‘mix’.
Visits to suppliers and customers sites to understand suppliers and customers processes and requirements will allow employees to understand the needs of others and accommodate these needs into their area of work.
‘Automation has improved efficiency although old fashioned craftsmanship is still needed.’
TENSOREX C+: Spring Automatic Tensoning Device
FOR TODAY´S AND FUTURE CHALLENGES
Our Expertise for Railway and Tramway:
- Railway Catenary Systems
- Tensioning
- Insulation technology
- Power supply
- Safety equipment
Insulators
Safety Equipment
Bonding Connectors
Catenary Clamps
Mosdorfer Rail Ltd. 2 – 4 Orgreave Place, Orgreave Sheffield S13 9LU, South Yorkshire, UK
Phone: +44 114 3878370
E-Mail: OrdersRailUK@mosdorfer.com
Droppers
‘Lunch is for wimps’, so said Gordon Gekko in the film Wall Street. This often-quoted phrase is memorable because, in a society that often glorifies overworking, many think it is true
However, I believe it is essential to recognise the value of working smarter, not harder, for our mental health. In today's fast-paced world, the idea of working harder has been ingrained in our minds as the key to success. However, recent studies and experiences of individuals have shed light on the importance of working smarter, not harder, not just for productivity but also for our mental health. In this article, we explore the value of adopting a smarter approach to work and how it can positively impact our overall well-being.
We need to understand the basic principle that smart working is not the same as work avoiding. When I was 17, I worked in a bakery, the company didn’t feel compelled to pay overtime. I set about reorganising the layout of the bakery and changing the order of production, reducing the reliance on unpaid overtime to ensure full production. The manager of the bakery said to me one day: ‘If there is an easy way to do something you will find it,’ I said: ‘Thank you’, to which he replied: ‘It wasn’t a *** compliment’. As it happens, by the time I was 18, I was the manager of that bakery. Working smarter doesn't mean avoiding hard work altogether; it's about optimising our efforts and resources to achieve better results. It involves prioritising tasks, leveraging technology, streamlining processes, and focusing on efficiency rather than mere effort. By working smarter, we create a balanced approach that emphasises productivity while protecting our mental health.
One of the most significant benefits of working smarter is the reduction of
stress and burnout, regardless of your role as a manager or an assistant. When we constantly push ourselves to work harder, we risk overwhelming our mental and physical capacities. By prioritising tasks, setting realistic goals, and embracing productivity tools, we can alleviate excessive workloads and create a healthier work-life balance. This approach allows for more time for self-care, relaxation, and pursuing activities that bring joy and fulfilment.
When we work smarter, we free up mental space and energy, allowing us to be more present and focused on the task at hand. By avoiding unnecessary distractions and implementing strategies like time blocking and prioritisation, we can devote our full attention to important projects. This enhanced focus not only improves productivity but also nurtures creativity and innovation, as our minds are not preoccupied with constant stress and fatigue.
Increasing efficiency and productivity is not a by-product of smarter working, but the fundamental aim of working smarter, because being more efficient with our time and resources has so many benefits beyond our working environment. By identifying and eliminating time-wasting activities, implementing automation tools, and leveraging our strengths, we can accomplish tasks more effectively; this newfound efficiency not only boosts productivity but also instils a sense of accomplishment and fulfilment, that leads to increased job satisfaction and improved mental well-being.
Adopting a smarter approach to work allows us to prioritise and allocate time for activities beyond our professional
responsibilities. By establishing boundaries, setting realistic expectations, and practising self-care, we can cultivate a healthier worklife balance. This balance is crucial for mental health, as it prevents the detrimental effects of overworking, such as chronic stress, fatigue, and strained relationships.
Chronic stress refers to a prolonged state of psychological and physiological tension that occurs in response to ongoing or recurring stressors. Unlike acute stress, which is a temporary and manageable reaction to immediate threats or challenges, chronic stress persists over an extended period and often lacks a clear endpoint and can have detrimental effects on both mental and physical health. Prolonged exposure to stress can contribute to the development or exacerbation of mental health conditions, including anxiety disorders, depression, and burnout. It can disrupt cognitive function, impair memory and concentration, and lead to emotional instability.
It can also take a toll on the body, increasing the risk of numerous health problems. It can weaken the immune system, making individuals more susceptible to infections and illnesses. Additionally, it can contribute to cardiovascular issues, such as high blood pressure, heart disease, and stroke. Digestive disorders, sleep disturbances, headaches, and muscle tension are also commonly associated with chronic stress.
By embracing strategies that enhance efficiency, reduce stress, and foster work-life balance, we can experience increased wellbeing and satisfaction in both our personal and professional lives. In retirement, when we look back on our lives are we more likely to regret the time not spent at work, or the time not spent with loved ones? Remember, true success lies not in the quantity of work accomplished but in the quality of life we lead. So, let's work smarter and nurture our mental health along the way!
‘By identifying and eliminating timewasting activities, implementing automation tools, and leveraging our strengths, we can accomplish tasks more effectively.’
Joining HUBER+SUHNER as an RF Application Engineer in 2015, Antonio has risen through the ranks of the company and now holds the title of Vice President MM S&BD Railway. He has previously worked as a Project Engineer at Alstom Power, and as a Test and Development Engineer at RUAG Space.
HUBER+SUHNER offers customers around the globe products and services for their electrical and optical connectivity needs. The company focusses on the three main markets of industrial, communication and transportation which are addressed with applications from the three technologies radio frequency, fiber optics and low frequency.
Want to know more about HUBER+SUHNER?
Email: railway-marketing@ hubersuhner.com
Visit: www.hubersuhner.com/en
How did you get started in the industry?
My journey in the railway industry started in Portugal with a three years electromechanics apprenticeship from 1994 to 1997, together with the train operator CP Portugal. I then joined HUBER+SUHNER in February 2015.
How did you start at HUBER+SUHNER and what is your role within the company?
I started at HUBER+SUHNER in February 2015 as an application engineer for the Aerospace & Defence Market. Now I lead the railway market strategy and business development for North & South America. In my day-to-day business, I maintain a strong customer engagement, support our sales force, attend market related events and scout the industry for new technologies as well as new partners.
Tell us about your career before you joined HUBER+SUHNER?
After completing my education in Portugal, I moved to England where I spent eight years in the electronics manufacturing industry as an assembly technician and test engineer. Prior to moving to Germany, I was working for Airbus Space UK as a test engineer working on communication satellites. While living in Germany and still with Airbus Space I held the A.I.T (Assembly, Integration, Testing) responsibility for scientific payloads for the Space Station. In 2009 my career path shifted to Switzerland where I spent a few more years in the aerospace industry until joining HUBER+SUHNER in February 2015.
What challenges have you faced in the industry?
Industrial competition is always tough but exciting at the same time. Presenting and pushing new disruptive technologies into the industry can be very challenging.
What success have you experienced in the last twelve months and how do you measure success?
My family and I moved to the US during the Covid-19 pandemic, and we’ve been able to watch our children flourish in their new home/environment. This also meant supporting my wife as she returned to work after being a stay-at-home mum for 14 years. I have made new friends in the industry, winning new projects, strengthening HUBER+SUHNER presence in the Americas and laying the path for future successes. Success is not always measured with a $ sign: watching the industry adapting to new ways and technologies can also be considered as a success.
What does sustainability mean to you?
Sustainability means meeting our own needs without compromising the ability of later generations to meet their own in the future. In addition, we also need personal and professional social sustainability to maintain a healthy way of living.
How has technology developed since you started in the industry?
Technology in the railway industry has been growing steadily over the last ten years. From the implementation of the first generation of onboard passenger Wi-Fi systems to the integration of safety related and monitoring systems. Now, more than ever, the arrival of 5G in the industry is enabling further innovations and digitalisation, such as artificial intelligence and communication systems. These can now coexist within one digital ecosystem, and I look forward to seeing future developments in this industry going forward.
How long has your company been in business and what types of products and services do you offer?
HUBER+SUHNER has been in business since 1864. Our products deliver high performance, quality, reliability and a long service life – even under the toughest of conditions. We offer our customers around the globe outstanding products and services for their electrical and optical connectivity needs. We focus on the three main markets: industrial, communication and transportation. These are addressed with applications from crucial technologies such as radio frequency, fiber optics and low frequency.
What are some major projects you’re currently working on?
We are currently working on some projects devised to support the modernization and digitalisation of the railway industry in North America. We hope to share some of the details with you all soon!
What are some standout projects you’ve been involved in over the years?
There are far too many to mention! But I’m proud of the impact HUBER+SUHNER has had through our projects across the globe. Be it the implementation of passenger Wi-Fi on board the TGV high speed trains in France, onboard fiber optics to a CBTC System in Brazil or an onboard passenger entertainment system in the Czech Republic, our solutions are making a difference to both operators and commuters. I’d also like to mention the implementation of a passenger information system in Peru, which was another great success.
What types of companies do you collaborate on projects with?
HUBER+SUHNER is a trusted supplier and holds a strong engagement with international train builders, original equipment manufacturers (OEMs) and system integrators. As part of my day-today business, I tend to collaborate with any company that has a need for a specific application and where a HUBER+SUHNER product can facilitate the end result.
What would you say is the most exciting technology in the industry?
I’m not sure I can name just one, but 5G in particular is very exciting and is already proving to be a strong technology enabler for the ongoing industry revolution.
What do you think is the biggest challenge currently facing the rail industry?
There are always common issues regarding supply chains and funding, but there can also be hesitancy within the industry to accept new technologies. I would say retaining a strong workforce is essential in overcoming these, but maintaining one is a challenge within itself.
What are your hopes for the new regulatory bodies, such as Great British Railways?
For newer bodies, the goal should be to watch, learn, cooperate with the similar bodies around the world, then unify/ standardise. This will go some way to accelerating future developments within the rail industry.
What are your views on collaborative working?
I think that this is key for anything that we do in our daily business. Whether we’re talking about an internal collaboration or a customer collaboration, we always need to work as a team to achieve our goals, financial or otherwise.
In terms of technology, how do you anticipate things might change in the next five to ten years?
We are currently experiencing a digital revolution in the railway industry. At the rate of innovation we are currently seeing, within the next five to ten years I expect that we will see a more efficient and green industry, and a preferred way of transportation.
How are trackside technologies benefiting rail operators and their customers?
Trackside technologies are playing a crucial role in the collection and transmission of data so essential to control centres and stations. Conditional data provided from train to trackside are being used by operators to detect and repair malfunctioning or disrupted trains. This is enabling a reduction in operational costs, as it allows condition-based maintenance to take place. Data provided by these devices is also providing real-time updates for CCTV cameras, passenger information systems (PIS) and ticketing systems found within the stations. Not only does this help establish safer, efficient services but also improves customer and staff satisfaction, as they gain a greater understanding of the effects on a schedule.
Why is CBTC so important to the railway industry?
Communication based train control (CBTC) and other digital systems are essential in supporting train-to- ground applications. No matter if it's a metro, underground, regional and intercity railway, train control can be used to efficiently condense transportation cycles, whilst increasing track capacity and reducing any significant gaps in service for commuters. This has only grown in significance with the increasing digitalisation of the industry.
Which HUBER+SUHNER solutions are key to supporting the ongoing revolution?
It would be easier to advise which are not! Ever since the portfolio was first developed, the SENCITY® Rail antennas have been supporting operators in meeting the special requirements needed for all elements of their network. Antennas such as the SENCITY® Rail ACTIVE Rooftop, SENCITY® Rail and SENCITY® Rail MIMO+ all provide a solution suitable for high current and high voltage applications. We designed these with digital train control systems in mind, so the portfolio establishes reliable connections, whether WLAN, GPS or cellular, to make sure rapid and accurate transmission of data from the train or trackside can be achieved.
For trackside and metro applications where high data transfer rates are crucial, the SENCITY® SPOT antenna portfolio supports Wi-Fi 6E bands, coming in a range of sizes and types to suit our customer’s needs. Within a tunnel, CBTC Yagi Antennas enable stable communication between train to station and ensure customers and staff can stay informed of any essential updates.
There is no doubt rail systems have and will continue to become more sophisticated. That’s why our cables and cable systems are designed to be ‘future ready’, with preassembled, ready to connect fiber solutions to serve the rapid and safe installation of connections both within the train and by the trackside. Fiber optic technologies are the best option when it comes to transmitting data quickly, supporting the antennas to put it in the hands of rail staff, control centre operators and the commuters themselves. All our cables comply with the latest rail and fire safety regulations, so our customers know they are safe, robust and won’t let them down.
‘For newer bodies, the goal should be to watch, learn, cooperate with the similar bodies around the world, then unify / standardise.’
‘There is no doubt rail systems have and will continue to become more sophisticated. That’s why our cables and cable systems are designed to be ‘future ready’’
‘No matter if it's a metro, underground, regional and intercity railway, train control can be used to efficiently condense transportation cycles, whilst increasing track capacity and reducing any significant gaps in service for commuters.’
Trackside
• Radio frequency connectivity
Rolling stock
• Wires and cables
• Cable systems
• Radio frequency connectivity
• Fiber optic connectivity
Our market-leading connectivity solutions for data and power transmission are designed to meet the unique requirements of the railway industry, including space-saving and lightweight RADOX® cables, high performance SENCITY® Rail antenna portfolio as well as future-proof fiber optic systems. Moreover, they are keeping operating costs down and the environmental impact low.
Critical infrastructure is a broad area, at least from a cybersecurity point of view. It refers to the essential services and industries that underpin not only national, but global economies. When discussing these services, none would be functional without reliable and robust supply chain and transportation networks. Compromise these, and threat actors could cripple an industry, or even an entire country’s operations, in mere months. This potential for such widespread, indiscriminate disruption has made the transport industry, especially key logistic routes like rail networks, a prime target for threat actors.
For instance, our research into the threat landscape unveiled insights into tracked telemetry across the globe. We found that, in Q4 of 2022, the global transportation sector had become the new focus of nation-state backed advanced persistent threat (APT) groups, comprising a significant 69 per cent of tracked attacks, compared to 27 per cent in Q3. Not only this, but transportation has also become the fifth most targeted by ransomware advanced persistent threats (APTs) – with approximately twelve per cent of observed attacks being attributed to the sector.
Transportation and shipping organisations are currently at risk of attack from all sides. While these organisations do have some security strategies in place to protect critical networks, the recent shift in focus from threat actors has highlighted the need for cybersecurity to become a core business priority.
There are a few strategies that transportation and rail organisations can look to implement to further enhance their security and keep in step with an everevolving threat landscape.
A core aspect in ensuring critical infrastructure is protected is through
mapping operational supply chains. Having a complete visual plan of all the ins and outs seems simple enough, but in reality, gaps can expose organisations to significant vulnerabilities. Having blind spots when it comes to a threat surface could, ultimately, leave a system vulnerable to attack.
Fortunately, there are resources available to critical services offering guidance in how to undertake a full inventory of suppliers, subcontractors, and logistic routes. For example, one such resource is available on the NCSC (National Cyber Security Centre) website, sharing guidance into mapping supply chains to better manage risk. Further, new European regulations such as the NIS 2 Directive have been introduced, which outline cybersecurity measures essential service providers can follow, to manage risk.
By visualising and gaining a better understanding of the threat landscape as a whole, railway and transportation infrastructure companies can map potential attack routes within critical operations. Weaknesses along the transportation supply chain can be identified to provide enhanced insight into cybersecurity considerations and improve responsiveness to emerging situations.
However, supporting these functions is an ongoing effort. There is an onus on organisations to collaborate and work together, sharing gathered intelligence and building a robust and secure network across industries.
Resourcing these functions and protecting supply chains must be a core element of an organisation’s attitude to business functions. Our research showed that while 94 per cent of cybersecurity professionals agree that there is a well-defined ownership of cyber risk at a board level; a third (31 per cent) feel that cybersecurity has been deprioritised when it comes to business objectives set by the c-suite and above.
Having a strong top-down approach to cybersecurity is vital in aligning management and security goals –organisations operating with rail networks need to be supported by the appropriate tools when keeping core infrastructure and important business assets safe.
But the best way to really cement these themes as a core business priority is through implementing and embedding security procedures. Ensuring employees and subcontractors have a clear understanding of these measures and how to report breaches and compromises is also crucial. This is not only from a regulatory aspect, but also in improving responsiveness in the event of a breach, to reduce impact and risk.
Our research also showed that 89 per cent of cybersecurity professionals find their organisational approach to cybersecurity is too siloed. It’s therefore important for transportation, logistics and rail companies to find a balance by implementing technologies that allow them to build a level of organic protection.
There are several ways to achieve this, but fundamentally, sophisticated tools yield sophisticated results. Upgrading existing legacy infrastructure to use predictive monitoring through machine learning and artificial intelligence can take the pressure off teams, automating breach detection and improving responsiveness.
Essentially, having a living, breathing security system that works to protect key transport infrastructure on an ongoing basis allows organisations to centralise security. Coupled with a collaborative ecosystem, intelligence can be gathered to learn from previous incidents, correlating threat telemetry and implementing pattern recognition to threats can be quashed even before they have any real impact.
Ultimately, it is important to consider the bigger picture when it comes to cybersecurity. Organisations that rely on transportation and rail lines as a part of the critical business infrastructure need to understand the significance of having insufficient cybersecurity protection. Trends have shown that threat groups have the sector in their sights now, and their focus is only going to grow – it’s already grown at an alarming rate.
Seeing the forest for the trees is part of the solution, but the tone at the top must be conducive to providing sufficient support to cybersecurity professionals in their defence of their logistical routes. Mapping supply chains and all the players on the board, resourcing upgraded legacy tools, and integrating new innovative technology as a part of organisational cybersecurity policies and procedures are the cornerstones to ensuring critical infrastructure is protected.
Steve has over 35 years’ experience in the global railway industry, with a background in railway operations and experience in successfully delivering numerous railway and ports projects ranging from small and medium sized feasibility studies, right through to the delivery of major railway infrastructure projects around the world.
iPort Rail is a high-volume inland port just outside Doncaster, South Yorkshire, offering sustainable logistics solutions with connections to regional, national and international supply chains. It is part of the award-winning, major multimodal logistics hub, iPort, which has capacity for six million square feet of industrial and logistics warehousing at the heart of the country’s transport networks.
Tel: 01302 590 759.
Visit: www.iPortRail.com
Address: iPort Rail, Railport Terminal, Railport Way, New Rossington, Doncaster DN11 0BQ
We are the UK’s fastest growing rail freight facility, and since opening in 2018 we have rapidly increased services and routes across the country. Our state-of-the-art terminal can accommodate the longest trains running to and from deep-sea ports across the country and connecting with Channel Tunnel routes. We hold Authorised Economic Operator status from the UK Government and offer market-leading customs facilities away from seaports. Most importantly, we have a great team of experienced logistics professionals who work closely with clients to solve their challenges and offer tailored solutions to meet their needs.
Our main focus is of course rail freight, which was the original driver for the entire iPort logistics hub, but from the start it has been important to offer a truly multimodal service from port to warehouse door for businesses of all kinds and sizes across the country.
This means working and integrating with the full range of supply chain businesses, including road haulage, customs and freight operating companies.
In terms of goods, retail, particularly ecommerce, makes up the majority of our cargo and also supports iPort’s warehouse customers, but we can ship almost all kinds of goods and more and more businesses are turning to rail freight as they look to cut carbon in their supply chains.
What types of products and services do you offer?
We support cargo journeys from port of entry right up to the warehouse door and help regional/national businesses to export goods to the EU and the Rest-of-the-World. With an 800-metre length reception siding, capable of accommodating the UK and Europe’s longest train lengths, plus two 400 metre load/unload sidings, iPort Rail can handle up to eight trains per day and offers secure storage of up to 1,500 TEU of laden and empty containers.
The terminal operates 24 hours a day, six days a week and the rail yard has been designed to maximise operational flexibility and efficiency for rail and road movements, while keeping costs and time to a minimum.
How passionate are you about sustainability in the rail sector, and how do you go about sourcing the materials for your products?
In a trading environment where sustainability is increasingly important, more people should be aware of how rail freight can help businesses decarbonise without compromising on supply chain efficiency.
It is a faster, greener, safer and more economical way of transporting goods compared to long distance road journeys. Every tonne of freight carried by rail produces at least 70 per cent less carbon dioxide than if it was moved by road and as a sector rail freight contributes less than one per cent of total UK CO2 emissions, compared to 21 per cent by road transport. On top of this, iPort’s occupiers use electric tug and trailer services which provides a door-to-door container transport service, cutting the need for HGV transport to make short journeys between the terminal and its warehouse, just one of the measures in place to help decarbonise supply chains. Since opening, iPort Rail has helped its customers cut over 600,000 tonnes of CO2, a figure set to increase over the coming months.
At the same time, we are working with various partners and the local authority to reduce our own carbon footprint, including being part of Doncaster Council’s Hydrogen Project.
When a client comes to you with a particular problem, what’s your process for coming up with a solution, and how closely do you work with clients throughout the projects?
Our terminal is managed by a dedicated, professional and experienced logistics professionals using modern terminal management systems. They also have a very strong connections in the sector and are happy to offer new ideas as well as solid on the ground support.
So our most successful method for helping clients is very simple and often involves little more than a site visit. Many of our customers are ‘new to rail’ and once they are able to visualise our operations and articulate their logistics needs, we simply overlay this on to our existing rail operations. Where needed, though, we have sourced dedicated services to help with high volume campaigns, which often requires a flexible and rapid final-mile service to avoid charges by the shipping companies.
What types of companies do you collaborate on projects with?
For us collaborative working is essential. We work closely with freight operating companies, their customers, road haulage businesses, other inland terminals and Network Rail to make current activity more streamlined as well as developing new strategies and ways of working to meet customers’ needs.
We are also an integral part of the local economy, working closely with the local Council and Chamber of Commerce and supporting their aims for the area as much as we can. Local politicians and government officials visit the site regularly and the team also collaborates with Government agencies, such as Sheffield City Region and Invest in Yorkshire.
What new developments and strategies do you have?
With the terminal running very successfully, we are now exploring potential for increasing our size to offer more services as well as the number of containers we can store here. Warehouse development at iPort continues to increase, and more customers are taking advantage of the port to door services on offer, but we are also keen to continue with businesses based further afield and needing short-distance road connections alongside long-distance rail.
We also worked hard to become one of the UK’s first inland port facilities to provide customs clearance, offering customers an alternative to seaport border controls. We operate a Customs Rail Terminal, approved by HM Government Border Force, with a Customs Examination area and a Temporary Storage facility as well as holding AEO (Authorised Economic Operator) status that provides an internationally recognised mark of quality and security.
We are External Temporary Storage Facility (ETSF) approved and inventory linked. For our customers, this means local customs clearance, avoiding the congestion of larger ports, viable alternative trading
routes between the UK and EU via the Channel Tunnel, warehousing and storage for goods until required, with duties payable on release, shorter transit times to end destination post-customs helping maintain security for goods and support managing trade documentation.
If you were in charge of the UK rail industry, where would you target investment and/or look for improvement?
There is huge potential to build up commercial routes and opportunities across the country to proactively support UK plc as well as reducing current friction points. We should look further than the proposed border target operating model (TOM) and take a holistic approach to goods not just coming into the UK but how they can move around the country more effectively.
Within that, there should be significant value attached to inland rail terminals and investment in a hinterland rail freight strategy to support the rapid movement of goods away from congested road networks and with the carbon-reduction benefits this will bring.
iPort Rail is a high-volume inland port close to Doncaster, providing lower carbon logistics solutions for regional, national and international supply chains.
Our experienced and highly professional team works closely with customers, from strategic advice to practical support, always focussed on the rapid movement of goods www.iportrail.com
What do you expect to be the biggest challenges that come from this transformation of the railway industry?
For us, rail needs to become the obvious choice over road when it comes to longdistance freight movements.
Passenger improvements are always important but at a national, strategic level this needs to be balanced with a recognition that freight has an essential part to play in the success of the network and its contribution to the UK economy and, if done well, further investment will bring greater benefits.
Above all, reliability is essential, which includes resolving industrial action as well as putting in place clear strategies and practical changes to help all trains run more efficiently as the demands placed on them increase.
Powerful disruptive trends over recent years have lifted resilience up the rail agenda – yet new research shows there’s a risk that the focus is already fading
After an uneasy past three years, is the worst behind the rail sector? If you think it is, you’re in agreement with the majority of our survey respondents. Our Europe-wide study of transport leaders found that 63 percent of those in rail believe the worst has already happened. This is the highest score across all modes. So, what do they know that rail doesn’t?
More worryingly, almost two thirds (65 percent) of rail leaders have no plans to increase their investment in resilience. This, despite the fact that the majority recognise that resilience is a strategic imperative, and that conventional resilience plans, ‘switched on’ in the event of a flood, strike action or another disruptive event, are no longer enough.
Instead, resilience needs to be an always-on priority during good times and bad. This is the only way for rail to deal with sustained, compounded disruptive events. These include the ongoing impact of the Covid-19 pandemic, shifting travel habits, economic and labour challenges, the sustainability imperative, and overhauling legacy infrastructure.
Because, while rail has a history of battling through disruption to deliver, and rising to the challenge, the disruptive landscape has changed – and so too must the resilience response. To achieve this, there are three areas of focus that can help drive change:
Our survey found that more than four in ten rail leaders say ‘more disruptive events’ are the number one accelerator of resilience as a strategic priority. Effectively, almost half of rail organisations are reliant on fresh disruption to reignite a sense of urgency. They are hooked on the drug of disruption, where resilience is only activated in response to a disruptive event.
And while rail is very capable at responding to operational disruptions, our findings come at a time where conversations are ongoing about crucial strategic challenges. These include proposed rail reform legislation, advances in technology and automation, and a growing skills gap against a backdrop of increasing tensions in industrial relations.
To tackle these strategic challenges, rail needs to do more than respond to disruptive events on an ad-hoc basis. It needs to build and embed a resilience mindset across the industry. This means allocating time and headspace to longer-term strategic goals – not just the immediate operational challenges.
In some instances, this means leaders need to step back from their immediate problems to focus on the future. Delegation can feel uncomfortable, but leaders need to be free to lead. It is this strategic resilient mindset that can unhook rail leaders from the drug of disruption and set them up for enduring success – while developing rail leaders of the future.
Joanna Grove-Lafarge, Sally Shellum, and Sara Ulrich are rail resilience experts at PA Consulting. For more information, visit www.paconsulting.com/industries/ transport/the-always-on-advantage
GLASGOW ROAD TO CLOSE FOR A YEAR FOR BRIDGE WORKS
Shields Road on the south side of Glasgow will close to traffic for a year to enable the demolition and rebuilding of the bridge over the railway. The bridge has been subject to weight restrictions for more than 20 years, and the work will be undertaken by Network Rail and Glasgow City Council. When complete, in summer 2024, the bridge will be stronger, wider and better able to handle the size and volume of traffic that needs to travel over it.
SERCO BIDS A FOND FAREWELL TO THE CALEDONIAN SLEEPER
The night of Friday 23 June saw the last Caledonian Sleeper services run under Serco’s management when the Caledonian Sleeper franchise expires almost eight years and three months since Serco’s inaugural service departed from Fort William on Tuesday 31 March 2015.
ANDREW HAINES CONFIRMED AS KEYNOTE SPEAKER AT RIA ANNUAL CONFERENCE
Andrew Haines OBE, will address RIA’s award-winning Annual Conference & Dinner 2023, taking place 1-2 November at the Millennium Gloucester Hotel, London. Alongside Andrew Haines, a number of major keynote speakers have also been confirmed for the conference, including Beth West, CEO, East West Rail, Steve White, MD, Southeastern, Maggie Simpson OBE, DG, Rail Freight Group, Martin Tugwell, Chief Executive, Transport for the North, and Emma Porter, MD, Story Contracting, with many more to be announced in the coming weeks.
The disruptive events of the past few years have brought multiple resilience learnings for rail leaders. Our survey found that these lessons include the need to plan for global disruption, not just local; that resilience can be an opportunity to do things better; and that it calls for a breadth and depth of skills.
At the same time, rail leaders have learnt that resilience is an opportunity to gain momentum – providing they embed stronger governance; provide clear resilience leadership and accountability; and invest in technology and automation.
Effectively, disruptive events have provided an opportunity for organisations to sharpen their resilience muscle across the resilience lifecycle: prevent, detect, withstand, handle, recover, and transform.
Wargaming exercises are one way to help rail leaders to prepare for an automatic response for when disruption arrives. They help build psychological safety by taking people away from their comfort zones, removing barriers, and encouraging bold decision-making. These exercises also encourage a culture of continuous improvement, where lessons from previous disruptive events become a springboard for transformation.
Collaboration across rail can improve, according to our survey respondents. Just under half (40 percent) told us that the lack of ecosystem collaboration is a key barrier to resilience. Across all modes, rail leaders were the most likely to say that increased connectivity and interoperability across the transport system was a major challenge.
Yet there are also encouraging signs: 80 percent told us that increased connectivity – with partners, customers, technologies –‘makes us more resilient’. So, rail leaders see
the potential for collaboration to help them move towards always-on resilience but are yet to achieve it.
To drive progress, rail leaders need to stop thinking of resilience as being separate from long-term objectives such as increased innovation, sustainability, and rail reform. When asked if resilience can co-exist with these imperatives, rail scored lowest for the first, and second lowest for the second.
Imagine, instead, if rail leaders used these objectives as reasons to sustain the push for always-on resilience, and alwayson resilience as the fuel to meet these goals. By becoming more resilient across the enterprise, organisations can ensure they have the skills and headroom to shape the future agenda rather than react to the present.
After three years of unprecedented disruption, rail leaders have boosted their organisational resilience, learned of the need to embed it as an always-on priority, and glimpsed the opportunities that this permanent level of resilience can bring.
The key, now, is for this opportunity to be grasped. This is the challenge of the moment for rail leaders who need to put in place some practical steps to kick-start action.
‘Wargaming exercises are one way to help rail leaders to prepare for an automatic response for when disruption arrives.’
I have had reasonable success in writing following my lifetime investigating crime, and this summer sees the publication of my latest, a novel about the Great Train Robbery
August will mark the 60th anniversary of the crime that shocked the nation, and a previous 60 year step backwards in time takes us to Victorian times. ‘The Great Train Robbery and The South Coast Raiders’ is thus a work of historical fiction.
The best books of historical fiction always contain a good deal of accuracy. Readers seem to want as much of the truth as possible, and only falsehood to better illustrate the essential truth of the central story. That is what I have tried to do.
My efforts to provide a more accurate and wider picture of the robbery have been aided by several years of research, the active involvement of Tom Wisbey, a former Great Train Robber (and member of the South Coast Raiders), and my own extensive experience of arresting those involved in the theft of high value mails.
It is often assumed the Great Train Robbery was a one off, and it seems to follow train robberies before it had hardly
ever taken place. Yet nothing could be further from the truth. In reality, it was only the scale and audacity of the Great Train Robbery that made it unique.
From the 1850s (until the late 20th century), the railways carried the Royal Mail across the country. And from the earliest days, the mail was attacked by robbers and thieves.
By 1961, after several years of escalating mail robberies, it was obvious to all, including the national press, that a particular gang was enjoying outstanding success across the south of England. They became known as ‘The South Coast Raiders’ (and also, ‘The Red Light Gang’).
The South Coast Raiders stole high-value mails from the old British Rail Southern Region (which included trains travelling from Waterloo, Charing Cross, Victoria, London Bridge, Cannon Street and Blackfriars to stations across Kent, Surrey, Sussex, Hampshire, Dorset, Somerset, Devon and Cornwall). And the gang remained undetected right up to the time they merged
with other experienced and hardened criminals to commit the crime of the century.
The book tells their story through the eyes of an honest young man who, owing to poverty and his determination to provide for his family, is drawn into serious and violent crime, and ultimately, The Great Train Robbery.
So how much of my story is true? Most of it, but don’t expect to read an account you are familiar with. To get the most from it, park what you know about the robbery, but hold in the back of your mind just how normalised police corruption was in that time.
So, this novel contains a lot of true information about the Great Train Robbery that will probably be new to you. Only one central character is entirely fictitious (identity revealed at the end of the book), but all other central characters really did take part in the ‘Crime of the 20th century’.
Available to order from mid August in bookshops, and online in print and Kindle format.
‘A rollicking crime novel.’
Duncan Campbell, Journalist and author.
‘Fascinating and inventive… a real page-turner… a gripping narrative.’
Stewart Tendler, former chief crime correspondent, The Times
Great Western Railway has embarked on a revolutionary journey with the trial of new software that will allow customers to see realtime train service information. The four-month trial of the digital platform from rail tech developer Whoosh began at the start of May and allows customers to see real-time journey information for the train they are on as well as real-time rail and travel information for every station in the country.
The digital platform, which is being trialled on board three trains, and also at Patchway and Newton Abbot stations, is accessed by scanning bespoke station and at-seat QR codes. Customers simply scan a QR code to unlock a wealth of relevant travel information, featuring station info, onward journey planning and Welsh language options.
Whoosh’s recently patented ‘Tell Us’ functionality also enables contextualised fault reporting by passengers and staff onboard. Whoosh already operates several successful journey information services for other UK transport operators. The tech company teamed up with Network Rail last year to provide personalised information across the UK’s largest stations.
Freightliner, a subsidiary of Genesee & Wyoming Inc. (G&W), was named “Rail Freight Company of the Year” at this year's Multimodal Awards, which recognise excellence and best practise across the UK logistics industry. This is the eighth time that Freightliner has won this award.
‘It’s a fantastic achievement, especially as we were up against some of our largest competitors and was voted for by the industry and our customers’ said Becky Lumlock, interim CEO for Freightliner. ‘We are very proud of this accolade, and we could not have achieved this without the hard work and dedication of our people. We pride ourselves on our exceptional customer relationships and look forward to continuing to deliver unrivalled services to our customers.’
Running alongside the Multimodal Awards this week was the Multimodal Exhibition – the industry's annual event attended by cargo owners and shippers looking for ways to improve their supply chains and discover innovative ideas to solve their transport and logistics issues.
Freightliner exhibited once again at this year’s Multimodal Exhibition with an impressive stand that featured six digital totem screens, representing our six brand pillars, as well as interactive content screens, featuring our Intermodal3 Logistics solution. Alongside these new additions, we reused our container café and meeting room from last year, demonstrating the capabilities of our sister company, Pentalver, and their container conversions team.
New director to lead railway improvements in the West Midlands
Experienced rail industry leader Mal Drury-Rose has been appointed to the twin role of Director of Rail for Transport for West Midlands (TfWM) and Executive Director of the West Midlands Rail Executive (WMRE).
Chief People Officer appointed at The GoAhead Group
The Go-Ahead Group has appointed Carolyn Ferguson as the group’s Chief People Officer with oversight over all aspects of human resources.
A new chaplain for the Northwest and North Wales Karen Schofield has joined the railway as the new Railway Mission Chaplain for the Northwest and North and Mid Wales area.
Rail North Committee elects new Chair and Vice Chair
The Rail North Committee (RNC) has announced the election of a new Chair, Mayor of Greater Manchester Andy Burnham, and majority group Vice Chair, Councillor Susan Hinchcliffe Leader of Bradford Council.
Kilborn Consulting Limited is an independent railway engineering consultancy and design business, with over 21 years of railway experience.
We specialise in the design of new and altered railway Signalling & Telecoms systems for the UK railway infrastructure.
Our areas of specialism are:
•Signalling and Telecoms Consultancy, including technical advice & support;
•Asset Condition Assessments, Correlation and Surveys;
•Signalling & Level Crossing Risk Assessments;
•Feasibility and Optioneering Studies;
•Concept and Outline Signalling Design;
• Telecoms Option Selection Reports (including AiP), Reference System Design and Detailed Design;
•Detailed Signalling Design;
•Competency Management & Assessments;
•Signal Sighting assessments, covering the full Signal Sighting Committee process with a competent Chair.
The new office which is located in the heart of Wellingborough can accommodate all staff and visitors alike and offer widespread views across Wellingborough and the surrounding green spaces
We would be delighted to welcome you to our office to discuss your requirements and how we can support you to achieve those. Kilborn Consulting Limited 6th Floor, South Suite, 12 Sheep Street Wellingborough, Northamptonshire NN8 1BL
We are at the forefront of providing innovative technical solutions which enables our clients to meet their sustainability objectives. Our inspired thinking approach allows us to utilise our long-term expertise to work in partnership with our clients to deliver resilient, bespoke and cost efficient solutions.