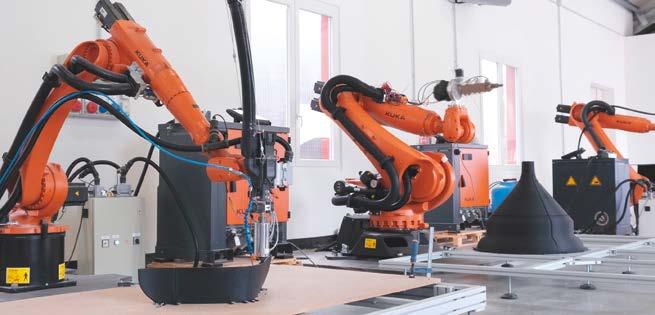
18 minute read
stampa 3D Caracol accelera l’innovazione
il sistema robotico proprietario sviluppato da Caracol s.r.l. Nel suo spazio a Lomazzo (Como)
CARACOL ACCELERA L’INNOVAZIONE DELL’INDUSTRY 4.0, PUNTANDO AD EFFICIENZA, QUALITÀ E SOSTENIBILITÀ
CARACOL È UNO ONE-STOP-PARTNER PER I SERVIZI AVANZATI DI ADDITIVE MANUFACTURING PER AZIENDE IN DIVERSI SETTORI INDUSTRIALI. LAVORANDO CON DIVERSI CLIENTI IN SETTORI COME AUTOMOTIVE, MOTORSPORT, AEROSPAZIO E DIFESA, MACCHINARI INDUSTRIALI, DISPOSITIVI MEDICI, DESIGN E ARCHITETTURA, CARACOL OFFRE SOLUZIONI CUSTOMIZZATE PER RISPONDERE ALLE LORO ESIGENZE
di Francesco De Stefano e Violetta Nespolo
CCaracol va oltre ai tradizionali limiti della stampa 3D combinando l’expertise nel generative design e manifattura additiva, con la conoscenza del settore industriale e manifatturiero, per produrre componenti per applicazioni performanti, geometrie articolate e pezzi di grandi dimensioni. Grazie all’ampio know-how sviluppato e alle partnership strategiche sviluppate con produttori di materiali, l’azienda è capace di processare un’ampia gamma di materiali, da tecnopolimeri ad alta performance, rinforzati con fibre (e.g., carbonio, vetro) a materiali da fonti di riciclo, andando anche rigenerare scarti produttivi dei clienti per produrre nuovi componenti. Inoltre, la vasta serie di tecnologie che include tra le migliori stampanti 3D industriali e la tecnologia robotica proprietaria sviluppata in-house, permettono a Caracol di offrire soluzioni che massimizzano l’efficacia e migliorano la performance dei prodotti dei propri clienti.
Ciò che caratterizza Caracol è la flessibilità con cui si approccia alla risoluzione dei problemi dei propri clienti. L’azienda infatti ha sviluppato una varietà di servizi chiave che spaziano dal design per additive manufacturing, alla ottimizzazione topologica dei componenti, dalla produzione in linea parti finite senza limiti di scala grazie alla tecno-
logia robotica proprietaria, dallo sviluppo di prototipi funzionali dalle piccole alle grandissime dimensioni, all’internalizzazione delle tecnologie di stampa 3D nei centri produttivi dei suoi clienti, offrendo poi il proprio supporto con training e workshop.
Caracol vuole rivoluzionare l’attuale sistema produttivo, accompagnando le aziende manifatturiere nel trovare soluzioni più efficienti ed innovative, che permettano il raggiungimento di un futuro più sostenibile
La tecnologia
All’interno del suo capannone a Lomazzo, Caracol, sta dando vita al primo cluster robotico di manifattura 4.0 in Italia.
Con i quattro sistemi robotici proprietari installati nella propria sede, Caracol ha sviluppato una tecnologia capace di produrre applicazioni avanzate, con materiali altamente performanti, di grandi dimensioni per clienti come Leonardo, Lamborghini, Maire Tecnimont e FCA.
Il cluster robotico proprietario di Caracol è un sistema che permette di andare oltre ai vantaggi e ai limiti che tradizionalmente derivano dalla produzione di componenti in additive manufacturing (e.g., customizzazione, riduzione costi, tempi di produzione, e performance). Infatti, la tecnologia brevettata consente di stampare componenti nell’ordine dei metri di grandezza, geometrie complesse e una vasta gamma di materiali: da tecnopolimeri avanzati a materiali da fonti di riciclo.
“Grazie all’utilizzo del nostro sistema robotico proprietario siamo in grado di andare a sostituire tecniche di produzione tradizionali, andando a risolvere dei problemi fondamentali per i nostri clienti. Come, ad esempio, andando a ridurre l’impatto della manodopera sulla produzione delle loro applicazioni o andando completamente ad eliminare la necessità di utilizzare tooling per la produzione, ed anche il materiale di scarto,” dice Francesco De Stefano, CEO di Caracol.
Il sistema brevettato da Caracol permette anche di andare incontro agli obiettivi di efficienza e sostenibilità che cercano le aziende. La tecnologia è stata studiare per massimizzare gli aspetti di sostenibilità che caratterizzano le soluzioni di produzioni di stampa 3D: dalla flessibilità della produzione attivabile on-demand che elimina la necessità di avere magazzini di componenti stoccati, alla possibilità di produrre senza l’utilizzo di stampi e accessori aggiuntivi, fino alla capacità della tecnologia di produrre generando zero scarti. Inoltre, il know-how aziendale lato design e ingegnerizzazione per la manifattura additiva permettono di andare ad ottimizzare i componenti per un utilizzo di quantità minori di materiale e tempi di produzione ridotti.
Il sistema di Caracol viene alimentata con polimeri in formato pellet, non necessitando quindi l’utilizzo di materiali ulteriormente processati e filati, e quindi andando ad aumentare ulteriormente i risparmi di costi e materiale in fase produttiva. Caracol ha pensato anche di introdurre nel suo centro produttivo, un mulino per macinare eventuali componenti a cui si vuole dare una nuova vita, scarti di produzione o componenti prodotti che mostrano difetti, ultimando appieno la capacità dell’azienda di attivare dei circoli virtuosi di economia circolare – per sé e per i suoi clienti. Infine, grazie al forte network di partnership sviluppate con produttori di materiali, Caracol ha la possibilità di customizzare il materiale per le loro necessità, con blend di tecnopolimeri e fibre in percentuali diverse.
Storia & futuro
La start-up è stata lanciata circa quattro anni fa con l’obiettivo visionario dei suoi founder di rivoluzionare il sistema produttivo tradizionale, sfruttando la tecnologia 3D ma andando oltre ai suoi limiti. Partita dall’insediamento nell’Innovation Hub di ComoNext, Caracol ha continuato a duplicare il proprio fatturato anno per anno, per continuare ad investire sul proprio R&D. Lavora con i bracci robotici armati di teste d’estrusione brevettate e oltre 27 tra le migliori stampanti 3D industriali sul mercato per lavorare con tecnopolimeri più performanti sul mercato.
“Siamo partiti dall’immaginare una nuova tecnologia ed un nuovo approccio produttivo. Oggi, che sta diventando realtà, le nostre sfide per il futuro sono quelle di andare a scalare il nostro modello di produzione diffusa e sostenibile su nuovi mercati, ed andare ad industrializzare le nostre soluzioni, secondo i requisiti certificativi richiesti dai nostri clienti,” dice Francesco De Stefano, CEO di Caracol.
Oltre a continuare la ricerca sui materiali, per andare a stampare tecnopolimeri rinforzati con fibre di carbonio sempre più avanzati, e su il perfezionamento ed efficientamento del suo sistema, attualmente Caracol sta espandendo la propria capacità produttiva e al contempo lavorando per andare a certificare l’intera linea.
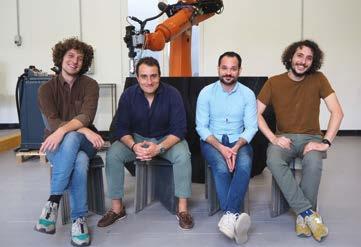
QUATTRO FOUNDER DI CARACOL S.R.L., DA SINISTRA: GIOVANNI AVALLONE (Head of Innovation), FRANCESCO DE STEFANO (CEO), JACOPO GERVASINI (CFO), PAOLO CASSIS (Head of Operations)

Strutture Circular di Grandi Dimensioni
Esempi di casi studio
Alettone per Macchina da Corsa
Il settore automotive è sempre alla ricerca di componenti più resistenti, leggeri ed affidabili, capaci di migliorare la performance dei veicoli che sviluppano. Questo è soprattutto vero per quanto riguarda il settore del motorsport e le macchine da corsa.
Caracol ha quindi deciso di applicare la sua tecnologia robotica di manifattura per portare la sua innovazione a questo settore, dando evidenza tangibile di come la stampa 3D possa segnare una svolta nel processo produttivo di questo settore.
Per fare ciò abbiamo lavorato su uno spoiler per una macchina da corsa per un leader nel settore. Abbiamo ridisegnato l’alettone, ottimizzandolo per la produzione in additive manufacturing. Combinando la nostra tecnologia robotica che permette di stampare su larga scala alcuni dei più performanti tecnopolimeri sul mercato, anche rinforzati con fibre come carbonio e vetro. Lo spoiler è stato prodotto in PA12, additivato con fibra di carbonio, un polimero che può resistere fino a 240°c, ed in seguito laminato in fibra di carbonio per garantire la massima resistenza e conformità con gli standard richiesti dal settore automotive.
La produzione del componente ha impiegato solamente 72 ore, dalla stampa alla laminazione, andando a ridurre il tempo notevolmente rispetto al mese richiesto con i metodi tradizionali. Inoltre, il componente finale aveva un peso ridotto di circa 1 kg rispetto alla versione originale, migliorando notevolmente la performance finale.
3D Bar
La tecnologia di Caracol permette anche di processare materiali derivanti da fonti di riciclo, reimmettendo in produzione gli scarti produttivi. Un progetto che ha affermato la tecnologia di Caracol sul tema circular economy è stato sicuramente lo sviluppo del 3D Bar – il primo bar, di oltre due metri, completo di tavoli e sgabelli, ad essere interamente stampato in 3D, grazie al sistema robotico proprietario di Caracol.
Le geometrie del bancone sono state concepite grazie a processi di generative design, permettendo di dar vita a forme organiche, avvolgenti e naturali su tutti gli elementi che componevano il bar presentato alla Milano Design Week.
Il bancone del bar è stato completamente stampato da PLA riciclato, recuperato dagli scarti della produzione di bicchierini usa e getta per il caffè di Flo s.p.a.. Le caratteristiche della tecnologia poi hanno permesso di produrre generando zero scarti. Inoltre, questo bar può essere interamente riciclato per poi produrre nuove applicazioni, dando potenzialmente una vita infinita alla materia prima e rendendo questo progetto un esempio virtuoso di innovazione e sostenibilità.
Questo progetto è stato poi ulteriormente sviluppato in una nuova versione per Maire Tecnimont, leader nel settore energy. Per loro sono stati sviluppati una serie di arredi modulari e custom, andando incontro alla loro esigenza di flessibilità, riciclando il materiale di scarto produttivo generato dalla loro azienda NextChem MyReplast Industries. Processando il loro polipropilene insieme a fibra di vetro è stato possibile dare maggiore solidità alle applicazioni prodotte. Oltre alle caratteristiche di sostenibilità e dimensione la tecnologia di Caracol assicura elevati standard qualitativi, di precisione, compattezza e resilienza dei manufatti prodotti.
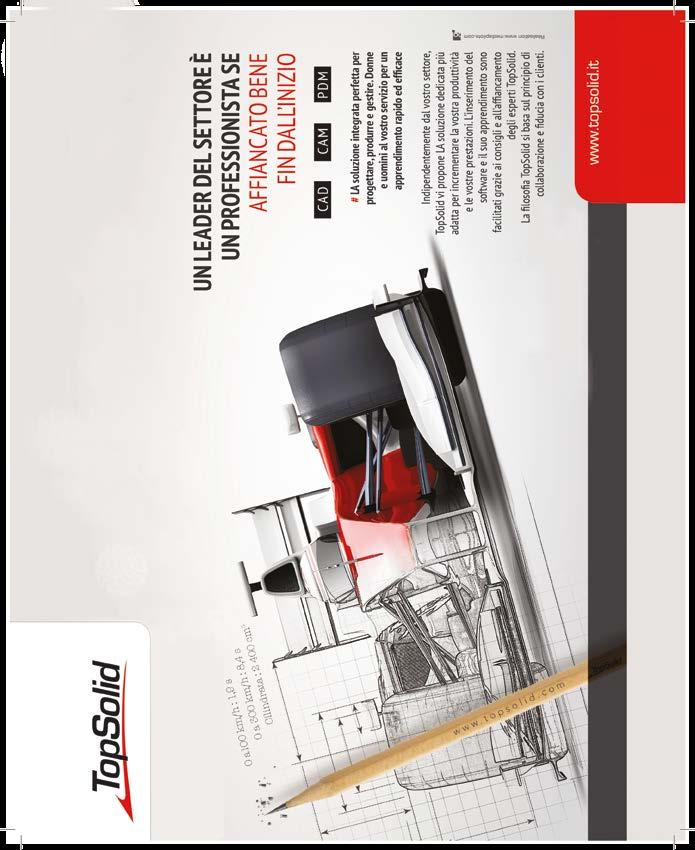
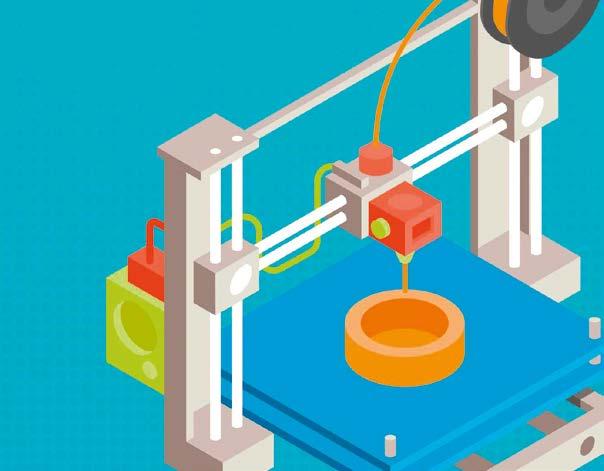
NEL 2016, IL PIANO NAZIONALE “INDUSTRIA 4.0” HA IDENTIFICATO LA MANIFATTURA ADDITIVA COME UN INSIEME DI TECNOLOGIE CARDINE IN GRADO DI PROMUOVERE, IN COMBINAZIONE CON LE ALTRE KEY ENABLING TECHNOLOGIES (KETS), L’EVOLUZIONE DEL SETTORE MANIFATTURIERO FAVORENDO LA TRANSIZIONE VERSO UNA PRODUZIONE PIÙ COMPETITIVA, PERSONALIZZATA E A ELEVATO VALORE AGGIUNTO
a cura di A. Mazzoleni – AFIL; E. Malfa, M. Boccadoro – Tenova; F. Stortiero – GFM; D. Tamborini, B. Previtali – Politecnico di Milano; A. Crosato – BLM; A. Romanini – GF Machining Solutions
AA differenza della modalità di produzione convenzionale, la manifattura additiva, o additive manufacturing (AM), è un processo tecnologico che parte dal modello digitale in 3D di un bene, a cui segue la realizzazione fisica dello stesso, mediante la deposizione strato dopo strato di materiale.
Ne consegue come il paradigma di lavorazione tradizionale sia rinnovato: la produzione non avviene più per asportazione di materiale bensì a partire dal gemello digitale dell’oggetto che, attraverso un opportuno software, è codificato in layers ed inviato alle macchine di stampa per essere fisicamente realizzato senza necessità di assemblaggio.
Per questa ragione, le tecnologie additive offrono la possibilità di ripensare il modo in cui un prodotto è progettato, sviluppato ed infine realizzato.
Sebbene i primi brevetti risalgano agli inizi degli anni ’80 è solamente in anni recenti che il mercato delle tecnologie per la manifattura additiva ha accelerato la propria crescita.
A tale riguardo, in Europa, il CAGR del settore è stato del 33,8% nel periodo 2014-2017 con valore stimato di 9,64 miliardi di € per il 2021 a testimonianza di come l’AM stia raggiungendo la maturità necessaria per trasformare i processi manifatturieri, passando da un utilizzo focalizzato sulla prototipazione rapida e in materiale plastico, verso una integrazione nei processi complementare alle modalità di produzione convenzionali.
Ad oggi, le principali sfide e opportunità riguardano l’applicazione a volumi elevati e un utilizzo che non si limita alla sola prototipazione in materiale polimerico ma che si estende anche alla realizzazione di parti in metallo, ampliando, di conseguenza, gli ambiti applicativi manifatturieri.
Tra essi, a titolo non esaustivo, l’aerospazio con la ricerca di soluzioni leggere e al contempo performanti e il re-manufacturing delle parti critiche, l’automotive per la riduzione di peso e la manifattura rapida di parti funzionali, il settore dei macchinari per la rigenerazione della componentistica a cui si aggiungono i beni di consumo - ad esempio gli elettrodomestici - e il biomedicale.
Numerosi sono i vantaggi per le aziende manifatturiere, sia grandi che PMI: ad esempio, la riduzione del time to market, la produzione di beni con geometrie complesse e non convenzionali, la riduzione degli sprechi, la realizzazione rapida di prototipi nonché la possibilità di creare oggetti personalizzati in produzioni seriali, senza incorrere in costi aggiuntivi.
Inoltre, tra i benefici della manifattura additiva, vi è la possibilità di facilitare la progettazione dei prodotti secondo la logica dell’economia circolare concependo beni che ottimizzano l’uso di materiali, il riuso e siano sostenibili anche in ottica di smaltimento.
Per tutte queste ragioni, l’AM si configura come un insieme di tecnologie che contribuiscono sia ad indirizzare le sfide attuali della produzione sia ad abilitare la completa digitalizzazione della Fabbrica, coerentemente con il concetto di Smart Factory.
Infatti, anche attraverso essa, è possibile rendere efficiente la lavorazione, prevenire le difettosità attraverso la raccolta e l’utilizzo dei dati generati durante la stampa, distribuire i processi tra diverse realtà e abilitare al contempo la collaborazione tra i soggetti della filiera, per consentire flessibilità e produzioni personalizzate.
Alla luce di queste considerazioni, il cluster AFIL - Associazione Fabbrica Intelligente Lombardia è attivamente impegnato nel favorire l’adozione dell’AM tra le imprese del territorio.
In coerenza con la propria mission, ovvero supportare e sviluppare la leadership e la competitività del sistema manifatturiero lombardo, sin dal 2015 AFIL ha promosso la nascita e lo sviluppo di un Gruppo di Lavoro dedicato all’ AM con lo scopo di integrare, in logica di filiera, i soggetti lombardi attivi sul tema, promuovendo la definizione di progetti strategici e il consolidamento delle competenze e delle conoscenze dell’ecosistema.
È proprio facendo leva su questa rete del cluster che, nel 2016, è stato concepito il progetto MADE4LO – Metal additive for Lombardy con l’obiettivo di stimolare lo sviluppo dell’AM delle parti metalliche, ponendo attenzione ad aggregare, secondo una logica e un modello di “Fabbrica Diffusa”, le competenze, i processi e le infrastrutture presenti sul territorio.
Con l’obiettivo di supportare la competitività delle imprese del territorio, i membri del Gruppo di Lavoro hanno lavorato sulla sfida di incrementare la produttività e sviluppare in ottica di mass customization l’AM di parti metalliche, facendo leva su attività congiunte di R&I per indirizzare le barriere ancora esistenti. Tra esse, la complessità del processo, i costi delle polveri metalliche, gli sprechi dovuti agli scarti e gli alti costi di investimento nelle tecnologie che non sono assorbibili da un volume di produzione limitato, in particolare per le PMI.
Da queste considerazioni nasce il progetto MADE4LO, co-finanziato da Regione Lombardia con 3,5 milioni di € nell’ambito degli “Accordi per la Ricerca, lo Sviluppo e l’Innovazione”, nel contesto del POR-FESR 2014/2020 Programma Operativo Regionale 2014-2020 obiettivo “Investimenti in favore della crescita e dell’occupazione”.
Coordinato da Tenova S.p.A., il progetto vanta un partenariato nato dalla collaborazione sinergica di 10 realtà rappresentative di aziende, università e centri di ricerca, in particolare: 3 Grandi Imprese attive nel settore siderurgico e dei macchinari (Tenova, BLM e GF Machining Solutions), 5 PMI tra cui fornitori di tecnologie per la manifattura additiva, produttori di componenti meccanici di precisione, stampi e lavorazione di metalli (3D-NT, GFM, Fubri, Co.Stamp e Officine Meccaniche Lafranconi) e 2 Università (Politecnico di Milano e Università di Pavia).
A questi si aggiungono l’Istituto di Sistemi e Tecnologie Industriali per il Manifatturiero Avanzato CNR-STIIMA e CSM – Centro Sviluppo Materiali.
Con l’obiettivo di svolgere uno studio approfondito sull’intera catena del valore, i partner del progetto MADE4LO hanno condiviso le rispettive conoscenze e competenze sia in merito alle tecnologie sia in riferimento ai requisiti dei vari ambiti applicativi: dalla progettazione di componenti, polveri e processi, continuando con l’analisi, l’approfondimento e lo sviluppo dei processi di deposizione – in particolare, Laser Metal Deposition e Selective Laser Melting, per concludere con gli aspetti legati alla necessità di finitura e trattamento termico (es. fresatura, rettifica) nonché di qualifica e test per la messa in esercizio di componenti, prodotti e processi.
Pertanto, il progetto ha affrontato e proposto soluzioni innovative alle prin-
La Fabbrica Diffusa di MADE4LO e i casi di studio
In MADE4LO, si è concepita la visione di una “Fabbrica Diffusa” che si basa su tre linee principali: i) Accrescere e diffondere la conoscenza sui processi additivi; ii) Realizzare nuovi sistemi additivi innovativi sia per la produzione delle polveri sia per la stampa; iii) Formare personale tecnico con le competenze necessarie per sfruttare al meglio le potenzialità delle tecnologie additive. In questo contesto, MADE4LO ha messo a disposizione dei vari partner una serie di impianti pilota e un network attraverso cui diffondere le conoscenze generate, dando vita a una rete di sistemi sia fisici sia digitali interconnessi in grado di scambiarsi informazioni digitali sui prodotti da stampare, sui dati del processo, sulle polveri nonché in merito alla qualifica dei beni realizzati. Le applicazioni innovative sono state esplorate dai partner attraverso 5 casi di studio proposti sulla base delle esigenze e delle criticità riscontrate nell’implementazione dell’AM e focalizzati su settori chiave nel contesto industriale regionale come la siderurgia, l’energia, l’utensileria e i trasporti. CASO 1 - Stampa di componenti in rame puro. La sfida tecnologica risiede nella capacità di realizzare lo stampaggio di un materiale altamente riflettente e a elevata conducibilità che rende complessa la lavorazione con metodologia convenzionale. L’applicazione, realizzata da una collaborazione tra Tenova, Politecnico di Milano, 3D-NT e GF Machining Solutions, prevede la stampa di un iniettore di ossigeno in rame puro per forni ad arco elettrico attraverso un innovativo sistema additivo con sorgente pulsata nella lunghezza d’onda del “verde”.
Figura 1: Iniettore di ossigeno in rame puro
CASO 2 – Materiali difficili, con elevate prestazioni in termini di durezza. La sfida tecnologica risiede nella stampa di leghe metalliche per alte prestazioni di durezza e taglio. Le attività, realizzate in collaborazione tra Politecnico di Milano, Fubri e Bohler - un’ azienda esterna al partenariato - hanno previsto lo studio di nuove leghe a base ferro in assenza di carbonio e lo stampaggio di un “creatore”, ovvero un utensile da taglio per la realizzazione di ingranaggio, che è convenzionalmente realizzato tramite un processo di sinterizzazione.
Figura 2 Il “creatore” stampato
CASO 3 – Realizzazione di componenti di grandi dimensioni, multimateriale, geometricamente complessi e con una componente di lavorazione ibrida. Politecnico di Milano, BLM, Lafranconi, Tenova, GF Machining Solutions con il supporto di CNR STIIMA, Team3DSiemens hanno lavorato alla realizzazione di uno scarico per motocicletta, stampato in un unico pezzo. Il pezzo è stato stampato con il sistema robotizzato di deposizione LMD – Laser Metal Deposition – Additube, sviluppato da BLM ed arricchito nel contesto del progetto di dispositivi di sensing e monitoraggio nonché integrato con una soluzione CAD/ CAM ah hoc per applicazioni robotizzate additive. Esso permette la stampa multimateriale ed è equipaggiato con opportuna sensoristica per garantire la corretta esecuzione delle lavorazioni.
cipali sfide tecnologiche della manifattura additiva, come: produzione di nuove polveri metalliche, la stampa di materiali complessi, di grandi dimensioni e multimateriale e l’adozione di lavorazioni ibride che contemplino sia aspetti additivi sia sottrattivi.
Sostenibilità economica, ambientale e sociale sono state le principali linee guida del progetto che ha previsto attente analisi costo – beneficio dei processi, nonché attività rivolte a favorire l’utilizzo di leghe riciclate per la formulazione delle polveri, il riuso dei prodotti e la tutela della salute dei lavoratori. In quest’ultimo caso, è stata realizzata una dettagliata analisi dei rischi connessi con i processi di AM, il cui risultato è unico in Italia e tra gli unici a livello EU.
Molteplici le ricadute in termini di risultati scientifici, innovazione e impatti sul territorio.
Le imprese hanno integrato i risultati nei loro processi ed ampliato il portafoglio delle tecnologie offerte, mentre in termini occupazionali sono stati attivati 13 assegni di ricerca e generati 6 nuovi posti di lavoro.
MADE4LO ha anche contribuito alla nascita di due centri di competenza di rilievo regionale e nazionale dedicati all’AM; GFM ha fondato, in collaborazione con altre realtà industriali, l’Additive Technology Centre – ATC (Link) mentre GF Machining Solution (Link) ha costituito un competence centre dove la stampa additiva è affiancata a tecnologie tradizionali.
Ringraziamenti
Si ringrazia per il contributo apportato all’articolo tutto il partenariato di MADE4LO: Tenova, BLM, Co.Stamp, GFM, GF Machining Solutions, Fubri, Lafranconi, 3D-NT, Politecnico di Milano e Università di Pavia. Il progetto MADE4LO è stato co-finanziato da Regione Lombardia nel contesto del POR-FESR 2014/2020 - Programma Operativo Regionale 2014-2020, obiettivo “Investimenti in favore della crescita e dell’occupazione”.

Figura 3 Lo scarico della motocicletta
CASO 5 – Realizzazione di uno stampo con processo ibrido additivo e sottrattivo Co.Stamp, con il supporto di Politecnico di Milano e GFM, ha realizzato canali conformali applicati ad uno stampo, attraverso un processo ibrido, che ha combinato una parte additiva – tramite processo Laser Metal Deposition - ed una sottrattiva durante la fase di finitura e non solo. L’inserto stampo è stato ridisegnato sfruttando le possibilità della tecnologia ibrida di combinare processi additivi e sottrattivi nello stesso ciclo CASO 4 – Realizzazione di un macchina alternando pertanto le fasi di recuperatore di grandi dimensioni e machining per realizzare i canali verticali multimateriale e la deposizione per i canali orizzontali Tenova, con il coinvolgimento del e freeform come evidenziato nel modello Politecnico di Milano, Università di Pavia, 3D dell’inserto. Il redesign è stato BLM e GF Machining Solutions, ha finalizzato in ottica di riduzione dei costi. sviluppato un recuperatore per il settore siderurgico. Anche in questo caso la sfida tecnologica risiede nella realizzazione tramite LMD di una componente composto da due materiali e caratterizzato da dimensioni rilevanti. Il recuperatore difatti è stato stampato LMD in acciaio inossidabile per la parte meno sollecitata e in lega a base nichel per la parte più sollecitata Figura 4 Il termicamente. recuperatore per il Complessivamente settore siderurgico l’altezza dell’oggetto è circa mezzo metro.
Figura 5 Il Tassello con canali conformali
Figura 6 Modello 3D dell’inserto ridisegnato per sfruttare la tecnologia ibrida e ridurre i costi di realizzo Caso 6 Realizzazione di un Vorticatore Assiale per Turbine a Gas GFM in collaborazione con Ansaldo Energia ha proposto la realizzazione di un oggetto complesso come un vorticatore assiale che presenta palette con geometrie complesse. Il caso studio ha mostrato come la tecnologia ibrida (sottrattiva e additiva) possa essere utilizzata anche per deposizioni in 5 assi per ridurre i costi di oggetti che diversamente dovrebbero essere prodotti con stampi costosi e con tempi di approvvigionamento molto lunghi. Nella figura seguente si mostra il mock-up del vorticatore realizzato con tecnologia ibrida a dimostrazione dell’efficacia della tecnica.