
98 minute read
MACCHINE & ATTREZZATURE
MONOVITE PIÙ BIVITE COROTANTE
IL SENSO COMPIUTO DELL’UPCYCLING
SE LA TANTO AUSPICATA “ECONOMIA CIRCOLARE” È REALTÀ SOLO QUANDO OFFRE UN’ADEGUATA SOSTENIBILITÀ SIA AMBIENTALE CHE ECONOMICA, ECCO CHE NEL MONDO DEL RICICLO MARIS PROPONE OGGI UN UPCYCLING CHE - IN VIRTÙ DI UN ORIGINALE TANDEM MONOVITE+BIVITE COROTANTE - CONFERISCE AI “PRODOTTI DI RECUPERO” UN REALE VALORE AGGIUNTO
DI ERMANNO PEDROTTI E LUCA MEI
L’ economia circolare è un sistema economico pianificato per riutilizzare i materiali in successivi cicli produttivi, riducendo in tal modo al minimo gli sprechi. Secondo la visione utilitaristica di Luciano Battistutta, sales area manager di Maris: “Dal Green Deal alla prima legge sul clima europeo, passando dal Next Generation EU, tutti noi siamo consapevoli che l’Unione Europea si è data una strategia di crescita verso una società a impatto climatico e ambientale zero. Per adeguarsi alle conseguenti politiche green, il mercato industriale, materie plastiche in primis, sta cercando di riciclare il più possibile. È poi noto agli operatori del settore che il business del riciclo di materie plastiche è partito dai materiali più nobili o dai materiali più facilmente riciclabili, per i quali c’è una filiera già ben consolidata. Basti pensare a un polimero come il polietilentereftalato delle bottiglie (PET), che ha una composizione ben definita, che è facilmente selezionabile e che di recente ha avuto l’autorizzazione per il reimpiego nella produzione di bottiglie per il settore alimentare. Poi, però, c’è tutta una serie di altre materie plastiche che sono la maggioranza o, comunque, che sono una parte consistente e che, per una serie di motivi, perché contaminate da altri polimeri o da altri inquinanti, hanno bisogno di una valorizzazione più importante, più complessa, più impegnativa”.

Compound ottenuto con il processo di upcycling effettuato mediante linea Evorec Plastic Plus
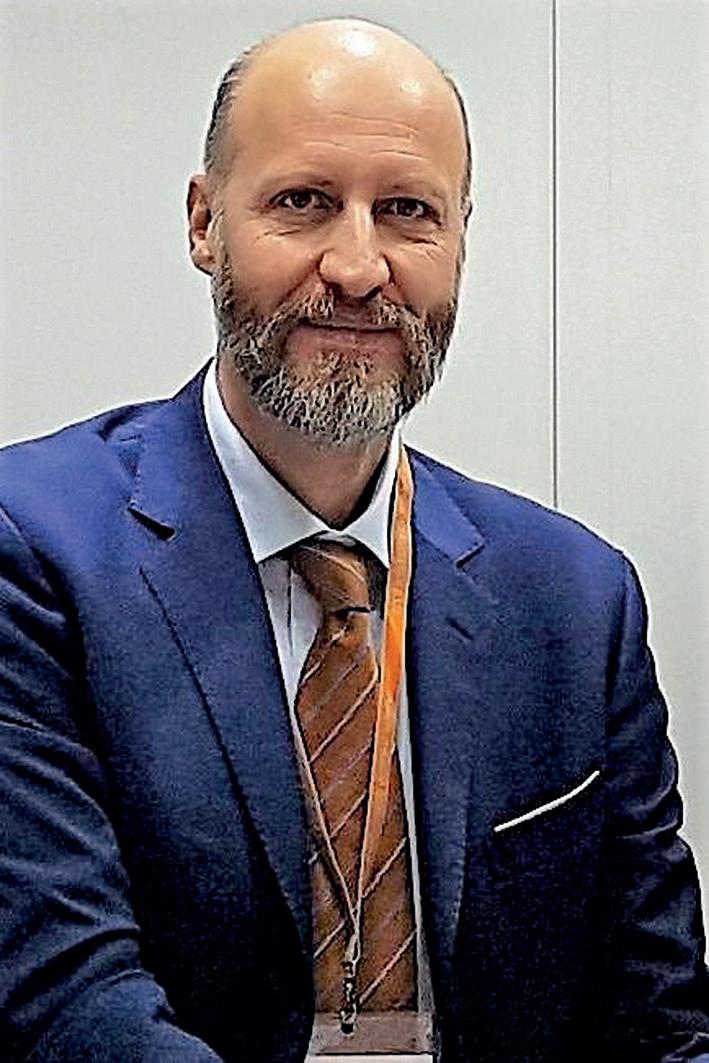
Queste parole ci portano celermente al cuore di quest’articolo: il processo di riciclo in continuo frutto della combinazione in tandem di un estrusore monovite e di un estrusore bivite corotante di Maris. Un’unione non nuova nella trasformazione delle materie plastiche, ma che, per l’elevato mix d’accorgimenti e di sviluppi tecnologici e di processo, fornisce nuova vita e maggior valore ai prodotti di scarto. Prima di procedere nella disamina di questa combinazione, risulta però utile, oltreché interessante, tracciare l’identikit di Maris, realtà tutta italiana, a gestione familiare, giunta alla seconda generazione e che, con i suoi circa 100 addetti, si confronta con concorrenti che sono veri e propri colossi industriali a livello mondiale.

PAROLE D’ORDINE: TECNOLOGIA E PRODOTTI SU MISURA… DA SEMPRE

Nata nel 1962 in quella che è l’immediata cintura torinese con l’obiettivo di produrre estrusori e filiere per tubi e profili, Maris assume in breve un ruolo da protagonista in quelli che erano i primi sviluppi dei prodotti polimerici, con l’ambizione di dare un contributo all’evoluzione delle relative nascenti tecnologie. È un fatto che ben presto in Maris si sceglie il compounding come missione principe e, negli Anni Settanta, nascono nuovi estrusori bivite corotanti con viti autopulenti e settori componibili. Gli Anni Ottanta portano a estrusori con viti a due o tre principi, mentre gli Anni Novanta vedono sia l’avvio della produzione di linee ad alta coppia e a elevate prestazioni sia l’impiego delle linee Maris in nuovi settori applicativi. “Una famiglia avveduta, che fin dagli Anni Sessanta s’è concentrata nella produzione di estrusori bivite corotanti da applicare ovunque vi fosse l’esigenza di processare in continuo i materiali”, riprende Luciano Battistutta, che così prosegue: “Mi riferisco a settori applicativi che spaziano dalla produzione di masterbatch, divenuti ben presto un’applicazione tradizionale per Maris, passando poi per la produzione di compound alto caricati, rinforzati, TPE, TPV, adesivi, biomateriali, sino ai compound elastomerici o, sempre nel mondo della gomma, al recente brevetto relativo al processo di devulcanizzazione in continuo. In quest’ultimo caso, le gomme vulcanizzate vengono riciclate con un sistema in continuo, consentendone il riutilizzo in nuove formulazioni dal 15 al 50% per la stessa applicazione di origine. Per formulazioni diverse, la percentuale di materiale devulacanizzato all’interno della mescola può essere incrementata ulteriormente. A tal proposito possiamo affermare che, attraverso un’accurata selezione, identificazione e trattamento del materiale, il nostro processo di devulcanizzazione può essere applicato anche a ma-

Luciano Battistutta, sales area manager di Maris
teriali post consumo; mi riferisco, in particolare, ai grandi volumi di pneumatici fuori uso (PFU), i quali possono senz’altro rappresentare un’utilissima “materia prima seconda”. Sempre in termini applicativi, il riciclo, o meglio l’upcycling, è un settore in continua evoluzione e crescita. Maris è già fortemente presente e operativa in questo campo e si pregia di aver già realizzato numerosi processi innovativi nel trattamento di materiali post consumo o di scarti di produzione, per esempio nell’ambito generale delle poliolefine, del PVC, del PET, finanche ai materiali espansi”. E qui si introduce un’ulteriore peculiarità di Maris: la scelta di essere fabbricanti a tutto tondo.
TRA “MAKE” E “BUY” MARIS SCEGLIE SENZA INDUGI “MAKE”
“Make or buy” si riferisce alla scelta di un’azienda di costruire un prodotto al proprio interno oppure di acquistare all’esterno il prodotto stesso e/o un servizio utile alla produzione. La scelta si basa sul raffronto tra i costi totali da sostenere nei due casi, tenendo conto sia delle caratteristiche di reperibilità all’esterno - e quindi d’eventuali criticità - sia delle risorse disponibili all’interno dell’azienda. È una scelta strategica fondamentale per la gestione dell’azienda, che definisce il livello d’integrazione delle attività - a monte e a valle - e determina la struttura dei costi, l’organizzazione e anche il posizionamento sul mercato. L’opzione “make” offre soprattutto il vantaggio di garantire un controllo diretto sull’attività, sugli approvvigionamenti e sulla qualità del prodotto finale. Consente, inoltre, di mantenere e sviluppare il proprio knowhow tecnologico.
“Da sempre ci pregiamo di essere padroni al 100% della nostra tecnologia”, specifica Battistutta, “e ciò è possibile perché le parti fondamentali dei nostri estrusori bivite corotanti sono realizzate internamente con processi produttivi e qualitativi d’alto livello. Ne sono l’evidenza la produzione degli elementi vite, delle sezioni di processo (i cilindri), come pure la fabbricazione in toto dei riduttori, che rappresentano uno dei punti nevralgici dell’estrusore. È questa una scelta che ci consente di produrre macchinari che si contraddistinguono per gli elevati standard qualitativi e per la loro versatilità”. Logisticamente Maris si compone - oltre che della palazzina uffici - di altri tre ampi e distinti reparti. Il più grande è quello di produzione, dove sono in funzione sia centri di lavoro CNC di ultima generazione sia sistemi di lavorazione meccanica più consolidati, perché, come ben spiegato da Battistutta: “Macchinari all’avanguardia, che si alternano ad altri più tradizionali, consentono di gestire le singole fasi delle commesse con flessibilità e di raggiungere, dunque, un livello di personalizzazione elevatissimo”. Altrettanto importante è il reparto destinato all’assemblaggio e al collaudo delle linee. Qui viene anche effettuata la manutenzione degli estrusori. “Siamo in grado di eseguire manutenzioni ordinarie e straordinarie su estrusori costruiti anche svariati decenni orsono (e tuttora operativi). Tale prerogativa ci permette di fornire un servizio post vendita affidabile, efficace, di elevata qualità e, quindi, di consolidare le relazioni con i nostri clienti in modo duraturo”, aggiunge Battistutta. Il terzo e ultimo reparto è il Maris Technological Center, che merita un capitolo a sé. MILLE METRI QUADRI DOVE LE IDEE DIVENTANO REALTÀ Il Maris Technological Center è l’area preposta allo studio e all’ottimizzazione dei processi produttivi dei clienti, nonché alle attività di ricerca e sviluppo per il miglioramento costante delMaris è da sempre padrona della sua tecnologia; anche le parti fondamentali dei suoi estrusori bivite corotanti sono realizzate interamente al proprio interno, con processi produttivi e qualitativi di elevato livello
la tecnologia degli estrusori bivite corotanti. In quest’azienda, infatti, non esiste una commessa standard e la parola d’ordine è flessibilità al servizio del cliente. In questo reparto i clienti comunicano al team di ricerca e sviluppo le informazioni utili alla configurazione della linea pilota; successivamente tale linea viene testata con i materiali forniti e, se necessario, vengono effettuate analisi di laboratorio per comprovare la qualità del prodotto finito in diverse condizioni di processo. “Per valutare in tempo reale i risultati delle prove svolte nel Maris Technological Center abbiamo un laboratorio di caratterizzazione”, esordisce a questo punto Bruno Muscato, esperto di processo all’interno del team di ricerca e sviluppo, “ove effettuiamo sia la caratterizzazione con un microscopio ottico in riflessione e uno in trasmissione sia le analisi reologiche con Melt Index. Possiamo poi valutare le proprietà meccaniche dei materiali, preventivamente stampati, mediante dinamometro”. È con un certo orgoglio che Bruno Muscato - il quale di estrazione culturale è chimico industriale - ci mostra il Filter Test. Un’analisi veloce ideata da Maris, grazie alla quale, misurando la velocità di intasamento del filtro, è possibile misurare la dispersione di cariche/pigmenti all’interno della matrice polimerica. Tutto questo consente di comprendere come un’azienda a gestione familiare possa competere in un contesto internazionale nel mondo dell’estrusione; a conferma di ciò, infatti, Maris collabora con università, enti pubblici e privati (nazionali ed esteri), ma anche con fabbricanti di sistemi produttivi complementari, con studi d’ingegneria e con case automobilistiche nello sviluppo di progetti di ricerca, come quello che ha portato al citato brevetto sulla devulcanizzazione della gomma. “Il nostro centro tecnologico è attrezzato con quattro linee di diverse dimensioni che ci permettono di svolgere dalle attività di ricerca di base sino a simulazioni di produzione su scala industriale”, spiega sempre Muscato, “partendo da quella con diametro vite di 20 mm (da laboratorio o per produzioni molto limitate), passando a una versione da 30 mm, una da 40 mm e, infine, alla più grande da 58 mm. Queste linee ci consentono d’inquadrare il contesto applicativo con un ottimo grado di precisione e di eseguire gli opportuni scale-up individuando la taglia di macchina più idonea a raggiungere il target produttivo atteso dal cliente. La gamma dei nostri estrusori è molto ampia: il loro diametro può arrivare sino a 223 mm e la portata oraria varia in funzione della formulazione e della taglia della macchina. Gli estrusori bivite corotanti hanno la peculiarità di essere modulari e questo ci dà la possibilità di allungarli e accorciarli in base alle esigenze di processo, nonché di alimentare materiali solidi o liquidi in diversi punti dell’estrusore, grazie a specifici cilindri. Le linee di estrusione che forniamo ai nostri clienti possono essere integrate con equipaggiamenti a monte e a valle (in pratica una soluzione “chiavi in mano”), grazie alla collaborazione con i più rinomati marchi del settore. Nel centro tecnologico tutti questi equipaggiamenti sono a nostra disposizione in modo da individuare la scelta più opportuna volta a soddisfare le esigenze dei clienti”. Tali equipaggiamenti includono un’ampia scelta di dosatori gravimetrici per solidi e liquidi a monte dell’estrusore, mentre a valle troviamo pompa a ingranaggi, cambiafiltro, sistemi di taglio immerso, ad anello liquido, in aria e a distanza e, infine, pompe a vuoto e ad alto vuoto.

ESTRUSORE MONOVITE
È possibile processare materiali con:
• Bassa densità apparente • Elevata percentuale di umidità (livelli superiori a 12%) • Elevata percentuale di contaminanti
1a FASE
Macinazione, deumidificazione e stoccaggio Alimentazione dell’estrusore monivite tramite alimentazione forzata Fusione del materiale nell’estrusore monovite Primo degassaggio Filtrazione ESTRUSORE BIVITE COROTANTE
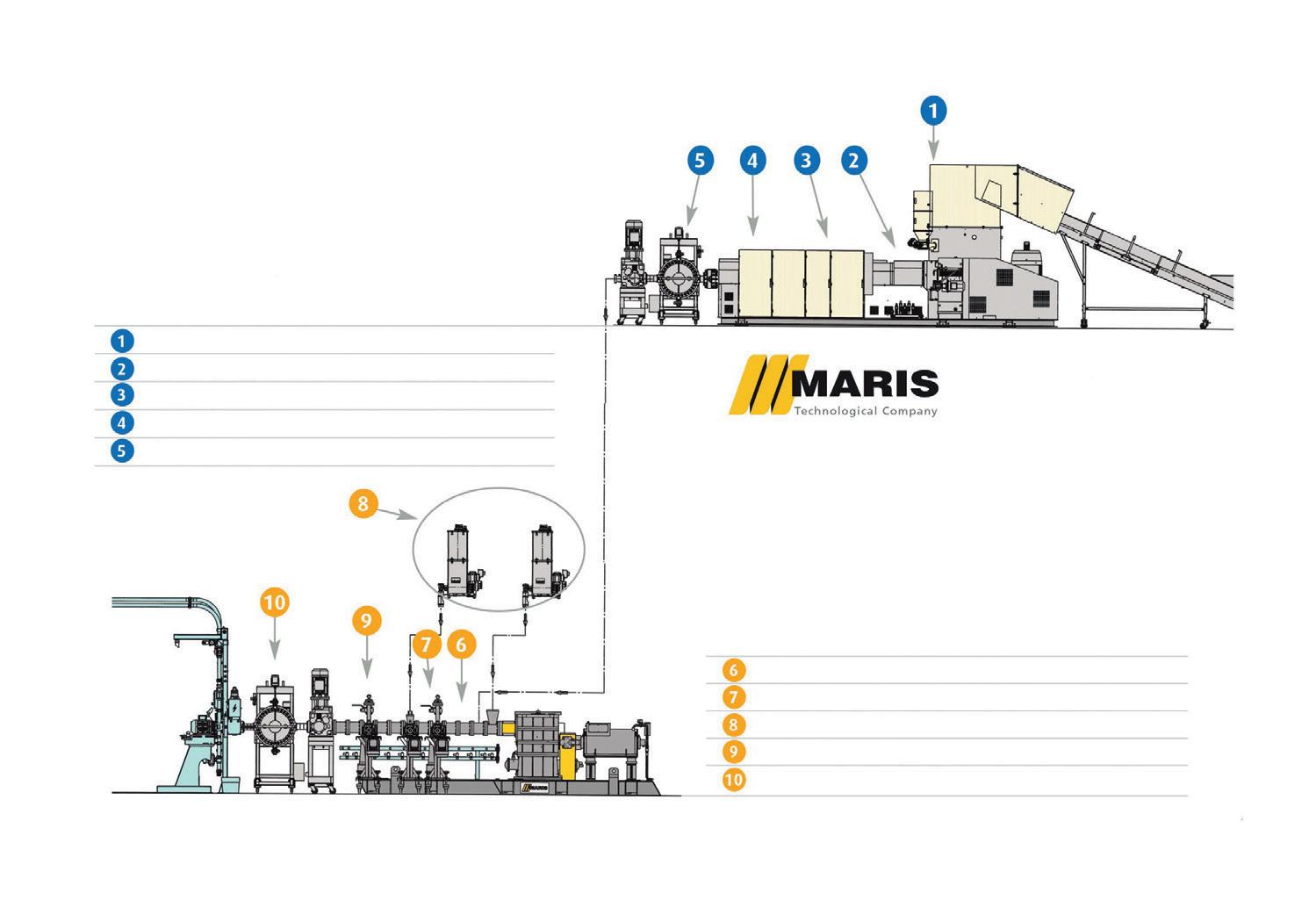
Prestazioni e qualità:
• Elevata mescolazione • Elevato degassaggio • Granuli di alta qualità • Possibilità di aggiungere cariche/additivi
2a FASE
Elevata omogeneizzazione dei materiali Secondo degassaggio Alimentazione di polimeri/cariche/additivi Terzo degassaggio Filtrazione e granulazione
Fig.1 - “Volendo riassumere le peculiarità del tandem”, spiega Muscato, “siamo giunti alla condizione in cui è possibile sfruttare appieno le potenzialità sia dell’estrusore monovite che dell’estrusore bivite corotante, il tutto in un’unica macchina e in un unico passaggio” Bruno Muscato, esperto di processo all’interno del team di ricerca e sviluppo del Maris Technological Center
FOCUS SU EVOREC PLASTIC PLUS: MONOVITE + BIVITE COROTANTE
Alla necessità di riciclare materiali molto contaminati e con elevate percentuali di umidità, Maris risponde con Evorec Plastic Plus. La combinazione di due tecnologie ha permesso - all’interno di un unico impianto - di riciclare materiali molto critici utilizzando un estrusore monovite più un estrusore bivite corotante. “Volendo riassumere le peculiarità del tandem”, spiega Muscato, “siamo giunti alla condizione in cui è possibile sfruttare appieno le potenzialità sia dell’estrusore monovite che dell’estrusore bivite corotante, il tutto in un’unica macchina e in un unico passaggio. Ecco, quindi, che, in virtù dell’unione di due specifici know-how aziendali complementari tra di loro, ora è possibile alimentare materiali non “free-flowing”, eseguire una doppia filtrazione, ottenere materiali con un elevato livello di omogeneità e additivare/caricare il polimero di riciclo. Si possono inoltre processare materiali con un’umidità di partenza e un grado di contaminazione molto elevati; sul solo bivite ciò non sarebbe possibile, ma la combinazione delle due soluzioni lo rende ora fattibile”. Si giunge quindi all’upcycling citato da Battistutta. A tal proposito ci viene in aiuto la figura 1, che mostra le cinque fasi dell’estrusore monovite: 1) macinazione, deumidificazione, stoccaggio; 2) alimentazione; 3) fusione; 4) primo degassaggio; 5) prima filtrazione. Dopo queste operazioni il cosiddetto rifiuto post industriale o post consumo è pronto per essere alimentato in continuo verso l’estrusore bivite corotante. Sempre la figura 1 elenca le fasi di questo secondo step: 1) omogeneizzazione; 2) secondo degassaggio; 3) alimentazione laterale di polimeri, di cariche o di additivi; 4) terzo degassaggio; 5) seconda filtrazione e granulazione.
NUOVI TRITURATORI E NUOVO LABORATORIO IN CASA GAMMA MECCANICA
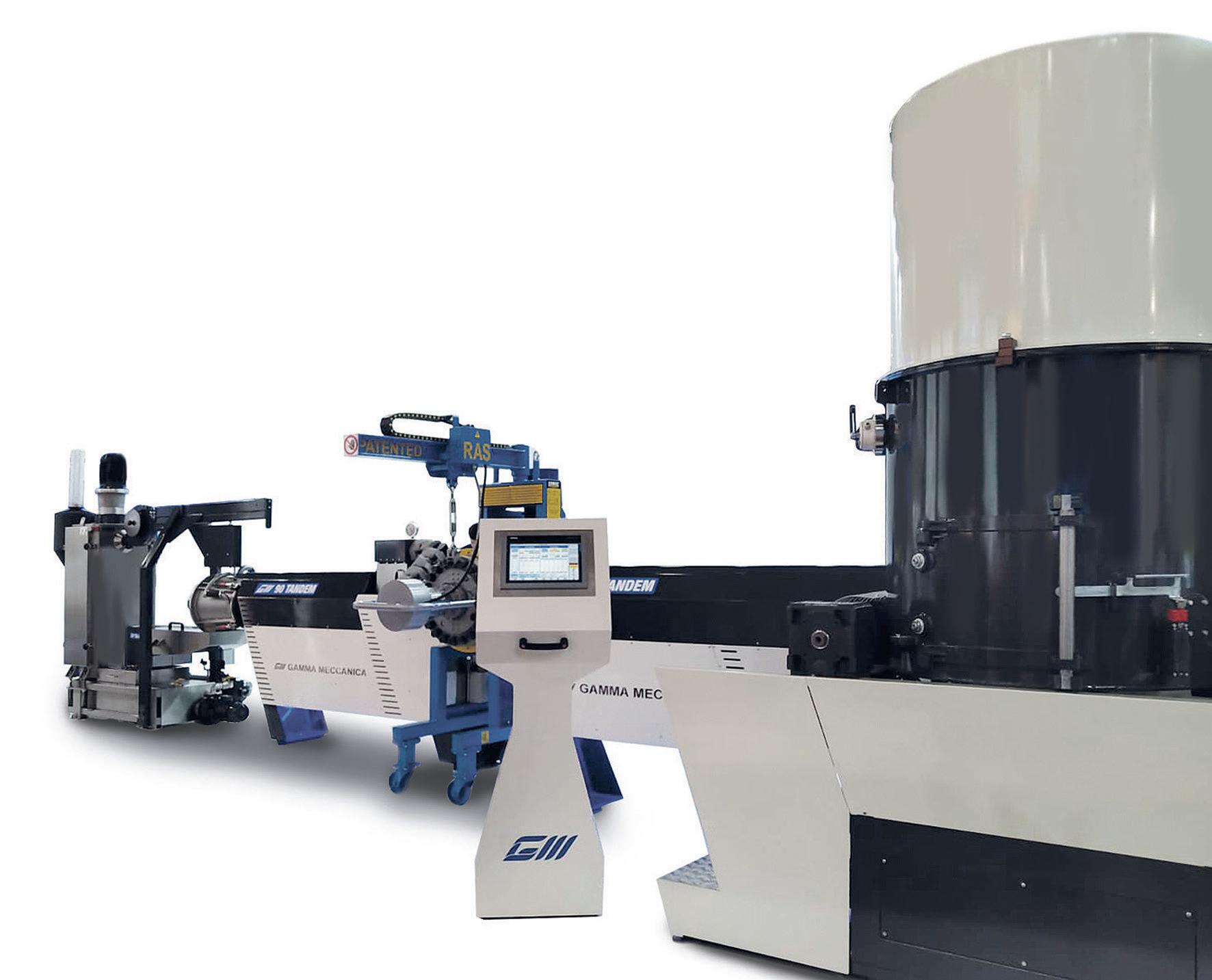
SVILUPPO TECNOLOGICO E MIGLIORAMENTO DEI SERVIZI PER IL RICICLO
NEGLI ULTIMI MESI GAMMA MECCANICA HA PORTATO AVANTI UNA FERVENTE ATTIVITÀ DI SVILUPPO DI NUOVE LINEE E DI MIGLIORAMENTO DEI PROPRI SERVIZI, NELLA CONSAPEVOLEZZA CHE I MATERIALI RICICLATI SIANO OGGI UNA GRANDE RISORSA, MA ANCHE CHE SI POSSA FARE DI PIÙ
Secondo recenti dati di Conai, l’Italia nel 2020, con un tasso di riciclo del 73% degli imballaggi immessi nel mercato, ha superato le previsioni al riguardo. Ciò nonostante, la plastica, rispetto ad altri materiali “rinnovabili” (acciaio, alluminio, carta, legno e vetro), resta sempre quello più “ostico” da recuperare. Nel 2020, con il 48,7% di plastica riciclata, era stato quasi raggiunto l’obiettivo del 50% imposto dalla UE per il 2025, anche se quest’obiettivo comprende anche la rivalorizzazione del materiale sotto forma di combustibile, e parlare di termovalorizzazione vuol dire vedere una risorsa economica andare in “cenere”. Il riciclo, comunque, registra una crescita significativa della termovalorizzazione e questo grazie alla raccolta differenziata degli scarti post consumo, ma anche alla continua evoluzione tecnologica delle attrezzature che permettono di ampliare la gamma di rifiuti plastici che possono essere rigenerati. Specializzata nella progettazione e nella realizzazione di linee per la rigenerazione delle materie plastiche, Gamma Meccanica ha raccolto per circa cinque anni una serie di suggerimenti, informazioni e richieste per arrivare allo sviluppo della nuova generazione di trituratori AFT. L’obiettivo era quello di migliorare le prestazioni di queste macchine e la loro applicazione con i materiali più difficili da rigenerare e per raggiungerlo l’azienda ha eseguito test e condotto studi coinvolgendo anche i suoi fornitori. Determinanti sono state le prove svolte sulle linee pilota installate al proprio interno, le informazioni arrivate dal servizio clienti, le richieste di questi ultimi e la volontà di migliorare e innovare.
MODIFICHE STRUTTURALI E NUOVI ACCESSORI
Il trituratore di una linea di rigenerazione per materie plastiche è la macchina che riceve il materiale di scarto in varie forme e che al proprio interno lo tritura appunto, lo densifica e, quando richiesto, lo mescola con additivi anche in polvere, preparandolo per essere immesso nell’estrusore. I nuovi trituratori AFT offrono diversi vantaggi grazie a una serie di modifiche strutturali e accessori tecnologici. Per azionare il disco su cui poggiano le lame rotanti sono state adottate cinghie Kraft Band,
meglio tensionabili e in grado di migliorare l’efficienza produttiva. Sul disco possono essere installate sei lame rotanti contro le tre dei modelli precedenti, assicurando livelli produttivi più alti soprattutto con i materiali che richiedono più tempo di preparazione. Inoltre, sono state ridisegnate le geometrie interne di diversi componenti. Sotto il silo, nella zona dei cuscinetti, è stato sviluppato un sistema di tenuta per le polveri che consente di mantenere più pulito l’ambiente di lavoro, evitando che le polveri danneggino le parti più sensibili della linea. Anche la posizione del motore della vite premente, che spinge il materiale dal trituratore all’estrusore, è stata ridefinita, rendendo l’unità più compatta e concedendo all’operatore più spazio per muoversi intorno alla macchina, stabilizzando inoltre il motore, che risulta meno sollecitato dalle vibrazioni. Su richiesta, può essere installato un dosatore per additivi in polvere, la cui nuova posizione consente una migliore miscelazione dell’additivo e ne limita la dispersione nell’ambiente. Da sempre i trituratori AFT sono dotati di sistemi di aspirazione dei vapori prodotti al loro interno, come, per esempio, l’aria satura dell’umidità estratta dal materiale trattato. Ultimamente, però, è richiesta una maggiore attenzione nel trattamento delle polveri che spesso accompagnano questi vapori. Pertanto, è possibile dotare il sistema di un dispositivo di preabbattimento delle polveri, in modo da rendere meno gravoso per l’utilizzatore il trattamento dell’aria liberata in ambiente. Uno degli aspetti più interessanti dei nuovi trituratori AFT consiste nella possibilità di abbinarli con estrusori di taglie diverse. Per esempio, in precedenza l’estrusore GM125 Compac di gamma Meccanica poteva essere collegato al solo AFT125, mentre ora è possibile abbinarlo al trituratore di taglia superiore, un AFT160. Dovendo trattare materiali molto umidi, con un trituratore dal volume maggiore si migliora la preparazione del materiale stesso per la fase di estrusione, ottenendo una capacità produttiva più elevata e una miglior qualità del granulo, oppure è possibile processare materiale con tasso d’umidità che può arrivare al 20%. I nuovi abbinamenti sono efficienti anche quando si hanno materiali con pezzature o spessori particolarmente alti e quindi più difficili da trattare.
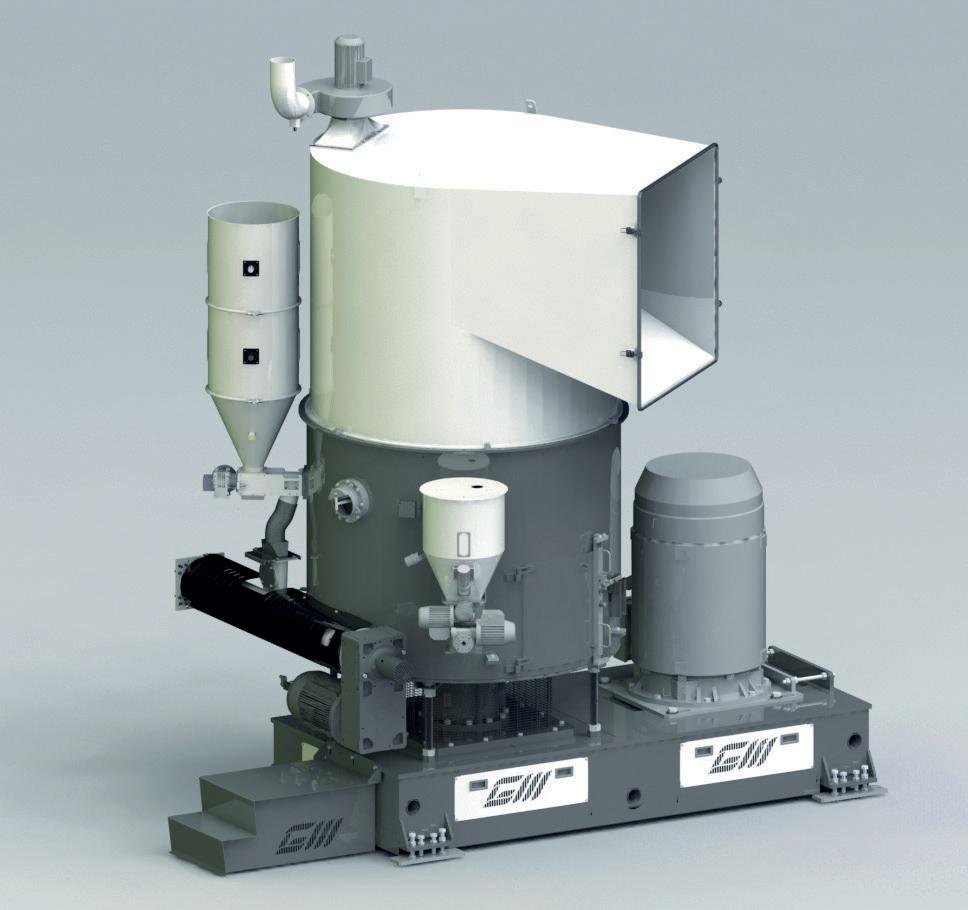
MIGLIORARE ANCHE IL SERVIZIO
Per soddisfare sempre meglio le esigenze dei clienti e assicurare loro risposte precise e complete, Gamma Meccanica ha deciso di ampliare il proprio laboratorio interno e l’area test. La nuova struttura sarà infatti destinata ai test sui materiali forniti dai clienti e a verificare la qualità del processo. Le aziende avranno a disposizione più linee pilota per rigenerare i propri materiali e ricavarne tutti i dati utili sia per pianificare l’acquisto di una linea per il riciclo sia per verificare la qualità e la produzione con essa ottenibile. A tale scopo è stato acquistato un nuovo stabilimento destinato a ospitare il laboratorio, in cui verrà inserito personale tecnico dedicato. Nel nuovo laboratorio saranno in funzione diverse linee dedicate esclusivamente ai test, tra cui una GM 90 Tandem “configurabile” e una GM90 Compac. La linea Tandem (nella foto di apertura) sarà dedicata alle prove con materiali “difficili”, con il 100% di superficie stampata, elevata umidità e molto sporchi. Si tratta di una linea “super-sensoriata” per immagazzinare dati sul funzionamento e sul processo a seconda del materiale, e la versione base comprenderà: nastro di alimentazione con metal detector, trituratore Compac con vite premente, estrusore primario, cambiafiltro, camera del vuoto ad alte prestazioni, collo di collegamento per predisporre due possibili configurazioni con il primo estrusore: un secondo estrusore monovite, un altro cambiafiltro, un sistema di taglio e la bilancia; oppure un secondo estrusore bivite, per ottenere la versione Tandem Plus che permette anche di arricchire il materiale dandogli valore aggiunto (upcycling). Insieme alla linea Tandem sarà disponibile una linea GM90 Compac per il riciclo di materiali “puliti” di origine prevalentemente post industriale, composta da nastro di alimentazione con metal detector, trituratore Compac con vite premente, estrusore con rapporto L/D = 35, cambiafiltro automatico, taglio in testa TDA 4.0 e bilancia. Poiché, durante le prove, i dati devono essere i più esaustivi possibile, questo modello sarà dotato di attrezzare opzionali rispetto a uno standard, quali traino, bypass per dosatore del macinato, dosatore per il / per i master e per le polveri e un vibrovaglio a tre vie. Per i materiali ad alta fluidità, come PET o PA, le prove saranno effettuate con il nuovo sistema di taglio immerso TI 2.3, sviluppato da Gamma Meccanica appositamente per riciclare questo tipo di materiali. Presso il nuovo laboratorio potranno essere effettuate anche prove per rilevare l’umidità, l’indice di fluidità, la viscosità intrinseca del PET, di densità, reologiche, calorimetriche, termo-gravimetriche e roast test per determinare le impurità sulle scaglie di PET.
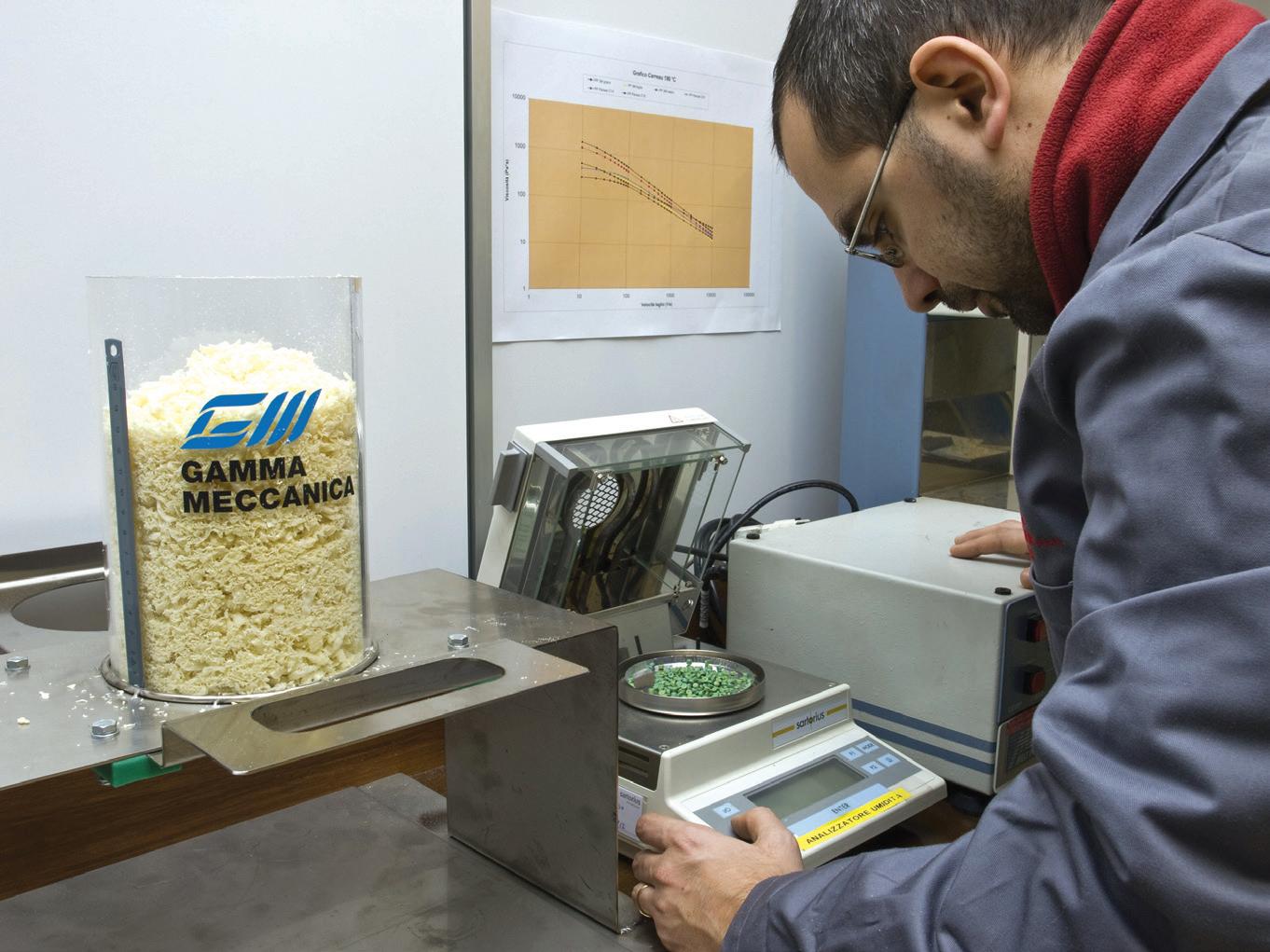
Un esemplare del nuovo trituratore AFT
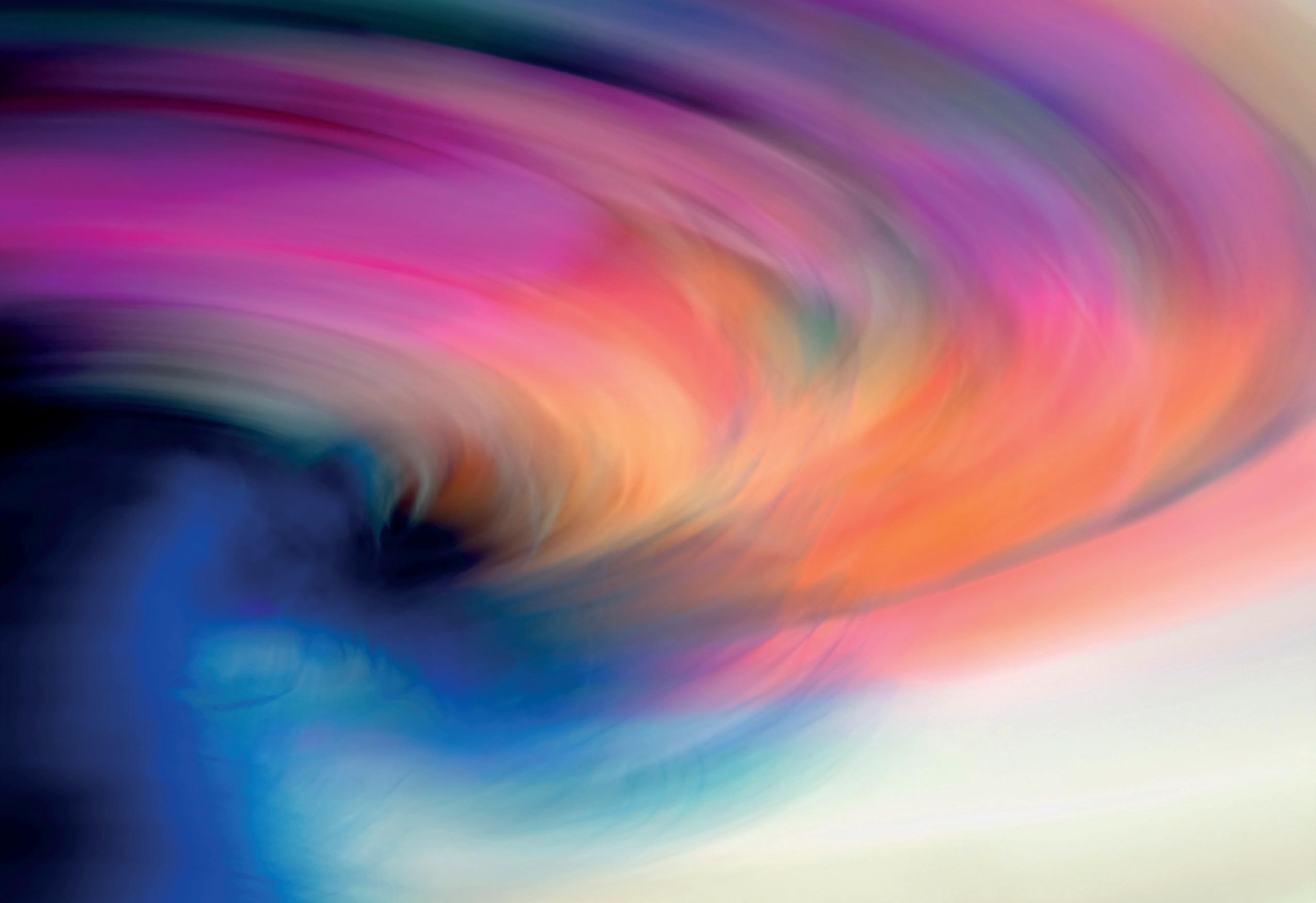
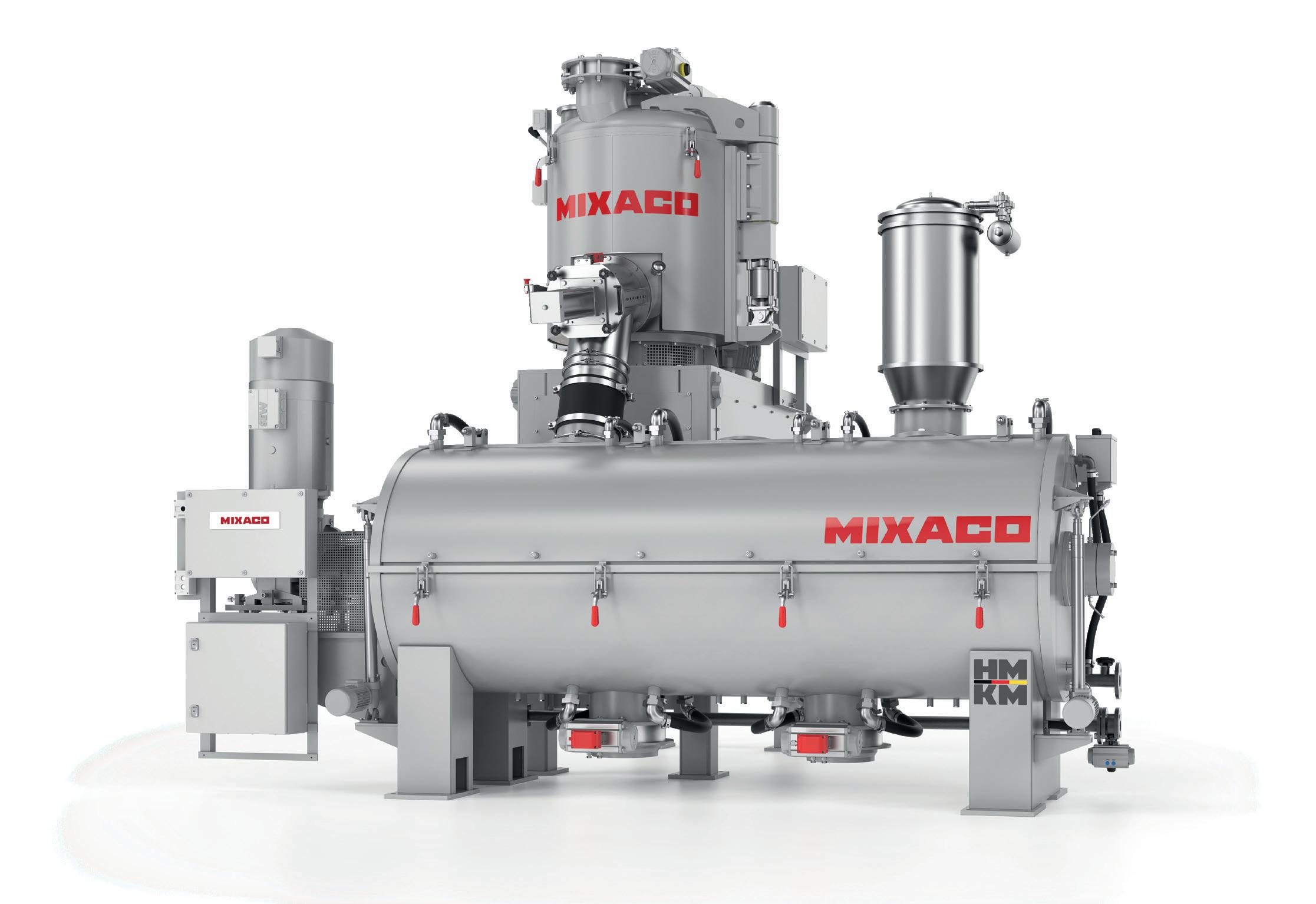
FORNITURA “ACCADEMICA” PER COPERION
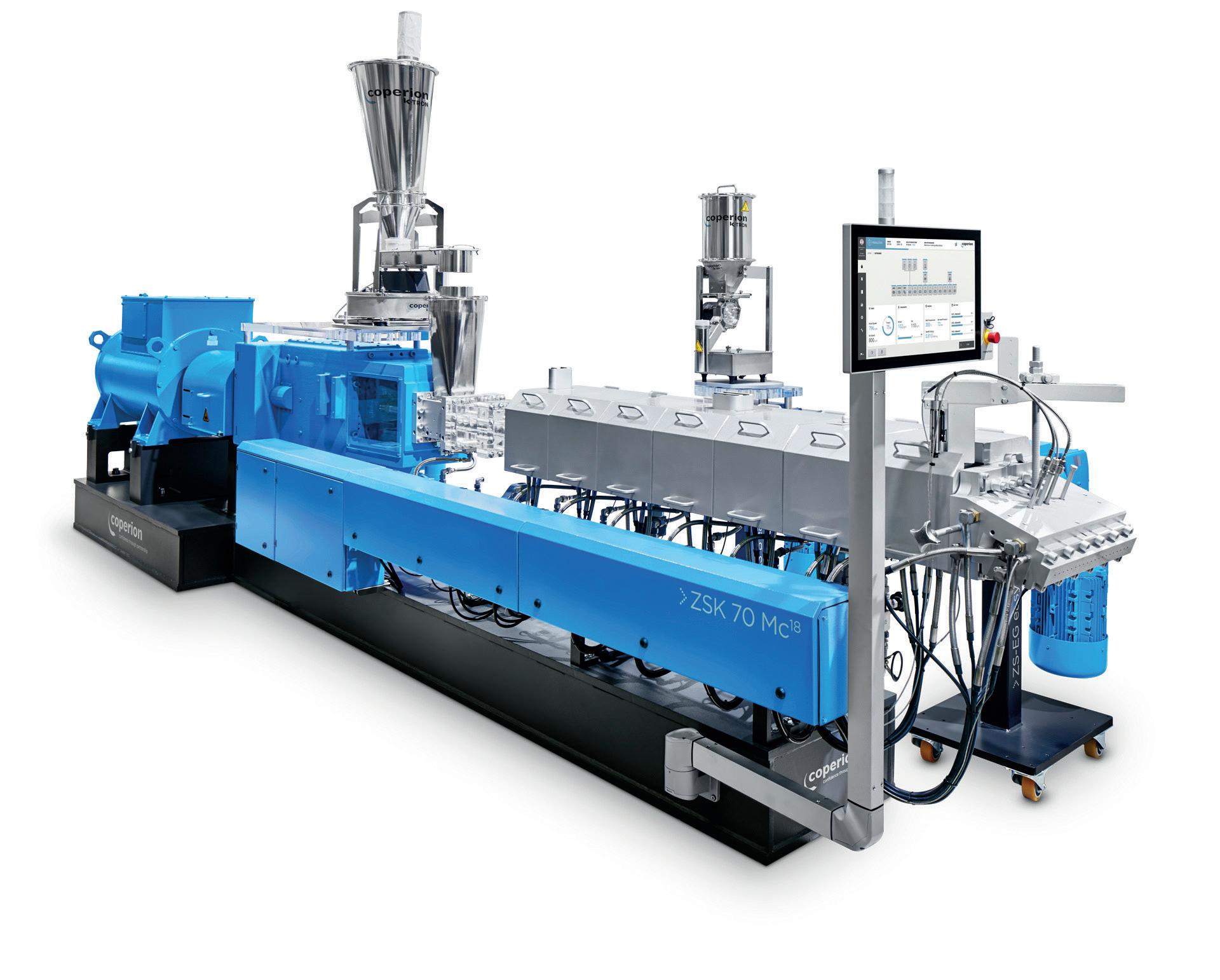
UN ESTRUSORE BIVITE PER IL RICICLO CHIMICO ALL’UNIVERSITÀ DI GAND
IL COSTRUTTORE TEDESCO COPERION HA FORNITO UNA LINEA DI ESTRUSIONE ALL’UNIVERSITÀ DELLA CITTÀ BELGA PER PROGETTI DI RICERCA E SVILUPPO NELL’AMBITO DEL RICICLO CHIMICO DI PLASTICHE MISTE POST CONSUMO. IL SISTEMA SI BASA SU ESTRUSORE BIVITE ZSK 18 MEGALAB, ALIMENTATORE K-TRON E UNITÀ DI ASPIRAZIONE E HA UNA CAPACITÀ TRA 1 E 10 KG ALL’ORA
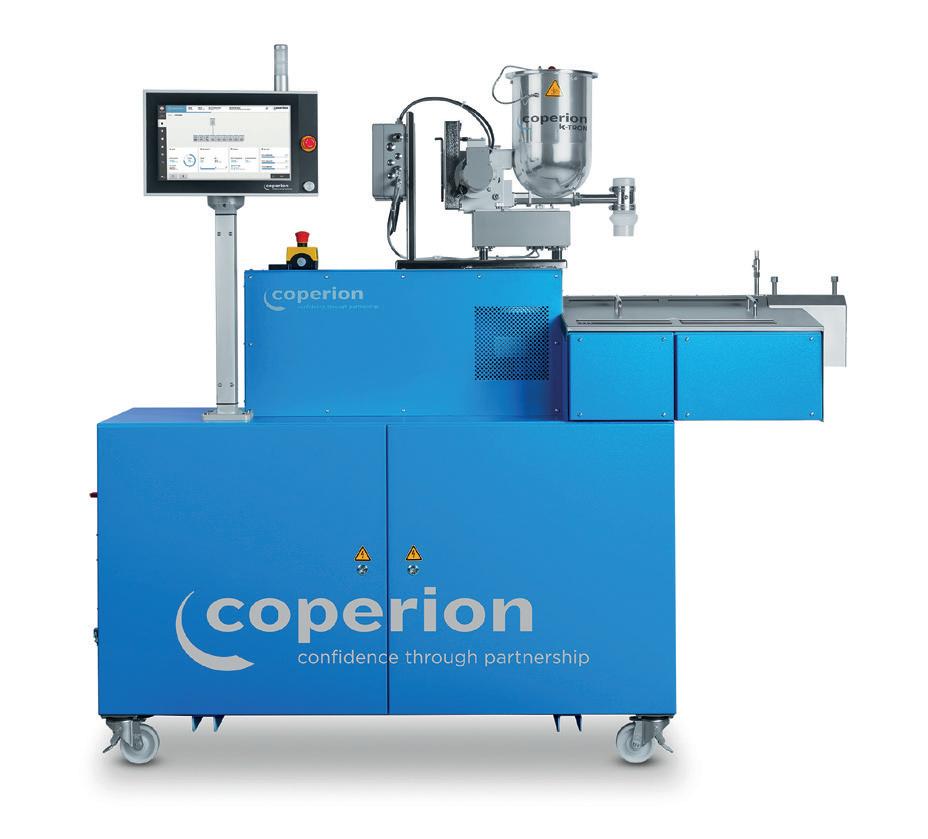
L’estrusore ZSK 18 MEGAlab e il sistema di alimentazione K-Tron installati all’Università di Gand Un estrusore della gamma ZSK di Coperion, a cui appartiene anche quello fornito all’università belga
Irifiuti in plastica, e in particolare quelli da imballaggi, sono generalmente un insieme di materiali con un alto grado di contaminazione e il loro riciclo è di solito difficile, poiché in molti casi la selezione e la pulizia non sono né economicamente sostenibili né tecnicamente fattibili. Il riciclo chimico rappresenta, quindi, un metodo promettente per trasformare questi flussi di materiali in sostanze chimiche, cere o “vettori liquidi di energia”. L’Università di Gand, in Belgio, ha gettato le basi per vari sviluppi di ampia portata in questo campo, contribuendo ad aprire la strada a una maggiore sostenibilità dell’industria della plastica. Il controllo delle reazioni chimiche in generale e della loro cinetica rappresenta l’asse principale delle ricerche svolte presso il Laboratorio di Tecnologia Chimica (LCT) dell’Università di Gand. Sono oggetto delle ricerche: l’ottimizzazione dei processi industriali esistenti e lo sviluppo, l’intensificazione e il miglioramento di nuove tecnologie volte a ridurre al minimo i flussi di rifiuti e il consumo di energia.
ESTRUSORE BIVITE PER UN EFFICIENTE ACCUMULO DI ENERGIA
La tecnologia dell’estrusore bivite ZSK 18 MEGAlab, fornito da Coperion all’Università di Gand, è particolarmente adatta per il riciclo chimico delle materie plastiche. I rifiuti post consumo, triturati o compattati, vengono introdotti nel processo dall’alimentatore K-Tron e nel materiale si accumula una grande quantità di energia meccanica in un tempo assai breve, grazie al continuo
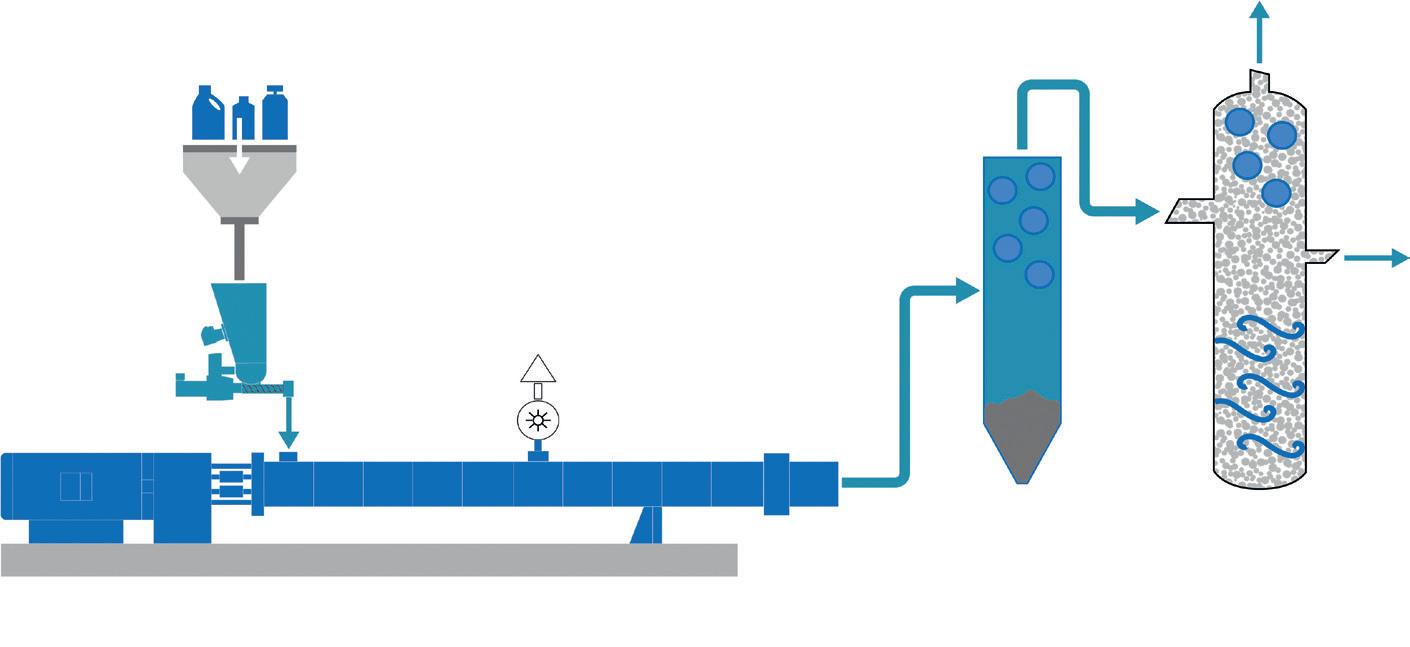
rimescolamento superficiale e all’intensa azione di dispersione e taglio a opera delle due viti. Grazie a tale accumulo di energia, nel giro di circa 30 secondi viene prodotto un fuso omogeneo, degassato e riscaldato a una temperatura fino a 350°C. Altri materiali, come i catalizzatori, possono essere aggiunti e miscelati secondo le necessità, mentre in alcuni casi può accadere che residui d’acqua o cloruri di PVC siano introdotti nell’estrusore in quantità minime, insieme ai rifiuti plastici. Queste sostanze vengono tuttavia estratte in modo affidabile tramite il degassaggio ad aspirazione. Gli estrusori bivite possiedono numerosi vantaggi, che si rivelano particolarmente utili in sede di riciclo chimico. La tecnologia copre un ampio campo di capacità di produzione e, con questo processo, sugli estrusori ZSK più grandi è possibile arrivare fino a 20 tonnellate all’ora. Polimeri di varie viscosità vengono plastificati in modo affidabile grazie all’efficienza del design bivite e la dissipazione dell’energia del materiale plastico avviene in pochissimo tempo. Qualora necessario, la protezione dalla corrosione e dall’usura di tutte le parti a contatto con il prodotto, all’interno della sezione di processo, può garantire una lunga durata dell’estrusore anche nella lavorazione di materiali molto aggressivi.
Estrusore bivite - Dispersione, degassaggio, introduzione di energia Reattore Distillatore
Schema del processo di riciclo chimico presso l’Università di Gand
RECUPERO DI MATERIE PRIME
All’interno del reattore, il fuso, già riscaldato fino a 350°C dall’estrusore bivite, viene ulteriormente riscaldato. A 500°C avviene la pirolisi dei polimeri, con la scissione delle catene polimeriche in unità più corte in un ambiente privo d’ossigeno. La pirolisi dei polimeri si basa su di un meccanismo di scissione casuale, in cui si generano radicali liberi. Allo stesso tempo, si avviano le reazioni a catena che portano alla scissione dei polimeri (cracking) in una serie di idrocarburi in fase liquida e gassosa. I fattori più importanti per guidare questo processo sono il tempo di permanenza, la temperatura e il tipo di agente di pirolisi. La maggior parte dei componenti inorganici dei rifiuti post consumo finisce nel pozzetto del reattore, da dove viene rimossa. Gli idrocarburi organici dei polimeri evaporano. Vengono trasformati in monomeri, materie prime petrolchimiche o gas di sintesi, e quindi, trasformati ulteriormente all’interno di un distillatore in prodotti commerciali come: oli, combustibili pesanti o cere. Il riciclo chimico è un settore di ricerca molto attivo all’Università di Gand. Anche se è già dimostrato che il riciclo meccanico rappresenta un metodo più semplice per la valorizzazione della plastica, sono state riscontrate alcune limitazioni causate dalle difficoltà a livello di separazione dei rifiuti; limitazioni che possono essere superate con il riciclo chimico. L’estrusore bivite ZSK di Coperion farà parte di un nuovo sistema per il riciclo chimico presso l’Università di Gand e, tra l’altro, sarà accoppiato a un reattore a vortice, in modo da far fluire il fuso direttamente nel reattore. Possono essere applicate diverse tecnologie per la conversione dei rifiuti plastici in sostanze chimiche, come la pirolisi catalitica e il trattamento termico-chimico (cracking).
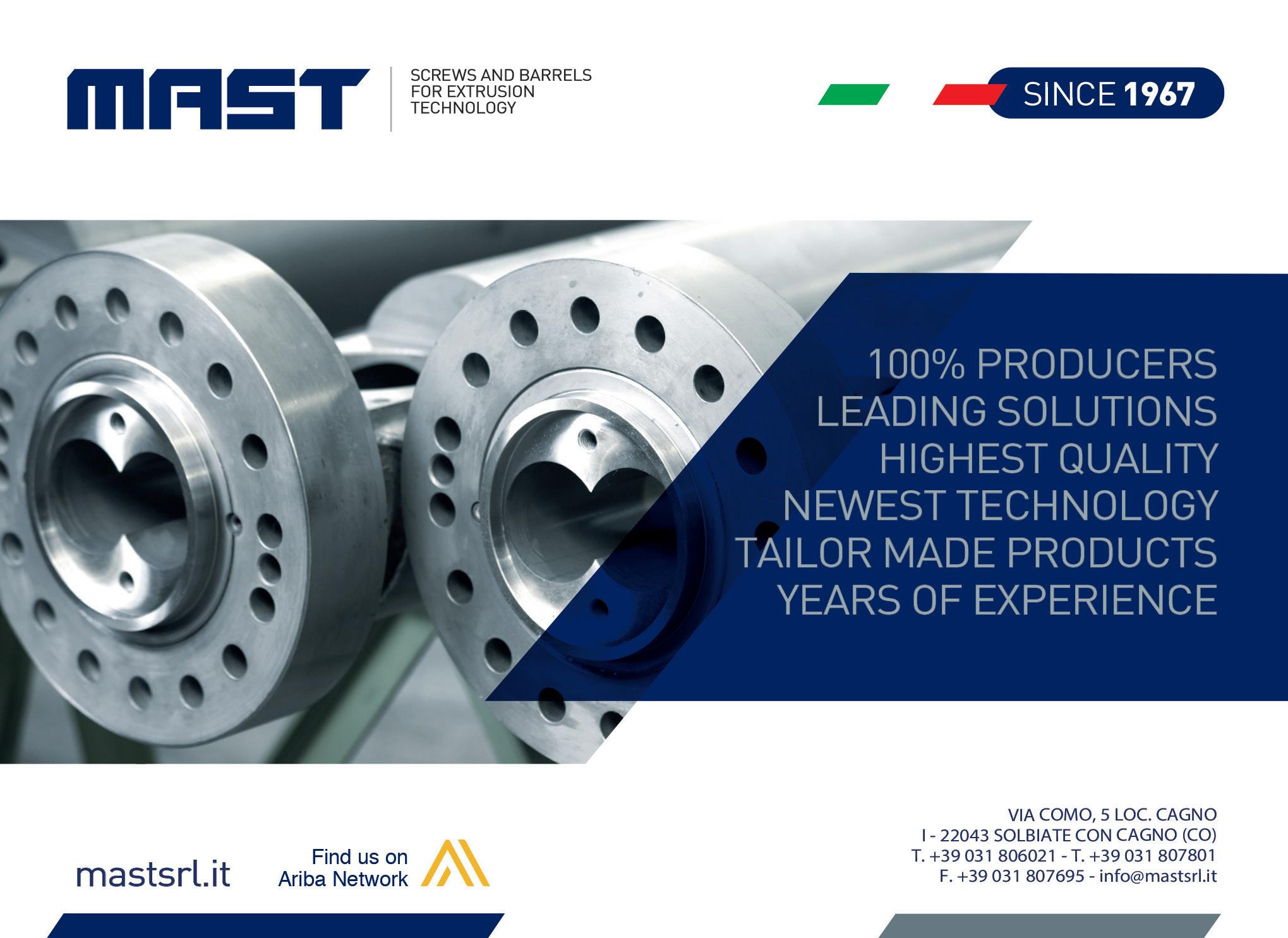
LA TECNOLOGIA MRS DI GNEUSS
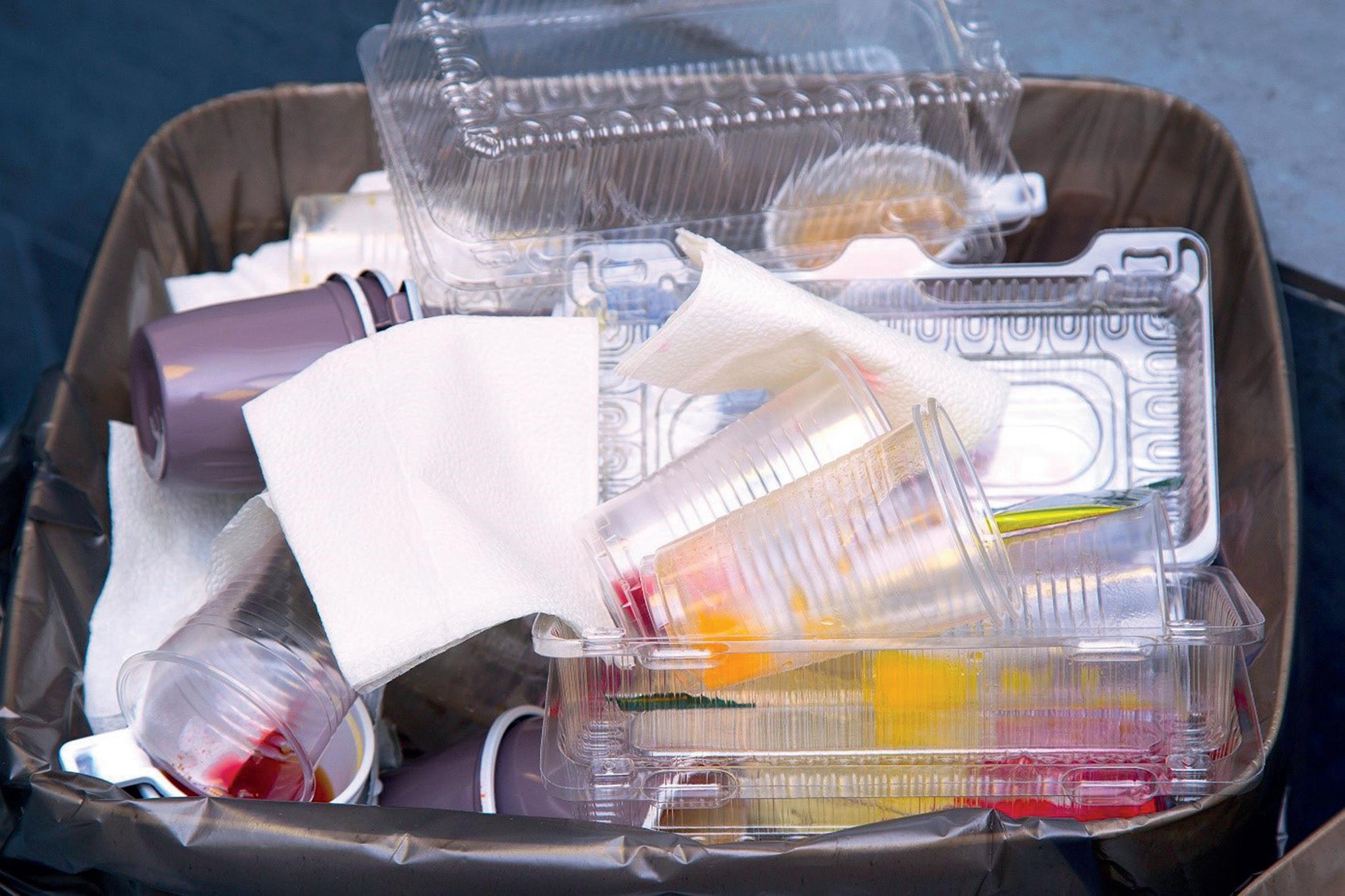
L’EVOLUZIONE DEL RICICLO DI PET POST CONSUMO
IL RICICLO DEL PET IN SCAGLIE VA OGGI OLTRE L’IMPIEGO DELLE SOLE BOTTIGLIE POST CONSUMO E INCLUDE MATERIALI PROVENIENTI ANCHE DA ALTRE FONTI. SE DA UN LATO QUESTO PORTA A SVILUPPARE APPLICAZIONI E TECNOLOGIE, DALL’ALTRO PONE ALCUNE PROBLEMATICHE LA CUI CONSIDERAZIONE NON PUÒ ESSERE TRALASCIATA, IN PARTICOLARE PROPRIO DAL PUNTO DI VISTA TECNOLOGICO. ECCO LE SOLUZIONI PROPOSTE DAL COSTRUTTORE GNEUSS
Oggi, il riciclo del PET in scaglie proveniente da bottiglie post consumo è ben consolidato e l’attenzione si sta spostando verso l’utilizzo di rifiuti in PET di diversa provenienza, come le fibre post industriali e altri articoli post consumo, quali recipienti, vaschette e vassoi termoformati. La differenza in termini di riciclo consiste nel fatto che nel caso del PET in scaglie proveniente da bottiglie post consumo è accettabile una certa diminuzione della viscosità intrinseca (IV), mentre con le fibre post industriali, o con i rifiuti di diverso tipo, qualsiasi diminuzione della viscosità intrinseca si tradurrebbe in proprietà meccaniche inaccettabili nei prodotti finali. In questi casi, la soluzione è generalmente quella di eseguire una fase liquida complicata e/o energivora, oppure processi allo stato solido, per l’incremento dell’IV a valle dell’estrusore. IV PRESERVATA
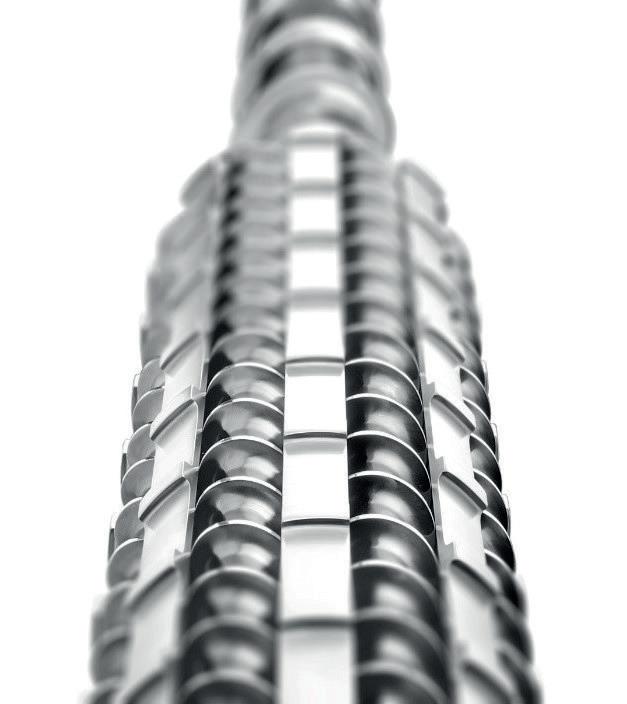
Per fare fronte a tale inconveniente, l’estrusore MRS di Gneuss per la lavorazione di PET offre elevate prestazioni di decontaminazione e, nel caso di rifiuti post consumo di origine diversa dalle bottiglie, ha ottenuto l’approvazione per utilizzare il materiale con esso processato a contatto con alimenti, senza dover effettuare alcun trattamento termico aggiuntivo. La nuova versione MRSjump fornisce una maggiore superficie di scambio sottovuoto, in modo che la policondensazione parziale abbia luogo all’interno dell’estrusore stesso e sia possibile preservare l’IV iniziale. A ciò si aggiunge il fatto che l’intensa devolatilizzazione e il prolungato tempo di residenza sottovuoto del polimero possono essere controllati per fornire una
Vite dell’estrusore MRS con sezione a rotazione multipla, per efficienti degassaggio e decontaminazione
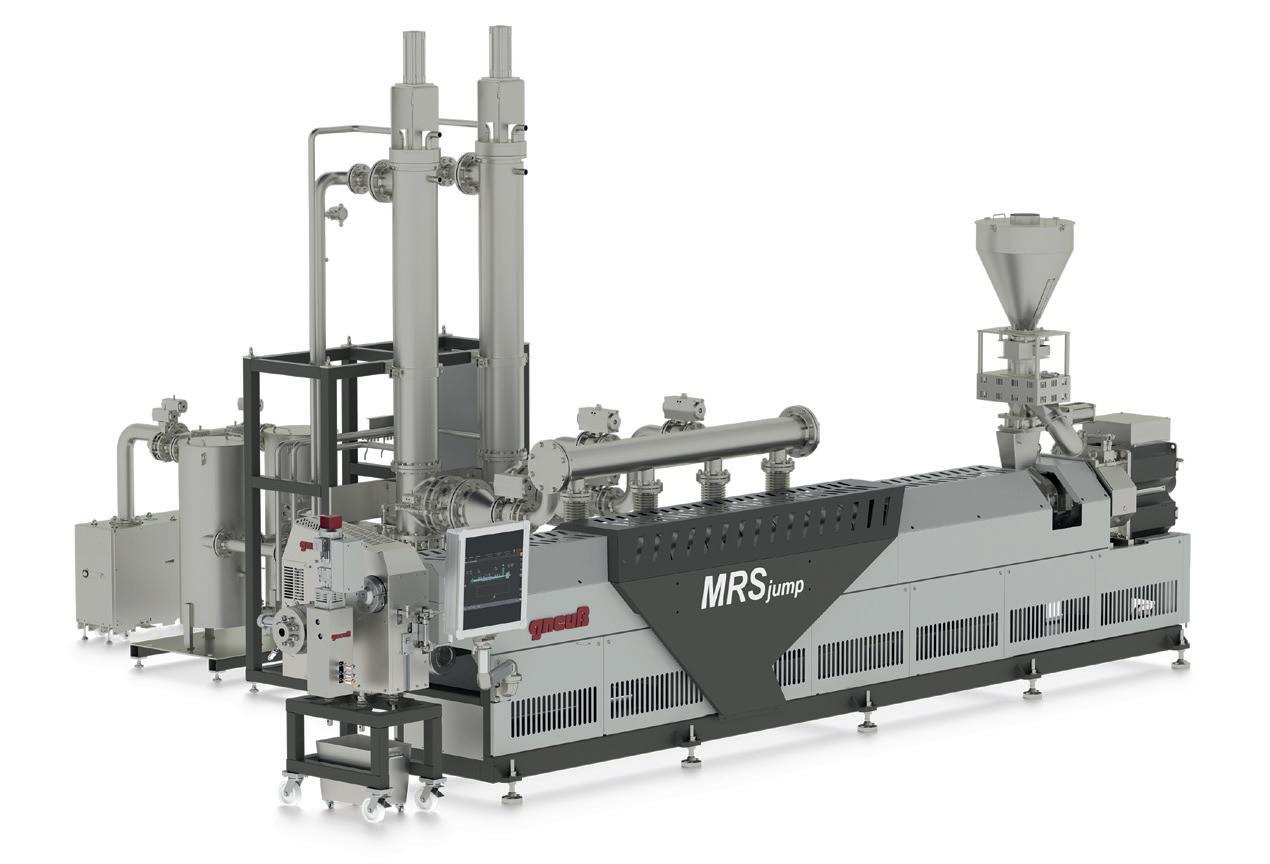
IV costante in uscita, nonostante le inevitabili variazioni del livello di umidità residua del materiale in ingresso. Il sistema MRSjump, quindi, offre sia prestazioni di decontaminazione che rendono il materiale idoneo al contatto con gli alimenti sia la possibilità di preservare e controllare l’IV in un’unica fase di lavorazione dell’estrusione. Non è così necessario trattare il materiale prima dell’estrusione, né un ulteriore processo di fusione o d’incremento allo stato solido dell’IV dopo l’estrusore. Ne conseguono minori consumo energetico, ingombro, complessità dell’impianto e lavoro per l’operatore, così come migliore qualità dei materiali, maggiore flessibilità e possibilità di utilizzare materiali il cui riciclo in precedenza non risultava economico.
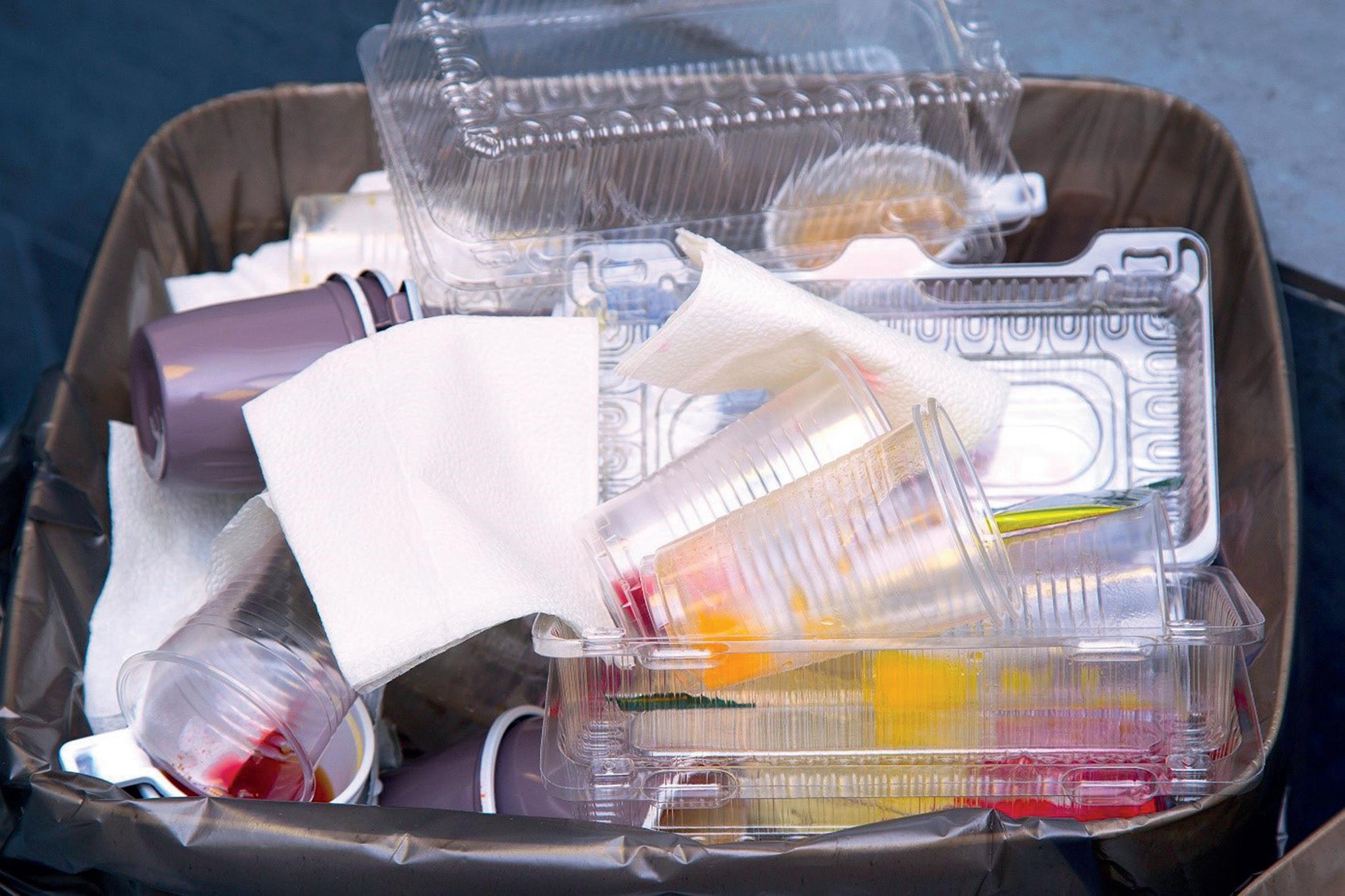
DA VASCHETTA A VASCHETTA
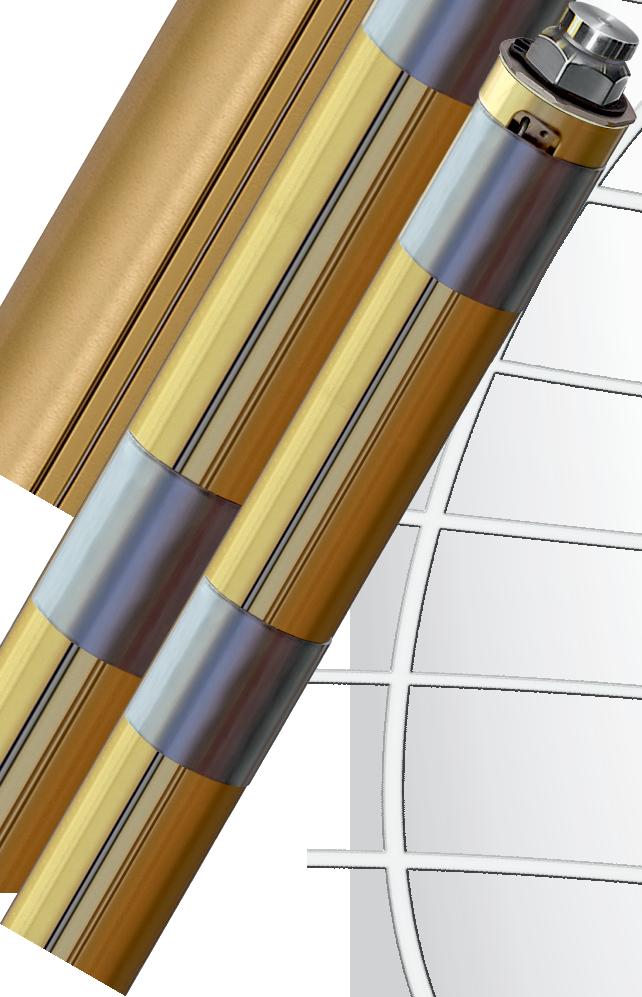
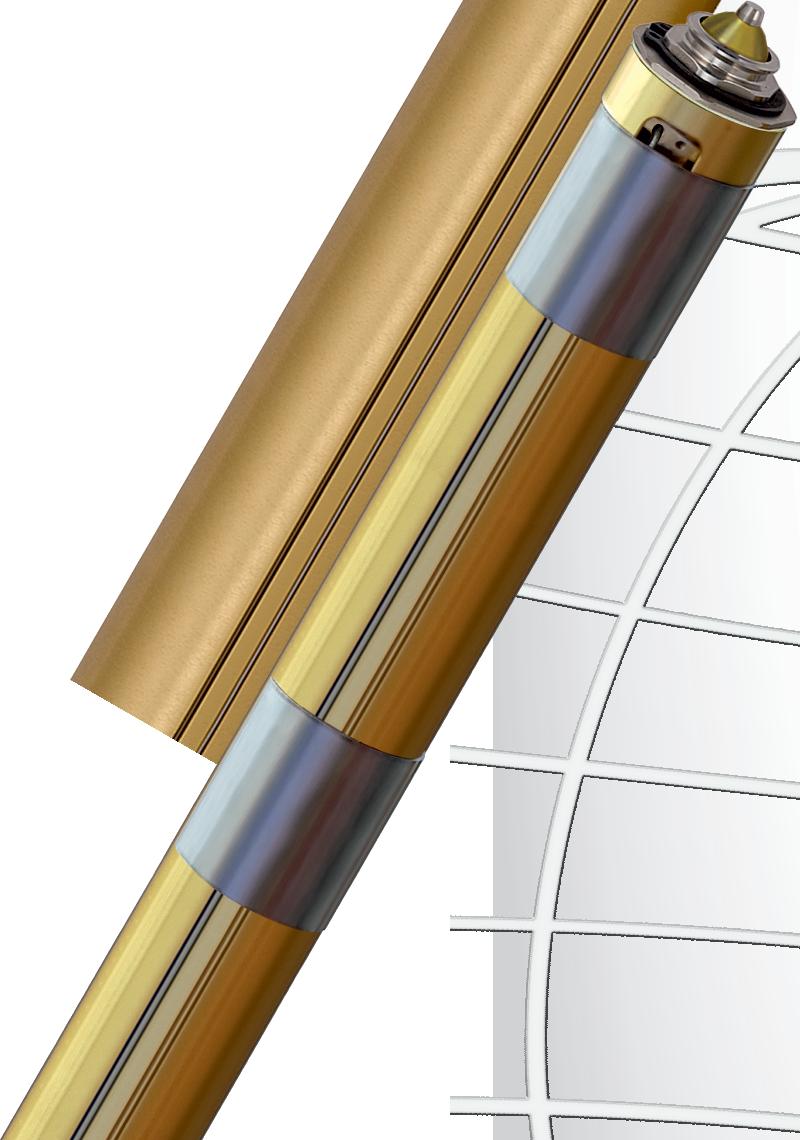
L’utilizzo di vaschette post consumo in PET per produrre nuovi imballaggi per alimenti pone requisiti stringenti al processo di estrusione del semilavorato da destinare a tale scopo. Anzitutto, come si è visto, a differenza delle scaglie di PET provenienti da bottiglie post consumo, la viscosità intrinseca del rimacinato ottenuto dalle vaschette in PET risulta troppo bassa per consentirne il riciclo diretto su una linea per l’estrusione di lastre convenzionali. Vi è poi da tenere in considerazione il fatto che la provenienza delle vaschette in PET post consumo non è (ancora) controllata come nel caso delle scaglie in PET da bottiglie post consumo, a cui si aggiunge il fatto che in circolazione vi è una vasta gamma di diversi tipi di vaschetta impiegati in modi altrettanto differenti, che determinano una variabilità considerevole di qualità e proprietà del rimacinato. Inoltre, è pressoché inevitabile che il rimacinato ottenuto da vaschette in PET sia contaminato da altri polimeri, la cui presenza non può essere completamente esclusa dato che le vaschette possono essere realizzate utilizzando semilavorati coestrusi o laminati. Va da sé che è estremamente importante una decontaminazione efficiente del polimero da impiegare per produrre strutture monostrato, in particolare quando destinate al contatto con alimenti. Infine, il materiale, seppur debba essere decontaminato in maniera efficiente, allo stesso tempo, e proprio a questo scopo, deve anche essere trattato nel modo più delicato possibile, soprattutto se deve essere lavorato in un ciclo chiuso e se la qualità del prodotto finale non può essere pregiudicata.
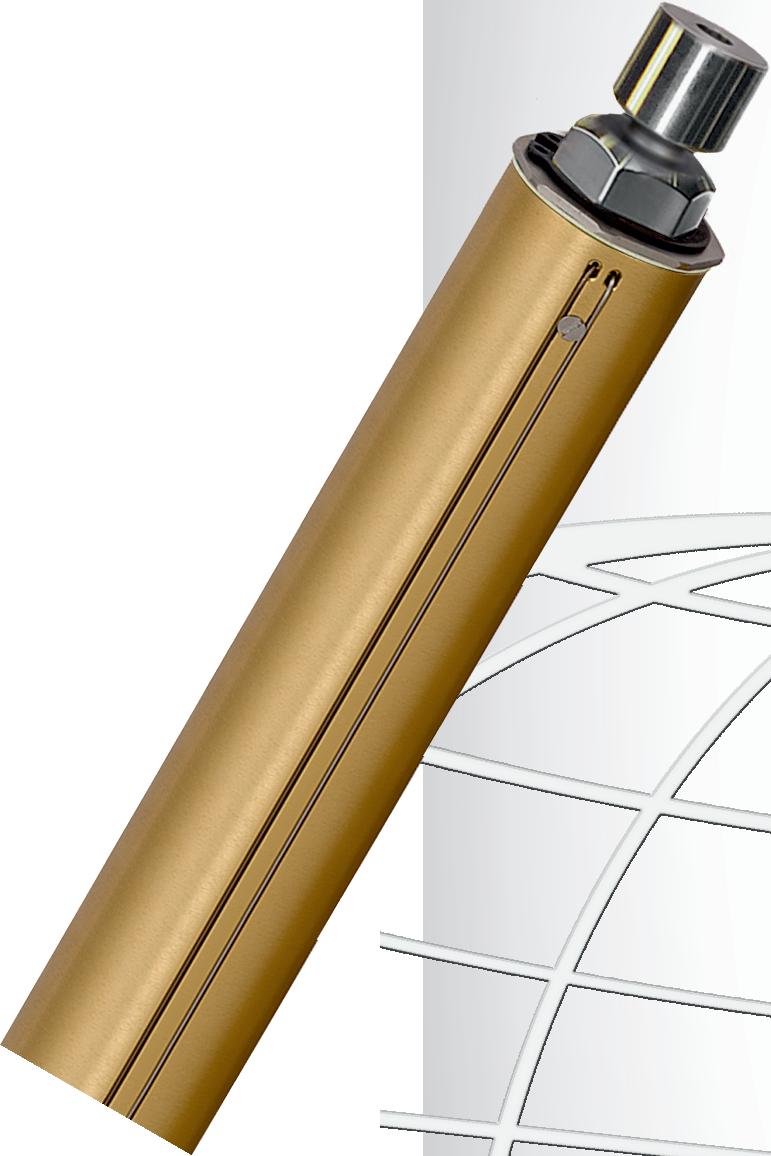

Un esemplare dell’estruore MRSjump
UN APPROFONDIMENTO SULL’MRSjump
Per questo impegnativo processo di riciclo da vaschetta a vaschetta, Gneuss ha sviluppato l’estrusore MRSjump, che combina le elevate prestazioni di decontaminazione della gamma MRS con la capacità di incrementare la viscosità in una sola fase di lavorazione. Il processo dell’MRSjump non richiede alcun pre o post trattamento del materiale, come la cristallizzazione e la pre-essiccazione del riciclato, o l’incremento di IV in un sistema SSP (Policondensazione allo Stato Solido). L’elevata efficienza di degassaggio consente di rispettare i parametri fissati per il contatto con alimenti senza lunghe e costose fasi di trattamento dei materiali, a monte o a valle. Grazie alla breve filiera di processo, la fusione avviene in uno spettro temporale ristretto e definito e lo stress termico e meccanico sul materiale viene mantenuto basso, ottenendo eccellenti proprietà meccaniche e ottiche dell’estruso. Il layout estremamente compatto dell’MRSjump richiede solo poco spazio, energia e manutenzione rispetto ad altre soluzioni. L’estrusore MRSjump è abilitato a lavorare un’ampia gamma di materiali in ingresso, dai rimacinati provenienti da vaschette mono e multistrato a combinazioni di materiali che tendono a raggrupparsi durante il pretrattamento termico. In combinazione con la tecnologia di filtrazione rotante di Gneuss, viene garantita un’elevata purezza di fusione. A favore della qualità, sono inoltre disponibili dispositivi opzionali in linea per la rilevazione della viscosità e delle proprietà ottiche. L’estrusore MRSjump rappresenta dunque una soluzione ottimizzata per il riciclo post consumo da vaschetta a vaschetta, che soddisfa pienamente le esigenze del moderno imballaggio alimentare. Riciclo e decontaminazione sono possibili in una semplice fase di estrusione, senza alcun trattamento del materiale a monte o a valle, aprendo nuovi sbocchi al riciclo del rimacinato da vaschette.

WITTMANN BATTENFELD A FAKUMA
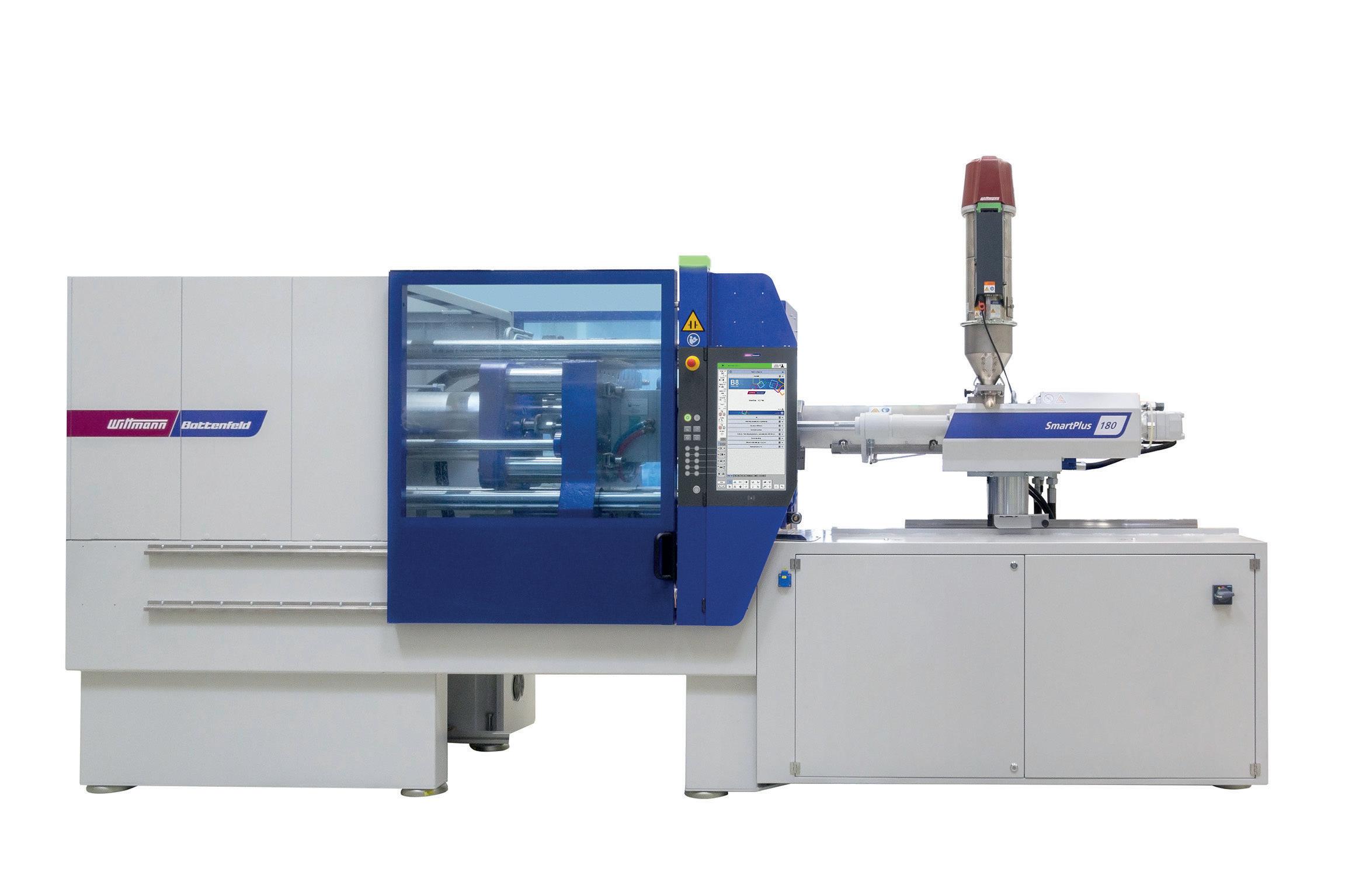
INNOVAZIONE A TUTTO TONDO
TANTE LE NOVITÀ E LE CONFERME PRESENTATE DAL COSTRUTTORE AUSTRIACO ALLA FIERA SULLE RIVE DEL LAGO DI COSTANZA, DESTINATE A MOLTI AMBITI APPLICATIVI NELLA TRASFORMAZIONE DI MATERIE PLASTICHE E GOMMA. ECCONE ALCUNE NELLE COLONNE CHE SEGUONO
A CURA DI RICCARDO AMPOLLINI E LUCA MEI
Vasta e varia la schiera di prodotti presentati da Wittmann Battenfeld alla recente fiera Fakuma 2021, svoltasi a Friedrichshafen (Germania) dal 12 al 16 ottobre, a cominciare dalla pressa a iniezione SmartPlus 180, la prima di una nuova serie basata sulla gamma SmartPower a essere presentata al grande pubblico. Tuttavia, mentre le SmartPower sono soluzioni servoidrauliche di fascia alta, configurabili con diverse opzioni di equipaggiamento, le SmartPlus offriranno una scelta più limitata di dotazioni e, di conseguenza, saranno destinate principalmente ad applicazioni standard. L’intento del costruttore austriaco, infatti, era quello di creare una serie di macchine orientate ad applicazioni meno complesse
e con minori necessità di equipaggiamento, mantenendo tuttavia un elevato standard qualitativo. Queste considerazioni sono sfociate nello sviluppo della serie SmartPlus, dove “Plus” sottolinea il valore aggiunto che questa nuova serie di macchine offre nelle tipologie di applicazioni a cui è destinata. STAMPAGGIO DI MATERIALI VERGINI, RIGRANULATI ED LSR SmartPlus viene fornita equipaggiata con il sistema di controllo Unilog B8 e l’hardware B8X ad alte prestazioni, che consentono Un dettaglio della tecnologia di servoazionamento “Drive-on-Demand 2.0” cicli più veloci, tempi di rispo-
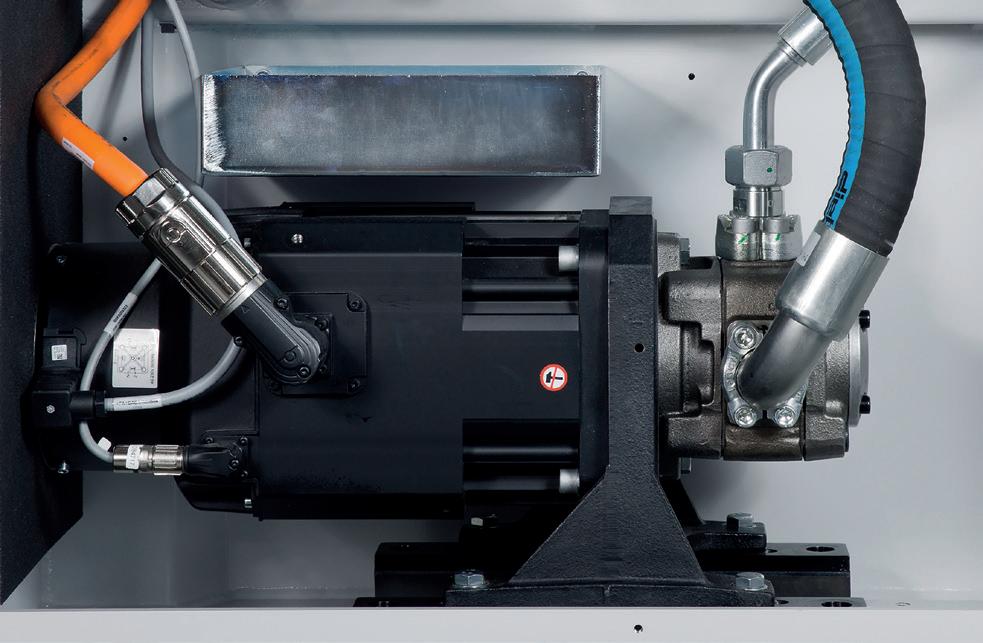
sta più brevi e una maggiore ripetibilità della produzione. Come le altre presse di Wittmann Battenfeld, le SmartPlus supportano l’integrazione di robot e ausiliari Wittmann 4.0 e sono inoltre dotate della tecnologia Kers per il recupero energetico. Per consentire la lavorazione senza problemi di materiali rigranulati, in un’ottica di produzione sostenibile, questa pressa viene offerta anche con il software applicativo HiQ Flow, sviluppato per compensare le fluttuazioni di viscosità che possono verificarsi quando si lavorano materiali di questo tipo. I gruppi di plastificazione/iniezione sono liberamente accessibili, compatti e girevoli. Le macchine SmartPlus, inoltre, integrano un gruppo di plastificazione particolarmente resistente all’usura. Un’ulteriore loro caratteristica specifica è rappresentata dalla tecnologia di azionamento “Drive-on-Demand 2.0”, che consente di aumentare la velocità di risposta della macchina grazie a un booster appositamente sviluppato dal costruttore. L’azionamento viene attivato solamente per il tempo necessario a eseguire i movimenti e per generare la pressione richiesta. Durante il raffreddamento, o le interruzioni di ciclo necessarie per la movimentazione delle parti, l’azionamento rimane spento e non consuma energia. La tecnologia “Drive-on-Demand 2.0” consente movimenti macchina altamente controllati dal punto di vista della dinamica e tempi di ciclo più brevi. Anche le SmartPlus sono disponibili in versione “Insider”, con sistema integrato di movimentazione delle parti, nastro trasportatore e alloggiamento di protezione collegato in modo permanente alla macchina, oppure in versione “Ingrinder”, con smaterozzatore integrato, trasportatore ad aspirazione e granulatore. Le nuove presse saranno disponibili in una prima serie con forze di chiusura tra 60 e 180 tonnellate. A Fakuma 2021 era esposto il modello SmartPlus 180/750 che produceva un coprimozzo in PP per tosaerba. In un’ottica di produzione sostenibile, il componente era prodotto utilizzando una miscela di materiale vergine e materiale rigranulato, assistito dal software HiQ Flow per garantire componenti con un adeguato livello di qualità. A Fakuma 2021, Wittmann Battenfeld produceva anche un anello di supporto in silicone e policarbonato, ottenuto mediante uno stampo a otto impronte. Con

I trent’anni di Wittmann Battenfeld Italia Il Belpaese è un mercato che conta da tre decenni
Circa 100 persone, tra clienti, dipendenti e giornalisti della stampa specializzata, hanno preso parte ai festeggiamenti per il trentesimo anniversario di Wittmann Battenfeld Italia, svoltisi nel suggestivo scenario di Villa Esengrini Montalbano, con spettacolare vista sul lago di Varese, lo scorso 30 settembre. “La celebrazione dei trent’anni d’attività di Wittmann Battenfeld Italia rappresenta naturalmente il motivo principale della nostra presenza in questa bellissima villa di Varese. Ma siamo qui anche e semplicemente per ritrovarci di nuovo insieme. Dopo la pandemia da coronavirus, infatti, credo che siano tutti quanti ansiosi di potersi incontrare nuovamente di persona, senza riunioni virtuali, e che sentano la mancanza di questi momenti di convivialità. Si tratta, senza alcun dubbio, di un aspetto importante per Wittmann Battenfeld, al fine di riprendere finalmente una vita più normale”, ha commentato il CEO del gruppo austriaco, Michael Wittmann, il quale ha fatto gli onori di casa insieme al direttore generale e CEO della filiale italiana, Gianmarco Braga. “A parte questo, devo dire che l’Italia si è rivelata un mercato eccellente per il nostro gruppo. Lo dimostra proprio il fatturato di Wittmann Battenfeld Italia, che si colloca in quinta o sesta posizione tra le filiali globali. Intravedo inoltre un futuro roseo per l’Italia, anche solo per il fatto che la Germania sta continuando a spostare attività industriali all’estero, soprattutto nei Paesi dell’Europa orientale, ma anche nella vicina Italia. È chiaro, quindi, che anche Wittmann Group tenderà a stringere legami solidi con Polonia, Repubblica Ceca, Slovacchia e Ungheria, ma sicuramente uno dei paesi con cui intratterrà rapporti eccellenti sarà sempre l’Italia”, ha proseguito Wittmann. “Grazie alla citata “delocalizzazione tedesca”, prevedo che il Belpaese crescerà ulteriormente nel giro di un paio d’anni. Un altro grande vantaggio dell’Italia è costituito dal programma d’incentivi statali per l’Industria 4.0, che contribuirà certamente a modernizzare le attività industriali e gli impianti in loco, per renderli più efficienti. Tutto ciò si rivelerà molto utile, nel lungo periodo. In sintesi, prevedo quindi un futuro molto positivo, direi anzi luminoso, per l’industria italiana delle materie plastiche”, ha aggiunto il CEO. Parlando più in generale del settore materie plastiche a livello globale, Michael Wittmann ha poi affermato: “A causa del lockdown, purtroppo, il settore aveva cominciato a divenire meno efficiente all’inizio del secondo trimestre 2020. Direi, però, che a partire dallo scorso mese di settembre si è registrata una ripresa significativa. Purtroppo, il comparto automobilistico soffre ancora per la carenza di materie prime e di componentistica elettronica. Ma, per fortuna, rappresenta praticamente l’unico settore industriale che, al momento, si trova alle prese con problemi di tale portata. In generale, invece, le materie plastiche stanno andando molto bene in varie applicazioni finali. Per esempio, per tutto ciò che riguarda il giardinaggio e il fai da te: pare, forse sempre a causa del lockdown, che le persone si siano impegnate a rinnovare l’arredamento delle proprie case e anche i mobili da esterni. Infine, il settore degli elettrodomestici bianchi è in grande espansione e stanno crescendo anche elettrico/elettronico e medicale”. Fondata nel 1991 e rinominata Wittmann Battenfeld Italia nel 2019 (fino ad allora si chiamava Battenfeld Italia), proprio nel maggio di quell’anno la filiale italiana aveva inaugurato la nuova sede di Ceriano Laghetto (Monza-Brianza), trasferendosi lì da Solaro (Milano). Oggi può contare su circa 30 dipendenti, su moderni uffici e su una più ampia showroom, in cui è possibile anche effettuare diverse tipologie di prove per i clienti.
Michael Wittmann e Gianmarco Braga fanno gli onori di casa alla festa per i trent’anni di Wittmann Battenfeld Italia
un diametro di circa 6 mm, uno spessore di 1,8 mm e un peso totale di soli 23 mg, il punto forte di questo componente è la membrana in silicone, pesante non più di 120 microgrammi e spessa soli 20 micrometri, che permette di rilevare con precisione le differenze di pressione pressoché impercettibili tra due fluidi diversi nella metrologia industriale, anche con temperature di esercizio fino a 150°C, o con fluidi difficili. Il silicone liquido veniva alimentato da cartucce da un litro, i flussi di materiale erano prelevati in microlitri dall’unità di dosaggio e la qualità del materiale misurato veniva registrata e trasmessa al sistema di controllo B8 della macchina tramite interfaccia OPC UA. L’unità di dosaggio Servomix X1 per LSR rientra nel pacchetto per la produzione di microcomponenti. Per questa applicazione è stata utilizzata una pressa multimateriale MicroPower 15/10H/10H Combimould, dotata di due gruppi di iniezione orizzontali e di una piattaforma girevole e predisposta per operazioni di stampaggio a iniezione in camera bianca. La piattaforma girevole era completamente incapsulata, mentre, analogamente alla macchina standard, anche i gruppi di iniezione del modello multimateriale MicroPower consistevano in unità con vite punzonante a due stadi, volume d’iniezione di 4 cm³ e canali di adduzione di lunghezza minima, per consentire la lavorazione di fusi termicamente omogenei e, di conseguenza, la produzione di parti di eccellente qualità.
AUSILIARI PER LO STAMPAGGIO
Nel campo dell’automazione, l’azienda austriaca ha proposto l’ultima versione del robot WX. Già disponibile sul mercato, il robot WX153 in versione aggiornata rappresenta la soluzione ideale per applicazioni di stampaggio a iniezione su macchine con forze di chiusura da 500 a 1300 tonnellate. Il sistema è costituito da una struttura cartesiana con asse X mobile per l’estrazione dallo stampo. Corsa orizzontale e verticale arrivano rispettivamente fino a 18 m e a 2600 mm. Per la rimozione degli articoli, la corsa dell’asse X può raggiungere i 1400 mm, che consente uno sbraccio (parametro essenziale per la configurazione spaziale dei sistemi robotici e qui inteso come distanza massima tra asse orizzontale e piastra di montaggio dell’asse girevole collocata all’estremità inferiore dell’asse verticale) di circa 1790 mm. Tre assi aggiuntivi possono essere montati all’estremità dell’asse verticale di ciascun robot per azionare la pinza di estrazione. Inoltre, Wittmann è anche in grado di realizzare robot in configurazione tandem, ossia due unità che operano insieme scorrendo sul medesimo asse. Varie ottimizzazioni consentono al robot WX153 di funzionare con una pinza di peso superiore a 20 kg anche quando si utilizzano i tre assi aggiuntivi. Rispetto al modello precedente, ciò equivale a un possibile aumento della portata di oltre il 30%. Per quanto riguarda invece il controllo di processo, nell’ottica dell’efficienza di funzionamento, l’impiego di stampi voluminosi e pesanti richiede una grande capacità di riscaldamento e, di conseguenza, un flusso elevato nei canali di raffreddamento. Il nuovo termoregolatore Tempro basic L120 rappresenta la soluzione ideale per tali compiti e il suo sviluppo è stato determinato dalle crescenti necessità di un riscaldamento rapido degli stampi di grandi dimensioni, garantendo allo stesso tempo le elevate prestazioni di raffreddamento richieste nella fase di processo successiva. Inoltre, poiché occorreva ottimizzare il tempo di ciclo, la funzione di raffreddamento di Tempro basic L120 ha assunto la forma di un sistema estremamente efficace per il raffreddamento diretto dell’acqua nello stampo. Numerose nuove applicazioni richiedono soluzioni molto speciali per la termoregolazione degli stampi. Per questo motivo la gamma di termoregolatori Tempro plus D è stata ora ampliata con l’aggiunta del nuovo modello Tempro plus D200, in grado di gestire temperature fino a 200°C. Con questo apparecchio, Wittmann ri-
Il microcomponente stampato a Fakuma: anello di supporto con membrana in silicone Il granulatore G-Max per impieghi a fianco delle presse

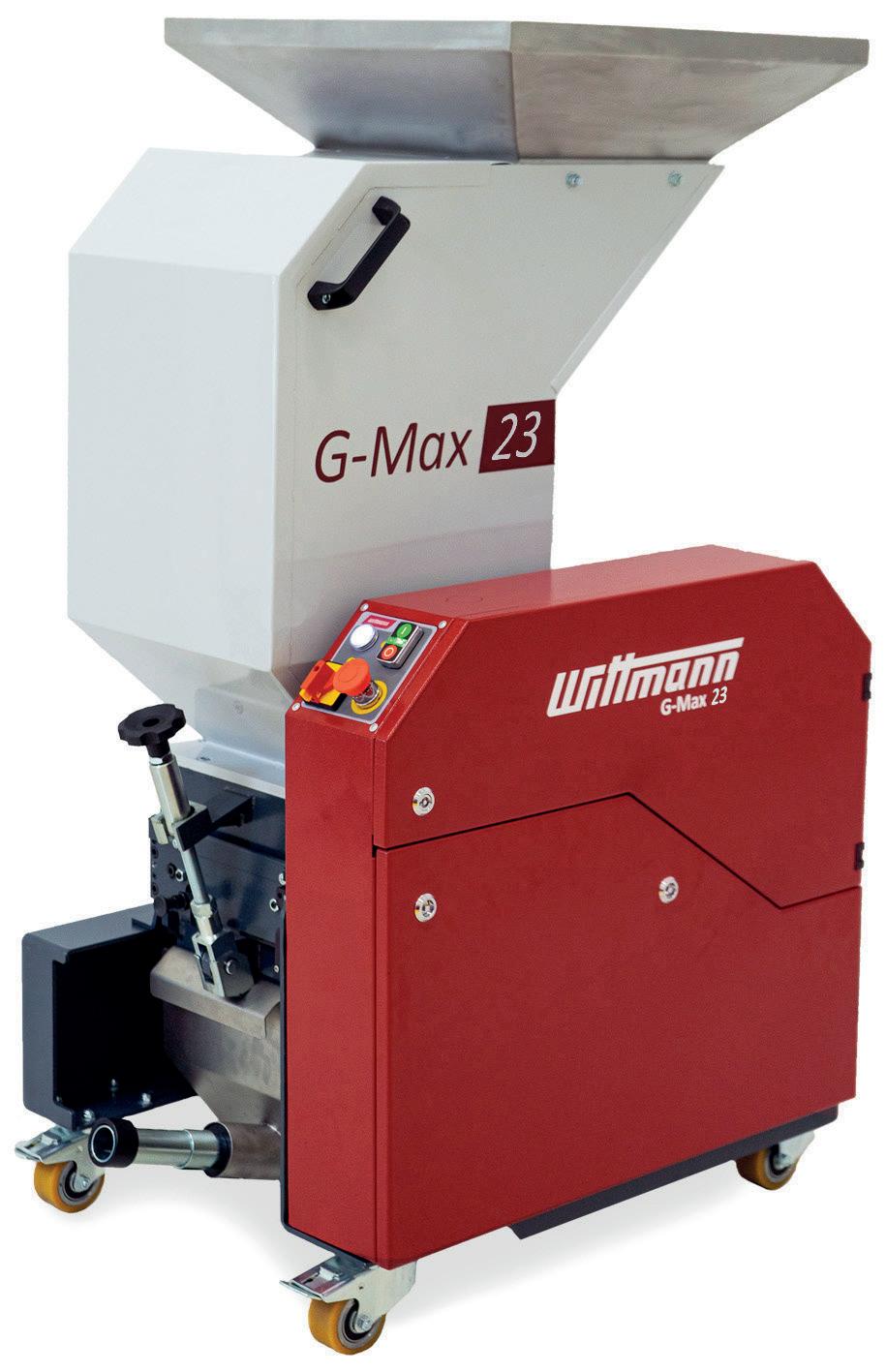
sponde alla tendenza generale del mercato verso temperature di processo più elevate. Le alte temperature dell’acqua - e le conseguenti alte pressioni - pongono requisiti particolarmente elevati in termini di resistenza all’usura degli stampi e dei componenti meccanici, un aspetto che è stato particolarmente considerato per lo sviluppo di Tempro plus D200. Infine, la serie G-Max di granulatori compatti per impieghi a fianco pressa è stata specificamente progettata per il riciclo a ciclo chiuso delle materozze generate da macchine con forza di chiusura fino a 500 tonnellate. Il suo design è stato standardizzato sulla base del modello G-Max 13 e, di conseguenza, i modelli G-Max 23 e G-Max 33 sono ora dotati di tramogge con aperture più grandi, che permettono di scegliere tra una versione fissa e una girevole per l’uscita del materiale. I vagli della serie G-Max sono disponibili in calibri diversi, garantendo la lavorazione in presenza di materiali e condizioni di produzione variabili. Il cambio di vaglio può essere effettuato senza attrezzi particolari e i tempi necessari per la manutenzione sono ridotti al minimo, mentre la tramoggia inclinabile semplifica la pulizia e la manutenzione dell’apparecchiatura.
PARTNERSHIP TRA BATTENFELD-CINCINNATI E MOLECOR

“FORNIAMO AI NOSTRI CLIENTI UNA SOLUZIONE “PLUG&PLAY” GIÀ PRONTA PER L’USO”. COSÌ GERNOT DORN, DIRETTORE VENDITE PVC DI BATTENFELD-CINCINNATI AUSTRIA, DESCRIVE LA PARTNERSHIP CON LA SOCIETÀ SPAGNOLA MOLECOR
Dalla sua fondazione nel 2006, la spagnola Molecor ha registrato una crescita sostenuta e oggi è conosciuta come una delle aziende più grandi e più esperte al mondo nella produzione di tubi in PVC-O, con impianti in Spagna, Malesia, Sud America e Sud Africa. Ma la società è anche costruttrice di impianti d’estrusione insieme a battenfeld-cincinnati, con cui offre linee complete personalizzate per la realizzazione di tubi, appunto. Le due aziende, grazie al vasto bagaglio di conoscenze che deriva dalla loro collaborazione, sono in grado di mettere a punto soluzioni tecnologiche con cui soddisfare al meglio la crescente domanda di tubi in PVC-O, che progressivamente stanno sostituendo quelli in metallo o poliolefine nel settore delle applicazioni in pressione. “Grazie al nostro patrimonio di esperienze, realizziamo tubi a pressione di alta qualità con un rapporto prezzo/prestazioni senza precedenti”, dichiara Dolores Herran, direttore dello sviluppo delle attività di Molecor. Il PVC è una materia prima ideale per la produzione di tubi, grazie alle sue proprietà e a un prezzo relativamente favorevole. Rispetto ai tubi in metallo, quelli in plastica si contraddistinguono per resistenza alla corrosione e facilità di posa, mentre rispetto ai tubi in PE, i tubi in PVC si fanno preferire per il prezzo del materiale, inferiore di circa il 15-20%.
PRODUZIONE IN DUE FASI
PVC-O è rappresentata dalle proprietà meccaniche, ottenute grazie a un metodo di produzione speciale che consente di avere una sezione libera più elevata e quindi una maggiore portata. Questo metodo di produzione si divide in due fasi: la produzione di una preforma di tubo a pareti spesse su di una linea per l’estrusione di tubi in PVC standard; il successivo riscaldamento della preforma e la realizzazione del tubo finale con orientamento del materiale in uno stampo speciale. Mentre la lunghezza del tubo rimane invariata, il diametro esterno viene quasi raddoppiato, con la contemporanea significativa riduzione dello spessore di parete. Durante la fase di orientamento, le molecole del polimero vengono appunto orientate in direzione circolare con-
ferendo al manufatto elevate proprietà meccaniche come alta resistenza agli urti, prevenzione della propagazione delle cricche e resistenza alla fatica. Rispetto ai tradizionali tubi in PVC-U, quelli in PVC-O presentano spessori di parete più sottili fino al 50% per la stessa classe di pressione. La leggerezza che ne deriva facilita enormemente la movimentazione in cantiere. Ciò vale anche nei confronti dei tubi in metallo e in materiale poliolefinico. E sono proprio tutti questi vantaggi che determinano la crescita della domanda globale dei tubi in PVC-O in tutti i settori della gestione delle acque.

ESTRUSORI BIVITE PARALLELI

Nel suo stabilimento principale a Loeches, Molecor opera attualmente con sette linee di estrusione fornite da battenfeld-cincinnati per produrre tubi in PVC-O con diametro esterno da 90 a 1200 mm. Tutte queste linee sono dotate di estrusori bivite paralleli ad alte prestazioni della serie twinEX, filiere “spider” con circuito di raffreddamento interno e tutti i necessari componenti a valle, come bagno sottovuoto, traino e taglierina a sega. Molecor non fabbrica solo le proprie linee di produzione, ma anche i componenti per la seconda fase del processo, che comprendono: una stazione di riscaldamento, una stazione di soffiaggio e un’unità di raffreddamento. “Naturalmente, ci avvaliamo della nostra esperienza come produttori di tubi per assicurare l’ottimizzazione continua della nostra tecnologia”, commenta Herran, evidenziando una caratteristica che fornisce ulteriore valore aggiunto per i clienti. Finora battenfeld-cincinnati e Molecor hanno installato congiuntamente oltre 15 linee per la produzione di tubi in PVC-O in tutto il mondo, presso trasformatori in paesi come India, Kazakistan, Malesia e Australia. “Il nostro successo dimostra che abbiamo visto giusto: le linee di estrusione complete perfettamente coordinate e combinate con la tecnologia Molecor offrono ai produttori di tubi un chiaro vantaggio competitivo”, conclude Gernot Dorn.
Un particolare - la testa di estrusione con un tubo di ampio diametro in uscita - delle linee di estrusione in funzione presso lo stabilimento spagnolo di Molecor, tutte basate su estrusori bivite paralleli ad alte prestazioni della serie twinEX
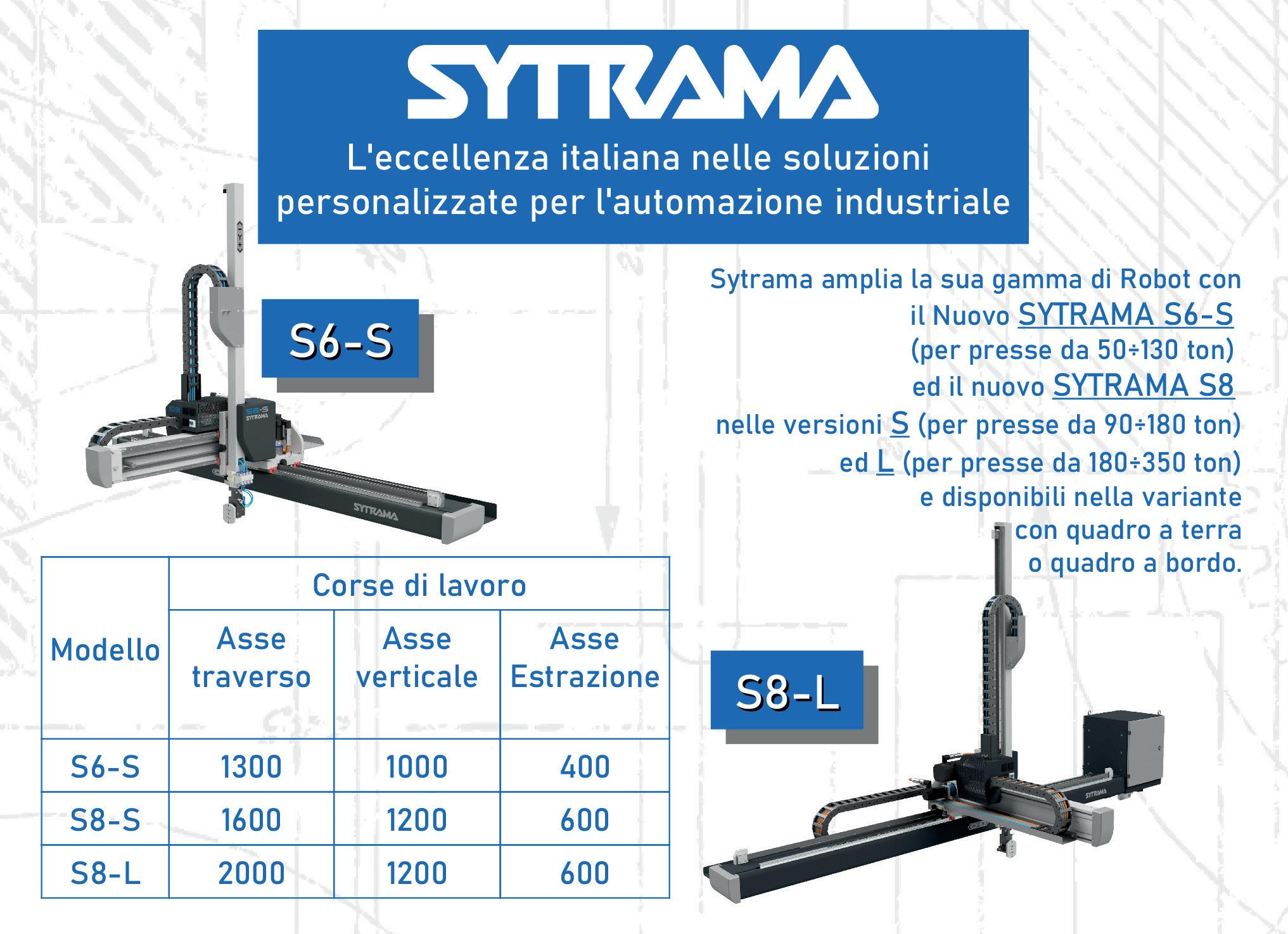
NEWS
Tecnologia ReFresher di Erema Odori sotto controllo nel riciclo post consumo
La crescente domanda di rigranulati di alta qualità da riciclo post consumo per un’ampia gamma di applicazioni ha fatto registrare a Erema un incremento delle richieste di sue linee per il riciclo equipaggiate con la tecnologia ReFresher, per la riduzione degli odori sgradevoli a valle del processo di estrusione. L’HDPE riciclato con sistema Intarema TVEplus RegrindPro e tecnologia ReFresher integrati può essere utilizzato fino al 100% per produrre imballaggi adatti al contatto diretto con alimenti e bevande, come confermato dalla statunitense FDA. Questo nuovo sviluppo ha preso le mosse da due fattori principali: gli ambiziosi obiettivi in materia di riciclo fissati dall'Unione Europea, secondo cui entro il 2025 il 50% dei rifiuti di imballaggi in plastica dovrà essere riciclato; il fatto che le tecnologie di riciclo diventano sempre più efficienti. "Entrambi questi fattori hanno reso possibili applicazioni dei rigranulati postconsumo inimmaginabili solo alcuni anni fa, una tendenza destinata a continuare anche in futuro. Questo perché gli obiettivi di riciclo fissati dall'UE presuppongono che ogni anno si dovranno riutilizzare nella fabbricazione di nuovi prodotti 10 milioni di tonnellate di materiali di riciclo", afferma Clemens Kitzberger, direttore dello sviluppo di Erema per le applicazioni post consumo. Un flacone per gel doccia realizzato al 100% in HDPE riciclato, lanciato nella primavera del 2019, rappresenta un valido esempio di prodotto di fascia alta per il comparto cosmetico realizzato con materiale da riciclo post consumo. Il rigranulato per questa applicazione è ottenuto appunto con una macchina Intarema TVEplus RegrindPro equipaggiata con modulo ReFresher. Nell'agosto del 2019 questo processo di riciclo estremamente pulito ha ottenuto la certificazione FDA per la produzione di bottiglie per latte e succhi di frutta, nonché di vassoi per carni, stoviglie e posate usa e getta, a condizione che il materiale in ingresso provenga da bottiglie del latte e succhi di frutta. Nel novembre del 2020, sempre la FDA ha confermato la disponibilità di un flusso aggiuntivo in ingresso per il materiale trattato con questo processo. Oltre ai contenitori per bevande in HDPE, è possibile processare anche le chiusure in HDPE di bottiglie per bevande in HDPE, PP e PET. Il materiale riciclato può essere utilizzato fino al 100% nella produzione di contenitori adatti al contatto diretto con alimenti di ogni tipo. "Per produrre un rigranulato di così alta qualità da materiale riciclato post consumo, la macchina di riciclo deve fornire prestazioni di decontaminazione molto elevate", spiega Thomas Hofstätter, ingegnere di processo di Erema. "Mentre il sistema di estrusione a elevata capacità di degassaggio rimuove principalmente sostanze altamente volatili e a basso peso molecolare, ReFresher garantisce una significativa riduzione, nel rigranulato, dei composti organici a bassa volatilità e ad alto peso molecolare. Allo stesso tempo, il processo termo-fisico opera in modo tale da consentire un significativo risparmio energetico, dal momento che sfrutta l'energia termica dei granuli ancora caldi dopo il processo di estrusione". "Oltre ai collaudati sviluppi di Erema, la combinazione di estrusore e ReFresher ha rappresentato un fattore chiave per ottenere l'approvazione della FDA. Questo processo super pulito produce rigranulato di alta qualità per aprire nuovi mercati economicamente sostenibili, che potranno essere sviluppati collaborando con i partner lungo l’intera filiera", conferma Michael Heitzinger, amministratore delegato di Erema.
Nel Customer Center di Erema, a partire dallo scorso aprile è possibile eseguire test utilizzando una combinazione estrusore-ReFresher in versione industriale
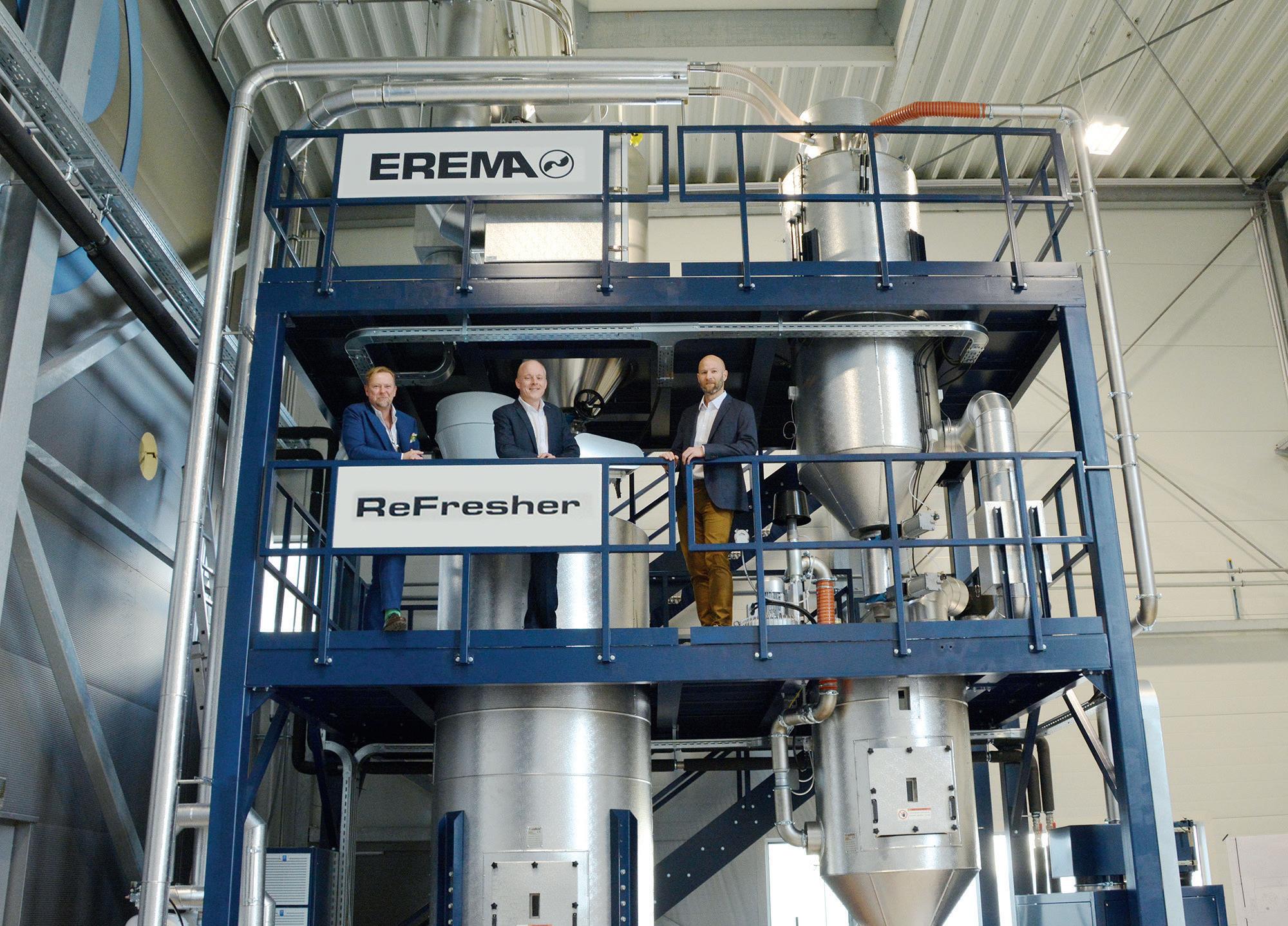
NEWS
EdelweissCompounding di KraussMaffei Tecnologia di estrusione per il riciclo termico-meccanico
Nella lavorazione meccanica di rifiuti plastici, la struttura chimica del materiale rimane inalterata. Il ciclo di recupero prevede che i manufatti plastici post consumo siano frantumati, lavati, selezionati in base al tipo di materiale e riprocessati. Come spiega Franz-Xaver Keilbach di KraussMaffei, la tecnologia EdelweissCompounding, proposta dal costruttore tedesco per questo processo, si basa su due estrusori in configurazione a cascata. Nella prima stazione, un estrusore bivite viene alimentato con scarti plastici e li prepara in maniera tale da consentire il passaggio del fuso degassato attraverso un filtro con maglie di dimensioni tra 100 e 300 micrometri, a seconda delle specifiche tecniche del prodotto da ottenere. In base all’uso previsto per il materiale finale da produrre, viene installato un sistema di granulazione a valle dell’estrusore ZE o, in alternativa, il fuso pulito viene convogliato direttamente alla seconda stazione: un estrusore di compoundazione impiegato per il ricondizionamento controllato del materiale mediante l’aggiunta di cariche, additivi, stabilizzanti e coloranti. Per la lavorazione di granulati con una densità apparente inferiore a 0,25 kg / litro, la tecnologia EdelweissCompounding può essere integrata con una stazione di compressione a monte. Più il materiale in ingresso è “soffice”, più è importante ricorrere a una taglierina compattatrice per riscaldare, essiccare e agglomerare gli scarti di foglie e film, al fine di agevolarne la successiva lavorazione nell’estrusore bivite. “Il processo con solventi rappresenta un’alternativa interessante, in particolare, per il riciclo di materiali compositi che non possono essere separati meccanicamente. I solventi vengono utilizzati per separare i polimeri da compositi o compound plastici. Tuttavia, occorre poi rimuovere il solvente”, sottolinea Keilbach. In questo caso, entra in azione l’estrusore bivite ZE BluePower. La rotazione delle viti assicura un ricambio ampio e costante della superficie del fuso, consentendo una più agevole espulsione del materiale volatile intrappolato al suo interno. I solventi vengono rimossi attraverso una serie di aperture nell’estrusore, collegate a un dispositivo di aspirazione. I solventi sono rimossi gradualmente, a diversi livelli di pressione, e poi vengono fatti evaporare e condensati per poterli riutilizzare. Anche in questo caso, le caratteristiche del processo vengono determinate in modo mirato,

Tecnologia EdelweissCompounding di KraussMaffei: soluzione in cascata per la lavorazione e il compounding in un unico ciclo di scarti plastici selezionati
in base alle proprietà richieste al polimero da produrre. Per ridurre dal 30% iniziale al 2% la concentrazione del solvente nel materiale, per esempio, è sufficiente un estrusore bivite. Se invece è necessario ottenere livelli di purezza nell’ordine di pochi ppm, è consigliabile predisporre due stazioni configurate a cascata. Per l’implementazione di questa particolare configurazione, KraussMaffei combina un estrusore monovite e uno bivite. A prescindere dalla lavorazione subita dal materiale, termico-meccanica o con solventi, il risultato consiste sempre in un fuso perfettamente pulito, che può essere rigranulato in un polimero standard od ottimizzato in un’ulteriore fase di compoundazione. Uno dei vantaggi offerti dalla serie di estrusori ZE BluePower è rappresentato dai bassi consumi energetici. I costi operativi risultano sensibilmente ridotti grazie alle numerose innovazioni introdotte sul fronte dell’efficienza energetica e delle funzionalità di processo, quali organi di trasmissione con punto operativo ottimizzato, motori a corrente alternata trifase raffreddati ad acqua e riduttori ad altissima efficienza. La gamma modulare di sezioni di cilindro, con L/D da 4 e 6, e l’ampia varietà di elementi vite garantiscono un’alta flessibilità nella progettazione degli estrusori bivite ZE BluePower, personalizzabili per applicazioni specifiche. La combinazione di ampio volume libero nella sezione di processo ed elevata densità di coppia offre condizioni ottimali per processi di riciclo e compoundazione altamente economici.
Biffa sceglie ancora Amut Bis per il riciclo nel Regno Unito
Un rendering dell’impianto Amut per Biffa
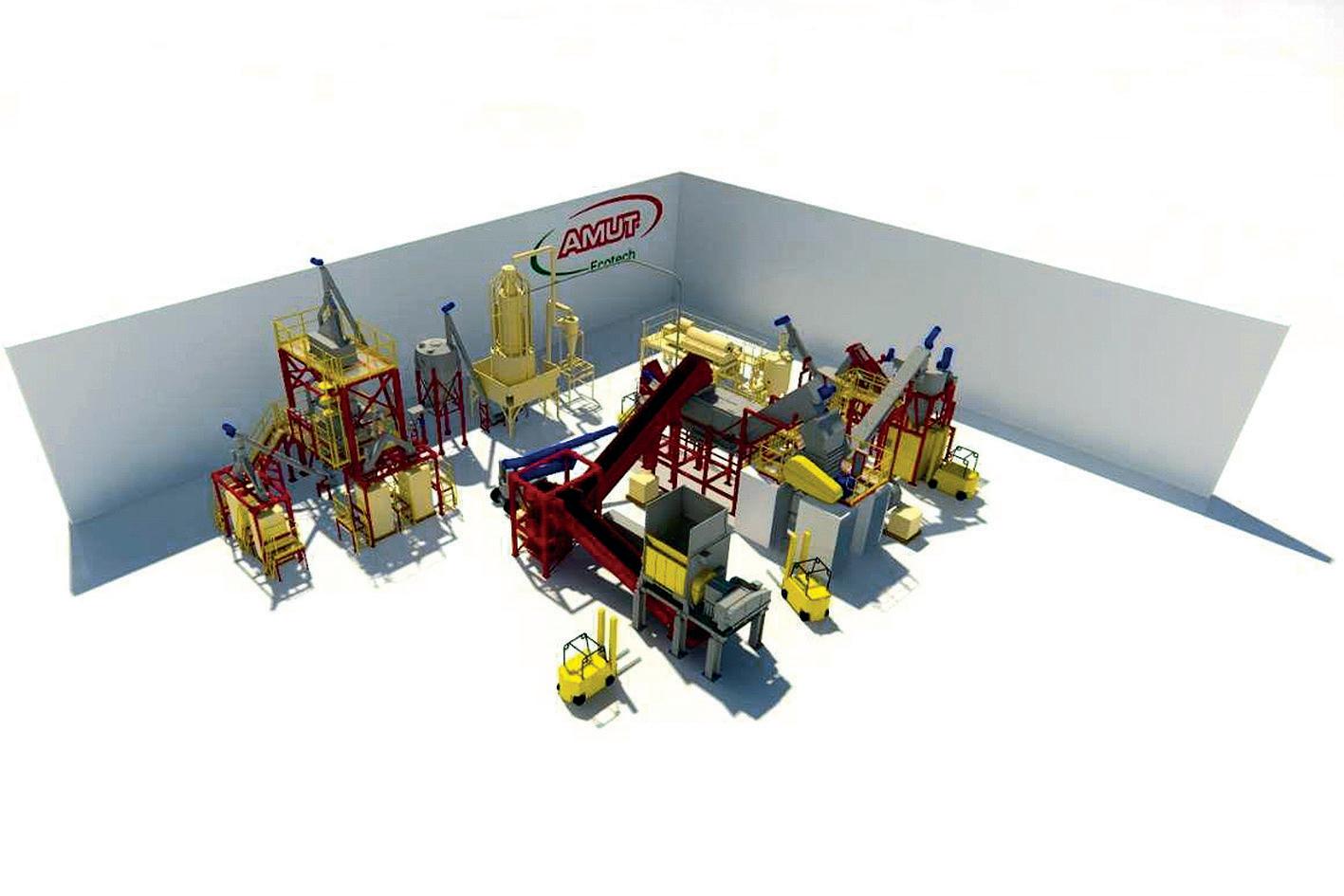
INNOVATION IN EXCELLENCE
Dopo l’impianto per il riciclo realizzato da Amut per Biffa a Seaham, nel Regno Unito, uno dei più moderni e tecnicamente avanzati al mondo, le due società sono recentemente tornate a collaborare per un altro impianto di Biffa a Washington, sempre nel Regno Unito. Nella prima collaborazione Amut aveva fornito alla società britannica, specializzata nella gestione e nel trattamento di materiali di scarto, un impianto integrato per la selezione e il lavaggio di balle di bottiglie in PET, da cui ottenere scaglie di elevata purezza. Tale impianto aveva una capacità di 4000 kg all’ora e comprendeva un sistema Mini-PRF (Plastic Recycling Facility) in grado di riciclare fino a 1,3 miliardi di bottiglie all’anno. Dopo la prima installazione, Biffa si è affidata nuovamente al costruttore novarese per un progetto di espansione della propria capacità e riciclare così annualmente fino a 1,6 miliardi di bottiglie post consumo in HDPE per latte. Amut ha dunque fornito un impianto con una capacità di 2000 kg all’ora. “Biffa è impegnata a favorire l’economia circolare nel Regno Unito e l’aumento del riciclo della plastica costituisce una parte fondamentale della nostra strategia; entro il 2030 speriamo di quadruplicare la nostra capacità attuale di riciclo della plastica. Dopo una partnership di successo con Amut nel nostro impianto all’avanguardia di Seaham, siamo lieti di lavorare di nuovo con loro nel nostro impianto di Washington, dove stiamo aggiungendo altre 14 mila tonnellate di capacità per riciclare HDPE”, ha dichiarato Martin Brass di Biffa, in occasione della nuova fornitura. Quella tra Amut e Biffa rappresenta una “cooperazione green” determinante per ridurre l’inquinamento da plastica nel Regno Unito, incrementando la capacità nel paese di riciclare attraverso sistemi ecocompatibili, si tratta, quindi, di un passo importante verso la salvaguardia dell’ambiente.

NEWS
Dettaglio della linea di Icma San Giorgio individuata tra le 1000 soluzioni in grado di rispondere concretamente e profittevolmente alla sfida della sostenibilità ambientale
Il riciclo avanzato targato Icma Una risposta concreta e profittevole alla transizione ecologica
Il costruttore milanese Icma San Giorgio ha recentemente contribuito al raggiungimento di un importante risultato da parte di Solar Impulse Foundation. Già promotrice della World Alliance for Efficient Solutions, questa fondazione, dopo un attento processo di selezione durato più di quattro anni, ha infatti individuato le prime 1000 soluzioni che offrono una risposta concreta e profittevole alla grande sfida della sostenibilità ambientale. Il contributo dell’azienda di San Giorgio su Legnano (Milano) è passato attraverso la linea Ecosheet per il recompounding destinata al riciclo avanzato, che, grazie a estrusori bivite corotanti ad alta coppia, frutto di uno sviluppo pluriennale nel campo del riciclo di materie plastiche, consente di trattare e mescolare plastiche miste di scarto per ottenere un materiale da riutilizzare per realizzare prodotti tecnici altamente funzionalizzati. L’inclusione di questa soluzione impiantistica nel selezionato gruppo identificato da Solar Impulse Foundation è avvenuta con il conferimento del suo esclusivo marchio, di cui oggi Icma San Giorgio può fregiarsi. La linea Ecosheet è stata sviluppata dal team tecnico di Icma San Giorgio in oltre tre anni di intenso lavoro e ha conquistato l’attenzione anche della Commissione Europea, con il conferimento del Seal of Excellence e la premiazione del progetto nell’ambito del programma Horizon 2020 fase 2. “Siamo molto contenti del contributo dato a Solar Impulse per questo importante risultato, che arriva dopo un grande sforzo di sviluppo e che conferma il nostro impegno concreto e ultratrentennale per la transizione ecologica. La linea Ecosheet combina benissimo almeno tre elementi che ci distinguono: la nostra naturale predisposizione all’innovazione, i nostri estrusori corotanti dedicati al riciclo più avanzato, ricchi di sistemi tecnici d’avanguardia per questo settore d’impiego, e, infine, le capacità ingegneristiche uniche di Icma per progetti complessi chiavi in mano. Siamo protagonisti nelle sfide poste dal nuovo paradigma dell’economia circolare; questa è una certezza”, ha dichiarato per l’occasione Giorgio Colombo, CEO di Icma.
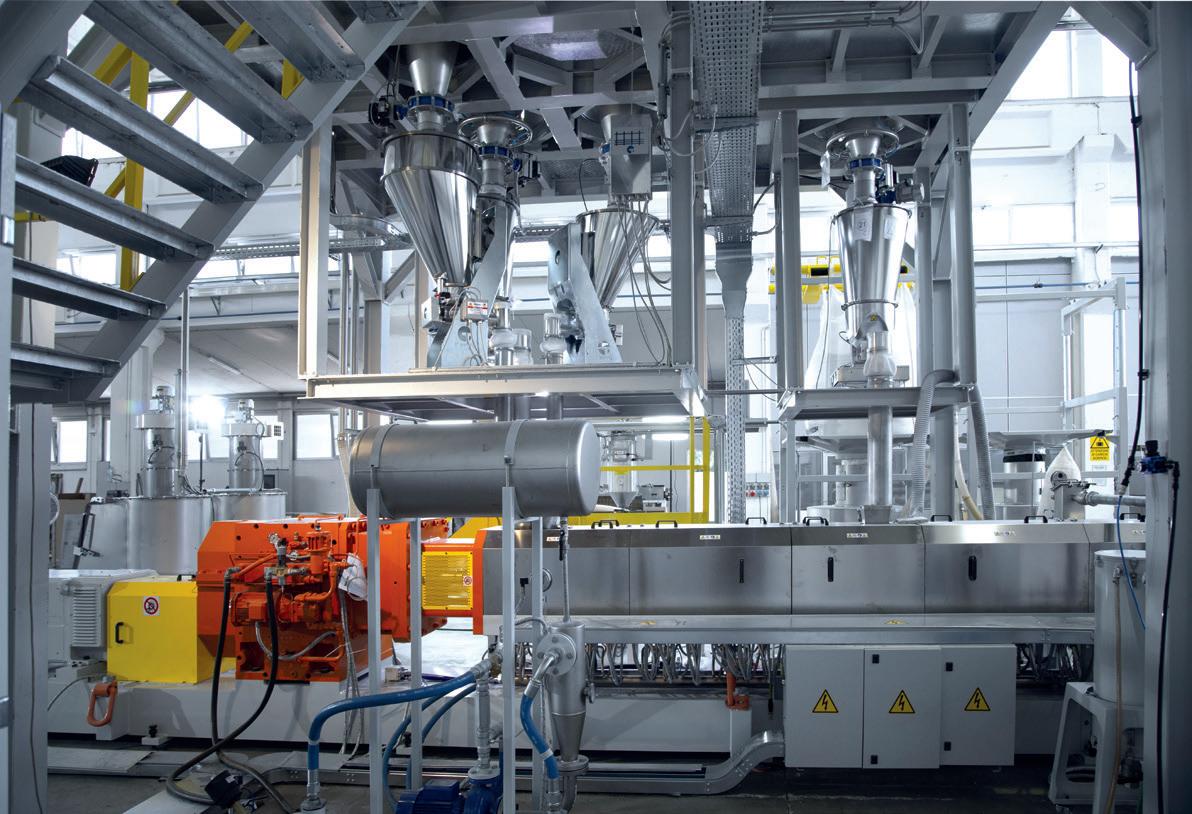

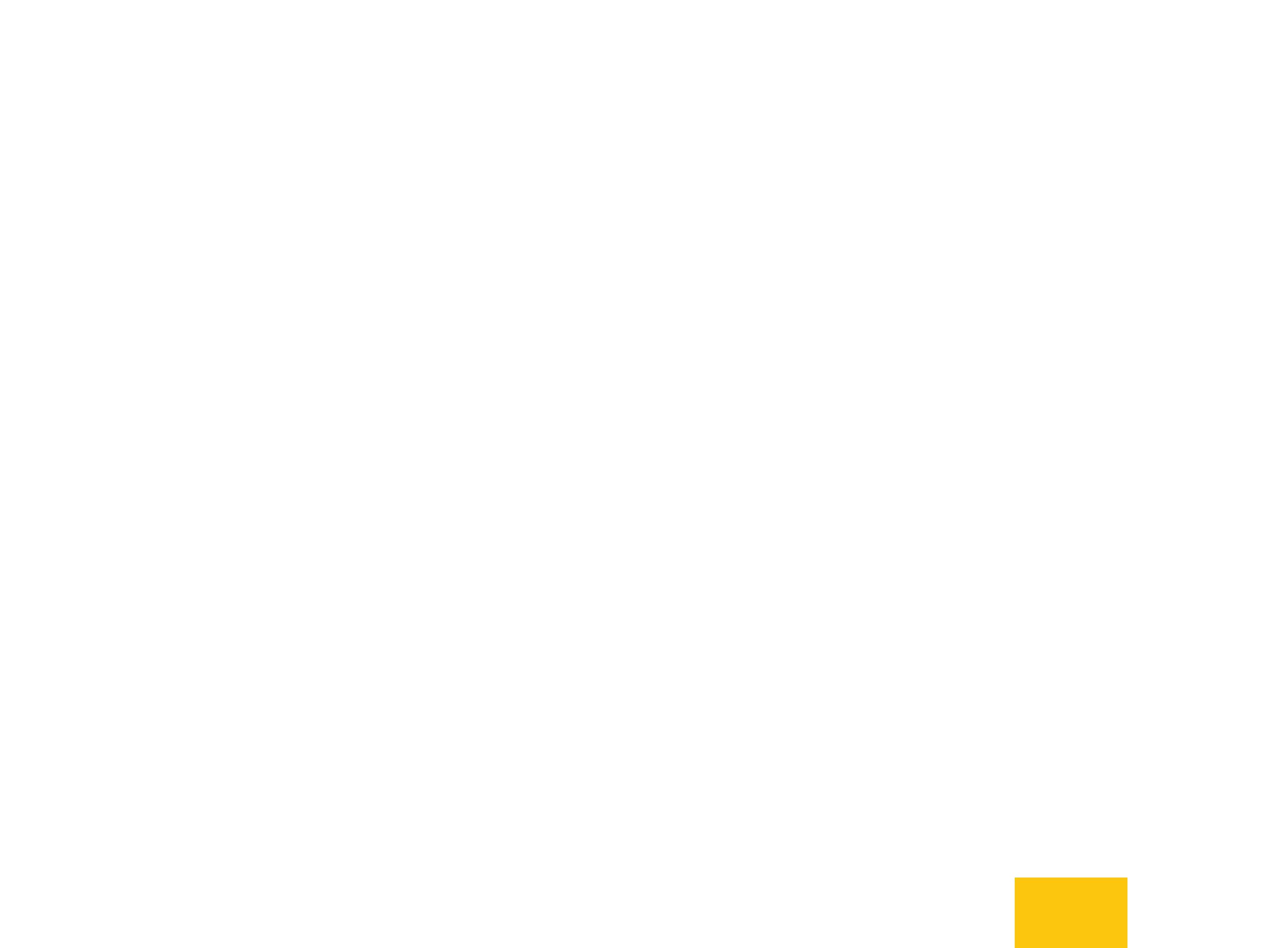
BiReC di Binova Riciclo “due in uno”
La tecnologia BiReC, messa a punto da Binova per trattare teli poliolefinici post consumo provenienti da linee di lavaggio e macinati, consente di eseguire in un’unica fase di processo sia il riciclo che la compoundazione, che normalmente vengono effettuati in due passaggi separati, ottenendo granuli in grado di garantire prodotti finali di elevata qualità. Indipendentemente dall’origine, grazie alla doppia filtrazione automatica, l’utilizzatore finale è in grado di produrre film con spessori fino a circa 20 micron. La linea è dotata di un estrusore bivite corotante con capacità da 1400 a 1800 kg/ora, a seconda del materiale in ingresso. L’impianto è in grado di eseguire la compoundazione di rifiuti industriali con elevata umidità residua (fino all’8%). La presenza di un sistema di degassaggio ad alto vuoto, distribuito lungo quasi l’intera lunghezza del cilindro (tre condotti di degassaggio sotto vuoto e uno di scarico a pressione atmosferica) permette la granulazione di film stampati fino all’80% della superficie. La mescolazione direttamente in macchina porta a ottenere un materiale omogeneo, a tutto vantaggio della qualità del prodotto finale. L’impianto può essere dotato di sistema di dosaggio sia gravimetrico sia volumetrico. Inoltre, Binova ha sviluppato e brevettato un nuovo dispositivo di controllo gravimetrico per film macinato con densità apparente di circa 0,05 kg/dm3, che assicura l’esatta quantità di macinato con cui alimentare l’estrusore. Questo sistema di riciclo “due in uno”, oltre alla ridotta gestione dei materiali all’interno della fabbrica, si contraddistingue per i ridotti consumi energetici, che con i materiali a base di LDPE non superano 0,26-0,27 kW/kg e con quelli a base di PP, PS o HIPS si attestano a circa 0,22-0,23 kW/kg (escluso il raffreddamento dell’acqua di processo). Rispetto ai sistemi monovite, il risparmio di energia si aggira intorno al 30%.
Veduta di una linea completa di Binova

PER IL RITORNO IN PRESENZA ALLA FIERA DI FRIEDRICHSHAFEN, L’AZIENDA DI MASSANZAGO HA PRESENTATO UNA GAMMA “A RANGHI COMPATTI” DI SOLUZIONI PER GESTIRE L’AUTOMAZIONE DEL PROCESSO DI TRASFORMAZIONE DELLE MATERIE PLASTICHE SECONDO I DETTAMI DELLA MANIFATTURA MODERNA: FABBRICA INTELLIGENTE E RICICLO
MORETTO A FAKUMA 2021

UN RITORNO NEL SEGNO DI CONNETTIVITÀ ED ECONOMIA CIRCOLARE
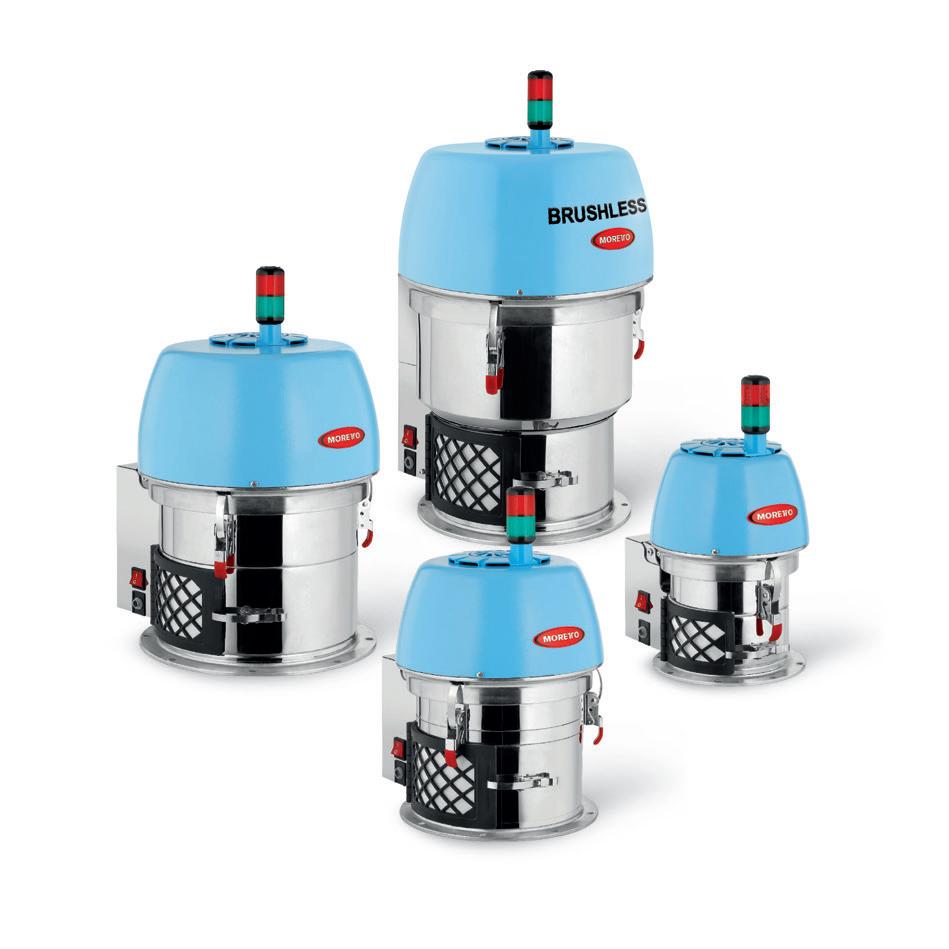
Alcuni esemplari della serie Compact I l ritorno a Fakuma da parte di Moretto è avvenuto attraverso le soluzioni sviluppate per la fabbrica intelligente, in linea con il tema della ventisettesima edizione della fiera di Friedrichshafen (Germania): “Il digitale incontra l’economia circolare”, e la gamma di prodotti dedicati al riciclo, settore in costante crescita che richiede sistemi particolarmente sofisticati anche per la lavorazione di materiali plastici già sottoposti a un precedente utilizzo e che devono essere reintrodotti nella filiera produttiva. Attualmente, la quasi totalità delle soluzioni dell’azienda di Massanzago (Padova) è in linea con le esigenze di una produzione intelligente, in cui i sistemi siano automatici, interconnessi e in grado di offrire elevate prestazioni. Oltre ai prodotti realizzati in ottica 4.0, sulle rive del Lago di Costanza è stata presentata infatti la piattaforma software Mowis, modulare, autoconfigurabile e utilizzabile in sito o da remoto, che tramite il protocollo di comunicazione OPC UA consente una connettività totale e permette di ge-
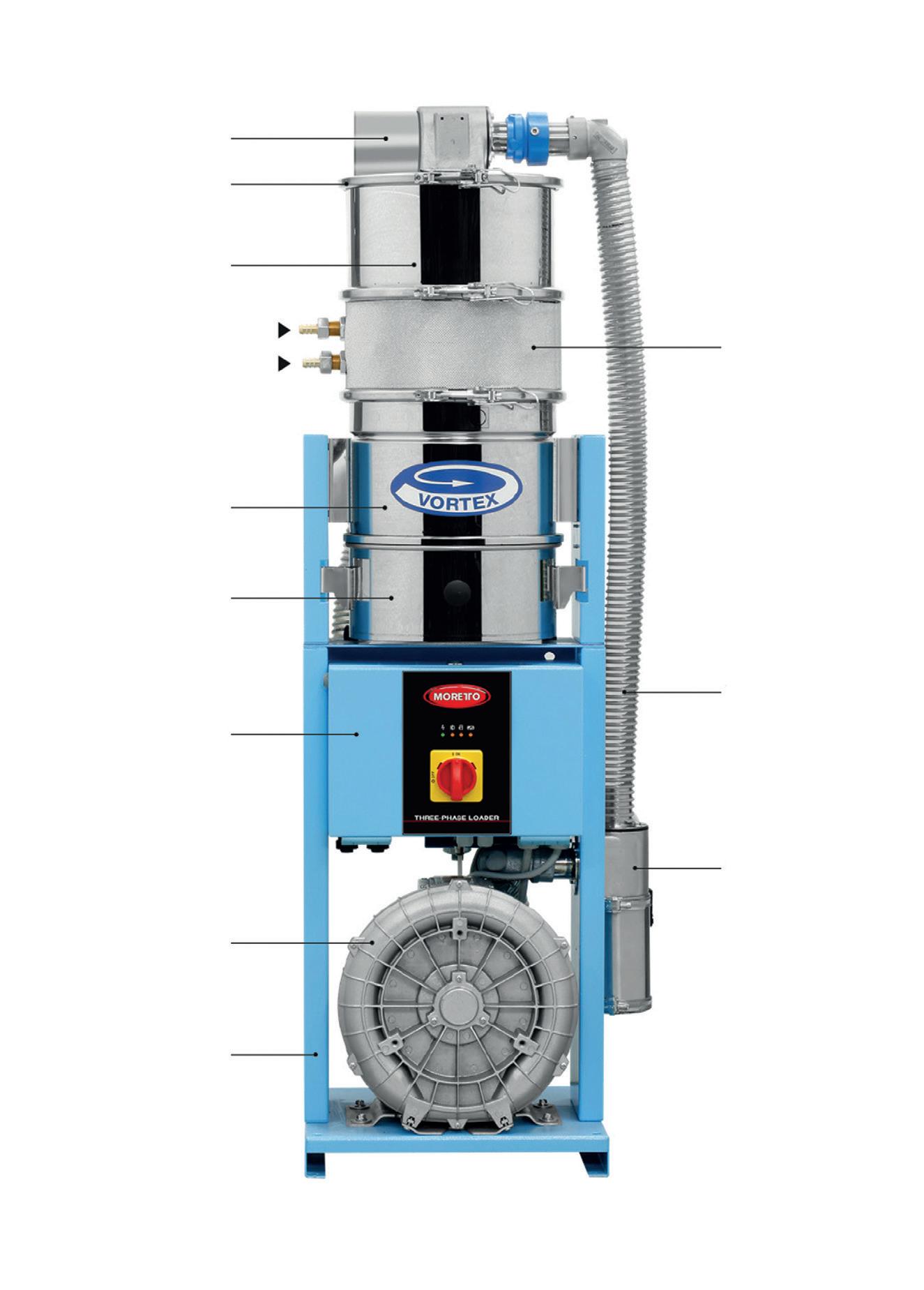
stire sistemi molto complessi in maniera facile e ottimizzata.
ALIMENTAZIONE PIÙ COMPATTA E PERFORMANTE
Ottimizzare gli spazi produttivi utilizzando soluzioni compatte che assicurino impianti lean è un’esigenza ormai ricorrente, che Moretto soddisfa con un restyling della gamma dedicata all’alimentazione. La nuova linea Compact di alimentatori, contenitori e ricevitori ad alto rendimento, con dimensioni in media inferiori del 30%, è adatta anche all’impiego in settori critici, grazie alla struttura in acciaio inossidabile contro le contaminazioni. La serie introduce la grandezza “zero”, con capacità di 0,5 dm3 e produttività di 30 kg all’ora, per trasporto di master e microalimentazione, ed è disponibile anche in versione monofase e con ricevitore per One Wire. La gamma monofase è stata ampliata con i modelli brushless nelle taglie F12 e F24. Come tutta la linea Compact, anche questa versione si caratterizza per bassa rumorosità (inferiore a 73 dB), avviamento dolce, filtro autopulente e apertura assistita con dispositivo di sicurezza. Gli alimentatori Venturi sono dedicati al trasporto di piccole quantità di materiale plastico, masterbatch e/o additivi e, grazie a sei nuove versioni, il loro campo di applicazione si estende anche a dosatori volumetrici, miniessiccatori, dosatori a perdita di peso e piccole presse a iniezione. I nuovi dispositivi di sgancio rapido, realizzati per contenitori, ricevitori e tramogge di mantenimento, permettono di svincolare in modo rapido e sicuro le apparecchiature per gli interventi di pulizia e manutenzione. Questi meccanismi in materiale anticorrosivo sono disponibili con base quadrata o rotonda. A Fakuma è stata esposta una nuova gamma di unità aspiranti trifase caratterizzate da ingombro ridotto e nuovi filtri Vortex. Queste unità sono modulari e componibili con accessori diversi a seconda dell’applicazione: il filtro Vortex separa le polveri grazie a un’azione centrifuga che protegge e aumenta l’efficienza del sistema; la valvola di bypass accelera i tempi di caricamento ed elimina i ripetuti on/off, preservando la soffiante; la valvola Duo può servire due utenze dalla stessa unità aspirante; l’implementazione di un anello di raffreddamento integrato consente il trasporto di materiale caldo fino a 180°C. In esposizione a Fakuma anche la serie completa di tubi flessibili in poliuretano, disponibili in sei versioni, per il trasporto di granuli, che, grazie ai diversi diametri disponibili, consentono di ottenere fino a 60 configurazioni diverse. Contraddistinti da elevata resistenza sono particolarmente indicati per il trasporto di materiali rinforzati con cariche minerali o fibre di vetro. Prodotto Contrex, azienda del gruppo Moretto specializzata in sistemi a perdita di peso, Counter è invece il dispositivo in grado di pesare con estrema precisione il materiale che passa dal contenitore/ricevitore alla tramoggia, fornendo dati reali sul consumo della macchina di processo. Sempre in ambito di alimentazione, in fiera era presente anche KruiseKontrol, brevetto ormai parte dei prodotti di punta sviluppati da Moretto per il trasporto dei materiali. Sistema automatico e intelligente, capace di definire le migliori condizioni di trasporto per ogni materiale plastico, KruiseKontrol gestisce in automatico la velocità del materiale durante il trasporto, eliminando i picchi iniziali e finali e i problemi tipici di questo processo, quali polvere, usura, formazione di capelli d’angelo e stress del materiale. L’integrazione con il sistema One Wire 3 consente ottenere un trasporto su misura semplicemente selezionando tipo di materiale da trattare e di macchina di processo, favorendo efficienza e produttività dell’impianto.
VALVOLA DI PULIZIA DEL FILTRO
CERNIERA DI APERTURA
FILTRO
INGRESSO
USCITA
CONO VORTEX
ASPIRATORE POLVERE
BOX ELETTRICO
UNITÀ DI ASPIRAZIONE
STRUTTURA MODULARE DEUMIDIFICAZIONE EFFICIENTE PER PICCOLE E GRANDI PRODUZIONI
Alla fiera Fakuma è stato poi presentato il restyling della serie manuale di mini dryer Dry Air, aggiornata con l’implementazione di tramoggia OTX e touchscreen semplificato. Si tratta di un modello con circuito a doppia torre e regolazione manuale dell’aria di processo, disponibile in sei grandezze, di cui in fiera sono state proposte la più piccola (D0 TX) e la più grande (D5 TX). Non è mancato X Comb, il mini dryer super compatto sviluppato per lotti ridotti di produzioni con polimeri tecnici. Totalmente elettrico, è dotato di potenti turbocompressori a portata variabile, setacci mole-
ANELLO DI RAFFREDDAMENTO
CONDOTTA DEL VUOTO
VALVOLA DI BYPASS
Layout della nuova unità aspirante trifase, contraddistinta da ingombro ridotto e nuovi filtri Vortex
colari, equalizzatore del punto di rugiada (dew point) con rendimenti fino a -52°C e tramoggia OTX. Compattezza e facilità di utilizzo hanno guidato invece la realizzazione del nuovo Trolley CRX, carrello disponibile in tre configurazioni. La versione standard comprende dryer e tramoggia con alimentazione elettrica One Power e gestione da touchscreen da sette pollici. Il dispositivo può essere integrato con unità aspirante VS DUO e misuratore di umidità Moisture Meter.
CONTENUTO TECNOLOGICO NEL DOSAGGIO

Per quanto riguarda il dosaggio gravimetrico, il dispositivo DGM Gravix, in esposizione a Fakuma, consente di configurare fino a otto componenti ed è dotato di un meccanismo di scarico a doppia palpebra con un tempo di reazione di 25 millisecondi. L’algoritmo di pesatura restituisce rilevazioni estremamente precise grazie al dispositivo Vibration Immunity System, che permette l’installazione del dosatore direttamente sopra la macchina di processo. Le tramogge sono amovibili, intercambiabili e disponibili in dieci versioni, mentre la connettività (Modbus, Ethernet, USB) permette la tracciabilità completa dei consumi e la certificazione della composizione delle ricette. L’integrazione con il software Mowis consente di monitorare ogni aspetto della produzione.
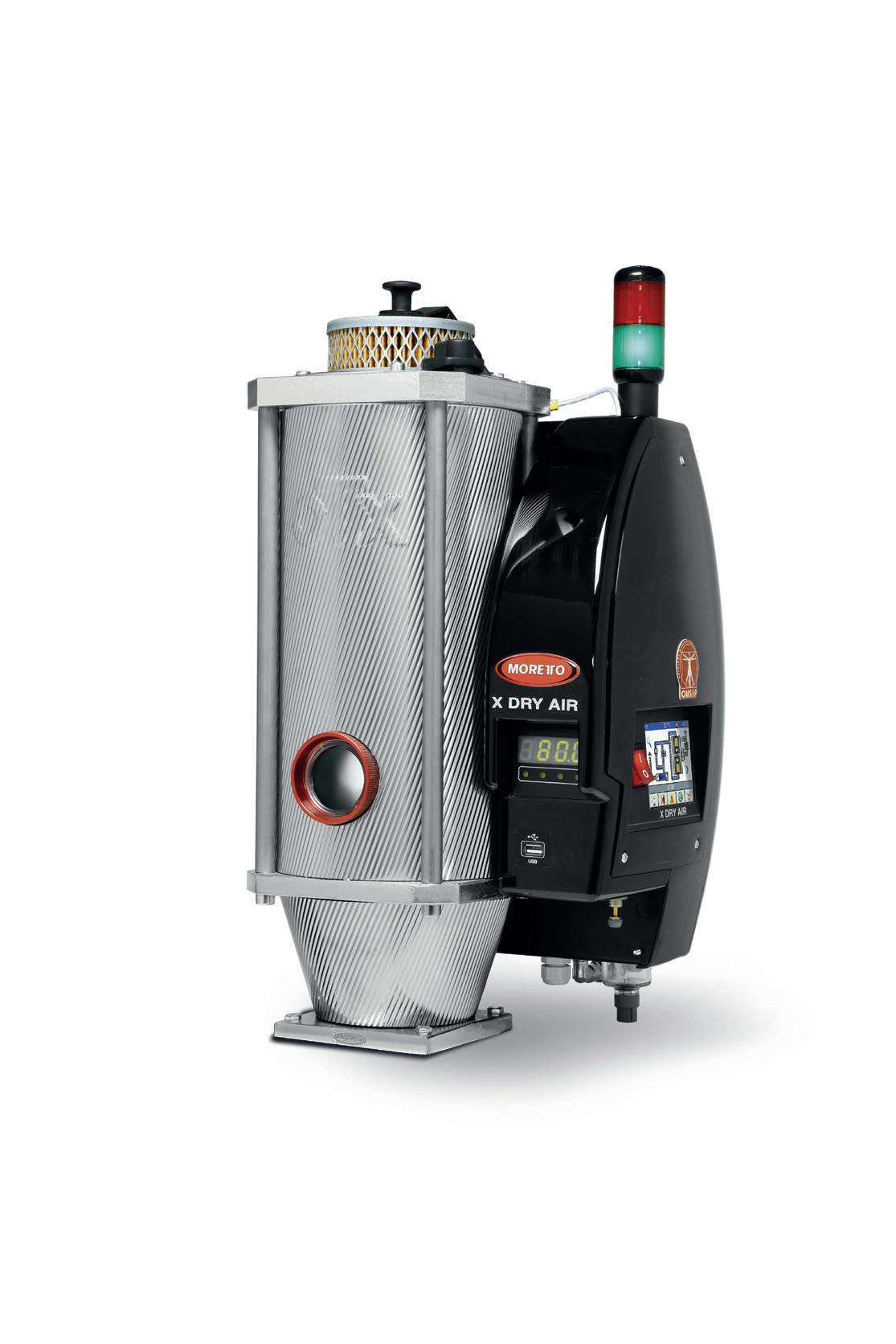
La versione del trolley CRX, con dryer e tramoggia con alimentazione elettrica One Power e touchscreen da sette pollici ANALISI DEL POLIMERO IN TEMPO REALE
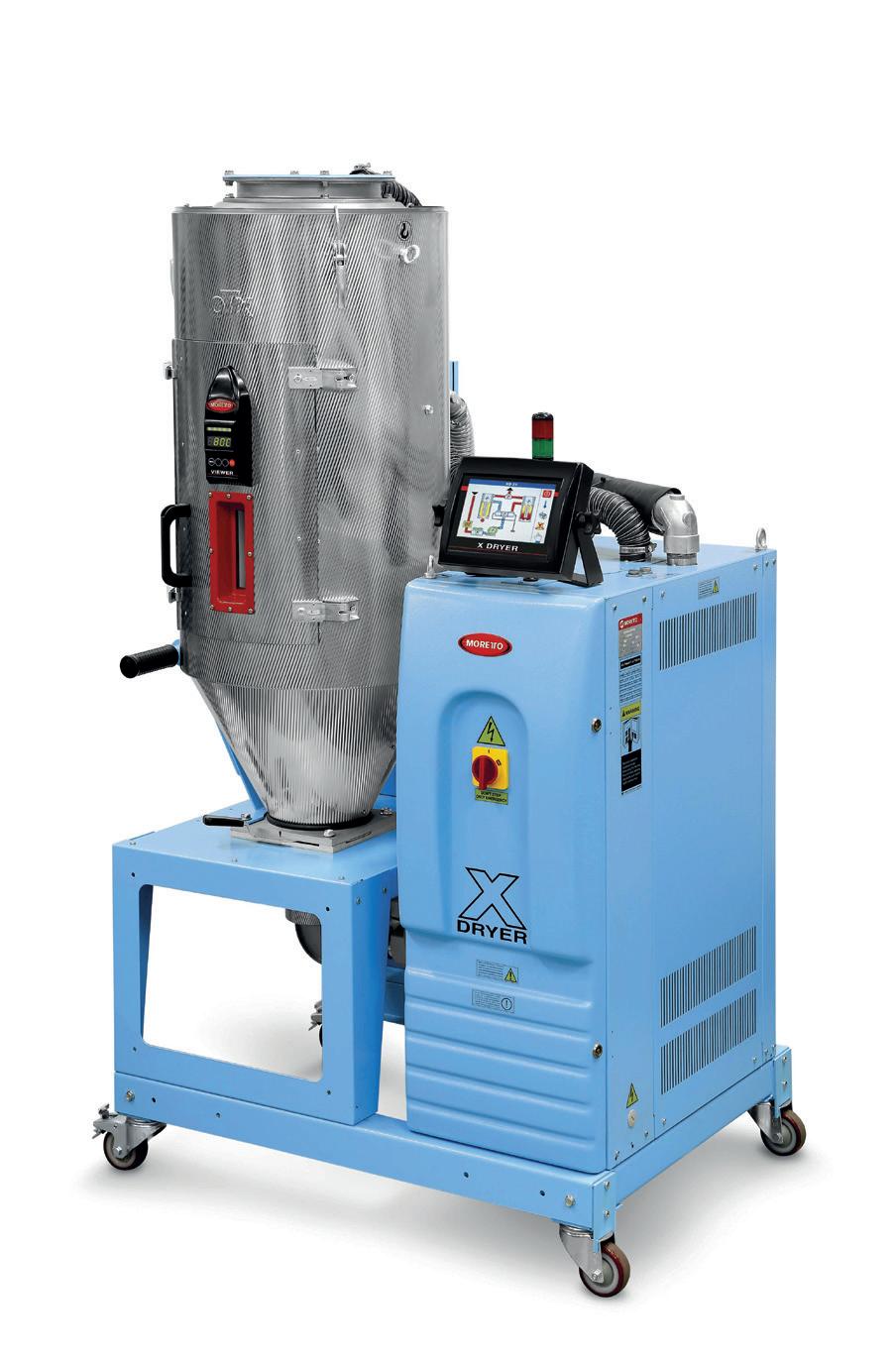
Il dispositivo di ultima generazione Moisture Meter rileva in tempo reale, in linea, l’umidità residua dei polimeri dopo la deumidificazione e prima dell’entrata nella macchina di processo, garantendo l’esattezza della misurazione senza campionature fuori linea, grazie alla tecnologia Power Peak. Il dispositivo effettua la misurazione in continuo fino a 15 ppm ed è disponibile in versione Control, Sentinel e Loop.
INNOVAZIONE A SUPPORTO DELL’ECONOMIA CIRCOLARE
Impegnata ormai da anni nello sviluppo di soluzioni dedicate al riciclo, Moretto è in grado di proporre soluzioni per ogni fase del processo di recupero di materiali pre e post consumo, con: sistemi per macinare, contenere, trattare e trasportare scaglie. Tra i prodotti proposti dall’azienda in questo ambito rientrano i granulatori GR a bassa rumorosità, con camera di taglio modulare, trasformabile in versione antiusura, e raffreddamento per applicazioni particolari. Le lame a forbice garantiscono tagli netti senza polvere e rendono la camera di taglio particolarmente efficiente
La serie manuale di mini dryer Dry Air è stata sottoposta a restyling con l’implementazione di tramoggia OTX e touchscreen semplificato Moisture Meter installato: il dispositivo rileva in linea l’umidità residua dei polimeri dopo la deumidificazione e prima dell’entrata nella macchina di processo; l’esattezza della misurazione senza campionature fuori linea è garantita dalla tecnologia Power Peak
nella presa di corpi voluminosi e/o flaconi, grazie alla geometria a “bocca affamata”. Per un riciclo di qualità, la cristallizzazione del materiale amorfo risulta un processo fondamentale. Per questo, a Fakuma è stato presentato il nuovo sistema MPK Krystallizer, contraddistinto, tra le altre peculiarità, da: cono inferiore apribile, per facilitare manutenzioni e pulizia; struttura interna del corpo miscelatore con pale regolabili e amovibili, per un’elevata flessibilità di utilizzo con materiali diversi; struttura alare delle pale, per movimentare il materiale amorfo in maniera omogenea. La gestione di tutte le funzioni del sistema è affidata a un touchscreen a colori da dieci pollici, con interfaccia a icone integrata e semplice da utilizzare. Le dotazioni di MPK sono completate dal dispositivo di filtrazione Vortex, che intercetta polveri fino a 20 micron, e dal separatore di condensati Purex, che filtra il flusso del circuito di ritorno catturando sostanze resinose e oleose tipiche dei materiali post consumo.
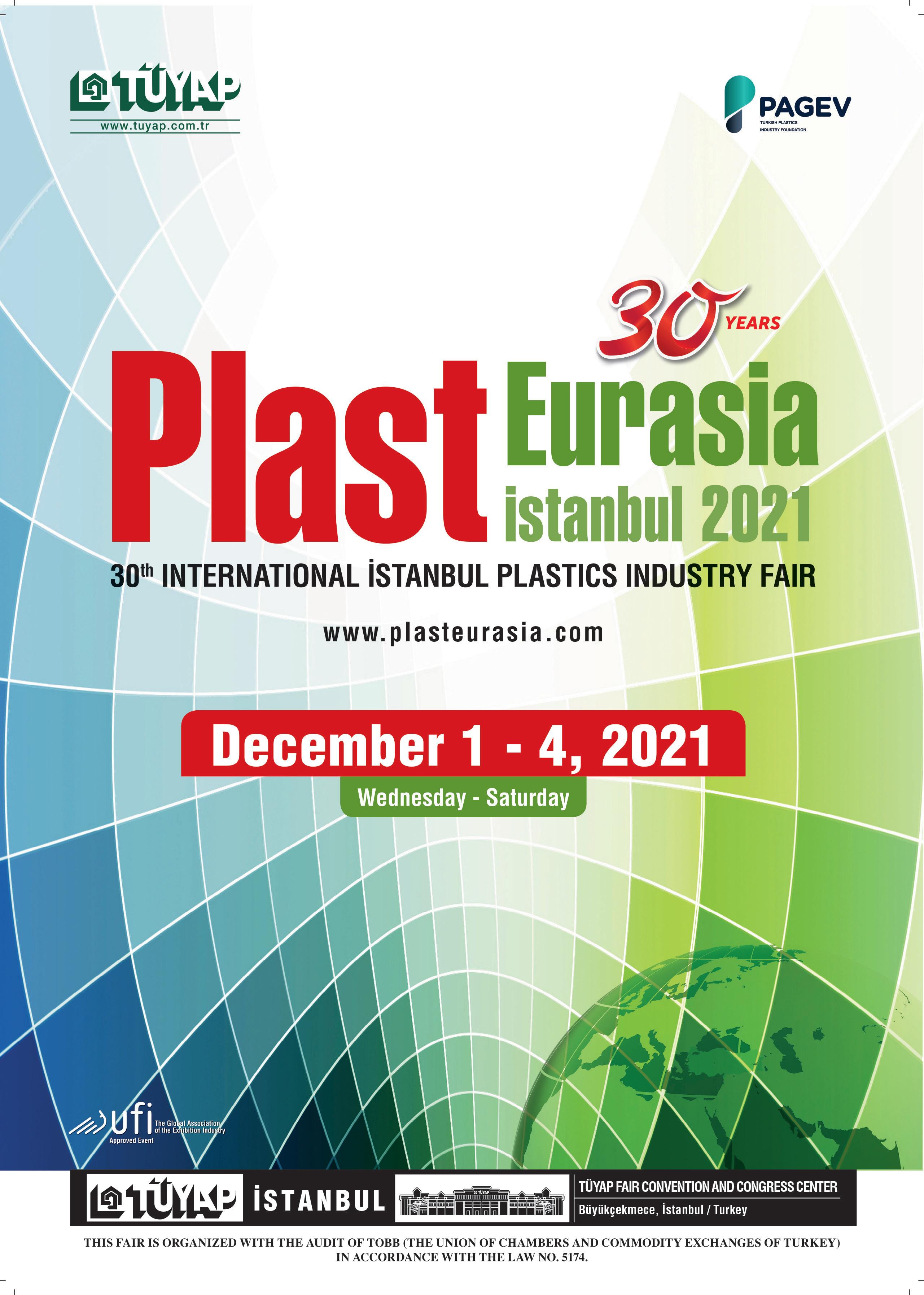
I RECENTI SVILUPPI IN CASA CMG GRANULATORS
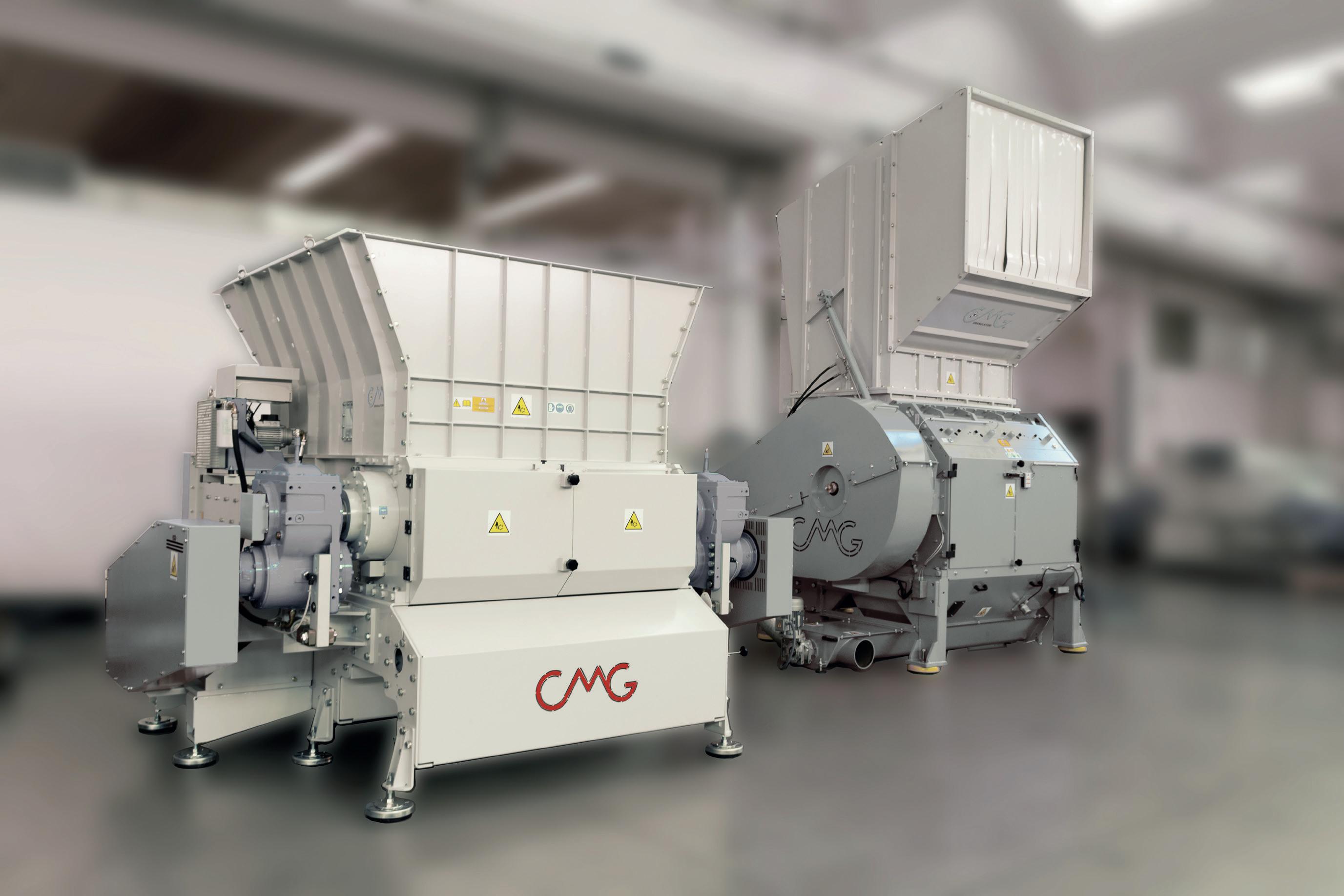
L’EVOLUZIONE DELLA GRANULAZIONE DI NOME E DI FATTO
NEGLI ULTIMI MESI L’ATTIVITÀ DI RICERCA E SVILUPPO DA PARTE DELL’AZIENDA DI BUDRIO (BOLOGNA) È STATA PARTICOLARMENTE INTENSA E HA PORTATO AL LANCIO DI VARIE NOVITÀ PER QUANTO RIGUARDA TECNOLOGIA E SERVIZI OFFERTI
A CURA DI LUCA MEI
“N omen omen” dicevano i latini quando volevano indicare che il destino di qualcuno o di qualcosa era già scritto nel suo nome. E, forse, in questa chiave di lettura si può interpretare il nome “Evoluzione” dato da CMG Granulators a una delle sue più recenti serie di granulatori, ossia la volontà di seguire da vicino, se non addirittura di anticipare, con essa l’evoluzione della granulazione nel riciclo di materie plastiche. La serie Evoluzione garantisce costanza operativa e resistenza all’usura di grado superiore, grazie a soluzioni costruttive che prevedono l’utilizzo di acciaio armonico Hardox e strutture modulari assemblate. Oltre a una precisione al centesimo di millimetro nella costruzione della camera di taglio, a vantaggio di una maggiore durata delle lame, tutti i modelli della gamma sono dotati di controlli avanzati, in chiave di Industria 4.0, per rendere l’operatività della macchina gestibile e monitorabile al 100% anche da remoto. Temperatura d’esercizio, usura delle lame, produttività, efficienza operativa, utilizzo dell’energia, tutti parametri funzionali della macchina, sono solo alcune delle caratteristiche distintive di questi granulatori gestibili a bordo macchina o da remoto con connettività su protocollo OPC-UA. I modelli EV916 ed EV616, in particolare, sono stati presentati dal costruttore ad alcune recenti fiere dedicate al riciclo e alla sostenibilità, tra cui Ecomondo 2021. Si tratta di soluzioni adatte alle condizioni operative più critiche nella granulazione con acqua oppure a secco, laddove le capacità orarie devono attestarsi da 2000 a oltre 5000 kg e sono richieste prestazioni di versatilità, efficienza e sostenibilità.
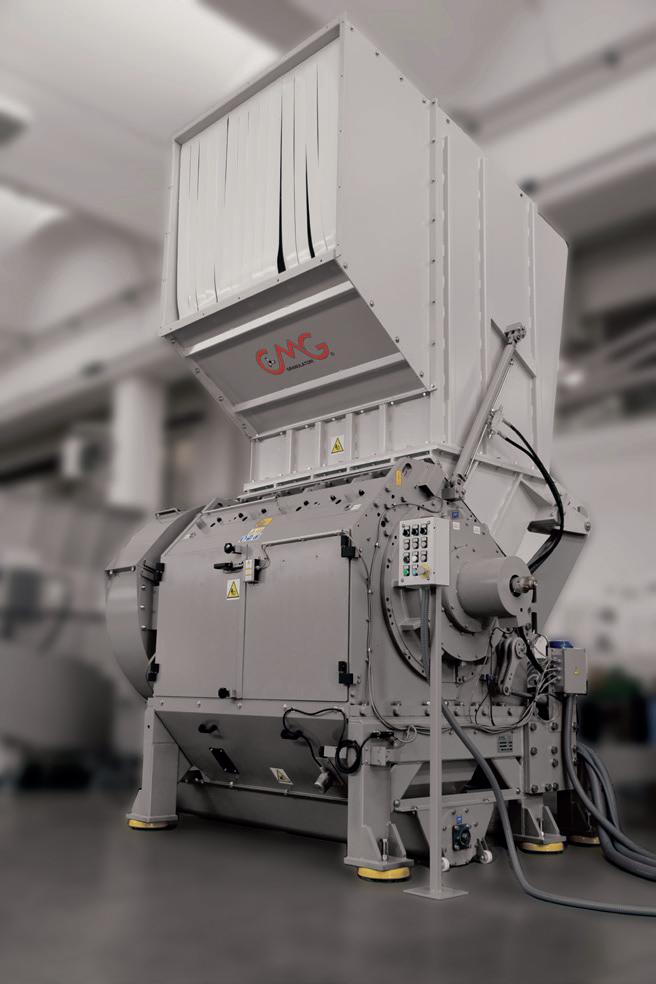
Il “super granulatore” EV916 PER STAMPAGGIO E PER SOFFIAGGIO
Tra gli ultimi sviluppi di CMG Granulators rientra anche la gamma SL di granulatori a bassa velocità e senza griglia, per impieghi nel campo dello stampaggio a iniezione altamente tecnico. I quattro i modelli in cui si dipana questa serie coprono capacità da 5 a 30 kg all’ora e sono contraddistinti da caratteristiche innovative finalizzate a ottenere elevati livelli di produttività, qualità di rimaci-
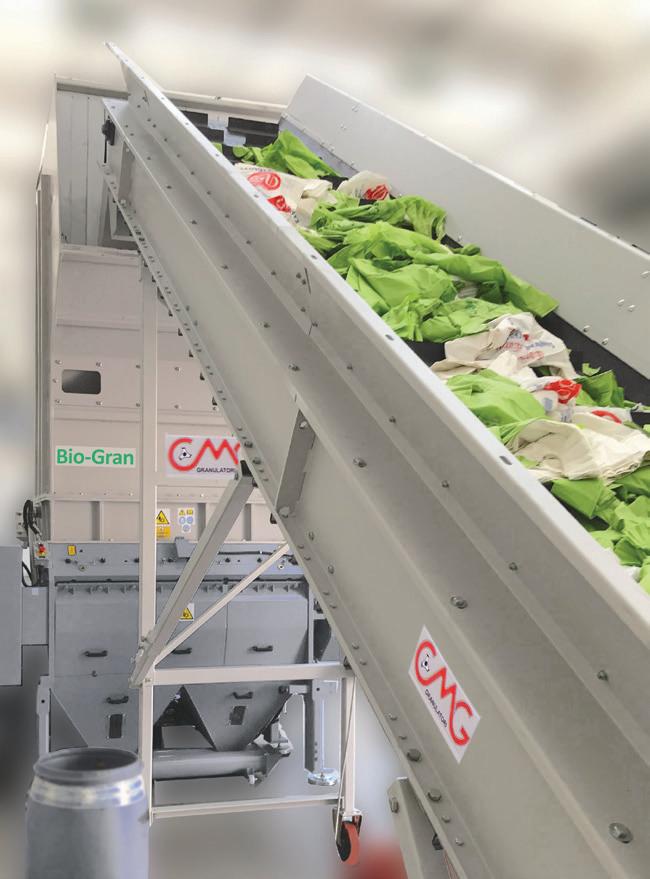
nato (omogeneità dimensionale e assenza di polvere), efficienza di funzionamento, facilità di pulizia e flessibilità applicativa. Per l’utilizzo nel comparto del soffiaggio, invece, il costruttore ha lanciato una nuova serie di granulatori che, oltre alle caratteristiche della gamma SL, vanta uno tra i più bassi TCO (Total Cost of Ownership) del settore di riferimento. Questa serie è composta da 11 modelli, tutti progettati per la macinazione di contenitori prodotti mediante soffiaggio, appunto, o di articoli ingombranti e le cui configurazioni standard coprono produzioni da 20 a 1500 kg all’ora.
GRANULAZIONE DI PLASTICHE BIODEGRADABILI
Le plastiche biodegradabili possiedono caratteristiche fisiche uniche, che non corrispondono a quelle dei polimeri convenzionali. La loro lavorazione risulta quindi altrettanto unica, in quanto tali polimeri sono molto sensibili al calore e allo stress meccanico. Spesso i sistemi di granulazione convenzionali non riescono a trattare adeguatamente gli scarti di produzione in plastica biodegradabile, che, di conseguenza, non vengono reintrodotti nel processo produttivo e sono spesso immessi in circuiti di riciclo convenzionali, a loro volta scarsamente equipaggiati di tecnologie specifiche. Partendo da tutte queste valutazioni, CMG Granulators ha sviluppato la nuova tecnologia Bio-Gran, che, guardando da vicino agli obiettivi delineati dal Next Generation EU Plan, consente il riciclo e il riutilizzo degli scarti di produzione in plastica biodegradabile, eseguendo un’adeguata riduzione dimensionale e i successivi stoccaggio, trattamento e lavorazione senza compromettere l’integrità del polimero. Il tasso di scarto, derivante prevalentemente dalle fasi finali di produzione del prodotto, può variare da pochi a decine di punti percentuali e proprio per questo la tecnologia Bio-Gran è stata progettata per gestire in modo efficace e affidabile un ventaglio variabile da piccole a grandi quantità di polimero, preservandone tutte le caratteristiche fisico-meccaniche. La capacità dei sistemi Bio-Gran (per cui l’azienda ha depositato domanda di brevetto) si estende da 200 a 2000 kg all’ora e le prime unità sono state messe in funzione presso siti industriali che realizzano prodotti in plastica biodegradabile, mentre un esemplare è disponibile per test e prove presso il Technical Center di CMG a Budrio (Bologna).
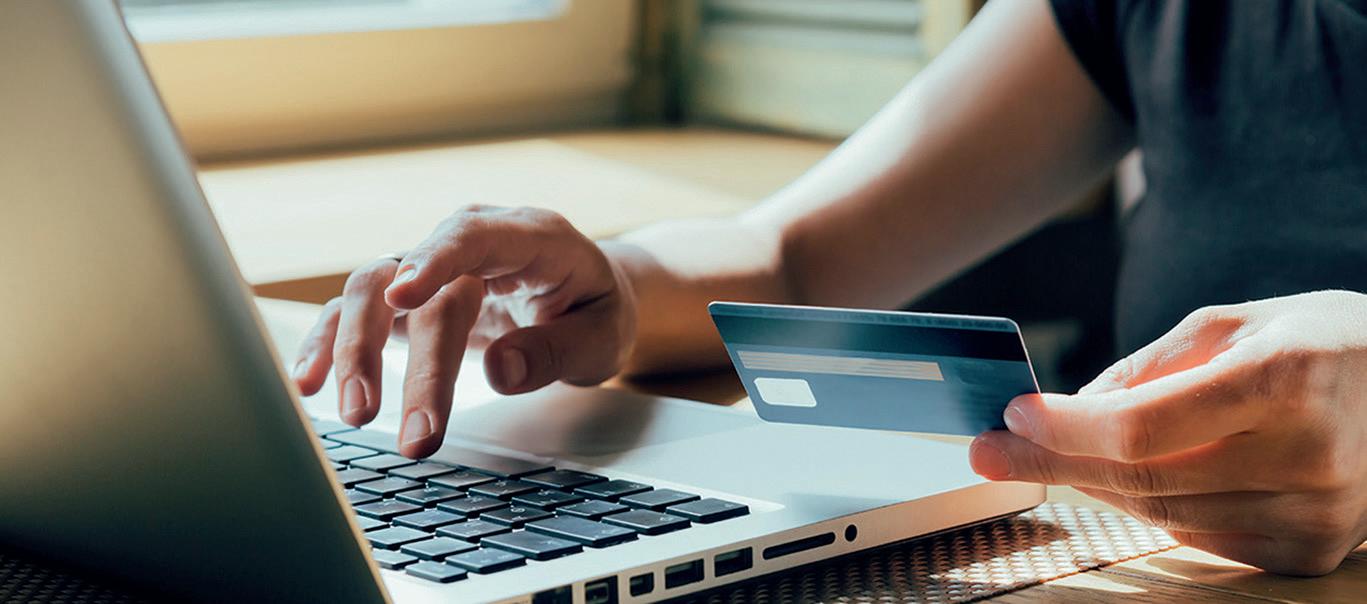
Gli speciali materiali biodegradabili richiedono sistemi di riciclo e recupero altrettanto speciali. Per tale scopo e secondo questa concezione è stato sviluppato il sistema Bio-Gran
La costruzione di tutti i macchinari presso gli stabilimenti di CMG Granulators e l’esecuzione di tutti i test presso il suo Tech Center rispondono al 100% alle linee guida dell’economia circolare. Il fabbisogno di energia elettrica per le attività aziendali è infatti soddisfatto grazie a pannelli solari in loco e la capacità extra dell’impianto da 2 GW supporta i piani di transizione verso la decarbonizzazione della comunità locale. In più, ogni nuovo sviluppo di CMG è intrapreso con l’obiettivo di fornire all’industria soluzioni a ridotto impatto ambientale. L’intera gamma di macchine del costruttore, comprendente, oltre ai granulatori, anche trituratori, nastri di alimentazione e sistemi di evacuazione e trasporto, depolverizzazione e gestione delle polveri e filtraggio, inoltre, viene fornita con certificazione di conformità all’Industria 4.0 e, quindi, ai requisiti richiesti dal Piano Nazionale Transizione 4.0. Conformità che caratterizza tutti gli elementi distintivi dei singoli prodotti impiegati in ciascuno dei settori di applicazione, dalla termoformatura all’estrusione, dal soffiaggio allo stampaggio a iniezione, fino, ovviamente, al riciclo. Tutte le soluzioni CMG per produzioni medio-alte, da 200 a oltre 5000 kg all’ora, dispongono anche della funzione Adaptive Motor Power (AMP). La macchina rileva autonomamente quale livello di potenza adottare per svolgere il proprio lavoro, in funzione di quantità, forma, peso, spessore, tipo e temperatura del materiale da macinare. La funzione AMP consente di ottimizzare la qualità del rimacinato e ridurre al minimo l’utilizzo di energia elettrica. In questo modo, i granulatori consumano da 20 a 25 Wh/kg, rispetto agli oltre 40 Wh/kg di una unità convenzionale.
Semplice e intuitivo, economico e funzionale Un e-shop per l’acquisto online dei pezzi di ricambio
L’attività di CMG Granulators non procede solo sul fronte dello sviluppo tecnologico, bensì anche su quello dei servizi offerti ai clienti, direzione in cui va proprio il servizio attivato recentemente per l’acquisto online dei ricambi per tutta la gamma di prodotti del costruttore. Un nuovo strumento dedicato ai clienti è adesso disponibile per semplificare e accelerare l’approvvigionamento dei ricambi attraverso una nuova piattaforma di e-commerce raggiungibile dalla home page del sito internet di CMG. Il processo di acquisto dei ricambi dall’e-shop non è solo estremamente semplice e intuitivo, ma è anche economicamente conveniente e funzionale, con opzioni aggiuntive come la disponibilità online di un manuale d’istruzioni pronto per il download. Per quanto riguarda i ricambi, l’utente deve registrarsi e inserire il numero di matricola della macchina, così che venga eliminata ogni possibilità di errore nell’acquisto, poiché tutti i pezzi sono collegati e riferibili a ogni singola unità attraverso il numero di matricola inserito.
Anche il servizio di acquisto online risponde alla transizione digitale
POMPA A VITE DI FIMIC
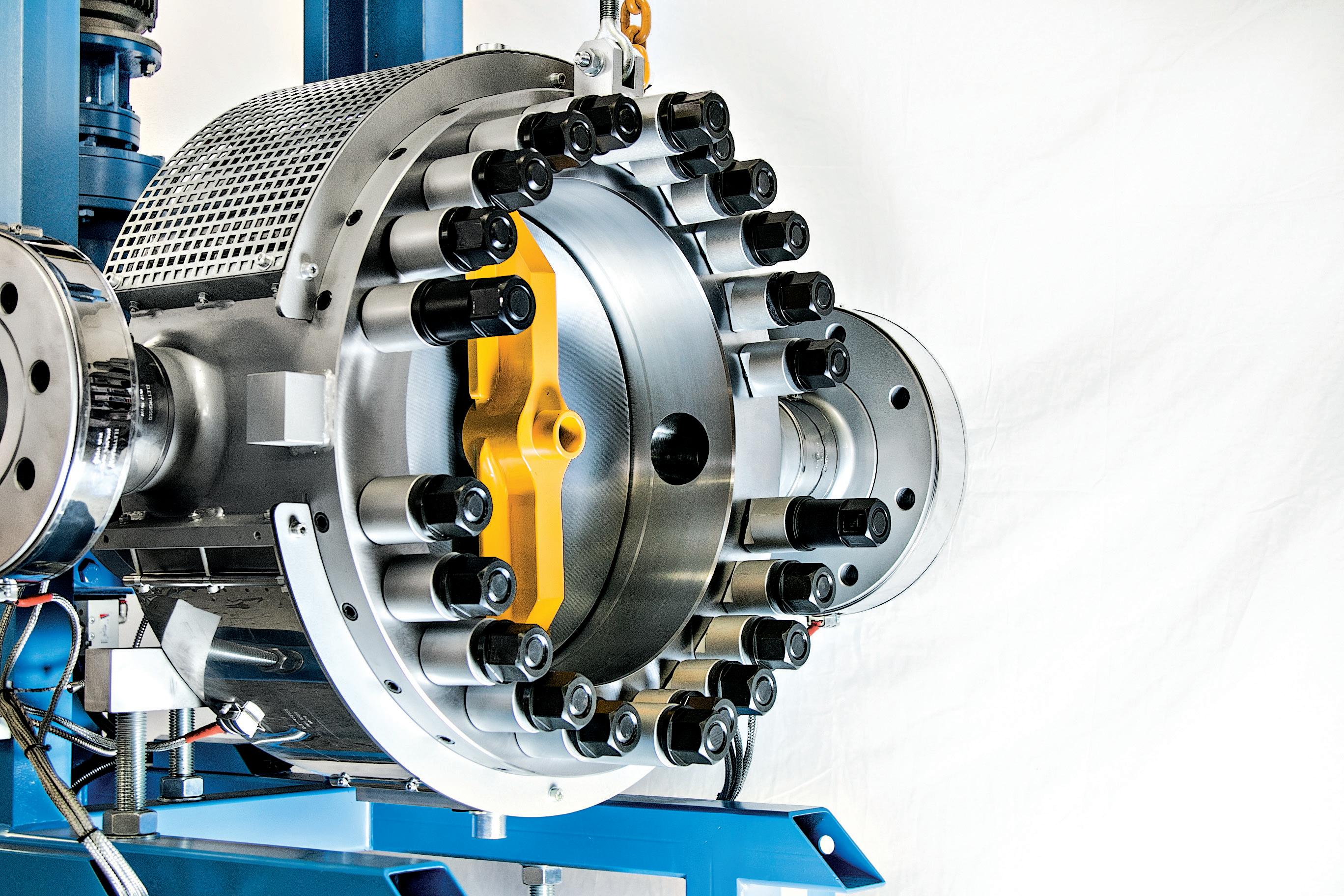
RENDERE IL RICICLO PIÙ EFFICIENTE ED ECONOMICO
DA SEMPRE LE SOLUZIONI DI FIMIC SI CONTRADDISTINGUONO PER LA CAPACITÀ DI APPORTARE INNOVAZIONE NEL SETTORE DEL RICICLO DI MATERIE PLASTICHE, CHE PER L’AZIENDA VUOL DIRE AVERE LO SGUARDO RIVOLTO AL FUTURO. ANCHE L’ULTIMA POMPA A VITE DATATA 2021 SI PROPONE DI MIGLIORARE IL PROCESSO IN TERMINI DI RESA PRODUTTIVA E COSTI DI GESTIONE
Azienda specializzata nella costruzione di sistemi per la filtrazione automatica, Fimic è stata in grado di introdurre negli anni alcuni prodotti che, per le soluzioni proposte, sono riusciti a portare una ventata di innovazione nel settore del riciclo di materie plastiche. Risale al 1997 la realizzazione e l’installazione del primo sistema a controflusso e all’anno successivo l’introduzione del sistema a raschiamento, che ha cambiato il “core business” di Fimic. Da allora, l’azienda ha sviluppato varie soluzioni per gestire materiali plastici altamente contaminati, in particolare di origine post industriale e post consumo, con l’obiettivo di garantire agli utilizzatori produzioni sempre più efficienti. Oggi Fimic è in grado di presentarsi al mercato con una gamma di cinque diversi modelli di filtri, tra cui scegliere di volta in volta quello più adatto al materiale da lavorare, alla produzione oraria desiderata, al livello di contaminazione e alla filtrazione da eseguire. Copertura del ventaglio più ampio possibile di esigenze ed elevata qualità del materiale finale sono le linee guida nello sviluppo delle soluzioni da parte del costruttore.
PRODUTTIVITÀ SU, COSTI DI GESTIONE GIÙ
Il 2021 per Fimic è l’anno di una tecnologia innovativa per un’altrettanto innovativa applicazione, che vuole imprimere una svolta e reinventare, se possibile, il processo di riciclo della plastica. Le comuni pompe a ingranaggi utilizzate per il riciclo risultano molto delicate, poiché le contaminazioni presenti nei materiali plastici possono es-

sere facilmente causa di danni. Ne deriva la necessità di una manutenzione costante e spesso anche dell’installazione di un secondo filtro a protezione della pompa stessa, con un dispendio economico rilevante, sia per l’acquisto del macchinario sia per gli interventi indispensabili al funzionamento. Senza dimenticare che gli ingranaggi devono essere periodicamente sostituiti, a ulteriore svantaggio dell’operatività. Per fronteggiare questo insieme di aspetti non trascurabili, Fimic ha sviluppato la tecnologia SPA con cui rendere più efficace e veloce il lavoro dei riciclatori, portandolo a prestazioni in precedenza non raggiungibili. Si tratta di una pompa che permette di trasportare agevolmente il materiale plastico fuso dall’estrusore fino al filtro senza utilizzare ingranaggi. SPA, infatti, funziona mediante un’unica vite e richiede una manutenzione estremamente ridotta, risultando così la soluzione ideale per chi cerca la massima qualità a costi di gestione notevolmente contenuti. L’adozione della nuova pompa a vite SPA si traduce in un immediato risparmio grazie alla sensibile riduzione delle spese di gestione conseguente all’eliminazione di: manutenzione, secondo filtro protettivo e costosi ingranaggi di ricambio. Anche la semplicità operativa ne risulta accresciuta. La pompa a ingranaggi, infatti, è un dispositivo dal funzionamento molto più complesso, mentre la SPA è facile da utilizzare e non richiede sostituzioni periodiche. Inoltre, può essere installata sia prima sia dopo il filtro, ed è perfetta anche per la doppia filtrazione. Se installata prima del filtro, protegge l’estrusore bivite utilizzato per la realizzazione del compound, mentre se installata dopo il filtro stabilizza la pressione del materiale, aumentando produttività del filtro e dell’estrusore. SPA unisce l’alto livello di progettazione ingegneristica delle tecnologie Fimic e l’elevata qualità dei materiali costruttivi, per offrire un prodotto di classe superiore, affidabile e dalle elevate prestazioni. Allo stesso tempo, il funzionamento innovativo della pompa garantisce ai riciclatori un netto risparmio nei costi di gestione, oltre che un’eccellente qualità del materiale finale.
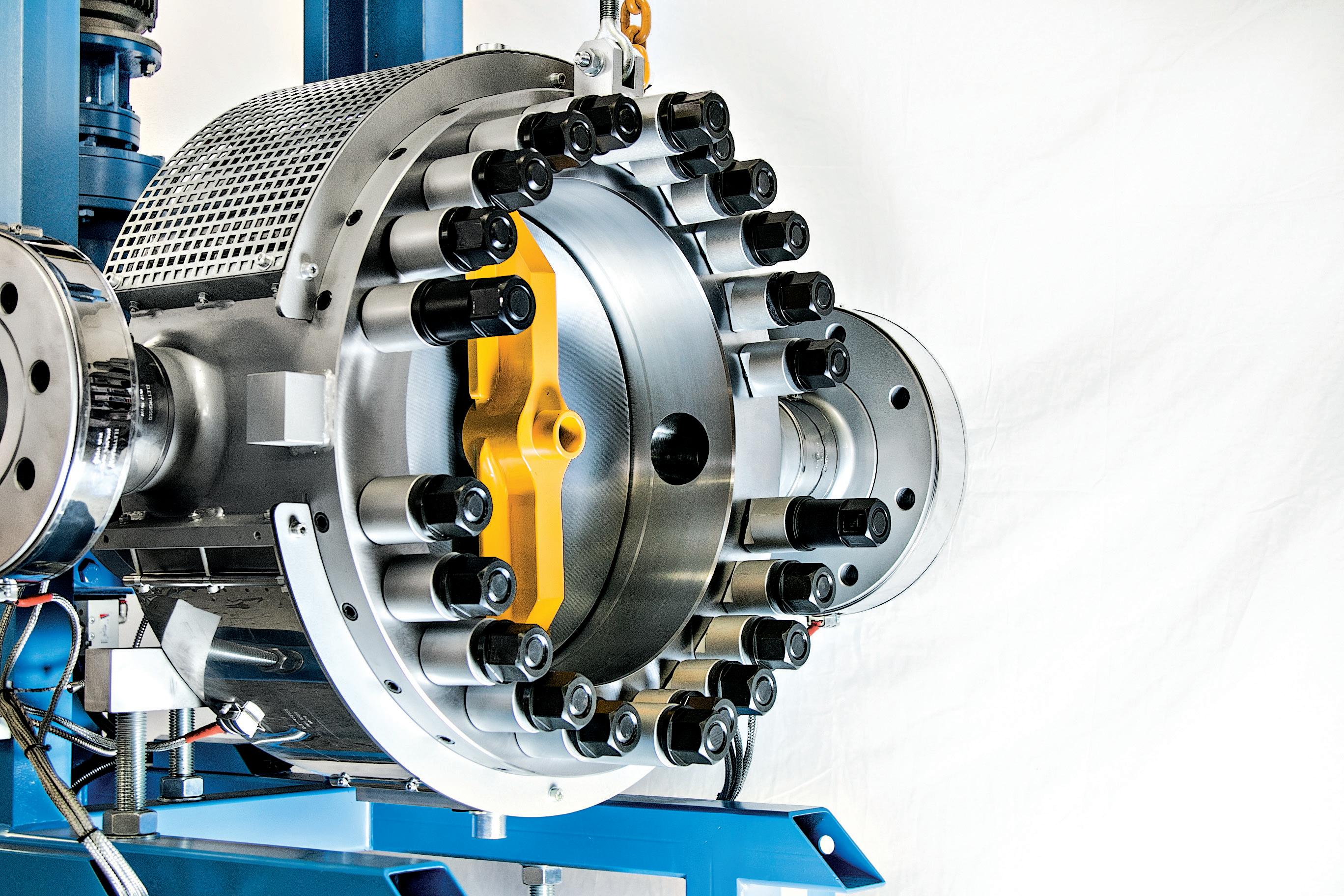
Una versione della pompa a vite SPE
Un ruolo nell’economia circolare
L’Unione Europea sta aggiornando la legislazione su gestione e utilizzo dei materiali plastici, per promuovere la transizione verso un’economia circolare in alternativa all’attuale modello economico lineare, processo impegnativo e che esige cambiamento culturale e sviluppo tecnologico. Nel modello di economia circolare, il riciclo della plastica è fondamentale e la filtrazione dei materiali plastici post consumo altamente contaminati diventa un passaggio strategico. Una delle basi fondamentali per sviluppare un’economia circolare consiste infatti nel considerare il riutilizzo dei materiali post consumo ponendo la massima attenzione alle tecnologie di riciclo. E per ottenere plastica pulita partendo da materiali altamente contaminati è necessario disporre di sistemi di filtrazione di alta qualità. In quest’’ottica i cambiafiltri automatici e continui risultano essenziali e strategici. È qui che Fimic entra in campo, alla ricerca costante di soluzioni tecnologiche efficienti per rendere sempre più agile e performante il processo e per ottenere un prodotto il più possibile omogeneo e privo di contaminazioni, anche nella ferma convinzione che la sostenibilità ambientale sia la chiave del progresso. Un esempio di questo impegno è rappresentato dal filtro autopulente RAS, che non solo permette di rigenerare materiali anche molto contaminati in autonomia e con continuità, senza dover ricorrere a un operatore, ma garantisce anche un materiale molto pulito e integro per quanto riguarda le caratteristiche meccaniche. La scelto della soluzione laser per la filtrazione in continuo si traduce in un materiale con eccellenti caratteristiche di flessibilità e pulizia. In definitiva, le scelte tecnologiche, come il corretto cambiafiltro per trattare i materiali post consumo, possono rivelarsi decisive e abilitanti come basi del modello di economia circolare.
Dai materiali postindustriali e postconsumo ai granuli di materiale riciclato, pulito e performante, il passo è breve con la scelta delle corrette tecnologie di processo

NEWS
TRITURATORI FORREC PER VALORIZZARE I RIFIUTI
RENDERE SEMPLICI I PROCESSI DI LINEE COMPLESSE
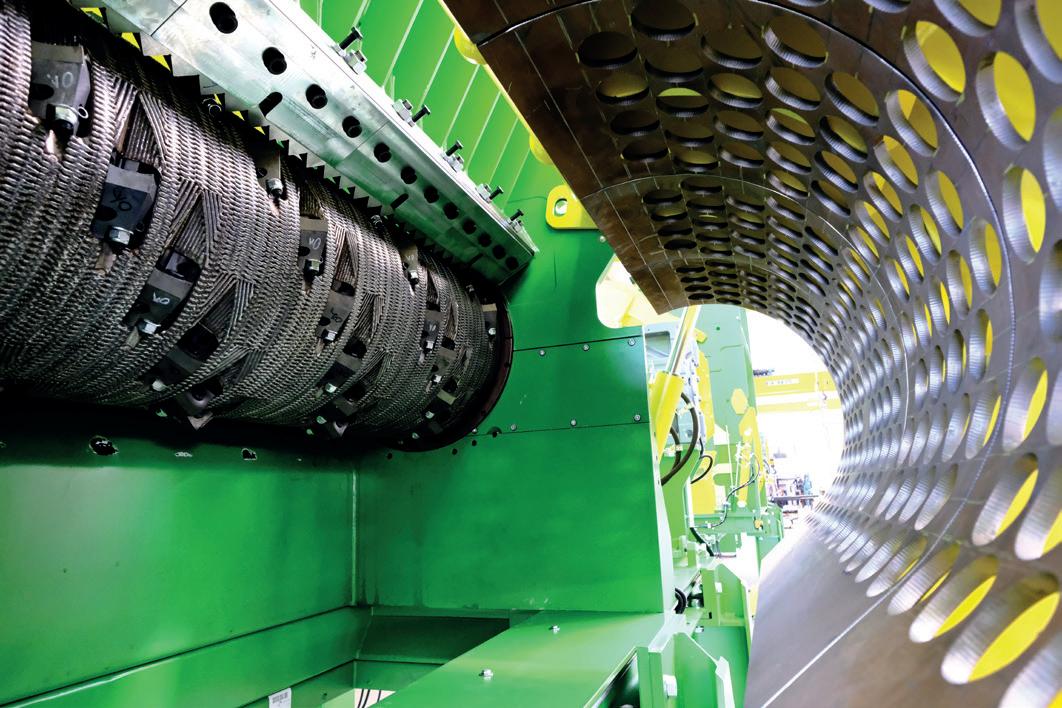
Una vista interna dei trituratori Forrec
Azienda che progetta e realizza sistemi per la triturazione e la riduzione dimensionale degli scarti plastici, Forrec ha recentemente avviato una partnership con un’impresa nel settore del lavaggio che prevede l’utilizzo dei suoi trituratori in linee complesse di valorizzazione della plastica. Le cinque linee frutto della collaborazione, installate tra Regno Unito e Tailandia, hanno permesso la realizzazione, di impianti che eseguono tutte le fasi della rigenerazione della plastica, dalla macinazione al lavaggio, fino all’estrusione, il tutto completato da varie fasi di selezione e separazione. Forrec si è occupata del processo che porta tutto il materiale a una dimensione granulometrica ben calibrata, adatta ai trattamenti successivi, fornendo trituratori della serie XM, perfettamente adattati alle esigenze dell’utilizzatore e ottimizzati per lavorare in continuo per sette giorni, su turni che coprono le 24 ore. Per questi processi sono stati scelti i robusti modelli monoalbero X2000M e X2500M, con motori da 132 a 200 kW. La potenza è definita in base al tipo di materiale da trattare e alla granulometria richiesta in uscita. Le macchine sono dotate di vaglio da 80 mm, dimensione ideale per i successivi trattamenti di lavaggio ed estrusione, mentre rotore saldato e piastre piane consentono di ottenere le prestazioni più elevate. Le tre linee parallele installate nel Regno Unito trattano rispettivamente 3000 kg/h di HDPE, 2200 kg/h di HDPE colorato e 1800 kg/h di PP, dove il materiale post consumo arriva ai trituratori dopo aver superato una selezione ottica. A questo progetto ne è seguito un secondo, sempre nel Regno Unito, per trattare HDPE e PP separatamente con una capacità di 2400 kg/h e ottenere granulato con dimensioni di 80 mm. L’ultima linea sarà installata in Tailandia e sarà destinata al trattamento di HDPE con una capacità di 2600 kg all’ora.
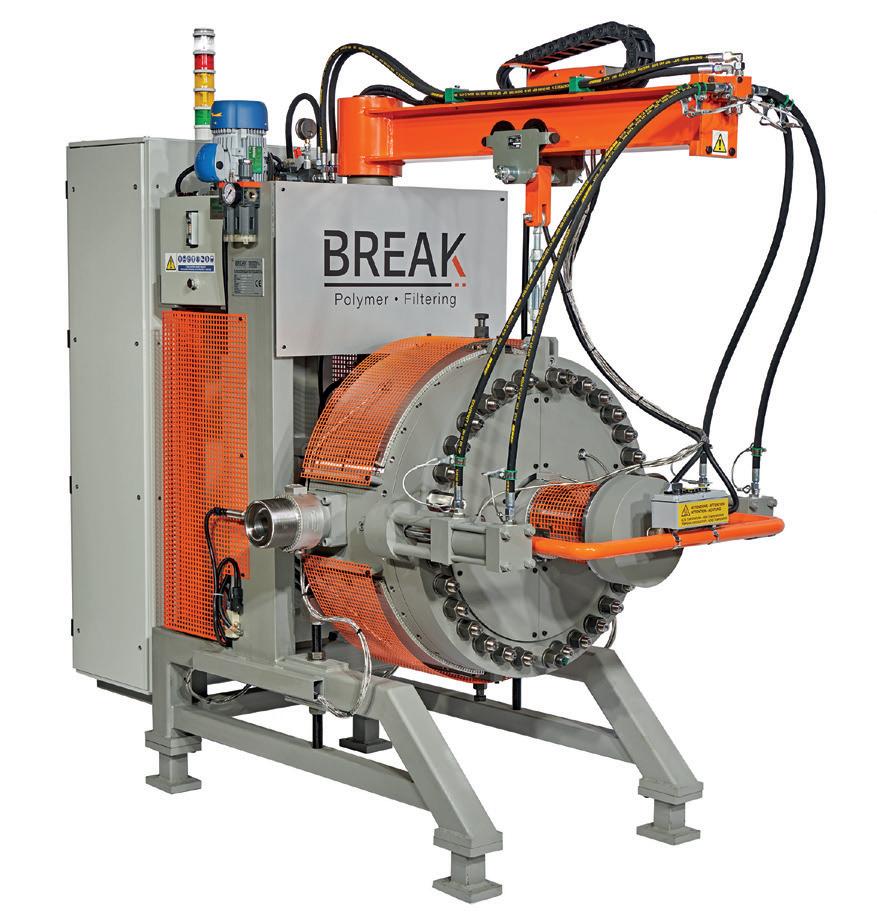
Un nuovo approccio alla filtrazione Ridurre i costi operativi, ottimizzare il processo e risparmiare energia
Alla guida di Geoplast Group, di cui Break Polymer fa parte, la famiglia Pegoraro comprende da sempre le potenzialità della plastica, tanto che dal 1974 è impegnata nella costruzione di macchine per lo stampaggio di materiali polimerici e la rigenerazione di scarti post consumo. “Grazie al nostro centro di ingegneria interno, contribuiamo a sviluppare sistemi tecnologicamente avanzati per nuove soluzioni applicative sempre meno impattanti sull’ambiente e sulle nostre vite, volte a favorire la riciclabilità dei prodotti a fine vita aumentando l’impiego della plastica riciclata”, ha dichiarato Massimo Pegoraro, CEO di Geoplast e direttore generale di Break Polymer. Un approccio visionario, compatibile con il modello dell’economia circolare. Tutti i nuovi progetti dell’azienda sono orientati a macchinari e prodotti finiti in grado di offrire soluzioni tecnologiche con un maggior tasso di sostenibilità ambientale e un vantaggio competitivo in termini di risparmio economico per l’utilizzatore finale. Dopo oltre 45 anni di esperienza nel settore, adottando un approccio innovativo nella ricerca e nello sviluppo, è stata ideata una nuova generazione di cambiafiltri automatici e autopulenti a flusso continuo, con l’intento di conferire valore aggiunto alle materie plastiche da trattare. Break Polymer si ispira alla massimizzazione dell’intero ciclo produttivo pensando a un nuovo modello di business e vuole essere un punto di riferimento nella decontaminazione delle materie plastiche. “Le nostre macchine filtranti e autopulenti sono costruite secondo i più alti standard di progettazione meccanica e la tecnologia di filtrazione garantisce eccellenti standard qualitativi e di affidabilità. Gli innovativi sistemi Break possono essere facilmente integrati nella catena di processo esistente per garantire la massima qualità dei prodotti. Il nostro obiettivo è quello di ridurre i costi operativi, ottimizzare i processi produttivi e risparmiare energia nell’intero impianto di produzione. L’innovazione sta alla base dello sviluppo tecnologico e il nostro intento è rompere gli schemi, ripensare le soluzioni e adottare metodi e sistemi più sostenibili per impattare in modo profittevole nella vita di tutti i giorni”, ha aggiunto Pegoraro.
Le innovative macchine prodotte da Break Polymer adottano sistemi di controllo digitale e sono predisposte per applicazioni in chiave di Industria 4.0.
BD PLAST PRESENTA CLEANCHANGER© IL CAMBIAFILTRI DEL FUTURO
PROGETTATO DALL’AZIENDA EMILIANA BD PLAST, CLEANCHANGER© È UN CAMBIAFILTRI IDRAULICO A FUNZIONAMENTO CONTINUO, AUTOMATICO E AUTOPULENTE
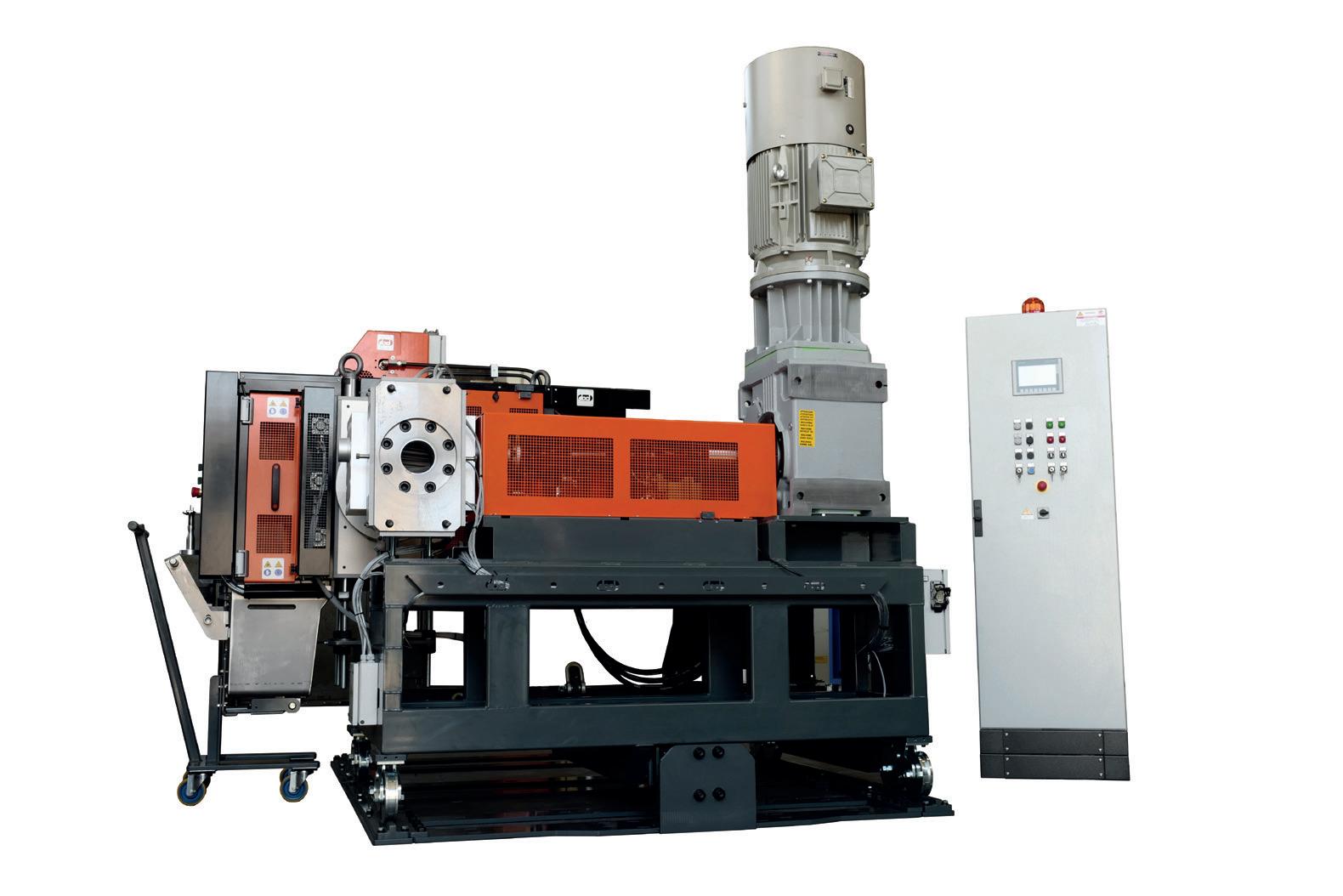
Azienda italiana costantemente impegnata nell’implementazione della filiera e nello sviluppo di nuove soluzioni per l’estrusione, BD Plast di prodotti presenta CleanChanger© con l’obiettivo di stare al passo con le richieste del mercato generando nuove linee. Si tratta di un nuovo cambiafiltri idraulico autopulente auto-
Un cambiafiltri automatico continuo può rendere efficiente l’intera filiera produttiva

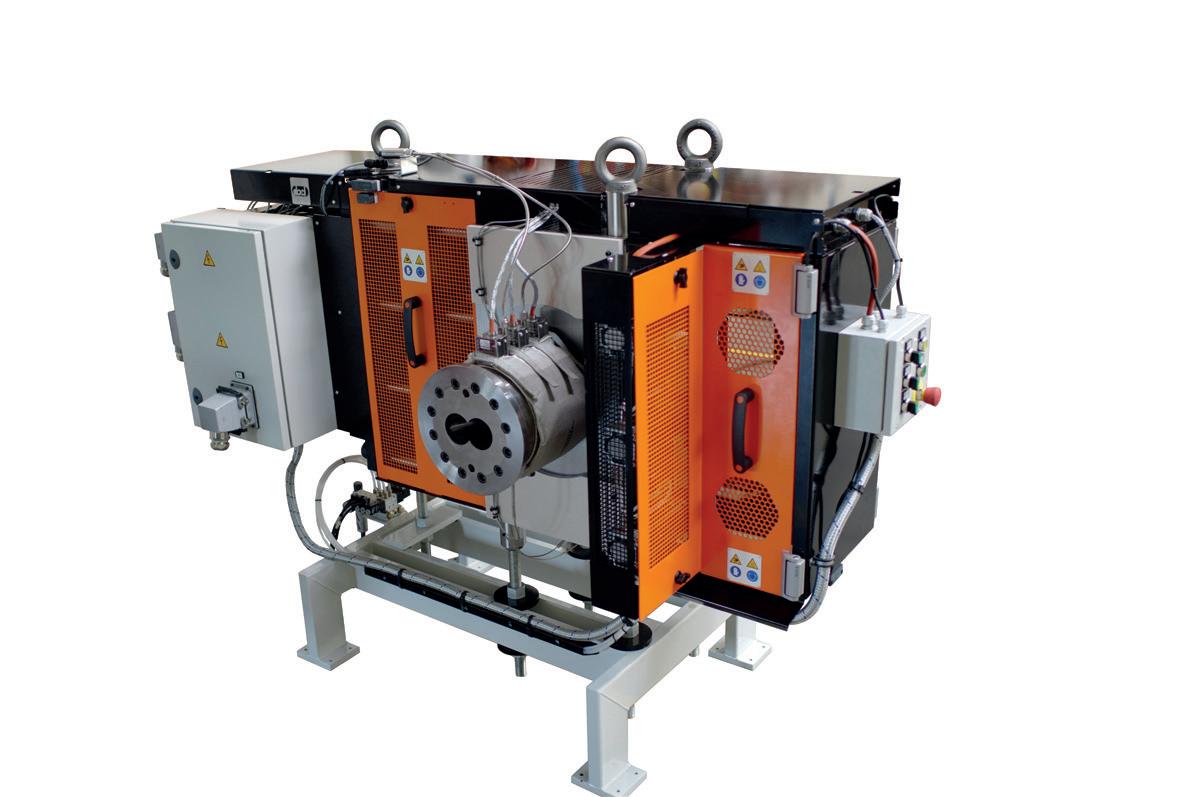
Il cambiafiltri CleanChanger© è un prodotto 100% made in Italy matico e continuo, a tripla piastra, che nasce dal know-how BD Plast per avere un’operatività autonoma e per non produrre alcuno spreco, permettendo il riutilizzo del 100% del materiale. Attraverso l’implementazione di un ciclo di pulizia delle reti ad alta efficienza, CleanChanger© è in grado di garantire un livello di pulizia pari al nuovo, con conseguente ulteriore riduzione dei costi di produzione. Un cambiafiltri performante è una garanzia di sostenibilità dell’intera filiera produttiva: il sistema di filtrazione autopulente CleanChanger©, realizzato con una completa coibentazione, rientra tra i prodotti di punta di BD Plast. Lavorare plastica riciclata richiede capacità tecnologiche, oltre a un know-how avanzato nell’eseguire processi di filtrazione particolarmente efficaci, in modo da poter ricavare
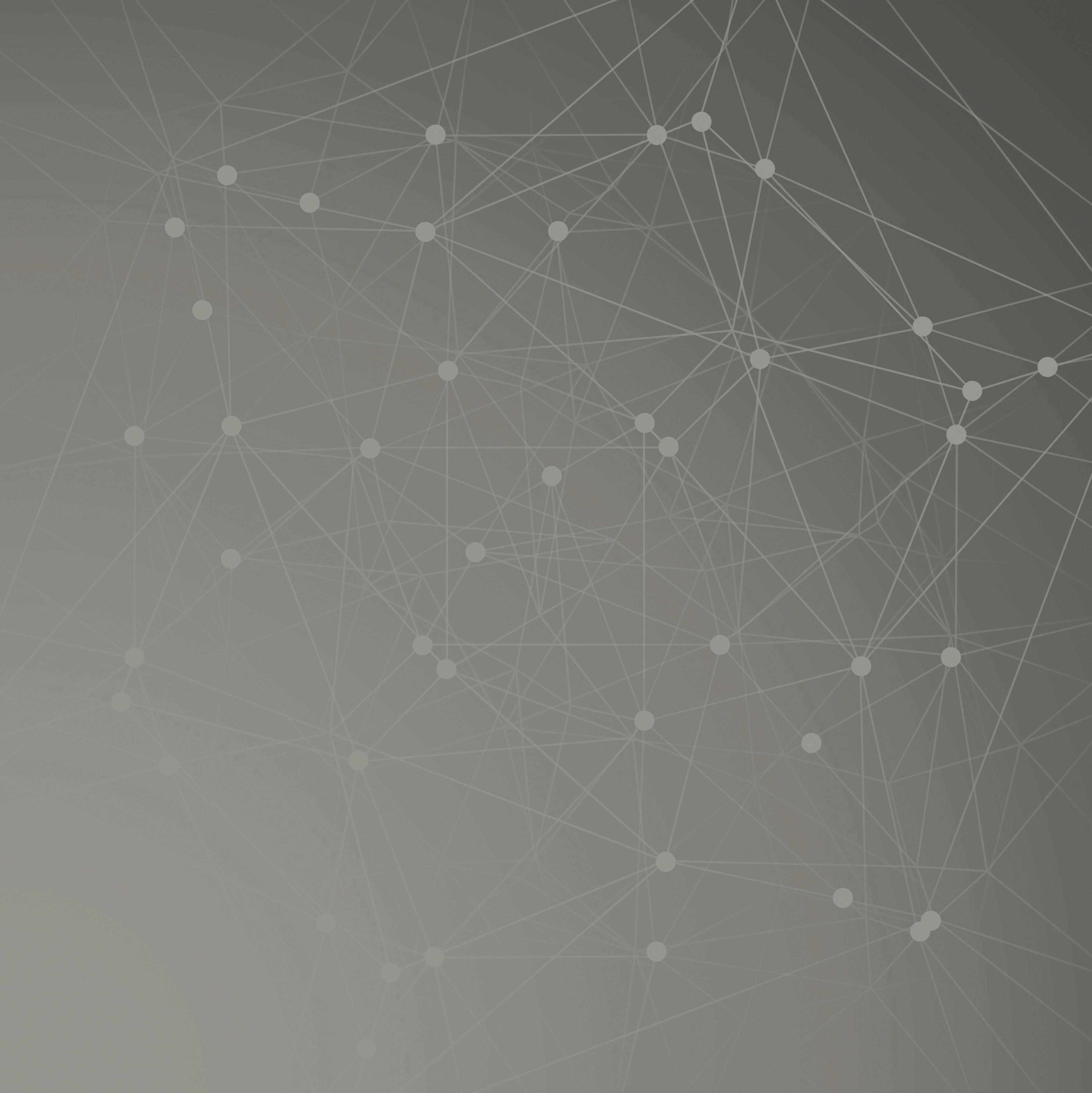
Il cambiafiltri idraulico a funzionamento continuo progettato da BD Plast è automatico e autopulente plastica “nuovamente” pulita, pura e di qualità. La frequenza della sostituzione dei filtri è fondamentale per raggiungere il massimo grado di pulizia e purezza dei polimeri plastici, prima di plasmarli per i diversi usi. Le modalità di sostituzione e la tipologia di macchina utilizzata per questa attività incidono non solo sulla qualità, ma anche sulla velocità e sul costo dell’intero processo: un cambiafiltri automatico e continuo può efficientare l’intera filiera produttiva aziendale e generare un aumento di business. Studiati per una filtrazione completa del termoplastico destinato all’estrusione, i cambiafiltri garantiscono eccellenti risultati sui rigenerati, consentendo un processo di lavorazione di alta qualità su materiali con un elevato grado di purezza.
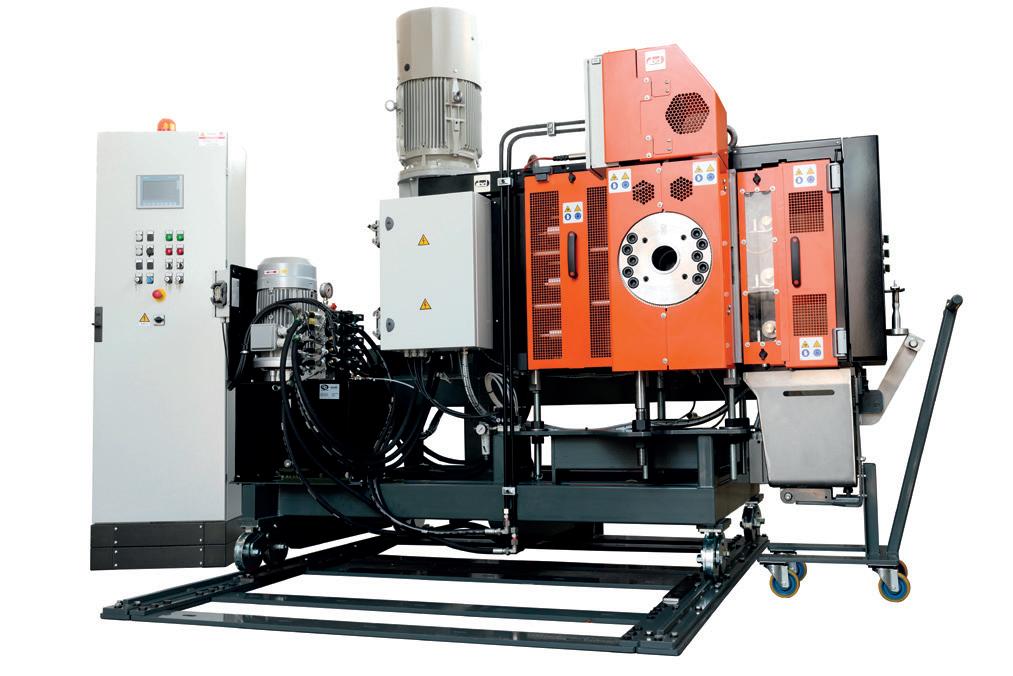
I PUNTI DI FORZA DI CLEANCHANGER©
- 100% made in Italy - Compatto a tre piastre - Automatico: filtrazione automatica con movimento indipendente di ciascuna piastra, area di filtrazione ampliata, assenza di dispositivi di ritenzione delle reti - Unico: sistema automatico di espulsione delle breaker plate quando è necessaria la sostituzione della rete - Sicuro: protezione completa con interblocchi di sicurezza a codifica RFID - Versatile: utilizzabile a tutti i livelli di pressione - Durevole: tecnologia di tenuta
Una veduta del cambiafiltri CleanChanger©
autoattivante a prova di perdite, che assicura una maggiore durata della guarnizione - Produttivo: produttività aumentata e bassa contropressione per l’autopulizia delle reti (8 bar testati) - Efficiente e autonomo: fino a 200 cicli di pulizia prima della sostituzione delle reti e, di conseguenza, riduzione al minimo dei costi del personale necessario per operazioni manuali - Personalizzabile: il cambiafiltri può essere personalizzato grazie alla capacità di BD Plast di ingegnerizzare soluzioni totalmente ritagliate sulle esigenze del cliente - Performante: soluzione integrata di processo, garantisce ottimizzazione dei canali di flusso, stabilità e continuità, eccellente controllo di temperatura - Soluzione di processo: studiato per inserirsi all’interno della sezione di filtrazione e degli altri componenti di sistema (estrusore, pompa volumetrica, valvola deviatrice, testa di estrusione e carrello o piattaforma di sostegno) - Sostenibile: l’assenza di fermo impianto e di materiale di scarto riduce i costi, la manutenzione risulta semplice, la continua sostituzione delle reti non è più necessaria, il che elimina anche la necessità di presidiare il dispositivo.
Per ulteriori informazioni su azienda e CleanChanger©: www.bdplast.com
NEWS
La granulazione secondo Bruno Folcieri La potenza è una cosa semplice
I granulatori Easy Power di Bruno Folcieri sono caratterizzati da un’elevata robustezza costruttiva, risultando indicati per applicazioni particolarmente difficili come la macinazione di materiali plastici tenaci, abrasivi e con elevata contaminazione e, quindi, fortemente usuranti. La costruzione notevolmente robusta rappresenta la peculiarità principale di questi granulatori e trova il suo apice nella configurazione del rotore, ricavato da un blocco di acciaio pieno forgiato e bonificato, così da risultare completamente privo di saldature, a riprova di estrema solidità, robustezza e resistenza. L’intercambiabilità della maggior parte dei componenti carcassa, come i portalama del rotore, i cunei di bloccaggio delle lame e le piastre di protezione in acciaio antiusura (che rivestono totalmente la carcassa), preserva la macchina nel tempo e si traduce in un’elevata efficienza. Inoltre, l’apertura completa della tramoggia e la speciale conformazione della carcassa stessa permettono di accedere direttamente al cuore della macchina, raggiungendo in modo agevole il rotore e i portalama in caso di interventi di ispezione e manutenzione. Questi granulatori sono disponibili anche in versione ad acqua Easy Power Wet, mentre tra gli accessori a disposizione dell’utente vi sono: ventilatore per trasporto macinato, realizzato in carpenteria pesante con parti soggette a maggior consumo in acciaio antiusura; coclea di scarico materiale; nastro trasportatore realizzato in costruzione pesante e robusta; metal detector; cabina di insonorizzazione. Infine, opzionalmente è disponibile anche uno spintore per materiali voluminosi.
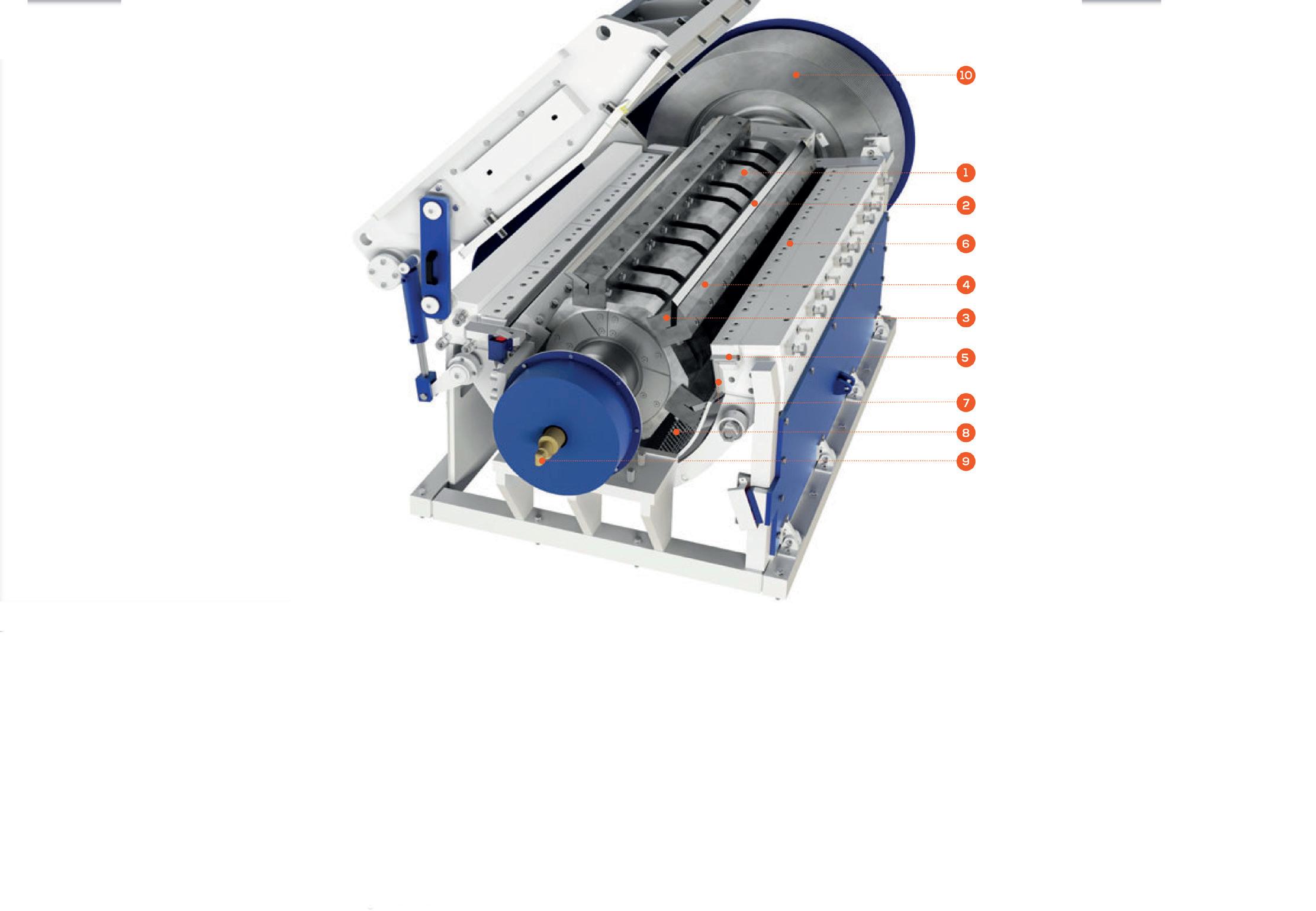
DETTAGLIO DEL GRANULATORE EASY POWER: 1 - Rotore ricavato da blocco pieno di acciaio forgiato, radiografato e ispezionato con ultrasuoni a garanzia di assenza di difetti 2 - Lama rotante 3 - Bloccaggio a cuneo rotante 4 - Portalama intercambiabile 5 - Controlama 6 - Piatto bloccaggio controlama 7 - Lamiera di protezione sede controlama in acciaio antiusura 8 - Griglia di scarico 9 - Giunto rotante per raffreddamento ad acqua di rotore e carcassa 10 - Puleggia con diametro di 1400 mm (2,8 tonnellate) con elevata coppia tagliente
Nuovi filtri ECO di Ettlinger Economici ed ecologici
La nuova gamma di filtri ECO, lanciata da Ettlinger (Gruppo Maag) per il riciclo di PET, offre nuove funzionalità che tengono conto della necessità di avere sistemi con produttività superiori ed è al momento disponibile in versioni adatte a linee di riciclo di medie dimensioni. ll modello ECO 350, dalle prestazioni potenziate, sostituisce il precedente ECO 250, mentre il modello ECO 500, che raggiunge capacità fino a 4000 kg/h, rimpiazza ECO 250 Twin. La gamma
comprende inoltre il modello ECO 200. La tecnologia di filtrazione di Ettlinger si basa sul principio del filtro autopulente con flusso continuo del fuso dall’esterno verso l’interno di un tamburo rotante perforato. Un raschiatore rimuove i contaminanti trattenuti sulla superficie e li trasporta al sistema di scarico. Come i filtri ERF, anche gli ECO presentano un design modulare, fornenIl nuovo filtro ECO 500 raggiunge portate do così una vasta gamma di fino a 4000 kg all’ora opzioni in termini di caratteristiche. Un nuovo sistema favorisce una concentrazione ancora più elevata di contaminanti nel flusso di scarico, consentendo di ridurre ulteriormente le già basse perdite di PET fuso dei filtri Ettlinger. L’accesso al raschiatore è stato migliorato per ridurre i tempi di manutenzione e sostituzione, mentre lo scarico è posizionato sul lato anteriore del filtro, per garantire un più facile accesso all’operatore. I filtri ECO sono progettati per trattare materiali a bassissima viscosità (principalmente PET e PA) e per facilitare la separazione efficiente di contaminanti come carta, legno, alluminio, silicone ecc. Inoltre, il sistema di scarico chiuso evita punti neri (bruciature) nel materiale finale. Per questo motivo, i filtri ECO sono indicati per linee d’estrusione in cui le scaglie in PET da bottiglie post consumo vengono convertite in film per imballaggi alimentari, pellicole o fibre.
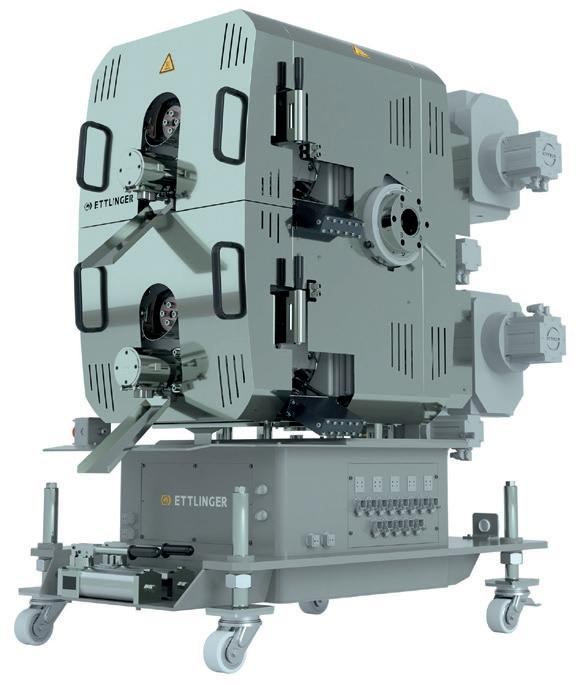
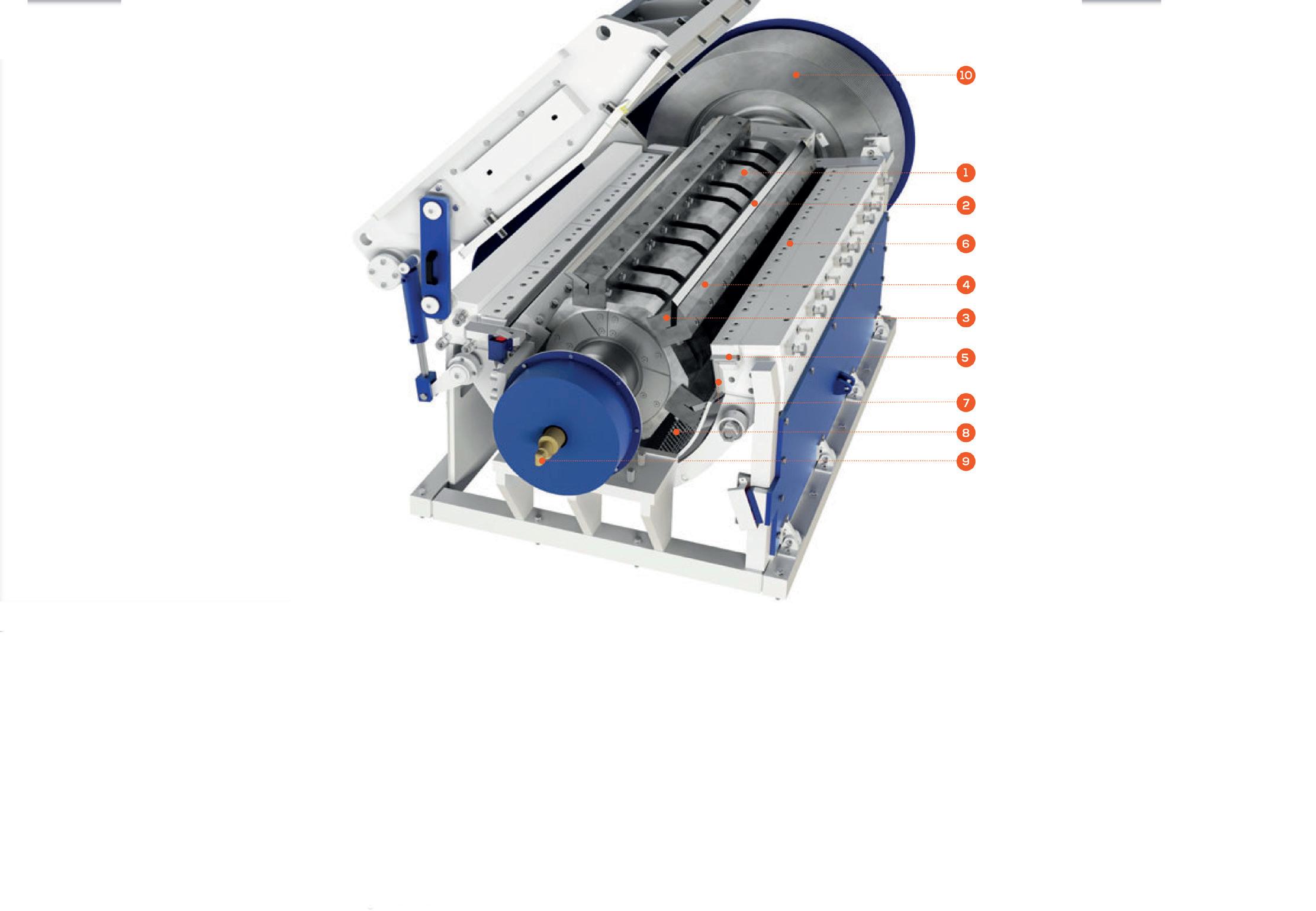
Separatore ad aria Un soffio di precisione
Il sistema completo: nastro trasportatore SpeedCon, separatore ad aria AirLift, unità AirWheel
I dispositivi di separazione ad aria sono cruciali per smistare rifiuti di peso diverso e AirLift di Westeria risulta particolarmente selettivo a tal fine. Si tratta di un separatore per materiali ultraleggeri in grado di smistare frazioni di plastica con minime differenze di peso specifico. Le sue possibili applicazioni includono il riciclo delle bottiglie in PET, che possono essere separate in modo efficiente da contaminanti leggeri come le etichette in PE. Le normative che disciplinano i prodotti in plastica richiedono la presenza di percentuali sempre più elevate di materiali di riciclo. Inoltre, l’eccesso di offerta di scarti in plastica e gli attuali bassi prezzi dei materiali vergini fanno sì che i requisiti di qualità, come la purezza dei materiali da riciclare, siano in costante aumento. Di conseguenza, se si punta all’utilizzo di quantità maggiori di materiali post consumo, occorre prestare sempre più attenzione alla fase di lavorazione a monte del processo di riciclo, vale a dire appunto la separazione. I separatori convenzionali, inclusi quelli ad aria utilizzati, per esempio, negli impianti di compostaggio, sono particolarmente adatti a separare le frazioni di diverso peso presenti nei rifiuti, ma si rivelano poco adatti quando si tratta di differenziare i componenti leggeri dopo la preselezione. AirLift viene proposto proprio in sostituzione dei separatori ad aria convenzionali per separare, per esempio, il film plastico dalla carta o per separare materiali plastici diversi gli uni dagli altri. Il sistema completo è costituito da tre parti: il nastro trasportatore ad alta velocità SpeedCon, che alimenta il materiale a una velocità fino a 4 metri al secondo nell’elemento centrale; il separatore AirLift; l’unità AirWheel, posizionata a valle di quest’ultimo. A seconda del modello, le larghezze di lavoro variano da 1000 a 3500 mm, dove la più ampia è in grado di gestire portate fino a 320 m3 all’ora con pezzature da 60 mm a 250 mm, mentre la capacità massima in uscita è di 5,6 tonnellate all’ora. I dispositivi di controllo automatico dell’apertura (gate) prevengono i blocchi di materiale in ingresso e in uscita ed es-
sendo regolabili in continuo garantiscono che l’altezza di passaggio possa essere regolata esattamente in base all’obiettivo specifico di separazione. Il nastro SpeedCon è inclinato verso il basso di 20° e corre direttamente sotto all’aspiratore, così che il flusso d’aria possa penetrare più facilmente sotto le parti leggere e l’inclinazione impartisca una traiettoria balistica a tutti i componenti in ingresso. Il controllo integrato può regolare la curva di incidenza o la distanza di lancio, variando la velocità del nastro e adattandola con precisione al processo. A seconda del materiale in ingresso, è possibile ottenere livelli di purezza superiori al 95%. Di conseguenza, il sistema riduce considerevolmente i costi di smaltimento e aumenta l’efficienza di quelli del processo di riciclo. La separazione del film dalle plastiche miste, facilita il funzionamento della selezionatrice NIR e ne migliora nettamente MACCHI_ADV_ISTIT_MACPLAS ITALIA 172X125mm IT 60.ai 1 10/03/21 10:22 i risultati.
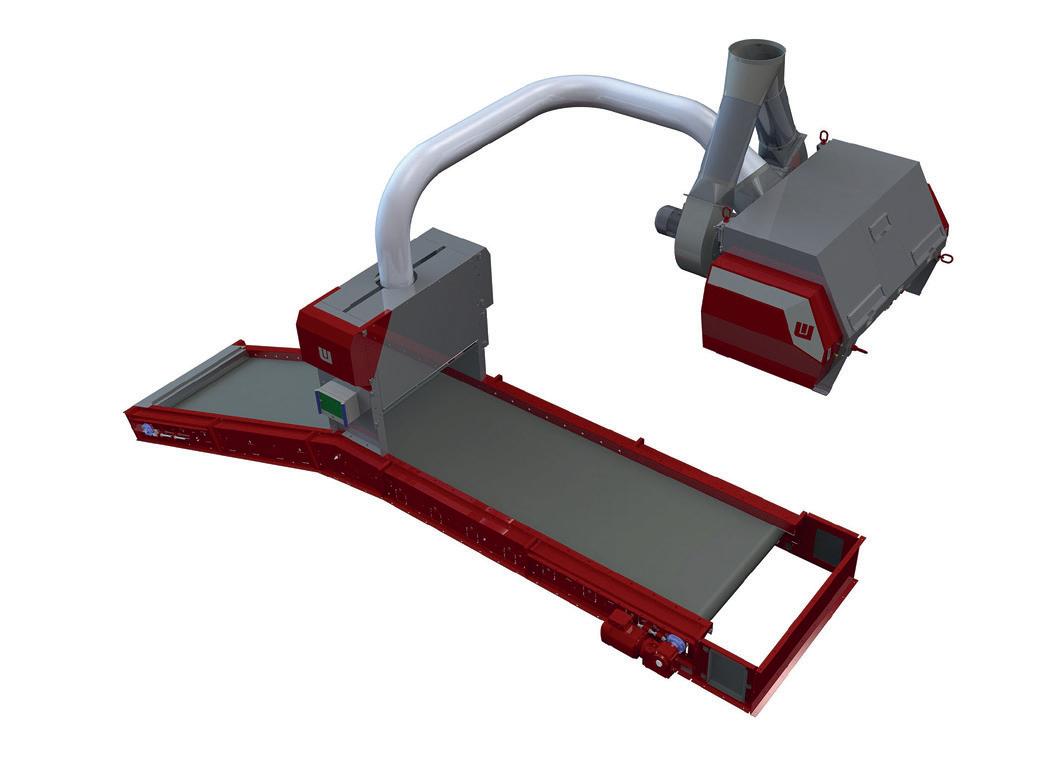
We take you to the top of extrusion
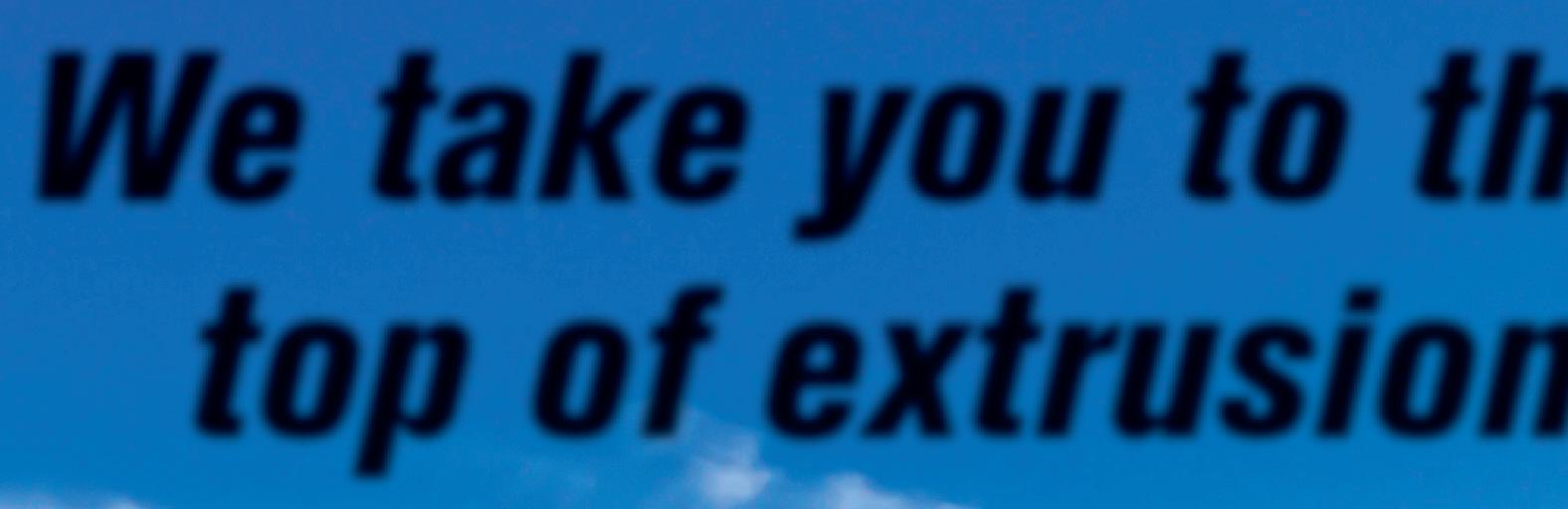
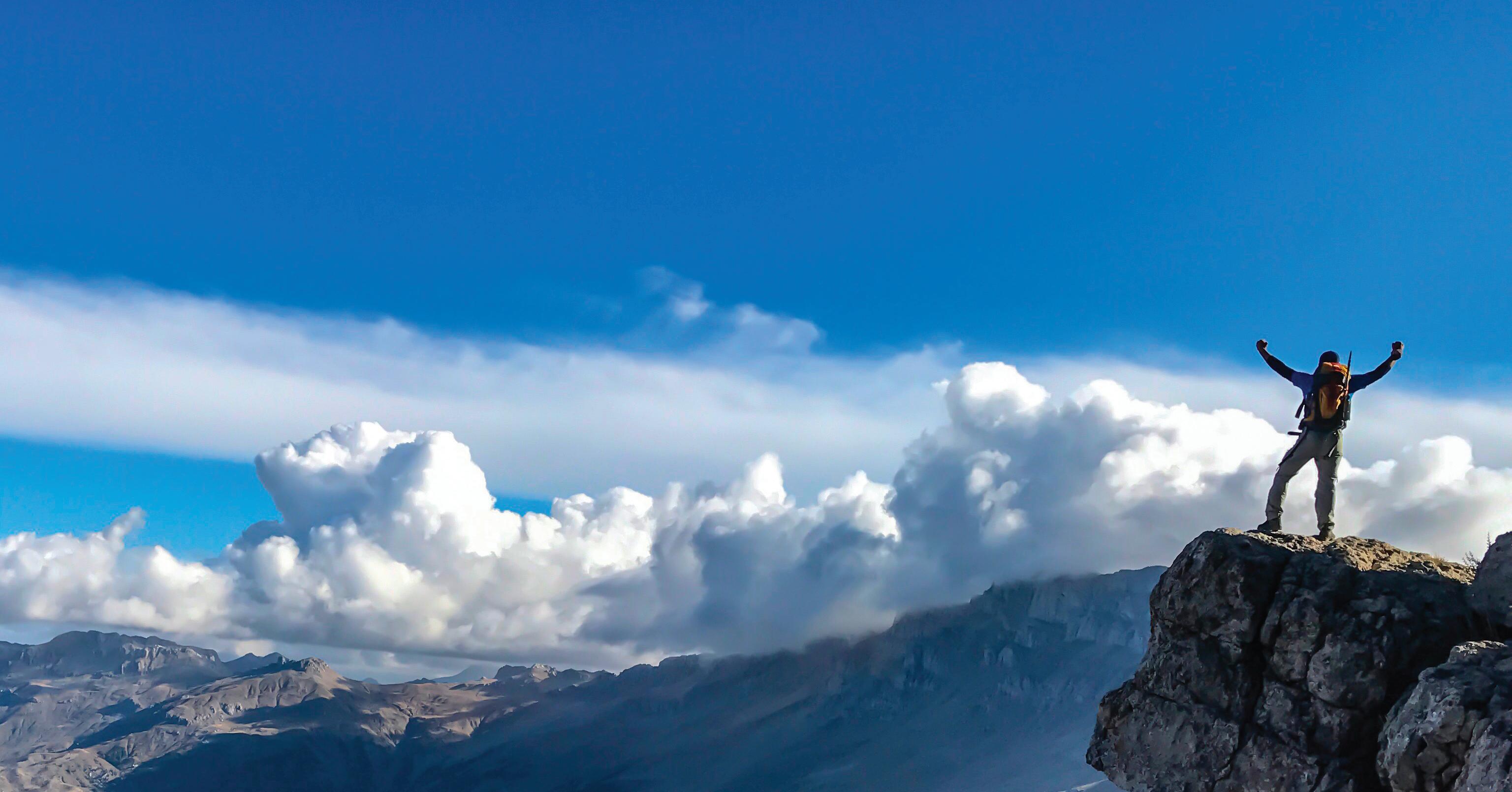
Macchi S.p.A. Via Papa Paolo VI, 5 21040 Venegono I. (VA) Italy
Tel. +39 0331 827 717 E-mail: macchi@macchi.it www.macchi.it
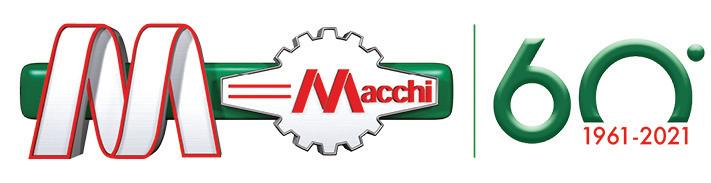
MASOTINA E TOMRA SORTING RECYCLING

SELEZIONE DI RIFIUTI PLASTICI SEMPRE PIÙ SU MISURA
L’AZIENDA LOMBARDA MASOTINA SELEZIONA E RECUPERA TONNELLATE DI PLASTICA, PROVENIENTE PRINCIPALMENTE DALLA RACCOLTA DIFFERENZIATA, GRAZIE ALLA TECNOLOGIA DI 32 MACCHINE SELEZIONATRICI AUTOSORT DI TOMRA SORTING RECYCLING. L’AGGIORNAMENTO ALLA NUOVA GENERAZIONE DELLA TECNOLOGIA TOMRA RENDE LA SELEZIONE ANCORA PIÙ “SARTORIALE”
Grazie a uno dei maggiori centri europei per la separazione e la selezione di rifiuti plastici, provenienti principalmente dalla raccolta differenziata, Masotina tratta i rifiuti urbani a prevalente componente plastica come una vera risorsa, preparandoli al riciclo e al successivo riutilizzo in base alle specifiche dei consorzi Corepla, Coripet e Conai. Per questo scopo l’azienda si avvale di 32 selezionatrici di Tomra Sorting Recycling, tutte utilizzate nel centro di Corsico, alle porte di Milano, uno dei tre di cui dispone Masotina, autorizzato a lavorare ogni anno 250 mila tonnellate di plastica post consumo. “Nel 2011, quando l’impresa è stata acquisita da Pioneer Point Partners, sono stati avviati importanti investimenti in management e tecnologia per diventare un gruppo primario nel settore del recupero e della valorizzazione della plastica”, commenta il direttore generale Sebastiano Chizzali. Investimenti in tecnologia che hanno coinvolto le selezionatrici Autosort di Tomra Sorting Recycling, uno dei principali costruttori di tecnologia di selezione a sensori che detiene il 65% del mercato a livello mondiale. Le macchine sono entrate in funzione nell’impianto nel 2014, con una linea di trattamento e una di preselezione, e nel 2019 ne sono state aggiunte altre per avviare due ulteriori linee, per un totale attuale di 32 Autosort. La configurazione dell’impianto è molto articolata e flessibile; un’abbinata che consente di trattare i flussi di plastiche provenienti dalla raccolta differenziata e dai principali consorzi di filiera e sistemi EPR, sia per polimero che per colore. La tecnologia a sensori è stata scelta per ottimizzare i processi di selezione. “Abbiamo un notevole numero di lettori ottici Tomra e ne siamo molto soddisfatti. Sono 16 sulla linea principale (polimeri), 12 su quella storica, 4 sulla linea di preselezione comprendente la linea del Tetra Pak”, racconta Francesca Romana Febbo, direttrice qualità, ambiente e sicurezza di Masotina. Ad oggi, la linea principale
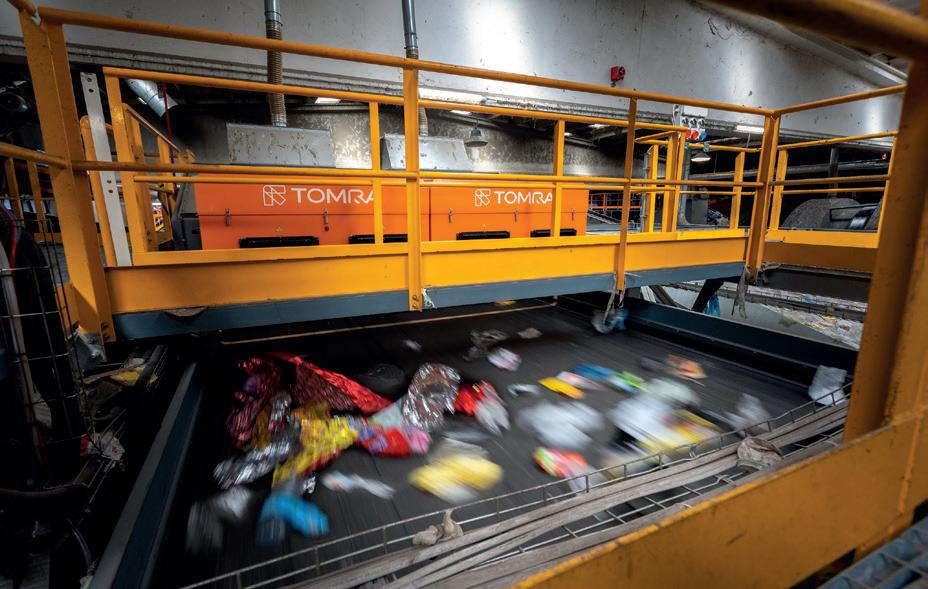
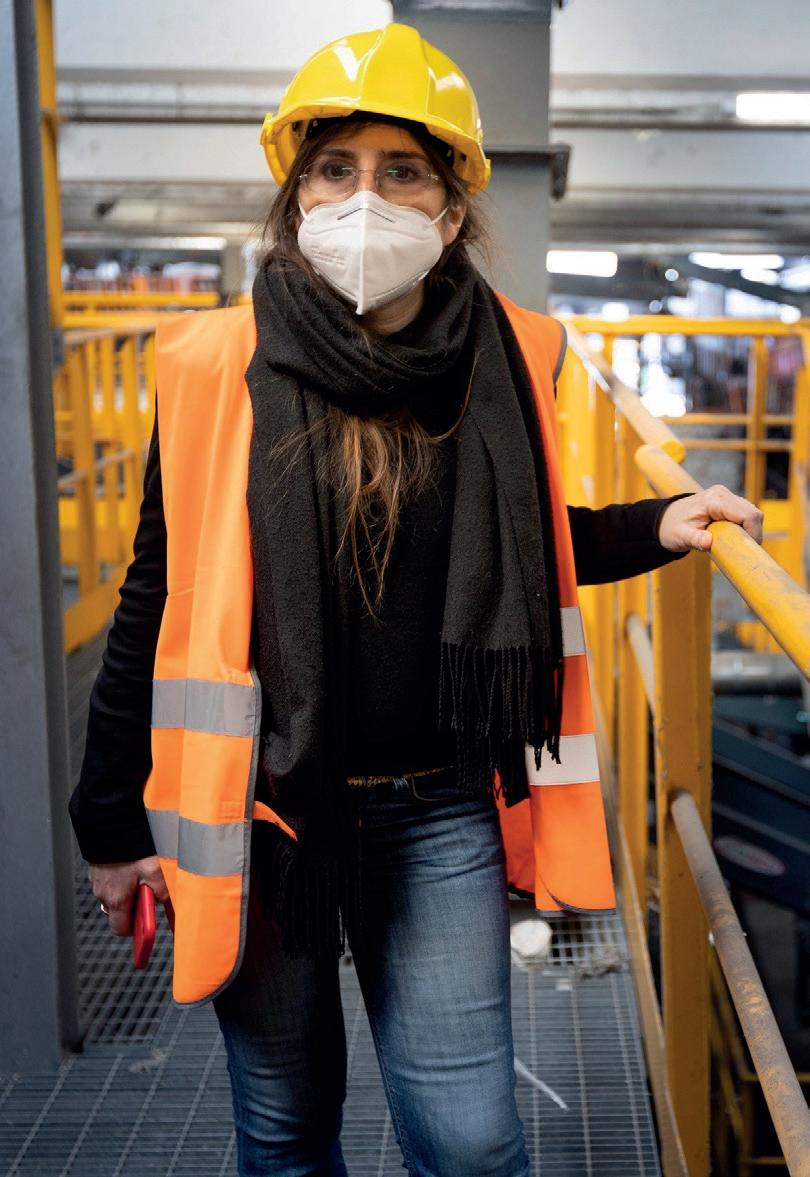
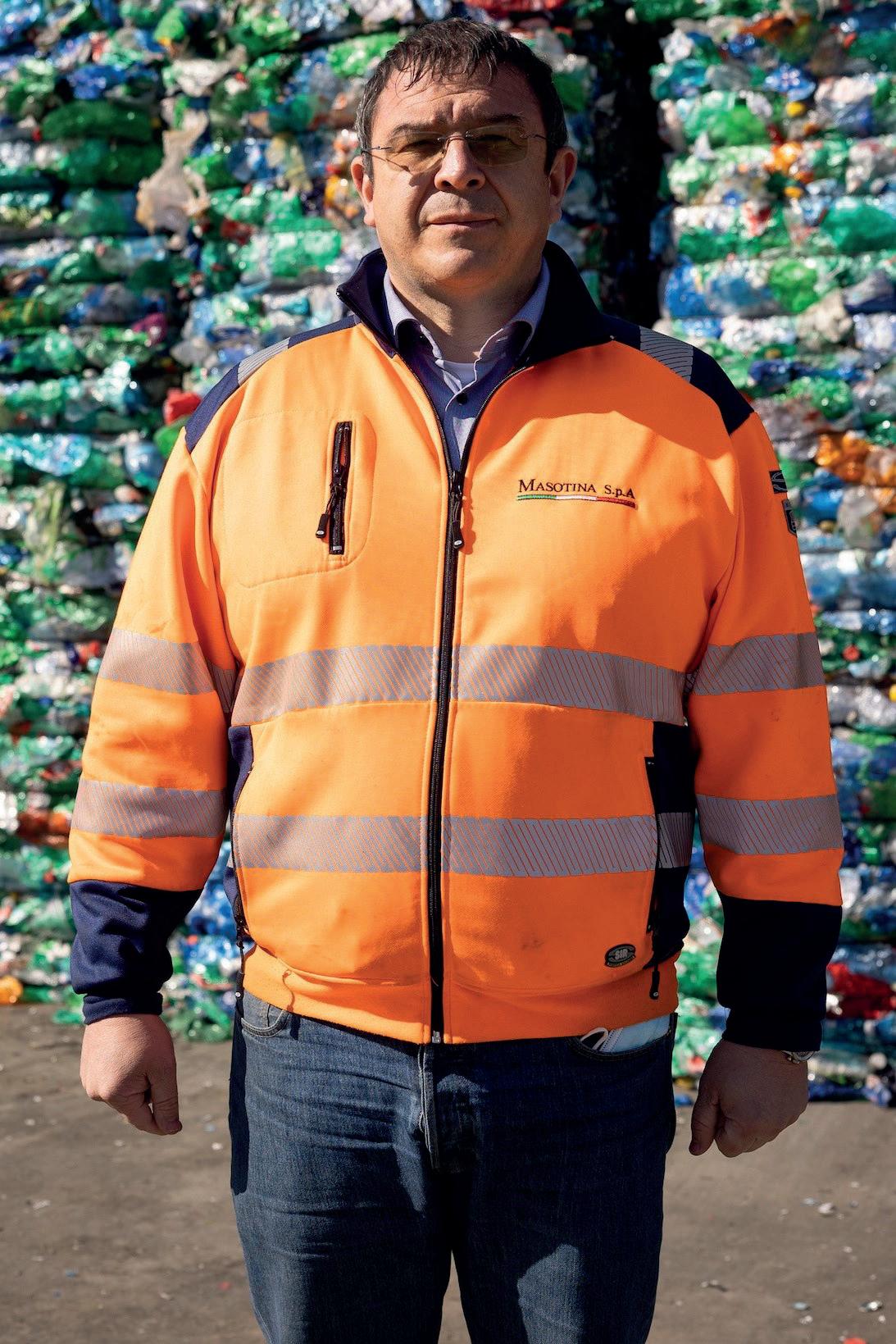
può trattare 15 tonnellate all’ora, quella storica tra 7 e 10, quella di Tetra Pak 4 tonnellate all’ora. Grazie alla selezione molto accurata effettuata dalle Autosort, oltre alle vaschette in PET monostrato, anche quelle multistrato recuperate dall’impianto di Masotina sono state ammesse nel vPET (ottenuto cioè mediante processo da vaschetta a vaschetta) da Corepla. Uno dei lettori Autosort è dedicato alla selezione del vPET, consentendo di distinguerlo dal PET delle bottiglie. Oltre alla precisa lettura del PET monostrato, la selezione delle vaschette è quintuplicata in volume: dato importante in relazione a un flusso che precedentemente non trovava una facile recuperabilità e veniva selezionato manualmente.
AUTOSORT, ANCHE IN VISTA DI ULTERIORI SVILUPPI AZIENDALI
Le macchine Autosort a sensori spettrometrici abbinano sensori NIR (lunghezze d’onda vicine all’infrarosso) e VIS (lunghezze d’onda nel campo del visibile) in un sistema di selezione modulare che consente di riconoscere e separare con esattezza e alla massima velocità una gran quantità di materiale, in base al tipo e alla composizione, ottenendo frazioni di elevata purezza. All’interno dell’impianto, la tecnologia NIR consente la selezione in base al tipo di polimero e quella VIS in base al colore (nel caso del PET). Ultimamente, Masotina ha sostituito quattro Autosort con l’ultimissima generazione delle selezionatrici, con riscontri molto positivi. È stato testato il nuovo sistema di classificazione, che consente una personalizzazione più mirata e una semplice scelta della priorità di selezione dei materiali, rilevando sia un incremento nella resa dal 5 al 10% sia un miglioramento del 2-3% in termini di qualità del prodotto selezionato. I riscontri positivi porteranno entro il 2021 alla sostituzione di altri due lettori, dal modello precedente alla nuova generazione di Autosort. L’azienda ha contrattualizzato anche il servizio di manutenzione Tomra Care. In futuro Masotina punta a terminare la filiera del riciclo al proprio interno fino alla produzione di scaglie dei principali polimeri. Per questo sta completando le fasi previste per l’autorizzazione e sta già pensando a una linea dedicata con tecnologia Tomra per il recupero di scaglie. “A quel punto potremo anche testare altre configurazioni di sensori, come Autosort con pacchetto Fines e con tecnologia Deep Laiser per la selezione delle plastiche nere, il cui inserimento è previsto per quest’anno”, aggiunge Chizzali.
Sebastiano Chizzali e Francesca Febbo, rispettivamente direttore generale e direttrice qualità, ambiente e sicurezza di Masotina
SELEZIONARE UN CAMPO DA CALCIO IN MENO DI 15 MINUTI
Con un massimo di 320 mila punti di scansione al secondo, i sensori ad alta risoluzione di Autosort raccolgono in tempi rapidissimi dati relativi a molteplici caratteristiche, per garantire l’identificazione precisa di un’ampia gamma di materiali. Per dirla con un’immagine efficace: la selezionatrice ottica di Tomra può analizzare e differenziare l’equivalente di un campo da calcio coperto di rifiuti in meno di 15 minuti. Autosort combina caratteristiche e tecnologie all’avanguardia in un’unica macchina. Compatta e flessibile nella costruzione, permette una semplice integrazione in impianti esistenti o nuovi. Grazie alla tecnologia Flying Beam (sistema NIR con scansione puntiforme), è garantita un’eccellente distribuzione omogenea della luce, per un migliore rilevamento e monitoraggio su tutta la larghezza del nastro, distinguendo anche le più sottili differenze molecolari dei materiali che scorrono lungo la linea. Nell’ultima generazione di Autosort è integrata di serie anche la tecnologia Sharp Eye, che assicura un miglioramento dell’efficienza luminosa e della nitidezza di selezione, facilitando la separazione delle frazioni difficili da selezionare, come il PET delle bottiglie da quello delle vaschette. L’integrazione opzionale della tecnologia Deep Laiser consente inoltre il rilevamento di materiali precedentemente non rilevabili e aumenta ulteriormente i livelli di purezza della selezione.
Pipe bends & Couplings stainless steel pipe bends and aluminium couplings suitable for vacuum and pressure conveyors stainless steel pipe bends in all common pipe dimensions from 38.0 x 1.5 mm till 204.0 x 2.0 mm; radii: 75, 250, 300, 500, 800, 1.000, 1.200 and 1.500 mm (AISI 304) highly wear-resistant pipe bends: glass pipe bends and HVA NIRO® stainless steel pipe bends - immediately, from stock HS Umformtechnik GmbH D-97947 Grünsfeld Germany Phone +49 (0) 93 46 / 92 99-0 Fax +49 (0) 93 46 / 92 99-200 www.hs-umformtechnik.de
FAKUMA Hall A7 / booth 7505
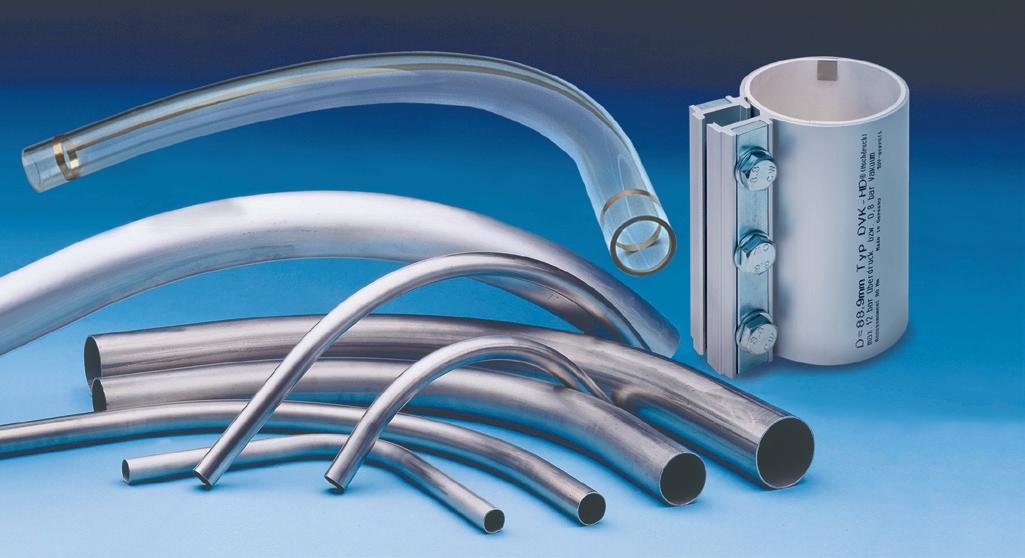
SORTCO SI AFFIDA A SIKORA
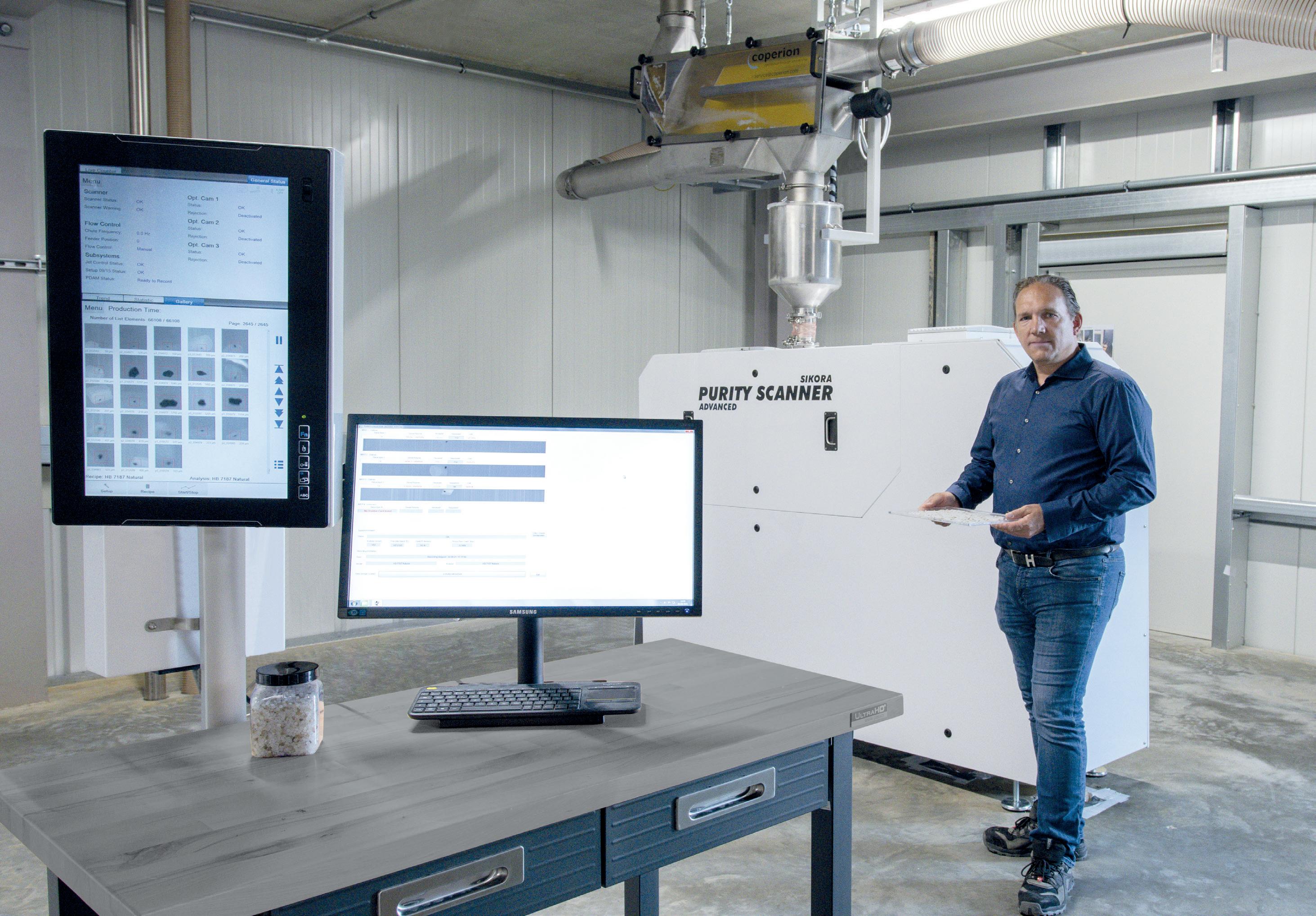
ISPEZIONE E RILEVAMENTO ONLINE DELLA PUREZZA DEI MATERIALI
SORTCO UTILIZZA DUE SISTEMI PURITY SCANNER ADVANCED DI SIKORA NEL SUO NUOVO CENTRO DI ASSISTENZA ALL’AVANGUARDIA PRESSO LA SEDE DI NIEDERZISSEN, IN GERMANIA. GRAZIE A QUESTI SISTEMI, IL MATERIALE GRANULATO PUÒ VENIRE CONTROLLATO OTTICAMENTE AL 100%, ELIMINANDO AUTOMATICAMENTE TUTTE LE IMPURITÀ FINO A DIMENSIONI DI 50 MICROMETRI
Le materie plastiche tecnicamente impegnative, come quelle utilizzate nelle industrie medicale, aeronautica o automobilistica, richiedono i migliori standard di qualità e un controllo e una lavorazione affidabili. Di conseguenza, i requisiti di purezza dei materiali in questi casi sono sempre molto elevati. Sortco è un’azienda specializzata nelle operazioni di selezione per conto terzi e prepara i granulati plastici secondo le esigenze dei committenti. Nel suo centro di assistenza, inaugurato nella primavera del 2021, l’azienda effettua la selezione di materie plastiche standard e tecnopolimeri difficili da trattare dal punto di vista ottico. A tale scopo, utilizza due sistemi d’ispezione e rilevamento online forniti da Sikora.
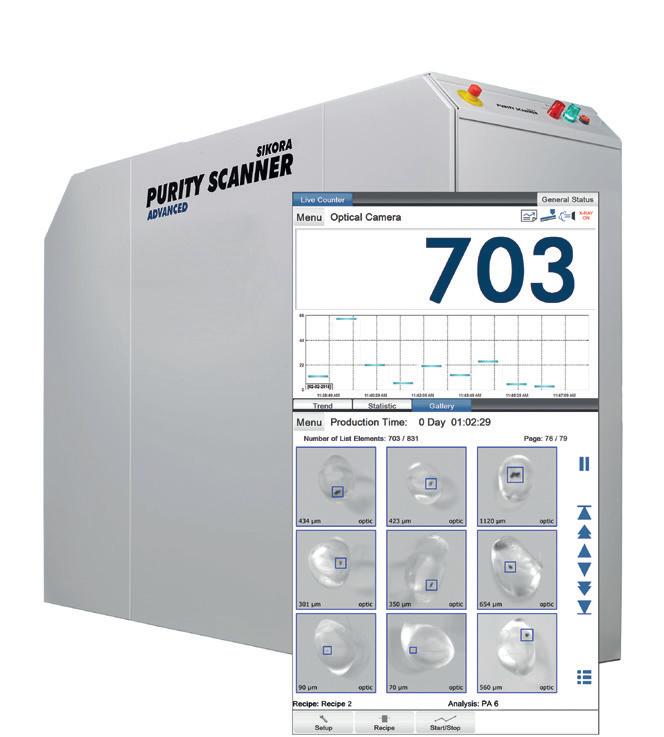
RILEVAMENTO SENZA DIFFICOLTÀ
la base delle migliori prestazioni di rilevamento, dell’eccellente capacità di analisi e della vicinanza fisica, un aspetto non irrilevante per noi”, afferma Hilger Groß, responsabile vendite e qualità di Sortco. “Purity Scanner Advanced viene in genere utilizzato dove altri sistemi di rilevamento vanno in difficoltà. Vale a dire, nel rilevamento di difetti ottici molto piccoli, fino a dimensioni di 50 micrometri”, precisa Groß. “Sortco utilizza Purity Scanner Advanced soprattutto per la selezione di granulati trasparenti, con colore naturale e anche colorati, seppure in misura minore. L’attenzione si concentra sui materiali non rinforzati che, dopo la selezione, vengono impiegati in applicazioni ottiche di alta qualità”. Ogni sistema è dotato di tre telecamere che rilevano anche le più piccole impurità ottiche, con dimensioni minime di 50 micrometri, e le espellono automaticamente con un soffio d’aria compressa. Se necessario, Purity Scanner Advanced può anche essere dotato di telecamera a raggi X per il rilevamento di particelle metalliche. “Le macchie nere sono al centro
L’hardware e il software del Purity Scanner Advanced installato presso Sortco (foto di apertura)
del nostro lavoro di selezione. Inoltre, rimuoviamo tutti i granuli di colore diverso”, spiega ancora Groß. “Come fornitore di servizi, Sortco si confronta ogni giorno con nuovi materiali e contaminanti vecchi e nuovi. Ciò significa che dobbiamo anche riuscire ad adattare Purity Scanner Advanced a prodotti in continua evoluzione, oltre che alle esigenze dei clienti. Creiamo quindi una ricetta speciale per ogni prodotto, che si presta anche a essere ripresa e adattata in operazioni future”. Durante la selezione, Purity Scanner Advanced registra automaticamente il numero dei difetti, le loro dimensioni minime, l’area contaminata, oltre alla classe dimensionale del difetto, che può essere liberamente regolata e specificata in base alle esigenze del cliente. Inoltre, il sistema rileva la frequenza delle deviazioni di colore.
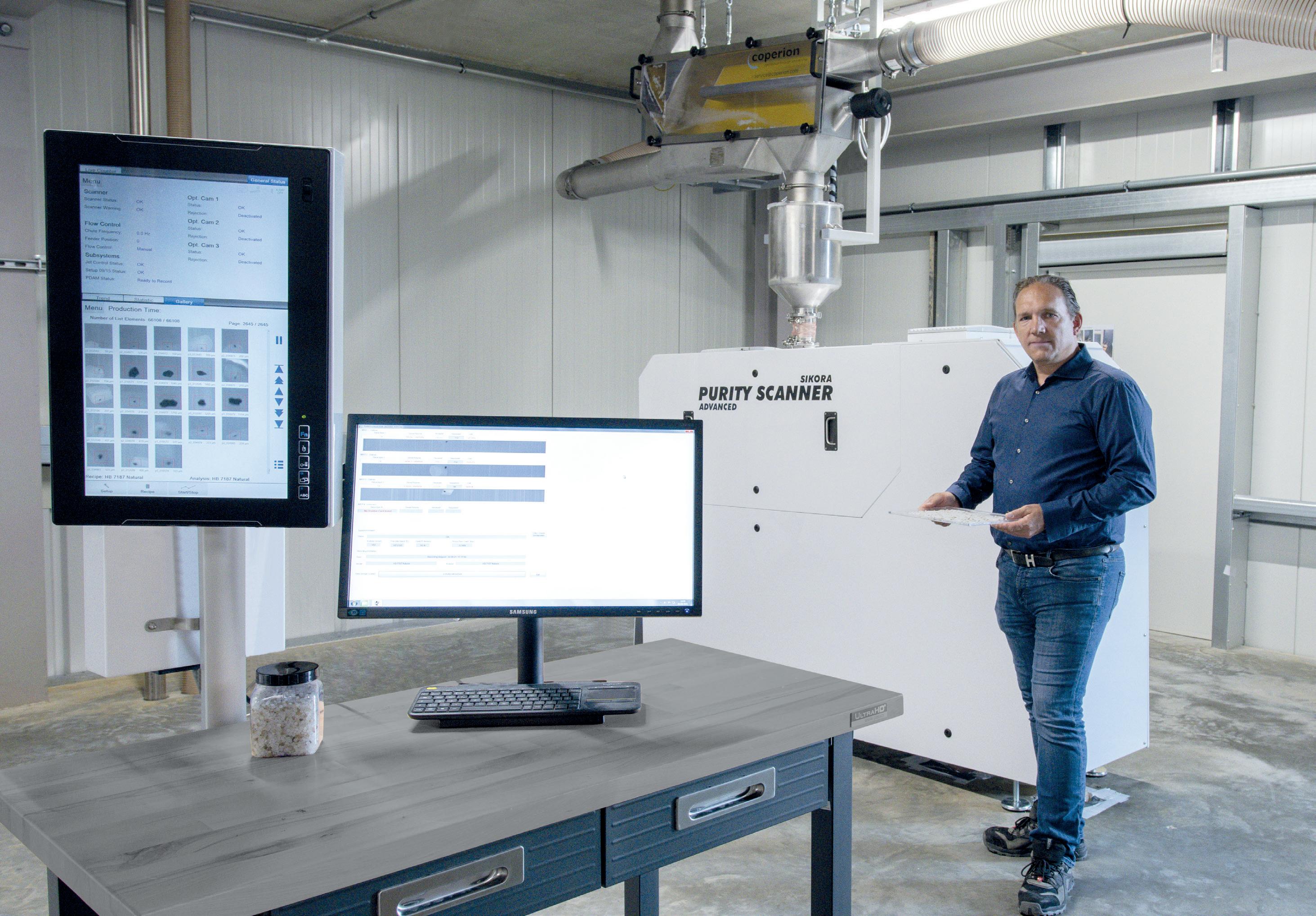
UNA SOLUZIONE PER RISPARMIARE
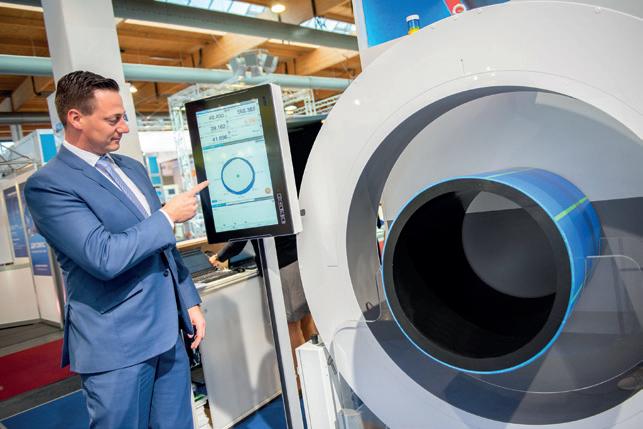
“I nostri clienti apprezzano il fatto che comprendiamo i problemi che hanno quando si tratta di identificare la causa e l’effetto dei difetti, che mettiamo a disposizione il nostro know-how, che offriamo la soluzione appropriata e che ci occupiamo di tutto quanto necessario per garantire la qualità ottimale del materiale”, riassume Groß. “Affidandoci il servizio di selezione ottica, i clienti contribuiscono in misura significativa a proteggere l’ambiente e a evitare gli sprechi”. La raccomandazione alle aziende interessate alla selezione, ma che la considerano tuttora come un’opzione, è quella di dare un’occhiata più da vicino ai prodotti che hanno recentemente evidenziato costi di recupero più elevati. “Il semplice confronto tra i costi della selezione e i potenziali risparmi sembrerebbe non lasciare spazio a questa soluzione. Tuttavia, se il cliente tiene conto anche del possibile calo di vendite, della perdita d’immagine e di tutti i costi determinati dalle risorse consumate inutilmente, come l’energia, le macchine, il personale, i materiali, i prodotti ecc., si ricrede in fretta. I vantaggi della selezione superano sempre gli svantaggi”, conclude Hilger Groß. All’ultima edizione della fiera Fakuma, Sikora ha presentato le sue tecnologie di misura e controllo dedicate al settore dei tubi, oltre ai sistemi online e offline per l’ispezione, la selezione e l’analisi dei granulati plastici. Nell’ambito dell’ispezione e della selezione in linea dei granuli, ha presentato il sistema Purity Scanner Advanced, di cui si parla nell’articolo, mentre ha offerto test gratuiti dal vivo sui materiali mediante l’impiego di Purity Concept V. La tavola luminosa ispeziona in pochi secondi e automaticamente il materiale collocato su di un vassoio per campioni, mediante una telecamera a colori, e valuta le immagini registrate. Il sistema rileva le bruciature e le deviazioni di colore con dimensioni minime di 50 micrometri ed evidenzia a colori la contaminazione sul monitor del sistema e, in parallelo, anche sul supporto del campione tramite un proiettore. Per un controllo di qualità al 100% nelle operazioni di estrusione dei tubi, Sikora ha poi presentato Centerwave 6000, basato sulla tecnologia delle onde millimetriche. Il dispositivo misura con precisione il diametro e l’ovalità, oltre allo spessore di parete, il profilo interno e la deformazione del tubo. Questa tecnologia di misura non richieIl sistema de alcuna calibrazioCenterwave 6000 ne e non è soggetta a in dimostrazione a Fakuma influenze come quelle determinate dalla temperatura del materiale plastico.
EFFICIENT ECONOMICAL RELIABLE

POWERFUL FILTRATION
STRONG STAND-ALONE FILTERS FROM EREMA
EREMA has been the innovation leader for highly effi cient plastics recycling systems for 35 years. Our melt fi lters are at the heart of them. Robust, safe and with high throughput –even with high degrees of contamination. Filters made by EREMA have proven their reliability for decades in the toughest recycling conditions. With our new brand POWERFIL you can now use our high-performance filters for your existing extrusion system. Plug in experience. Plug in performance.
www.powerfi l.com
NEWS
PIATTAFORMA SDC DI STADLER
Dagli impianti di selezione al cloud e ritorno
La piattaforma cloud-based SDC è stata sviluppata da Stadler per raccogliere i dati operativi dalle macchine e dai sensori degli impianti di selezione dei rifiuti dell’azienda stessa e memorizzarli nel cloud, così da disporne in qualsiasi momento e luogo attraverso un portale web. SDC sfrutta automazione e IIoT (Industrial Internet of Things) per ottimizzare e aumentare l’efficienza dei processi negli impianti di selezione di Stadler e fornire un supporto migliore e più rapido agli utilizzatori, anche grazie a interventi da remoto. È ugualmente efficace in tutti i tipi d’impianti di selezione e può essere implementata in quelli esistenti. I dati acquisiti dal sistema sono un utile strumento per migliorare il processo, identificare eventuali colli di bottiglia o problemi e agire per risolverli rapidamente. L’analisi dei dati storici può aiutare a ottimizzare le prestazioni delle macchine e rivelare opportunità di miglioramento dell’efficienza dell’impianto. Il sistema segnala dove si trova l’errore nel diagramma di flusso dell’impianto con una chiara indicazione del nome del dispositivo che presenta un guasto. I tempi di inattività sono ridotti al minimo grazie al monitoraggio dello stato e delle prestazioni della macchina e all’assistenza rapida: un vantaggio importante per l’utilizzatore. SDC ha una sezione dedicata alla documentazione completa e aggiornata relativa a ciascuna delle macchine dell’impianto. Questa comprende non solo schede tecniche e manuali operativi, ma anche un catalogo dei pezzi di ricambio. Al momento di fare un ordine, è possibile identificare facilmente il pezzo corretto grazie alla fotografia, alla descrizione e al numero del pezzo a catalogo. La sezione documentazione offre anche video tutorial preparati dal Service Team Stadler, che illustrano le operazioni di manutenzione tipiche degli utilizzatori.


Soluzione per presse a iniezione Regolazione e manutenzione semplificate
L’innovativa soluzione integrata IN-4000 SET, per la misurazione della pressione d’iniezione e della forza di contatto dell’ugello, è stata sviluppata da Gefran e Sensormate (azienda del Gruppo Gefran specializzata nella misurazione della forza su macchine per stampaggio a iniezione e pressofusione e su presse industriali) per semplificare la regolazione e la manutenzione delle presse a iniezione. “Regolare con assoluta precisione e controllare puntualmente sia la pressione d’iniezione che la forza di contatto dell’ugello sullo stampo, principali variabili coinvolte nel processo, è di fondamentale importanza per coglierne appieno i benefici e garantire qualità costante e affidabilità della produzione. Con gli attuali metodi, la pressione d’iniezione viene misurata indirettamente durante il funzionamento e viene determinata attraverso una conversione corrispondente nel sistema di controllo. I sensori di forza utilizzati a tale scopo, come le celle di carico a membrana nel caso degli azionamenti elettrici o i sensori di pressione per quelli idraulici, devono quindi essere regolarmente confrontati con la pressione d’iniezione effettiva e, se necessario, corretti con parametri appropriati, con conseguente dispendio di tempo e risorse”, spiega Piero Tempini, direttore generale di Sensormate. Per questa ragione, Gefran, in collaborazione con i principali costruttori di presse a iniezione, ha potenziato il sistema plug-and-play IN-4000 SET, composto da sensori compatti, adattatori magnetici e unità di visualizzazione, per misurare direttamente la pressione (IN Sensor) e la forza di contatto degli ugelli (DAK Sensor). Le sonde possono essere montate singolarmente o insieme, con fissaggio magnetico, tra stampo e ugello d’iniezione. Il principale vantaggio risiede nel tempo per l’installazione, la misurazione e la rimozione, eseguite facilmente da un solo operatore, che risulta ridotto da diverse ore a 30-60 minuti. IN Sensor misura la pressione d’iniezione in prossimità dell’ugello fino a 4000 bar, con temperatura di melt fino a 400°C. Può raggiungere i 230°C, per assicurare che la massa fusa nella camera conica rimanga liquida. Un disco isolante tra sensore e adattatore magnetico consente il disaccoppiamento termico delle parti della macchina, favorendo una distribuzione uniforme della temperatura e un’elevata accuratezza della misurazione. Il riscaldamento opzionale del sensore è particolarmente interessante per le misurazioni multiple, con diversi livelli di pressione d’iniezione, per esempio 500, 1000, 1500 e 2000 bar. Per la misurazione regolare, precisa e ripetibile della forza di contatto dell’ugello nelle presse elettriche, Gefran offre il sensore DAK, robusto e di semplice utilizzo. L’unità di visualizzazione Gefran, con regolatore di temperatura e display di pressione preimpostati, è collegata sia ai sensori IN e DAK che al nastro di riscaldamento. I due modelli possono essere commutati attraverso un semplice interruttore.
IN-4000 SET è stato sviluppato da Gefran e Sensormate per la misurazione della pressione d’iniezione e della forza di contatto dell’ugello

Accordo Acea Ambiente-Recycleye Controllo qualità automatizzato nella separazione dei rifiuti
In virtù di un recente accordo, il sistema Recycleye Vision della startup Recycleye è stato adottato da Acea Ambiente per automatizzare il controllo qualità negli impianti di separazione dei rifiuti post consumo. Recycleye Vision, un sistema di visione con intelligenza artificiale, è in grado di migliorare le prestazioni della visione umana nell’identificare e classificare tutti gli articoli nei flussi di rifiuti in base a materiale, oggetto e persino marchio. Inoltre, è in grado di apprendere il rilevamento di nuovi articoli, consentendo al sistema robotico di raccolta di adattarsi ai cambiamenti della composizione dei rifiuti senza bi-
sogno di aggiornamenti manuali. In questo modo, Acea potrà ottenere in tempo reale informazioni sui propri impianti, garantendo costantemente un livello elevato di purezza del prodotto. “La gestione e la valorizzazione dei rifiuti fa parte dell’impegno di Acea Ambiente per l’economia circolare. La nostra collaborazione con Recycleye, per sviluppare il primo sistema automatizzato di controllo qualità in Italia, aumenterà il volume di materiali riciclati. Recycleye sta sviluppando tecnologie all’avanguardia nella gestione dei rifiuti e siamo consapevoli dell’importanza e dell’efficacia di questo accordo, basata sulla ricerca e l’innovazio2021_NEW-DGTS_01_172x125-Btr.pdf 1 12/02/21 17:40 ne”, ha commentato Giovanni Vivarelli, presidente di Acea Ambiente. “Questa collaborazione è un altro esempio tangibile del cambiamento che sta avvenendo nel settore della gestione dei rifiuti: il cambiamento che speravamo di ottenere quando abbiamo fondato Recycleye. Consentire ad Acea Ambiente di mantenere il proprio impegno verso un’economia circolare con la nostra tecnologia è un altro passo verso la risoluzione della crisi dei rifiuti”, ha aggiunto Peter Hedley, CTO di Recycleye.
Selezione senza (a sinistra) e con (a destra) sistema di visione con intelligenza artificiale




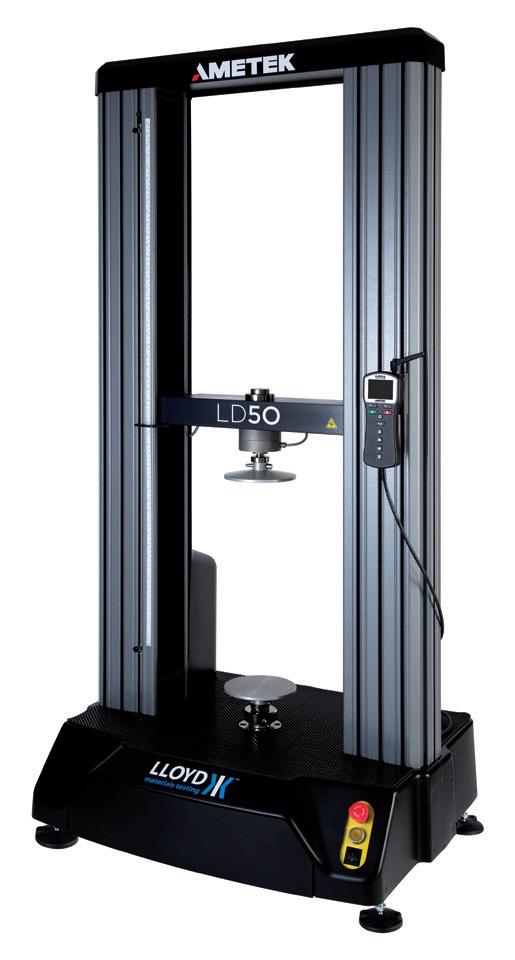
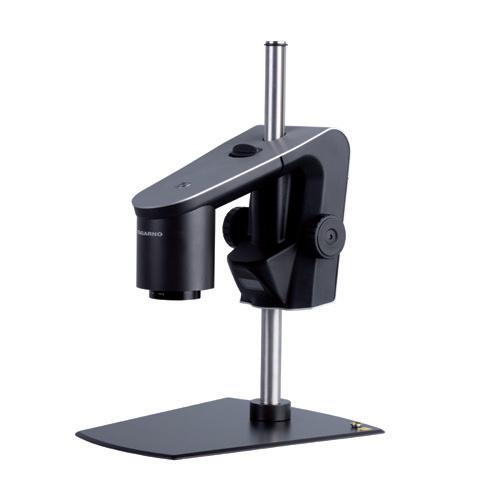