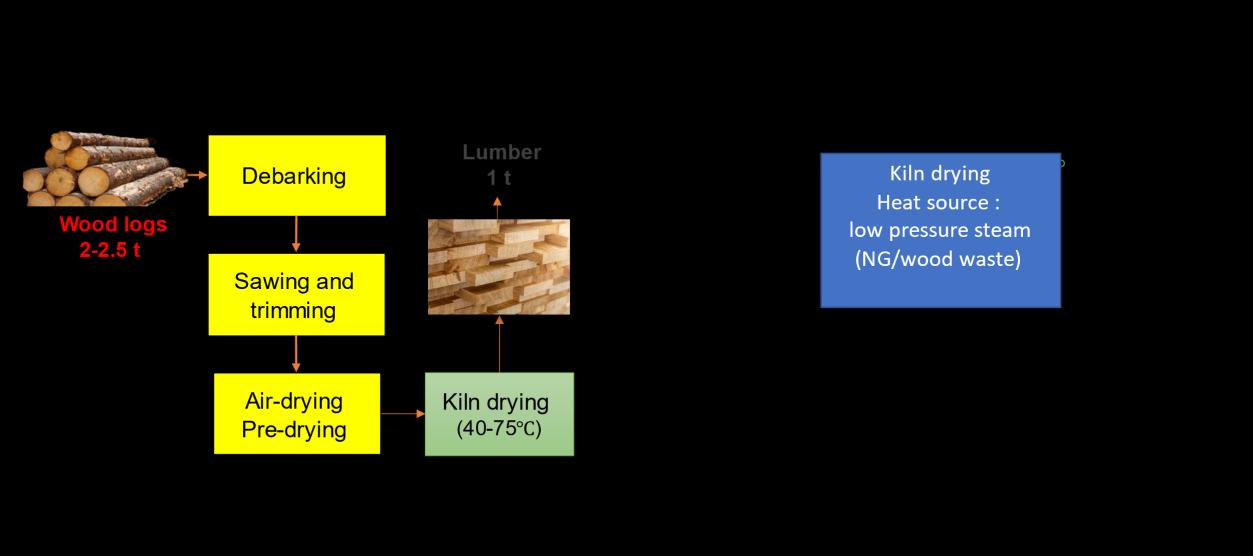
5 minute read
2.3.3 Pulp and paper industry
Figure 13. Lumber processing overview, (a) simplified block flow diagram showing key heating methods and their relative temperature/ energy intensity, (b) for medium temperature heating.
2.3.3 Pulp and paper industry
Advertisement
2.3.3.1 Background The pulp and paper industry accounts for 29% of the total volume of harvested logs in 2018-2019 (6 million cubic metres) [24]. According to ANZSIC, the pulp and paper industry is categorised under group 15 of the manufacturing subdivision. Figure 14 provides the locations of Australia’s pulp and paper mills [2].The primary heat users in this sector are across 44 sites, which mostly use up to 0.5 PJ per year [2, 6] although several large pulp/paper factories use more than 0.5 PJ. More details are provided in Figure 15 [2, 6].
Figure 14. Location of pulp and paper manufacturing industries [2]
The pulp and paper industry produces a wide range of products, including various types of pulp, photocopier papers, packaging papers, newsprint, and tissue. In 2018-2019, 4 million cubic metres of wood logs were used in domestic pulp and paper, and industry sales were more than 10.5 billion AUD,
which accounts for 40% of total sales in the wood and wood-based products sector [24]. According to literature and the recent AES report, it can be estimated that pulp and paper industry demand is around 21.2 PJ/year in Australia [2]. The two distinct processes form the basis of papermaking: pulping (converting wood to an intermediate pulp product for shipment) and paper making (producing thin sheets). Although the process is sometimes integrated for large factories, non-integrated paper factories in Australia are more numerous, so they are treated as two separate processes.
Chemical pulping (dominated by the kraft process) uses the highest energy in the papermaking supply chain, hence its inclusion here; however, it also produces a large amount of by-product (black liquor) that is used as an energy source. In contrast, mechanical pulping – used for newsprint and low-cost products – mostly uses electrical energy and provides low-quality fibres. Semi-chemical processing is a further pulping process which applies chemicals to mechanical pulping, reducing thermal energy requirements compared to both processes, but it introduces complexity in environmental management due to the absence of chemical recovery in waste streams [40]. Australia has three large mills that produce pulp from wood chip, including Maryvale (VIC), Boyer (TAS) and Tumut (NSW), which are all located in regional areas [2]. Note, Boyer is a newsprint mill which uses mechanical pulping process, which is substantially different from chemical processes.
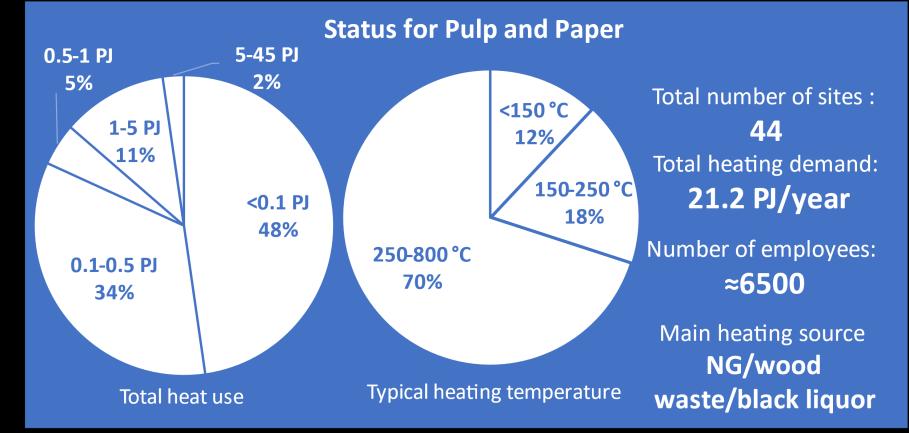
Figure 15. Status for pulp and paper [2, 6], ANZSIC Subdivision 15, under division C (manufacturing), groups 151 and 152
2.3.3.2 Typical process flow diagram and heating demand in kraft chemical pulping (Maryvale and Tumut) This report focuses on kraft pulping, which is most common in the Australian pulp industry due to the high-quality pulp produced [7]. Figure 16 provides a flow diagram of the pulping process [2, 7, 40-44]. The most important steps are as follows:
Debarking (electricity) Evaporation (100-1100 °C)
Pulp digestion (65-175 °C) Pulp drying (40-55 °C)
Pulp washing (60-70 °C) Lime kiln (340-1200 °C)
Pulp bleaching (30-90 °C)
It should be mentioned that pulp bleaching is used if a white product is desired (Maryvale, not Tumut). The bleached pulp can be forwarded to the pulp drying process for transport to a paper mill, or retained as a wet slurry for paper making in the case of an integrated plant.
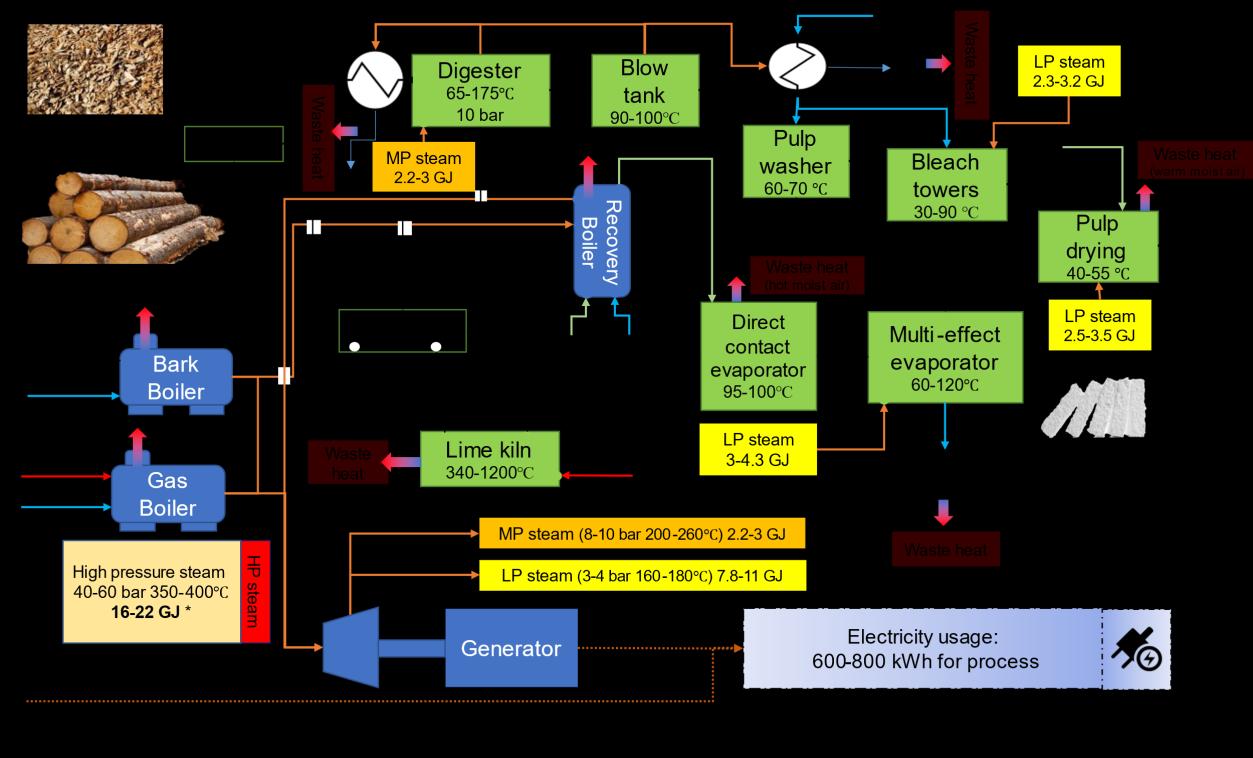
Figure 16. General process diagram for kraft chemical pulping.
Evaporation, pulp drying, digestion and bleaching are the main heating consumers in kraft pulping. The typical energy consumption for producing 1 tonne of bleached pulp is 7.5-10.5 GJ/t, increasing to 10-14 GJ/t by applying pulp drying [40-43]. In addition, a significant amount of energy (≈1.2 GJ/t pulp) is also required for the lime kiln, mostly supplied by natural gas in the conventional rotary kilns [42]. In contrast, the repulping of wastepaper requires considerably less energy, as 0.06-0.35 GJ/t is needed for producing the recovered pulp for different products (e.g., newsprint, sanitary items, corrugated board, and boxboard) [45]. The ARENA report [2] indicates a high share of high temperature heating (≈70%), potentially referring to the high temperature steam in the CHP plant in pulp mills. Note that a large amount of process heating temperatures in the sector is less than 250 °C, with a substantial proportion of natural gas being used in boilers in paper mills. 2.3.3.3 Opportunities in pulping Figure 17 provides a simplified overview of the kraft chemical pulping in relation to energy and temperature demand. The main external fuel source for the process is natural gas, and wood wastes such as bark and sawdust are typically sourced from local sawmills [2]. These fuels are mostly used in boilers (to generate steam for electricity and heat), and in a lime kiln. Some mills use natural gas as a supplementary fuel in the recovery boiler instead of a separate gas-fired conventional boiler. Black liquor combustion in the recovery boiler can supply more than 80% of heating demand, although additional fossil fuel is required (e.g., for generating electricity). For example, Maryvale Mill can only supply 58% of its total energy demand from renewable energy and is the largest industrial user of natural gas in Victoria [46]. Australian Paper and SUEZ recently developed an 600 million AUD project to supply the rest of the energy using a municipal waste gasification plant [47]. However, the necessity for process efficiency improvement and final energy consumption reduction remains. Improving the efficiency, reducing kiln waste heat and using the best available techniques can reduce the total heating consumption, increasing the potential for electricity production and reducing fossil fuel consumption. Additionally, the European Commission recently discussed available techniques and state-of-the-art technologies in the pulp and paper sector [40].
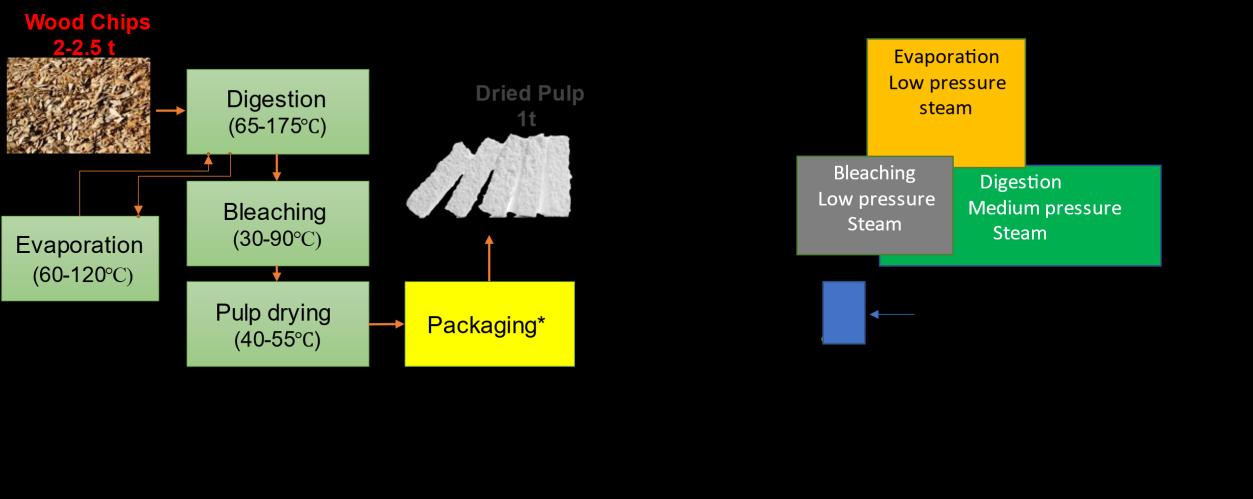
Figure 17. Kraft pulping overview, (a) simplified block flow diagram showing key heating consumers and their relative temperature/ energy intensity, (b) for medium temperature heating.
2.3.3.4 Process flow diagram for papermaking Figure 18 provides a flow diagram of the papermaking process [40, 42, 48-52]. The papermaking could be in an integrated site (such as Maryvale and Tumut) or separated (essentially all tissue/toilet paper manufacturers, which are numerous). There are many more paper/tissue factories than pulp factories in Australia. The most important steps are as follows:
Stock preparation (40-100 °C) Drying paper (70-90 °C)
Forming paper (no heating) Finishing (no heating)
Pressing paper (40-50 °C)
The stock preparation stage is mostly a mechanical process [51] to make pulp from solid bales into a slurry in the correct proportions, which varies significantly with the intended final product. However, it only uses 8-16% of heating energy for some processes such as dispersion [42, 49]. The papermaking from pulp needs almost 4.5-6 GJ/t of dried paper, largely for drying [41, 42, 45].
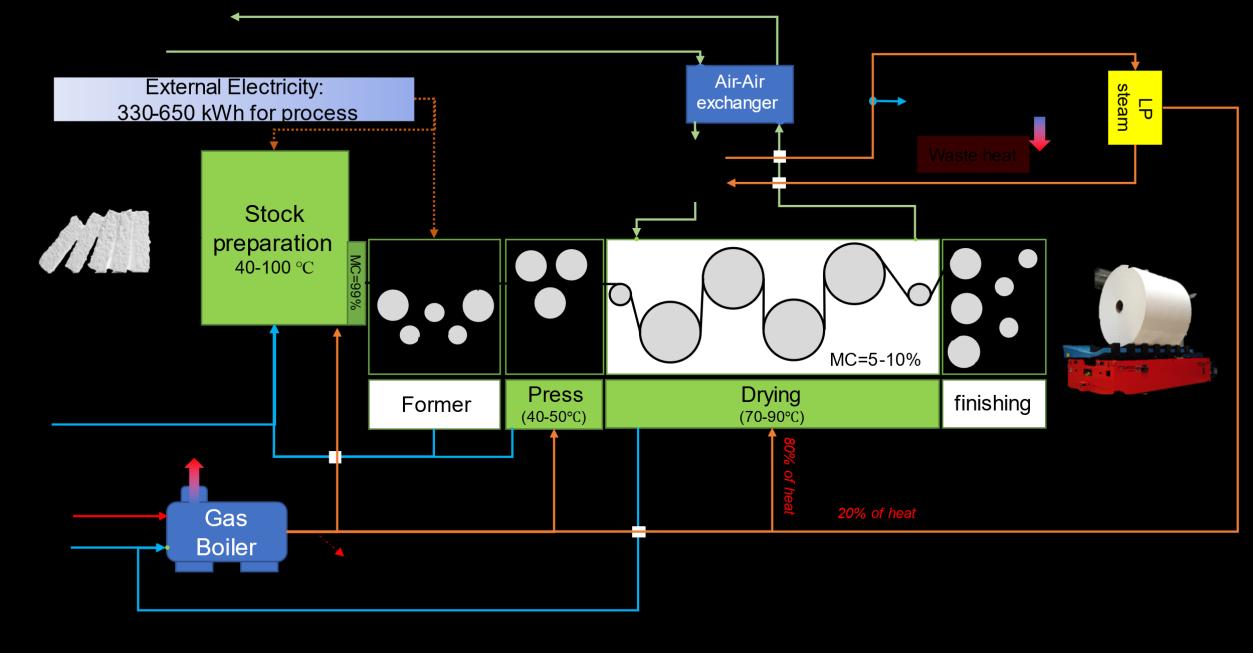
Figure 18. General process diagram for paper making.