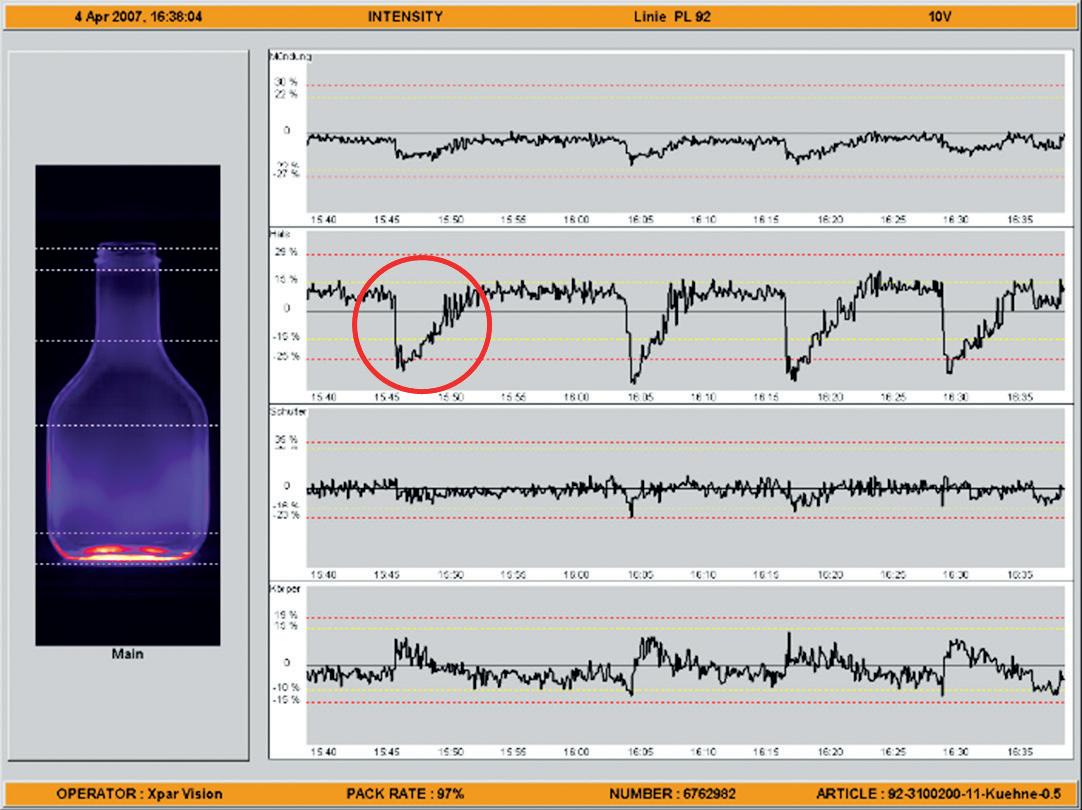
10 minute read
Lubrication: Xpar Vision
Integrated process approach is key to lubrication
Paul Schreuders* discusses further trends towards digitisation of the glass forming process, with further integration of technologies and intelligent use of data. Xpar Vision’s BlankRobot forms an important element in that trend.
Until coatings on surfaces of moulds and neck rings are not durable enough to provide long term protection against the harsh impact of gob loading, proper lubrication is inevitable. Besides lubricating moving parts, lubrication or swabbing aims to minimise the friction of hot glass at loading (blank side) and final forming (blow side) by applying a layer of graphite to the surface of the moulds and neck rings. It is necessary to keep the ISMachine running!
Glassmakers wish for consistent operation and do not want to exchange moulds and neck rings frequently. Generally, swabbing is seen as a remedy for many inconsistencies in the forming process, such as changing gob shapes, instable loading conditions, deteriorating coatings of moulds, and changing cooling conditions. These result in different state per cavity in terms of performance throughout the production run; cavities with worst performance are the trigger for swabbing the full machine (all sections) again. As a result the machine operator is instructed to swab moulds on average every 20 minutes.
Analysing the effectiveness of traditional swabbing gives the answer to the reason for this high frequency.
Firstly the application of lubricant is inconsistent; not one mould receives the same quantity every time. Operators change every shift and do not have the same skills or follow the exact routine. Typically they take the brush soaked in lubricant and swab multiple sections. Logically the first section receives more lubricant than the next ones.
Together it results in uneven distribution of graphite to the moulds.
At the same time the procedure of lubrication is considered as a standard for years, where no attention to possible improvements is given to: ‘We have always done it like this’.
Fig 1 illustrates the control chart of a single cavity from the Xpar Vision IR-D system each time the operator swabs. The forming process has to deal with the impact and needs time to recover. As mentioned earlier this process behaviour is different from cavity to cavity resulting in a variety of unwanted effects from the common swabbing procedures.
Overlooking the above, the question to answer is when is lubrication effective? Two elements play a role here.
Firstly the lubricant used gives a durable layer of graphite to the blank and neck ring surface. Additional ingredients in the lubricant determine how long this layer of graphite performs during production. Here we observe clear differences between the available lubricants. Often glassmakers are committed to a brand and type of lubricant already for years, simple because it is worked initially.
At the same time the lubricant can only perform durably when it is applied perfectly to the mould surface. Next to the requirement that lubricant actually has to connect to the surface, in this context it also means that the layer of graphite should be evenly distributed horizontally and in a vertical direction you would like to apply a thinner or thicker layer thickness depending on the friction caused by gob loading. And this has to be done consistently in time, from shift to shift.
Bottom line, it is all about a lubricant with the right composition of ingredients that is applied precisely and consistently for a durable result.

Fig 1. The heavy
� impact of swabbing is clear. � Fig 2. BlankRobot by Xpar Vision.
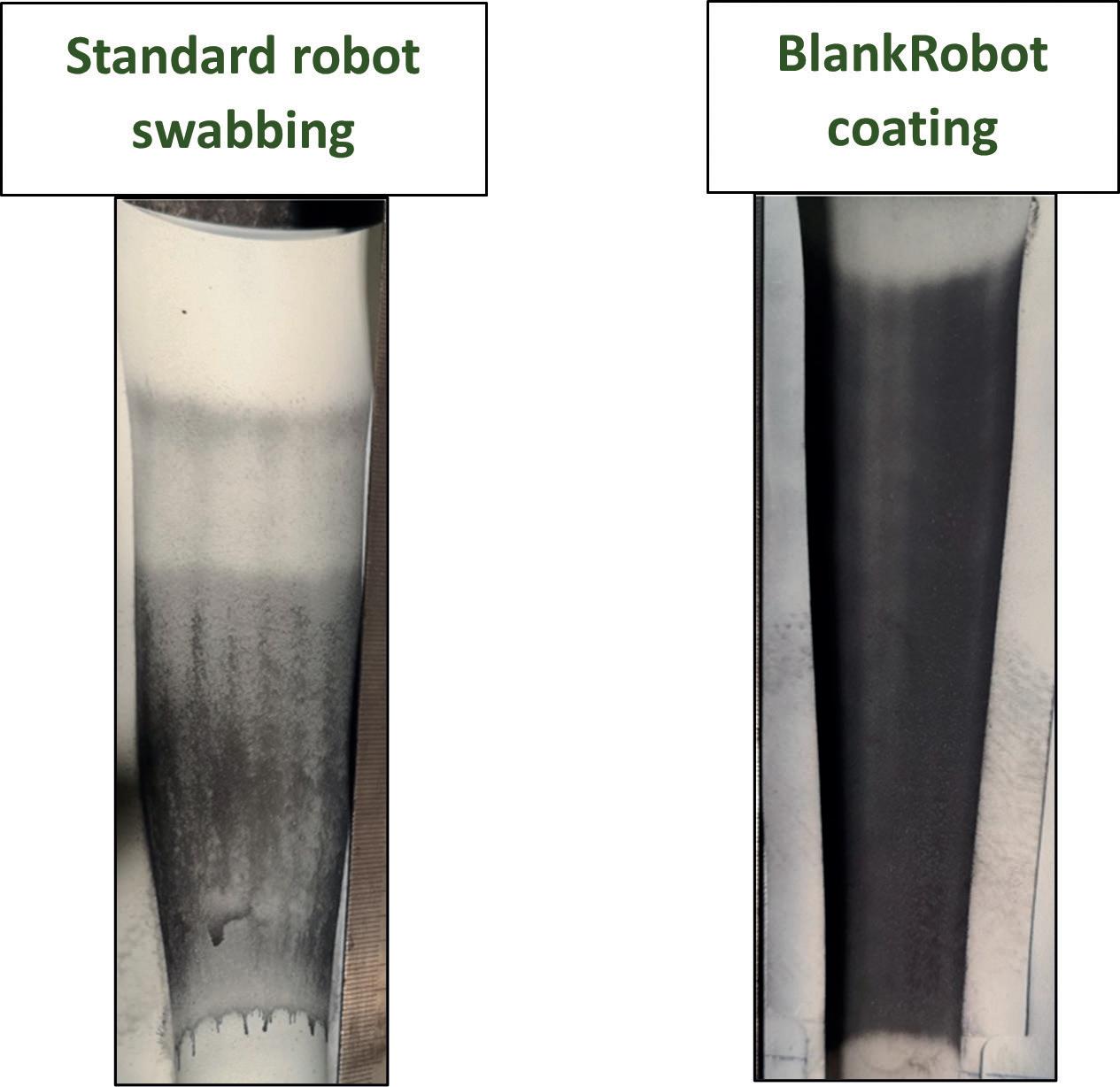
For many years the only method of lubrication was carried out by the operator. Manual swabbing can never give a consistent performance as it is dependent on skills and accuracy of the machine operator who is exchanged shift by shift. Due to this inconsistency each time the operator swabs, a (heavy) disturbance in the forming process occurs resulting in low quality product. As a reaction to the losses caused by swabbing the operators were expected to swab ‘onthe-fly’ with higher health and safety risk as a consequence. At the same time, in terms of consistency of application, this aspect was compromised even more.
In summary, manual lubrication has many negative side effects when trying to achieve the need to swab: apply grease in an optimised way for best mould performance.
Automated swabbing
It was inevitable that the consistency was searched for in automatic lubrication systems. Several automatic systems have been introduced over the years: � Spraying assemblies fixed per section � ABL or Carboflam technology based on cracking (burning) acetylene � Robotised swabbing systems moving from section to section
In recent years the majority of automatic lubrication systems installed have been based on a robot moving along the IS machine swabbing section by section. This method has been considered to be safer and healthier for workers on the shopfloor, has a lower total cost of ownership (less maintenance and exchange of parts) and importantly brings higher consistency as there is less or no variation in application between sections.
The operating methods differ if you review the different swabbing robots offered today. Generally their starting point is to copy the traditional manual swabbing procedures into automated ones. Still the same swab intervals are used or even in a higher frequency: every five to seven minutes is not uncommon.
We should again realise that every swab action results in an impact to the forming process stability.
It raises the question why these swabbing robots need to swab so often? The answer lies in the fact that the knowledge of application is failing with the swabbing robot suppliers, thus with the users as well.
Connection between type of lubricant and how to apply this lubricant by the specific swabbing robot is often failing, resulting in poor application which is compensated by swabbing more often.
Automated precision swabbing
Application of the lubricant is the key factor for good lubrication.
Prior to the market introduction of the BlankRobot, (Fig 2) knowledge of application has been the basis of design (Fig 3). From the drawing board Xpar Vision’s BlankRobot is developed for high precision application. The result, as
seen in Fig 3, is obvious when comparing application of lubricant.
Clearly seen is the difference between the two examples. The uneven and uncontrolled application by the alternative swabbing robot illustrates the answer to the earlier stated question: why do these robots need to swab so often? With BlankRobot the application is nearly perfect. The BlankRobot performs with high precision to maintain a durable layer of graphite to the mould surface for a long time. It could be considered as coating rather than swabbing. The ‘coating’ is a result of good evenly distribution of the graphite inside the lubricant while having good adhesion to the mould surface. It allows the user to apply lubricant where he wants and how thick he wants.
The high precision of application comes with several important advantages. As mentioned, the user has full control where and how thick he wants to swab, resulting in good quality bottles without swab impact (defects or pollution).
Next, it ensures durable operation which results in extended lubrication intervals of up to two hours while maintaining good quality. The impact of swabbing to the forming process performance is minimised dramatically.
Side effects are that mould sets remain longer in operation (less repairs), and maybe even more important, the health and safety of the machine operator is positively impacted.
� � Fig 3. result of applying lubricant by BlankRobot compared to an alternative.
Vision about automated swabbing
While automated precision swabbing today already provides a higher level of forming process performance we strongly believe there is room for further improvement! In our vision the next developments will integrate automated precision swabbing with the requirements of the individual performance of the cavity as well as using the BlankRobot for additional automated tasks at the blank side.
Automated precision swabbing integrated in process control
Robot swabbing needs new thinking and working methods. We recognise that more automated swabbing procedures are needed. Differentiation is required at start up of the production run, in stable operation, immediately after exchange of blanks and towards the end of the production run. In every situation the BlankRobot should provide accurate precision swabbing.
At the same time forming process parameters that influence the automated precision swabbing should be controlled.
You can consider the temperature working range of the blanks in relation to the adhesion of the graphite layer to the mould surface. You can also think of reducing the friction (impact) at the loading of the gob by allowing less variation in gob loading parameters as length, speed and position where the gob enters the blank.
Users would also reconsider their procedures in regards to mould repair and preparation. Is common use of blank coating in mould preparation
needed or would uncoated blanks give better performance in combination with automated precision swabbing?
Intelligent automated precision swabbing
Our aim is to minimise the impact of swabbing as much as possible. When looking at line/machine performance it is built up by adding the individual cavity performances. Every cavity essentially has its own forming behaviour depending on gob delivery, gob loading, mould condition, timing set-up and so on. To improve the forming process behaviour or performance at line level it is necessary to optimise the individual cavity performance. In this context automated swabbing should be adapted to the individual cavity behaviour. Here the intelligent use of process monitoring data comes in.
With sensors different process steps of the forming process (gob cut; gob weight; gob loading; blank temperatures; cavity performance; bottle quality) are monitored on cavity level giving the status of individual cavity performance. Based on sensor data analysed intelligently in real-time, the automated swabbing procedure will be adapted per single cavity.
Cavity differences which originate by IS-Machine design (outer vs. inner sections/cavities) are eliminated and it will be possible to anticipate on process deviations (coming from e.g. loading, temperatures, mould condition).
Only when the swabbing cavity is based in an adaptive automated way, full alignment with the forming process is in place which results in maximum forming process control, with a boost of line performance as logical consequence.
Additional automated tasks at the blank side
While reading this article carefully you have noticed that swabbing intervals are increased up to two hours or even more where alternative swabbing robots continue swabbing in 20 minutes intervals. Within the design concept of the BlankRobot it has been anticipated that the idle time in between swab actions gives opportunities to assign other tasks to the BlankRobot as well. The development of additional tools to connect to the BlankRobot arm will allow for new tasks to execute automatically to relieve the workload of the Machine Operator further and to reduce his/her exposure to health and safety risks.
With adapted tooling the BlankRobot will be able to maintain deflector coating, control gob loading by alignment of deflector and long trough. It will (visually) inspect the blank side for misalignments of malfunctions of equipment and measures temperatures and wear of coating and parts. The BlankRobot will not only generate additional sensor data for intelligent use (AI) but is also steered by AI to perform corrective actions of alignment to prevent deviations of process parameters and thus control the forming process for better performance.
Summary
In this article the need and necessity of lubrication is outlined and placed in the context of traditional swabbing by hand for which a transformation to automated lubrication is started in recent years. Simply installing a swabbing robot to the IS-Machine is not enough. In depth knowledge of the parameters that influence proper application of the lubricant exposed the opportunities for increase of forming process performance when automated lubrication methods are optimised further. Xpar Vision explained the relation between automatic lubrication and individual cavity performance and how these are optimised by using sensor data intelligently. The vision goes even further with more automated tasks will be assigned to the BlankRobot. �
*CEO, Xpar Vision, Groningen, The Netherlands www.xparvision.com
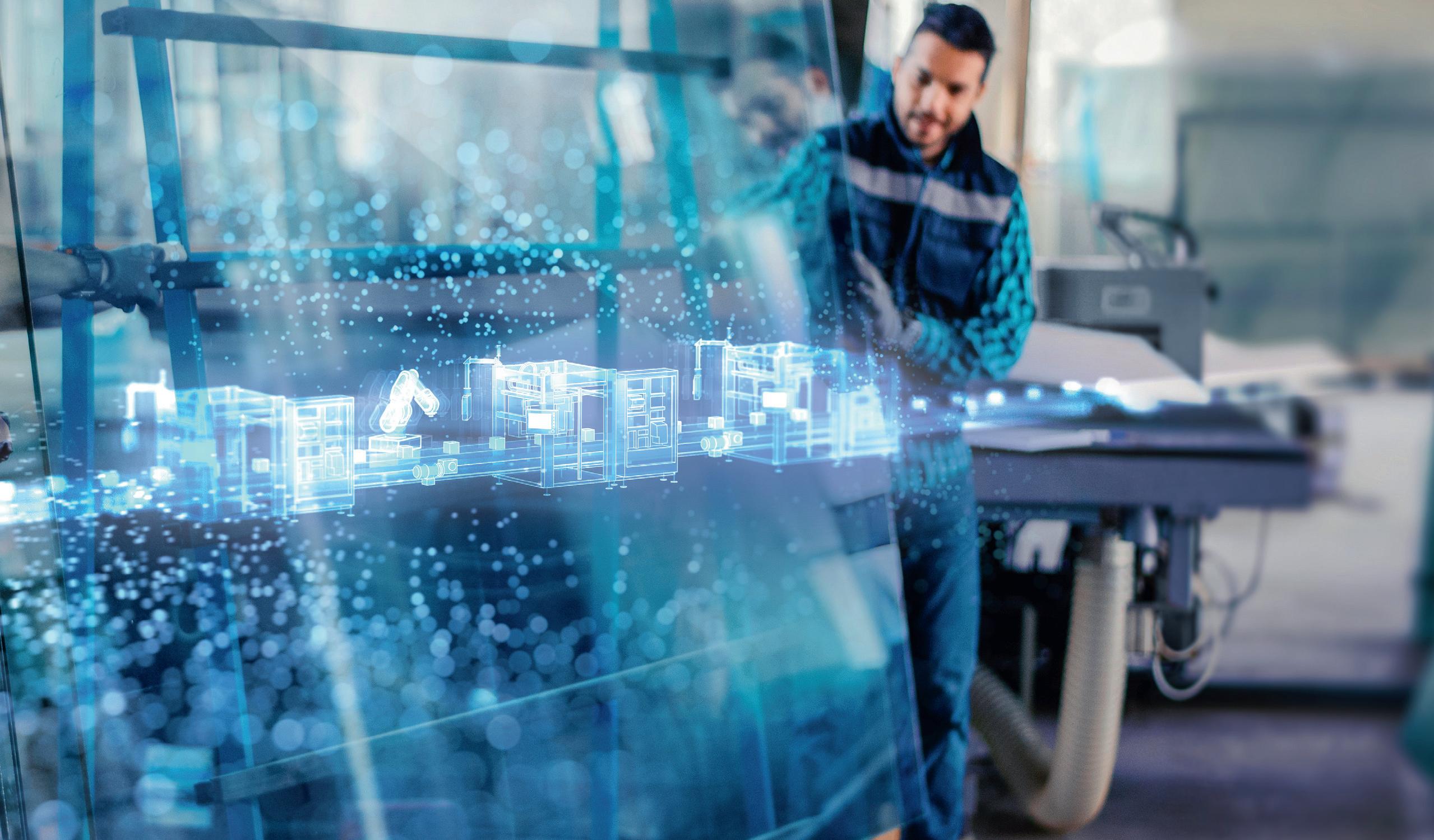