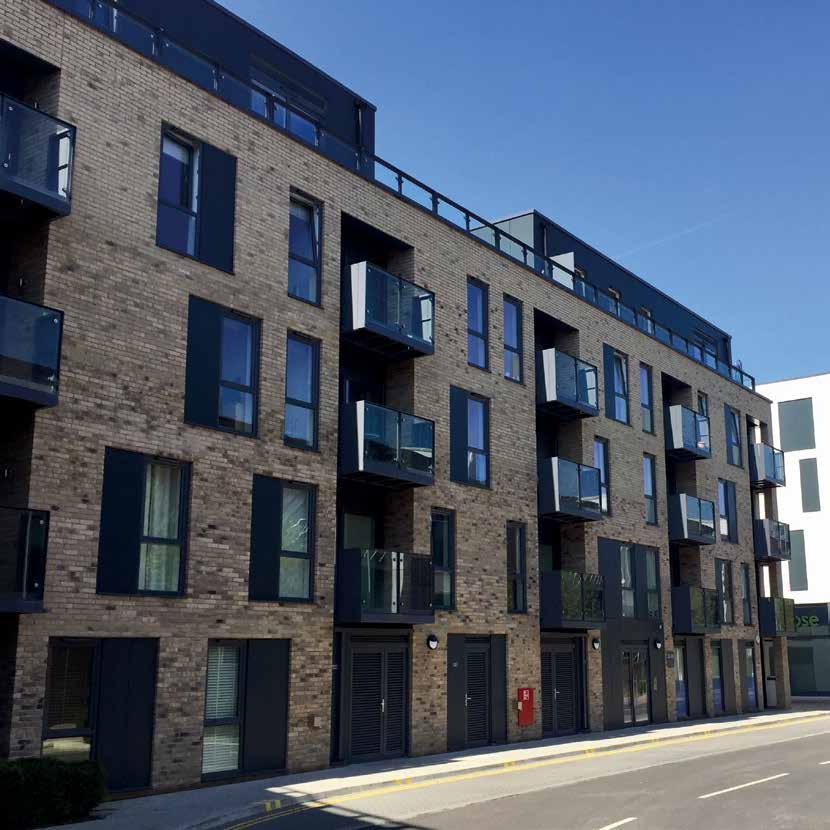
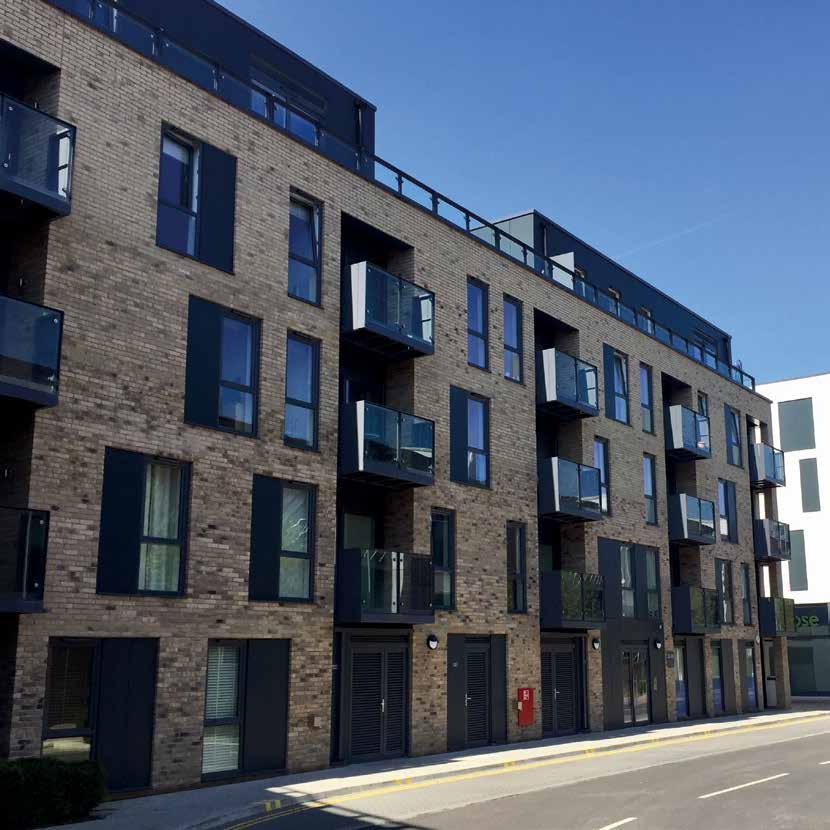
PUBLISHING
FRONT COVER
Fusion Steel Framing
PRINTED ON:
FSC Mix paper by Buxton Press
PUBLISHER:

Offsite Magazine is produced and published by Radar Communications: ©Radar Communications Ltd.

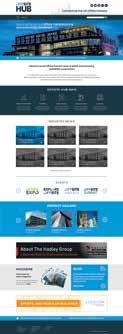
Radar Communications Ltd, 101 Longden Road, Shrewsbury, Shropshire, SY3 9PS
T: 01743 290001 www.radar-communications.co.uk
SUBSCRIBE TO RECEIVE OFFSITE:
This magazine is a bimonthly publication and the annual subscription fee for UK postage is £29.70 plus VAT for all six issues (£4.95 per copy). Visit www.offsitemagazine.co.uk
ADVERTISING ENQUIRIES PLEASE CONTACT:
Julie Williams // T: 01743 290001
E: julie.williams@offsitemagazine.co.uk
SEND US YOUR NEWS:
Gary Ramsay // T: 01743 290001
E: gary.ramsay@offsitemagazine.co.uk
BACK ISSUES VISIT: www.offsitemagazine.co.uk
FOR OFFSITE ENQUIRIES PLEASE CONTACT:
E: info@offsitemagazine.co.uk
DISCLAIMER: The content of Offsite Magazine does not necessarily reflect the views of the editor or publishers and are the views of its contributors and advertisers. The digital edition may include hyperlinks to third-party content, advertising, or websites, provided for the sake of convenience and interest. The publishers accept no legal responsibility for loss arising from information in this publication and do not endorse any advertising or products available from external sources. The publisher does not accept any liability of any loss arising from the late appearance or non-publication of any advertisement. Content including images and illustrations supplied by third parties are accepted in good faith and the publishers expect third parties to have obtained appropriate permissions, consents, licences or otherwise. The publisher does not accept any liability or any loss arising in the absence of these permissions for material used in both physical and digital editions. No part of this publication may be reproduced or stored in a retrieval system without the written consent of the publishers. All rights reserved.
KEEP IN TOUCH:
HOME IS WHERE THE HEAT IS
Welcome to the first edition of Offsite Magazine for 2023. For everyone picking this up at Futurebuild, hopefully this magazine will show you some of the ways that offsite manufacture is improving the built environment.
This issue we cover our usual spread of core materials with a slant towards housing and volumetric modular. After just over a year in operation Make UK Modular is making huge progress. We heard from Steve Cole on how they have been progressing so far. With some leading industry names on the membership list, its first key output of 2023 will be a major report into modular’s role in solving the housing labour market crisis. You will be able to read more about that in our next issue.
I also spent some time inside the Energy House 2.0 facility at Salford University. It grabbed national TV and newspaper headlines for its work on better understanding how houses work from a thermal and fabric perspective. Based on an innovative i-Stud structural closed panel timber frame, the e2Home is based in an amazing facility that will see it bombarded with flexed weather conditions, with an array of embedded sensors tracking heat and fabric performance, with results published via Salford University later this year.
Across the construction sector, the need to embed a clear, futureproofed environmental strategy in how your building operates is so important. With running costs and energy bills an ever-present concern, creating a building without one is risky. The e2Home concept house will hopefully prove with hard data what can achieved. Perhaps the new Department for Energy Security and Net Zero will be convinced to help more? Perhaps government can stop the revolving door of housing ministers and/or construction ministers?
However, looking to the future, it was interesting to hear that the BSi is on a mission to create a ‘British Standard for MMC’ and is working with DLUHC to create a universally recognised British Standard geared towards creating recommended technical standards for building homes using a range of offsite categories. Another addition to the vast array of accreditations, quality marks and industry seals of approval but an indicator of the seriousness that offsite manufacture is being taken after decades of being side-lined.
Thanks to all our contributors, advertisers and supporters for their help and support this issue. Enjoy!
Gary Ramsay Consultant Editor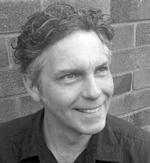
TheGramophoneWorks
YorkSt.JohnUniversityCreativeCentre

28.03.2023
THINK TANK, BIRMINGHAM
SHOWCASING THE BEST IN STRUCTURAL TIMBER
The Structural Timber Conference is open to architects, engineers, clients, contractors, local authorities, housebuilders and developers. The event will shine a spotlight on the 'best of the best' in structural timber, featuring stellar guest speakers from the Structural Timber Awards winners, highly commended and finalists.
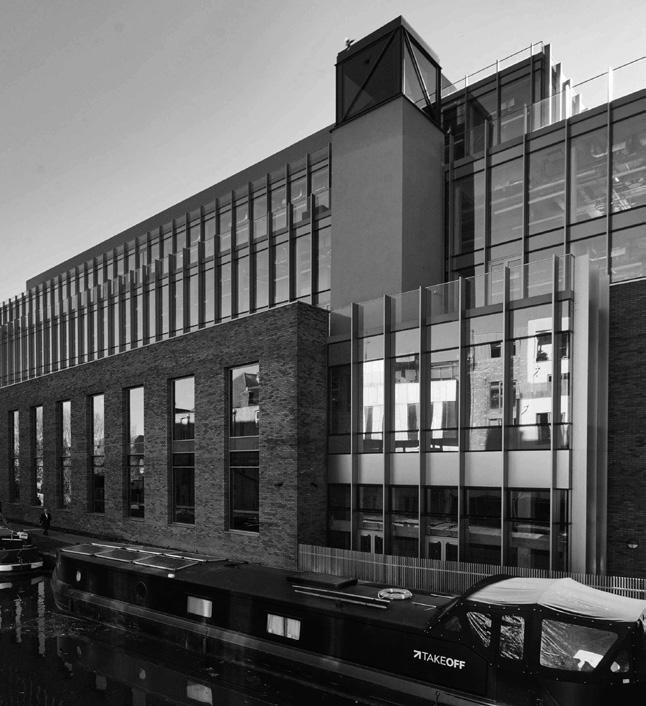
CrosfieldsSeniorSchoolBuilding

In partnership with:
STRUCTURAL TIMBER MAGAZINE
PROMOTIONAL OPPORTUNITIES AVAILABLE
For more information, please contact the team on 01743 290044
COVER STORIES
P06
CONTENTS
P24 | MILESTONES IN MODULAR
40 | Sustainability at Every Stage
Richard Hipkiss, MPBA’s Development Director, explains why we need to think of the ‘end’ at the initial design stages to enhance a project’s sustainability value chain.
42 | Bringing Co-ordination & Accuracy to Offsite
One company using Trimble’s co-ordinated and constructible Tekla software and leading the way in the offsite sector with its full RIBA workflow approach is Design4Structures.
By delivering exceptional Pre-Manufactured Value (PMV), Fusion Steel Framing systems help construction clients achieve exceptional programme and performance benefits. With an eye firmly on the future, Managing Director Mike Fairey outlines his vision for a better built environment.
Make UK Modular is helping promote the benefits of modular homebuilding and bring a fresh focus to the use of offsite technology. Head of Make UK Modular Steve Cole, spoke to us about progress so far and a busy year ahead.
46 | Material Combination
James Mead from Saint-Gobain Weber and Mike Doolan from LoCal Homes, share their experience of combining traditional building products with offsite manufacturing.
54 | Opportunities for LSF Expansion
The UK Procurement Bill will have many implications for the UK’s built environment and should play to the strengths of an offsitedelivered light frame steel approach.
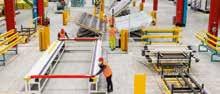
64 | Creating a New Construction Model
The way we build our homes and communities is changing. Richard Lankshear, Programme Director at the Future Homes Hub, outlines how the organisation is providing expertise on the major challenges surrounding carbon reduction and new homes.
As part of a wider project designed to accelerate progress towards low carbon and net zero housing, the pioneering eHome2 concept house built using offsite technology at Salford University will soon enter an intensive testing period to measure the different heating systems and fabric performance.
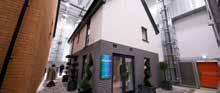
FEATURES
08 | Industry News
News and developments from across the UK offsite industry and wider construction arena including: Everton FC’s new stadium looks to offsite MEP, Algeco appoints a fresh UK MD, Crown Commercial Service awards huge offsite framework and Celtic Offsite teams up with one of the UK’s leading timber suppliers to reduce its carbon footprint and support the local economy.
30 | Precast Concrete Cladding & Fire Resilience
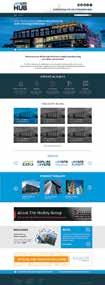
In recent years the construction industry has begun to re-evaluate building safety with the hope that we never again witness a tragedy on the same scale as Grenfell Tower. MPA UK Concrete explains how precast concrete can improve safety.
The fifth Modular Matters event recently took place at Birmingham’s NCC, with delegates benefiting from two days of discussion about the most efficient ways to transform the UK built environment.
68 | Modular Routes and Funding Options
Ecology Building Society is launching the UK’s first dedicated mortgage for modular construction homes – could this be a pivotal moment for offsite construction?
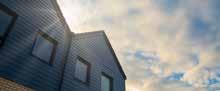
74 | Attainable Net Zero Goals
John Charles, General Manager at NG Bailey Offsite Manufacture, explains how the company is embedding a net zero mindset into factory-based design and delivery.
76 | Futurebuild 2023

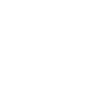
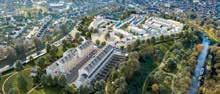
What is on offer at this year’s show? There will be plenty to interest offsite designers and manufacturers to help them create net zero buildings faster, more safely and more efficiently.
ONLINE PROJECT GALLERY INCLUSIONS
Our project gallery is the perfect opportunity to shout about your successes! The gallery functionality allows visitors to filter by sector and/or technology, then tailor the results according to their specific interest. With over 5,000 visitors every month, the Offsite Hub provides the ideal opportunity for you to reach your target audience.
Our offsite portfolio includes an abundance of profile-raising opportunities and this is just one way you can get involved!
For more information contact a member of our team on 01743 290001
Prices start from £200 for more information visit www.offsitehub.co.uk
COVER STORY FUSION STEEL FRAMING
BOOSTING OFFSITE EFFICIENCY ONSITE
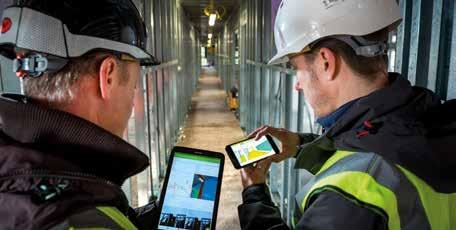
By delivering exceptional Pre-Manufactured Value (PMV), Fusion Steel Framing systems help construction clients achieve exceptional programme and performance benefits. With an eye firmly on the future, Managing Director Mike Fairey outlines his vision for a better built environment.
task virtually impossible on occasions. Using Design for Manufacture and Assembly (DfMA) principles, Fusion Steel Framing can take the detailed processes offsite into our advanced manufacturing facility. Our precisionengineered light steel framing systems offer high performance combined with numerous sustainability benefits, as well as creating a much safer working environment for operatives.
1 2
Since inception in 2000, we have delivered more light steel residential structures than any other European producer, working with some of the most prestigious contractors and developers in the UK construction industry. Our focus is now on improving the entire building process and streamlining supply chains through replacing a multitude of construction components with
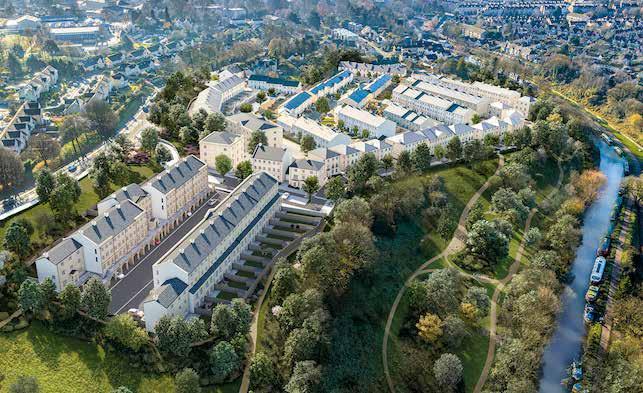
complete integrated systems. While the supply chain involves many elements, synergy lies in bringing the sum of the parts together both offsite and onsite to achieve construction objectives.
Engineering Excellence
Construction sites can be tough environments. Periods of extreme heat and torrential rain make a challenging
We support our construction clients to achieve exceptional programme benefits through a range of fully integrated panelised solutions backed by comprehensive services from design to installation. Through taking ownership of every building component, we have created an industry-leading solution in our through-wall FusionX™ system which, when combined with the Fusion Xterion™ cladding range, offers a complete through-wall integrated system with precise value-engineering and tried and tested performance. We also have the capability to provide structural kits for volumetric modules, bathroom pods and prefabricated utility cupboards (PUCs) – offering the opportunity for fully integrated structures. From engineering excellence and meticulous manufacturing to fire test certification and acoustic performance, we tailor our light steel framing systems precisely to meet the brief – offering speed of build, high quality and great value.
Collaborative Approach
Our ethos at Fusion has always been one of collaboration, this starts at project inception. As leaders in light steel framing solutions, we have put more than twenty years of knowledge and experience into creating our five-
step construction process. Synergy between our team and the people we work with is key to yielding the best results – focusing on the theory that the combined value and performance of several companies will be greater than the sum of the separate individual parts.
Our digitally enabled methodology focuses on safety, sustainability, efficiency, performance, cost and added value. By being involved collaboratively throughout the supply chain process – visibility and traceability improves dramatically, enabling us to identify opportunities for optimisation and improvement at the right time and avoid complications further down the line. When you build robust relationships throughout the
SYSTEMS OF CHOICE
FusionX™ – Tried, Tested and Approved
supply chain, utilising the benefits of each party’s knowledge, the potential value of the total project is increased. This is what we bring to the table through our five-step Fusion FocusTM process.
Having a team of highly skilled installers results in the efficiency and quality embedded in the offsite design and manufacturing processes being carried right through to the onsite arena. Our vision at Fusion is to be the offsite supply chain partner of choice, helping clients to achieve net zero carbon targets using our FusionXeroTM light steel frame superstructure solution. Quality, innovation and collaboration are at the heart of our company.
As Fusion Steel Framing continues to further its reputation as a market leader at the forefront of the offsite sector, the team is eager to engage with new clients and project teams who would like to find out more about our innovative systems and the overall benefits of light gauge steel framing. The team offers a wealth of knowledge in the steel sector, having advised numerous government and industry bodies, and can provide guidance from project conception through to completion.
For more information visit:
www.fusionsteelframing.co.uk
FusionX™ is a fully tested non-combustible integrated walling solution developed in response to Building Regulation changes. Approved by the NHBC, registered under NHBC Accepts, FusionX™ also holds LABC Warranty and is BOPAS accredited. This loadbearing external walling system is SCI and NHBC certified up to 10 storeys and can form part of a structure up to 14 storeys. FusionX™ is factory assembled for fast, cost-effective and quality-assured construction and has been tested thoroughly as an integrated system for thermal performance with fire resistance durations of 60, 90 and 120 minutes predictably achievable. Precision manufactured for rapid installation, FusionX™ can achieve U-values of 0.20W/m2k.
Xterion™ – Innovative Through-Wall Solution
Researched and developed specifically to enhance FusionX™ – Xterion™ is a high-performance, through-wall system that incorporates a range of cladding solutions. Creating a rapid dry building envelope, when combined with FusionX™ this warm frame solution delivers optimum performance values from 0.18W/m2K to Passivhaus standards – depending on the brief and specification. This complete through-wall system is manufactured with a standard build-up of insulation between the studs and a 100mm mineral wool slab outside the frame and is factory-fitted with noncombustible external boarding and is completed onsite with a range of lightweight render, brick and contemporary cladding finishes.
TraX™ – Infill Walling System
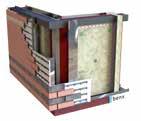
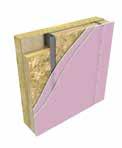
Non-loadbearing infill walling system developed for concrete or steel mainframes. Suitable for multi-storey construction across a range of building types, TraX™ is an economic and efficient method of providing facade walls. With layouts engineered to support windows and openings together with additional studs around for lateral tie back for brick channels and brackets for facades. The elements of the primary structural frame consist of a bottom track attached to the floor and a head track fixed to the underside of the floor above, allowing for building deflection.

CCS Announce New Agreement
Crown Commercial Service (CCS) recently awarded a new agreement for offsite construction, aiming to support the public sector to innovate, drive efficiency and continue to work towards their net zero carbon targets.
The Offsite Construction Solutions (RM6184) agreement reflects continuous offsite innovations and will broaden the premanufactured building solution provision currently available to public sector buyers through CCS agreements. It will have an increased scope to include more MMC categories, specifically 2D panelised structural systems and panelised external building retrofits, as specified within the new MMC Definition Framework.
The agreement will continue to align with the policies outlined in the Construction Playbook on offsite construction adoption. It replaces the Modular Buildings Agreement which closes on 1 April 2023. It has been designed to assist all public sector customers, with a specific focus on the health, housing, education, justice and defence sectors.
In a bid to help the public sector to continue to meet their carbon net zero targets, a specific lot (Thermal Efficiency Upgrades) has been introduced to address the increasing demand to retrofit existing estate portfolios with thermally efficient external systems. The new agreement aims to build on the progress made on making it easier for small and medium-
Launched in January 2023, The Offsite Guide (TOG) is a new B2B marketplace in the UK and Europe for businesses to explore options for using offsite methods and interact with specialist manufacturers.
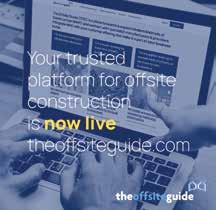
As a marketplace TOG facilitates engagement between key market participants and drives awareness of the many benefits of MMC including more efficient production, economies of scale and repeatability. In doing so it provides a central point of reference for product variety, availability, and pricing specification. Crucially, it provides a platform for direct communication between a wide range of providers and their potential customers in this fragmented market.
Ingrid Orbie, TOG Director said: “At The Offsite Guide we attract and facilitate early interaction with customers, allowing manufacturers of commercial and domestic modular buildings and offsite solutions to
sized enterprises to become suppliers. It includes 29 suppliers, 18 (62%) of which are SMEs. The agreement will run for four years with the possibility of a three-year extension and there is no maximum duration for call off contracts. It includes:
• A simple six lot structure, encompassing an increased range of premanufactured building turnkey solutions within a single, consolidated agreement
• Promotes the standardisation of building design across large portfolios of government infrastructure, therefore enabling greater efficiencies of time and cost savings through the project lifecycle, saving the taxpayer money
• The new agreement aims to make it easier for clients to contract with SME organisations, with 62% of suppliers being classed as an SME
• Public sector contracting terms and conditions create an easier, more flexible route to market, tailorable to customers’ specific operational needs
• An evaluated pool of suppliers allowing customers to drive cost reductions and increase value for money through healthy competition.
John Welch, Deputy Director – Construction, Crown Commercial Service said: “This new framework will support the public sector in the design, delivery and commissioning of a whole range of offsite construction projects in the coming years, including social housing, new schools and hospital extensions. These projects, and the many more which will come, have the potential to improve services and the lives of millions of people. It is yet another example of how CCS is helping the public sector to support the government’s construction strategy and further supports the recently published refresh of the Construction Playbook with its MMC guidance note.”
To find out more about Offsite Construction Solutions (RM6184) visit www.crowncommercial.gov.uk or contact the CCS Service Desk at: info@crowncommercial.gov.uk
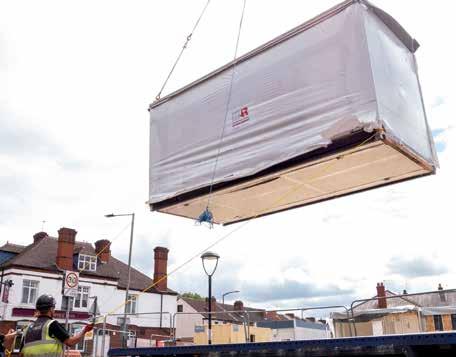
showcase a range of their products and help educate potential customers. We provide a trusted platform not only for showcasing offsite construction, but also to facilitate initial dialogue and ongoing interaction between customers, manufacturers and MMC suppliers.”
Whether listing as a TOG Partner on the marketplace or as Advertiser in the Directory, TOG offers an opportunity to raise brand awareness, increase a company’s visibility and gain access to new customers. Through TOG’s marketing and launch promotion campaigns TOG is striving to elevate MMC sales channels and engage with the market in a more efficient and effective way. The TOG marketplace facilitates that search for proven solutions and gives examples and case studies that show ways that organisations and developers can break tradition and drive efficiency using MMC.
Source: www.theoffsiteguide.com
wedi Sanwell® shower wall module
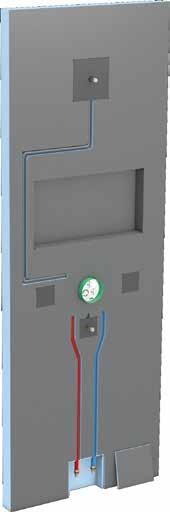
with factory-integrated, sealed Hansgrohe iBox & waterpipes
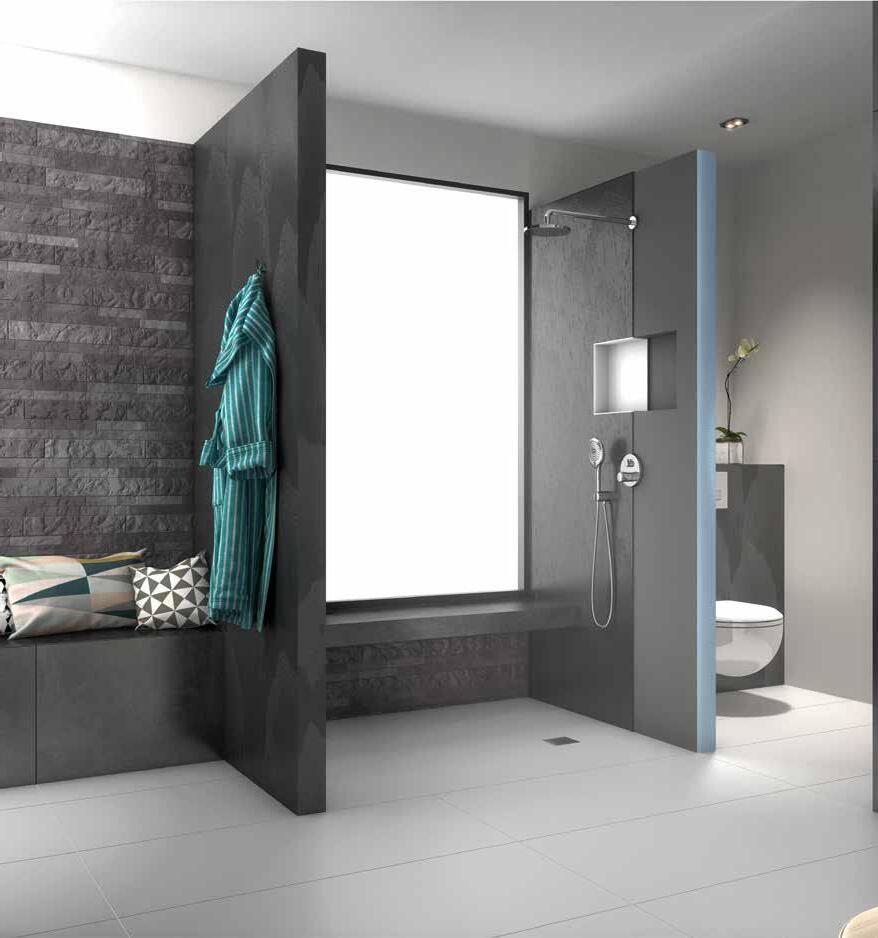
√ to suit over 200 thermostatic mixer designs

√ use as a fixed wall or as a free-standing partition
√ directly tileable, 100% waterproof and adjustable on site
√ in 900mm or 1200mm width and 80mm or 100mm thickness
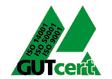
√ individualisation options to meet customer specific needs (i.e. niche)
√ reinforcement plates for shower head attachments at selectable heights
M-AR Teams up with Centrepoint for New Homes
Specialist offsite contractor, M-AR is nearing completion on an ambitious newbuild project in partnership with the UK’s leading youth homelessness charity, Centrepoint. The project’s goal was to create single occupancy homes for young people experiencing homelessness in London – a first for the charity which up until now has relied on refurbished accommodation.
Centrepoint provides housing and support for almost 13,000 homeless young people every year in London, Manchester, Yorkshire and the North East. Its bold new Independent Living Programme aims to pair over 300 young people with a job and a home across London and Manchester within the next three years and this new development, which will be known as Reuben House, in Peckham is the first step.
M-AR manufactured 33 modular homes in its factory to create the new two storey apartment building. The design features repeatable modular units that can easily be delivered on multiple sites – which means Centrepoint and M-AR will be able to replicate this model on future projects as the Independent Living Programme rolls out to other locations over the next five years.
Each self-contained 21sq m home has its own private access, a small functional kitchen, dining area and a
bathroom as well as space to sleep and relax, making the units a comfortable home for young people to live independently. The homes were delivered to site fully fitted with the kitchen and bathroom, with all electrics and plumbing installed as well as being fully decorated throughout for greater programme efficiency.
Another key aspect of the project was to ensure each home was as energy efficient as possible to keep future running costs low for residents, which has become even more important as the cost of living crisis continues. The homes have energy-saving features including photovoltaic (PV) solar panels and air source heat pumps to reduce energy consumption and shield residents from spiralling costs.
As well as offering Centrepoint cost predictability from the outset, the use of offsite building techniques provided a solution to the specific constraints of this project including its location on an extremely tight site. By moving much of the first and second fix works offsite and into M-AR’s factory, it freed up space on site while also minimising disruption to the local community during the build.
The new homes had to meet the requirements of the London Plan, the new spatial development strategy for Greater London, as well as the latest
building regulations governing energy efficiency. The development also had to fit seamlessly into the local neighbourhood - the landscaping and exterior cladding works perfectly achieve this aim.
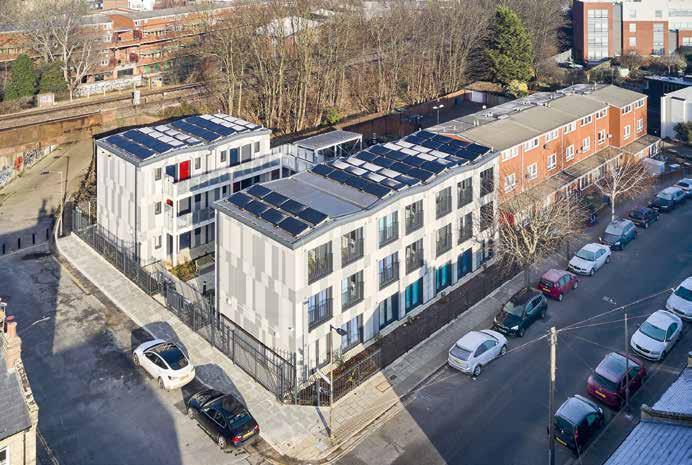
Ryan Geldard, Director at M-AR said: “It’s a privilege for us to be able to do our bit to help Centrepoint in its mission to end youth homelessness by delivering these new safe and secure independent living homes. We’ve worked closely with the whole team to make sure that the units are perfectly suited to the young people who will call them home and it’s great to see them starting to be occupied and know that our job is here is done. We’ve learnt a lot from this build and are looking forward to the next project with Centrepoint.”
Sally Orlopp, Director of Centrepoint’s Independent Living Programme, said: “It has been a real privilege to watch these units turn into homes over the last few months. M-AR and our other partners have been fantastic in helping us take this first step towards building 300 homes for those people under 25 ready to escape homeless but unable to afford skyrocketing rents. We can’t wait to hand over the keys to our new tenants who will now have the space and stability they need to stop worrying about the roof over their head and get on with achieving their ambitions.”
Source: www.m-ar.co.uk
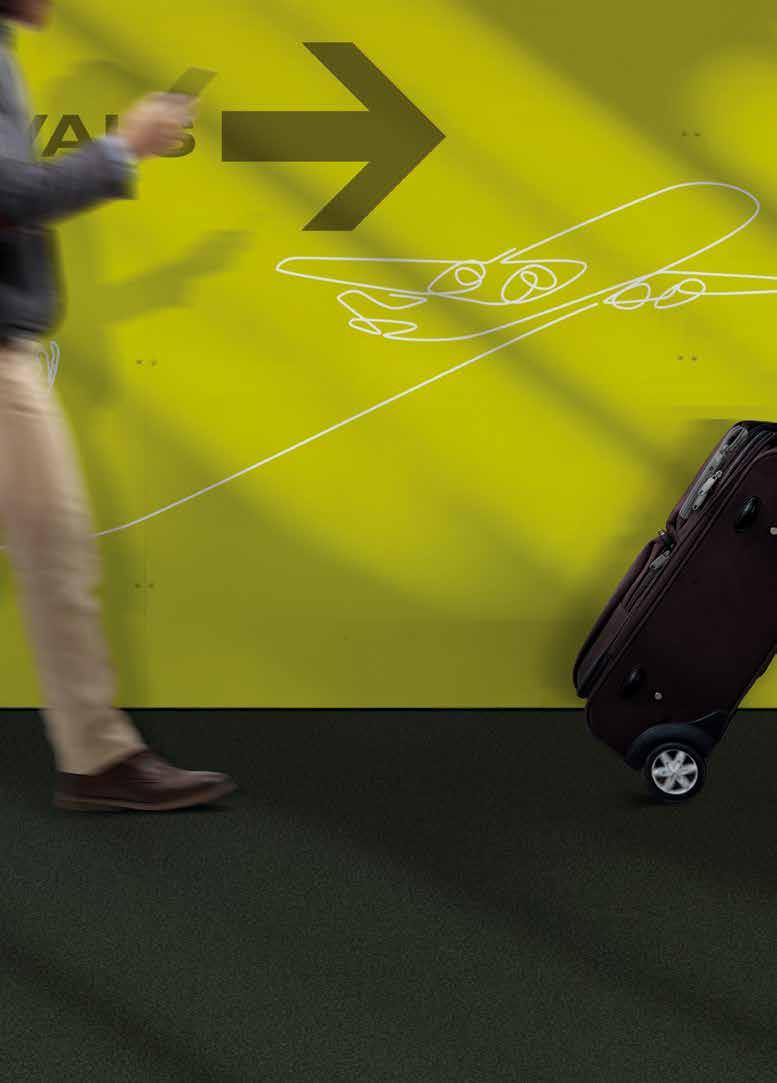
ilke Homes and Man GPM Start Work at Glenvale Park
Leading modular housing pioneer ilke Homes has started work to deliver 146 energy-efficient, affordable homes at the Glenvale Park development in Wellingborough, as part of Man GPM’s community housing focus.
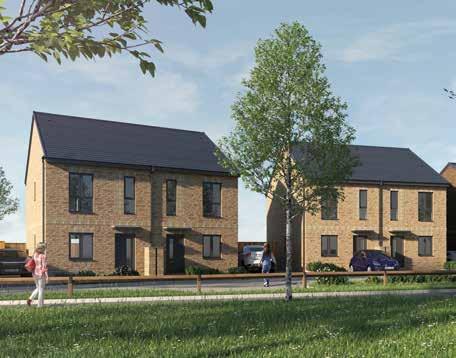
The announcement marks the second time ilke Homes and Man GPM have worked together to deliver an affordable-led scheme, having struck a £31million deal in December 2020 for a 226home affordable housing development in Grantham, Lincolnshire. The 7.8-acre site forms part of phase one at Glenvale Park, which once complete, will deliver a total of 3,000 homes, over 200 acres of parkland, a new local centre and two new schools.
The wider masterplan for Glenvale Park is expected to generate more than 3,000 jobs and £1.4billion in economic impact for the area – with £2 of social value generated for every £1 spent during construction. Having received approval from North Northamptonshire Council, ilke Homes has started work delivering a mix of multi-tenure single family houses, apartments and maisonettes, ranging in sizes from one to four bedrooms homes.
The homes – which are due for completion in 2024 – are being manufactured offsite at ilke Homes’ 25,000sq ft factory in North Yorkshire. With a likely EPC rating of A, the properties are in the top 5% nationally for energy efficiency, with the knock-on effect of saving consumers hundreds of pounds a year on energy bills. Thanks to most of the build stage taking place offsite, traffic disruption to the local community will be kept to a minimum.
Tom Heathcote, Executive Director of Development at ilke Homes, said: “This scheme is testament to the continued confidence our customers have in our product, and we’ve enjoyed working with local planning officials and other stakeholders throughout
Algeco UK Appoints New MD
Algeco has appointed Keith Dorling as UK Managing Director. The announcement comes as increased demand and recent acquisitions open up new opportunities for the UK business and its customers.
Keith takes overall responsibility for Algeco in the UK, a role that encompasses modular hire solutions and permanent offsite buildings. Algeco continues to grow its presence in the UK with the recent acquisition of Mobile Mini. This follows on from Carter Accommodation Ltd and Procomm Site Services Ltd being added to the Algeco portfolio in early 2021/2.
the planning process and into the construction phase. After the success of our first joint scheme in Lincolnshire, we’re delighted Man Group have shown the confidence in us to deliver a second sustainable urban development scheme together.”
Man Group’s Community Housing team seeks to achieve the dual objectives of providing both social and financial returns, addressing the housing crisis in the UK by building homes that are affordable to households. The UK has experienced a significant, long-term mismatch between supply and demand in the housing market, which has led to an affordability crisis impacting households earning the median income and below. The team deploys institutional capital to build new homes with the aim of generating positive returns for investors and delivering a demonstrable social impact.
Shamez Alibhai, Managing Director and Head of Community Housing at Man GPM, said: “The development at Wellingborough is an exciting
demonstration of how like-minded partners can deliver homes that address the housing challenges of families. ilke’s track record on housing delivery and its commitment to innovation fits naturally with our focus on social and environmental responsible investment.
Mark Best, Director of Midtown Capital Ltd, managing partner of Glenvale Park LLP also added: “As a leading provider of sustainable modular properties, we’re delighted to welcome ilke Homes and Man Group to Glenvale Park. With the range of properties and mix of tenures available, the new homes will be an exciting new offering to our growing community. With hundreds of families calling Glenvale Park home, there is already a strong sense of community spirit within the development. We can’t wait to see that grow further.”
Source: www.ilkehomes.co.uk
Keith joins Algeco with extensive senior leadership experience across construction, infrastructure and distribution: including successfully leading complex acquisitions and integrations across multiple sectors. This is an exciting time for Algeco and Keith will be supporting the team’s future success, and strengthening the business where it adds value to the customer proposition.
Keith explains: “I am delighted to have joined Algeco, an organisation that has solid foundations built on excellence, innovation and collaboration. The strong team of people and competitive positioning of the business means that I am confident we can continue to achieve great things on behalf of our customers.
We have a major role to play in delivering the Group’s sustainable strategy through our commitment to innovation and collaborative relationships. I look forward to working with all our stakeholders to make a lasting positive impact on the built environment.”
Mark Higson, Group Chief Executive Officer of Modulaire Group, added: “I am delighted Keith is joining us to lead the next phase of our growth in the UK. His focus on operational and commercial excellence along with his people-first approach, means that he is well-placed to lead the Algeco UK business and help to deliver our medium-term plan.”
Source: www.algeco.co.uk
Vinci Building Choose Pod Technology for Bristol
Offsite Solutions has been awarded its second student living contract at the University of the West of England’s Frenchay Campus in Bristol – a £1.7million project to manufacture 757 bathroom pods for VINCI Building.
Offsite Solutions has delivered 16 pod projects for VINCI Building to date which includes major student accommodation schemes for universities in Swansea, Cardiff, Coventry, and Liverpool. This latest project is for the University of the West of England (UWE Bristol) – and it is Offsite Solutions’ third for this university. This highly sustainable development is one of the largest Passivhaus projects in the UK. It is designed to provide a high level of comfort for students whilst using very little energy for heating and cooling, helping UWE Bristol and VINCI Building to meet their environmental aspirations.
As part of the certified low carbon strategy, the buildings aim to yield a reduction of around 50% in running costs and carbon emissions. To help achieve this, the cold water pipework in the bathroom pods will be insulated and the thermostatic shower and mixer taps for the hand basins are designed to run at lower temperatures. Both of these measures will reduce energy consumption for heating hot water.
Steve O’Leary, Regional Business Services Manager at VINCI Building, said: “I have managed the procurement and delivery of around 3,500 pods manufactured by Offsite Solutions in the past nine years. Their approach suits VINCI Building’s model of student accommodation very well. They have robust factory testing processes in place which mean the quality is better and more consistent. In my view, Offsite Solutions’ pods are the best in their sector and I would not hesitate to recommend.
“This solution reduces the numerous trades for bathroom construction to a single supplier, which results in a considerable time saving. Each bathroom typically takes around three weeks to construct traditionally, whereas with offsite manufacturing, we just have to position the pods, make connections, and hang the doors. This is incredibly fast.”
James Stephens, Managing Director of Offsite Solutions, said: “This is an exciting development


which will help to meet the rising demand for modern, high quality student living whilst demonstrating a clear commitment to addressing climate change issues. It is a ground-breaking project which will set new standards for the development of sustainable student accommodation.”
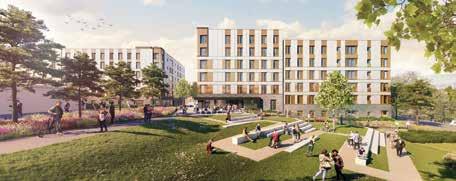
Due for completion for the 2023/24 student intake, this phase of the Frenchay Campus development will provide 900 bedspaces in three buildings spanning over 26,000sqm and in clusters of four, six and eight bedrooms and with ensuite or shared bathrooms. The shower pods have a robust and low maintenance GRP construction. Each will be fully finished in Offsite Solutions’ Somerset factory and will be fitted with a D-shaped wall-mounted hand basin, wall-hung toilet with dual flush, thermostatic shower, and sliding shower door.
Source: www.offsitesolutions.com

Britlift are a designer and manufacturer of lifting equipment, specialising in the lifting of modular homes, bathroom pods, commercial modules, containerised structures and pre-cast components.
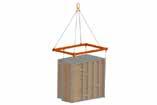
With a wealth of experience in the design and manufacture of lifting frames and lifting systems to the Offsite Construction sector, Britlift are the Offsite sector partner of choice.

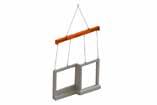

Celtic Offsite Teams up with Premier Forest Group

Caerphilly-based social enterprise, Celtic Offsite, has teamed up with one of the UK’s leading timber suppliers, Premier Forest Products, as part of their ambitious plan to develop a Welsh supply chain to reduce its carbon footprint and support the local economy.

Celtic Offsite, part of the United Welsh Group, manufactures low carbon homes by producing high quality, sustainable timber frame structures, complete with factory fitted insulation and windows, to build up to 250 low carbon homes a year.
Premier Forest Products was initially approached by Celtic Offsite to supply Oriented Strand Board (OSB) for sheathing for timber frame panels, plywood and chipboard. However, thanks to Premier’s growing product offering, they have recently started supplying roof trusses, engineered floor joists and Laminated Veneer Lumber (LVL) for structural beams, taking Celtic Offsite ever closer to their goal of using Welsh suppliers for more of their manufacturing work.
Neil Robins, Managing Director of Celtic Offsite said: “We are actively committed to making the areas in which we work better and more environmentally sound. We have been certified as a Climate Positive Business by Earthly, meaning we will remove more greenhouse emissions than we produce. One of the ways that we will do this is by working with local suppliers who have a similar mindset to our own. We have been so impressed by the service and quality of
Construction Starts on Europe’s Largest Modular Housing Facility
the products supplied by Premier Forest that we have consistently increased the range of items that we order from them.”
Co-founder and CEO of Premier Forest Products Terry Edgell said: “As an organisation, we firmly believe that the use of timber should be at the forefront of sustainable housing development. At the moment, wood in construction is the only commercially viable carbon capture and storage system so, simply by using more wood in construction, we can turn our built environment into a weapon against climate change. It is so inspiring to be working with an organisation in Wales that not only recognises the benefits of using timber but is actively working to build a sustainable supply chain, hopefully changing the way that homes are built.”
The new facility will bring together the latest robotics and TopHat’s proprietary technology to manufacture and distribute up to 4,000 homes per year. Construction will be commencing shortly at the new site and expected to be complete later this year. The factory will then be fitted out with its bespoke state-of the art robotic production line and will deliver its first units during 2024. The new facility will be built to BREEAM Excellent standard.
Key to the success of the new facility is the partnership TopHat has established with local colleges – branded the TopHat Academy – to support local people looking to train or retrain for roles in the new facility. A key part of the investment in skills will be supporting apprentices who will be approximately 5% of the employees on day 1 rising to 20% over three years.
Premier Forest Products is a vertically integrated timber operation engaged in the importation, sawmilling, processing, merchanting, and wholesale distribution of timber and timber products from its 12 sites in the UK. As part of its commitment to the local community, Celtic Offsite offers an on-site training suite to provide skills development and apprenticeships for green construction jobs. Celtic Offsite has also achieved PEFC certification for the chain of custody of forest-based products and was awarded Gold by the Structural Timber Association (STA) in their latest audit.
Photo: (L) Neil Robins, Celtic Offsite, and (R) Terry Edgell, Premier Forest Products
Source: www.unitedwelsh.com
Commenting on his visit to the site, Tom Pursglove MP for Corby & East Northamptonshire and Minister of State for Disabled People, Health and Work, said: “It is fantastic to see a major step forward in a scheme which will create a thousand new jobs here in Corby and play an important part in bringing making beautiful, low carbon 3D modular homes much more widely available. I am particularly pleased by the partnership with Bedford College and commitment to skills and training through the TopHat Academy. I look forward to seeing the factory again when all the robots have been installed.”
Tom Pursglove MP, the Conservative MP for Corby & East Northamptonshire, recently visited the construction site where 3D modular housebuilder TopHat will open Europe’s largest modular housing facility in 2024. The cutting-edge 650,000sq ft factory (equivalent to the size of 11 football pitches), will be capable of manufacturing a home every hour and will create 1,000 highly skilled new, green jobs across a wide range of roles.
TopHat is already at the forefront of a housebuilding revolution, applying robotics and lean manufacturing techniques to increase housing supply, improve quality, reduce costs and protect the environment. TopHat has pioneered an ultra-low carbon approach to building and operating homes, which significantly reduces household cost at a time when the cost-ofliving crisis threatens to plunge millions of families into fuel poverty.
Jordan Rosenhaus, CEO and Founder of TopHat, said: “The cost of living and housing crises, and climate emergency, require a bold approach that harnesses innovation to manufacture high-quality low carbon homes. TopHat’s new facility will ensure that Corby is at the heart of this revolution in house building, all the while creating 1,000 highly skilled, green jobs.”
James Atkinson, Development Director at GLP also commented: “Magna Park Corby is GLP’s third Magna Park site in the UK. With anchor tenants like TopHat, the site will make a huge contribution to the local community providing jobs, professional training and public realm for the benefit of all.”
Source: www.tophta.io
From interim housing for the homeless to on-the-spot overnight accommodation for keyworkers...
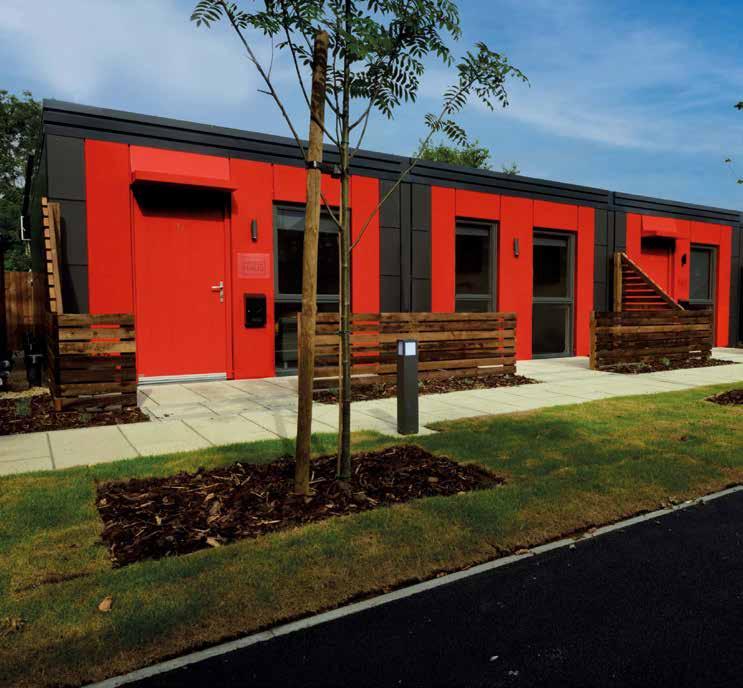
MODULHAUS™ provides award-winning, energy efficient and secure accommodation
...rigorously tested to ensure outstanding performance and quality




Offsite Transforms Worcester Nightclub into Student Accommodation
NHBC Accepts Welcomes Etopia and Istidama
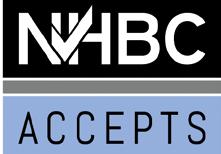
The former site of Images Nightclub in Worcester has been transformed into 83 student flats, with Intrastack supplying the steel-frame structure and the installation being undertaken by installer, Intastruct, on behalf of the main developer, Spec Projects.
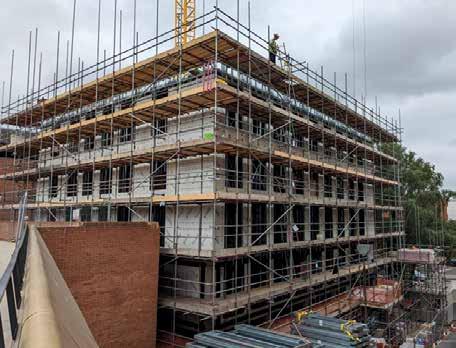
Intrastack, part of the Saint-Gobain Off-Site Solutions division, manufactured and delivered the light gauge steel frame (LGSF) system which saw three installers erect the seven-storey student accommodation block in just 10 weeks. A recent report considered there to be a lack of purpose-built accommodation (PBSA) in Worcester, with the existing stock made up mainly of conversions, houses in multiple occupation (HMO) and existing halls. With these low levels of vacant PBSA facilities in the city, the Images project aimed to provide modern rooms for the student population. With over 10,000 students at the University of Worcester, local plans to increase PBSA aim to reduce pressure on the on-street rental market to free up accommodation for families. Meanwhile, meeting the specific needs of students with purpose-built and managed schemes makes the city an attractive prospect to future learners.
The old Images nightclub site, demolished late in 2021, now houses the new seven-storey accommodation. The building comprises five selfsupporting storeys of light gauge steel frame panels atop a two-storey concrete base. The speed of construction was noticeable to onlookers, as the work took place over just 10 weeks – a reduction from the originally scheduled 12 weeks – and was noted as one of the reasons for the developers choosing LGSF for the project in the first place. The system also required fewer installers on-site at any given time, with most of the work completed by a team of three.
Rapid turnaround of design and materials, as well as the speed of installation and safety benefits, were also indicated as reasons for going with offsite steel frame manufacture. Capitalising on LGSF’s shorter construction times can provide developers with a quicker return on investment, as students are able to move in sooner than they would be able to with a traditional build.
The build site, which was first used over 150 years ago, is very restricted with limited space available for storage of the steel panels needed for the construction. Intrastack scheduled and delivered the panels to the site on a ‘just-in-time’ basis, working with the installer to ensure materials were on site as and when they were needed. This also reduced the waste on-site at any given time, with all system elements arriving cut to size.
Andy Higson, Business Director at Intrastack, said: “This year, PBSA in the UK has surpassed 30,000 rooms for the first time, showing that there’s demand for this type of housing. An offsite approach is essential to deliver on the scale required. LGSF systems can help developers to build accommodation faster while tackling on-site challenges such as safety risks and labour shortages. When you discover how much smoother it makes the process, it becomes a no-brainer.”
Paul Hazelwood, Contracts Manager at Intastruct, the system installers, added: “There’s no doubt that the steel frame system sped up the job, and allowed us to comfortably build a storey every two weeks. It’s a fast system, and incredibly robust.”
Source: www.intrastack.co.uk
NHBC, the UK’s leading warranty and insurance provider for newbuild homes has welcomed Etopia and Istidama to NHBC Accepts with its 4wall panel. NHBC Accepts enables quicker assessment of a home for warranty and reduces the risk to the builder of delays in their project. Any product or system with the NHBC Accepts logo will have been rigorously assessed to ensure it can meet NHBC’s robust standards, giving confidence to developers, investors, lenders and homeowners.
Etopia, a leading provider of offsite solutions, and Structural Insulated Panels (SIP) manufacturer Istidama are proud to announce that they have been awarded the NHBC Accepts accreditation for the 4wall patented hyper SIP. Etopia’s commitment is to innovate, design, manufacture, deliver and install a high-performance building system for residential and light commercial construction.
The flexibility of the system allows any housetype to be designed using ‘stock’ small or large panel formats. The system provides high structural strength, airtightness, and low U-values of 0.144 W/m²K creating incredibly energy efficient houses and buildings. Projects using the system will have a high pre-manufactured value (PMV) due to full elevations, internal walls, intermediate floors and roof trusses manufactured offsite; more than 55% can be achieved when combined with other PMV products.
Alexander Fink, Executive Director of Etopia, said: “Etopia is a pioneering force in the modern methods of construction industry, pushing the boundaries of what is possible and demonstrating the potential for offsite construction to revolutionise housebuilding and achieve net zero carbon emission. We look forward to working with NHBC on offering warranties on upcoming schemes. Our partnerships with leading financial institutions and global technology companies mean that Etopia offers the best sustainable product on the market.”
Nicholas Edwards, Managing Director of Istidama, added: “We are very pleased this year to add NHBC Accepts to our list of accreditations alongside Etopia's BOPAS, our KIWA BDA Agrément certification and triple ISO accreditations. The 4wall panel system is now one of the most widely accredited systems using modern methods of construction in the UK.”
Source: www.etopia.eco
Donaldson Timber Systems Secures OSHA Position
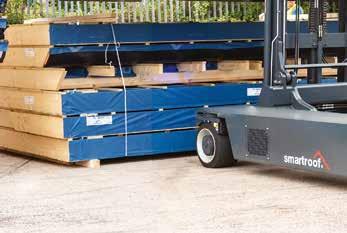
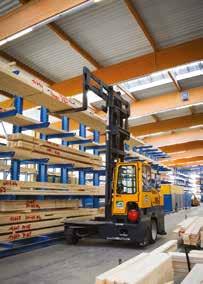
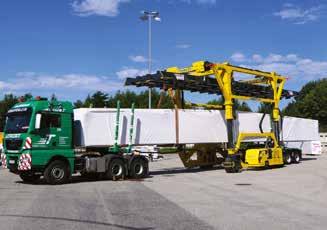
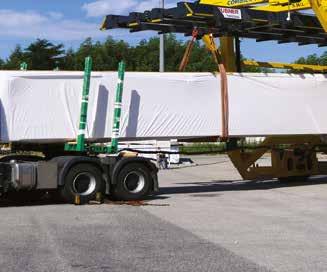
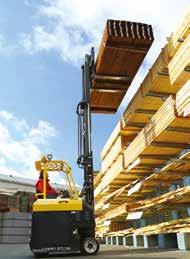
Donaldson Timber Systems (DTS), has secured a position on the Off-Site Homes Alliance (OSHA) national construction framework for volumetric (CAT 1) and panelised (CAT 2) Modern Methods of Construction (MMC). The framework is valued at £2billion. DTS will deliver offsite timber panelised system build for Category 2 housing over four years.
Working closely with 23 local authorities and housing associations nationally, DTS will design, manufacture and install timber frame wall panel building systems that meet build speed, fabric performance, building design and cost requirements. With a fabric-first approach that achieves net zero operational carbon, housing providers can use DTS’ timber systems to create sustainable, resilient, and affordable homes that meet the Future Homes Standard.
Earlier this year, DTS became one of the first manufacturers to achieve Buildoffsite Property Assurance Scheme Plus (BOPAS Plus) in recognition of the quality and durability of its offsite build systems. With DTS’ state-of-the-art open and closed panelised systems – Alpha, Delta or Sigma ll – works can still be carried out on-site, ensuring that social value potential is reached within the communities served.
Mike Perry, Business Development Director, Donaldson Timber Systems, said: “By securing a position on the OSHA MMC Cat 1 and Cat 2 Framework, we can build upon our strong relationship with affordable housing providers nationally and bring them along on DTS’ timber frame, fabric-first journey. We look forward to facilitating greater efficiency and value for clients who procure via this framework and supporting OSHA’s mission to deliver 20,000 homes with MMC technology.”
Matthew Harrison, Chief Executive of OSHA member Great Places Housing Group, said: “We’re delighted to be working with Donaldson Timber Systems on the new OSHA framework. We’re confident they will be able to work with us and the OSHA clients in delivering the sector’s extensive development
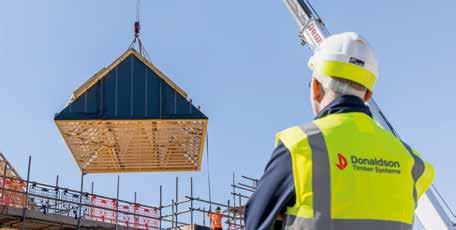
ambitions. We were pleased with the positive response from the market and received high quality proposals and substantial social value pledges for our communities. We are now looking forward to mobilising the framework and working together on new projects to realise our ambitions of delivering much-needed affordable homes.”
With unrivalled experience and knowledge in offsite construction, DTS has an established history of bringing new commercial and operational innovations to the market with the Sigma II closed panel system, offering near-Passivhaus standards of performance and sustainability.
Source: www.offsiteha.org
www.donaldsontimbersystems.com
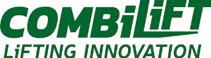
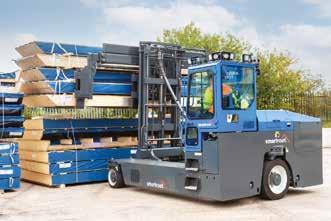
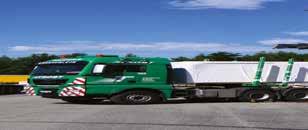
Safety Storage Efficiency
Kier JV Created with McAvoy and Metek
Kier, with Joint Venture (JV) partners, McAvoy and Metek has been appointed to all six Lots of Crown Commercial Services’ (CCS) new £10billion Offsite Construction Solutions (OCS) framework. The new framework replaces the existing modular building framework and will run for the next four years.
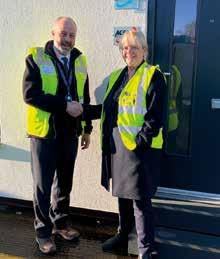
Kier has created two unique JVs with external offsite manufacturing partners McAvoy and Metek, who are both experts in their method of construction, bringing high quality, innovative design, manufacturing and installation ability. The two JVs will allow Kier to deliver on every Lot in the OCS framework, which provides public sector organisations with all elements of offsite construction solutions, from design, fabrication, construction and installation, through to direct access to manufacturers.
• Kier with manufacturer McAvoy, known as Kier McAvoy, will deliver projects using pre manufactured 3D primary structural systems
• Kier with manufacturer Metek, known as Kier Metek, will deliver projects using pre-manufactured 2D primary structural systems.
Stuart Togwell, Group Managing Director at Kier Construction, said: “Building on the ambitions of the Construction Playbook of using MMC and offsite solutions to drive improvements is a core imperative
FHP MEP Specified for Huge Wembley Project
for Kier, and securing a place on all Lots means we are well-placed to support the delivery of vital new infrastructure in the UK. Our forward-thinking JVs with McAvoy and Metek will allow us to provide more capacity and high-quality end-to-end solutions for our public sector clients and to continue to deliver the best value through innovation across the wider industry.”
Ron Clarke, CEO, McAvoy, from the Kier McAvoy consortium, added: “This is a significant milestone for McAvoy, and we are delighted to be combining our leading-edge, high-quality precision manufacturing capabilities with Kier’s scale and expertise. We have been innovators and market leaders for more than 50 years. Our team is firmly focused on delivering consistently high-quality product and customer service across the UK and Ireland. With significant experience of MMC we are very much focused on helping our clients meet their ESG goals. We look forward to working in partnership with Kier to deliver on that commitment within the OCS framework.”
Oliver Rogan, Managing Director of Metek, said: “Winning this OCS framework has demonstrated the importance of working as a team. Metek and Kier have been working closely together for the past 12 months, driving a strategy to build projects in a more energy efficient and cost-effective manner, whilst maintaining the very highest health & safety standards. This ground-breaking collaboration unlocks Metek’s manufacturing and installation potential, whilst enabling us to grow, learn and develop alongside a formidable Kier team.
Building services and engineering consultants FHP has been specified to provide MEP and design services for a multi-million-pound residential led mixed-use regeneration project in North London.
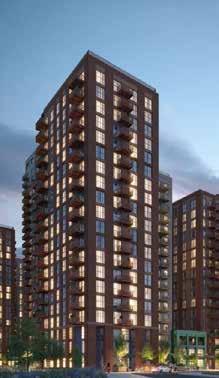
The firm is providing a range of RIBA Stage 3, 4 and 5 MEP technical and construction Revit design services to the city’s leading residential-led mixeduse developer Regal London, which is leading the £270million redevelopment of the former Euro Parts headquarters in Wembley. The site is currently being transformed into 759 new residential units across five high-rise buildings, which will feature 78 three-bedroomed family homes and more than 200 affordable properties. It all comes under plans to deliver a sustainable mixed-use development in line with the local authority’s wider aspirations for the growth and prosperity of the Wembley area.
More than 33,000sq ft of flexible commercial space is also under construction to accommodate retail, light industrial and logistics businesses. New communal amenity spaces within the upper roof terraces and at podium level area will eventually feature along with new landscaping, improved public access along the Wealdstone Brook, and the creation of 31,000sq ft of children’s play space.
FHP has been closely involved in the project from the start of RIBA Stage 3 providing mechanical, electrical and public health services together with sustainability, building physics and digital engineering support for
“Here at Metek, we have been at the forefront of light steel framed Modern Methods of Construction for over 23 years. I feel that this new alliance is a game changer in terms of adding components to the manufacturing process. Working with the Kier team on this bid has been inspiring and the whole Metek team are excited to be embarking on this journey and committed to delivering the key requirements of the agreement, whilst continuing to champion UK manufacturing.”
Photo: Oliver Rogan, Managing Director, Metek with Kier’s, Chief People Officer, Louisa Finlay
Source: www.kier.co.uk
what is being seen as one of North London’s most prestigious regeneration projects.
A key aspect of FHP’s work centred on a review of proposed heating systems, developing two design options for either a 100% electric heating scheme or an alternative connection to a local district heat network. This allowed the developer to decide the best approach – a 1.7MW ASHP (air source heat pump) in conjunction with 1.7MW electric boilers –as part of a revised energy strategy submitted within the overall planning submission.
Services to facilitate design stage and As-Built SAP and SBEM energy use and carbon emissions calculations were also completed by FHP as part of a comprehensive package of support. The Regal London project is the latest success for rapidly growing FHP, which employs 52 people and continues to see strong demand for services and growth across its London and Leeds operations.
Tony Hewitt, FHP Managing Director, said: “Fulton Road demonstrates the added value and insight we bring to multi-million-pound investment projects through innovative design-led MEP services. It’s also a reflection of the excellent work our team provides as we develop our commercial offering. We expect to see a strong
Source: www.fhpp.com
what will you take a stand for?
Build a better future for the built environment
Futurebuild provides the stage for inspiring ideas, innovative solutions & knowledge sharing to drive sustainable construction and help us reach our goal of net zero. The exhibition brings together the entire supply chain to showcase, debate and understand the advancements in sustainable construction and the emerging technologies that will make net zero possible.
Futurebuild is taking a stand for a better built environment and is urging companies and professionals throughout the construction supply chain to make a similar commitment by ‘taking a stand’ on an issue they passionately believe will help propel the industry towards a more sustainable future. Join us in taking a stand.
SCAN HERE
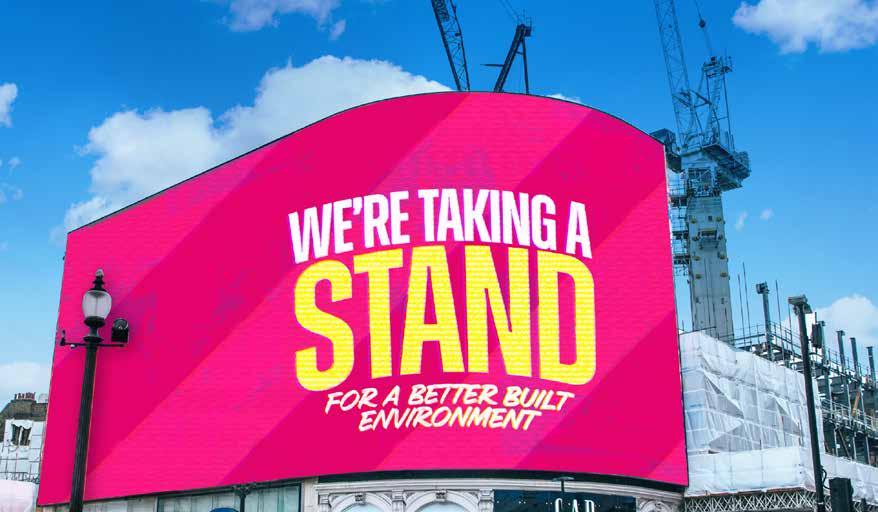
Merit Expands Team and Factory Capacity
Northumberland-headquartered Merit has announced a 4000sq m factory expansion at its Cramlington site, to accommodate its plans for continued growth. Merit already has one of the largest construction manufacturing facilities in the UK at 270,000sq ft (25,084sq m) and it is now extending its factory space to address increasing demand and to better meet customers’ needs.
In line with its impressive growth plans, Merit has already doubled its workforce in the last two years and expects this facility expansion to add over 50 new jobs. The extended high-bay facility will accommodate two new manufacturing lines for Merit’s UltraPOD+ product, an expandable full building solution, and will enable the pre-assembly and testing of two-modules vertically stacked.
This provides an enhanced understanding of the alignment of modules prior to the transportation to the site. Additional equipment, such as two 50T gantry cranes and a module lifting frame, will also be included into the new setup. The factory expansion will enable Merit to compete even more successfully for larger contracts against global competition and deliver long term growth for the business and is expected to be operational by April 2023.
Net Zero Roadmap Examines Carbon & Cost Savings
Tony Wells, CEO of Merit, commented: “Merit’s strategic objective is to deliver a step change in productivity within the construction industry and to show that investment in R&D and leveraging innovative approaches, such as advanced 4D BIM modelling technology, can lead to significant improvements. Our factory expansion will enable us to further optimise our way of working and better serve our customers.”
Merit has also announced plans to double its apprenticeship targets in 2023, as part of its ongoing efforts to address future skills needs. This follows the latest report from the Construction Skills Network (CSN) which predicts that an extra 7,900 workers will be needed in the North East from 2023 to 2027 to meet construction demand. If projected growth is
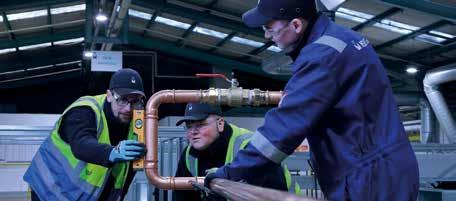
met, the construction workforce in the UK will remain around 2.67 million.
Merit has been committed to investing in homegrown talent for many years, starting its apprenticeship programme back in 2013. It has so far worked with nearly 60 local apprentices, in which all have received a full-time employment offer once completing the programme. Now in its tenth year, Merit plans to create a further 20 opportunities this year to help meet the business’ need for more skilled workers following a string of successful project wins, including the UK’s first CAR-T cell manufacturing facility for Autolus Therapeutics and Piramal’s ACD manufacturing facility expansion. (For more on this project see p50.)
Source: www.merit.co.uk
to better meet the needs of a low-carbon world. Commissioned by Timber Development UK (TDUK) in collaboration with eleven UK timber trade associations, the Timber Industry Net Zero Roadmap was developed following a
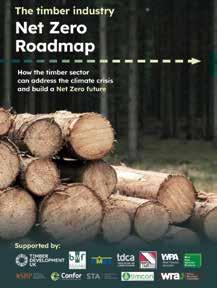
comprehensive
effort to map and measure carbon emissions across the whole supply chain.
The first step of the roadmap has been to outline the size of the challenge, with 12 months of expert analysis showing the timber supply chain is responsible for 1,575,356 tonnes CO2e territorial emissions – which is about 0.35% of the UK total.
While this is very low compared to other manufacturing industries such as UK steel production, which is responsible for 12 million tonnes CO2e (2.7% of UK emissions), and concrete, which is responsible for 7.3 million tonnes CO2e (1.5% of UK emissions), the Roadmap starts from the position that no emissions are acceptable.
The Roadmap also seeks to influence the 3,655,715 tonnes CO2e of imported embodied emissions which comes from the processing of wood products in the country of origin. This figure, taken together with territorial emissions, would make the timber industry responsible for about 0.68% of the UK’s total emissions. Of the total consumption emissions, 49% of these emissions are from the transport of timber products, and 34% are embodied in imported materials. The remaining 17% are from the UK production processes within the industry, and waste.
One of the key aims of the Roadmap says Timber Development UK Sustainability Director Charlie Law, is to challenge the misconception that as the timber supply chain comes from a low-carbon base, there
are few opportunities for the timber supply chain to influence their emissions.
“There are some really quick wins in there for businesses – wherever you are in the supply chain –which can be put into practice now. And if you reduce your carbon, you reduce your costs. If you change the energy source for heat for your factory processes, reduce the waste from your product manufacture, or reduce your energy use by using better lightbulbs – there are literally thousands of ways both big and small you can start reducing your emissions.
“This includes for the single biggest contributor to the timber industries carbon profile – transport. While there aren’t yet many fully electric HGV options, to remove these emissions, there are ways to be more efficient. And if you’re using less diesel, you reduce your emissions and your fuel costs. Once you have an emissions profile for your business, you see not just your environmental impact, but also your operational inefficiencies. From here you can start your business on a pathway to be more competitive in a low-carbon market.”
With a range of pathways now set out in the Roadmap for the industry to achieve Net Zero by 2050 – at the very latest – this document has been made freely available for all businesses in the timber supply chain to adopt, alongside a set of ten highlevel policy recommendations.
Source: www.timberdevelopment.uk
Anew timber industry net zero roadmap aims to accelerate the productivity, sustainability, and innovation of the sector
Integra Buildings Appointed to CCS Offsite Framework
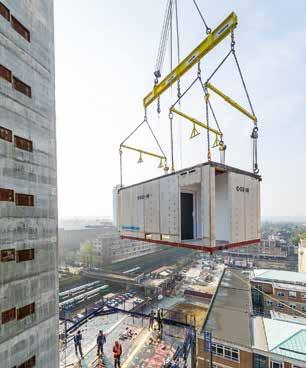
Modular specialist Integra Buildings has been appointed onto a £10billion Government framework to drive investment in the offsite construction sector. Integra has been named as a supplier on the newly launched Offsite Construction Solutions (OCS) framework, which spans a variety of sectors including health, housing, education and defence.

A total of 29 suppliers have been named on the new framework, which runs for four years, with the possibility of a three-year extension. It means Integra will be able to tender for major contracts with public sector clients across the UK.
Gary Parker, Managing Director at Integra Buildings, (pictured) said: “To be named on the new Offsite Construction Solutions framework is a huge vote of confidence in Integra and our proven capability to deliver major public sector projects to the very highest standards. Since being appointed onto the old framework four years ago, we’ve delivered some of the biggest projects in our 25-year history. Integra continues to grow and evolve, with clients right across the UK. The offsite and modular construction sector continues to expand at pace and being named on this framework ensures we’ll remain right at the forefront of that exciting journey.”
Integra has delivered a series of key projects for clients including Network Rail, the Environment Agency and the Department for Work and Pensions. Contracts completed under the previous framework include the construction of temporary housing for Reading Borough Council, a new job centre in Birmingham and modular units which were shipped to Cyprus for use by the Ministry of Defence.
Integra designs and constructs buildings offsite in controlled conditions at its purpose-built factories in Paull, East Yorkshire, before delivering and installing them in situ, a process that reduces project timescales and minimises disruption to customers, with no compromise on quality.
Plumbing as versatile as your modular design
You get complete freedom of design with our pipes and fittings, because our system fits in effortlessly with your plans.
• A vast range of fittings and pipes to suit all designs
• MLC pipes can be formed easily around corners and obstructions without having to add connections, saving on both time and cost
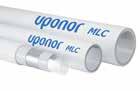
• Fast 3-step installation with no special skills required– designed to fit and forget
• S-Press PLUS fittings includes multiple observation windows for complete joint security
• Fewer connections for a faster install with less cost
• Optimal flow rates and reduced pressure drop

Integra enjoyed a busy 2022 which saw it complete significant contracts including the delivery of new offices for Triumph Motorcycles at its site in Coventry, providing school buildings across the country, from Merseyside to Surrey, and forge an exciting new partnership with More Housing to supply modular accommodation units to combat homelessness across the UK.
Source: www.integrabuildings.co.uk
Everton Stadium Build Employs Offsite MEP
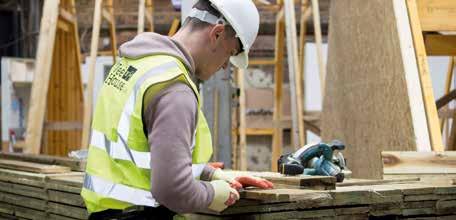
The new Everton Stadium is set to enter a transformative phase in 2023, with work ramping up on the internal works. As the external appearance continues to develop, the race is on to make the build watertight to allow tradesmen to begin work in installing hundreds of miles of piping, wiring and the internal fittings.
“I think we should just warn spectators that in 2023 it will look like things are slowing down from an external perspective,” said Chief Stadium Development Officer Colin Chong. “A big milestone that people will want to see is the east stand steelwork that will fill in the gap between the north and south steelwork. However, it will slow down externally, although internally it’s going to be a hive of activity. In real terms, the fit-out is starting in January, when we will start putting all the wires and piping in. People won’t notice it as much, as it’s internal, but it’s equally as important to the stadium development as the roof going up.”

As with the external concrete and steel components, much of the internal walls are pre-manufactured in factory conditions and transported to site in just-intime slots for installation. All mechanical, electrical
Wee House Group Expands Premises & Executive Team
The Wee House Group has announced the opening of a significant additional working space in their East Ayrshire factory, taking their premises to 120,000sq feet, an area the size of almost two full-sized football pitches. The new space, Hall 4, is an additional area for the construction of modular homes, required to facilitate fulfilment of a burgeoning order book.
The facility is itself a repurposed entity, once home to the bustling Kingsmead Carpets factory – a major employer in the town of Cumnock at the turn of the century. Breathing new life into this enormous, historic building has been an outstanding achievement for The Wee House Group, especially in the short time since the company was formed, and the production of sustainable, modular housing, using modern techniques continues to provide a real boost to the local economy.
The Wee House Group comprises: The Wee House Company (bespoke solutions for small sites), Connect Modular (delivering large scale, affordable developments) and Hope South West (groundworks division) and provides a full, turnkey service from concept design including statutory consents, to the manufacturing of new homes and their completion on-site, to a variety of clients, from private individuals to local authorities and housing developers.
and plumbing (MEP) systems in the stadium will be manufactured offsite in the Oldbury (West Midlands) factory of Laing O’Rourke’s specialist MEP business, Crown House Manufacturing. The six-foot high modules and an innovative product called Techwall, will be delivered to site, lifted into place, connected and commissioned, in an approach that helps save time and energy.
“There are life-safe systems, resilience to be planned, and all the toilets on the concourses will be coming in in modules, pre-manufactured,” explained Chong, in a special club podcast on the stadium build. “The pipework will arrive pre-manufactured, tested in the factory, and be offered up and connected, so there
are less connections throughout the whole building. There’s less welding, so less risk of fire and it’s the modern way of building things.
“Again, we’ll be working on all four concourses simultaneously, along with the hospitality lounges starting, probably in March. The skeleton of the dressing rooms is already in place (in the west stand). We’ve got the pit for the hydrotherapy pools and all the apertures for all the incoming services. We ramp up with people and we’ll end up with 1,000 people there next year and probably up to around 1,400 on-site the year after.”
Source: www.evertonfc.com
Jennifer Higgins, Managing Director at The Wee House Group commented: “We’re absolutely thrilled to have expanded our manufacturing facility to cope with the growing pipeline of work. It’s wonderful to see the volume of houses increasing in the factory week on week and great that we have the space to maximise production.”
The Wee House Group has also announced a new Executive Management layer within their organisation, comprising Richard Reid, who will take on the role of (Acting) Chief Executive Officer and Emma Robertson who will step up to a new role as Chief Finance Officer, as Jennifer Higgins, current CEO of the group takes a step back due to maternity leave.
Emma Robertson, Chief Finance Officer comments: “I am really excited to work with Richard and the teams across the business to build on the tremendous
success we have already achieved. I am confident that as a team we can achieve all our ambitious goals and create an environment where people can grow and develop in their career.”
Richard Reid, Acting Chief Executive Officer, said: “I would like to sincerely thank Jennifer for giving me the opportunity at The Wee House Company in 2019, and putting her trust in me to continue to manage and push the company forward in line with our 5-year strategy. I would also like to thank our staff, sub-contractors, and consultants without whom, we would not be in this position. It is my intention to be bring the same enthusiasm and drive to the business as Jennifer, therefore I am asking for the continued support and effort from everyone over the next year to ensure we meet our targets for 2023 and beyond.”
Source: www.theweehousecompany.co.uk
Tide Construction Reaches New Heights at CTBUH Awards
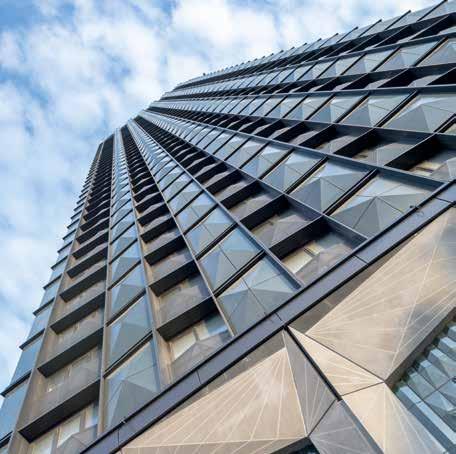
UK modular developer and contractor, Tide Construction Limited with its volumetric modular company Vision Modular Systems recently received five Awards of Excellence at the Council on Tall Buildings and Urban Habitat (CTBUH) Awards in Chicago: Best Tall Building 100-199m, Best Tall Residential Building, Construction Award, Innovation Award, and an overall category win for Structural Engineering. These accolades were awarded to Tide and Vision alongside the design team, including MJH Structural Engineers, Barrett Mahony Consulting Engineers and HTA Design, for the work completed on Tide’s Croydon residential development, Ten Degrees.
This international recognition places Tide alongside iconic buildings and fellow 2022 winners, including Dubai's Museum of the Future and KPF's One Vanderbilt, the tallest office tower in Midtown Manhattan, and follows an award earlier in the year for Innovation at the World of Modular conference in Texas.
The CTBUH is a world-leading organisation for those working on the future of cities, the role of urban density and of vertical growth. Celebrating innovative developments in the construction of tall buildings worldwide, the annual CTBUH Conference and Awards recognises the achievements of those working at the height of these ambitions and how vertical construction can make our cities more sustainable and healthier.
Tide and Vision’s winning development, Ten Degrees, is an exemplar of its track record of building greener, safer, faster and better-quality homes. Comprising 44- and 38-storey towers and reaching a total height of 136m, Ten Degrees is the first modular building over 40 storeys to be delivered in the world and construction was completed in just 26 months. The towers were designed by HTA Design and delivered using Tide’s sister company Vision Modular Systems with engineering by MJH Structural Engineers and Barrett Mahony Consulting Engineers using advanced 3D volumetric methods. The scheme is now owned
by Greystar; a global leader in rental housing and Henderson Park; a pan-European private real estate equity platform.

Ten Degrees shows how modular construction can contribute to global industry innovation while responding to worldwide housing, skills and sustainability challenges. Providing 546 new Build-toRent homes for the London borough of Croydon, this development also puts Tide and Vision at the forefront of placemaking.
John Fleming, Chairman and Founder of Tide Construction & Vision Modular Systems, said: “These awards recognise Tide and Vision’s industry-leading position worldwide. The work delivered on Ten Degrees demonstrates how we can revolutionise construction methods while providing housing faster, safer, and more sustainably at scale, both in the UK and globally.
MAXIMISE THE OFFSITE OPPORTUNITY
“It is an honour to receive such high-profile accolades from the CTBUH, an organisation that continues to actively shape the future of the urban environment and lead the way in sustainable vertical urbanism. This recognition also testifies to the momentum building up for volumetric construction in the UK and across the globe. We believe we are demonstrating the potential of volumetric modular as a mainstream method of construction and our track record is showcasing the many benefits it brings. We are determined to drive forward the delivery of smarter, greener, quality homes with our significant pipeline planned for 2023 and beyond.”
Source: www.tideconstruction.co.uk
www.offsite-expo.co.uk/exhibit
OFFSITE EXPO has a range of exhibition packages available to suit any marketing aims, resources and budget.
MAKE UK MODULAR
MILESTONES IN MODULAR
Make UK Modular is helping promote the benefits of modular homebuilding and bring a fresh focus to the use of offsite technology. Head of Make UK Modular Steve Cole, spoke to us about progress so far and a busy year ahead.
the sector. Nearly £1billion of finance has been invested and modular alone is responsible for nearly 1/3 of all R&D investment in the construction of buildings sector. Between 2022 and 2025 we expect to see modular increase it’s delivery fivefold to roughly 15,000 new homes per annum.
Of course, the external operating environment remains extremely challenging. The construction industry as a whole saw over 2,500 insolvencies registered in 2021, amounting to 19% of all insolvencies and modular is certainly not immune to the pressures facing our economy. Which is why we believe it’s so important that Government continues to back the sector.
Q: Since your launch in December 2021 – with some of the sector’s leading names – how is Make UK Modular progressing as a trade body?
Steve Cole (SC): I’m delighted with Make UK Modular’s first year, though I must say I did not think we’d have got through five housing ministers. Year 1 was always going to be about getting the fundamentals right. We had five priorities to create the foundations we needed to deliver for the sector: establishing a strong working relationship with Government, the opposition, MPs, and the Civil Service, building a robust and credible evidence base about the benefits and potential of modular housing, establishing and delivering against a new set of sector policy priorities, delivering a consistent, positive media and public affairs presence and of course, growing our membership.
With more than 20 MP meetings, the publication of ‘Greener, Better, Faster: Modular’s Role in Solving the
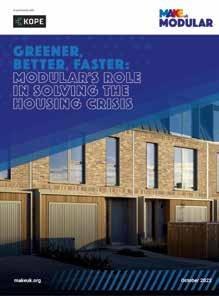
Housing Crisis’ is the first ‘state of the sector’ report into UK Modular housing, establishment of five core policy asks, more than 80 pieces of positive media coverage and a 40% growth in membership, we really delivered in a political environment of unprecedented volatility. We couldn’t have done any of this without our amazing members who have taken the time to craft policy asks, attend party conference, host factory visits for MPs, journalists, and TV crews and provided data to inform our reports.
Q: There has been a lot of investment into UK modular businesses and offsite systems in the last 5-6 years with new industry entrants, but also some notable failures – is the sector at a crucial stage of development?
SC: Absolutely, if you look at the innovation curve the sector is now at the inflection point between innovators and early adopters. What is often unreported is the sheer scale of investment which has gone into
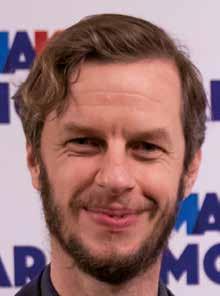
Q: The discussion surrounding the number of new homes required across the UK never ends. How can the modular sector make a dent in the oft-quoted 300,000 homes a year?
SC: Our ambition is for modular to deliver 30,000 new homes a year by 2030. 10% of all homes but, importantly, 30% of the current shortfall on the country’s new homes target. With 15,000 new homes a year expected to be delivered by 2025, we’re convinced that modular can make a real dent in that shortfall. Equally importantly, modular can do this without cannibalising the existing (and rapidly shrinking) housebuilding workforce as 65% of the jobs in modular are in manufacturing rather than construction.
Q: The built environment is under pressure to be more energy/ material-efficient, decarbonise and use more sustainable approaches to construction – how does modular construction fit into this equation?
SC: In my mind, net zero and modular are two sides of the same coin. The sort of efficient low carbon designs, net zero, ESG, and, more importantly, the physics of climate change demand of housing are ideally suited to modular. In 2022, an academic study of Vision Modular Systems’ modular high-rise development in Croydon found that it contained 40 to 45% less embodied carbon than an equivalent building built using traditional methods. For low-rise buildings, these savings are even greater.
One of our members produces low-rise homes with just 18% of the whole-life embodied carbon of the average new home being built today, already surpassing RIBA’s 2030 targets for the residential building sector. Some manufacturers who produce low-rise homes using timber (one of the building materials with the least embodied carbon) calculate upfront carbon savings to be over 80% on traditional build. In one case study, it cost just £3,000 extra to make a modular home zero-carbon (and £5,000 extra for an apartment), whereas achieving this through traditional building methods would be prohibitively expensive for clients.
Q: A criticism levelled at volumetric modular generally, is the lack of interoperability amongst systems and providers in the event of failures and this is putting off clients and developers from adopting long term modular commitments – is that a genuine worry?
SC: This is something we’ve had very productive engagement with government about. It’s more of a concern in the infrastructure space than residential where designs have only the government as a client
and there is far less investment in proprietary IP. Housing is a much more varied market and developers (both traditional and modular) need varied products to compete in that space and deliver the different homes people need such as apartments vs houses or affordable vs luxury. The experience to date has been where there have been failures, another developer comes in and builds out the scheme just as they do in traditional construction.
Another thing we’re seeing, is that as more clients work with modular, they better understand the unanticipated benefits of modular such as a 50% reduction in on-site disruption and 80% fewer vehicle movements, meaning lower than expected costs and reduced concern from local people and planning authorities.
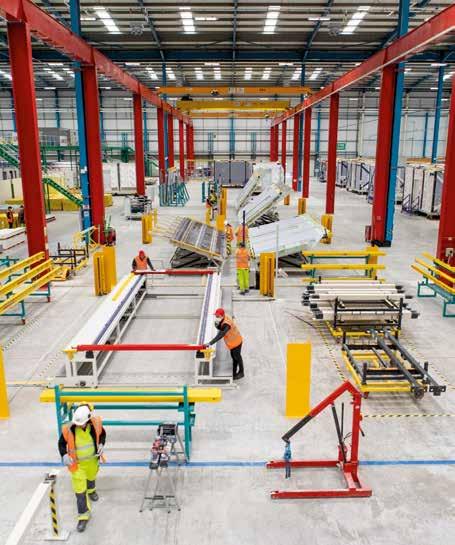
ALIGN YOUR PRODUCTS AND SERVICES WITH THIS INCREASINGLY IMPORTANT SECTOR
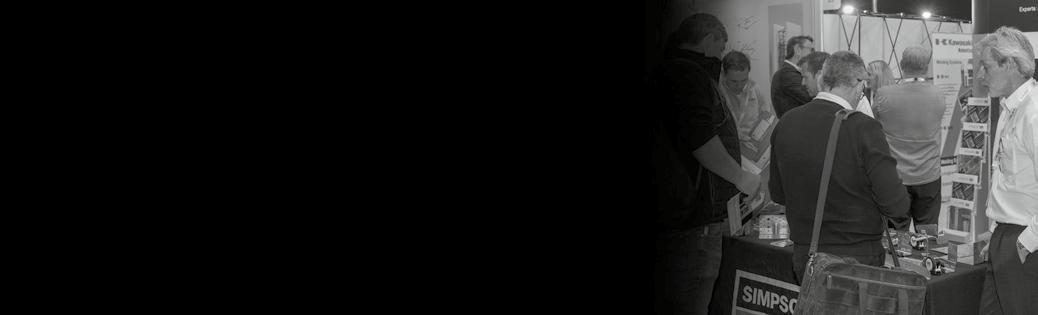
...at the UK’s biggest showcase of offsite manufactured construction technology and solutions.
www.offsite-expo.co.uk/exhibit
MAKE UK MODULAR

Q: The UK suffers from low levels of productivity– how can modular methods bring improvements here and boost building safety and design?
SC: Construction is one of the least productive sectors of the UK economy – falling behind both service and manufacturing. Shockingly, construction of buildings is less productive now than it was 25 years ago. Modular housebuilding is over 40% more productive in terms of hours worked per m2 built than traditional brick and block/timberframed on-site building. It takes a modular manufacturer seven to nine hours of labour per m2 to build the superstructure of a house, compared with 12 hours per m2 for both brick and block and on-site timber framed methods. In addition, modular reduces waste by an average of 90%. This is unlocked through the efficiency gains of the factory’s assembly line system.

In terms of building safety, we’ve had experts like Dame Judith Hackitt and the Government’s Director General of Building Safety, visit our members and see first hand how homes manufactured in a controlled factory environment, using a continuous improvement process, delivers industry leading levels of safety both for the buildings and the workforce producing them.
Q: Modular buildings are faster to produce and construct than traditional build but there seems to be a lack of data to prove its many merits – can Make UK Modular help here?
SC: It’s an area we’ve been keen to address and was covered in our first major report ‘Greener, Better Faster: Modular’s Role in Solving the Housing Crisis' which came out last autumn. We found that modular homes are typically built 50% faster than traditional build and that’s without considering the potential to deliver a more efficient critical path in which homes are produced in a factory as the groundworks are undertaken.
Q: What plans does Make UK Modular have for 2023?
SC: As you’d expect given the sector leaders we work with, our board and I are extremely ambitious about 2023. Likely, it will be the last year before we see a General Election so a lot of the agenda until 2030 will be set in the next 12 months. In 2022 we created a platform to engage with Government. In 2023 we want to build on our success by delivering a more campaigning approach focusing on: tackling the cost-of-living crisis through net zero, energy efficient homes, developing new skills and creating new jobs for the UK economy and delivering new housing to meet growing demand.
We have several major reports planned and have already begun speaking with major political figures such as our recent roundtable with Shadow Business Minister Bill Esterson. The first key output of this year will be a major report into modular’s role in solving the housing labour market crisis which will be published in March. We are also actively looking to grow our membership. You’ll see announcements about new members joining us soon. We are also launching several new membership categories for smaller modular manufacturers, members of the supply chain, and Category 2 providers. We’re always keen to hear from anyone who is interested in joining us. As an organisation, we’re only ever as strong as our membership.
For more information visit: www.makeuk.org
Images:
01. Steve Cole, Head, Make UK Modular
02. The report ‘Greener, Better, Faster: Modular's Role In Solving The Housing Crisis’
03. Precision factory methods are at the centre of solving the UK’s housing problems
04. Time and costs can be reduced using modular methods
M-AR JOINS MAKE UK MODULAR
M-AR has become a member of the UK’s modular housing trade body, Make UK Modular, and will join industry leaders including, among others, Ilke Homes, Vision Modular Systems, L&G Modular, Top Hat, as members of Make UK Modular.
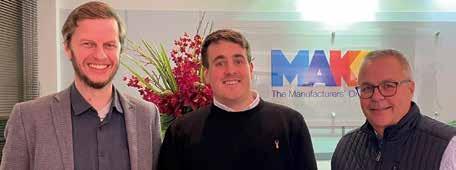
“This year we’re celebrating our 15th anniversary as a business and we’ve got big plans to continue to grow and scale up our operations. We’re continually investing in and innovating our offering and we’re now seeking investment to scale the business further as part of our strategic growth programme - our inclusion as a member of Make UK Modular is a key strategic step towards this goal.”
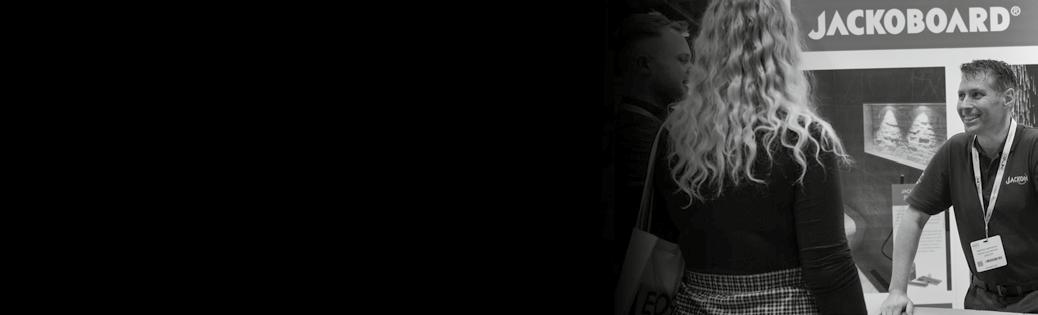
Steve Cole, Head of Make UK Modular said: “We are delighted that M-AR Offsite is joining Make UK Modular. M-AR is the perfect fit as the team is committed to driving innovation in the modular sector and the company’s outward-looking approach means M-AR is focussed on promoting the use of modular widely for the benefit of all not just its own clients –something which aligns closely with what we’re aiming to achieve.
“M-AR’s recent track record delivering schemes ranging from an independent living project with Centrepoint to new homes with Bromley Council demonstrates the ever-increasing diversity of homes modular is delivering up and down the country.
The modular industry needs ambitious and innovative businesses like M-AR Offsite to thrive. I, and all our members, look forward to working with them.”
Ryan Geldard,Director at M-AR added: “One of our guiding principles at M-AR is to strive to challenge accepted industry norms to unlock the full potential of MMC in order to build future-proof homes and buildings quicker and more efficiently. I’m a firm believer that collaboration is key to doing this so it’s really exciting to be part of Make UK Modular so we can continue to work closely with our industry peers to drive innovation in modular construction as part of our mission to take MMC into the mainstream.
Make UK Modular’s recent groundbreaking report titled ‘Greener, Better, Faster: Modular’s Role in Solving the Housing Crisis’ highlights how the modular housing sector is currently responsible for one third of the construction industry’s research and development spending. The report also concluded that with Government backing the offsite sector would be able to deliver more than 20,000 new modular low energy homes per annum by 2025.
For more information visit: www.m-ar.co.uk
OFFSITE CONNECT BUYERS AND SPECIFIERS FORUM - facilitating meetings with those seeking the latest offsite innovation.
www.offsite-expo.co.uk/exhibit
FIT-OUT FOR OFFSITE
Morland’s timber-based fit-out materials have machining, cutting, drilling and finishing completed within quality-controlled manufacturing facilities and benefit from lean manufacturing methods ideally suited to offsite projects.
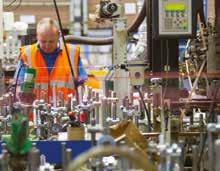
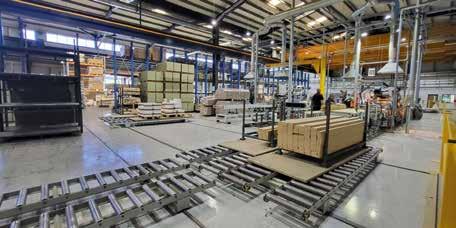
1 2 3
As the construction industry faces well documented challenges in key areas such as inflation, labour and skill shortages and the increasing focus on sustainability, the offsite and modular section has a bigger role to play now more than ever and Morland UK are proud to be part of the solution and supporting its customers in this sector.
Paul Millington Morland UK, Key Account Manager and industry expert believes. “Whilst the country starts to recover from the impact of COVD-19 it is obvious the significant role Modern Methods of Construction (MMC) plays in meeting market requirements moving forward. With a growing population driving a clear need to provide more schools, hospitals,
prisons, homes and other vital services the modular sector and Morland UK are perfectly positioned to meet the challenges the industry currently faces.”
Based in Welshpool, employing over 130 people, the privately owned company, historically known across the leisure industry, has taken their manufacturing experience and ‘justin-time’ production skills to become a trusted supplier within the offsite and modular sector from education, healthcare, retail and residential homes to MoD and MoJ projects. “Over the last five years we have increased our manufacturing capability and introduced several products to support the sector,” Paul continues.

“From prefinished plasterboard, MDF skirting and architrave along with Partition Kits which are all fully finished and ready for onsite installation. These products were all developed with the aim to reduce the use of wet trades.” Morland UK continually invest in its site and employees and to support the offsite industry they have established a dedicated team of estimators and project co-ordinators. On-site 20,000 plasterboard panels are produced per week along with 120,000 metres of profiles. Supported by a fully stocked 60,000sq ft distribution unit which enables quicker lead times.
One of the key areas of investment and growth at Morland UK has been the crucial area of fire and certification. Producing fully encapsulated FD30 and FD60 fire doors and doorsets and as part of the British Woodworking Federation (BWF) Certifire and Certisecure schemes have gone through vigorous, independent, UKAS accredited testing, to BS 476-22:1987 and BS EN 1634-1:2014.
Morland UK also holds both FSC® and PEFC-certification for the purchase, processing, sales and distribution of certified timber and actively supports sustainable practices to protect resources for the future.
“Morland UK will continue to bring innovative new products and manufacturing processes to the offsite construction industry,” adds Paul. “Please get in touch to find out how we can support your business.”
For more information visit: www.morlanduk.com
SAVE THE DATE AND SIGN UP EARLY FOR OFFSITE EXPO 2023!
OFFSITE EXPO brings together those who are driving change in the construction sector – the event will play host to the leading UK and international offsite manufacturers and component suppliers showcasing a broad spectrum of panelised and volumetric modular systems, plus pod and prefabricated MEP solutions.
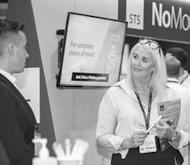
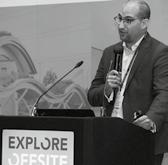
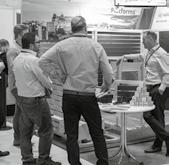
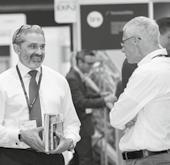

>4000
ALIGN YOUR PRODUCTS AND SERVICES WITH THIS INCREASINGLY IMPORTANT SECTOR
Maximise your business development potential at the UK’s biggest showcase of offsite manufactured construction technology and solutions.
BOOK YOUR EXHIBITION SPACE NOW!
For more information contact julie.williams@radar-communications.co.uk or call 01743 290042
PRECAST CONCRETE CLADDING LEADS THE WAY IN FIRE RESILIENCE
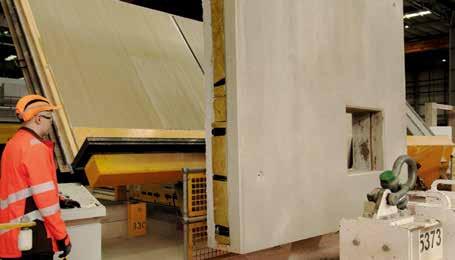
In recent years the construction industry has begun to re-evaluate building safety with the hope that we never again witness a tragedy on the same scale as Grenfell Tower, however as MPA UK Concrete explain, the threat of fire in the spaces we live and work remains.
In 2021, the fire and rescue services dealt with 185,437 fires in England alone, tragically including 276 firerelated fatalities. That threat becomes even more significant in multiple occupancy buildings such as flats, hotels, and student accommodations and those with vulnerable occupants including schools, hospitals, and care homes. So how can we ensure that our buildings are designed to protect against fire and give peace of mind to the people that occupy, own and insure them?
The obvious answer – prioritise the use of non-combustible building materials
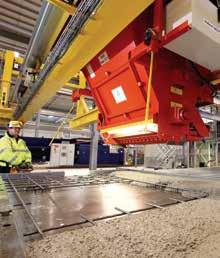
Building with non-combustible materials means building resilience into the spaces we occupy. While the best protection is always prevention, if a fire does break out, concrete is a reliable material and a low-risk solution that can save lives and property. Concrete is an inherently non-combustible material – it has the highest A1 reaction to fire classification possible (in accordance with BS EN 13501-1:2018).
Material Choice Can Reduce Risk from Fire
Concrete is non-combustible – it does not burn
Concrete does not add fuel to a fire
Concrete does not emit any toxic fumes
Concrete does not produce smoke
Concrete has a slow rate of
Conducting routine fire tests on concrete facades isn’t necessary to prove that concrete is a noncombustible material or a necessary part of building certification. However, to show how resilient this material can be, MPA Precast carried out a full-scale fire test on precast concrete cladding panels.
Fire test demonstrates superior performance
It was important that any test or demonstration was carried out by a trusted industry body and in adherence with recognised standards. For this reason, MPA Precast commissioned the Fire Protection Association (FPA) to carry out a
BS 8414-2:2020 test. The test method sets out a clear process of assessing the behaviour of non-load bearing external cladding, rainscreen over cladding, and external wall insulation systems exposed to an external fire.
The fire exposure is designed to be representative of an external fire source or a fully developed (postflashover) fire in a room, venting through an opening such as a window aperture that exposes the cladding to the effects of external flames.
During the test period, in which a timber crib within the concrete panels was set alight, temperatures of greater than 600ºC were recorded mid-way up
the facade. Despite the ferocity of this fire, internal temperatures barely rose above an ambient level and remained cool enough to touch, showing how effectively concrete can act as a heat shield between the fire and anything behind it.
Once the fire was extinguished, the panels exhibited minor cosmetic damage, but were otherwise structurally sound. If the panels were in use in a building, the work needed to get the building in working order again would be minimal.
Combustible materials introduce risks for owners and occupants
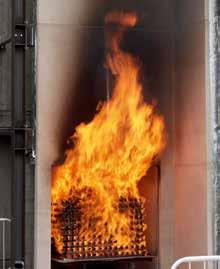
The MPA Precast test shows the advantages of concrete’s relatively low thermal conductivity and inherent non-combustibility which enables it to act as a fire shield not only between adjacent spaces but also to protect itself from fire damage.
In almost all cases concrete does not require any additional fire protection. Conversely, once a structure or cladding element made of combustible materials such as timber becomes involved in a fire, it adds significant fuel. This not only increases the chances of the fire spreading but ultimately raises the potential of the building collapsing. In addition to adding to the fire burden, construction methods such as lightweight Modern Methods of Construction (MMC) solutions create voids formed of combustible materials and the reignition potential of timber structures also creates safety concerns for fire services. In many cases, these factors result in the need for a building to be partly or completely demolished to fully extinguish the fire.
This risk has been recognised by groups including the National Fire Chiefs Council, whose operational guidance highlights some of the hazards present in timber structures – especially those still under construction. The insurance challenges presented by mass timber construction have also been emphasised in a recent report by the RISC Authority. Currently, little emphasis is put on the protection of property itself, with regulations focused only on the safe escape of its occupants. Subsequently, raising questions of whether this is adequate.
5 4
According to research, 60-80% of businesses fail within 18 months of a serious fire. This can cause a greater impact on insurers than the damage to the building itself. The loss of personal possessions in a fire and spending time in temporary accommodation also adds significantly to the trauma, with lasting repercussions on mental health. In short, the long-term cost of losing a building to fire can reach a long way beyond its initial aftermath.
Concrete provides ‘peace of mind’ Concrete is a reliable material and a low-risk solution that can save lives and properties. The MPA Precast fire test can help to give peace of mind to insurers, owners and occupiers of buildings built with concrete facades, a fact which is especially pertinent in the façade sector given the challenges post-Grenfell.
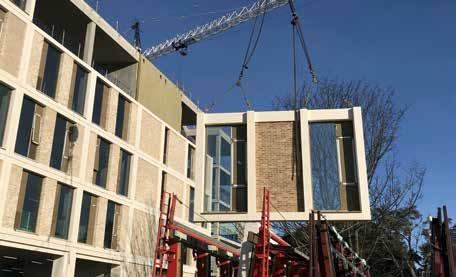
It is incumbent on both the regulators and the construction sector to design and build with the safest possible materials. The answer is obvious, by using non-combustible materials in construction, industry can create safer, more resilient, and longer-life buildings so that if a fire does occur, the damage and impact on lives is limited.
Full details of the BS 8414 test method are available at: www.thefpa.co.uk/fire-testing
For more information and details of the MPA Precast fire test and the non-combustibility of concrete visit: www.thisisukconcrete.co.uk
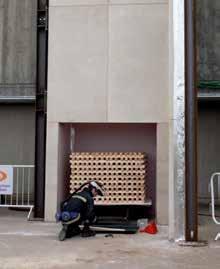
Images:
01-03. Precast concrete is a resilient MMC solution, that is low risk and can help to protect people and property in the event of fire 04-05. The MPA Precast test shows the advantages of concrete’s relatively low thermal conductivity and inherent non-combustibility
SOLVING CARBON QUESTIONS
The way we build our homes and communities is changing. Richard Lankshear, Programme Director at the Future Homes Hub, outlines how the organisation is providing expertise on the major challenges surrounding carbon reduction and new homes.

1 2
In September 2020, the Future Homes Task Force was set up to develop a long-term delivery plan for the sector, in line with the Government’s legally binding net zero and wider environmental targets. These are not targets that can be delivered alone and require a whole industry approach from homebuilders – both large developers and SMEs – designers, the supply chain and beyond. And that is why the Future Homes Hub was founded.
Our mission is to facilitate the collaboration across the housebuilding sector to deliver the climate and environmental targets for new homes as set out in the delivery plan. Through the Hub, the industry is sharing successes and lessons learned, opening up discussion, building expertise and strengthening those areas that are integral to the delivery of the roadmap.
Homes of the future
We know that the home of the future is thermally efficient, with electric services, mechanically ventilated, in places of enhanced biodiversity, built of low carbon materials and more water efficient. We know this because the path is set out through the climate change act, environment act and Task Force for Climate Related Disclosure, affecting the homes we live in, how they are built and the quality of the places around them.
And these changes are coming thick and fast. This year, the Government will begin consultation on the Future Homes Standard and will make biodiversity net gain mandatory. In addition to this, in January, it set out its 25-year environment improvement plan. While this change is significant and rapid, the new homes sector is leading the way with a viable roadmap with tangible objectives being met
as set out in the delivery plan and facilitated through the Hub. While our first year has been impactful – helping the implementation of the 2021 building regulations, producing guidance on the parts L, O and S, a Part O calculator, reports on supply chain and water efficiency – the big changes are yet to come.

Future Homes Standard
The Future Homes Standard will set the regulations to deliver zerocarbon-ready homes from 2025 and government will consult on the new Part L this year.
We brought together over 170 people from over 100 organisations at the end of last year, to inform the consultation by reviewing how to deliver the Standard at scale. We have submitted our report to help refine the 2025 Future Homes Standard (FHS) – carried out under a Terms of Reference set
by the Department for Levelling up Housing and Communities (DLUHC) – that investigates the range of ‘contender specifications’ and how they perform at scale, taking account of all factors such as consumer, design, cost, planning, fabric, ventilation, heating, skills, manufacturing, maintenance and grid infrastructure. Among 26 key recommendations, is the creation of an Implementation Board, bringing together policy makers, developers, the supply chain, skills providers, customer groups, consultants and infrastructure organisations to deliver the Standard. We will support the creation of this board with expert groups drawn from across our membership to help the sector’s transition.
Whole-life carbon
While the FHS addresses operational carbon, the next major challenge is to reduce embodied and, hence whole-life carbon. We began the year with the publication of the sector’s implementation plan for whole life carbon. Here, we found that the new homes sector is performing better than originally thought, but there is clearly a long way to go. The next steps are clear and, again, will need support from multiple parts of the sector. Over the coming months we will work with the supply chain to obtain and
maintain accurate default values of construction products. And developers have agreed to capture more data through voluntary reporting to enable sensible benchmarks that, ultimately, will lead to whole-life carbon targets for the sector.
Biodiversity net gain
For biodiversity net gain (BNG), the 10% uplift becomes mandatory in November 2023, meaning time is tight. Close dialogue is important here to resolve issues at speed, which is why we have a liaison group with key policy makers and agencies to help identify early any challenges and find means of resolving them. In addition, we continue to co-ordinate guidance, and produce our own to answer specific needs, as well as working
GET INVOLVED WITH THE FUTURE HOMES HUB
We welcome all stakeholders to join as members – and for organisations who are members, we encourage colleagues to join our network as it is only through close collaboration that we can all benefit. You can find out more about membership at: www.futurehomes.org.uk
with organisations to help smooth the process of trading BNG units. The new homes sector is coming together to address a myriad of challenges and it is heartening to see the extent of its collaboration. Organisations are sharing their lessons learned and we are compiling a schedule of all tests and trials that are occurring (and have occurred) so that we can all benefit from the lessons that individual organisations are learning as we move to production of zero carbon ready homes.
Our roadmap and delivery plan shows the scale of the task ahead, but the goals are achievable. The network built up through the Hub is delivering tangible change and a change that is creating ever better homes and communities.
Images:
01. Richard Lankshear, Programme Director, Future Homes Hub
02. Embodied & Whole-life Carbon Report published in January 2023
03-05. The pressure is on to deliver zero-carbon ready homes in line with 2030 and 2050 targets
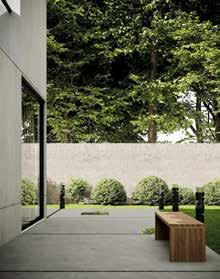
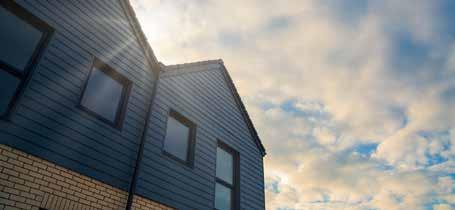
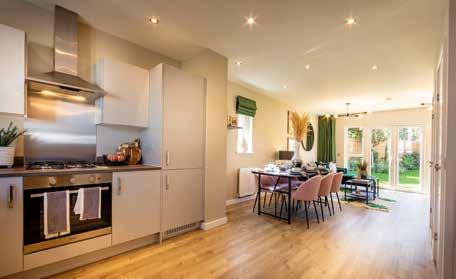
HOUSING
SAFE & SECURE LIVING LIFELINE
The Hill Group, has donated six innovative modular homes to Emmaus Cambridge, a charity offering homes, employment and personal support to a community of formerly homeless people.

The homes will provide safe, secure temporary accommodation for the area’s most vulnerable people to assist the charity’s work and were donated as a part of Hill’s Foundation 200 initiative, a £15million pledge to design and donate 200 modular homes to charities working in homelessness by 2025.
The charity took ownership of the units at a hand-over ceremony at Emmaus in Landbeach, Cambridge on 23 January. The Lord Lieutenant of Cambridgeshire, Mrs Julie Spence OBE, the official county representative for His Majesty The King, joined the president of Emmaus UK, Terry Waite CBE, Selwyn Image, the founder of Emmaus Cambridge and Tom Hill, Managing Director of The Hill Group to officially handover the homes.
"We are delighted to handover these SoloHaus homes to Emmaus and applaud the fantastic work they do supporting the local community here in Cambridge,” said Tom Hill, Managing Director at The Hill Group. “As a major local housebuilder, central to our outlook is to apply our energy and expertise making a positive social impact in the areas in which we work.
We are confident that these innovative new homes will continue to benefit the most vulnerable people in the area for many years to come.”
Designed in collaboration with leading homelessness charities, the homes are purpose-built, fully furnished, and equipped for a single person to move into straight away. The homes, which are built to last for at least 60 years, are highly energy efficient keeping costs low and are designed to Future Homes Standards, exceeding building regulations for energy efficiency and sound insulation.
HM The Lord Lieutenant, of Cambridgeshire, Mrs Julie Spence said: “It is a pleasure to join Emmaus and The Hill Group at this event, which sees the handover of these six impressive modular homes that will provide such great support to the Emmaus community.”
With data indicating that 300,000 households across Britain could be forced into homelessness this year, the support from Hill comes at a critical time. Emmaus will use the six SoloHaus homes to give people in the Cambridge area who have recently experienced homelessness the opportunity to live independently once again. They provide a safe space for residents to rebuild their selfesteem, establish stability, and provide a pathway to moving on from the Emmaus program into more long-term accommodation.
South Cambridgeshire District Council’s Lead Cabinet Member for Housing, Cllr John Batchelor, said: “We’re pleased to have supported Emmaus Cambridge in this initiative. The charity does such incredible work to help those who are experiencing homelessness, and these new homes will provide additional accommodation so that more residents, or Companions as they are known, can have a safe, secure space of their own. The funding that we have provided Emmaus Cambridge within the past year has been used to help employ an additional support worker, who will work with existing companions and the companions living in these new homes. I hope that the two elements combined provides each of them with the time and space to overcome issues which may have contributed to them being homeless, rebuild relationships and potentially turn around their lives.”
Emmaus Cambridge offers its residents a place to call home for as long as they need it. The organisation supports up to 45 people at a time, with the charity offering a stable environment for people to gain new skills and confidence so they can get back on their feet. Residents of Emmaus Cambridge gain work experience in the on-site social enterprises, Joan’s Coffee Shop and the Land beach Second-Hand shop.
Terry Waite CBE, President of Emmaus UK, added: “A safe, comfortable, independent space is vital to helping those who experience homelessness to rebuild their lives and make the transition into more permanent accommodation. The SoloHaus homes will provide us with a great opportunity to support more people who find themselves in this position and will make a real difference in our efforts to tackle homelessness in the Cambridge area.”
For more information visit: www.solohaus.co.uk
Images:
01.
Our OJEU-compliant framework agreements provide public sector organisations with easy access to procure works, products and services for the construction, refurbishment and maintenance of social housing, schools and public buildings.
LHC strives for excellence in the services provided to their clients and aims to deliver the best solution to suit every project’s individual needs.
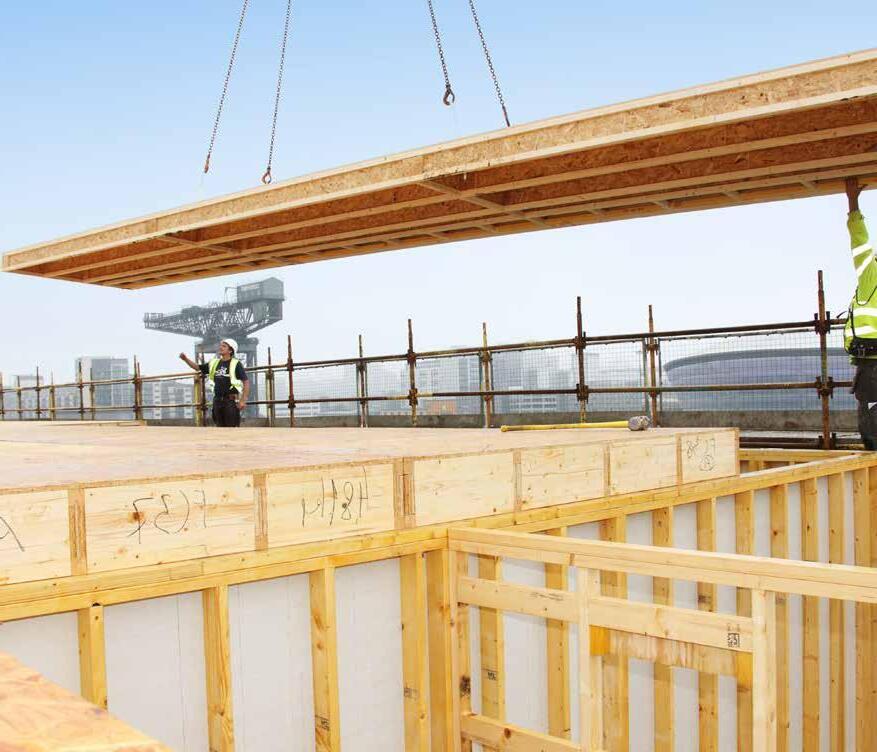
Our dedicated Client Support and Project Support teams are on-hand to assist throughout the life of the project.
For more information on how our frameworks can work for you, get in touch.
THE OFFSITE INDUSTRY UNDER ONE ROOF
65% of 2023 stands have already been reserved or sold. Targeting 4,000 plus visitors, OFFSITE EXPO will be taking place on 19-20 September
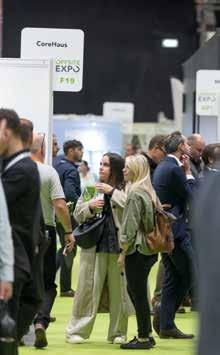
2023 at the Coventry Building Society Arena. Providing the ideal setting for exhibitors, this centrally located venue with ample free parking and a hotel on-site, is within two hours’ drive of 75% of the UK’s population.
Maximise Offsite Exposure
“This will be our third year at OFFSITE EXPO, and we keep coming back as we get such a good response,” said Paul Cashman, BDM from British Offsite. “We find the organisation in terms of logistics and installing our feature builds is absolutely superb. This event provides access to potential clients from all over Europe. Last year we met developers, architects, designers, and housing associations –so it is excellent exposure to the wider offsite world.”
Come September the arena will be totally transformed. Two-storey feature builds and full-size modules will rise above the exhibition floor alongside an array of panelised light steel frame, precast and timber structures together with pod and prefabricated MEP solutions from leading UK and international offsite manufacturers.
Pioneering technology forms a major part of the event. Presenting promotional opportunities to align your latest innovations with a highly targeted and receptive audience, OFFSITE EXPO is also the preferred exhibition platform for those involved in augmented and virtual reality together with the latest digital design and construction technologies.
Offsite Connect
Buyers & Specifiers Forum
Exhibiting companies will have an exclusive opportunity to participate
in the unique Offsite Connect Buyers & Specifiers Forum. Offering major business development prospects, those with the ‘power to procure products and systems’ will gather in the forum and exhibitors will be able to book one-to-one meetings with major contractors, developers, architects, specifiers and purchasing managers.
Leading the Debate
The OFFSITE EXPO Masterclass
Theatres will feature presentations and panel debates focusing on the technologies. In partnership with the Offsite Alliance, the Spotlight on Offsite Theatre is the place to gain valuable insight and get to grips with emerging trends from a host of industry pioneers who are leading the debate in the offsite arena.
Promote Your Presence
Exhibitors are advised to secure stand space early in 2023 to maximise the
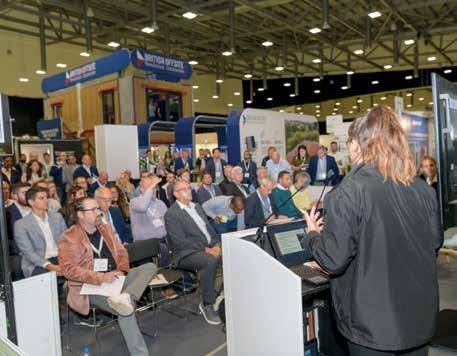
As the largest dedicated exhibitions of its kind, OFFSITE EXPO is leading the way in promoting the technologies that are transforming the built environment – and the show is getting bigger for 2023.
promotional opportunities that the extensive PR and marketing campaign surrounding OFFSITE EXPO brings. Enhance your company profile through pre- and post-event brand placement, advertising, digital marketing, social media, speaker opportunities and much more. Buyers taking part in the Offsite Connect Forum will be announced in July and the diary will be opened the following month to allow exhibitors exclusive access to book meetings with those who have a procurement remit.
Dynamic Offsite Construction Event

OFFSITE EXPO has a range of exhibition and sponsorship packages available. These have been designed to be flexible and offer a wide range of promotional opportunities to suit any marketing aims, resources and budgets.
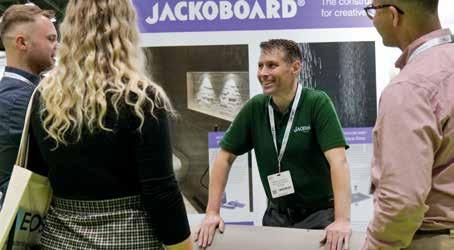
To find out more visit: www.offsite-expo.co.uk/exhibit
To Book Your Exhibition Space Contact: Julie Williams on 01743 290042 or email julie.williams@radar-communications.co.uk
OFFSITE AWARDS 2023 –co-located with OFFSITE EXPO

Taking centre stage on the evening of 19 September 2023 – the Awards will once again be returning alongside OFFSITE EXPO
Creating a dramatic climax to the first day, the awards recognise projects large and small but without doubt, its technical innovation that catches the judge’s eye. Offsite technology is changing the contemporary built environment – driving forward projects that represent outstanding examples of prefabrication and factory-based methods, products, systems and disciplines.
Last year the judges reported record entries and claimed the calibre of submissions revealed how far the industry has moved on in just eight years.
Entry Deadline – Friday 26 May 2023
If you have an outstanding project, product or person that is making transformational change in the way buildings are designed and engineered, now is the time to start planning for the 2023 awards.
Free to enter, there are 25 categories that cover every aspect of the industry from hybrid and modular technology to engineering and installation, ensuring that all phases of the offsite building process is celebrated.
The Offsite Awards submission platform is now open for entries with the final deadline confirmed as Friday 26 May. Finalists will be announced in July 2023. For more information and to enter visit: www.offsiteawards.co.uk
To discuss sponsorship packages and the bespoke opportunities available contact: Julie Williams on 01743 290042 or email: julie.williams@radar-communications.co.uk
Limited Sponsorship Packages

Remaining
The 2023 Offsite Awards sponsorship packages have already been snapped up by savvy companies wanting to gain full exposure in the coming months.
Current sponsors include:


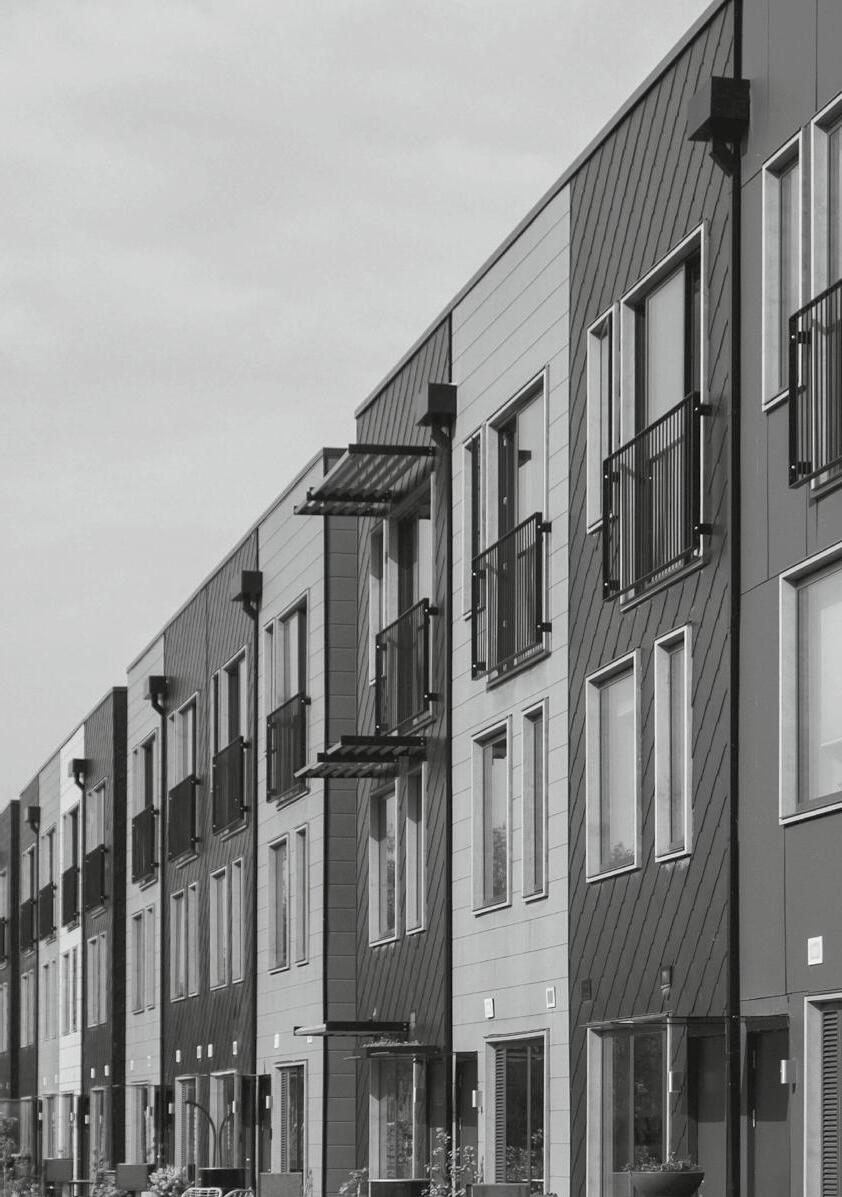
MEET THE JUDGES...
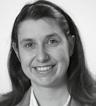
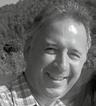
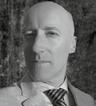

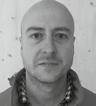
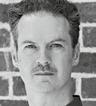
LIMITED SPONSORSHIP PACKAGES REMAINING
The 2023 marketing campaign is ramping up and many of the sponsorship packages have already been snapped up by savvy companies wanting to gain the full exposure in the coming months leading up to the event.
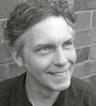

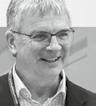
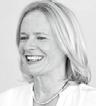
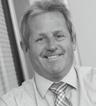
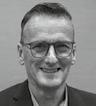
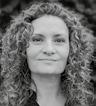
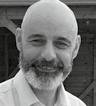
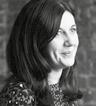
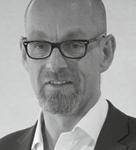
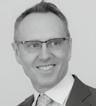
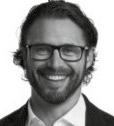
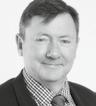

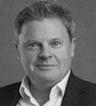
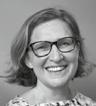
To discuss the sponsorship packages and bespoke advertising opportunities available please contact Julie Williams on 01743 290042 or email julie.williams@radar-communications.co.uk
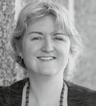
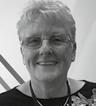
SUSTAINABILITY AT EVERY STAGE
Richard Hipkiss, Development Director of the Modular and Portable Building Association (MPBA) explains why it is imperative to think of the ‘end’ at the initial design stages to enhance a project’s entire sustainability value chain.
The construction sector is facing multiple challenges – some historic such as low productivity, others more recent such as environmental impact and a lack of lifecycle information. In some cases, progress has been slow but now with the advances in digital technology and new construction techniques such as design for deconstruction (DfD), design for reuse (DfR) and the one gaining most traction – design for manufacture and assembly (DfMA), we are finally making great strides in modernising the construction industry.
These three disciplines can be difficult to implement in site-based approaches however the stringent management and digital protocols within volumetric modular design and manufacturing processes create the ideal environment to optimise their use.
The UK government has been promoting volumetric modular construction as a method that can improve productivity, but modular technology can help deliver sustainability gains throughout the entire construction value chain. At present the focus is concentrated
on using volumetric technology to improve resource efficiency upstream at the design, manufacturing, and construction phases. This appears to be detached from the need to promote resource efficiency and productivity at the stages occurring downstream – disassembly and endof-life management. Such divergence could hamper the construction industry’s efforts to reduce its long term environmental and economic impacts and points to the need of an integrated, holistic approach to improving the sustainability value chain as an end-to-end concept.
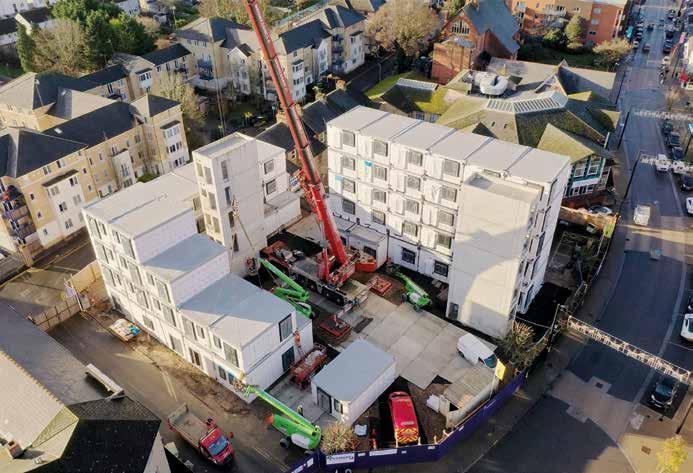
MPBA
What are the benefits throughout the entire construction value chain?
Volumetric modular construction does indeed offer multiple benefits upstream, including ease of constructability, increasing quality and reducing time of construction as well as the capacity to cope with skilled labour shortages and creating much safer working environments. Most importantly, it can substantially reduce construction waste generated onsite via promoting resource efficiency at the manufacture and installation stages. But the efficacy of this construction method to yield benefits downstream at the end-of-life has received comparatively little attention.
Advances made in the UK towards improving productivity in the construction sector via the application of volumetric modular technology and digitalisation are well documented, however as the trade body for the sector, the MPBA also needs to shine a light on the opportunity to improve sustainability performance throughout the value chain from concept to end-of life.
DfMA, DfD and DfR protocols are an exemplary way of connecting upstream and downstream construction stages and can be used to actively apply sustainability principles. The digitally enabled volumetric construction model has the potential to capture and record this valuable lifecycle data. The rise of digital technology offers an opportunity to bring business transformation in the construction sector and promote a new way of doing things; effectively enabling transformative change which will enhance the sustainability credentials of volumetric manufactured buildings.
MPBA
2
Implementing smart modular regimes to mitigate the impact of climate change
As the construction sector develops and adapts to meet changing government strategies to enhance sustainability credentials, I firmly believe the upward trajectory of volumetric modular buildings will
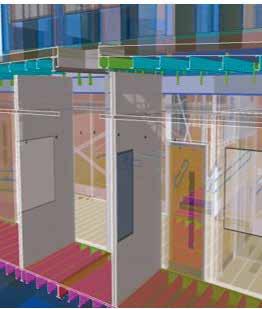
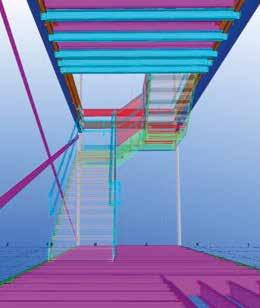

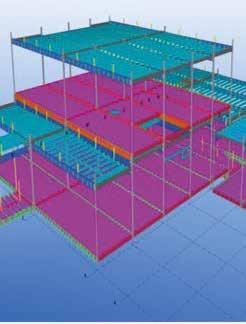
The MPBA plays a key role in supporting all sections of the industry. Leading best practice principles and specialist training schemes, the association is represented on many committees for the benefit of members. Most importantly, the MPBA ensure evolving government policies and decisions are not made on behalf of the construction industry without due consideration for the impact they may have on the volumetric modular sector. Founded in 1938, with an in-depth understanding of the industry, the MPBA has represented this advanced and highly innovative sector for over 80 years.
For more information visit: www.mpba.biz
continue and we need to act now to help mitigate the impact of climate change.
A smart volumetric modular construction regime can operationalise the collection and storage of components' lifecycle information, and help the sector build the capabilities needed to support the maintenance, recovery and reuse of modular components, and reduction of waste. For this to take precedence it is imperative to think of the ‘end’ right at the beginning of the design stage and foster improved collaboration between all construction partners involved in the supply chain.
Images:
01. Desborough Road. Premier Modular generates zero waste in their manufacturing processes. Courtesy Premier Modular 02. Digital technologies can operationalise the collection and storage of lifecycle information. Courtesy McAvoy Group
DIGITAL DESIGN BRINGING CO-ORDINATION & ACCURACY TO OFFSITE
One company using Trimble’s co-ordinated and constructible Tekla software and leading the way in the offsite sector with its digital adoption and full RIBA workflow approach is Design4Structures.

Offsite and modular construction is a fast-growing market, with digitisation and innovation at the core of its success. Design4Structures is an innovative structural engineering and design company, with delivery spanning across a range of sectors and has been operating within the offsite space for over six years, the company has worked on a range of panelised, SFS and volumetric projects – from student accommodation, hotels and hospitals, to high and low-rise residential.
Within offsite construction, Design4Structures has adopted a slightly different approach. With both an engineering and construction modelling division, Design4Structures commonly delivers the full RIBA workflow on its offsite and modular projects, taking responsibility from the design and engineering stages right through to fabrication.
Speaking about its approach, CEO, Daniel Leech, says: “All too often, we found ourselves becoming frustrated with the level of information that we were receiving from our supply chain partners – which is why we chose to bring together the structural engineering and construction modelling arms of the business. We’re proud to deliver RIBA Stages 0 (Strategic Design) to 5 (Manufacturing and Construction) under the one roof and this method has been met with a great response from our customers.
“Not only does this give us a greater degree of control but it also offers us (and our client) the assurances that the project data and information is up-todate and correct. In many ways, there is a clear need for this style of working to be adopted more within both the offsite sector and wider construction industry. We all need to be taking collective responsibility and in-doing so essentially de-risking a project as
far as possible, moving away from the ‘blame culture’ that can often be present.”
A key part of this innovative service offering is digital technology, in particular Trimble’s range of Tekla constructible modelling software, including Tekla Structures, Tekla Structural Designer and Tekla Tedds.
John Breeze, Offsite Operations Manager at Design4Structures explains: “Everything that we deliver to a manufacture-level of detail is co-ordinated and detailed in Tekla. While there’s many benefits of having a digitised and 3D-enabled workflow, perhaps the main value of BIM is the enhanced coordination and accuracy of what we can deliver. Co-ordination is key on any construction project but especially so with offsite, with a number of supply chain partners and factors to bring together successfully, including MEP services and structural openings.
“It is this digital co-ordination, combined with the assurances of accuracy provided by BIM and the detailed 3D environment, that can help to protect against change management and design issues further down the line. With Tekla, thanks to the customisability of the software, we’re also able to mould it to suit our needs as a company and those of our customers too. Through the creation of custom components and macro development, we can automate otherwise repetitive tasks and generally improve our productivity levels across the board.
“Of course, that said there are still challenges within the construction industry that can act as roadblocks to this efficient and digested workflow being fully adopted and its value truly maximised. For example, there are consultants that still work in 2D, which can present an issue when it comes to IFC exchange and translating this information into the 3D environment. It can defeat the object of the productivity enhancements we’re trying to achieve in Tekla. Ultimately, the widespread adoption of BIM and 3D is needed if the whole industry is to benefit. How can we look to the future when we haven’t thoroughly got the basics in order?
“The value of Trimble Connect really comes to life on the larger and more complex projects, especially the to-do list function. This is hugely valuable for us, enabling a more productive and streamlined way of working, essentially replacing physical RFIs and TQs. Instead, users can easily raise an item on the to-do list, which links directly back to the 3D model; everyone can then review and discuss
the highlighted query and work to rectify it.”
An example of this co-ordinated workflow in action is Minden Court in Doncaster, a residential development for the over 55s, consisting of a three-story apartment block and a number of individual bungalows. Design4Structures completed the structural design of the modules and detailed 3D Tekla models, fully coordinated with appointed Brewster Bye Architects and the MEP Consultant.
With the engineering and construction modelling teams working together on the project for client M-AR, Tekla Structures played an important role in creating efficiencies in the project delivery, including overcoming issues related to connection design. The 3D visualisation offered by Tekla enabled Design4Structures to resolve these challenges, enhanced even more so through the collective review and input from both teams.
Tekla software’s cloning capabilities also enabled the effective delivery of standardised module design. Naturally, as a modular project there was an element of heavy repetition, however, the use of Tekla helped to speed up the design process, from modelling to drawing creation.
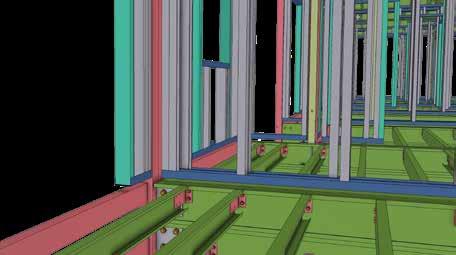
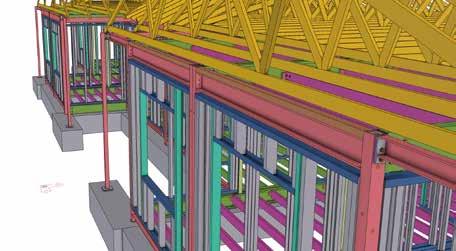
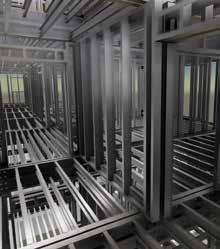
“In total, over 60 general arrangements drawings and 3,000 fabrication drawings were produced for the modular frames and SFS infill panels,” says John Breeze. “Tekla’s custom component creation to suit connection design, plus the automatic lists feature for weights, materials and assemblies, all contributed to achieving results for our client that enabled a seamless manufacture and installation.”
For more information visit: www.tekla.com/uk
www.design4structures.com
Images: 01-04. Minden Court, Doncaster where digital software helped deliver the effective delivery of standardised module design
ADOPTING A GREENER PATTERN
Collaborative leadership? It’s what a sustainable future in the built environment sector requires. Dr Tim Forman, from the Cambridge Institute for Sustainability Leadership, at the University of Cambridge explains more.
1 2
The built environment sector is experiencing a seismic shift – this may be obvious to some but not yet apparent to others. For decades it has ranked among the slowest sectors to adapt and innovate, and it has remained a principal driver of carbon emissions, and therefore climate change, countless forms of pollution, depletion of natural capital, and labour and social concerns the world over. It now faces a new reality.
In this new reality, changes in consumer demand, finance, regulations, government policy, and in society’s expectations of corporate responsibility, mean the viability of business-as-usual practices is waning. Unchecked climate and nature emergencies are bringing larger and more frequent weather extremes and calamitous events. Built environments need to be made more resilient if they are to be sustainable – financially, ecologically, and physically.
Our patterns of working and living are changing, and major technological and social shifts are emerging at increasing rates. As our demands of built environments evolve, new realities are shaping not just how people use built assets and land, interact within communities and spaces, and how we transport ourselves and our goods, but
also how we build, operate, and value assets, exchange information, and increasingly, define the roles of built environment professionals. With world governments and industry setting incredibly ambitious targets for energy, carbon, waste, and natural capital, the sector’s path to a sustainable future is virtually cliff-like. Unsurprisingly, demand is soaring for those who can do things differently – whether it be planning, designing, constructing, operating, or critically, adapting, reusing, retrofitting and conserving built assets. Change is being led across disciplines, at all levels, and noticeably, by the scaling of innovations achieved through collaboration.
The Cambridge Institute for Sustainability Leadership’s (CISL) engagement with this central global challenge extends from its educational and programme activity to its recent refurbishment and retrofit of a 100-year-old building in Cambridge, renamed Entopia. Originally built to house a telephone exchange, the building now provides newly refurbished flexible office space for the Institute’s 140 staff and Canopy, a dynamic network of start-ups and innovators. This was delivered through a deep green refurbishment and retrofit to optimise energy efficiency and indoor environmental quality
and address myriad sustainability targets. The project employed circular design and used bio-based, reused, and recycled materials where possible, followed responsible practices, and produced a fraction of the embodied carbon associated with new construction (and many refurbishments). The building has received the EnerPHit standard and aims to achieve WELL Gold and BREAAM Outstanding certification.
These successes were borne from collaboration and ‘shared leadership’ in pursuing demanding targets. This empowering and collaborative approach to sustainability also underpins CISL’s part-time accredited and non-accredited education programmes for built environment professionals. The programmes, which deepen individuals’ understandings and develop competencies in sustainability practice, include a two-year Master's, a 10-month Postgraduate Certificate, and an eightweek online certificate course.
Meaningful, timely change and scaling of innovation are enormous challenges only surmountable when professionals develop and apply new knowledge and expertise through effective collaboration. The built environment sector’s future is here now.
For more information visit:
www.cisl.cam.ac.uk/about/entopia-building
Images: 01-02. Entopia – originally built to house a telephone exchange – has benefited from a refurbishment and retrofit to optimise energy efficiency and indoor environmental quality, employing circular design and using bio-based, reused, and recycled materials where possible
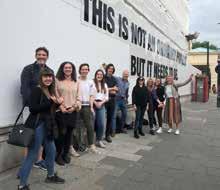
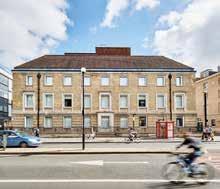
The University of Cambridge Institute for Sustainability Leadership offers part-time courses in Sustainability Leadership for the Built Environment that develop the knowledge, understanding and leadership skills needed to drive meaningful change in professional practice.

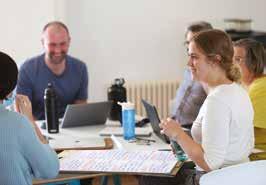
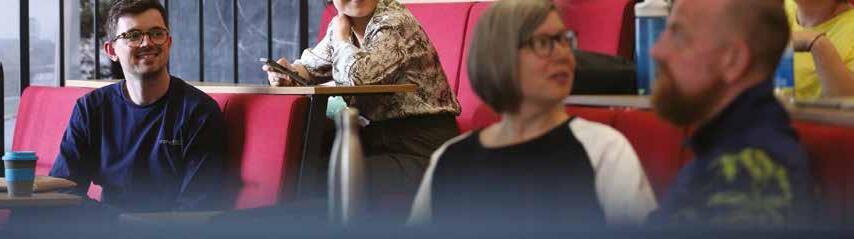
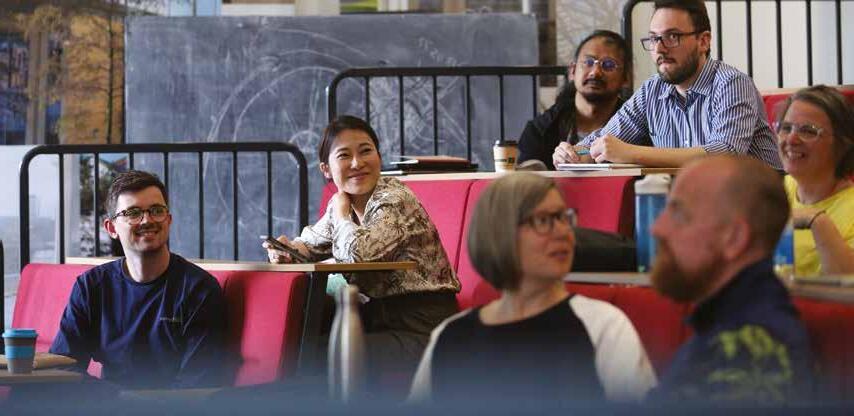
Learn global best practices through project-based learning. Embark on a highly interactive and collaborative learning experience. Delivering exceptional future-fit built environment projects requires skill and expert coordination of individuals toward shared vision and purpose. Our programmes are highly interactive and designed to foster reflection and debate.
Through the programmes, students learn about emerging trends, opportunities, and challenges in the built environment sector and develop deeper understandings of sustainability and resilience in professional practice, including health and wellbeing, retrofit and reuse, energy and carbon, conservation and heritage, stakeholder engagement, and cultural, political and regulatory contexts.
MATERIAL COMBINATION
James Mead, Projects Director at Saint-Gobain Weber, and Mike Doolan, Sales and Partnerships Manager at LoCal Homes, share their experience of combining traditional building products with offsite manufacturing.
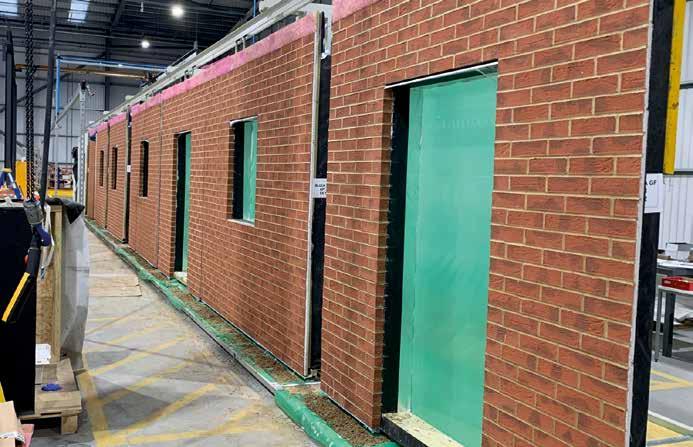
In 2019, the government set a target of 300,000 new homes a year by the mid-2020s. This figure was originally unveiled in 2017 by then Chancellor Philip Hammond as the number of new homes needed to make “inroads on the affordability of housing.”
The closest we have been to achieving this target was in 2019-20 with 243,770 net additional dwellings. With housing output continuing to fall short, it has been debated over recent years whether increasing the use of modern methods of construction (MMC) is the quickest way to reduce the deficit. The government seems to be supportive of this approach and is encouraging
the use of MMC via initiatives like the Affordable Homes Programme (AHP) from Homes England which requires strategic partners to deliver 25% of homes using MMC if they’d like to access funding. Under the AHP, homes will only be considered as “being delivered using MMC” if they have a pre-manufactured value (PMV) score of 55% or more.
In 2020, real estate advisor Savills predicted that the proportion of homes built using MMC over the next 10 years would rise from around 8% to closer to 20%. “Awareness of the possibilities that offsite construction offers is definitely increasing,” says
Mike. “The drive from government, as well as the need for housing associations to deliver new homes that meet the new Part L (conservation of fuel and power) Part F (ventilation) and Part O (overheating) requirements of the Building Regulations in England, are providing a good platform to showcase the benefits of using MMC. We’ve also found that there is a growing appetite for offsite timber frame with factory pre-fitted external finishes. An offsite panelised timber frame is a viable alternative to full modular or volumetric systems due to its lean and flexible production processes.”
Traditional facades, modern construction
Although clients are more open to building this way, many still want newbuild homes to have a traditional appearance. Around 70% of the UK’s new homes are built with a brick façade, and therefore, James argues, more traditional products still have a large role to play. “Category 6 of the MMC definition framework includes traditional single building products, that are manufactured in large format, pre-cut configurations or with easy jointing features to reduce extent of site labour required to install,” explains James.
“As we transition from traditional building methods to offsite manufacturing, products within this category are set to play a huge part in bridging the gap. Builds will become quicker thanks to the ease and speed of installation, and there will be, on the whole, no requirement to retrain, as existing labour is sufficient – it simply needs redeploying.” Weber developed its weberwall brick – a fast-fix, lightweight brick system – as a solution for offsite manufacturers who wanted to give their homes a brick finish without having to manually apply brick slips.
“When we were looking for a brick slip system to use on our closed panel timber frame system, we found lots of them required additional labour and works on-site to achieve a similar appearance,” says Mike. “This impacts both the assured quality of the build and speed of programme. Introducing site application also reduces your build’s percentage of PMV which goes against the whole principle of offsite construction. We also needed something that wouldn’t add lots of additional weight to the panels. Using a brick effect finish like this can also help us meet the requirements for colour and brick texture as required by planners.”
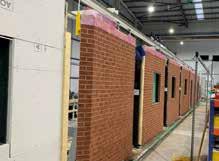

“The weberwall brick suited LoCal Homes’ system because it can be fixed more than three-times faster than traditional brick slips and one sheet, which contains 20 bricks, weighs the same as one brick so only adds 13kg per metre squared to the timber frame panel,” adds James. A lighter overall wall structure means that the build can become more efficient in other ways such as foundation design. Smaller foundations means that less concrete is required.
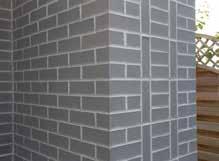
Benefits of factory application of final facades Weber worked with LoCal Homes to develop an efficient application process with minimal waste. “We’ve designed a precise setting out method which enables projects to be priced accurately with very little wastage,” says James. “Lasers are used in LoCal Home’s factory to ensure accuracy when making any cuts and we’ve also optimised the adhesive application to make it even faster.
For LoCal Homes, another benefit of keeping all elements of the build within the factory includes being able to buy products in bulk and store them in secure, weathertight facilities which helps to maintain a steady flow of products. “There are two huge benefits of working this way – noticeable time improvements on project delivery and the ability to design and build more sustainable homes in line with the latest standards,” says Mike. “There is no ‘down time’ as the works aren’t weather dependent. And that’s not just bad weather - during this summer’s heatwave lots of building sites had to
pause works further highlighting the advantages of manufacturing offsite.
“We are currently producing around 1,000 units a year and are expecting an increase in social housing orders because closed panel timber building is extremely efficient, helping all stakeholders towards net zero targets and will also help to ensure adherence to the uplift in Part L that came into place on 15 June, as they can be constructed with this in mind.” LoCal Homes is currently using weberwall brick at a development in Daventry where it is building two three-storey blocks to create 22 apartments, and in Kirton, Lincolnshire, where it has been used on two bungalows and four houses.
For more information visit: www.uk.weber
www.localhomes.co.uk
Images:
01-04. Keeping all elements of the build within the factory includes being able to buy products in bulk and store them in secure, weathertight facilities
SHAPING UP WITH STEEL
Focus on Framing, hosted by the Light Steel Frame Association, returns to The Building Centre in London on Tuesday 25 April, for what promises to be one of the cornerstone events of the offsite calendar.
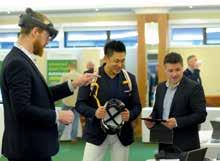
FOCUS ON FRAMING
The event will see Light Steel Framing System (LSFS) experts and leading professionals coming together to offer learning, networking, and development opportunities. The only specialist event of its kind, Focus on Framing 2023, will host a packed schedule with an exciting line-up of special guest speakers and presentations. Delegates will be given the chance to gain a greater understanding of best practises and delivery through the informative seminar, as well as visit the packed exhibition to explore the latest innovations and products shaping the market.
Who is speaking at Focus on Framing 2023?
Focus on Framing Seminar Chair: Mike Fairey
Mike Fairey is the Chairman of the Light Steel Framing Association and will be opening this year’s conference. Mike brings to the event an unprecedented wealth of experience, knowledge, and engineering expertise in the light steel framing sector.

Andrew Way, Associate Director of the Steel Construction Institute
Simon Lovering, Business Development Manager of Fusion Steel Framing
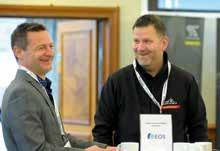
Nik Teagle, Technical Director of Frameclad
Craig Johnson, Business Development Manager, Detailing & Manufacturing of Trimble
Jaime Livingston, Associate Director of Corstophine & Wright
Focus
on Framing Case Study Highlights
Holburne Park
Presented by Simon Lovering of Fusion Steel Framing, this case study will give guests an insight into the delivery of Fusion’s short-listed entry into the 2022 Best Use of Steel category at the 2022 Offsite Awards. Holburne Park is a stunning development situated in the World Heritage city of Bath. Fusion manufactured the light steel framing systems for the Georgianstyle terraces, villas, and apartment buildings, working alongside lead construction contractor, Bect. Simon will be going into detail about the processes and approaches taken by Fusion, in successfully delivering cold-rolled light steel frame systems for this ambitious £26million high-end residential project.
Becketwell, Derby – One Year On
Jaime Livingston, Associate Director at Corstophine Wright will be offering valuable insight into the developments of their Becketwell project’s phases one and two. The Becketwell project will see the construction of 259 Buildto-Rent (BTR) apartments, funded and operated by leaders in the UK BTR sector, Grainger. Completion of the first phase of the build is anticipated in the spring of this year. This will be followed by phase two, involving the construction of an exciting 3,500-capacity performance venue. World-leading operator ASM Global will manage the venue following the handover, scheduled for Spring 2024. In this detailed case study, Jaime will take delegates through each phase, highlighting the processes and practises required to deliver this complex project.
You can find out more about this year’s agenda and developments surrounding the event at: www.focusonframing.co.uk
FOCUS ON FRAMING SEMINAR
Displaying ground breaking innovation through light steel framing solutions.
The use of Light Steel Frame is fundamental as a construction material within a wide range of building types and applications in the offsite sector.
FOCUS ON FRAMING provides the opportunity to hear insightful case studies from those who are designing and developing the industry’s ground-breaking projects. The seminar will be complimented by an exhibition of leading businesses across the sector, and provide networking prospects with those who are shaping the future of the Light Steel Frame industry.
25.04.23
THE BUILDING CENTRE
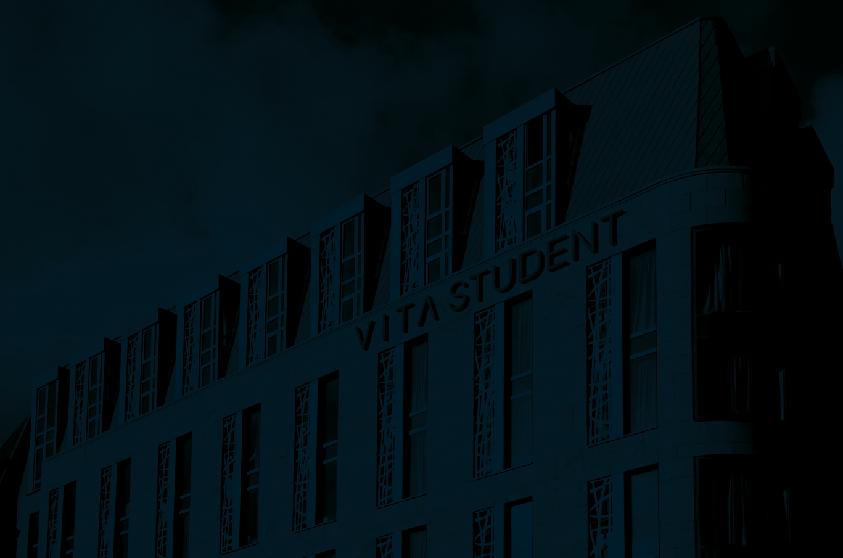
LONDON
FOCUS ON FRAMING provides positive return-on-investment and is one of the only events of its kind.
• Strengthen your brand positioning
• Generate sales leads
• Build relationships with prospects
• Launch new products
• Survey attendees about new product ideas
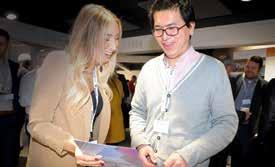
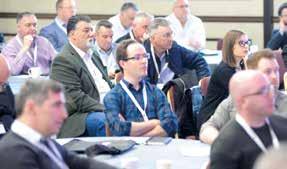
• Research competitors’ products and messaging
• Keep up on industry trends
• Meet with key clients
BOOK NOW
Tickets to FOCUS ON FRAMING cost £125 plus VAT or £95 plus VAT for LSFA members, which includes entry into the seminar, lunch and refreshments throughout.
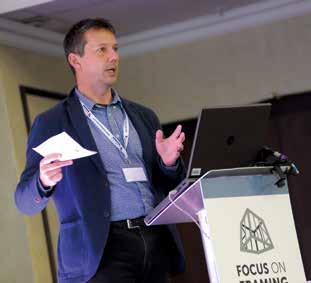
RADICAL CONSTRUCTION CHANGE
our in-house design division, with Merit’s innovative and technologybased approach from concept design to commissioning and validation, produced a unique and successful recipe for accelerating the construction programme of what is very a complicated project.”
Merit has completed the UK’s first CAR-T cell manufacturing facility for Autolus Therapeutics in record time using its offsite POD production approach.
Merit have developed a proprietary DfM&A Platform design through 5D BIM and vertically integrated offsite manufacturing to deliver construction through an entirely new ‘clean sheet of paper’ approach focused on productivity, sustainability, and successful repeatable project outcomes.
The offsite approach has been instrumental in driving significant construction productivity growth to conclude the phase one completion of the new facility in Stevenage. In line with the urgent need to bring life-saving advanced therapies to the UK, Merit delivered the milestone in 17 months, which is three years faster than the biotech industry standard of approximately five years. This included planning and design and only 12 months spent on-site.
Merit was appointed as the main contractor to deliver the new four-storey 7,500sq m facility for Autolus Therapeutics, a clinicalstage biopharmaceutical company developing next-generation programmed T cell therapies for cancer treatments. The new facility is part of a larger plan to create a life sciences district in Stevenage by developers, Reef Group and UBS Asset Management, and will assist in the growth of the cell and gene cluster in the town centre, which is currently the third largest in the world.
The phase one completion of the facility saw the handover of Grade C clean rooms to Autolus, enabling them to transition seamlessly into their next phase of growth. Once completed, the facility is expected to process 2,000 treatments annually and create 400 new jobs in Stevenage. Tony Wells, CEO of Merit: “This project is of critical importance to the UK biotech industry and therefore we are very proud to have been able to deploy our unique offsite construction methods to deliver this vital facility in record time. Productivity is an issue in traditional construction methods, but our approach means projects are delivered more quickly and also crucially more sustainably.”
The £66million project showcases Merit’s industry leading position as a disruptor of construction approaches with the objective to bring real improvement in terms of productivity. The design of the new facility utilises Merit’s FLEXI POD®, a hybrid solution which is particularly suitable for complex high technology facilities, comprising aspects of modern methods of construction for the shell and core, and an offsite manufactured fit out which is facilitated through a PreAssembled Module (PAM) and POD strategy.
Merit’s innovative product-based approach to deliver this pioneering facility enabled three-quarters of the construction work to take place offsite, with 300 PAMs and 15 UltraPODs totalling 900 tons manufactured in Merit’s 270,000sq ft factory in Northumberland and shipped to Stevenage for installation by its specialist team. Piers Slater, Chief Executive of Reef Group: “Combining the expertise and capability of UrbanR,
The result is a radical step change in construction productivity, sustainability and time to use, reducing carbon emissions while accelerating the delivery programme of the whole project to 22 months – a significant time saving achievement over the five-year average traditional build time for similar facilities in the sector. In addition, it offers Autolus reduced capital and revenue costs, as well as a substantial reduction of external professional consultant fees.
Olivia Drew, Portfolio Manager of UBS UK Life Sciences: “As momentum behind the life sciences sector continues to grow, we’re delighted to have partnered with Merit on this next generation facility in Stevenage. Merit’s approach to quality, speed, sustainability and resilience has enabled them to deliver on all the key requirements for this project, and we look forward to continued collaboration across our platform.”
Merit’s commitment to driving measurable improvement for sustainability means the facility has been designed to BREEAM Excellent rating, with scope 1 net zero carbon enabled using heat source pumps and heat recovery systems and 5D BIM technology to reduce waste. Merit is a trusted and well-respected expert in the construction of biopharma facilities, with experience in delivering an impressive portfolio of highcontainment facilities, including the new RNA Centre of Excellence for the Centre for Process Innovation (CPI), Abingdon Health’s lateral flow manufacturing site, and Piramal’s ADC manufacturing facility expansion.
For more information visit: www.merit.co.uk
Images: 01-02. Offsite delivery is providing the healthcare sector with fast and efficient cutting edge facilities
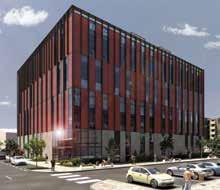
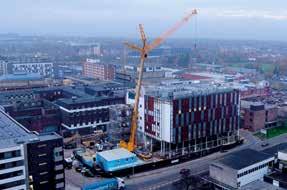
Packaged Plant Solutions.
Armstrong Packaged Plant solutions provide savings through the project life-cycle. Shortened project schedules, procurement savings, space savings, labour savings, long term savings from design quality and professional assembly, and perhaps most importantly, energy savings and carbon footprint reduction through improved operating efficiency.
Packaged plantroom solutions from Armstrong leverage our industry-leading Design Envelope technology, delivering the best possible operating efficiency across a wide range of duty points.
Active Performance Management.
Our innovative pump manager Active Performance Manager software also provides customers with real-time connected intelligence to track and maintain optimised performance, and better manage maintenance and service.
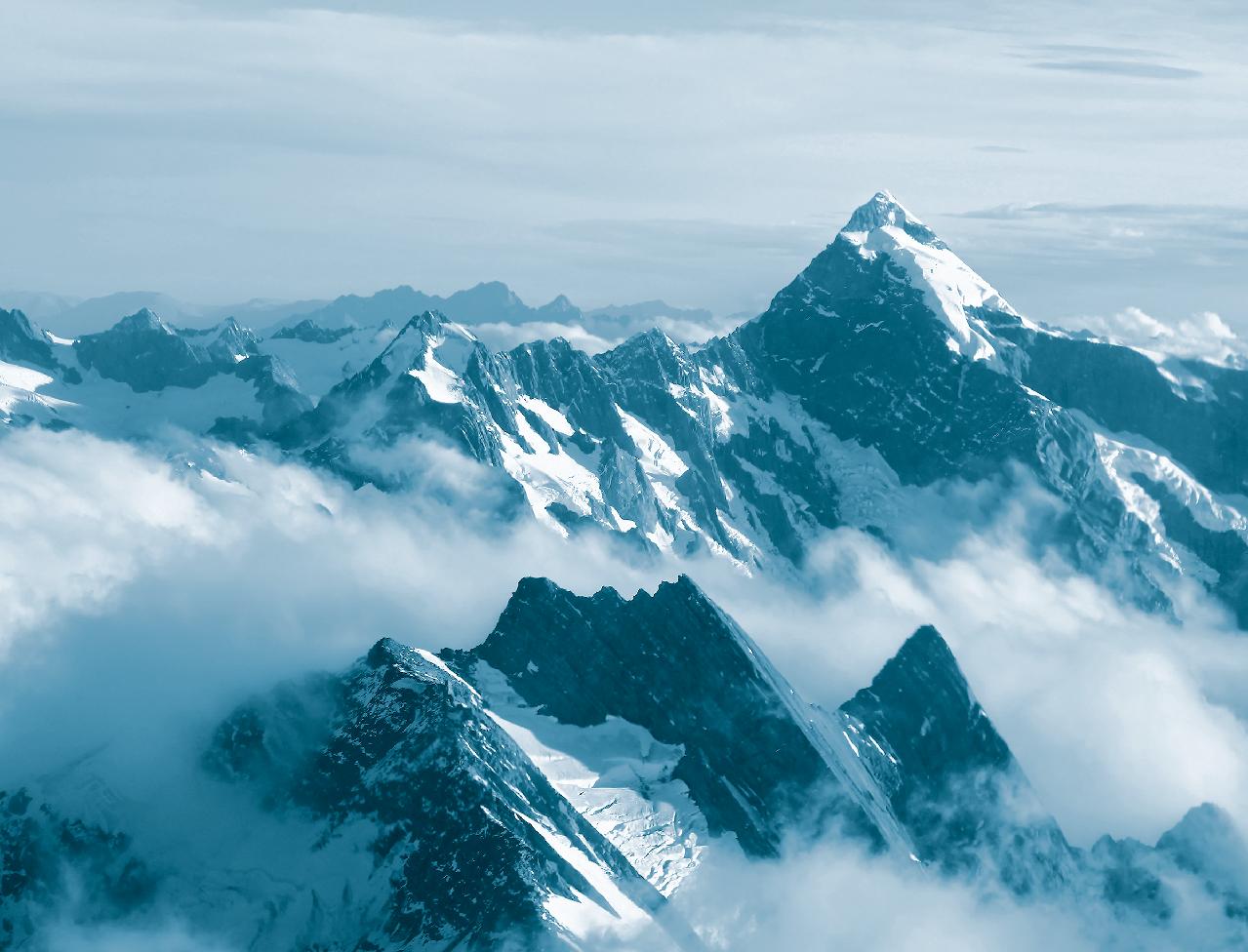
save up to hvac energy cost
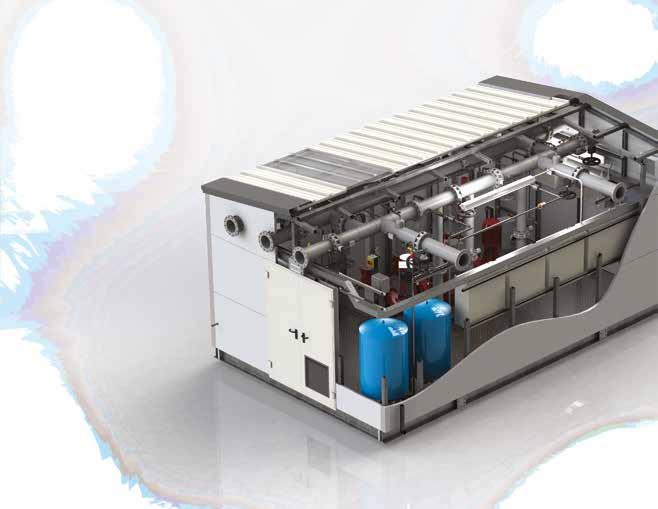
STEEL BUILDING SAFER BY DESIGN
After receiving Royal Assent in April 2022, the Building Safety Act covers a raft of changes for housebuilders and developers to integrate into project development. EOS explains how their systems respond to the new regulations.
It is claimed to be the biggest change in building safety for over 40 years. Among the many changes are a new system of accountability for safety in projects, a construction products regulator, and a refreshed regulatory framework.
The overhaul of regulations will require building owners to demonstrate safety at each of three new ‘gateways’ for planning/design, construction and occupation. Compliance will be monitored by the newly established
Building Safety Regulator, with significant powers to demand documents and stop works, and a new National Regulator for Construction Products, with power to remove dangerous products from the market.
Research and perspective interviews with sector experts have equipped EOS and Etex Group partners with a deep understanding of the challenges faced by housing specifiers with a lack of test data seen as a major concern in achieving building safety.
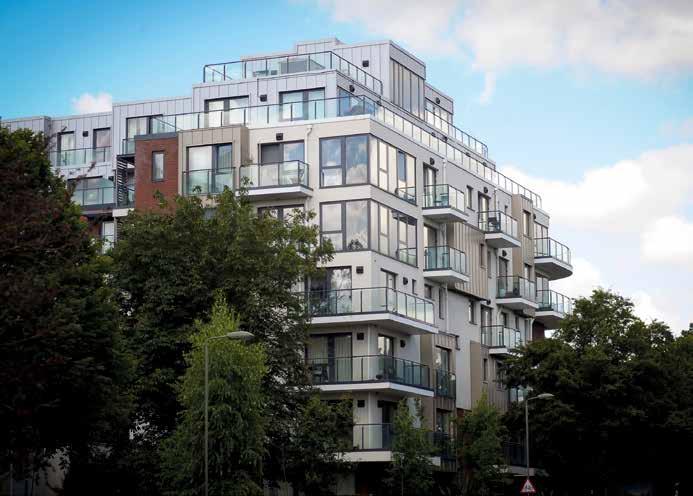
Ensuring robust and predictable performance
The light steel systems designed and manufactured by EOS fully comply with the requirements of Building Regulations and leading warranty providers. Steel is non-combustible and does not add to the fire load of a building therefore the risk of fire during construction and when in use is reduced. According to a poll of the industry undertaken by the NHBC last year, fewer than three in 10 housebuilders expect to use timber frames.
The performances of EOS loadbearing light steel systems are determined as a result of testing to BS EN 1365-1 for walls and BS EN 1365-2 for floors (and to BS EN 1364-1 for non-loadbearing walls). Systems are tested and evaluated to provide for a safe ‘worst case’ performance. Loads applied during testing are selected to simulate representative stresses in accordance with the test standard.
From early design and engineering advice to simplifying specification and procurement, products, processes and their whole business philosophy show that as a manufacturer, EOS take their responsibilities extremely seriously. At the heart of this is rigorous testing and a systems approach to their light steel solutions.
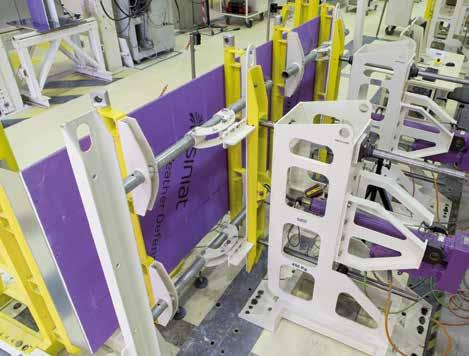
Etex Group have three Innovation and Technology Centres where the company has its own fire, acoustic, mechanical, structural and thermal testing facilities, equipment and laboratories. Annually they conduct over 500 tests in Europe alone. Etex also fully support and endorse third party certification such as BBA, BRE Global, Certifire and EOS has also recently gained EPD and BOPAS Accreditation. Etex work closely with certification bodies to jointly develop and design technical solutions.
Mitigating risks
Current regulations typically deal with individual products and how they
perform in laboratory tests. However, EOS believe material providers should have full-scale testing regimes that study the performance of products working together to see how they interact in ‘real’ circumstances, like under fire conditions or when exposed to wind and rain.
When walling and flooring systems are built entirely with Etex components and materials in line with their latest standards, after a validation process— Etex award Pre-Assembled Frames (PAF), Thrubuild® and Thruwall® systems with a 30-year manufacturer’s warranty. This approach mitigates risk because these integrated solutions have been tested as complete systems and assessed for compliance with the latest regulations and standards, to ensure reliable performance.
Ground-breaking reforms
The Building Safety Act makes groundbreaking reforms to give residents and homeowners more rights, powers, and protections – so homes across the country are safer. Many of the detailed provisions in the Act will be implemented over the next two years through a programme of secondary legislation.
EOS are continually looking at ways to make the building process not only inherently safer but also to offer performance assurances to architects, housebuilders and specifiers to ensure they can provide sufficient
levels of protection to occupants. EOS have developed an award-winning range of unitised loadbearing and non-loadbearing light steel framing systems. By working closely with developers, EOS are now able to provide real scalable light steel frame residential solutions – delivering precision-engineered homes that meet building safety regulations that can be produced at scale better than, faster than and more cost-efficiently than other market offerings.
Images:
01. The Building Safety Act provides residents with more rights, powers and protection
02. Effective testing regimes ensure building safety performance
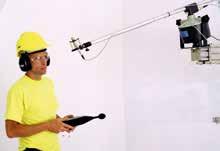

EOS are committed to technical competence and as part of Etex, have some of the best fire protection experts in the UK on their team. Technical support is there for specifiers throughout the lifecycle of the project, from concept to completion – in person, online, or by phone.
For more information visit: www.eosframing.co.uk
OPPORTUNITIES FOR LSF EXPANSION
With UK public spending reaching over £300billion per year, the Procurement Bill aims to simplify and transform current laws surrounding procurement processes applicable to publicly funded works. Mike Fairey, Chairman of the Light Steel Frame Association (LSFA) and Managing Director of Fusion Light Steel Framing, views the upcoming changes as a golden opportunity to highlight the benefits of complete light steel framing systems from a procurement perspective.
“The proposed UK Procurement Bill simplifies a currently over-complex and time-consuming process,” says Mike. “Historically procurement has been a case of bringing together various construction elements from different sources. Now many LSFA members have transitioned from manufacturers of components to innovators in complete and compliant ‘through the wall’ panelised light steel systems that offer a consolidated approach to meet the requirements outlined in the proposed Bill.”
Following the UK's exit from the European Union, the new bill will replace 350 different regulations. Approximately one-third of current public sector spending goes on
procurement. With a focus on driving innovation and creating a more open, transparent system, the Bill will ensure UK needs are met while complying with international obligations.
One particular benefit will be an increased focus on ‘Levelling Up’. The Procurement Bill will set out requirements for buyers to consider areas such as supplier resilience, technical and system innovation, and the creation of new jobs and skillsets. The changes will also include the creation of a digital platform on which suppliers can register details to use for bids on multiple projects.
The new centralised, web-based platform will allow businesses to find out about upcoming work earlier, detailing available projects in their regions. The platform aims to speed up and streamline previous procedures, which would have seen businesses forced to register details across multiple digital platforms for different works and types of procurement.
By increasing the requirement for more sustainable, efficient, and highperformance systems, the changes will ideally position light steel frame as the system of choice for those looking to meet the widened scope

of procurement requirements set out by the Bill. There will also be greater transparency and a supplier-barring system based on performance. The aim of this would be to block suppliers with a record of non-compliance from securing further work.

It is here that light steel frame’s wellevidenced performance benefits offer yet a further boon to companies looking for assurance when it comes to procurement. “From a technical and performance perspective,” adds Mike. “The fact that light steel frame solutions are so rigorously tested, with warranties often supplied from a single source, mean we can offer the kind of certainty and compliance which will be a priority within the new Procurement Bill. As the sector strives to champion offsite as the construction method of choice, the changes to the Bill will allow companies to demonstrate how light steel frame systems provide a perfect fit for many of the new procurement requirements.”
For more information visit: www.lsf-association.co.uk
The UK Procurement Bill will have many implications for the UK’s built environment and should play to the strengths of an offsite-delivered light steel frame approach.Images:
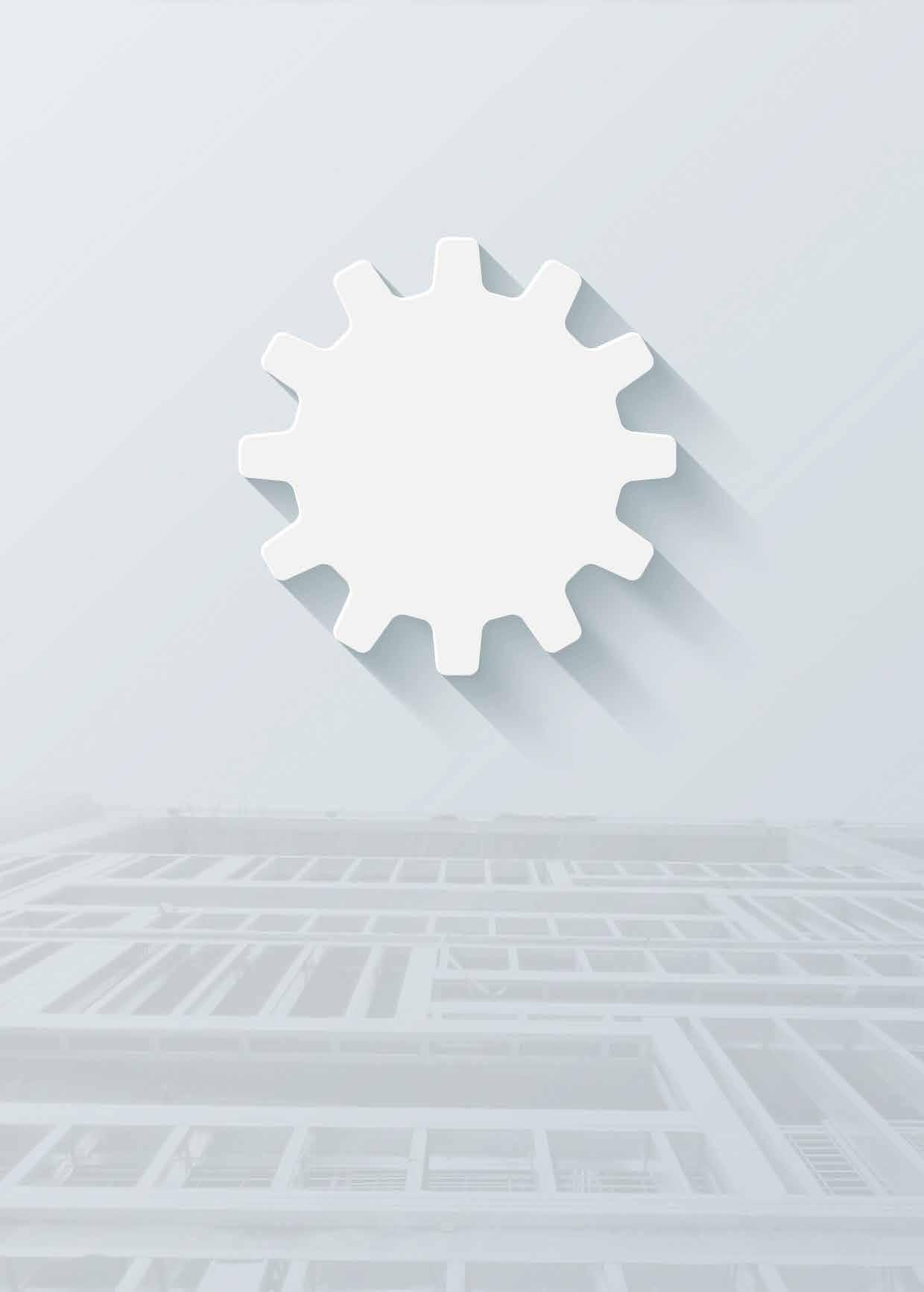
OFFSITE AMBITIONS
Although a housebuilding slowdown is likely this year, the company remains confident that it will gain market share in each of its segments, with the greatest opportunities being offsite. According to Group Chairman, Ian Wilson: “Having supplied customers using offsite processes for several years now, it feels like the transition is approaching a tipping point – we know modern methods of construction (MMC) is still in the early stages, but the momentum seems to be growing.” And Wilson believes the group’s innovative façade systems are ideally suited to support offsite construction, adding: “We want to become the supplier of choice for offsite façade systems.”
Benx’s proprietary Supertech® rainscreen facade is gaining significant traction. A lightweight, yet durable, cladding solution that combines strength and stability with the appearance of traditional timber, Supertech® has been well-received by housebuilders. To meet increasing demand, Benx has invested in a stateof-the art automated spray paint line to coat the weatherboards in-house – dramatically scaling capacity, while ensuring consistent product quality. Benx also worked with a leading international coatings manufacturer
to create an A-1 (non-combustible) fire-rated coating - the first of its kind. These initiatives have helped to dramatically increase the sales of Supertech® and provide a platform for continuing growth.
The most recent addition to the Benx portfolio is its innovative SLIPFAST® brick slip system. Following customer feedback that existing mechanical-fix systems were, ‘too heavy, too slow to install, or too expensive’, Benx set about creating something which ‘ticks all the boxes.’ SLIPFAST® utilises a unique ‘rail and clip’ mechanical fixing system, allowing its clay slips to be attached very quickly, without the need for skilled operatives. Stainless steel fixings as standard, makes it suitable for coastal environments and it also carries an A-1 fire-rating. Since its launch in mid-2022, SLIPFAST® has been getting a lot of attention, with several large projects underway and a growing project pipeline.

Benx has also been ramping up its fabrication activity. In addition to cutting Y-Wall and multipurpose sheathing boards for both offsite and site-based applications, the business has been busy supplying ‘made-to-measure’ Swisspearl facades and support framing for Volumetric
Modular’s iconic MODULHAUS™ housing units. Among other fabrication activities, it is also supplying facades for new schools, delivered through the Department for Education (DfE) Offsite Framework.
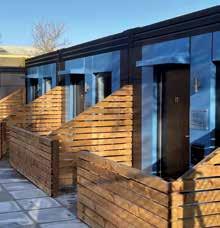
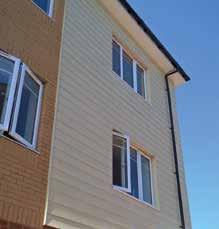
Notwithstanding the company’s success, Benx recognises that offsite construction is a fast-developing realm which will require it to continuously improve its processes, invest, and always listen to customer feedback. According to CEO, Kevin Ruane: “Benx is a learning organisation – we strive to get better all the time.”
As Group Chairman, Ian Wilson states: “We never forget that like everyone, we are finding our way and, as the processes evolve, the goalposts will continue to move – so we must continue to adapt, while using our experience to help shape the future of facades.”
For more information visit: www.benx.co.uk
After a record year in 2022, Benx Facades remains optimistic for continued growth in 2023 with more work in the offsite sector firmly in its sights.
PRECISION ENGINEERED
Fire Resistant
Performance Assured
Reduce Risk
Operate with Certainty & Confidence
Fully Tested & Warranted Systems
Safety-First approach with:
THRUWALL THRUBUILD PRE-ASSEMBLED FRAMES
www.eosframing.co.uk Find out more:
Specialists in Steel
Framing Systems for Residential Applications
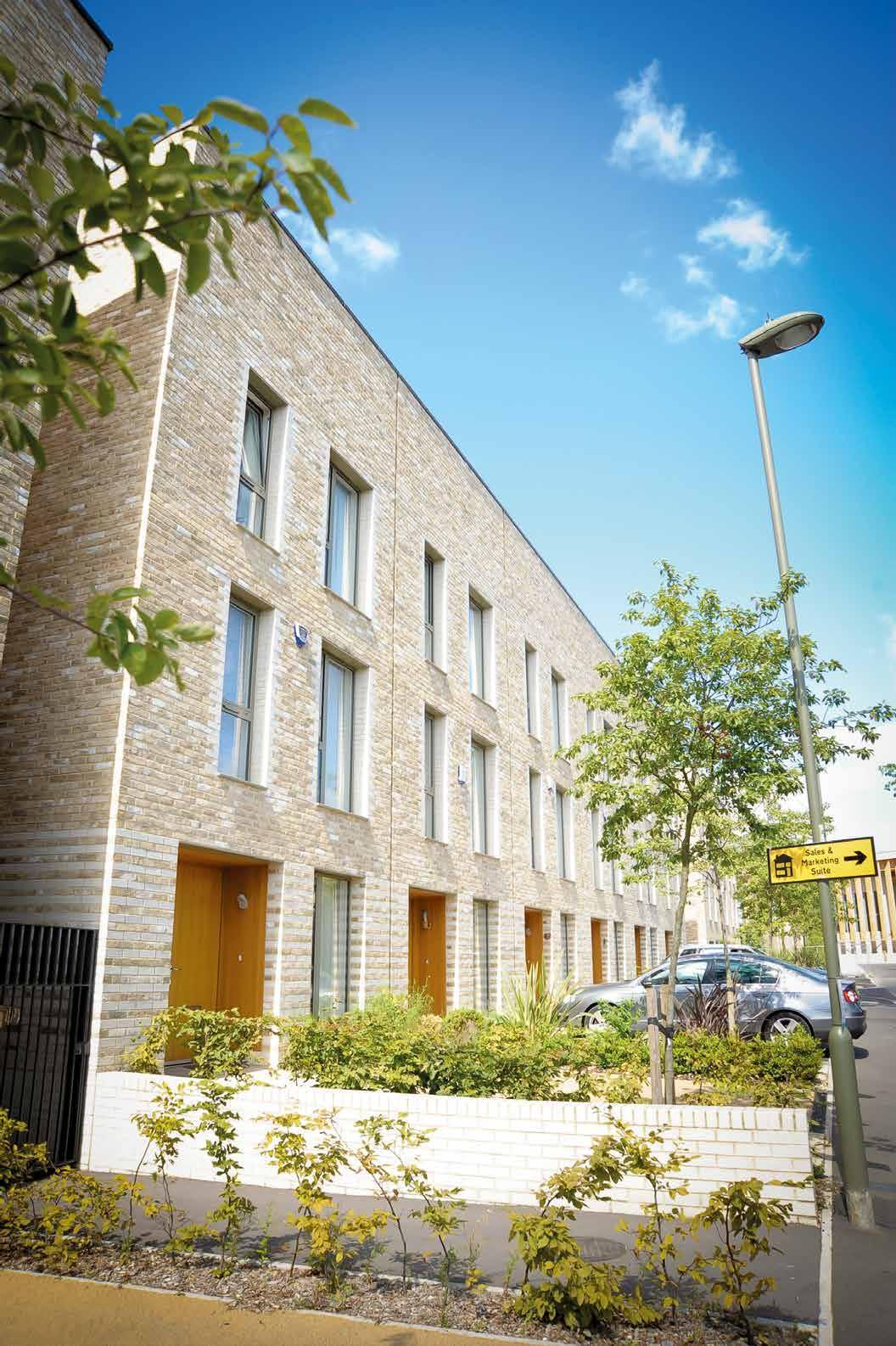
Martin Elze, Associate Director at Buro Happold, illustrates how EDGE Suedkreuz – the largest modular timber-hybrid building in Germany – holds some structural, MEP and sustainability lessons for UK designers.
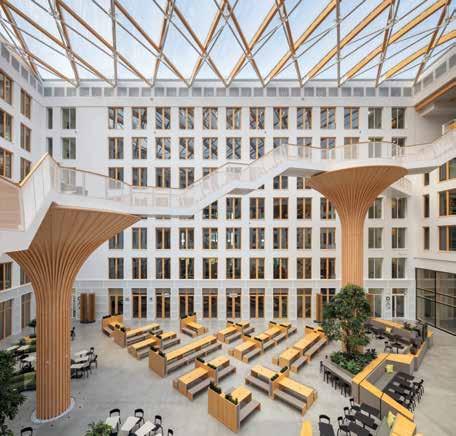
MODEL SUSTAINABLE BUILDING DESIGN 1
Climate change and sustainability are at the top of the agenda across every industry. The built environment is no exception. The sector is currently responsible for 39% of global CO2 emissions. This is a huge percentage of total greenhouse gas emissions and across the industry action is already being taken, with many commercial property developers focused on improving energy efficiency.
And yet, a key part of the puzzle still needs to be solved. Whilst the operation of buildings represents 28% of total emissions, 11% of this total still comes from the construction process and building materials, many of which don’t have zero-carbon
alternatives. Concrete, for instance, is responsible for 8% of total greenhouse gas emissions and whilst the industry is working hard to create low-carbon alternatives, the technology is still in its infancy.
New solutions to reach climate targets are therefore important for any new project. That is why modular timber hybrid construction is so exciting. Using timber allows for a large reduction in concrete use, and a modular method of construction reduces emissions produced during the construction phase. All while maintaining impressive energy efficiency and without compromising on user experience.
But what do the possibilities and benefits look like in reality?
EDGE Suedkreuz, a new working space located in the heart of Berlin, is a great and recently completed project to look at. The scheme is comprised of two joined buildings – the Carrée office and the smaller Solitaire building, each with six floors and connected by an underground car park. The result is the largest project completed as a modular timber-hybrid construction in Germany, and one of the largest in Europe. The Carrée office is now occupied by one of Europe’s leading energy suppliers, themselves very closely focused on sustainability.
The modular timber-hybrid construction system used was created by CREE Buildings and applied by engineers from Buro Happold. The decision to choose timber was integral to achieving the ambitious environmental and sustainability targets set by the office developer.
There are clear sustainability advantages to a modular timber-hybrid construction. Reducing the amount of concrete used lowers the building’s the total emissions, as timber is less carbon-intensive to produce.
Upon completion of the EDGE Suedkreuz building, a lifecycle assessment was carried out as part of DGNB certification – one of Germany’s most respected sustainability accreditations. It found that compared to a DGNB reference building, the embodied carbon for EDGE Suedkreuz was reduced by more than 50% overall.
The modularity of the system also greatly improves the speed and efficiency of construction, reducing on-site production time, energy use and waste. In addition, this allows for
higher quality environmental standards such as soil and waste protection, avoidance of dust and lower levels of noise pollution. And this project went even further too, aiming to build in a way that would make re-use, retrofit or recycling much easier. Special emphasis was placed on using materials that can be recycled, with materials used tested for their environmental impact and recyclability. The timber used in the structure, for instance, comes from certified forests, and other materials are recycled or recyclable wherever possible.
EDGE Suedkreuz Berlin is the first building in Germany to be uploaded to the MADASTER material database for building construction. The platform documents and stores materials, products and elements used in construction objects. It generates a material passport for a building, enabling precise monitoring of ecological sustainability.
Again, the modular timber construction method played a key
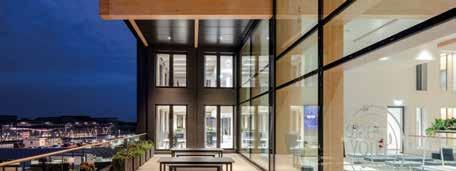
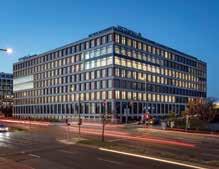

role here because it will ultimately make deconstructing and recycling the structure much easier. However, it can also make re-use easier too. Close co-ordination of the structural grid and the MEP design allows the building to adapt to future needs by separating rooms with partition walls every 1.35m, ensuring longevity through possible re-use.
In conjunction with the recyclability of the materials, modularity ensures a sustainable building system that reduces waste and future-proofs the building. The result of all these measures is a building with hugely impressive sustainability credentials, without compromising user experience. The result is a truly greener building both in design and construction, but also a brilliant case study on how we can create spaces in more sustainable ways. The message to commercial office developers is therefore a clear one: don’t overlook and miss out on the opportunities modular timber construction can unlock.
The use of prefabricated modules had a positive effect on various aspects of the construction process. Through the intelligent combination of wood with concrete, the modular hybrid solution from CREE-Buildings can save up to 80% per m2 of usable space… a flexible modular floorplan grid on all levels can be adapted to individual wishes when converted. In this way modern, multi-functional working environments can be created.
For more information visit: www.burohappold.com
FROM MINING COMMUNITY TO NET ZERO
The Hart School in Rugeley has recently completed a new, highly efficient development with sustainable experts, Net Zero Buildings using a panelised timber offsite method.
Less than two miles from Lea Hall Colliery, a disused mine that produced over one million tons of coal per year on several occasions between 1970 to 1980, The Hart School is leading Rugeley into a new era by committing to its net zero in operation expansion.

This huge investment for the local community offers additional capacity for the growing school, as it becomes a part of a net zero future. As a result of the new building’s A+ energy efficiency rating, the school will save an estimated £30 per m2 per year. This will see an approximate saving of up to £11,500 on energy bills this winter. As a part of the Creative Education Trust, this development, which was completed in October 2022, is a part of a larger scheme to encourage net zero school buildings across the country.
“We’ve had net zero aspirations for a long time,” comments Jon Ward, Director of Estates and Facilities, Creative Education Trust. “But when the local authority asked us to take on additional children at The Hart School, these aspirations became more urgent, as we needed to continue to provide an excellent and sustainable learning environment for the children of Rugeley.”
Net Zero Buildings designed a sustainable solution for the Trust to replace the existing 1960s singlestorey building, which offered much-
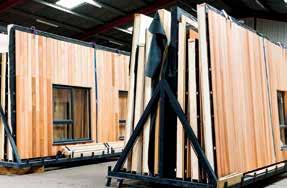
needed teaching spaces within the existing group of buildings. The 385m2 project supports the school in handling increasing student numbers – with 147 more students starting in 2022 than three years ago. It includes a new teaching block, made up of five classrooms, as well as female, male and accessible toilets, which is connected to one of the school’s existing buildings, ensuring seamless transitions for staff and students between the old and new.
The new building uses a combination of sustainable technologies to reach an A+ energy efficiency rating including a roof covered in photovoltaic (PV) panels and super-insulated timberfaced panels, which are extremely airtight for minimal heat loss. Internally, the building uses mechanical heat recovery ventilation and sensorcontrolled low-energy lighting, while maximising natural daylight, to create a sustainable, yet comfortable, internal environment.
This combination of lean, green and clean technology results in a highly sustainable building, with an air permeability value of 1.73m3/(h.m2) at 50 Pa, which is much lower than the typical value of 5 for a building like this. The Creative Education Trust chose Net Zero Buildings to deliver the Hart School extension, as it was able to deliver a highly sustainable solution that reflected the school’s net zero carbon ambitions. This means in operation, the school will generate more electricity than it uses, reducing running costs and helping to offset its carbon – which is more important than ever, given the current economic climate.
The Trust chose to build using offsite solutions as its highly sustainable, reducing carbon emissions, construction waste and energy consumption during the construction stage. Offsite also meant the new school building could be in operation up to nine months quicker than traditional construction methods. It also enabled a more cost-effective build, with Net Zero Buildings completing the project under budget.
“It’s been wonderful to work so closely with Net Zero Buildings as it developed the Hart School designs. We understood the challenges associated with achieving a net zero environment on the existing school site, but we were keen to push further to ensure our investment was a sustainable one, and Net Zero Buildings enabled us to do this,” continues Jon Ward. “The project was completed in the spirit of partnership, and it was all achieved ahead of expectation, so we could accommodate the additional children as soon as possible.
“Net Zero Buildings has delivered excellent teaching spaces that are sustainable for the children of Rugeley, and the work we’ve achieved together has enabled us to better understand options for further construction projects. We’re very much looking forward to working with Net Zero Buildings in the future.”
For more information visit: www.netzerobuildings.co.uk
Images: 01-02. The
highly sustainable school
Setting the standards for timber fastening
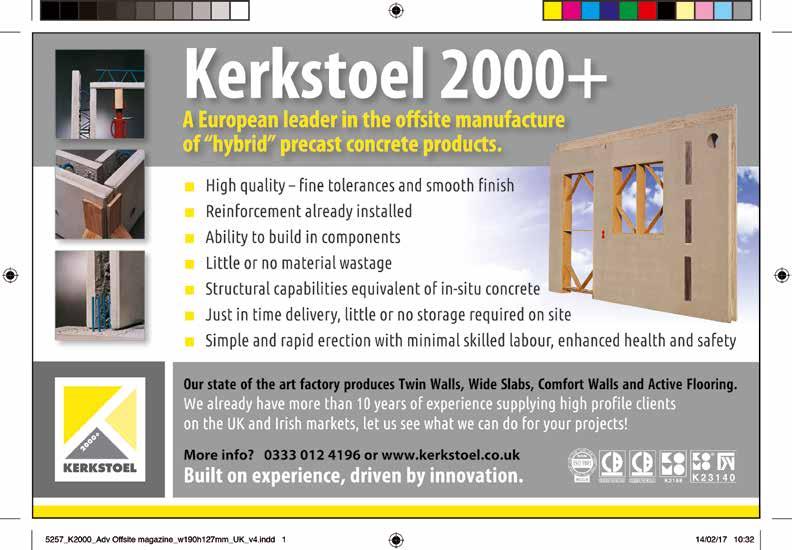
BeA your partner for timber frame and offsite construction manufacturing
Across Europe and worldwide, BeA’s fastening technology, tools and consumables are the trusted choice for some of the biggest and best known names in timber frame and offsite construction.
BeA manufacture an extensive range of market leading fasteners, nails, staples and tools. We offer customers:
• An unrivalled range of manual and semi-automatic fastening solutions combined with a fully automated range in Autotec.
• I ndustry leading quality controls, BeA meet or exceed standards such as Eurocode 5.
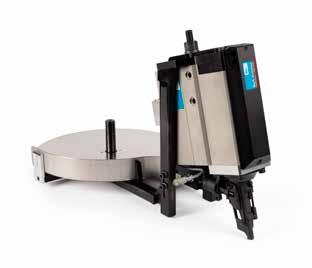
Reliable products, competitive prices and the kind of service and delivery you can depend on from BeA.

01482 889 911 sales@uk.bea-group.com visit our website www.bea-group.uk
THE POWER OF FASTENING

MTX NAMED ON CCS FRAMEWORK
The new framework agreement broadens the premanufactured building solution provision currently available to public sector buyers through CCS agreements. Through the new framework the Wilmslowbased company is eligible to supply buildings manufactured offsite for both the healthcare and education sectors, supporting the public sector plans to innovate, drive efficiency and continue to work towards their net zero carbon targets.
The Offsite Construction Solutions (RM6184) agreement reflects MMC innovations and continues to align with the policies outlined in the Construction Playbook on offsite construction adoption. It is designed to assist all public sector customers, with a specific focus on the health, housing, education, justice and defence sectors.
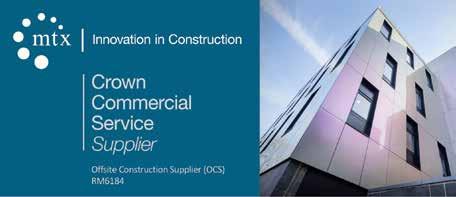
The agreement replaces the CCS Modular Buildings Agreement, which closes on 1 April 2023, and will run for 4 years with the possibility of a 3-year extension. CCS supports the public sector to achieve maximum commercial value when procuring common goods and services. In 2021/22, CCS helped the public sector to achieve commercial benefits equal to 2.8 billion – supporting world-class public services that offer best value for taxpayers.
John Welch, Deputy Director –Construction, Crown Commercial Service says: “This new framework will support the public sector in the design, delivery and commissioning of a whole range of offsite construction projects in the coming years, including social housing, new schools and hospital extensions.
“These projects, and the many more which will come, have the potential to improve services and the lives of millions of people. It is yet another example of how CCS is helping the public sector to support the government’s construction strategy and further supports the recently published refresh of the Construction Playbook with its MMC guidance note.”
MTX
MTX Managing Director David Hartley adds: “Offsite construction is a key element within the MMC processes MTX has developed and refined through its delivery of an extensive range of public sector projects, over many years. MMC is proven to deliver new facilities faster, greener and more cost effectively and achieves objectives within the Design for Manufacture and Assembly (DfMA) concept.
“Qualifying as a supplier is an important milestone for MTX which sees the new agreement as a vital tool in promoting wider adoption of off-site manufacturing within the construction industry and public sector procurement.”
MTX is a Cheshire-based construction and engineering company specialising in the use of innovative Modern Methods of Construction (MMC) to deliver advanced fasttrack building solutions to the NHS and private healthcare sector throughout the UK.

With almost 40 years’ specialist healthcare experience MTX continues to refine its innovative MMC solutions in line with the latest Design for Manufacture and Assembly (DfMA) principles. Quality is maintained, waste is reduced by up to 60% and delivery is faster, greener and more cost-effective. Time on site is reduced by up to 50% with building components pre-manufactured off-site under factory conditions while at the same time sub-structures are prepared on site, shortening the overall programme.
For more information visit: www.mtxcontracts.co.uk
Modern Methods of Construction (MMC) specialist MTX has been named as a supplier on Crown Commercial Service’s new £10billion Offsite Construction Solutions Framework.
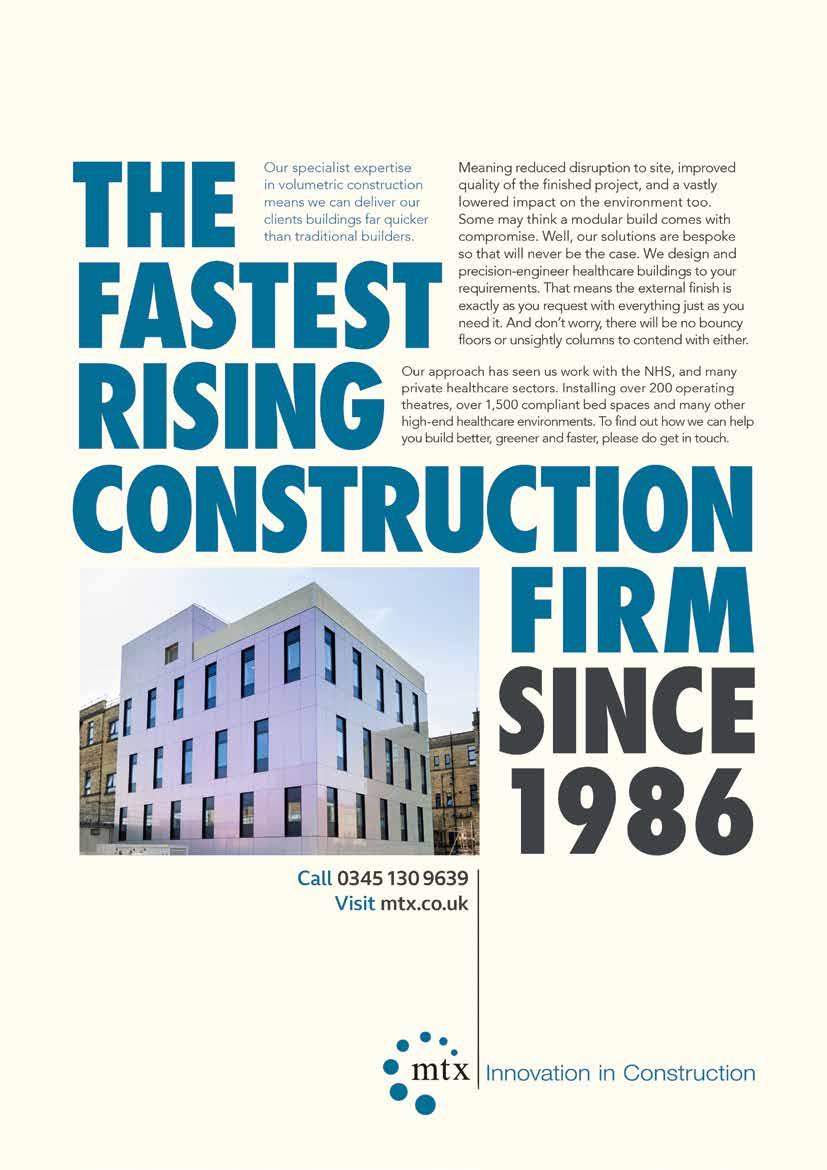
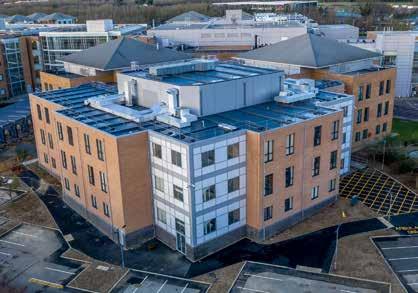
MODULAR MATTERS 2023
CREATING A NEW CONSTRUCTION MODEL
The Birmingham National Conference Centre (NCC) on the 7-8 February, saw the fifth Modular Matters event take place with delegates benefiting from two days of discussion about the most efficient ways to transform the UK built environment.
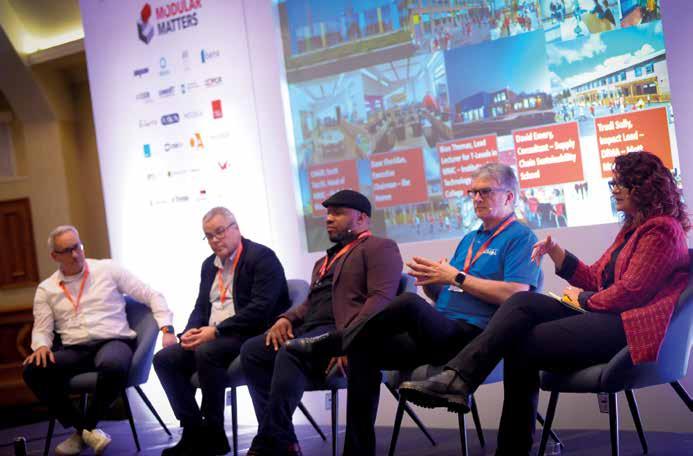
Over 350 delegates came to hear expert speakers and panel sessions plus view a wide range of pop-up exhibitors showcasing cuttingedge offsite products and systems. These included headline sponsor and exhibitor OBEX that took the opportunity to highlight several products geared towards the offsite market – in particular a ‘one piece’ modular roof membrane, meaning
fewer junctions and leakage and potentially reducing installation time by 50%.
In a break with tradition, the event changed format slightly to include several panel-led discussions on key areas shaping the modular and wider world of offsite manufacture. After David Hyland from MJH Structural Engineers started proceedings with an overview of its work on the landmark Ten Degrees – the world’s tallest modular building that maximised modularisation to awardwinning effect – Andrew Shepherd, Managing Director of TopHat, outlined their technology-driven approach
to housing design and delivery, alongside the vision behind its new 650,000sq ft mega-factory in Corby –one of the largest of its type in Europe that will help deliver 5,000 homes per annum.
This led into a key panel discussion on Design for Manufacture and Assembly (DfMA) facilitated by Darren Richards, Managing Director of Cogent Consulting. Taking part: Andrew Pryke, Managing Director, BAM Design, Anne Daw, Head of MMC Delivery at HLM Architects, Ben Haldin, Managing Director, Fulcro Engineering Services and Renee Puusepp, Founder of Creatomus Solutions. This set
about defining and exploring what DfMA means. In many respects this boils down to a ‘simple clarity of approach and understanding of detail’ and seeing the DfMA approach as a collaborative one, from design decisions to standardisation and choice of materials.
It is also about getting to grips with ‘how buildings are made, not how they look’. Architects perhaps need to get ‘a better grip on the power that standardisation can bring’. There was also some minor criticism of the RIBA Plan of Works DfMA Overlay for not allowing the contractor to come into the design process early enough, plus the role of the MMC Advisor not being fully realised – perhaps a specific ‘DfMA expert’ would be better suited to address the intricacies of platform design and digital software to boost quality and productivity.
New Thinking
Debate on skills development and creating a new industry talent pool was facilitated by Scott Tacchi, Head of MMC at Sir Robert McAlpine and included Rion Thomas, Lecturer in MMC/BIM, Institute of Technology at Dudley College, Dave Sheridan, Executive Chairman, ilke Homes, David Emery, Consultant, Supply Chain Sustainability School and Trudi Sully, Impact Lead DfMA at Mott MacDonald.
The Skills and Supply Chain debate surrounded ‘trades v tasks’. As Rion Thomas pointed out regarding the challenges of young people, the better use of role models provides a connection and can help overcoming barriers to entry. “It is about creating content that can be understood and joining the education and construction industries together more.” A cleaner and safer industry will also attract a more diverse workforce but ‘each company has to look at its own workforce and how to attract them and hold them there’.
Net Zero Carbon
A complicated subject and an entire conference in itself with many differing aspects to discuss and explore. Facilitated by Richard Hipkiss, Development Director, MPBA with Dr Rehan Khodabuccus, Operations Director, Zedpods Philippa BirchWood, Local Network Co-ordinator, UKGBC and Imran Kassim, Director, AHR. For many, the future of building regulations and carbon targets will dictate the direction of travel but also a better ‘understanding and control of what net zero carbon is and developing ways of assessing operational and embodied carbon effectively.’
One key issue raised: whilst accreditation is important (e.g.
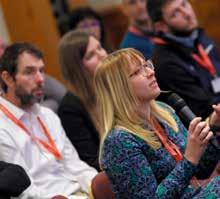
Passivhaus) perhaps it is less important than the actual approach. Collectively the construction industry needs to look for an appropriate low carbon solution rather than obsess about accreditation. This could be helped by more detailed post-occupancy studies that map out operational carbon and reveal a better understanding on how buildings are used.
Day 1 ended with Wayne Yeomans, Sales Director at Algeco providing a case study on their use of the SEISMIC approach and work with McDonalds, including its net zero restaurant at Market Drayton with Jim Mitchell, Design Director, Stelling Modular, outlining their innovative modular connector system and road to low carbon design.
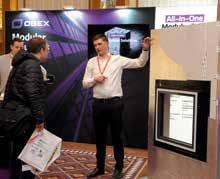
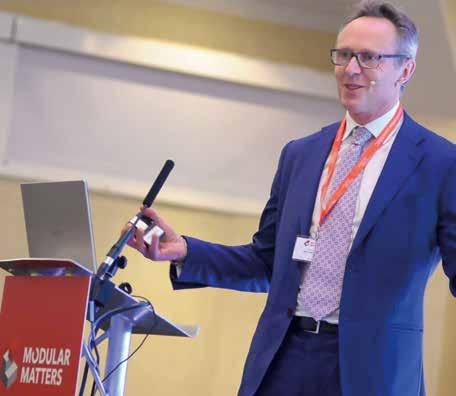
Revolutionary Homes
Day 2 was chaired by Sam Stacy, Chief Executive of Stacx International and started with ilke Homes’ R&D Director Nigel Banks giving a wideranging presentation on how they are ‘revolutionising housing supply’ and changing the modular homes market dynamic. Ilke Homes has very quickly become synonymous with quality modular homes and Nigel gave an update on the ZERO Bills home and potentially how these kinds of developments are: “the key to unlock consumer appetite for low carbon high
performing modular homes.” The Digital Platforms panel debate saw David Philp, Chief Value Officer, Cohesive Group, Chris Spiceley, Client Accounts Director, Modulous, Nick Marriott, Digital Engineering Lead at Portakabin and Craig Johnson, Business Development Manager at Trimble, describe some of the ways that digital platforms are driving change and innovation, with the ‘golden thread’ becoming more important. However, the wealth of information, data and work-flow complexities, ‘have to be understandable for all users from architect, engineer to manufacturer, to aid better collaboration between services and trades.’ Although digital tools are visually exciting and a way of attracting a more diverse talent pool to the sector, it has to remembered that a digital strategy is not appropriate for every employee. There does need to be a reduction in the ‘clicks required to perform a task.’
The final two panel sessions covered Modular Design and Social Value and Designing for Modular. The first facilitated by: Peter Morgan, Deputy Chief Engineer, MTC, Mike De’Ath, Partner at HTA, Penny Anderson, Head of Social Value, Akerlof and Fenella
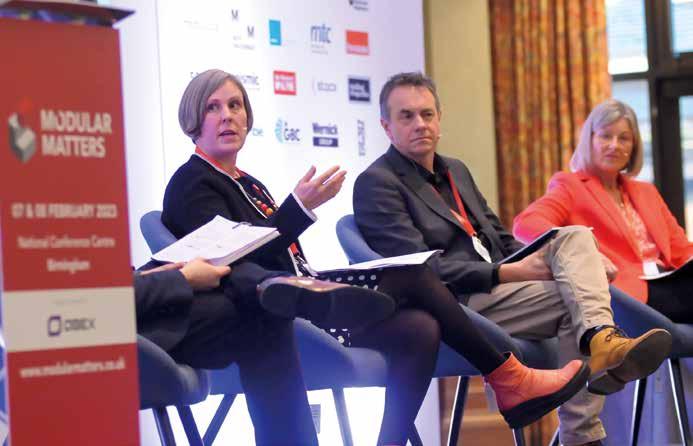
Lowden, Client Solutions Manager, Tophat, with the final panel led by Andy King, Group Technical Director, MPBA, Charlotte Garrett, DfMA Lead at KOPE, Richard Crosby, Director, the Seismic Group and Simon Reid, Managing Director, Lungfish. Core to much of the afternoon discussion was the pressing need for modular design to prove what it can do – both from a technical perspective but from a skills transfer and workforce creation perspective as well – with factories created where jobs are needed and able to cater for desired flexible worklife patterns.
As ever, designing for modular needs early engagement and more than once over the two days, talk surrounded how the industry should be looking at what can be standardised for manufacturers to produce systems that are easy to specify and replace if there is a problem. The search for interoperability and commonality to link design and supply together –probably through digital tools – can provide more confidence for clients and developers erring on the side of caution of offsite adoption. Here, digital software is understood to be a huge enabler to building design work and providing a huge boost
to productivity: ‘making something consistently, makes it easier to improve.’
Two days of in-depth discussion and debate ended with Stephen Webb, Design Manager at McAvoy and Alan Davidson, Healthcare Director at Darwin Group, providing an overview of projects at Merstham Park School and Hampshire Hospital’s Heart Centre respectively.
Across both days the benefits of offsite modular design and delivery were laid out clearly. Not just from technical and net zero carbon standpoints –regular concepts of early engagement, developing simpler tools and processes and greater interoperability between the various platforms and systems on the market – but from their wider societal effects on skills, job roles and employment. Ultimately modular construction matters as it is a way to not only change construction, but create a brand new construction model fit for 2023 and beyond.
To find out more about Modular Matters and to keep tabs on what is happening in 2024 visit: www.modularmatters.co.uk
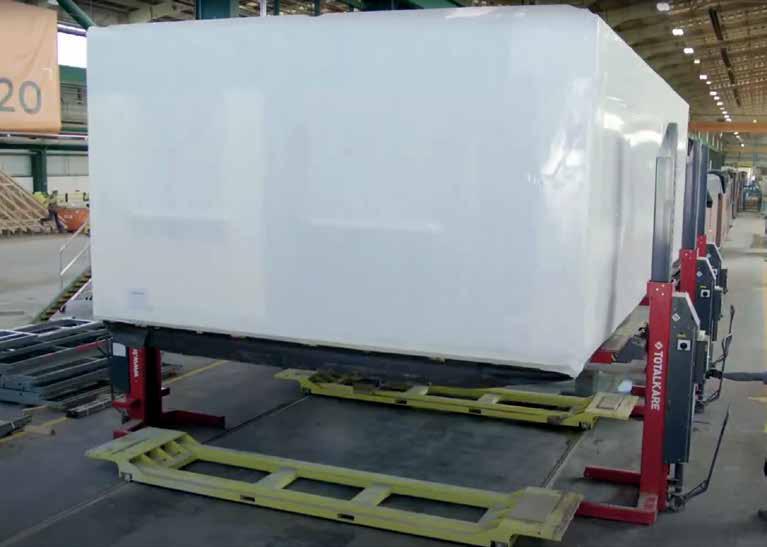

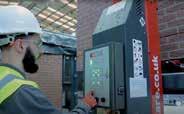
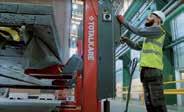
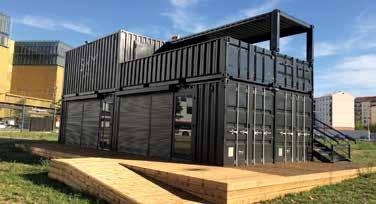
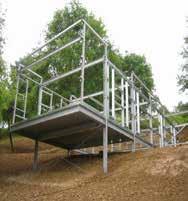
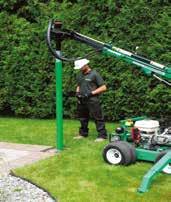
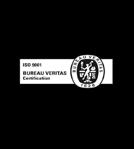


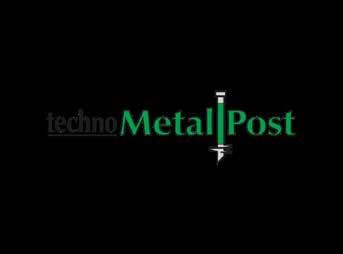
MODULAR ROUTES AND FUNDING OPTIONS
Ecology Building Society is launching the UK’s first dedicated mortgage for modular construction homes – could this be a pivotal moment for offsite construction?

Gareth Griffiths, Ecology’s Chief Executive explained: “Decarbonising our homes is key to meeting our net-zero ambitions. Now, more than ever, it’s important that lenders play an active role in incentivising green building and helping to reduce energy bills. We’ve been leading the way on sustainable mortgages for over 40 years, and we’re really pleased to be working in partnership with offsite manufacturers, who have a track record of delivering sustainable homes. We hope that our new mortgages will help scale-up modern methods of construction to deliver more homes built to higher energyefficiency standards.
Although initially aimed at the selfbuild and custom-build market, Ecology Building Society has partnered with several modular manufacturers to launch a new range of mortgages to support the growth of offsite manufacture across the homebuilding sector. Ecology’s innovative approach secures lending on the modular panels before they arrive on-site ensuring mortgage finance is available for different types of self-builders.
The sustainable lenders ‘offsite build’ products enhance its range of green mortgages for self- and custom-build in a drive to encourage and accelerate the construction of the most energy efficient homes to help meet the UK’s net-zero ambitions. The lender has initially teamed up with four modular manufacturers to offer the offsite build
mortgages to their customers only. The Society expects to partner with more suppliers in the coming months.
Supporting offsite manufacture
The decision to introduce the new offsite build mortgages comes at a time when the Government is recognising the urgent need to reduce the carbon impact of house building and has stated that new homes must reduce carbon emissions by 75% by 2025. Supporting the role of offsite manufacturing and modern methods of construction to deliver greener homes was a key recommendation in Richard Bacon MP’s independent review of custom and self-build housing. The Society hopes that the offsite build mortgages will improve the supply of mortgages and help to scale-up modular construction, which is recognised as a key part of the solution to address the housing crisis.
“The introduction of the ‘advanced payment’ mortgage option is an exciting first for Ecology, making energy efficient offsite build homes more accessible for those borrowers who may require up-front funding. Our innovative approach, to secure our lending, in advance, on the modular panels while they are in the factory, has the potential to be a game-changer, helping to realise the environmental benefits of offsite construction, which will be critical in the fight against climate change.”
Mortgage options
Ecology is offering borrowers a choice of two products, an arrears payment option and, for the first time, an advanced payment mortgage, which may be of particular interest to those who require upfront finance to fund the purchase of land and manufacture of the modular panels. On completion of the works, borrowers will also be eligible for one of the Society’s C-Change discounts which are designed to incentivise and encourage borrowers to build their home to a better energy efficiency rating leading to a long-term saving in both energy and borrowing costs.
“People wanting better built energy efficient homes need a mortgage provider who can make buyers dreams become reality. Ecology have actually done something pioneering, genuine and intelligent in launching these new mortgages. Hopefully others will follow their lead. It’s real change like this that is going to make a difference.”
Nick Fulford, Chief Executive, nHouseOn completion of the works, borrowers are eligible for a C-Change discount of up to 1.5% based on the SAP rating in the EPC (Energy Performance Certificate) or if the property is accredited to the exemplary AECB Building or Passivhaus standards. All of the offsite self-build projects must show they will achieve a minimum SAP rating of 88.
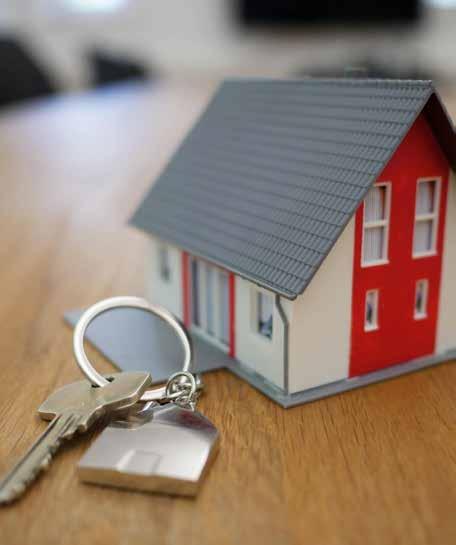
“The time is ripe for the housing industry to consider how we redefine sustainable and affordable living,” says Craig White, Chief Executive, Agile Homes. “By adopting modern methods of construction in our panellised build system, made from naturally renewable materials, Agile can produce energy-efficient, carboncapturing homes with minimal impact on the environment and significantly enhanced quality. The Agile team has the skills, industry experience, and methods to make this happen, on a significant scale, together with Ecology Building Society.”
Alasdair Stephen, Architect and Managing Director, HebHomes said: “These new mortgage products reflect the changing construction sector with more and more homes manufactured offsite and assembled on-site. HebHomes are delighted to partner with the Ecology Building Society as we know these innovative new mortgages will allow more people to finance and build their dream homes.”
For more information visit: www.ecology.co.uk/mortgages
Images:
01. Gareth Griffiths, Chief Executive, Ecology Building Society
MODULAR PROVIDERS
Agile Homes
Established in July 2019, Agile's latest project has helped homelessness charity, Emmaus Bristol, secure planning permission for 15 modular homes, with community space, to be built on the roof of Emmaus’ Bristol office and retail store. For more information visit: https://agile.property
HebHomes
Founded in 2004, HebHomes is a leading architect-led kit home company and recognised as a pioneer in bringing sustainable, modern housing to rural Scotland and the wider UK. HebHomes together with its sister company Dualchas Architects, has developed five signature house ranges and 40 designs, re-imagined as modern and affordable living spaces. For more information visit: www.hebhomes.com
nHouse
Award winning nHouse offers self-builders and custom-build buyers a range of contemporary, spacious and energy efficient timber-framed homes. Using offsite methods means their homes are typically ready for buyers to move in 16 to 24 weeks after contract. For more information visit: www.the-nhouse.com
R. HOUSE
R.HOUSE is a collaboration between award-winning architects Rural Design and James MacQueen Builders on the Isle of Skye. This partnership means that they have the expertise of strength of design and construction, together, under one roof. For more information visit: www.ruralhouse.co.uk
VISION OF THE FUTURE
The pioneering eHome2 is a threebedroom family home built inside the world-leading Energy House 2.0 climatic chamber facility at the University of Salford. Over a period of nine months, the house will undergo rigorous whole-building testing – including thermal performance, energy efficiency, running costs and residential comfort, as well as its ability to cope with extreme temperatures and climatic conditions.
Energy House 2.0 is a £16million testing facility that is part-funded by the European Regional Development Fund and harnesses the University of Salford’s expertise in climate and the built environment. This unique facility builds upon the success of the original Energy House Laboratory, which was opened in 2012. Completed in February this year, the Energy House 2.0 facility is the largest of its kind in the world, with two chambers which
can accommodate two detached homes. These chambers can replicate weather conditions including rain, wind, snow and solar radiation, with temperatures ranging from -20 degrees to +40 degrees centigrade.
The eHome2 house was built using a combination of offsite methods, with Saint-Gobain Off-site Solutions brands Scotframe and Pasquill supplying advanced timber frame products and factory-installed pre-insulated walls. eHome2 – a collaborative partnership between housebuilder Barratt Developments, Saint-Gobain Off-Site Solutions, and additional brands within the Saint-Gobain UK & Ireland group, seeks to change the way we build high-quality, sustainable and future-ready new homes in the UK. As such, the data gathered from eHome2, which is operationally net zero, will help inform how the housebuilding sector will design and
build zero-carbon housing at scale using sustainable building materials and offsite solutions.
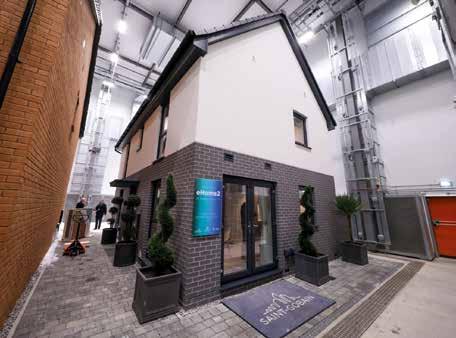
Futureproofing with Posi-Joists
Manufactured and assembled at Pasquill’s flagship Chorley site, the floor cassettes supplied to eHome2 are a timber frame construction. As the project is being built to exceed Future Home Standards requirements, it has been designed to accommodate many more heating, ventilation and renewable energy services than the houses commonly built today. Pasquill’s Posi-Joist™ cassettes’ metal webbed design creates a larger service void, allowing for easy and free routeing of utilities such as Mechanical Ventilation and Heat Recovery systems (MVHR) throughout the home.
These top-hung Posi-Joist floor cassettes also help speed up the process of installation and reduce the thermal bridging at wall-floor interfaces. Pasquill has also supplied the roof trusses for eHome2 to help create a thermally efficient attic space. Combining traditional trusses with attic trusses has created a space that can also house additional services and pipework required to run future smart homes. Both the Posi-Joist cassettes and the roof truss systems add to the pre-manufactured value of the eHome2 build.
Thermally efficient panellised solution
eHome2 features a new proposed MMC category 2 closed panel solution from Scotframe. The wall panel system, which is assembled with BRE A+ rated Isover mineral wool between the i-stud based timber frame, provides maintenance-free and long-lasting insulation. This cuts energy bills, while innovative connections reduce thermal bridging design and enhance airtightness.
As part of a wider project designed to accelerate progress towards low carbon and net zero housing, the pioneering eHome2 concept house built using offsite technology at Salford University will soon enter an intensive testing period.
Get creative with space & light
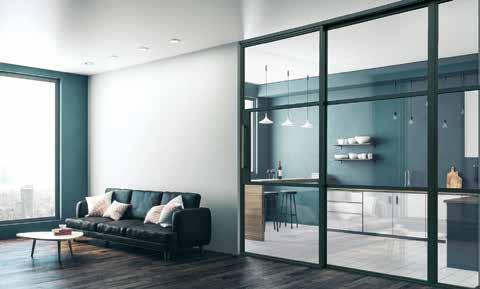
Our AluSpace Interior Screening System is designed to divide or delineate both residential and commercial spaces, while at the same time providing an effective acoustic barrier. Choose from hinged single, double doors, pivot or sliding doors to accompany our stylish fixed glazed screen. This flexible and versatile system provides almost limitless design options whilst requiring minimal maintenance. AluSpace will provide many years of assured, reliable and robust performance.


For more information visit smartsystems.co.uk/aluspace
E sales@smartsystems.co.uk
GRATED GRP PANELS AVAILABLE FOR

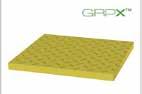
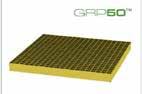
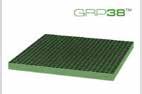
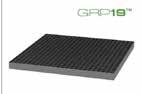
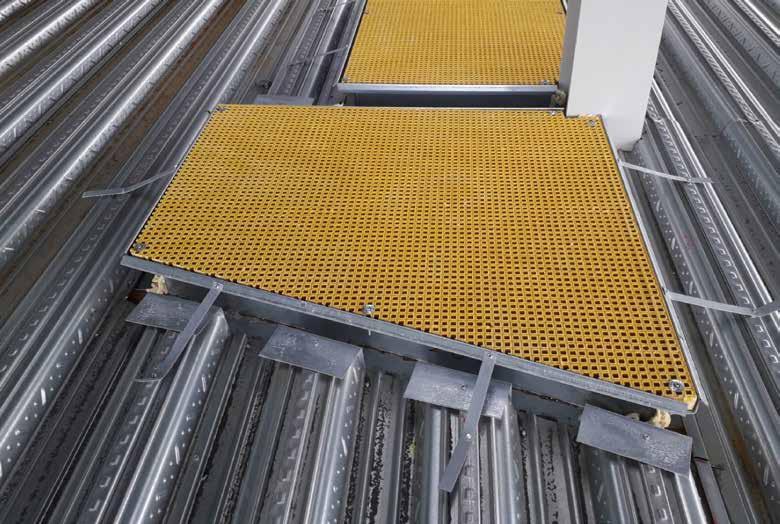
DELIVERY TO THE UK
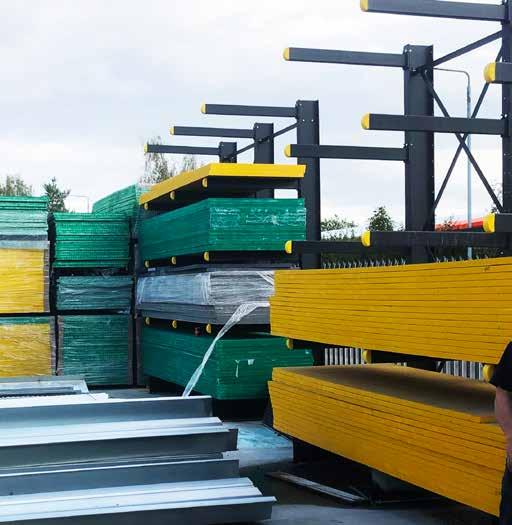
ENERGY HOUSE 2.0

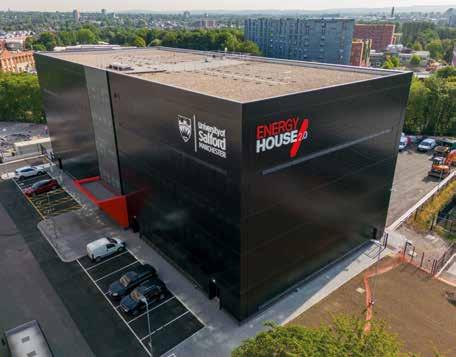
“eHome2 will produce a new blueprint for building homes en masse that are capable of operating at net zero carbon level, consuming far less water and creating less waste. At times like this, with the cost of energy at a critical point, new modern methods of construction which see homes constructed offsite in controlled factory settings are essential to create sustainable, comfortable and efficient homes that will cost consumers far less to heat.”
Mike Chaldecott, CEO of Saint-Gobain UK & IrelandWith the inclusion of critical vapour control membranes, service zones and externally fitted battens, the system speeds up on-site build time and ensures a high-performing fabric –achieving 0.13 W/m2k. The result is a solution with a performance point that exceeds Future Home Standard requirements without the need for additional site-installed installation. It also means that the house can be erected from the slab to the finished roof in only two weeks, including cladding and windows.
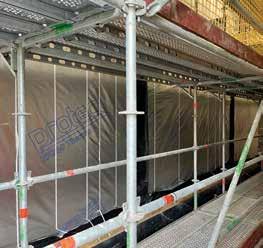
PROTECTIVE MEMBRANES
Ross Baxter, Managing Director, Saint-Gobain Off-Site Solutions, said: “eHome2 is an investment in the future of UK housing, and has the potential to completely revolutionise how we design and build homes. The fact so many organisations are working together towards a common goal shows that collaboration undoubtedly is the best way for us to tackle the challenges facing the industry.
Glidevale Protect is working alongside Bellway Homes by supplying its specialist construction membranes for use on The Future Home@The University of Salford, one of the two detached timber frame houses that are currently being constructed within the Energy House 2.0 energy performance test facility, with the structure having been manufactured offsite.
Glidevale Protect’s reflective, low emissivity Protect TF200 Thermo breather membrane and Protect BarriAir air and vapour control layer have been used on the innovative eco home. To provide high levels of thermal efficiency, the Protect TF200 Thermo breather membrane has been installed to the external walls, while the Protect BarriAir membrane has been fitted to the internal walls with the company’s universal reinforced sealing tape to eliminate air leakage and energy loss. Also installed is the Protect FCM 750 floor cassette membrane to maintain the integrity of the airtightness system at the floor junction and to provide condensation control at the edges of the floor cassette.
Once complete, The Future Home@The University of Salford will be subjected to various weather conditions within the Energy House 2.0 environmental chambers, which utilise state-of-the-art technology to test how well the specified building products and systems perform even under the harshest of environments. The research from the Energy House 2.0 project will provide a greater understanding of how energy efficient and low carbon building techniques can reduce the environmental impact of housebuilding and the wider construction industry.
For more information visit: www.glidevaleprotect.com
“It's our aim to help national housebuilders and other volume housing providers find a way of delivering zero-carbon homes of the future at scale and speed. The project is a brilliant showcase of how off-site manufacturing can help achieve this, with innovative solutions driven by sustainability and performance that can help make the world a better home.”
Tom Cox, Technical and Development Director, Saint-Gobain Off-Site Solutions, added: “This project is a fantastic demonstration of how offsite can deliver a high premanufactured value to housing developers. In particular, our brands Pasquill and Scotframe have made a significant contribution, with innovative timberengineered panels and cassettes which have sped up the build and increased its sustainability credentials. “When working with the Barratt design team on the project, designers chose to use the Posi-Joist™ cassette system to allow for easy rooting of utilities, which are required for future homes design. Meanwhile, the new panel system itself has also had a number of tests carried out on it so it's looking like it's going to be quite an exciting solution for developers moving forward.”
During 2023, the house will undergo rigorous whole-building research and testing including thermal performance, energy efficiency, running costs and comfort as well as its ability to cope with extreme temperatures and climatic conditions. The chamber can replicate environmental conditions experienced by 95% of the world’s population. Many of the technologies being tested are due to be in common use by 2026, so data gathered from this research period will inform how the housebuilding sector will design and build properties to meet the 2025 Future Homes and Building Standard and deliver low and zero carbon housing at scale.
For more information visit: www.saint-gobain.co.uk/eHome2 https://energyhouse2.salford.ac.uk
Images: 01-03. eHome2 will be trialled across a range of weather conditions for energy and thermal efficiency 04. Protective membrane installed at Home@The University of Salford

TEST MEASURE & DELIVER
What is a comfortable and affordable home? This is something very different for every individual and every homeowner. But with the chamber soon to close and enter its test phase all eyes will be on the results of the many sensors embedded in the homes to measure the different heating systems and fabric performance.
“With offsite, you have the capability to build a robust, standardised, repeatable product and get the same results every time,” says Tom Cox, Technical Director, Saint Gobain Off-Site Solutions. “This will demonstrate that a home produced in the same way, delivered and commissioned in the same way can deliver the end result that you want in terms of thermal efficiency and airtightness. The end product is thought about all the way through the design process.”
“Offsite systems are engineered within a factory process with controls in a very ordered and qualified way. You are not facing the potential risks of site-based mistakes resulting in issues down the line during a building’s lifespan. Offsite is not a brand-new ‘space-age thing’ it's often a lot of established materials being brought together in more solution- based way. This all needs to be communicated in the right way.
“As we deal with the climate emergency we need to look at how we can change building models and mindsets to be more sustainable and more productive. It is a perfect time for offsite to demonstrate it capabilities and benefits.
“A big piece of the research is trying to understand how you balance design and deliver a comfortable, sustainable well-heated home in a scalable and achievable building shell. Balancing the fabric first approach with MEP, glazing and bring it all together in a number of flexible weather conditions, we can prove that this type of system will give you a specific cost to run with a certain comfort perception. Being able to qualify the embodied carbon of a kit at the level of the full structure and bring together all these different elements, all detailed correctly and knowing it works will be a game changer.”
With questions always surrounding long-term scalability and affordability of concept homes, it is certain that for businesses that can supply a high levels pre-completed elements and pre-manufactured value (PMV) whether through a panellised, full volumetric or something in between, the scope for improving the quality and energy efficiency of UK newbuild housing stock built is huge.
Operating as a collaborative ‘chamber’ project and not ‘silo’ data being driven and collected by Saint Gobain, the final results will be published through Salford University and disseminated through the Future Homes Hub. The hope is to extend the testing for a further two years via Innovate UK to establish greater understanding of how the homes operate.
ATTAINABLE NET ZERO GOALS
John Charles, General Manager at NG Bailey Offsite Manufacture, explains how the company is embedding a net zero mindset into factory-based design and delivery.
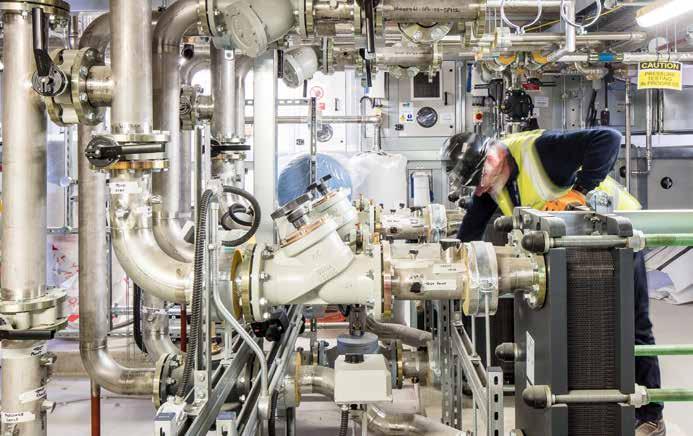
At NG Bailey we have been pioneering offsite construction since the late 1990s, providing solutions to our clients in the public and private sector through our specialist production facility in Yorkshire, the largest of its kind in the UK.
Delivering improved environmental performance for our clients is one of our key values and putting offsite methods at the heart of our strategy has been instrumental in helping us to make positive progress in our Net Positive strategy. Offsite and modular methods of construction are increasingly being viewed as more environmentally efficient ways to construct buildings. Advancing the use of these methods in the industry is going to be key to achieving net zero
goals at pace, both in our own work and those of our clients.
Making net zero possible at The Forge
The Forge, the first net zero office building in the UK, is an example of how offsite methods could be the future of low carbon construction. Working alongside multi-disciplinary design consultants, Bryden Wood, we developed, manufactured, and installed a mechanical and electrical (M&E) kit of parts. The development was the world’s first large scale office building to be designed and constructed using a ‘kit of parts’ led solution, built on a platform design for manufacturing and an assembly approach.
Through early engagement, collaboration and exercises to ascertain value engineering opportunities, we identified products that could be assembled by operatives more efficiently in the factory environment. This also extended to our supply chain, with discussions ensuring that elements, such as ductwork and FCUs, worked with our lightweight bracket solution in the factory.
Prioritising early collaboration with stakeholders on a project like this is key to achieving positive outcomes. By designing out risk at the earliest opportunity and moving as many on-site processes to a factory setting as possible, the industry can realise the positive environmental benefits that are made possible by having decreased numbers of people on-site.
This is vital for firms increasingly looking at ways they can achieve their net zero targets. By manufacturing offsite, the local impact of a build is improved greatly, with less people travelling to site meaning reduced traffic levels and noise. It can also minimise the number of deliveries to site, all of which has a positive effect on environmental outcomes of a project.
At The Forge, the removal of 20,000 on-site labour hours delivered substantial carbon benefits by avoiding 35,600km of vehicle movements, which alone saved six tonnes of carbon from entering the atmosphere. This is the equivalent to the carbon dioxide removal from 276 tree seedlings grown for 10 years.
Low carbon construction
Putting lower carbon methods of construction into practice on projects has been a key part of our Net Positive strategy and wider net zero goals. We have committed to reducing our absolute Scope 1 and Scope 2 greenhouse gas emissions – which covers the emissions from sources we own and control directly, as well as those we cause indirectly – by 50% by 2031.
As well as putting in place a clear roadmap for reducing our own emissions, we are also well-placed to offer lower emissions solutions for our clients. Offsite construction has been

a key part of being able to achieve this both in our own work and that of clients, providing ways to utilise less carbon intensive construction methods, use resources more efficiently and reduce wastage. With offsite construction accounting for less than 5% of the total construction market in the UK, there is still some way to go before we see widespread adoption of this modern method of construction. However, as net zero targets loom closer and companies look to how they can increase efficiency, offsite construction could offer the missing piece in the puzzle to achieving these goals.
SCIENCE-BASED CLIMATE CHANGE PLAN APPROVED
NG Bailey has become one of just ten UK construction and engineering companies to have a science-based target to tackle greenhouse gas emissions approved by the Science Based Targets initiative (SBTi). The UK’s largest independent engineering and services business has had a 1.5°C near term and net zero commitment target approved.
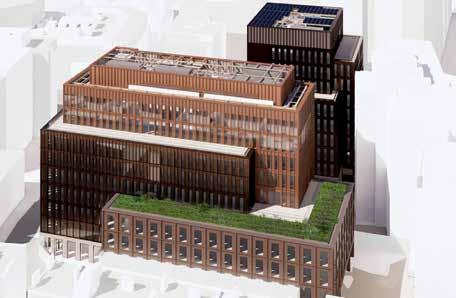
NG Bailey has committed to reduce greenhouse gas emissions from sources it owns and controls directly, as well as those it causes indirectly, by 50% by 2031. It has also pledged to ensure 75% of its suppliers have science-based targets in place themselves by 2027. The SBTi is driving ambitious climate action in the private sector by enabling companies to set science-based emissions reduction targets.
Natalie Wilkinson (pictured), Head of Responsibility at NG Bailey said: “NG Bailey already has a long history of being a responsible business when it comes to sustainability, reducing our absolute emissions by 27% to date while setting out our longer-term ambitions in our Net Positive strategy.
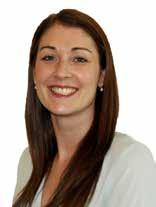
“However, as one of the UK’s leading M&E suppliers, we know we are at the forefront of being able to directly influence the transition to a lower carbon future. By taking the steps to have our science-based targets approved, we now not only have a clear roadmap for reducing our own emissions but can offer better lower emissions solutions for our clients, many of whom are on their own journeys. We know that the road ahead will be a long one, but by working together as an industry and committing to setting science-based targets, we are one step closer to making a net zero future possible.”
For more information visit: www.ngbailey.com/who-we-are/our-responsibilities
FUTUREBUILD 2023: A BETTER BUILT ENVIRONMENT
Futurebuild 2023 is set to provide offsite designers and manufacturers from across the construction sector with the ideas, inspiration and innovative solutions that will help them create net zero buildings faster, more safely and more efficiently.
Taking place at ExCeL London from March 7 – 9, the event will focus on our most pressing challenges in order to accelerate the shift to a net zero built environment. Sustainability remains at the core of this year’s show and is why Futurebuild 2023 is also urging visitors to act now and ‘take a stand’ on an issue they passionately believe will help propel the industry towards a more sustainable future.
Explore the ZED Micro Home
This year’s event will see sustainability champion and industry legend Bill Dunster OBE bring his latest innovations, the ZED Micro Home and revolutionary e-port, to the show. A truly flatpack micro home that can be assembled with only a rubber mallet and power drill, visitors will be able to explore the micro home at Futurebuild 2023 and see first-hand what the answer to several issues could be
currently affecting the UK, namely the housing crisis and continued demand on an already overstretched power grid. Bill will also be discussing ‘A decade of building zero bills homes’ on the Buildings & Offsite seminar stage on day one of the programme.
New spotlights and show sections
Futurebuild will be curated into eight show sections: Offsite will be packed with some of the most forward-thinking organisations in the sector including: Modular and Portable Building Association (MPBA), Proxim, ARLU, Magply and, Light Steel Frame Association (LSFA) to name a few. The seven other sections are: Buildings sponsored by Steico, Digital sponsored by Zutec, Energy sponsored by Kensa Group, Retrofit sponsored by Elmhurst Energy, Sustainable Infrastructure sponsored by ACO, Interiors sponsored by Lutron
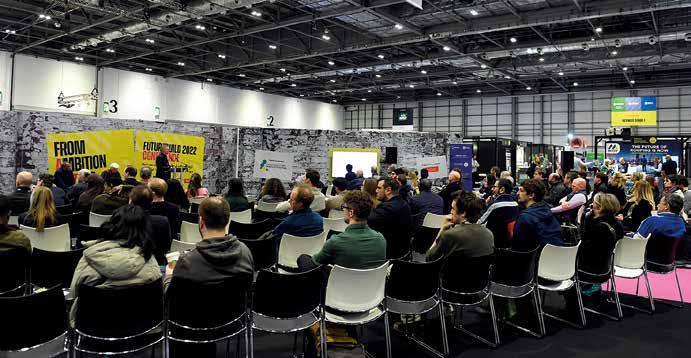
and Materials sponsored by Aggregate Industries. The event will also feature three new spotlights: Lighting in partnership with KNX UK, District Energy in partnership with UKDEA and FutureX Innovation sponsored by the Department for Energy Security and Net Zero (DESNZ) and in partnership with Ryder Architecture.
Share the knowledge
Curated and delivered by over 90 industry leading partners and featuring a stellar line-up of over 300 speakers, the expanded seminar programme is bringing the whole industry together to debate and learn from each other. The programme features practical and actionable CPD accredited sessions so visitors can gain many CPD points in one visit and at the same time acquire the knowledge and skills that will help them in their day-to-day role. Speakers will explore and tackle some of the
industry’s biggest and most critical topics with standout sessions on day one include ‘(Non-Domestic) Modular Construction and the journey to net zero’ curated by MPBA and ‘Scaling up offsite: collaboratively delivering MMC at scale’ curated by BRE. On day two MPBA will be discussing ‘Building modular and the Building Regulations: building a more sustainable future’ and in the afternoon the Light Steel Frame Association have a high-profile line-up of speakers to discuss the significant role light steel frames play in future developments.
Conference is ‘taking a stand’
This year’s conference programme brings together an outstanding line-up of expert speakers who are distinguished experts in their field to deliver the best possible understanding of what collectively we all need to do to meet our climate challenges. We are pleased to have two notable sponsors of this year’s conference: SNRG and Hub Brussels. Day one will focus on Looking Forward and why we need to develop the foresight necessary to break out of our current mindset, with a fantastic Activism session entitled: ‘Act now, or face extinction’ chaired by Ben Goldsmith Chair, Chief Executive at Menhaden and member of the Conservative Environmental Network Board. On day two, the conference will explore the nature of Changing
and especially ‘behaviour change’. Dr Viktoria Spaiser, Associate Professor in Sustainability at the University of Leeds, will chair a discussion on the ‘Big Issue of Changing’ how we do things in our professional and personal behaviour to live within planetary boundaries which features Dr Niamh Murtagh on the panel. Day three will move on to Taking Action, hearing from those who have been doing just that, and exploring plans that can take society and the construction industry forward.
Platform for innovation
Futurebuild will continue to be the industry platform for innovation and features a wealth of opportunities to showcase the most innovative technology, products and services. At the heart of this is the return of the renowned Innovation Trail that will give visitors the opportunity to explore revolutionary products, solutions and materials, and meet the leading thinkers behind these innovations. The Big Innovation Pitch will also return and offer exhibiting companies the chance of being crowned winner in 2023.
Those attending can also find further inspiration at FutureX Innovation, sponsored by the Department for Energy Security and Net Zero (DESNZ) and in partnership with Ryder Architecture, which will shine
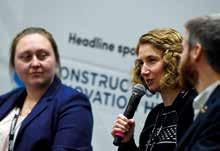
a spotlight on 40 start-ups and SMEs who will bring never seen before innovations to the event. The 40 companies exhibiting in the will have the chance to enter Futurebuild’s new competition the ‘Big Ideas Pitch’, a motivator for them to show how their game-changing innovation can potentially disrupt the built environment.
More than 15,000 professionals from across the entire supply chain will come together to discover these solutions and find new ways of delivering quality buildings more sustainably, whilst meeting and exceeding regulatory and compliance requirements. Everyone in the supply chain has a solution that can make a positive change. Futurebuild 2023 will provide the ultimate stage to showcase that commitment to the creation of a better building industry and achieving net zero.
Futurebuild 2023 will take place from 7-9 March at London’s ExCeL. For more details visit: www.futurebuild.co.uk
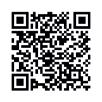
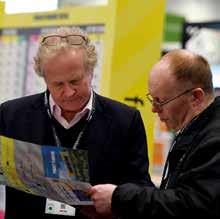
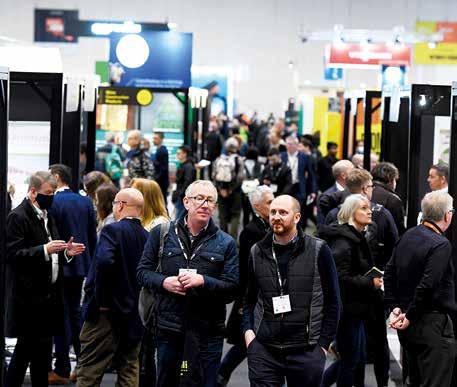
PRODUCT INNOVATION
FULL REACTION TO FIRE SERVICE
Efectis explain more about reaction to fire testing and classification as part of its ongoing expansion and continuous efforts to offer customers fire testing options.
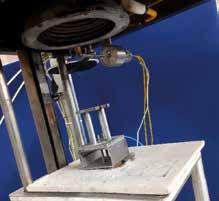
Reaction-to-fire (RtF) is the response of a product in contributing by its own decomposition to a fire to which it is exposed, under specified conditions. The RtF performance is considered in relation to products’ end use application and is measured through various parameters: fire growth rate, smoke production rate, fire spread, flaming droplets, ignition time, flaming duration, mass loss rate, to name a few.
Reaction to fire testing and classification offers a significant method for assessing the fire performance of materials, product and/or assemblies in a fire. To meet the relevant Building Regulations and
associated guidance with regard to fire safety, it is essential to provide evidence for the RtF performance of materials, products and/or assemblies used in buildings and infrastructure.
Efectis UK/Ireland as an Accredited Laboratory
Efectis UK/Ireland is accredited by the United Kingdom Accreditation Service (UKAS) for RtF test standards; namely the BS EN ISO 1716, BS EN 1182 BS EN 13823, BS EN ISO 11925-2, BS EN ISO 5660-1, BS EN 60332-1-2 and BS EN ISO 9705-1. Our team has accumulated experience and the expertise in carrying out the aforementioned standard tests on construction products and systems related to wall/ceiling applications and cables. Beyond that, our team is capable to advise on research and/ or ad-hoc test programs (non-UKAS) for providing our customers with tailored-fit solutions depending on their project-specific objectives and conditions.
WELLBEING & COMFORT
1 2
AJ Products is a full-service supplier of workplace furniture and equipment for offices, warehouses, industrial facilities, canteens, changing rooms and much more.
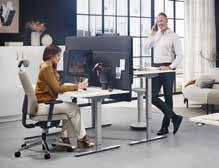
Established in Sweden in 1975, our Scandinavian heritage and design give our offering a distinctive modern look
while our European manufacturing facilities ensure consistent high quality.
Throughout our range, we place ergonomics front and centre to help businesses improve employee wellbeing and productivity. Our combination of over 15,000 quality products, expert knowledge, in-house design and manufacturing, and high service levels allows us to offer smart
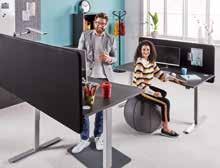
As part of our ongoing expansion and continuous efforts to offer our customers further testing options, the CEN/TS 1187: Test methods for external fire exposure to roofs, will be added to our scope of services. With that added, classification using data from external fire exposure to roof tests, as per BS EN 13501-5, will be possible, coming into force by the end of 2023.
For more information email: uk@efectis.com
Images: 1
solutions for every workplace, all of which come with a minimum sevenyear guarantee.
The close relationship between product development and our factories is a huge strength for AJ Products, allowing us to stay at the forefront of new product design and maintain high quality levels while minimising our environmental footprint. With our huge range of stocked products, we can offer quick turnaround, while our bespoke solutions allow us to provide a more tailored option where required.
Our team can support you every step of the way from free-of-charge project planning and design suggestions through to delivery and installation. Our aim? To be a one-stop shop for all your workplace needs, delivering the best solutions for your business.
Images:
SUPERPLUS BLS: AN ASSURED ANCHORING SOLUTION
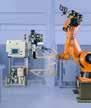

The innovative LIEBIG Superplus BLS range of heavyduty anchors from EJOT UK can deliver important cost and time savings in a wide variety of offsite and MMC projects without compromising performance.
Offsite’s key advantages of installation speed and rapid project delivery, coupled with high quality construction, can be leveraged further with Superplus BLS, because it has the potential to tick all the boxes.

Crucially, the ETA and UKTA approved anchor enables cost savings by providing more “kN per £”. This is because it is the only self-undercutting anchor that, without special tools, creates its own undercut. It works in a
slightly different way to all other types of concrete attachment products to deliver game-changing results.
Its design also enables greater flexibility to adapt to onsite challenges because it is suitable for shallow concrete depths and can be used at closer spacings or closer to the edge of the concrete than is typically possible. And not only is Superplus BLS designed for easy installation, but its modular design also means bespoke anchor lengths can be
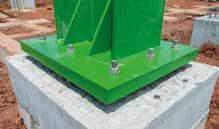
Unique market positioning. Infinite fastening solutions.
Unique means ‘the only one of its kind’
No other manufacturer of fastening solutions has the breadth of knowledge or the range of products to span market sectors that include the entire modern building envelope, heavy duty anchoring, through to advanced joining systems that can be found in high volume engineering assemblies around the world.
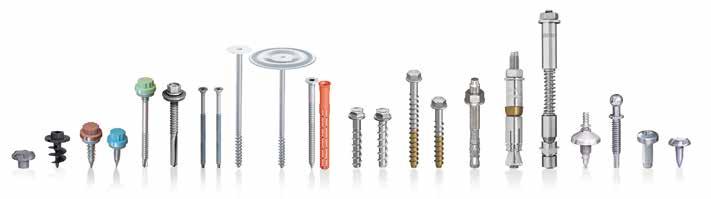
If you’re serious about volumetric construction, we’re perfectly placed to help.
manufactured in short lead times without the cost premium usually associated with such products.
For more information visit:

www.ejot.co.uk/LIEBIG_BLS
Images:

01. A typical application for LIEBIG Superplus BLS anchors
02. The self-undercutting design of Superplus BLS gives it a 'cone of influence' for greater application versatility
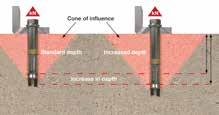
BREAKING DOWN THE BARRIERS TO SUSTAINABILITY
Client demand for environmental product data is outstripping manufacturers’ ability to provide it. Fortunately, a new approach is making Environmental Product Declaration (EPD) creation accessible for all.
Driving down the costs and complexity of EPDs
EPDs have the potential to accelerate industry-wide embodied carbon reduction, but to do so the barriers to take up need to be reduced. One Click LCA, one of the world’s most widely used construction LCA platforms, is driving down the costs of EPDs via a streamlined but fully verified process that slashes the cost and time involved in developing an EPD.
One Click LCA’s Pre-verified EPD Generator offers an end-to-end EPD publishing solution, removing the need to co-ordinate complex thirdparty verification and publishing. It is designed for LCA and EPD newcomers to make EPDs accessible for all.
Supporting the rise of low carbon concrete
Buildings and construction account for 25% of the UK’s total greenhouse gas emissions, a quarter of which comes from new materials. Pressure is growing for the construction sector to reduce emissions. In response, developers are favouring products that transparently document their environmental footprint, via an EPD.
Unfortunately, the UK is falling behind Europe in terms of EPD availability. The parliamentary Environmental Audit Committee reported in May 2022 that British firms are losing business as developers choose European products with EPDs over UK equivalents without one. Fortunately, new approaches are making EPDs more accessible for all.
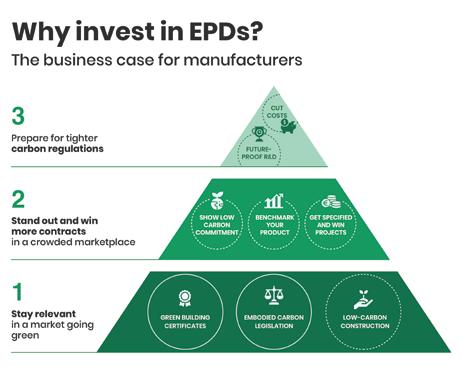
What is an EPD?
EPD is a document which transparently communicates the environmental performance of a product over its lifetime: from raw material extraction to end-of-life. EPDs support emission
reduction by enabling architects, designers and specifiers to choose the most sustainable option for their project. They also enable manufacturers to market their carbon transparency.
The demand for EPDs has accelerated with the rise of legislation setting lifecycle carbon limits for buildings. National legislation is now in place in France, Sweden and Finland, while in the UK, the updated London Plan, mandates whole lifecycle carbon assessments for major developments within the capital. In practice, this means that project owners need to calculate the lifetime impact of every element of their project, from foundation to facade, via a building lifecycle assessment. As a result, they prioritise products with EPDs. EPDs also support green building credits and certification, for example within the industry leading schemes, LEED and BREEAM.
One Click LCA’s new turnkey Concrete EPD Generator offers seamless EPD publishing, allowing users to create project or tender-based EPDs quickly and flexibly. Concrete is estimated to cause four gigatons of carbon emissions a year. Buyers know this and are looking for ways to reduce their impact. One Click LCA Concrete EPD Generator enables manufacturers to demonstrate their solution’s decarbonisation potential at the click of a button.
For more information visit: www.oneclicklca.com/pre-verifiedepd-generator and www.oneclicklca.com/concrete-epdgenerator You can also speak to us at Futurebuild 2023 on Stand F50 and see a live demo.
The Offsite Hub receives over 5,000 unique visitors per month, complemented by 42,300 newsletter subscribers, making these digital opportunities an attractive proposition for marketers planning future activity.
Prices start from just £150
Suppliers Directory
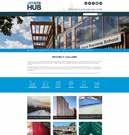


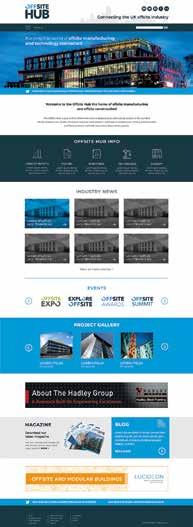
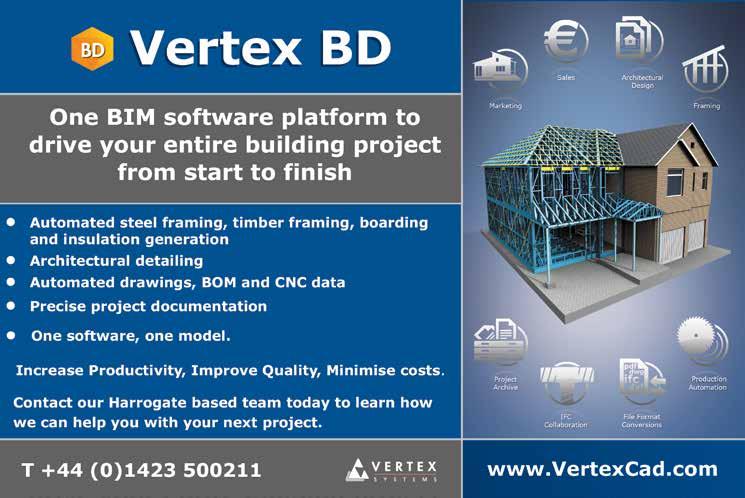
Monthly Newsletters
Video Features
If you are interested in learning more about offsite construction and the associated manufacturing processes then the following industry events may be of interest:
DATES FOR YOUR DIARY 2023
28
The groundswell of interest in engineered timber is driven by both technological advances and concern for the environment and sustainable construction practices. It is undergoing a ‘revival’ where it is used in widespread applications delivering high-quality architecture to the realisation of cutting-edge structural engineering. Experts from the structural timber sector will come together to address timber’s use in the construction industry as a versatile and natural material undergoing a contemporary design resurgence. 25
The only specialist event of its kind, Focus on Framing provides a solution for construction professionals looking to gain a greater understanding of the latest advances and best practise principles from sector experts. Through informative speakers and case study presentations the seminar will focus on the fast-track non-combustible solutions that are having a significant impact delivering outstanding buildings across all construction sectors. 26
Returning for it’s nineth year, there will be 25 categories that cover every aspect of the industry from hybrid and modular technology to engineering and installation, ensuring that all aspects of the offsite building process is celebrated - recognising the design and technology that makes these inspiring projects possible.
13 June Tall Buildings Conference
Tall Buildings Conference brings together industry leaders and pioneers, offering a wealth of knowledge and learning opportunities. Providing insight into revolutionary engineering principles, the Tall Buildings Conference gives delegates the chance to engage in invaluable networking and intelligence sharing with those at the forefront of technological building advances.
23 June Structural Timber Awards Entry Deadline
Featuring compelling examples of what can be achieved using the most natural and sustainable of materials, the 2023 Structural Timber Awards will be a celebration of not only outstanding projects and inspiring individuals, but the coming together of an industry.
19
Offsite Expo brings together those who are driving change in the construction sector. The event will play host to the leading UK and international offsite manufacturers and component suppliers over two days showcasing a broad spectrum of panelised, volumetric modular solutions, pod and prefabricated MEP solutions, as well as the latest in Digital and BIM technology.
Taking centre stage at Offsite Expo, the Offsite Awards will be a major coming together of the industry where over 500 guests will gather to celebrate ground-breaking achievements and the pioneers who are developing radical new offsite technologies, innovative product developments and landmark projects using factory-based methods.
Do
Timber continues to stand at the core of success across so many sustainable construction projects. This, combined with enhanced speed and performance benefits, are just some of the reasons for the abundance of exceptional projects. The Structural Timber Awards provide one of the most effective platforms to promote brands or companies alongside the best of the best.
you have a project that you think is worthy of winning an Offsite Construction Award?
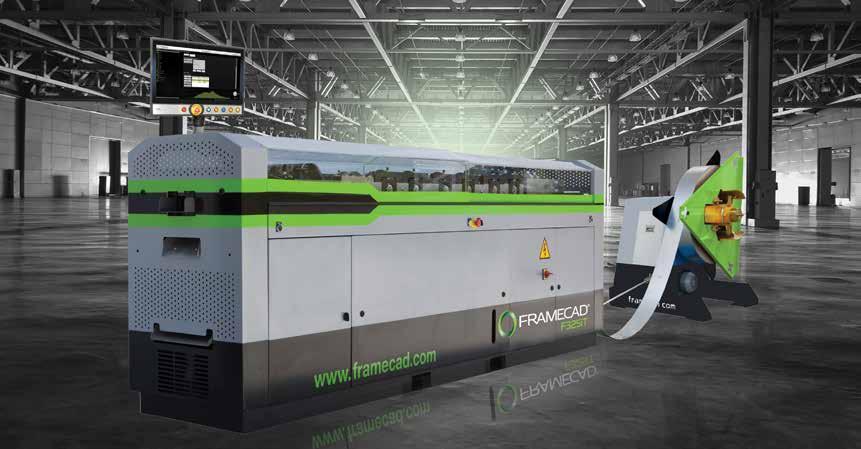

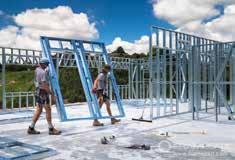
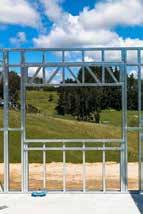
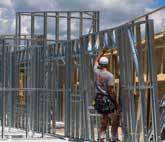
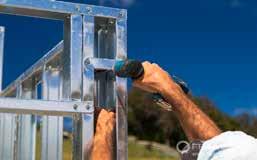
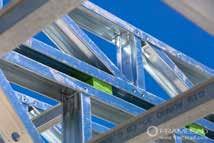
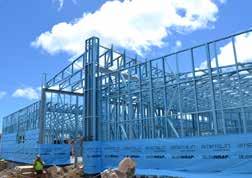
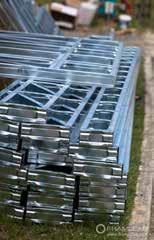

Precast Concrete Cladding leads the way in fire resilience
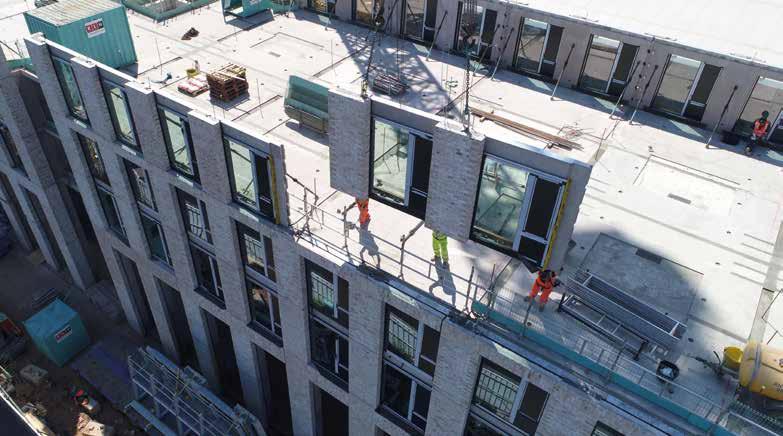
Concrete is at the cutting edge of modern methods of construction (MMC) through new technology, including innovative offsite factory manufacture and advanced onsite installation techniques.
Concrete MMC also provides additional safety benefits both during production and installation. Concrete construction protects people and property because it is A1 fire rated and does not burn.

Independent fire test demonstrates performance
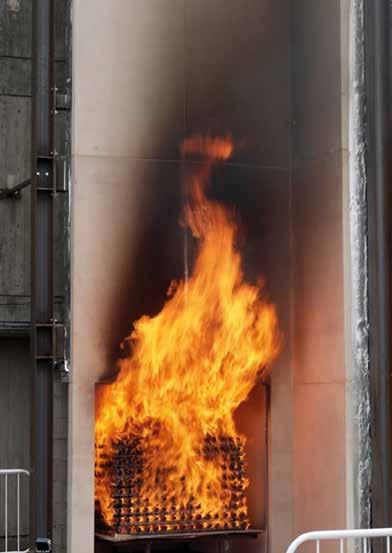
MPA Precast commissioned The Fire Protection Association to carry out a BS 8414 fire test to demonstrate the performance and robustness of concrete cladding systems. Concrete construction provides peace of mind for property and life safety.
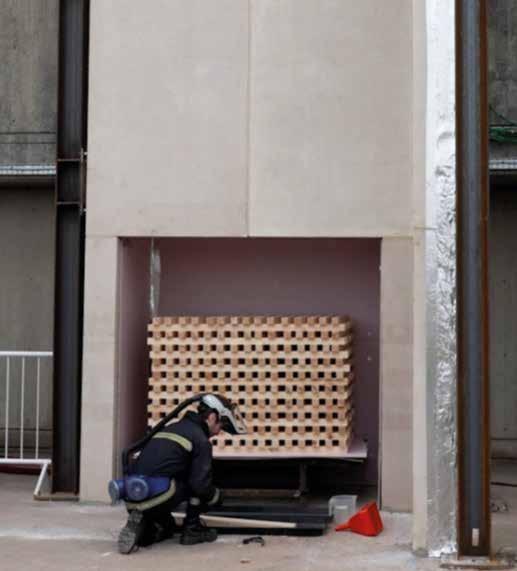
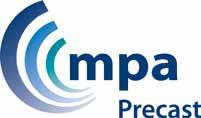
Learn more about why using concrete to protect against fire is a responsible design decision, providing long term resilience to the places we live and work in.
Concrete is non-combustible –it does not burn, you cannot set it on fire
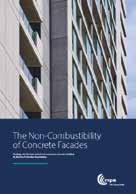
Concrete does not add fuel to a fire
Concrete does not emit any toxic fumes
Concrete does not produce smoke
Concrete has a slow rate of thermal conductivity, acting as a shield against heat READ https://www.thisisukconcrete/firetest
WATCH https://www.youtube.com/watch?v=ofmOoYd4lAg&t=5s

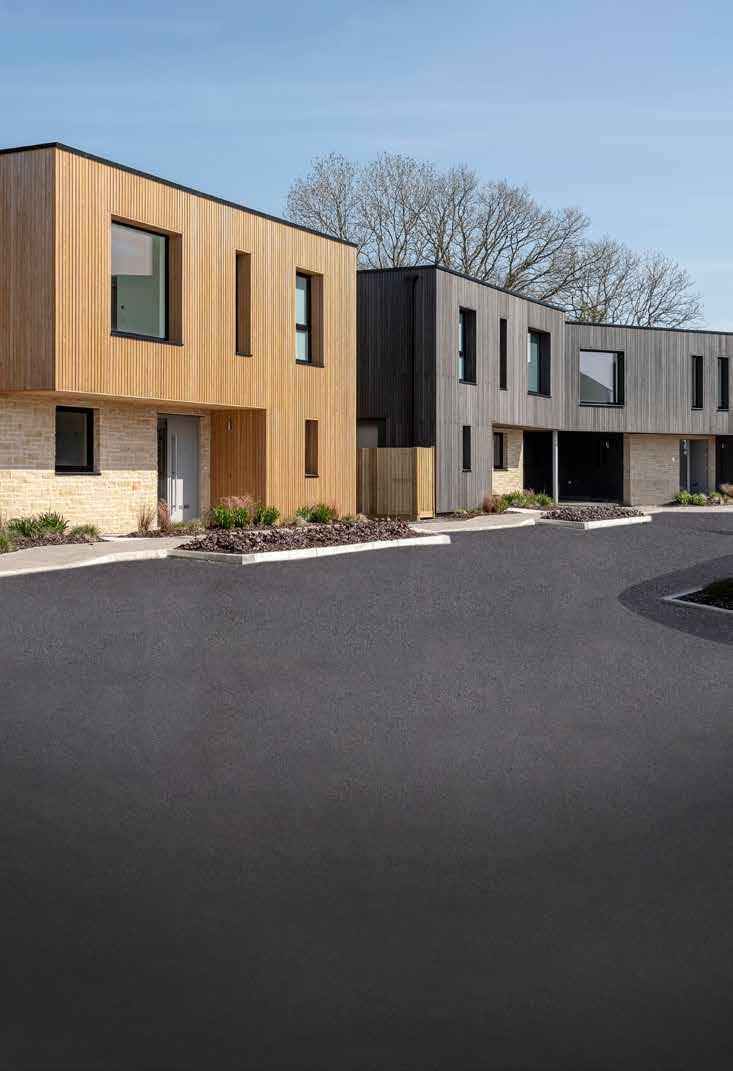


