
74 minute read
Multi-task una tecnologia
MULTI-TASK, UNA TECNOLOGIA IN CONTINUA EVOLUZIONE!
MACCHINE VERSATILI E CAPACI DI EVOLVERE NEL TEMPO GRAZIE ALL’IMPLEMENTAZIONE DI SEMPRE NUOVE FUNZIONALITÀ, SVILUPPATE PER RISPONDERE AL MEGLIO ALLE NUOVE ESIGENZE DEL MERCATO, CHE RICHIEDE PEZZI SEMPRE PIÙ COMPLESSI E PRECISI SENZA RINUNCIARE ALLA FLESSIBILITÀ OPERATIVA.
LLa tecnologia multitask è una realtà sempre più tornitura su una macchina a portale, il concetto di multitask si importante e presente nell’attuale panorama tecnologico. evolve in una macchina che accorpa anche altre funzionalità, Nella lingua italiana, il significato più generale di questo tipiche di macchine dedicate. Accade sempre più spesso che termine di derivazione inglese è quello dello svolgimento di i clienti chiedano di inglobare la capacità di realizzare, ad più funzioni contemporaneamente, indipendentemente dal esempio, degli ingranaggi. La multitasking integra dunque contesto. In ambito meccanico, il concetto di multitask si lavorazioni proprie di un’altra categoria di macchine. Lo stesso applica a macchine che sono in grado di assolvere due o più accade per la rettifica, nel momento in cui il cliente chiede funzioni. In questo contesto, è un termine “relativamente” una macchina che abbia la capacità di tornire, forare, fresare giovane che ha subito una notevole evoluzione negli ultimi e anche rettificare, integrando questa ulteriore applicazione vent’anni, procedendo di pari passo con quella tecnologica. nel tornio. La definizione di macchina multitasking è perciò Di fatto non esiste una definizione rigorosa di cosa sia qualcosa di dinamico, che varia in relazione all’evoluzione del una macchina multitask, ma generalmente una macchina mercato, definendo di volta in volta il nuovo standard della viene considera tale quando, in un unico piazzamento, può macchina. Se agli inizi del novecento, la macchina multitasking realizzare tutte le lavorazioni che portano dal grezzo al pezzo più spinta era semplicemente quella che torniva e fresava, oggi finito. L’evoluzione di questa tipologia di macchine origina il 90% di queste macchine diventano macchine multitasking dalle prime soluzioni ibride, datate intorno agli anni 90, a cui vengono integrati degli accessori che consentono altre che realizzavano un tornio/fresa sulla base di un centro di lavorazioni. Parliamo di macchine fortemente personalizzabili lavoro orizzontale o verticale. Nel corso dei successivi venti- in funzione delle esigenze del cliente. venticinque anni, forti della propria esperienza, i costruttori di queste macchine sono arrivati a dedicare un’architettura I vantaggi di un unico centro di produzione specifica proprio a quelle macchine che possono fare L’obiettivo di una MTM è produrre un’intera parte con sia tornitura, che fresatura, integrando due tecnologie un unico programma automatico ininterrotto, senza fermarsi complementari in una sola macchina. Una soluzione di per cambiare la configurazione o sostituire gli utensili tornitura e fresatura all’interno di un unico centro di lavoro, manualmente. L’utilizzo di un unico centro di lavoro con capace però di assicurare performance del tutto sovrapponibili una singola operazione di setup elimina la variabilità causata ai tradizionali impianti concepiti per le due singole operazioni da più operazioni e configurazioni e consente di consegnare ad asportazione di truciolo e di oltrepassare quindi il confine parti di qualità superiore più velocemente, determinando fra macchina ibrida e macchina multitask, conseguendo alte un aumento dei profitti. Questo perché l’utilizzo di una performance per entrambe le lavorazioni, senza alcun tipo di macchina multitask determina riduzioni del tempo ciclo, il che compromesso. La filosofia ispiratrice è quella del “all in one”. significa minori setup, meno errori e possibilità di realizzare Oggi quindi con macchina multitask si intende una qualsiasi lavorazioni non presidiate, unitamente ad un miglioramento macchina multiasse, che in genere presenta più di un flusso di della qualità in termini di maggiore accuratezza e precisione, operazioni, in grado di completare una parte con una singola migliore ripetibilità da parte a parte, resa più rapida, output operazione di setup e staffaggio. La lavorazione multitask superiore e tasso di scarto inferiore. La somma di questi due consiste dunque nella combinazione di diversi processi di aspetti comporta un aumento della redditività perché l’uso di asportazione, tra cui tornitura, fresatura, foratura, filettatura e un’unica macchina ha come diretta conseguenza la possibilità barenatura di fori profondi, in una sola macchina con un’unica di disporre di una più ampia capacità dell’officina, realizzare operazione di setup. nuove opportunità di guadagno, l’acquisizione di un numero di commesse maggiore e il completamento di un numero Ibrido o multitask? maggiore di lavori e, come naturale conseguenza, profitti più Partendo quindi dalle macchine ibride, cioè macchine elevati. Esistono diversi tipi di macchine multitask con varie che hanno capacità di tornire e fresare, dando per scontata configurazioni di torrette, mandrini e altri parti in movimento l’applicazione della fresatura sul tornio verticale o della o dispositivi accessori. Le apparecchiature multitask sono
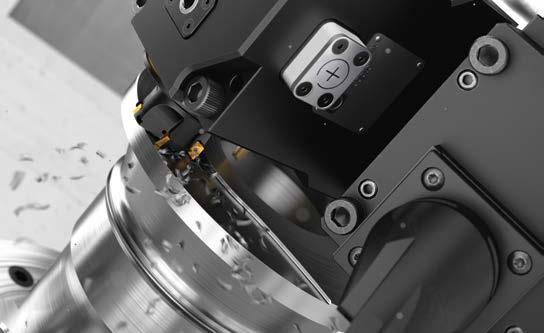
veramente utili quando si hanno piccoli lotti, parti molto diversificate o molte versioni di parti appartenenti a un’unica famiglia di pezzi.
Efficienza e flessibilità di produzione
Le macchine multi-task sono le più efficienti per la produzione di parti che richiedono più tipi di funzioni di lavorazione. Rispetto ai torni e alle frese standard, una tipica macchina multi-task è la più efficiente quando si ha bisogno di alternare operazioni di tornitura e fresatura per lavorare una parte. L’acquisto di una macchina multitask non va considerato solo in termini puramente economici, posto che il costo di queste macchine è superiore rispetto alla tecnologia di pura fresatura, ma va fatto, per aziende di grandi dimensioni, in considerazione dei vantaggi connessi all’impatto organizzativo che comporta l’inserimento di una macchina multitasking nella linea di produzione, e per aziende di dimensioni inferiori, ad esempio piccoli conto terzisti, per la flessibilità che la macchina consente in termini di produzione. Al giorno d’oggi, alla luce delle prospettive incerte del mercato, attuale e futuro, in cerca di una reattività immediata e una flessibilità più elevata possibile, poter disporre di un mezzo flessibile consente di acquisire commesse diversificate, in quanto la flessibilità della macchina consente di riconvertire rapidamente la produzione in un’altra lavorazione, peraltro con una prospettiva di lungo termine, trattandosi di macchine che hanno una vita utile di almeno una ventina d’anni. In quest’ottica la tendenza a concentrare sempre più tecnologia all’interno del medesimo mezzo produttivo aiuta molto durante i processi di lavorazione. Inoltre, limitare il numero di volte in cui i pezzi vengono movimentati, riduce la possibilità di errore e aumenta la precisione, con tutti i vantaggi della produzione combinata.
Software sempre più complessi
Per utilizzare le macchine multi-task in maniera efficiente sono necessari software CAD/CAM specializzati per definire il movimento degli utensili, simulare le operazioni e postprocessare il codice. La programmazione di queste macchine è infatti molto complessa. I software devono affrontare e superare la complessità delle macchine dovuta alla possibilità di interferenze e guasti a causa di diversi utensili che lavorano simultaneamente e devono garantire tempi di operatività rapidi, flessibilità, facilità di utilizzo, interoperabilità, automazione e tempi di inattività minimi. L’obiettivo di questi software è infatti l’aumento dei profitti conseguibile attraverso la riduzione dei guasti macchina, la riduzione degli scarti ed il miglioramento del ROI della macchina.
Il dossier che segue prende in considerazione una panoramica delle macchine multi-task di ultima generazione di alcune tra le più importanti aziende del settore con l’intento di mettere in luce l’evoluzione di tale tipologia di macchine e i possibili impieghi. Accanto alle macchine, il lettore trova anche sistemi e strumenti a servizio delle stesse, ovvero utensili, componenti e software con specifici programmi. Buona lettura!
IL MIGLIOR RITORNO SULL’INVESTIMENTO, DALL’ALLUMINIO AL TITANIO, DALL’AEROSPACE ALL’AUTOMOTIVE

BRETON
ULTRIX E3:
IL CENTRO DI LAVORO MULTITASKING
CON TAVOLA ROTOTILTANTE
PIÙ GRANDE DEL MERCATO
DDopo numerosi incontri con i principali player del settore Nella progettazione è stata data una grande attenzione al layout, aerospace e automotive, e dopo avere analizzato le loro principali in modo da minimizzare al massimo l’ingombro in pianta. Le applicazioni nonché le tendenze emergenti, Breton ha capito aziende si trovano spesso a dover soddisfare esigenze logistiche che era il momento di creare il centro di lavoro verticale a 5 assi stringenti ed è proprio qui che Breton vuole risultare ancora più con la tavola rototiltante più ampia del mercato. Con corse di vincente. Per questo motivo ha introdotto un indicatore, working 1.700x1.700x1.000 mm e uno swing massimo di 1.600 mm di area footprint rate indicator, che va a confrontare le dimensioni diametro risulta la più grande tra le rotobasculanti. della macchina con le corse degli assi. Nel processo di sviluppo
Questo prodotto ha lo scopo di andare a soddisfare una fascia del nuovo prodotto questo è uno dei fattori a cui i tecnici prestano di clientela ben precisa. È rivolto infatti a chi è alla ricerca di un maggiore attenzione in modo da realizzare prodotti sempre più centro di lavoro multitasking, che permetta di combinare fresatura competitivi. Per quanto riguarda Ultrix E3 questo rapporto supera ad alta velocità e tornitura ad altissime prestazioni in precisione. di più del doppio il valore del migliore tra i concorrenti.
Versatilità e potenza
Ultrix E3 è un centro di lavoro nato allo scopo di fornire per la prima volta una risposta ben precisa a chi cerca l’investimento più efficiente per la lavorazione di pezzi come case di motori aerospace, ingranaggi di medie-grandi dimensioni ma anche componenti molto complessi che richiedono molta coppia, la massima accessibilità ed elevatissime precisioni. È un centro fresatura che permette di lavorare materiali come il titanio, acciaio e leghe leggere grazie alla vasta gamma di elettromandrini disponibili tra cui scegliere. Il mandrino verticale e la tavola basculante permettono un’elevata accessibilità sia nella parte interna che nella parte esterna del pezzo da lavorare, e laddove necessario si può utilizzare la testa di rinvio a 90° con cambio automatico collocata nell’apposito magazzino accessori che può ospitare fino a due teste angolari. Grazie al bloccaggio diretto e preciso della testa al RAM tutta la coppia dell’elettromandrino verticale viene resa disponibile all’utensile in orizzontale. Tra le automazioni messe a punto da Breton, sono disponibili magazzini utensili con versatili sistemi di scambio in grado di caricare in modo automatico utensili HSK (63 o 100) o Capto (C6 o C8) sia sul mandrino principale che sulle teste a rinvio. Le robuste strutture consentono di realizzare anche asportazioni consistenti di materiale sfruttando al massimo l’innovativo elettromandrino da 600 Nm e, grazie al RAM con movimentazione idrostatica, le vibrazioni vengono smorzate nel modo più efficace senza però sacrificare in alcun modo la dinamica. Con la barra di tornitura, estensibile di 450 mm, è possibile realizzare lavorazioni di tornitura sia interna che esterna del componente senza ricorrere ad utensili lunghi che hanno il rischio di causare l’innesco di vibrazioni. Unire le fasi di tornitura e fresatura in un unico serraggio permette di ottimizzare enormemente il tempo di lavorazione e ridurre al minimo gli errori di setup nel passaggio da una macchina all’altra.
Prestazioni da prima della classe
Questo centro di lavoro è dotato di tecnologia High Dynamics che permette un notevole incremento di velocità, accelerazione e jerk pur senza ricorrere all’utilizzo di motori lineari, evitando in questo modo l’aumento dei consumi energetici e complicazioni in fase di manutenzione.
La tecnologia High Dynamics inoltre, attraverso l’eliminazione delle frizioni date dai sistemi di bilanciamento, porta a movimenti molto più fluidi che garantiscono finiture superiori e precisioni più elevate lavorando anche alle massime velocità. Le motorizzazioni Direct Drive vengono utilizzate solo dove i benefici sono evidenti e immediati: sugli assi A e C.
La bascula che supporta la tavola di fresatura prevede la rotazione dell’asse A mediante due motori torque a coppia elevata, 15.000 Nm, e può essere bloccata grazie a un doppio freno, uno
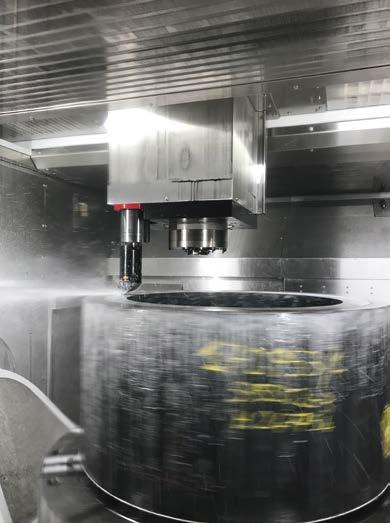
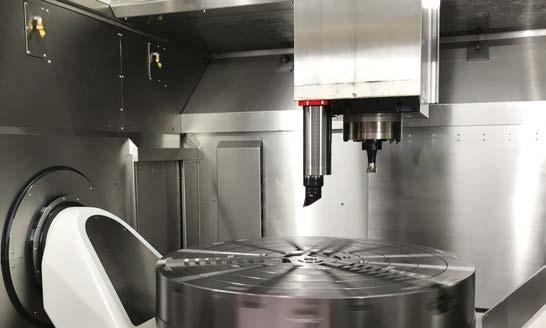
per lato. L’intera tavola può tiltare da -120° a +120°. Il pallet circolare da 1.350 mm di diametro ruota anch’esso grazie a un motore Direct Drive che consente di raggiungere i 450 giri al minuto continui, con una coppia di 3.500 Nm riuscendo a portare un carico massimo di 2.500 kg.
Struttura a prova di sbalzi termici e vibrazioni
Il design termosimmetrico consente di ridurre al minimo gli effetti delle naturali deformazioni termiche e speciali algoritmi sviluppati da Breton assicurano il loro continuo monitoraggio e la successiva correzione ottimale. I punti nei quali viene generato il calore, come negli organi di trasmissione, i motori Direct Drive, l’elettromandrino e la tavola vengono stabilizzati in temperatura attraverso l’impiego di appositi chiller ad alta efficienza.
In questo modo si eliminano anche i casi di trasferimento ad altri punti della struttura del calore autogenerato. Il basamento della macchina è costituito da un rigido monoblocco che sfrutta la brevettata tecnologia Metalquartz, un elettrosaldato normalizzato di elevato spessore, fortemente nervato, le cui cavità sono riempite con uno speciale mix di quarzo e polimeri sviluppato da Breton grazie al proprio know-how nel settore dei materiali agglomerati. La struttura risultante è superiore a un monoblocco in ghisa sia dal punto di vista della rigidità che dello smorzamento delle vibrazioni.
Produttività H24
Insieme alla macchina, Breton può fornire specifiche soluzioni di automazione e monitoraggio sviluppate al fine di incrementare la produttività, riducendo al minimo le esigenze di presidio anche su lavorazioni in continuo H24.
Ultrix E3 è un centro di lavoro che può essere facilmente integrato con un sistema di cambio pallet automatico o con asservimenti di robot per il carico/scarico di pezzi sia sulla singola postazione che all’interno di più complessi
L’attenzione ai dettagli che contraddistingue Breton L’ergonomia è uno degli aspetti a cui Breton tiene particolarmente e questo centro di lavoro non fa eccezione. Il pannello operatore può essere sia sospeso, grazie a un braccio articolato, che installato dal basso su un braccio fisso rotante e traslante che permette di essere regolato in altezza e inclinazione nonché di essere spostato nella posizione più comoda per l’operatore. L’accessibilità al particolare in lavorazione è un altro punto di forza di questa macchina: permette infatti all’operatore di arrivare a soli 15 cm dalla tavola una volta aperte le porte. L’attenzione alle esigenze dell’operatore si può vedere anche da come è stato curato il posizionato del magazzino utensili. Sviluppato verticalmente a lato della macchina, è dotato di una postazione di carico/scarico frontale comodamente raggiungibile dall’operatore in modo rapido e che gli permette di mantenere il controllo sulla lavorazione in corso. L’apertura automatica del soffietto superiore in acciaio inox è totale e agevola l’attrezzaggio della macchina con l’ausilio del carroponte. L’area di lavoro è interamente rivestita in acciaio inox che, oltre a evitale totalmente la fuoriuscita di trucioli, rende gli spazi interni luminosi, facili da pulire e inattaccabili dal tempo e dall’usura. I pannelli sono accuratamente sigillati e insonorizzati, mentre ogni sigillatura degli organi mobili è pressurizzata evitando che sporco ed emulsione ad alta pressione possano infiltrarsi.
sistemi FMS. In questo modo, ottimizzando al massimo il layout aziendale, si arriva a lavorazioni in continuo con ridotta o assente sorveglianza dell’operatore. Anche alcune scelte progettuali come l’impiego di sistemi di filtrazione refrigerante autopulenti o il controllo in I/O Link di tutta la sensoristica permettono di ridurre drasticamente i tempi e i costi di manutenzione.
Industry 4.0 inside
Anche Ultrix, come gli altri centri di lavoro, può essere integrato nel mondo Sentinel, la piattaforma Breton che permette la raccolta e l’analisi dei dati relativi sia alle macchine che ai processi di lavorazione collegati. Il sistema è dotato di numerosi indicatori e strumenti grafici facilmente accessibili e consultabili sia a bordo macchina che da remoto (in real time o nella fase di post processing), che permettono di tenere sotto controllo tutti i consumi e i parametri di funzionamento della macchina nonché di monitorare l’efficienza della lavorazione individuando possibili aree di miglioramento. Sentinel avvisa con sufficiente anticipo il sopraggiungere delle necessarie manutenzioni programmate, permettendo di calendarizzarle in modo ottimale. Inoltre, attraverso complessi algoritmi basati sul machine learning che Breton ha sviluppato negli anni, il sistema ricerca tra serie di dati storici le relazioni che permettono di predire stati o eventi futuri. Per comprenderne a pieno le potenzialità basta pensare ai vantaggi di potere prevenire un guasto costoso come per esempio la rottura di un mandrino. Nella gestione della manutenzione entra in gioco un’altra tecnologia sviluppata da Breton: SmartDoc. Questo pacchetto permette di gestire in modo digitale e intelligente contenuti come manuali d’uso, immagini, video tutorial e varie note. Il sistema può funzionare su numerose piattaforme per lasciare la massima flessibilità all’utilizzatore. Il lavoro viene semplificato attraverso l’utilizzo di immediati QR code che portano l’utente direttamente alla parte del manuale di interesse e lo guidano nel processo di individuazione di eventuali parti di ricambio.
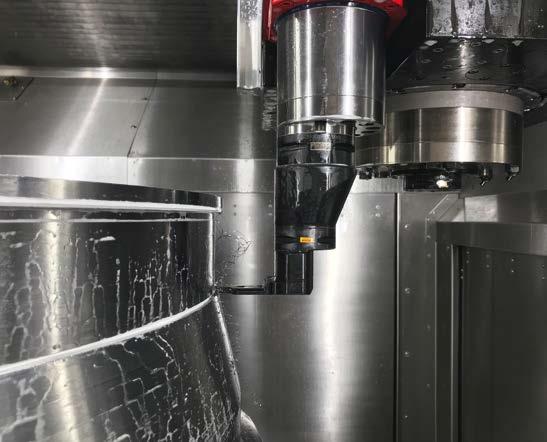
CELADA
CELADA UN’AZIENDA DINAMICA AL L’L’offerta prodotto è stata ampliata per soddisfare ancor di più tutte le esigenze dei clienti. “Abbiamo aggiunto nuove tecnologie – spiega Paolo Capelli, Product Manager Celada Group - come le martellatrici, le rettifiche di alta precisione, le macchine additive. Abbiamo inoltre creato un ufficio di consulenza che supporta il passaggio ad Industria 4.0 ed affianca i clienti nel ridisegno dei processi produttivi. Non è infatti la macchina di per sé ad essere 4.0, ma è l’azienda nel suo complesso. Il miglioramento delle attività di service passa attraverso la formazione dei tecnici, l’incremento del personale ed il progetto “e-service” che digitalizza il dialogo con i clienti. L’utilizzo della tecnologia consente infatti una maggiore PASSO CON I efficacia d’intervento grazie alla teleassistenza ed un migliore dialogo nella gestione degli ordini ricambi e nella pianificazione degli interventi presso i clienti”.TEMPI Centro di lavoro orizzontale
5 assi OKUMA: MU-10000H
Il centro di lavoro orizzontale a 5 assi Okuma MU -10000H si
CELADA STA SVILUPPANDO PROGETTI pone come punto di riferimento a livello mondiale principalmente
IMPORTANTI PER AFFIANCARE I nel settore Aerospace ma in generale nella lavorazione di particolari
CLIENTI CON SEMPRE MAGGIORE meccanici dove sono richieste tolleranze e finiture di superfici elevate PROFESSIONALITÀ e di grande dimensione. Tutto questo è reso possibile grazie ad una struttura macchina decisamente sovradimensionata di circa 63.000 kg, una gamma di linee mandrino con elevate potenze fino a 1.920 N/m e 45Kw, attacchi mandrino in versione Bt50 /Hsk100 e corse degli assi generose X 1.550 - Y 1.600 - Z 1.650, A +35°/-115°, B+/-360°. La tavola roto-basculante con pallet da 1.000 x 1.000 è gestita dal sistema tandem – drive su entrambi gli assi con una portata carico massimo di 2.500 kg.

In configurazione standard MU-10000H prevede righe ottiche sugli assi X-Y-Z, raffreddamento delle viti, cambio pallet a 2 posizioni espandibile con cambio pallet a 6 posizioni e interfacciabile con magazzini pallet Fastem, magazzino utensili a 177 posizioni, compensazione termica che si differenzia tra compensazione mandrino (TAS-S) e compensazione sulla struttura macchina (TASC). TAS-S considera non solo le temperature dell’ ambiente e del mandrino ma anche sulla velocità di utilizzo di rotazione del mandrino, i cambi di velocità del mandrino e il tempo di fermo del mandrino ottenendo il massimo controllo e precisione della deformazione del mandrino e dell’asse Z. Il TAS-C si basa sulle caratteristiche strutturali della macchina e con sensori di temperatura opportunamente posizionati e i dati di posizionamento degli encoder Okuma prevede e controlla con precisione la deformazione termica della struttura della macchina. Il Thermo-Friendly Concept nasce fin da subito dalla progettazione simmetrica della struttura macchina per gestire il problema della dilatazione termica e affrontare questo elemento che non può essere eliminato. L’ unione dell’ hardware con il software Okuma garantisce una compensazione termica estremamente accurata gestendo la dilatazione in ogni momento della giornata a partire da 0.1 micron , garantisce inoltre di avere una stabilità dimensionale senza precedenti per tutte le operazioni in ambienti di lavoro ed evita perdite di tempo e quindi di denaro nel set-up quotidiano della macchina. La macchina non necessità di lunghe operazione di riscaldamento quindi si riducono costi energetici e costi di non produttività.
Software anticollisione CAS
Un’altra funzione inclusa nella macchina è il software anticollisione indispensabile poiché le macchine diventano più complesse, coinvolgendo anche gli assi rotanti aggiuntivi. Il sistema di anticollisione CAS integra la modellazione 3D delle nostre macchine nei minimi dettagli e dà la possibilità al cliente di inserire i modelli di attrezzature e utensili nel controllo OSP in maniera semplice per creare a tutti gli effetti una LASER EX macchina virtuale. Il controllo numerico OSP300-MA calcola virtualmente tutto il processo e in caso di collisioni incombenti arresta la macchina evitando i rischi di fermo macchina e costi da parte del service. Il CAS genera la forma effettiva ed esatta del pezzo durante il ciclo aggiornando in continuazione il nuovo grezzo per avere sempre sotto controllo il processo e verificare che non si manifesti alcun tipo di interferenza. Massimizza i tempi di set-up della macchina e consente agli operatori di concentrarsi sulla lavorazione. Protegge la macchina da errori da parte dell’operatore anche in modalità manuale, jog, rapido e MDI.
SERVONAVI – M, il software per ottimizzazione di tempi e lavorazioni
Altro software è il SERVONAVI – M, è una tecnologia ad alta precisione che migliora i tempi ciclo e l’accuratezza durante la lavorazione dei particolari. Questa tecnologia è STANDARD su tutti i centri di lavoro Okuma e permette di variare l’accelerazione e decelerazione effettiva con diversi carichi sulla tavola (pezzo + attrezzatura). La funzione gestisce automaticamente il carico sulla tavola macchina e calcola automaticamente le migliori velocità di accelerazione e decelerazione per ottenere tempi di ciclo più rapidi e per utilizzare l’elettronica e la meccanica al meglio. Inoltre è possibile regolare automaticamente l’inversione degli assi per ottenere nel tempo un’interpolazione sempre al massimo della precisione. Si possono regolare automaticamente le vibrazioni causate dallo scorrimento lineare degli assi quando le condizioni della macchina cambiano nel tempo. Il software SERVONAVI è presente anche sui torni per gestire automaticamente l’inerzia sul mandrino garantendo super finiture sulle superfici tornite.
Okuma LASER EX
Le nuove macchine super multitasking della serie Laser EX uniscono il meglio delle lavorazioni sottrattive e additive, effettuando lavorazioni intensive di tornitura, fresatura, rettifica, tempra di precisione e rivestimento indurente mediante laser. La deposizione di metalli al laser (LMD) ad alta definizione offre qualità senza paragoni nella produzione additiva, nel trattamento termico e nelle riparazioni. I requisiti di produzione e di lavorazione stanno diventando sempre più particolari e stringenti, per questo motivo e per far fronte a tutte le tipologie di richieste, le macchine della serie Laser EX presentano capacità di lavorazioni multitasking di un livello ancora superiore. Progettate per essere le prime macchine “done-on-one” al mondo, MU-6300V LASER EX e MULTUS U3000 LASER EX sono in grado di eseguire lavori di fresatura, tornitura, rettifica, tempra laser e stampa 3D in metallo per una vasta gamma di pezzi di lavoro, con svariate forme e dimensioni. L’indurimento, effettuabile direttamente sulla macchina, fornisce la soluzione ad un grande problema produttivo: rispetto all’indurimento con trattamenti termici più convenzionali, il processo è veloce e causa meno distorsioni producendo un notevole incremento della produttività. Queste macchine supportano appieno la produzione agile e le applicazioni intensive. Si può quindi parlare di tecnologia laser per lavorazioni intensive. Con al proprio interno una sorgente laser di alta qualità, la serie LASER EX di Okuma permette di effettuare lavorazioni laser stabili e prolungate. Le macchine sono anche in grado di eseguire il processo di Deposizione Metallica Laser (LMD), per una fabbricazione additiva a elevata capacità e ad alta definizione. La possibilità di regolare il diametro dello spot del fascio laser da 0,4 e 8,5 mm garantisce una produttività senza pari indipendentemente dall’applicazione. Il controllo OSP di Okuma monitora l’intero processo garantendo una fabbricazione additiva affidabile e stabile per tutti i prodotti, allo stesso livello dei componenti forgiati.
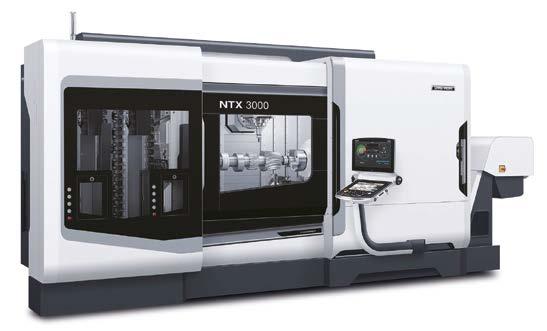
Su una superficie di soli 16,5 m² NTX 3000 2nd Generation unisce elevata stabilità e flessibilità di processo con un’ampia zona di lavoro.
QUALITÀ ECCELLENTE GRAZIE A PRESTAZIONI PERFETTE!
LA NECESSITÀ IMPOSTA DAL MERCATO DELLE MACCHINE UTENSILI DI RIDURRE I TEMPI CICLO PRESERVANDO AL CONTEMPO LA QUALITÀ DELLA LAVORAZIONE, INDUCE I COSTRUTTORI A PRODURRE SISTEMI MULTITASKING IN GRADO DI RESTITUIRE UN PEZZO PRESSOCHÉ FINITO SENZA CHE ESSO ABBIA SUBITO NESSUNO SPOSTAMENTO DA UNA MACCHINA A UN‘ALTRA
PPer rispondere a questa esigenza, DMG MORI, gruppo in fondamentale per la massima precisione nella lavorazione continua a 5 costante crescita ed espansione a livello mondiale da sempre assi. Questa anteprima è progettata per un diametro barra maggiorato estremamente attento alle esigenze del mercato in termini di qualità e pari a ø 102 mm e consente anche la realizzazione dei componenti più innovazione e ai suoi andamenti, offre un’ampia gamma di macchine complessi con coppia fino a 1.194 Nm. Come i modelli più piccoli con soluzioni multitasking integrate. di questa serie, anche l’NTX 3000 di seconda generazione racchiude l’esperienza di oltre 1.000 NTX 2000 già installate. Questo modello di NTX 3000 di seconda generazione nuova generazione è, dunque, sinonimo di elevata stabilità di processo
I centri di tornitura turn & mill sono considerati la prima classe ed alta flessibilità con un’ampia zona lavoro (675 mm nell’asse X e +/- delle lavorazioni meccaniche d’avanguardia. Dopo la presentazione 150 mm nell’asse Y) su una superficie di installazione di soli 16,5 m². dell’NTX 2500 di seconda generazione in occasione della EMO Il componente chiave che contraddistingue questa macchina è l’asse B 2017, DMG MORI presenta l’ultimo modello dei suoi centri di dotato di mandrino compactMASTER, prodotto da DMG MORI, tornitura/fresatura compatti: l’NTX 3000 di seconda generazione. che permette la lavorazione a 5 assi di pezzi complessi con valori di Un nuovo modello, la cui base è costituita dal robusto basamento coppia fino a 122 Nm. Il mandrino principale, che vanta una coppia macchina, unitamente alle guide a rulli ad elevata stabilità. A ciò di 1.194 Nm, e il contromandrino, disponibile in opzione, ampliano si aggiungono le eccezionali soluzioni di raffreddamento di cui ancor più le prestazioni dell’NTX 3000 di seconda generazione sono provvisti i mandrini e le viti a ricircolo di sfere, a garanzia nel settore della truciolatura pesante su 6 lati per le applicazioni di condizioni termiche particolarmente stabili, come prerequisito dell’industria aerospace, automotive o medicale. Shigetsugu Sakai,
Operating Officer responsabile del DMG MORI Turning Center di Iga, riassume: “Con l’NTX 3000 di seconda generazione, stiamo estendendo la già ampia gamma di prodotti con diametri di barre ancora più grandi e una coppia significativamente più elevata. Questa è un’ulteriore risposta alla forte domanda proveniente da un mercato eterogeneo.”
Prestazioni di lavorazione eccezionali
Un altro importante pregio di questa anteprima mondiale è il mandrino corto compactMASTER dell’asse B, che misura solo 350 mm, offrendo ulteriore spazio nella zona lavoro, oltre a fornire prestazioni di lavorazione eccezionali. Come il mandrino turn & mill, anche il secondo portautensili, costituito da torretta BMT dotata di utensili motorizzati, è provvisto di asse Y (+/- 40 mm). I tempi brevi di attrezzaggio sono, inoltre, garantiti dal magazzino utensili toolSTAR di marchio DMG MORI, dotato di 38 stazioni utensili, che possono essere estese fino a 114 posti a seconda delle esigenze del cliente. L’NTX 3000 di seconda generazione sposa il trend all’automazione da due punti di vista. Mentre la misurazione integrata degli utensili, il controllo della rottura utensile e la misurazione dei pezzi nella zona lavoro assicurano un processo di lavorazione efficiente, la scelta dei sistemi di gestione pezzi orientati al fabbisogno del cliente consente la miglior soluzione di carico e scarico dei pezzi, di cui la variante robotizzata è solo un esempio.
Controllo di processo garantito
Per quanto riguarda i controlli, la seconda generazione dell’NTX 3000 segue il “Path of Digitization”, ideato da DMG MORI per promuovere la digitalizzazione. Anche questo nuovo centro di tornitura/fresatura è dotato, infatti, dell’interfaccia gestionale e operativa basata su APP, CELOS, e di un ampio display multi-touch da 21“. CELOS consente la completa gestione, documentazione e pianificazione degli ordini per organizzare tempi e metodi e le attività in officina. Inoltre, le sue APP, come il “CONDITION ANALYZER” o il “PERFORMANCE MONITOR”, offrono all’utente una panoramica dettagliata dei processi di lavorazione o dello stato macchina – ottimo punto di partenza per un costante miglioramento. Infine, CELOS funge sempre più spesso da interfaccia IoT, gettando, così, le basi per un’interazione intercompany attraverso le reti produttive del futuro.
Anche per l’NTX 3000 di seconda generazione sono disponibili i cicli tecnologici DMG MORI. “Easy Tool Monitoring” permette, ad esempio, il monitoraggio del carico del mandrino e dell’avanzamento degli assi. I cicli tecnologici consentono agli operatori di eseguire in tutta semplicità lavorazioni complesse, attrezzaggi e misurazioni con macchine universali nonché con utensili e alloggiamenti standard. Queste attività richiedevano in passato macchine, programmi e utensili speciali.
Un ibrido anche per l’additive
L’Additive Manufacturing sta iniziando ad affermarsi sempre più come procedura pionieristica per usi industriali. Le stesse domande basate sulla tecnologia stanno di conseguenza mutando. DMG MORI sta sistematicamente tenendo in considerazione ciò
NTX 3000 - L’asse B con Direct Drive consente la lavorazione simultanea a 5 assi di pezzi complessi.
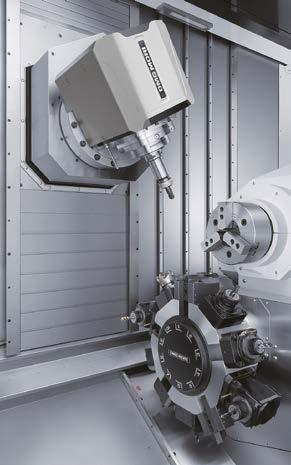
per lo sviluppo futuro dei propri macchinari, come è efficacemente rispecchiato nella nuova LASERTEC 125 3D hybrid. Basata sulla solida serie monoBLOCK, è progettata per parti che misurano fino a ø 1.250 x 745 mm e pezzi dal peso fino a 2.000 kg. La rigorosa costruzione della macchina e le elevate dinamiche della LASERTEC 125 3D hybrid permettono lavorazioni complete di parti 3D impegnative accurate, affidabili e allo stesso tempo dai costi contenuti. Il passaggio automatico tra sinterizzazione laser e fresatura simultanea a 5 assi in un unico serraggio riduce i tempi di processo fino all’80 percento. Tale risparmio avviene grazie alla completa eliminazione di parti di processo, come il trattamento termico, dal momento che la LASERTEC 125 3D hybrid può depositare materiale con una durezza fino a 63 HRC. L’uso alternato della sinterizzazione laser e della fresatura a 5 assi in simultanea è particolarmente proficuo per incrementare i processi produttivi o sviluppare nuove geometrie pezzo. Negli ultimi cinque anni, la sinterizzazione laser è emersa anche come eccellente tecnologia per le riparazioni e l’area dei rivestimenti in molte industrie target.
NEL SETTORE DELLE MACCHINE UTENSILI DUPLOMATIC AUTOMATION DAL 1952, DUPLOMATIC AUTOMATION OFFRE SOLUZIONI INNOVATIVE E FLESSIBILI. SIN
DIRECT DALLA FONDAZIONE, LA STORIA DELL’AZIENDA È STATA CARATTERIZZATA DA DIVERSE FASI DI SUCCESSO
DRIVE B-AXIS,
L’UNITÀ SPECIFICA PER D MACCHINE MULTITASKING Da oltre sessant’anni Duplomatic si è, infatti, distinta nel settore della componentistica per macchinari industriali sviluppando soluzioni tecnologiche che spaziano da quelle oleodinamiche, a quelle elettriche o elettromeccaniche. Partendo dalla produzione di dispositivi automatici di copiatura idraulica e proseguendo con l’introduzione delle prime torrette portautensili e delle unità asse B, Duplomatic ha sviluppato modelli sempre più sofisticati per diverse applicazioni di macchine utensili, fornendo ai clienti non solo prodotti tecnologicamente avanzati, ma soprattutto soluzioni Direct Drive B-Axis Unit Grazie alle costanti innovazioni tecnologiche, negli ultimi vent’anni il settore delle macchine multitasking ha subito una forte innovazione ed evoluzione per soddisfare la domanda crescente del mercato in termini di flessibilità, di elevate prestazioni sia in tornitura che in fresatura e massima precisione, grazie all’implementazioni di funzionalità sempre nuove. L’uso di una “unità asse B” di tornitura/fresatura combina la capacità di tornitura di un tornio con le lavorazioni di fresatura/ foratura di un centro di lavoro, trasformando i tradizionali centri di diversificate per il settore automazione, sfruttando appieno lavoro e/o i centri di tornitura in innovative macchine Multitasking know-how e competenze. Innovazione, velocità e flessibilità e rendendo possibili una vasta gamma di operazioni automatiche sono da sempre i valori aziendali. mediante utensili statici e rotanti, in risposta alla richiesta del
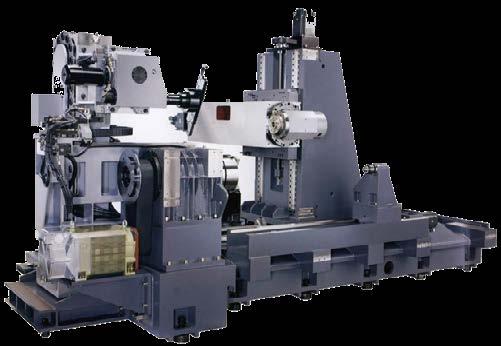
mercato, tipica di settori quali Automotive e Aerospace, di ottimizzare il processo produttivo e di accorparlo su macchinari in grado di eseguire se non tutte, almeno la gran parte delle lavorazioni necessarie per completare la produzione del componente.
La nuova generazione B-Axis Duplomatic, sviluppata con la più recente tecnologia Direct Drive, fornisce maggiore precisione e tempi di set-up più brevi, aumentando capacità e flessibilità della macchina per operazioni di tornitura e fresatura. Frutto di un’esperienza unica di 60 anni nel settore delle macchine utensili, l’unità Direct Drive B-Axis di Duplomatic è il risultato di un design innovativo e della collaborazione fianco a fianco con i clienti che ha consentito all’azienda di ottenere prestazioni operative eccezionali ai più alti standard di qualità. Per il sistema B-Axis sono previste tre opzioni di elettromandrino, High speed (HS), Basic (B) e High torque (HT), che il costruttore sceglie in funzione delle tipologie di lavorazioni che la macchina deve realizzare. Il design dell’elettromandrino è stato sviluppato, per ogni dimensione, per creare modularità tra tutte le diverse versioni (utensileria, velocità, coppia, ecc.) in modo da offrire la piena intercambiabilità, mantenendo lo stesso layout macchina. Inoltre l’ampia scelta di unità di azionamento diretto ad asse B, per operazioni di tornitura e fresatura di Duplomatic Automation è disponibile in due diverse configurazioni base “Slant Bed” o “Flange Type”, dalla taglia 16 alla 25.
“Spesso accade tuttavia – spiega Loris Andreoli, Direttore Tecnico di Duplomatic Automation - che le nostre proposte “base” non soddisfino le specifiche esigenze del cliente. Il nostro punto di forza è la capacità di rispondere alle richieste del cliente offrendo una completa personalizzazione delle nostre soluzioni, sia dal punto di vista delle prestazioni che della dimensione che deve avere l’oggetto. Inoltre, a partire dalle due diverse morfologie “Slant Bed” o “Flange Type”, proposte in funzione del diverso tipo di montaggio dell’unità alla macchina, fissato al carro piuttosto che flangiato nel ram della macchina, le unità possono essere ulteriormente personalizzata per rispondere alle diversità costruttive della macchina e per soddisfare le specifiche esigenze del cliente”. Per ciascun modello può essere scelta anche l’interfaccia utensile in varie opzioni, conformi alle diverse normative, in funzione del tipo di attacco: Capto, HSK , BT o ISO, quest’ultima laddove ancora richiesto.

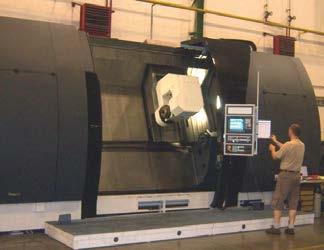
Produzione e qualità
Tutti i principali componenti dei prodotti Duplomatic sono realizzati all’interno del Reparto Produzione. Il Sistema Qualità tiene sotto controllo ogni fase del processo produttivo effettuando un controllo finale sul 100% dei prodotti, secondo procedure precise e definite, con rilascio di Certificati di Collaudo.
Vendita e post-vendita
Completamente e totalmente orientato al cliente, la Direzione Commerciale del Gruppo risponde alle specifiche richieste e coordina l’attività della Rete di Vendita in tutto il mondo. Presenza territoriale e frequenti visite dei clienti garantiscono un continuo supporto di partnership. Grazie all’organizzazione Post Vendita e ad un magazzino strategico di ricambi, è garantita una pronta risposta alle problematiche dei clienti con tecnici specializzati in ogni zona del mondo.
LA LAVORAZIONE DI COMPONENTI DI GRANDI DIMENSIONI E DI GEOMETRIE COMPLESSE COMPORTA SPESSO UN’ESECUZIONE IN TEMPI ELEVATI E L’AUMENTO DEI COSTI PER SINGOLO COMPONENTE

EMAG
VMC 450-5 MT
DI EMAG: CENTRO DI TORNITURA/
FRESATURA A CINQUE ASSI
CCiò è dovuto ai diversi processi di lavorazione da realizzare, dalla o trasmissione, proseguendo con i settori della cantieristica, tornitura alla dentatura, spesso eseguiti su macchine diverse non dell’agricoltura ed estrazione, che, oltre ad essere richiesti in grandi concatenate le une alle altre. Un’ulteriore difficoltà è rappresentata quantità, si presentano spesso come lavorazioni molto complesse. dal numero di lotti da lavorare, ovvero dalla necessità di lavorare Queste tipologie di componenti presentano numerosi fori, superfici componenti sempre diversi sulle varie macchine, con conseguente o dentature inclinati, da eseguire con estrema precisione e senza aumento dei tempi di riattrezzamento richiesti. Per far fronte a tutte errori. La VMC-450-5 MT si dimostra adatta anche per piccoli queste problematiche e alle esigenze di produzione, EMAG Leipzig lotti, che richiedono soluzioni flessibili, sempre prestando attenzione Maschinenfabrik ha sviluppato il centro di tornitura/fresatura VMC ai costi di equipaggiamento, da ridurre il più possibile. La VMC 450-5 MT, in grado di eseguire tutti i processi di tornitura, fresatura, 450-5 MT di EMAG è stata appositamente sviluppata per queste alesatura e dentatura in un’unica zona di lavoro, grazie ai 5 assi con i esigenze, come spiega Georg Händel, Technical Sales Manager di quali è equipaggiata la macchina. Il risultato sono tempi ciclo più brevi EMAG Leipzig. “Per lo sviluppo di soluzioni di produzione dedicate e costi di equipaggiamento minimi, supportati da un aumento della a componenti complessi con diametro fino a 450 mm ci affidiamo a qualità. questo centro di tornitura/fresatura multifunzionale a cinque assi. La tornitura rappresenta sempre la tecnologia produttiva principale. Il La VMC 450-5 MT mandrino portapezzo posizionato in basso, esente da manutenzione, Le possibilità di applicazione della VMC 450-5 MT sono è integrato nel nuovo asse Y ed è inoltre disponibile un asse B con molteplici, a partire dai componenti, destinati a veicoli commerciali angolo di rotazione di 195° con mandrino di tornitura/fresatura
integrato. Ciò consente, grazie alla combinazione degli assi, di eseguire applicazioni per la dentatura a creatore oppure il “power skiving”. Tornitura, fresatura, alesatura e dentatura: sulla VMC 450-5 MT è possibile eseguire tutte le tecnologie richieste per la realizzazione di un componente complesso”.
La lavorazione dei portasatelliti
Un ottimo esempio per evidenziare le qualità del centro multifunzionale di EMAG è fornito dalla lavorazione dei portasatelliti. Se la lavorazione completa viene eseguita in modo tradizionale, per la lavorazione di questo componente sono necessarie diverse macchine, ognuna dedicata ad una specifica tecnologia e spesso non concatenate tra loro. Si parte dal processo iniziale di tornitura, proseguendo con la brocciatura/dentatura a creatore, passando poi all’alesatura e all’equilibratura. Quando si esegue un cambio lotto, l’operatore deve quindi preparare sei macchine diverse, andando ad incidere sulla sicurezza del processo e sulla produttività. L’intero processo di lavorazione tradizionale si presenta come particolarmente lungo e poco flessibile, poiché i componenti devono essere trasportati di macchina in macchina. La situazione migliora nettamente utilizzando la VMC 450-5 MT. Nel caso dei portasatelliti, la lavorazione completa richiederà l’impiego di sole due macchine, con automazione robotizzata. I processi di lavorazione da eseguire, cioè tornitura, alesatura, fresatura e power skiving vengono ripartiti in modo flessibile su entrambe le macchine, ottenendo un tempo di lavorazione compensato ed un elevatissimo rendimento. L’equilibratrice viene integrata nella cella di lavorazione EMAG, inoltre la marcatura e il lavaggio dei componenti possono essere eseguiti parallelamente. Nel complesso, il portasatellite viene prelevato solo tre volte (invece delle sei previste dalla lavorazione tradizionale) e il numero limitato di fasi di serraggio permette di aumentare la qualità dei componenti lavorati e la sicurezza di processo.
I vantaggi della multitasking
Con la lavorazione multitasking i tempi di inattività sono ridotti al minimo, grazie al coordinamento delle macchine all’interno della cella di lavorazione EMAG, con un notevole risparmio anche dal punto di vista del consumo energetico. Le VMC 450-5 MT possono opzionalmente essere equipaggiate con diversi sistemi di misura, che garantiscono una gestione continua della qualità, ottenendo una produzione eseguita in modo più preciso, rapido ed economico e quindi nel complesso con costi inferiori. Un altro elemento da non sottovalutare del centro multifunzionale è il magazzino utensili di cui è equipaggiato, con fino ad 80 posizioni utensile. Qui è possibile depositare tutti gli utensili e gli utensili gemelli (in caso di usura) necessari per i diversi lotti. Il cambio utensile viene eseguito in modo automatico, quindi in fase di riattrezzamento macchina, l’operatore deve sostituire solamente le griffe. Questa operazione viene eseguita sul lato anteriore, mentre il caricamento dei particolari tramite robot può proseguire senza fermi macchina o fermi linea attraverso un portello laterale.

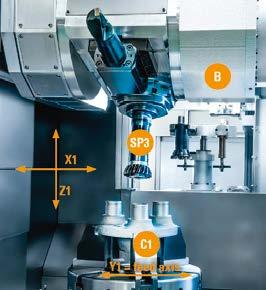
Configurazioni personalizzate
Naturalmente la VMC 450-5 MT non è solamente adatta per la lavorazione dei portasatelliti, ma può essere configurata in modo personalizzato, in base alle richieste del cliente, partendo dalla struttura base modulare standard. Sono ad esempio disponibili diverse varianti di mandrino, portapezzi specifici oppure una contropunta. Per tutte queste ragioni la VMC 450-5 MT rappresenta una vera e propria soluzione multifunzionale, concepita anche con una struttura ad ingombro ridotto, per accogliere anche le esigenze dei clienti in termini di spazio. Con questo centro di tornitura/fresatura a 5 assi EMAG crea il futuro, offrendo una soluzione di lavorazione completa per tutti i settori dell’industria meccanica.
DAL 1991 AD OGGI, L’ESPERIENZA DI MANDELLI SISTEMI NEL SETTORE DELLE MACCHINE MULTITASKING HA PORTATO LA SOCIETÀ ALLA PRODUZIONE DI IMPIANTI VERSATILI E CAPACI DI EVOLVERE NEL TEMPO GRAZIE ALL’IMPLEMENTAZIONE DI SEMPRE NUOVE FUNZIONALITÀ
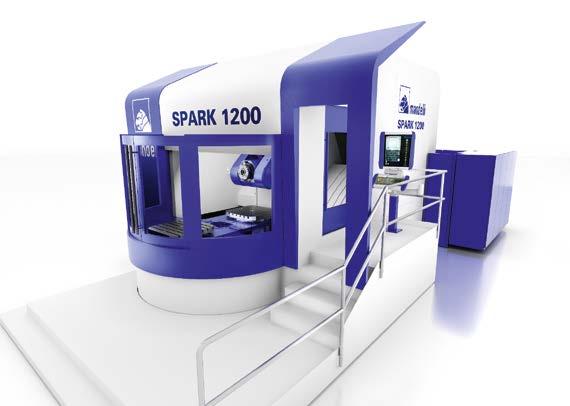
MANDELLI SISTEMI
IN MANDELLI IL FUTURO ARRIVA
FPRIMA, DA PIÙ DI 80 ANNI
Frutto di una costante evoluzione tecnologica dei sistemi Macchina ibrida o multitask? proposti, con oltre trent’anni di esperienza nel settore “Per macchina multitasking – precisa Marco Colombo - si delle macchine multitasking, l’innovativa linea di centri di intende una macchina che è capace di integrare tecnologie lavoro proposta da Mandelli Sistemi risponde al concetto di diverse, senza alcun tipo di compromessi. Nel nostro caso, flessibilità, sempre più richiesto dal mercato, assicurando, il concetto di multitasking è riferito alle due tecnologie al contempo, elevate prestazioni sia in tornitura che in di asportazione di truciolo ad utensile rotante, quindi fresatura e massima precisione, grazie all’implementazioni fresatura, foratura, alesatura, barenatura e maschiatura, e a di funzionalità sempre nuove. Una sfida, quella della pezzo rotante e utensile fisso, ovvero la tornitura. Una linea realizzazione di centri di lavoro che integrino due o più di prodotto storica per Mandelli, che per prima, nel 1991 tecnologie complementari in una sola macchina, frutto realizzò una macchina di fresatura – tornitura a partire da un dell’esperienza e delle conoscenze maturate da Mandelli centro di lavoro orizzontale, la Mandelli 8UT, una macchina nel settore della costruzione di centri di lavoro sin dal di fresatura a cui fu aggiunta una tavola che potesse ruotare lontano 1932. Per definire meglio il concetto di macchine velocemente. Quello che si ottenne, una macchina che aveva multitasking per Mandelli, le tipologie e gli impieghi di perso un po’ di performance in fresatura ma non riusciva queste macchine, abbiamo incontrato Marco Colombi, a tornire quanto un tornio verticale, può essere definito Responsabile commerciale di Mandelli Sistemi. un ibrido. Per rispondere alla domanda, possiamo definire
“ibrido” una macchina in cui si integra una tecnologia ottenendo un sistema che ha una qualche limitazione nelle performance, mentre per “multitasking” intendiamo una macchina in cui si integrano due o più tecnologie integrate nello stesso mezzo produttivo, conseguendo alte performance per entrambe le lavorazioni, senza alcun tipo di compromesso. Una macchina, nel caso di Mandelli Sistemi, capace di assicurare performance del tutto sovrapponibili ai tradizionali impianti concepiti per le due singole operazioni ad asportazione di truciolo”.
Innovazione e tradizione
Una sfida affrontata e vinta con la linea d’impianti SPARK che affonda le sue radici nell’esperienza e nelle conoscenze maturate nel settore della costruzione di centri di lavoro da una realtà presente sul mercato sin dal lontano 1932, a cui si è giunti , sulla base di una ventina d’anni di esperienza nel settore delle macchine multitasking e con una serie di accorgimenti particolari, a partire proprio da quel prodotto fin da subito di grande successo lanciato nel lontano 1991. La linea SPARK, lanciata negli anni 2000, è una linea che sviluppa un nuovo concetto di Centro di Lavoro Orizzontale a 5 assi. Nel 2005 viene presentata al mercato la nuova linea di centri di lavoro veloci e performanti: nasce la SPARK X che rivoluziona il concetto tradizionale del centro di lavoro con una configurazione a tre assi lineari dal lato utensile ed il pezzo in lavorazione sulla tavola girevole fissata nel basamento. “Quando abbiamo realizzato la nuova linea di macchine tornitura-fresatura – spiega Colombo - abbiamo deciso di dedicare un’architettura particolare alle macchine che possono fare sia tornitura che fresatura. La specificità di questo sistema consiste nel fatto di avere la tavola fissa, con il solo movimento rotatorio, mentre tutti gli assi lineari si trovano sul lato utensile: questo consente, in tornitura, di avere le performance proprie di un tornio grazie alla tavola annegata nel basamento, che garantisce la massima stabilità e robustezza dell’impianto, dunque grande precisione. L’approccio di Mandelli Sistemi è quello di una linea di prodotto dedicata, la linea SPARK, completata da una serie di opzioni standard. La personalizzazione riguarda circa il 20-30% della produzione di macchine. la capacità di soddisfare le richieste speciali del cliente costituisce una parte importante della nostra offerta”.
La macchine Mandelli sono dotate di una serie di accessori che possono essere standard o personalizzati che determinano le performance della macchina per una specifica applicazione. “In queste macchine, tutte dedicate alla lavorazione di materiali metallici, da quelli più tenaci, ad esempio le leghe a base di nichel o cobalto, agli acciai di svariata composizione e durezza, le ghise e le leghe leggere, come l’alluminio e il rame, - aggiunge Colombo - l’elemento che va specializzato è il mandrino, oltre alle opzioni di automazione disponibili: le sonde di misura pezzo, il laser di presetting utensile, i sensori di controllo integrità utensile per garantire il funzionamento delle macchine senza il presidio dell’operatore, le opzioni per ottimizzare la tecnologia, ad esempio, sempre più importante nel settore dell’aeronautica, la gestione del refrigerante con possibilità di arrivare a 350 bar in tornitura e 100 in fresatura per massimizzare la vita dell’utensile”.
Efficienza in ottica Lean
“La linea SPARK X – continua Colombo - rappresenta il nostro centro di lavoro orizzontale per eccellenza. SPARK è pensata per la lavorazione ad elevate prestazioni di un’ampia gamma di materiali: dall’alluminio ai metalli più duri e tenaci, eccelle nel campo degli acciai e delle ghise. Un punto di riferimento per le lavorazioni complesse a 5 assi. La linea SPARK X va dalla 1200 alla 3500, dove il dato numerico rappresenta il diametro del pezzo lavorabile in termini di mm, e prevede l’opzione multitasking offerta sui tre modelli 1200, 1600 e 2100”.
La SPARK 1200, nata nel 2020, è il risultato delle ottimizzazioni sviluppate da Mandelli attorno all’architettura del prodotto SPARK. Nasce per estendere le lavorazioni multitasking a pezzi di dimensione medio/piccola con swing di 1200 mm e portata di 2000 kg e per soddisfare
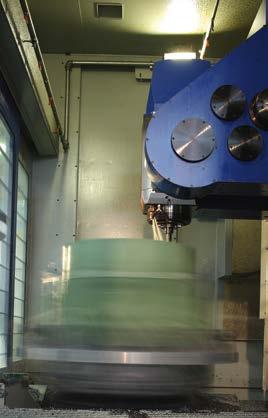
Testa A con spruzzo refrigerante.
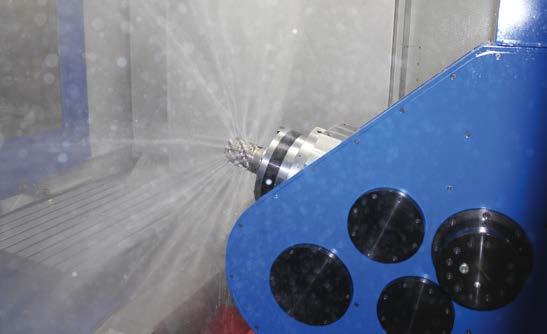
la richiesta di conseguire un alto grado di flessibilità in aggiunta all’efficienza produttiva. “Oggi essere presenti sul mercato globale, comporta la necessità di lavorare in maniera flessibile, non facendo magazzino e potendo riconfigurare rapidamente la propria produzione. In quest’ottica la tendenza a concentrare sempre più tecnologia all’interno del medesimo mezzo produttivo aiuta molto durante i processi di lavorazione. Inoltre limitare il numero di volte in cui i pezzi vengono movimentati, riduce la possibilità di errore e aumenta la precisione, con tutti i vantaggi di natura puramente tecnologica della produzione combinata che si riflettono positivamente anche in termini di riorganizzazione del processo produttivo in ottica Lean che ruota intorno a questa tipologia di macchina”, prosegue Colombi.
“Eliminare intere fasi di lavorazione, eliminare delle isole porta non solo vantaggi ma aiuta queste riorganizzazioni. Ad esempio, una recente applicazione che ha visto protagonista la linea Spark è stata realizzata per un cliente impegnato del comparto aeronautico che aveva lavorazioni eseguite su tre macchinari, tornio verticale, centro di lavoro orizzontale e centro di lavoro verticale - un sistema molto efficiente ma al contempo molto rigido perché un guasto nel tornio verticale comporta una perdita di produzione del 100%. In questa commessa, l’esigenza del cliente, che era quella di avere una macchina flessibile che fosse in grado di fare tutte e tre le lavorazioni, è stata soddisfatta con un centro multitasking a 5 assi che potesse fare sia da centro orizzontale che verticale che da macchina di tornitura. È chiaro che questo tipo di soluzione, nell’ipotesi di un guasto, comporta una perdita del 33% della produzione e garantisce al cliente finale una maggiore certezza della produzione. Attualmente la richiesta maggiore delle aziende verte sul bisogno che sia garantita la sicurezza della produzione e queste macchine consentono una maggiore continuità in tal senso”.
Opzioni in ottica 4.0
“Per Mandelli Sistemi – spiega Colombi - l’investimento maggiore in termini di Ricerca&Sviluppo è sul tema Industria 4.0, ambito in cui eravamo già presenti prima ancora dell’Iperammortamento della legge Calenda. Oggi siamo in grado di offrire iPum@suite4.0, il pacchetto Mandelli di nuove soluzioni, accessori e App incentrate sulla Smart Factory quale soluzione pratica ed efficace al nuovo paradigma dell’Industria 4.0 e dell’ IoT (Internet of Things) che si basa sui 6 concetti fondanti di “innovatività”, “immaginazione”, “intelligenza”, “ingegnosità”, “ispirazione” ed “intuitività” e si compone di 5 moduli indipendenti costituiti da un software e applicativi gestionali capaci di garantire le condizioni di lavoro più performanti. iPum@ Suite 4.0 nasce dall’idea di fornire una manutenzione predittiva efficiente e prevede un insieme di prodotti e servizi che integrano le più avanzate tecnologie di raccolta, condivisione e analisi dati in tempo reale fornendo una supervisione completa del flusso di lavoro e dell’operatività di ogni macchinario sia al cliente che al costruttore permettendo così di massimizzare l’operatività dell’impianto”.
FONDATA NEL 1922 DA PIETRO CARNAGHI A VILLA CORTESE, L’AZIENDA È OGGI UN IMPORTANTE PUNTO DI RIFERIMENTO NEL PANORAMA INTERNAZIONALE DEI PRODUTTORI DI MACCHINE UTENSILI, GRAZIE AL CONTINUO E COSTANTE SVILUPPO DELLE TECNOLOGIE E DELLE IDEE, SUPPORTATE DA QUASI 100 ANNI DI ESPERIENZA DIRETTA SUL CAMPO

PIETRO CARNAGHI SPA
UNA
MULTITASKING
FSU MISURA! in verticale – molte delle quali destinate a settori applicativi estremamente esigenti - offre una vasta gamma di soluzioni multitasking che includono una serie di modelli che fanno leva sull’alta possibilità di personalizzazione. “Lo spirito con cui
La famiglia Carnaghi è oggi rappresentata dalla terza e dalla l’azienda realizza una macchina o un suo accessorio su commessa quarta generazione, attiva nella gestione aziendale, affiancata da del cliente – spiega Davide Lavazza – è quello di un approccio figure manageriali che ne condividono la visione strategica. Da a quattro mani, nel corso del quale, a fronte dell’esperienza del sempre, punto di forza dell’azienda è quello di offrire una gamma cliente su lavorazioni simili, la Pietro Carnaghi offre la propria di prodotti fortemente personalizzati in funzione delle esigenze capacità di customizzazione dei prodotti e di definizione del cliente in termini di lavorazioni, flessibilità e produttività del delle specifiche degli accessori speciali a completamento della processo richiesto. Ne parliamo con Davide Lavazza, Direttore soluzione richiesta”. Nel corso degli ultimi dieci anni, nell’ambito commerciale di Pietro Carnaghi. della produzione di macchine multitasking, la richiesta del mercato, e quindi dei clienti, è stata quella di ottimizzare il Una produzione fortemente personalizzata processo produttivo e di accorparlo su macchinari in grado di eseguire se non tutte, almeno la gran parte delle lavorazioni
La Pietro Carnaghi, forte di decenni di esperienza nella necessarie per completare la produzione del componente. “Una progettazione e nella costruzione di macchine per la lavorazione richiesta – aggiunge Lavazza - molto forte anche su macchine
estremamente importanti dal punto di vista delle dimensioni: i nostri torni verticali partono da un minimo diametro tornibile di 1 m ad un massimo di 17 metri di tornitura mentre le nostre macchine gantry, fresatrici a portale, vanno da un minimo di 3 m di passaggio a 14. La macchina con la corsa più lunga mai realizzata ha 52 m di corsa utile. Questo ha fatto sì che, nella naturale evoluzione del prodotto Carnaghi, si sia passati da torni verticali in grado di eseguire operazioni di tornitura e fresatura, cioè prodotti sostanzialmente ibridi, a vere e proprie macchine multitasking, in grado di eseguire operazioni molto complesse, al fine di migliorare e ottimizzare il processo produttivo e nello stesso tempo limitare gli interventi umani nel processo stesso”.
L’evoluzione dei prodotti Carnaghi è stata guidata da una scelta che fonda le sue radici in motivazioni sia economiche che logistiche che sono alla base delle richieste dei clienti: “le prime – spiega Lavazza – sono finalizzate al contenimento dell’impegno economico conseguente all’acquisto di due macchine che realizzino lo stesso componente, puntando all’acquisto di un’unica macchina in grado di eseguire entrambe le lavorazioni, le seconde dettate da motivazioni logistiche e di maggiore precisione legate alla riorganizzazione del processo produttivo, conseguenti alla limitazione del numero di volte in cui i pezzi vengono movimentati da una macchina all’altra per l’esecuzione delle lavorazioni, alla difficoltà di reperire gli spazi in officina per il posizionamento di due macchine, oltre che all’impegno di due operatori per il funzionamento delle due macchine impiegate. Tutto ciò può essere risolto con l’acquisto di una macchina singola flessibile. Eliminare intere fasi di lavorazione, eliminare delle isole porta grandi vantaggi in termini di produttività”.

Come nasce la multitasking
“In Carnaghi, – spiega Lavazza - avendo una lunga storia di macchine ibride, cioè macchine che hanno capacità di tornire

e fresare, dando per scontata l’applicazione della fresatura sul tornio verticale o della tornitura su una macchina a portale, che costituisce per noi lo standard di richiesta, la macchina multitasking è quella che accorpa anche altre funzionalità, tipiche di macchine dedicate. Capita sempre più spesso che il cliente chieda di inglobare all’interno della produzione tipica Pietro Carnaghi, ovvero macchina tornio-fresa, la capacità di realizzare, ad esempio, degli ingranaggi. La multitasking integra lavorazioni proprie di un’altra categoria di macchine. Lo stesso accade per la rettifica, nel momento in cui il cliente chiede una macchina che abbia la capacità di tornire, forare, fresare e anche rettificare, integrando questa ulteriore applicazione nel tornio verticale. In Carnaghi la definizione di macchina multitasking è perciò qualcosa di dinamico, che varia con il mercato: in relazione a quella che è la sua evoluzione, viene definito il nuovo standard della macchina. Se agli inizi del novecento, la macchina multitasking più spinta era semplicemente quella che torniva e fresava, oggi queste macchine coprono il 90% del nostro mercato. Di questo 90% una buona parte diventa macchina multitasking perché vengono integrati degli accessori che consentono altre lavorazioni. In una nostra recente applicazione per il settore della difesa, che abbiamo definito “fresatrice a portale super multitasking” abbiamo integrato tornitura, fresatura, rettifica e, in aggiunta, un trattamento termico di tempra. La macchina è in grado di realizzare il ciclo complessivo del componente: dalla lavorazione meccanica, al trattamento termico, all’operazione di finitura tramite rettifica. Oggi, per noi, la multitasking è quella che ingloba anche altre tipologie di applicazioni, non solo lavorazioni meccaniche”.
Precisione e affidabilità
L’esperienza decennale di Pietro Carnaghi nella progettazione e nella costruzione di queste macchine – molto spesso destinate a settori applicativi estremamente esigenti e critici, quali l’aeronautico – ha fatto sì che i clienti si affidino all’azienda non solo per la qualità delle macchine ma anche per il servizio correlato alla macchina dal punto di vista dell’applicazione: dai miglioramenti del processo produttivo con attrezzature e utensili speciali alle lavorazioni con alta pressione, in cui il lubrorefrigerante raggiunge e talvolta supera i 350 bar di pressione durante le operazioni di tornitura per migliorare la vita utile dell’utensile, fino alla messa in servizio della macchina, al supporto alla produzione ed infine alla scolarizzazione. “Si tratta – precisa Lavazza - del consolidamento, contestuale a tanti anni di esperienza in tornitura, della produzione di macchine che nascono già ibride e vengono arricchite con una “iniezione tecnologica” importante, includendo altre applicazioni e lavorazioni. L’elevato grado di precisione delle nostre macchine è legato non solo alle caratteristiche tecnologiche delle macchine ma anche all’esperienza e alla capacità dei nostri tecnici montatori di realizzare un controllo molto elevato della qualità del processo, attraverso il ferreo controllo delle fasi di montaggio e della qualità del montaggio eseguito. Questo rappresenta un punto di forza di Carnaghi che peraltro ha un turn over molto basso, caratterizzato spesso da un trasferimento dell’esperienza acquisita dai nostri tecnici che si tramanda di padre in figlio”.
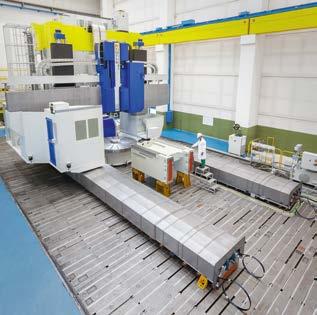
Innovazione al centro della produzione
L’innovazione tecnica in termini di ricerca e sviluppo ha determinato scelte tecniche dell’azienda che garantissero la vita utile e la precisione della macchina. “Tutte le macchine – spiega Lavazza - sono idrostatiche con sostentamento degli assi su cuscinetto di olio, cosa che rende la manutenzione semplice e saltuaria rispetto alle soluzioni tradizionali con guide a rulli, grazie alla capacità della macchina di assorbire le vibrazioni e forze di taglio superiori. In questo modo, la macchina è più stabile nel tempo e garantisce le tolleranze per un tempo decisamente superiore”. In tal senso si è da sempre operata una manutenzione preventiva per il mantenimento della macchina e delle sue performance. “Le macchine Carnaghi – aggiunge Lavazza – sono dotate di sensori digitali affidabili per il monitoraggio dello stato di salute della macchina che rendono possibile la manutenzione predittiva attraverso l’analisi e l’elaborazione dei dati raccolti. Inoltre la Carnaghi ha sviluppato internamente un sistema software e hardware dedicato CMS (Carnaghi Machine Supervisor), una tecnologia smart che nasce ormai alcuni anni fa per eseguire la manutenzione predittiva e che, oggi, si sposa con i paradigmi dell’Industria 4.0, per rielaborare i dati e renderli all’operatore in formato leggibile e facilmente comprensibile, in grado di autodiagnosticare lo stato di salute della macchina. Attualmente si sta lavorando per rendere il sistema sempre più efficiente e integrato e in grado di essere controllato anche da remoto”.
RENISHAW
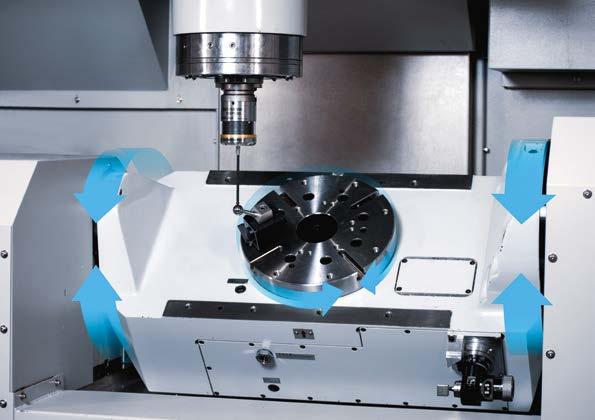
LA TECNOLOGIA RENISHAW AL SERVIZIO DELLE MACCHINE MULTITASK
LE MACCHINE DI NUOVA GENERAZIONE, IN PARTICOLARE LE MULTITASK, SONO MACCHINE ESTREMAMENTE COMPLESSE CHE OFFRONO NOTEVOLI VANTAGGI IN TERMINI DI PRESTAZIONI E PER LE QUALI SONO NECESSARI SISTEMI DI MESSA A PUNTO EFFICACI: PROCESSI SEMPLICI E AL CONTEMPO AFFIDABILI PER ESEGUIRE L’ANALISI DELLE PRESTAZIONI DEGLI ASSI ROTATIVI, CHE IDENTIFICHINO I PROBLEMI CAUSATI DA IMPOSTAZIONI NON CORRETTE, COLLISIONI O USURA
UUn punto chiave per effettuare lavorazioni corrette è la conoscenza della posizione del centro di rotazione degli assi rispetto agli assi lineari. Se non si conoscono con precisione questi punti, il controllo della macchina non può guidare gli assi in maniera affidabile e i risultati di lavorazione saranno incoerenti. È necessario dunque uno strumento che sia in grado di determinare i centri di rotazione in modo semplice, veloce ed accurato, in modo che, direttamente in macchina ed in maniera automatizzata, si possano effettuare le verifiche per poter garantire la precisione della macchina nel tempo. AxiSet™ Check-Up, il sistema di Renishaw costituito dal tastatore Rengage™ e dal software AxiSet™, rappresenta la soluzione più conveniente per controllare le prestazioni di allineamento e posizionamento degli assi rotativi e aiutare gli utenti a preservare la stabilità dell’ambiente di lavoro. Sono sufficienti pochi minuti per identificare e, se possibile, correggere automaticamente, i problemi di allineamento e geometria di centri di lavoro 5 assi e macchine multitasking che porterebbero a pezzi non conformi e perdite di tempo nella preparazione dei processi. Ne parliamo con Patrizio Titotto, Responsabile dei prodotti per macchine utensili di Renishaw.
AxiSet Check-Up
“Il sistema costituito dal tastatore Renishaw Rengage™ e dal software AxiSet™ – spiega Titotto - effettua semplici tastature su una sfera in varie posizioni degli assi rotativi in modo che il software possa determinare i valori dei centri di rotazione da immettere nei parametri del controllo numerico. Il nome della famiglia di sonde utilizzate, Rengage™, sta per Renishaw – strain gauge, a ricordare la tecnologia di base del sensore di tipo estensimetrico. Questa consente una precisione più elevata rispetto ai tastatori tradizionali, con un metodo 100% elettronico, in cui il segnale del tastatore, inviato al controllo numerico, misura la forza del tastatore a contatto con il pezzo. Questo garantisce eccellenti prestazioni di misura tridimensionale (3D) e ripetibilità al sub-micron.
Questo sistema può essere utilizzato sia dal costruttore nelle fasi di costruzione e montaggio della macchina ma anche e soprattutto dall’utilizzatore, che disponendo del sistema a bordo macchina, può utilizzarlo con cadenze regolari per monitorare lo status della macchina e applicare delle correzioni, laddove queste si rendano necessarie. Infatti, se utilizzato correttamente, il sistema consente di compensare le piccole variazioni che si determinano in officina ed avere dei centri di rotazione sempre accurati in qualsiasi condizioni di lavoro”.
AxiSet Check-Up Renishaw fornisce un metodo di prova accurato e ripetibile usando routine di ispezione automatiche su un pezzo di riferimento e include una analisi semplice e completa. Per i test si utilizzano sonde a contatto collocate nel mandrino, complemento standard già a bordo della maggior parte delle macchine multiasse, in combinazione con routine di ispezione generate usando macro software specifiche per il modello di macchina e fornite con AxiSet Check-Up.
Il piazzamento è rapido e semplice. Per eseguire la prova si colloca all’interno dell’area di lavoro della macchina una sfera calibrata, utilizzando una semplice base magnetica, mentre la sonda misura automaticamente diversi punti sulla sfera, guidata dalle macro generate dal software. L’utente ha sempre il pieno controllo del processo e può definire specifici angoli di prova per assicurarsi di provare la macchina nelle orientazioni critiche. Per ottenere la massima accuratezza vengono impiegate sonde Renishaw con sistema estensimetrico Rengage™.
“La tendenza degli ultimi anni – continua Titotto - è quella
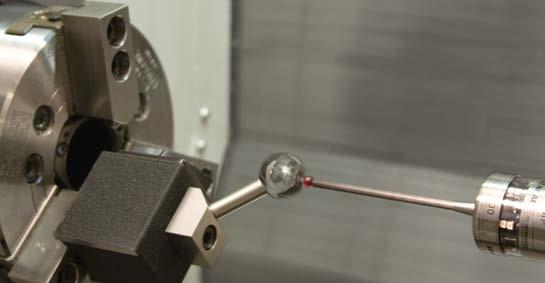
Misura di un particolare con sonda RMP600
di fornire una macchina già accessoriata, in cui il sistema sia già presente, ma è anche possibile retrofittare la macchina con questo dispositivo. Chiaramente ciò è possibile su macchine di ultima generazione che prevedano una compatibilità con il sistema. Inoltre questo sistema può essere applicato su ogni tipo di macchina multitask. In particolare, nel caso in cui la macchina effettui anche lavorazioni di rettifica, prima di questa lavorazione sarebbe opportuno lanciare il sistema, eseguire il controllo e la verifica della cinematica della macchina, eventuale fare l’aggiornamento e la compensazione degli errori, e poi eseguire la rettifica, in quanto questa lavorazione richiede maggiore precisione e accuratezza”.
L’evoluzione tecnologica delle sonde per macchine utensili
Renishaw ha inventato la prima sonda a contatto per macchine utensili negli anni ‘70. Il successo di questo prodotto innovativo, basato su un principio a resistenza cinematica, ha contribuito a garantire all’azienda una posizione di leadership mondiale nella progettazione, produzione e supporto di prodotti di misura dimensionale. Grazie a decenni di continui investimenti nella ricerca e sviluppo, Renishaw è oggi in grado di fornire prodotti di altissima qualità con prestazioni che non temono rivali sul mercato. Le sonde Rengage™, impiegate nel sistema AxiSet Check-Up, incorporano una tecnologia estensimetrica di provata affidabilità, con elettronica ultracompatta e un design meccanico di precisione per prestazioni e capacità che non temono rivali. Sono adatte per un’ampia gamma di applicazioni su macchine utensili e superano le limitazioni legate alle prestazioni 3D che affiggono molte altre sonde. I più recenti prodotti Renishaw che includono questo tipo di tecnologia sono MP250, OMP400 e RMP600.

Le sonde RENGAGE™
Nelle sonde Rengage™, i componenti estensimetrici sono posizionati su micro supporti progettati con estrema attenzione per renderli parte della struttura della sonda, lasciandoli contemporaneamente separati dal meccanismo cinematico. Sono disposti in modo da rilevare le tensioni su tutti gli assi e i loro output vengono combinati elettronicamente tramite alcuni algoritmi brevettati. Quando si raggiunge il livello di soglia in una direzione qualsiasi, viene generato un segnale di trigger con forze decisamente inferiori rispetto a quelle necessarie per le sonde convenzionali. Ciò comporta notevoli vantaggi in relazione a un’ampia gamma di problemi applicativi. Le sonde Rengage sfruttano il meccanismo cinematico Renishaw per riportare lo stilo in posizione. Il sistema vanta 30 anni di continui perfezionamenti e garantisce un ritorno ripetibile, elemento fondamentale per una metrologia accurata. “Dato che la rilevazione è completamente indipendente dal meccanismo della sonda, - spiega Titotto - i dispositivi Rengage sono caratterizzati da bassa forza, elevata ripetibilità ed una caratteristica di comportamento costante, tutti fattori che non sono ottenibili con sonde dal design convenzionale. L’utilizzo di questa tecnologia consente di eliminare fino al 90% gli errori di lobing, che altro non sono che l’errore metrologico del tastatore quando effettua misure interpolate (vedi box). Nelle applicazioni a due assi, tale riduzione rende superflue le operazioni
Lobing della sonda Il lobing è una caratteristica di tutte le sonde. È causato dalla flessione dello stilo e dal movimento del meccanismo della sonda prima che questa registri il contatto con una superficie. Pertanto dipende da: • Lunghezza e rigidezza dello stilo • Forza richiesta per la generazione del segnale della sonda • Direzione del contatto con la superficie • Design del meccanismo della sonda Tutte le sonde presentano un certo livello di lobing. Nel caso delle misure a due assi, gli errori potenziali possono essere calibrati con relativa facilità. Tuttavia, nella misura a tre assi, gli errori di lobing sono maggiori o più complessi da compensare, soprattutto con alcune sonde convenzionali. Tali errori sono significativi e possono avere un impatto negativo sull’accuratezza e sulla ripetibilità delle misure 3D. “Solitamente - spiega Titotto - la ripetibilità è un parametro unidirezionale, misurato in base all’errore del tastatore lungo un unico asse, ma se la misura è effettuata lungo una diagonale, che sia un piano inclinato o un profilo, una superficie curva o una sfera, il sensore che viene eccitato lungo i tre assi contemporaneamente può determinare nei tastatori tradizionali un errore più elevato, che nei tastatori Rengage viene contenuto comunque al di sotto del micron”. di calibrazione, mentre nelle applicazioni a tre assi o con geometrie complesse garantisce prestazioni assolutamente impareggiabili. Di questa famiglia fanno parte tastatori sia a trasmissione radio che infrarossi”. La miniaturizzazione dei componenti e la tecnologia a stato solido vengono combinate per dare vita a una serie di sonde Rengage compatte e ultracompatte, in grado di fornire soluzioni innovative per soddisfare le esigenze odierne di accuratezza e di installazione in macchine di piccole dimensioni. “Il confronto tra le sonde dotate di tecnologia Rengage™ con prodotti convenzionali di altre marche, effettuato con esempi basati su test reali, - aggiunge Titotto - mette in risalto le eccellenti prestazioni della tecnologia Rengage. L’errore medio a 40 µm è 10 volte superiore rispetto a quello della sonda Rengage. In altre parole, l’accuratezza 3D delle sonde Rengage è 10 volte migliore! Dato che la macchina utensile utilizzata per il test era una tipica macchina da produzione, vale la pena valutare le possibilità derivanti dall’utilizzo della tecnologia Rengage in combinazione con macchine ad elevata accuratezza. Grazie alla sua ripetibilità unidirezionale di soli 0,25 µm 2σ, la tecnologia Rengage garantisce un’accuratezza senza paragoni su tutti i piani”.
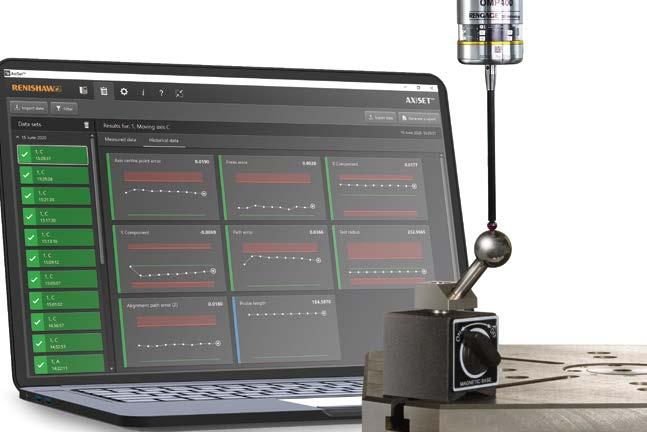
SANDVIK COROMANT

SANDVIK COROMANT, CHE FA CAPO AL GRUPPO GLOBALE DI INDUSTRIAL ENGINEERING SANDVIK, È ALL’AVANGUARDIA NEGLI UTENSILI PER ASPORTAZIONE TRUCIOLO, NELLE SOLUZIONI DI LAVORAZIONE E NEL KNOW-HOW E SEGNA CONTINUAMENTE NUOVI STANDARD, CON INNOVAZIONI IN GRADO DI SODDISFARE LE ESIGENZE DEL SETTORE DELLA LAVORAZIONE DEI METALLI, GUIDANDOLI VERSO LA PROSSIMA ERA INDUSTRIALE
TWIN-TOOL COROTURN PRIME, IL
PORTAUTENSILE PER MACCHINE MULTI-TASK
II cospicui investimenti in R&S, nonché in servizi di formazione elementi permettono agli utilizzatori di massimizzare i vantaggi e le forti partnerships con i clienti assicurano lo sviluppo di di PrimeTurning sui centri di torni-fresatura multi-task e sui torni tecnologie di lavorazione innovative, che continueranno a plasmare verticali (VTL). Considerando i portautensili radiali già esistenti, il futuro dell’industria manifatturiera indicando nuove strade da Sandvik Coromant dispone adesso di un’offerta completa per le seguire. operazioni PrimeTurning.
L’azienda, specialista in utensili da taglio e sistemi di Una delle novità della gamma è il portautensile Twin-tool attrezzamento, ha presentato la nuova gamma di portautensili CoroTurn Prime per macchine multi-task. Sui portautensili assiali e multi-task CoroTurn® Prime, pensati per aiutare le Twin-tool, è possibile montare insieme inserti CoroTurn Prime officine meccaniche a implementare la nuova metodologia di tipo A e di tipo B e ciò consente ai costruttori, ad esempio, di PrimeTurning™ per la tornitura in tutte le direzioni. Questi nuovi eseguire la sgrossatura con un inserto di tipo B prima di passare
alla finitura con un inserto di tipo A. “Le moderne macchine multitask sono pensate per la lavorazione completa dei componenti ma, generalmente, hanno un tempo di cambio utensili lento, spesso attorno ai 15-20 secondi - spiega Håkan Ericksson, Product Manager General Turning presso Sandvik Coromant. - Di conseguenza, il nuovo portautensile Twin-tool permetterà ai clienti di risparmiare una notevole quantità di tempo nel momento in cui devono cambiare utensile”.
Inoltre, la possibilità di lavorazione sull’asse B delle macchine multi-task permette all’operatore di programmare l’angolo dell’utensile per incrementi precisi. Quando la macchina lavora sull’asse B, i portautensili neutri consentono di godere della massima accessibilità. Tutto questo, se combinato a operazioni ottimizzate, crea i presupposti per enormi risparmi in termini di tempo e per un notevole incremento della produttività, aiutando i costruttori a ridurre le scorte di utensili e ad assicurarsi un vantaggio competitivo.
Twin-tool CoroTurn Prime
Sono sei i nuovi portautensili multi-task che possono essere montati a un angolo di 45° per la lavorazione sull’asse B e utilizzati con inserti CoroTurn Prime di tipo A o B. Le opzioni per le macchine multi-task includono quattro portautensili per un solo inserto e due portautensili Twin-tool per due inserti. Il
C
portautensile Twin-tool CoroTurn Prime può essere utilizzato
M
anche con Coromant Capto® C5 – C8. La gamma, inoltre, prevede Y
una serie di portautensili assiali per torni verticali che completa
CM l’offerta di Sandvik Coromant per PrimeTurning, consistente
in portautensili assiali, radiali e multi-task. In totale, sono otto i
MY
CYnuovi portautensili specifici per montaggio assiale. Questo tipo di CMYportautensili è compatibile con la maggior parte dei torni verticali e può essere utilizzato con Coromant
K
Capto con inserti CoroTurn Prime di tipo A o B. Anche se il metodo PrimeTurning è applicabile all’intera area della tornitura generale, chi può trarne i maggiori vantaggi sono le officine meccaniche con lotti di grandi dimensioni (automotive) e quelle che lavorano componenti di grandi dimensioni (aerospaziale), settori in cui la riduzione di cambi utensile, tempi di setup e fermi di produzione è fondamentale.In definitiva, il metodo in tutte le direzioni PrimeTurning e gli utensili CoroTurn Prime permettono ai costruttori di eseguire le loro operazioni di tornitura in modo molto più efficiente. Rispetto alla tornitura convenzionale, è possibile ottenere un aumento della produttività del 50-80% e una durata utensile superiore di 1.5–2 volte.
Maggiore velocità di
traslazione con le soluzioni di filettatura personalizzate di Eichenberger

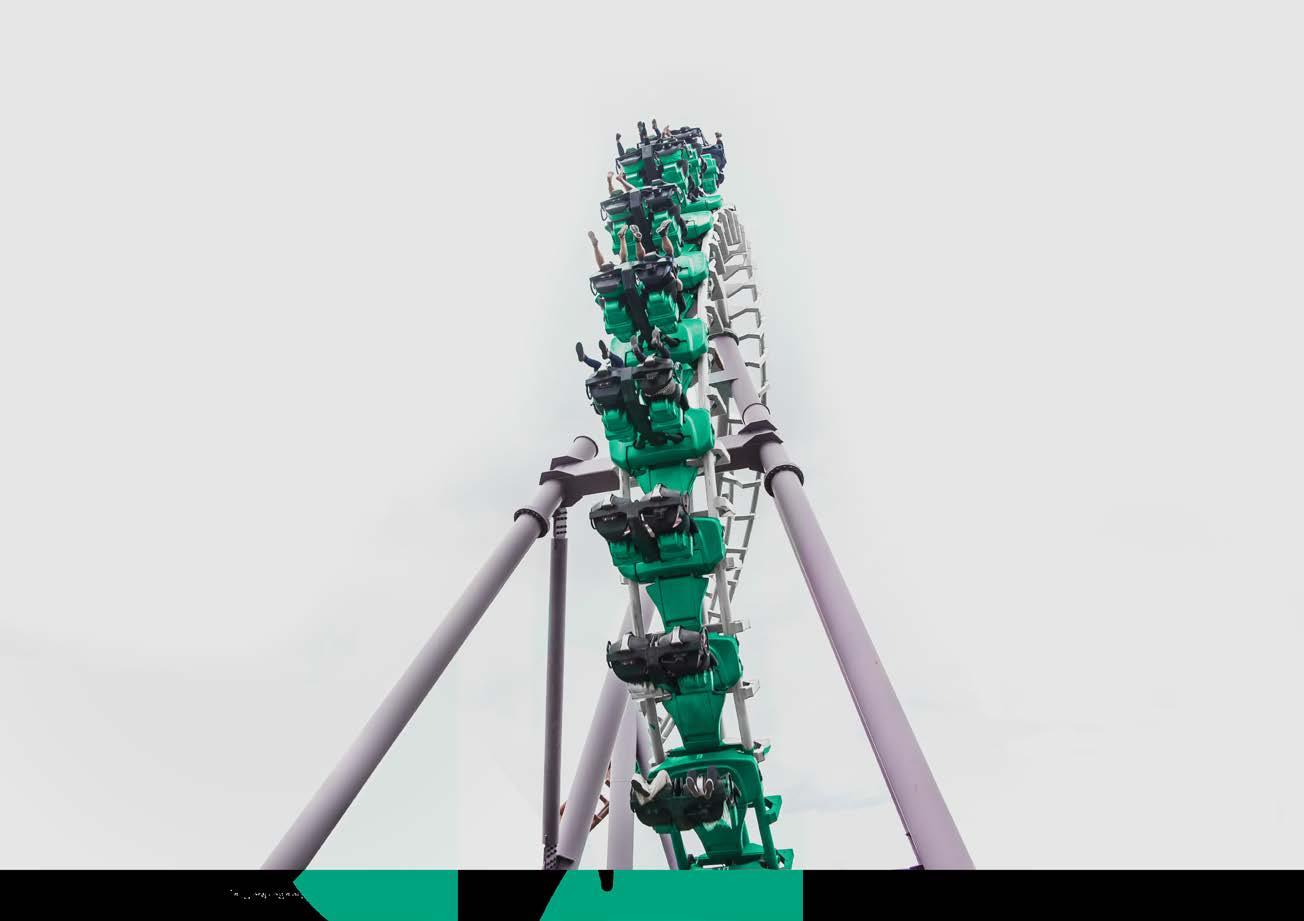
100% Swiss made
Eichenberger Gewinde AG 5736 Burg · Schweiz T: +41 62 765 10 10
www.eichenberger.com
Un’impresa del gruppo Festo
LE SOLUZIONI MULTITASKING, CHE PERMETTONO DI EFFETTUARE DIFFERENTI OPERAZIONI DI LAVORAZIONE CON UN’UNICA MACCHINA, CONSENTONO DI RIDURRE TEMPI CICLO E COSTI, AUMENTANDO NEL CONTEMPO IL LIVELLO DI EFFICIENZA DEI PROCESSI DI LAVORAZIONE
SORALUCE
SOLUZIONI COMPLETE ORIENTATE
ALLA MASSIMIZZAZIONE DELLA L PRODUTTIVITÀ Le piccole e medie realtà del panorama industriale italiano hanno già da qualche anno evidenziato la necessità di rinnovare il proprio parco macchine, talvolta obsoleto e con impianti aventi una media di circa 15 anni di vita, sostituendole con soluzioni innovative che le rendano sempre più competitive, che consentano la riorganizzazione della propria struttura interna e che permettano di massimizzare la loro capacità produttiva. Le macchine multitasking rappresentano una tra le svariate proposte che SORALUCE elettrosaldate, un fattore che su macchine di medio-grandi dimensioni può alterare considerevolmente la geometria dell’impianto provocando errori geometrici sul componente in lavorazione. Inoltre, la ghisa presenta un elevato coefficiente di assorbimento delle vibrazioni e consente quindi di preservare tutte le componenti della macchina e permette all’utensile di lavorare nelle migliori condizioni, con un conseguente aumento della vita dell’utensile e della qualità della finitura del pezzo. Il sistema delle guide offre al mercato. I centri multitasking SORALUCE, che lineari a ricircolo di rulli combinate con pattini smorzatori vanno dai centri di fresatura SORALUCE modello TA-M, è importante e garantisce elevata dinamica, rigidità e alle fresalesatrici a montante mobile della serie F, fino alle precisione nelle lavorazioni, ottenendo così una eccellente macchine a portale gantry della serie P, sono la soluzione produttività, riducendo i costi di manutenzione al minimo. ideale per ottenere la massima reddittività nella lavorazione Quindi, estrema rapidità nelle lavorazioni senza rinunciare di componenti tecnicamente complessi. In tutti i settori alla precisione e alla produttività. Flessibilità dunque è la industriali è stata evidenziata la necessità di realizzare parola d’ordine per le macchine multitasking SORALUCE componenti in un unico set-up, abbattendo i tempi morti e le quali permettono di effettuare diverse lavorazioni, tra aumentando la produttività. Per rispondere a questa esigenza cui operazioni di fresatura, tornitura, alesatura, foratura, SORALUCE ha sviluppato numerose macchine utensili atte maschiatura e rettifica in un’unica macchina ed in un unico alla fresatura/tornitura/rettifica pensate per clienti attivi in piazzamento. Ciò è oggi possibile con efficienza e precisione differenti settori merceologici: meccanica generale, energia, per pezzi di differenti dimensioni e forme. L’ampia offerta beni strumentali, stampi, ferroviario, ecc.... Più che mai oggi i SORALUCE include una serie completa di dispositivi clienti hanno la necessità di lavorare rapidamente, riducendo multitasking progettati in-house come teste, tavole girevoli e i costi di manutenzione e di attrezzaggio e incrementando le cicli personalizzati, che garantiscono una elevata produttività tipologie di operazioni effettuabili in un’unica macchina. e una maggiore funzionalità. Le opzioni multitasking Flessibilità e precisione complessi e pesanti che presentano forme differenti di medie Le fresatrici SORALUCE sono realizzate con una e grandi dimensioni con risultati di lavorazione ottimali. struttura interamente in ghisa e adottano guide lineari a permettono di lavorare in un unico piazzamento componenti ricircolo di rulli combinati con pattini smorzatori, elementi Non solo fresatura e tornitura che garantiscono rigidità dinamica ed elevata precisione In questo contesto SORALUCE ha riformulato il concetto volumetrica. La scelta legata all’impiego di una struttura in di multitasking, tradizionalmente associato all’integrazione ghisa è legata al fatto che quest’ultima soluzione non risente in un’unica macchina di processi di tornitura e fresatura, di tensioni interne che si generano invece nelle strutture grazie allo sviluppo di tecnologie avanzate che permettono di

incorporare anche i processi di rettifica. Quest’ultima operazione costituisce la fase che richiede maggior precisione e permette di concludere lavorazioni di pezzi industriali ad alto valore aggiunto. Il centro di fresatura/tornitura/rettifica SORALUCE modello TA-M, è una macchina capace di realizzare operazioni di fresatura, tornitura e rettifica per pezzi di differenti dimensioni e forme con grande efficienza e precisione. “Questa soluzione permette di ridurre la quantità di fermi macchina necessari e il tempo richiesto per la preparazione dei pezzi. Oltretutto minimizza i tempi ciclo e il rischio di errori, rispondendo appieno Operazione di rettifica nella fresatrice multitasking SORALUCE modello TA-M ai requisiti di versatilità, produttività ed efficienza del concetto “multitasking”. Si tavola di fresatura-tornitura con capacità per pezzi fino a tratta di un modello concepito come risposta alla necessità 8000 kg in fresatura e 2000 kg in tornitura e con una gamma di lavorare componenti estremamente complessi” aggiunge di velocità di 6 ÷ 400 giri/min. Progettata per ottenere la Andres Mazkiaran (Presidente di SORALUCE S.COOP.). massima stabilità, questa soluzione dispone di corsa verticale In concreto, il centro di fresatura/tornitura/rettifica 1250 ÷ 1500 mm e trasversale 1200 mm, l’elevata potenza SORALUCE modello TA-M è dotato di testa di fresatura/ di cui è dotata permette di realizzare importanti operazioni tornitura multifunzione SORALUCE H200T, equipaggiata di sgrossatura. Allo stesso tempo, questa macchina può di un innovativo sistema di bloccaggio della rotazione del eseguire operazioni di rettifica incorporando cicli specifici mandrino, che le permette di utilizzare utensili di fresatura che rendono possibile una facile programmazione delle e tornitura direttamente, senza la necessità di avere altri differenti operazioni. Compatta ed ergonomica, si distingue elementi intermedi. Inoltre, la macchina incorpora una per la facilità d’accesso alla zona di lavoro, sia dalla parte frontale che dalla zona posteriore, per facilitare il set-up dei pezzi ed operazioni di misurazione. Oltre al modello TA-M, SORALUCE produce le fresatrici-alesatrici multitasking della serie F. L’architettura del montante mobile di questa famiglia di macchine utensili permette, in base alla versione scelta, di integrare più stazioni di lavoro per la lavorazione in pendolare, consentendo la lavorazione di pezzi di tipologie diverse con il carico e scarico in tempo mascherato. La macchina risponde sia ai requisiti di multitask e di versatilità, sia alle esigenze di lavorazione con un numero minimo di piazzamenti del pezzo. Il centro Fresatrice a portale multitasking SORALUCE modello PMG-W20000 multitasking FMT è una macchina
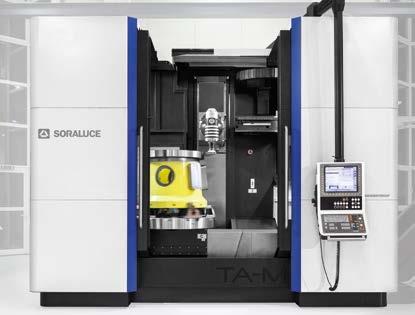
DAS+ DYNAMICS ACTIVE STABILIZER applicato per ottenere la massima qualità superficiale durante le lavorazioni su materiali ostici
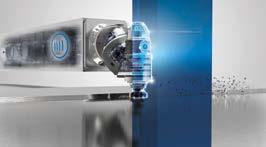
di medie dimensioni dal design innovativo in grado di effettuare lavorazioni di fresatura e tornitura in un unico set-up di pezzi estremamente complessi, mentre i centri multitasking a portale di tipo gantry serie P sono dotati di una elevata precisione e produttività ed integrano diversi processi di lavorazione come la fresatura, l’alesatura e la tornitura (con specifiche tavole girevoli e teste di fresatura e tornitura) per pezzi di medio-grandi dimensioni lavorati in un unico piazzamento.
Tecnologie integrate nei centri multitasking
Tutte le macchine multitasking SORALUCE sono dotate del dispositivo Accura Heads che viene utilizzato dopo lavorazioni di sgrossatura con elevata asportazione ALL in ONE premiato con il Ringier Technology Innovation Award 2020 - Metalworking Industry A fine agosto 2020 si sono tenuti a Shanghai il Summit High Efficiency Processing e Advanced Manufacturing Technology Development 2020 e il Ringier Technology Innovation Awards 2020, ospitati dalla Shanghai Mechanical Engineering Society e Ringier Trade Media. Premiato con diversi illustri premi in Europa, il Centro di lavoro multitasking SORALUCE - Tornitura / Alesatura / Fresatura / Rettifica (ALL in ONE) - è stato molto apprezzato dagli esperti cinesi e premiato con il Ringier Technology Innovation Award 2020 - Metalworking Industry quale riconoscimento delle avanzate e complesse funzioni del centro multitasking, della testa multitasking sviluppata da SORALUCE e della tecnologia di smorzamento attivo delle vibrazioni Dynamics Active Stabilizer Plus (DAS +) (brevetto SORALUCE n. EP 3 017 911).
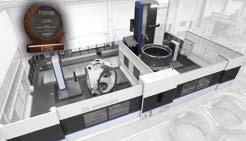
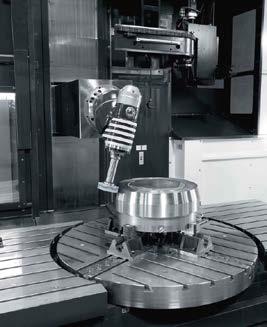
per l’autocalibrazione delle teste automatiche dotate di posizionamento millesimale, prima della successiva lavorazione di finitura. Inoltre, tutte le macchine possono integrare il Dynamic Active Stabilizer (DAS), un innovativo dispositivo, frutto del lavoro congiunto tra SORALUCE e il suo centro di ricerca IK4-IDEKO. In grado di aumentare la rigidità dinamica della macchina, incrementando la produttività della macchina fino al 300%, ed eliminando così il rischio di chatter durante la lavorazione, ovvero le vibrazioni autorigenerative, il sistema DAS migliora la capacità di asportazione e la qualità delle superfici lavorate, riduce lo stress meccanico della macchina, aumenta la vita utile degli utensili e favorisce la lavorazione non presidiata. DAS+®, evoluzione del sistema DAS, include il monitoraggio del livello di vibrazioni, la rilevazione del chatter e due differenti strategie per eliminare il chatter: la nuova funzione di taratura della velocità mandrino e le funzioni di variazione della velocità mandrino. Le macchine di medie e grandi dimensioni integrano anche il Ram Balance System, sistema elettromeccanico gestito con un asse del CNC per la compensazione effettiva della flessione dello slittone. Tale sistema non deforma le strutture e garantisce un’ottima rettilineità di uscita della RAM/slittone anche con svariati tipi di teste caratterizzate da pesi diversi.
BRETON ULTRIX E3 Ultrix E3 è un centro fresatura che permette di lavorare materiali come il titanio, acciaio e leghe leggere grazie alla vasta gamma di elettromandrini disponibili tra cui scegliere. Il mandrino verticale e la tavola basculante permettono un’elevata accessibilità sia nella parte interna che nella parte esterna del pezzo da lavorare, e laddove necessario si può utilizzare la testa di rinvio a 90° con cambio automatico collocata nell’apposito magazzino accessori che può ospitare fino a due teste angolari.
DATI TECNICI
Assi Corsa asse X (longitudinale) Corsa asse Y (trasversale) Corsa asse Z (verticale) Avanzamento rapido (X,Y,Z) Avanzamento lavoro (X,Y,Z) Accelerazione Sistemi di lettura mm 1.700 mm 1.600 mm 1.000 mm/min 50.000 mm/min 30000 m/sec² 3 righe ottiche assolute safety
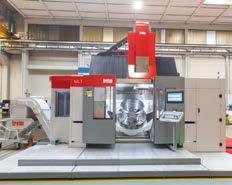
Mandrino Cono di attacco HSK-A63 / HSK-A100 / Capto C6 / Capto C8 Velocità di rotazione standard giri/min 14.000 - 28.000 Gamme di velocità n° NA Potenza massima kW 85 Coppia massima Nm 730 Distanza naso mandrino/pallet - min/max mm 1080 Distanza asse mandrino/montante mm NA
CELADA OKUMA MULTUS U5000 I centri di tornitura e fresatura ad alta tecnologia con lavorazione di materiali ostici, quali le leghe nikel ed il struttura a montante mobile della serie MULTUS U sono titanio, le lavorazioni complesse sono facilitate grazie in grado di soddisfare le più complesse esigenze delle alla lavorazione simultanea a 5 assi, anche grazie ad un aziende moderne. La lavorazione simultanea sincronizzata pacchetto software di gestione dedicato. A supporto del viene gestita in modo semplice ed intuitivo, grazie al controllo OSP P300 di ultima generazione, si abbinano contromandrino e alla torretta inferiore, opzioni disponibili le funzioni lavorazione ad alta velocità, che garantiscono a seconda della configurazione. Le generose corse degli processi efficienti abbattendo i tempi di produzione. assi e la potenza dei gruppi mandrino sono adatti alla Il sistema di prevenzione delle collisioni, Collision Avoidance System, fa parte della dotazione standard della serie Okuma MULTUS U, contribuendo a completare una già ricca dotazione macchina. Si aggiunge inoltre lo schermo touch da 19“ con pannello di controllo ottimizzato studiato per una corretta ergonomia operativa. Il nuovo Multus U5000 è l’espressione massima nel panorama delle macchine multitasking, adatta alle aziende che necessitano lavorazioni complesse di componenti in un unico piazzamento, sia che si tratti di piccole serie che di produzione di lotti medio grandi.
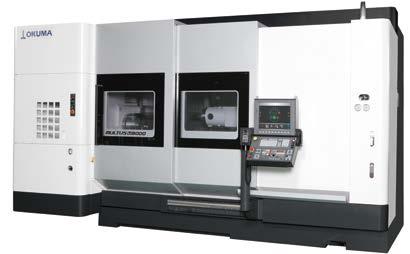
DMG MORI NTX 3000, LAVORAZIONE COMPLETA DI TORNITURA / FRESATURA DI PEZZI DI GRANDI DIMENSIONI
Con il mandrino turn & mill compactMASTER, la torretta aggiuntiva con asse Y e un diametro barra di ø 102 mm, il nuovo modello NTX 3000 di seconda generazione di DMG MORI assicura la massima produttività su soli 16,5 m² di superficie. • Superficie di installazione più piccola di questa categoria di macchine: 16,5 m² • Mandrino principale con velocità di rotazione di 3.000 giri/min e coppia max. di 1.194 Nm • Grande diametro barra pari a ø 102 mm • Ampia zona lavoro grazie al mandrino turn & mill compactMASTER con lunghezza di 350 mm e coppia pari a 122 Nm • Multi-tasking: Asse B con Direct Drive per la lavorazione simultanea a 5 assi di pezzi complessi Elevata flessibilità grazie alla corsa in X fino a -125 mm sotto il centro mandrino Disponibile CELOS con FANUC e CELOS con SIEMENS

EMAG IL CENTRO DI TORNITURA/FRESATURA VMC 450-5 MT GARANTISCE TEMPI SECONDARI MINIMI
La dotazione a cinque assi risulta determinante: la tornitura rappresenta sempre il processo principale. Inoltre è possibile eseguire operazioni di foratura e fresatura interamente con il mandrino portautensile. EMAG ha poi dotato la macchina di un’asse B e un’asse Y – in questo modo è possibile eseguire la dentatura a creatore oppure il power skiving, realizzando tutte le tecnologie necessarie su un’unica macchina. A seconda del componente, è possibile eseguire la lavorazione completa da pezzo grezzo a finito. In questo modo la VMC 450-5 MT di EMAG sostituisce processi eseguiti con tre diversi impianti. Ciò comporta vantaggi straordinari per l’utilizzatore: i costi di equipaggiamento dopo un cambio lotto sono minimi, i singoli processi sono perfettamente coordinati (e i tempi di inattività minimi) e viene garantita un’elevata sicurezza di processo grazie ad un’unica fase di serraggio. Non da ultimo, i costruttori EMAG utilizzano materiali di alta qualità: la VMC 450-5 MT è dotata ad esempio di un basamento in MINERALIT® , con elevate proprietà di assorbimento delle vibrazioni, eccellenti guide lineari, una slitta a croce ad elevata velocità di avanzamento e un ampio magazzino per 80 utensili. DATI TECNICI Diametro mandrino max. 630 mm Diametro di oscillazione 800 mm Corsa asse X 780 mm Corsa asse Z 500 mm Corsa asse Y 350 mm Indexaggio asse B ± 95 ° Magazzino utensili fino a 80 pos. utensili

MANDELLI SISTEMI PRESTAZIONI E FLESSIBILITÀ PER LA NUOVA SPARK 1200
La SPARK 1200 è il risultato delle ottimizzazioni sviluppate da Mandelli attorno all’architettura del prodotto SPARK. Garantisce prestazioni eccellenti come dinamica, asportazione e precisione e può essere configurata per lavorare materiali tradizionali come ghisa ed acciaio, leghe leggere e materiali tenaci. Presenta DATI TECNICI l’architettura a tavola fissa che massimizza Assi precisione ed asportazione in configurazione Corsa asse X (longitudinale) multitasking. Tutti gli assi lineari possono essere Corsa asse Y (trasversale) Corsa asse Z (verticale) dotati di doppia vite a ricircolo di sfere per Avanzamento rapido (X,Y,Z) ottenere un eccellente comportamento dinamico. Avanzamento lavoro (X,Y,Z) La struttura è stata ottimizzata con avanzate Accelerazione Mandrino simulazioni meccatroniche per ottimizzare la Cono di attacco rigidezza dinamica. È disponibile in configurazione Velocità di rotazione standard stand alone, con cambio pallet automatico e sistema a margherita per gestire fino a 9 tavole, Gamme di velocità Potenza massima Coppia massima oppure può essere configurata in linea con navetta Distanza naso mandrino/pallet - min/max mono, bi e tri-livello. Distanza asse mandrino/montante mm 1200 mm 1200 mm 1450 mm/min 60000 mm/min 20000 m/sec² 5
giri/min n° kW Nm mm mm HSK100 6000-30000 1 60-100 800 100-1300 625
PIETRO CARNAGHI FLEXTURN, UNA SOLUZIONE CHE NON SCENDE A COMPROMESSI La struttura della FLEXTURN strutturale e ad elementi finiti. è stata progettata grazie ad Hanno avanzamenti rapidi assi oltre 90 anni di esperienza della X/Y/Z da 40 m/min grazie Pietro Carnaghi nella produzione all’idrostatica ottimizzata, frutto di centri di lavoro verticali, ed di anni di sviluppo continuo ad arricchita con le funzionalità opera di Pietro Carnaghi. I pattini di fresatura avanzate (direct idrostatici avanzati offrono la drive a 6000 giri). Considerata massima accelerazione a zero la vasta esperienza che Pietro attrito. La tavola rigida permette Carnaghi può vantare in termini rotazioni con velocità fino a di strutture di grandi dimensioni, 400 giri/min, grazie ad una Flexturn mantiene il concetto dinamica elevata, conseguenza di ancoraggio su livellatori, dell’utilizzo di motori direct garantendo la massima stabilità. drive di ultima generazione, La stabilità della struttura e sviluppati dal reparto R&D Pietro la perfetta rigidità assicurano Carnaghi. Il design rispecchia ai nostri Clienti la massima le caratteristiche tipiche di un performance in termini di tornio verticale Pietro Carnaghi: stabilità, dinamicità, precisione, rigidità e precisione unite a elevata rigidità e capacità di funzionalità di fresatura ai smorzamento. massimi livelli, con la capacità di Tutte le macchine sono costituite entrare in profondità nel pezzo da una struttura ottimizzata in direzione verticale, sia durante e sviluppata utilizzando un le operazioni di fresatura che di software di ottimizzazione tornitura.

SORALUCE
FRESATRICE A MONTANTE MOBILE MULTITASKING SORALUCE MOD. FLP6000 LA SOLUZIONE MULTITASKING DI SORALUCE PER I COSTRUTTORI DI MACCHINE PER IL LEGNO
SORALUCE ITALIA ha recentemente fornito ad un cliente dell’Emilia Romagna, punto di riferimento nel settore delle macchine per le lavorazioni del legno, il centro di fresaturatornitura multitasking SORALUCE FLP 6000 per la lavorazione di componenti per macchine per la lavorazione del legno. È una soluzione multitasking completamente versatile mirata a massimizzare la produttività, con la possibilità di eseguire operazioni di fresatura e tornitura nella stessa macchina in un unico set-up, consentendo la lavorazione di pezzi di diverse geometrie e dimensioni. Si tratta di una macchina dall’elevata capacità di asportazione e dotata di una grande versatilità. Presenta corsa longitudinale di 6000 mm, verticale di 2200 mm e trasversale di 1300 mm, l’area di lavoro della macchina è stata personalizzata in base alle esigenze specifiche del cliente. La fresatrice a montante mobile modello FLP incorpora due stazioni di lavoro; una stazione dotata di tavola girevole di tornitura/fresatura di ø 1600 mm e la seconda di un piano di lavoro avente superficie 4500 x 1500 mm. L’architettura della fresatrice a montante mobile facilita il lavoro in pendolare, garantendo una lavorazione continua senza tempi morti. Il processo di carico / scarico pezzi in una stazione di lavoro avviene con la macchina in ciclo nell’altra stazione di lavoro. Inoltre, la macchina è dotata della testa multifunzione SORALUCE H200T per operazioni di tornitura e fresatura. La soluzione fornita da SORALUCE incorpora il sistema di e reporting SORALUCE Monitoring I4.0, uno strumento di analisi che estrae informazioni preziose dai dati generati dalla macchina e ne monitora lo stato per garantire le massime prestazioni possibili del processo di lavorazione, con visualizzazione dello stato della macchina in tempo reale.
Fresatrice a montante mobile multitasking SORALUCE mod. FLP6000.


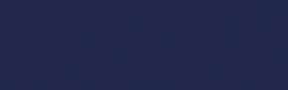
FOCUS ON
GEFRAN
