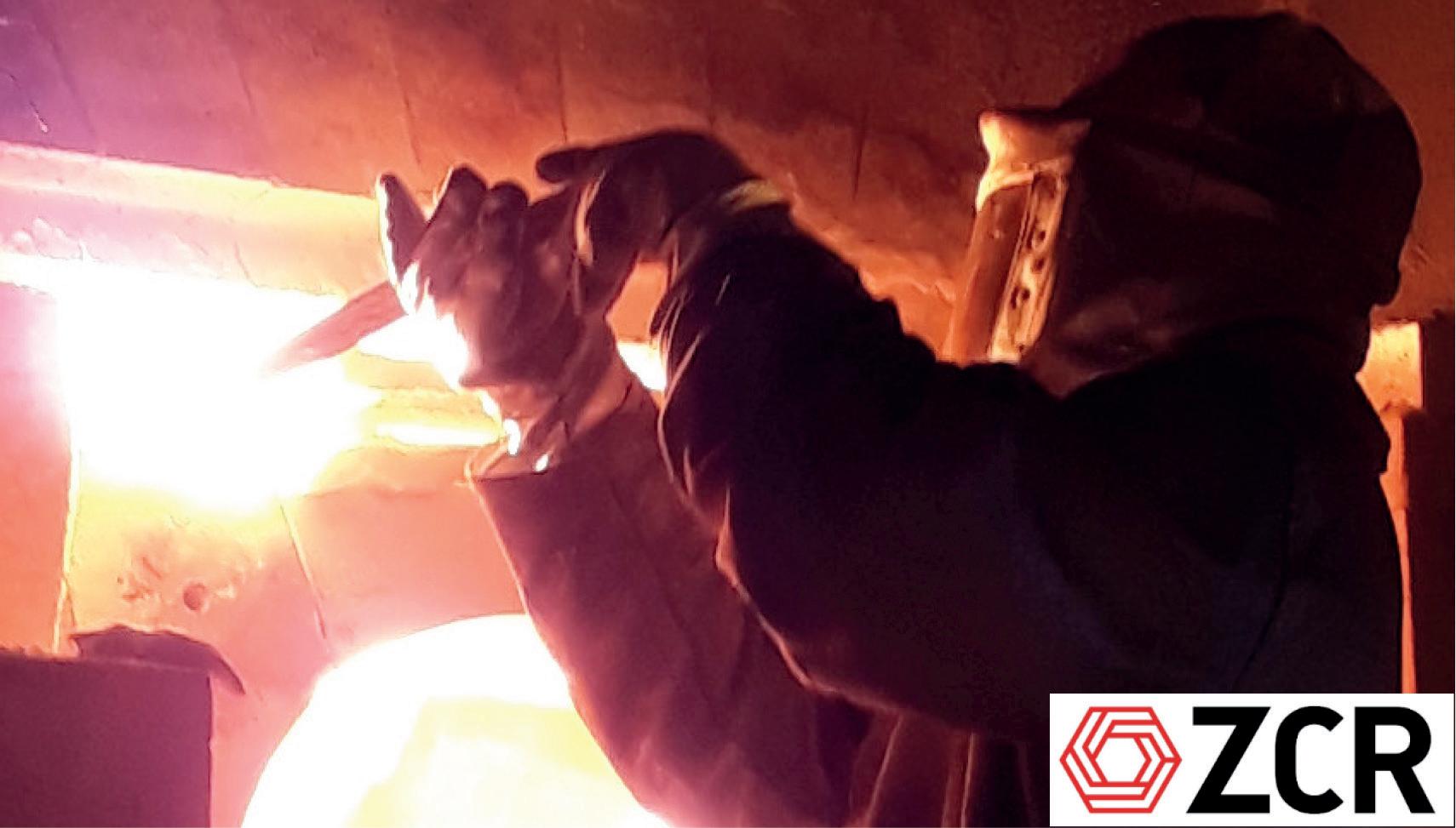
3 minute read
Refractories: ZCR
Thinking outside the box – refractory linings by ZCR
Oliver Claußnitzer* and Michael Kampmann** discuss why both steel and refractory trades should be organised from a single source and under the leadership of an experienced project manager.
Recently, we were explaining our business to a young trainee at ZCR. It was always obvious that in theory all the work steps for refractory linings are clear and logical, but in practice things are different, especially when there are several interfaces. “Taking a holistic view of the process and looking beyond the confines of one’s own trade can reduce these problems” said Michael Kampmann, Branch Manager of ZCR Darmstadt.
Traditionally the refractory installation or hot repair team arrives and does their job until the last block fits and the last mastic is casted. Setting AZS, proper lehring and feeling for the mastics are the classic lining challenges at site.
Here you have to think outside the box as the trades do not stand on their own but are built on each other - like steel and refractory construction.
Often steel and refractories need to be installed simultaneously. This means that on the one hand you can use synergies, but on the other hand you are more dependent on each other.
If the flow of information is guaranteed and the interfaces are clearly defined, then there is little potential for conflict. However, the situation is often different.
Thinking outside the box
“In order to optimise this interaction between steel and refractory, both trades should be organised from a single source and under the leadership of an experienced project manager,” said Oliver Claußnitzer, Project Manager and specialist on glass at ZCR.
Since we know the processes and working methods of steel and refractory construction, we should be involved in the planning of the construction site at an early stage. This is to ensure that optimisation potential does not go unrecognised and interface losses are minimised.
In concrete terms, this means accompanying the customer from the moment the material orders are placed to the piping until the tempering. If everyone gets together at an early stage, a project can be set up safely and successfully. This creates security and provides the chance to monitor and control keep costs together with the client.
� Oliver Claußnitzer and (below) Michael Kampmann
What the future holds
We recognise two interesting trends in our environment. A lot of technical knowledge has been lost in recent years. Even to customers, those employees who know the firing process or all the quirks of the kiln are becoming less.
On the other hand, we as ZCR are part of one of the largest construction groups in Europe. Everyone is talking about digitalisation and building information modelling (BIM) among our colleagues in building construction and infrastructures.
“Digitalisation can no longer be stopped in the construction industry. At ZCR, we are currently testing the use of data glasses. But that will only be the beginning,” said Mr Claußnitzer. BIM describes the model-based planning, realisation and operation of construction projects with the aim of optimising the transfer of knowledge, the quality of results and the efficiency of all participants. All relevant data is digitally recorded, combined and networked throughout the entire life cycle of the project.
“This results in a comprehensible, transparent and resilient information network for all those involved,” said Mr Kampmann.
He concluded: “I think it is only a matter of time before this method also becomes an issue in the glass industry. We, as a member of Strabag SE, one of Europe’s leading construction groups, will then be ready for it.” �
*Project Manager glass, oliver.claussnitzer@zueblin.de Branch Manager Darmstadt, Michael.kampmann@zueblin.de www.zueblin-cr.de