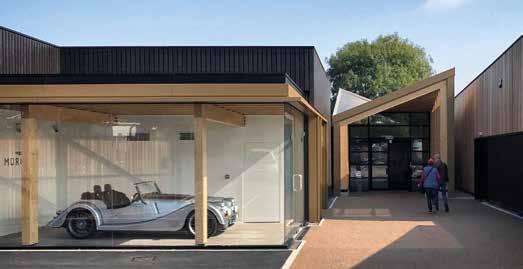
9 minute read
Driving Sustainability
CASE STUDY
DRIVING SUSTAINABILITY: MORGAN EXPERIENCE CENTRE
Hewitt Studios have repurposed a collection of ageing post-war buildings as a sustainable new visitor Experience Centre for the Morgan Motor Company in Malvern, England with timber as the perfect solution.
Hewitt Studios were invited by the Morgan Motor Company to reimagine their ageing cafe, museum and showroom spaces as an exciting new £1.8million visitor Experience Centre. The Morgan Motor Company has been making cars on the same site in Malvern England since 1914, employing generations of local craftsman to construct their cars from three reusable and recyclable core elements: ash timber, aluminium and leather.
Consistent with a brand that prides itself on ethical sourcing, natural materials, local craftsmanship and a long-lived legacy, the solution had a strong focus on sustainability – a series of low-carbon buildings designed to improve building thermal performance, increase natural daylight, reduce energy consumption, reduce surface water run-off and provide for end-oflife recycling of materials. The three new buildings all utilise prefabricated, modular timber structures which relate to the historic ash construction of the Morgan body frame. Moreover, they actually all utilise the same inexpensive, off-the-shelf industrial product (Metsä Wood Kerto LVL), which has been
1
manipulated in a number of different ways to achieve a variety of different outcomes. The building is also partly constructed using local materials, including cedar from local forests. This strategy of using a single conventional product in a number of unconventional ways delivers terrific value for Morgan, creating the impression of an expensive bespoke outcome using readily available ‘stock’ timber sections. It also creates an important legacy for the site, employing sustainably-sourced timber detailed to enable easy dismantling for re-use and/or recycling at the end of the structure’s life.
Timber is also used extensively for cladding, with easily recyclable aluminium flashings and cladding panels employed in critical weathering locations as a reference to Morgan’s chosen panel material, and that of its latest chassis. The result is a dramatic transformation of the site. The refurbished Experience Centre has a greatly reduced energy requirement, due in part to the choice of timber structure. This project has been delivered in a short window (effectively six months, allowing for a two month COVID-19 related shutdown). Morgan were instrumental in the choice of offsite timber technologies as they wanted the project to be undertaken as quickly and as safely as possible and saw prefabrication as the solution to this. As a car manufacturer they are accustomed to efficient production methods (e.g. zero-waste, just in time,
2

etc.) and very much wanted this project to adopt a similar approach on this project. The innovative offsite approach (seldom employed on refurbishment projects like this) has resulted in a significantly accelerated and de-risked construction process, delivering significant benefit for the client on a busy site which has remained operational throughout the process. The rapid assembly of the LVL frames quickly created dry workshop conditions on site, enabling trades to work safely undercover from the earliest possible opportunity. The timber structure also meant that no dangerous site welding was required, only simple bolted connections. The prefabricated timber frame and aluminium flashings meant that site waste was minimised, with the other main materials (e.g. plywood cladding, acoustic panels, polycarbonate, etc.) utilised in standard modules to reduce cutting waste. Maintenance requirements for the Morgan estate have been significantly reduced through the project.
For more information visit: www.hewittstudios.co.uk www.constructionaltimber.com
Images:
01-02. Consistent with a brand that prides itself on ethical sourcing, natural materials and local craftsmanship the solution had a strong focus on precision and sustainability. Courtesy Morgan Motor Company/Hewitt Studios LLP
DELIVERING SWEDISH STYLE
AND SUSTAINABILITY
Although BoKlok may be an unfamiliar brand name in the UK, its joint owners Skanska and IKEA are familiar faces to most of us. As Graeme Culliton, BoKlok Managing Director and Country Manager told us, things are about to change.
1

BoKlok has huge experience in developing and manufacturing homes in the Nordic region and to date has developed around 12,000 homes in Sweden, Finland and Norway. The homebuilding joint venture sees homes built primarily from timber, using a smart, industrialised factory process. The homes are completed offsite in a safe and dry precision environment enabling high-quality and predictable costs. It is now aiming to set new customer satisfaction standards in the UK market. What drew it to the UK and what can Swedish expertise deliver to the UK housing market? “Simply put the need for low cost home ownership in the UK and the opportunity to make a difference,” says Graeme. “We have been delivering this model in the Nordics for 20 years. Our experience in delivering modular homes is derived from the fact we own our own factory but also manufacture homes with manufacturing partners. The need for modern methods of construction (MMC) and the support from central and local government was also key to knowing this was the right time for this.”
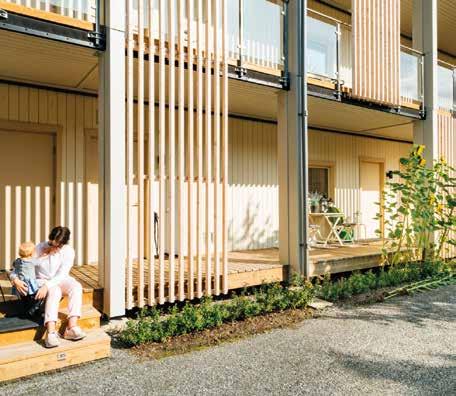
How does Skanska and IKEA work together to create this housing model and the wide and potentially endless customer interior requirements? “IKEA understand how people live, great design and industrialisation,” says Graeme. “Skanska understand construction, logistics and development. Together a powerful combination. Both organisations have high ambitions and achievements
2
in sustainability. Together all this drives the way we think about our customer, the homes we design but also delivering a low cost home. All our homes have an IKEA kitchen as standard, but customers can also work on their own interior design with IKEA, if they choose. This is part of our sales process.” The system is a volumetric timber system involved with most of the timber sourced from Sweden and Finland. BoKlok has worked closely with NHBC and BOPAS (Building Offsite Property Assurance Scheme) to ensure compliance with UK regulations and requirements. A panellised system was never considered. “It’s what we know and we know it works,” says Graeme.
To help deliver part of its first product offering in the UK, BoKlok has appointed technology-driven modular housing manufacturer TopHat on a five-year contract. This will see TopHat work with BoKlok to manufacture two and three-bedroom houses.
“We are delighted to be working with TopHat, says Graeme. “We share the same ambition to bring innovation and sustainability to the UK housing market, which means attractive and good quality homes for people on average incomes. Our two companies complement one another well, with TopHat bringing its high levels of automated manufacturing expertise. As we venture into the UK, we believe that TopHat will contribute to our long-term vision and success, to provide quality, low-cost homes, using sustainable materials and modern methods of construction.”
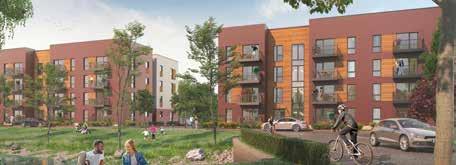
TopHat is a technology-driven modular housing manufacturer, aiming to revolutionise the digital construction industry, from housebuilding to commercial property. Founded in 2016 and commencing production in early 2018 at its state-of-theart manufacturing facility in South Derbyshire, this offers a huge opportunity to boost the profile of volumetric timber homes. “We wanted a UK supplier and because timber is at the heart of our business, as the most sustainable building product, they were at the top of the list. Once we engaged with TopHat we could see that they shared our values and had invested significantly in their manufacturing facility. It was the most
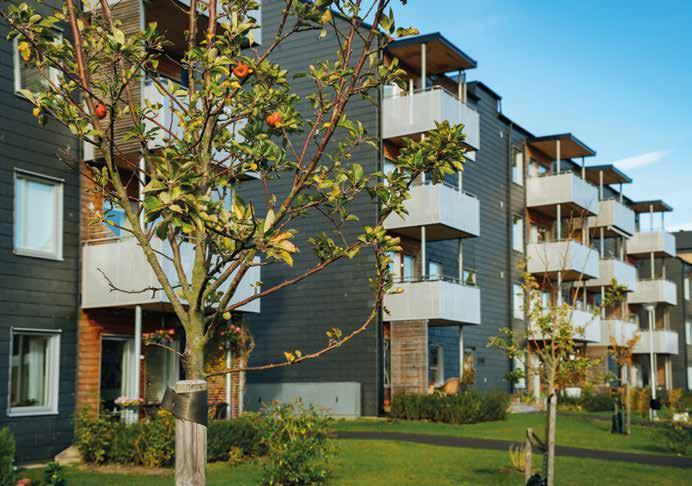
3
4
advanced that we saw in the UK by some way. We also met with their investors and could see a commitment for the long term.” “Modular housebuilding will be central to addressing the UK’s housing crisis by providing modern, desirable and connected housing far more quickly than traditional methods,” says Kate Davies, Non-Executive Director of TopHat. “TopHat is in a strong position to lead the sector. Not only does its technology and manufacturing platform enable TopHat to produce homes of outstanding quality at low cost, but also its approach to design reshapes perceptions of what modular homes look like and feel like to live in.”
The first BoKlok community will be in Bristol at Airport Road. Bristol City Council, who owns the site, has committed to pursuing the development of this partnership with BoKlok as part of the five-year Bristol Housing Festival which is trialling innovative offsite housing solutions across the city. Jez Sweetland, Bristol Housing Festival’s Project Director, said: “The festival is all about reimagining new and better ways to live in our cities. BoKlok provide creative solutions with a fantastic track record of creating great homes and strong communities, we are really thrilled to be working with them.” The proposed development will consist of 173 homes – 77 two-storey houses and 96 flats built under the BoKlok brand. “BoKlok have been working with Bristol Council and the Housing Festival for the past two years, says Graeme. “They are fantastic partners to work with and we share the vision for the city in providing great sustainable homes for people that really need it. This made our decision to focus within the South West a very easy one, when we planned the launch of the business. We expect to start work at Airport Rd in Bristol by the end of the year. First sales will be in Spring/Summer of 2021. We now have six sites across the south of the UK in various stages of development.
“Broadly our homes will be delivered in half the time of traditional forms of construction. Our ambition is to bring zero carbon homes to UK a lot quicker than 30 years. Our building system and design makes a big step toward zero carbon, but we will move our focus to this once we have delivered our first developments and timber is an essential part of achieving our carbon targets.”
For more information visit:
www.boklok.co.uk www.tophat.io
Images:
01. Graeme Culliton, Managing Director and Country Manager, BoKlok 02-05. Planned developments will provide a range of housing options with timber at the core of the design
5
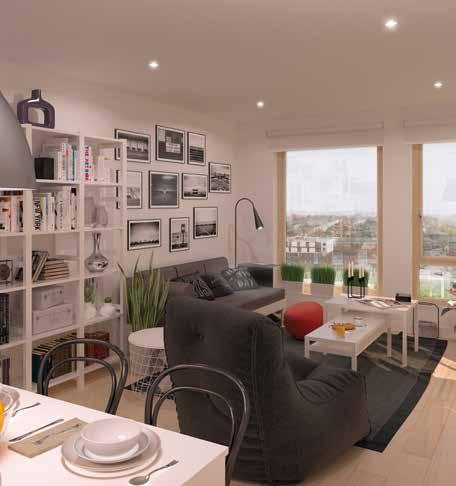
NHBC WELCOMES BOKLOK TO ITS NEW MMC ACCEPTANCE SCHEME
NHBC has announced that BoKlok’s volumetric timber frame system – BoKlok Flex UK – has been officially welcomed to NHBC Accepts. NHBC Accepts is as allinclusive, end-to-end service launched this summer, that will help to build confidence in innovative construction and enable MMC systems to be fast-tracked for NHBC warranty.
NHBC’s, Innovation Manager, Richard Lankshear said: “Following a thorough review process we are delighted to welcome BoKlok to NHBC Accepts. An NHBC Accepts certificate is a way of demonstrating that innovative products or systems have already been reviewed by NHBC thus reducing the risk of delays on-site. NHBC Accepts will play a critical role in ensuring developers, manufacturers, lenders and consumers have faith and confidence in MMC quality as the industry delivers more innovative new homes for the country.”
As part of the new service, a detailed and robust technical review at key stages has resulted in the provision of a certificate (and acceptance for NHBC warranty), usage licence for a bespoke NHBC Accepts logo and listing on the NHBC Accepts web pages alongside other accepted systems.
Noel Sheehan, BoKlok Housing Director adds: “We are very pleased to have been given a seal of approval for NHBC Accepts. We use quality materials and build with well-proven methods to ensure sustainable homes. We hope that this additional accreditation will provide further confidence in our home development to our customers and the wider industry.”