P22
PERFORMANCE
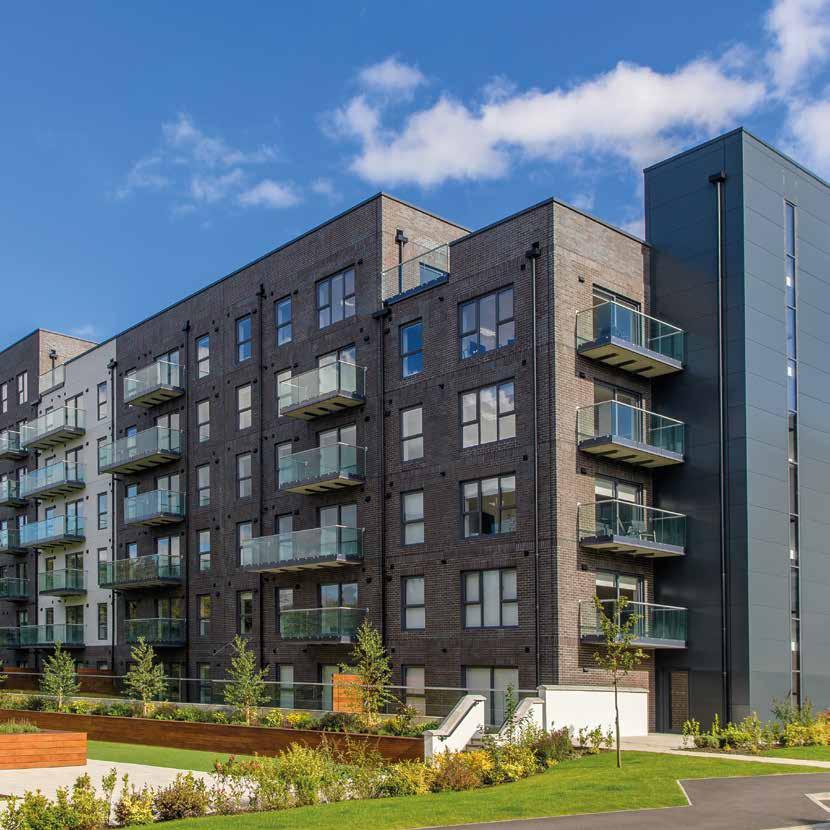
P66
25% BY 2025
Streamlining and the seven steps to offsite and modular building with Balfour Beatty
P74
The
P22
PERFORMANCE
P66
25% BY 2025
Streamlining and the seven steps to offsite and modular building with Balfour Beatty
P74
The
Masonry homes provide superior performance benefits, both in construction and in use.
The thermal performance of concrete and masonry homes can provide homeowners with the lowest energy bills because of the superior insulation, airtightness and thermal mass.
Purchasing a home is a major investment and the inherent performance of concrete and masonry provides robust and secure homes that will last for many generations.
Concrete and masonry are non-combustible protecting life and property safety for occupants. During construction, these properties also protect the developer and surrounding community from spread of flame.
Masonry walls can support precast floors which do not squeak: 48% of homeowner noise issues raised with NHBC for detached homes were creaking floors (NHBC Foundation Report NF56).
Homes built from concrete and masonry suffer less damage because they are robust, dimensionally stable and do not rot.
Visit www.modernmasonry.co.uk for:
-
-
-
FOLLOW US ON TWITTER UNDER: Twitter.com/ExploreOffsite
ADVERTISING ENQUIRIES PLEASE CONTACT:
Julie Williams // T: 01743 290001
E: julie.williams@offsitemagazine.co.uk
BACK ISSUES VISIT:
www.offsitemagazine.co.uk
FRONT COVER
Creagh Concrete
PRINTED ON:
PEFC 16-33-576 paper stock by Buxton Press
PUBLISHER:
Offsite Magazine is produced and published by Radar Communications: ©Radar Communications Ltd.
Radar Communications Ltd, 5 Darwin Court, Oxon Business Park, Shrewsbury, Shropshire. SY3 5AL
T: 01743 290001
www.radar-communications.co.uk
For offsite enquiries please contact: E: info@offsitemagazine.co.uk
DISCLAIMER: The content of Offsite Magazine does not necessarily reflect the views of the editor or publishers and are the views of its contributors and advertisers. The digital edition may include hyperlinks to third-party content, advertising, or websites, provided for the sake of convenience and interest. The publishers accept no legal responsibility for loss arising from information in this publication and do not endorse any advertising or products available from external sources. No part of this publication may be reproduced or stored in a retrieval system without the written consent of the publishers. All rights reserved.
Welcome to the latest edition of Offsite Magazine. This issue will be doing the rounds at UK Construction Week where offsite technology will be on show and under discussion as part of The Build Show and Timber Expo.
Having spoken to many disparate offsite industry insiders in the last few weeks about where they feel offsite manufacture sits in the grand scheme of Construction UK, the feedback has been overwhelmingly positive, while still openly acknowledging that hurdles to total acceptance remain from a cautious marketplace. Times are changing though. The level of interest in all methods of delivery –precast concrete, light gauge steel, engineered timber and volumetric modular – seems to be at an all-time high.
The recent Construction Sector Deal may not have satisfied everyone but its support for offsite construction was clear enough and a pivotal way to: “minimise the wastage, inefficiencies and delays that affect onsite construction and enable production to happen in parallel with site preparation – speeding up construction and reducing disruption.” Ultimately offsite manufacture is pivotal to improving construction productivity, efficiency and overall quality.
The future of offsite productivity and performance are at the heart of two industry discussions in this issue. One
hosted by Etex Building Performance delving into the world of housing and PRS and another hosted by Futurebuild – where the Offsite Hub in 2019 will be an important gathering ground for the offsite industry. More of these discussions in the following pages.
For a further peek into the future of construction we have a special feature from the Manufacturing Technology Centre – one of the dynamic centres of excellence in the UK – and the ways in which they are responding to the construction industry and standardisation, robotics and Design for X – that’s design for manufacture, assembly, maintenance and disassembly. The future is already here.
Finally, Balfour Beatty recently published a key policy statement. While many companies are beginning to consider ‘offsite and modularisation on a case-by-case basis for new schemes’, Balfour Beatty has made it a core part of its strategy with commitment to reduce onsite activity by 25% by 2025. It is hugely encouraging that a Tier 1 contractor has made a major declaration to adopt more ‘industrialised construction methods’ to boost productivity and plug skills shortages.
As always special thanks to all our contributors, advertisers and supporters.
Gary Ramsay Consultant Editor Email: gary.ramsay@offsitemagazine.co.ukCreagh Concrete are championing the use of precast concrete in the UK and are at the forefront of cutting edge offsite manufacture with its Rapidres fastrack build system, that is presently revamping central Birmingham with the Arena Central development.
Andy Ormerod, Balfour Beatty Managing Director, Plant and Fleet Services is leading Balfour Beatty’s commitment to reducing onsite activity by 25% by 2025. He explains how the new generation of industrialised construction methods has the potential to transform the way the building industry operates.
08 | Industry News
News and developments from across the UK offsite industry and wider construction arena including: ZEDpods chosen for keyworker housing, a new wave of suppliers announced for Fusion21’s modular framework and Saint Gobain place offsite as a key ‘emerging reality’ in a new industry report.
P22 |
OFFSITE: SUPPLY CHAIN ENGAGEMENT AND INTEGRATION FOR
When and how to engage with the offsite supply chain to get the most value from it is always a hot topic for discussion. Etex Building Performance recently hosted a Roundtable Event to discuss issues surrounding this and the burgeoning private rented sector (PRS) approach to housing.
74
Mark Farmer said, ‘Modernise or Die’ and whilst this message has generally been accepted by the construction and infrastructure industry, it may not be clear what ‘modernisation’ actually means. Mark Ireland, Chief Engineer, Construction at the Manufacturing Technology Centre (MTC) explains more.
28 | UKCW Embraces Offsite
Offsite is due to make its mark on UK Construction Week (UKCW) by showcasing all its advantages in its very own dedicated Offsite area within the Build Show alongside an additional presence at Timber Expo.
30 | Offsite: Essential to Sector Deal
After some delay, the Government finally launched its much-anticipated Construction Sector Deal (CSD) in July, with a vison to develop an industry able to respond to the pressures of changing demographics, technological change and sustainable building.
34 | A Rising Global Profile
In the past few years, the tall building industry has become increasingly interested in the use of timber as a major structural element in skyscrapers. We hear from Daniel Safarik, Senior Editor at the Council on Tall Buildings and Urban Habitat (CTBUH) on what the future may have in store.
42 | Influencers and Disruptors
As Managing Director of Cogent Consulting, Darren Richards is well placed to comment on how the world of offsite manufacturing has gained traction over the past 12 months. Here he shares his views on how the market is developing and which factors are influencing the sector.
44 | Precast Revamp for Police HQ
Lancashire Constabulary’s new divisional HQ has reached completion and features offsite precast technology to provide one of the UK’s largest custody suites, with innovative design and a more secure environment for officers and those in custody.
52 | The Power of Steel – delivering cost and programme certainty
Driven by the demand for more predictability throughout the construction process, EOS are geared up and ready to bring new systems to the market. Managing Director, Steve Thompson discusses the benefits of light gauge steel (LGSF) for load-bearing applications.
68 | Futurebuild Think Tank
After a turbulent few years, confidence is returning within the construction world with interest in offsite construction in particular on the rise. Futurebuild and Offsite Magazine recently hosted a special ‘think tank’ session to discuss progress and understand what the future may hold.
72 | Building Skills for Offsite Construction
The development of skills in offsite construction could revolutionise the construction industry and help provide a solution to the UK’s housing shortage. Ben Lever, CITB Future Skills Manager outlines how.
MODULAR MATTERS conference and exhibition will create a platform to learn directly from leading sector designers, engineers, architects and manufacturers on how to apply innovative volumetric modular technology and also dispel the myths on design constraints.
The event provides a dynamic and interactive learning experience for all visitors and a fantastic business development opportunity for exhibitors and sponsors.
ONLY A FEW DELEGATE TICKETS REMAINING
Creagh Concrete are championing the use of precast concrete in the UK and are at the forefront of cutting edge offsite manufacture with its Rapidres fastrack build system, that is presently revamping central Birmingham with the Arena Central development.
A collection of high and low-rise shops, offices and residential buildings are emerging around the existing Alpha Tower, a Grade II-listed office built in the 1970s and one of Birmingham’s most well-known architectural landmarks.
Main contractor Galliford Try is now two-thirds of the way through a £40million 323-apartment Private Rented Sector (PRS) scheme for client Dandara Living, one that will significantly boost the number of homes available in close proximity to Birmingham’s city centre. Comprising two blocks of 17 and 22 storeys linked by bridges at each level, the
1development will feature studio, onebed and two-bed apartments with balconies across all elevations.
The building is located within the footprint of a subterranean car park that used to serve the Alpha Tower and hotel behind. That car park was a two-level facility built below ground with an open central section. The new building has been launched largely through that central void, with the reinforced concrete car park broken away in areas to accommodate the new development. The building ties into the remaining sections of car park to provide spaces for its residents.
“Some of the car park has been incorporated into the design for the development,” says Aidan Smith Project Manager, Galliford Try. “Our temporary works department had to look closely at the design of the car park to accommodate the different loading on the structure during the demolition process, as well as tying it back into the new building as it came up from the ground.”
The structural frame from Creagh
Concrete for the new dual-block building is largely precast concrete with a cast in-situ reinforced concrete basement and ground floor featuring a 1.8m-thick transfer slab – cantilevered across the south-east corner. A precast concrete frame springs from this slab from levels 1-22 on block A and 1-17 on block B.
The decision to use precast concrete systems for the bulk of the building’s structural frame, cladding and balcony units was taken at an early stage on the project, with Dandara wanting a robust finish on the building, which would limit the amount of ongoing maintenance required.
With Creagh’s precasting facilities in Northern Ireland able to provide both the structural units and the acid-etched finished architectural cladding units for the facade, the Galliford Try team was quick to bring the firm in as main supplier on the project. “We did lots of due diligence,” adds Adrian Smith. “We felt Creagh could deliver and complete the work on-time and we liked its in-house design capability. The team there spent months perfecting the mixes to make sure it could manage to consistently produce the dark grey of the facade.”
The scheme uses the Rapidres fastrack build system. The bulk of the Arena precast panels measure 8m in length, with the floorplan based on a similar 8m grid. They arrive onsite from a holding point just outside the city and are lifted directly into position. The inner wall panels are formed from 180mm thick solid concrete and arrive with a perfect surface that just requires a few coats of paint. The insulated structural facade panels are 300mm thick and require no further treatment onsite.
The exclusive Forbes Place development at Stoneywood, Aberdeen comprises of four apartment blocks – two with seven storeys and two with five storeys –providing a total of 276 apartments. Each apartment block has underground parking for approximately 80 cars. Forbes Place is one of the first Build to Rent (B2R) developments in Scotland, built by premium contractor Dandara to address a critical lack of high standard accommodation for professionals in the city of Aberdeen.
Dandara turned to Creagh Concrete to use their innovative offsite fastrack build system ‘Rapidres’ for the site. ‘Rapidres’ is ideally suited to multi-storey projects where the layout is replicated consistently across each floor. While most projects will have variation of layout in mixed use spaces on the ground floor, this is routinely dealt with by the use of a structural podium which forms the base for the offsite structure. The total frame solution comprises of structural walls and solid hollowcore flooring, with construction speed far greater than alternative systems. Creagh designed, manufactured, and installed the complete structure from foundation to roof level. Units were manufactured offsite at the factory in Toomebridge and delivered to Forbes Place for installation over a 40-week build period. Units included external sandwich precast panels, precast columns, hollowcore floors, internal cross walls, lift shafts, stair-flights, landings and external brick-clad retaining walls.
You can view more on Rapidres here: http://bit.ly/2rRH2AN
The building’s design features one stair and lift core in the taller block, which provides access and emergency access for both blocks. Like the rest of the building, this is formed of cast in-situ concrete to the first level and then precast concrete beyond.
Precast concrete had always been the material of choice for the frame construction and cladding. The project team looked at various different options for the structure and its subcontractors, before settling on the team at Creagh Concrete to deliver and install the frame panels, cladding sections, balconies and floor slab. The hollowcore floor slabs are lifted into place with reinforcing steel rods used to stitch the sections together, before a final screed is placed to address any level differences and deliver the final slab level.
“We knew we wanted the robustness that precast concrete offers and spent a lot of time researching our subcontractors,” says Adrian Smith. “Creagh has the capability and experience to deliver both the hollowcore floor slab and the architectural precast concrete that we wanted. The screed that we place on top of the floor slab is there just to iron out any changes in level. It gives us a little wriggle room.”
The placing of each level is based on a turnaround time of just 10 days. Prefabricated bathroom pods, manufactured in Hull, are lifted directly into position at each level as the building edges further towards completion.
“We are seeing strong interest in our rapid build concrete systems because developers now understand the true value of slashing programme times,” says Creagh Concrete’s CEO, Seamus McKeague. “Investors not only benefit from revenue gained by the early occupation of units but, also, from the mobility of their capital resource. Quite simply, shorter build times mean developers can complete more projects with the same pot of finance. The market for custodial accommodation has also been open to offsite for some time now and we are engaging there too.”
For more information visit: www.creaghconcrete.co.uk or email: structures@creaghconcrete.co.uk
Images: 01-03. Arena Central during construction with 8m panels being raised into position
The McAvoy Group has been awarded its first contract in the residential sector following the announcement of its expansion into offsite housing. The £4.7 million contract for Clanmil Housing Association will be the first offsite housing scheme to be built in Northern Ireland. The use of the McAvoy offsite housing solution will reduce the build programme by around 60% to just 40 weeks.
Designed by Knox Clayton Architects, the Joymount development in Carrickfergus will provide 40 much needed homes to help address the severe shortfall in social and affordable housing in Northern Ireland. It will feature eight one and two-bedroom apartments for couples and families, 17 two-bedroom apartments for active older people and 12 two-bedroom houses for families. There will also be three detached bungalows specifically designed for individual families with complex needs. The scheme is due for completion in spring 2019.
The homes will be manufactured and fully fitted out offsite at McAvoy’s production centre in Lisburn, Northern Ireland. McAvoy will manufacture 111 steel-framed building modules and the homes will be installed onsite, complete with bathrooms, kitchens, partitions and glazing.
Carol McTaggart, Group Director of Development at Clanmil, said: “We have been exploring different delivery models for social housing to help address the rising cost of building materials, the shortage of skilled labour in the construction industry in Northern Ireland, and the uncertainty created by Brexit. There are currently 24,000 households in housing stress in Northern Ireland. We want to be able to deliver new homes more quickly for people on the housing waiting list whilst still maintaining our high standards of design and build quality.
“Significant time savings can be achieved with offsite construction. Offsite manufacture avoids delays caused by poor weather and it improves both quality and health
and safety – with less impact on the environment. By partnering with McAvoy on this pioneering project and using advanced offsite construction technology, we believe we can reduce the build programme for these 40 new homes by around 56 weeks which is crucial to reducing waiting lists.”
Eugene Lynch, Managing Director of The McAvoy Group added: “It is fantastic to see such a progressive provider of social and affordable housing as Clanmil who are looking at more innovative ways of delivering high quality new homes, more quickly to address the housing shortage in Northern Ireland.
“This scheme is the first to use our new modular housing solution and successfully demonstrates its application for apartments, detached and semidetached homes. It also illustrates our capabilities as a principal contractor. We are not just supplying building modules on to a pre-prepared site but are responsible for the full range of services for Clanmil – from site preparation and clearance of this brownfield site to design, manufacture, factory fitting out, building installation, landscaping and infrastructure. We look forward to creating a much needed and vibrant new community for this area.”
Following extensive product development and collaboration with Queen’s University Belfast, McAvoy has developed a steel-framed offsite housing solution for multi-storey apartments, detached, semi-detached and terraced family homes. The new homes are designed in accordance with Lifetime Homes and Secured by Design standards.
McAvoy will work as principal contractor on its housing projects, taking responsibility for design, manufacture, fitting out, installation and external works. This will mean easier procurement, fewer management resources, greater cost efficiency, and improved quality control for developers and housing providers.
Source: www.mcavoygroup.com
An innovative unitised facade, combining handmade bricks, aluminium, triple glazing and precast concrete, was developed for University College London Hospitals (UCLH). The unitised facade is part of an offsite solution for the new centre for ear, nose, throat and dental services.
Created by a team led by main contractor Mace and architect Pilbrow & Partners, the facade’s design aims to reduce onsite health and safety risks, improve quality and slash months off the programme – up to five of these panels will be installed a day, and the entire envelope should be complete and watertight in just 13 weeks. Most of the 248 panels are hybrids that combine traditional handmade bricks, chosen to blend with the historic context, with precast concrete, aluminium and glass. The heaviest weigh 11 tonnes.
Nicola Scammell, Senior Project Manager at Mace, says: “Prefab is often considered uncreative and repetitive but with the hospital being in a largely brick-built conservation area, a lot of work has gone into the fine detailing to ensure it is respectful to the architectural surroundings, but delivered in a modern and efficient way. Building the facade traditionally, by hand-laying bricks, would have taken 40 weeks; by unitising the panels we managed to reduce that to 13 weeks. It takes various activities off the critical path, we simply get panels delivered ‘just-in-time’ to go straight onto the building.”
The large bays on Huntley Street are the most complex and include a perforated brick element, orientated south west to increase solar shading, a triple-glazed window element, and a precast concrete element. Each panel on levels one and two is around 5.5m wide by 4m tall, while slightly taller panels feature on the upper levels.
The idea of modularising the facade was first mooted by Mace at bid stage and subsequently taken forward when it won the design and build contract and started on site in summer 2016. The new centre, which brings together services from the Royal National Throat Nose and Ear Hospital and Eastman Dental Hospital, is due to open in 2019.
Source: www.techrete.com
Central Bedfordshire College and a private developer have chosen ZEDPods, ready-made, quality starter-homes for a new development of 23 homes on college land.
The one and two-bedroom houses, a break-through development in low cost, low carbon and high-quality homes are fabricated offsite. Their modular construction allows them to be rapidly erected on pieces of land not generally considered suitable for housing. With a variety of design options covering single or multi-occupancy sites, ZEDPod homes can be tailored for a range of accommodation needs, offering a viable, affordable solution to the keyworker housing crisis.
Designed and developed by RIBA award-winning architect Bill Dunster, the ZEDPods are designed to take advantage of existing city centre car park locations and hard standings across the UK, either on the ground or assembled on raised platforms. Homes are built to higher standards than conventional houses, being super-insulated, triple-glazed, with heat recovery ventilation, low carbon technology and lots of daylight.
While the company is busy working on several new developments following the launch of the concept, this is the first ZEDPod project to go into planning. Bill Dunster, Director of the new ZED Pods company says: “We understand that Savills has reported ‘the identified requirement for affordable housing is greater than could be delivered through the planning system’ and that there is a ‘need to explore other ways of providing affordable housing’ so we look forward to working constructively with planners across the UK in explaining our new technology.”
Ali Hadawi, Principal, of Central Bedfordshire College said: “We are delighted that Central Bedfordshire College is able to support the local area needs and ZEDPods with the creation of environmentally friendly housing solutions. We look forward to working with ZEDPods to develop new courses teaching on modern forms of construction utilising the most cutting edge, eco-friendly construction techniques to our learners and to seeing the benefits that this innovation will have on our community.”
Local MP, the Rt Hon Andrew Selous is enthusiastic about this first development, which will offer affordable homes to Dunstable’s nurses, teachers and firefighters saying: “Bill Dunster set out a compelling case for affordable zero energy bill homes that people want to live in. There is a huge demand for affordable housing and I will do what I can to keep this matter at the top of the Government’s list of priorities.”
Bill Dunster added: “As the pods are constructed from quality fireproof, durable and robust materials, they are designed to last as long as a traditionally built home. The pods’ solar roofs generate more energy than the houses consume, so they will also have the lowest possible running costs.”
ZEDPod owners will have their own balcony and front door, a kitchen and dining table, a bathroom, a lounge with stairs leading to a mezzanine floor bedspace, with home office desk, double bed, wardrobe and storage. ZEDPods will be sold with a ‘Q Assure’ mortgageable warranty.
Source: www.zedpods.com
Architectural practice, astudio, has launched a revolutionary modular housing partnership in the hopes of reducing the cost of modular housing, providing high-quality homes and offering a potential solution to the UK’s housing crisis.
amodular, is astudio’s proprietary modular building method with Be First, the London Borough of Barking and Dagenham’s pioneering regeneration company. The innovative volumetric modular construction method developed by astudio enables the expedited assembly of low-energy homes, fitted-out, completed and manufactured offsite to provide robust, high-design modular housing.
astudio’s homes are supplied on a turnkey standardised production basis. Costs are minimised through bulk purchasing of materials and components. The small selection of standardised modules speeds up production and reduces the potential for defects during build. Multiple fixtures, fittings and cladding options both internally and externally are available, enabling each building to have a distinctive look and feel.
Working in collaboration with Be First and offsite modular manufacturer Rollalong, astudio’s pioneering approach is being implemented in two new developments in the borough, at Mellish Close and Sugden Way in Barking. Consisting of eight council flats in Mellish Close and 13 in Sugden Way, the homes
The first prototype homes manufactured using an innovative 3D injection printing process, and incorporating technologies inspired by the automotive and aerospace industries, are due to begin production by the end of the year.
Prefabrication specialist RDA Modular developed the technology behind the low rise homes and apartments, which will be produced in large monolithic panels, up to 16.5m long and 3.5m wide. The firm recently launched an investment and fundraising round to build its first production facility, capable of manufacturing a minimum of 2,000 homes in its first year. The long-term plan is to build several factories capable of manufacturing 6,000-8,000 houses each.
Romy Jardine, Chief Technology Officer at RDA Modular, said: “We’ve been working for the past couple of years on some brand new technology that hasn’t been used in construction, including housing or modular. We build the walls and floors in single massive pieces then ship them flat-packed standing upright,
will be built in complete accordance with building and health and safety regulations, more sustainably, cost-efficiently and within an accelerated time-frame of 60 weeks from design to handover compared to the 24-30 months it would take for traditional builds, saving the council vital resources.
Richard Hyams, Co-founder and CEO of astudio, said: “We are delighted to be working in close partnership with Be First and the London Borough of Barking & Dagenham to help address the critical housing shortage in the borough, using our amodular proprietary production method. It is vital that landowners, developers, local councils and the community collaborate if we are to free up land and develop innovative solutions to address the critical
shortage of housing in this country. It makes sense that one of those innovations is modular housing. We believe that in the very near future, building will become like car production, with houses becoming quality manufactured products.”
Iain Ferguson, Commercial Director for Be First, added: “At Be First we are determined to increase the pace and quality of development in Barking and Dagenham. So, we are excited to be working with astudio on this ground-breaking scheme which we expect to reduce costs and deliver top-class housing in a fraction of the normal build time.”
Source: www.astudio.co.uk/modular
like an Ikea system for apartments and big housing developments. Using modern materials means we can make much stronger and lighter panels that are more eco-friendly and close to Passivhaus standards. The main cost saving comes from factory automation and reducing labour by 95% compared to traditional construction.”
The prefab elements are a form of ‘superior SIPS panel’ but plug and play and are extremely lightweight. They comprise two layers of OSB with all mechanical, electric and plumbing services sandwiched in between. The homes and apartment blocks will be built up to four storeys high and located outside London, either
in the suburbs or in new garden cities, towns and villages proposed as a way to meet the current housing shortfall.
RDA Modular is working with companies in Italy and Germany to apply existing production technology, used in the aerospace, automotive and defence sectors, to construction. The company has already ordered some machinery and plans to start production for testing and certification purposes and to develop initial prototype houses by the end of the year.
Source: www.rda.global
Offsite construction specialist, Sigmat, has launched its biggest hunt yet to find Yorkshire’s ‘Hidden Talent’, as it recruits for an elite Academy to develop some of the region’s brightest individuals. The ‘Detailing Academy’, will provide opportunity for a diverse range of people from all backgrounds.
Chief Finance Officer for the company, Matthew Jowett, said: “Sigmat is the UK market leader for offsite light gauge steel framing which, in layman’s terms, means we design, manufacture and assemble steel frames for buildings in our production facility before installing them onsite, taking significant time and cost out of construction projects. Consequently, we have grown rapidly over the last few years as our technology has established itself in the UK building sector, prompting the need for more professionals to support our continuing expansion.”
Recognising that the right sort of people were hard to find, Sigmat decided to launch its pioneering ‘Detailing Academy’, with the aim of recruiting men or women returning to work after a career break, those with an interest in the ‘built environment’ or simply bright individuals looking for a career change.
“The labour market has been volatile in recent years, driven in part by the Brexit debate, so we decided to take a pro-active approach,” added Matthew. “Due to continued growth in our business we want to recruit either ready-made Structural Detailers or people looking for a new challenge, even if they have no experience.”
There are a few mandatory requirements, essentially a keen eye with excellent attention to detail, a flare for all things technical and the determination to see projects through to the end. Technical Director, Clive Webberley, added: “We have designed a unique programme to enhance existing or dormant skills within those people selected, and successful candidates will be trained in an academy-based environment and taught
the necessary skills to become a Structural Detailer, including software and 3D modelling.“
Academy graduates will eventually join Sigmat’s Detailing Team and develop their career as a Structural Detailer, using their new skills to support Sigmat in delivering some of the UK’s most exciting construction projects.
Anyone interested in learning more can email: recruitment@sigmat.co.uk or visit: www.sigmat.co.uk
Three storeys of office and welfare space have been installed over four days at Wembley Park. Construction workers on the development site will have use of the industry’s highest quality site accommodation solution as Portakabin provides almost 800m2 of welfare and office space.
McLaren was awarded three building contracts by developer Quintain, for the Wembley Park development plot, which will provide around 30,000m2 of residential and retail space. The 10-storey and 15-storey buildings constructed by McLaren will include 490 build-to-rent units with associated common spaces, commercial office space and ground floor retail units.
For the duration of the construction project, Portakabin installed a three-storey site accommodation building adjacent to Wembley Stadium. Thirty modules were carefully craned into place, over just four days, on the site next to Olympic Way, known to fans the world over as ‘Wembley Way’ which welcomes more than 11.5
million visitors a year. This minimised disruption to the site and also ensured there was no risk to public safety.
The building will be in use for 120 weeks in total and provides 795m2 of space for McLaren office staff and construction workers. The space includes three large open plan offices, two meeting rooms, an induction room, bathroom facilities on each floor, two kitchenettes, a large canteen and professional kitchen plus a drying room and reception for visitors. The white modular building, with black exterior staircases at either end, provides a clean, modern appearance for the iconic stadium site – challenging the perception of traditional site accommodation products.
Karl Salter, Logistics Manager, McLaren Construction at Wembley Park said: ‘’We used Portakabin knowing we would receive a high level of service and the McLaren team on the Wembley projects were not let down. They provide great temporary office and welfare facilities
finished to a very high standard and their customer service is excellent, from start to finish. The installation of the facilities was completed on time and in a very safe and professional manner, I can honestly say they exceeded our expectations here at Wembley. The team at Portakabin are a pleasure to work with, and I’m sure we will be working together again in the near future.’’
David Griffiths, General Manager at Portakabin added: “We worked closely with the McLaren team to achieve a solution that worked for them. Portakabin offers the highest quality site accommodation solutions and for a site and team of this prominence, quality and finish were most important. We were able to exceed that level of quality, delivering the building safely and quickly with minimal disruption.”
Credit: Quintain/High Level Photography
Source: www.portakabin.co.uk
Fusion Building Systems has completed its works on three residential housing projects in the south of England for Barratt Developments. St Mary’s Place, Felpham, West Sussex, New Quarter, Bordon, Surrey and Cane Hill Park, Couldson, Surrey, are the first schemes to be delivered by the offsite manufacturer since it successfully completed a trial project for Barratt in Southampton in 2017.
Across the three sites – working on almost 200 units – Fusion adapted existing Barratt house types as well as developing bespoke multi-storey designs, to make them suitable for use with its light gauge steel panelised system. The work was completed on each site over the past 12 months, but was the result of almost three years of intense integration and education at all levels across both companies, exploring how offsite systems could be used as a viable alternative to traditional methods of construction.
Rotherham Metropolitan Borough Council is recruiting specialist housing suppliers for a new series of modular low-cost, single-person ‘pod’ homes. The project will deliver 10 pilot pod homes across two tight urban sites. Each 22m² unit will be expected to feature a bedroom, living space and shower room. The team or teams chosen for the estimated £400,000 contract will use offsite construction to deliver a pilot programme of innovative affordable council houses which could be rolled out across the region on a larger scale if successful. In its brief, the council says it: “has ambitions to significantly increase the number of new homes built in Rotherham. To help
“Our system was proven to work on a small number of houses for Barratt’s trial 18 months ago, so it’s exciting now for us to see how we can scale up to deliver a much larger number of units,” said Robert Clark, Fusion Head of Business Development.
The three sites were very different in their requirements however, from two, three and four-bedroom standard house types, to non-standard designs with challenging ground conditions and four-storey apartment buildings. “Each site put our design and engineering teams to the test,” added Robert. “With the successful delivery of each, from concept through to installation onsite, reliant on effective collaboration and communication throughout the supply chain. The early phases on site once again presented a learning curve for each company, but as each development progressed, all parties worked well together and were ultimately convinced offsite was the future for volume housebuilding.”
achieve this, the council is piloting the use of modern methods of construction as a swifter and more efficient way to deliver new homes.
“The council is seeking tender returns from housing providers using MMC to deliver a pilot project which will consist of 10 small ‘pod’ type homes for single-person households requiring affordable accommodation. This is identified as a pilot scheme which the council hopes to roll out as a larger programme, depending on the success of this pilot. The new homes will be added to council stock and will be developed on council land.” The first sites revealed for the project include Chatham Street in the town centre, close to the site of the new University Centre Rotherham on Doncaster Gate. Six units are envisaged here. At Vine Close in Masborough, four units are proposed. Two bungalows at Hounsfield Road and Hounsfield Crescent, East Herringthorpe and
Oliver Novakovic, Technical and Innovation Director, Barratt Developments, added: “Fusion has now successfully delivered full scale pilots on three sites with our Southampton and Southern Counties divisions. We have seen a real improvement in speed as predicted and are now continuing to work closely with the Fusion team to roll this technology out further. We believe the work we have done over the last two years on things like standard details and the construction approach really supports the application of the Fusion system into our private housing market.”
Source: www.fusionbuild.com www.barratthomes.co.uk
eight bungalows at Symonds Avenue, Rawmarsh are proposed.
If the pilot proves to be successful, it could provide a delivery route for many of the other 200-300 small sites in the borough. The overall number of homes in the borough increased by 479 units in the 2017/18 financial year, below the Council’s target of 641 units.
Source: www.rothbiz.co.uk
www.rotherham.gov.uk
Hallsville Quarter is one of the most significant regeneration projects in London and forms part of the £3.7 billion Canning Town and Custom House Regeneration Programme. Working with developer Bouygues and specialist cladding contractor Facade Concepts Ltd, Aquarian Cladding Systems have supplied over 8,000m2 of its offsite-manufactured Gebrik insulating brick cladding system for two 15-storey residential tower blocks, which were built in just seven months.
With a desire to achieve a brickwork façade using mast climbers, Bouygues’ design team identified that Gebrik would allow the brick cladding to be incorporated within other trades using mechanical access, enabling a quicker build programme without the need for scaffolding. Gebrik’s BBA certification also ensured warranty provider NHBC would approve its use over 18m, provided the entire build-up met the tested conditions in accordance with BS8414:2.
With the building footprint effectively the site footprint, storage space was at a premium, and so all deliveries were made on a ‘just-in-time’ basis. With fewer deliveries and less storage than conventional brickwork, this meticulously-timetabled project proved more straightforward and Gebrik’s swift installation meant that when materials arrived, they were used within a few days.
“We believe Gebrik installation is generally easier than brickwork,” explains Guillame Simon, Project Manager for Bouygues UK, “Its installation is typically less affected by weather conditions, it needs less storage and load space onsite than brick, and it can be installed safely from mast climbers. Its adaptability also made it possible to co-ordinate with GRC features, which would have been difficult using traditional brick.”
Source: www.aquariancladding.co.uk
Saint-Gobain UK and Ireland’s new report ‘Emerging Realities in the Construction Industry’ curates statistics and opinion from independent contributors on aspects of construction facing imminent disruption – and what it means for the future of the industry. This report covers the trends, technologies and approaches in their infancy which will change our industry now and in the immediate future. Four key topic areas facing disruption are explored: economic, technological, socio-demographic and environmental realities. The report features independent opinion from organisations across the industry including from The Carbon Trust, SNC-Lavalin’s Atkins, The Royal Institution of Chartered Surveyors, Mott MacDonald and The Manufacturing Technology Centre.
Offsite manufacture is referenced several times as a technology and innovation megatrend stating: “There’s a big link to manufacturing. You can get better productivity offsite. It’s about cross-sector learning – for example, about processes, which are about creating more structure for people to work within. We are trying to drive horizontal innovation and are learning a lot from discussions with the manufacturing, aerospace and automotive sectors. We are redrafting the narrative of our sector. It should be seen as being built asset manufacturing, rather than construction. This approach can benefit so much of what our society depends on – housing, schools, hospitals, roads and railways. It will enable us to build more, to a higher quality, with less resources.”
Mike Chaldecott, CEO of Saint-Gobain UK and Ireland said, “I’d like to thank all of the contributors who took part in the formation of this report. Business thrives on foresight and I hope this report helps spark a debate about the future of our industry. Specifically, how we all might prioritise our thinking and activity across our industry to maximise the opportunities at our fingertips and capitalise on the vast potential of our sector.”
Offsite manufacturing is a progressive step that challenges outdated assumptions –the construction sector has been advised to ‘modernise or die’. This technology will generate savings in the long term, but the overwhelming message has to be – get involved sooner rather than later, or risk being left behind.
Spotlight on Offsite brings together distinguished speakers from a broad spectrum of pioneering organisations representing clients, construction professionals and suppliers.
The combined conference and exhibition will showcase ground-breaking offsite construction solutions and focus on the latest developments, innovations and investments in the offsite sector across a range of vertical markets.
Get involved as an exhibitor for the two-day event from as little as £1500 + vat.
Please contact:
julie.williams@radar-communications.co.uk
01743 290042
If you are working within the offsite sector and believe that you can present some leading-edge ideas or some ground-breaking case studies and would like to share your insight with an audience of over 300 interested delegates - then please get in touch with:
grace.baker@radar-communications.co.uk
Fusion21 has announced the suppliers successfully appointed to its Modular Building Framework following an expansion worth £175 million over a four year period. A total of eight highly skilled firms have secured a place on the framework which is designed to service the blue light, health and leisure sectors, in addition to providing buildings for educational purposes and wider public use.
With a full turnkey solution for the Design, Manufacture and Installation of Buildings of Modular construction the framework worth, a total of £400 million, offers Fusion21 members including schools, academies, colleges and universities, temporary or permanent quality modular buildings, which are compliant with all building regulations and present lower carbon emissions than traditional builds.
Nick Verburg, Procurement and Supply Chain Manager at Fusion21, said: “Modular offsite construction is an innovative and cost-effective way to deliver buildings for the 21st century, and we are delighted to have expanded this flexible procurement solution in response to market demand and member feedback.
“Fusion21 members accessing this framework from the education sector will benefit from significant efficiency savings and social value, whilst accessing a range of sustainable building solutions specific to their building needs and requirements. Members can also enjoy the advantages of prefabricated construction including reduced labour and onsite costs, and a faster turnaround – which is ideal when classrooms are urgently required.”
Fusion21 provides procurement services and OJEU compliant frameworks to the public sector, and is committed to making a difference in communities across the UK. To date the firm has saved its members more than £177 million through the procurement process, created more than 5,100 jobs and generated £76 million of community impact.
The successful suppliers appointed to Fusion21’s national Modular Buildings Framework include: Danzer, MTX Contracts, Wernick Buildings, Elliott Group, Qube Structures, Western Building Systems, Integra Buildings and REDS10 (UK)
Source: www.fusion21.co.uk
be announced early next year, now that the Heathrow team has completed visits to all 65 longlisted sites Last year, Heathrow invited organisations across the country to showcase how their area could contribute to the delivery of one of the UK’s largest infrastructure projects. An initial 121 expressions of interest were whittled down to a longlist of 65 potential sites, all of
which have been visited by Heathrow representatives over the past six months. The nationwide tour concludes in the Midlands with the Heathrow team visiting sites from Balfour Beatty, SEGRO and Prologis located in Tamworth, Derby and Daventry.
The hubs are integral to the airport’s plans to ensure every corner of the UK benefits from the expansion of Heathrow, helping to spread job creation and economic benefits up and down the country. Offsite construction will also help to make the project more affordable and sustainable – by transporting assembled components in consolidated loads. Heathrow expansion is an opportunity to consider a new approach to the construction of major infrastructure and will be the first of this scale to use this method – with the objective of encouraging other major projects to explore offsite construction.
“Heathrow expansion is much more than the delivery of Britain’s new runway, said Emma Gilthorpe, Expansion Executive Director at Heathrow. “Expansion is a once in a generation opportunity to transform British construction as the country prepares for life post-Brexit. This nationwide tour has shown us the possibilities offsite construction offers and we’re looking forward to announcing the shortlist early next year.”
Business & Industry Minister Richard Harrington said: “We want the UK to lead the bytes and mortar revolution within the built environment and our Construction Sector Deal lays the foundation to take advantage of these opportunities – boosting productivity, creating better jobs and increasing new offsite manufacturing technologies to speed up construction. The Heathrow Logistics Hubs have the potential to be an example of this modern construction in action, embodying the principles of our Industrial Strategy and benefitting millions by allowing businesses across the UK to harness the strengths of their own regions to deliver a landmark infrastructure project.”
Marie-Claude Hemming, Director of External Affairs at the Civil Engineering Contractors Association (CECA), added: “CECA has long argued that expanding our airport capacity is vital in securing future economic growth across the UK, and we are fully supportive of Heathrow’s development of a third runway. As strong advocates of rebalancing the economy, we welcome Heathrow’s decision to use logistics hubs which will drive project efficiencies, improve site welfare and will also contribute to growing the economy for the long term outside of London and the South East.”
The next stage of the selection process will be a pre-qualification questionnaire (PQQ) which opens in autumn this year. A shortlist of potential Logistics Hubs will be announced early in 2019, before the final four sites are announced later in the year, with construction set to begin at these sites in 2021.
Source: http://mediacentre.heathrow.com
Hadley Group have announced the appointment of Ben Towe (pictured) as Group Managing Director while Stewart Towe becomes Executive Group Chairman. In line with Hadley Group’s strategic 2020 vision, Ben Towe has been appointed Group Managing Director leading the day-to-day worldwide activities of Hadley Group and Associates. As Executive Group Chairman Stewart Towe will continue to promote, drive and support the strategic intent of Hadley Group.
Ben will continue to drive the company’s growth strategy while Dr Michael Castellucci will take the reign as Group Engineering Director responsible for all technical and operational functions. Michael was instrumental in the development of Hadley Group’s patented UltraSTEEL® process – a groundbreaking steel strengthening technology.
Stewart Towe, Executive Group Chairman, Hadley Group, said: “I have really enjoyed my role as Chairman and Managing Director of Hadley Group over the past 12 years building highly effective Board members and a successful business. My new role will give me the opportunity to pursue activities within the wider business community while still supporting the pursuit of Hadley Group’s strategic business development
and investment activities globally.” Jonathan Jaggar continues as Group Sales Director and Richard Neale as Group Finance Director.
Hadley Group recently acquired EWS (Manufacturing) Ltd. In a move that reaffirms its commitment to support the construction market, both in the UK and internationally, Hadley Group announced the acquisition of EWS (Manufacturing) Ltd with Stewart Towe, commenting: “I am delighted to confirm the addition of EWS into the Hadley Group. The company greatly complements our wide range of value added construction products. We look forward to supporting
EWS as they continue to progress in the markets they serve.”
EWS produces in excess of 25 million metres of cold roll-formed sections annually and is the market leader in window and door steel reinforcement with core strengths in other construction market products. The Wolverhampton-based manufacturer will now form part of Hadley Group’s global chain of manufacturing locations.
Source: www.hadleygroup.com
Hadley Group is a world leader in advanced cold rolled steel technology, with manufacturing facilities in Europe, the Middle East and Southeast Asia, delivering innovative solutions across sectors as diverse as construction, industrial and agriculture.
Our technical, structural and design abilities, coupled with our unsurpassed expertise in cold rollforming, have resulted in an extensive range of innovative products. From steel profiles and steel framing to innovative, market leading solutions like our purlin system, ceiling grids and SFS panelised bolted frame; we work hand in hand with our industry partners to deliver products designed to streamline construction, enhance performance and maximise sustainability.
www.hadleygroup.com
When and how to engage with the offsite supply chain to get the most value from it is always a hot topic for discussion. Etex Building Performance recently hosted a Roundtable Event to discuss issues surrounding this and the burgeoning private rented sector (PRS) approach to housing.
Arguments about how to deliver the vast quantities of newbuild housing required in the UK over the next decade to fuel demographic demand are complex. But what most people can agree on is that a new breed of affordable, flexible and purposebuilt housing is needed that appeals to discerning tenants and anxious investors alike. New commercial and technology models are shaping the ways of delivering construction quality and consistency.
The role offsite construction has to play – not just in delivering new housing –but across all building types has never been more important and over the last 18 months in particular, offsite has seen its status at an all-time high. But problems still surround lack of early engagement – when in any project cycle are clients engaging with offsite suppliers and how could the process be improved?
“Procurement behaviour needs to change, says Rory Bergin Partner, Sustainable Futures, HTA Design LLP. “There is still a struggle with people trying to procure new things in an old way and we come across that on multiple projects. There is still a maturing awareness of what products and systems are available on the market. Not everybody wants the same technology or has the same considerations, but there is a worry about limited suppliers out there. Or what is increasingly happening with these limited suppliers is that they are incredibly busy.”
Early supply chain engagement is the oft-repeated mantra and starting the process of adopting offsite at project inception means its long-term benefits are maximised. “Certainly everyone is on a different stage of the journey to understand what products and systems are in the marketplace,” says
Joe Thornton, Founding Director, Cast Consultancy. “But we are finding that far more people are ‘open’ to talking about offsite than ever before from a very early stage.”
Many clients and investors needs to widen their expectations and understand that offsite adoption is a: “business strategy first and a procurement strategy second”, and is about absorbing the culture of offsite manufacture into the business model. Confidence levels are growing about the use of offsite – but with confidence everything in long-term investment decisions – this is putting the pressure on disparate parts of the supply chain. As Brendan Geraghty, Director of Geraghty Taylor Architects says: “Funders have a profound influence on this space, on design decisions and greater control of the supply chain. They are being very strategic about
what they control and what brings less cost and ultimately what saves them money on the operational side.”
Overall the feeling is that a ‘leap of faith’ is still required into an uncertain market with challenges surrounding capacity and whether existing facilities can scale up to cater for increased delivery of systems or more products. To underpin greater confidence, better collaboration and more partnerships between contractors and the offsite supply chain are required, that make the best of both worlds. What needs to be better understood, communicated and sold as a positive, is the concept of ‘moving the value of a project away from the construction site to inside a factory’ and where the levels of quality and reliability can be controlled and streamlined. The age-old problem of overlapping trades, site snagging and endless site revisits can be made a thing of the past - for the PRS sector this is critical.
Hurdles & Barriers
With more education required on what offsite can deliver generally, what does the offsite industry itself need to do to get greater engagement with PRS clients, and what are the barriers to overcome to facilitate a better understanding over what factory manufactured building components can do?
One hurdle and a deep underlying issue is that the manufacturing and traditional construction industries are entrenched in the way they work and neither fully understand what each other does. Each have different thought processes, different histories and modes of operating. Certainly the role of precision factory engineering is at odds with the traditional construction mindset.
“There is definitely a need for precision design and high mechanisation,” says Matt Voyce, Director, Quintain. “Offsite construction is being sold as precision manufacture so more of that will give us more confidence in specifying across a range of projects.”
It is often here, where the varying quality of factory facilities and where businesses are in their business evolution is often queried. “Newer entrants have gone more towards precision engineering,” adds Darren Richards, Managing Director of Cogent
Consulting. “The newer businesses are sophisticated and starting from a blank page. The older established suppliers are having to evolve their systems, sometimes job by job.” As the quest for cutting edge technology and greater digitisation drives factory manufacture, there is a feeling that the UK is slightly lagging behind the continent with pressure from the Netherlands, Germany and Poland with large scale production of precast elements, volumetric modules and bathroom pods.
“The building industry has always been notoriously slow to pick up new technologies,” adds Kevin Wylde, Director ESA Architecture. “There is a huge amount of technology out there but we are slow to pick it up. It’s all about shifting perceptions.”
The difficulty seems to be there is often a ‘traditional approach to a technological problem’.
Technology & Collaboration
While technology is changing the ways buildings are constructed everywhere and transforming the way components are produced, the specification and design process would be far more efficient if the investor/client business requirements were more clearly articulated at an early stage to designer and architect teams and the supply chain. This would enable them to combine and collaborate and work out the optimum way to deliver client proposals. Stronger client leadership and where they see their ‘value points’ needs to be communicated better to illicit a better integrated response from the offsite supply chain.
“A lot of entrepreneurs have set up an offsite solution that works for various clients,” says Neil Ash,
Facilitator: Darren Richards –Managing Director of Cogent Consulting
Neil Ash – Managing Director, Etex Building Performance
Matt McKay – Commercial Manager Etex Building Performance
Joe Thornton – Founding Director, Cast Consultancy
Rory Bergin – Partner: Sustainable Futures, HTA Design LLP
Brendan Geraghty – Director, Geraghty Taylor Architects
Matt Voyce – Director, Quintain
Kevin Wylde – Director, ESA Architecture
Colin Westpfel – Head of Design, Balfour Beatty
Gary Ramsay – Editor, Offsite Magazine
Managing Director, Etex Building Performance. “And there is a flip side where a customer has a list of specific requirements of what they want and somehow these are not gelling together, so along the way there needs to be far better collaboration.”
A cultural shift in collaboration seems to be clear. Advice on which products and systems to use and where they would be most successful is an area where developers and clients need to know more about. The manufacturing market is a mature one and what developers would like to see is a clear presentation or proposition of what offsite systems can deliver versus a traditional approach. An oft-repeated stumbling block is the lack of statistical evidence and hard data that proves the benefits of offsite manufacture. It is very difficult to underpin the numerous benefits of what offsite can deliver without independent statistical data to prove it.
In an ideal world what is required is a thorough cost risk appraisal of a ‘traditional versus a manufactured offsite project’. Offsite manufacture is unquestionably not without risks but they are fewer and more manageable than via a traditional route. “Traditional costs are more commonly understood but there are so many intangibles in a traditionally delivered project, that to truly get a comparison would be nigh on impossible,” says
Colin Westpfel, Head of Design, Balfour Beatty.Generally, architects need to get to grips more with offsite and factory manufacture. Building design is still commonly centred on the delivery of traditional construction, with little understanding of factory-based system parameters and methods. And with the pressures of design, work-flow and supply chain integration key to success, the spotlight is on the architect, who could be best placed to be the ‘integrator’ of all these factors. “We are often in a central position between the competing bits,” says Brendan Geraghty. “From building design to interior fit out or assembly, we have to wear a number of hats but we need to know more detail to be able to make all of those competing bits work smoothly.”
Standardisation brings many cost benefits but may not always deliver wide choices. What the vast majority of clients and customers want when choosing a home is choice – and this is key to the PRS model as well. So will the focus on greater standardisation create a potential ‘turn-off’ for clients? Certainly some architects are wary of standardisation and the fear that it can stifle creativity, whereas for a manufacturer standardisation is the perfect scenario.
So there is sometimes a perception within architectural and construction circles that standardisation is a bad thing. “One of the challenges with offsite and volumetric modular is its repetitive nature,” says Kevin Wylde. “I understand that there can be lack of flexibility. Fear of standardisation is not the issue its understanding what
should get standardised. Introduction of standardisation can add real value by taking out the mundane bits and leaving you to focus on the elements that deliver true value.”
Of course the 3D volumetric modular approach is not the only one driving the PRS market. “We are very much in the thought process of looking at where the construction industry is going to change in the future,” says Matt McKay, Commercial Manager, Etex Building Performance. “We are looking to see what is required and what we can bring to the offsite market. There is a bigger role for standardisation – there is something behind that which really needs to be thought about – either at component level or as a producer of 2D panelised or full volumetric systems.”
The increased use and popularity of new technology including BIM and immersive environments such as AR/ VR and the connected world are set to bring a younger generation and different thinking into the industry with lifetime transferable skills that extend careers beyond the building site. Are they set to deliver the massive benefits that everybody says they can?
Digital has a big role to play in enabling closer supply chain integration. Once there is a better understanding of what technology can do and how companies can co-ordinate better within the digital environment, then it will make big differences. The role of digital technology can identify contractor risk
by checking small details and this can deliver huge material efficiency and potentially save millions of pounds over a major developments. These kind of cost savings for clients that are caught early ultimately reduce the risk for contractors and improve the chances of offsite acceptance.
Also, beyond the digital and software aspects of BIM, the crux of its success rests in its ability to improve project productivity and optimise the construction process and bring about lasting quality benefits that everyone along the building supply chain – from client to customer – can profit from. BIM helps reduce costs and defects onsite and instils discipline into project teams to deal with problems earlier in the design process. “Offsite needs to possibly mature to open platforms,” says Colin Westpfel. “With a range of asset tagging and intelligent graphics minimising defects, these de-risk the building process and solve problems early via digital technology not on the construction site.”
Whilst repeat footprints and standard layouts allow for massive efficiencies in the hotel and student accommodation sectors, can the same be said for PRS? It has the right attributes and footprint for low level of changes and variations with offsite systems and components in a perfect position to produce a broad range of homes consistently. The key aspect rests in that homes being ‘living spaces’ need to align with client and brand values and ultimately geographical location. Quality is
As pioneers of light gauge steel construction, EOS Facades specialise in the design, manufacture and supply of a wide range of steel sections for panelised or volumetric offsite solutions.
Through careful design detailing and value engineering, EOS Facades is able to offer the highest quality award winning light gauge steel solutions - delivering environmentally sustainable projects on time and to budget.
As an advanced high performance offsite solution, steel is a robust, rigid and dimensionally stable material that does not suffer from movement created by moisture related issues. Light gauge steel is perfectly positioned to meet construction industry demands – it is future proof and future ready.
If you have a project in mind then why not challenge EOS Facades to help value engineer the most efficient solution for you?
T: 01325 303030
E: enquiries@eosuk.org
W: www.eos-facades.co.uk
Clearer Understanding – clients, contractors and supply chain need to have a better understanding of each other’s business models to engage and work with efficiently.
PRS in its Infancy – while the use of volumetric modular is perfect for repeatability of hotel and student accommodation, the specification for PRS housing has to be more flexible.
Selling Offsite – overcoming the ‘front of house’ issue and having better client-facing teams that understand offsite manufacture and deliver a convincing proposition to the marketplace.
Technology Cultural Shift – technology is fast becoming the common ground to make client – manufacturer – customer integration easier.
Building Ownership – unlike the ‘sold’ housing model, those holding the PRS assets need to think clearly about its future development and building lifecycle.
Cost Comparisons – better and transparent industry data to show genuine cost comparisons between traditional methods and offsite manufacture.
Creativity Crunch – more efficient buildings come from the understanding of technology and focusing on how to apply this to design and supply chain integration.
Upwards Trajectory – the interest and trend for offsite manufacture is heading upwards with clients happier to invest in long-term assets than ever before.
Quality Management – the evolution of BOPAS is encouraging but warranty providers also need to understand and scrutinise the quality standards and expectations that underpin investor decisions.
Procurement Behaviour – this needs to change. Organisations are still trying to procure new products and systems with an old traditional mindset.
critical but when people buy a home it is an ‘emotional decision’, when renting it’s about ‘quality of service’ and making the rental experience a positive one. As the PRS customer becomes more sophisticated, clients and suppliers need to be more attentive to the long-term life-cycle of the building and the wider role of place-making – it is here where a large paradigm shift rests: “it’s not about the building it’s about the customer.”
Looking ahead to where the offsite industry is heading in relation to the PRS sector and housing generally, there is now a continuous incline and increase of interest in offsite systems but there is still a reticence to engage from a sometimes wary client base. High levels of investment and large sums of money are available, but there still needs to be a convincing argument created for offsite to be deployed. The PRS sector in particular wants more validation of products above and beyond mortgageability and warranty – people are seeking in-service performance validation. Institutional lenders have high expectations about their long term investments and this kind of thinking is underpinning procurement decisions.
So while there is as positive relationship between the offsite sector and PRS market, a lot of effort still needs to be expended on defining clearly what offsite can provide for clients and specifiers and why construction fuelled by repeatability and standardisation is ideal. Economy of scale rests in repeatability and standardisation – so this and the wider use of design for manufacture (DfMA) plus the injection of creativity from architects and building designers, can bring about the changes that the construction sector and housing sector desperately need.
Many thanks to Etex Building Performance for hosting the Roundtable Event and thanks to all participants for their time and contributions to the discussion.
For more information on Etex Building Performance visit: www.etex-bp.co.uk
For more information on offsite related activity visit: www.offsitehub.co.uk.
Product & service portfolios
Manufacturing operations
Supply-chain integration
Business processes
Management systems
Marketing strategies
Sales routes to market
Offsite is due to make its mark on UK Construction Week (UKCW) by showcasing all its advantages in its very own dedicated Offsite area within the Build Show alongside an additional presence at Timber Expo. 1
Offsite construction will help take over Birmingham’s NEC between 9 – 11 October, with more than 10,000 products and 650 exhibitors, seminars, CPD sessions and networking opportunities across nine shows: Build Show, Energy 2018, Timber Expo, Surface and Materials Show, Building Tech Live, HVAC 2018, Civils Expo, Plant and Machinery Live and Grand Designs Live. To demonstrate how effective offsite construction is becoming, a two-storey house and student apartment will be installed at the show plus a high-end hotel bathroom pod and a timber house will be on display.
With a wide and varied range of offsite exhibitors on hand there is a plethora of products to discover. Many of which are embracing new technologies that will enable faster, more efficient and better-quality buildings.
The Elliott Group will be discussing everything from telecoms packages through to fire equipment thanks to their 360 degree service package for offsite construction. REM will be showing its unique approach by using living containers to build schools, offices and showrooms. And Containex will be showcasing its new selfcontained staircase modules, which are easy to transport and install, with strong and flexible guardrails that can be repositioned anywhere.
Other exhibitors include: KC Cabin Solutions offering personalised modular and portable buildings, Kerkstoel the precast concrete experts, Extenda Line with portable flat packed storage units and Morland will be displaying its new Forever FirecheckTM fire door frame and its brand-new Water Vapour Barrier tongue and groove panels.
Visitors won’t want to miss out Michael Dall from Barbour ABI’s talk, delving deeper into the market, where he looks at the key sectors for offsite, how it will develop and grow in the next few years and which sectors it appeals to most. Stephen Wade-Palmer from Offsite Solutions will talk about specifying factory-built bathrooms, looking at the critical considerations needed to optimise efficiency in using bathroom pods. An elegant bathroom pod, which is earmarked for luxury Canary Wharf hotel, will be on display in the Offsite area.
Visitors will have access to numerous CPD sessions and seminars. Don’t miss out on the Innovation Trail, networking opportunities and the Offsite Theatre, supported by MPBA and the Structural Timber Association. Modular building specialist, Vision Built, is installing a two-storey house and student
apartment for all to experience at the Offsite Theatre. Following the event, the construction will be taken to its final location in Suffolk.
For visitors who want to learn as much as possible about the speed of modular construction, you won’t want to miss out on the following seminars:
• Building more homes, with the Central Housing Investment Consortium
• Developing your offsite strategy, with Action Sustainability
• Flexible and high-rise modular constructions, with MJH Structural Engineers.
Other essential seminars include:
• New assessment methodology and certification scheme for modular homes presented by David Gall, Associate Director, BRE
• Digitising offsite construction by David Clark, Head Of Manufacturing And Innovation, The McAvoy Group
• Routes to market for modular and volumetric housing delivered by Joanne Booth, Construction Business Manager, Lucideon.
This year’s ‘Future of Construction’ theme, there is plenty to discover for the future of offsite. The Future of Construction Hub, in collaboration with Birmingham City University, provides an immersive opportunity to discover pioneering techniques such as digital
construction, 3D printing, robotics, AI and AR and modern methods of construction. Visitors will be able to try out these new technologies first hand and learn how they will shape the built environment in years to come. An Innovation Trail uncovers products from Danosa, Hekim Yapi, Max, SFL Mobile Radio, and Velux. Plus Carwyn Lloyd Jones will be building a timber home at Timber Expo, where he will deliver lessons on natural construction techniques too.
This year also sees the launch of the UKCW Role Models Campaign to champion the existing talent in the industry and to inspire the next generation. 36 inspiring men and women have recently been shortlisted for this campaign, and the overall Role Model of the Year will be announced on 10 October.
Debates on major national and international construction issues will take place on the UKCW Stage. Speakers already confirmed include: Barbara Res, Project Manager behind Trump Tower, Lord David Blunkett, Heathrow Skills taskforce Chair, Phil Wilbraham, Expansion Programme Director at Heathrow, Bridget Rosewell OBE, Commissioner at the National Infrastructure Commission; Ben Derbyshire, RIBA President and Ruth Davidson, National Housing Federation Executive Director.
Celebrations will all be in order at the Construction Enquirer Awards,
the Structural Timber Awards and Voltimum Smart Solutions Awards, all taking place throughout UKCW.
Once inspired by the exhibitors and seminars it’s time to unwind at the Beer Festival, sponsored by Velux, with street food, rockaoke, and a gin and fizz bar. FIX Radio will be broadcasting from here throughout the event. You can also visit the Central Bar in Hall 11 sponsored by Elliott Group and the Timber Bar in Hall 9 sponsored by Germany Trade & Invest.
Keep up to date via www.ukconstructionweek.com and Twitter at @UK_CW or using the hashtag #UKCW2018.
Images: 01-03. UKCW will feature the Offsite Theatre and a range of offsite exhibitors 2 3
After some delay, the Government finally launched its much-anticipated Construction Sector Deal (CSD) in July, with a vison to develop an industry able to respond to the pressures of changing demographics, technological change and sustainable building. 1
The construction sector is central to the UK’s economic health and wellbeing yet forever seems to be tarnished by pockets of poor productivity, low quality, unpredictability and resistance to change. Talk of industry transformation, better collaboration and modernisation has been swirling around since the late Sir Michael Latham’s landmark report ‘Constructing the Team’ in 1994. The latest report to crystallise the industry’s key problems was Mark Farmer’s 2016 review, now simply known as ‘Modernise or Die’. This report was perhaps more brutal in its assessment of where things need to improve with the introduction of more offsite manufacture and the adoption of digital technology driving advanced industry and building performance.
The Construction Sector Deal – “an ambitious new partnership between the government and the construction industry” – was unveiled by the Business and Energy Secretary Greg Clark, in a speech to the Northern Powerhouse Summit in Newcastle, and set out how it will form part of the Clean Growth Grand Challenge (itself part of the wider Industrial Strategy) with the ‘Transforming Construction’ investment that is supporting lowcarbon approaches to housing.
With almost half of the economy reliant on the built environment and the services it enables, the Government is bringing together the construction, manufacturing, energy
and digital sectors to deliver innovative approaches that improve productivity and accelerate a shift to building safer, healthier and more affordable places to live and learn that use less energy.
“The construction industry is fundamental to growing our economy as we build to invest in our future,” said Business and Energy Secretary Greg Clark. “Major infrastructure projects like HS2 and the commitment to deliver 1.5 million homes by 2022 mean that we need a construction sector that can drive innovation, delivering homes and infrastructure quicker. As buildings account for around 30% of total emissions, we also want to ensure that we are at the global forefront in designing and building smart, energy efficient and affordable homes and buildings through the Clean Growth Grand Challenge. This Sector Deal is supported by the biggest government investment in construction for at least a decade and will drive economic growth and create well-paid highlyskilled jobs in every part of the UK.”
The Construction Sector Deal will deliver:
• £420 million investment in ‘bytes and mortar smart construction’investment will transform construction through use of digital building design, new manufacturing technologies and offsite manufacturing helping cut the time taken to deliver new build by 50%
• Cheaper energy bills for families and businesses – support Industrial
Strategy mission to halve the energy use of new builds by 2030
• 25,000 construction apprenticeship starts and 1,000 Construction T Level placements by 2020 to help give young people the skills that industry needs – with £34 million to scale up innovative training models across the country
• Improved global access to a $2.5 trillion export market – a globally-competitive sector targeting the growing international infrastructure market that is set to grow by 70% in the years ahead.
The £420 million joint investment aims to transform construction productivity by driving the development of new innovative construction materials and techniques which will speed up building time, reduce disruption and ensure the homes, workplaces and public buildings of the future are more energy efficient. The deal will support the development of affordable, ‘easy to construct’ homes, schools and other buildings which can be quickly and sustainably manufactured offsite, then assembled where and when needed.
Offsite methods are central to many of the projected upgrades in the UK’s built environment and wider infrastructure and a key way to:
“minimise the wastage, inefficiencies and delays that affect onsite construction, and enable production to happen in parallel with site preparation – speeding up construction and reducing disruption.”
The Government’s action to support construction and its ‘presumption in favour’ of offsite construction by 2019 across suitable capital programmes, where it represents best value for money plus the adoption of digital technologies, offers the potential to significantly improve the safety of buildings and to support the implementation of the recommendations of the Hackitt Review of Building Regulations and Fire Safety.
An upgrade in the procurement process is certainly something that many industry insiders have highlighted as necessary, alongside a radical change in how building performance is measured. The Construction Sector Deal clearly states: “The adoption of digital and offsite manufacturing techniques must be driven by construction clients who seek to procure for the ‘whole life’ performance of built assets, and to optimise this performance.”
Of course the problems rest in ‘what and how’ performance is measured. There is no single accepted standard procurement methodology for delivering whole-life performance. A standard methodology used across the sector, “would drive the construction supply chain to focus on the performance of assets across their whole life, and invest in the
capability and skills needed to deliver this. If this standard methodology is to be adopted by clients and the construction sector, then it will need to be supported by a single body of knowledge, a shared digital asset that is accessible to all and enables the rapid sharing of expertise and best practice.”
The Construction Sector Deal will also support the development of digital technologies that can underpin better integrated supply chains, through improved project management processes and logistics. It will also support the development of new construction products and construction applications for materials that are suitable for use in building components that are manufactured offsite.
“Securing this deal sends out a statement about the vital contribution our sector makes to the country,” said Andrew Wolstenholme, Co-Chair of the Construction Leadership Council. “Our industry builds the schools to educate the young, the hospitals to care for the sick, the police stations to keep us safe, the roads and railways that get us to work, the power stations
that keep us warm and the homes we return to each day. We are an industry that must be at the forefront of the UK’s drive for future growth and prosperity – and I’m confident that this deal will help to achieve that.”
Historically the Government has seemed reticent to engage with the construction industry even though in 2016, the construction trades, including the supply chain and professional services, created a turnover of £370 billion and employed around 3.1 million workers. But it would seem the pressing concerns of the dysfunctional and moribund housing market plus some blunt feedback from the construction industry itself has led to the type of positive commitments and direction of travel contained within the Construction Sector Deal.
For more information or to download the report Industrial Strategy: Construction Sector Deal visit: www.gov.uk/government/ publications/construction-sector-deal 2
Images:
01. Industry Strategy: Construction Sector Deal
02. The Government’s action to support construction and its ‘presumption in favour’ of offsite construction by 2019 across suitable capital programmes is driving offsite growth.
Courtesy PortakabinIn the past few years, the tall building industry has become increasingly interested in the use of timber as a major structural element in skyscrapers. We hear from Daniel Safarik, Senior Editor at the Council on Tall Buildings and Urban Habitat (CTBUH) on what the future may have in store.
This interest in tall timber has resulted in a now worldwide wave of research, built projects and ever-more daring speculative proposals using ‘mass timber’ – engineered wood products that are just as robust as their concrete and steel counterparts. In 2008 there was one mass timber building over eight stories tall. Today, there are nearly 40 complete, under construction or planned.
The reasoning behind building tall in timber lies in the inherent sustainability of wood as a building product. Foremost, wood is a renewable resource. By absorbing carbon dioxide, trees sequester carbon that would otherwise be released into the atmosphere. If wood is used – or re-used – as a building material, the carbon stays sequestered. This has always been true of wood, of course, but the reason it’s now considered scalable for taller construction has to do with the advancement of manufacturing methods that can bind and compress fragments of lower quality or waste wood into consistently strong glue-laminated panels. Such engineered systems, can provide structural integrity and fire resistance far beyond what is possible with ‘platform’ framing, which uses studs, wall plates and headers (dimensional lumber) to build structural platforms floor-by-floor.
Most importantly, engineered timber systems comparable to the fire resistance and loadbearing attributes of materials that most skyscrapers are made of – concrete and steel. Having said this, significant obstacles to widespread adoption remain.
The key to mass timber’s viability as a structural material for tall buildings lies in its name. Massive wood walls
and structural beams and columns comprised of engineered panels have demonstrated fire performance equal to concrete and in some cases, superior to steel. Wood unquestionably burns, so there would be smoke issues, which would require proper sprinklering, pressurisation and other tactics used in tall buildings today. But mass timber has to burn through many layers before it is structurally compromised – basically, it chars long before it collapses.
As more jurisdictions come to appreciate the aesthetic, economic and environmental advantages of tall timber, this is expected to change. Successful implementation of projects around the world – particularly in areas where forestry is a major regional industry such as in Scandinavian countries, the Pacific Northwest of the U.S. and British Columbia in Canada – will provide additional reference studies for practitioners elsewhere.
The second biggest obstacle is a lack of standardisation of construction materials, methods and definitions. There are many forms of mass timber and a wide degree of variance in approach when it comes to supporting tall timber structures. So there is a range of techniques from assemblages of highly similar panels for both floors and walls, to complex column/beam/outrigger combinations, such as are found in high-rises of steel and concrete. There are numerous proprietary systems and the connections between elements also vary widely. Often it is the location and orientation of the steel connectors between wood elements that can make all the difference to how long a structure can withstand fire or seismic action, and so determines its feasibility under local codes.
But this has not stopped a steady stream of proposals and construction projects, each taking on some of the vernacular characteristics of local conditions. Although on the one hand this is a limiting factor of mass standardisation, on the other it is a positive condition that encourages designers to exercise creativity and sensitivity to the local built and natural environment. CTBUH have developed an international committee with a plan to ultimately produce a CTBUH technical guide on high-rise timber construction.
For clarity, the structural types above indicate the primary structural system only, e.g., core, floor beams or horizontal trusses, and vertical columns. In reality, most mass timber buildings use some combination of timber, steel and concrete. Many rely on a concrete core or concrete slabs in order to provide stability and fire protection that will satisfy local codes. ‘All Timber’ generally means the core and the horizontal and vertical structure are all composed of timber.
Some of the more intriguing projects – completed, currently underway or on the drawing board –can be found overleaf.
A not-for-profit organisation founded in 1969 and headquartered at Chicago’s historic Monroe Building, the CTBUH is the world’s leading resource for professionals focused on the inception, design, construction, and operation of tall buildings and future cities.
For more information visit: www.ctbuh.org
Aptus Fastener Systems have developed the most comprehensive range of certified fastening solutions for the volumetric modular market.
Based in the UK, we have been stocking and servicing the developing offsite construction market for more than 20 years, supplying fastener solutions through the entire build process:
• Construction screws
• Reinforcement screws
• Connectors and brackets
• Facades and cladding
• Onsite / offsite lifting and installation
PRODUCT RANGES INCLUDE:
Heco Topix – Comprehensive range of ETA approved structural screws manufactured in Germany
Pitzl – Certified wood connection systems manufactured in Munich to the highest standards
Prostruct – ETA approved brackets and screws
Powerclamp and Rapid T-lift – lifting devices for on and offsite transportation.
For further information or to download our new brochure “Fastener solutions for modern methods of construction” visit our website:
www.aptusfasteners.co.uk
This map highlights several examples of tall timber buildings currently built, under construction or proposed around the world.
Timber at height is a construction trend that has spread across the globe. ZÜBLIN Timber have been at the forefront of tall timber in Germany with a number of projects including – when completed – the tallest timber building in Germany.
The ten-storey SKAIO high-rise in Heilbronn, based on a design by Berlin-based architectural firm Kaden+Lager, is being built by Stadtsiedlung Heilbronn GmbH and ZÜBLIN Timber. The SKAIO will be Germany’s first timber high-rise building and another milestone in multi-storey timber construction. When completed, it will be the tallest timber building in Germany.
The 34m building, being erected as part of the city exhibition for the BUGA 2019 horticulture show in Heilbronn, will have an above-ground gross floor area of 5,685m² and will offer space for 60 rental units with a total of 3,300m²
of living space. A bakery will move into the commercial space on the ground floor. The design for the SKAIO project was awarded to Kaden+Lager. The architectural firm has been a specialist in urban timber construction for many years and has designed several timber and timber hybrid buildings for a number of different clients. The building will be erected by ZÜBLIN Timber with the walls and ceilings constructed from timber. The hybrid structure will consist of a concrete base floor and the stairwell will consist of reinforced concrete. The façade will then be clad with aluminium panels externally.
A major advantage of timber construction is the relatively short time needed for construction, as the timber elements are largely prefabricated and merely require mounting and assembly onsite. “We build one floor a week,” says Markus Brandl, Project Manager at ZÜBLIN Timber. “The supports for the new buildings are made of glulam timber. For the timber walls and ceilings, ZÜBLIN Timber uses only spruce – mainly from German forests and is fully PEFC-certified.” That is an important requirement for additional certification as Stadtsiedlung Heilbronn GmbH is applying for gold certification for SKAIO from the German Sustainable Building Council (DGNB).
ZÜBLIN Timber, headquartered in Aichach, will build the new 34m building. The order by Stadtsiedlung Heilbronn GmbH includes a second hybrid timber building with five floors. This building, which is also being erected by ZÜBLIN, will have a gross floor area of 1,572m² and room for 13 apartments over five floors. Both structures form part of the city exhibition at the BUGA 2019 horticulture show and the new Neckarbogen neighbourhood.
For more information visit: www.zueblin-timber.com
Images:
01. The 34m SKAIO is Germany’s first timber high-rise.
02. 3XGRÜN is a five storey hybrid timber and concrete residential complex and was a highly successful prefabricated timber house prototype
03. The Treet in Norway is a 14-storey residential tower and is regarded as the world’s first timber skyscraper
04. Superior engineered timber products are boosting timber construction, Image: Leno®-3D (3D shaped CLT)
ZÜBLIN Timber stands for ambitious and pioneered solutions in the field of timber construction. We are your singlesource provider for the development, production, delivery and execution of high-quality construction systems, from timber construction projects to timber engineering to turnkey project execution. We work hand in hand with our clients to develop efficient solutions and a sustainable quality of life.
www.zueblin-timber.com
Western Building Systems, a Tyrone-based specialist construction firm has been a modular and offsite champion for decades. Celebrating its 35th anniversary in 2018, Western is steadfast when it comes to producing the next generation of offsite buildings across the UK and Ireland. Managing Director, Declan McCloskey, explains more.
Modular and offsite construction techniques are more important than ever in an era of increased market competitiveness, tight timescales, reduced spending and greater environmental impact awareness.
With the UK’s construction output reaching a record high in July 2018 it has been a busy time for the industry. However, the latest data from the office of National Statistics (ONS) shows that the total number of new orders in construction declined 6.5% between April and June. With fewer full order books, labour shortages, rising interest rates and utilities as well as increased material costs, the construction industry is not as efficient as it could be. In order to tackle these issues, it is crucial that Government bodies, local
authorities, architects, urban planners and key decision makers across the UK infrastructure landscape embrace the new generation of offsite construction techniques.
Western Building System’s state-ofthe-art offsite technique provides savings of approximately 20% as well as a total reduction in build-time of up to 50% for many projects. In light of the current climate, Western’s marketleading offsite approach is the obvious answer when it comes to delivering large scale projects quickly within tight budgets to precise standards.
Western Building Systems built its first modular classroom in 1986 in a time where the phrase portable classroom
roused images of draughty cabins with unreliable water and electricity connections that had been used far beyond their intended short-term lifespan – a far cry from the state-ofthe-art modular buildings delivered today. We have spent decades fine-tuning our approach to offsite projects and are proud of Western’s ability to challenge and overthrow negative preconceptions related to prefabricated buildings through our dedicated craftmanship, high standards and superior client service levels.
As a single source systems provider, Western has the capacity to manage project delivery from start to finish. From value engineering design
through to manufacturing modules and classroom furniture, integrating M&E and smart classroom technology, transportation, onsite construction and fit-out, we strongly believe that our ability to act as the single point of contact for programme delivery and management sets us apart from other offsite providers.
Western’s specialist modular construction technique delivers superior levels of efficiency compared to the wider market. For example, by utilising ‘lean’ process optimisation within our manufacturing plant, we are able to work towards zero-waste targets across all of our offsite projects.
Each fabricated modular building produced by Western Building Systems includes all mechanical, electrical, internal and external finishes. This streamlined approach to construction plays a huge role in significantly bringing down programme delivery timeframes. While this approach allows for consistent quality levels throughout, it also reduces the amount of time carbon dioxide-emitting machinery is used onsite. Approximately 50% of greenhouse gas emissions in the built environment are eradicated with our offsite technique.
A New Era for Western
With a well-established offsite portfolio spanning decades, Western has always been a family-run business valuing integrity and quality. As part of our long-term investment and expansion plan to ensure we remain at the forefront of the offsite and modular innovation and execution, our senior management team grew in 2018 with the appointment of a brand new Chief Executive.
A solid addition to Western’s marketleading management team, Shane Taggart brings with him a wealth of experience to help Western tackle increased demand for ultra-efficient solutions across the UK. Shane sees early engagement and planning as key to increasing efficiencies within the industry in a responsible way. In order to learn from pre-recession mistakes, it is vital that the offsite construction industry takes a long-term approach when delivering projects. Through effective planning, early engagement, high standards and horizon scanning, Western can provide the very best offsite solutions, built to stand the test of time and fully flex around future trends in technological innovation.
4
Western Building Systems is a family-owned specialist construction business that celebrates its 35th anniversary in 2018. It has delivered a wide range of significant traditional, offsite and hybrid construction projects throughout the UK and Ireland within the health, education, industrial, commercial and residential sectors. To find out more visit: www.westernbuild.com
Images:
01. Declan McCloskey, Managing Director, Western Building Systems
02. As a Single Source Systems provider, Western has the capacity to manage project delivery from start to finish
03: Western project: University of Essex Teaching Centre
04: Western’s Head Office and factory
As Managing Director of Cogent Consulting, Darren Richards is well placed to comment on how the world of offsite manufacturing has gained traction over the past 12 months. Here he shares his views on how the market is developing and which factors are influencing the sector.
The offsite manufacturing sector is an exciting place to be. We are seeing more inward investment than I have witnessed in my 25 years of working within the offsite arena. There are some acquisitions of existing players but primarily the investment is from new entrants and disruptors in to the space. This is making some of the mature and long-established businesses sit up and take notice.
The levels of confidence in the sector in respect of the long-term viability of offsite technology is greater than previously witnessed and is underpinned by the consistent and now joined-up messages from Government. Policies for procuring in favour of offsite technology and being held to account by the recent House of Lords Select Committee Report, is
changing the political landscape. Add to this, the rapid immergence of new private sector investments, especially in the housing industry and most notably within the Build to Rent (B2R) sector.
A number of significant procurement frameworks in the education and affordable housing sectors have also had major impact on changing the way offsite solutions are procured – in many instances with clients leaning heavily on the framework selection process to narrow down their technology and supplier options, thereby giving them more confidence to make the change.
Wider acceptance of offsite construction techniques will always be an ongoing challenge and the sector cannot afford to become complacent.
That said, the latest Cogent market statistics that we review on a half-yearly basis, indicate that offsite technology now has around a 12% share of total construction activity in the UK – which is a rise from circa 8% back as recently as 2015. Whilst this figure is a long way from reflecting the true potential of the sector, it is still significantly short of the declared 20-25% offsite construction activity that many of our contractor and developer clients are seeking, but most certainly heading in the right direction.
Naturally, offsite penetration varies in different markets but if we look in particular at structural timber technology and its success in the low-rise residential sector, a market share of circa 30% can be measured, and the recent cost comparison
report into timber and masonry –undertaken independently by Rider Levett Bucknall (RLB) – show that cost parity is being routinely delivered and in some instances, where DfMA has been truly embraced, timber frame as a build method is proving to be more cost-effective than masonry methods. This equation is likely to continue to develop further in favour of offsite technologies as the traditional industry skills crisis begins to harden in parallel to greater offsite manufacturing volumes and significant economies of scale. I do believe that with mature offsite technologies we are now genuinely at a tipping point and a point of no return, where certain traditional construction methods will be eroded and eventually eliminated.
Most of the offsite manufacturing clients that we work with – across all offsite technologies – are overloaded with work, so you would estimate that they are taking advantage of the opportunities presented. However, many are finding it challenging to fund the growth and to access the working capital required to cash-flow some of the major projects that are being presented as opportunities in the marketplace. It is a tricky balance to find – the balance between growth and over-extension. Many of the established offsite manufacturers are taking a sensibly cautious approach.
Capacity and skills within the offsite manufacturing sector will become a constraint in the not too distant future, so offsite manufacturers will need to keep investing and to do this they will need to be given the confidence of promised pipelines becoming reality. Many have been ‘bitten’ by false dawns and false promises in the past, where potential pipelines remained just that – potential. They are rightly nervous about over-extending. This is a long-term transformation of the construction sector and my view is that the opportunities will not disappear, so a sensible but accelerated approach is right for now – we’re now at a fast walking pace and just about ready to start jogging!
Clearly new offsite manufacturing entrants have the luxury of setting up advanced manufacturing facilities from day one and do not often have the historical burden of entrenched cultures or long-term fixed assets, that were perhaps purchased in a different
era, which is what the majority of the established offsite manufacturers have to contend with, so we don’t have a level playing field on which to make comparisons.
All of our ‘new entrant’ clients have embraced world-class manufacturing techniques and implemented integrated management systems, ERP solutions and BIM-enabled design techniques and it is totally gratifying to see that the sector is attracting this type and scale of investment. But I can count on my fingers and thumbs the numbers of companies that have entered the offsite manufacturing arena in this way and actually seen the light of day. Just as many have declared their intent and then never gone on to realise their ambitions. We currently receive half a dozen enquiries per month regarding new offsite manufacturing facilities and maybe one of these six will actually go on to achieve their ambition, as many are still struggling to raise the capital required.
There are plenty of visionaries out there but not many of them have got deep pockets. As such, our focus is to concentrate on the established players within the offsite manufacturing sector and to help them to realise their full potential and to get more out of the assets that they have. More often than not we are focusing on getting the
basics of the manufacturing operation right – estimating methods, design control, cost reconciliation, workflow mapping, capacity planning, material requirement planning, pre-kitting, labour balancing – much of which is not ‘rocket science’ but all of which requires a robust and well sequenced implementation plan (a Manufacturing Blueprint) and one that is cognisant of the needs of the business to continue to produce and to make money.
It is not often, if ever, that a business can hit the pause button to be restructured or reconfigured and so we find ourselves working in some pretty challenging environments. This is what makes us tick – we love the challenge and having done this type of activity for 25 years we can have complete empathy with the people that we are working with. After all, it is the people that run these businesses not the machines – yet!
For more information visit: www.cogent-consulting.co.uk
Hear more about offsite manufacturing at Modular Matters taking place at the NEC, Birmingham30.10.18 for more information visit: www.modularmatters.co.uk
reduce floor space and that provide flexibility for the constabulary’s everchanging operational requirements.
The site’s 42-cell suite exemplifies this. It is housed in a semi-circular precast concrete building and is served with an abundance of natural light. By positioning the main custody desk centrally, with the cell corridors radiating out, the suite also serves to guarantee custody officers a line of sight to each cell corridor. The custody suite, with the natural light and view of each corridor is not only designed to help officers but also improve the wellbeing of those being held in custody.
Lancashire Constabulary’s new divisional HQ has reached completion and features offsite precast technology to provide one of the UK’s largest custody suites, with innovative design and a more secure environment for officers and those in custody. 1 2
The facility – which sits on a 10,000m2 site on the outskirts of Blackpool, near the M55 motorway, and designed by leading property and construction consultancy McBains – will serve as the new headquarters for the police force’s West Division and house one of the largest custody suites in the UK.
Work on the three-storey facility, which has cost in excess of £20 million,
commenced in 2015, with McBains providing architecture, mechanical, electrical, and civil and structural engineering support to the building’s main contractor, Willmott Dixon. The new facility will replace the West Division’s existing base on Bonny Street, and, courtesy of its design, will provide staff with a more efficient work environment. This has been achieved through subtle design solutions, which
Mark Baseby, Director at McBains who oversaw the project, said: “It’s great news for Lancashire Constabulary and the wider community that officers will start moving into the new stateof-the-art headquarters over the next few weeks. The external appearance of the building takes its cues from Blackpool and the vibrant seaside environment with the use of colour and form derived from the sea and sand. The internal central atrium space is known as the Promenade. The essence of the scheme is the interface of three contrasting building types and fusing them together in an efficient and flexible way. This will provide an improved environment for staff and detainees, while delivering important efficiencies for the force.”
PCE was appointed by main contractor Willmott Dixon as specialist on a design and build basis to provide a single level custody suite building to the rear of the new Lancashire Constabulary West Division headquarters situated on Clifton Road in Blackpool. The 1,020m² custody suite consists of 95 internal walls, 26 corridor walls, 52 duct units, 87 solid slabs, that were manufactured in
precast reinforced concrete offsite to the high quality specifications required by the client and PCE’s own quality processes.
Nickie Brown, Managing Director of PCE said: “We were pleased to be working again with Willmott Dixon on such a project as the synergy between our two companies always provides
a first class outcome for the client, which is important and satisfying. Our combined approach to providing quality with speed of construction whilst maintaining the highest possible levels of Health and Safety, is a credit to the employees of both companies”
Tony Whitehead, Enabler for the Ministry of Justice, who recent visited
the new headquarters, said: “McBains and Willmott Dixon have delivered a building to be proud of – a welldesigned and well-constructed police base that effectively combines imaginative concept with careful attention to detail. The building represents a step-change in police accommodation, and will surely help strengthen staff well-being, service delivery, and the image of the Lancashire Constabulary in the community.”
The building reached Practical Completion on 19 June 2018 with staff set to move across from the Bonny Street base in the following weeks.
For more information visit: www.mcbains.co.uk www.pceltd.co.uk
Images:
01-02. A modern facility for Lancashire Constabulary. Courtesy McBains 03. A key feature of the erection process is the safe and careful turning of units. Courtesy PCE Ltd
Milbank Concrete Products, who have over 70 years’ experience in the production of high quality precast concrete products introduce Kallisto Stairs – a new concept in the UK for precast concrete curved stair design.
Kallisto’s expertise has been commissioned for luxury staircase installations in some of the most prestigious venues in the UK, working with architects, engineers and designers on a daily basis to produce stunning, durable precast concrete helical staircase installations.
Kallisto are dedicated to helping their customers succeed by providing beautifully sculpted precast concrete curved staircases as a cost-effective alternative over traditional, insitu methods – they believe they are the only company in the UK that can provide precast concrete curved staircases as economically as possible.
Manufactured and crafted by hand at their facility in Essex, Kallisto stairs are
delivered in one complete piece and fitted with ease in less than a day by their expert installation team covering the whole of the UK.
By offering an unparalleled service from the design stage through to manufacture, delivery and installation, Kallisto ensure that their client’s expectations are exceeded every time, whilst keeping production costs to a minimum. Kallisto ensures an element of sophistication and elegance; their stairs offer a versatile alternative to other traditional materials such as timber or steel. Resilient, solid and durable, a Kallisto stair can be attractively finished in a material best suited to the individual style and character of a development, such as marble, stone or timber.
For more information about how a Kallisto stair could completely transform your project, email: info@kallistostairs.co.uk or call 01787 220 564.
We have all experienced one of the hottest summers that the UK has had since 1977 and in its recently published report ‘Heatwaves: adapting to climate change’, the Environmental Audit Committee has called for tougher rules to ensure homes can deal with extreme heat.
As homes become more highly insulated, it is difficult for unwanted heat to escape during the summer months, resulting in a greater risk of overheating – a problem that is further compounded by a warming climate.
Alongside adequate ventilation and shading, the thermal mass provided by concrete and masonry construction offers another means of tackling overheating. Concrete and masonry’s thermal mass allows it to absorb and later release excess heat, helping smooth out the gains and stabilise the internal temperature. Heat stored in concrete and masonry is expelled at the end of the day by ventilating the building with cool night air. The combined benefit of thermal mass and night ventilation is accounted for in the SAP overheating check, which allows a reduction in the peak internal temperature of up to 3.5°C compared to an equivalent lightweight dwelling with night ventilation. Overheating in homes is increasing for two key reasons:
• Summertime temperatures are gradually rising as our climate continues to warm. 2015 was the warmest year on record and the Met Office is predicting a temperature increase of around 3°C in the south of England over the 21st century.
• There is a greater tendency for modern, highly insulated and airtight homes to overheat as heat is more easily trapped.
The use of thermal mass has become well established and is one of a number of good practice design techniques that can be employed to reduce the growing risk of overheating. Its use ranks highly in the
1
London Plan hierarchy of overheating measures, which designers and architects should apply to new buildings.
When it comes to modern construction, modern masonry homes can be designed to minimise the risk of overheating by deploying the thermal mass and other design measures whilst also delivering the highest levels of energy efficiency for heating in winter.
Tom de Saulles, Building Physicist at The Concrete Centre offers his view: “As you would expect, the masonry and concrete sector has for many years highlighted the role of thermal mass in helping address overheating in homes and the dangers of lightweight construction. Numerous organisations have also published design guidance on overheating that acknowledges the role thermal mass can play in helping tackle the issue. The collective understanding of all these organisations underpins the masonry and concrete sector’s messaging on thermal mass.”
Guidance on thermal mass and how to use it can be found in ‘Thermal Mass Explained’ a publication available at: www.concretecentre.com
• CIBSE TM60: Good practice in the design of homes, 2018
• The London Plan – cooling hierarchy, 2016
• Zero Carbon Hub: Overheating in Homes – The Big Picture, 2015
• Zero Carbon Hub: Solutions to Overheating in Homes, 2016
• Building Research EstablishmentOverheating in dwellings –guidance document, 2016
• Good Homes Alliance: Preventing overheating, 2014
• NHBC Foundation: Understanding overheating – where to start, 2012
• Technology Strategy Board: Design for future climate, 2008
• Energy Savings Trust – energy efficiency best practice in housingreducing overheating a designer’s guide, 2005
• Faber Maunsell: Control of overheating in future housing –design guidance for low energy strategies, 2003”
Image:
01. Courtesy Laing O’Rourke
A variety of wall construction membranes, roofing underlays and accessories from Protect has been installed into an innovative new modular concept manufactured by Tingdene Homes, holiday and park home specialists.
‘The Loft’ is a LABC-approved, two-storey holiday home designed and manufactured completely offsite in Tingdene Homes’ factory to UK Building Regulations, using cutting edge design to meet the needs of the growing ‘staycation’ market. A number of Protect products were installed on the first show home, including Protect BarriAir, an internal airtightness membrane, Protect VC Foil Ultra used as the insulating low emissivity vapour control layer, Protect TF200 Thermo, the insulating low emissivity breather membrane for external walls and Protect VP400 Plus LR, a roofing underlay offering unrestricted wind uplift resistance and exceptional vapour permeability.
Phil Harold, Quality Assurance Manager at Tingdene Homes commented: “The use of numerous Protect products for this development helped us meet specification and achieve our target U-values of 0.18 W/m2K for external walls and 0.14W/m2K for the roof element. With the many benefits of offsite manufacture over traditional construction including build speed, quality precision and reliability, we wanted a supplier who understood these principles to ensure our delivery demands were met. Protect supplied products quickly which enabled our process to run without interruption and facilitated swift turnaround at the factory.”
For details of Protect products and their suitability for modular construction, please visit www.protectmembranes.com, email info@protectmembranes.com or call 0161 905 5700, quoting ‘The Loft.’
Images:
01. The Loft from Tingdene Homes uses Protect construction membranes
Optimising design for manufacture and assembly (DfMA) and embracing a world-class manufacturing ethos are at the heart of the new EOS Facades operation which recently opened its doors to a wide range of delegates as part of the CPD certified Inside Offsite Factory Tour programme. 1
Developed for architects, contractors, engineers and clients - the EOS technical team together with the Etex Building Performance specification team hosted delegates at the company’s advanced manufacturing facility in County Durham. The tours included a presentation by the estimating team on how the EOS ‘lump sum’ quote is generated, a demonstration of EOS Facades’ design software, followed by a tour of the manufacturing facility and demonstrations of the advanced rollforming machinery.
Preceding the tour, the EOS technical team presented a CPD session covering a variety of topics relating to light steel framing technology plus examples of best practice applications and project case studies.
As one of the leading steel framing systems innovators, with over 14 years expertise across all construction sectors - EOS Facades’ expansion programme continues with a major extension to the company’s advanced offsite manufacturing facility and the development of a new metal fabrication centre.
In addition to the five Howick steel roll-forming machines currently in operation, to further expand the light steel-based product portfolio and capacity, EOS have invested in a new multi-width roll-forming machine, guillotines, press-brakes and automated sheet punching equipment, plus installed overhead cranes for lifting and moving frames and steel coils around the extended facility.
This activity has been undertaken in preparation for the increased workload generated by the development of a complete closed-panel (Thruwall®) walling solution and load-bearing panelised and cassette systems to support the acceleration of a wide array of offsite initiatives.
Steve Thompson, Managing Director of EOS Facades said of the expansion programme: “We have invested in our own fabrication plant to be self-sufficient in manufacturing our ancillary parts such as angles, brackets and wind-posts, for example. This will support our market leading ‘lump-sum’ all-inclusive pricing initiative and complement our ‘total supply’ offering – enabling us to support downstream sub-assembly
and volumetric module manufacturing operations as well as façade infill walling activity on site.”
EOS Facade’s light gauge steel frame range offers 65mm, 100mm, 150mm, 200mm and 250mm deep sections in gauge thicknesses ranging from 1.2mm to 2mm and section lengths are fully customisable. With the latest addition of the multi-width roll-forming machine, the company can now also produce U-track sections ranging from 65mm – 254mm wide in thicknesses ranging from 1mm to 3mm with a capability to run a wide range of slotted head track profiles.
In expanding the machinery operation, EOS have also been able to focus on material flow - minimising non-valueadded tasks, and adopting truly lean manufacturing principles to embrace greater process standardisation and repeatability to offer clients reduced lead times and enhanced quality control. The new manufacturing facility layout also permits greater capacity for framing and panelisation together with enhanced offsite manufacturing processes in respect of boarding activity.
Tried, Tested and WarrantiedThruwall® Systems
EOS Facades is now part of Etex Building Performance which brings together the products and solutions of three major construction materials companies. Through combined expertise in drywall, passive fire protection and steel framing systems – the group has created a range of unique solutions for building envelopes. The manufacturing facility extension has also been designed
to manage the increase in volume of work with the development of the Etex Building Performance Thruwall® system, integrating the product ranges from the group including Siniat, Promat and EOS Facades.
The Thruwall® solution was of particular focus for many of the Factory Tour delegates with many interested in the increased offsite value-adding that is now in operation.
Steve Thompson continued: “The combination of expertise from the Etex Building Performance group in drylining, external sheathing and steel framing systems, as well as passive fire protection - means that we are uniquely positioned to bring together these elements to create a range of tested and warrantied Thruwall® systems. Meeting building performance requirements for fire, thermal, weathering, acoustics and airtightness – the newly launched Thruwall® systems provide an ‘all in one’ certified solution with crucial time and costs benefits.”
The fully tested Thruwall® solutions for non-loadbearing external building envelopes - combines BBA Certified non-combustible A1 external sheathing, engineered steel framing system and internal wall linings. With a turnover of over £200 million, Etex Building Performance Group backs the Thruwall® Systems with a 30-year warranty.
To register for future Inside Offsite Factory Tours visit: www.offsitehub.co.uk/inside-offsite/
For more information on the technology and offsite solutions offered by EOS Facades visit: www.eos-facades.co.uk/our-solutions/
Images: 01-03. Delegates were shown the new multi width roll-forming machine, guillotines, press-brakes and automated sheet punching equipment
Driven by the demand for more predictability throughout the construction process, EOS are geared up and ready to bring new systems to market. With 14 years’ design and manufacturing expertise in panelised, volumetric modular and pod technology, Managing Director, Steve Thompson discusses the benefits of light gauge steel (LGSF) for load-bearing applications.
Being part of the Etex Building Performance group brings tremendous benefits to our clients. The combined expertise of Siniat, Promat and EOS in drywall, passive fire protection and light gauge steel frame has created a range of unique offsite manufactured load-bearing systems. The backing of a global brand has resulted in a continuous investment programme for EOS to expand and advance our factory facility, together with increasing our manufacturing capacity and product portfolio.
Optimising value engineering, EOS together with our partners within the Etex Building Performance group, are
developing and engineering a range of fully tested and warrantied LGSF systems with a load-bearing capability of up to nine storeys. We also supply load-bearing systems for pod and modular specialists. EOS turn cold formed steel into structures which are pre-boarded offsite – providing highly engineered, lightweight and robust non-combustible systems.
Where margins are tight, cost certainty and predictability are of paramount importance. Certainty in specification and performance is also crucial. Essential to delivering the best and most profitable results, is early integration in the design
and construction process. Our most successful outcomes are where we have been engaged prior to the main contractor’s tender and where we have tailored full design and manufacturing packages for the tender submission. For specifiers there is a great deal to consider and a system approach removes much of the hassle and uncertainty in achieving the design brief.
The high strength to weight ratio of LGSF load-bearing systems significantly exceeds that of timber or concrete and by reducing the total load up to 60%, these systems allow developers to save costs in the ground by reducing the foundation requirement. Insurance offers more costs savings as light gauge steel is non-combustible, it has a lower builder’s risk premium.
Offsite manufacture reduces site labour costs and construction waste but also importantly, improves quality by the factory-fitting of boards and the integration of M&E in the design process.
Manufactured to highly accurate tolerances of +0mm / -2mm – our total building frames are supplied in pre-assembled offsite manufactured panels and cassettes. All floors and roofs are supplied in either C-sections or lattice beam cassettes. All ancillary components are included within the scope of supply. Operating to BIM Level 2, EOS use design for manufacture and assembly (DfMA) protocols to fully test designs to
digitally eliminate clashes and errors, ensuring smooth installation onsite or within upstream manufacturing activity. Loading factors taken into consideration during the design and engineering phase include – overall stability, imposed, dead and wind loads and disproportionate collapse.
Profit margins for main contractors are often extremely tight and the unpredictability of traditional building methods, led to a boom and bust construction economy. Change has been a long time coming but the very nature of the industry and uncertainty within, has led to a lack of investment and subsequent innovation. Without innovation, the market stagnates and
to advance and develop, you must be prepared to invest – which is our approach. To take our industry forward, dedicated investment is required in research, development and testing – only then can genuine product innovation be realised.
For the optimum results and costs savings, main contractors, architects and designers need to engage at an early stage. Supply chain integration and collaboration throughout the design and installation, is equally important. With every project, EOS operatives are available to attend site to offer technical advice, design assistance and installation training.
Installer teams can benefit from our ‘Tool Box Talks’ and phased site visits to offer independent quality checks on the installation. We are operating in exciting times for the built environment – whatever the construction sector –there has never been a better time to capitalise on the raft of benefits that factory-based offsite technologies can deliver.
For more information visit: www.eos-structures.co.uk
Images: 01-04. Light gauge steel frame is central to a wide range of building types in a number of sectors
A critical concern for the construction industry is its poor level of productivity. When assessed against other industries, especially manufacturing-led ones, the disparity is stark. The Modular Matters conference taking place at the Birmingham NEC, 30 October 2018 will focus on how to improve and maintain a more efficient built environment.
Valuable insights and intelligence can be gained from the Modular Matters conference and event. Chaired by Darren Richards, leading offsite expert from Cogent Consulting, the conference and exhibition will focus on the latest developments, innovations and investments in the volumetric modular sector and outline the continuing evolution of this dynamic offsite construction technology.
Recent levels of market activity relating to Government announcements, major investments and industry reports represent a real opportunity for manufacturers and suppliers in the volumetric modular sector. Innovation is happening at pace and those operating in the supply chain need to keep informed of the latest technological developments.
The use of volumetric modular construction is directly influenced by the client’s requirements for speed of construction, quality, added benefits of economy of scale, as well as single point procurement. Architects and engineers who understand the parameters of volumetric modular technology and have the right mindset to optimise the real benefits, are now moving away from design for construction approaches to design for manufacture and assembly principles.
With a diverse range of volumetric modular system technologies, architectural interest can be maintained through innovative design and invisible standardisation. Volumetric modular solutions can radically reduce risk for developers and contractors on a number of levels.
Delivering enhanced predictability, volumetric modular technology reduces the financial risk and personal implications of delays, project overruns and accidents onsite together with mitigating the impact of an increasingly volatile labour market.
With a diverse product portfolio, the range of volumetric modular technologies, materials and applications is rapidly expanding, encompassing education, commercial, hotels, student residences, military accommodation private and social housing together with the private rental sector. Growth in the sector is exponential and cannot be ignored.
Volumetric modular solutions are becoming increasingly commercially viable, with structural engineers and architects now designing and engineering for high rise modular buildings and embracing true Design for Manufacture and Assembly (DfMA) principles. It is clear that economies of scale are being realised and modular construction is becoming a truly viable alternative to traditional construction
techniques. There can be no doubt that there is a groundswell of activity in respect of offsite construction and there is a growing sense that the time is now right to embrace the latest technology on offer.
Modular Matters is organised in partnership with the Modular & Portable Building Association (MPBA) and this one-day conference will
create a platform for delegates to learn directly from specialist counterparts on how to apply volumetric modular technology and bust the myths on design constraints. The event will create a dynamic and interactive learning experience through presentations, panel debate and the wide array of exhibitors. This is an excellent opportunity for construction clients and their professional advisers to network with industry experts and discuss the latest advances in volumetric modular technology.
For more information on the conference programme and to book your place visit: www.modularmatters.co.uk
Images:
01. Chapman Taylor – Holiday Inn Trafford Park
02. HTA Design – Greenwich Creekside
03. Studio Anyo – Marriott Hotel Luton Airport
The recent Social Housing Green Paper aims to rebalance the relationship between residents and landlords, tackle stigma and ensure that social housing can be both a stable base that supports people when they need it and support social mobility.
The Green Paper also aims to break down inequalities in social housing and ensure tenants feel at home in their community rather than seeing it as just a place to live. The design and quality of homes and their surrounding area are at the heart of this paper that highlights the importance of good design ideas in newbuild social housing.
The paper outlines plans to build on the new borrowing capacity granted to local authorities by exploring new flexibilities on how they spend the money from homes sold under the Right to Buy scheme, and not requiring them to sell off vacant, higher value stock. The paper asks how the current complaints process can be reformed so that it is quicker and easier –especially important when dealing with safety concerns.
The Green Paper and additional consultation gives everyone the opportunity to submit views on proposals for the future of social housing and will run until 6 November 2018.
Launching the Green Paper, Secretary of State for Communities, Rt Hon James Brokenshire MP, said: “Providing quality and fair social housing is a priority for this government. Our Green
Paper offers a landmark opportunity for major reform to improve fairness, quality and safety to residents living in social housing across the country. With four million households living in social housing and this projected to rise annually, it’s crucial that we tackle the issues facing both residents and landlords in social housing.”
Björn Conway, Chief Executive of modular provider ilke Homes said: “The Government report is a welcome step towards levelling the playing field between social tenants and landlords. The details included in the report show that the Government is committed to ramping up efforts to remove the stigma attached to social housing. However, if we want to create the thriving communities detailed in the report, we first need to tackle the wider issue at hand of delivering a pipeline of housing availability to those that need it most. While this report is making inroads by granting new borrowing capacity to local authorities to be able to borrow to build homes, it is just a start. We need a firm commitment by the Government to support local authorities across the country to help build these new homes.
“This is where innovative technology can play a part, implemented through
modern methods of construction. Modular homes built in factories and delivered to sites across the UK can be fitted in a single day, with up to six properties installed per day. This means the timeframe from installation of the homes to families moving in can take just two weeks, providing a reliable and predictable timeline for local authorities, housing associations and developers to work towards. Offsite construction is gaining momentum as one of the only viable solutions to overcome the challenges the industry is facing and solve the housing shortage.”
ilke Homes were recently appointed as preferred modular homes provider for Efficiency East Midlands’ (EEM) modular homes Dynamic Purchasing System (DPS). EEM is a not-for-profit procurement consortium that was set up eight years ago to generate efficiencies for its membership through collaboration, combined volumes, quality products and high-level construction services.
Ilke Homes will now be part of EEM’s supply chain, delivering high-quality residential homes on behalf of clients, for those who need it most in the region – including ALMO’s and Housing Associations. The 129 member organisations of the EEM are able to use services compliantly without having to undertake their own tender process.
For more information visit: www.ilkehomes.co.uk
To respond to the Green Paper consultation visit: www.gov.uk/ government/consultations/a-newdeal-for-social-housing
On the back of the Government’s latest disclosure on the shortage of secondary school places, now more
than
ever, speed and efficiency
come
to the forefront of decision making for academy trusts and local authorities.
Modular and offsite construction specialist Portakabin is working hard to revise any traditionally held perceptions about what can be achieved using modular and showcase not only the capability of offsite but also the speed.
Last month, Portakabin secured a place on the Education and Skills Funding Agency (ESFA) modular framework for the secondary schools block replacement programme.
Emily King, Education Specialist for Portakabin comments: “Our appointment to this new framework comes as work continues on completing Priory Fields School in Dover. This is the final school following the successful delivery of five other
schemes under the original Priority Schools Building Programme. It’s positive to see the Government switch from Primary Schools to Secondary Schools and on this framework, modular innovation brings valuable time-saving benefits to schools which often have an urgent demand for space within increasingly tight timeframes.”
With half the local authorities in England expected to have a shortfall of 134,000 places by 2023-24, the new framework comes at a crucial time. With manufacturers working closely with bodies such as the ESFA, they can help drive cost-savings by sharing product knowledge as well as encouraging standardisation of certain structures.
In the past year, Portakabin has developed an advanced product to enhance its ever evolving educational offer. Now schools, colleges and universities can benefit from a modular double height space fulfilling requirements for sports halls and events spaces; considerably reducing time on site and in turn, any disruption to students.
Find out more about developing the potential of education offsite with Emily King at Modular Matters on Tuesday 30 October at the NEC in Birmingham.
MPBA representing the industry for 80 years in the Offsite Sector.
• High quality learning and training
• Industry wide marketing promotion
• Access to the
• FREE Guidance and support on all health and safety issues
• FREE Technical Advice
• FREE Employment law services
• FREE Regular industry and legislative updates
McAvoy recently handed over a new passenger facility at Dublin Airport that at over 19m wide, is believed to be the largest single span modular building delivered to date in the UK and Ireland.
The new €22 million South Gates passenger boarding area has been developed to meet the huge growth in passenger numbers at Dublin Airport and will be used mainly by Aer Lingus for flights to the UK and continental Europe. It provides seven boarding gates to serve nine aircraft stands and is designed to accommodate around 8,000 passengers a day. Dublin Airport has experienced a 6% increase in passenger numbers in the past year and a record 29.6 million passengers used the airport in the last year.
The management contractor for the project was Flynn Management & Contractors and the lead consultants were Arup. The building was designed by concept architects Kavanagh Tuite and delivered by project architects Blue Sky. The 2,200m2 facility was constructed offsite at the McAvoy production centre in Lisburn, Northern Ireland and was craned into position in 16 days as 77 steel-framed modules. The building system was engineered to achieve over 19m wide uninterrupted clear spans, which is believed to be an industry first for modular construction.
Hot rolled steel beams were used to remove the requirement for internal columns.
The building, which is around 120m long, has the flexibility to accommodate departing flights in the busy early morning period and flight arrivals in the evening. It can also be segregated so around 1,000 departing and arriving passengers can be processed at the same time. Facilities include boarding gates, a café, toilets, baby changing and a workstation area with plugs and charging points.
Commenting on the new facility, Iain Heath, Project Manager at Dublin Airport, said: “This is one of the fastest projects we have ever completed at the airport – from planning to the first flight in just 18 months. The finished building speaks for itself. It is a handsome new facility with high quality finishes and clean architectural lines. We were working to a very constrained programme to have the building operational ahead of the busy summer season. The project and its innovative use of offsite construction is a fantastic achievement for the whole team.
“We were impressed with how McAvoy used BIM and virtual reality. As an airport we have a complex approvals process, but the digital techniques allowed the senior management
team to ‘walk through’ the building and to experience the facility, which facilitated design sign off. In addition to the programme benefits, offsite construction also meant fewer trades working onsite and a smaller site footprint. This approach had far less operational impact for the airport and the closure of fewer aircraft stands with reduced timeframes.”
The Dublin Airport scheme was designed to meet stringent fire safety regulations that exceeded Building Regulations. All mechanical and electrical services – including data communications, fire and security –had to link into the existing live airport terminal systems, which was a hugely complex operation undertaken by McAvoy. A specially-designed ceiling solution provides a high standard of acoustics and its chequerboard appearance has created a strong visual feature.
Brian Looney, Contracts Manager at Flynn Management & Contractors said: “The principal driver for offsite construction was to reduce the programme. Having fewer trades onsite is also a benefit for airport projects such as this where the site is very constrained, and the highest standards of security have to be maintained at all times. This project has pushed the boundaries of offsite construction to create a valuable infrastructure facility. The quality of the finished building is excellent, and you would never know this is a modular building.”
Eugene Lynch, Managing Director of The McAvoy Group, added: “This project successfully demonstrates the potential for offsite to improve the efficiency of airport construction, particularly in the development of airside facilities where it is so critical to minimise any impact on existing operations. We can reduce work on highly secure and constrained sites and rapidly install the buildings in a fast and efficient process, with no compromise on design.”
For more information visit: www.mcavoygroup.com
O pen conversation to scope the why, the how and the where-for to deliver a smart offsite proposal to meet budget and timing considerations.
Working through the project methodology, logistics and compliance requirement to achieve the necessary approvals and cost affordability.
02.
Understanding the finer detail of your requirements and enabling you to contract test your proposal with the use of virtual reality.
03.
Smart Offsite construction running in tandem with onsite activity to ensure your building is on time, on budget and delivered safely.
Transition management with agreed maintenance periods to guarantee a soft landing as your building comes to life and inspires brighter futures.
05.
Moduloft are proving that bespoke modular building makes sense for commercial projects for speed and cost certainty and recently installed modules at St Albans High School for Girls, Hertfordshire.
offsite construction is now the way forward for commercial projects, where focus is on speed, quality and cost certainty is paramount. Moduloft offers the ideal solution to commercial projects whereby time, cost certainty and an agreed completion date of the build are guaranteed. Modular offsite build is fast becoming a key to existing properties extending with new additional space that is built offsite so reducing impact and disruption onsite.
Moduloft are experts in bespoke modular build, so that you can gain your individually designed space to an agreed schedule. Our expert team can work alongside the architect or independently to produce a design that meets all the project specification for the internal space and the external finish to work with the existing building.
1Bespoke modular build by Moduloft means every project we design, build and complete is totally tailored to its commercial environment and agreed specifications. Our focus is to deliver the highest standard on every project and as we handle all aspects of the project from build, delivery, lift and install, we can give our customers total confidence.
Commercial projects need a partner that can deliver to an agreed budget and time plan and Moduloft offers both cost certainty through their thorough quote to specification process, and your build schedule is planned into the factory and is scheduled to your delivery date. Our projects to date demonstrate that Moduloft can work to deliver a variety of modular buildings ranging from school extensions gaining additional classrooms to rooftop air space
developments gaining additional penthouse apartments. We have the skills to accommodate all size and scale of projects.
St Albans High School for Girls was keen to gain new classrooms during the six week summer holiday while the school was closed. The build was to be completed during the summer break so all works had to take place during the six weeks and be completed in time for the new term in September. Moduloft’s expert team carried out all stages of the project from factory build, delivery of modules, crane lift, completion and commissioning, all to schedule.
The factory build took 12 weeks, key updates of the progress were communicated every step of the way by the Moduloft team. The delivery and lift were planned for the end of July and took place with ease, all handled by the install team. Any project lift is fully managed by us and includes traffic management, road closures and overall co-ordination onsite.
“The Moduloft solution was selected as the most efficient option to deliver three new classrooms in the physical space available,” said Paul Owen MBA, St Albans High School Estates Manager. “And within a very tight and time-constrained summer holiday period. We are extremely pleased with the end-result that was completed on-time and to budget, and it looks great both internally and externally.”
For more information visit: www.moduloft.co.uk
Images:
01. Moduloft’s expert team carried out all stages of the project from factory build, delivery of modules, crane lift, completion and commissioning
Adding Real Value in Recruitment
Passionate about offsite construction
With a passion for the construction industry, we are the UK’s leading recruitment consultancy for the offsite sector and its supply chain.
• Over 80% of our business is repeat or referral
• Many of our vacancies are exclusive - you will not find them elsewhere
• We have dedicated divisions for Sales, Design, Construction and Manufacturing
• Our staff are experts in their field and will understand exactly what you are looking for
2687.18
0117
959
2008
www.arvsolutions.co.uk
info@arvsolutions.co.uk
Follow us: @arvsolutions
SYSTEMS ADVERT_OFFSITE MAGAZINE.qxp_Layout 1 17/05/2018 10:42 Page 1
Our Eco Classroom builds on our decades of experience in providing modular solutions. It’s a sustainable future-proof system that meets our customers’ needs for years to come.
/ Regulated temperature without the need for additional summer cooling
/ High performance triple glazed windows and triple-layered wall insulation
/ Solar PV roof panels create all the energy the building requires*
Modular and portable buildings The possibilities are endless... t. 01274 873 232 e. info@elitesystemsgb.co.uk w. www.elitesystemsgb.co.uk
/ Environmentally focused materials throughout
/ Rainwater harvesting system built into the design, so no large unsightly exterior tank is required
/ Assessed** to BREEAM Outstanding
*Based on average across the year, dependent on final installation and site conditions. **Dependent on final installation and site conditions.
ELITEThe great advantage that offsite construction holds over traditional methods in terms of durability is the controlled factory environment in which the units are assembled. The benefits of factory processes are clear: greater accuracy, speed and precision, reliability of materials and manufacture, improved performance and a potential reduction in construction costs if units can be delivered at scale and through repeatable design.
Traditionally constructed buildings in the UK have been seen to fall short by up to 30% in terms of design performance versus actual performance. Properties built in a factory have a higher level of quality control compared with a construction site, improving the performance of the building over its lifetime as well as leading to improved overall durability.
The factory environment is free from many of the variables that plague onsite construction such as unpredictable weather and variable quality control procedures. This is an important factor considering there is a growing deficit of skilled workers within the sector. Creating professional, controlled and safe working environments, as offered by offsite construction, can help to attract new talent and go some way to addressing this shortfall in industry resource.
When it comes to construction and durability, market and consumer confidence lies predominantly with tried and tested methods. It is therefore unsurprising that the sector is still very much getting to grips with offsite construction, with some funders and insurers remaining nervous and unsure as to how non-traditionally built properties will perform over time. While caution in the face of change is
prudent, it would be unwise to allow it to impede progress and innovation. Insurers and others in the industry are concerned about systemic failure, fire spread and water ingress affecting offsite techniques both during and after construction. These concerns are, in part, being addressed by the Buildoffsite Property Assurance Scheme (BOPAS) which seeks to provide long-term assurance to mortgage lenders, valuers, funders, landlords and homeowners that properties built using non-traditional forms of construction will be robust for at least 60 years, without requiring disproportionate maintenance.
The BOPAS assessment process –which reviews all aspects of the offsite technology including the requisite onsite works – is setting the benchmark for quality assessment in the offsite sector. BOPAS registration levels for 2018 should significantly exceed those of previous years and schemes of this kind will be integral to winning over the market’s confidence.
For more information visit:
www.blpinsurance.com
Images: 01-02. Offsite manufactured buildings are of the highest quality and indistinguishable from traditional-led construction 2
Offsite manufacturers are continually looking to refine and improve their build process in order to supply better quality products into the marketplace by reducing production time, waste and cost.
On The Level (OTL) manufacture and supply wet room flooring solutions in readiness for either vinyl sheet for level access or tiled finishes. Their pre-tanked bathroom floors can be manufactured to suit any bathroom design, offering flexibility and choice for end-user clients. Early engagement and collaboration with volumetric and bathroom pod manufacturers allows OTL to overcome any design challenge and contribute towards delivering quality product using sustainable construction materials, whilst keeping the installation process simple for factory-based operatives to install their floors.
Made to exacting measurements, complete bathroom floors can be produced with integrated falls in shower areas, upstands for internal walls to be constructed upon, and flexibility on gully location, allowing floors to be produced in line with your design requirements. For wet rooms – decorative grilles and channels are available in many designs and finishes providing lots of choice for architects and designers. Established for over 30 years, OTL have a wealth of experience working with well-known offsite manufacturers, delivering projects in multiple sectors, including hotel, residential, healthcare, student and MOD accommodation.
For more information visit: www.onthelevel.co.uk
Images: 01-02. Pre-tanked bathroom floors can be manufactured to suit any bathroom design
One of the key selling points for offsite construction is the vast improvements in quality. What procedures are in place for monitoring product performance and maintaining high levels of real value?
When a house is built using standard onsite construction methods, the building regulations officer and thirdparty insurance representatives attend site during five different stages to inspect the quality of the workmanship and check that all the procedures are followed to achieve a building, extension or alteration which meets current building regulations and standards. This procedure permits final sign-off of the building, and typically provides third party warranty for the first 10 years of its life.
In essence the process works well, however on a large housing development, not every house is inspected at each of the check points. As a test house, Lucideon is often called in to identify failures due to a number of different mechanisms, including incorrectly placed wall ties, under strength mortars, and cracking in floors and brickwork. The failures are generally a result of inferior quality materials or poor workmanship, and ultimately, the insurance provider is responsible for correcting the structural faults.
In the past, offsite construction has had a reputation for poor quality build whereas the reality is quite the opposite. The selling point for offsite construction should be the quality of the build with regards to repeatability, consistency and high standards of workmanship. In spite of this, there can be some concern over the quality as no third-party checks are made during the prefabrication process and hence the insurer is only seeing the finished product and issuing guarantees against an unknown quantity.
There are schemes in place that rely on the manufacturer to prove the finished product is fit for purpose, and this may be the case for the modules and panels submitted for the upfront assessment, however to ensure the consistency of the product, it may be necessary to prove the on-going quality of the product during the manufacturing process.
The certification of most individual construction products falls under the Construction Products Regulations (CPR). Since July 2013, the CPR
requires products which are produced in line with harmonised European Standards to be tested and CE marked. CE marking proves the suitability of the product and ensures the on-going quality using Factory Production Control (FPC) – this is often required to be monitored by a third-party accreditation body.
When products do not have a route to enable them to be CE marked, the market will generally push these down the path of third-party certification. Buildings of a modular and panel construction fall outside of this scope. As a result, there are no mandatory requirements for performance testing of either the individual panels or full modules, and there is no schedule for a FPC system to be implemented throughout the production process. At present this does not appear to be an issue, but as the market grows, there may be a need for manufacturers to differentiate themselves from competitors by providing additional assurance of the ongoing quality of their end products. Ensuring only quality products enter the market will help the offsite sector continue to prosper and banish the old stigma of poor quality buildings.
For more information visit: www.lucideon.com
Hear more at:
Lucideon can help you at all stages of the design and construction process for offsite and modular buildings, from materials selection and manufacturing to installation and verification. Our wide-ranging testing, process and verification capabilities cover every aspect of your products, so you can create a comprehensive, reliable solution.
Andy Ormerod, Balfour Beatty Managing Director, Plant and Fleet Services is leading Balfour Beatty’s commitment to reducing onsite activity by 25% by 2025. Here, he explains how the new generation of industrialised construction methods has the potential to transform the way the industry operates and offers seven steps on how in the construction industry can work towards securing the benefits of offsite construction. 1
As construction professionals, we are all too aware of the problems that we have to manage on a daily basis in terms of: delivering within budget, margins, mitigating any environmental impacts, managing the shortage of skills and above all – ensuring the safety of all those who come into contact with our sites.
Many in the industry are also aware that the new industrialised construction techniques available –which include offsite and modular building techniques – have the potential to reduce the amount of onsite activity. This will enable the industry to overcome its long-standing problems by increasing efficiency
and production, improve the quality construction projects and enhance safety on our construction sites.
Yet despite the widespread recognition of the very real benefits that industrialised construction methods bring, only 12% of construction today involves offsite
methods. On the surface this seems strange because the construction industry in the UK can rightly be proud of its investment and development of new technologies – such as Building Information Management (BIM) – so how can companies embrace these industrialised construction techniques and realise the many benefits they bring?
At Balfour Beatty, we have embraced such techniques and are already realising the benefits. Recently, in collaboration with our client Scottish & Southern Electricity Networks, we installed 140 newly-designed composite poles to carry a power cable connecting the remote Dorenell wind farm to the Blackhillock Substation, near Keith in Scotland. We shipped two specialist Erickson S64-F Air Crane helicopters from the USA to lift and install the poles. This innovative installation method meant that we did not need access tracks for the erection process and could install the poles far quicker in locations that would have been difficult to access by traditional crane methods, whilst also minimising the impact of our works on the Scottish countryside. Using this method also meant we could preassemble all the poles in a single location, creating a standardised high quality assembly and fabrication facility and reducing the work that was required at each tower location. This made the fabrication and assembly of each pole safer, quicker, easier and more accurate.
So if the benefits can easily be proven: Why the inertia? In an industry where interests are unaligned, competition is intense and margins are thin, ‘breaking the mould’ does not seem to be a viable option for construction providers. Additionally, the fear of failing by trying something new still persists for those responsible for procuring construction projects. But doing things in the same way will mean that the construction industry will continue to be dogged by the same issues.
In our recent policy paper: ‘25% by 2025: Streamlined construction by 25% by 2025 – seven steps to offsite and modular building’, we not only outline how Balfour Beatty has made offsite production a core part of our strategy with our commitment to reducing onsite activity by 25% by 2025, but we also offer seven steps on how both providers and procurers
in the construction industry can overcome its inertia towards offsite production and transform its model:
1. Ensuring the continuity of pipeline flow – construction commissioners must take a long-term view of their construction requirements. The economies of scale are not realised in one scheme, but over an extended timeframe over a number of schemes.
2. Improve the standardisation of components and design – prioritising the standardisation of designs and components will incentivise the increased use of offsite manufacture.
3. Invest in research and development (R&D) – we welcome the £170 million Transforming Construction Programme, which aims to leverage a further £250 million from the industry through its contribution to funding R&D projects. However, the sums involved are still relatively small. More investment is needed given the changes involved to make offsite construction a reality which means construction has to fundamentally change the way it has operated since its inception.
4. Change the construction procurement model – the current procurement model, which favours lowest-cost tendering, leads to a false economy of short-term cost savings at the expense of investment in the innovative new techniques and materials required.
5. Collaborate relentlessly –construction must become more collaborative and work harder at sharing best practice in order to drive change.
6. Learn from the manufacturing industry – construction has much to learn from the manufacturing industry. For example, the aerospace and automotive sectors use offsite manufacturing techniques from digital models in the design phase through to components in a factory. These methods can be applied to the construction industry.
7. Invest in skills for the future - offsite manufacturing requires a completely different approach and set of skills –again this requires investment. We must accelerate the pace of change. The costs to the construction industry by not embracing the new
methods on offer are high in terms of efficiencies, quality and safety. Government, as the industry’s largest client, should take a lead, however to fully realise these benefits of offsite construction – all in the construction sector must commit to change.
You can read or download the recent Balfour Beatty policy paper: 25% by 2025: Streamlined construction – seven steps to offsite and modular building at: www.balfourbeatty.com/howwework/public-policy 2 3
Images:
01. Construction has much to learn from the manufacturing industry and digital design
02. Erickson S-64 Air Crane helicopter installing the new composite poles
03. 25% by 2025: Streamlined constructionseven steps to offsite and modular building report
After a turbulent few years, confidence is returning within the construction world with interest in offsite construction in particular on the rise. Futurebuild and Offsite Magazine recently hosted a special ‘think tank’ session to discuss progress and understand what the future may hold.
The Construction Sector Deal published in July sets out a clear and ambitious plan to progress the adoption of offsite construction to meet key governmental targets in a number of areas, including housing, education and healthcare. But many consider this to be the latest in a line of promises which, that without positive action, will do little to continue the forward momentum being experienced across the sector.
Futurebuild’s whole ethos is to bring together opinion-shapers, decisionmakers and product innovators to debate the biggest issues, and central to this is the future of offsite. With this in mind, one of the key questions posed to the think tank was what needs to be done to make sure offsite techniques are adopted more widely by clients and contractors?
Losing the Disguise
There’s been a real shift in recent years from “disguising” volumetric modules to “celebrating” the expression of the module, according to Philip Breese, Senior Partner at Weston Williamson + Partners. This has shaken off past beliefs that offsite construction was a “dirty secret” as Brian Alborough, Director at Geraghty Taylor put it. But this has only been possible with the buy-in from a growing number of architects, who are without doubt some of the most influential decision makers when it comes to any project.
In fact, Paul Tierney, Managing Director at Extraspace, said he has seen: “a seismic shift, particularly in the last 12 to 18 months, where we’re being asked by architects to come in to talk to them,” rather than going out and knocking on doors to try to
convince them to sign up to offsite projects. He added that his company is seeing more “intelligent” thinking from architects and clients who are designing from the outset with offsite construction techniques in mind.
While Darren Richards, think tank Chair and Cogent Consulting Managing Director noted, it’s now viewed as “aspirational” to be seen to be talking about offsite, the question remains as to how the recent increase in architects adopting and championing the idea of offsite can be translated more widely across the profession.
A lot of the discussion focused around the role of RIBA and how it can further engage its members. Past RIBA president, Jane Duncan, previously stated in the Design for Manufacture and Assembly overlay to the Plan of
Facilitator: Darren Richards, Managing Director - Cogent Consulting
Ben Drake, Associate - Peter Dann Consulting Engineers
Brian Alborough, Director - Geraghty Taylor Architects
Brian Maunder, Sales Director - Totally Modular
Chris Holleron, Group Product Manager: Construction - Hadley Group
Jason Powell, Head of Offsite Manufacturing - Accord Group/Local Homes
Jeff Maxted, Director of Technical Consultancy - BLP Insurance
Martin Hurn, Managing Director - Futurebuild
Nick Milestone, Associate Director - William Hare Group
Paul Tierney, Managing Director - Extraspace
Philip Breese, Senior Partner - Weston Williamson + Partners
Trevor Crawford, Business Development - Futurebuild
Work, that bodies such as Buildoffsite have been part of: “driving initiatives nudging us towards the next major transformation in how we construct buildings.” But added that: “the tipping point, where we fundamentally change the culture around how we design for construction, has still to be reached.”
Despite this declaration of intent by RIBA, Darren Richards believes the organisation is not sufficiently engaged at a strategic level and that: “the offsite sector needs to bring them to the top table because they’re still massively influential in the architectural arena and also on procurement. We need to ensure that the architects of the future are trained to embrace offsite technology and that it becomes core to good building design and delivery.”
Although they’re a key link in the chain, it isn’t just architects who are vital to progressing the growth of offsite. Nick Milestone, Associate Director at the William Hare Group, told said he’s been knocking on the doors of architects for 10 years, but then you hit the problem of the principal contractor who didn’t understand the offsite cost model and say they could complete the project using traditional methods for less money.
He said with more architects and developers getting on board with offsite techniques, there’s been another “huge shift” among this group and his company is now being called in more because there’s finally some recognition that: “we’ve not only got a skills shortage and a lack of knowledge, we don’t know what’s
going to happen post March 2019.” If Brexit means we lose access to the number of skilled overseas workers we need for traditional construction, then we have to go further towards offsite and there’s a lot of political movement to stimulate parts of the UK with increased manufacturing.
Winning over contractors is clearly a key part of the challenge that lies ahead, and the idea of greater integration and collaboration from the outset is one which offers a solution to the problem. Jason Powell, Head of Offsite Manufacturing at the Accord Group and Local Homes, said his organisation hit the same issue with contractors on external projects. They didn’t understand the cost model and claimed they could complete projects more cheaply using traditional methods.
Accord Group’s approach was to bring everyone around the table and build a partnership with like-minded contractors who want to move in the same direction. He added: “you have to be integrated as a team, internally or externally, you’ve got to work together, and if you can get everyone round the table from the very beginning it is a much simpler process and everyone has a fair say.”
If we’re seeing this behavioural shift in both architects and principal contractors towards offsite construction, who is responsible for making sure the uptake continues on this upward trajectory? Does the government’s Construction Sector Deal go far enough in championing offsite? This is an issue which clearly divides opinion and one where personal preference plays a key part.
Jeff Maxted, Director of Technical Consultancy at BLP Insurance, believes the government has a big part to play in promoting offsite and they need to deliver: “a substantial, sustainable pipeline to encourage people to produce.” He said that: “without that we will tick along but we won’t see the growth we need.” This idea of supporting a pipeline, over adopting the approach of subsidies was one which received widespread support from the panel.
Brian Maunder from Totally Modular says the local authorities and registered providers he’s engaged with are “frustrated” with central government, despite the fact they’ve done: “more in the last 18 months than they’ve ever done.” He said the delivery programme is changing and there are some local authorities looking for real partnership, some of which will be established through official joint ventures and some unofficial.
But some believe local authorities themselves have more of a role to play in the smooth implementation of offsite. The challenges presented by procurement are a big factor here. Paul Tierney said when it comes to residential projects, traditional procurement methods just don’t work. He believes delivery teams understand offsite, but procurement teams “can’t get their heads around it.”
Brian Maunder revealed he’d refused a local authority tender request on one project, as there’s no benefit to being squeezed to the point of not being able to make any money when you have significant manufacturing facility overheads to recover.
Brian Alborough added that commercial businesses are also now key influencers in this area. He said we need to recognise that these firms are disruptors, in the same way offsite is, and there needs to be a collective effort, particularly in the Build to Rent sector to make sure nobody goes down the traditional route, as it no longer makes sense.
Despite the fact that the overwhelming sense around offsite and its future is positive, there is still unquestionably a delay to wider adoption. One word which kept being repeated during
the discussions was confidence, and confidence across a number of areas. Chris Holleron, Group Product Manager for Construction at the Hadley Group, believes there’s still a lack of confidence around the size of many offsite manufacturing companies to be able to reliably deliver on a significant scale. He said a lot of people have approached many within the offsite sector with plans to build homes, but clients: “haven’t got the confidence in who they are and what they can produce.”
Darren Richards said this often boils down to financial stability, a sentiment echoed by Brian Maunder. He highlighted the fact that offsite construction is competing with multi-billion pound organisations and despite being “minnows, we’re now playing with the big boys.” It’s all about transitioning from niche to the mainstream, which requires confidence in mortgageability and balance sheets, alongside credibility.
Philip Breese believes that, even though big steps have been made in recent years, there’s still a lot of work to do when it comes to confidence in products and the longevity they offer. Research carried out by Futurebuild ahead of this year’s event showed there’s still a great deal of confusion around offsite homes, with a fifth of consumers surveyed believing it is of poor quality. It’s a fact that people want to know that the homes they’re buying or renting are durable and can stand the test of time with minimal maintenance. The people involved in building those properties need the same assurances.
This is where the idea of certification can play a key role in providing reassurance to lenders and investors. A simple internet search shows that at present there’s a variety of accreditations companies can apply for and it’s a confusing picture.
Jeff Maxted says this is impacting confidence across the board and he’s been working with a group chaired by Mark Farmer on behalf of the Housing Minister to come up with a single accreditation scheme, based on the Build Offsite Property Assurance Scheme (BOPAS), which major warranty providers would sign up to. The details of this are expected to be released later this year.
Better education about the benefits of offsite manufacture was identified as a key stumbling block to progress. Getting architects on board with offsite is one part of the puzzle, but the idea of getting everyone involved from the earliest stages of planning a project was highlighted by Ben Drake, Associate at Peter Dann. He said that as a structural engineer there’s a real need to consider offsite from the beginning to get the starting point right. It is inefficient to implement offsite elements retrospectively and being brought in at a later point often creates unnecessary hurdles. But crucially it’s also important to recognise that not: “every part of every project is suitable for offsite.”
This is something which Brian Alborough agreed with, and said certain types of offsite are going work with some schemes but not with others. He said for example there are instances where companies or designers might try to force cross laminated timber (CLT) because it’s what they know and understand, when in fact steel frame or volumetric might be a better solution. He warned that it’s only going to take: “a couple of schemes to fail, for the entire industry to be discredited.” It is key to recognise the huge reputational risk that’s being taken and make sure the right systems are being used for the right projects.
The final question surrounded confidence in the offsite supply-chain when it comes to future market share growth and whether the current upwards trajectory can be maintained. A number of people expressed the need to communicate outwardly that their businesses are in it for the long-term. In order to continue to grow there needs to be a belief that businesses will survive no matter what bumps in the road they encounter. “We’re more confident than we’ve ever been,” was the resounding message from Paul Tierney and this sentiment was shared by a number of people around the table. But this confidence is driven by a level of support from lenders who share the optimism in
his business and are happy to work collaboratively in order to progress.
Nick Milestone said the William Hare Group wants to diversify its risk portfolio and be market opportunistic, engaging with the right materials and players. He said their approach is to spread the net far, which is possible because the group is backed with brand equity and a balance sheet.
This idea of having tangible results to back up a business was repeated a number of times – people want proof of success in order to be able
to buy into offsite in the future. This is where Futurebuild comes in. The physical Offsite Hub is much more than an opportunity for people within the industry to come together and share ideas and innovation, it offers a platform to put offsite on the wider agenda and drive cross sector collaboration. It answers the questions of how to further engage architects, contractors, local authorities, housing associations and developers whilst allowing visitors to immerse themselves in the very best the offsite sector has to offer.
To find out more about exhibiting in the Offsite Hub at Futurebuild visit: www.futurebuild.co.uk
At Futurebuild 2019, opinion-shapers, decision-makers and product innovators will join together under a common purpose to explore the latest technologies and approaches, and debate the biggest issues facing the built environment – now and in the future – both in the UK and overseas.
This ethos will be brought to life through six Futurebuild Hubs. Providing dedicated platforms that unite sector-specific experts and innovators with leading brands and organisations, the Hubs are the place to showcase innovation and launch and promote products with highly engaged audiences. Home to focused education, research and inspiration, the Hubs enable visitors to prepare for tomorrow by taking action today.
The Futurebuild Hubs surround the central ecobuild conference, which will sit at the heart of the event. This ideas arena will challenge industry to ‘think the unthinkable’ with a programme of inspiring speakers and game-changing discussions – all focused on examining and sparking action on the most important, far-reaching societal and environmental issues.
Over 26,500 decision-makers will descend on London’s ExCeL, London, from 05-07 March 2019 to learn about the latest products and collaborate around delivering improved results. Learn more at: www.futurebuild.co.uk
Be part of the future - contact: Trevor Crawford, Business Development E: trevor.crawford@futurebuild.co.uk M: 0774 001 7035
The development of skills in offsite construction could revolutionise the construction industry and help provide a solution to the UK’s housing shortage. Ben Lever, CITB Future Skills Manager outlines how.
We produced a report last year titled ‘Faster, Smarter, More Efficient: Building Skills for Offsite Construction.’ The report, with its foreword by industry expert Mark Farmer, encouraged everyone in the sector to recognise and define the growing changes to skills needs through collaboration between industry, educators, training providers and government.
New innovations, a sharper focus on productivity and targeted government policies, are changing contractor needs. Activity looks set to become increasingly industrialised and digitally-led, which is leading to a demand for people with competencies in manufacturing, digital processes and multi-trade skills. Our research has led us to work closely with those in manufacturing– particularly those already working with construction companies – to provide effective training as the boundaries between traditional building sectors become blurred.
Policies announced in the recent Construction Sector Deal may drive uptake of digital and manufactureled process, with measures such as a presumption in favour of offsite for new public projects.
Our offsite report highlighted that 42% of construction employers expected to use offsite methods in five years’ time – a significant increase on the 10% of industry output it currently makes up. In the last year we have seen the launch of several modularonly housing association contractor frameworks, along with offsite having been placed firmly at the centre of several infrastructure projects, including Heathrow’s extension plans.
Our report detailed the six key skills and functions needed for successful offsite construction, including digital design, estimating/commercial, offsite manufacturing, logistics, site management and integration and onsite placement and assembly. It’s clear these skills will become increasingly important as technology advances.
We’ve used the ‘personas’ and associated skill-sets to guide the development of new offsite-related standards, and influence the content of apprenticeship standards so that the future workforce has the skills it needs. We have followed this up with a new fund to support trainers to deliver offsite construction content –recognising that the training network often lacks the skills and resources to teach this relatively new area, creating barriers to provision. The improving skills for offsite construction fund will invest £500,000 into projects that can easily be scaled up across Great Britain.
CITB has a clear role to play in enabling the wider changes in industry through targeted skills investment based on robust evidence. Our upcoming report into digital skills will help to identify what interventions are needed to enable the adoption of new technology that underpins processes like offsite. CITB has also targeted funding at innovative training solutions using virtual and augmented reality, as a direct result of our research which highlighted the value of this tech for improved learning and the wider role it will play in a modernised industry.
Our research and steps taken are the start of a response to a changing sector. We’ve been encouraged with the collaborative effort across industry.
We hope, through our research, influencing and funding streams, to develop projects that will deliver the skills and training needed for the future of construction.
CITB want to hear from those engaged in offsite manufacturing, production or onsite assembly but also with expertise outside of construction, and in developing training materials. After extensive consultation with industry we have set up a £500,000 fund to help provide quality and standardised training for Offsite Upskilling.
The desired outcome for industry is to achieve greater quality and consistency in the delivery of offsite construction training. This will apply across relevant apprenticeships, vocational qualifications and short courses. CITB is now calling on organisations who are best placed to deliver the stated outcomes of funding as detailed above.
Applications for the funding to improving skills for offsite construction is open for submissions.
If you have any questions in relation to this, please contact the funding team direct using the contacts below - funding@citb.co.uk or www.citb. co.uk/offsiteskills
For more information visit: www.citb.co.uk
Images:
01. Ben Lever, CITB Future Skills Manager
With the Gebrik cladding system, you are assured of a simpler, faster brick façade that performs precisely as it should.
Tried, tested and simple to install, our solutions provide you with the freedom to create strikingly versatile buildings.
To find out more, visit our website www.aquariancladding.co.uk
0044 (0)808 223 9080
info@aquariancladding.co.uk
@aquarian_cladd
Mark Farmer said, ‘Modernise or Die’ and whilst this message has generally been accepted by the construction and infrastructure industry, it may not be clear what ‘modernisation’ actually means. Mark Ireland, Chief Engineer, Construction at the Manufacturing Technology Centre (MTC) explains more.
One parallel which can be drawn is to the automotive industry. In the 1950s 40 manufacturers in the UK produced approximately 785,000 vehicles per year. By the 1970s four main companies dominated the market and vehicle manufacturing achieved – an unbeaten record of – 2,098,000 vehicles in 1972. A remarkable increase in a relatively short period of time. One of the drivers for this increase was a move away from skilled labour delivering bespoke manufactured products, made in sheds, to huge production facilities with investment in design, inspection, logistics and manufacturing technologies. The smaller companies
who couldn’t make the investment, to compete, became low volume niche vehicle manufacturers, went bust or were absorbed into the larger corporations.
In my view, the UK construction and infrastructure industry is in the same position as the automotive industry in the 1950s and will inevitably go through the same change, provided global exports don’t destroy the industry first (as happened to the automotive industry in the 1980s and 1990s). So, is a manufacturing approach the secret to “modernisation”?
One of the tools that we know is proven in other sectors is good, complete, engineering design before a project is committed. This needs to include design for manufacture, assembly, maintenance, disassembly etc., often called Design for X or DFX. There are a number of quantitative and qualitative tools that can be used but fundamentally an assembly needs to be fully defined such that the quality of a product or building should not be dependent on the person making it. There are also a few tricks that can be applied from other sectors such as; modularising products and subassemble as much as you can and test
it before you build it into the finished product. Components such as Bryden Wood’s ceiling cassette (see Image 1) show that this is achievable today but also that there is still a long way to go to change the way construction thinks about components. Do you really want all of the wiring in your house bespoke made or a pre-made and tested wiring loom complete with tested and validated connectors? The future needs collaboration with suppliers and product integrators to provide sub-assemblies which are designed with DFX in mind and not just what is on the shelf.
In a manufacturing approach it is known that Just-In-Time, carefully packaged, fully sequenced part delivery minimises business overheads whilst increasing product quality with less risk of parts getting damaged during storage. In the automotive industry, £3.50 glossy plastic trim pieces are handled with gloves and stored in special packaging whilst in construction we have to do our best not to damage products which are delivered to site at the wrong time. Currently around 20% of plasterboard is damaged during transport, there is a tendency for skilled trades to work around this problem, masking
the scale of the issue but what is the impact of cost, defects and poor quality on projects later down the line? In a future world of construction parts will be delivered at the right quality at the right time for just in time assembly with custom made re-usable packaging.
Inspection doesn’t just mean measure what you have done it also includes measurement of the inputs and the process. In construction and infrastructure the general challenge is measuring ‘as built’ but by this point it is too late to do anything about it without accruing re-work costs. It is generally accepted in manufacturing that if you measure the input and the processing you know that the output is going to be of good quality. When parts are being made as subassemblies, functional testing can be completed before assembly into a building or system, supporting the improvement in quality and right first time.
One major difference to the more established manufacturing industries is the type of technology which is going to be needed in the future construction supply chain. While the industry
moves to off-site and ultimately define the direction in terms of materials and processes, investment in flexible equipment with minimum hard tooling is going to be vital. Hard tooling e.g. press tooling, offers low cost at high rate but until standardisation can be achieved this is going to be limited to commodity products.
One of the biggest areas of opportunity for construction is to use laser and water jet cutting. These proven process can be deployed on a large scale and are exceptionally accurate, allowing pieces to be ‘jig sawed’ together with sub mm accuracy. Standardised, self-locating and high tolerance connections will allow for components to be accurately assembled without the need for shimming and fitting. In conjunction with laser cutting, CNC folding and bending methodologies can be used to give metal components the form they need to become part of assemblies with minimum investment in dedicated tooling.
Robotics and automation has two main areas of opportunity: 2
Flexible conventional automation for offsite processing and assembly work
All of the equipment and understanding is proven and available off the shelf today but to make it work the DF approach is needed to design structures and systems which support automation, trying to automate a manual task rarely works but when integrated early into design work huge benefits can be realised. When integrated into re-configurable tooling
industry is starting to move towards self-driving equipment but the key to automation is starting become more mainstream through companies such as Trimble and, if integrated with equipment such as the JCB Hydradig large robotic equipment, is almost a reality today.
The final piece of the jigsaw puzzle is meeting the requirements of an ever more demanding customer. Currently construction and infrastructure projects don’t deliver what we need as users. Using housing as an example, why do we not have electric windows, central locking, integrated security systems, climate control, single point service integration for water, gas, electricity etc. Why do nearly all garages get used to store items other than cars? We should be able to play music as loud as we want without disturbing anyone but I don’t want to hear anyone else in the bathroom. Designers have yet to come up with an innovative product design that reflects how we really use our house. We have started to demand more from our mobile phones, white goods, cars, and product development is a key part of differentiation for suppliers but in housing, choice is driven by cost and location.
For more information visit: www.the-mtc.org 3 4
and fixturing systems automation can be rapidly built up, used on a project then reconfigured for the next project allowing the
Flexible mobile automation/semiautomated positioning and fixing
In a future world of construction there should be an aspiration to remove general use of cranes and slinging to sites with semi-automated handling and fitting of components. The
A manufacturing approach should be used to develop offsite, modularisation and sub-assembly for construction, but as we all know these approaches have been tried before and don’t necessarily come with a good reputation. The failures in the past were driven by a desire to achieve cheaper and faster but not better. By using better design, logistics, inspection and manufacturing technologies we can have Better, Faster and Cheaper!
Images:
01. Bryden Wood Ceiling cassette
02. Robotic and yellow goods handling of components
03. Robotics and automation will play a huge role in the future of construction. Courtesy Construction Innovation Centre Scotland (CSIC)
04. MTC Associate Director of Construction, Trudi Sully, and Willmott Dixon National Product Director, Tim Carey. Willmott Dixon recently became a member of the MTC.
The new TDBL nonut® self-threading screw from SFS, one of the world’s leading manufacturers of high performance fasteners, enables a secure connection of pre-drilled supporting steel structures without any nuts or washers.
Compared with the standard method of using nuts, bolts and washers, the precision-engineered TDBL nonut® fastener is a quicker, more efficient and more secure way of fixing together supporting steel structures of various thickness and hardness subject to static load. The installer only needs one component instead of three, and one hand tool. Installation is onehanded and requires access from just one side. European-manufactured to a high quality, the plated carbon steel, case hardened TDBL nonut® is available in eight variants according to length, diameter and clamping length with a hexagon head.
Andy Stolworthy, Director of Product and Market Development, at SFS
UK says: “The traditional method of fixing steel structures together by using bolts with nuts and washers represents an unnecessarily awkward and time-consuming way of doing things. We’ve worked to overcome this by developing the TDBL nonut®, a technically superior fastener in one piece rather than three. It’s a risk-free alternative that is guaranteed to make steel structure assembly faster, and the customers get the peace of mind of knowing that it’s a product from a global-market leader renowned for quality.”
Operating from its UK HQ in Leeds, the company is part of the Swiss-based SFS Group which has annual sales in excess of £1.1bn.
For more information visit: www.sfsintec.co.uk
Images:
01. The SFS TDBL nonut® fastener
Techno Metal Post (TMP) UK has recently joined the UK offsite housing market to offer their accredited foundation screw piles for all types of residential and commercial buildings. TMP Screw Piles are the ideal substructure and foundation solution for the offsite housing market.
Since 1993 TMP has been developing, designing, engineering and testing, helical screw piles to the highest standards ensuring they can support and withstand the heaviest loads and conditions possible. TMP Helical Screw Piles are formed of structural steel according to ASTM A500 grade C and by BSi to meet the EU CE EN9001 Regulations, which the company guarantees and certifies through its many accreditations, that installations will meet all current recognised building codes and standards.
The key USP of screw piles is the speed of installation – undertaken by remote controlled robots, each robot has an on-board calibrated computer that provides valuable confirmation
pile data and a hard copy print-out that confirms each pile’s status, depth and torque with the load capacity of each pile. Prior to installation there’s no need for any ground excavation –concrete is not required – and in many instances a levelled site is also not required. As soon as the CE screw piles are installed, by licensed Installers, the structural steel is ready to take the imposed loads and is immediately ready to build on.
They have a minimal environmental impact, and are the greenest and most sustainable foundation piling system in the world. They can also be used for short term temporary structures and subsequently can be removed when the structure is no longer required.
For more information visit: www.technometalpost.co.uk
Images: 01. EM1 - our mid-range model
The buzz around offsite construction is not slowing down and with the Government’s policy for the ‘presumption of offsite’ technology, demand is on the rise – as the offsite sector rises to the challenge, it is time for innovators to step forward and prepare to take centre stage at the 2019 Offsite Awards.
The list of previous winners reads like the ‘who’s who’ of building technology but it’s not only the major players and the iconic buildings that pick up an award – the Offsite Awards are renowned for unearthing those projects that may be small in stature but are awe inspiring in terms of innovation. But it’s not only projects that receive great acclaim – people are at the forefront of the Awards –architects, engineers, installers and clients are all recognised for their outstanding achievements.
Why Get involved?
Entries into the 2018 Offsite Construction Awards were phenomenal and the profile and coverage gained by all the finalists and winners has helped to propel the offsite sector to another level.
This event is the ideal opportunity for construction professionals to maximise industry exposure by demonstrating what separates them from their competitors. The winning organisations will be promoted to a national audience, giving entrants the opportunity to make their mark on this vibrant market.
So, if you are proud of your exceptional team, project development or product innovation there are just five questions to answer to grasp the opportunity to take centre stage at the 2019 Offsite Awards.
Entering the Offsite Construction Awards allows the most innovative achievements of the offsite industry to be held up alongside those considered the nation’s best. Being shortlisted for the Awards
will earn recognition within the offsite community and the wider construction industry – opening doors to securing new business development opportunities.
Returning for 2019, the Offsite Construction Awards promises to be the best year yet with a high calibre of industry leading companies and inspiring projects expected to enter the 22 different categories.
The Offsite Construction Awards are taking place on 5 March 2019, during Futurebuild, at the ExCeL, London where circa 500 delegates will gather to celebrate the best in the offsite industry. The drinks reception will provide the perfect opportunity to unwind and network before the awards ceremony.
Do you have a project that you think is worthy of winning an Offsite Construction Award? If yes, start your entry today! The closing date for Award Entries is the 11 January 2019 – enter any of the 22 categories free of charge by visiting: www.offsiteawards.co.uk
For sponsors, this prominent event provides one of the most effective platforms for engaging with the offsite industry, presenting the ideal opportunity to maximise exposure and penetrate this economically important market.
Categories still available to sponsor:
• BIM/Digital Construction Award
• Commercial Project of the Year
• Contractor of the Year
• Engineer of the Year
• Health & Safety Award
• Healthcare Project of the Year
• Best Use of Hybrid Technology
• Project/Construction Manager of the Year
The full 2019 events programme will be published in the next issue of Offsite Magazine but in the meantime if you are interested in learning more about offsite construction and the associated manufacturing processes then the following industry events may be of interest:
9-11 Oct 18 UK Construction Week NEC, Birmingham
www.ukconstructionweek.com
One of the UK’s largest built environment event, UK Construction Week (UKCW), is FREE to attend and consists of nine shows: Timber Expo, Build Show, Civils Expo, Plant & Machinery Live, Energy 2018, Building Tech Live, Surface & Materials Show and HVAC 2018 running from 9-11 October and Grand Designs Live which is open to the trade on 10-11 October.
10 Oct 18 Structural Timber Awards NCC, Birmingham
www.structuraltimberawards.co.uk
The Structural Timber Awards are back for 2018, celebrating it’s fourth year rewarding the very best in structural timber construction. Over 600 construction professionals will gather at the prestigious ceremony to celebrate the great, the good and the simply outstanding. Limited tickets available – book now to avoid disappointment!
30 Oct 18 Modular Matters
NEC, Birmingham
www.modularmatters.co.uk
New for 2018, the Modular Matters conference and exhibition will focus on the latest developments, innovations and investments in the volumetric modular offsite sector and aims to engage with industry pioneers from within the offsite supply-chain, leading designers, specifiers, engineers and ground-breaking clients. Limited tickets available – book now to avoid disappointment!
4 & 5 Dec 18 Spotlight on Offsite NEC, Birmingham www.spotlightonoffsite.co.uk
Spotlight on Offsite brings together distinguished speakers from a broad spectrum of pioneering organisations representing clients, construction professionals and suppliers. The combined conference and exhibition will showcase ground-breaking offsite construction solutions and focus on the latest developments, innovations and investments in the offsite sector across a range of vertical markets. Tickets are now available online!
12 Feb 19 Explore Offsite Housing London www.exploreoffsite.co.uk
HOUSING
Experts have hailed offsite construction as the only way to respond to the demand for new housing. Moving the construction of houses into factories enables the build to take place both efficiently and economically, making the national shortage of labour less of a concern. This two day conference brings together technology leaders to discuss the growing opportunities that the housing shortage presents for offsite construction solutions.
5-7 Mar 19 Futurebuild ExCeL, London
www.futurebuild.co.uk
A fresh format that’s nothing like an ordinary trade show bringing together the most innovative, exciting and inspiring brands, companies, speakers and experiences. The centrepiece will be the comprehensive conference programme curated by top industry figures surrounded by eight unique ‘futurebuild districts’ that will each explore a different aspect of the built environment. These will include building performance, infrastructure and energy.
5 Mar 19 Offsite Construction Awards
ExCeL, London
www.offsiteawards.co.uk
Celebrate the best in precision building design and delivery at the Offsite Construction Awards. The Awards will reward outstanding examples of prefabrication and factory-based methods, products, systems and disciplines that increasingly strive to develop a sustainable, streamlined and cost-effective way to deliver a better built environment. Entries close 11 January 2019.
MODULAR MATTERS conference and exhibition will create a platform to learn directly from leading sector designers, engineers, architects and manufacturers on how to apply innovative volumetric modular technology and also dispel the myths on design constraints.
The event provides a dynamic and interactive learning experience for all visitors and a fantastic business development opportunity for exhibitors and sponsors.
ONLY A FEW DELEGATE TICKETS REMAINING
Recognised
for innovative or non-traditional methods of construction. BLP helped to develop BOPAS which addresses the perceived risks associated with innovative construction and is recognised by the principal mortgage lenders as providing the necessary assurance underpinned by a warranty provision.