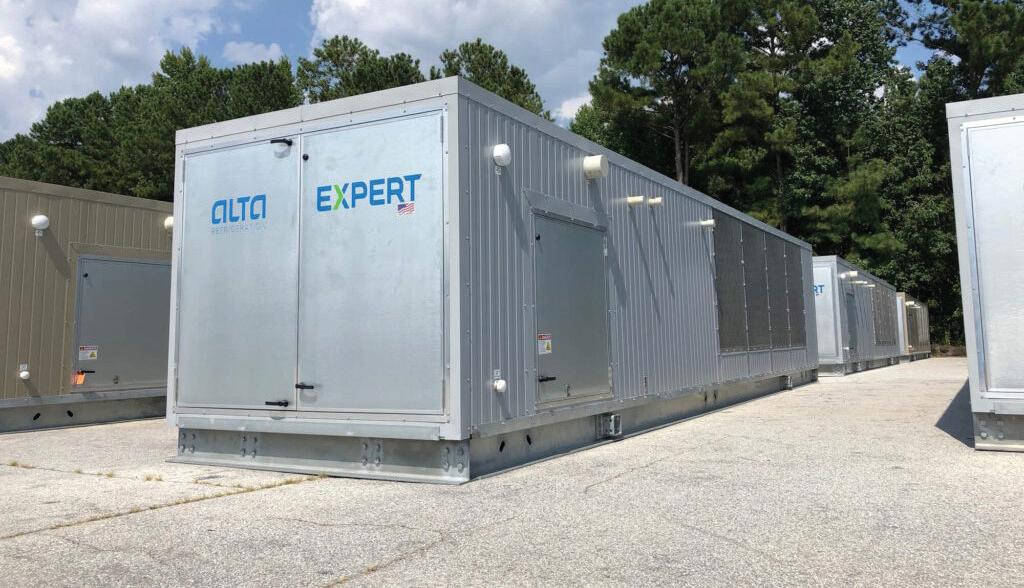
31 minute read
DIGITAL TRANSFORMATION SECTION
How Network Communications Drive the IIoT Revolution
Internet of Things communication methods such as OPC UA, MQTT, and REST API make field level data available to the cloud, creating flexible production networks to support efficient manufacturing.
By Lukas Pogoda, product manager for industrial communication, Pepperl+Fuchs
The properties of IIoT (industrial Internet of Things) communications differ significantly from more familiar control protocols, such as EtherNet/IP, Profinet, and EtherCAT. So, how can manufacturers assess the numerous communication methods available to them to take advantage of the IIoT?
The first step is realizing that IIoT and Industry 4.0-based solutions require detailed data. IO-Link is a standardized sensor interface, which provides access to detailed sensor/actuator data from the lowest field level, meets this requirement. While digital switching sensors provide only individual bits, IO-Link provides access to detailed identification, diagnostic, and parameter data from a sensor or actuator.
Next, take note of the fact that most automation systems are based on a PLC that contains the logic of the application. For applications such as controlling a robot arm, sensor data needs to be highly accurate and reliable. In a few milliseconds, the PLC calculates the output signals and transfers them to actuators, such as valves and motors. Control-based Ethernet protocols, such as Profinet, EtherNet/IP, and EtherCAT, meet these requirements.
Although these protocols are essentially based on the Ethernet standard, specific properties have been changed to achieve the high degree of timing accuracy and quick millisecond cycle times required in industrial applications. The data carried by these protocols can only be exchanged using special hardware, such as a PLC, and processed using specific software offered by the control system manufacturers. But transferring data from the field level to higher-tier systems, such as cloud-based systems, is a basic requirement for IIoT.
OPC UA, MQTT, and REST APIs
This is where IIoT communications such as OPC UA, MQTT, and REST APIs come in. These communication methods rely less on real time data in the millisecond range and more on end-to-end data availability across different systems from different manufacturers. IIoT is not about the individual process data of sensors and actuators, but rather about the overall picture. The most important process may be collecting condition data to avoid any future failures or detecting correlations in process parameters that have an influence on product quality. In these operations, real time is not a top priority.
OPC UA is an entire framework with sophisticated security mechanisms. A key advantage of OPC UA is that no specific device description files are required. Each individual device has all the necessary data, such as its own data structure, in a format that can be read by both people and machines. OPC UA is especially suitable for larger IIoT projects, where devices from different manufacturers must be combined but the network can still be dimensioned accordingly.
While OPC UA largely operates using client/ server connections, MQTT is based on the publish/subscribe mechanism (note: OPC UA also now supports publish/subscribe, though most existing installations use the traditional client/ server method). In publish/subscribe, a publisher (data provider) provides its data to a centrally located server (often referred to as a broker) on the network. Subscribers (data consumers) can flexibly subscribe to all the publisher’s data or to individually selected topics. Since there is no permanent connection between the publisher and each subscriber, the data overhead for MQTT is significantly lower. This makes MQTT especially suitable in networks with limited availability or when information must be transmitted to several consumers at the same time.
An API (application programming interface) is a programming interface provided on a device. REST stands for Representational State Transfer and outlines the conditions for designing the API. A REST API allows customers to create their own applications based on the device data, where basic conditions are defined without obligation. The APIs for an organization’s own devices are standardized within that organization. This makes REST APIs especially suitable for applications where many different devices from the same manufacturer are used.
The key difference between IIoT communications and control network protocols is that IIoT communication methods were designed to allow for an end-to-end and transparent data flow from the sensor to the cloud, enabling the huge potential of Industry 4.0 and IIoT.
Aligning Manufacturing Teams with Data, Collaboration, and Visibility
How industrial organizations can leverage trustworthy information in real time to boost their ability to aggregate, contextualize, and share data to support key business drivers such as improving productivity and cost optimization.
By Rashesh Mody, executive vice president, operations business, Aveva
As organizations manage through ongoing value chain disruptions that have been contributing to worldwide inflationary pressures, many are taking a step back to assess their supply chain strategies, including the role of the plant. Organizations are looking deeper at the adoption of technology and how they connect data to their people at the right time and in the right way to stay competitive and drive value.
In a 2021 consumer packaged goods (CPG) study by Google, digital initiatives—including data platforms and connectivity—were recognized to have the potential to unlock US$490 billion by 2023. Additionally, 90% of top CPG manufacturers are not yet using digital solutions at scale in support of workforce augmentation or automation, according to SmarterChains in a 2020 report. Taking these two data points together, one can recognize the potential opportunities and challenges manufacturers must navigate amid the ongoing need to drive agility and efficiency in support of operational excellence.
Whether the focus is on driving product quality and food safety, energy utilization, or increased production efficiency, one key step organizations should take is to give teams and individuals full visibility across operations relevant to their roles. This gives organizations the visibility and control to be agile and drive efficiency and collaboration from the edge to the enterprise. On the plant floor, this could translate to providing teams with access to information on their smart devices so that, when an anomaly is detected, operators can quickly access cloud collaboration tools and determine the next steps or call for help. Skills and knowledge development on the plant floor also becomes more critical as workers change roles or leave the organization. New technology that offers collaboration, skills development, and better ways to handle abnormal situations can help organizations manage through skills gaps and spread the knowledge held by plant floor subject matter experts.
Organizations can further expand awareness by leveraging trustworthy information, in real time, structured in a way to bring forward insights and amplify value. This becomes a stepping-stone toward an organization’s ability to aggregate, contextualize, and share its data throughout the enterprise. Then it can begin to leverage artificial intelligence (AI) and predictive analytics to support key drivers like improving productivity and cost optimization. In the control room, supervisors could leverage their SCADA applications across a single or multi-site operation and push data to a centralized information management system. This enables organizations to gather AI-infused insights that support asset management and overall equipment effectiveness (OEE) for proactive monitoring and downtime tracking.
Beyond the plant floor and control room, organizations are looking for new ways to drive awareness and performance guidance across the enterprise. Deploying single-pane-of-glass enterprise visibility is beginning to help some manufacturers uncover previously inaccessible value by converging engineering, operations, and other business data in context. These systems need to aggregate data from any available data sources, which could include HMI/SCADA, historians, information management, IIoT (industrial Internet of Things), ERP, finance, market data, maintenance, and connected worker systems. This convergence goes beyond charts and numbers to provide rich intelligence that helps analysts and decision-makers respond quickly to performance-influencing events. At this level, going beyond a plant-centric view can help guide strategies to mitigate immediate supply chain impacts and help organizations plan for the future.
To succeed in the current market environment, organizations must become more adaptable, agile, and collaborative and they must ensure that information gets in front of the right people quickly. Their technology must align to the needs of their teams and it must scale and adjust with their businesses over time. To achieve this, they must continue their transition toward hybrid (on-premises and cloud) solutions and software-as-a-service (SaaS) for greater flexibility. This helps to ensure that organizations achieve longterm benefits from the technology they employ, and specifically the software their teams require to be successful, independent of location or device, from the edge to the enterprise.
Case Study: Launching a Nationwide Equipment Network
A look at how Alta Refrigeration achieves faster, easier product development and servicing with groov EPIC and MQTT.
By Benson Hougland, vice president of product strategy, Opto 22
What’s the secret to providing superior service and staying competitive in a changing market? Well, you might learn something from Alta Refrigeration’s experience. Over 10 years, it transformed itself from a custom engineering services company into a scalable industrial equipment manufacturer using an edge-oriented control architecture to efficiently manage a growing installed base.
Alta has been designing and installing refrigeration systems across the United States for more than 45 years. For many years, these systems were large, custom-designed systems that used a central machine room to deliver refrigerant to various facility areas through long, overhead piping runs. Due to their size, these systems required significant time to design and program, and competitors were able to steal some of their market share with cheaper, simpler offerings.
“Competitors could use 20-30 cheaper units with control limited to a dumb thermostat to compete against one of Alta’s large systems,” says Peter Santoro, controls engineer at Alta.
Alta knew it couldn’t compete by reducing its product quality, so the company looked for a way to standardize its offering without sacrificing features.
We’re the Experts
In 2013, Alta introduced its Expert series of modular refrigeration control units. Each unit uses a standard, reliable design and can be mounted on the roof above the area it served, simplifying installation.
“A single Expert has almost as much I/O as an entire centralized system and, because the units are much smaller, the wiring and conduit runs are incredibly short, allowing us to cram in a ton of sensors,” explains Santoro. “The units themselves are also incredibly efficient. We analyze external ambient conditions and refrigerated space and do real-time thermodynamic calculations. This lets us do variable capacity refrigeration, and only run exactly the amount of refrigeration as needed. All motors are on variable speed drives. We also design many of the sensors we use on the system,
Each Expert follows a standard, reliable design that can be mounted on the roof above the area it serves.
allowing us to get precise valve positioning and monitor refrigerant levels throughout the system. We make good use of Hall effect sensors in various configurations to monitor refrigerant levels and motor positions. There is also a dedicated energy monitor on each unit so we can monitor voltages and power usage.”
Since all Expert systems are essentially the same, Santoro and his colleague, Todd Hedenstrom, were able to focus on creating a robust and complete solution that works for many different applications.
A good problem to have
Market response to Expert has been very positive. Alta has sold nearly 600 units and is typically sold out into the next year. But growth brings its own challenges. With only a small controls engineering team, servicing the growing installed base became time-consuming.
Adding to this time crunch, some aspects of Alta’s previous designs related to system maintenance issues. For example, the control system required numerous steps to properly update control strategies in the field, including exchanging files between the control engine and the web server used for remote connectivity. And because Alta had previously left the details of remote connectivity to each customer, this increased the team’s workload by requiring them to check in on each site every day using different methods—such as VPN, Citrix, LogMeIn, and TeamViewer.
Alta’s centralized control system design was built around an industrial PC (IPC) running custom C++ code on top of a distributed I/O system from Opto 22. When designing Expert, this control system was simplified by replacing the IPC with an Opto 22 PAC (programmable automation controller).
Though this change was an improvement because it allowed for all the components of the system to be managed through the PAC, it still required a multi-step update process and didn’t provide as much data access as Alta wanted. This led Alta to explore use of Opto 22’s groov EPIC (edge programmable industrial controller) system.
EPIC supports all the power, I/O, communications, storage, and networking functions of an IPC and PLC on a single backplane without the complexity of maintaining a full Windows OS environment. Alta upgraded the Expert control system to Opto 22's groov EPIC to gain access to more flexible control and communication options.
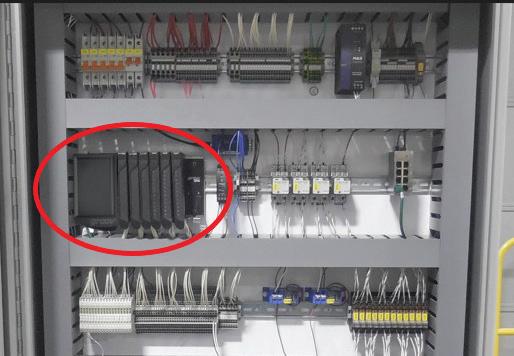
Each Expert provides a local unit interface through an embedded web server that runs on the unit’s EPIC.
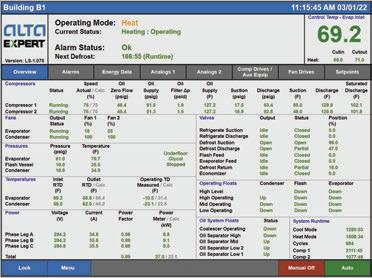
Web interface via the controller
Santoro and Hedenstrom started by using groov EPIC’s operating system shell to port their PAC application to C++.
The new program controls the installed I/O modules—voltage and current sensing inputs and discrete AC outputs—using Opto 22’s C++ OptoMMP SDK (software development kit). The application also includes its own Modbus server that creates and manages connections to variable frequency drives, the local energy monitoring unit, and other remote devices.
“We [also] have our own REST API and webserver running on the C++ application,” Santoro adds, “allowing us to create our own web page interfaces in HTML and Javascript,” such as a Google Chart API (application programming interface) to display energy metrics in the HMI.
Each Expert web interface is served from an EPIC controller. The interface includes prebuilt templates for different unit configurations and verifies system settings to help technicians identify configuration values that are out of range or not recommended. It also generates alarms as needed. Alternatively, customers can access unit data through the Expert’s Modbus server or REST API.
For managing groups of Experts, Alta uses a separate HMI server to read data from each unit and present a unified view of the entire system. “All of our sites are required to have a local interface for operators to see a global view of their refrigeration units, instead of having to manage network connections to hundreds of individual units,” Santoro explains.
To create this site-level HMI, each Expert stores transient data in the shared memory scratchpad area of the groov EPIC. Alta’s HMI server runs on Windows and uses Opto 22’s .Net OptoMMP SDK to retrieve data from all units in one-second increments. Data is stored in cyclical files that maintain a oneweek buffer, and the HMI server uses this data to generate trends, charts, and email notifications.
Alta can also access this data remotely for troubleshooting recent events. By default, groov EPIC does not route traffic between its Ethernet ports, so Alta can use the controller to create a security zone for each Expert. One port on each EPIC connects to a private network exclusively for the controller and its remote devices. The other port is connected to a common network between all the units at a given site, as well as the local HMI server.
This server is connected to the internet and uses MQTT to send and receive data, acting as a middleman for each individual Expert to the MQTT broker that resides in Alta’s headquarters. When Alta’s remote HMI requires new data, it sends a request to the local server over MQTT. The data is then queried and sent back. External connections to local HMI servers are restricted so that the only traffic allowed through is from outbound MQTT TLS connections.
Recently, Alta also made it possible for customers to access this remote server. The server has its own database that records temperatures and energy usage for each Expert in 10-minute intervals.
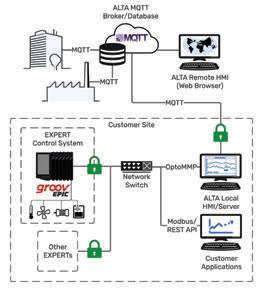
Alta’s nationwide network connects each Expert to its central server through a local HMI and MQTT gateway.
Nationwide data aggregation
Using groov EPIC, Alta has now built a nationwide HMI that aggregates data from its network of Expert units and highlights any issues the team needs to act on. Instead of spending hours every day to check on each site, they can monitor their entire installed base in minutes. They know when there is a problem, can input and track necessary work orders, track technicians’ locations, and monitor energy usage per unit. When an alarm occurs, the system creates an interactive timeline of events before and after the alarm event.
“Often, we know what the problem is before the customer calls. We just need to drive there and fix it,” says Santoro. “With the amount of data we get from our units, we are capable of diagnosing the vast majority of problems remotely. This allows many of our end users to not even staff on-site maintenance. And there’s no interfacing with third-party systems anymore. It’s all integral.”
Servicing the systems themselves has also become much simpler now that Alta can manage the entire platform—I/O configuration, control strategy, communications, and networking—through a single device. “One of the best features we introduced was the ability to update the programs through our web interface. Now a batch program packages all the program files into a .gz (compressed) file. Technicians can upload the file and restart the system,” Santoro says.
Alta also uses the groov EPIC’s touchscreen as a maintenance interface inside the control cabinet. The native groov Manage application allows them to view and modify I/O and network settings directly on the controller without using a separate computer interface. Using the EPIC’s native HMI server, groov View, Alta also provides technicians with local control options and basic information about the Linux program’s status.
Why So Complicated?
By Michael Bowne, executive director, PI North America
As Industry 4.0 trends have taken shape over the last number of years, rapid advances in technology are now awaiting adoption by industry. But creating technology merely for technology’s sake serves the few rather than the many. Focusing instead on addressing use-cases has proven effective, but something more is needed for adoption to occur. And that is: ease-of-use. A renewed focus on usability is required for today’s technologies to become tomorrow’s solutions.
Let’s all take a trip down memory lane to the days of Profibus DP. Which, by the way, isn’t going away and is still a great technology used in many factories today. If we think back to the way we installed these serial networks, there were certainly opportunities for mistakes. You had 9-pin D-Sub connectors, rotary switches for device addressing, segmentation with repeaters, termination resistors, and so on. It wasn’t overly complicated, but it wasn’t idiot-proof either.
The result was that the most common causes of problems on a Profibus network were wiring or installation issues. With industrial Ethernet all of that changed. Now, instead of an RS-485 physical layer, we use the Ethernet physical layer, eliminating all those wiring complications.
This means that, if you need to extend the network, you simply install an Ethernet switch. Rotary switches for addressing and termination resistors are no longer needed. With the step from Profibus DP to Profinet, we’ve eliminated most causes for problems on an industrial network.
With Profinet, we’ve made addressing easy because the controller handles it. And with Profinet we use names—not numbers—to address devices. BOOTP or DHCP are not needed (although they are optional). Instead, you assign the names, and the controller assigns the IP addresses. And it gets even easier. If you program the network topology into the controller, it can auto-assign device names, making the process even easier.
But what if you need to replace a device? The same underlying technologies—DCP (discovery and configuration protocol) and LLDP (link layer discovery protocol)—that enable easy naming and addressing also make it possible to swap a failed device for a replacement. Simply remove the failed device and swap in a replacement. That’s it. No computer or configuration tools are required. Just plug and play. Profinet leverages these IT technologies to make it happen ‘automagically’.
TSN and APL
So how does the future look with TSN (time-sensitive networking) and Ethernet-APL (advanced physical layer)?
First things first. You might be asking: I have been hearing about TSN for years now, where is it? The reason TSN is taking time to reach fruition is because of how fundamental it is. And if fundamental networking aspects are not transparently usable by upper layer protocols, then the whole building collapses. So while the underpinnings of TSN were completed a few years ago, the work being done now is to make it easy to manage. At the end of the day, TSN is just Ethernet. And just as Ethernet is easy to use today, TSN should be just as easy.
As for Ethernet-APL—an intrinsically safe version of Ethernet for explosive and hazardous environments—it is as fundamental as TSN, if not more so. Whereas TSN is an ISO/OSI layer 2 technology, APL is a layer 1 technology. But the same principles should apply regarding usability. Profibus PA already exists as an intrinsically safe way to network instruments directly in hazardous areas, so the concept is not new. Ethernet-APL now allows Profinet to do the same. And just like the step from Profibus DP to Profinet, usability is greatly enhanced moving from a serial physical layer to Ethernet. It is left to the protocol to implement the naming, addressing, device replacement, and other usability features. In other words: Ethernet-APL takes Profinet down to the instrument, with Profinet making it all easy to manage.
Our goal at PI is to make technological advances like TSN and APL easy to use. Otherwise, adoption will lag. These technologies are foundational, but not the complete story. TSN gets us there for robust converged networks, but because it’s just Ethernet, it should have the same level of usability as non-deterministic Ethernet does today. That’s where efforts are focused now. APL brings Profinet into hazardous areas, but APL is just the physical layer. The Profinet protocol is what makes the difference in terms of usability.
Why Edge Devices are Essential to IIoT Applications
From reducing the amount of data that needs to be sent to the cloud for analysis to improving condition-based monitoring applications, edge computing devices are the local devices enabling an on-site industrial Internet of Things.
By Charlie Norz, product manager, automation, Wago Corp.
Digitalization in today’s global economy has become a necessity for modern manufacturing facilities. When running IIoT (industrial Internet of Things) applications, most—if not all—data needs to be collected, sorted, and analyzed in real time. To move between the cloud and local devices, an edge device is needed. These edge devices can transmit data between protocols used by local devices into the protocols used by the cloud. Instead of directly sending data to an off-site cloud to calculate analytics, edge devices can provide local execution of data analysis with low latency and a high level of determinism.
Data at the edge of the network can also be aggregated and contextualized to send rich, summary information directly to the cloud, ultimately reducing cloud data storage costs. Other edge computing benefits include condition-based monitoring, which can help prevent critical failures and downtime, as well as lower parts inventory and maintenance costs.
Another advantage to many edge devices is their use of the future-proof Linux operating system. Linux has been around for more than 30 years, and its acceptance has been growing exponentially. Used in most servers as well as in many military applications, it is robust and users can be confident that this open-source platform will continue to be available. Not having to update to a new platform every few years makes Linux-based edge devices ideal for innovative IIoT applications.
How to begin using edge devices
The first step in using edge devices is to find a business problem you are looking to solve. Instead of looking at the entire scope of the problem, try to break the issue down into small, manageable sections. Once you have done that, determine the priority of each— from highest to lowest.
The next step is to start collecting your plant floor data using containerized applications to analyze all the data. The benefit here is that both the connected worker on the plant floor as well as management can use the data to troubleshoot problems at the manufacturing level as they happen. It also helps off-site management look at efficiency, logistics, and other data to determine what is working, what areas need to be looked at more closely, and formulate plans for improvement on a long-term basis.
Depending on your industry, a good place to start may be your asset management program. If we look at this as an example, there are many pieces of key data that can be analyzed to help improve your company’s bottom line. These may include power consumption, vibration, bearing temperature, pressure, and uptime. Using this information, patterns can be recognized to determine causes of failure and what can be done to avoid those failures in the future. This can all done using edge computers to track and store data for delivery straight to the user when needed.
Wago’s edge approach
Wago combines the advantages of decentralized cloud computing with local control networks with our Edge Controller and Edge Computer. The Edge Controller is used to collect plant floor data information from industrial fieldbuses. If the application calls for it, these data can then be published directly to the cloud. If not, the Edge Computer can take the Edge Controller data, sort them and run analytics locally before posting to the cloud for anyone with proper access rights to see.
Digital Transformation Lessons from a Smart Monitoring System for Potable Water Treatment
How the German city of Oberzent connects decentralized measurement points using LoRaWAN and Endress+Hauser’s Netilion IIoT technologies.
Acritical task for a water master in Oberzent, the third largest city in terms of area in the German state of Hessen, is to visit each water reservoir and plant individually to read the measured values and check the instruments. That has changed with Oberzent’s adoption of a new low-power LoRaWAN network (long range wide area network) for its water management system. The LoRaWAN specification is a networking protocol designed to wirelessly connect battery operated devices to the internet in regional, national, or global networks, and targets key Internet of Things (IoT) requirements such as bi-directional communication, end-to-end security, mobility, and localization services.
In addition to the LoRaWAN adoption, parts of the city’s measuring systems have been modernized to integrate the individual reservoirs and plants into a cloud-based monitoring system. This provides the city’s water masters with all information they need at any time, whether they are using a mobile device or at their computer in the operations center.
A reservoir in Oberzent, Germany.
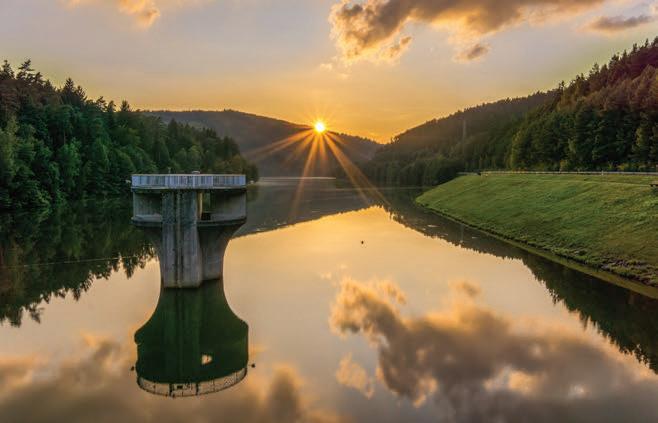
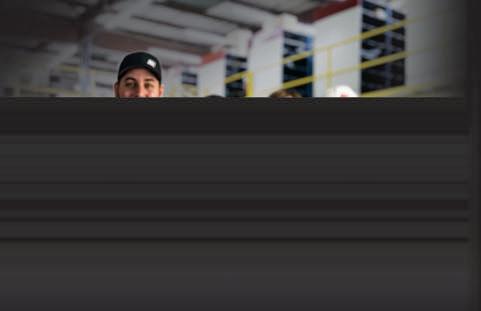
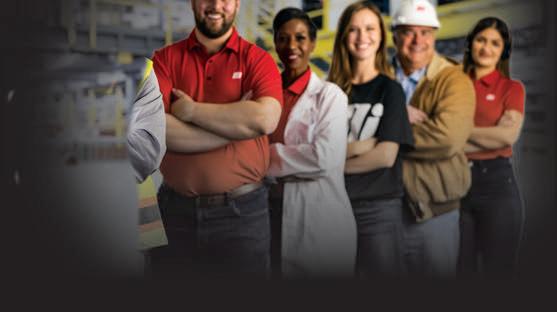
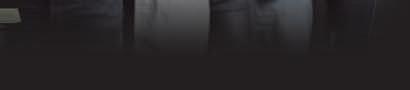
Motion is a leader in delivering the services and supplies that keep essential industries up and running.
Smart technology boosts efficiency
The reliability of the water supply in each of the city’s 19 districts has top priority in serving the city’s 10,248 citizens. The local water masters maintain a total of seven springs, two deep wells, and 18 reservoirs. As there are just four water masters in charge of maintaining the water network, each has a corresponding high workload. To ensure the water supply network is always running smoothly, the water masters had to deal with obstacles in the Odenwald forest every day, as they were required to gather and process information from 19 decentralized water infrastructure facilities spread out over a territory of 165 km2. To do this, water masters spent a large portion of their workday driving around to the facilities, taking away time that could be spent on other water management tasks.
The installation of a cloud-based monitoring system has now made all relevant information available in centralized form for the water masters. This makes it possible to visualize data from 60 decentralized sensors across 35 flowmeters, 17 level meters, seven pressure meters, and two analysis panels for quality monitoring. The lack of stable cellular service coverage in many areas of the Odenwald forest made it necessary to set up wireless data transmission that does not use much energy. The LoRaWAN technology is ideal for this application where small amounts of data have to be transmitted over long distances (up to 15 km/9.3 miles). Additional benefits of LoRaWAN are low energy consumption, low costs, and secure data transfer. Even though the LoRa alliance specifies a uniform standard, LoRaWAN can be used without a contract with a mobile communications provider. The local energy utility, Entega, manages construction and operation of the LoRaWAN network in Oberzent.
Everything at a glance
The city’s water masters now see all relevant data points from their water treatment system on a cloud-based dashboard. The dashboard, developed by Endress+Hauser using its Netilion IIoT (industrial Internet of Things) technology, shows the various networks and can be used by the water masters on a variety of devices, including smartphones, tablets, and laptops. This makes it possible to skip the daily routine visits to the reservoirs and water treatment stations and perform work on various terminal devices remotely through the technology’s web-based service access. This allows the water masters to use their time much more effectively. It has also increased the water masters’ ability to react thanks to proactive processing of problems in the water network.
“Our water masters can now spend more time on their core tasks and less time making trips out to plants. This is key because these specialists are currently in short supply on the job market,” says Christian Kehrer, mayor of Oberzent.
With the Netilion IIoT ecosystem, Endress+Hauser offers a variety of solutions for a smart city. In Oberzent, Netilion provides the basic data needed for creating and programming individual dashboards that display the entire process of water treatment and storage. This is implemented in the online service Netilion Water Network Insights, which enables monitoring of water networks as well as process optimization via actions such as leak detection or reservoir management.
Endress+Hauser has vast process knowledge in the water and wastewater industry as well as in instrumentation. This makes us a strong partner, whether you need one individual sensor or a fullfledged cloud application as a complete solution. Endress+Hauser offers plant operators certified instrumentation for all processes, combined with solutions for data transfer as well as data processing and visualization.
Creating an Energy Management System
With the help of Mitsubishi Electric technologies, automation and engineering company Versatech has developed a system to collect and visualize real time plant-wide energy consumption that can be accessed remotely.
Versatech, a multi-faceted engineering company based in Effingham, Ill., continually expands its offerings to meet the needs of its customers with automation, robotics, work holding, machining, contract manufacturing, and lean manufacturing consulting. Recently, Versatech has focused on offering energy management systems among their data management solutions.
As an authorized systems integrator for Mitsubishi Electric, Versatech uses Mitsubishi Electric technologies to deliver turnkey energy management solutions. The energy management offerings from Versatech can be used to perform ASHRAE energy assessments; provide in-depth analysis and reporting; identify specific energy conservation opportunities; and help design, integrate, and install energy saving hardware and software that deliver both immediate and ongoing savings.
The company’s energy management offerings are already providing significant cost savings for large industrial facilities.
Cost reduction via better energy management
Energy costs around the use of water, air, gas, electric, and steam represent a large portion of the operating expenditures for most manufacturing facilities. They also represent a huge savings opportunity. In fact, the U.S. Department of Energy estimates that energy management efforts at large American manufacturers have saved about $2.4 billion in the past five years alone. And this figure comes from facilities representing only a tiny fraction of the country’s overall manufacturing energy footprint, meaning that there are likely savings representing tens of billions of dollars more yet to be achieved through smart energy management solutions.
“Many times, companies assume that high energy costs are just a cost of doing business and that not much can be done to reduce them. This is simply not the case,” explained Greg Gillespie, data program manager at Versatech. “Measuring energy costs is the first step in reducing them, and that’s where Versatech and Mitsubishi Electric come in.”
Agri-Fab uncovers hidden energy drains
As leader of Versatech’s Energy Management Solutions offering, Gillespie is working to open the eyes of manufacturers to the significant results that can be achieved. A good example of this can be seen in Versatech’s work with lawn equipment manufacturer Agri-Fab, which asked Versatech to perform an energy assessment in its plant. Based on the resulting suggestions, Agri-Fab had Versatech install a customized energy management system to monitor its production equipment.
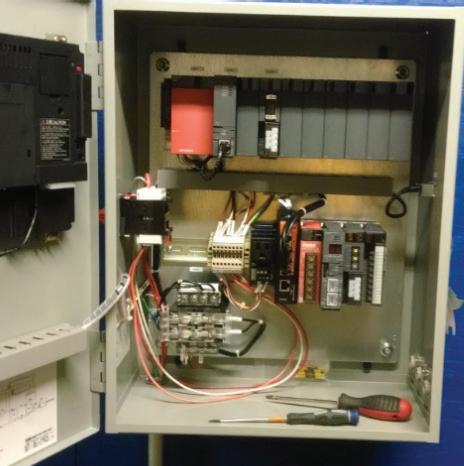
A control cabinet created by Versatech for Agri-Fab featuring Mitsubishi Electric technology.
An Agri-Fab 100-lb. two drop spiker/seeder/spreader.
Versatech specified Mitsubishi Electric energy management components for this system, including the high-speed, high-accuracy Q Series programmable logic controller and the EcoWebServer III, an easy-to-use, scalable system that collects energy consumption data throughout the plant and provides snapshots and trend data to be viewed in graph form in real time, 24/7, from anywhere using a standard web browser. This web-based visualization method eliminated the need for a server and related management and maintenance costs.
Since Agri-Fab did not yet have any networked metering devices in place on its equipment, Versatech installed several networkable meters, including four Mitsubishi Electric meters, allowing for the capture and storage of equipment energy usage data.
Not long after Versatech installed the system, Gillespie said they received a call from Agri-Fab indicating the energy management system was malfunctioning. Agri-Fab thought the system was generating incorrect consumption data, but that wasn’t the case.
“We investigated right away and found that the energy management system was operating just fine. It had discovered a significant energy drain that Agri-Fab probably wouldn’t have found otherwise,” explained Gillespie.
The source of the energy drain was Agri-Fab’s paint curing ovens. After a recent maintenance procedure, the ovens weren’t reset properly, causing them start up for brief periods after hours when no one was likely to be in the facility and wasting significant amounts of energy.
Fixing this issue alone immediately led to annual energy cost savings of nearly $70,000 for Agri-Fab.
But that was only the beginning of the fast and easy energy savings generated by the Mitsubishi Electric technologies in the Versatech system. For example, an anomaly was discovered in air compressor use at the plant. Correcting this issue led to an estimated additional $50,000 in annual energy cost savings.
As with the paint curing ovens issue, Gillespie said “there was probably little chance of the air compressor issue being discovered without the Versatech system in place.”
Gillespie believes that there is much more savings yet to come with Agri-Fab continuing to monitor energy consumption over time.
“This is a continuous improvement tool that allows customers to benchmark, monitor, and continue to reduce their energy costs,” he explained. “We provide training so that our customers can be self-sufficient in getting the most out of it, and we are also always at their service to provide any additional support that they might need.”
Other parts of the Mitsubishi Electric energy management product line carried by Versatech include the MC Works software with analytics package, which gives users highly customizable dashboards and reporting capabilities, and MES Interface IT—a unique tool that allows the consolidation of data from nearly any brand of network equipment into a single database without the need for a PC.
“MES Interface IT is a great product,” said Gillespie. “The integration is fast and seamless, with nearly no coding involved. And you avoid the hassles of a PC, alleviating the need for firmware upgrades and the threat of a computer crash or of the computer choking on the data flow. Once the MES is installed, it just sits in the rack and does its job very, very well. It’s the most robust solution out there.”
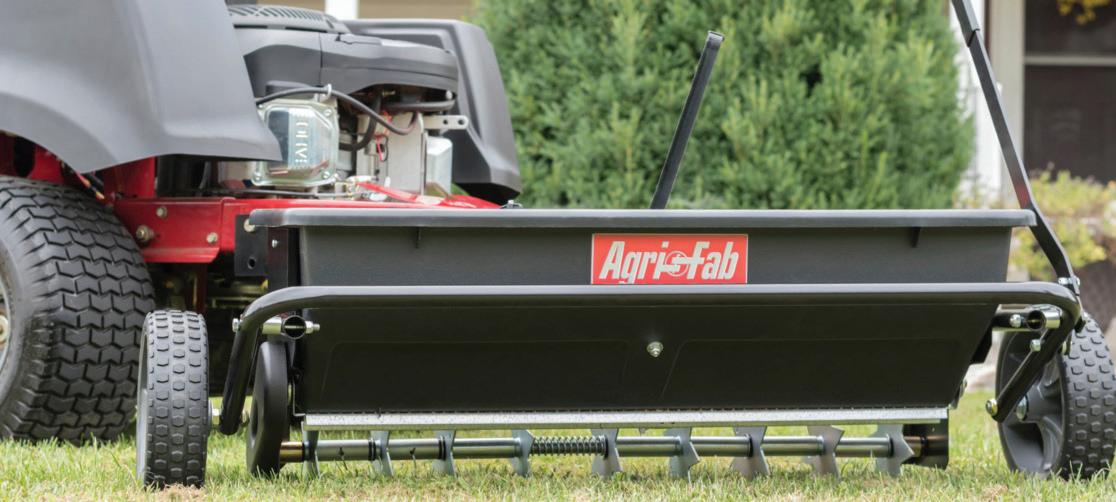
Getting started with energy management
No matter what system is ultimately chosen by a user, Gillespie says the most important step is to start the measurement process so that sources of wasted energy can be identified and addressed.
“Energy management is not a complex concept. You collect your data, establish a baseline, and act on the information to effectively save energy and save money,” he explained. “Mitsubishi Electric products help give us the capability to do that very successfully for our clients—and they’re excellent products at very reasonable prices.”