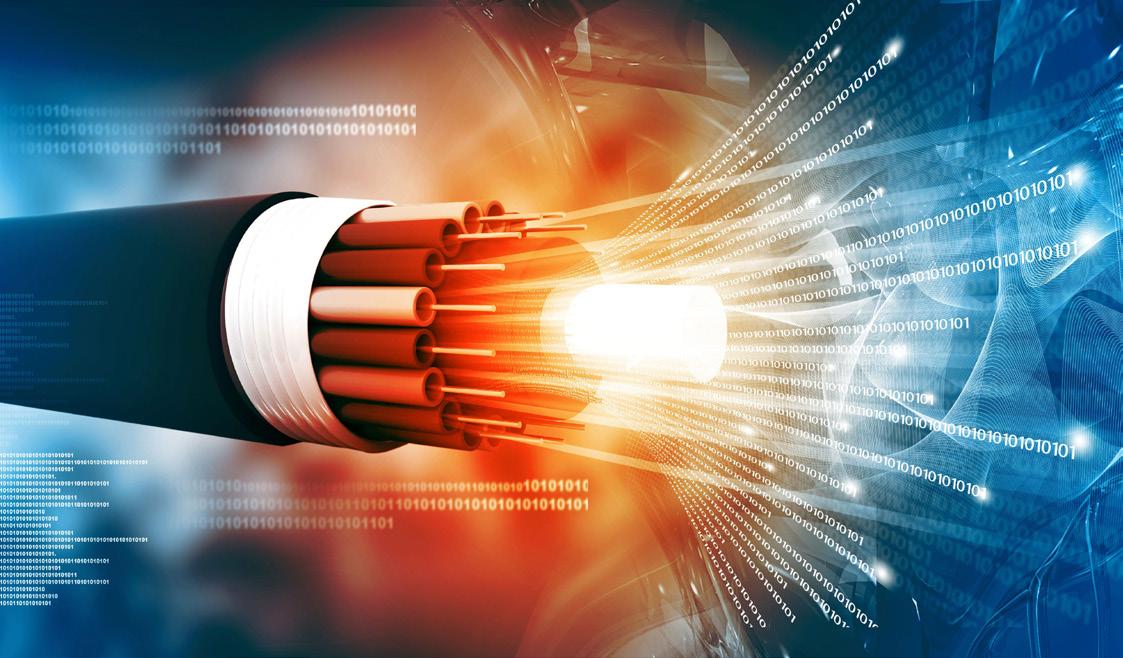
3 minute read
Providing a safer welding environment
Figure 3. Using photonics, DAS technology essentially turns a fibre optic cable running alongside a pipeline network into thousands of vibration sensors.
lights and audio, acting as a deterrent and preventing a theft attempt.
Preventing long-term damage Having identified an incident and deterred criminals, it is vital to ensure that no long-term damage to the pipeline has occurred that could cause a serious future incident. For example, if the criminals had already started to strike or to hammer the pipeline while digging, they could have caused mechanical damage such as dents with metal loss or gouging. These dents could threaten the pipeline’s integrity resulting in future cracks, leaks or ruptures. Being aware of everything that is happening around the pipeline is the only way to ensure the safety and security of the pipeline. Frequent monitoring of the pipeline is essential to preventing theft and protecting against long-term mechanical damage. This can be achieved confidently with the real-time monitoring that DAS provides over vast lengths of pipeline. DAS delivers a pipeline with no security gaps. This increases the efficacy and accuracy of identifying potential breeches, as well as boosting the speed of response through the real-time detection of incidents anywhere on the pipeline. As the trend for oil prices continues to rise and criminal ganges see the opportunities, the need for a robust security strategy becomes ever more pressing. A
DAS monitoring system with integrated UAV technology creates a powerful detection and response system particularly for extreme locations. They can alert criminals of detection, ultimately capable of preventing illegal hot-tapping of pipelines as well as preventing any potential resulting safety and environmental disasters.
References
1. www.statista.com/statistics/409404/forecast-for-uk-brent-crude-oil-prices/ 2. www.reuters.com/business/energy/exclusive-colombia-oil-theft-surgessmuggled-gasoline-dries-up-data-show-2021-11-08/ 3. www.thisdaylive.com/index.php/2022/02/16/massive-oil-theft-high-pipelinerepairs-cost-bleeding-nigerias-economy/ 4. en.wikipedia.org/wiki/Tlahuelilpan_pipeline_explosion
ADDING ADDING VERSATILITY VERSATILITY
Midwestern’s line of high-performance recovery
winches with line pull from 30,000 to 100,000 lb, can be installed on various types of construction equipment. These winch packages tie into the machine hydraulics, use the existing cab controls, and are easy to install. Make your equipment more versatile by adding on one of our recovery winches. MIDWESTERN - built for the
toughest jobs.
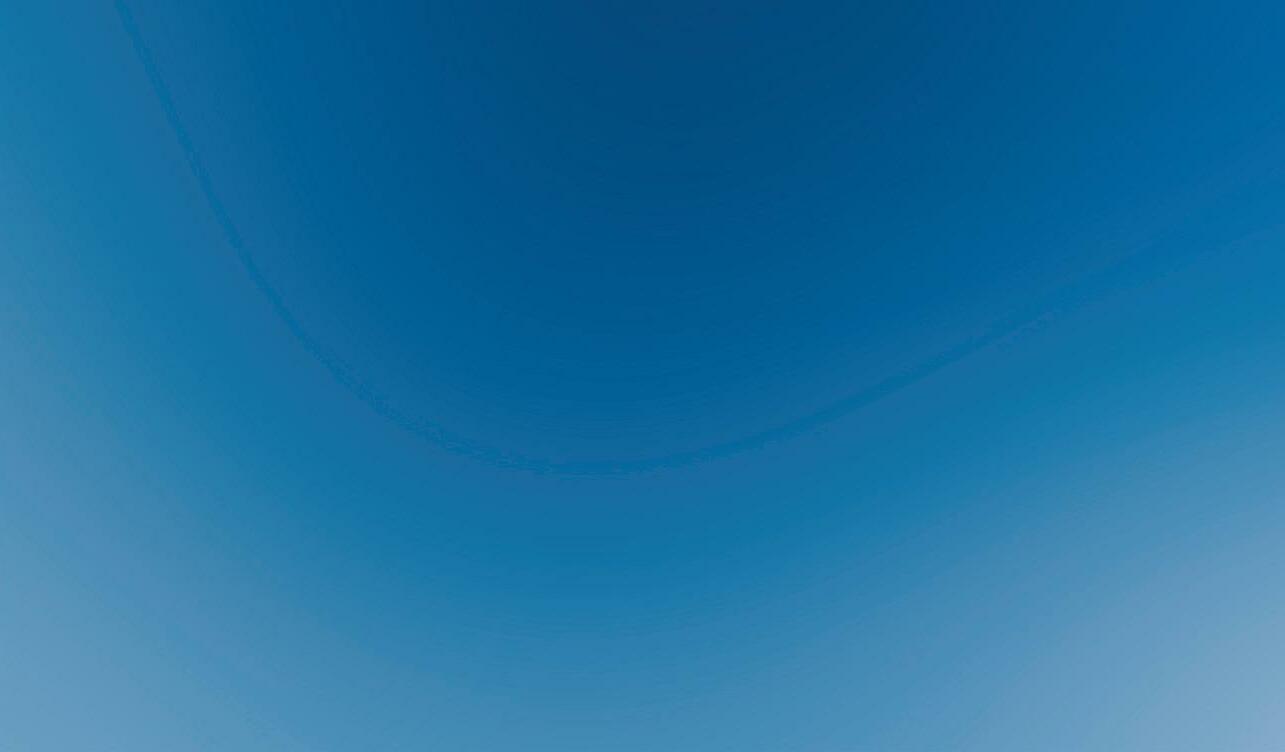
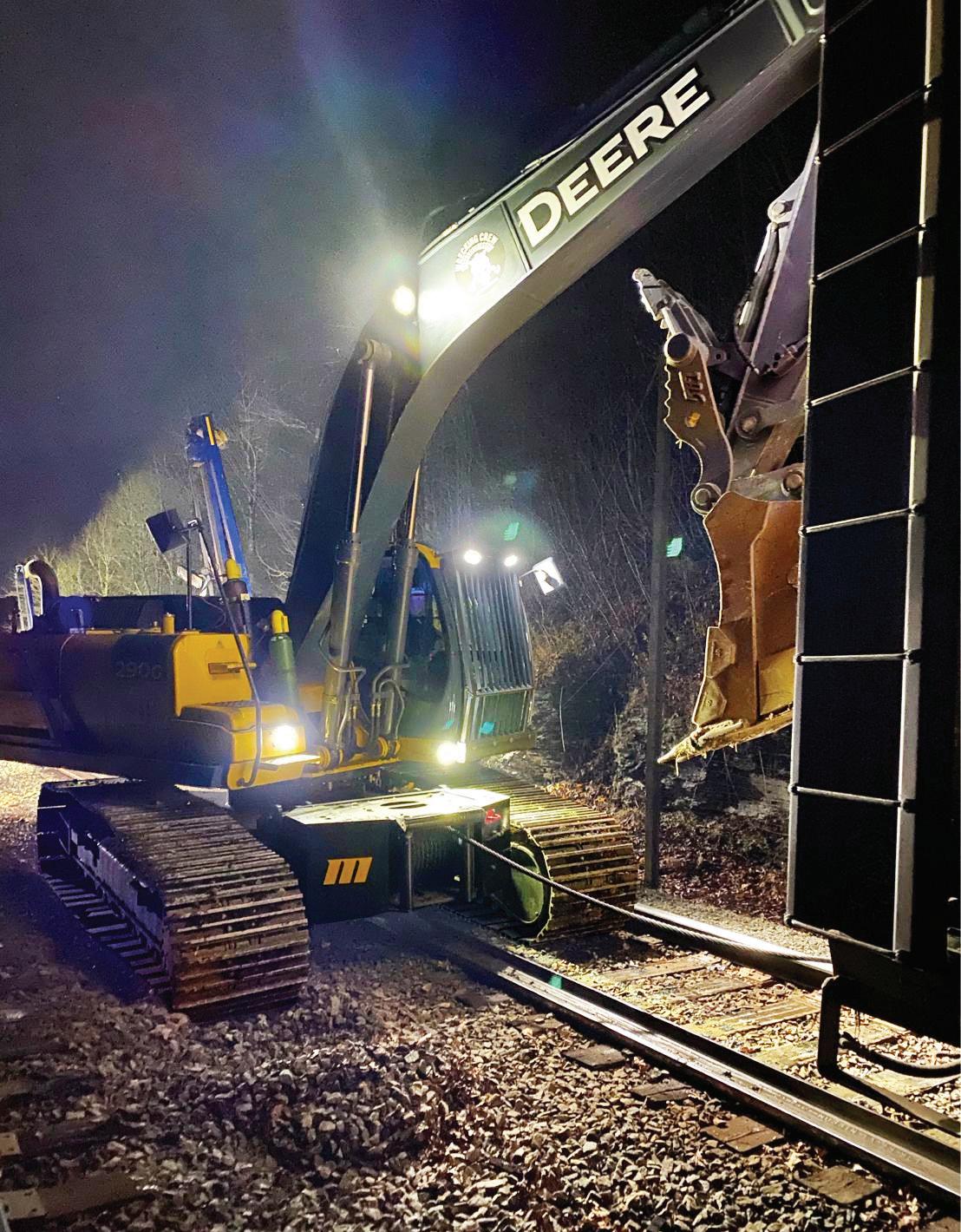
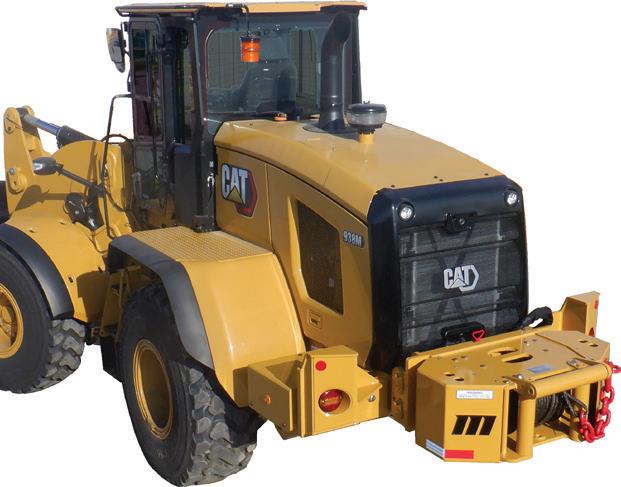
on CAT 938M 30,000 lb line pull on JD 300G 100,000 lb line pull
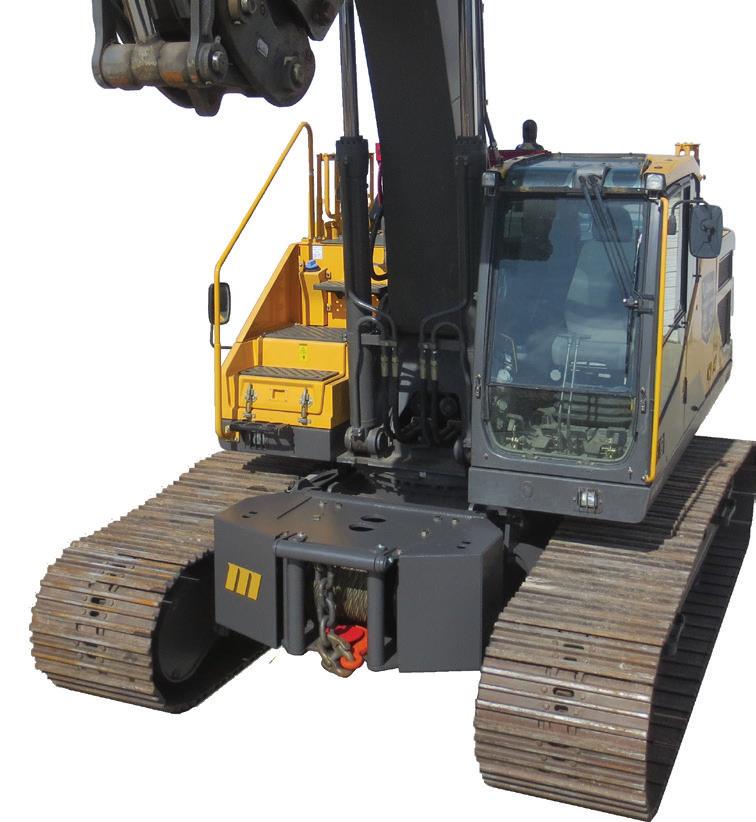
Weld cameras allow operators to work remotely, therefore remove themselves from a danger zone, explains Cameron Serles, President of Xiris Automation Inc., Canada.
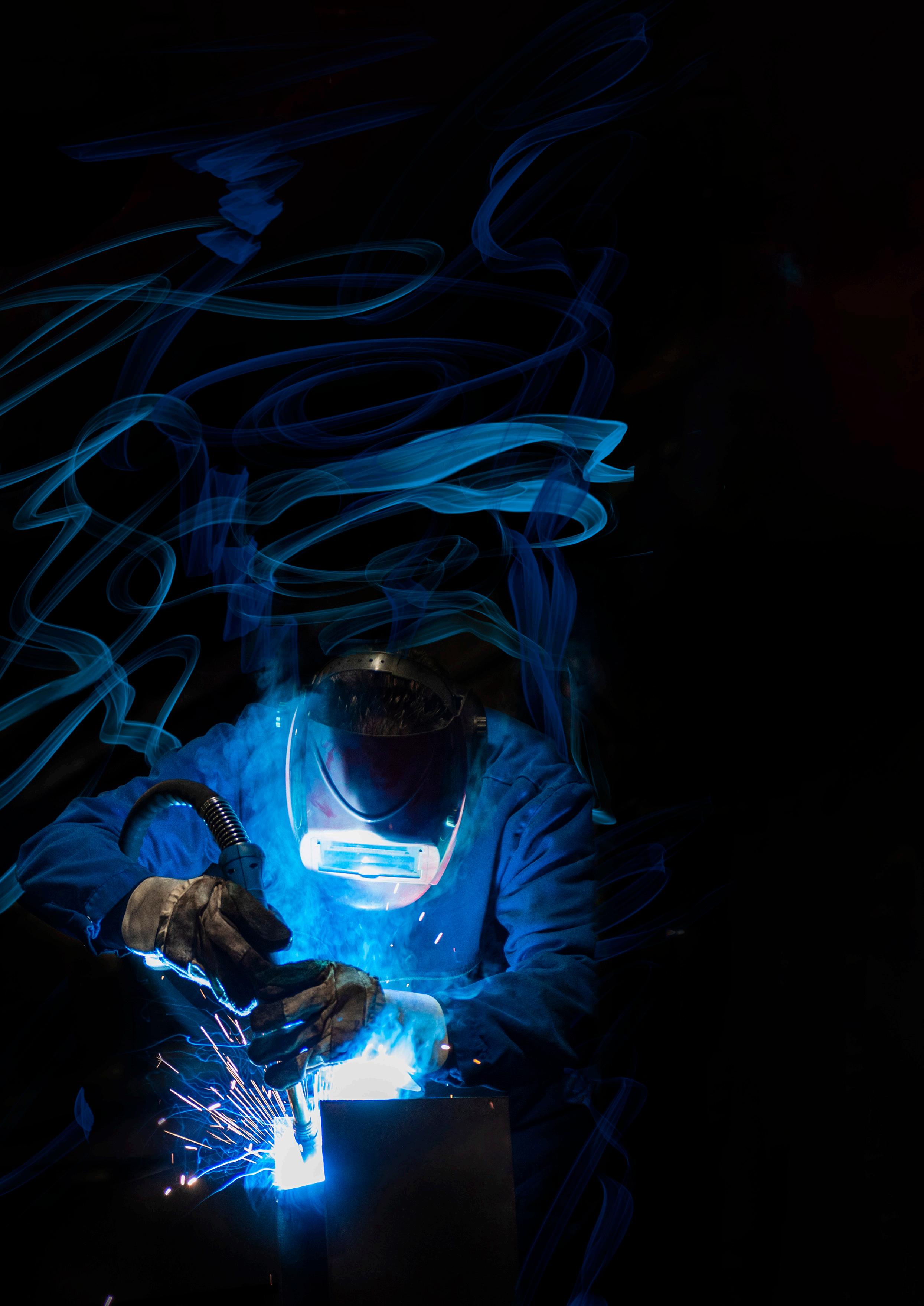
Acting as the veins of a region, pipeline infrastructure is essential in transporting energy to help us live comfortably. Carrying water, gas, oil and more, these materials get distributed to power plants, businesses, and consumer homes, and wherever these pipelines are, welding follows.
As in many industries, metal joining is required in pipeline construction to install and maintain pipes across critical networks of pipelines. With extensive demands of the job, pipeline welders are required to have experience and expertise in dealing with potentially dangerous materials, often in harsh weather conditions and knowing how and when to use different welding techniques. There are serious potential economic and environmental consequences should there be any mistakes made in the welding process, as they could jeopardise the entire network of pipelines. As a result, there is emphasis on quality and consistency in pipeline construction and why typically, pipeline companies will perform automated orbital welding processes. In an orbital welding process, the torch is travelling 360˚ around the outside of the tube or pipe continuously. Two pieces of the tube or pipe are held in place by clamps powered by hydraulic pressure, to be joined together in the field. An automated orbital welding process provides precise