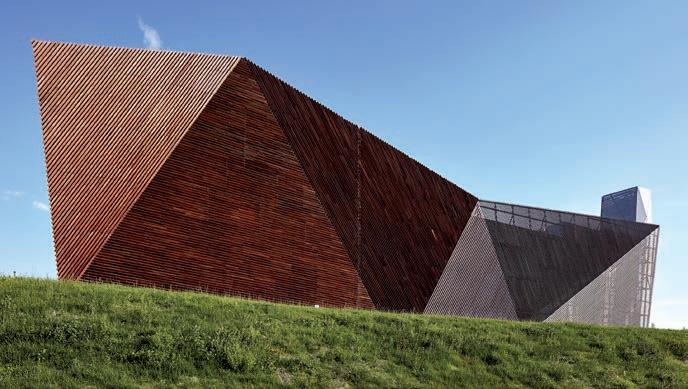
6 minute read
Ridefinire i rapporti tra produzione di energia e territorio agricolo
Esempio virtuoso di coesistenza tra mondo industriale e mondo agricolo. Powerbarn, realizzato da Giovanni Vaccarini Architetti, interpreta il programma di riconversione di una parte dell’area industriale appartenuta a Eridania in una centrale di produzione di bioenergia
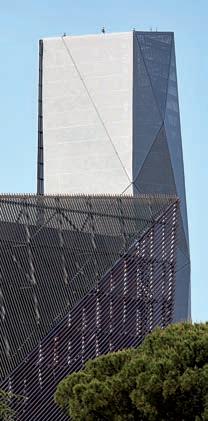
Credit: Massimo Crivellari
Nel cuore della Romagna, in un’area storica per la coltivazione e la lavorazione della barbabietola da zucchero, sorge un nuovo polo per la produzione di energia elettrica da fonti rinnovabili. Delimitata a nord-ovest dall’ultimo tratto del fiume Lamone, attraversata dalla ferrovia che da Faenza conduce a Ravenna, lambita a sud-est dalla strada del Carrarone sulla quale si apre il suo ingresso, l’area industriale appartenuta a Eridania si pone a margine di un ampio territorio agricolo tuttora dedicato alla coltura della barbabietola e di alberi da frutta e copre un’area di 47 ettari adiacente alla città di Russi (RA). Il sito industriale ha visto il mantenimento di magazzino e inscatolamento, dismettendo la produzione di zucchero, su un’area complessiva di 46.000 mq. Il restante territorio, circa 280.000 mq, è stato bonificato e restituito alla comunità, mentre per altri 167.000 mq sono previsti interventi di riqualificazione. Tra gli interventi di riconversione spicca il polo produttivo il cui masterplan prende spunto da terrapieni o “dune piantumate” e con piste ciclabili. Si è deciso di non intervenire e lasciare il polo industriale “aperto” ai cittadini, con i confini tracciati dalla natura e dalle infrastrutture.
ENERGIA A KM 0
L’impianto a biomasse (con una potenza di 30 MWe) è alimentato con cippato di legna, ma anche da residui di sfalcio, dalla pulizia degli argini dei fiumi e dalla potatura, il tutto proveniente da una filiera corta entro un raggio di 70 Km. In un più ampio programma di riduzione ai minimi termini dell’impatto sul territorio, la realizzazione delle dune è stata ottenuta con la sola terra di scavo. La produzione annua del polo è stimata di 222 GWh e soddisferà il fabbisogno di 84.000 famiglie, garantendo significativi risparmi nell’immissione di gas serra nell’atmosfera. Accanto alla produzione di energia da cippato, nel polo trovano sede anche un impianto a biogas alimentato da liquami zootecnici e un piccolo impianto fotovoltaico di circa 1.000 mq che contribuiscono alla produzione di energia pulita. Le linee guida dell’Unione Europea riguardo all’utilizzo di fonti rinnovabili nella produzione di energia elettrica segnano il traguardo da raggiungere per il 2020 al 20% e al 32% per il 2030. Attualmente l’energia prodotta da biomasse contribuisce al 10% di tutte le risorse di energia e rappresenta la quota più importante tra le energie rinnovabili, costituendone il 59%.
L’INSERIMENTO NEL TERRITORIO
Il masterplan del polo definisce un dispositivo ambientale a bassa tecnologia, originato dal disegno di un terrapieno che funge da punto di interfaccia tra l’area rurale e quella industriale. “Tutto il progetto parte dal disegno del margine”, racconta l’architetto Giovanni Vaccarini per spiegare come – attraverso la presenza e il progetto naturalistico delle dune, tipiche del paesaggio adriatico e qui realizzate su tutto il confine dell’area – si sia proceduto a una generale opera di schermatura e mitigazione ambientale del polo. I bordi dell’area sono stati pensati come dei terrapieni dall’altezza variabile tra 3 e 10 metri, sormontati da alberi e percorsi da piste ciclabili e pedonali, che definiscono il margine dell’intervento e l’interfaccia tra i due ambiti: quello agricolo e quello dedicato alla produzione energetica. L’inserimento di un complesso industriale in un contesto rurale così consolidato e delicato poteva rappresentare un ostacolo insormontabile alla realizzazione. Attraverso una tecnica di
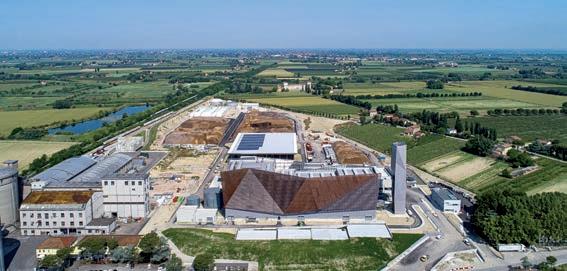
UNA FACCIATA DA 7.600 DOGHE IN LEGNO

Sulla trave esterna sono poste delle mensole in acciaio su cui posano le 7.600 doghe in legno che costituiscono il rivestimento di facciata. La non linearità delle forme ha fatto sì che ogni modulo di facciata fosse diverso dall’altro, richiedendo un’accurata ingegnerizzazione in officina del costruttore metallico. Sono in totale 540 le tonnellate di carpenteria metallica impiegate per le sole facciate, in qualità S355J0. Oltre all’aspetto sfaccettato dell’edificio caldaia, anche il camino offre una visione mutevole, con un rivestimento in pannelli grigi di forma triangolare e dimensioni variabili. Esteriormente i corpi di fabbrica trasmettono l’impressione di una gemma, con superfici geometriche scandite dalle strutture portanti in acciaio. L’orditura delle scandole segue però un pattern che cambia direzione a ogni faccia del poliedro, offrendo così all’osservatore percezioni costantemente mutevoli in funzione del punto di osservazione delle differenti ore del giorno o delle condizioni di luce.
Credit: Massimo Crivellari camuffamento militare nota come “razzle dazzle” l’impatto della Powerbarn è stato mitigato. La soluzione architettonica è coerente con l’idea di mitigazione ambientale che ha ispirato il progetto.
La tecnica di camuffamento, ispirata dall’arte cubista e sviluppata in ambito navale durante la Grande Guerra, ci ha permesso di sviluppare delle soluzioni architettoniche impreviste. Non si tratta di nascondere, bensì di proporre all’osservatore una realtà diversa, che paradossalmente tende a richiamare l’attenzione dell’osservatore e a farlo riflettere su ciò che sta guardando “
Giovanni Vaccarini “
Sono due i principali corpi di fabbrica che contraddistinguono Powerbarn: gli edifici caldaia e camino dalle imponenti dimensioni. La caldaia è lunga 100 m e raggiunge un’altezza di 30 m, mentre il camino svetta per 50 m. Completano il quadro sale macchine, un condensatore, edifici di stoccaggio e uffici. Il camuffamento avviene principalmente grazie alla spettacolare facciata, realizzata in carpenteria metallica, così da non gravare eccessivamente sui corpi di fabbrica, soprattutto nel rispetto del disegno architettonico. Sulle strutture della caldaia, in carpenteria pesante con rivestimenti in pannelli sandwich (8.500 mq di pareti e 2.100 mq di copertura) e lamiere forate (4.900 mq), si installano mediante piastre di giunzione delle braccia in HEA 240. Sulle braccia si intersecano internamente una trave HEA 160 ed esternamente profili IPE 240, creando una sorta di reticolato con traversi in angolari di dimensioni e spessori variabili. L’impiego dell’acciaio si fa quindi fondamentale. Da un lato strutture industriali di tali proporzioni vedono nel suo utilizzo l’alleato ideale per assecondare grandi luci a rapidità e solidità costruttiva. Dall’altro lato diviene il fil rouge su cui si basa l’intera concezione architettonica.

Credit: Massimo Crivellari
SCHEDA PROGETTO
PROGETTO ARCHITETTONICO: Giovanni Vaccarini Architetti COMMITTENTE: Powercrop Russi srl SOCI: Enel Green Power SpA Seci Energia SpA BUSINESS DEVELOPER: Alfredo Donati PROJECT MANAGER: Santo Riganello, Carlo Manganelli, Giovanni Pasqui, Venanzio Garau, Fernando Maltinti PROJECT ENGINEERING: Franco Meroni, Corrado Zampatti, Antonino Caronia
SITE MANAGER: Paolo Innocentini
DIRETTORE DEI LAVORI: Stefano Salvotti (Studio DueEsse)
CSE (COORDINATORE SICUREZZA IN FASE DI ESECUZIONE): Daniele Arasi (Techno-HSE) CSP (COORDINATORE PER LA SICUREZZA IN FASE DI PROGETTAZIONE): Alessandro Pazzi (Libra Ravenna) GEOLOGIA: Studio Garassino LANDSCAPE DESIGN: Antonio Stignani (Studio Paisà) STUDIO IMPATTO AMBIENTALE: Corsi/Retini (Steam)
Principali imprese esecutrici GENERAL CONTRACTOR: Termokimik Corporation SpA CALDAIA: AET gmbh TURBINA E CICLO TERMICO: TOSI SpA INVOLUCRO ARCHITETTONICO E COSTRUTTORE FACCIATE: MAP SpA COSTRUZIONI GENERALI: Impresa Salvati SpA ELETTRODOTTO: Cantamessa SpA
Dati di progetto AREA DI PROGETTO: 167.000 mq EDIFICIO CALDAIA E LINEA FUMI LUNGHEZZA: 110 metri LARGHEZZA: 25 meters ALTEZZA MASSIMA: 40 meters ALTEZZA MASSIMA CAMINO: 52 meters AREA: 2400 metri quadrati UFFICIO STAMPA: Image MEDIA AGENCY