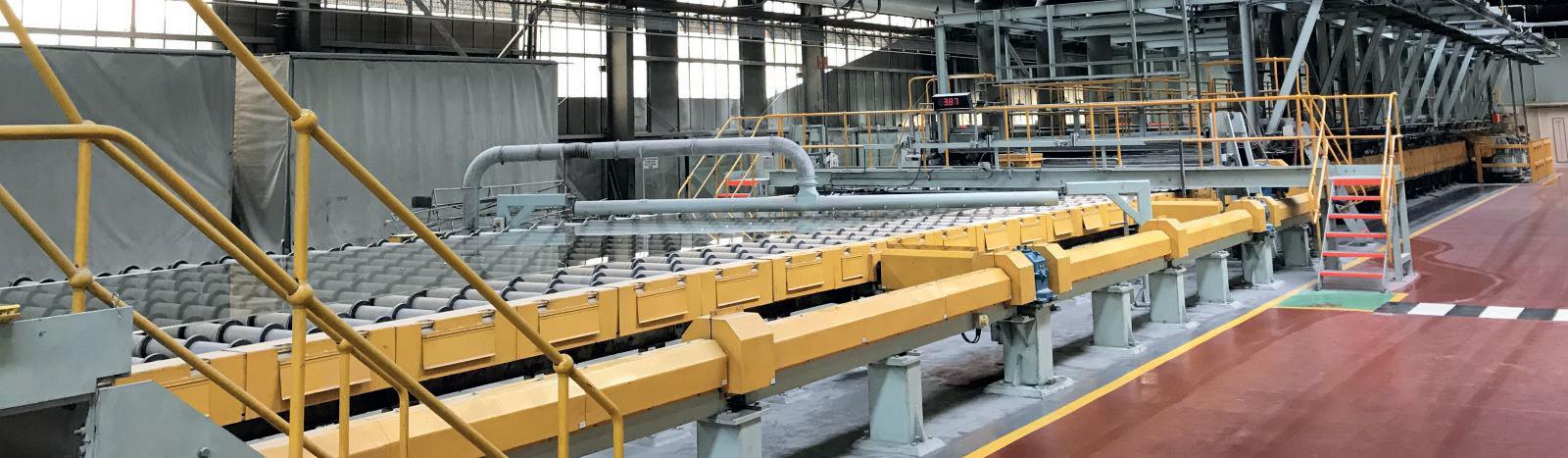
5 minute read
Decarbonisation: NSG Group
NSG’s successful hydrogen trials
Andy Keeley* shares his experience of leading NSG Pilkington’s recent hydrogen trials in St Helens, UK. The trials aimed to demonstrate that the furnace could run safely at full production without impacting product quality as part of the manufacturer’s plans to decarbonise.
� Pilkington’s Greengate furnace at St Helens, UK. � Andrew Keeley, Principal Technologist at NSG Pilkington, led the hydrogen trials.
As part of our decarbonisation strategy, we are investigating low carbon fuels as part of our commitment to reduce our CO2 emissions by 30% by 2030 and to achieve net zero by 2050. We have been working with the HyNet project for a number of years on the feasibility of using hydrogen as a fuel to fire our furnaces.
The hydrogen firing trials were funded by the UK government as part of the Industrial Fuel Switching Programme. The HyNet consortium applied for funding under this programme for a series of trials at industrial sites in the North West including ourselves and Unilever, the UK-based household goods maker. Hydrogen looks to be one of the most favourable alternative fuels for flat glass manufacturing although other fuels such as biofuels also have good potential.
I was the NSG project manager for the hydrogen firing trials at our Greengate Works in St Helens, UK. The role involved working with Otto Simon, the installation project lead, site engineering and our central engineering team during the installation phase and then working with the R&D and operations teams during the trials as well as with BOC, who supplied the hydrogen for the trials (Fig 1).
It was a great opportunity to lead this project but really it was a team effort overall. The site team (Fig 2), R&D team, Otto Simon and subcontractors all worked well together and delivered the project.

Trials
The Port One trials took place over a threeweek period. The first challenge was that this project kicked off in May 2019 and we then ran into Covid which led to some delays due to restrictions on travelling. Site installation started in January 2021 and generally went very well. The main challenge was installing pipework for the trial around a live furnace and ensuring that it was all gas tight as fully welded was not practical for a temporary installation. The scale of the trials meant that we needed to co-ordinate across the teams each day to cover modifications to the burners as well as monitoring the furnace behaviour during the trials. Above 70% hydrogen the flames became invisible, which was expected but still new (Fig 3). I have worked on furnaces for many years,
� Fig 1 - Hydrogen trailer. At full flow, a tanker of hydrogen was used every 40 minutes during the Port One Trials. Continued>>
�Fig 2. The site team for the hydrogen trials.
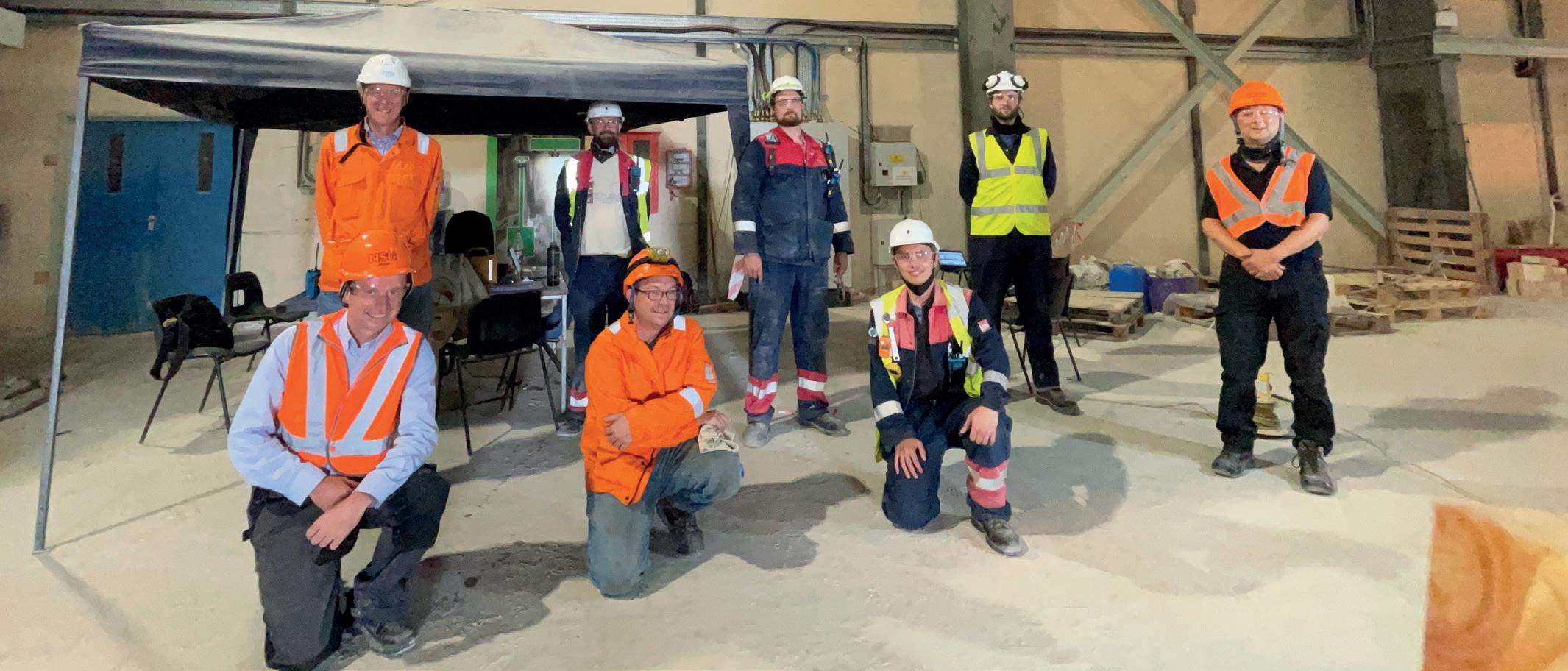

but this was the first time I have been involved in such large-scale R&D trials.
During the trials, we monitored the furnace closely and were able to produce high quality glass throughout. Apart from the change of fuel on the port firing hydrogen, we were able to operate the rest of the furnace the same with no other process changes being required.
The main outcome of the trials was that we could fire 100% hydrogen on the furnace and get effective melting of the batch. Based on these results, we have confidence that we could convert the upstream part of the furnace to 100% hydrogen and then progressively move downstream once we have assessed the impact of firing hydrogen on foam clearing and glass chemistry. If we could convert the furnace to run on 100% hydrogen, we could reduce our Scope 1 CO2 emissions by more than 65%, with the remaining CO2 coming from the raw materials.
Challenges
On the upstream ports, the main challenge is heat transfer while downstream you are clearing foam and heating the glass for refining. For downstream ports, the higher water content in the atmosphere can lead to more foam. It has not been possible to test this at scale due to the limited availability of hydrogen. We will only be able to test this when we have large volumes of hydrogen available in the future when the HyNet project goes live.
Wayne Bridger of BOC said at Furnace Solutions there is unlikely to be enough hydrogen infrastructure in place to meet industry requirements for at least 10 years. So, the question is how will furnaces be fuelled in the intervening years? In the North West of England, we are lucky to be close to the HyNet cluster which is quite advanced and so I believe hydrogen is a realistic fuel for this site. For other sites in the group, we would have to assess the options based on what was available.
� Fig 3. Natural gas flames compared to the invisible hydrogen flames in glass furnace.
Green hydrogen could prove particularly challenging for the following reasons: � Getting reliable and cost-effective access to sufficient renewable electricity and water.
� Physical space on or close to our sites.
� Cost – green hydrogen is currently much more expensive than grey or blue hydrogen.
� Capex if directly investing or finding a suitable third party.
Fuel of the future?
Hydrogen is one of the potential low carbon fuels we could use for the future. We also carried out trials in February 2022 firing 100% bio-oil on the same float furnace which was also a world first. In reality, we expect to use a mixture of electricity and low carbon fuels to fire our furnaces with the choice of fuels dependent on what is available and commercially viable locally. We also expect to use an increasing proportion of cullet to reduce our overall energy requirement.
We believe we have carried out sufficient trials to allow us to fire hydrogen on our furnaces, at least on the upstream ports, so we are not planning any further largescale trials. The next major step will likely be when the HyNet project goes live and we have a hydrogen pipeline to site.
*Principal Technologist, NSG Pilkington, Lathom, Lancashire, UK https://www.pilkington.com/en-gb/uk