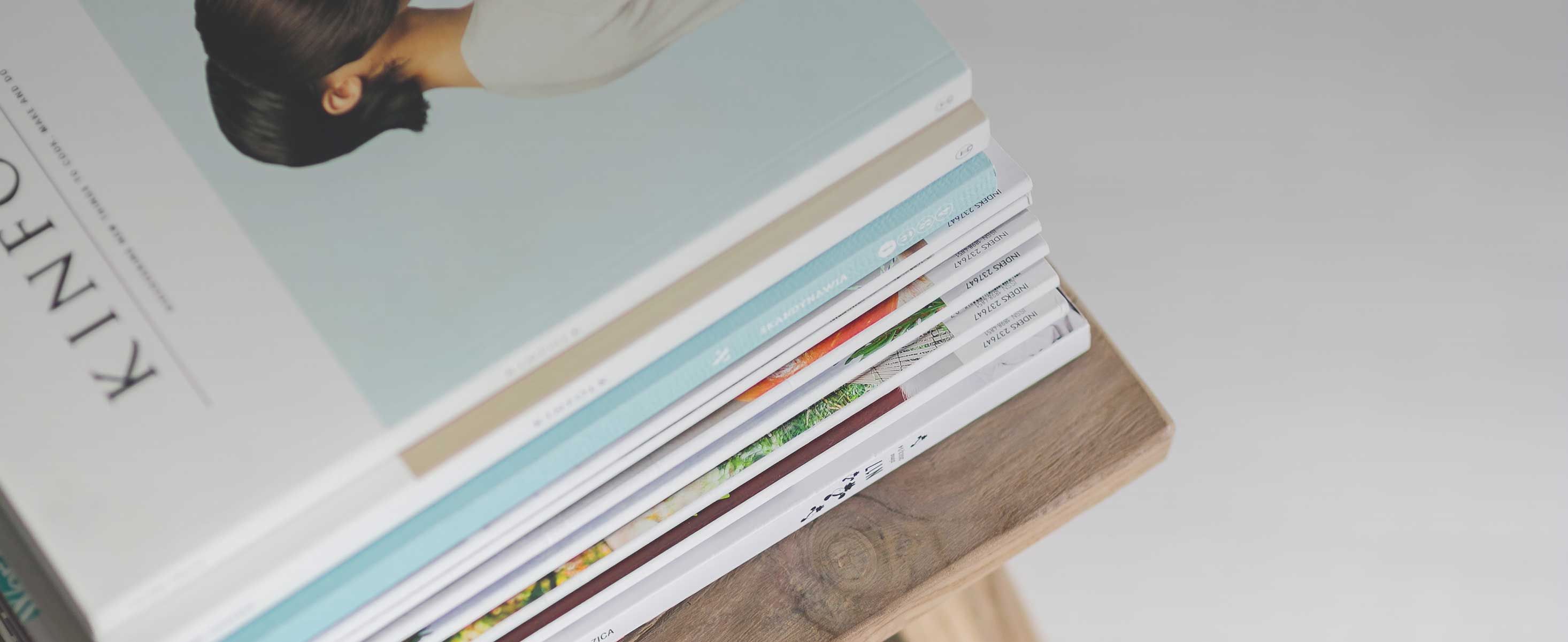
12 minute read
Green Cleaning Specifications
The intent of green maintenance and cleaning services is to reduce the negative impacts on health and the environment that have long been a traditional part of conventional cleaning products and practices. The focus of this section is on pollution prevention strategies and some specific opportunities to modify traditional procedures to reduce impacts on health and the environment. Our goal is to create a balance between reducing the impact our buildings have on the environment, social responsibility and increasing value for our clients.
Elements of Green Cleaning Policy
All safety, health and environmental practices must comply with applicable local regulatory requirements.
All cleaning waste should be disposed properly, recycling when appropriate.
All janitorial service personnel should be properly trained in the use, maintenance and disposal of cleaning chemicals, dispensing equipment and packaging. Training records certifying each person’s specific training dates will be documented.
Training on Procedures: Sequencing of cleaning steps and use of personal protective equipment.
Training on Safety: Training on how to reduce and prevent ergonomic injuries and exposure to hazardous materials.
Annual In-Service Training: Training on use of certified green cleaning products, materials, and equipment.
Training on Purchasing: Training of purchasing personnel in the selection of green cleaning materials.
Cleaning products must meet one or more of the following standards for the appropriate category:
Green Seal GS-37, for general-purpose, bathroom, glass and carpet cleaners used for industrial and institutional purposes.
Environmental Choice CCD-110 (now UL Ecologo 2792), for cleaning and degreasing compounds.
Environmental Choice CCD-146 (now UL Ecologo 2759), for hard surface cleaners.
Environmental Choice CCD-148 (now UL Ecologo 2795), for carpet and upholstery care.
UL Ecologo 2791, for drain or grease trap additives
UL Ecologo 2796, for odor control additives
Green Seal GS-2796, for specialty cleaning products
EPA Design for the Environment Program’s Standard for Safer Cleaning Products
Disinfectants, metal polish, floor finishes, strippers or other products not addressed by the above standards meet one or more of the following standards for the appropriate category:
Green Seal GS-40, for industrial and institutional floor care products.
Environmental Choice CCD-112 (now UL Ecologo 2798), for digestion additives for cleaning and odor control.
Environmental Choice CCD-147 (now UL Ecologo 2777), for hard floor care
California Code of Regulations maximum allowable VOC levels for the specific product category.
Disposable janitorial paper products and trash bags meet the minimum requirements of one or more of the following programs for the applicable product category:
U.S. EPA Comprehensive Procurement Guidelines for Janitorial Paper and Plastic Trash Can Liners.
Green Seal GS-01, for paper towels and napkins
Green Seal GS-01, for tissue paper
UL Ecologo 175 for toilet tissue and hand towels
Janitorial paper products derived from rapidly renewable resources or made from tree-free fibers. Hand soaps meet one or more of the following standards:
No antimicrobial agents (other than as a preservative) except where required by health codes and other regulations (i.e., food service and health care requirements).
Green Seal GS-41, for industrial and institutional hand cleaners.
Environmental Choice CCD-104 (no UL Ecologo 2783), for hand cleaners, hand soaps, and hand sanitizers
A log must be kept that details all housekeeping chemicals used or stored on the premises (stored products include those that are no longer used, but are still in the building). Attachments to the log must include Material Safety Data Sheets (MSDS) and Technical Bulletins. MSDSs from suppliers should provide full disclosure of ingredients. Additionally, suppliers must provide training materials on hazards and proper use of housekeeping chemicals for workers.
When available, chemical concentrates dispensed from portion-controlled, closed dilution systems should be used as alternatives to open dilution systems or non-concentrated products.
Resilient tile and hard flooring coating systems, including floor finishes and restoration products, should be slip resistant (as defined by ASTM STD D 2047). Additionally these floor coating systems should be highly durable in order to maintain an acceptable level of protection and appearance for a minimum of one year before stripping/removal and re-coating is necessary.
Definitions
Disinfect - A process for hard inanimate surfaces undertaken to destroy or irreversibly inactivate infectious fungi and bacteria, but not necessarily their spores.
Environmentally Preferable Product - A product certified as such by a Type 1 (i.e., third-party) environmental label that was developed in accordance with the ISO 14024 Environmental Labeling Standard.
Sanitize - A process intended to reduce, but not necessarily eliminate, microorganisms from the inanimate environment to levels considered safe as determined by public health codes or regulations
Bathroom cleaners - This includes products used to clean hard surfaces in a bathroom such as counters, walls, floors, fixtures, basins, tubs, and tile. It includes products that are required to be registered under the Federal Insecticide, Fungicide, and Rodenticides Act (FIFRA), such as disinfectants and sanitizers, but does not include products specifically intended to clean toilet bowls.
A written floor maintenance plan and log will be kept that details the number of coats of floor finish applied as the base and top coats, along with relevant maintenance/restoration practices and the dates of these activities. The duration between stripping and re-coat cycles should be documented
Carpet cleaners - This includes products used for routine cleaning of carpets and rugs. This may include, but is not limited to, products used in cleaning by means of extraction, dry foam, bonnet or absorbent compound. It does not include products intended primarily for spot removal. This does not include any products required to be registered under FIFRA, such as those making claims as sterilizers, disinfectants, or sanitizers. Powder carpet cleaning systems must be used in place of traditional carpet extraction systems, which includes dry encapsulation.
Concentrate - This is a product that must be diluted by at least eight parts by volume water (1:8 dilution ratio) prior to its intended use.
Dispensing-system concentrates - These are products that are designed to be used in dispensing systems that cannot be practically accessed by users.
General-purpose cleaners - This category includes products used for routine cleaning of hard surfaces including impervious flooring such as concrete or tile. It does not include cleaners intended primarily for the removal of rust, mineral deposits, or odors. It does not include products intended primarily to strip, polish, or wax floors, and it does not include cleaners intended primarily for cleaning toilet bowls, dishes, laundry, glass, carpets, upholstery, wood, or polished surfaces. This category does not include any products required to be registered under FIFRA, such as those making claims as sterilizers, disinfectants, or sanitizers.
Glass cleaners - This category includes products used to clean windows, glass, and polished surfaces. This category does not include any products required to be registered under FIFRA, such as those making claims as sterilizers, disinfectants, or sanitizers.
Ingredient - Any constituent of a product that is intentionally added or known to be a contaminant that comprises at least 0.01% by weight of the product.
Optical brighteners - Additives designed to enhance the appearance of colors and whiteness in materials by absorbing ultraviolet radiation and emitting blue radiation. Also known as fluorescent whitening agents.
Ozone-depleting compounds - An ozone-depleting compound is any compound with an ozone-depletion potential greater than 0.01 (CFC 11 = 1). Product as used. This is the most concentrated form of the product that the manufacturer recommends for a product’s intended use. For example, if a manufacturer recommends a product be diluted 1:64 or 2:64 for use as a general-purpose cleaner, the product shall meet the environmental and performance requirements at a dilution of 2:64. Primary packaging. This packaging is the material physically containing and coming into contact with the product, not including the cap or lid of a bottle.
Recyclable package - This package can be diverted from the waste stream through available processes and programs, and can be collected, processed, and returned to use in the form of raw materials or products.
Undiluted product - This is the most concentrated form of the product produced by the manufacturer for transport outside its facility.
Cleaning Cloths
Microfiber cleaning cloths (microfiber is made from nylon and polyester) are durable and have numerous uses which provide clear advantages over using disposable cleaning materials.
Mops, Rags, and dusters must be microfiber with a denier no higher than 1.0.
Microfiber benefits include:
Cleaning multiple types of surfaces – it is ideal for wiping surfaces, as it is lint-free and it holds dirt until the fabric is washed in hot water.
Ecological saving by reducing the need for paper towels – according to microfiber manufacturers, high-quality microfiber cleaning cloths typically have the potential to last 600 washings.
Microfiber towels and cleaning cloths of all sizes are available to use for scouring, cleaning, drying (absorbent microfiber) and wiping down surfaces. After using microfiber cleaning cloths, the trapped dust and dirt is visible. Cloths must be laundered separately (do not mix with non-microfiber materials) in hot water, either by machine or by hand.
Disposable Paper and Plastic Bags (Selection Based on Management Direction)
EPA Recommended Content Levels for Commercial/Industrial Paper Products
Bleaching process - environmentally preferable paper products recommended for use should meet the following standards for each of the following product categories:
Bathroom tissue - 20- 100% recovered content and 20-60% post-consumer content.
Toilet seat covers - minimum 100% recovered materials and 40% post-consumer content.
Paper towels - 40-100% recovered materials and 40-60% post-consumer content.
Plastic trash bags - 10-100% recovered materials and 10-100% post-consumer content.
Paper napkins - 30-60% post-consumer Content and 30-100% Recovered Content
Janitorial Equipment
In selection of all equipment it is preferable to select those that are durable, energy-efficient and quiet. Additional considerations for equipment selection include the following:
Vacuum cleaners must meet, at a minimum, the Carpet and Rug Institute (CRI) Green Label Program requirements and shall operate at a sound level of less than 70 dBA.
Carpet extraction equipment must meet at a minimum the Carpet and Rug Institute Bronze “Seal of Approval” for deep cleaning extractors.
Powered floor maintenance equipment must be equipped with controls or other devices for capturing and collecting particulates and shall operate at a sound level less than 70 dBA.
Propane-powered floor equipment must have low-emission engines certified by the California Air Resources Board (CARB) or the Environmental Protection Agency (EPA) for the specific engine size and operate with a sound level of less than 90dBA.
Current in-use propane-powered equipment may only be used when the building is unoccupied, and under conditions allowing for as much air circulation and exchange as possible.
Automatic powered scrubbing machines must be equipped with variable-speed feed pumps and on-board chemical metering to optimize the use of cleaning fluids.
Battery-powered equipment is equipped with environmentally preferable gel-batteries (If utilized)
Powered equipment is ergonomically designed to minimize the vibration, noise and user fatigue.
Equipment is designed with safeguards, such as rollers or rubber bumpers, to reduce potential damage to building surfaces
A current list of janitorial equipment used at the property will be on file in the management office.
A component of this plan also shall include a quarterly maintenance program that inspects and maintains the performance of janitorial equipment, as defined by the equipment vendor and records results in a maintenance log.
Where possible, equipment that eliminates or reduces chemical use and qualifies as a sanitizing device under EPA when used with water and no chemicals, including steam vapor equipment and spray/vacuum touch-free cleaning systems, must be used.
Dusting and Dust Mopping
Ensure that dust mops are properly treated to capture dust.
Use wide area vacuums fitted with appropriate bags/filters.
Use reusable lint-free dusting cloths or Microfiber technology in lieu of paper products or no feather dusters.
Entryways
Keep outside entryways clean and free of debris.
Use walk-off matting outside and inside entry for a minimum length of 12 continuous feet total. Vacuum walkoff mats at least daily and more frequently in high traffic entryways using a vacuum with a beater bar and vacuum in both directions.
Walk-off mats must be wet-cleaned once every two days and allowed to dry before being used. They should be and cleaned underneath once a day, and twice during inclement weather
Entry mats must be vacuumed using a vacuum with a beater bar in both directions, at least once a day and twice a day during inclement weather.
Appropriate dispose of captured vacuum cleaner material before half full.
Non-toxic and environmentally safe ice melting compounds (e.g., non-corrosive, non-phosphate) must be selected through the winter months.
Floor Care – General Maintenance
Select appropriate metal-free floor finishes that are extremely durable to minimize the need for stripping and recoating.
Build a solid base, which can be between 6 and 12 coats for a 20% solids floor finish.
Develop a system to maintain floors on a daily basis, using walk-off mats, dust mopping or vacuuming.
Use mops equipped with reusable/cleanable heads (clean daily)
Hard floors should be cleaned daily
Develop an interim restoration program
Floor Care – Floor Stripping
Notify occupants beforehand if a strip-out is scheduled.
Select the least toxic products available (see section on product selection). Mix and use products according to manufacturer's directions.
Use the appropriate personal protective equipment. Gloves, goggles and non-slip foot ware are a must. Aprons, may be necessary depending on products selected.
Ventilate both during and after stripping.
Floor Care – Restoration/Buffing and Burnishing
Make sure that adequate floor finish exists. Determine if it is time for a scrub and recoat.
Select the appropriate restoration product. Use water-based or low VOC products.
Apply in a stream or coarse spray to minimize amount that gets in the air to breathe and overspray. Do not overapply.
Select the appropriate equipment (see section on product selection). If burnishing, use a vacuum attachment. Use appropriate buffing/burnishing pads.
Establish an initial base of floor finish thick enough to maintain adequate levels of floor finish and appearances (buffed, burnished, scrubbed, etc.) that will last at least one year. Depending on the durability of the floor finish and the percentage of solids, it may require an initial base of 3 to 4 coats.
Carpet Care – General Maintenance
Ensure that vacuums are in good working order using appropriate bags and/or filters.
Vacuum should be emptied or replaced when half full.
Clean spills while fresh. Minimize the amount of moisture used during cleaning.
Food Areas: Cafeterias, Break rooms, Etc
Clean and sanitize floors, tables, etc.
Separate recyclables from trash and makes sure recyclable areas are kept clean (i.e. rinse soda cans) not to attract pests.
Make sure that occupants understand how to properly separate trash and recyclables and proper disposal of each. Refer to Section 3 – Recycling for more information.
Make sure that waste containers are covered and emptied at least daily.OSHA Blood‐Borne Pathogen Standard
Use safety cones or other means to make sure that occupants do not come in contact with spill.
Use proper personal protective equipment (i.e. gloves, goggles).
Disinfect area with appropriate solution.
Dispose properly in a red bag.
Measuring/Diluting Concentrated Cleaning Products
Use appropriate protective equipment when mixing concentrated cleaning products. This includes a control system such as a “wall mounted dispensing system for concentrates that limits the direct handling and worker exposure to chemicals, [and] ensures proper dilution of mixtures and prevents overuse and waste.”
Follow manufacturer's dilution directions.
Make sure that spray bottles (secondary containers) have appropriate labels.
Never mix different cleaning products together
Restrooms
Make sure sanitizing and disinfecting solutions are prepared and used properly (i.e. dwell time) and remix as required.
Frequently clean surfaces that hands touch to eliminate the spread of germs (i.e. door knobs, light switches, handles, etc.).
Frequently eliminate moisture.
Keep floors dry to eliminate slip falls and the build-up of bacteria, mold and mildew.
Standard Operating Procedures for Green Cleaning Maintenance System
SELECT will manage the cleaning process by taking a comprehensive process approach to cleaning according to the following principles:
Identifying the cleaning task and performance requirements
Defining or outlining steps of the cleaning procedure
Selecting the correct products and equipment (that satisfy the Green requirements set forth in the Green Cleaning Policy)
Training cleaning personnel to use correct procedures and to understand the potential health, safety, and environmental impacts of the cleaning products and processes
Ongoing inspection and monitoring programs
Communicating clearly with building occupants and practicing appropriate storage and disposal methods
Approaching building cleaning holistically (not just separate components)
Cleaning to protect health and safety
Recognizing occupant impacts on the indoor environment
Ensuring cleaning personnel and building occupant safety at all times
Being aware of the impacts to the outdoor environment (energy requirements, water usage, and disposal of products in terms of solid waste, down-the-drain to the appropriate water works, and emissions to the air during storage or use of products.)
Cleaning shall be done Sunday through Thursday. All cleaning products must be pre-approved by management (in accordance with the Green Cleaning Policy) and must be low VOC and non-fragrance wherever applicable. MSDS sheets must be kept on file and updated as appropriate in the property management office as well as by