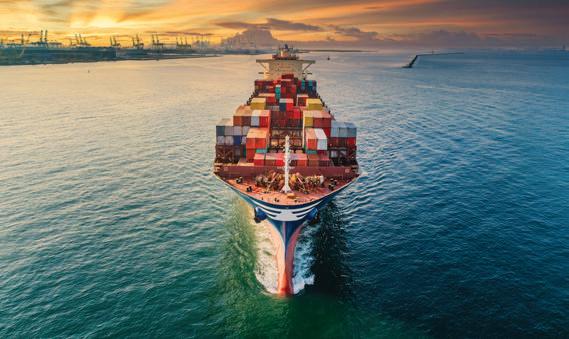
44 minute read
NEWS
from OEM Spring 2021
The Logistics of Supply Chain Visibility
By Stephanie Neil
Senior Editor, Automation World
The pandemic has put pressure on manufacturers to pivot production in order to accommodate new product needs. Those new product needs require additional raw materials, added components or controls for machinery, and are under more pressure to deliver to end-users as e-commerce surges. To make matters more difficult, all of this is taking place amid closed borders, trade wars, and a disconnected multimodal transportation system.
COVID-19 has hit the supply chain very hard when it comes to logistics, which has created the need for more visibility and data sharing for everything in-transit. This big picture problem is why the recent announcement from Boston-based Tive to deliver an open network for connecting shippers, logistics service providers (LSPs), brokers, and customers is so important.
Tive, a provider of multi-sensor trackers and software for real-time location tracking, condition alerts, and analysis, launched the Open Visibility Network, which reportedly breaks down the silos between supply chain visibility providers to enable the collection and sharing of shipment data across platforms. To work across multimodal transportation networks, there must be an ecosystem of players, and the first partner in the Open Visibility Network program is project44, a provider of supply chain visibility technology for shippers and logistics service providers.
The goal is to create an open, collaborative platform that combines insights and data among supply chain participants. “Today, project44 has a ton of data. And we have a ton of data produced from trackers,” said Krenar Komoni, Tive’s founder and CEO. “We are putting technology providers like Tive and project44 together to provide better data. We want to benefit customers [by giving them] full visibility.”
For example, Kodis, a fourth-party logistics (4PL) company provides a nationwide network of warehouses, including the data analytics to help businesses improve productivity and control supply chain costs. Kodis and project44 work together, combining data and insights from the transportation management system that Kodis uses with project44 telematic data. Now, leveraging the Open Visibility Network, Kodis users gain additional in-transit visibility to Tive data from shipment trackers at the load level, which is not specific to carriers.
“In the past this has been a fragmented space with everyone focused on their own [platform],” said Vernon O’Donnell, chief product officer of project44. “We are trying to standardize and remove information asymmetry, [to] create parallel ecosystems.”
While the Open Visibility Network is about connecting what’s happening to materials, ingredients, medicine, and products in-transit, this is just the beginning, Komoni said. The goal is to achieve 100% visibility across all modes of transportation, across all geographies, and across all types of carriers. “We are just getting started. First, we need to make sure things are going from point A to point B with open collaboration, and then we’ll go inside the four walls,” he said, noting the future need to integrate with enterprise reources planning and supply chain management software, as well as warehouse management systems.
Increased Adoption, Acquisitions, and Partnerships Mark 3D Printing’s Advance
By David Miller
Senior Technical Writer, Automation World
3D printing, or additive manufacturing (AM), has been gaining traction in industry for some time now, particularly as it has moved beyond prototyping and into actual production applications.
For instance, many manufacturers have begun using AM to rapidly 3D print spare and replacement parts for onsite equipment to speed repairs, cut costs, reduce unplanned downtime, and save valuable warehouse space by avoiding the need to stock parts in advance. In the automotive and aerospace industries, its chief benefit has been in producing innovative and lightweight components that cannot be achieved via traditional manufacturing techniques—a development that has been a boon as vehicle manufacturers strive to increase fuel economy without compromising the safety or structural integrity of their automobiles and aircrafts.
Perhaps more pertinently, AM has been a vital ingredient in many COVID-19 relief efforts, as manufacturers have raced to produce respirators, face masks, and other personal protective equipment (PPE) at unprecedented speeds.
For example, in March 2020, automotive manufacturer Ford teamed up with 3M and GE healthcare to expand their output of PPE, using 3D printing to both rapidly generate respirator designs using components they had on-hand amid supply chain breakdowns as well as to scale production of simpler goods such as face shields.
Growing adoption
This uptick in the deployment of AM technologies during the pandemic is highlighted in a recent research report from Essentium, a provider of industrial AM services. The study found that during the COVID-19 pandemic, 57% of manufacturers increased their use of 3D printing for production parts to keep their supply chains flowing. Similarly, AM investment plans have changed substantially at many major companies, with 24% of respondents indicating they plant to go “allin,” while another 25% intend to ramp up their use of AM to fill supply chain gaps. Overall, the report indicated that AM use has more than doubled in the past year for 70% of the manufacturing companies surveyed.
“The results of this survey show we’re at the beginning of radical change,” said Blake Teipel, CEO and co-founder at Essentium. “Additive is ready for prime time, and manufacturers are using it to save manufacturing costs while building stronger supply chains that can withstand the worst type of unforeseen events—such as the pandemic.”
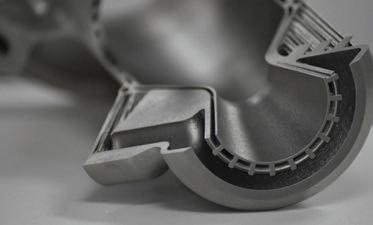
Mergers and acquisitions
In addition to the rising adoption rates observed by Essentium, mergers and acquisitions in the AM space signal excitement among some suppliers of AM products and services for further growth to come.
The recently formalized acquisition and merger of Betatype with Oxmet Technologies, which began at the end of 2019, is a prime example. The new corporate entity, called Alloyed, plans to bring together the expertise in advanced process controls and performance previously provided by BetaType with the knowledge of physical metal AM production capabilities specialized in by Oxmet. The company is focused on multi-scale materials and multi-physics modeling, prediction and analysis of thermomechanical fatigue and failure, and the optimization of complex AM processes.
Software partnerships
The software element involved in AM’s growing success cannot be neglected either. Better CAD modeling has improved the ability of end-users to reverse engineer parts, and digital simulations have been invaluable in improving the accuracy and repeatability of various 3D printing applications. Also, cloud computing has allowed databases of parts and components to be digitally stored and shared across space.
Siemens in particular has been a trailblazer in this space, with its previously released AM Path Optimizer and NX CAD convergent modeling software. These software products have seen high growth, not only keeping pace with the 25% annual AM market growth forecasts, but exceeding it over the past three years, according to Siemens.
Following on the success the company has seen here, Siemens recently announced that it plans to partner with Sintavia, Morf3d, and Evolve Additive Solutions to expand its digital portfolio.
Sintavia, a metal additive manufacturer, will work with Siemens to connect all phases of the AM process in an end-to-end manner for optimal efficiency. By driving operations through Siemens software, Sintavia hopes to be able to deliver AM parts more quickly and cost effectively.
Morf3d, an additive engineering service provider, has signed an agreement with Sie-
mens to leverage its AM software to accelerate the delivery of metal-based products across a range of industries. The company has expertise ranging from design optimization for prototyping and AM part qualification to industrial-scale production.
AM machine developer Evolve Additive Solutions, whose technology applies polymers onto rollers to enable high-speed, high-accuracy, and high-volume thermoplastics molding, will equip its machines with Siemens’ AM software to optimize build preparation. This will include part slicing and nesting, global production planning, scheduling, and execution.
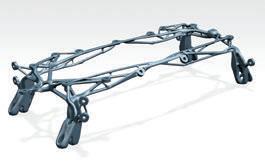
Remaining challenges
Although AM is seeing increased use across industry, some challenges remain. For instance, material costs for 3D printing remain high, and issues with quality assurance, low reproducibility, and the need for expensive post-processing steps abound. In addition, a high degree of expertise is necessary to operate 3D printers themselves, with proper material selection and processing vital to ensuring that the parts printed can properly withstand the stresses they will be subjected to. Currently, with few standards in place, AM is still more suited to batches of one than the machine-to-machine variability larger scale production would entail.
However, industry continues to move toward solving these issues. America Makes, a national accelerator for AM managed and operated by the National Center for Defense Manufacturing and Machining is currently engaged in standard-setting and alignment efforts.
Essentium’s survey also highlights these concerns. Even as 84% of respondents felt that companies investing in AM will have a clear competitive advantage in the next five years, 37% noted that further material innovations will be critical to overcoming obstacles facing 3D printing, while 24% felt that unreliable materials were their biggest barrier.
Morf3D and Siemens are working together to accelerate the adoption of metal additive manufacturing for disruptive innovations such as this light weight bracket.


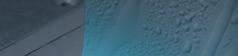
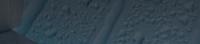
Device-to-Cloud Communications Bypass the Purdue Model

By David Miller
Senior Technical Writer, Automation World
During a recent Endress+Hauser digital press event, the company focused on its cloud-based Netillion industrial internet of things (IIoT) ecosystem. A key point of this press conference was to address industry’s continuing caution about moving operations data to the cloud as part of an IIoT initiative.
Endress+Hauser’s managing director Rolf Birkhofer stressed that industry’s transition to the cloud will ultimately offer users far more benefits than disadvantages. A key aspect of this assertion is that cloud ecosystems require less installation effort due to their centralized nature, Birkhofer said. Plus, these ecosystems offer users continuous real-time access and an evergrowing array of applications powered by big data.
The Netillion ecosystem
Endress+Hauser’s Netillion is a digital ecosystem that enables field instrumentation to be integrated into a cloud-based service platform to boost efficiency, ease asset management, and perform predictive maintenance. Since 2018, all Endress+Hauser field devices and sensors have been made compatible with Netillion. Birkhofer noted that the platform works with devices from other manufacturers as well, though universal compatibility cannot be guaranteed.
Direct connection of field devices to the cloud, such as with Netillion, is gaining traction as more technology suppliers offer new devices and platforms.
The broad level of connectivity fostered by Netillion requires field devices, such as sensors, to contain some level of onboard computing power to collect and transmit the continuous time-series data that feeds Netillion’s analytic capabilities.
Endress+Hauser also provides an assortment of edge devices to enable the twochannel communication that powers Netillion’s analytics. These devices include the
company’s Field Xpert, Fieldgate, and Fieldedge. By allowing dedicated sensors to connect directly to the internet and send data to the cloud without first passing through the various layers of the hierarchical Purdue model, Endress+Hauser says potential latency issues caused by excessive bandwidth consumption can be avoided.
Once data is collected and processed by Netillion, users can download diagnostic information to their smartphone or tablet to monitor values, reconfigure threshold limits, or engage in predictive maintenance. An application programming interface eases the processes of integrating the Netillion database with applications from other vendors.
And while the complexity of the Netillion ecosystem may seem daunting to some, use case examples provided by Endress+Hauser help make its value proposition significantly more clear. For instance, Endress+Hauser’s Micropilot FWR30 wireless radar-level sensor can reportedly be installed inside an intermediate bulk container used for the safe transportation and storage of fluids in ten minutes or less. From there, it can continuously and instantaneously transmit level readings to the cloud for access via the Netillion application from any location.
German steel manufacturer Salzgitter Flachstahl was the first company to adopt Netillion. Its adoption of the technology featured prominently in the press conference. Salzgitter Flachstahl reports significant productivity gains since integrating its operations into the platform. At present, the company has connected all of its field devices to the cloud and is identifying the data necessary to begin engaging in predictive maintenance.
Because the data accumulated from Salzhitter Flachstahl’s operation will be used to train Netillion’s algorithms, subsequent adopters of the platform will be able to benefit from the company’s experience.
Cybersecurity concerns
To address industry’s security concerns about sending production data to the cloud, Birkhofer explained that the two-channel system used by Endress+Hauser’s edge gateways effectively address this issue. He said the gateways only “listen in” to channel the data through a firewall and proxy server, meaning that the devices themselves are not directly connected to the internet. In essence, field-to-cloud connectivity via the company’s gateways are a one-way street—data goes out, but no data can be sent back into the devices.
Birkhofer added that EuroCloud, a vendor-neutral digital competence organization, is in the process of granting Netillion an ISO/IEC 27001 information security management certification. This soon-to-beawarded certification for Netillion requires the platform to undergo a rigorous audit, Birkhofer said.
Maximize Machinery with MaaS
By Sean Riley, Senior Director, Media and Industry Communications, PMMI
While predictive maintenance has existed as a buzz word in recent years, PMMI, The Association for Packaging and Processing Technologies, recognized the need for an industrywide definition and recently released an in-depth 2021 Predictive Maintenance White Paper (awgo.to/1153). It defines predictive maintenance as monitoring a machine or machine component to determine when it is likely to fail and to take action to stop it, thus avoiding unplanned downtime.
In the broadest sense, there are two categories of technology that must be implemented to create a predictive maintenance solution. One of these is the hardware. Increasingly, the key category of hardware in any predictive maintenance solution consists of smart sensors. These sensors are constantly growing in capability, and will increasingly include advanced processing capacity.
The key pre-requisite to deciding where to deploy smart sensors for predictive maintenance within specific machines is understanding which data is useful. OEMs and integrators believe that run-time, current/voltage draw and speed are the three most useful data types for performing predictive maintenance. However, run-time for predictive maintenance assumes that equipment is most likely to fail in the latter part of its life, which is often not the case.
Gathering data is the easy part. The second key technology for predictive maintenance is software and analytics to understand the data. Since most machine builders don’t possess the ability to write this software in-house, this stage usually requires a predictive maintenance specialist.
The benefits to predictive maintenance are pretty obvious: reduced downtime and increased machine lifetime. So why isn’t everybody doing it? If taken to its full potential predictive maintenance could radically extend the average lifetime of a machine. This will mean new business models are essential for OEMs to maintain revenue streams.
The most promising business model candidate so far is Machines as a Service (MaaS). Essentially, it involves pricing based on performance goals set between the OEM and the end user (such as the number of items processed). If there is one hindrance to stop the widespread adoption of an MaaS business model for predictive maintenance, it is the aversion that many companies have to allowing remote access.
MaaS requires the continued growing acceptance of remote access, which has increased in use during the COVID-19 pandemic. Companies have learned that remote connectivity is usually no less secure than on-site connectivity. Remote connections and cloud storage are not as insecure as is usually assumed with expert third-party providers such as Microsoft Azure or Amazon Web Services. These are companies that have huge teams of cybersecurity experts dedicated to protecting their customers.
For more information on MaaS and the key barriers to its acceptance, download the full white paper at pmmi.org.
COVID-19-related supply chain disruptions have prompted manufacturers to consider bringing operations back to the U.S. But successful reshoring depends on disruptive technology.
In January, President Joe Biden ordered government agencies to take action and require the wearing of masks in airports, on commercial aircraft, ferries, and all public transportation, while encouraging “masking across America.” And, if we are going to be buying more face masks, why not purchase other products that are also “made in America?”
When the pandemic reached the U.S. early last year, about half of the world’s disposable masks were produced overseas in China. And as COVID-19 became a global healthcare crisis, face masks became essential and countries imposed restrictions on exports, which increased the worldwide shortages of masks and raw materials, according to the U.S. National Institute of Health’s National Library of Medicine.
“All it took was stopping the supply of disposable masks produced overseas from coming to the U.S. for us to be critically impacted,” said Raphael Kryszek, founder and CEO of Intrepid Protect, a manufacturing start-up focused on producing face coverings made at a new state-of-the-art facility in Los Angeles, Calif. It was the PPE shortage, a dependence on foreign sourcing of goods, and a lack of quality-control standards that prompted Kryszek to make manufacturing in America a viable option. It is also his way to create jobs and help bolster the U.S. economy.
And Kryszek is not alone when it comes to setting up shop stateside. According to a recent Thomas Industrial Survey assessing the ongoing impacts of COVID-19 on North American manufacturing, there is heightened interest in reshoring and hiring—mainly as a result of rethinking supply chains.
Of the 746 manufacturing companies surveyed in May and June of 2020, 69% are looking to bring production back to North America, 38% are actively hiring, and 55% said they are likely to invest in automation, specifically as it pertains to production performance, process control, and product testing and quality. “With the growing appetite for reshoring and onshoring, respondents shared the top products they are looking to source domestically: metals (15%), machining tools and parts (13%), fabricated materials (13%), and PPE (12%),” the Thomas report states.
“Clearly, the pandemic has been an accelerant to reshoring, as well as nearshoring,” noted Paul Wellener, a vice chairman at Deloitte LLP, and the leader of the company’s U.S. industrial products and construction practice. “Nearshoring is getting into your time zone, like utilizing manufacturing in central or south America if you are in the U.S., and reshoring is bringing production back into your country. But as things come back to the U.S., it is not coming back in the same way as it’s being done in another part of the world. There is technology being added to help continue to drive the cost targets, quality targets, and safety targets that manufacturers have.”
According to Wellener, automation and robotics play a significant role as a way to offset labor costs, but machine learning, artificial intelligence (AI), cloud computing, 3D printing, and supply chain management (SCM) are also aiding in the effort to reshore manufacturing.
Intrepid Protect, for example, uses servo motors and absolute and relative encoders on the assembly line and relies heavily on AI and machine learning to ensure quality control and predictive maintenance to optimize operations and accelerate the delivery of mask inventory at the lowest cost. “There are a lot of moving parts on the assembly line, and they fail due to wear and tear. But we’ve seen huge improvements due to AI and predictive maintenance cycles, which has increased productivity, efficiency, and reduces pricing due to our ability to minimize waste and minimize faulty products,” said Kryszek. “We didn’t reinvent the production of three-ply masks, what we did was streamline and automate it by adding technology to improve different parts of the assembly line.”
The high price of production
In recent history, the U.S. has had an $800 billion/year trade deficit. The U.S. has been dependent on imports primarily because the cost to manufacture here is
Bright Machines’ Microfactory uses computer vision, machine learning, cloud computing, and robotics to get products to market faster.

just too high. According to Harry Moser, founder and president of the Reshoring Initiative, his data shows that U.S. manufacturing costs are often 20% higher than European manufacturing and 40% higher than China and other low labor cost countries, which makes offshore manufacturing more appealing from a cost-competitive standpoint. And the price is too high mainly because the dollar is too high, he said.
In addition, in the U.S. there aren’t enough engineers and the country lacks the quantity and quality of skilled manufacturing trades people relative to the opportunities, hindering productivity growth that could overcome the impact of the U.S. dollar, Moser said. Plus, the U.S. has too many regulations, high corporate tax rates—which until 2017 were 35% when most of the world was around 22%—and there are no value-added taxes (VAT) here, whereas other countries apply it. “These are important things that we concentrate on, and reversing those over 10-to-20 years would balance the trade deficit and get us out of the problem we’re in,” Moser said. “We call it leveling the playing field, and if you do that then it is a lot easier to get companies to decide to bring work back.”
With that said, Moser agrees that the latest interest in reshoring is driven significantly by COVID-19. “From March 2020 through the end of the year, about 60% of reshoring cases mentioned COVID-19 as one of the factors causing them to reshore. Some of those cases involved COVIDrelated products, like masks, gowns, and ventilators, and others were related to the company recognizing that whatever it makes, it is too dependent on China or offshore sources, and COVID-19 has educated it to not be so dependent.”
In addition, from a longer term perspective, growth and productivity is the only way to raise living standards. The average U.S. manufacturing growth rate for the last ten years is 0.4%, Moser said. So the lack of applying automation due to concerns that robots will take jobs, for example, has not helped U.S. productivity. In contrast, China’s productivity is growing at 6% per year.
“If we don’t invest in automation, we don’t increase our competitiveness,” Moser said. “Some people are afraid of automation because they’ll lose their jobs. But, throw away that statement, because the U.S. will lose more jobs to Chinese automation if we don’t automate than we will to U.S. automation if we do. Since we are competing, you have to automate the best you can just to stay even.”
But automation, too, must change to help manufacturers compete. Moser points to Bright Machines, a San Francisco-based manufacturing technology startup that is transforming this space with its modular system for electromechanical product assembly.
The future is bright
The Bright Machines’ Microfactory for assembly, testing, and inspection, is designed to get products to market faster by leveraging intelligent software and adaptive hardware, using computer vision, machine learning, cloud computing, and robotics.
The platform is focused on hardware standardization and common interfaces that map to a common data model. On top of that, there is a set of algorithms and microservices combined via an API gateway for a common set of apps that take the manufacturer through all stages of automation, such as line planning, configuration of robotic cells, deployment, and service and support. Key to this is an AI-powered software layer that configures, monitors, and manages machines and operations.
“We are automating automation,” said Bright Machines’ chief product officer Abhishek Pani. To that end, Bright Machines will work across a variety of controllers and different components through an abstraction layer that makes it PLC agnostic. “There are a bunch of things happening through different
vendors, but it is how we bring it together in one common interface and one common workflow and a common software tool.”
To understand how the Bright Machine Microfactory works, and the speed at which this all comes together, look at Argonaut Manufacturing Services, a U.S.based contract manufacturer for the biopharmaceutical, diagnostics, and life sciences industries. With a focus on molecular diagnostics and parenteral drug products, the company currently has many active programs in the COVID-19 area, partnering with companies on the manufacturing and supply chain side.
For example, the company produces kits for COVID-19 testing and collecting of the swabs and the liquid that preserves the sample to be tested. The company does both filling and packaging of materials, which can involve different chemicals in different tubes that make up a kit. “We work with Bright Machines as an enabler to significantly automate the process to increase our scalability in the areas of filling and finalizing these kits,” said Eric Blair, chief commercial officer at Argonaut. The benefit is the modularization that fits well into the operational budget. “It enables us to take what tends to be a capital-intensive process and turns it into taking the key parts and building it out for specific needs in shorter periods of time.”
This is important for reshoring because there’s a need for innovative diagnostic testing and drug discovery here in the U.S., and to do it quickly and at scale while mitigating supply chain risk. To do that, many companies will look to contract manufacturers, like Argonaut.
Inventory made easy
Another technology that can speed up supply chain operations and on the assembly line is additive manufacturing, otherwise known as 3D printing, which is a way to fabricate an object by sequentially layering material, such as plastics and metals, in successive crosssections. It has been used by manufacturers to make parts while eliminating tooling costs and shortening lead times.
Part of the evolution of additive manufacturing is introducing new materials, like carbon composites, a strong lightweight material. Arris Composites, founded in 2017, is a pioneer of next-gen composites for mass market applications, including aerospace, automotive, and consumer products. The company developed continuous carbon fiber composites that can be combined with other materials in a high-speed process that brings 3D printing together with the traditional high-volume manufacturing method of injection molding.
The Arris Additive Molding technology is capable of manufacturing complex geometries using continuous fiber and it can integrate hardware with advanced electronics. So, for example, a smartphone enclosure could have the electronics embedded within the structure. In addition, combining additive manufacturing and injection molding creates repeatability for production volume at lower production costs—producing parts that are stronger than titanium at about one-third of the weight. Skydio, a U.S. drone manufacturer, worked with Arris to redefine airframe designs using the Arris Additive Molding carbon fiber manufacturing technology. It resulted in taking 17 parts in an assembly and consolidating them into one single, multifunctional structure with a 25% weight reduction, better strength and durability, and an improved appearance.
“Industrial design teams at consumer products companies are excited about the cosmetic latitudes we give them to make beautiful products,” said Ethan Escowitz, CEO and founder of Arris. But the beauty of it all goes beyond aesthetics. “The ability to collaborate with customers and take the functional requirements for a single part or an assembly of parts and design something better is the key.”
Skydio is a success story in that the drone company figured out how to innovate from the ground up and manufacture on U.S. soil. A lesson other companies looking to reshore can learn from. “One of the most important things about reshoring is that it requires rethinking how something is made,” Escowitz said. Sometimes companies just look at a bill of materials to figure out what is made overseas that could be made here. “I think there are more disruptive reshoring opportunities that are more interesting…like taking advantage of new manufacturing technology…looking at the architecture to make a more desirable product, and picking the right location based on the customer supply chain.”
Making it in America
Deloitte’s Wellener notes that what is coming back to the U.S. shores are high-value products—like the Skydio drone, highly engineered items, and components that go into larger subsystems. So there is a balancing act for companies considering what to reshore and how to make investments at the right time.
To that end, the Reshoring Initiative offers a free online tool, the TCO Estimator, that helps companies quantify all offshoring costs and risks. The tool helps account for all relevant factors—overhead, balance sheet, risks, corporate strategy, and other external and internal business considerations—to determine the true total cost of ownership. Using this information, companies can better evaluate sourcing, identify alternatives, and even make a case when selling against offshore competitors. In addition, the Reshoring Initiative created the Import Substitution Program (ISP) to convince and facilitate importing companies to produce or source more domestically. Customized versions of ISP are available for U.S. manufacturing companies, technology suppliers, trade associations, economic development organizations, and manufacturing extension partnerships. Moser estimates that consistent use of the program would increase domestic manufacturing by about 10%.
For companies like the Intrepid Protect, the labor costs, capital equipment costs, material costs, and technology costs all factored into the equation when deciding where to build a facility. “It was a challenge,” Kryszek said. But making masks in America was always the goal. “The founding principle of the project was to help the American supply chain and the American labor force.”
Last year proved itself a veritable rollercoaster of disruptions and developments, resulting in robotics adoption growing in some areas and shrinking in others, yet still painting a picture of continued growth for robotics ahead.



Like collaborative robots (cobots), mobile robots may also see their growth accelerate as many move beyond fi xed applications and toward more fl exible robotic systems.


proved to be a uniquely tumultuous and challenging year, beset not only by the unprecedented disruptions of the COVID-19 pandemic and its associated economic impacts, but the uncertainty that so often accompanies election years as businesses are forced to hold their breath on major decisions until the policy environment they will have to navigate over the next four years becomes more clear. Accordingly, a recent survey on robotics adoption conducted by Automation World shows some industry verticals seeing a huge uptick in robotics due to the need to socially distance, reshore supply chains, and increase throughput, while others saw investment stall as demand for their products cratered and their decision-making process became paralyzed by political and economic uncertainty.
Still, given the turbulent dynamics of the prior year, the general consensus among robotics suppliers—much of which is borne out in our survey data—is that strong growth remains expected in their space and robotic adoption should see continued acceleration in the near future.
Adoption to date
Of the respondents surveyed, 44.9% reported that their assembly and manufacturing facilities currently use robots as an integral part of their operation. More specifically, of those with robots, 34.9% have adopted collaborative robots (cobots), while the remaining 65.1% use only industrial robots.
With a few caveats, robotics suppliers interviewed for this article concur that the results of the survey were consistent with the overall landscape they see. However, they did note that adoption is clearly more advanced in some areas of industry than others.
For instance, automotive manufacturing in particular has seen a high penetration of robotics, having automated long before many other industry verticals. According to Mark Joppru, vice president for consumer segment and service robotics at ABB, this is not only because of the automotive industry’s ability to make high CAPEX investments, but also due to the rigid and standardized nature of automotive manufacturing, which can be accommodated by fixed robotics technologies.
Similarly, packaging has seen automation growth for the same reason, though many of the packaging machines that move products along lines would not qualify as robotics in the eyes of some. All the same, much use has been made in recent years of robotic arms, sometimes on mobile carts, at the beginning and end of packaging lines, where they perform material handling tasks, such as loading, unloading, and palletizing. It is in these end-of-line applications for which further growth of robotics in packaging is expected to take greater hold.
Meanwhile, smaller job shops and contract manufacturers— whose high-mix, low-volume (HMLV) production environments often require more flexibility—still have a long way to go when it comes to robotics adoption. Joe Campbell, senior manager of applications development at Universal Robots, feels that this is where much of the next wave of adoption is to be found. In fact, Campbell posits that overall adoption figures to date may be even lower than the 44.9% our survey detected, as he feels many of the small
and medium enterprises (SMEs) his company serves are liable to fly under the radar, remaining essentially invisible to trade associations, industry surveys, and other data. "There's a large chunk of the market that's really been underserved by the whole automation community, and we continue to uncover every week more and more [SMEs] that have very little automation, if any. They have no robots, and so that's a big growth area going forward," Campbell says. "A lot of surveys that associations and other publishers do might not be touching these people. They don't go to trade shows, and I don't know how many automation publications they're looking at, but these small companies have growth potential."
The COVID-19 effect
While many have opined that COVID-19 would accelerate robotics adoption, one of the biggest surprises of our survey was that 75.6% of respondents indicated that the pandemic did not drive any purchase of new robots within their facilities. Furthermore, of those who did bring in robots in response to the pandemic, 80% purchased five or less. These findings do not, of course, mean that COVID-19 has had a wholly negative effect on robotics adoption, as several suppliers note. Rather, it may imply that the degree to which the pandemic has accelerated robotics is highly variable between different industries and applications. In some cases where manufacturers did purchase new robots throughout 2020 it may have been in response to other factors that were only indirectly tied to COVID-19, such as the need to increase throughput in verticals that saw a surge in demand or quickly meet labor requirements in fields where supply chain disruptions forced reshoring.
For example, Scott Marsic, senior project manager at Epson Robotics, points out that his company has seen strong adoption from medical equipment and device manufacturers facing soaring demand amid the need for personal protective equipment (PPE). Marsic stresses the primary interest in robots from these industries has been focused on increasing throughput rather than using robots to space out production for social distancing purposes. At the same time, the automotive industry—though already wellautomated and a typical source of new robot purchases—has seen demand crater as lockdowns have reduced transportation demand exponentially. As a result, these companies have put large CAPEX spends on hold.
“I’ve put about 2,000 miles on my car in the past 10 months. I'm not getting oil changes or new tires,” Marsic says. “My demand is down and, if you look at automotive manufacturing, they've followed suit. If the demand is not there for automotive components, they won't invest in more automation. On the other side, if you look at fields where demand has gone up, like medical devices, pharmaceuticals, and even consumer packaging, they're seeing [increased] demand, and that's where the robots are being sold."
The logistics and warehousing spaces have also seen an uptick in robotics adoption for similar reasons, says Melonee Wise, CEO at Fetch Robotics. With more homebound consumers ordering all manner of goods online, demand has spiked.
On the topic of adopting robots for social distancing purposes, the overall response of those surveyed was fairly weak, with only 16.2% of respondents indicating it as a factor driving their decision to purchase new robots. More prominent reasons for robot
Automotive manufacturing is one of the industry verticals where extreme demand drop-o amid the COVID-19 pandemic and its associated lockdowns has caused robotics adoption to slow, rather than speed up.
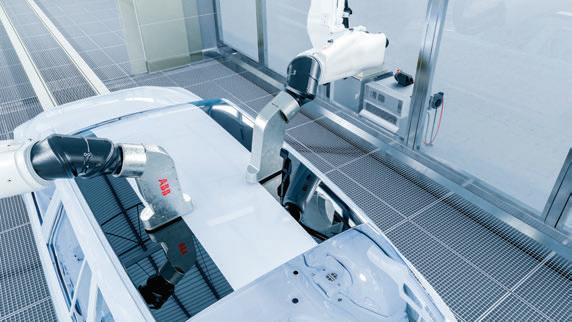
purchase included cutting labor costs at 62.2%, increasing capacity at 54.1%, and navigating a lack of available workers at 37.8%.
On a related note, of those who did purchase robots in response to COVID-19, 45% indicated that they purchased cobots, while the remaining 55% opted for industrial robots. As cobots have often been held up as the best robotic solution for social distancing due to their ability to flexibly work alongside humans when attempting to space out a line or work cell, their lower-than-expected adoption rates among those responding to the pandemic may further highlight that concerns related to labor cost and availability, quality, and throughput are greater.
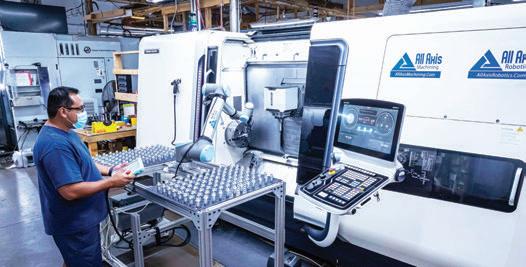
Forecasting future adoption
Looking ahead, the expectations of robotics suppliers are bullish, with many believing that with the elections over and increased availability of COVID-19 vaccines on the horizon, much demand will return in industries where market skittishness has slowed robotic adoption. Meanwhile, those industries already seeing an uptick are expected to plough ahead at an even faster pace.
As a potential caveat to suppliers’ high expectations, our survey results were a bit more modest, with slightly less than a quarter of respondents reporting that they plan to add robots in the next year. Of those respondents, 56.5% plan to purchase cobots and 43.5% plan to purchase typical industrial robots.
However, some suppliers suggest that the lower expectations apparent in the survey results might be misleading. For instance, Wise feels that, with installations of traditional fixed robotics systems sometimes taking as long as 9-15 months, many respondents who indicated they do not plan to add more robots in the next year may already have projects underway. In addition, Joppru notes that though only 23% of respondents plan to add robots, some may add a substantial amount, meaning that overall growth for the industry could be significantly higher.
In terms of the factors driving specific robot purchases, 52.8% said ease of use and 52.6% said end-of-arm-tooling options, while only 38.5% were interested in specific collaborative capabilities. This result seems to imply that flexibility, rather than collaborative safety features themselves, may be driving end-users’ growing preference for cobots.
This is most certainly reflected in the HMLV space where manufacturers are dealing with a challenging combination of high labor costs and labor shortages on the one hand, and shorter product lifecycles mandating rapid changeover and an increased degree of production variability on the other. Doug Burnside, vice president of North American sales and marketing at YaskawaMotoman, notes the paradox of dealing with rapid changeover using a manual workforce is actually easier, as human beings are, by their nature, adaptable. It’s only when automation is brought in that the process becomes more challenging. However, increasing flexibility enabled by the integration of vision, artificial intelligence, and more diverse and modular tooling options are helping to surmount these challenges.
Elsewhere too, there are some areas where robots may prove themselves useful that haven’t yet begun adoption. According to Joppru, ABB has had preliminary discussions with the oil and gas industry about integrating new types of robots into their field operations, though the realization of these projects may be years off.
“In oil and gas, there’s still a lot of manual processes that happen where three guys grab a pipe, and then they put a chain around it, grab a new pipe, and attach it so that they can drill another 20 feet,” Joppru says. “Could we automate that with some robotic arms that would eliminate a dull, dirty, and dangerous job? That’s one example, and we’ve had discussions with customers about this being a new area of penetration for robots that we just haven’t been able to go after yet.”
With that in mind, even should job shops, contract manufacturers, and SMEs become as robot-laden as the biggest automotive manufacturers, there will still be plenty of room for expansion in the future.
Small job shops and contract manufacturers in the high-mix, lowvolume space may represent the next frontier of growth for robotics with collaborative robots (cobots) in particular proving popular due to their flexibility.
OEM Digitally Transforms Its Business for Remote Support
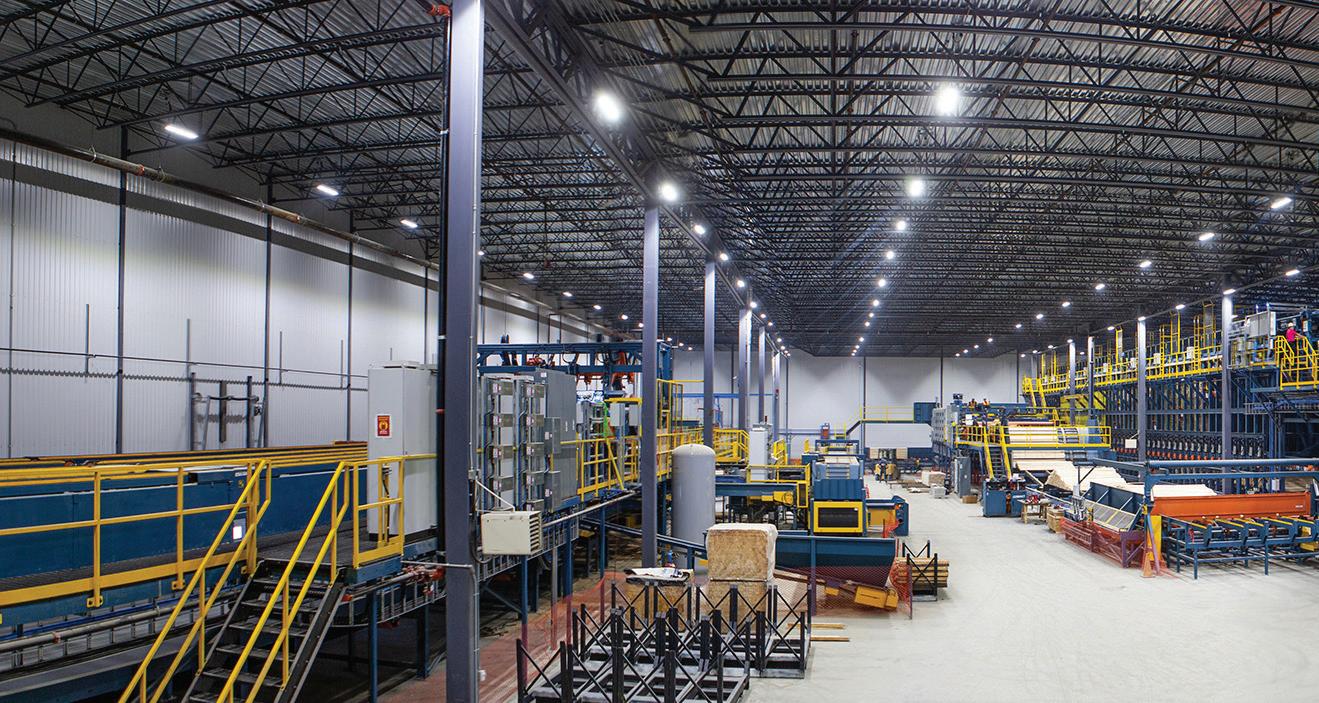
BID Group, a sawmill equipment manufacturer, adopts PTC’s ThingWorx IIoT platform and Vuforia augmented reality technologies to reduce customer downtime and eliminate asset component failures.

By Jeanne Schweder, Contributing Writer, Automation World
Guiding your business through a digital transformation is no walk in the park, as many companies have learned the hard way. The BID Group, a North American supplier of forest products equipment, had tried a do-ityourself approach to the Industrial Internet of Things (IIoT) for several years before managers acknowledged it was time for a reset.
The first technology company BID worked with on its digital transformation was still in the process of building an IIoT platform, leaving BID managers dissatisfied with the lack of progress. So BID chose to restart the process, this time working with PTC. PTC was able to augment the initial development work done for BID by using PTC’s ThingWorx Industrial IIoT Platform. With this addition in place, BID was able to make significant strides in just a few months using IIoT connectivity to improve productivity and profitability for its customers.
Now the company is moving forward with the next stage in its transformation, deploying a number of PTC’s Vuforia augmented reality (AR) products to boost frontline worker efficiency, safety and agility, and improve remote customer assistance and troubleshooting.
“As part of our digital transformation initiatives, we have prioritized the use of IIoT and AR to help create smarter, more connected products and services,” says Chris Wells, BID senior vice president of aftermarket service and reliability. “By incorporating PTC’s AR offerings, we expect to unlock new opportunities to service our clients in a more efficient and interactive manner. The COVID-19 pandemic has made it abundantly clear that these technologies are essential to business continuity.”
BID saw a 9.4% increase in call volume for remote support through its 24/7 service center in the 25-weeks ending December 1, 2020, compared to the same period in 2019. “We attribute this to the COVID-19 situation driving more clients to look for alternate methods of support to the traditional onsite technician. This trend is increasing, and we do not foresee this changing,” adds Wells. “It’s why we’re implementing new technology-based approaches around remote support, remote monitoring, and remote work instructions that leverage IIoT and AR.”
Remote service has been a growing trend among OEMs. With travel restricted by the pandemic and customers wanting to keep visitors out of their plants, many machine builders are beginning to rethink their reliance on field-deployed service teams. “AR is an ideal tool for providing remote assistance,” explains PTC’s Ken Rawlings, vice president, solution management for connected products. “You can digitally mark-up a shared view, identify problems with a component or in a process, and virtually walk a technician stepby-step through the corrective procedure so they can fix it right the first time.”
AR also allows OEMs like BID to capture digital references of equipment or procedures, which can be used for training or by their technicians or a customer’s maintenance team when they’re troubleshooting a problem. “With an aging workforce, you’re often relying on younger, less experienced workers to identify and fix problems,” says Jon Kadane, PTC’s product marketing director for connected products. “AR provides on-demand access to visualizations of critical information and allows technicians to interact with the system in context, using visual cues to guide them through tasks more proficiently.”
Driven by analytics
As an OEM, BID’s priority since its founding has been to make the highest quality sawmill equipment. But it is unique in that, over the past five years, the company has shifted its business model to providing customers with turnkey sawmills. BID has been involved in 18 installations in less than two years, according to Wells, most of them new facilities and many of them in the southeastern U.S.

Panoramic view of sawmill line.

By shifting from making sawmill equipment to delivering a complete facility, the company’s focus has invariably widened to optimizing mill performance. Adopting IIoT technologies has been critical to BID’s successful business transformation and its ability to meet customer demand for maximum productivity and profitability.
A sawmill has a very complex manufacturing process, combining a raw material stream of great variability with the multiple steps required to turn a log into lumber. Faced with commodity pricing that varies minute to minute, it’s critical for sawmill owners to achieve optimum productivity if they are to be profitable. New mill owners are now requiring the real-time operational view that IIoT technology can deliver when they place an order with BID.
“One of the most valuable features of PTC’s software is that it enables us to properly orchestrate the data our machines generate, so that everyone has a single place to look for real-time information from the manufacturing process,” explains Sefton Jubenvill, BID vice president for digital transformation. “We were able to quickly prove the concept at one of our sites, then use the platform to meet several commercial commitments within two or three months.”
The ability to deliver quick time-to-value returns for their digital investment is attracting many new customers to BID, whether it’s for a greenfield facility or an existing one that involves multiple suppliers’ equipment. “We’ve seen up to a 30% increase in machine center throughput where our IIoT insights are used to drive operator behavior, as well as up to a 10% increase in factory efficiency when our digital system, which we call OPER8, is implemented across the entire factory floor,” says Wells.
The OPER8 system collects and analyzes data in four key areas: production health, such as key performance indicators and realtime, minute-to-minute changes in operator behaviors; throughput health, which deals with the performance and productivity of equipment and operators; asset health, which monitors leading process indicators such as vibration or temperatures and detects imbalances in a process; and quality health, where improperly functioning equipment could cause product defects.
“We’ve achieved downtime avoidance of up to four hours per incident,” explains Wells, “eliminating targeted and specific asset component failures through the application of asset health real-time condition monitoring and analytics. This is made possible through additional sensors and instrumentation.”
Monetizing data capture
Data capture and contextualization have now become an integral part of BID’s equipment package. As a result, software suppliers like PTC are key to delivering on BID’s promise of performance. “We’ve become an OEM supplier, just like companies that provide pumps or motors,” says Rawlings. “Our IIoT technologies are another sub-component built into the system. By providing an enterprise-wide view and putting streams of data into context, our software is able to provide the right insights to the appropriate person or function. It’s a way for OEMs to monetize data capture and provide a higher level of service.”
Adds Kadane, “ThingWorx tools allow OEMs to configure rather than code, enabling easier integration of equipment and systems for greater scale and impact. And since data is fully contextualized for both machine builder and customer, decisions can be made in real time, rather than at the end of a shift, to better control processes. Being able to visualize operations makes for faster and repeatable troubleshooting, with less downtime and greater throughput.”
To help produce its custom-configured cars more rapidly, BMW used Nvidia’s Isaac robotics platform to add advanced computing and visualization to its factory logistics robots.
By David Greenfield,
Building cars at BMW involves the handling of millions of parts flowing into a factory from more than 4,500 supplier sites. One factor increasing the factory logistics challenge for the BMW Group is the customizability offered by the company. With an average of 100 different options available, this translates into 99% of customer orders being unique to each customer.
“Ultimately, the sheer volume of possible configurations became a challenge to BMW Group production in three fundamental areas—computing, logistics planning, and data analysis,” said Jürgen Maidl, senior vice president of logistics for the BMW Group.
To better handle logistics within its factories, BMW now uses four types of material handling robots and a smart transport robot. These robots were developed using Nvidia’s Isaac robotics platform.
According to Nvidia, its Isaac software development kit provides these robots with neural networks capable of “addressing perception, segmentation, and human pose estimation to perceive their environment, detect objects, navigate autonomously, and move objects. These robots are trained both on real and synthetic data using Nvidia graphics processing units (GPUs) to render ray-traced machine parts in a variety of lighting and occlusion conditions to augment real data.”
STR in Isaac Sim with dolly.

Nvidia Isaac robotics platform working in sync with robot.

Hanns Huber, with BMW Group’s Communications Production Network, explained how the five different types of robots the company outfitted with Nvidia’s technology support factory logistics in production operations.
He said that, after delivery to the plant, parts are transported to the assembly line in containers of various sizes. Stationary SplitBots take full plastic boxes from the pallet in the incoming goods area and place them on a conveyor system that transports the boxes to a warehouse. The SplitBot also makes sure the containers are lined up correctly for automated storage. Using Nvidia’s artificial intelligence (AI), the SplitBot can detect and process up to 450 different containers.
Mobile PlaceBots unload tugger trains and place boxes loaded with goods on a shelf. These robots use Nvidia’s image recognition system to classify the small load carriers and determine the ideal grip point from the combined input of sensors, cameras, and artificial intelligence. These technologies allow the PlaceBots to move autonomously in a predetermined area.
Another logistics robot, the PickBot has a robotic arm that it uses to collect various small parts from supply racks. Like the SplitBots, the PickBot uses Nvidia’s AI technology to calculate the right grip point.
The robotic manipulation arm of the SortBot takes empty boxes and puts them on a palette to be sent back to the supplier area. These SortBots are deployed in series production to stack empty containers on pallets before they re-enter circulation.
BMW’s autonomous Smart Transport Robots (STRs) can identify obstacles such as forklift trucks, as well as humans, to more accurately and quickly suggest alternative routes as needed. They can also learn from the environment and apply different responses to people and objects.
Huber noted that all of these robots have been developed by BMW in the past five years, with most being deployed and tested in BMW factories since 2019. “The robots are trialed during our development process at various BMW plants in Germany, as well as at our logistics laboratory in Munich,” he explained.
The STR was developed by BMW’s logistics innovation team together with Fraunhofer Institute Dortmund,” Huber added.
BMW’s work with Nvidia on this project began in 2019. “A BMW Group team of engineers worked on implementing the Nvidia technology with the robots,” Huber said. “The complete implementation was done in-house at BMW. Two teams from both sides—BMW Group and Nvidia—worked closely to customize and adapt a suitable solution. The first STR with Nvidia technology was deployed as a proof-oftechnology in our logistics laboratory in Munich in May 2020.” The first production test was expected to go live by the fourth quarter of 2020 or early 2021.
Nvidia notes that the real and synthetic data generated during the testing of these robots are used to train deep neural networks on Nvidia’s DGX AI infrastructure development systems. The robots are then continuously tested in Nvidia’s Isaac Sim simulators for navigation and manipulation development, operating on Nvidia’s Omniverse platform, where multiple BMW Group personnel in different geographies can all work in one simulated environment. Huber said that, incorporating Nvidia’s AI technology into BMW’s robots allows BMW to “optimize our robotics and material flow, as well as take simulations in the planning process to a new level.”