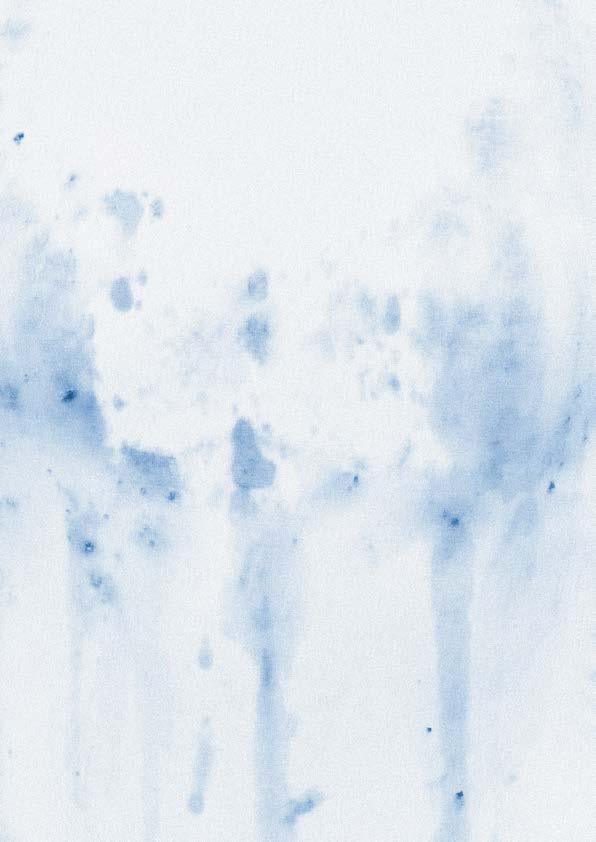
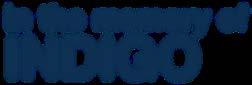
“Karm,” in Thai, holds a twofold meaning: it refers to the captivating “indigo color” and also the name of a native plant that thrives in the lush forests across different regions of Thailand. Thai indigo, a cherished natural dye, has been passed down through generations, drawing its essence from the leaves of the indigo plant (Indigofera tinctoria) and a blend of local ingredients that unlock the distinct richness of its blue hues.
As I delve into the craft of creating the indigo tank, the journey commences with the collection of indigo plant leaves during the monsoon season, followed by a process of fermentation in water. This meticulous endeavor yields a profound and vibrant blue pigment, which is then meticulously extracted and employed to infuse textiles with its vibrant shades.
The indigo tank is alive. It is a microcosm that teems with microorganisms coexisting alongside the indigo. Formed through the alchemy of ashes, herbs, and a touch of sugar, this organic compound serves as a precursor to indigo dye. When nurtured and tended with care, the resulting color can endure for years, breathing life into the fabric it adorns.
Through my exploration of this traditional craft, I am rejuvenating techniques that blend seamlessly with the indigo-dyed fabric tradition. By harnessing the crystallisation of indigo, I create artefact captured the movement of the fabric This transformative process imbues the indigo with the power to evolve over time, symbolizing the craft’s need to adapt and grow, lest it fade away.
Overview of the process of making Thai indigo, from harvesting the leaves to dyeing the fabric:
The journey begins with the careful harvesting of indigo leaves, a crucial step in the creation of Thai indigo. This task is usually undertaken during the rainy season in Thailand when the leaves are at their fullest and most abundant.
Once the leaves have been collected, they undergo a transformative process known as fermentation. They are delicately soaked in water and left to ferment for several days. It is during this period that the naturally occurring bacteria present in the water work their magic, breaking down the plant matter and releasing
This fermentation process plays a vital role in extracting the essence of indigo, unlocking its true potential as a dye. The patience and time devoted to this step are essential in capturing the vibrant and enduring shades that Thai indigo is renowned for.
With the leaves fermented and the blue pigment unleashed, the stage is set for the next chapter in the indigo-making process. This is where the magic happens, where fabrics are immersed in the indigo dye bath, eagerly awaiting their transformation into radiant blue masterpieces.
Straining the liquid: Once the fermentation process is complete, the liquid is strained to remove any solids.
Adding other ingredients: Depending on the specific recipe being used, other ingredients may be added to the liquid at this point. For example, lime juice may be added to increase the pH and help the dye adhere to the fabric.
Additional ingredients may be added to the indigo tank during the dyeing process.
Tamerind juice: Tamerind juice is often added to the indigo tank to increase the pH of the solution. This helps the blue pigment adhere to the fabric fibres more effectively. Tamerind juice also helps to prevent the indigo from becoming too frothy during the dyeing process.
Ash water: Ash water, which is made by burning rice straw and mixing the ashes with water, is sometimes added to the indigo tank. Ash water helps to reduce the amount of oxygen in the solution, which can prevent the blue pigment from oxidizing and turning green.
Sugar: Sugar may be added to the indigo tank to help feed the bacteria that are responsible for breaking down the indigo leaves during the fermentation process.
Rice husks: Rice husks may be added to the indigo tank to help maintain the temperature of the solution. They also help to prevent the indigo from becoming too foamy during the dyeing process.
Natural oils: Some recipes may call for the addition of natural oils, such as sesame oil or coconut oil. These oils can help to create a softer, smoother finish on the fabric.
Each family may have their own unique recipes and techniques for making Thai indigo. The specific ingredients and proportions used can vary based on factors such as the local climate, water quality, and the particular strains of bacteria used for fermentation. The role of bacteria in the fermentation process for making Thai indigo.
The bacteria that live in the indigo bath are an essential part of the process of making Thai indigo. These bacteria are responsible for breaking down the indigo leaves and releasing the blue pigment. The specific strains of bacteria involved in the fermentation process can vary depending on the location and the specific recipe being used.
One of the most common bacteria used for indigo fermentation is the species Lactobacillus plantarum. This bacteria is naturally found in soil, plants, and fermented foods and is known for its ability to produce lactic acid during fermentation. Lactic acid helps to lower the pH of the indigo bath, which creates an optimal environment for the pigment to dissolve and bond with the fabric.
Fermentation can have a significant impact on the final colour and quality of the dye. For this reason, some dye masters carefully cultivate and maintain their own cultures of indigo bacteria, which they may have inherited from previous generations of dye masters. These cultures are often considered to be precious and valuable resources and are carefully guarded and passed down within families and communities.
To keep the bacteria in the indigo bath alive and healthy, there are several key factors that need to be considered:
Temperature: The temperature of the indigo bath should be kept within a specific range to ensure optimal conditions for the bacteria. In general, the temperature should be maintained between 25°C and 40°C, depending on the specific strain of bacteria being used.
Oxygen: The indigo bath should be kept in a relatively oxygen-free environment, as exposure to air can cause the blue pigment to oxidise and turn green. Some dye masters cover their indigo vats with a layer of oil or an airtight lid to minimise the exposure of the solution to oxygen.
pH: The pH of the indigo bath is important for creating an environment that is conducive to the growth of the bacteria. The pH should be kept between 9 and 10.5, which can be achieved by adding lime juice or other alkaline ingredients to the bath.
Nutrients: The bacteria in the indigo bath need a source of nutrients to thrive. Some recipes call for the addition of sugar, rice husks, or other organic matter to provide the bacteria with the necessary nutrients.
Maintenance: The indigo bath needs to be regularly stirred or agitated to help distribute the bacteria throughout the solution. Additionally, the indigo bath may need to be replenished with fresh leaves or other ingredients periodically to keep the bacteria active and healthy.
By carefully controlling these factors, the bacteria in the indigo bath can be kept alive and active for extended periods of time, allowing dye masters to produce high-quality indigo dye on an ongoing basis.
During this project, I had the amazing opportunity to meet Suparuk, a local from Sakhonakorn, which is famous for its indigo dyeing tradition in Thailand. It all started when she helped me source some condensed indigo pigment. We began chatting online and gradually developed a connection and got to know each other better. Interestingly, I discovered that she is one of the youngest people still actively involved in the indigo craft community in her hometown. So, when I finally had the chance to go back to Thailand, I made sure to plan a visit to meet her in person.
After a year of online messaging, we finally had the chance to meet in person. I booked an overnight coach ticket from Bangkok to Sakon Nakhon, a town in northeastern Thailand, which took around nine hours. Her small village was just a 40-minute drive from the town center.
When I arrived at her place, Suparuk, her father, and their friendly neighborhood granny were busy weaving indigo fabric on traditional looms. It was a cozy twostory wooden house with a spacious yard and an openair workspace on the ground floor, where Suparuk use as her workspace.
We had a delightful conversation on the patio underneath her home, surrounded by indigo tanks and looms dedicated to weaving. Suparuk shared that the art of indigo dyeing has been passed down from generation to generation in her family and the village she calls home. While she couldn’t pinpoint the exact time it began, she knew it had been handed down from her grandmother to her mother and, eventually, to her. The tradition has stood the test of time and remains an integral part of their cultural heritage.
As the youngest generation still working in this craft, Suparuk shared with me her story of how she, like many young people in Thailand, left her hometown after university and headed straight to Bangkok, the capital city, in search of better opportunities and a better life. After completing medical school, Suparuk worked as a nurse over 600 kilometres from her hometown for over 10 years. During that time,
Living and working in Bangkok for over a decade, Suparuk attended various workshops during her free time. Among them was a dyeing workshop, but she did not think much of it at the time nor see how it related to her family’s craft. However, everything changed when her mother fell seriously ill due to old age. Suparuk realised it was time for her to return home and care for her mother. As she reconnected with her family and the craft of indigo dyeing, she started to see the potential to improve and elevate what she already had at home using the knowledge she gained from her work experience. She delved into serious research on indigo dyeing, first by tapping into her family’s knowledge and later by collaborating with researchers and university professors.
She revealed that working with the locals is the most challenging part of her job. Despite growing up in the same community, she has realised that there is a significant generation gap between her and the people who have been practising this craft for their whole lives. Most of them are elders who resist any change that might happen. According to Suparuk, they are true masters in what they do, and they are content with their traditional techniques. They do not see the need to try new methods.
To give us a better understanding of the situation, she explained that indigo dyeing used to be a hobby for women in the area. As the main source of livelihood was farming and agriculture, cotton and indigo plants were the most common crops in the region. The community would produce cloth for themselves to wear while working in the fields. Indigo dye was the primary choice as it had the unique function of cooling the body temperature, making it ideal for making worker’s clothing.
Suparuk also shared another challenge she encountered with the craft, which is the uncontrollable nature of both the craft itself and the people who work with it. Like many natural dye colours, it is difficult to predict the outcome of each dyeing batch due to various variables, such as plant quality, temperature, and humidity, which cannot be fully controlled. Additionally, those who work with the craft do not always prioritise it as their main focus, as they may have other commitments such as religious ceremonies, funerals, or family gatherings that require their participation, causing the entire manufacturing process to come to a halt. These factors make it difficult to establish a fixed deadline for final production. Drawing from her experience working in the hospital, Suparuk believes that her strengths in management and working within a system can be applied to the production of the craft.
While the community may be content with the current state of the craft, Suparuk sees the potential for it to go further. The craft itself is organic and sustainable, as most of the ingredients can be sourced from the region, aligning with the trend of people being more aware of what they consume. To illustrate her point, Suparuk took me on a tour of her backyard, where she grows various local fruits such as papaya, banana, and tamarind, which are used to feed the indigo tanks. She explained that the process of making indigo dye is not just about the dyeing itself but also about the entire ecosystem that supports it.
During the interview, she expressed her concern about the future of the craft, stating that she worries about its continued existence. She emphasised that the only people who are currently masters of the craft are from the older generation and that if this trend continues, the beautiful, valuable, yet complex craft may one day disappear.
Suparuk’s passion for indigo dyeing is not just about the craft itself but also about its potential to create a sustainable ecosystem that benefits the community. She hopes to continue to explore new techniques and collaborate with researchers and organisations aiming to make her village a learning centre for people interested in Thai indigo dyeing to elevate the craft and take it to new heights.
My interest in the beauty of this endangered craft have grown since when I did my internship with local textile artisan 8 years ago, sparked my project to study the process of making an indigo colour in details. I was struck by the fact that life is inherent in most of the process, from the plant’s life before it is harvested to make the colour to the colour itself containing life. As a result, I aim to create a design that preserves the life cycle of the colour..
As previously mentioned, families have varying recipes for maintaining the longevity of their indigo tanks. Some use pure sugar obtained from local sugarcane, while others use sweetened local fruits, like bananas, to nourish the dye. Sugar plays a crucial role in the fermentation stage. The sugar is used as a food source for the bacteria that are responsible for creating the indigo pigment. During the fermentation process, the bacteria break down the sugar and produce a byproduct called indoxyl, which is then converted into indigo when it comes into contact with the air. Without the sugar, the bacteria would not have enough food to produce the indigo pigment, and the dyeing process would not be successful.
For this project, I conducted experiments by increasing the amount of sugar that was fed to the indigo tanks. I discovered that with enough sugar, it could transform into a preservative ingredient and undergo crystallisation at the end while still maintaining the indigo colour and dyeing ability.
Using the crystals produced from this process, I aim to challenge the fast-paced fashion industry with my heritage slow craft. The jewellery created gradually dissolves over time, delicately surrendering to the elements when exposed to weather. This gentle dissolution leaves behind a captivating indigo-colored mark on the fabric, forging a lasting memory between the cloth and our exquisite creations.
As time goes by, the jewelry undergoes a graceful transformation, mirroring the everevolving nature of life itself. The mark on the cloth, once vivid, gradually fades, symbolising the wearer’s unique daily experiences. It is a beautiful testament to the wearer’s individual journey, capturing the essence of their personal story within the fabric and jewellery.
Interviewer: Can you tell me how indigo dyeing started here initially?
Suparuk: It all began in the royal project back in 1979. In 1982, the project provided each household in the village with 400 baht and encouraged them to save 10 baht per day. In 1991, a group of housewives was formed using the accumulated savings. By 1995, the villagers had started dyeing fabric and planting indigo. Initially, the indigo was used for personal consumption, with any excess being sold. In 2005, the community enterprise specializing in fabric weaving and indigo dyeing was established. This was because the farmers grew their own cotton and indigo, and the resulting indigo dye had a rich color that didn’t easily fade w hen exposed to sunlight or washed.
Interviewer: When did you personally start indigo dyeing?
Suparuk: During my younger years, I went to work and pursued my dreams in Bangkok. However, one day my mother fell ill, and I had to return to take care of her. That turned out to be a pivotal moment because during that time, while helping my mother sell goods at temporary events, a friend recommended a tie-dyeing Facebook page. This introduction sparked my interest, as I realized that many people needed to attend classes or workshops to learn tie-dyeing. However, my mother already practiced it at home, and I was unaware of indigo dyeing. So, I want to express my gratitude to the person who recommended that page, as it introduced us to indigo dyeing. I began learning tie-dyeing, which eventually developed into a keen interest. Initially, I started selling it ie-dye products as a side business, taking them to work to sell.
As the sales grew, I delved deeper into learning different natural dyeing techniques from various sources.
Interviewer: So, while you were studying various dyeing techniques, your family already knew how to make an indigo vat?
Suparuk: Indeed, my mother was the one who handled everything. She had her own traditional recipe for the vat, which took around 7 days to prepare. It took me only a day to adjust the recipe for myself since some people required a faster process for workshops. I learned from YouTube, teachers, and observed my mother. Eventually, I found my own way.
Interviewer: Could you briefly explain the process of making the indigo bath?
Suparuk: To commence the indigo dyeing process, we first need to carefully harvest the indigo leaves from the tree. It’s vital to carry out this task in the morning during the monsoon season to ensure we have fresh leaves. Using stale leaves wouldn’t yield the desired color, which is why timing is crucial.
Once the leaves are cut, we gather them into sizable bundles and proceed to soak them in water. To ensure they sink, we place a weighty object on top. After soaking for a period of 12 hours, we flip the leaves and leave them undisturbed for an additional 24 hours.
Upon completing this initial stage, we extract the leaves. At this point, you may observe the presence of the blue pigment, but it’s not yet ready for fabric dyeing. To achieve the desired dark blue color through a crystallization process, the pigment needs to be mixed with lime or red lime. As you mix the ingredients, you’ll notice bubbles forming on the surface, which should be gently stirred down.
After approximately a day, the color will crystallize at the bottom of the tank. We carefully drain out the water while retaining the pigment. However, it’s important to note that at this stage, the pigment is still not suitable for dyeing purposes.
The final step involves a fermentation process where we combine the pigment with local ingredients. The specific ingredients used vary according to each family’s recipe, but commonly include tamarind juice, sugar, or banana. These additions serve to nourish the bacteria within the tank, facilitating the fermentation process.
Interviewer: Some areas also use sugarcane?
Suparuk: Yes, in the past, people used sugarcane, sugarcane juice, or sugarcane stalks. When they built the kiln, I tried to fill the same amoun t of food in one day, and it works as well. But in the past, they built the kiln for 7 days, gradually fed it and added food every day for about 7 days. The bacteria would thrive, and the water would turn yellow before it could be used for dyeing.
Interviewer: So, are the results different between gradually feeding for 7 days and doing it all in one day?
Suparuk: The longer it takes, the more fragrant and concentrated the kiln will be. It’s better to take longer than in the past.
Interviewer: How long can one kiln last?
Suparuk: It depends on how well we take care of it. It can last for many years, even several years, if we take care of it and observe its colour and smell. In case there is a foul smell, it can be remedied by adding alcohol to help eliminate the odour and kill the fungi. The foul smell will disappear, making it fragrant. But it’s also possible not to add alcohol.
Interviewer: So, we have to rely on experience to know what to add and when?
Suparuk: At first, when the kiln was built for 7 days, there was no recipe book available.
Interviewer: Nowadays, do elderly people in the village still do it?
Suparuk: Yes, they still do it.
Interviewer: Do the younger generation still do it?
Suparuk: Very few. Actually, I came back to take care of my mother because she was not feeling well. Then, I started doing it for about a year, and my mother got better. It was during the COVID-19 period.
Interviewer: Who is your group of customers?
Suparuk: At first, we were not sure about the market direction. We dyed fabric like everyone else, but we didn’t have knowledge about marketing. We didn’t know what type of fabric young people would like. We had to learn and try different things until now when we can group our customers.
Working people aged 30 and above and government employees can afford to buy. In the past, those who wore dyed fabric would go to work in the fields because the dyed colour wouldn’t quickly fade. Or they belonged to a group of economically disadvantaged people. Nowadays, those who prefer authentic dyed fabric made from hand-woven silk will have higher prices. They must be relatively well-off. Those who like dyed fabric will have their own specific group.
Suparuk: We focus on sourcing raw materials. Our customers are teachers, students, and university students. We emphasise selling equipment because vocational subjects taught locally include weaving, dyeing, and local crafts. So, we target the market for selling raw materials on Shopee (Online shopping application).
Interviewer: What kind of people prefer this natural dyed fabric?
Suparuk: They are people who understand nature. The colours they get may not always be the same. It’s the essence of natural dyeing, and the higher price is acceptable to them. Villagers like dark colours. The darker, the better, as they wear them to work in the fields. They prefer dark, almost black shades.
Interviewer: When you first returned to do this craft again, was there any pr oblem you encountered?
Suparuk: The problem was that I used to work in a hospital where everything was done according to a scheduled timeline. But the villagers work at their own pace. It’s not like working in a city with a well-defined system. The majority of the workers here are older and used to working in a certain way, such as making noodles. Sometimes it’s challenging to do tasks that are different from what we’re used to. They have never seen the demands of the market for specific styles. They would just follow what they have done before. Sometimes they have difficulty meeting deadlines and spe cific requirements. Sometimes they can’t keep up with the deadlines, so we have to find solutions. Later on, we stopped taking orders. We weave and sell fabrics in whatever style is available. Working together with people in the community requires an open mind, acceptance, and a calm attitude.