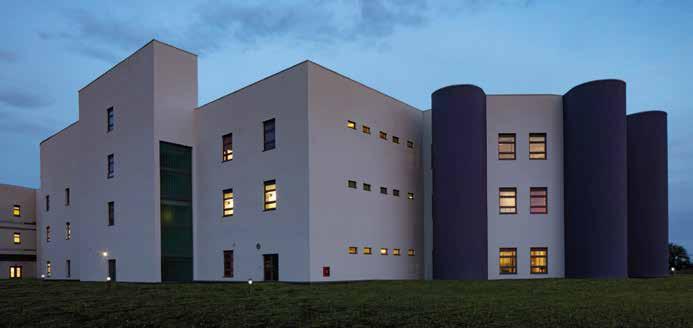
4 minute read
Providing a Better Hospital Estate
PROVIDING A BETTER
HOSPITAL ESTATE
The McAvoy Group used offsite methods to deliver a £15million contract for the construction of a new wing at Northumbria Specialist Emergency Care Hospital, with the 6,500sq m three-storey building having to integrate seamlessly with the existing hospital.
Northumbria Healthcare had previous experience of modular construction on other sites and fully appreciated how the speed of offsite manufacture can impact positively on patient care. The Trust had established a clinical need for a purpose-designed ambulatory care facility to help decompress a very busy emergency department and ensure patients are seen quickly by the most appropriate healthcare professional. This was a highly complex project on a live hospital site that pushed the boundaries of offsite construction. McAvoy integrated the new wing with the design of the existing traditionally-built hospital and used offsite construction to reduce the build programme by 50% to less than 12 months. This helped the Trust to meet the rising demand for acute patient services. The approach achieved exceptional value for money and met the Trust’s stringent quality standards. The new wing was constructed using an advanced offsite solution and featured a number of innovations. It used larger, bespoke modules up to 14.85m long, specially engineered to provide a structural flooring solution that seamlessly integrated with the existing building. This met the key requirement for efficient patient flows, removing the need for ramps and steps.
The first floor was fitted out as part of this contract to accommodate one of the UK’s first purpose-designed ambulatory care units, with the other two floors fitted out in the next phase of the development. McAvoy developed a hybrid solution which incorporated both offsite and in-situ building methods and maximised fit-out in the factory to enhance quality and reduce disruption to patient care.
1
The ambulatory care unit provides medical, surgical and gynaecology care and a fracture clinic in a relaxed environment. It allows up to 150 patients to be treated the same day across four specialisms without the need for hospital admission. This has helped to decongest the emergency department, allowing patients to be seen by the most appropriate clinician earlier and offering an enhanced service to the community. The larger, bespoke modules, engineered to provide a structural flooring solution seamlessly integrate with the existing building. This met the key requirement for efficient patient flows, removing the need for ramps and steps. Mechanical ventilation, heating and cooling systems were installed in the ceiling voids in the factory – an industry first in the healthcare sector.
The new wing replicated the appearance of the existing hospital which opened in 2015. It has a faceted external facade to create curved ends to the wing and is finished in blue and white render. This hybrid construction solution has a three-storey offsite structure with an in-situ built curved link on each floor, a roof-top plant room and full-height stair towers. It complies with all relevant HTM and HBN requirements. P+HS Architects assessed the clinical flows with the user group to produce a schedule of accommodation before developing the detailed design. Planning was achieved soon after, and McAvoy started foundations at the same time as the manufacture of the building structure began at the McAvoy factory. James Almond, Director, P+HS says: “This project is unprecedented in its scale and complexity, delivered in such a short timescale. We estimate it would have taken around 18 months onsite to build this traditionally. With an innovative offsite solution and a completely focused client, design and delivery team, it was operational nine months earlier and well ahead of the busy winter period. This speed of construction was a critical benefit to the Trust – ensuring less on-site disruption to patient care, reduced waiting times, and a faster return on investment.”
Flexibility for future growth had to be designed into the project from the outset. The facilities are constructed around a central corridor to which a further wing can be added at a later date if required, mirroring the recent construction. The internal space was also designed to accommodate changing needs. The roof was structured to allow a light well to be constructed in the future to bring light deep into the upper floor of the building, creating greater flexibility in the range of options for this space. This would allow more external wall area and natural light for an additional ward if required. The plant room was sized to accommodate two further air handling units for when the two other floors of the new wing are fitted out in the next phase, meeting the future demands of the building. The facility was designed collaboratively with stakeholders via a clinical user group led by P+HS and
2
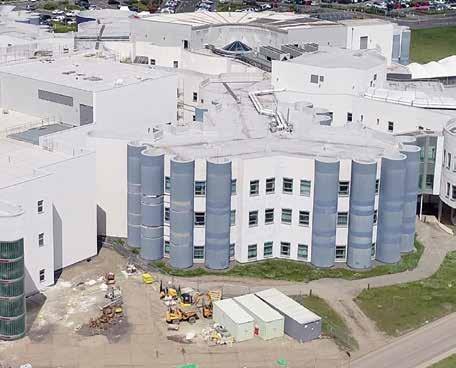
made up of around 25 healthcare professionals – clinicians, nurses and facilities/estates managers, who met weekly to develop the design. The users also visited the McAvoy factory to view the building in manufacture. Dr Eliot Sykes, Clinical Director, says: “Users were engaged from the outset and had the freedom to express their views on the design development. The building was clinically designed and led and there was fantastic collaboration
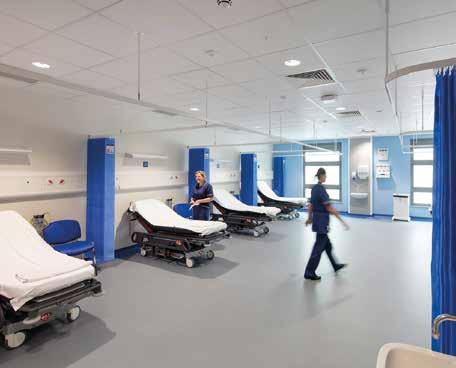
3
and engagement across the clinical, estates, design, and construction teams. This strong relationship at every level was key to the project’s success.”
For more information visit:
www.mcavoygroup.com
Images:
01-03. This was a highly complex project on a live hospital site that pushed the boundaries of offsite construction. Courtesy McAvoy Group