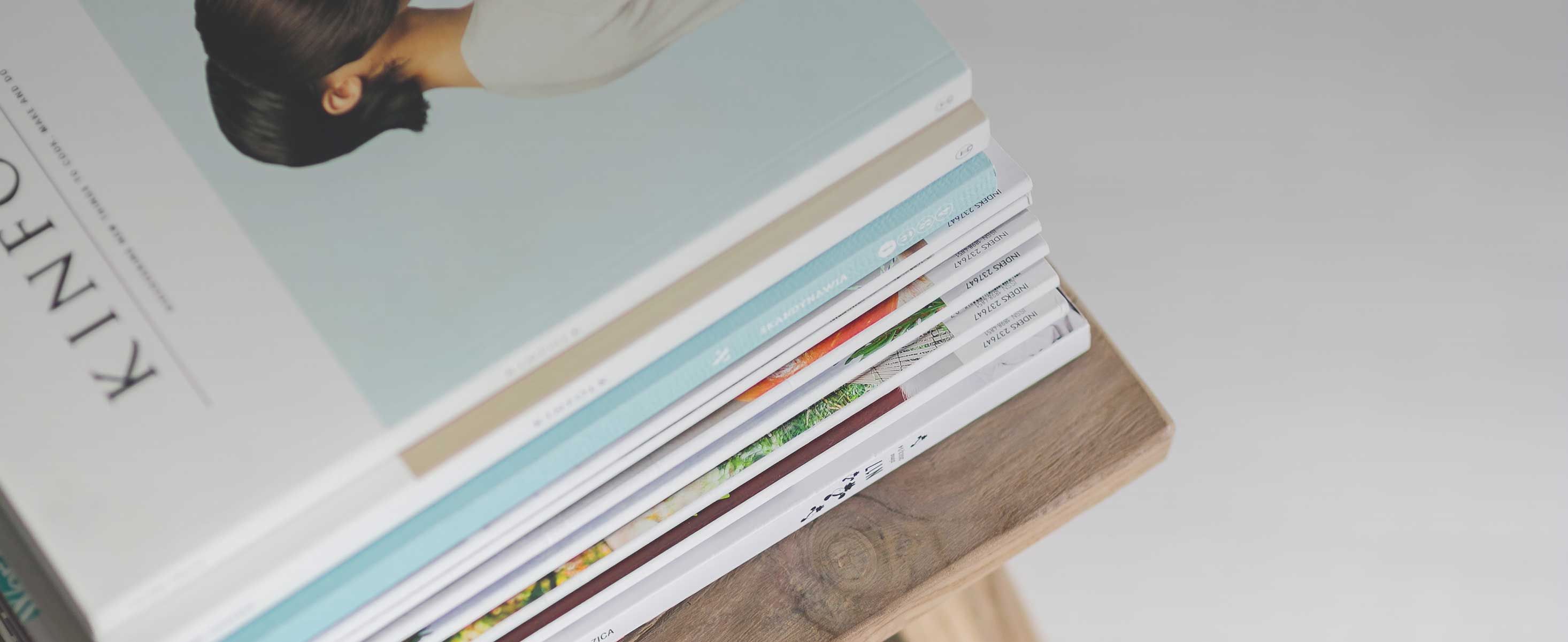
3 minute read
BATCH OF IDEAS
Wearable Safety in the Warehouse
By Stephanie Neil
sneil@automationworld.com sneil@automationworld.com
Senior Editor
This past August, the U.S. Department of Labor’s Occupational Safety and Health Administration (OSHA) launched an initiative aimed at protecting workers in warehousing, storage, and distribution facilities who are at more risk of injury as a result of an increase in e-commerce. This regional five-year initiative will focus on the hazardous conditions workers face every day.
The program follows a Bureau of Labor Statistics’ (BLS) 2020 finding that the injury rate for workers in warehousing and storage is higher than the U.S. average among all private industries. In addition, from 2017 to 2020, BLS reported 93 work-related fatalities nationally in the industry.
That’s just not okay. And nobody understands how devastating these numbers are more than Sean Petterson, whose father passed away while on a construction job.
It was that experience that prompted Petterson to study industrial design and engineering to find ways stop injuries and fatalities in industrial settings. He started by developing exoskeletons to strengthen human capabilities, building an algorithm for kinematic movement. But the exoskeleton model was limited to specific applications, so Petterson pivoted to create wearables that can predict the potential of injuries, ultimately resulted in something more sustainable and datadriven than exoskeletons.
Petterson’s company, StrongArm Technologies, delivers IoT safety wearables designed to prevent injuries before they happen. Consisting of a sensor that sits on a hip clip or strapped between an individual’s shoulder blades, it collects data measuring a variety of inputs at a rate of 12.5 times per second and analyzes all the moves of the wearer’s torso. That information provides real-time alerts to the wearer—which Petterson calls the “industrial athlete”—to tell them when they are doing something that could compromise their safety.
It calculates the most common predictors of injury, such as twisting velocity, and other factors that weigh into a safety score. If the worker enters into an unsafe range of movement, the sensor will send a vibrational or light-based alert that prompts the person to modify behavior. “If there are too many unsafe movements, the safety score begins to drop and if it drops below a threshold, [the system] gives feedback, like a tap on the shoulder [urging them] to rethink things before completing the task.”
When the wearer returns the sensor to StrongArm’s SafetyWork system dock, the information is sent to a cloud-based platform providing managers with actionable insights over time. Logged events are mapped each day and a proprietary algorithm populates the dashboard for individualized safety metrics, customized reports, and industry benchmarks. Taken together, these insights enable proactive intervention and facility-wide risk engineering.
“We are not trying to engineer around something but, rather, create a baseline to engineer out all of the risks,” Petterson said. “It was complicated to get here, but in practice we’ve made it simple.”
The SafetyWork system processes the data into profiles so industrial athletes can see where they can improve. But it also gives managers actionable insight to do predictive injury analysis and correlate how a change in safety score may result in injury, giving them information to adjust the work environment for improvement. For example, if someone’s safety score drops, the manager can identify underlying causes. Perhaps they need training, or they’ve worked too many shifts and need a break. “Most injuries happen over time and get worse with indicators, so we are finding the way movement leads to early indicators to be ahead of the curve before an injury happens,” Petterson explained.
According to Petterson, it’s a call to action. And it pays off, especially in the current environment of high employee turnover. Many companies operate on pay incentive, offering a bonus for every unit fulfilled above the 100% threshold. But overworking employees in the warehouse often leads to injuries which results in added costs to the company. “We found you can incentivize up to 2%, but anything over that there is so much risk that the ROI is backwards.” And employees often respond favorably to companies that encourage them to go home when they are done with their shift. “You can retain about 50% of the workforce just by keeping them safe.”
And let’s not forget that the government is watching. OSHA’s Regional Emphasis Program for Warehousing Operations is currently focusing on employers in Pennsylvania, Delaware, the District of Columbia, and West Virginia, and it will include on-site inspections that will hold employers accountable for providing a safe environment. StrongArm Technologies offers a way to mitigate risk, making worker safety a priority.